高压液压缸受力变形研究
液压缸的常见故障及处理预防措施介绍

液压缸的常见故障及处理预防措施介绍液压缸的常见故障及处理预防措施介绍液压缸的常见故障及处理预防措施液压缸广泛应用于各种液压系统中,它将液体压力转换为机械运动,是机械自动化中不可缺少的一部分。
液压缸一旦出现故障,会影响整个机械设备的安全运行,下面分析一些液压缸的常见故障及处理预防措施。
1 液压缸不工作由于液压缸内活塞杆停止的位置不准确、活塞杆的推力不够、活塞杆运动速度过低、工作不稳等故障表现,造成液压缸不能带动负载运动。
具体引起原因分析及处理措施如下:1.1 液压缸内部漏油液压缸内部漏油主要有两种:液压缸活塞杆与活塞内孔,活塞密封磨损过量造成漏油。
活塞杆与活塞内孔漏油的原因是密封件老化磨损变形,及时更换密封件可解决这个问题。
活塞密封磨损过量的原因主要有:①速度控制阀失调造成背压过高;②安装密封件时出现失误造成液压油污染;③在安装液压缸过程中有杂物进入和低质的密封材料。
活塞密封磨损过量造成液压缸工作无力,还会导致缸筒磨损,出现拉缸现象。
解决方法是及时调整速度控制阀,更换清洗滤油器滤芯,更换液压油。
1.2 液压回路漏油液压回路漏油主要指阀件和液压管路的漏油。
处理方法是通过换向阀来判断各管路和阀件的漏油状况,及时维修更换漏油的阀件和管路。
1.3 液压油通过溢流阀直接返回油箱如果杂物卡死溢流阀的阀芯,溢流阀就变成常开状态,液压油直接返回油箱,液压缸内得不到足够压力的液压油,无法执行连续带负荷的动作,外部表现为动力不足,无法带动负载工作。
遇到这种情况时,应检查调整溢流阀。
2 液压缸工作不灵敏、有阻滞液压缸的不灵敏指液压缸在收到动作指令后,可以执行动作,但必须经过短暂的时间等待才可以执行动作,或者有时候执行动作有时候不执行动作。
液压缸不灵敏的故障分析及处理措施如下:(1)液压缸内进入空气。
液压缸中进入空气的主要原因是活塞杆往复运动部位的密封损坏,吸入空气。
解决措施:更换损坏的密封圈,打开液压缸的排气阀,排出空气。
高压液压缸受力变形研究
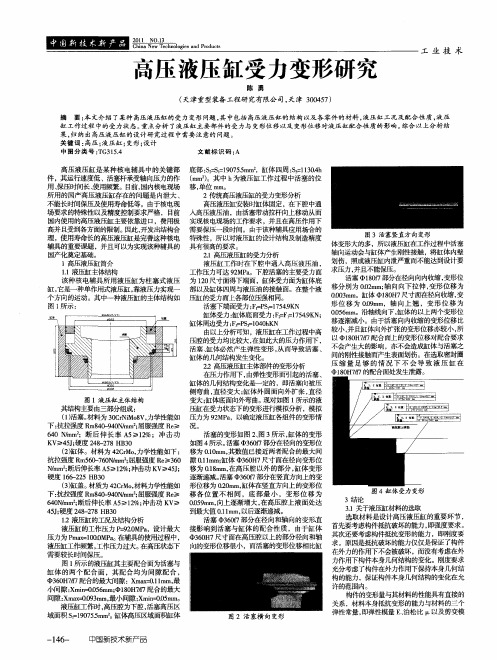
底 部 : ̄ l10 5 m 缸 体 四周 :3 0 h s .=97 . m , - s 5 s 13. =1 4 (m) 中 h m 。其 为液压缸 工作过程 中活塞 的位 移, 单位 m 。 m 2传 统高压 液压缸 的受力变形分析 高压液压缸安装时缸体 固定 , 在下腔 中通 入 高压 液压油 ,由活塞带动拉杆 向上移动从 而 实 现核 电现场的工作要求 ,并且在高压作用 下 需要保 压一段时间 。由于该种辅具应用场 合的 特殊性 , 以对液压缸的设计结构及制造精度 所 具有很 高的要求 。 2 . 1高压液压缸的受力分 析 液 压缸工作 时在下腔 中通入 高压液压 油 , 工作压力 可达 9M a 2 P 。下腔活塞 的主要受 力面 为 10 2 尺寸面得下端面 ,缸体受力面为缸 体底 部 以及缸 体 四周与液压油 的接触 面。在 整个液 压缸 的受力 面上各部位压强相 同。 图 1 示: 所 活塞下端面受力 :l s 15. N F P F 4 K _ 7 9 缸体受力 : 缸体底面受力 : 1 7 4 K ; F F l5. N = 9 缸体周边受力 :F F 00 K F l 14h N S 由以上分析可知 ,液压缸在工作过程 中高 压 腔的受 力均 比较大 , 在如此大 的压力作 用下 , 活塞 、 缸体必 然产生 弹性变形 , 从而导 致活 塞 、 缸体 的 八 结构发生变化 。 何 2 高压液压缸主体部件的变形 分析 2 在压力作用下 , 由弹性变形 而引起 的活塞 、 缸体 的几何结构变化是一定 的,即活塞 向被压 侧 弯 曲 , 变大 ; 体外 圆面 向外 扩张 , 直径 缸 直径 图 1液压缸主体结构 变 大; 缸体底面 向外弯 曲。 对如 图 I 现 所示 的液 其结构 主要 由三部分组成 : 压 缸在受力状态下 的变形进行模 拟分析 ,模拟 () 。 为 3 CNM 8 , 1活塞 材料 0 ri oV 力学性能如 压 力为 9M a 2 P ,以确定液压缸各组 件的变形情 下: 抗拉强度 R 4- 4Nm  ̄ 服强 度 R ≥ 况 。 