利用垂直分型技术生产高品质球墨铸铁件[1]
铸造用高纯生铁的定标及生产要义

铸造用高纯生铁的定标及生产要义钱立;刘武成【摘要】简要介绍了铸造用高纯生铁的定标及生产要义.对球墨铸铁件和高牌号灰铸铁件使用的生铁作了说明.在铸造用高纯生铁的研发和生产中具有一定的指导意义.【期刊名称】《铸造设备与工艺》【年(卷),期】2010(000)005【总页数】4页(P37-39,58)【关键词】铸造高纯生铁;生产技术;质量管理【作者】钱立;刘武成【作者单位】河北工业大学,天津300130;河北龙凤山铸业有限公司,河北武安056300【正文语种】中文【中图分类】TG143我国铸件产量已连续十年居世界之首,但铸件在质量和稳定性方面与工业发达国家还有较大差距。
生铁是铸造业的粮食,是装备制造业发展的基础性保障原料。
铸铁件品质的提高,在相当程度上有赖于生铁的品质。
我国现有《球墨铸铁用生铁》、《铸造生铁》、《炼钢用生铁》、《含钒生铁》和《铸造用磷铜钛低合金耐磨生铁》等五个标准。
球墨铸铁件和高牌号灰铸铁件,主要使用GB/T1412-2005《球墨铸铁用生铁》和GB/T718-2005《铸造生铁》,间或使用YB/T5296-2006《炼钢用生铁》。
随着我国装备制造业的快速发展,现有生铁已不能满足高端铸铁件的需要,亟须开发生铁的升级新品种。
近年来,在辽宁、河北、河南、山西和山东,涌现出了一批优势生铁企业,他们生产低Ti和低P生铁、风电铸件用生铁、“高化”生铁等等。
不过,这些生铁只限于个别品种,并未升华为企业标准,并未在有关质量主管局例行标准审定、备案等程序。
而且在定义和技术要求等方面亦尚不够完备。
河北龙凤山铸业有限公司,装备、人才和管理条件较好,走了一条由优质铸造生铁,而风电铸件用生铁,而铸造用高纯生铁的技术进步之路。
现就《铸造用高纯生铁》研发过程中有关该生铁定标和生产要义简述于后。
生铁是以Si含量确定牌号的。
为了适应低温工作铁素体球墨铸铁件、大件,以及大孕育量等的需要,特设了05和08两个牌号,共有05、08、10和12四个牌号。
科技成果——高韧性耐低温球墨铸铁生产技术
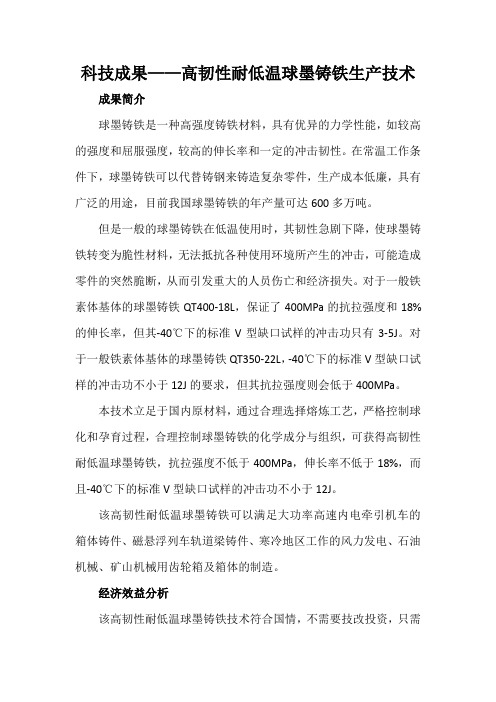
科技成果——高韧性耐低温球墨铸铁生产技术成果简介
球墨铸铁是一种高强度铸铁材料,具有优异的力学性能,如较高的强度和屈服强度,较高的伸长率和一定的冲击韧性。
在常温工作条件下,球墨铸铁可以代替铸钢来铸造复杂零件,生产成本低廉,具有广泛的用途,目前我国球墨铸铁的年产量可达600多万吨。
但是一般的球墨铸铁在低温使用时,其韧性急剧下降,使球墨铸铁转变为脆性材料,无法抵抗各种使用环境所产生的冲击,可能造成零件的突然脆断,从而引发重大的人员伤亡和经济损失。
对于一般铁素体基体的球墨铸铁QT400-18L,保证了400MPa的抗拉强度和18%的伸长率,但其-40℃下的标准V型缺口试样的冲击功只有3-5J。
对于一般铁素体基体的球墨铸铁QT350-22L,-40℃下的标准V型缺口试样的冲击功不小于12J的要求,但其抗拉强度则会低于400MPa。
