无碳小车 设计说明
无碳小车 设计说明
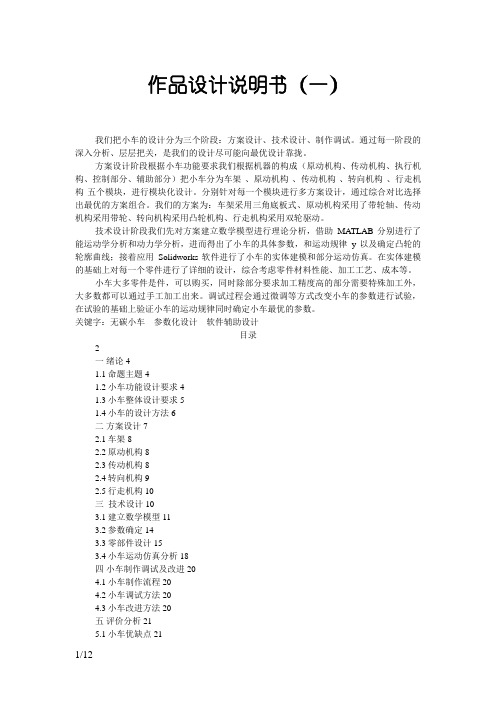
作品设计说明书(一)我们把小车的设计分为三个阶段:方案设计、技术设计、制作调试。
通过每一阶段的深入分析、层层把关,是我们的设计尽可能向最优设计靠拢。
方案设计阶段根据小车功能要求我们根据机器的构成(原动机构、传动机构、执行机构、控制部分、辅助部分)把小车分为车架、原动机构、传动机构、转向机构、行走机构五个模块,进行模块化设计。
分别针对每一个模块进行多方案设计,通过综合对比选择出最优的方案组合。
我们的方案为:车架采用三角底板式、原动机构采用了带轮轴、传动机构采用带轮、转向机构采用凸轮机构、行走机构采用双轮驱动。
技术设计阶段我们先对方案建立数学模型进行理论分析,借助MATLAB分别进行了能运动学分析和动力学分析,进而得出了小车的具体参数,和运动规律y以及确定凸轮的轮廓曲线;接着应用Solidworks软件进行了小车的实体建模和部分运动仿真。
在实体建模的基础上对每一个零件进行了详细的设计,综合考虑零件材料性能、加工工艺、成本等。
小车大多零件是件,可以购买,同时除部分要求加工精度高的部分需要特殊加工外,大多数都可以通过手工加工出来。
调试过程会通过微调等方式改变小车的参数进行试验,在试验的基础上验证小车的运动规律同时确定小车最优的参数。
关键字:无碳小车参数化设计软件辅助设计目录2一绪论41.1命题主题41.2小车功能设计要求41.3小车整体设计要求51.4小车的设计方法6二方案设计72.1车架82.2原动机构82.3传动机构82.4转向机构92.5行走机构10三技术设计103.1建立数学模型113.2参数确定143.3零部件设计153.4小车运动仿真分析18四小车制作调试及改进204.1小车制作流程204.2小车调试方法204.3小车改进方法20五评价分析215.1小车优缺点215.2小车改进方向21六 22一绪论1.1命题主题根据第四届全国大学生工程训练综合能力竞赛主题为“无碳小车越障竞赛”。
命题与高校工程训练教学内容相衔接,体现综合性工程能力。
无碳小车设计说明书

无碳小车设计说明书小组成员:指导教师:学校:一. 设计思路:1.根据设计要求,为达到无碳小车走8字形轨迹重叠的目的,无碳小车应具备重力势能的转换和周期性的转向的功能,即小车分为传动机构和导向机构两部分。
其中传动机构要求能量损耗少、传动比精确,故优先选用齿轮和皮带轮传动。
导向机构要求方向控制度高、摩擦损失小,选用凸轮直线滑块机构。
2.为减轻车身质量同时保证小车刚度要求,小车采用尼龙作为底板材料,上面安装轴承座以支撑输入轴、驱动轴、吊挂重物的立杆等,小车导向机构中的滑块也需固定在底板上。
4.通过计算并确定两齿轮的传动比i,并实现小车驱动轮每行走i个周长长度,转向机构运动实现一个周期,小车也行走一个完整的8字路线。
为了使小车适应不同间距桩,我们采用凸轮机构,控制小车走重叠的8字,使得小车的工作效率更高。
二. 工作原理:当重物下落时,细绳绕过立杆定滑轮带动驱动后轮上面的绕线轮,驱动中间齿轮转动驱动后轮前进,同时通过齿轮啮合传动带动凸轮旋转,带动转向前轮周期性左右转向,从而实现小车在前进过程中自动转向。
这样小车便能在重力势能驱动下沿着“8”形路线前进,并能自动绕过障碍物。
三、设计说明我们可以将小车行走路线简化为余弦曲线和两段圆弧来处理,通过小车的传动比以及驱动轮的大小我们可以计算出该余弦曲线的幅值,可计算出小车的出发点,我们将小车出发位置定在向左转弯的圆弧中点。
