切屑控制与断屑措施
车削加工中控制断屑的几种方法

车削加工中控制断屑的几种方法当加工产生连绵不断的带状切屑时,不仅容易划伤工件加工表面和损坏刀刃,严重时还会威胁到操作者的安全,所以采取必要的工艺措施,控制屑型和断屑一直是机械加工行业中极为重要的工艺问题。
由于切屑是切屑层变形的产物,所以,改变切削加工条件是改变切屑种类、实现断屑的有效途径,而影响切屑加工条件的因素主要包括工件材料、刀具几何角度及切屑用量等。
一般切屑需要满足以下几个基本条件:1、切屑不得缠绕在刀具、工件及其相邻的工具、装备上;2、切屑不得飞溅,以保证操作者与观察者的安全;3、精加工时,切屑不可划伤工件的已加工表面,影响已加工表面的质量;4、保证刀具预定的耐用度,不能过早磨损并竭力防止其破损;5、切屑流出时,不妨碍切削液的喷注;切屑不会划伤机床导轨或其他部件等。
一、切屑形状的分类由于塑性变形程度的不同,可能会产生不同种类的切屑,如图1所示。
加工塑性材料时,主要形成带状切屑、节状切屑或粒状切屑,加工脆性材料时,一般形成崩碎状切屑。
图11、带状切屑:带状切屑是一种连绵不断的,底面光滑,背面呈毛绒状的切屑,如图1—1a所示。
当采用较大前角的刀具,以较高的切削速度加工塑性金属材料时,容易产生这种切屑。
它是切削层不充分变形的产物。
产生带状切屑时,切削过程平稳,工件表面粗糙度较小,但切屑不易折断,往往引起缠绕,拉毛工件,甚至影响操作,所以不能忽视它的断屑问题。
2、节状切屑:节状切屑是一种底面光滑,背面有明显裂纹,且裂纹较深的切屑,如图1—1b所示。
当采用减小前角的刀具,以较低的切削速度加工塑性材料时,容易产生这种切屑。
它是切屑层较充分变形的产物,已达到了剪裂程度,产生节状切屑时,切屑工作不平稳,工件表面粗糙度较大。
3、粒状切屑:粒状切屑是一种均匀的颗粒状切屑,如图1—1c所示。
当采用小前角刀具,以很低的切削速度加工塑性金属材料时,容易产生这种切屑。
它是切削层充分变形的产物,达到了材料产生剪切破坏,使切屑沿厚度断裂的程度,产生粒状切屑时,切削工作不平稳,工件表面粗糙度较大。
金属切削中的切屑控制技术与策略

金属切削中的切屑控制技术与策略金属切削是制造业中常见的一项工艺,通过切削金属材料来制造零部件和构件。
然而,在这个过程中常常会产生切屑,对于切削加工的稳定性和效率产生负面影响。
因此,切屑控制技术与策略成为了一项重要的研究和应用领域。
切屑是在金属切削过程中由于金属材料在刀具作用下被切割而形成的长薄片,通常以螺旋形或弧形堆积。
它们不仅影响了表面质量和加工精度,还可能引起设备故障、刀具损坏及操作人员伤害等问题。
因此,切屑控制对于提高加工质量、延长设备寿命和保障操作安全具有重要意义。
首先,合理选用刀具材料、形状和涂层是切屑控制的关键。
切削加工过程中,刀具与工件的相互作用会产生高温和高压,不合适的刀具材料和形状会导致切削力过大,从而加剧切屑产生。
合适的刀具涂层能降低摩擦和热量的产生,减少切削力,改善切削过程,避免切削过程中的问题。
其次,良好的切削参数设置也能有效控制切屑的产生。
切削速度、进给速度和切削深度都对切屑形状和数量产生影响。
如果切削速度过高、进给速度过慢或切削深度过大,都会导致切削时金属材料断裂过早,产生大量切屑。
因此,合理设定切削参数是实现切屑控制的重要策略之一。
另外,使用切屑控制装置也是一种有效的方式。
切屑控制装置可以帮助收集和控制切屑的产生,减少切削床上的切屑堆积。
