涡旋压缩机论文翻译
涡旋压缩机的研究
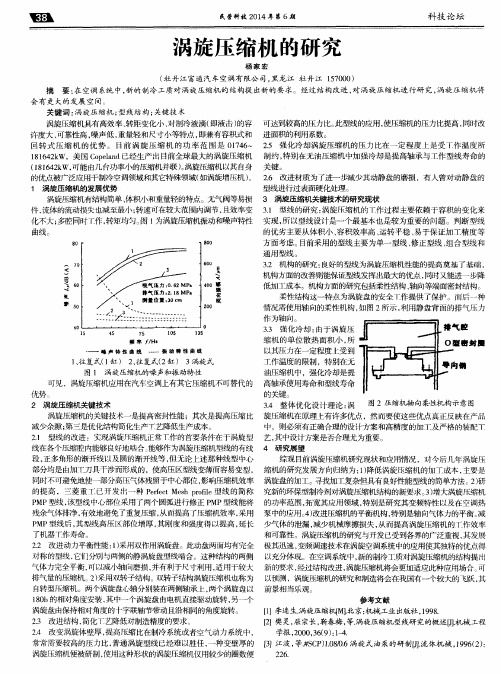
《
盛 Βιβλιοθήκη 爨 3 . 2 机 构 的研究 : 良好 的型线 为涡 旋压 缩栅 l 生能 的提高 奠 基 了基 础 , 机构方面的改善则能保证型线发挥出最大的优点 , 同时又能进一步降 低加工成本。机构方面的研究包括柔l 生结构 、 轴向等端面密封结构 。 柔性结构这一特点为涡旋盘的安全T 作提供了保护。而后一种 情况需使用轴向的柔性机构 , 如图 2 所示 , 利用静盘背面的排气压力 作 为轴 向。
泵中的应用 。 4 ) 改进压缩机的平衡机构 , 特别是轴向气体力的平衡。 减 少气体的泄漏, 减少机械摩擦损失, 从而提高涡旋压缩机的T作效率 和可靠I 生。涡旋压缩机的研究与开发已受到各界的广泛重视 , 其发展 2 . 2 改 进 动力平 衡 性能 : 1 ) 采 用双 作用 涡旋盘 。此动 盘两 面均有 完全 极其 迅速 , 变频 调速技 术在 涡旋 空调 系统 中的应 用使 其独 特 的优点 得 对称的型线 , 它们分别与两侧的静涡旋盘型线啮合。这种结构的两侧 以充分体现。在空调系统中, 新的制冷丁质对涡旋压缩机的结构提 气体力完全平衡 , 可以减小轴向磨损 , 并有利于尺寸利用 , 适用于较大 新的要求 , 经过结构改进, 涡旋压缩机将会更加适应此种应用场合。 可
艺, 其中设计方案是否合理尤为重要。
4 研 究展 望
部分均是由加 刀具干涉而形成的,使高压区型线变薄而容易变型 , 同时不可避免地使一部分高压气体残留于中心部位, 影响压缩机效率 的提高 ,三菱重T 已开发 出一种 P e f r e c t Me s h p r o i f l e型线的简称 P MP型线 , 该型 线 中心 部位 采用 了两个 圆弧 进行 修 正 P MP型线 能 将 残余气体排净 , 有效地避免了重复压缩 , 从而提高了压缩机效率 , 采用 P M P型线后 , 其型线高压 区部位增厚 。 其刚度和强度得 以提高, 延长 了机器 一 r 作 寿 命
涡旋压缩机研究概述

87科技资讯 S CI EN CE & T EC HNO LO GY I NF OR MA TI ON 工 业 技 术涡旋式流体机械从20世纪70年代以来追求的效率高,可靠性强,转速高,个头小,震率低,噪音小的发展进程,使其迅速推广在制冷空调领域,涡旋压缩机坚持在实际生产中进行理论和实践的实际应用,大大提高了涡旋压缩机的整体性能。
综合各种文献,本文从以下几方面来简单介绍一下涡旋机械近几年的技术研究。
1 涡旋型线研究涡旋压缩机能够正常工作的条件就是动涡盘与静涡盘在压缩腔内能够啮合。
而基于涡旋体直壁等高的形状特性,在几何计算时完全可以仅讨论其投影的涡线,即把空间啮合问题转化为平面啮合问题。
常见的涡旋型线有基圆渐开线、正多边形渐开线、线段渐开线、半圆渐开线、阿基米德螺旋线、代数螺旋线、变径基圆渐开线、包络型线、以及通用型线等。
由于圆的渐开线容易加工,并且该型线的压缩机有良好的工作性能,所以目前应用的型线以圆渐开线为主。
由于单一型线无法随意改变其压缩比,再加上所存在着的中心腔余隙容积以及因加工刀具的干涉容易在型线两端出现比较大的应力,因此,必须对单一型线进行修正。
常见的型线修正方法主要有:双圆弧修正、直线圆弧组合修正、多段圆弧组合修正、二次曲线修正和直接截断修正。
其中双圆弧修正结构简单、有效而可行的方法,也是目前大多数涡旋压缩机的修正方法。
2 气体力方面的研究气体在涡旋压缩机经历中吸气、压缩、排气连续的过程,同时气体被动的由外到内运动直到排气,这个过程中产生气体力。
动、静涡盘所受的气体力大小相等、方向相反,且静涡盘所受的气体力传递到支架体,而作用在动盘上的力则影响到十字环、轴等所有的运动部件的受力。
动涡盘受三个气体力作用,其中一个是涡旋盘所受的轴向气体力,另外的两个是涡旋齿所受的切向气体力和法向气体力。
气体力模型文献[1]已有说明,在文中提出了整数圈和非整数圈、单头和双头涡旋压缩机的气体力模型。
涡旋压缩机英文论文(翻译)

涡旋式汽车空气压缩机的设计与制造艾克考比,JA;伊,OI 生产工程部,贝宁城市大学, 贝宁,尼日利亚摘要:这项工作的重点在于汽车用空调涡旋压缩机的设计制造。
涡旋压缩机是一种容积式压缩机,用两个互相配合的螺旋形涡盘压缩空气。
这是半封闭压缩机的设计,具有噪音小,性能可靠,效率高等优点。
@ 詹姆斯压缩机的主要功能将低压区的液体压缩和输送到高压区(罗杰斯;梅,1994)。
压缩机可分为位移式和涡轮式。
位移型进一步分为往复式和旋转式(可瑞克斯,1995)。
涡旋压缩机是一种新型的旋转式压缩机。
它的排量是靠两个相互啮合的螺旋形涡齿的压缩作用来实现的,其中一个是固定的,而另一个是有其固定轨道的,(安斯赫尔,2004)。
汽车空调系统用的典型的涡旋压缩机主要由以下几部分组成:涡齿,壳体,轴,轴承,冷冻室,橡胶密封件,平衡弹簧,电磁离合器和压力阀,如图6所示现代的涡旋压缩机技术的发展在20世纪70年代,涡旋压缩机的概念是由制冷行业提出来的。
而由他们介绍进入空调行业在上世纪80年代末,涡旋压缩机在住宅和商业应用上取得了广泛的成功。
空调压缩机主要用在小型公寓和车辆系统,如用于加热和冷却的个人家庭或企业热泵系统。
更大的压缩机是在商业领域中的应用,如冷冻机、多种冷凝机组系统。
制冷涡旋压缩机的应用范围很广,包括超市货架,散装牛奶冷却运输货车和海运集装箱等(美国制冷学会,1998;载体,2004)在这种情况下,我们提出了汽车空调涡旋压缩机的设计制造。
而据我所知,目前我们没有国产的压缩机。
致使大量的外汇用于进口它们。
因此,本研究致力于涡旋压缩机的设计和制造技术,以促进我国压缩机技术的发展从而使我们的经济得到改善。
工作原理:压缩过程的设计理念是基于两个相互啮合的涡旋盘压缩使(如图1所示)空气通过旋转轴与电机相连。
上部和下部的涡旋叶片形成新月形的压缩腔。
为降低滚动轨道,密封点在叶片两侧向内移动,推动月牙形的压缩腔向渐开线中心移动。
而随着压缩腔的移动,他们的容积逐渐减少,气体得到压缩(麦卡洛,1979;王;乔培,1994)。
毕业论文外文翻译-小型制冷压缩机研究

Small COMPRESSORCompressor refrigeration system is the core and heart of its decision to the refrigeration system capabilities and features. This paper not only energy efficient, noise and vibration and refrigeration agent analyzed small refrigeration compressor technical performance, Analysis also have appeared in recent years, the new, special small compressor main feature for us small refrigeration compressor future development trend of laying a technological foundation.As we all know, the compressor refrigeration system is the core and heart. Compressor and decided that the cooling system capacity and features. In a sense, the