我们以绕8字的两个桩位置方向为X轴,在水平面内垂直于X轴为Y 轴方向,通过计算桩间距,障碍物距离,传动比,驱动轮周长可以得出确定曲线方程,通过数学知识我们可以得出小车在出发点的前轮偏向角度(即凸轮角度),偏向角度可以适当调节。
由此我们便可以得出小车出发时垂直摆桩方向的距离以及此时小车前轮的偏向角度,从而确定小车的理论出发位置。
四、设计总结对于大赛给定的命题,重力势能转换为机械能的能量转换原理是设计的重点之一,小车动力传动结构和摩擦传动装置的设计是最重要的部分。
无碳小车结构设计报告_4

无碳小车结构设计报告一、设计概述根据题目要求,为达到“8”字绕行的目的,无碳小车应实现两个功能:重力势能的转换和周期性的转向。
据此可以将小车分为驱动机构和转向机构两部分。
驱动机构要求能量损耗小、传动比准确,优先选用齿轮机构。
转向机构因为轨迹重复性要求高,采用齿轮和拉杆结合控制前轮转向来满足小车走周期性“8”字要求。
二、设计方案1.小车以钢板做的底板为主体,上面安装三根吊挂重物的立杆。
2.使用滑轮机构将重块的能量通过细绳以转矩的形式传递到输入轴。
3.输入轴通过一级齿轮传动将能量传到驱动轴,带动驱动轮并驱使小车向前运动。
4.输入轴转动一圈,带动转动的大齿轮转动四分之一,使与之啮合的小齿轮转动二分之一,用连杆机构链接,使前轮走了一个圆时实现转向,从而小车走了“8”字形运动。
三、相关计算驱动机构转向齿轮(控制方向)转向机构(控制周期)1主动轮2驱动轮3主动轮4从动轮传动比2.5:1传动比1:2 主要零件尺寸:前轮半径后轮半径驱动1半径驱动2半径转向3半径转向4半径转向1半径转向2半径5mm 50mm 35mm 14mm 35mm 14mm 30mm 30mm厚度为10mm 厚度为6mm 设为转角30度,两个障碍物的距离为300毫米:设为小车的轨迹半径为x,则150*150-75*75=16875,对其开方约得130毫米。
由此可知,小车的轨迹为3.14*2*130*2=1632.8毫米,车轮要转5圈,所以轴的周长为2毫米才能保证小车在理论上转了8圈。
四、整体装配图五、作品创意1.优化各零件布局,降低小车重心2.三根立杆防止小车运行中重块摞动3. 不用其它额外的传动装置,直接由动力轴驱动轮子和转向机构,此种方式效率高、结构简单。
在不考虑其它条件时这是最优的方式。
4.曲柄连杆面积所受压力较小,且面接触便于润滑,故磨损减小,制造方便,已获得较高精度;两构件之间的接触是靠本身的几何封闭来维系的,它不像凸轮机构有时需利用弹簧等力封闭来保持接触5.小车机构简单,单级齿轮传动,损耗能量少六、心得与体会在设计无碳小车的环节中,我们在此过程当中反复探索、不断前进。
无碳小车设计报告

2014年****工程训练综合能力竞赛无碳小车设计报告参赛者:指导老师:2014/10/151、设计概述“无碳小车”是将重力势能转换为机械能,使小车实现行走及转向功能的装置。
小车由能量转换机构、传动机构、转向机构和车身构成,首先通过能量转换机构获得动力来驱动后轮转动,继而通过传动机构将运动传给转向机构使转向轮,利用横纵向直线运动复合运动使转向轮呈正弦波形周期性摆动,从而避开设置在波形内固有间距的障碍物。
具体设计为小车以1kg重物块下落500mm产生的重力势能作为动力,通过线绳带动齿轮轴等传动机构,单轮驱动;通过正弦机构带动前轮周期性摆动实现转向。
无碳小车结构设计总装图如图所示。
2、设计思路和方案小车的设计分为三个主要阶段:功能分析、、制造加工调试2.1功能分析对小车功能要求进行分析,寻找功能元解,将小车分为车架、原动机构、传动机构、转向机构、行走机构、微调机构六个模块。
