涡流探伤原理知识讲解
涡电流原理及探伤技术介绍

四、涡电流探伤检测技术
(一)涡电流传感器的基本工作原理 1.当把通有交变电流的线圈(激磁线圈)靠近 导电物体时,线圈产生的交变磁场会在导电体中感 应出涡电流,该涡电流的分布及大小除了与激磁条 件有关外,还与导电体本身的电导率、磁导率、导 电体的形状与尺寸、导电体与激磁线圈间的距离、 导电体表面或近表面缺陷的存在或组织变化等都 有密切关系.涡电流本身也要产生交变磁场。
二、涡电流的产生
1.涡电流产生的基本电路
2.交流电的振幅与相位
頻率:f × 106Hz 角頻率:ω=2πf=2π/T 單位時間所繞的徑度 (rad/s) 正弦波的交流電流:i=I0Sinωt i:交流電瞬時值 I0:交流電最大值,即振幅 ωt:表示在時間t,交流電之相位 同理正弦波的交流電壓亦可表示為 υ=V0Sinωt 若正弦波有一相角 i=I0Sin(ωt+θ)
3.涡电流产生机理
1.將载有交流电之激发线圈接近金属物体,使得金 属导体引发交流磁场,感应产生旋涡状电流。 2.产生的感应电流之振幅及相位會随导体特性(如导 电率、导磁系数)差异而变化,这些涡电流亦感应 交变磁场,以改变线圈之磁场。
三、涡电流在检测方面的应用
1、探伤:检测金属表面或次表面之瑕疵。 2、检测物性: (a)检测金属物理性质(如导电率)。 (b)识别、控制热处理及加工条件。 3、测量尺寸及定位: (a) 测量金属薄片及薄管厚度 (b) 测量涂层膜厚 (c) 精密测量微小尺寸变化
涡电流原理及探伤技术
刘国晖
一、什么是涡电流? 在圆柱形铁芯上绕有螺线管,通有交 变电流 I,随着电流的变化,铁芯内磁通 量也在不断改变。我们把铁芯看作由一层 一层的圆筒状薄壳所组成,每层薄壳都相 当于一个回路。由于穿过每层薄壳横截面 的磁通量都在变化着,因此,在相应于每 层薄壳的这些回路中都将激起感应电动势 并形成环形的感应电流。我们把这种电流 叫做涡电流。
涡流探伤仪工作原理

涡流探伤仪工作原理
涡流探伤仪是一种利用涡流感应的原理来检测材料缺陷的无损检测设备。
其工作原理如下:
1. 原理基础:
涡流感应是指当导体材料中有交变磁场通过时,会在导体内部产生一个涡流。
涡流的生成会消耗磁场能量,并且会产生电阻热。
当存在缺陷时,由于缺陷部位的形状和存在的电阻差异,涡流的形成和强度会发生改变,从而可以利用涡流的变化来检测缺陷。
2. 工作过程:
涡流探伤仪中的电磁线圈产生一个交变磁场,然后将待检测的导体材料放置在电磁线圈附近。
当交变磁场通过导体时,导体内部会产生一个相应的涡流。
涡流的形成会导致局部磁场发生变化。
3. 检测原理:
涡流探伤仪通过测量涡流感应产生的磁场变化来检测材料中的缺陷。
当涡流通过缺陷时,涡流的形状和强度会出现变化,进而改变磁场的分布。
探测器会测量并分析这些磁场变化,并将其转化为信号。
4. 缺陷探测:
根据不同的涡流变化情况,该仪器可以检测出导体材料中的各种缺陷,例如裂纹、异物、孔洞等。
通过对涡流变化的分析,可以确定缺陷的位置、形状、大小等信息。
综上所述,涡流探伤仪通过利用涡流感应的原理来检测导体材料中的缺陷。
通过测量磁场的变化,可以分析缺陷的特征,从而实现无损检测。
涡流探伤设备的原理和维护讲解
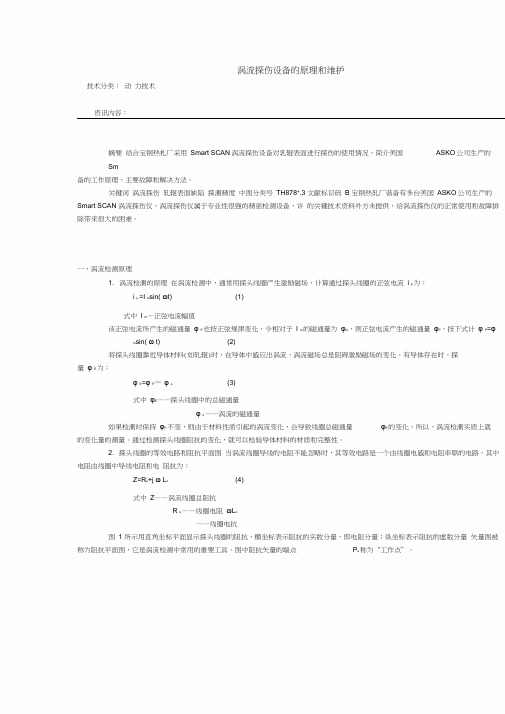