例如,切屑槽、滚花刀具和专用切屑收集设备等,都能够有效收集切屑,并降低对加工过程的干扰。
这些装置可以根据金属切削的特性和需求进行选择和应用,从而实现切屑的有效控制。
此外,定期清理切屑也是重要的措施。
切削过程中产生的切屑若长时间堆积在设备和加工区域,会影响切削加工的稳定性和效率。
因此,操作人员应定期清理切屑,保持工作区域的清洁和整洁,以减少切屑带来的不利影响。
综上所述,金属切削中的切屑控制技术与策略对于提高加工质量、延长设备寿命和保障操作安全具有重要意义。
合理选用刀具材料、形状和涂层,设定合适的切削参数,使用切屑控制装置,以及定期清理切屑,都是实现切屑控制的有效手段。
铰孔加工中的切屑控制
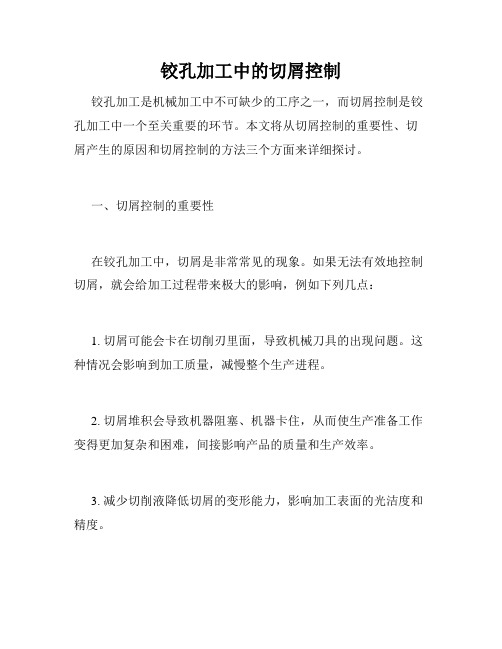
铰孔加工中的切屑控制铰孔加工是机械加工中不可缺少的工序之一,而切屑控制是铰孔加工中一个至关重要的环节。
本文将从切屑控制的重要性、切屑产生的原因和切屑控制的方法三个方面来详细探讨。
一、切屑控制的重要性在铰孔加工中,切屑是非常常见的现象。
如果无法有效地控制切屑,就会给加工过程带来极大的影响,例如下列几点:1. 切屑可能会卡在切削刃里面,导致机械刀具的出现问题。
这种情况会影响到加工质量,减慢整个生产进程。
2. 切屑堆积会导致机器阻塞、机器卡住,从而使生产准备工作变得更加复杂和困难,间接影响产品的质量和生产效率。
3. 减少切削液降低切屑的变形能力,影响加工表面的光洁度和精度。
综上所述,切屑的控制对于铰孔加工质量的影响非常明显,因此要尽可能采取有效措施进行控制。
二、切屑产生的原因为什么切屑会产生呢?产生切屑的原因有很多,可以总结为如下几点:1. 切削过程中热流的存在,增加了切削力,导致切屑变形。
(切屑束在离开刀具之前的热变形)。
2. 材料的硬度过高,使得废屑形成较难。
3. 刀具形状不当,切入场合不合理,或者是刀具钝化等问题都会导致切屑过多积累。
4. 切削过程中的振动也会对切屑的产生起到举足轻重的作用。
5. 切削液对切削力的降低效果不理想。
如何控制切屑?从上面的分析我们可以看出,切屑的产生是由很多因素造成的。
因此,我们需要从下列几点入手来有效地控制切屑。
1. 优化刀具结构和刀具形状,减少切削力,从而减少切屑的产生。
2. 选用合适的切削液,降低热力金属屑的变形率,从而减轻切削力,降低生产环境中的切屑产生。
3. 材料硬度较高的时候,可以采用预切削的方法,减少铰孔加工的难度,降低切削力。
4. 对于废料变形难的材料,可以采取切断点滑动的方式,使切削受力更加均匀,减轻切屑的压力。
5. 在加工中,适量增加切削液的润滑效果,有助于降低热力起伏,提高切屑的控制效率。
6. 铰孔加工时注意刀具与加工表面级别的统一,减少切削力,控制切屑产生。
切屑控制与断屑措施
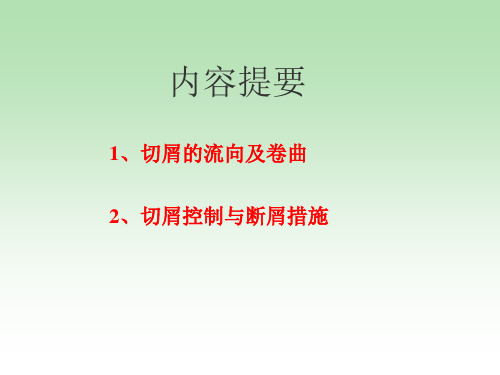
① 带状切屑:切塑性金属,Vc较高、 较小、γo较大时 ② 挤裂切屑:切塑性金属,Vc较低、 ③ 单元状切屑:切塑性金属,Vc低、 ④ 崩碎状:切脆性金属时 较大、γo较小时 大、γo小时
屑形细分
(2)断屑措施: ① 在刀具前刀面上磨断屑槽或安装断屑台 槽形:a) 折线形 b) 直线园弧形 c) 全圆弧形
槽向:a) 外斜式→粗加工 b) 平行式→粗加工 c) 内斜式→半精、精加工
(2)断屑措施: ② 改变切削用量:提高f、适当降低Vc
③ 改变刀具角度: ↑Kr、↓γ