cooling system design and matching of the compressor is the ability demonstrated. Therefore, countries in the world are all in the refrigeration industry refrigeration compressor research invested a tremendous amount of energy, new research direction, and research results continue to emerge. Compressor technology and performance level with each passing day.1.A compressor Efficiency StudyCompressor refrigeration system is the core energy components, improve the efficiency of refrigeration systems of the most direct and effective means is to increase the efficiency of the compressor, It will bring the energy consumption decreased significantly. Moreover, can only avoid the system take measures (such as simply increasing heat exchanger area, etc.) caused by the consumption of materials increased. In recent years, as world energy shortage situation worsens day by day, more and more attention to various energy-saving work the energy efficiency of products made by the ever-increasing demands. Due to losses such as friction, leakage, harmful heat, the electrical loss, flow resistance, noise vibration of existence, Compressor work far below the actual efficiency of theoretical efficiency. Therefore, from a theoretical point of view, any reduction in a loss of arbitrary measures toimprove the efficiency of the compressor. The objective facts have led to the energy saving compressor scope, direction, width, research topics and results varied.On the current international energy-efficient compressors research concentrated mainly in a few areas : research lubrication properties Compressor parts of the friction bearings to reduce friction characteristics of power, improve the efficiency of the compressor; reduce leakage losses to improve the efficiency of the compressor; using frequency modulation technology or refrigeration system through the effort with the user load to match the best energy saving In this regard the particular frequency technology has been relatively mature well known and not repeat them here. Valve Research is an old topic but it is also an eternal topic, Improvement of the valve designed to improve the efficiency of the compressor also Nagamochi endless harvest. Research in this area many times, from the valve material, sports law, optimizing the structure of the applicable theory, exhaustive testing methods. In short, energy-saving compressors on the research in recent years has become one of the refrigeration industry first hot issues.In recent years, domestic refrigeration compressor industry to studyenergy-saving products are also giving great concern. Progress larger products mainly refrigerator compressor industry. In China efficient refrigerators GEF projects to promote and support, both the enterprises for energy-efficient products is the understanding of the performance of refrigerator compressors have a qualitative leap. At present, domestic enterprises refrigerator compressor products of the highest energy efficiency has reached 1.95%. Refrigerator compressor domestic enterprises to take a lot of technical measures such as high efficiency motors or synchronous motor, concave valves, Plane thrust bearing, low viscosity lubricants, the new Getter muffler, reducing friction losses, and achieved great results. The