案例26PDCA循环在产品质量提高中的应用案例分析报告
产品质量提升的PDCA案例
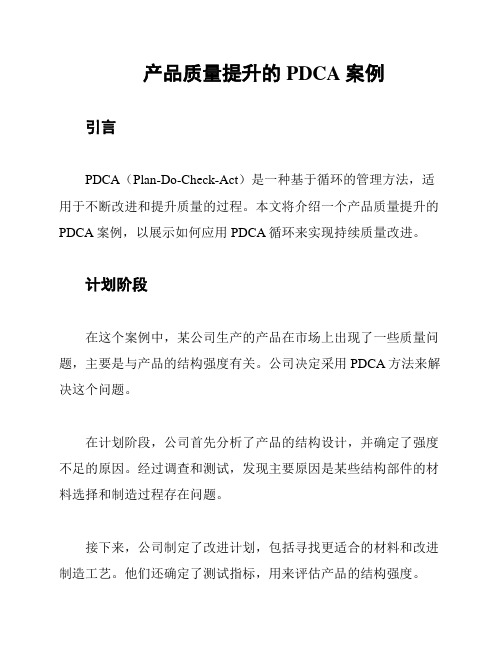
产品质量提升的PDCA案例引言PDCA(Plan-Do-Check-Act)是一种基于循环的管理方法,适用于不断改进和提升质量的过程。
本文将介绍一个产品质量提升的PDCA案例,以展示如何应用PDCA循环来实现持续质量改进。
计划阶段在这个案例中,某公司生产的产品在市场上出现了一些质量问题,主要是与产品的结构强度有关。
公司决定采用PDCA方法来解决这个问题。
在计划阶段,公司首先分析了产品的结构设计,并确定了强度不足的原因。
经过调查和测试,发现主要原因是某些结构部件的材料选择和制造过程存在问题。
接下来,公司制定了改进计划,包括寻找更适合的材料和改进制造工艺。
他们还确定了测试指标,用来评估产品的结构强度。
执行阶段在执行阶段,公司采取了一系列措施来实施改进计划。
他们与供应商合作,寻找更优质的材料,并对制造工艺进行优化。
同时,他们进行了一系列的试验和测试,以确保产品的结构强度满足要求。
这个阶段的关键是及时跟进和协调各个环节的工作。
公司设立了项目组,负责协调制造、采购和测试等方面的工作。
大家共同努力,确保改进措施的顺利实施。
检查阶段在检查阶段,公司对已改进产品进行了全面的检测和评估。
他们使用了事先确定的测试指标,对产品的结构强度进行了验证。
结果显示,改进后的产品结构强度得到了显著提升,满足了原先设定的要求。
这表明改进计划取得了一定的成果。
行动阶段在行动阶段,公司对改进计划进行总结和评估。
他们回顾了整个PDCA过程,并对百盈来取得实际的成果进行了总结。
基于这次改进的成功经验,公司决定继续应用PDCA方法来提升产品的质量。
他们将不断改进和完善PDCA过程,以实现持续的质量改进。
结论通过这个PDCA案例,我们可以看到应用PDCA循环方法可以有效提升产品质量。
在计划阶段,公司通过分析和制定改进计划,找出了问题的根源。
在执行阶段,他们采取了措施来实施改进计划。
在检查阶段,他们对产品进行了评估和验证。
最后,在行动阶段,公司将经验总结并持续改进。
案例26pdca循环在产品质量提高中的应用案例分析
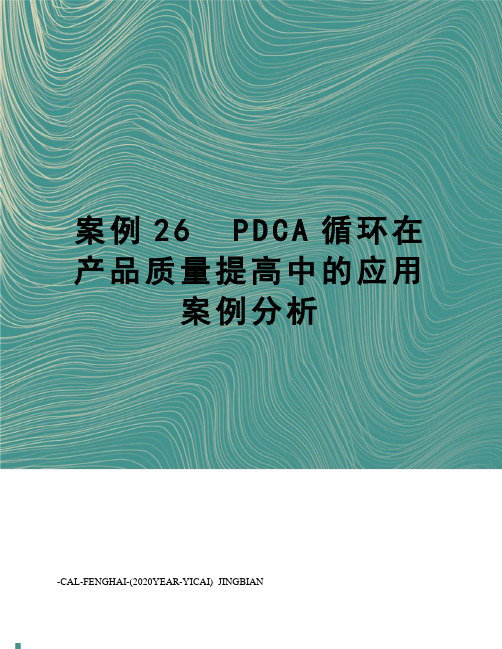
案例26P D C A循环在产品质量提高中的应用案例分析-CAL-FENGHAI-(2020YEAR-YICAI)_JINGBIAN案例26 PDCA循环在产品质量提高中的应用案例分析摘要:PDCA循环是提升产品质量的一种科学方法。
在工艺改进中按照P、D、C、A四个环节来展开并运用相关管理技术是取得实效的好模式。
工件的定位不允许过定位,采用球面支承解决过定位现象是常见的一种有效方式。
