轴流泵后导叶设计的几何参数法
混流与轴流水轮机转轮流道几何参数
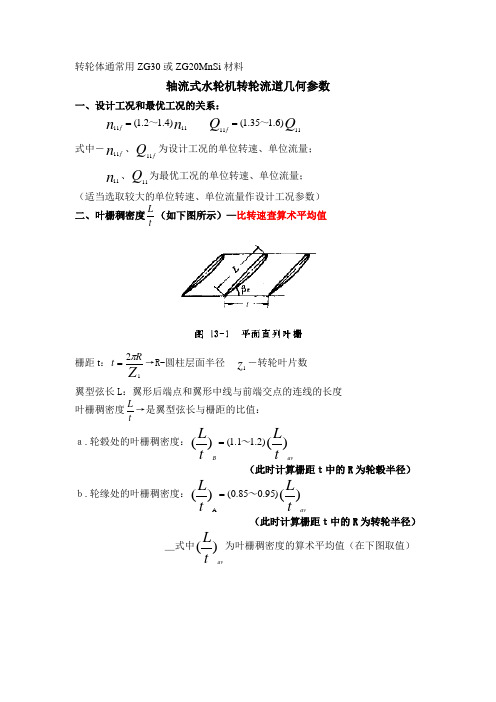
转轮体通常用ZG30或ZG20MnSi 材料轴流式水轮机转轮流道几何参数一、设计工况和最优工况的关系:n n f 1111)4.12.1(~=Q Q f 1111)6.135.1(~= 式中-n f 11、Qf 11为设计工况的单位转速、单位流量; n 11、Q 11为最优工况的单位转速、单位流量; (适当选取较大的单位转速、单位流量作设计工况参数) 二、叶栅稠密度tL (如下图所示)—比转速查算术平均值栅距t :Z Rt 12π=→R-圆柱层面半径 z 1-转轮叶片数翼型弦长L :翼形后端点和翼形中线与前端交点的连线的长度 叶栅稠密度tL →是翼型弦长与栅距的比值: a.轮毂处的叶栅稠密度:)()()2.11.1(t L tL av B ~= (此时计算栅距t中的R 为轮毂半径) b.轮缘处的叶栅稠密度:)()()95.085.0(A t L t L av~= (此时计算栅距t中的R 为转轮半径)_式中)(t L av为叶栅稠密度的算术平均值(在下图取值)三、转轮叶片数-算术平均值算叶片数确定Z 1的原则是:不使叶片太长,且平面包角θ不太于90°;所谓平面包角-指叶片位于水平位置时,叶片进出水边所对应的中心角当叶片栅稠密度确定后,Z 1按下式计算取整:)()(1360tL Z av θ= 当θ=70°~90°时,Z 1与)()(L av 关系见下表: 四、转轮体转轮体有环形与圆柱形两种外观形式:球形转轮体(用于ZZ 式水机)时:转轮叶片内表面与转轮体之间的间隙较小,不同转角时间隙可保持不变。
圆柱形转轮体时:一般按最大转角确定转轮叶片与转轮体之间的间隙附:相同直径下,采用球形转轮体的水机效率高于圆柱形转轮体水机五、泄水锥泄水锥长度系数指:转轮叶片转动轴线到泄水锥底部的高度。
其高度采用主:D L 1165.0=同时,采用高度为0.4D 1与0.6D 1泄水锥的大型高水头ZZ 水机其水机效率一样六、导叶相对高度-b 0、轮毂比-d h 及转轮叶片数Z 1与最大水头的关系 轮毂比计算式建议采用以下公式:-d h =-0.0005n s +0.75一+0.065 或,-d h =0.25+n S 64.94 式中-n s 为水轮机比转速(m ·hp )七、转轮室ZL 式水轮机转轮室有圆柱形、球形和半球形三种现多采用半球形转轮室:转轮叶片转动轴线以上采用圆柱形,在其以下采用球形ZL 水机宜采用喉部(指转轮室直径最小的部位)直径为(0.955~0.985)D 1的半球形转轮室较为适宜混流式水轮机转轮流道几何参数(40m ~450m 水头选混流式最为有利)一、 设计工况和最优工况的关系:120 m 水头段: n n f 1111)08.193.0(~= QQf 1111)91.069.0(~= 200m 水头段,有些转轮:n n f 111107.1=Q Q f 111104.1= 式中-n f 11、Qf 11为设计工况的单位转速、单位流量; n 11、Q 11为最优工况的单位转速、单位流量; 二、 导叶相对高度-b 0三、上冠上冠流线形状有直线形与曲线形两种;现多采用曲线形上冠,它可以增大单位流量与水力效率,但曲率不能太大-会加大出口附近上冠表面的局部所蚀四、下环下环形状有直线形与曲线形两种(a)为低比转速水轮机(H >230m)下环,一般为曲线形;最优直径比为76.06.012~D D =(b)为中高比转速水轮机(H <115m)下环,一般为直线形,用下环锥角α表示扩散程度,一般α<13°,(c)(115m <H<230m )范围的转轮,下环可做成圆锥形或圆柱形,0.112=D D ;但(115m <H<170m )推荐采用10.19.012~D