main problem is the lack of domestic enterprises currently free technology, the technology has to imitate the line mainly, Most of the enterprises to build their own technology infrastructure alsounconscious, nor the interest, and this restricts the development of technological capacity.Relative to the refrigerator compressor industry, domestic energy-efficientair-conditioning compressor study it was not perturbed, Over the years the efficiency of the compressor is no substantive change, greater market demand makes most of the air-conditioning compressor enterprises will concentrate on expanding production on. With the nation on the air conditioner energy efficiency standards set for the further improvement of China's air conditioner exports various perils of showing, domestic air-conditioning compressor of this short-sighted enterprises will be unable to adapt to the energy-saving development of the situation. Enterprise also on the follow-up is weak.2. Compressor noise and vibration studyCurrently, the noise has been regarded as one of the serious pollution. Household refrigeration equipment as the source of power and heart, refrigeration compressor noise, to be a measure of its performance as an important indicator. In fact, to a compressor speaking, Most of the noise is due to shell by some noise from the source excitation (such as springs, refrigerant pressure pulsation, exhaust pipe, lubricants etc. excited). But compressor noise sources and pathways complex and diverse, which gives the compressor noise silencer brought great difficulties.On the compressor noise, vibration and foreign scholars have conducted a large number of long-term research. Here in this regard to the main research results are summarized below :The main refrigeration compressor noise Exaggerative inlet, exhaust radiation aerodynamic noise, mechanical moving parts of machinery noise and noise-driven motor three components :2.1 Aerodynamic noiseCompressor inlet airflow noise is due to the intake manifold pressure pulsation in the elections. Inlet-frequency noise and the intake manifold gas Lane same frequency pulsating with the speed of the compressor. Compressor exhaust noise is due to air in the exhaust pipe caused by fluctuating pressures. Exhaust noise than the inlet noise weak, so the compressor aerodynamic noise generally Inlet mainly noise2.2 Mechanical NoiseCompressor mechanical noise, including members of the general impact and friction, the piston vibration, noise impact of the valve, These noise with randomness, was puted.2.3Electromagnetic noiseCompressor electromagnetic noise is generated by the motor. Motor noise and aerodynamic noise and mechanical noise is weaker compared. Noise source compressor inlet, exhaust, aerodynamic noise, the strongest, followed by mechanical noise and electromagnetic noise. Through in-depth studies, we can further that the main compressor noise from the vibration (from the Department of spring, Refrigeration medium pressure pulsation and smoke exhaust pipe and lubricants have incentive) to the ambient medium spread formation noise. On the effort to reduce compressor noise, much of the literature (abbreviated) proposed a series of measures and the Noise and Vibration Reduction program :① increase rigid