连铸坯质量
连铸坯质量缺陷

连铸坯的质量缺陷及控制摘要连铸坯质量决定着最终产品的质量。
从广义来说所谓连铸坯质量是得到合格产品所允许的连铸坯缺陷的严重程度,连铸坯存在的缺陷在允许范围以内,叫合格产品。
连铸坯质量是从以下几个方面进行评价的:(1)连铸坯的纯净度:指钢中夹杂物的含量,形态和分布。
(2)连铸坯的表面质量:主要是指连铸坯表面是否存在裂纹、夹渣及皮下气泡等缺陷。
连铸坯这些表面缺陷主要是钢液在结晶器内坯壳形成生长过程中产生的,与浇注温度、拉坯速度、保护渣性能、浸入式水口的设计,结晶式的内腔形状、水缝均匀情况,结晶器振动以及结晶器液面的稳定因素有关。
(3)连铸坯的内部质量:是指连铸坯是否具有正确的凝固结构,以及裂纹、偏析、疏松等缺陷程度。
二冷区冷却水的合理分配、支撑系统的严格对中是保证铸坯质量的关键。
(4)连铸坯的外观形状:是指连铸坯的几何尺寸是否符合规定的要求。
与结晶器内腔尺寸和表面状态及冷却的均匀程度有关。
下面从以上四个方面对实际生产中连铸坯的质量控制采取的措施进行说明。
关键词:连铸坯;质量;控制1 纯净度与质量的关系纯净度是指钢中非金属夹杂物的数量、形态和分布。
夹杂物的存在破坏了钢基体的连续性和致密性。
夹杂物的大小、形态和分布对钢质量的影响也不同,如果夹杂物细小,呈球形,弥散分布,对钢质量的影响比集中存在要小些;当夹杂物大,呈偶然性分布,数量虽少对钢质量的危害也较大。
此外,夹杂物的尺寸和数量对钢质量的影响还与铸坯的比表面积有关。
一般板坯和方坯单位长度的表面积(S)与体积(V)之比在0.2~0.8。
随着薄板与薄带技术的发展,S/V可达10~50,若在钢中的夹杂物含量相同情况下,对薄板薄带钢而言,就意味着夹杂物更接近铸坯表面,对生产薄板材质量的危害也越大。
所以降低钢中夹杂物就更为重要了。
提高钢的纯净度就应在钢液进入结晶器之前,从各工序着手尽量减少对钢液的污染,并最大限度促使夹杂物从钢液中排除。
为此应采取以下措施:⑴无渣出钢。
提高连铸坯内部质量的方法
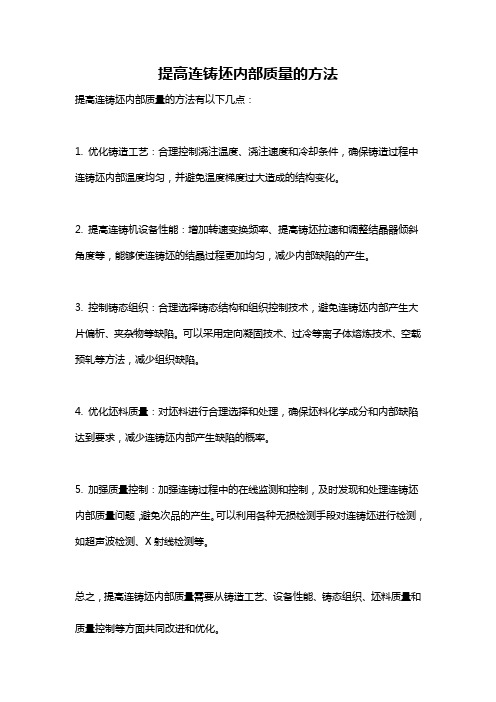
提高连铸坯内部质量的方法
提高连铸坯内部质量的方法有以下几点:
1. 优化铸造工艺:合理控制浇注温度、浇注速度和冷却条件,确保铸造过程中连铸坯内部温度均匀,并避免温度梯度过大造成的结构变化。
2. 提高连铸机设备性能:增加转速变换频率、提高铸坯拉速和调整结晶器倾斜角度等,能够使连铸坯的结晶过程更加均匀,减少内部缺陷的产生。
3. 控制铸态组织:合理选择铸态结构和组织控制技术,避免连铸坯内部产生大片偏析、夹杂物等缺陷。
可以采用定向凝固技术、过冷等离子体熔炼技术、空载预轧等方法,减少组织缺陷。
4. 优化坯料质量:对坯料进行合理选择和处理,确保坯料化学成分和内部缺陷达到要求,减少连铸坯内部产生缺陷的概率。
5. 加强质量控制:加强连铸过程中的在线监测和控制,及时发现和处理连铸坯内部质量问题,避免次品的产生。