对每一个模块进行多方案设计,综合对比选择最优的方案组合。
2.2参数分析与个性化设计利用Solidworks软件进行小车的实体建模、部分运动仿真。
对方案建立数学模型进行理论分析,使用MATLAB软件分别进行能耗规律分析、运动学分析、动力学分析、灵敏度分析,得出小车的具体参数和运动规律。
2.3 机械总功能分解及功能元解表1.势能转向小车形态学矩阵2.4 机构选型基本原则①满足工艺动作和运动要求。
②结构最简单,传动链最短。
③原动机的选择有利于简化结构和改善运动质量。
④机构有尽可能好的动力性能。
⑤机器操纵方便、调整容易、安全耐用。
⑥加工制造方便,经济成本低。
⑦具有较高的生产效率与机械效率。
2.5转向机构分析目前,能够实现无碳小车车轮转向控制的机构主要有曲柄摇杆机构、正弦机构(曲柄移动导杆机构)、RSSR空间四杆机构凸轮推杆机构和圆轮导杆机构。
这5 种机构在结构和功能上有各自的特点。
转向机构是本小车设计的关键部分,直接决定着小车的功能。
转向机构也同样需要尽可能的减少摩擦耗能,结构简单,零部件已获得等基本条件,同时还需要有特殊的运动特性。
无碳小车设计说明

无碳小车设计说明设计说明:无碳小车设计背景:现在的交通工具使用化石燃料作为能源,不仅对环境造成了严重的污染,还加剧了全球变暖的问题。
为了解决这个问题,设计了一种无碳小车,它使用清洁能源作为驱动力,减少对环境的污染。
设计目标:1.使用清洁能源作为驱动力,减少对环境的污染。
2.提供舒适的乘坐体验和良好的操控性能。
3.具备足够的续航里程和快速充电功能。
4.物理结构紧凑,方便停放和携带。
5.引入智能控制系统,提供高效的安全性和智能交互。
设计特点:1.清洁能源驱动:无碳小车使用电能作为驱动力,充电器可使用太阳能或者风能进行充电,以减少对传统能源的依赖。
2.舒适性和操控性能:小车配备高质量的悬挂系统和减震系统,确保乘坐舒适性。
此外,小车采用电动驱动系统,提供平稳加速和操控性能。
3.续航里程和快速充电功能:小车配备高效的电池系统,提供足够的续航里程,以满足日常通勤需求。
同时,可支持快速充电功能,短时间内充电至80%以上。
4.紧凑的物理结构:小车采用紧凑的物理结构设计,尺寸较小,方便停放和携带,适合城市环境使用。
5.智能控制系统:小车配备智能控制系统,包括导航系统、安全辅助系统和智能交互界面。
导航系统可以提供最佳路线规划和实时交通信息,安全辅助系统可提供驾驶员警示和自动刹车等功能,智能交互界面可以通过语音或手势控制实现乘坐舒适性和便利性。
实施方案:1.动力系统设计:小车采用纯电动驱动系统,电池系统采用高能量密度的锂离子电池,以提供足够的续航里程。
充电器可以使用太阳能充电板或风力充电机,充电时间约为4小时。
2.悬挂系统设计:小车配备高质量的悬挂系统,以提供舒适的乘坐体验。
采用独立悬挂设计,可根据路面情况自动调节减震幅度。
3.控制系统设计:小车配备智能控制系统,包括中央控制单元、传感器和执行器。
中央控制单元接收传感器数据,并将其转换为相应的控制信号,通过执行器实现对小车的控制。
该系统可以提供导航、安全辅助、车辆诊断等功能。
无碳小车设计说明

其它的一些细节设计
车身的设计 车轮的设计 轴承的设计 车身部件的一些材料的取用 以上的各种细节设计都要以减小小车重力和阻 力为目的 ,同时要考虑其价钱的多少和设 同时要考虑其价钱的多少和设 计出来的艺术效果。 计出来的艺术效果。
驱动部分的大致结构图
物体在下落过程中所受到的阻力图
