汽车传动轴设计
汽车传动轴设计范文

汽车传动轴设计范文汽车传动轴是汽车动力传输系统中的关键组成部分,承担着将发动机产生的动力传递到车轮的任务。
传动轴设计的目标是实现高效率、低噪音和可靠性。
在设计传动轴时,需要考虑多个因素,包括传动轴的材料选择、传动轴的结构设计和传动轴的加工工艺等。
传动轴的材料选择是影响传动轴性能的重要因素之一、传动轴通常采用高强度合金钢或碳纤维复合材料制作。
高强度合金钢具有优异的强度和韧性,能够承受高强度的扭转和弯曲力。
而碳纤维复合材料具有高强度、低密度和优异的疲劳寿命,能够降低传动轴的重量并提高耐久性。
传动轴的结构设计是实现高效率传输的关键。
一般来说,传动轴的截面形状决定了其刚度和重量。
传动轴通常采用圆柱形的实心杆或中空杆设计。
实心杆传动轴具有较高的刚度,能够抵御大扭矩和弯曲力,但重量较大。
而中空杆传动轴由于空心结构的设计,能够降低传动轴的重量,并提高传动效率。
但对于承受较大扭矩和弯曲力的应用来说,中空杆传动轴的刚度较低,需要在设计中进行综合考虑。
除了结构设计,传动轴的加工工艺也对传动轴性能产生重要影响。
精确的加工工艺能够提高传动轴的平衡性、可靠性和传动效率。
在加工过程中,需要进行精确的尺寸控制、表面处理和动平衡处理。
尺寸控制是确保传动轴高度精度的关键。
表面处理能够提高传动轴的耐腐蚀性和抗磨性。
动平衡处理能够减少传动轴的振动和噪音,并提高传动效率。
除了上述因素,传动轴设计还需要考虑其他一些因素,如传动轴的长度、传动轴的安装方式和传动轴的支撑方式等。
传动轴长度的选择需要权衡传动效率和车辆布局的要求。
传动轴的安装方式一般分为固定式和可伸缩式两种,根据车型和传动需求进行选择。
传动轴的支撑方式包括悬挂式和支架式,需要根据车辆底盘结构和传动需求进行选择。
在传动轴设计中,还需要进行性能计算和结构优化。
性能计算可以通过计算机辅助工程软件进行,包括传动效率、传动轴的疲劳寿命和传动轴的振动等。
结构优化可以通过有限元分析方法进行,通过调整传动轴的结构参数,优化传动轴的性能和重量。
汽车传动轴设计范文

汽车传动轴设计范文首先,汽车传动轴的主要功能是传递动力。
在设计传动轴时,需要考虑到车辆的功率输出和转速范围。
一般而言,高功率车辆需要更加强固的传动轴来承受更大的转矩和压力。
此外,传动轴的设计还需要考虑到车辆的运行速度范围,以确保传动轴在高速情况下能够承受住转动力。
其次,汽车传动轴的设计对于车辆的平顺性和舒适性也有很大影响。
传动轴的设计需要考虑到轴的重量和平衡性,以减少振动和噪音。
一种常见的设计方法是在传动轴上使用平衡块来平衡轴的重量和减少振动。
此外,传动轴的设计还需要考虑到轴的刚度和弯曲性,以确保传动轴在运转过程中不会发生变形或弯曲,从而影响车辆的平顺性和舒适性。
另外,对于四驱车辆而言,传动轴的设计也需要考虑到车轮之间的差速问题。
差速器通常安装在传动轴上,它能够根据车轮速度的差异来实现差速作用,并帮助车辆更好地应对转弯情况。
因此,传动轴的设计需要考虑到差速器的安装位置和传动轴与差速器之间的连结方式。
此外,与传动轴密切相关的还有轴承和万向节的设计。
轴承的选材和设计对于减少传动轴的摩擦和磨损至关重要。
对于高速和高功率的车辆而言,可能需要采用更耐磨和耐高温的轴承材料来提高传动轴的使用寿命。
万向节的设计则用于传递动力和允许轴的角度变化,以适应车轮的悬挂和转向。
综上所述,汽车传动轴的设计对于汽车性能、安全和舒适性都起着至关重要的作用。
