湿法冶金工艺中的除油技术
湿法冶金原理

湿法冶金原理
湿法冶金原理是一种将金属从其矿石或废料中提取的方法。
在湿法冶金过程中,金属物质首先被溶解或氧化,然后通过化学反应将其转化为可利用的形式。
湿法冶金的原理通常涉及以下步骤:
1. 矿石或废料的浸取:将矿石或废料放入特定的溶解剂(如酸、碱或盐溶液)中,以便溶解金属物质。
2. 过滤:通过将浸取液通过滤网或其他过滤介质进行过滤,去除其中的杂质和固体颗粒。
3. 溶液处理:对过滤后的浸取液进行进一步的处理,以去除杂质、提高金属纯度或调整溶液的pH值。
4. 电解:对溶液中金属物质进行电解,使金属离子在电流作用下还原成金属沉积在电极上。
5. 结晶:通过控制溶剂的温度和浓度,将金属沉淀物以晶体形式从溶液中分离出来。
湿法冶金原理的应用非常广泛,可以用于提取多种金属,包括铁、铜、铝、锌、镍等。
尽管这种方法相对于干法冶金而言更为复杂,但由于其高效和可持续的特性,它在金属冶金工业中得到广泛应用。
Dow 除油技术
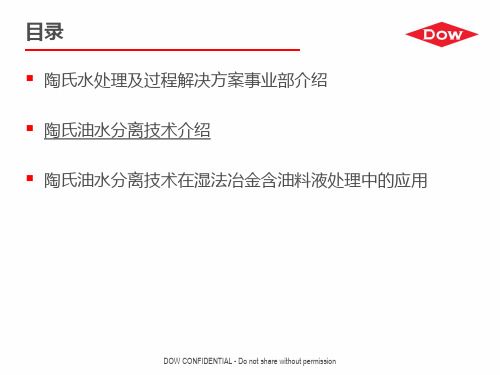
陶氏水处理及过程解决方案事业部介绍 陶氏油水分离技术介绍 陶氏油水分离技术在湿法冶金含油料液处理中的应用
DOW CONFIDENTIAL - Do not share without permission
陶氏油水分离技术 – (Oil-Dock)
陶氏在有机物去除技术SMART工艺 的基础上,针对油类物质的性质以 及在水中的分布特征,Dow利用自 身在材料科学和工程应用领域的经 验,开发了Oil-Dock油水分离技术; Oil-Dock技术可以回收浓缩去除含 油料液中的大部分油类, 同时可根 据客户需求提供组合除油工艺,以 满足生产工艺对油浓度的要求; 创新型的除油填料,具有捕捉油粒 能力强,易于脱附的特点,具有很 强的抗冲击性;针对的除油装置设 计可以方便的实现除油填料的吸、 脱附和回收捕捉的油。
油水分 离填料
DOW CONFIDENTIAL - Do not share without permission
可应用领域
含油凝结水处理回收; 特殊含油料液的处理:如含油高盐废液的回收;
油的回收:湿法冶金含油料液的处理;
………..
DOW CONFIDENTIAL - Do not share without permission
目录
陶氏水处理及过程解决方案事业部介绍 陶氏油水分离技术介绍 陶氏油水分离技术在湿法冶金含油料液处理中的应用
DOW CONFIDENTIAL - Do not share without permission
在湿法冶金含油料液处理中的应用
在湿法冶金中,利用溶剂煤油配置萃取剂来萃取浸出液中 的金属是最主要的工艺形式; 在萃取、反萃的过程中,不可避免存在着有机相的流失, 具体表现为料液的含油量超标,因此需要进行除油来满足 后续工艺的要求,或减少对环境的影响; 重力隔油、气浮除油、吸附介质除油等技术已经在湿法冶 金行业有大量研究和使用经验,如何进一步提高除油效果 一直被业界所关注; 陶氏的Oil-Dock技术为进一步优化除油效果带来了解决方案。
金属加工制程工艺过程去除油污方法

金属加工制程工艺过程去除油污方法金属加工制程工艺过程中的清洗,从原理上来说,去除油污是有三种方法。
一是乳化法,利用表面活性剂的两亲性质,亲油端吸附油污分子,亲水端吸附水分子,卷缩、乳化形成悬混乳液,从而将清洗工件表面的油污洗去。
二是溶剂法,油不溶于水,但溶于有机溶剂,使油污溶解分散在溶剂之中,实现油污与清洗工件的剥离清除。
三是皂化法,是利用酯(尤指羧酸酯)在碱的作用下水解生成羧酸盐和醇,再获取所要提取的有机物,与表面活性剂清洗油污一样,可以将油污剥离清洗工件的表面。