可以利用各种无损检测手段对连铸坯进行检测,如超声波检测、X射线检测等。
总之,提高连铸坯内部质量需要从铸造工艺、设备性能、铸态组织、坯料质量和质量控制等方面共同改进和优化。
连铸连轧生产:连铸坯质量含义

寸、分布状态 主要取决于进入结晶器之前钢液的洁净度以及钢液在传递
过程中被污染的程度。
6.1连铸坯质量含义
连铸坯的表面质量缺陷 是指连铸坯表面是否存在裂纹、夹渣及皮下气泡等缺陷,主
要是式水口的设计、
连续铸钢生产
6.1连铸坯质量控制
6.1连铸坯质量含义 6.2连铸坯的洁净度 6.3连铸坯表面质量 6.4连铸坯内部质量 6.5连铸坯的外观质量
6.1连铸坯质量含义
连铸坯质量是指合格产品所允许的铸坯缺陷程度。 其含义包括连铸坯的洁净度、连铸坯的表面质量、连铸坯内
部质量以及连铸坯外观质量。
结晶器振动以及结晶器液面的稳定因素有关。
6.1连铸坯质量含义
连铸坯的内部质量缺陷 是指连铸坯是否具有正确的凝固结构,以及裂纹、偏析、疏
松等缺陷的程度,主要是由二冷区液相穴钢水的凝固过程所决定 的。
二冷区冷却水的合理分配,连铸结晶器、扇形段等关键设备 的精度控制是保证铸坯质量的关键。采用铸坯压下技术和电磁搅 拌技术会进一步改善连铸坯内部质量。
6.1连铸坯质量含义
连铸坯的外观质量 是指连铸坯的形状是否规矩,尺寸误差是否符合规定要求,
主要包括脱方、鼓肚等。 与连铸设备状态(结晶器内腔尺寸、二冷区辊子的对中等)
和铸坯冷却状态(冷却强度大小、是否均匀)有关。
感谢聆听
连铸坯质量控制

连铸坯质量控制连铸坯质量控制1. 引言2. 连铸坯质量特点连铸坯的质量特点主要包括以下几个方面:2.1 凝固结构连铸坯是通过冷却凝固过程形成的,其凝固过程直接影响到坯体的凝固结构。
凝固结构的好坏会对后续的加工以及材料性能产生重要影响。
2.2 化学成分均匀性连铸坯的化学成分均匀性是其质量的重要指标之一。
成分不均匀容易导致后续钢材性能不稳定,从而影响到产品的质量。
2.3 表面缺陷由于连铸坯制造过程中的一些不可避免的因素,气体夹杂、氧化皮等,会在坯体表面形成一些缺陷。
这些表面缺陷会对后续产品的外观质量产生负面影响。
2.4 尺寸偏差连铸坯的尺寸偏差是指坯体的实际尺寸与标准尺寸之间的差异。
尺寸偏差会影响到钢材的加工工艺和成形质量。
3. 连铸坯质量控制因素及措施连铸坯质量的影响因素众多,包括原料质量、连铸工艺参数、设备状况等。
针对这些影响因素,可以采取以下控制措施来提高连铸坯的质量:3.1 原料质量控制通过严格控制原料的化学成分和物理性能,确保连铸坯的化学成分均匀性和机械性能达到要求。
3.2 连铸工艺参数控制连铸工艺参数的合理设置对坯体的凝固结构和表面质量具有决定性影响。
需要通过优化连铸工艺参数,如冷却水流量、浇注速度等,来控制连铸坯的质量。
3.3 设备维护与改进连铸设备的状态对连铸坯质量也有重要影响。
定期进行设备维护和检修,及时处理设备故障,可以保证设备处于良好状态,进而提高连铸坯的质量。