在设计传动轴时,需要兼顾动力传递、平顺性、舒适性和差速等因素,以确保传动轴能够满足车辆的需求。
此外,轴承和万向节的设计也是传动轴设计的重要考虑因素,它们对于传动轴的耐磨性、耐高温性和角度变化能力都有着重要影响。
因此,对于汽车制造商和工程师而言,对于传动轴设计的细节和原理的深入了解是非常必要的。
浅谈汽车传动轴设计的基本要求与考虑因素

浅谈汽车传动轴设计的基本要求与考虑因素
前言
随着科学技术的进步,汽车的发展已经步入了一个新的时代。
汽车电子器件(汽车空调控制器)也已成为汽车性能的标志。
汽车传动轴是汽车构造中重要的组成部分(汽车电子控制技术),所以对于汽车传动轴的设计就变得尤为重要。
那么,怎样设计一款高性能的汽车传动轴呢,作者通过搜集整理资料,从汽车传动轴设计的基本要求,需要考虑的因素以及对汽车传动轴设计优化等方面做了详细介绍。
汽车传动轴设计(汽车控制系统)的基本要求:
1.保证所连接的两根轴相对位置在预计范围内变动时,能可靠地传递动力。
2.保证所连接两轴尽可能等速运转。
3.由于万向节夹角而产生的附加载荷、振动和噪声应在允许范围内。
4.传动效率高,使用寿命长,结构简单,制造方便,维修容易等第三章五十铃万向传动轴结构分析及选型由于五十铃货车轴距不算太长,且载重量。
变速器与驱动桥之间的万向传动装置
汽车传动轴设计时需考虑的几个方面
空心传动轴具有较小的质量,能传递较大的转矩,比实心传动轴具有更高的临界转速,所以此传动轴管采用空心传动轴。
传动轴的长度和夹角及它们的变化范围,由汽车总布置设计决定。
设计时应保证在传动轴长度处在最大值时,花键套与花键轴有足够的配合长度;而在长度处于最小时,两者不顶死。
传动轴夹角大小会影响万向节十字轴和滚针轴承的寿命、万向传动效率和十字轴的不均匀性。
变化范围为3。
汽车传动轴经常处于高速旋转状态下,所以轴的材料查机械零件手册选取。
传动轴设计及应用解读

• 准等速万向节:是指输入轴和输出轴以近似等速传递运动 的万向节。双联式万向节、凸块式万向节和三销轴式万向 节等为准等速万向节。主要用于转向驱动桥。
• 等速万向节:等速万向节是指输入轴和输出轴以等速传递 运动的万向节。球笼式万向节和球叉式万向节等为等速万 向节。主要用于轿车和驱动桥。 • 挠性万向节:挠性万向节依靠其中弹性零件的弹性变形来 保证在相交两轴间传动时不发生干涉。它能减小传动系的 扭转振动、动载荷和噪声,结构简单,使用中不需润滑, 一般用于两轴间夹角不大和很小轴向位移的万向传动场合。
传动轴的动平衡
• 传动轴总成不平衡是传动系弯曲振动的一个激 励源,当高速旋转时,将产生明显的振动和噪 声。所以传动轴装配后必须100%进行动平衡 检验,并在传动轴两端焊平衡片校正不平衡量, 其剩余不平衡量不应低于GB 9293中规定的G40 平衡品质等级。 • 影响传动轴动平衡品质的因素: 1、万向节十字轴的轴向间隙; 2、传动轴滑动花键副中的间隙; 3、传动轴总成两端连接处定心精度; 4、高速回转时传动轴的弹性变形。
传动轴额定载荷的确定
• • 传动轴的额定载荷是根据车型的配置参数计算出来的。先按发动机最大扭矩 计算,再按车轮的最大附着力计算,取二者中的小值作为额定扭矩。 1、按发动机最大扭矩计算: Mg=Memax×ik1×ip1/n 式中 Mg—按发动机最大扭矩计算时传动轴承受的扭矩,N.m Memax—发动机最大扭矩,N.m ik1 —变速箱一档速比 ip1 —分动箱低档速比 n —使用分动器低档时的驱动轴数目 2、按车轮最大附着力计算: Mφmax=G×rk×ψ/io 式中 Mφmax—按附着力计算时传动轴承受的扭矩,N.m G—满载时驱动轴上的载荷,N rk —车轮的滚动半径,m ψ —轮胎与地面的附着系数(在良好的沥青路面上取0.8) io —减速器速比