设刃倾角改变切屑流向 ④ 适当提高工件材料的脆性→↓εb λs>0 → 切屑流向刀杆、切屑碰后刀面 λs<0 → 切屑流向已加工面 ⑤ 采用振动切削装置
内容提要
1、切屑的流向及卷曲
2、切屑控制与断屑措施
切屑的控制
1、切屑的流向及卷曲
(1)流向
-λs使切屑流向已加工表面 +λs使切屑流向已加工表面
1、切屑的流向及卷曲
(2)卷曲与折断机理: 流经前刀面时的摩擦、滞 留使切屑底层拉长 碰到障碍是受到附加弯曲 力矩作用 断屑的原因:τmax>σb
2、切屑控制与断屑措施
关于 钻孔时的切屑控制

钻孔时的切屑控制
转速与进给对切屑的影响
当切屑能够从钻头中顺畅排出时,切屑形成是可以接受的。
对其进行识别的最佳方法是在钻削过程中进行监听。
连续的声音表示排屑良好,断续的声音表示切屑堵塞。
检查进给力或功率监视器。
如果存在异常,则原因可能是切屑堵塞。
查看切屑。
如果切屑长而弯曲,但未卷曲,则表示出现切屑堵塞。
查看孔,如果出现切屑堵塞,则将看到不平整表面。
优秀切屑
良好切屑
异常切屑(堵塞危险)
客户处常见的寿命判断标准为了避免切屑堵塞:
·确保使用正确的切削参数和钻头/刀尖槽形
·检查切屑形状- 调整进给量和速度
进入工件时产生的开始时的切屑总是很长,并不会造成任何问题
可转位刀片钻头(U钻)
中心刀片形成容易识别的锥形切屑。
周边刀片形成类似于车削时形成的切屑
外冷
外冷可在切屑形成良好以及孔深较浅时使用。
由于切削刃温度较高,外冷却液的使用可帮助防止积屑瘤的形成。
切屑的防护和处理范本

切屑的防护和处理范本切屑是在加工过程中产生的金属碎片或碎屑,如果没有正确进行防护和处理,会对机器操作者的安全造成威胁,并且容易导致设备故障。
因此,切屑的防护和处理是非常重要的。
下面将介绍切屑的防护和处理范本。
一、设备的切屑防护1. 安装合适的切屑防护罩:在进行切削、铣削、钻孔等加工时,应该使用合适的切屑防护罩来覆盖机器的切削区域,从而防止切屑溅射。
2. 定期清理废料:对于机床等设备,在加工过程中会产生大量的废料和切屑,必须定期进行清理,以防止积累和堵塞机器。
二、操作者的切屑防护1. 穿戴个人防护装备:操作者在进行加工作业时,应该穿戴个人防护装备,包括防护眼镜、防护手套、防护面罩等,以减少切屑对身体的伤害。
2. 注意站姿和姿势:操作者应该正确站立和采取正确的姿势,保持身体平衡,并尽量做到远离切削区域,以防止切屑溅射到自己身上。
3. 维护和保养工具:操作者在进行加工作业前,应该对工具进行维护和保养,确保工具的切削刃锋利,减少切屑的溅射。
三、切屑的处理1. 使用合适的容器:在清理切屑时,应该使用合适的容器进行收集,以防止切屑飞溅或散落。
2. 定期清理切屑:切屑会堵塞设备和导致设备故障,因此要定期清理切屑,保持设备的正常运转。
3. 将切屑处理为废料:切屑是金属材料的副产品,可以将其处理为废料,以便进行再利用或者妥善处置。
切屑可被送至回收站或经专门处理设备处理。
4. 确保切屑安全处理:在处理切屑时,应该注意安全,避免手部和身体受伤。
使用适当的工具和装备,例如长柄铲子、铲斗等,以防止直接接触切屑。
5. 防止切屑散落:处理后的切屑需要妥善堆放和封存,防止其散落和引发其他安全隐患。
总结:切屑的防护和处理是保障操作者安全和设备正常运转的重要环节。
使用切屑防护罩、穿戴个人防护装备,定期清理废料,注意站姿和姿势,维护和保养工具等都是有效的切屑防护措施。
同时,合理选择容器收集切屑,并定期清理和处理切屑,以保持设备的正常运转。