3.4 检测手段与技术利用先进的检测手段和技术,如超声波检测、磁力检测等,可以对连铸坯进行质量检测,及时发现问题并采取相应措施。
4.连铸坯质量控制是钢铁生产中至关重要的环节。
通过对连铸坯质量特点的分析和影响因素的控制,可以采取相应的措施来提高连铸坯的质量。
这不仅对于保证下游产品质量,还对于提高工业生产效益和降低资源消耗具有重要意义。
开展连铸坯质量控制工作是必不可少的。
连铸坯质量

● 对于极细的钢丝(如直径为0.10-0.25mm 对于极细的钢丝(如直径为0 10- 25mm
的轮胎钢丝)和极薄钢板(如厚度为 025mm的镀锡板) mm的镀锡板 0.025mm的镀锡板)中,其所含夹杂物的尺 寸就可想而知了。 寸就可想而知了 。 夹杂物的尺寸和数量对 钢质量的影响还与铸坯表面积有关。 钢质量的影响还与铸坯表面积有关。
采用压缩浇铸技术或者应用多点矫直技术二冷区采用合适夹辊辊距支撑辊准确对弧二冷水分配适当保持铸坯表面温度均匀合适拉辊压下量最好采用液压控制机构带液心的铸坯在运行过程中于两支撑辊之间高温坯壳中钢液静压力作用下发生鼓胀成凸面的现象称之为鼓肚变形
连铸坯质量控制
内容提要
◆ 连铸坯的质量评价 ◆ 连铸坯的纯净度及控制 ◆ 连铸坯表面质量及控制 ◆ 连铸坯内部质量及控制 ◆ 连铸坯形状缺陷及控制
星状裂纹 一般发生在晶间的细小裂
呈星状或呈网状。 纹,呈星状或呈网状。通常是隐藏在氧化铁 皮之下难于发现, 皮之下难于发现,经酸洗或喷丸后才出现在 铸坯表面。主要是由于铜向铸坯表面层晶界 铸坯表面。 的渗透,或者有AlN,BN或硫化物在晶界沉淀, AlN,BN或硫化物在晶界沉淀 的渗透,或者有AlN,BN或硫化物在晶界沉淀, 这都降低了晶界的强度,引起晶界的脆化, 这都降低了晶界的强度,引起晶界的脆化,从 而导致裂纹的形成。 而导致裂纹的形成。
其实早在结晶器内坯壳表面就存在细小裂纹, 其实早在结晶器内坯壳表面就存在细小裂纹,铸坯进 入二冷区后, 微小裂纹继续扩展形成明显裂纹。 入二冷区后 , 微小裂纹继续扩展形成明显裂纹 。 由于结 晶器弯月面区初生坯壳厚度不均匀,其承受的应力超过 晶器弯月面区初生坯壳厚度不均匀 , 了坯壳高温强度, 在薄弱处产生应力集中致使纵向裂纹。 了坯壳高温强度 , 在薄弱处产生应力集中致使纵向裂纹 。 坯壳承受的应力包括: 坯壳内外, 坯壳承受的应力包括 : 坯壳内外 , 上下存在温度差 产生的热应力; 产生的热应力 ; 钢水静压力阻碍坯壳凝固收缩产生的应 力; 坯壳与结晶器壁不均匀接触而产生的摩擦力。这些 坯壳与结晶器壁不均匀接触而产生的摩擦力。
连铸坯的质量控制概述

提高铸坯洁净度的措施: (1)无渣出钢 (2)选择合适的精炼处理方式 (3)采用无氧化浇铸技术 (4)充分发挥中间包冶金净化的作用 (5)选用优质耐火材料 (6)充分发挥结晶器的作用 (7)采用电磁搅拌技术,控制铸流运动
三、铸坯表面质量及控制