四驱车辆传动轴系统的设计
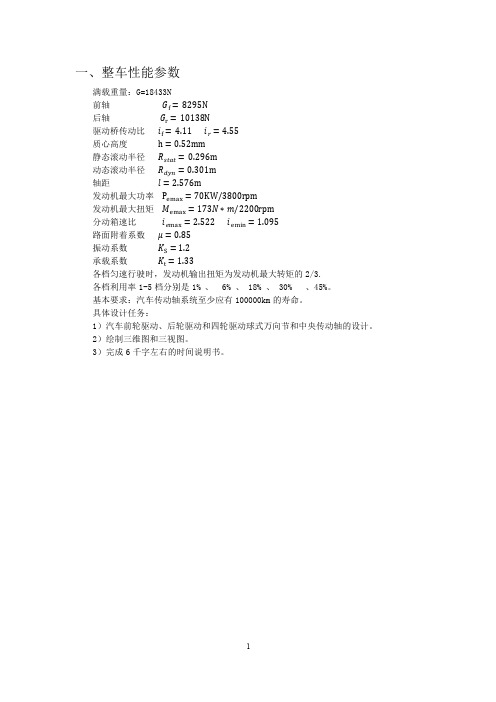
一、整车性能参数满载重量:G=18433N前轴G f=8295N后轴 G r=10138N驱动桥传动比i f=4.11i r=4.55质心高度h=0.52mm静态滚动半径R stat=0.296m动态滚动半径R dyn=0.301m轴距l=2.576m发动机最大功率P emax=70KW/3800rpm发动机最大扭矩M emax=173N∗m/2200rpm分动箱速比i emax=2.522i emin=1.095路面附着系数μ=0.85振动系数K S=1.2承载系数K t=1.33各档匀速行驶时,发动机输出扭矩为发动机最大转矩的2/3.各档利用率1-5档分别是1% 、 6% 、 18% 、 30% 、45%。
基本要求:汽车传动轴系统至少应有100000km的寿命。
具体设计任务:1)汽车前轮驱动、后轮驱动和四轮驱动球式万向节和中央传动轴的设计。
2)绘制三维图和三视图。
3)完成6千字左右的时间说明书。
二、各轴的启动转矩M A和附着转矩M H计算用两者中的最小值作为静态转矩选择万向节,计算结果列入表1。
表1 启动转矩和附着转矩的计算结果三、球笼式万向节的设计选用1、万向节概述万向传动轴由万向节和传动轴组成,有时还加装中间支承。
它主要用来在工作过程中相对位置不断改变的两根轴间传递转矩和旋转运动。
万向传动轴设计应满足如下基本要求:1)保证所连接的两轴相对位置在预计范围内变动时,能可靠地传递动力。
2)保证所连接两轴尽可能等速运转。
由于万向节夹角而产生的附加载荷、振动和噪声应在允许范围内。
3)传动效率高,使用寿命长,结构简单,制造方便,维修容易等。
万向传动轴在汽车上应用比较广泛。
在发动机前置后轮或全轮驱动的汽车上,由于弹性悬架的变形,变速器或分动器输出轴与驱动桥输入轴的轴线相对位置经常变化,所以普遍采用十字轴万向传动轴。
在转向驱动桥中,内、外半轴之间的夹角随行驶需要而变,这时多采用等速万向传动轴。
当后驱动桥为独立悬架时,也必须采用万向传动轴。
传动轴设计及应用

传动轴设计及应用首先,传动轴的设计需要考虑到以下几个方面的因素:材料选择、强度计算、匹配设计和制造工艺。
材料选择是传动轴设计的重要环节。
一般来说,传动轴要求具有高强度、良好的韧性和耐磨性。
常见的传动轴材料包括碳钢、合金钢和不锈钢等。
选择合适的材料可以保证传动轴的寿命和可靠性。
强度计算是传动轴设计中的重要一环。
传动轴工作时会承受扭矩和弯曲力,因此需要进行强度计算来确定传动轴的尺寸和形状。
一般情况下,传动轴的强度计算包括静态强度计算和疲劳强度计算两部分,其中疲劳强度计算对于传动轴的使用寿命至关重要。
匹配设计是指传动轴的轴径和连接方式的设计。
传动轴的轴径设计需要根据所传递的扭矩大小来确定,一般可以通过静态强度计算得到。
传动轴的连接方式有多种,常见的有键槽连接和销轴连接等。
选择合适的连接方式可以确保传动轴的可靠性和安全性。
制造工艺是传动轴设计中的最后一环。
传动轴通常需要进行多道工序的加工,如车削、铣削和热处理等。
制造工艺的选择和控制对于传动轴的尺寸精度和表面质量至关重要。