切屑控制与断屑措施
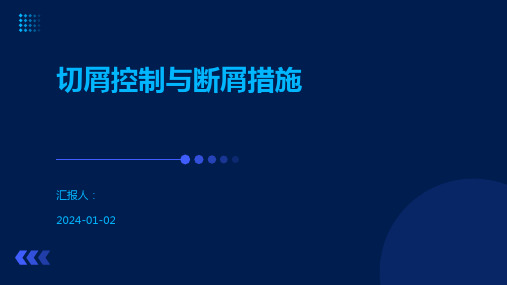
切削液使用中的问题
总结词
切削液在切削加工中起到冷却、润滑和清洗的作用,但在使用过程中也可能出 现泡沫、异味和腐蚀等问题。
详细描述
切削液在使用过程中可能会产生泡沫,影响冷却和润滑效果,同时也会带来异 味和腐蚀等问题。为解决这些问题,可以采取添加消泡剂、更换切削液或加强 切削液管理等措施。
05
未来研究方向与展望
THANKS
谢谢您的观看
选择合适的切削液对于切屑控 制至关重要,应根据加工材料 和刀具材料选择合适的决方案
切屑缠绕问题
总结词
切屑缠绕是切削加工中常见的问题,它可能导致设备损坏、生产效率降低和安全 隐患。
详细描述
切屑缠绕通常发生在铣削、车削和钻孔等加工过程中,当切屑不能及时排出或断 屑不彻底时,切屑会缠绕在刀具或工件上,影响加工质量和效率。为解决这一问 题,可以采取调整切削参数、更换刀具或优化切削液等方式。
02
切削过程中,切削力、切削热和 切削振动等多种因素相互作用, 影响切屑的形成。
切屑的类型
根据切屑的形状和形成机理,切屑可分 为带状屑、节状屑、崩碎屑和锯齿状屑 等类型。
锯齿状屑是由于切削刃上的切削力周期 性变化而形成的,其断面呈锯齿状,容 易产生振动和噪音。
崩碎屑是由于切削刃上的切削力突然变 化而形成的,其断面呈崩碎状,容易飞 溅伤人。
新型切削液的开发与研究
总结词
随着工业技术的不断发展,对切削液的性能要求也越来越高。未来研究将更加注重切削液的环保性、高效性和低 成本化,开发出新型的切削液以满足不断变化的市场需求。
详细描述
新型切削液的开发与研究将注重提高切削液的润滑性、冷却性和防锈性,以减少切削过程中的摩擦和热量,提高 切削效率和刀具寿命。同时,研究将探索切削液的生物降解性和低毒性能,以降低对环境的污染和危害。
金属切削中的切屑处理与管理方案

金属切削中的切屑处理与管理方案在机械加工过程中,金属切削是一种常见且重要的加工方法。
然而,金属切削过程中产生的切屑处理与管理成为了一个值得重视的问题。
合理的切屑处理与管理方案可以提高生产效率,减少能源浪费,且对环境保护也具有重要意义。
金属切削过程中产生的切屑主要包括连续切屑、螺旋切屑和碎裂切屑。
这些切屑的特性和数量与切削过程中的材料、切削速度、刀具状况等因素密切相关。
因此,切削过程中的切屑处理与管理需要根据不同的情况制定合适的方案。
首先,切削过程中的切屑处理应该进行及时清理。
及时清理切削产生的切屑可以保持工作环境的清洁与卫生,避免切削刀具因为积屑而损坏。
对于连续切屑和螺旋切屑,可以设置专门的切屑槽或切屑收集装置,在切削过程中将切屑直接引导至切屑槽中进行集中管理。
对于碎裂切屑和小颗粒切屑,可以采用切削油膜、水冷却等辅助手段,将切屑固定在切削液或切削液中形成悬浮液,然后通过切削液循环系统进行处理与过滤。
其次,切屑处理与管理方案还应注重资源利用。
金属切屑中含有大量的金属资源,如果直接丢弃,不仅造成了资源的浪费,还给环境带来了污染。
因此,切削中的切屑可以通过回收、再利用等方式得到合理利用。
例如,可以对切屑进行磁选、洗涤等处理,分离出切屑中的金属物质,然后通过回收再加工,利用于其他生产过程中。
这种方式不仅可以减少资源消耗和环境污染,还可以实现资源的循环利用。
同时,切屑处理与管理方案还需要考虑安全因素。