m8090 /m ; 屈 e 60 Nm 4 /m;断后伸长率 A ≥1%;冲击功 5 2 活塞的变形如 图 2图 3 示 , 的变形 、 所 缸体 KV ̄4 J硬 度 2 8 2 8 HB 0 > 5; 4-7 3 如图 4 所示 。 活塞 q30 部分在径 向的变形位 b 6t 7 () 。材料为 4C M , 2缸体 2 r o力学性 能如下 : 移 为 0 0 m, . m 其数值 已接 近两者配合 的最大间 1 抗拉强度 R 5070 /m; m 6-6 Nm 2 屈服强度 R  ̄30 隙 01m i k 30 7 e 6 > . m; l  ̄ 中 6 H 尺寸面在径 向变形位 Nm /m ; 断后伸 长率 A ≥1%; 5 2 冲击功 K  ̄4J 移为 0 8 m 在 高压 腔 以外 的部分 , 变形 V 5; > .m , 1 缸体 硬度 16- 5H 3 6 -2 B 0 2 逐渐递 减。 活塞  ̄307 6f部分在竖直方 向上 的变 () 。 3缸盖 材质为 4 CMo材料力学 眭能如 形位移为 0 0 m 缸体 在竖直方 向上 的变形位 2r , .m , 2 下 : 拉强度 R 80 90 /m ; 强度 R ≥ 移 各 位 置 不 相 同 ,底 部 最 小 ,变 形 位 移 为 抗 m 4-4 Nm Z 屈服 e 4 Nm 60 / m; 断后伸 长率 A ≥1%; 5 2 冲击功 K 0 5r 向上逐渐 增大 , 高压腔上 液面 处达 v≥ . 9 m, 0 a 在 4 J硬度 2 8 2 8 HB 0 5; 4-7 3 到最大值0 m, .l 以后逐渐递减。 1m 1 _ 2液压缸 的工况及 结构 分析 活塞 q 6 f部分 在径 向和轴 向的变 形直 b 0 3 7 液压缸的工作压力 P 9. P ,设计最大 接 影 响到活 塞与 缸 体 的配合 性质 ,由于缸 体 =2 M a 0 压力为 P a=0. a 在辅具的使用过程 中, q30 7尺寸 面在高压 腔以上的部分径 向和轴 m x10 MP。 0 b6H 液压缸工作频繁, 工作压力过大。 在高压状态下 向的变形位移很小 , 而活塞 的变形 位移相 比缸 需要较长时间保压 。 图 1 示的液压缸其主要配合 面为活塞与 所 缸体 的两个配合面,其配合均为间隙配合 , 30 77 6 H / 配合的最大间隙 : m xO l , f X a=. mm 最 1 小间隙 :m n0 5 m ; 8 H / 配合 的最大 X i . 6 m  ̄10 7' =0 f / 间隙 :m x0 9m 最小 间隙 :mn0 5 m。 X a=. 3 m, 0 X i .m -0 液压缸工 作时 , 高压腔为下腔 , 高压区 活塞 域面积 S 105 m 缸体高压 区域面积缸体  ̄ 97. m。 = 5 图 2 活 塞横 向 变形
液压缸系统基于ANSYS的有限元应力分析_蒋理剑

液压缸系统基于ANSYS的有限元应力分析蒋理剑,张文辉(丽水学院工学院,浙江丽水323000)摘要:液压缸在能源机械等工业领域有着重要用途,然而当前针对液压缸系统可供参考的有限元分析方法还较少.提出了基于ANSYS的有限元系统分析方法.首先建立液压缸系统的有限元模型,进而通过设定边界条件及载荷分布对液压缸系统进行了力位移计算、全局应力分布及局部应力应变分布计算.计算结果能够为产品研发与分析提供重要参考,对于改进液压缸系统的性能与寿命具有重要意义.关键词:液压缸;有限元;静力分析;应变分析中图分类号:TH11文献标志码:A 文章编号:1008-7516(2014)04-0067-03Hydraulic cylinder system modal stress force analysisbased on ANSYSJiang Lijian,Zhang Wenhui(InstituteofTechnology,LishuiUniversity,Lishui323000,China)Abstract:Hydraulic cylinder has important use in industrial sectors such as