本技术立足于国内原材料,通过合理选择熔炼工艺,严格控制球化和孕育过程,合理控制球墨铸铁的化学成分与组织,可获得高韧性耐低温球墨铸铁,抗拉强度不低于400MPa,伸长率不低于18%,而且-40℃下的标准V型缺口试样的冲击功不小于12J。
该高韧性耐低温球墨铸铁可以满足大功率高速内电牵引机车的箱体铸件、磁悬浮列车轨道梁铸件、寒冷地区工作的风力发电、石油机械、矿山机械用齿轮箱及箱体的制造。
经济效益分析
该高韧性耐低温球墨铸铁技术符合国情,不需要技改投资,只需
要适当改变现有生产工艺,能在较短时间内取得预期的效果,生产出符合技术指标的高韧性耐低温球墨铸铁件,可取得很好的经济效益,为提高制造企业档次、产品更新换代提供坚实的技术基础。
合作方式
以技术转让费或技术入股的方式进行合作,具体项目签订相应的合同。
铸造技术的发展历程
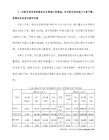
来源:机械专家网 发布时间:2007-01-20
铸造是人类掌握比较早的一种金属热加工工艺,已有约6000年的历史。中国约在公元前1700~前1000年之间已进入青铜铸件的全盛期,工艺上已达到相当高的水平。中国商朝的重875公斤的司母戊方鼎,战国时期的曾侯乙尊盘,西汉的透光镜,都是古代铸造的代表产品。早期的铸件大多是农业生产、宗教、生活等方面的工具或用具,艺术色彩浓厚。那时的铸造工艺是与制陶工艺并行发展的,受陶器的影响很大。中国在公元前513年,铸出了世界上最早见于文字记载的铸铁件晋国铸型鼎,重约270公斤。欧洲在公元八世纪前后也开始生产铸铁件。铸铁件的出现,扩大了铸件的应用范围。例如在15~17世纪,德、法等国先后敷设了不少向居民供饮用水的铸铁管道。18世纪的工业革命以后,蒸汽机、纺织机和铁路等工业兴起,铸件进入为大工业服务的新时期,铸造技术开始有了大的发展。
不同的铸造方法有不同的铸型准备内容。以应用最广泛的砂型铸造为例,铸型准备包括造型材料准备和造型造芯两大项工作。砂型铸造中用来造型造芯的各种原材料,如铸造砂、型砂粘结剂和其他辅料,以及由它们配制成的型砂、芯砂、涂料等统称为造型材料造型材料准备的任务是按照铸件的要求、金属的性质,选择合适的原砂、粘结剂和辅料,然后按一定的比例把它们混合成具有一定性能的型砂和芯砂。常用的混砂设备有碾轮式混砂机、逆流式混砂机和叶片沟槽式混砂机。后者是专为混合化学自硬砂设计的,连续混合,速度快。
铸造工厂如何才能具有先进技术水平(1)
来源:机械专家网 发布时间:2007-04-28
Vulcan Engineering, Mount, Peter E, Macler Assoc 等三公司,对高科技铸造工厂应是什么样的状态有新考虑,对制芯、造型、熔化、浇注以及清理精整等工序都有设想,现摘要加以介绍。
金属型铸造与砂型铸造的比较

金属型铸造与砂型铸造比较:在技术上与经济上有许多优点。
(1)金属型生产的铸件,其机械性能比砂型铸件高。