涡流探伤设备的原理和维护技术分类:动力技术资讯内容:摘要结合宝钢热札厂采用Smart SCAN涡流探伤设备对乳辊表面进行探伤的使用情况,简介美国ASKO公司生产的Sm备的工作原理、主要故障和解决方法。
关键词涡流探伤轧辊表面缺陷探测精度中图分类号TH878+.3 文献标识码B 宝钢热轧厂装备有多台美国ASKO公司生产的Smart SCAN 涡流探伤仪,涡流探伤仪属于专业性很强的精密检测设备,许的关键技术资料外方未提供,给涡流探伤仪的正常使用和故障排除带来很大的困难。
一、涡流检测原理1. 涡流检测的原理在涡流检测中,通常用探头线圈产生激励磁场,计算通过探头线圈的正弦电流i p 为:i p =I m sin( ωt) (1)式中I m—正弦电流幅值该正弦电流所产生的磁通量φP也按正弦规律变化,令相对于I m的磁通量为φm,则正弦电流产生的磁通量φP,按下式计φP=φωt) (2)m sin(将探头线圈靠近导体材料(如轧辊)时,在导体中感应出涡流,涡流磁场总是阻碍激励磁场的变化。
有导体存在时,探量φ E 为:φE=φP-φs (3)式中φE——探头线圈中的总磁通量φs ——涡流的磁通量如果检测时保持φP 不变,则由于材料性质引起的涡流变化,会导致线圈总磁通量φE的变化。
所以,涡流检测实质上就的变化量的测量。
通过检测探头线圈阻抗的变化,就可以检验导体材料的材质和完整性。
2. 探头线圈的等效电路和阻抗平面图当涡流线圈导线的电阻不能忽略时,其等效电路是一个由线圈电感和电阻串联的电路,其中电阻由线圈中导线电阻和电阻抗为:Z=R o+j ωL o (4)式中Z——涡流线圈总阻抗R o ——线圈电阻ωL o——线圈电抗图 1 所示用直角坐标平面显示探头线圈的阻抗,横坐标表示阻抗的实数分量,即电阻分量;纵坐标表示阻抗的虚数分量矢量图被称为阻抗平面图,它是涡流检测中常用的重要工具。
图中阻抗矢量的端点P o 称为“工作点”。
涡流探伤的基本原理
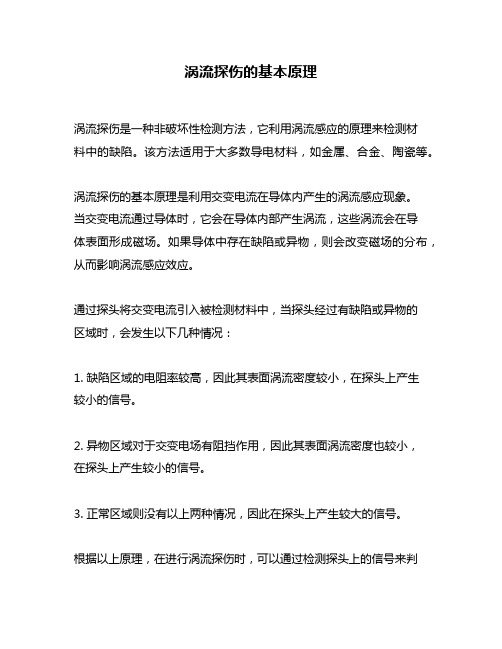
涡流探伤的基本原理涡流探伤是一种非破坏性检测方法,它利用涡流感应的原理来检测材料中的缺陷。
该方法适用于大多数导电材料,如金属、合金、陶瓷等。
涡流探伤的基本原理是利用交变电流在导体内产生的涡流感应现象。
当交变电流通过导体时,它会在导体内部产生涡流,这些涡流会在导体表面形成磁场。
如果导体中存在缺陷或异物,则会改变磁场的分布,从而影响涡流感应效应。
通过探头将交变电流引入被检测材料中,当探头经过有缺陷或异物的区域时,会发生以下几种情况:1. 缺陷区域的电阻率较高,因此其表面涡流密度较小,在探头上产生较小的信号。
2. 异物区域对于交变电场有阻挡作用,因此其表面涡流密度也较小,在探头上产生较小的信号。
3. 正常区域则没有以上两种情况,因此在探头上产生较大的信号。
根据以上原理,在进行涡流探伤时,可以通过检测探头上的信号来判断被检测材料中是否存在缺陷或异物。
此外,涡流探伤还可以通过改变交变电流的频率和幅度来适应不同材料和不同缺陷的检测需求。
涡流探伤具有以下优点:1. 非破坏性:涡流探伤不会对被检测材料造成任何损害。
2. 高灵敏度:涡流探伤可以检测到微小的缺陷和异物。
3. 高效率:涡流探伤可以快速地进行大面积的检测,提高生产效率。
4. 易于操作:涡流探伤设备简单易用,只需要经过简单的培训即可操作。