energy machinery,however the current system analysis methods still are lack,the system finite element analysis methods based on ANSYS was put forward in this paper.Firstly finite element model of the hydraulic cylinder system was established,and then through boundary conditions are set and load distribution on the hydraulic cylinder system has carried on the force displacement calculation,the stress distribution of global and local stress distribution were calculated to provide an important reference for product development and analysis,The proposed finite element analysis methods based on the ANSYS have important engineering values for the hydraulic cylinder system research.Key words:hydraulic cylinder ;finite element ;static force analysis ;stress analysis液压缸是将液压能转变为机械能的、做直线往复运动(或摆动运动)的液压元件.它结构简单,工作可靠.用它来实现往复运动时,可免去减速装置并且没有传动间隙,运动平稳,因此在能源、机械等各种工业领域的有着重要用途,然而液压缸的刚度、强度、稳定性特性等因素将直接影响到液压缸的使用寿命和工作性能,因此对其进行深入研究具有重要意义[1-2].目前国内外学者液压缸也进行了比较深入的研究,取得了具有一定指导意义和工程价值的成果.文献[3]针对液压支架结合力学原理进行了分析计算,利用ANSYS对应力和稳定性进行了研究.文献[4]针对车用液压缸进行静态、动态和压杆稳定性分析,获得了结构稳定性条件.文献[5]针对液压缸承受径向载荷力,对其进行非线性分析,获得了最大载荷计算办法.文献[6]针对翻卷机液压缸各部件承受轴向力进行静力分析,分析了刚度等指标.上述分析方法具有一定借鉴意义,然而考虑到针对液压缸的有限元分析方面的研究结果还较少,本文提出了基于ANSYS的有限元系统分析方法.首先建立液压缸系统的有限元模型,进而通过设定边界收稿日期:2014-05-23基金项目:国家自然科学基金项目(61171189);国家科技支撑计划项目(2013BAC16B02);浙江省自然科学基金项目(LY14F030005);浙江省公益技术项目(2013C3110);浙江省教育厅项目(Y201330000)作者简介:蒋理剑(1977-),男,浙江丽水人,硕士,助理讲师.主要从事液压传动与有限元分析研究.doi:10.3969/j.issn.1008-7516.2014.04.016第42卷第4期424Vol.No.河南科技学院学报Journal of Henan Institute of Science and Technology 2014年8月2014Aug.67图1液压缸有限元模型Fig.1Finiteelementmodelofhydrauliccylinder条件及载荷分布对液压缸系统进行了力位移计算、全局应力分布及局部应力应变分布计算.计算结果能够为产品研发与分析提供重要参考,对于改进液压缸系统的性能与寿命具有重要意义.1基于ANSYS的应力分析1.1液压缸有限元模型建立HSG型工程液压缸主要用于各种工程机械、起重机、运输机械及工程车辆的液压传动系统中,具有典型意义.本文以HSG型工程液压缸为例,进行有限元方法的详细分析.