关键词: PDCA 产品质量夹具设计球面支承一、PDCA循环的概念PDCA循环由美国质量管理专家戴明(Edwards Deming)博士在1950年挖掘出来,并加以广泛宣传和运用于持续改善产品质量的过程中。
它是全面质量管理应遵循的科学程序。
全面质量管理活动的全部过程,就是质量计划的制订和组织实现的过程,这个过程就是按照PDCA循环,不停顿地周而复始地运转的。
PDCA循环是能使任何一项活动有效地进行一种合乎逻辑的工作程序,特别是在质量管理中得到了广泛的应用。
P、D、C、A四个英文字母所代表的意义如下:① P(Plan)——计划。
包括方针和目标的确定以及活动计划的制定;② D(DO)——执行。
执行就是具体运作,实现计划中的内容;③ C(Check)——检查。
就是要总结执行计划的结果,分清哪些对了,哪些错了,明确效果,找出问题;④A(Act)——行动(或处理)。
对总结检查的结果进行处理,成功的经验加以肯定,并予以标准化,或制定作业指导书,便于以后工作时遵循;对于失败的教训也要总结,以免重现。
对于没有解决的问题,应提给下一个PDCA 循环中去解决。
全面质量管理活动的运转,离不开管理循环的转动,这就是说,改进与解决质量问题,赶超先进水平的各项工作,都要运用PDCA循环的科学程序。
不论提高产品质量,还是减少不合格品率,都要先提出目标,即质量提高到什么程度,不合格品率降低多少就要有个计划;这个计划不仅包括目标,而且也包括实现这个目标需要采取的措施;计划制定之后,就要按照计划进行检查,看是否实现了预期效果,有没有达到预期的目标;通过检查找出问题和原因;最后就要进行处理,将经验和教训制订成标准、形成制度。
pdca的应用及案例分享

pdca的应用及案例分享PDCA是一种持续改进的管理方法,它由四个阶段组成:计划(Plan),执行(Do),检查(Check)和行动(Action)。
下面是PDCA的一些应用和案例分享:1. 应用在生产流程改进:在一个制造公司中,生产流程的效率低下成为一个问题。
经过分析,公司决定使用PDCA方法进行改进。
首先,他们制定了改进计划,确定了目标和具体的改进措施。
然后,他们执行了计划,进行了一段时间的生产测试。
在检查阶段,他们收集了生产数据并进行了分析。
他们发现某些环节的效果不理想,并根据分析结果制定了相应的行动计划。
最后,他们对生产流程进行了改进,并通过持续的监控和调整来确保改进效果的持续。
2. 应用在质量管理:一家电子产品制造公司发现产品的不良率较高,影响了客户满意度和公司声誉。
为了解决这个问题,他们采用了PDCA方法。
首先,他们制定了质量改进计划,包括加强员工培训和提高产品质量控制的措施。
然后,他们在生产过程中执行了这些计划,并对产品进行了检查。