同样合金,其抗拉强度平均可提高约25%,屈服强度平均提高约20%,其抗蚀性能和硬度亦显著提高;(2)铸件的精度和表面光洁度比砂型铸件高,而且质量和尺寸稳定;(3)铸件的工艺收得率高,液体金属耗量减少,一般可节约15~30%;(4)不用砂或者少用砂,一般可节约造型材料80~100%;此外,金属型铸造的生产效率高;使铸件产生缺陷的原因减少;工序简单,易实现机械化和自动化。
金属型铸造虽有很多优点,但也有不足之处。
如:(1) 金属型制造成本高;(2) 金属型不透气,而且无退让性,易造成铸件浇不足、开裂或铸铁件白口等缺陷;(3) 金属型铸造时,铸型的工作温度、合金的浇注温度和浇注速度,铸件在铸型中停留的时间,以及所用的涂料等,对铸件的质量的影响甚为敏感,需要严格控制。
因此,在决定采用金属型铸造时,必须综合考虑下列各因素:铸件形状和重量大小必须合适;要有足够的批量;完成生产任务的期限许可。
编辑本段金属型铸件形成过程的特点金属型和砂型,在性能上有显著的区别,如砂型有透气性,而金属型则没有;砂型的导热性差,金属型的导热性很好,砂型有退让性,而金属型没有等。
金属型的这些特点决定了它在铸件形成过程中有自己的规律。
型腔内气体状态变化对铸件成型的影响:金属在充填时,型腔内的气体必须迅速排出,但金属又无透气性,只要对工艺稍加疏忽,就会给铸件的质量带来不良影响。
铸件凝固过程中热交换的特点:金属液一旦进入型腔,就把热量传给金属型壁。
液体金属通过型壁散失热量,进行凝固并产生收缩,而型壁在获得热量,升高温度的同时产生膨胀,结果在铸件与型壁之间形成了“间隙”。
在“铸件一间隙一金属型”系统未到达同一温度之前,可以把铸件视为在“间隙”中冷却,而金属型壁则通过“间隙”被加热。
金属型阻碍收缩对铸件的影响:金属型或金属型芯,在铸件凝固过程中无退让性,阻碍铸件收缩,这是它的又一特点。
铸态低温高韧性球墨铸铁件生产,三要素不可缺
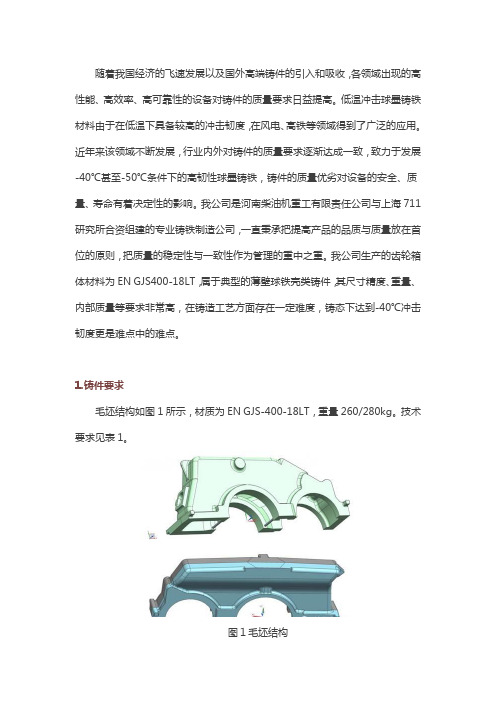
随着我国经济的飞速发展以及国外高端铸件的引入和吸收,各领域出现的高性能、高效率、高可靠性的设备对铸件的质量要求日益提高。
低温冲击球墨铸铁材料由于在低温下具备较高的冲击韧度,在风电、高铁等领域得到了广泛的应用。
近年来该领域不断发展,行业内外对铸件的质量要求逐渐达成一致,致力于发展-40℃甚至-50℃条件下的高韧性球墨铸铁,铸件的质量优劣对设备的安全、质量、寿命有着决定性的影响。
我公司是河南柴油机重工有限责任公司与上海711研究所合资组建的专业铸铁制造公司,一直秉承把提高产品的品质与质量放在首位的原则,把质量的稳定性与一致性作为管理的重中之重。
我公司生产的齿轮箱体材料为EN GJS400-18LT,属于典型的薄壁球铁壳类铸件,其尺寸精度、重量、内部质量等要求非常高,在铸造工艺方面存在一定难度,铸态下达到-40℃冲击韧度更是难点中的难点。
1.铸件要求毛坯结构如图1所示,材质为EN GJS-400-18LT,重量260/280kg。
技术要求见表1。