阻 力
速 度
驱动
原理:绳拉力为动力。 原理:绳拉力为动力。将物块下落的势能尽 可能多的转换为小车的动能, 可能多的转换为小车的动能,进而克服阻力 做功。 做功。物块在下落的过程中不可避免的要与 小车发生碰撞,碰撞过程必然要有能量损失, 小车发生碰撞,碰撞过程必然要有能量损失, 所以要解决的问题: 下降过程中 下降过程中, 所以要解决的问题:1下降过程中,尽可能的 降低下落的速度; 在将要下降到小车时 在将要下降到小车时, 降低下落的速度;2在将要下降到小车时,改 变转速比,使物块减速下落, 变转速比,使物块减速下落,进一步减少碰 撞损耗。 撞损耗。
小车的运动轨迹
其他方面的一些想法
1,在后轮转轴上安放多个不同半径的带轮, ,在后轮转轴上安放多个不同半径的带轮, 微调转矩,适应不同的环境下阻力的不同。 微调转矩,适应不同的环境下阻力的不同。 2,传输功率 转矩 角速度 ,通过一系列 转矩X角速度 通过一系列 ,传输功率=转矩 的齿轮,带轮,转轴产生转速比, 的齿轮,带轮,转轴产生转速比,使作用 在后轮的转矩和阻尼转矩平衡, 在后轮的转矩和阻尼转矩平衡,物块低速 匀速下落。 匀速下落。 3,制作多套后轮,微调转矩。改变后轮时, ,制作多套后轮,微调转矩。改变后轮时, 也要相应的改变转向传动轮的大小, 也要相应的改变转向传动轮的大小,同时 保持车身水平,适当调整前轮转轴的长度。 保持车身水平,适当调整前轮转轴的长度。
无碳小车设计说明书
无碳小车设计说明书目录一、本作品的创新与特色简介;二、设计方案拟定;三、动力与传动方案的设计、计算与分析;四、动作执行机构的设计、计算与分析;五、其它设计计算与说明,设计总结;一:本作品的创新与特色简介;①所有的动力来自载荷重物,所纯机械结构,无碳排放;②在转向方面,采用内凸轮连杆机构,使得转向的角度、时间更加精确,并辅助以有图的可调机构,是转向调节更加明确。
③在重物下落阶段,增加了一动滑轮,使得做功行程加长,并合理的利用了扭矩。
④绕桩曲线部分的轨迹无需精确的计算出,由上图的机构可在完成后对中间连杆进行调试,已达到目标要求。
二:设计方案拟定;小车的方案设计关键在于传动部分与转向部分。
①传动部分;传动部分的问题在于是用什么进行传动,齿轮、带轮、直接驱动等。
最后结合传动的效率、制作的难易程度,最终确定了采用二级齿轮进行传动,如有图所示。
此方案的优点在于,以中间轴为主动轴,以小于1的传动比带动后轮,再以大于1的传动比带动凸轮轴,这样就很好的解决了行驶路程与转向周期间的关系,并且将传动比控制在合理数值内。
另外,以一个动滑轮来增加做功行程,减小瞬时扭矩,使小车前进平缓。
缺点在于,采用了二级齿轮组,使得摩擦耗能增加,机械效率降低。
②转向部分;转向部分在于采用什么机构,最大的争议在于是采用内凸轮还是外凸轮。
最终确定是采用内凸轮连杆机构。
原因在于采用外凸轮的话需要在连杆的回程部分提供一个力——增加一个弹簧;如果这样的话,可能会因为的弹簧的弹性系数,及位置的放置问题上增加设计的难度。
而采用内凸轮的话就不存在这些问题,不过增加了整体的重量,但这可以通过将凸轮在合理的条件下将其镂空来解决。
为了使后期调整时有更大的可能性,因此在连杆部分采用了右图的结果,如此便可以使小车的转向更加的准确。
③材料方面;除了前后轮采用有机玻璃之外,其余的材料都采用铝材。
底板:厚3mm的铝板,300*160*3.后轮:直径160的有机玻璃,厚5mm。
《无碳小车设计说明》-公开课件
·在整个过程中,重力势能完 全转换为小车运动过程的损
耗。使小车行进的更远.