在检查阶段,他们发现产品的质量有所提高,但仍存在一些问题,并制定了相应的行动计划来解决这些问题。
通过持续的PDCA循环,公司逐渐提高了产品的质量,不良率明显降低。
3. 应用在项目管理:一个项目经理发现项目进展缓慢,无法按计划完成。
他决定采用PDCA 方法进行改进。
项目经理首先分析了项目的问题,确定了导致延误的原因,并制定了改进计划。
然后,他执行了计划,并进行了项目的检查。
在检查阶段,他发现项目进展有所改善,但还需要进一步的调整。
他根据检查结果制定了行动计划,并对项目进行了相应的调整。
通过持续的PDCA循环,项目最终按计划完成,并获得了良好的评价。
总的来说,PDCA方法可以应用于各个领域和管理方面,帮助组织不断改进和提升绩效。
无论是生产流程的改进、质量管理还是项目管理,PDCA方法都可以帮助组织识别问题、制定解决方案并持续改善。
PDCA的应用及案例分享

PDCA的应用及案例分享PDCA(Plan-Do-Check-Act)是一种管理方法和问题解决工具,广泛应用于各种组织和行业中。
它强调通过循环的方式不断改进,并在每个阶段进行反思和调整。
以下是PDCA在实际中的应用及案例分享。
首先,PDCA可以应用于质量管理。
举一个汽车制造公司的例子,该公司在每一轮生产过程中都会进行质量管理。
首先,他们进行了计划阶段,确定了每一道工序的质量标准和要求。
然后,在执行阶段(Do),工人按照标准进行生产,并在每个环节仔细检查产品的质量。
接下来,在检查阶段(Check),质检人员对产品进行抽样检验,并记录下任何质量问题。
最后,在行动阶段(Act),公司对质量问题进行分析,并采取相应的纠正措施,以确保问题不会再次发生。
通过PDCA循环,这家汽车制造公司能够不断改进产品的质量,提高客户满意度。
其次,PDCA也可以应用于流程改进。
假设一个银行机构想要提高客户服务的效率。
在计划阶段,他们可能通过流程分析和员工反馈来识别出存在的问题,例如多个审批环节导致的拖延,或是工作流程不明确。
然后,在执行阶段,他们会试验改进的流程,并记录下所取得的效果。
接下来,在检查阶段,他们会评估新流程是否达到了更高的效率,并收集员工和客户的反馈。
最后,在行动阶段,他们可以根据反馈和评估结果来继续优化流程,确保每一轮循环都取得进步。
通过PDCA循环,银行机构能够不断提高客户服务的质量和效率。
再次,PDCA还可以应用于问题的解决。
假设一个制造公司的生产线出现了频繁的故障。
在计划阶段,他们可能会对故障进行分析,并制定修复计划。
然后,在执行阶段,工人根据计划进行维修工作,并监控故障的修复。
接下来,在检查阶段,他们会确认修复是否有效,并记录下故障的详细信息。