控制表面质量的必要性 表面缺陷的形成 表面裂纹的主要种类 液面结壳 凹坑和重皮
4.3.2 内部纵向裂纹
包括中心线裂纹、三角区裂纹和角部裂纹 形成原因:液相穴末端板坯鼓肚;
板坯宽面、窄面鼓肚 主要影响因素:
1、浇铸速度过快; 2、浇铸温度过高; 3、钢水含硫量过大; 4、结晶器锥度太小; 5、铸流不对正。
减少内部裂纹的措施
采用多点矫直技术以弥补单点矫直的 不足
二冷区采用合适的夹辊辊距,支撑辊 准确对弧
对弧,并确保二冷区的均匀冷却
5.2 圆柱坯变形
定义:圆坯变形成椭圆形或不规则多边 形。圆坯直径越大,变成随圆的倾向越 严重。
椭圆变形原因: (1)圆形结晶器内腔变形 (2)二冷区冷却不均匀 (3)连铸机下部对弧不准 (4)拉矫辊的夹紧力调整不当,过分压下
应对圆柱坯变形的措施: (1)及时更换变形的结晶器 (2)连铸机要严格对弧 (3)二冷区均匀冷却 (4)可适当降低拉速
3.5 深振痕
结晶器上下振动时,在铸坯表面形成 周期性的和拉坯方向垂直的振动痕迹。 较深(大于0.5mm)时,振痕谷部会 形成缺陷,危害成品质量。
振痕深度与振动参数、含碳量、保护 渣性能及结晶器液面波动状态等因素 有关。
3.6 表面气泡(和皮下气泡)
形成原因:凝固过程中,钢中氧、氢、氮 和碳等元素在凝固界面富集,当其生成的 CO、H2、N2等气体的总压力大于钢水静 压力和大气压力之和时,即有气泡产生。
连铸坯质量控制
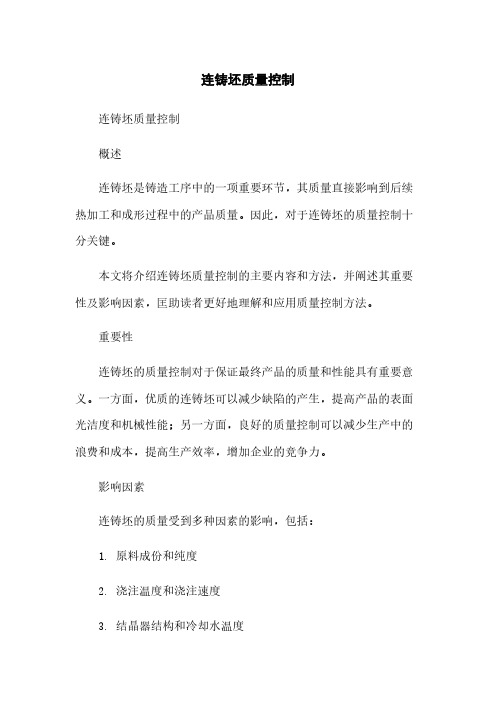
连铸坯质量控制连铸坯质量控制概述连铸坯是铸造工序中的一项重要环节,其质量直接影响到后续热加工和成形过程中的产品质量。
因此,对于连铸坯的质量控制十分关键。
本文将介绍连铸坯质量控制的主要内容和方法,并阐述其重要性及影响因素,匡助读者更好地理解和应用质量控制方法。
重要性连铸坯的质量控制对于保证最终产品的质量和性能具有重要意义。
一方面,优质的连铸坯可以减少缺陷的产生,提高产品的表面光洁度和机械性能;另一方面,良好的质量控制可以减少生产中的浪费和成本,提高生产效率,增加企业的竞争力。
影响因素连铸坯的质量受到多种因素的影响,包括:1. 原料成份和纯度2. 浇注温度和浇注速度3. 结晶器结构和冷却水温度4. 结晶器护盖的材质和形状5. 连铸速度和拉速6. 过度超熔度和段距这些因素的合理控制和调整,可以有效地提高连铸坯的质量。
质量控制方法质量控制步骤连铸坯质量控制主要包括以下几个步骤:1. 原料质量检验:对原料的成份、纯度及其它关键指标进行检验,确保原料的质量符合要求。
2. 浇注质量控制:合理控制浇注温度和速度,以避免过热或者过冷引起的坯体缺陷。
3. 结晶器质量控制:结晶器的结构和冷却水温度对坯体的结晶质量有直接影响,因此需加强结晶器的质量控制。
4. 连铸速度和拉速控制:坯体的连铸速度和拉速会影响坯体的晶粒细化程度和坯体的机械性能,需要进行合理的控制。