定义内径63mm,外径83mm,活塞杆直径32mm,行程500mm,最小安装距795mm,工作压力16MPa,试验压力20MPa.为减少有限元分析计算量,同时保证计算精度,考虑到液压缸的结构和载荷具有中间对称性,这里沿对称面建立了右半部有限元模型.利用三维建模软件Solidworks建立系统模型并导入ANSYS中,如图1所示.1.2液压缸系统载荷施加在力的作用下计算液压缸的力位移、全局应力分布及局部应力分布对于分析系统受力情况具有重要意义.具体分析步骤如下.1.2.1定义材料属性和网格划分HSG型工程液压缸材料为45号钢,其弹性模量为220GPa,泊松比为0.3.采用Solid95号高阶三维实体单元,其中Solid95单元是20节点六面体单元,仿真精度高.采用自由网格(free)划分,得到模型节点数24602,单元数12798.其网格模型如图2所示.1.2.2添加接触单元为了方便建立接触对,本文利用接触向导对话框对活塞杆与导向套之间和活塞与缸筒之间建立接触对来模拟活塞杆与缸筒之间的运动情况.设定接触刚度比例因子为1.1.2.3施加约束和载荷在模型上施加接近实际载荷,是获得结构应力云图的关键.在HSG工程用型液压缸中,所要得到的主要有液压缸的应力分布及位移变化.所以要将外载荷转为内载荷,将工作液的压强转为缸体内部载荷的方式.根据液压缸的实际工作压力为16MPa,根据国家规定的试验加载方式,对液压缸进行1.25倍载荷的施加,即对液压缸施加20MPa的力,分别对缸体内表面、下表面及活塞底端施加载荷,其中S处为施加部位.其约束和载荷的加载情况如图3所示.1.3液压缸系统应力分析基于ANSYS的有限元求解器计算液压缸系统的位移云图,全局应力云图及局部应力云图.1.3.1液压缸位移计算云图图4所示为液压缸位移云图.图4液压缸位移云图Fig.4Thedisplacementnephogramofhydrauliccylinder图2液压缸的网格划分Fig.2Themeshmodelofhydrauliccylinder图3液压缸的约束和载荷Fig.3Theconstraintandloadofhydrauliccylinder2014年河南科技学院学报(自然科学版)68由图4可知,活塞杆头部变形量最大,最大值位于Max处,最小值位于Min处.从其中液压缸的最大变形为0.224mm,位于活塞处.1.3.2液压缸应力计算云图图5为液压缸应力云图.图5液压缸应力云图Fig.5Thestressnephogramofhydrauliccylinder由图5可知,最大应力为175MPa,位于耳环与活塞杆的连接处.图6为活塞杆与耳环连接处的应力分布.图6活塞杆与耳环连接处的应力分布Fig.6Thestressdistributioninthepistonofrodconnectionwithearrings由图6可知,最大应力位于耳环与活塞杆的连接处,其应力值为175MPa.其中45号钢的屈服强度为360MPa,抗拉强度为610MPa,则液压缸的安全系数,45号钢的安全系数为1.2 ̄1.5,所以液压缸的设计满足强度要求.2结论本文基于ANSYS对液压缸进行了较为系统有限元分析,建立了液压缸系统的有限元模型,并设计了边界条件及载荷施加原则;获得了液压缸系统的位移云图,其变形量及变形位置为产品改进提供依据;获得了液压缸系统的应力云图,其最大应力数据为强度计算提供了依据.所提的基于ANSYS的有限元方法对于液压缸系统的研发与分析具有重要工程价值.参考文献:[1]刘相新,孟宪颐.ANSYS基础与应用教程[M].北京:科学出版社,2006.[2]严海纲,黄泊戬,梅雪峰.采煤机摇臂壳体有限元分析[J].煤矿机械,2011,3(10):45-50.[3]WangHF,JiaKK,GuoZP.RandomvibrationanalysisforthechassisframeofhydraulictruckbasedonANSYS[J].JournalofChemical&PharmaceuticalResearch,2014,6(3):53-55.[4]陈敏;徐延金;涂能安.PDC钻头单齿工作角度有限元仿真研究[J].宜春学院学报,2009(6):32-35.[5]杨宏亮,彭岩.液压缸承受径向载荷的非线性有限元分析[J].机械设计与制造,2008,3(6):23-26.[6]罗海萍,潘佐云,唐清春.基于ANSYS的翻卷机液压缸的有限元分析[J].广西工学院学报,2011,9(9):45-49.(责任编辑:卢奇)蒋理剑等:液压缸系统基于ANSYS 的有限元应力分析第4期69。