最后,在行动阶段,他们可以对故障进行深入分析,并采取预防措施,以避免类似的问题再次发生。
通过PDCA循环,制造公司能够不断改进故障处理的流程,减少生产线的停机时间,提高生产效率。
浅谈pdca在提高产品质量中的应用实例分析课件
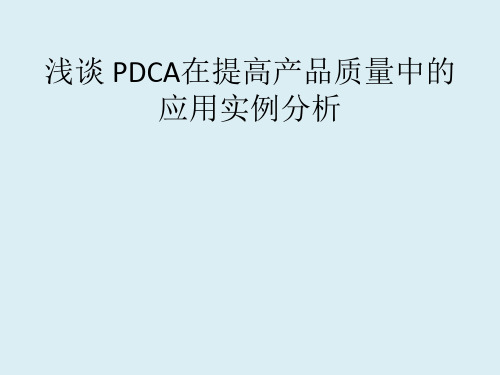
PDCA循环的Βιβλιοθήκη 本原理• PDCA循环把质量管理 的思想方法和工作程 序系统化、科学化、 具体化和全面化,依次 为基础,来展开具体的 质量研究改进工作。
PDCA循环的基本原理
PDCA循环的步骤
• 计划阶段(P阶段)
• 实施阶段(D阶段) • 检查阶段(C阶段) • 处理阶段(A阶段)
计划阶段(P阶段)
处理阶段(A阶段)步骤
• 处理阶段的定义:行动改进阶段,对检查的 结果进行相应的处理,成功的经验得以标准 化、制度化加以巩固;失败的教训加以经验 总结,避免重蹈覆辙;未解决的问题放入下一 轮PDCA循环。 • 在这一阶段,对C阶段的结果对照,采取以下 相应的处理措施:
处理阶段(A阶段)的措施
• 第一,标准化、制度化地巩固既有成果:如果 计划方案执行达到预期的效果,则进一步巩 固并持续提高,总结经验教训,对各生产过程 工艺书面化、规范化、标准化;完善、细化 标准化作业指导书,并规定定期内部审核制 度,以此巩固质量研究改进的成果,使之得到 稳定持续。
PDCA循环的特点
PDCA循环的基本原理
• PDCA循环的定义是在质量管理中,严格按照 计划、实施、控制及行动四个阶段依次进 行的管理工作循环,使质量管理活动周而复 始的运转,使各项具体业务工作始终处于一 种受控制的状态,以保证和推动质量水平周 而复始地不断进步、上升到一个新的起点。 PDCA循环把质量管理的思想方法和工作程 序系统化、科学化、具体化和全面化,依次 为基础,来展开具体的质量研究改进工作。
• 计划阶段定义:计划和目标阶段,确定方针 和目标,确定活动实施计划。 • 这是PDCA循环的第一个阶段,用来确定质量 改进研究项目的方针和目标、计划及方法 措施等。这一阶段要通过以下四个步骤实 现:
供应室PDCA策略提升腔镜器械包装质量的案例分析
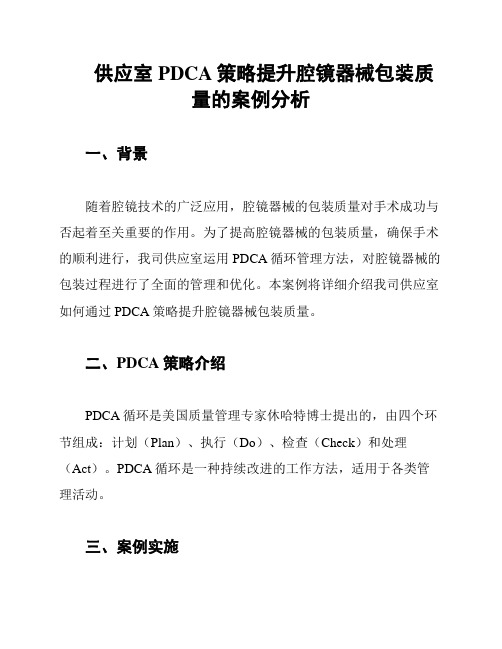
供应室PDCA策略提升腔镜器械包装质量的案例分析一、背景随着腔镜技术的广泛应用,腔镜器械的包装质量对手术成功与否起着至关重要的作用。
为了提高腔镜器械的包装质量,确保手术的顺利进行,我司供应室运用PDCA循环管理方法,对腔镜器械的包装过程进行了全面的管理和优化。
本案例将详细介绍我司供应室如何通过PDCA策略提升腔镜器械包装质量。
二、PDCA策略介绍PDCA循环是美国质量管理专家休哈特博士提出的,由四个环节组成:计划(Plan)、执行(Do)、检查(Check)和处理(Act)。