同时,传动轴的装配和调试也需要注意,以确保传动系统的正常运行。
传动轴的应用非常广泛。
汽车传动轴是其中最常见的应用之一、汽车传动轴通常由前后驱动轴、中间驱动轴和传动装置等组成,用于传递发动机的动力到车轮上。
传动轴的设计需要考虑到汽车的整体性能、可靠性和经济性。
此外,传动轴还广泛应用于船舶、工程机械、风电设备等领域,用于传递动力和扭矩,实现各种机械设备的运行和工作。
总之,传动轴是机械设备中非常重要的一种机械元件,其设计和应用涉及到材料选择、强度计算、匹配设计和制造工艺等方面的因素。
传动轴的设计需要考虑到所传递的动力和扭矩的大小,以确保传动系统的正常运行和工作。
传动轴的应用范围非常广泛,主要用于汽车、船舶、工程机械等领域。
传动轴的合理设计和应用可以提高机械设备的性能、可靠性和经济性。
汽车传动轴设计
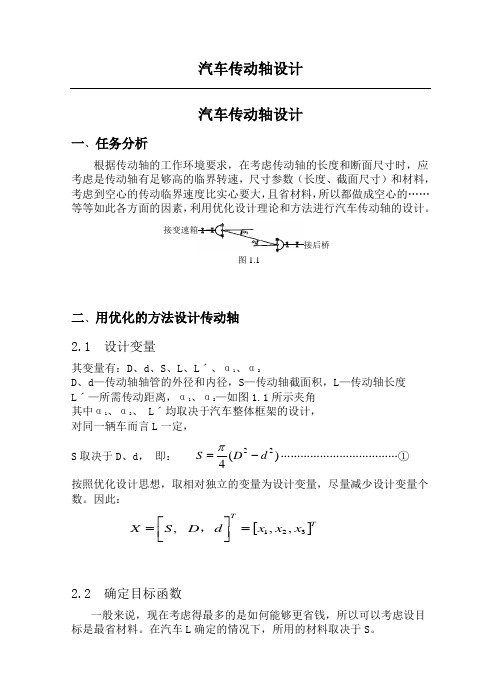
汽车传动轴设计一、任务分析根据传动轴的工作环境要求,在考虑传动轴的长度和断面尺寸时,应考虑是传动轴有足够高的临界转速,尺寸参数(长度、截面尺寸)和材料,考虑到空心的传动临界速度比实心要大,且省材料,所以都做成空心的…… 等等如此各方面的因素,利用优化设计理论和方法进行汽车传动轴的设计。
二、用优化的方法设计传动轴 2.1 设计变量其变量有:D 、d 、S 、L 、L ˊ、α1、α2D 、d —传动轴轴管的外径和内径,S —传动轴截面积,L —传动轴长度 L ˊ—所需传动距离,α1、α2—如图1.1所示夹角 其中α1、α2、 L ˊ均取决于汽车整体框架的设计, 对同一辆车而言L 一定, S 取决于D 、d , 即: )(422d D S -=π………………………………①按照优化设计思想,取相对独立的变量为设计变量,尽量减少设计变量个数。
因此:[]TTx x x d D S X 321,,,=⎥⎦⎤⎢⎣⎡=,2.2 确定目标函数一般来说,现在考虑得最多的是如何能够更省钱,所以可以考虑设目标是最省材料。
在汽车L 确定的情况下,所用的材料取决于S 。
接变速箱接后桥图1.1使S 的值在满足强度要求的情况下最小便成为了这次设计的目的。
即:)(4)(22d D x f -=π2.3 建立约束条件2.3.1传动轴应有足够高的临界转速临界转速:当传动轴的工作转速接近于其弯曲固有频率,即出现共振现象,所以通常将其弯曲固有频率对应的轴的速度称为临界转速。
若固有频率为f (Hz ) 则:k n =2πf rad/s=60 f r/minJ -抗弯惯性矩m kf π21=ρπLd D m ⋅-=)422(代入f 式,代入k n =60 f 整理后得2228102.1Ld D n k +⨯=设计传动轴时通常取0.2~2.1max=n n kn max -传动轴最高转速 m a x 222228353.152102.1n d D L d D n k ⋅≤+=+⨯=δ …………②δ—临界安全系数)(min x f 35384L EJ k =)(6444d D DJ -=π2.3.2传动轴应有足够的扭转强度设传动轴传递的最大转矩为Ts ,则截面上最大剪切应力[]τπτ≤-=⋅=)(16244max d D T D DI T s P s …………………………③ I p -极惯矩 32)(44d D I P -=π[]τ——许用应力,;2.3.3 传动轴应满足空心轴扭转失稳条件要求按最大扭转应力验算:2/3max )(292.0D d D E -≤τ……………………………………④E —传动轴材料的弹性模量,25/101.2mm N E ⨯=2.3.4 传动轴应满足制造工艺条件要求2.3≥-d D …………………………………………⑤ 2.3.5 传动轴外径尺寸不能过大可设 100≤D …………………………………………⑥ 根据以上的各条约束条件以及①式,可建立以下数学优化模型: []TTx x x d D S X 321,,,=⎥⎦⎤⎢⎣⎡=,)4)(min 22d D x f S -==(πmax 222228353.152102.1n d D L d D n k ⋅≤+=+⨯=δ[]τπτ≤-=⋅=)(16244max d D T D DI T s P s2/3max )(292.0Dd D E -≤τ 2.3≥-d D 100≤D三、优化算法的实现3.1优化设计理论优化设计方法是应用数学最优化远离解决实际问题的设计方法。
传动轴设计

Upe 许用不平衡量(g ·mm) M 传动轴质量(kg) G 平衡精度(mm/s) ω 角速度(rad/s) 2.4 传动轴布置角度 因十字轴万向节本身的不等速性,使传动轴部件产生扭转振动, 从而产生附加的交变载荷,影响零部件使用寿命。为改变这种不等速 性,而应尽量使传动轴两端万向节叉处于同一平面,使第一万向节两 轴间夹角与第二万向节两轴间夹角相等。 实际上变速箱输出轴和驱动 桥输入轴之间的相对位置是变动的,因此不可能设计夹角为零。但轴 间夹角越大,传动轴转动的不均匀性越大,产生的附加交变载荷也越 大,对传动件的使用寿命越不利,同时也降低传动效率,所以在汽车 总体布置上应尽量减小这些轴间交角。 轻型载货汽车设计的两轴线夹 角在空载静止时,一般不超过 6-8 度。
3 常见故障及解决方法 传动轴常见失效模型主要有以下几种: 3.1 传动轴管折 分析原因及解决方法:首选通过理论计算、试验及故障出现前后整车 的一现象来判断传动轴的失效原因, 出现该种失效模式多半是由扭矩 及临界转速引起的。 扭矩原因引起的传动轴失效模式多为轴管折或扭 成麻花,出现该现象时车速一般不高或在起步时,扭矩或冲击扭矩发 挥到最大。这时应采取加粗轴管的措施提高传动轴的承载扭矩。当由 临界转速原因导致该故障时,传动轴管多为扭成麻花,并且车速较高 行驶,当故障发生前整车会感觉到激烈的抖动。这时应采取将轴管加 粗管壁减薄的措施来提高传动轴的临界转速。当传动轴较长时,可采 取将传动轴分成两节来提高传动轴的临界转速。 3.2 十字轴滚针损坏 分析原因及解决方法:十字轴滚针损坏一般有以下几种原因:制造缺 陷、万向节间隙大、油封破损、注油不及时、万向节超负荷运转。当 万向节间隙较大时,会使传动轴动不平衡量值加大,出现该失效模式 一般在早期。这时要求厂家加强万向节质量控制。油封破损、注油不 及时都会导致万向节润滑不充分, 加剧轴承磨损, 导致滚针断裂失效。 这时应及时更换油封和按时注油,以使用润滑充分。万向节承载负荷 超过万向节的设计载荷时,会使用万向节的寿命大大缩小,导致滚针 失效。这时应从万向节结构、材料及工艺要求上做一些改进,以进一 步提高万向节的承载能力
- 1、下载文档前请自行甄别文档内容的完整性,平台不提供额外的编辑、内容补充、找答案等附加服务。
- 2、"仅部分预览"的文档,不可在线预览部分如存在完整性等问题,可反馈申请退款(可完整预览的文档不适用该条件!)。
- 3、如文档侵犯您的权益,请联系客服反馈,我们会尽快为您处理(人工客服工作时间:9:00-18:30)。