图1毛坯结构表1 铸件技术要求2.影响因素低温环境下服役的球墨铸铁的韧性受生产过程中很多因素的影响,包括其化学成分、铸造工艺、熔炼、球化、孕育处理工艺及热处理制度等,这些因素决定了铸件最终的组织和力学性能。
(1)球墨铸铁组织对冲击韧度的影响实际生产应用中,在碳含量一定的情况下,球化率和石墨球数对冲击性能影响显著,其关系如图2、图3所示。
同时,圆整的石墨球可以改善球墨铸铁的冲击韧度,而石墨体积分数增加或石墨球数增多均可使脆性转变温度下降,并提高上限冲击吸收能量。
因此,在实际生产中必须严格控制球化处理和孕育工艺,要控制原材料(生铁、废钢、回炉料等)中的微量元素含量,特别是要限制反球化及干扰元素的含量。
图4 显示球墨铸铁的基体组织对其冲击性能有明显的影响。
由图4 可知,随着珠光体体积分数的增加,冲击性能降低,因此要保证低温高韧性球墨铸铁为全铁素体基体。
(2)球墨铸铁化学成分对冲击韧度的影响在工艺条件一定的情况下,球墨铸铁的化学成分对组织及会产生决定性的作用,从而决定其性能。
合工大材料成型技术基础复习知识点(全面)[1]
![合工大材料成型技术基础复习知识点(全面)[1]](https://img.taocdn.com/s3/m/b1ad87e20740be1e640e9a88.png)
合工大材料成型技术基础复习知识点(全面)(word版可编辑修改)编辑整理:尊敬的读者朋友们:这里是精品文档编辑中心,本文档内容是由我和我的同事精心编辑整理后发布的,发布之前我们对文中内容进行仔细校对,但是难免会有疏漏的地方,但是任然希望(合工大材料成型技术基础复习知识点(全面)(word版可编辑修改))的内容能够给您的工作和学习带来便利。
同时也真诚的希望收到您的建议和反馈,这将是我们进步的源泉,前进的动力。
本文可编辑可修改,如果觉得对您有帮助请收藏以便随时查阅,最后祝您生活愉快业绩进步,以下为合工大材料成型技术基础复习知识点(全面)(word版可编辑修改)的全部内容。
材料成型技术基础第二章铸造一、铸造的定义、优点、缺点:铸造指熔融金属、制造铸型并将熔融金属浇入铸型凝固后,获得具有一定形状、尺寸和性能的金属零件或毛坯的成型方法.优点:铸造的工艺适应性强,铸件的结构形状和尺寸几乎不受限制;工业上常用的合金几乎都能铸造;铸造原材料来源广泛,价格低廉,设备投资少;铸造适于制造形状复杂、特别是内腔形状复杂的零件或毛坯,尤其是要求承压、抗振或耐磨的零件.缺点:铸件的质量取决于成形工艺、铸型材料、合金的熔炼与浇注等诸多因素,易出现浇不到、缩孔、气孔、裂纹等缺陷,且往往组织疏松,晶粒粗大。
二、充型能力的定义、影响它的三个因素:金属液的充型能力指金属液充满铸型型腔,获得轮廓清晰、形状准确的铸件的能力.影响因素:①金属的流动性;②铸型条件;③浇注条件。
三、影响流动性的因素;纯金属和共晶成分合金呈逐层凝固流动性最好;影响充型能力的铸型的三个条件;浇注温度和压力对充型能力是如何影响的:影响流动性的因素:①合金成分:纯金属和共晶成分的合金,结晶过程呈逐层凝固方式,流动性好;非共晶成分的合金,呈中间凝固方式,流动性较差;凝固温度范围过大,铸件断面呈糊状凝固方式,流动性最差。