4.细节设计
· 车身 · 车轮 · 轴承 以减小小车重力和动过程
· 传输功率=转矩X角速度 ,通过一系列的齿 轮,带轮,转轴产生转速比,使作用在后 轮的转矩和阻尼转矩平衡,物块低速匀速 下落。
· 在后轮转轴上安放多个不同半径的带轮, 微调转矩,适应不同的环境下阻力的不同。
· 制作多套后轮,微调转矩。改变后轮时, 也要相应的改变转向传动轮的大小,同时 保持车身水平,适当调整前轮转轴的长度。 (现场可实现)
无碳小车设计说明
· 构架 · 转向部分 · 驱动部分 · 细节说明
1.构架部分
· 小车采用三轮结构(1个转向,2个驱动) · 重物落差0.5米物重1kg.
2.转向
· 转向机构与驱动轴相连
· 小车的转向轮周期性的摆动
· 计算传动机构,使小车行使200厘米时,转 向轮摆动一个周期。
· 确定连杆在转盘有位置,尽量减小转向轮 的摆动角度,从而使小车先驱的实际距离 变大。确定初始位置与摆轮角度的关系。
3.驱动
· 原理:绳拉力为动力。将物块下落的势能 尽可能多的转换为小车的动能,进而克服 阻力做功。物块在下落的过程中不可避免 的要与小车发生碰撞,碰撞过程必然要有 能量损失,所以要解决的问题:1下降过程 中,尽可能的降低下落的速度;2在将要下 降到小车时,改变转速比,使物块减速下 落,进一步减少碰撞损耗。
·
二、小车的起始和结束过程
· 梯形原动轮的设计实现小车的起 动和物块的从低速到减速下落。 减小因碰撞而损失的能量。
梯形原动轮
无碳小车设计说明书
无碳小车设计说明书一、基本构思通过对小车的功能分析小车需要完成重力势能的转换、驱动自身行走、形成固定路线。
在小车行走时尽量较小摩擦,实现能量较大化的转换。
而且需要灵活绕过障碍物。
在选择方案时综合考虑功能、材料、加工、制造成本等各方面因素,同时尽量避免直接决策,减少决策时的主观因素,使得选择的方案能够综合最优。
二、驱动机构1.通过重物自由下落,将重力势能转化为动能,由重物下落带动绕线轮转动,从而实现能量的转换。
2.为了增加下车的稳定性,在设计重物支撑杆时采用了三根杆,这样在小车转弯的时候控制重物左右摆动的角度。
3.在设计绕线轮时综合考虑到,要让小车跑的稳定,能轻松启动,而且跑得更远,设计成一个半径较小的二阶的绕线轮。
4.为了增加美光和方便,将固定线直接套在轴上,这样减小工作量,而且更美观更便捷。
三、传动机构1.重物的下落通过绕线轮(黄色)带动主动轴转动,然后通过二级齿轮(红色)将动力传递到后轮从动轴,从而驱动后轮转动。
2.二级齿轮实现对能量的储存。
四、转向机构(绿)1.转向机构采用偏心轴+曲柄、连杆机构(蓝色)。
U型槽的圆周运动通过连杆转化为曲柄的前后摆动,从而实现小车前轮的摆动。
(具有简单、高效、摩擦力小、能量损耗小的特点)2.还有可以无极可调。
这实现了创新,也非常符合比赛规则。
五、车身及其后轮等其他机构1.将其中的一个后轮变为从动轮,保证了小车的正常运行,而且增加差速,让下车启动更加轻松容易,跑的的也更加稳定。
2.降低了底板的高度,增加了小车的稳定性3.支撑杆支座的设计,采用尼龙,使车身更轻,更加美光。
4.后轮选用亚克力板,在车轮三割去三个圆形快,减轻车身重量,强度达到要求,美观实用。
无碳小车说明书
无碳小车设计说明书学院: 行知工学分院班级: 机械132班学生姓名:学号:指导老师:完成时间: 2015 年 6 月 15日1、绪论1、1小车得设计命题设计一种小车,驱动其行走及转向得能量就是根据能量转换原理,由给定重力势能转换来得。
给定重力势能为4焦耳(取g=10m/s2),设计时统一用质量为1Kg得重块(¢50×65 mm,普通碳钢)铅垂下降来获得,落差400±2mm,重块落下后,须被小车承载并同小车一起运动,不允许从小车上掉落。
如图1、1所示。
图1、1要求小车行走过程中完成所有动作所需得能量均由此重力势能转换获得,不可使用任何其她得能量来源。
要求小车具有转向控制机构,且此转向控制机构具有可调节功能,以适应放有不同间距障碍物得竞赛场地。
要求小车为三轮结构,具体设计、材料选用及加工制作均由学生自主完成。