PDCA循环是一种持续改进的工作方法,适用于各类管理活动。
三、案例实施计划(Plan)1. 收集数据:收集过去一段时间内腔镜器械包装过程中出现的问题,如破损、遗漏、装配错误等,并对问题进行归类分析。
2. 设定目标:根据数据分析结果,设定提高腔镜器械包装质量的目标,如降低器械破损率、减少装配错误等。
3. 制定措施:针对存在的问题,制定相应的改进措施,如加强员工培训、优化包装流程等。
4. 制定计划:将改进措施细化为具体的执行计划,明确责任人和执行时间。
执行(Do)1. 落实措施:根据计划,对腔镜器械包装过程进行改进,如开展员工培训、优化包装流程等。
2. 跟踪执行情况:对改进措施的执行情况进行跟踪,确保各项措施得到有效落实。
检查(Check)1. 收集数据:在改进措施实施一段时间后,收集腔镜器械包装过程中的相关数据,如器械破损率、装配错误率等。
2. 分析数据:对比改进前后的数据,分析改进措施的效果。
3. 评估结果:根据数据分析结果,评估改进措施的实际效果,发现问题是否存在反弹现象。
处理(Act)1. 总结经验:对改进措施的效果进行总结,提取可供借鉴的经验。
2. 处理问题:针对评估结果,对存在的问题进行处理,如调整改进措施、加强监管等。
3. 制定下一轮计划:根据总结的经验和处理结果,制定下一轮的改进计划。
四、案例成果通过实施PDCA策略,我司供应室在腔镜器械包装质量方面取得了显著的成果:1. 器械破损率降低至3%以下,远低于行业平均水平。
浅谈 PDCA在提高产品质量中的应用实例分析

计划阶段(P阶段)的步骤
• (3)在各种原因中,进一步搜寻出主要原因,掌 握主要原因及其主要分支。 • (4)针对主要原因及其主要分支制订优先解 决方案,即行动实施计划,预期效果目标及时 间进度限制。
PDCA循环在乳品生产过程中应用
• PDCA 循环在奶粉加工中的具体应用举例 • 制定措施: • (2) 在添加白砂糖等配料时需要擦拭其包 装外袋,以免带入更多微生物及杂质。 • (3) 浓缩杀菌过滤严格按照规定进行,并 有人监督,以确保杀菌的效果。 • (4) 严格按照 PPCH 的标准进行喷雾、干 燥、过滤,定期清洗过滤棉。
PDCA循环在乳品生产过程中应用
• 我国乳品加工业存在的问题: • 奶粉营养丰富,冲调容易,使用方便% 奶粉按其组成和功能可分为全脂奶粉、脱 脂奶粉、速溶奶粉、加糖奶粉、婴幼儿奶 粉和特殊配制奶粉几大类。
PDCA循环在乳品生产过程中应用
• PDCA循环在奶粉加工中的具体应用举例
• 日本著名质量管理专家池泽辰夫主张灵 活运用PDCA 方法,可先从CA入手,然后再 进入 PDCA 循环,即先检查、改进前一循环 的实施效果后,再进入策划阶段.