5. 坯体表面质量控制:通过加强护盖材料和形状的选取,合理调整过度超熔度和段距,以提高坯体表面的光洁度。
质量控制指标连铸坯的质量控制需要依据具体产品的要求和标准来制定相应的指标。
普通来说,常见的质量控制指标包括:1. 外观质量:包括表面光洁度、无裂纹、无疤痕等;2. 坯体几何尺寸:包括宽度、厚度、长度等;3. 结晶质量:包括坯体的晶粒细化程度、晶界清晰度等;4. 坯体力学性能:包括抗拉强度、屈服强度、延伸率等;以上指标应根据产品要求,通过实验和测试方法进行监控和评估。
连铸坯质量讲解
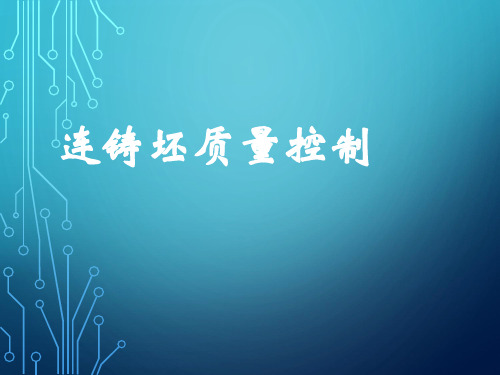
100-300微米不规则的CaO-Al2O3和Al2O3的大型夹杂物。
● 厚度为0.3mm的薄钢板,在1m2面积内,粒径小于50微
米的夹杂物应少于5个,才能达到废品率在0.05%以下,
即深冲2000个DI罐,平均不到1个废品。
● 对于极细的钢丝(如直径为0.10-0.25mm的轮胎钢丝
预防表面横裂纹的措施
◆ 结晶器采用高频率,小振幅振动 ◆ 二冷区采用平稳热冷却,控制矫直铸坯温度 ◆ 降低钢中S、O、N的含量,加入Ti、Zr、Ca ◆ 选用性能良好的保护渣 ◆ 保持结晶器液面稳定 ◆ 通过二次冷却使铸坯表面层奥氏体晶粒细化
星状裂纹一般发生在晶间的细小裂纹,呈星状
或呈网状。通常是隐藏在氧化铁皮之下难于发现,经酸洗 或喷丸后才出现在铸坯表面。主要是由于铜向铸坯表面层 晶界的渗透,或者有AlN,BN或硫化物在晶界沉淀,这都降 低了晶界的强度,引起晶界的脆化,从而导致裂纹的形成。
提高钢纯净度的措施
◆ 无渣出钢 ◆ 选择合适的精炼处理方式 ◆ 采用无氧化浇注技术 ◆ 充分发挥中间罐冶金净化器的作用 ◆ 选用优质耐火材料 ◆ 充分发挥结晶器的作用 ◆ 采用电磁搅拌技术,控制注流运动
连铸热加工 之前是否需要精整,也是影响金属收得率和成本 的重要因素,还是铸坯热送和直接轧制的前提条 件。
MnO-SiO2- Al2O3
UOE管 冷轧薄板 轮胎钢丝 弹簧钢丝
超声波探伤缺陷 冲压缺陷 冷拔断裂 冷拔断裂
200
Al2O3群;CaO·Al2O3
250
CaO-SiO2-Al2O3
30
Al2O3;Al2O3·SiO2
30 Al2O3-MnO-CaO;Al2O3
- 1、下载文档前请自行甄别文档内容的完整性,平台不提供额外的编辑、内容补充、找答案等附加服务。
- 2、"仅部分预览"的文档,不可在线预览部分如存在完整性等问题,可反馈申请退款(可完整预览的文档不适用该条件!)。
- 3、如文档侵犯您的权益,请联系客服反馈,我们会尽快为您处理(人工客服工作时间:9:00-18:30)。
侧固液相界面捕捉,在内弧侧距表
面约10mm处,有一夹杂物集聚带。 大型夹杂物多集中于内弧侧
1/5~1/4厚度处。
直结晶器+2~3m垂直段:注流冲击 是对称的,液相内夹杂物得到上浮, 同时夹杂物分布也比较均匀。见右 图和下页图