1、2小车得整体设计要求小车设计过程需要完成:机械设计、工艺方案设计、经济成本分析与工程管理方案设计。
命题中得工程管理项要求综合考虑材料、加工、制造成本等各方面因素,提出合理得工程计划。
设计能力项要求对参赛作品得设计具有创新性与规范性。
命题中得制造工艺能力项要求综合运用加工制造工艺得知识。
1、3小车得设计方法在小车得设计方法上,我们借鉴了参数化设计、优化设计、系统设计等现代设计发明理论方法。
采用CAXA、SolidWorks2012等辅助软件设计。
2、设计方案2、1尺寸设计由于小车实在平面上运行,转弯半径较小,所以定小车得宽度为150mm,长度为150mm,使其能拥有更佳得灵活性。
如图2、1所示。
图2、12、2最大转角因为小车长为150mm,当绕过最大偏移距离为500mm得圆弧时能得到最大转角,如图3、2所示,即可得最大转角位26、897°、如图2、2所示。
、、图2、2设曲柄长度为10,已知最大转角位26、897°,由图2、3所示可知可得最大偏移距离图2、3偏移距离L=10 /tan(26、897°)=19、71mm2、3后轮直径设计传动机构得功能就是把动力与运动传递到转弯机构与驱动轮上。
- 1、下载文档前请自行甄别文档内容的完整性,平台不提供额外的编辑、内容补充、找答案等附加服务。
- 2、"仅部分预览"的文档,不可在线预览部分如存在完整性等问题,可反馈申请退款(可完整预览的文档不适用该条件!)。
- 3、如文档侵犯您的权益,请联系客服反馈,我们会尽快为您处理(人工客服工作时间:9:00-18:30)。
作品设计说明书摘要我们把小车的设计分为三个阶段:方案设计、技术设计、制作调试。
通过每一阶段的深入分析、层层把关,是我们的设计尽可能向最优设计靠拢。
方案设计阶段根据小车功能要求我们根据机器的构成(原动机构、传动机构、执行机构、控制部分、辅助部分)把小车分为车架、原动机构、传动机构、转向机构、行走机构五个模块,进行模块化设计。
分别针对每一个模块进行多方案设计,通过综合对比选择出最优的方案组合。
我们的方案为:车架采用三角底板式、原动机构采用了带轮轴、传动机构采用带轮、转向机构采用凸轮机构、行走机构采用双轮驱动。
技术设计阶段我们先对方案建立数学模型进行理论分析,借助MATLAB分别进行了能运动学分析和动力学分析,进而得出了小车的具体参数,和运动规律y 以及确定凸轮的轮廓曲线;接着应用Solidworks软件进行了小车的实体建模和部分运动仿真。
在实体建模的基础上对每一个零件进行了详细的设计,综合考虑零件材料性能、加工工艺、成本等。
小车大多零件是标准件,可以购买,同时除部分要求加工精度高的部分需要特殊加工外,大多数都可以通过手工加工出来。
调试过程会通过微调等方式改变小车的参数进行试验,在试验的基础上验证小车的运动规律同时确定小车最优的参数。
关键字:无碳小车参数化设计软件辅助设计目录小车改进方向 (21)一绪论命题主题根据第四届全国大学生工程训练综合能力竞赛主题为“无碳小车越障竞赛”。
命题与高校工程训练教学内容相衔接,体现综合性工程能力。
命题内容体现“创新设计能力、制造工艺能力、实际操作能力和工程管理能力”四个方面的要求。
小车功能设计要求给定一重力势能,根据能量转换原理,设计一种可将该重力势能转换为机械能并可用来驱动小车行走的装置。
该自行小车在前行时能够自动避开赛道上设置的障碍物(间隔范围在700-1300mm,放置一个直径20mm、长200mm的弹性障碍圆棒)。
以小车前行距离的远近、以及避开障碍的多少来综合评定成绩。
给定重力势能为4焦耳(取g=10m/s2),竞赛时统一用质量为1Kg 的重块( 50×65 mm,普通碳钢制作)铅垂下降来获得,落差400±2mm,重块落下后,须被小车承载并同小车一起运动,不允许掉落。
要求小车前行过程中完成的所有动作所需的能量均由此能量转换获得,不可使用任何其他的能量形式。
小车要求采用三轮结构(1个转向轮,2个驱动轮),具体结构造型以及材料选用均由参赛者自主设计完成。