金属切削过程中产生的切屑往往具有高速旋转的趋势,并且会与刀具生产的高温碰撞,因此切屑会产生较高的温度和动能,并且可能对人员和设备造成伤害。
因此,在制定切屑处理与管理方案时,应考虑安全防护措施,如设置切屑防护罩、切屑收集装置等。
同时,也应加强对切屑清理与管理操作的培训,提高员工的安全意识和操作能力。
最后,切屑处理与管理方案还应考虑环境保护的因素。
金属切削过程中产生的切屑中可能含有有害物质,如重金属元素等,如果不妥善处理,可能会对环境造成污染。
- 1、下载文档前请自行甄别文档内容的完整性,平台不提供额外的编辑、内容补充、找答案等附加服务。
- 2、"仅部分预览"的文档,不可在线预览部分如存在完整性等问题,可反馈申请退款(可完整预览的文档不适用该条件!)。
- 3、如文档侵犯您的权益,请联系客服反馈,我们会尽快为您处理(人工客服工作时间:9:00-18:30)。
第四章
切削基本理论的应用
Schneider Electric
- ISC Marketing - 1/2010
1
第一节 切屑控制
切削过程中切屑不能折断而引起 切屑的失控,会影响操作者安全及机 床正常工作,导致刀具损坏、降低加 工表面质量,尤其在数控、自动化 生产中,应控制切屑确保自动化加 工循环的正常进行和实现切屑的无 人化处理。
4
切屑形状分析
●C、6形切屑50mm以下短螺旋 切屑最好; ●短锥管状切屑、平盘旋状切屑、 短锥螺旋状切屑、单元切屑等为可 以接受切屑; ●长带状切屑不好; ●缠乱切屑最差。
Schneider Electric
- ISC Marketing - 1/2010
5
二. 切屑的流向和折断
1、切屑的流向
3. 脆性金属(铸铁、高碳钢、 硬铝、石材、玻璃)
Schneider Electric
- ISC Marketing - 1/2010
21
本章重点
●切屑类型 ●切屑流向和折断 ●断屑措施
Schneider Electric
- ISC Marketing - 1/2010
22
本节练习
● 复习思考题 P90:第1、2、3
3. ac很大; 4. γ0小。
Schneider Electric
- ISC Marketing - 1/2010
20
4. 崩碎切屑
切屑 1. 不规则的碎块 形貌
产生 1. 靠近切削刃的局部金属塑性
原因
变形很小,被挤裂、脆断。
特点
产生 条件
ቤተ መጻሕፍቲ ባይዱ
1. 切削力波动很大,切削过程 很不平稳;
2. 已加工表面粗糙度很大; 刀具易崩刃。
- ISC Marketing - 1/2010
19
3. 单元切屑
切屑 1. 裂纹贯穿整个切屑; 形貌 2. 切屑为梯形单元。
产生 1. 整个剪切面的剪应力超过
原因
材料极限强度。
特点 1. 切削力波动大,切削过程 不平稳;
2. 已加工表面粗糙度大; 3. 刀具易损坏。
产生 1. 塑性金属; 条件 2. v很小;
1. 剪切位移未达到破裂程度,
2. 剪应力未超过材料极限强度
1.切削力波动小,切削过程平稳; 2.已加工表面粗糙度小; 3.需要断屑措施。
1. 塑性金属; 2. v较高; 3. ac较小; 4. γ0较大。
Schneider Electric
- ISC Marketing - 1/2010
18
2. 挤裂切屑
副切削刃B点 参与切削终 点
主切 削刃A
点参 与切 削终 点
Schneider Electric
- ISC Marketing - 1/2010
6
刃倾角对切屑流向的影 ●刃倾角响对切屑流向的影响刃倾角-λ s