1 弧形连铸机 2 直结晶器的弧形连铸机 3 立式连铸机
连铸机机型对大型夹杂物的影响
30 30
CaO- SiO2-Al2O3
Al2O3 ,Al2O3〃SiO2 Al2O3-MnO-CaO,Al2O3
⑵ 如何分析夹杂物对产品质量的影响
应从以下几个方面着手分析: ①夹杂物的形态和组成。塑性夹杂和球形不变形夹杂对钢性能的影响 不同,沿轧制方向伸长的塑性夹杂使钢横向力学性能恶化。MnS夹杂 能变形,FeO和MnO夹杂能稍变形,SiO2 和Al2O3 夹杂不变形。FeS、 FeO熔点低使钢产生热脆,MnS熔点高改善钢的热脆。 ②夹杂物的大小和聚集状态。夹杂物会使钢材产生分层,夹杂物越大, 影响越大。但即使存在着小的夹杂物聚集,也可能使钢材分层。
③ 预防及消除方法: — 结晶器铜板表面最好镀铬或 镀镍,减少铜的渗透; — 适当控制钢中残余元素,如 ω[Cu] <0.20%; — 降低钢中硫含量,并控制合 适的[Mn]/[S]比大于40; — 控制钢中Al、N含量,选择合 适的二冷制度。
⑸ 皮下气泡与气孔
① 缺陷特征:在铸坯皮下存在的直径约1mm,长约10mm,沿柱状晶生 长方向分布的气泡称为皮下气泡。若裸露于铸坯表面的气泡称为表面气 泡;小而密集的小孔叫皮下针孔。
①连铸时钢液凝固速度快,夹杂物集聚长大机会少→尺寸较小,不易从 钢液中上浮。
②连铸过程中多了中间包装臵,钢液与大气、熔渣、耐材接触时间长易
被污染;同时在钢液进入结晶器后,在钢液流股影响下夹杂物难以从钢 液中分离。
③模铸钢锭夹杂物多集中在钢锭头部和尾部,通过切除可将夹杂物的危
害减轻,而连铸坯仅靠切头切尾难以解决问题。 因此连铸坯中夹杂物比模铸严峻。
—控制好钢的化学成分;
—采用热顶结晶器。
⑵ 方坯角部凸包
①缺陷特征:发生在方坯倒角处沿浇注方向出现的不规则凸起称为凸包。 呈连续或断续分布。 产生原因、危害及防止措施同角部纵裂
⑶ 方坯横向裂纹
① 缺陷特征:多发生在方坯内弧侧振痕波谷处的横裂纹称为横向裂
纹。裂纹长度较短,一般在5~50mm之间。金相检查表明,裂纹处 于铁素体网状区,也正好是初生奥氏体晶界。
以上。 ③以Al2O3 为主并含有SiO2 、CaS、CaO的铝酸盐。呈球状,化学
组成为CaO-Al2O3系,含SiO2少。
④硫化物如FeS、MnS等。以中心偏析和枝晶偏析,或固溶于氧化 物夹杂的各种形态存在。
└从铸坯中夹杂物类型和组成可知,它们主要由氧化物组成。
B 夹杂物来源
氧化物夹杂来自内生和外来两个方面:
拉速↑,铸坯中夹杂物↑。因为拉速↑,水口熔损加剧,钢水浸入 深度↑,夹杂物难以上浮。
浇注温度对铸坯内部质量的影响
弧形连铸机:
mm /个· -2
1-低温浇注
2-高温浇注 立弯式连铸机: 3-低温浇注 4-高温浇注
内弧
离内弧距离/mm
中心
连铸坯内夹杂物分布图
⑶ 耐火材料质量对铸坯中夹杂物的影响 连铸过程中,钢液中元素会与耐火材料中氧化物发生反应
平均报废不到1个易拉罐。…….