目录摘要 (2)第一章概述 (3)1万向传动轴设计要求 (3)第二章万向节结构方案分析 (3)1万向节分为刚性万向节和挠性万向节 (3)2准等速万向节 (4)3等速万向节 (5)第三章万向传动的运动和受力分析 (6)1单十字轴万向节传动 (6)2双十字轴万向节传动 (8)第四章传动轴结构分析与设计 (9)1轴的结构设计 (10)2轴的强度验算 (11)3键的选择 (12)4验算轴承寿命 (12)第五章结束语 (16)第六章参考文献 (17)第七章致谢信 (17)【摘要】:在普通优化设计的基础上,根据可靠性设计准则,将空心传动轴的应力及强度视为随机变量,建立起空心传动轴的可靠性优化设计模型,结合实例说明可靠性优化设计方法比传统设计方法更可靠、经济。
从机械振动理论出发,用可靠性设计中的联结方程,得出了其在常用工况下按传动轴的临界转速进行可靠性设计的公式.并以实例对传动轴按上述准则进行可靠性设计,结果传动轴的重量比原设计减少了436%,可靠性达到0.9999876以上.【关键词】: 万向节万向节传动轴第一章概述万向传动轴一般是由万向节、传动轴和中间支承组成。
主要用于在工作过程中相对位置不断改变的两根轴间传递转矩和旋转运动。
万向传动轴设计应满足如下基本要求:1.保证所连接的两根轴相对位置在预计范围内变动时,能可靠地传递动力。
2.保证所连接两轴尽可能等速运转。
3.由于万向节夹角而产生的附加载荷、振动和噪声应在允许范围内。
4.传动效率高,使用寿命长,结构简单,制造方便,维修容易等。
变速器或分动器输出轴与驱动桥输入轴之间普遍采用十字轴万向传动轴。
在转向驱动桥中,多采用等速万向传动轴。
当后驱动桥为独立的弹性,采用万向传动轴。
第二章万向节第结构方案分析第一节万向节分为刚性万向节和挠性万向节。
刚性万向节可分为不等速万向节(如十字轴式)、准等速万向节(如双联式、凸块式、三销轴式等)和等速万向节(如球叉式、球笼式等)。
不等速万向节是指万向节连接的两轴夹角大于零时,输出轴和输入轴之间以变化的瞬时角速度比传递运动的万向节。
准等速万向节是指在设计角度下工作时以等于1的瞬时角速度比传递运动,而在其它角度下工作时瞬时角速度比近似等于1的万向节。
输出轴和输入轴以等于1的瞬时角速度比传递运动的万向节,称之为等速万向节。
挠性万向节是靠弹性零件传递动力的,具有缓冲减振作用。
典型的十字轴万向节主要由主动叉、从动叉、十字轴、滚针轴承及其轴向定位件和橡胶密封件等组成。
十字轴万向节结构简单,强度高,耐久性好,传动效率高,生产成本低。
但所连接的两轴夹角不宜过大,当夹角由4°增至16°时,十字轴万向节滚针轴承寿命约下降至原来的1/4。
二、准等速万向节双联式万向节是由两个十字轴万向节组合而成。
为了保证两万向节连接的轴工作转速趋于相等,可设有分度机构。
偏心十字轴双联式万向节取消了分度机构,也可确保输出轴与输入轴接近等速。
双联式万向节的主要优点是允许两轴间的夹角较大(一般可达50°,偏心十字轴双联式万向节可达60°),轴承密封性好,效率高,工作可靠,制造方便。
缺点是结构较复杂,外形尺寸较大,零件数目较多。
图2-1三、等速万向节1.球叉式万向节球叉式万向节按其钢球滚道形状不同可分为圆弧槽和直槽两种形式。
圆弧槽滚道型的球叉式万向节(图4-1a)由两个万向节叉、四个传力钢球和一个定心钢球组成。
两球叉上的圆弧槽中心线是以O1和O2为圆心而半径相等的圆,O1和O2到万向节中心O的距离相等。