D =五、叶片数Z 1与最大水头H m ax 、比转速n s 及叶片包角θ的关系六、叶片进出水边位置转轮轴面投影如图:1与3连线成进水边,2与4连线成出水边D 1为标称直径;D 113005.1或D D j =Dj 1的大小与叶片进水角β1和单位转速n '1有关;有β1>90°、β1=90°和β1<90°三种情况(如下图):一般按β1=90°计算: n D D g h j '60111πη=轮廓线绘制:叶片进水边-由1点向下引垂线,然后用弧线将垂线与3点相连 叶片出水边-参照相近比速的转轮确定(所有尺寸均为转轮直径的倍数)。
轴流泵的设计 本科生毕业设计
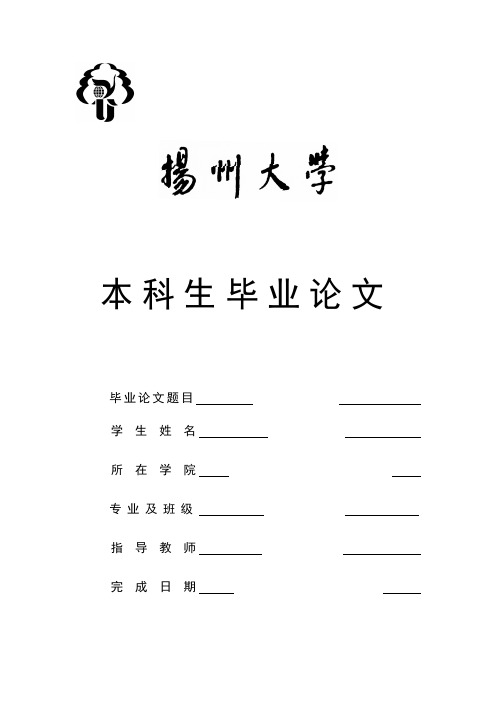
第二章
叶轮设计 ............................................................................................................................3 (一)叶轮设计流程 ........................................................................................................3 (二)叶轮基本参的选择数 ............................................................................................3 (三)流线法设计叶片 ....................................................................................................5 (四)选定截面及计算 ....................................................................................................7
I I
扬州大学本科生毕业论文
目
摘 目
录
要 ................................................................................................................................................ I 录 ..............................................................................................................................................III 概述 ....................................................................................................................................1 一、轴流泵的特点和工作原理 ................................................................................................1 二、我国轴流泵模型发展概况 ................................................................................................1 三、设计意思和目的 ................................................................................................................2