结晶温度范围越窄,合金流动性越好。
②合金的质量热容、密度和热导率:合金质量热容和密度越大、热导率越小,流动性越好.影响充型能力的铸型的三个条件:①铸型的蓄热系数:铸型从其中金属液吸收并储存热量的能力.蓄热系数越大,金属液保持液态时间短,充型能力越低。
垂直分型射压造型线型砂质量控制及生产应用

垂直分型射压造型线型砂质量控制及生产应用在粘土砂铸造生产过程中,型砂是关键,其性能控制得好与坏,质量稳定与否,将对铸件质量产生巨大的影响。
我公司的造型线为ZZ416垂直分型射压造型线,铁液采用中频电炉熔炼,铸件以薄壁铸铁(灰铸铁和球墨铸铁)件为主,产品包括汽车零配件、管道件、阀门件等。
我公司经过多年生产实践,在型砂质量控制方面做了大量工作,并取得了良好效果。
1原材料质量要求1.1原砂选用河北围场擦洗砂,含泥量<1.0%,SiO2>85%,原砂粒度70/140目。
由于垂直分型射压造型属高密度造型,为减少砂型受热膨胀,避免因砂粒受挤压从砂型表面脱落而引起铸造缺陷,粒度要求不宜过于集中,原砂最好采用4筛集中率85%以上,主峰筛(100目)量控制在40%以内。
新砂补加量在5%以下。
1.2煤粉煤粉灰份应<10%,煤粉含灰量过高,使得型砂含泥量增加,影响型砂使用性能。
含硫量≤1.5%;煤粉粒度≥95%以上的颗粒通过140目筛,并且煤粉不允许有大颗粒存在,因其在浇注过程中遇金属液燃烧时间长,阻止铁液靠近型壁,待铁液凝固后,便会造成铸件表面凹坑,影响铸件表面粗糙度。
挥发分的高低是衡量煤粉质量好坏的主要指标之一,好的煤粉挥发分含量较高,浇注时,型腔内易形成还原性气体,析出大量的光亮碳,提高铸件的外观质量。
但挥发分超过40%,型砂发气量增大,铸件易产生气孔、浇不足等缺陷。
因此,挥发分一般在30%-38%。
1.3膨润土选用钠基膨润土。
湿压强度≥120kPa,吸蓝量(g/100g)≥38,粒度过200目≥90%。
2型砂性能质量控制2.1湿压强度如果型砂湿态强度不足,在起模、搬运砂型、下芯、合型等过程中,砂型有可能破损和塌落;浇注时砂型承受不住金属液的冲刷和冲击造成砂孔缺陷,甚至铁液泄漏。
一般用湿压强度来表示型砂湿态强度,一般控制在150-200kPa。
2.2透气性型砂的透气率不可太低以免浇注过程中发生呛火和铸件产生气孔缺陷,但绝不能理解为型砂透气率越高越好。
高韧性球墨铸铁QT400_18AL的生产

1 前言
我公司生产的箱体铸件 ,要求牌号为 QT 400 18AL ,重量达 2 850 kg ,壁厚在 40~100 mm ,属中厚断 面球墨铸铁 。高韧性球墨铸铁在生产薄壁小件时 ,还 较容易控制 ,但在生产中厚断面时 ,就会出现低温冲 击韧度达不到要求 。这是因为生产铁素体球墨铸铁 , 对碳 、硅含量要求较高 。硅高 ,提高了低温脆性 ,降低 冲击韧度 ;碳高 ,则产容易产生石墨漂浮 、碎块状石墨 等铸造缺陷 。同时 ,锰和磷也对其低温冲击韧性有直 接影响[1] 。所以生产中如何控制其化学成分和组织 是生产 QT400 - 18AL 的关键 。
