微电子工艺原理- 第6讲 薄膜工艺 3
哈工大微电子工艺(3)----第七章外延

综合效果
7.3.3减小自掺杂效应措施
降低外延温度, 采用SiH2Cl2, SiHCl3;或SiH4, 降低外延温度,p-Si采用 采用 但这对As的自掺杂是无效 的自掺杂是无效。 但这对 的自掺杂是无效。 对于n-Si衬底,用蒸气压低、扩散速率也低的锑作为 衬底, 对于 衬底 用蒸气压低、 埋层杂质,但锑难以达到很高的掺杂浓度。 埋层杂质,但锑难以达到很高的掺杂浓度。 重掺杂的衬底,用轻掺杂的硅来密封其底面和侧面, 重掺杂的衬底,用轻掺杂的硅来密封其底面和侧面, 减少杂质外逸。 减少杂质外逸。 低压外延可减小自掺杂,这对砷,磷的效果显著, 低压外延可减小自掺杂,这对砷,磷的效果显著,对 硼的作用不明显。 硼的作用不明显。 用离子注入的埋层来降低衬底表面的杂质浓度。 用离子注入的埋层来降低衬底表面的杂质浓度。 可在埋层或衬底上先生长未掺杂的薄膜来避免衬底中 的杂质外逸,再原位掺杂。 的杂质外逸,再原位掺杂。 避免高温下用HCl对衬底进行腐蚀、或腐蚀后用低温 对衬底进行腐蚀、 避免高温下用 对衬底进行腐蚀 气流除去因腐蚀外逸的杂质。 气流除去因腐蚀外逸的杂质。
SiCl4摩尔浓度 大于0.27出现 大于 出现 腐蚀现象
7.3 外延层中的杂质分布
掺杂采用原位气相掺杂。 掺杂采用原位气相掺杂。 杂质掺入效率依赖于: 杂质掺入效率依赖于:生 长温度、生长速率、 长温度、生长速率、气流 中掺杂剂相对于硅源的摩 尔数、反应室几何形状, 尔数、反应室几何形状, 掺杂剂自身特性。 掺杂剂自身特性。 有杂质再分布现象
扩散效应 自掺杂效应
7.3.1 扩散效应
扩散效应也叫互(或外 扩散, 扩散效应也叫互 或外) 扩散,指在 或外 衬底中的杂质与外延层中的杂质在 外延生长时互相扩散, 外延生长时互相扩散,引起衬底与 外延层界面附近的杂质浓度缓慢变 化的现象。 化的现象。 若杂质扩散速率远小于外延生长速 衬底中的杂质向外延层中扩散, 率,衬底中的杂质向外延层中扩散, + +对应 对应n/n (p/p+) 对应 或外延层中杂质向衬底中的扩散, 或外延层中杂质向衬底中的扩散, 都如同在半无限大的固体中的扩散。 都如同在半无限大的固体中的扩散。 +(n/p+) -对应 对应p/n 对应 当衬底和外延层都掺杂时, 当衬底和外延层都掺杂时,外延层 中最终杂质分布
薄膜的工艺原理

薄膜的工艺原理薄膜工艺是一种制备薄膜材料的技术方法,通过将材料沉积在基底上形成薄膜。
这种技术广泛应用于电子器件、光学器件、太阳能电池等领域。
薄膜工艺主要包括物理蒸发、化学气相沉积、溅射和激光热解等几种不同的方法。
本文将详细介绍薄膜工艺的原理及其应用。
首先,物理蒸发是一种将材料以气态形式沉积在基底上的方法。
这种方法通常利用电子束蒸发、磁控溅射或激光蒸发等方式将材料加热到高温,使其形成气态,并在真空环境中使其沉积在基底上。
由于物理蒸发过程中材料处于高能态,因此薄膜具有高纯度、致密的特点。
物理蒸发除了可以制备金属薄膜外,还可以制备氧化物薄膜、硫化物薄膜等。
其次,化学气相沉积是一种将气态试剂在基底上发生化学反应生成薄膜的方法。
化学气相沉积通常利用载气将气态试剂输送到基底上,并在基底表面发生化学反应,形成所需的薄膜。
化学气相沉积可以制备多种薄膜材料,如金属薄膜、氧化物薄膜、氮化物薄膜等。
化学气相沉积具有高生长速率、较好的均匀性和良好的控制性能。
再次,溅射是一种利用离子轰击的方法使材料从靶点上剥离并沉积在基底上的方法。
溅射可以通过直流溅射、射频溅射或磁控溅射等方式进行。
在溅射过程中,离子轰击靶材使其失去原子,这些原子以高能态迅速扩散并沉积在基底上。
通过调整溅射过程中离子轰击能量和靶材的成分,可以得到所需的材料薄膜。
溅射可以制备金属薄膜、合金薄膜、氧化物薄膜等。
最后,激光热解是一种利用激光照射材料使其发生热解反应并沉积在基底上的方法。