但是面临日益强大的法规压力,传统的溶剂和强碱的使用已经减少。
相应地水基或非挥发性溶剂清洗剂和脱脂剂的使用正在增加。
从清洗效果来看,水基金属清洗剂技术已接近于成熟。
工业应用中,三种去除油污的原理,又可以分成以下两种清洗剂,即溶剂型清洗剂和水基型清洗剂。
1.溶剂型清洗剂简单的来讲就是选用合适的有机溶剂有效溶解目标油污,然后通过高压蒸馏的方法提纯有机溶剂,实现溶剂型清洗剂的循环使用。
使用溶剂型清洗剂,对清洗设备的要求较高,设计复杂,造价不菲,且使用安全性的余量较大,成本较高。
2.水基型清洗剂因其使用可以用水稀释,水作为大量的主要廉价溶剂,得到广泛的工业应用。
再用因安全性,以及对设备的要求低,操作简单,适合大量生产,因此应用广泛。
水基型清洗剂是综合了乳化法与皂化法的优点,进行清洗剂配方的优先复配,实现稳定的体系结构与实现分工协作和互补。
水基型清洗剂的不良反应主要是对腐蚀的控制,具体表现为防止在清洗过程中的金属腐蚀,以及清洗后进入下一个工序之间的工序间防腐蚀。
在工业化应用的就是大批量、可重复、稳定持续地使用,还必须控制不良反应,维持稳定有效的溶液体系。
稳定有效的溶液体系,反应了清洗剂的使用寿命,也就是说在一定的生产周期内持续稳定有效,是进入工业化生产的前提。
湿法冶金工艺流程

湿法冶金工艺流程湿法冶金工艺流程是一种常用的冶金工艺,主要用于提取和精炼金属。
以下是一个典型的湿法冶金工艺流程的简要描述。
首先,在湿法冶金工艺中,首先需要选矿。
选矿的目的是从原矿中分离出目标金属并去除无关的杂质。
这一步骤通常通过矿石研磨和浮选来实现。
研磨将矿石颗粒细化,以便更好地与分离剂相互作用。
浮选过程中,则是将矿石和分离剂混合,使目标金属的颗粒被吸附在泡沫上,从而分离出来。
然后,分离出的目标金属精矿需要经过浸出处理。
浸出是将金属从矿石中溶解出来的过程。
这一步骤通常使用化学溶剂,如含氯化物的溶液。
溶剂与精矿接触,以便溶解金属成分。
随后,通过搅拌和过滤等方式,将溶剂中的金属分离出来。
接下来,通过沉淀和氧化,将金属溶液中的杂质去除。
沉淀是将金属盐溶液中的杂质沉淀成固体颗粒,然后通过过滤或离心等方式分离。
氧化则是将金属溶液中的杂质氧化成不溶于溶液的化合物,然后通过过滤或沉淀等方式分离。
然后,通过还原和电解,将纯净的金属从溶液中析出。
还原是指将金属溶液中的金属阳离子还原成金属原子的过程。
这一步骤通常使用还原剂,如氢气或焦炭等。
电解则是利用电解质溶液中的电解作用,将金属阳离子在电极上合成金属原子,并沉积在电极上。
最后,经过上述步骤处理后得到的金属需要进行精炼。
精炼是将金属中的杂质去除,以获得高纯度的金属。
这个过程中通常使用真空蒸馏、电渣重熔等方法来实现。
真空蒸馏通过在低压环境下蒸发杂质,以获得高纯度的金属。
电渣重熔则是将金属材料与电渣混合,通过电流加热使杂质溶解在电渣中,从而获得高纯度的金属。
总的来说,湿法冶金工艺流程是一种通过选矿、浸出、分离、还原、电解和精炼等步骤,从原矿中提取和精炼金属的方法。
这个流程可以适用于不同种类的金属,在冶金产业中有着广泛的应用。
刚果(金)湿法炼铜电富液除油技术及实践

刚果(金)湿法炼铜电富液除油技术及实践
孟祥龙;张海宝;李强;陈燕杰
【期刊名称】《有色冶金设计与研究》
【年(卷),期】2024(45)1
【摘要】针对反萃后的电富液通常会夹带有机相,如不妥善处理的情况,会在电积过程中影响阴极板质量的情况,分析了电富液除油机理,以及常见的电富液净化除油技术。
以刚果(金)某铜钴湿法矿山企业电富液除油技术实践为例,着重研究了超声波-气浮除油装置和聚结式净化除油。