参考文献 1 陶令桓 等. 铸造手册 (铸铁) [M] . 北京 :机械工业出版社 ,
1993. P335.
ቤተ መጻሕፍቲ ባይዱ
纺织机械 2005 年第 2 期 ·行业动态· 55
强度大于 450 MPa ,伸长率大于 19 %(见表 1) ,做常温 冲击韧度试验 ,试验数值 (见表 2) ,达不到常温时的冲 击韧度要求 。
图 1 QT400218 金相组织
22. 1
19. 6
21. 3
表 2 铸态常温时的冲击韧度
试样编号
1
2
3
冲击韧度/ J ·cm- 2 6. 0
6. 5
7. 0
5 热处理工艺
由于达不到冲击韧度要求 ,说明铸态基体中铁素 体含量达不到要求 ,组织中存在降低冲击韧度的碳化 物及其他组织 ,故采用退火处理 ,其热处理工艺如图 3。
图3
原铁液化学成分 (WB %) 控制在 :3. 5 %~3. 8 % , 1. 2~1. 4Si ,Mn < 0. 4 , P < 0. 06 ,S < 0. 05 以下 。出炉 温度控制在 1 450 ℃左右 。 3. 3 球化处理工艺
- 1、下载文档前请自行甄别文档内容的完整性,平台不提供额外的编辑、内容补充、找答案等附加服务。
- 2、"仅部分预览"的文档,不可在线预览部分如存在完整性等问题,可反馈申请退款(可完整预览的文档不适用该条件!)。
- 3、如文档侵犯您的权益,请联系客服反馈,我们会尽快为您处理(人工客服工作时间:9:00-18:30)。
2010年第4期Aug.2010№4铸造设备与工艺近年来我国铸造业发展迅速,产量已稳居世界第一,而且随着自动线的不断引进,我国铸造技术和水平也达到了前所未有的进步。
然而我国铸造业发展却极不平衡,大型、合资及少数民营企业由于其资金优势,多采用自动化方式生产;而大多数中小企业仍采用半自动和手工方式生产,生产方式和技术落后、单一,铸件质量水平总体不高。
尤其对大平面和不易补缩铸件缺少可靠的方法,有些厂家也简单采用了横浇竖冷的工艺方法,但效果不明显,究其原因主要是对垂直分型工艺不了解。
此外横浇竖冷的工艺方法不适合批量生产铸件,对厚大件而言也存在安全隐患。
1水平分型工艺和垂直分型工艺的特点1.1水平分型工艺的特点水平分型是传统的工艺方法,具有适应性强的特点。
浇注系统常用的分类方法有两种:一是根据各组元断面比例关系的不同,即阻流断面位置的不同,可分为封闭式和开放式浇注系统;另一是按内浇道在铸件上的相对位置不同,将浇注系统分成顶注式、中间注入式、底注式和阶梯式等几种类型。
封闭式浇注系统是指从浇口杯底孔到内浇道的断面积逐渐缩小、其阻流断面正好是内浇道的浇注系统。
这种浇注系统在浇注开始不久各组元能迅速被金属液充满,故又称充满式浇注系统。
特点是有较好的挡渣能力,但产生金属飞溅而使金属液氧化加剧。
主要用于中小型铸铁件。
开放式浇注系统是指浇口杯底孔到内浇道的断面积逐渐加大、其阻流断面在直浇道上口的浇注系统。
其特点是充型平稳,但挡渣能力差,消耗的金属液也较多。
主要用于有色金属件、球墨铸铁件及漏包浇注的铸钢件。
半封闭式和封闭—开放式浇注系统兼顾了前两种的优点应用广泛。
1.2垂直分型工艺的特点垂直分型浇注系统中,金属液的充型静压头在铸型底部和顶部可相差几倍,如果在短时间内要求各层内浇道逐层接替地充满所有型腔(即像阶梯式浇注系统那样),势必造成每个型腔的充型速度太快,以及上下部位受热条件不一样,而使冲砂、气孔、粘砂(底部铸件)、浇不足(顶部铸件)等缺陷太多,因而要求在浇注过程中,所有型腔都能始终保持恒定的金属静压头(即各层内浇道的压头虽不同,但浇注的整个过程中不变化),达到各内浇道的流量相等,同时充满,以获得质量基本一致的合格铸件。
这样设计的浇注系统称为恒压等流量浇注系统。
设计时需注意以下几点:1)只有浇注过程中始终保持充满状态,整个浇注系统内金属的静压头才能稳定不变。
所以应采用封闭式,而不能采用开放式浇注系统。
2)不同高度的内浇道应有不同的断面积,以控制相同的浇注重量速度,让上下各层型腔几乎同时充型和同时充满,使铸型的受热条件和铸件的冷却条件都基本相同。
这样就可获得质量一致的铸件。
浇注时间应严加控制。
据经验,浇注时间的变化如果大于1s ,废品率大幅度地增加。
利用垂直分型技术生产高品质球墨铸铁件裴兵(安徽神剑科技股分有限公司,安徽合肥230022)摘要:作者根据多年的生产实践,分析了垂直分型工艺和水平分型工艺各自的特点,研究了垂分型工艺浇注系统和冒口的计算,重点讨论了垂直分型技术在实际生产中的应用,尤其是大平面和不易补缩铸件可利用垂直分型技术来弥补水平分型的缺憾,从而生产出高品质铸件。