夹杂物组成、尺寸对最终产品的影响
产品 缺陷类型 夹杂物尺寸 /um 组 成 CaO〃Al2O3 CaO〃Al2O3,,Al2O3群 MnO- SiO2-Al2O3
深冲镀锡板
电阻焊管
凸缘裂纹
超声波探伤缺陷
50
150
冷轧薄板
轮胎钢丝 弹簧钢丝
冲压缺陷
冷拔断裂 冷拔断裂
250
2、夹杂物的类型和来源 A 夹渣物类型
铸坯中常见夹渣物类型有四种:
①Al2O3单体。在低碳铝镇静钢中有两种分布模式,一种呈悬浮状,
尺寸小于100 um;另一种呈簇状,尺寸100~300um。 ②以SiO2为主并含有Al2O3、MnO、CaO的硅酸盐。呈球状,化学
组成为CaO-Al2O3-SiO2 系或Al2O3-MnO-SiO2 系,尺寸在100um
第五章 连铸坯质量
连铸坯质量是指合格产品所允许的铸坯缺陷程度。它决定着最终产品的质量。
连铸坯质量应从以下几个方面评价: ⑴ 连铸坯纯净度 — 指钢中夹杂物的含量、形态和分布。这主要取决于进入结 晶器之前的钢水是否“干净”。因此应选择合适的精炼方式,并采用全程保护 浇注,尽可能降低钢中夹杂物含量。 ⑵连铸坯表面质量 — 指连铸坯表面是否存在裂纹、夹渣及皮下气泡等缺陷。这 些表面缺陷主要是在结晶器内坯壳形成生长中产生的,与浇注温度、拉坯速度、 保护渣性能、浸入式水口参数、结晶器振动及结晶器液面稳定性等有关。 ⑶连铸坯内部质量 — 指连铸坯内部是否具有正确的凝固结构,等轴晶与柱状晶
—确定合适的结晶器倒角和倒锥度,
适;
—铸速、铸温不合理; —结晶器冷却不合理;
—确定合理的拉速和铸温并匹配;
—结晶器与足辊、零段对弧对中良 好;
—结晶器与足辊、零段对中不好;
—钢的化学成分在裂纹敏感区。 危害:导致钢材产生裂纹缺陷甚至
—结晶器液面稳定;
安装要对中;
—浸入式水口参数、插入深度合适,
报废。
5 提高连铸坯纯净度的措施
提高钢的纯净度需加强三稳定(温度、拉速、液面)操作,在钢水进入结晶 器前尽量减少污染,并最大限度促进夹杂物从钢水中排出。为此应采取 以下措施: ① 挡渣出钢,并加入钢包覆盖剂或改质剂保温和防止钢水二次氧化; ② 选择合适的精炼方式净化钢水,改变夹杂物形态; ③ 采用全程保护浇注技术; ④ 充分发挥中间包冶金的作用; ⑤ 连铸系统采用优质耐火材料;
3 夹杂物与产品质量的关系
⑴ 夹杂物对产品质量的影响 ①夹杂物的存在破坏了钢基体的连续性,使钢的力学性能↓。 ②凡是存在大于50um大型夹杂物的部位几乎都伴有裂纹。 ③夹杂会使板材产生分层、发纹等缺陷。 ④夹杂细小,呈球形弥散分布,对钢质量影响要小一些;如夹杂物颗
粒大,呈偶然性分布,即使数量少,对钢的危害也很大。
③ 预防及消除方法:
— 采用高频率小振幅的振动方 式,减小振痕深度。
— 采用合理的二冷制度,避免
在脆性温度区矫直。 — 采用性能良好的MD保护渣; 保持MD液面稳定。 — 应用多点矫直、连续矫直或 压缩浇注等技术。 — 降低钢中S、O、N等元素含 量,或加入适量Ti、Zr、Ca等 元素,抑制碳化物、氮化物、硫 化物沿晶界析出。
⑵ 连铸操作对铸坯中夹杂物的影响 a 正常操作和异常操作 正常操作:浇注过程稳定,铸坯中夹杂多少,主要由钢水纯净度决 定。 非正常操作:浇注初期、浇注末期和多炉连浇的换包期间,铸坯中 夹杂物往往有所增加。 b 注温和拉速 中间包温度低时,夹杂物指数升高,这是因为温低,钢液黏度增加,