重型液压支架歪架倒架机理

案例分析与实践经验分享
案例收集与整理
收集国内外重型液压支架歪架倒架的案例,整理并分析事故原因、处置过程及经验教训, 为预防和应对类似事故提供借鉴。
实践经验分享
通过组织专题研讨会、培训班等形式,分享行业内在预防和处理液压支架歪架倒架方面的 实践经验,共同提高行业安全水平。
技术创新与应用
鼓励企业、科研机构等进行技术创新,研发更加稳定可靠的重型液压支架,提升设备本质 安全,降低歪架倒架事故风险。
支架稳定性和平衡性分析
稳定性分析
• 地基承载力:支架的底座需与地层紧密接触,确保地 基承载力足够,防止支架下沉或失稳。
• 立柱平衡:支架的立柱在伸缩过程中需保持平衡, 避免因为受力不均导致支架扭曲或变形。
• 抗倾覆能力:支架的设计需考虑其抗倾覆能力,防 止在地下矿井不稳定岩层或受到外力时发生倾覆。
煤层厚度变化
煤层厚度的不均匀变化会对液压支架的稳定性产生影响,特别是在 薄煤层与厚煤层交替出现的情况下,支架容易失稳。
设备故障或操作不当导致的歪架倒架
1 2 3
液压系统故障
如液压泵、液压缸等部件发生故障,可能导致支 架无法正常升降或调整,进而引发歪架倒架事故 。
结构件疲劳断裂
液压支架在长时间高应力作用下,结构件可能发 生疲劳断裂,从而失去承载能力,导致歪架倒架 。
对制造工艺进行持续改进,采用先进的生产技术和设备,严格控制材料质量、热处理工艺、焊接质量等环节,提高支 架的制造精度和稳定性。
完善使用操作规程
制定更加完善的使用操作规程,加强对操作人员的培训和考核,确保在使用过程中能够正确、规范地操 作重型液压支架,减少因操作不当导致的歪架倒架事故。
推动行业安全标准与规范的提升
液压支架立柱以及千斤顶的故障原因与改善措施

机械管理开发MECHANICAL MANAGEMENT AND DEVELOPMENT 总第213期2021年第1期Total 213No. 1,2021经验交流DOI:10.16525/l4-1134/th.2021.()1.112液压支架立柱以及千斤顶的故障原因与改善措施宋昊妍(大同煤矿集团有限责任公司安全管理监察局,山西大同037003)摘要:基于液压支架立柱以及千斤顶在煤矿作业中的重要性,为了提高液压支架立柱以及千斤顶在生产工作中的效率,通过分析煤矿作业中殳柱和千斤顶可能会出现的损坏或者效果不佳等问题,对各千斤顶和立柱效果降低的原因进行探究,提出了相应的解决措施和提髙效率的方法,以改善殳柱以及千斤顶失效的情况,提高煤矿作业的安全生产效率。
关键词:千斤顶立柱影响因素密封件中图分类号:TD355-.3 文献标识码:A 文章编号:1003-773X ( 2021 )01 -0264-02引言同煤集团某矿具备664台采煤工作面液压支 架。
在各项条件中,该矿井的地质条件比较复杂,具 体而言地面标高的范围为-670—871 m,工作面的 倾斜长度为229 m,采高为7.2 m,工作面的平均倾 角度为28。
,走向长度的范围为600-1 211 m,并且具有较多的断层以及顶板具有破碎的情况。
除此之 外,工作面井下具备大量的腐蚀性介质,平均相对湿 度大约达到75%以上。
由于受腐蚀性介质的影响, 液压支架立柱以及千斤顶会有一定程度的磨损、侵 蚀以及偏载等,严重时导致设备失效,给现场的安全生产带来一定的危害。
基于这种情况和条件,本研究 经过对立柱和千斤顶的损坏情况进行详细研究分析,有针对性地寻找避免损坏的措施,并在现场进行 应用反馈取得了较好的成效。
1立柱和千斤顶的结构介绍1.1立柱的结构立柱是帮助液压支架实现承载以及支撑功能的重要构造,根据伸缩的级数,立柱可分为以下三种类型,分别是三伸缩(较少使用)、双伸缩以及单伸缩 (加长杆)。
从液压造成的高度看阿基米德原理和帕斯卡定律

阿基米德原理
浸在液体中的物体受到向上的浮力,浮力的大小等于物体 排开的液体所受的重力。
液体动力学基础