关键词:垂直分型;生产;高品质;铸铁件中图分类号:TG255文献标识码:B文章编号:1674-6694(2010)04-0030-02收稿日期:2010-06-11作者简介:裴兵(1967-),男,硕士,高级工程师,从事铸造技术开发应用和管理工作。
·铸造工艺·铸造设备与工艺FOUNDRY EQUIPMENT AND TECHNOLOGY2010年第4期Aug.2010№42010年8月30··2010年第4期铸造设备与工艺裴兵:利用垂直分型技术生产高品质球墨铸铁件(下转第38页)3)为保证浇注系统压力恒定、液流不紊乱,得到稳定的浇注速度,并能能排除主要的污物和熔渣,浇口杯应能容纳足够的金属液量,并在整个浇注过程中保持液面高度不变;浇口杯容积过大会过多地消耗金属,但太小又会导致金属外溢和严重的飞溅。
2垂直分型工艺浇注系统和冒口计算2.1浇注系统计算理论公式:V =2gH姨式中:V ———金属流速,mm/s ;g ———重力加速度,9810mm/s 2;H ———静压头,mm 。
实际公式:V=m 姨(1)式中:m ———摩擦因子,0<m <1。
W=GT(2)式中:W ———金属流速率,kg/s ;G ———金属质量,kg ;T ———浇注时间,s 。
W=ρ×F ×V (3)式中:ρ———金属液密度,kg/mm 3;F ———浇道截面积,mm 2。
由式(1)、式(2)和式(3)得:G T=ρ×F ×V G T =ρ×F ×m ×2gH姨可以得出:F =G ρ×2g 姨×T ×m ×H姨(4)将ρ=6.89×10-6(kg/mm 3),g =9810mm/s 2代入式(4)可得:F =1036G T ×m ×H姨(5)式中:F ——浇道截面积,mm 2;G ———型腔金属重量,kg ;T ———浇注时间,s ;H ———静压头,mm ;m ———摩擦因子取值0~1。
2.2冒口计算凝固模数:M C =V A(cm )式中:V ———厚大部体积,cm 3;A ———厚大部表面积,cm 2。
M R ≥K ×M C式中:M R ———冒口的凝固模数;K ———球铁取0.8~1.1。
冒口见图1,其尺寸见表1。
3垂直分型技术的应用3.1专用砂箱的制作利用垂直分型技术,最好设计专用砂箱来生产。
砂箱配对使用、需用柱销定位,砂箱侧面需留出浇口杯位置,以便造型时直接造出浇注系统。
序号2345678910111213141516172518040.49258.10.493031080.583014.00.58350.50.673522.30.674075.40.754033.30.6745107.30.834547.40.7550147.30.925065.00.8355196.0 1.05586.50.9260254.5 1.0860112.3 1.065323.5 1.1765142.8 1.0870404.0 1.2570178.4 1.1775497.0 1.3375219.4 1.2580603.0 1.3380266.2 1.3385723.0 1.4285319.3 1.4290859.0 1.5190379.1 1.51951010.0 1.5995445.8 1.591001178.01.68100520.01.681209.40.4020 4.20.40直径D R /mm 容积/cm 3凝固模数M R 直径D R /mm 容积/cm 3凝固模数M R 圆柱型冒口球形冒口表1冒口尺寸40°R 5R 2R 3D /2D /51.5DR 3D /2D /640°b )球形冒口a )圆柱型冒口图1冒口D31··2010年第4期Aug.2010№4铸造设备与工艺3.2典型模板设计典型模板设计见图2。
3.3造型和浇注利用成形模板可进行批量生产,既可用机械造型,也可用手工造型。
造型后将砂箱进行固定,再将砂箱立起,如垂直无箱挤压造型一般将一型一型靠拢,然后四周用型砂围起压紧,即可进行浇注。
4结论垂直分型技术越来越多的被利用到实际生产中,尤其是不易用水平分型生产的平面件和不易补缩铸件,可以用垂直分型技术来得到高品质铸件。