当万向节两轴绕定心钢球中心O转动任何角度时,传力钢球中心始终在滚道中心两圆的交点上,从而保证输出轴与输入轴等速转动。
球叉式万向节结构较简单,可以在夹角不大于32°~33°的条件下正常工作。
图2-2 球叉式万向节直槽滚道型球叉式万向节(图4-1b),两个球叉上的直槽与轴的中心线倾斜相同的角度,彼此对称。
在两球叉间的槽中装有四个钢球。
由于两球叉中的槽所处的位置是对称的,这便保证了四个钢球的中心处于两轴夹角的平分面上。
这种万向节加工比较容易,允许的轴间夹角不超过20°,在两叉间允许有一定量的轴间滑动。
图2-3 球叉式万向节 a)圆弧槽滚道型 b)直槽滚道型 万向节选择:由于传动轴的传递转矩大,承受冲击大,所连接的两轴转角不大,连接轴两轴转速相等,所以综合考虑选择准等速万向节。
第三章 万向传动的运动和受力分析一、单十字轴万向节传动当十字轴万向节的主动轴与从动轴存在一定夹角α时, 主动轴的角速度与从动轴的角速度 之间存在如下的关系;(3-1)由于cos 是周期为2 的周期函数,所以 也为 同周期的周期函数。
当 为0、 时, 达最大值 且为 ;当 为 /2、3 /2时, 有最小值 且为 。
因此,当主动轴以等角速度转动时,从动轴时快时慢,此即为普通十字轴万向节传动的不等速性。
十字轴万向节传动的不等速性可用转速不均匀系数k 来表示ααωωωtan sin 1min 2max 2=-=k 1ϕππαωcos /11ϕππ2ωmin 2ωαωcos 112/ωω2ωm ax 2ω1ω2ω12212cos sin cos ϕααωω=ππ如不计万向节的摩擦损失,主动轴转矩T1和从动轴转矩T2与各自相应的角速度有关系式:这样有:显然,当 小时,从动轴上最大的转矩为最大 当 最大时,从动轴上的转矩为最小 。
T1与 一定时,T2在其最大。
T1与值与最小值之间每一转变化两次。
附加弯曲力偶矩的分析 。
具有夹角 的十字轴万向节,仅在主动轴驱动转矩和从动轴反转矩的作用下是不能平衡的。
从万向节叉与十字轴之间的约束关系分析可知,主动叉对十字轴的作用力偶矩,除主动轴驱动转矩T1之外,还有作用在主动叉平面的弯曲力偶矩 。
同理,从动叉对十字轴也作用有从动轴反转矩T2和作用在从动叉平面的弯曲力偶矩 。
在这四个力矩作用下,使十字轴万向节得以平衡。
当主动叉 处 于0和时位置时(图3 -5a ),由于T1作用在十字轴平面,为零;而T2的作用平面与十字轴不共平面必有存在,且矢量T1垂直于矢量T2合矢量 +T2指向十字轴平面的法线方向与T1大小相等、方向相反。
这样,从动叉上的附加弯矩 =T1sin α。
(图3 -5a ),11222cos cos sin 1T T αϕα-=12/ωωαcos /1max 2T T =12/ωω2211ωωT T =αcos /1max 2T T =αα'1T '2T 1ϕ图3-5 十字轴万向节的力偶矩图3-5b ),同理可知 =0,主动叉上的附加弯矩 =T1tan α分析可知,附加弯矩的大小是在零与上述两最大值之间变化,其变化周期为,即每一转变化两次。
附加弯矩可引起与万向节相连零部件的弯曲振动,可在万向节主、从动轴支承上引起周期性变化的径向载荷,从而激起支承处的振动。
因此,为了控制附加弯矩,应避免两轴之间的夹角过大。
二、双十字轴万向节传动当输入轴与输出轴之间存在夹角α时,单个十字轴万向节的输出轴相对于输入轴是不等速旋转的。
为使处于同一平面的输出轴与输入轴等速旋转,可采用双万向节传动,但必须保证同传动轴相连的两万向节叉应布置在同一平面内,且使两万向节夹角α1与α2相等(图3-6)。