01
伯努利方程
在理想液体中作稳定流动时,具有压力能、位能和动能三种形式,它们
之间可以相互转化,且总和保持不变。
02
帕斯卡定律
加在被封闭液体上的压强能够大小不变地由液体向各个方向传递。
04
辅助装置
除上述三部分以外的其他装置, 例如油箱、滤油器、冷却器、加 热器、蓄能器、油管及管接头、 密封圈、快换接头、高压球阀、 胶管总成、测压接头、压力表、 油位油温计等。
液体静力学基础
静止液体中的压强分布规律 静止液体中任一点的压强,由液面上的压强(大气压强或 液面上的气体压强)和该点距液面的垂直高度所决定,而 与该点的方位无关。
帕斯卡定律
帕斯卡定律是流体静力学的基本原理,它指出在密闭容器内,施加于静止液体 上的压强可以等值传递至液体内部各个点和各个方向。帕斯卡定律为液压传动 提供了理论基础。
研究目的和意义
揭示液压传动基本原理
通过深入研究阿基米德原理和帕斯卡定律,可以更加深入地理解液压传动的基本原理和工作 机制,为液压传动系统的设计和优化提供理论指导。
02
阿基米德原理是流体力学的基础理 论之一,对于理解液体中物体的受 力情况和运动规律具有重要意义。
浮力产生原因及大小计算
浮力产生原因
物体在液体中受到向上的浮力,是因为物体排开了与其体积相 等的液体,使得液体对物体产生一个向上的压力差。
浮力大小计算
根据阿基米德原理,物体在液体中所受的浮力等于排开的液体 所受的重力,即F浮=ρ液gV排,其中ρ液为液体密度,g为重力 加速度,V排为物体排开液体的体积。
试析液压支架立柱外缸体的设计

试析液压支架立柱外缸体的设计引言立柱是支架的承載构件,它长期处于高压受力状态,它的工作性能直接影响整个支架的工作状态。
因此在设计立柱时除应具有合理的工作阻力和可靠的工作特性外,还必须有足够的抗压、抗弯强度,良好的密封性能,结构要简单,并能适应支架的工作要求。
在生产实际中,外缸体的变形主要有缸体胀缸、人为破坏、密封失效等几方面,其中液压支架立柱胀缸问题越来越突出,大修液压支架立柱的胀缸比例约占20%,给生产维检带来很大压力,对安全生产与优质高效造成影响。
因此,研究分析研究立柱外缸体的变形、探讨有效防范及处置处理措施,对于煤矿企业综合机械化采煤降耗提效、促进安全生产、提升企业科技管理水平等方面,都具有重要意义。
本文主要将以ZY10000/28/62D中的立柱外缸体为例,运用SolidWorks Simulation 有限元分析软件对外缸筒进行分析,提出具体的设计改进措施,避免出现由于缸体变形而影响工作的现象发生。
一、建模ZY10000/28/62D型支架立柱的结构如图1所示,为双伸缩柱塞式结构,主要由外缸体、中缸体、活柱等构成。
从二维零件图可以获得尺寸,其中主尺寸如下:立柱总长L=5860mm,外缸体L1=2278mm,中缸体L2=2168mm,活柱L3=2220mm,外缸体内径D1=400mm,中缸体外径D2=380mm,活柱直径D3=260mm。
二、缸体的强度校核双伸缩立柱的外缸、中缸多数用27SiMn无缝钢管制作,液压支架立柱的壁厚(mm)一般为,即中等壁厚,按(1-1)式计算:(1-1)式中p—液压缸的最大工作压力,MPa;C—考虑关闭公差及侵蚀的附加厚度,mm;一般取2mm。
—强度系数,无缝钢管的=1;[]—缸体材料许用应力,MPa。
已知D=400mm,p=31.5MPa,C=2,=1,查表取安全系数:n=5;选取缸体材料为27SiMn,经查表得σb=980 MPa ,[]=σb/n=196 MPa。
基于Creo的液压缸设计及优化

C r e o 软 件 对液压 缸进 行三 维建模 和 受力分析 , 得 出缸 体 的应 力和应 变分 布 图。利 用 C r e o软件
自身的优 化设计 功 能对液 压缸进 行 了优化 设 计。通 过 实践证 明 , 优 化设 计合理 。
关键 词 : 液压缸 ; 设计 ; C r e o ; 优 化 中图分 类号 : T H1 3 7 . 5 1 文 献标识 码 : A 文章 编号 : 1 0 0 9— 5 4 6 2 ( 2 0 1 6 ) 0 3— 0 0 4 9— 0 3