激光热解可以通过激光脉冲击穿材料表面,产生高能态的离子和原子,然后沉积在基底上。
激光热解具有高分辨率、高制备速率和良好的控制性能。
激光热解可以制备金属薄膜、碳化物薄膜、氮化物薄膜等。
薄膜工艺在很多领域都有广泛应用。
在电子器件制备中,薄膜可以用于制备电极、蓄电池、显示器件等。
在光学器件制备中,薄膜可以用于制备反射镜、透镜、滤光片等。
在太阳能电池制备中,薄膜可以用于制备光伏层和透明导电层。
微电子工艺课件第六章

在由质量输运速度控制的淀积过程中,对温度的控制不必 很严格,因为控制薄膜淀积速率的是质量输运过程,质量输 运过程对温度的依赖性非常小。而各硅片所有位臵的反应剂 浓度应当相等就显得非常重要,应严格控制。
16
四、表面化学反应控制过程
右图给出由实验中得到的硅膜 淀积速率与温度倒数的关系。 在低温条件下.薄膜淀积速率 与温度之间遵循着指数关系。随着 温度的上升,淀积速率也随之加快, 这是因为在低温下,hg>>ks,淀积 速率由ks限制,而ks随着温度 的升高而变大。 但随着温度的上升,淀积速率 对温度的敏感程度不断下降。当温 度高过某个值之后.淀积速率趋向 于稳定,淀积速率由通过边界层输 运到表面的反应剂速率所决定,而 hg值对温度不太敏感。
1
目 录
6.1、CVD模型
6.2、化学气相沉积系统
6.3、CVD多晶硅的特性和沉积方法
6.4、CVD二氧化硅的特性和沉积方法
6.5、CVD氮化硅的特性和沉积方法
6.6、金属的化学气相沉积
2
6.1 CVD模型
6.1.1 CVD的基本过程
化学气相沉积的主要步骤:
(1)反应剂气体(或被惰性气体 稀释的反应剂) 以合理的流速被 输送到反应室内,气流从入口 进入反应室并以平流形式向出口流动,平流区也称为主气流区,其 气体流速是不变的,如上图所示。 (2)反应剂从主气流区以扩散方式通过边界层到达衬底表面,边界 层是主气流区与硅片表面之间气流速度受到扰动的气体薄层。 (3)反应剂被吸附在硅片的表面,成为吸附原子(分子)。 (4)吸附原子(分子)在衬底表面发生化学反应,生成薄膜的基本元 素并淀积成薄膜。 (5)化学反应的气态副产物和未反应的反应剂离开衬底表面,进入 主气流区被排出系统。
集成电路中的薄膜技术与工艺

集成电路中的薄膜技术与工艺1引言薄膜技术是集成电路(IC)制造中的一种关键技术。
它是指将层状材料以较薄的方法涂敷于芯片表面,形成各种不同的电路元器件与线路。
薄膜技术的应用范围十分广泛,包括电容器、电阻器、电感器、场效应晶体管等等。
同时,薄膜技术也是IC制造中非常重要的工艺之一,为芯片的高度集成提供了技术保障。
本文将就薄膜技术及其工艺进行详细介绍。
2薄膜技术薄膜技术是以各种材料为基础,采用化学气相沉积(CVD)、物理气相沉积(PVD)和溶液沉积等方法将膜状材料涂敷于芯片表面的制造技术。
薄膜技术的制造精度高、制造的电路器件稳定性好,被广泛应用于各种电路元器件的制造中。
薄膜材料的种类众多,常用的薄膜材料有SiO2、SiNx、Ti、Al、Mo等。
这些材料经过各种化学或物理方法,形成较薄的均匀层状结构,提供制造各种高精度电路元器件的基础。
薄膜技术的应用范围广泛。
比如,在电容器制造中,利用薄膜技术在芯片表面涂上金属电极,然后将电介质材料(SiO2、SiNx等)涂敷在金属电极上,形成一定厚度的电介质层,最终形成高精度的电容器;在电阻器制造中,利用薄膜技术将SiO2沉积在金属线路上,然后控制SiO2的厚度,调节电阻器的阻值等等。
3薄膜制造方法薄膜技术的制造方法包括化学气相沉积(CVD)、物理气相沉积(PVD)和溶液沉积等方法。
CVD是将制造层状材料所需的原料气体通过化学反应,在芯片表面进行反应,产生需要的薄膜材料的过程。
CVD方法具有高制造精度和高稳定性的特点。
具体操作上,将适量的气体原料(比如SiCl4)引入反应室,然后加热至高温,待原料在高温下分解并反应,使沉积到芯片表面,形成所需的薄膜材料。