小车整体设计要求小车设计过程中需要完成:结构方案设计、工艺方案设计、经济成本分析和工程管理方案设计。
命题中的工程管理能力项要求综合考虑材料、加工、制造成本等各方面因素,提出合理的工程规划。
设计能力项要求对参赛作品的设计具有创新性和规范性。
命题中的制造工艺能力项以要求综合运用加工制造工艺知识的能力为主。
小车的设计方法小车的设计一定要做到目标明确,通过对命题的分析我们得到了比较清晰开阔的设计思路。
作品的设计需要有系统性规范性和创新性。
设计过程中需要综合考虑材料、加工、制造成本等给方面因素。
二方案设计为了方便设计这里根据小车所要完成的功能将小车划分为五个部分进行模块化设(车架、原动机构、传动机构、转向机构、行走机构)。
在选择方案时应综合考虑功能、材料、加工、制造成本等各方面因素,同时尽量避免直接决策,减少决策时的主观因素,使得选择的方案能够综合最优。
车架车架不用承受很大的力,精度要求低。
考虑到重量加工成本等,车架采用塑料加工制作成三角式底板。
原动机构原动机构的作用是将重物的重力势能转化为小车的驱动动能。
能实现这一功能的方案有多种,就效率和简洁性来看绳轮最优。
小车对原动机构还有其它的具体要求。
1.驱动力适中,不至于小车拐弯时速度过大倾翻,或重物晃动厉害影响行走。
2.到达终点前重物竖直方向的速度要尽可能小,避免对小车过大的冲击。
同时使重物的势能尽可能的转化到驱动小车前进的动能,如果重物竖直方向的速度较大,重物本身还有较多势能未释放,能量利用率不高。
3.机构简单,效率高,便于加工制作。
传动机构传动机构的功能是把动力和运动传递到转向机构和驱动轮上。
要使小车行驶的更远及按设计的轨道精确地行驶,传动机构必需传递效率高、传动稳定、结构简单重量轻等。
1.带轮具有结构简单、传动平稳、价格低廉、缓冲吸震等特点但其效率不是很高。
2.齿轮具有效率高、结构紧凑、工作可靠、传动比稳定但价格较高,不易加工制作。
因此在第一种方式不能够满足要求的情况下可优先考虑使用齿轮传动。
转向机构转向机构是本小车设计的关键部分,直接决定着小车的功能。
转向机构也同样需要尽可能的减少摩擦耗能,结构简单,零部件已获得等基本条件,同时还需要有特殊的运动特性。
能够将旋转运动转化为满足要求的来回摆动,带动转向轮左右转动从而实现拐弯避障的功能。
能实现该功能的机构有:凸轮摇杆、曲柄连杆等等。
凸轮摇杆:优点:只需设计适当的凸轮轮廓,便可使从动件得到任意的预期运动,而且结构简单、紧凑、设计方便;缺点:凸轮轮廓加工比较困难。
曲柄连杆:优点:运动副单位面积所受压力较小,且面接触便于润滑,故磨损减小;两构件之间的接触是靠本身的几何封闭来保持接触。
缺点:一般情况下只能近似实现给定的运动规律或运动轨迹,且设计较为复杂;当给定的运动要求较多或较复杂时,需要的构件数和运动副数往往比较多,这样就使机构结构复杂,工作效率降低,发生自锁的可能性增加。
综合上面分析我们选择凸轮摇杆作为小车转向机构的方案。
行走机构行走机构即为三个轮子,轮子又厚薄之分,大小之别,材料之不同需要综合考虑。
由摩擦理论知道摩擦力矩与正压力的关系为: δ⋅=N M对于相同的材料δ为一定值。
而滚动摩擦阻力 :RN RM f δ⋅==所以轮子越大小车受到的阻力越小,因此能够走的更远。
由于小车是沿着曲线前进的,后轮必定会产生差速。
对于后轮可以采用双轮同步驱动,双轮差速驱动。
双轮同步驱动必定有轮子会与地面打滑,使小车运动产生偏差,但由于小车速度较小时,可以大大减小差速带来的影响。
双轮差速驱动可以避免双轮同步驱动出现的问题,可以通过差速器或单向轴承来实现差速。
但差速器的构造较为复杂,且由于单向轴承存在侧隙,在主动轮从动轮切换过程中出现误差导致运动不准确。
综上所述行走机构的轮子应有恰当可调的尺寸,经过加工和成本的综合考虑我们选用双轮同步驱动。
三 技术设计技术设计阶段的目标是完成详细设计确定个零部件的的尺寸。
设计的同时综合考虑材料加工成本等各因素。
建立数学模型通过对小车建立数学模型,可以实现小车的参数化设计和优化设计,提高设计的效率和得到较优的设计方案,充分发挥计算机在辅助设计中的作用。