处理阶段(A阶段)步骤
• 处理阶段的定义:行动改进阶段,对检查的 结果进行相应的处理,成功的经验得以标准 化、制度化加以巩固;失败的教训加以经验 总结,避免重蹈覆辙;未解决的问题放入下一 轮PDCA循环。 • 在这一阶段,对C阶段的结果对照,采取以下 相应的处理措施:
处理阶段(A阶段)的措施
• 第一,标准化、制度化地巩固既有成果:如果 计划方案执行达到预期的效果,则进一步巩 固并持续提高,总结经验教训,对各生产过程 工艺书面化、规范化、标准化;完善、细化 标准化作业指导书,并规定定期内部审核制 度,以此巩固质量研究改进的成果,使之得到 稳定持续。
PDCA循环在提高产品质量中的应用实例分析

( 西旅 游 商 贸职 业 学 院 ) 江
[ 要 ] DCA循 环是 提 升产 品质 量 的一 种科 学方 法。在 工 艺 改进 中按 照 P D、 A 四个 环 节 摘 P 、 C、 来展 开并运 用 相 关管理 技 术是 取得 实效 的好 模 式 。 工件 的 定位 不 允许 过 定位 , 用球 面 支承 解 决 采 过 定位 现 象是 常见 的一 种有 效 方式 。
方法 , 实 施 需要 搜 集 大 量 数 据 资 料 , 综 合 运用 其 并
各种 管理 技术 和方 法 。
了广 泛 的应用 。 、 C、 四个 英文 字 母所 代 表 的意 P D、 A
义如 下 :
① P Pa ) — 计划 。包 括 方针 和 目标 的确定 ( ln —
以及 活动 计划 的制定 :
和方法 。
图 2
数 据表 一
l 课题立 项 、 根 据 现场 存 在 的薄弱 环 节所 暴 露 的 问题 , 们 我
余 建 青 :D A 循 环 在 提 高 产 品 质 量 中 的应 用 实 例 分 析 PC
g 管理 创新
也 , — — — —、 气
P C D A循 环 在 提 高产 品质 量 中的应 用 实例 分 析
Ap l aino DCA i mp o igP o u tQu l y pi t fP c o nI r vn r d c ai t
2所 示 。
巽袅
误 差 特 征 : 过 现 场对 加 工 产 品 观察 , 现进 经 发 刀 口、 出刀 口处壁 厚厚度 相差
O0 m . m。这说 明工件 径 向受力 不均 匀 , 削过 程 中 6 拉
发 生 径 向偏 移 。
- 1、下载文档前请自行甄别文档内容的完整性,平台不提供额外的编辑、内容补充、找答案等附加服务。
- 2、"仅部分预览"的文档,不可在线预览部分如存在完整性等问题,可反馈申请退款(可完整预览的文档不适用该条件!)。
- 3、如文档侵犯您的权益,请联系客服反馈,我们会尽快为您处理(人工客服工作时间:9:00-18:30)。
案例26 PDCA循环在产品质量提高中的应用案例分析摘要:PDCA循环是提升产品质量的一种科学方法。
在工艺改进中按照P、D、C、A四个环节来展开并运用相关管理技术是取得实效的好模式。
工件的定位不允许过定位,采用球面支承解决过定位现象是常见的一种有效方式。
关键词: PDCA 产品质量夹具设计球面支承一、PDCA循环的概念PDCA循环由美国质量管理专家戴明(Edwards Deming)博士在1950年挖掘出来,并加以广泛宣传和运用于持续改善产品质量的过程中。
它是全面质量管理应遵循的科学程序。
全面质量管理活动的全部过程,就是质量计划的制订和组织实现的过程,这个过程就是按照PDCA循环,不停顿地周而复始地运转的。
PDCA循环是能使任何一项活动有效地进行一种合乎逻辑的工作程序,特别是在质量管理中得到了广泛的应用。
P、D、C、A四个英文字母所代表的意义如下:① P(Plan)——计划。
包括方针和目标的确定以及活动计划的制定;② D(DO)——执行。
执行就是具体运作,实现计划中的容;③ C(Check)——检查。