PVD是用强流电子束、离子束或溅射法将薄膜材料通过物理方式沉积到芯片表面的方法。
PVD方法具有沉积速度快、晶体结构致密的特点。
这种方法经常被用于金属材料的制造过程中。
具体操作上,通过一定的电场作用,加速金属原子并喷向芯片基板表面,经过一系列物理化学反应,形成所需的金属薄膜。
微电子工艺原理-第6讲薄膜工艺物理气相淀积共68页

/隔膜的机械运动将 气体正向移位 有三步骤:捕捉气 体-压缩气体-排出 气体 压缩比
23
旋片泵 旋片泵主要由定子、转
子、旋片、定盖、弹簧等零件组 成。
其结构是利用偏心地装在定子腔 内的转子和转子槽内滑动的借助 弹簧张力和离心力紧贴在定子内 壁的两块旋片,当转子旋转时, 始终沿定子内壁滑动。
2
•饱和蒸汽压P 在一定温度下真空室内蒸发物质的 蒸汽与固态或液态平衡时所表现出来的压力
•蒸发温度 在饱和蒸汽压为133.3*10-2Pa时所对应的 物质温度
17
蒸发速率 蒸发 速率和温度、蒸 发面积、表面的 清洁程度、加热 方式有关,工程 上将源物质、蒸 发温度和蒸发速 率之间关系绘成 为诺漠图。
21
气体传导率C
C Q P1 P2
C与电导率一样并联相加;串联时倒数相加 若大量气体流过真空系统,要保持腔体压
力接近泵的压力,就要求真空系统有大的 传导率----管道直径;泵放置位置
•泵的抽速Sp----体积置换率
Sp
Q Pp
ቤተ መጻሕፍቲ ባይዱ
dνp dt
29.09.2019
泵入口压力
22
1.3真空泵
化学汽相淀积(CVD)(常压 CVD、低压 CVD、等离子 增强 CVD、汽相外延等)
外延生长(同质外延、异质外延、正外延、反外延)
29.09.2019
2
薄膜的生长三阶段
晶核的形成
聚集成束
形成连续膜
29.09.2019
3
薄膜特性要求
1、台阶的覆盖能力 2、低的膜应力 3、高的深宽比间隙填充能力 4、大面积薄膜厚度的均匀性 5、大面积薄膜的介电\电学\折射率特性 6、高纯度和高密度 7、与衬底或下层膜有好的粘附能力
【2024版】微电子工艺之薄膜技术

二、外延掺杂及杂质再分布
3.杂质再分布
再分布:外延层中的杂质向衬底扩散;
衬底中的杂质向外延层扩散。
总杂质浓度分布:各自扩散的共同结果。
①衬底杂质的再分布(图3-21)
初始条件:N2(x,0)=Nsub,x<0; N2(x,0)=0,x>0; 边界条件一:衬底深处杂质浓度均匀,即
当vt» D1t 时,有
N1x,t
Nf 2
erfc
2
x D1t
二、外延掺杂及杂质再分布
当vt»2 D1t 时,有
N1(x,t)≈Nf
③总的杂质分布(图3-24)
N(x,t)=N1(x,t)± N2(x,t) “+”: 同一导电类型;
“-”:相反导电类型;
三、自掺杂(非故意掺杂)
1.定义
N 2 x
x 0
二、外延掺杂及杂质再分布
边Jd界条D件2 二Nx:2 在xx外f 延J层b 表J s面 (h2x=vxfN)2 ,扩x f 散,t 流密度Jd为
解得:
N2x,t
N sub 2
erfc
2
x D2 t
v h2 2h2
v
ex
p
D2
vt
x erfc
2vt x 2 D2t
①当hG» ks,则 NGS≈NG0,V= ks(NT/ NSi) Y,是表面反 应控制。
②当ks» hG,则 NGS ≈0, V= hG(NT/ NSi) Y,是质量转 移控制。
二、外延掺杂及杂质再分布
1. 掺杂原理-以SiH4-H2-PH3为例
工学第六章薄膜工艺课件

约为10-3Torr,铝的密度2.7g/cm3,半径40cm,代入上式得:源自R d=17.4埃 /min
作业
• 希望用一台单源蒸发台淀积Ga和Al的混合 物,如果淀积温度是1000℃,坩埚内的初 始混合物是1:1,两种成分黏滞系数都为1, 则蒸发初期膜的组成将是怎样?膜的组成 如何随时间变化?