当输入轴与输出轴平行时图(3-6a ),直接连接传动轴的两万向节叉所受的附加弯矩,使传动轴发生如图3-6b 中双点划线所示的弹性弯曲,从而引起传动轴的弯曲振动。
图(3-6a )'2T图3-6 附加弯矩对传动轴的作用当输入轴与输出轴相交时(图3-6c),传动轴两端万向节叉上所受的附加弯矩方向相同,不能彼此平衡,传动轴发生如图3-6d中双点划线所示的弹性弯曲。
第四章传动轴结构分析与设计图4-1传动轴总成主要由传动轴及其两端焊接的花键和万向节叉组成。
传动轴中一般设有由滑动叉和花键轴组成的滑动花键,以实现传动长度的变化。
传动轴在工作时,其长度和夹角是在一定范围变化的。
设计时应保证在传动轴长度处在最大值时,花键套与轴有足够的配合长度;而在长度处在最小时不顶死。
传动轴夹角的大小直接影响到万向节的寿命、万向传动的效率和十字轴旋转的不均匀性。
在长度一定时,传动轴断面尺寸的选择应保证传动轴有足够的强度和足够高的临界转速。
所谓临界转速,就是当传动轴的工作转速接近于其弯曲固有振动频率时,即出现共振现象,以致振幅急剧增加而引起传动轴折断时的转速。
传动轴的临界转速nk (r/min )为式中,Lc 为传动轴长度(mm ),即两万向节中心之间的距离;dc 和Dc 分别为传动轴轴管的内、外径(mm )。
在设计传动轴时,取安全系数K=nk /n max=1.2~2.0,K=1.2用于精确动平衡、高精度的伸缩花键及万向节间隙比较小时,n max 为传动轴的最高转速(r/min )。
当传动轴长度超过1.5m 时,为了提高nk 以及总布置上的考虑,常将传动轴断开成两根或三根,万向节用三个或四个,而在中间传动轴上加设中间支承。
传动轴轴管断面尺寸除满足临界转速的要求外,还应保证有足够的扭转强度。
轴管的扭转切应力应满足 :式中,为许用扭转切应力,为300Mpa ;其余符号同前。
(一)轴的结构设计减速器中的轴是既受弯矩又受扭矩的转轴,比较精确的设计方法应该是按弯扭合成强度来计算各段轴径。
但当轴的支承距离未确定前,无法由强度决定轴径。
为解决这一矛盾,一般用初步估算的办法定出2228102.1cc c k Ld D n +⨯=[]c c c s c c d D T D τπτ≤-=)(1644最小轴径,然后按轴上零件的位置、考虑装配、加工工艺等因素,设计出阶梯轴的各段直径和长度;确定跨度后,再进一步进行强度验算。
传动轴材料的选择:综合考虑价格和材料的许用应力,选择45#钢。
见表4-3初估轴径可用两种方法:一是按轴受纯扭估算(请参考教材);另一方法是参照相近减速器的轴径,或按相配零件(如联轴器)的孔径及轴的结构要求(如齿轮轴或蜗轮轴的结构要求)等来确定轴的结构设计,应在初估轴径和初选滚动轴承型号后进行。
确定轴的各段直径和长度是阶梯轴结构设计的主要内容。
阶梯轴各段直径主要根据初估轴径、轴上零件的安装、固定及轴的加工工艺性等要求确定.阶梯轴各段的长度则由轴上零件的位置、配合长度及支承结构等因素决定.阶梯轴各段直径和长度的确定见表4-1、表4-2。
(二)轴的强度验算1.按弯扭合成强度进行轴的强度验算公式:(扭切应力)(正应力)轴的许用弯曲应力可用表4-3的推荐值。
2.按疲劳强度进行轴的精确验算对重要的轴还需要按疲劳强度进行轴的精确验算。
验算目的在于确定变应力情况下轴的安全程度。
通常选一个或几个危险断面进行验算,并按下式进行:式中:(S)—许用安全系数,式中各代号名称及确定方法见表4-4。