就是要总结执行计划的结果,分清哪些对了,哪些错了,明确效果,找出问题;④A(Act)——行动(或处理)。
对总结检查的结果进行处理,成功的经验加以肯定,并予以标准化,或制定作业指导书,便于以后工作时遵循;对于失败的教训也要总结,以免重现。
对于没有解决的问题,应提给下一个PDCA循环中去解决。
全面质量管理活动的运转,离不开管理循环的转动,这就是说,改进与解决质量问题,赶超先进水平的各项工作,都要运用PDCA循环的科学程序。
不论提高产品质量,还是减少不合格品率,都要先提出目标,即质量提高到什么程度,不合格品率降低多少?就要有个计划;这个计划不仅包括目标,而且也包括实现这个目标需要采取的措施;计划制定之后,就要按照计划进行检查,看是否实现了预期效果,有没有达到预期的目标;通过检查找出问题和原因;最后就要进行处理,将经验和教训制订成标准、形成制度。
PDCA循环作为全面质量管理体系运转的基本方法,其实施需要搜集大量数据资料,并综合运用各种管理技术和方法。
二、应用背景发动机是农机中的核心部件之一,其中滑动轴承承载能力对发动机的性能有着重要的作用。
笔者曾作为工艺工程师加工4E135系列衬套。
衬套产品示意图如图1所示。
该衬套孔中均布着24头螺旋油槽,因其为小批生产,选用了成型拉刀在通用油压机上进行加工。
其拉削成型模具结构如图2所示。
图1该产品的主要工艺流程如下:切基准下料扩孔粗车外圆平两端面半精车孔拉油槽切断端面倒角精车外圆磨外圆精镗孔。
生产加工过程中出现异常,加工油槽工序产生深度尺寸偏差较大,已经超出产品的技术要求。
合格率仅为12%,工序能力不足,直方图见图3。
三、应用过程(一)P阶段—计划阶段这个阶段的工作主要是找出存在的问题,通过分析,制定改进的目标,确定达到这些目标的措施和方法。
1.课题立项根据现场存在的薄弱环节所暴露的问题,我们成立了一个QC小组,将油槽深度尺寸超差的的问题作为一个课题。
小组成员包括包括工程师、技术员、操作者、检验员、技师,生产管理员。
2.确定目标值依照产品的要求,将油槽深度尺寸公差目标值定为0.2,使小组成员有一个明确的努力方向。
3.调查现状由产品图可知,油槽深度尺寸为0.5±0.1,测量时以外圆为基准。
为方便起见,加工时在基本尺寸确定后仅测量油槽处壁厚差,其壁厚公差值δ=0.2mm。
在加工过程中随机抽样50件,测量如数据表一所示,按照直方图的作法作出直方图图3。
图3表明工序能力明显不足,大部分的样点分布超出了产品的要求之外,由直方图可以看出分布中心偏向一侧,属于异常状态。
4.分析原因依照调查后掌握到的现状,发动全体组员动脑筋,想办法,依靠掌握的数据,通过开“诸亮”会,集思广益,选用适当的QC工具因果图进行分析,找出问题的诸多原因。
因果图见图4。
误差特征:经过现场对加工产品观察,发现进刀口、出刀口处壁厚厚度相差0.06mm。
这说明工件径向受力不均匀,拉削过程中发生径向偏移。
图2数据表一测量值(单位μm)27 15 17 24 21 31 29 23 25 2722 23 26 29 27 30 31 21 27 2524 26 28 30 31 26 27 23 25 2826 28 29 23 25 28 30 21 24 2528 18 20 27 20 22 19 21 24 27(检)等。
虽说影响质量问题的原因可能多种多样,但必须要抓住主要的。
要是“眉毛胡子一把抓”,结果找不出主要要素而导致质量改进的失败。
根据关键要素少数和次要要素多数的原理,进行排列,从中找出主要原因。
以便从主要原因入手解决存在的问题。
因果图 图4为了寻找主要原因,我们进行了相关试验如下: ① 选用适用的刀具在加工过程中发现,不同的刀具(外协件)对油槽的同轴度有一定影响,好的刀具可减少0.04mm 的同轴度误差。
② 工装的调试▲ 上下模具的对中:因上下模具没有导向机构,加工前的相互位置调试也很重要。