轴流泵叶轮水力模型设计参数
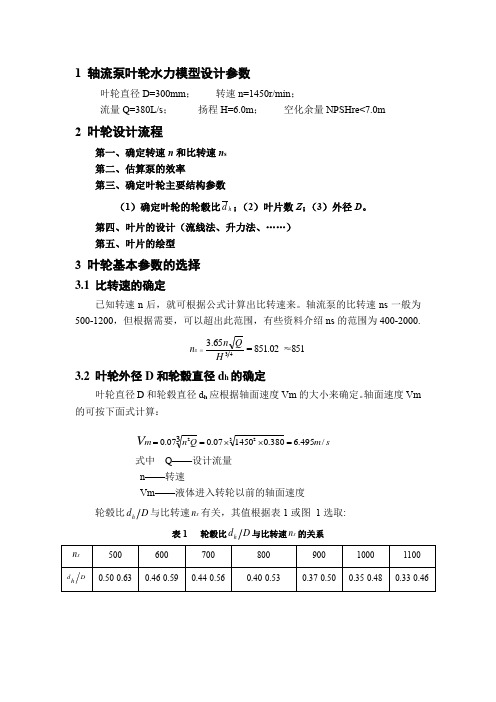
1 轴流泵叶轮水力模型设计参数叶轮直径D=300mm ; 转速n=1450r/min ;流量Q=380L/s ; 扬程H=6.0m ; 空化余量NPSHre<7.0m2 叶轮设计流程第一、确定转速n 和比转速n s 第二、估算泵的效率第三、确定叶轮主要结构参数(1)确定叶轮的轮毂比h d ;(2)叶片数Z ;(3)外径D 。
第四、叶片的设计(流线法、升力法、……) 第五、叶片的绘型3 叶轮基本参数的选择3.1 比转速的确定已知转速n 后,就可根据公式计算出比转速来。
轴流泵的比转速ns 一般为500-1200,但根据需要,可以超出此范围,有些资料介绍ns 的范围为400-2000.851≈851.02=65.343HQn n s =3.2 叶轮外径D 和轮毂直径d h 的确定叶轮直径D 和轮毂直径d h 应根据轴面速度Vm 的大小来确定。
轴面速度Vm 的可按下面式计算:式中 Q——设计流量n——转速Vm——液体进入转轮以前的轴面速度轮毂比D d h 与比转速s n 有关,其值根据表1或图 1选取:表1 轮毂比D d h 与比转速s n 的关系sm Q n m V /495.6380.0145007.0307.0322=⨯⨯==图 1 轮毂比D hd 与比转速sn 的关系曲线从图及表中可看出,轮毂比D d h 随比转速s n 的减小而增大,这是因为:为了减小叶片在液流中的迎面阻力,必须使叶片后面不产生漩涡层,必须要使每一计算截面上围绕翼型流动的速度环量Γ1相等。
所以根据以上叙述,选择轮毂比为3.3 叶片数Z 的选择轴流泵叶轮的叶片数Z 与比转速s n 有关,其统计数据列于表2表2 叶片数Z 与比转速s n 的关系根据上表选择叶片数Z=44 叶片各截面的叶栅计算(流线法)如果用半径为r 和(r+dr )的两个同心圆柱面去切割轴流泵的叶轮,则得到一个包括翼型在内的液体圆环,如图2所示,如将这个圆环剖开并展开于平面上,则得到一个无限直列叶栅,如图3所示。
轴流风机后导叶三维数值优化设计方法及其应用

轴流风机后导叶三维数值优化设计方法及其应用
本篇论文介绍了一种针对轴流风机后导叶的三维数值优化设计
方法,并探讨了该方法在实际应用中的效果。
首先,论文介绍了轴流风机后导叶的基本结构和工作原理,以及现有设计方法的局限性和不足之处。
接着,论文详细介绍了基于计算流体力学方法的三维数值优化设计方法的原理和流程,包括建立数值模型、确定优化目标和约束条件、选择优化算法等内容。
最后,论文通过实例分析和仿真验证,证明了该三维数值优化设计方法具有较高的设计效率和设计精度,能够有效优化轴流风机后导叶的性能表现,提高整机的效率和稳定性。
- 1 -。
第06章-轴流泵叶轮设计教材

c y mLcy1
升力法设计
三、升力法设计轴流泵叶轮的基本方程 叶轮所进行的能量传递是通过叶片 和液流的相互作用来实现的,为了满足 能量转换的条件,就必须使叶栅和翼型 的几何参数与液流运动参数之间有确定 的关系。这就是设计轴流泵叶轮的基本 方程。
升力法设计
tห้องสมุดไป่ตู้
l Px Pu βe λ α β∞ w∞ Py R β∞
轴流式叶轮
奇点分布法 是用一系列分布在翼型骨线上的 涡和源 (汇)来代替叶片,这些涡和源 (汇)对一平行水流的作用相当于转轮叶 片的作用,从而设计出叶片。奇点分 布法能有目的地控制翼型表面各点的 速度和压力分布,从而可能设计出空 化性能较好的转轮。它对实验资料的 依赖性也较少。
叶轮中的水流运动