该企业将原有除油系统升级为1台处理量为450 m^(3)/h的超声波-气浮除油装置与1台处理量为180 m^(3)/h的聚结式除油装置。
升级后的实践表明,两种除油方式都具有较好的除油效果。
【总页数】4页(P18-21)
【作者】孟祥龙;张海宝;李强;陈燕杰
【作者单位】中国瑞林工程技术股份有限公司;云南铜业股份有限公司
【正文语种】中文
【中图分类】TF811
【相关文献】
1.赞比亚某湿法炼铜厂萃取-电积车间生产实践
2.湿法炼铜电铜尾液的处理
3.混酸器在刚果(金)某湿法炼铜厂中的生产实践
4.针床澄清器在刚果(金)某湿法炼铜厂的生产实践
5.湿法炼铜中铜萃余液和浸出液高效处理技术分析
因版权原因,仅展示原文概要,查看原文内容请购买。
湿法冶炼工艺技术

湿法冶炼工艺技术湿法冶炼工艺技术是一种将金属矿石经过溶解、离析、净化等一系列的工艺过程,将其中的有价金属从矿石中提取出来的方法。
具体来说,湿法冶炼工艺技术是通过将矿石与溶剂接触,在特定的条件下使金属溶解于溶液中,再通过降温、淬火等手段将其沉淀或凝固,最终得到金属。
湿法冶炼工艺技术主要有火法、浸出法、溶解法等多种方法,下面就分别讲解一下这几种常用的湿法冶炼工艺技术。
首先是火法,火法是一种通过高温将矿石中的有价金属转化为氧化物的方法。
在这个过程中,矿石会在高温下发生化学反应,使金属元素从硫化物、碳酸盐等矿石中转化为金属氧化物,然后再通过还原反应将氧化物还原为金属。
火法工艺技术的优点是操作简单、能耗低、生产成本相对较低。
其次是浸出法,浸出法是一种通过化学溶解将金属从矿石中提取出来的方法。
在这个过程中,矿石会和一种溶液或气体接触,在特定条件下使金属溶解于溶液中,然后再通过沉淀、电解、萃取等方法将金属从溶液中分离提取出来。
浸出法工艺技术的优点是提取效率高、生产成本相对较低。
最后是溶解法,溶解法是一种将金属矿石通过化学溶解得到金属的方法。
在这个过程中,矿石会和特定的溶剂接触,在特定温度、压力、PH值等条件下使金属溶解于溶液中,然后再通过浓缩、结晶等方法将金属从溶液中提取出来。
溶解法工艺技术的优点是提取效率高、工艺灵活性强、产品质量好。
当然,湿法冶炼工艺技术也存在一些问题。
首先是废水和废渣的处理问题,湿法工艺产生的废水和废渣含有一定的毒性和污染物质,需要特殊的处理方法才能达到环保要求。
其次是能源消耗问题,湿法工艺需要耗费大量的能源才能维持其正常运作。
此外,湿法工艺的设备投资和维护成本较高也是一个问题。
总的来说,湿法冶炼工艺技术是一种重要的金属提取方法,具有提取效率高、操作简单等优点,但同时也存在着废水和废渣处理问题、能源消耗问题以及设备投资和维护成本高等一系列问题。
未来,随着科技的进步和工艺技术的不断改进,相信湿法冶炼工艺技术会越来越完善,为金属冶炼行业带来更大的发展机遇。
湿法冶金的工艺流程和原理

湿法冶金的工艺流程和原理嘿,朋友们,今天咱们来聊聊湿法冶金。
这玩意儿听起来挺高大上的,其实呢,就是把金属从矿石里提取出来的一种方法。
就像你从一堆沙子里淘金一样,只不过这里的沙子换成了矿石,金子换成了各种金属。
首先,咱们得从矿石说起。
矿石,就是那些含有金属的石头。
这些石头里,金属是以化合物的形式存在的,不是纯金属。
所以,咱们得想办法把这些金属从化合物里分离出来。
湿法冶金的第一步,就是把矿石磨成粉末。
这就好比你要把豆子磨成豆浆,得先把它磨碎。
磨矿石的机器叫做球磨机,里面有很多铁球,矿石放进去,铁球就在里面滚来滚去,把矿石磨成粉末。
磨好的矿石粉末,下一步就是浸出。
这一步,就是把金属从矿石粉末里提取出来。