5. 可重复性好:由于涡流探伤是一种非破坏性方法,因此可以进行多次重复检测,以确保结果准确可靠。
总之,涡流探伤是一种非常有用的非破坏性检测方法,在工业生产和科学研究中得到了广泛应用。
通过深入理解其基本原理和优点,我们可以更好地利用这种方法来提高产品质量和生产效率。
第3章涡流探伤-精选(公开课件)

1
3.1涡流检测简介
3.1.1 涡流检测的基本原理
当载有交变电流的检测线圈靠近导电工件 时,由于线圈磁场的作用,工件中将会感生 出涡流(其大小等参数与工件中的缺陷等有 关),而涡流产生的反作用磁场又将使检测 线圈的阻抗发生变化。因此,在工件形状尺 寸及探测距离等固定的条件下,通过测定探 测线圈阻抗的变化,可以判断被测工件有无 缺陷存在。
8
3.2.2.3涡流检测线圈的 阻抗
涡流的大小影响激励线 圈的电流大小。若施加的 交变电压不变,这种影响 可等效于激励线圈的阻抗 发生了变化。
设Z0为没有试件时线圈 的等效阻抗,Zs为有试件 时反射到激励线圈上的附 加阻抗,则线圈的阻抗Z可 表示为:
R0:激励线圈的电阻; X0:激励线圈的电抗; Rs:反射电阻;
号处理器消除各种干扰信号,最后将有用的信号输
入显示器显示检测结果。
15
3.3.1.1 振荡器
振荡器的作用是给电桥电路提供电源, 当作为电桥桥臂的检测线圈移动到有缺陷 的部位时,电桥输出信号,信号经放大后 输入检波器进行相位分析,再经滤波和幅 度分析后,送到显示和记录装置。
16
3.3.1.2 检出电路
查表得:μeff实=0.9798,μeff虚=0.1216;
当f=1000Hz时,f/fg=10,
查表得:μeff实=0.4678,μeff虚=0.3494
对某非磁性材料进行涡流探伤时,已知ur=1,
f=2kHz,ρ=20x10-8Ω·m,请计算渗透深度值为 多少?(ρ是电阻率) 5mm
2
3.1.2涡流检测的特点
3.1.2.1 用途及影响感生涡流的主要因素
涡流探伤的磁饱和工作原理

涡流探伤的磁饱和工作原理第一篇:涡流探伤的磁饱和工作原理涡流探伤的磁饱和工作原理涡流检测适用于导电材料探伤,常见的金属材料可分为两大类:非铁磁性材料和铁磁性材料。
后者为铜、铝、钛及其合金和奥氏体不锈钢;前者为钢、铁及其合金。
它们的本质差别是材质磁导率μ约为1或远大于1。
在发电厂,除復水器等少量管道使用铜、钛、奥氏体不锈钢非铁磁性材料外,大量管道都采用钢管等铁磁性材料,典型的应用有省煤器、水冷壁等。
常规涡流探伤应用于非铁磁性管子,已是非常成熟的技术,它不单能探测出缺陷,并可以利用阻抗平面技术分析出缺陷所在的位置与深度。
然而,将它简单地应用于铁磁性材料的钢管,却得不到预期的结果,其原因何在?这是由于铁磁性材料μ>>1,根据涡流标准渗透公式:δ=503.3/√fμrσ 可知在这种情况下,涡流只能集中在表面,无法渗透到材料的内部。
除此以外,铁磁性材料的磁畴结构,将对涡流检测信号产生极大的干扰,足以把缺陷信号完全淹没,而无法得到有用的信息。
克服铁磁性金属磁导率对探伤影响的方法有两种:其一,采用远场涡流检测方法;其二,对钢管进行饱和磁化后再探伤。
前一种方法需要更新仪器,后一种方法只需在原有常规仪器的基础上增加磁饱和装置即可对钢管等进行探伤,具有投资少的优点。
经过磁饱和处理后的铁磁性材料可以以非铁磁材料对待。