图2典型浇注系统示意图浇口杯横浇道冒口直浇道内浇道(上接第31页)要承受高温和高的爆发压力,随着发动机技术的不断更新发展,缸内直喷(DGI )和涡轮增压(TCI )等技术的应用,对缸盖燃烧室位置的要求会越来越高。
因此对材料的(高温)机械性能要求也越来越高,尤其是气门鼻梁区和燃烧室鼻梁区位置。
另外,接近燃烧室的火花塞安装孔A →D 剖面位置对机械性能的要求要比气门鼻梁区和燃烧室鼻梁区位置低,即气门鼻梁区→燃烧室鼻梁区→火花塞孔处(A →B →C →D 剖面)对应处材料的机械性能要求是从高到低的。
因此,根据Flemings 等人的研究结果,气门鼻梁区→燃烧室鼻梁区→火花塞孔处(A →B →C →D 剖面)这些位置的二次枝晶间距是应该逐渐增大的,这与实际的检测结果一致(见图5),这说明可以通过限定二次枝晶间距的大小来衡量铝合金铸件局部位置是否满足设计性能的要求。
综上所述,由于铸件的结构问题,无法直接检测铸件局部位置的机械性能,但是可以用二次枝晶间距作为一种判定依据,来判断铸件是否能满足机械性能设计的要求。
3结论通过对金属型重力铸造铝合金缸盖关键位置二次枝晶间距的研究,得出了以下结论,对铸件的铸造工艺设计和验收标准有着实际的指导意义:1)对于测量二次枝晶间距值的试样选取位置不同,对应的凝固速率不同,二次枝晶间距值也就不同,对于缸盖铸件,沿着燃烧室凸台向上,即从燃烧室面到顶部的SDAS 值是逐渐增大的;2)铸件局部的凝固速率是很难测量的,但可以用二次枝晶间距来反推铸件局部的凝固速率,从而判断铸造工艺的合理性,并为工艺调整实现铸件顺序凝固提供依据;3)对于不能对本体进行取样来检测铸件局部机械性能的,可以用二次枝晶间距来衡量铸件的机械性能,从而作为一种判定方法验证铸造工艺能否满足铸件的性能设计要求。
参考文献:[1]张炳荣,王斯勇,王一民.重力铸造铝合金发动机缸盖的二次枝晶间距研究[J ].铸造技术,2008,29(11):1546-1549.[2]张炳荣,田身军,王宏远.二次枝晶间距和热处理工艺对铝合金发动机缸盖机械性能的综合影响[J ].铸造技术,2009,30(10):1367-1375.[3]MI Guo-fa ,LIU Xiang-yu ,ZHU Zhao-jun.Effects of chill castingprocesses on secondary den -drite arm spacing and densification of Al-Si-Mg alloy [J ].Science Press ,Trans.Nonferrous Met.Soc.China 2007(17):1012-1017.[4]Hongjun Ni ,Baode Sun ,Haiyan Jiang ,etc.Ef -fect of JDN-I flux on DAS of A365alloy at different cooling rate [J ].Materials Sci -ence and Engineering ,2003,A348:1-5.[5]Marcin Kalka ,Janusz plex pro -cedure for the quan -titative description of an Al-Si cast alloy microstructure.Materi -als Characterization ,2006,56:373-378.[6]李晨希,郭太明,李荣德.二次枝晶臂间距的研究[J ].铸造,2004,53(12):1011-1014.[7]Bingrong Zhang ,Maurizio Garro ,Angelo Giglio.Effect of Dendrite Arm Spacing on Mechanical Properties of Aluminum Alloy Cylinder Heads and Engine Blocks [J ].SAE international ,2004(2):101-110.[8]Zhang B ,Garro M.an ,Tagliano C.Dendrite arm spacing in alu -minum alloy cylinder heads pro -duced by gravity semi-perma -nent mold [J ].Published by Metallurgical Science and Technolo -gy ,2003,21(1):3-9.30938··。