因此,我们采用了Matlab软件辅助设计。
小车后轮直径计算:function [D2] =fD2(LC,n)%D2 小车后轮直径%LC 小车行驶一个周期的路程%n 小车行驶一个周期,后轮转的圈数.%(确定n之后,也就确定了后轮轴与凸轮轴的转速比为n:1)D2=LC/pi/n;End推杆伸长量计算:function [Delta] = fDelta(theta,yT)%yT 导向杆长%Delta 凸轮的推杆伸长量(假定伸长为正,缩短为负)%theta 小车前轮转角(假定左转为正)Delta=yT*sin(theta);end小车路径上某点的曲率半径计算:function [r] = fr(x0,r0,l)%fr 求小车路径上某点的曲率半径%r0 零点处曲线的纵坐标,r0-y/2>10,y为两后轮间距%l 两个障碍物间距,700~1300% fx01,fx02 分别为fx0的一阶导,二阶导fx01=r0*pi*sin(pi*x0/l)/l;fx02=r0*(pi^2)*cos(pi*x0/l)/(l^2);r=(1+(fx01^2))^(3/2)/fx02;end小车前轮转角计算:function [theta] = ftheta(r,x )%theta 小车前轮转角(假定左转为正)%r 小车路径上某点的曲率半径%x 前轮轴与后轮轴间距theta=atan(x/r);end小车行驶一个周期的路程计算:function [ LC ] = fLC(r0,l)%运用第一类曲线积分,当被积函数为1时,即求曲线长度%r0 零点处曲线的纵坐标,r0-y/2>10,y为两后轮间距%l 两个障碍物间距,700~1300%LC小车行驶一个周期的路程x0=sym('x0');%r0=sym('r0'); l=sym('l'); %使结果带有r0和l这两符号f=sqrt(1+r0^2*pi^2*(sin(pi/l*x0))^2/(l^2));LC=int(f,0,2*l);LC=double(LC); %将结果转化为数值。
结果带有符号时不能使用end凸轮轮廓曲线绘图:l=800; %两个障碍物间距,700~1300r0=150; %零点处曲线的纵坐标,r0-y/2>10,y为两后轮间距x=200; %前轮轴与后轮轴间距yT=30; %yT 导向杆长rj=10; %凸轮基圆半径x1=72; %凸轮轴(轴1)与前轮轴水平间距x2=72; %轴1与轴2间距x3=48; %轴2与轴3间距x0=0;r=fr(x0,r0,l);theta=ftheta(r,x);maxDelta=fDelta(theta,yT); %maxDelta 推杆最大伸长(或缩短)的量maxDeltaxT=x1-rj-maxDelta; %xT凸轮的推杆长度xT i=1;for alpha=0::2*pix0=alpha*l/pi;r=fr(x0,r0,l);theta=ftheta(r,x);Delta=fDelta(theta,yT);TL=rj+maxDelta+Delta;n(i)=alpha;m(i)=TL;i=i+1;%hold on;%polar(alpha,TL); %描点法画出凸轮轮廓%plot(x0,Delta); %查看Delta(推杆伸长缩短量)随x0变化而变化的情况%plot(x0,theta); %查看theta(前轮转角)随x0变化而变化的情况%hold off;endpolar(n,m);%axis equal; %描点时,使横纵坐标单位间距相等参数确定单位:mm 前轮轴与后轮轴间距x=200导向杆长x=30凸轮基圆半径R=10凸轮轴(轴1)与前轮轴水平间距x=80轴1与轴2间距x=72轴2与轴3间距x=48零部件设计1.需加工的零件:a.驱动轴、传动轴b.车轮c.轴承座d.底板e.凸轮2.可购买的标准件:内圈Φ10的深沟球轴承、7个不同弹性模量弹簧、M8方形内六角螺栓3.部分加工零件二维图小车运动仿真分析为了进一步分析本方案的可行性,我们利用了Solidworks进行了动态仿真。