通常钢管涡流探伤采用通过式磁饱和器。
它是由通有直流电的线圈来产生稳恒强磁场,并借助于导套等高导磁部件将磁场疏导到被检测钢管的探伤部位,使之达到磁饱和状态。
为了充分利用线圈产生的磁场,装置一般都有由铁磁性材料(如纯铁)制作的外壳。
由于纯铁的μ值很大,磁阻很小,泄漏在空间中的磁力线会被铁壳收集,也被疏导到钢管的检测部位。
由于强大的磁化电流通过磁饱和器线圈,会使线圈发热,因此要有良好导热措施,以防线圈烧毁。
磁饱和装置除了用来产生强大的直流磁场外,检测线圈也常常用它来夹持,所以磁饱和装置的结构与检测线圈的外形有着密切关系。
无损检测之钢轨探伤 课件 项目八 涡流探伤
涡流探伤设备的调试
焊缝探头检测融合线
轨底探头检测融合线
轨底及轨角边表面检查
校准过程
涡流探伤设备的调试
焊缝探头检测融合线
轨底探头检测融合线
轨底及轨角边表面检查
检测焊缝融合线(铝热焊在两边、闪光焊和气压焊在中间),探头融合线处扫查,分 别与钢轨平面成30°、60°和90°角,从轨头下颚圆弧处开始,划至轨腰,最后是轨底上表面,边走边观察屏幕,发现可疑波形和图像及时分析。
四、轨底及轨角边表面检查
调试界面
涡流探伤设备的调试
焊缝探头检测融合线
轨底探头检测融合线
轨底及轨角边表面检查
按F4报警菜单,进入报警界面(如左图),将报警1打开,深度1选择试块裂纹深度(深度与试块裂纹深度一致,如6mm)。按F1涡流检测菜单,进入检测界面(如右图),此时,涡流检测处于暂停状态。按检测按键,使仪器切换到运行检测状态。
时基因子
设置时基的扫描速度。值越大,扫描速度越快;反之,扫描速度越慢;范围为1~50。
消隐因子
设置信号在屏幕上保留的时间。数值越小,消隐得越快。范围1~100。
涡流探伤仪器结构
涡流探伤仪器界面
报警菜单
菜单
参数选项
备 注
报警
报警1
报警框1:开、关。
深度1
报警框1报警深度,范围为1mm~10mm。
涡流探伤设备的调试
焊缝探头检测融合线
轨底探头检测融合线
轨底及轨角边表面检查
检测焊缝融合线(铝热焊在两边、闪光焊和气压焊在中间),探头融合线处扫查,探 头分别与钢轨平面成30°、60°和90°角,从对侧轨底边开始,划至轨底中心,最后是本侧轨底边,边走边观察屏幕,发现可疑波形和图像及时分析。
涡流检测—涡流检测基本原理(无损检测课件)
第2节 涡流检测的基本原理
原理
原理:当载有交变电流的线圈接近被检工件时,材料表面与近 表面会感应出涡流,其大小、相位和流动轨迹与被检工件的电 磁特性和缺陷等因素有关,涡流产生的磁场作用会使线圈阻抗 发生变化,测定线圈阻抗即可获得被检工件物理、结构和冶金 状态等信息。
第2节 涡流检测的基本原理
2. 涡流检测的特点
➢ (1ቤተ መጻሕፍቲ ባይዱ适用于各种导电材质的试件探伤。包括各种钢、钛、 镍、铝、铜及其合金。
➢ (2)可以检出表面和近表面缺陷。 ➢ (3)探测结果以电信号输出,容易实现自动化检测。 ➢ (4)由于采用非接触式检测,所以检测速度很快。 ➢ (5)不需接触工件也不用耦合介质,所以可以进行高温
在线检测。
2. 涡流检测的特点
➢ (6)形状复杂的试件很难应用。因此一般只用其检测管 材,板材等轧制型材。
➢ (7)不能显示出缺陷图形,因此无法从显示信号判断出 缺陷性质。