这就好比你要把豆浆里的豆渣过滤掉,留下纯豆浆。
浸出的方法有很多,最常见的就是用酸或者碱溶液。
把矿石粉末和酸或者碱溶液混合,金属就会溶解在溶液里,形成金属离子。
浸出后的溶液,里面含有金属离子,但是还有很多杂质。
所以,下一步就是净化。
这一步,就是把金属离子从溶液里分离出来,去除杂质。
这就好比你要把豆浆里的豆渣彻底过滤掉,留下纯豆浆。
净化的方法有很多,比如沉淀法、溶剂萃取法、离子交换法等等。
净化后的溶液,里面就只剩下金属离子了。
最后一步,就是把金属离子还原成纯金属。
这一步,就是把金属从溶液里提取出来,形成纯金属。
这就好比你要把豆浆里的蛋白质提取出来,做成豆腐。
还原的方法有很多,比如电解法、置换法、还原法等等。
好了,这就是湿法冶金的整个工艺流程。
听起来是不是挺复杂的?其实,这个过程就像你做豆浆一样,需要很多步骤,但是每一步都是为了把金属从矿石里提取出来。
湿法冶金的原理,其实就是化学反应。
金属从矿石里提取出来,就是通过化学反应实现的。
比如,浸出的时候,金属和酸或者碱发生反应,形成金属离子。
净化的时候,金属离子和杂质发生反应,形成沉淀或者被萃取出来。
还原的时候,金属离子发生还原反应,形成纯金属。
总的来说,湿法冶金就是通过一系列的化学反应,把金属从矿石里提取出来。
湿法冶金工艺流程

湿法冶金工艺流程
《湿法冶金工艺流程》
湿法冶金是一种利用水溶液来提取金属的工艺。
它包括了从矿石中提取金属的过程,其中矿石被浸入含有化学物质的水溶液中,金属离子被溶解到水中,然后通过沉淀或其他方法从水溶液中分离出金属。
湿法冶金工艺流程是一个复杂而精细的过程,通常包括以下基本步骤:
1. 矿石破碎和粉磨:首先将矿石破碎成小块,然后通过粉磨使其细化成粉末状。
2. 浸出:矿石粉末被浸入含有化学溶剂的水溶液中,这个过程被称为浸出。
溶液中的金属离子开始溶解到水中形成金属盐。
3. 沉淀:通过加入化学试剂或改变溶液的条件(如温度、pH 值等),使金属离子从溶液中沉淀出来,形成固体的金属沉淀物。
4. 过滤和干燥:将金属沉淀物通过过滤分离出溶液,然后对沉淀物进行干燥,得到纯净的金属。
湿法冶金工艺流程在生产中起着重要作用,它被广泛应用于提取铜、铅、锌、镍、钴、金、银等金属。
而且湿法冶金工艺相对于干法冶金来说,可以处理低品位矿石且生产出更高纯度的
金属产品。
然而,湿法冶金也面临着一些挑战,如对环境的影响和工艺流程的复杂性,需要使用大量的化学试剂和水,并产生大量的废水和废渣。
因此,在使用湿法冶金工艺时,需要重视环保、资源节约和安全生产等问题。
总的来说,《湿法冶金工艺流程》是一个综合性、复杂性和技术含量高的工艺流程,它能够为金属提取提供一种有效的方式,但也需要在生产过程中引起重视和关注。
- 1、下载文档前请自行甄别文档内容的完整性,平台不提供额外的编辑、内容补充、找答案等附加服务。
- 2、"仅部分预览"的文档,不可在线预览部分如存在完整性等问题,可反馈申请退款(可完整预览的文档不适用该条件!)。
- 3、如文档侵犯您的权益,请联系客服反馈,我们会尽快为您处理(人工客服工作时间:9:00-18:30)。
湿法冶金工艺中的除油技术
摘要:湿法冶金生产过程中,通常都会使用混合澄清槽、离心萃取器、萃取塔
等设备来实施大规模连续萃取及两相的混合与分离。
这种生产工艺通过设备分离
后的水相溶液会含有一定量的油相,因为普通的萃取剂有着一定的亲水性,所以
不仅会导致大颗粒油无法及时澄清,而且也会有少量油以稳定的乳化态或者是溶
解态留在料液中。
如果不能及时有效的清除水相中夹杂的油,就会增加萃取剂的
浪费,甚至也会影响到后续工艺的正常生产,从而影响冶金产品的质量。
另外残