1.4 物理淀积-溅射
简单平行板溅射系统腔体 晶片上形成薄膜。
离子入射到到晶片表面时,可能产生的结果
反射:入射离子能量很 低;
吸附:入射离子能量小 于10eV; 离子注入:入射离子能 量大于10KeV; 溅射:入射离子能量为 10 - 10KeV 。 一 部 分 离 子能量以热的形式释放; 一部分离子造成靶原子 溅射。
高真空
10-8 - 10-4 Torr 10-6 -10-2 Pa
超高真空 <10-8 Torr
<10-6 Pa
真空泵
1. 真空的产生要依靠真空泵。而在低真空和高真 空情形下,要分别使用不同的泵。
2. 低真空下一般使用机械泵,其抽真空过程可以 分为三个步骤:捕捉气体,压缩气体,排除气 体。比如:活塞泵,旋转叶片真空泵,罗茨泵 等。
• 溅射的物理机制:是利用等离子体中的离 子对靶材料进行轰击,靶材料原子或原子 团被发射出来,堆集在晶片衬底上形成薄 膜。
• 与蒸发工艺相比:台阶覆盖性好,容易制 备合金或复合材料薄膜。
靶-接负极
晶片-置于正极
进气-氩气(用于产生等离 子)
工作原理:高压产生等离子 体之后,正离子在电场作用 下向负极运动,轰击靶电极, 激发出来的二次电子向正极 运动,维持等离子体。而被 轰击出来的靶原子则堆集在
• 温度:实际上确定了蒸气压。温度越高,蒸气压 越大,淀积速率越快,但需要控制淀积速率不能 太大,否则会造成薄膜表面形貌变差。
薄膜生产工艺(3篇)
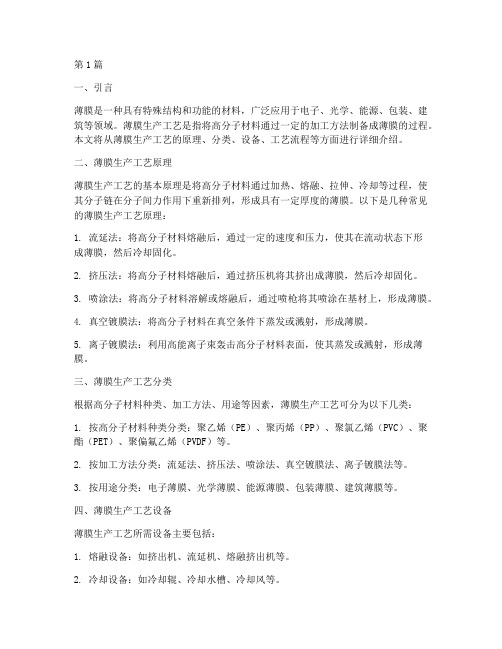
第1篇一、引言薄膜是一种具有特殊结构和功能的材料,广泛应用于电子、光学、能源、包装、建筑等领域。
薄膜生产工艺是指将高分子材料通过一定的加工方法制备成薄膜的过程。
本文将从薄膜生产工艺的原理、分类、设备、工艺流程等方面进行详细介绍。
二、薄膜生产工艺原理薄膜生产工艺的基本原理是将高分子材料通过加热、熔融、拉伸、冷却等过程,使其分子链在分子间力作用下重新排列,形成具有一定厚度的薄膜。
以下是几种常见的薄膜生产工艺原理:1. 流延法:将高分子材料熔融后,通过一定的速度和压力,使其在流动状态下形成薄膜,然后冷却固化。
2. 挤压法:将高分子材料熔融后,通过挤压机将其挤出成薄膜,然后冷却固化。
3. 喷涂法:将高分子材料溶解或熔融后,通过喷枪将其喷涂在基材上,形成薄膜。
4. 真空镀膜法:将高分子材料在真空条件下蒸发或溅射,形成薄膜。
5. 离子镀膜法:利用高能离子束轰击高分子材料表面,使其蒸发或溅射,形成薄膜。
三、薄膜生产工艺分类根据高分子材料种类、加工方法、用途等因素,薄膜生产工艺可分为以下几类:1. 按高分子材料种类分类:聚乙烯(PE)、聚丙烯(PP)、聚氯乙烯(PVC)、聚酯(PET)、聚偏氟乙烯(PVDF)等。
2. 按加工方法分类:流延法、挤压法、喷涂法、真空镀膜法、离子镀膜法等。
3. 按用途分类:电子薄膜、光学薄膜、能源薄膜、包装薄膜、建筑薄膜等。
四、薄膜生产工艺设备薄膜生产工艺所需设备主要包括:1. 熔融设备:如挤出机、流延机、熔融挤出机等。
2. 冷却设备:如冷却辊、冷却水槽、冷却风等。
3. 拉伸设备:如拉伸机、拉伸辊等。
4. 收卷设备:如收卷机、收卷辊等。
5. 辅助设备:如预热装置、输送装置、切割装置等。