刚度 校核 等分 析还不 成熟 。新设 计 的液压 缸采 用样 品 和人工 校 核 的方 法 费时 费力 , 不 能 提升 设计 效 率 。 而 采用数 字化 仿真技 术 , 不 但 可 以省 时省 力 , 还 能对 产 品进 行 仿 真 , 及 时进 行 优 化设 计 。C r e o软件 在 众
在 本设 计 中 , 缸壁、 缸底 和进 油 口受到 高压 油 的作用 , 故 对 这 三个 区域进 行 网格 细分 。在 A u t o G E M 选 项 中, 类 型选 择 “ 最大 元素 尺寸 ” , 参 照 曲面选择 缸 壁 、 缸底 和进 油孑 L , 元 素 尺 寸定 义 为 l O m m。进 行 网格 创 建, 创建了 3 2 0个 元 素和 1 0 0 0 5个 节点 , 计算 机 用时 5 . 1 8分钟 。而将 元 素尺寸 定义 为 2 0 m m 时则创 建 了
利用 C r e o软件 进行 三维建 模 。建模 过程 中用 拉伸 、 凸 台 和旋 转 等一 系列命 令 可 建 立液 压 缸 的实 体
模型, 如图 1 所示 。考 虑到 模型 的对 称性 , 在 进 行 分析 时 可 以 简化 成 半 个模 型进 行 析计 算 , 缩 短计算 时 间 。简化后 的模 型 如图 2所示 。
- 1、下载文档前请自行甄别文档内容的完整性,平台不提供额外的编辑、内容补充、找答案等附加服务。
- 2、"仅部分预览"的文档,不可在线预览部分如存在完整性等问题,可反馈申请退款(可完整预览的文档不适用该条件!)。
- 3、如文档侵犯您的权益,请联系客服反馈,我们会尽快为您处理(人工客服工作时间:9:00-18:30)。
高压液压缸受力变形研究
作者:陈勇
来源:《中国新技术新产品》2011年第13期
摘要:本文介绍了某种高压液压缸的受力变形问题,其中包括高压液压缸的结构以及各零件的材料,液压缸工况及配合性质,液压缸工作过程中的受力状态。
重点分析了液压缸主要部件的受力与变形位移以及变形位移对液压缸配合性质的影响。
综合以上分析结果,归纳出高压液压缸的设计研究过程中需要注意的问题。
关键词:高压;液压缸;变形;设计
中图分类号:TG315.4 文献标识码:A
高压液压缸是某种核电辅具中的关键部件,其运行速度低、活塞杆承受轴向压力的作用、保压时间长、使用频繁。
目前,国内核电现场所用的国产高压液压缸存在的问题是内泄大、不能长时间保压及使用寿命低等。
由于核电现场要求的特殊性以及精度控制要求严格,目前国内使用的高压液压缸主要依靠进口,费用极高并且受到各方面的限制。
因此,开发出结构合理,使用寿命长的高压液压缸是完善这种核电辅具的重要课题,并且可以为实现该种辅具的国产化奠定基础。
1 高压液压缸简介
1.1 液压缸主体结构
该种核电辅具所用液压缸为柱塞式液压缸,它是一种单作用式液压缸,靠液压力实现一个方向的运动。
其结构主要由三部分组成:
(1)活塞。
材料为30CrNiMo8V,力学性能如下:抗拉强度Rm840-940N/mm2;屈服强度Re≥640 N/mm2;断后伸长率A5≥12%;冲击功KV≥45J;硬度248-278 HB30
(2)缸体。
材料为42CrMo,力学性能如下:抗拉强度Rm560-760N/mm2;屈服强度
Re≥360 N/mm2;断后伸长率A5≥12%;冲击功KV≥45J;硬度166-225 HB30
(3)缸盖。
材质为42CrMo,材料力学性能如下:抗拉强度Rm840-940N/mm2;屈服强度Re≥640N/mm2;断后伸长率A5≥12%;冲击功KV≥45J;硬度248-278 HB30
1.2 液压缸的工况及结构分析
液压缸的工作压力P=92.0MPa,设计最大压力为Pmax=100.0MPa。
在辅具的使用过程中,液压缸工作频繁,工作压力过大。
在高压状态下需要较长时间保压。
液压缸其主要配合面为活塞与缸体的两个配合面,其配合均为间隙配合,Φ360H7/f7配合的最大间隙: Xmax=0.11mm,最小间隙:Xmin=0.056mm;Φ180H7/f7配合的最大间隙:Xmax=0.093mm,最小间隙:Xmin=0.05mm。
液压缸工作时,高压腔为下腔,活塞高压区域面积S1=19075.5mm2。
缸体高压区域面积缸体底部:S2=S1=19075.5mm2,缸体四周:S3=1130.4h(mm2)。