留在水相中的油也会在废水中积累,最终会给污水处理工作带来不利影响,鉴于此,笔者从油相组成及形成原因出发,针对湿法冶金工艺中的出油技术进行研究
分析,以供参考。
关键词:湿法冶金;溶剂萃取;除油技术
1油相组成及形成原因
溶剂萃取水相中的油相组分更加复杂,水相夹带的油不是单纯的萃取剂油相
残留,而是含有多种萃合物的复杂有机成分,所以萃取体系除油需要从油相的组
成着手进行研究。
湿法冶金中常用的萃取剂按酸碱性可分为酸性、碱性及中性萃取剂。
在酸性
萃取体系中,酸性磷类萃取剂、螯合类萃取剂和羧酸型萃取剂的萃取都是通过萃
取剂中活性基团上的阳离子与料液中的金属阳离子发生交换实现的,萃合物为含
金属阳离子的萃取剂大分子。
萃取体系水相中夹带的油相的主要成分是未萃取的
萃取剂分子、稀释剂、极性改性剂及萃合物。
萃取剂在长期使用后会存在一定程
度的降解,所以水相夹带的油相组分中还有微量的长碳链有机物分子。
其中,酸
性磷类萃取剂的功能基团是以P为中心原子的基团,按路易斯酸碱理论属于硬酸,而H?0属于硬碱,二者具有一定亲和力,容易形成配合物,所以萃取剂具有一定
的亲水性。
该体系中的溶解油含量不容忽视。
中性萃取剂的萃合物都以中性分子形式与萃取剂结合。
萃取过程是金属阳离
子与配体阴离子生成配合物大分子,再与萃取剂分子结合生成萃合物。
该萃取体
系中夹带的油相中所含的是配合物大分子、萃取剂、少量稀释剂及改性剂。
碱性萃取剂的萃取是以离子缔合形式实现。
萃取时金属以配阴离子形式存在
于溶液中,萃取剂与质子或水合成质子形成大阳离子,两者构成疏水性离子缔合体。
常用的该类萃取剂以N263、N235为代表,其功能基团是以N为中心原子的
基团,属于硬酸,也会与属于硬碱的H?O形成配合物。
同样会有相当一部分萃取
剂以溶解油形式存在于水相中。
2常用除油方法
2.1生化处理法
生化处理法是一种新兴的末端除油方法,是利用微生物的代谢作用分解有机
污染物使油相降解实现除油。
目前比较成熟的生物处理法有活性污泥法和生物膜法。
活性污泥法是利用活
性污泥中的微生物对有机物的富集作用实现深度除油,但生物处理法对进水水质
要求较高,要求水质、水量稳定,波动小。
生物膜法是利用膜反应器比表面积较
大的原理将微生物附着于填充料表面,在废水流经填充物时,利用微生物富集水
中的有机物并使其降解而实现除油。
生物膜法处理效率较高、基建费用稍低,但
运行成本较高,对管理的要求也较高。
对于有色冶金萃取体系,生物处理法由于其对料液的稳定性要求较高,通常
其BOD/COD的值很难达到可生物降解的范围,同时经过生物处理后的水溶液体
系可能发生改变,因此不适用于萃取中段料液除油,但由于生化法能达到很好的COD去除效果,所以,出口水质要求高的水相除油可以考虑采用。
2.2高级氧化法
由于萃取工艺中的水相往往是高盐度溶液,如某企业萃余液中钴质量浓度在50g/L以上,所以不宜采用生化法处理。
化学降解法通过不同的方式使油相组分
发生氧化反应分解碳、氮氧化物,进而实现除油。
常用的高级氧化法有臭氧催化
氧化法、芬顿氧化法和电解氧化法。
臭氧催化氧化法是用臭氧作为氧化剂,使有
机物氧化,实现有机物降解;芬顿氧化法则采用Fe2+和H?0?作氧化剂,二者共
同作用降解有机物;电解氧化法则采用直流电作用于料液,通过阳极提供电子强
化有机物氧化反应过程,实现降解除油。
但是高级氧化法除油的设备成本和运行
成本都相对偏高。
2.3膜分离法
膜分离法是一种新兴的油水分离法,是利用膜的选择性实现除油。
常用的除
油膜按孔径大小可分为微滤膜、超滤膜、反渗透膜和纳滤膜等。
常用的膜材料包
括有机高分子材料、无机材料、有机无机复合材料。
按照膜表面性质可分为超疏