➢ (8)各种干扰检测的因素较多,容易引起杂乱信号。 ➢ (9)由于集肤效应,埋藏较深的缺陷无法检出 ➢ (10)不能用于不导电材料的检测。
涡流探伤仪的原理 涡流探伤仪工作原理
涡流探伤仪的原理涡流探伤仪工作原理涡流探伤仪是用于金属在线、离线探伤的新一代涡流设备。
它接受了先进的数字电子技术以及微机技术,操作简单、便利。
为用户供应牢靠、稳定的操作平台,具备高灵敏的性能指标。
涡流探伤仪基本原理:涡流检测是以电磁感应为基础的,它的基本原理可以描述为:当载有交变电流的检测线圈靠近导电试件时,由于线圈中交变的电流产生交变的磁场,从而试件中会感生出涡流。
涡流的大小、相位及流动形式受到试件导电性能等的影响,而涡流的反作用磁场又使检测线圈的阻抗发生变化,因此,通过测定检测线圈阻抗的变化,就可以得出被测试件的导电性差别及有无缺陷等方面的结论。
具有相对独立的检测通道,可分别连接不同规格的检测探头,用于同时检测金属纵向裂纹或横向缺陷(如驳口)的缺陷信号,因此,该仪器特别适用于在线以及离线检测,并且可以在无磁饱和器的条件下进行调试检测。
接受计算机中英文菜单人机对话,大屏幕双踪信号显示,多模式报警技术,以及独特的数字电子平衡技术,使得仪器操作更加简单、牢靠。
智能金属涡流探伤仪具有64Hz~2MHz测试频率范围,能够适用于各种不同金属的检测要求,并且由于接受全数字化设计,因此,能够在仪器内建立标准检测程序,便利用户在改换金属管道规格时快捷调用。
可配耦合间隙要求很低的穿过式探头,亦可配接只有香烟盒大小的组合式平面探头,探头的选择完全依据用户的检测要求而定,且仪器能够适用于几乎全部厂家生产的涡流探头。
此外,仪器可配置高精度延时打标模块,实现在线自动探伤。
涡流探伤仪的原理涡流探伤仪是用于金属在线、离线探伤的新一代涡流设备。
它接受了先进的数字电子技术以及微机技术,操作简单、便利。
为用户供应牢靠、稳定的操作平台,具备高灵敏的性能指标。
涡流探伤仪基本原理:涡流检测是以电磁感应为基础的,它的基本原理可以描述为:当载有交变电流的检测线圈靠近导电试件时,由于线圈中交变的电流产生交变的磁场,从而试件中会感生出涡流。
涡流的大小、相位及流动形式受到试件导电性能等的影响,而涡流的反作用磁场又使检测线圈的阻抗发生变化,因此,通过测定检测线圈阻抗的变化,就可以得出被测试件的导电性差别及有无缺陷等方面的结论。
涡流探伤原理
涡流探伤原理涡流探伤是一种常用的无损检测方法,它通过利用涡流感应原理来检测材料中的缺陷和异物。
涡流探伤原理的核心是利用交变磁场产生涡流,通过检测涡流感应电阻的变化来判断材料是否存在缺陷。
本文将从涡流探伤的基本原理、应用领域和优缺点等方面进行介绍。
涡流探伤的基本原理是利用交变磁场在导体中产生涡流的现象。
当导体材料表面存在缺陷或异物时,其导电性会发生变化,从而影响涡流感应电阻的大小。
通过测量涡流感应电阻的变化,可以判断材料中的缺陷情况。
涡流探伤可以对导电性材料进行检测,如金属、合金等,对于非导电性材料则需要进行表面导电处理后才能进行检测。
涡流探伤在航空航天、汽车制造、铁路运输、核工业等领域有着广泛的应用。
在航空航天领域,涡流探伤常用于飞机发动机叶片、机身结构等零部件的缺陷检测,可以及时发现隐藏在材料内部的裂纹、气孔等缺陷,确保飞机的安全飞行。
在汽车制造领域,涡流探伤可以用于发动机零部件、制动系统等的缺陷检测,提高汽车的质量和安全性。