五、薄膜生产工艺流程以下是常见的薄膜生产工艺流程:1. 原料准备:根据所需薄膜的规格、性能要求,选择合适的高分子材料。
2. 熔融:将高分子材料加热至熔融状态。
3. 流延/挤压:将熔融的高分子材料通过流延机或挤压机,形成薄膜。
- 1、下载文档前请自行甄别文档内容的完整性,平台不提供额外的编辑、内容补充、找答案等附加服务。
- 2、"仅部分预览"的文档,不可在线预览部分如存在完整性等问题,可反馈申请退款(可完整预览的文档不适用该条件!)。
- 3、如文档侵犯您的权益,请联系客服反馈,我们会尽快为您处理(人工客服工作时间:9:00-18:30)。
2020-08-02
5
CVD技术不仅成为半导体超纯硅原料—超纯多晶硅生 产的唯一方法,而且也是硅单晶外延、砷化镓等Ⅲ~ Ⅴ旋半导体和Ⅱ~Ⅵ旋半导体单晶外延的基本生产方 法。
在集成电路生产中更广泛的使用CVD技术沉积各种掺 杂的半导体单晶外延薄膜、多晶硅薄膜、半绝缘的掺 氧多晶硅薄膜;绝缘的二氧化硅、氮化硅、磷硅玻璃、 硼硅玻璃薄膜以及金属钨薄膜等。
前苏联Deryagin Spitsyn和Fedoseev等在20世 纪70年代引入原子氢开创了激活低压CVD金刚 石薄膜生长技术,80年代在全世界形成了研究 热潮,也是CVD领域一项重大突破。CVD技术 由于采用等离子体、激光、电子束等辅助方法 降低了反应温度,使其应用的范围更加广阔。
2020-08-02
8
中国CVD技术生长高温超导体薄膜和CVD基础理论方面 取得了一些开创性成果。
Blocher 在 1997 年 称 赞 中 国 的 低 压 CVD(low pressure chemical型的信中说: “这样的理论模型研究不仅仅在科学意义上增进了这项 工艺技术的基础性了解,而且引导在微电子硅片工艺应 用中生产效率的显著提高。”
2020-08-02
14
CVD技术的基本要求
为适应CVD技术的需要,选择原料、产物及反应类型 等通常应满足以下几点基本要求:
(1)反应剂在室温或不太高的温度下最好是气态或有较 高的蒸气压而易于挥发成蒸汽的液态或固态物质,且 有很高的纯度;
2020-08-02
12
这是一种制造器件的半导体材料的系统,生长温度低 (425~600℃),但真空度要求小于1.33×10Pa,系统 的设计制造比分子束外延(MBE)容易,其主要优点是能 实现多片生长。
此外,化学气相沉积制膜技术还有射频加热化学气相 沉 积 (RF/CVD) 、 紫 外 光 能 量 辅 助 化 学 气 相 沉 积 (UV/CVD)等其它新技术不断涌现。
2020-08-02
11
随着激光的广泛应用,激光在气相沉积上也都 得到利用,激光气相沉积(LCVD)通常分为热解 LCVD和光解LCVD两类,主要用于激光光刻、 大规模集成电路掩膜的修正以及激光蒸发-沉 积。
在向真空方向发展方面在向真空方向发展方面, 出现了超高真空/化学气相沉(UHV/CVD)法。
在制造各类特种半导体器件中,采用CVD技术生长发 光器件中的磷砷化镓、氮化镓外延层等,硅锗合金外 延层及碳化硅外延层等也占有很重要的地位。
2020-08-02
6
在集成电路及半导体器件应用的CVD技术方面, 美国和日本,特别是美国占有较大的优势。