水超亲油膜和超疏油超亲水膜2类。
疏水亲油膜或亲水疏油膜都在除油过程中通
过膜材料对油和水的润湿性的不同而实现选择性透过。
膜的孔径大小决定了油的
处理效率和除油效果,微滤和超滤膜比较适合处理含油污水,这2种膜通常被制
作成中空纤维膜,有较好的除油效果。
膜处理法的优势在于不需向料液中添加试剂,不产生污泥,设备费用低。
为了优化除油效果防止膜污染,通常采用增加涂层、优化结构的方式改善膜性能。
目前,膜技术日渐成熟,但依然存在膜造价昂贵、寿命较短及处理量较小等
现实问题,料液通常需要经过预处理才能进人膜设备。
对于冶金萃取除油,通常
每批料液成分都有一定差别,对膜组件损耗较大;同时萃取过程中料液通常是高
盐度溶液,油相组成比较复杂,在除油过程中更容易发生膜污染甚至膜中毒;高
浓度金属盐更容易在膜表面结晶。
所以,膜除油技术在有色冶金萃取领域的应用
还有待进一步发展才能实现。
2.4吸附法
吸附法适用于处理废水中的微量油。
利用吸附材料的多孔结构和比表面积大
的特性,将废水中的油吸附在材料表面可以实现油水分离。
吸附剂有炭吸附剂、
无机吸附剂和有机吸附剂。
吸附材料通常要求吸油量大、吸水量小、吸油速度快,同时还要求能重复使用,压缩回弹性好。
目前,国内冶金企业常用的深度除油方
法是采用活性炭、粉煤灰、膨润土等易于获得、设备成本低廉的无机活性材料进
行吸附,这些传统材料虽然能达到良好的除油效果,但再生难度大,长期运行成
本高,同时会产生大量固体废弃物。
吸附法的优势在于不受料液限制,对于冶金料液的萃取除油,能较好地吸附
水中夹带的乳化油和溶解油。
其中复合材料吸附法因具有较好的反洗再生能力,
运行成本较低,具备替代目前工业中主流的活性炭吸附法的潜力,在料液除油方
面有广阔的应用前景。
2.5联合处理法
联合处理法是多种常用除油方法的有机结合,利用各种除油方法的优势实现
深度除油。
超声波破乳法与气浮除油法结合,可加快除油速度,有效提高乳化油
的去除效果。
将加压气浮法与波纹板油水分离法结合,可提高波纹板油水分离器
的油滴聚结效率。
生物处理与黏土吸附法结合,既能吸附油相又能实现降解。
对
于乳化油、溶解油含量高的水相,采用组合除油法,将沉淀除油兼气浮除油的竖
流式除油池、填充有亲油聚结材料的填料除油池、填充疏油材料的乳油分离池及
填充了改性有机膨润土药剂破乳的沉淀分离池相结合,可用于焦化废水的预处理。
对于硫酸镍除油,将树脂聚结、超声波破乳、气浮及活性炭纤维球吸附相组合,
能适应高盐体系料液深度除油。
对于高盐废水,采用电渗析和活性污泥相结合的
方式,先将废水脱盐再采用活性污泥可实现降解除油。
有色冶金萃取中水相夹带
的油相组分复杂,单一的除油方法无法兼顾深度除油和经济除油的目标,所以在
实际工业生产中,常需要多种技术联合使用。
3结束语
综上所述,有色冶金料液及废水中无论水相组分还是油相组分的构成都比较
复杂,因此,为了能够获得良好的除油效果,必须要加大湿法冶金工艺中相关除
油技术的研究力度,积极研发和引进先进的除油技术,同时也要对现行的物理除
油工艺进行优化改进,在工艺上采用联合处理方式,从而在提高除油效率及效果,实现除油成本的有效降低,最终促使我国冶金行业实现更加快速稳健的发展。
参考文献:
[1]高保军,丁叶民.萃取除油高效除油技术及应用[C].中国设备管理协
会.中国环保装备产业发展论坛论文集.宜兴,2011:223-228.
[2]李程,曾中贤.溶剂萃取工艺中水相除油方法[J].湿法冶金,2014,33(3):161-164.
[3]李秋红,娄世松,赵杉林,等.含油废水的除油技术研究[J].化工科技,2008,16(5),24 -28.。