一、圆柱层间无关性假设
Huazhong University of Science & Technology
轴流式叶轮的水力设计
轴流泵设计
public4course@ husthsj
轴流式叶轮
轴流式叶轮的设计方法
升力法 是利用单个翼型的空气动力特性, 并考虑到组成叶栅后翼型间的相互影 响来设计转轮叶片的方法。在积累了 丰富的实验数据的条件下,这种方法 能够方便而准确地设计出性能优秀的 转轮。
升力法设计
3.翼型的质量 合力与升力之间的夹角为λ,将1/tgλ 称之为翼型的质量。
c y1 1 = tgλ c x1
角度λ越小,则1/tgλ越大,质量越高。
升力法设计
4.哥廷根翼型 这种翼型因早年被哥廷根实验室实 验而得名,翼型的坐标数据均以翼型弦 长l的百分数给出。在设计时可根据需要 对翼型进行减薄或加厚。上述翼型的减 薄或加厚时所采用的相对厚度δ/l 或 ymax/l均不得超过20%。坐标改变后的 翼型特性可按以下公式计算:
轴流泵叶片三维画法

基于Solidworks轴流泵叶轮叶片的三维建模方法发表时间: 2011-10-10 作者: 何东林*石秀华*宋绍忠来源: 万方数据关键字: 轴流泵叶轮叶片曲面零件几何造型Solidworks三维建模轴流泵叶轮叶片是一种特殊的曲面零件,这种零件的几何造型是三维建模中的重点和难点。
基于Solidworks 的三维建模功能,研究了轴流泵叶轮叶片的三维建模方法,并以具体实例实现T轴流泵叶轮叶片的三维模型。
1 引言在叶轮机械的水力设计中,为了设计出性能优良的泵,目前的发展是采用正反问题相互迭代的方法,根据初步设计的泵,进行三维湍流计算,根据计算结果,修正某些几何边界,再进行流动计算,采用人机对话,反复迭代,会得到性能优良,即高效率,并满足空化条件及其它要求的泵。
近几年来,随着计算机计算能力和流体计算动力学的迅速发展,尤其是三维流动分析的使用,三维数值模拟应用越来越广。
这里基于Solidworks的三维建模功能,研究轴流泵叶轮叶片的三维建模方法。
2 基于Solidworks轴流泵叶轮叶片三维建模方法在轴流泵叶轮叶片的设计和加工中,叶片的表面是由翼型的型值点给定的。
用半径为:和r十dr的两个无限接近且与叶轮轴同轴的圆柱面截取一个微小圆柱层,取出并沿其母线切开展为平面,叶片被圆柱面截割,其截面在平面上展开就组成等距排列的一系列翼型,这一系列翼型称为平面直列叶栅。
在用平面直列叶栅理论设计轴流泵叶轮时,得到在平面上给定的型值点,如果把各型值点拟合的型值曲线直接作为半径r处的截面轮廓曲线,由此得到的叶轮叶片三维模型误差较大。
因此为了得到比较理想的三维模型,必须寻找一种好的方法。
经分析可知,如果能得到半径r处的截面,问题就解决了。
如何由翼型型值点得到半径r处的截面呢尸根据Solidworks的建模功能,研究了如下的方法:先由翼型型值点找到对应的截面在翼型展开面上的投影点,把各投影点拟合为投影曲线,然后通过一些命令就可得到轴流泵叶轮叶片的截面。
轴流泵设计说明书

JIANGSU UNIVERSITY本 科 课 程 设 计设计说明书题目: 立式轴流泵学院名称: 能源与动力工程学院专业班级: 流体机械及其自动控制卓越学生姓名: ***学 号: **********设计导师: 高波2013 年11月目录第一部分内容摘要————————————————3 第二部分概述—————————————————4 第三部分设计方案及原理说明———————————7 第四部分水力设计————————————————8 第五部分结构设计————————————————15 第六部分重要部件的校核—————————————20 第七部分参考文献————————————————25 第八部分课程设计小结——————————————26第一部分内容摘要轴流泵流量大,扬程低,比转速高,轴流泵的液流沿轴方向流动,其设计的基本原理与离心泵基本相同。