当上下模具中心不对中时,会增加刀杆的偏摆,加大油槽的误差。
但是,在调整好的模具位置状态下,测量的同轴度数据同数据表一。
▲ 衬套的定位套孔尺寸:衬套以外圆在定位套孔中进行预定位,其配合有1mm 的间隙。
当刀杆进入衬套孔时,是以孔加工表面自为基准,然后再进行油槽切削加工。
改变定位套孔尺寸对加工没有明显影响。
▲ 刀杆组合体的结构:考虑到刀杆组合体的上平面受上模体的作用力会引起刀杆组合体的偏摆,为消除 这个影响,在刀杆组合体的上平面与上模体之间加一钢球。
试验测量数据结果同数据表一。
③ 提高半成品的位置精度 ▲衬套孔直径:按照机械设计原理,自为基准的导向部分配合有相应的要求。
对半精加工孔尺寸进行了分组,以得到最佳配合。
试验测量数据结果同数据表一。
▲ 衬套孔与轴线的位置精度:考虑到衬套孔与孔轴心线不垂直,会增加加工误差,在半成品加工孔时将一端端面车一刀,并以此端面作为主要定位面放在定位套。
测量结果同数据表一。
④ 模具结构分析——过定位现象根据衬套两端油槽进刀口、出刀口处有明显的壁厚厚度偏差现象分析,认为刀杆组合体前端的导向部分虽然以衬套孔自为基准,但衬套径向受力还是不对称,加工过程中刀杆组合体与衬套之间仍有径向位移,造成油槽加工尺寸误差。
工件的定位分析:定位元件 限制的自由度相当定位支承点数 定位套 z 、x 、y3(平面定位) 刀杆组合体x 、y 、x 、 y4(孔定位)由定位分析可知,原工装重复限制了两个自由度x 、y ,产生了过定位现象,属于关键要素,是主要原因。
6.制定措施主要原因确定后,制定相应的措施计划。
解决过定位现象的措施——采用球面支承。
夹具改进结构如图4所示。
定位分析:定位元件 限制的自由度相当定位支承点数球面支承 z1 刀杆组合体x 、 y 、 x 、 y4夹具改良结构 图4频数分布表系列号组距 中心值 频数 xfx fx 2 4 6.5~8.5 a=13.5 1 -3 -3 9 5 8.5~10.54 -2 -8 16 6 10.5~12.5 7 -1 -7 7 7 12.5~14.5 16 0 0 0 814.5~16.51211212数据表二 测量值(单位 μm)157911 15 16 17 19 13 1413 14 10 12 14 15 20 17 18 14 16 13 15912 14 15 18 14 1514 16 10 19 20 12 13 16 17 13 16 13 15 12 11 14 16 18 11 14(二)D阶段—实施阶段针对过定位现象的原因,由工程师采用球面支承结构的方案来改良夹具。
对新夹具进行试生产。
(三)C阶段—检查阶段措施实施后,应进行效果检查。
效果检查是把措施实施前后的情况进行对比,看其实施后的效果,是否达到了预定的目标。
如果达到了预定的目标,小组就可以进入下一步工作;如果没有达到预定目标,就应对计划的执行情况及其可行性进行分析,分布表中所示,直方图如图5。
由图5可以看出,C p=T/6s =1.19,工序能力尚可,已经达到了预定的目标。
(四)A阶段—处理阶段1.分析遗留问题小组通过活动取得了一定的成果,其工序能力Cp值已经达到1.19尚可能力;但还不充分,还要用其它方法(如控制图)对生产过程进行监控,以便及时发现异常波动。
2.总结成果资料小组将活动的成果进行总结,是自我提高的重要环节。
经过PDCA循环达到了预定的目标值,说明该课题已经完成。
将活动成果应用到生产过程中,工艺规程中的夹具已经作了相应更改,并制定了拉油槽工序的作业指导书。
四、结束语以上是QC小组活动的全过程,实践了一个完整的PDCA循环。
生产过程中存在的问题都可以是课题选择对象,要取得活动成果关键是要找出主要因素并有的放矢采取措施,专业知识、数据分析也是成功的因素之一。
在工作过程中深入地开展,推动PDCA 循环,是不断提升工作质量的法宝。