其中h为液压缸工作过程中活塞的位移,单位mm。
2 传统高压液压缸的受力变形分析
高压液压缸安装时缸体固定,在下腔中通入高压液压油,由活塞带动拉杆向上移动从而实现核电现场的工作要求,并且在高压作用下需要保压一段时间。
由于该种辅具应用场合的特殊性,所以对液压缸的设计结构及制造精度具有很高的要求。
2.1 高压液压缸的受力分析
液压缸工作时在下腔中通入高压液压油,工作压力可达92MPa。
下腔活塞的主要受力面为120尺寸面得下端面,缸体受力面为缸体底部以及缸体四周与液压油的接触面。
在整个液压缸的受力面上各部位压强相同。
活塞下端面受力:F1=PS1=1754.9KN
缸体受力:缸体底面受力:F2=F1=1754.9KN;缸体周边受力:F3=PS3=1040hKN
由以上分析可知,液压缸在工作过程中高压腔的受力均比较大,在如此大的压力作用下,活塞、缸体必然产生弹性变形,从而导致活塞、缸体的几何结构发生变化。
2.2 高压液压缸主体部件的变形分析
在压力作用下,由弹性变形而引起的活塞、缸体的几何结构变化是一定的,即活塞向被压侧弯曲,直径变大;缸体外圆面向外扩张,直径变大;缸体底面向外弯曲。
现对液压缸在受力状态下的变形进行模拟分析,模拟压力为92MPa,以确定液压缸各组件的变形情况。
活塞Φ360f7部分在径向的变形位移为0.10mm,其数值已接近两者配合的最大间隙
0.11mm;缸体Φ360H7尺寸面在径向变形位移为0.18mm,在高压腔以外的部分,缸体变形逐渐递减。
活塞Φ360f7部分在竖直方向上的变形位移为0.20mm,缸体在竖直方向上的变形位移各位置不相同,底部最小,变形位移为0.059mm,向上逐渐增大,在高压腔上液面处达到最大值0.11mm,以后逐渐递减。
活塞Φ360f7部分在径向和轴向的变形直接影响到活塞与缸体的配合性质,由于缸体
Φ360H7尺寸面在高压腔以上的部分径向和轴向的变形位移很小,而活塞的变形位移相比缸体变形大的多,所以液压缸在工作过程中活塞轴向运动会与缸体产生刚性接触,将缸体内壁划伤,照成液压缸内泄严重而不能达到设计要求压力,并且不能保压。
活塞Φ180f7部分在径向向内收缩,变形位移分别为0.02mm;轴向向下拉伸,变形位移为0.003mm。
缸体Φ180H7尺寸面在径向收缩,变形位移为0.09mm,轴向上翘,变形位移为0.056mm。
沿轴线向下,缸体的以上两个变形位移逐渐减小。
由于活塞向内收缩的变形位移比较小,并且缸体向外扩张的变形位移亦较小,所以Φ180H7/f7配合面上的变形位移对配合要求不会产生大的影响,亦不会造成缸体与活塞之间的刚性接触而产生表面划伤。
在选取密封圈压缩量足够的情况下不会导致液压缸在Φ180H7/f7的配合面处发生泄露。
3 结论
3.1 关于液压缸材料的选取
选取材料是设计高压液压缸的重要环节,首先要考虑构件抵抗破坏的能力,即强度要求。
其次还要考虑构件抵抗变形的能力,即刚度要求。
原因是抵抗破坏的能力仅仅是保证了构件在外力的作用下不会被破坏,而没有考虑在外力作用下构件本身几何结构的变化。
刚度要求充分考虑了构件在外力作用下保持本身几何结构的能力,保证构件本身几何结构的变化在允许的范围内。
构件的变形量与其材料的性能具有直接的关系,材料本身抵抗变形的能力与材料的三个弹性常量,即弹性模量E、泊松比μ以及剪变模量G有关,对于各向同性材料三者之间的关系为[1]
E=G/2(1+μ)
在零件材料的选取过程中,要充分考虑零件材料本身的力学性能,选取E、G值较大的材料,从而保证零件的刚性得到加强。
3.2 关于液压缸零部件的结构
由以上的分析可知,液压缸在工作过程中由于受到高压油的压力作用,活塞、缸体均会产生不同程度的变形。
变形可以直接影响到活塞与缸体之间的配合性质,甚至会使活塞与缸体之间形成刚性接触。
配合性质发生变化必然导致密封件的压缩量产生变化,导致密封失效;活塞与缸体发生刚性接触必然导致配合密封面的划伤,导致密封失效,产生内泄。
所以在进行液压缸的设计过程中要合理设计各零部件的结构,一方面增加零件的刚性,一方面减小零件产生变形导致的密封失效。
参考文献
[1]刘鸿文.材料力学-2版(修订本).北京:高等教育出版社,1992.。