涡流探伤的优点是检测速度快、无损伤、对表面涂层无影响,可以实现自动化检测,提高工作效率。
然而,涡流探伤也存在一些局限性,如只能检测表面附近的缺陷,不能检测材料内部的缺陷;对于非导电性材料需要进行特殊处理才能进行检测;对材料的形状和尺寸有一定的要求。
总的来说,涡流探伤是一种非常有效的无损检测方法,可以广泛应用于工业生产中,帮助生产企业提高产品质量,确保产品安全。
随着科学技术的不断发展,涡流探伤技术也在不断完善,相信在未来会有更多的应用场景和更高的检测精度。
通过本文的介绍,相信读者对涡流探伤的原理、应用领域和优缺点有了更深入的了解。
涡流探伤作为一种重要的无损检测方法,对于工业生产具有重要的意义,希望能够得到更广泛的应用和进一步的发展。
- 1、下载文档前请自行甄别文档内容的完整性,平台不提供额外的编辑、内容补充、找答案等附加服务。
- 2、"仅部分预览"的文档,不可在线预览部分如存在完整性等问题,可反馈申请退款(可完整预览的文档不适用该条件!)。
- 3、如文档侵犯您的权益,请联系客服反馈,我们会尽快为您处理(人工客服工作时间:9:00-18:30)。
涡流探伤原理
涡流无损检测原理
最佳答案
涡流检测是建立在电磁感应原理基础之上的一种无损检测方法,它适用于导电材料。
当把一块导体置于交变磁场之中,在导体中就有感应电流存在,即产生涡流。
由于导体自身各种因素(如电导率、磁导率、形状,尺寸和缺陷等)的变化,会导致涡流的变化,利用这种现象判定导体性质,状态的检测方法,叫涡流检测。
至于区别,每一种检测方法都有它的局限性,要根据被检工件来选择检测方法,涡流检测适用于导电材料的金属表面缺陷检测,一般都用来检测小管子的,出场的时候都要检测的。
涡流检测的特点(Eddy-current testing)
ET是以电磁感应原理为基础的一种常规无损检测方法,使用于导电材料。
一、优点
1、检测时,线圈不需要接触工件,也无需耦合介质,所以检测速度快。
2、对工件表面或近表面的缺陷,有很高的检出灵敏度,且在一定的范围内具有良好的线性指示,可用作质量管理与控制。
3、可在高温状态、工件的狭窄区域、深孔壁(包括管壁)进行检测。
4、能测量金属覆盖层或非金属涂层的厚度。
5、可检验能感生涡流的非金属材料,如石墨等。
6、检测信号为电信号,可进行数字化处理,便于存储、再现及进行数据比较和处理。
二、缺点
1、对象必须是导电材料,只适用于检测金属表面缺陷。
2、检测深度与检测灵敏度是相互矛盾的,对一种材料进行ET时,须根据材质、表面状态、检验标准作综合考虑,然后在确定检测方案与技术参数。
3、采用穿过式线圈进行ET时,对缺陷所处圆周上的具体位置无法判定。
4、旋转探头式ET可定位,但检测速度慢。
涡流检测是运用电磁感应原理,将载有正弦波电流激励线圈,接近金属表面时,线圈周围的交变磁场在金属表面感应电流(此电流称为涡流)。
也产生一个与原磁场方向相反的相同频率的磁场。
又反射到探头线圈,导致检测线圈阻抗的电阻和电感的变化,改变了线圈的电流大小及相位。
因此,探头在金属表面移动,遇到缺陷或材质、尺寸等变化时,使得涡流磁场对线圈的反作用不同,引起线圈阻抗变化,通过涡流检测仪器测量出这种变化量就能鉴别金属表面有无缺陷或其它物理性质变化。
涡流检测实质上就是检测线圈阻抗发生变化并加以处理,从而对试件的物理性能作出评价。