夹杂物不易上浮的缘故。
③夹杂物的存在部位和数量。表面夹杂对钢材质量影响大。
④夹杂对各类轧材性能的影响。夹杂对条钢、棒材影响小;对钢帘线、 无缝钢管、深冲钢等影响大。
4 影响连铸坯纯净度的因素
铸机机型对铸坯内部夹杂物的数量 弧形连铸机:注流对坯壳的冲击是 不对称的,上浮的夹杂物易被内弧 Lcs 和分布有着重要影响。 Lcc 立弯式连铸机 弧形连铸机 液相穴内夹杂物上浮示意图 LCS—垂直段临界高度 LCC—弧形结晶器直线临界高度 ⑴ 机型对铸坯中夹杂物的影响
4 宽面纵向裂纹 5 星状裂纹 6 振痕 7 气孔 8 大型夹杂物
振痕和凹陷
裂纹形成的根本原因: ①取决于连铸坯形成过程中坯壳与液固界面的受力状况,是裂纹形成 的外因。 ②取决于钢在高温下的机械性能,是裂纹形成的内因。 钢在高温下的脆化理论: 研究表明,碳钢从凝固温度冷却到600℃,有三个延展性很差的脆性区。 ①高温脆性区:在凝固温度附近。其延展性下降的原因是:在已凝固 的树枝晶之间有液膜存在,这些液膜含P、S等偏析元素,强度、塑 性几乎为零,当坯壳受到外力作用时,沿晶界裂开形成裂纹。连铸坯 表面裂纹和各种内部裂纹大都在此脆性区发生。
⑷ 方坯星状裂纹(又称网状裂纹)
①缺陷特征:是发生在晶间的细小裂纹,呈星状或网状,深度一般在
5mm以下。通常被氧化铁皮覆盖,经酸洗或喷丸处理后才可显露出来。
② 产生原因及危害: — 高温坯壳与结晶器铜壁摩 擦时,铜渗透于铸坯表面层晶 界,降低了晶界的高温强度而 产生的星状裂纹; —有AlN、BN或硫化物在晶 界析出,降低了晶界的结合力, 引起晶界脆化而出现裂纹; 危害:严重时导致方坯报废。
2[Mn] +(SiO2) =2(MnO) + [Si], 4[Al] +3(SiO2)=2(Al2O3)+3[Si]
— 所生成的MnO可在耐火材料表面形成MnO〃SiO2低熔点渣层,随
后进入钢液,当其不能上浮时就留在铸坯中。
—所生成的Al2O3可与MnO和SiO2结合生成硅酸盐夹杂物。
所以钢包、中间包、浸入式水口材质的选择非常重要
A 方坯表面缺陷
⑴ 方坯角部纵裂纹
① 缺陷特征:发生在方坯倒角处沿浇注方向出现的裂纹。
② 产生原因及危害: — 方坯菱变率大; — 结晶器倒角半径过大、倒锥度过 小,使角部冷却不均; — 结晶器磨损变形严重; —结晶器保护渣性能或消耗量不合
③ 预防及消除方法: 使方坯角部冷却均匀; —根据结晶器磨损量确定合理的结 晶器更换周期; — 选择合适的结晶器保护渣;
⑥ 充分发挥结晶器钢水净化器和铸坯表面质量控制器等的冶金作用。
浸入式水口参数合理、用性能良好的保护渣;采用结晶器液位自动控制 装臵;采用空心整体塞棒吹氩。
⑦ 采用结晶器电磁搅拌或电磁制动技术(E—MBR)。
二 连铸坯表面质量
连铸坯表面质量与钢
液 在 MD 内 的 凝 固 密 切相关。控制铸坯表 面 质 量 就 是 控 制 MD 中坯壳的形成问题。 其好坏决定了铸坯在 热加工前是否需要精 整,是否热送热装, 是影响金属收得率和 成本的重要因素。 1 角部横向裂纹 铸坯表面缺陷示意图 2 角部纵向裂纹 3 表面横向裂纹