日本在蓝色发光器件中关键的氮化镓外延生长 方面取得突出进展,以实现了批量生产。
1968年K .Masashi等首次在固体表面用低汞灯 在P型单晶硅膜,开始了光沉积的研究。
1972年Nelson和Richardson用CO2激光聚焦束 沉积出碳膜,从此发展了激光化学气相沉积的 工作。
2020-08-02
7
继Nelson后,美国S. D. Allen,Hagerl等许多学 者采用几十瓦功率的激光器沉积SiC、Si3N4等非 金属膜和Fe、Ni、W、Mo等金属膜和金属氧化 物膜。
2020-08-02
13
4.2.1化学气相沉积法的概念 化学气相沉积乃是通过化学反应的方式,利用加
热、等离子激励或光辐射等各种能源,在反应器 内使气态或蒸汽状态的化学物质在气相或气固界 面上经化学反应形成固态沉积物的技术。 简单来说就是:两种或两种以上的气态原材料导 入到一个反应室内,然后他们相互之间发生化学反 应,形成一种新的材料,沉积到基片表面上。 从气相中析出的固体的形态主要有下列几种:在 固体表面上生成薄膜、晶须和晶粒,在气体中生 成粒子。
2020-08-02
4
化学气相沉积的古老原始形态可以追朔到古人类在取 暖或烧烤时熏在岩洞壁或岩石上的黑色碳层。
作为现代CVD技术发展的开始阶段在20世纪50年代主 要着重于刀具涂层的应用。
从20世纪60~70年代以来由于半导体和集成电路技术 发展和生产的需要,CVD技术得到了更迅速和更广泛 的发展。
在生命体中确实存在着大量反自发方向进行 的反应,据此可以把激活(即由外界输入能 量)条件下金刚石的低压气相生长和生命体 中某些现象做类比讨论。
因此这是一项具有深远学术意义和应用前景 的研究进展。
2020-08-02
10
目前,CVD反应沉积温度的耕地温化是一个发展方向, 金属有机化学气相沉积技术(MOCVD)是一种中温进行的 化学气相沉积技术,采用金属有机物作为沉积的反应物, 通过金属有机物在较低温度的分解来实现化学气相沉积。
微电子工艺原理- 第6讲 薄膜工艺 3
4.1 化学气相沉积合成方法发 展
化学气相沉积乃是通过化学反应的方式,利用加热、等 离子激励或光辐射等各种能源,在反应器内使气态或蒸 汽状态的化学物质在气相或气固界面上经化学反应形成 固态沉积物的技术。
化学气相沉积的英文词原意是化学蒸汽沉积 (Chemical Vapor Deposition,CVD),因为很多反应 物质在通常条件下是液态或固态,经过汽化成蒸汽再参 与反应的。
1990年以来中国在激活低压CVD金刚石生长热力学方 面,根据非平衡热力学原理,开拓了非平衡定态相图及其 计算的新领域,第一次真正从理论和实验对比上定量化 的证实反自发方向的反应可以通过热力学反应耦合依靠 另一个自发反应提供的能量推动来完成。
2020-08-02
9
低压下从石墨转变成金刚石是一个典型的反 自发方向进行的反应,它依靠自发的氢原子 耦合反应的推动来实现。
近年来发展的等离子体增强化学气相沉积法(PECVD)也是 一种很好的方法,最早用于半导体材料的加工,即利用 有机硅在半导体材料的基片上沉积SiO2。PECVD将沉积 温度从1000℃降到600℃以下,最低的只有300℃左右, 等离子体增强化学气相沉积技术除了用于半导体材料外, 在刀具、模具等领域也获得成功的应用。