●Κr ,Κr =90 ;-γ0 ; ●切屑易流向已加工表面
Schneider Electric
Schneider Electric
- ISC Marketing - 1/2010
2
主要内容
●切屑形状的分类 ●切屑流向和折断 ●断屑措施
Schneider Electric
- ISC Marketing - 1/2010
3
一、切屑形状的分类
Schneider Electric
- ISC Marketing - 1/2010
- ISC Marketing - 1/2010
14
2.改变切削用量
●f , 断屑,影响较大(aC影 响), ●ap,f 时有效, ●v的影响较小, v 时容易断屑。
Schneider Electric
- ISC Marketing - 1/2010
15
3. 其它断屑方法
●固定附近断屑挡块; ●采用间断切削; ●切削刃上开分屑槽
11
研究可知:增加切屑厚度,减小切屑卷曲半 径,切屑材料的极限应变值小,切屑易折断。
●减小断屑槽宽; ●增加断屑台高; ●增长刀——屑接触长度; 有利于断屑
Schneider Electric
- ISC Marketing - 1/2010
12
三. 断屑措施 1、作出断屑槽
a),b)加工碳钢、合金钢、工具钢和不锈钢; c)加工塑性更高的材料
- ISC Marketing - 1/2010
7
2.切屑的折断
● 切屑的卷曲是切屑 基本变形或经过卷屑 槽使之产生附加变形 的结果
Schneider Electric
- ISC Marketing - 1/2010
8
2. 第二变形区(前刀面摩擦区)
● 断屑是对已变形 的切屑再附加一次 变形
Schneider Electric
Schneider Electric
- ISC Marketing - 1/2010
- ISC Marketing - 1/2010
9
示例:切屑卷曲
● 刀具加工工件时 产生的切屑被卷曲 的情况
Schneider Electric
- ISC Marketing - 1/2010
10
示例:切屑卷曲
● 刀具切削工件 时产生断屑的 情况
Schneider Electric
- ISC Marketing - 1/2010
切屑形 1. 内表面有时光滑有时有裂纹;
貌
2. 外表面锯齿状。
产生原 1. 局部剪切位移达到破裂程度,
因
2. 剪应力超过材料极限强度。
特点
1. 切削力有波动,切削过程较不平稳; 2. 已加工表面粗糙度较大。
产生条 件
1. 塑性金属; 2 v较低; 3. ac较大; 4. γ0较小
Schneider Electric
Schneider Electric
- ISC Marketing - 1/2010
16
切屑种类和变化
Schneider Electric
- ISC Marketing - 1/2010
17
1. 带状切屑
切屑 形貌
产生 原因 特点
产生 条件
1. 内表面光滑; 2. 外表面毛茸状; 3. 连续、带状。
Schneider Electric
- ISC Marketing - 1/2010
13
断屑槽位置及刃倾角作用
●外倾式刃倾角-λ s,断屑范围广,粗加工;
●平行式刃倾角λ s =0,碰到切削表面折断,
用于粗加工、半精加工;
●内倾式刃倾角+λ s,半精加工、精加工。
Schneider Electric