轴流泵大多是单级立式的,可以分为固定叶片式和可调叶片式两种。
本设计的题目是可调叶片式轴流泵——即叶片可调节倾斜角度。
其内容只有大致工况设定,没有具体工作环境说明的要求,大致要求材料要有一定的耐腐蚀性能。
此外,轴流泵广泛应用于多种场合。
泵既有离心式的,也有轴流式的,既有立式的,也有卧式的,既有单级的,也有多级的,应不同场合而定。
本毕业设计要求为设计立式轴流泵,这就决定了设计方向为:立式、单级、轴流。
泵主要由泵体、传动轴和传动装置等组成。
其传动装置是将原动机的动力传递给泵轴的中间装置。
泵设计最主要的是水力设计——叶片及导叶的水力设计。
叶片的水力设计采用两种方法:圆弧法和升力法。
经分析比较:采用圆弧法设计的轴面投影图叶片更为光滑,难度相对更高;采用升力法设计的轴面投影图,虽然比圆弧法设计的稍微差点,但是,由于当今国内的制造水平对于三维曲面的加工还相对落后,即使是好的设计也是难以加工出来的,对于空间曲面加工效果好的机床是五轴联动机床,国内包括在国内的外企,拥有五轴联动机床的公司屈指可数。
轴流泵设计步骤

轴流泵设计数据1、设计参数:流量 Q = 1000( m ³/h )扬程 H = 4.5 (m) 转速 n = 1450 ( r/min )效率 η≧85℅ 汽蚀比转速C≧1000 2、结构形式: 采用60°出水弯管 3、 底板至叶轮中心距离:1m轴流泵水力设计一、叶轮的水力设计 (一)结构参数的选择 1.确定轮毂比根据轮毂比与比转速的关系表,取45.0=d h2.叶轮直径D叶轮直径一般根据轴面速度来确定,为了得到最优的影片安放角,叶轮进口前的轴面速度,采用C.C.鲁德涅夫推荐公式来确定:0(0.06m v =-根据液流的连续性条件,不考虑排挤,则叶轮区域内的轴面速度为 2241m h Qv d D D π=⎛⎫-⎪⎝⎭取0m m v v =,则(4.0D =- 根据轮毂比45.0=Dd h及给定的参数,叶轮直径即可求出。
则 取 D=272mm即 mm d h 12227245.0=⨯=3.确定叶片数Z叶片数通常按s n 选取为了更易于调节动平衡,取Z=44.确定叶栅稠密度l tZ=4,叶轮外缘的叶栅稠密度推荐为,0.750.85l t =-,同时,适当减小外缘的l t ,增加轮毂侧的l t ,以减小内外侧翼型的长度差,均衡叶片出口的扬程。
所以,轮毂和轮缘之间各截面的lt按直线规律变化,其值为 ()()()1.3 1.4hl lt t =-取()73.00=l ,则()96.0=h t l4.确定叶片翼型的厚度:通常轮毂截面的相对厚度为 lδδ==(10~15)%轮缘截面的厚度按工艺条件确定,通常轮缘截面的相对厚度 lδδ==(2~5)%从轮毂到轮缘其厚度按直线规律变化。
(二) 选定截面及计算 1.确定计算截面通常选取五个彼此等距离的计算流面,由于本设计要求为为半调节式轴流料浆泵,考虑到叶片的调节,轮毂和轮缘需作成球面。
各计算流面的半径可按下式确定: 21hd r =D r =52513r r r +=2312rr r +=2534r r r += 截面D 取值:122,160,198,236,2722.确定轴面速度和速度环量(1)确定轴面速度 取99.0v =η 即028.6)(422=-=vh m d D QV ηπ(2)确定速度环量 036.22==ΓwgH Tk π 3.升力法设计计算选定截面 计算表格4.计算泵的汽蚀比转速C知道设计流量Q 和轴流泵的转速n ,根据GB/T 13006-91,查取临界汽蚀余量r NPSH ,计算泵的汽蚀比转速C :C =1000112062778.0145062.5m 64/3r >=⨯==C NPSH 所以符合设计要求。