shell structure to improve the overall resonance frequency reduces vibration amplitude;② curvature of the shell to avoid mutation, the surface, and the natural frequency is inversely proportional to the radius of curvature. shell shape it should be the smallest curvature radius;③ spring bearing flags will be moved to higher rigid position;④ shell should be used as little as possible of the plane; bending stress and the stress coupling membrane (just on the surface) will shell itself is fairly rigid. Therefore compressor shell to be used as little as possible planar structure;⑤ avoid the exhaust pipe and condenser incentive, optimizing exhaust flow pulsation, Exhaust pipe used in the introduction of additional volume to the elimination of pressure fluctuation spectrum of high-order harmonics;⑥ non-symmetric shell shape; Symmetrical three-dimensional structure means that the axis, along the main axis biggest stress of least resistance. Therefore it is asymmetrical shell structure means that the compressor can be greatly reduced along the axis direction of a force while the probability;⑦ set inlet, exhaust muffler, the closed Compressor Muffler generally muffler. It uses Cross Section, resonant cavity caused acoustic impedance changes in reflectivity or sound energy consumption. or use acoustic-acoustic send phase difference of 180 degrees to offset the muffler of noise. Shell compressor in the lateral closed Unicom a Helmholtz resonator, namely : Helmholtz resonator from the chamber through the neck hole and shell compressor connected into the internal cavity, to reduce compressor cavity stimulated acoustic modal amplitude. The results showed : resonator resonance frequency modulation of the actual compressor cavity stimulated the greatest vibration modes, will be substantially reduced resonance peak response spectrum and lead to significant change. However, it will affect the appearance andthe compressor refrigerator settings, the research results are not yet applied to products.Lubricants and residual volume-coil motor windings will lead to the same types of bulk compressor levels between different (from levels average). By changing the shell external support to increase torsional stiffness and reduce vibration surface; Noise study the complex requirements of researchers has strong theory, the enterprise has good skills base and the need for greater investment and a longer timeframe. This is domestic enterprises compressor one of the weak links, which is now basically in the qualitative phase of experimental research, Along with a great chance and randomness.3. new refrigerants ApplicationBased on the new environmental requirements of refrigerant compressor refrigeration industry is a hot issue. As for the refrigerator product R22 refrigerant substitutes the end of the work, new refrigerant compressor in the past few years mainly concentrated in the air conditioning industry. Apart from the now relatively mature R410A, R407C the study, The largest is the hot issue of CO2 compressor. This is the only issue for a briefing.CO2 currently on the research and application of concentrated mainly in three aspects : one is the most urgent need of alternative refrigerants applications, such as automotive air conditioning, as refrigerant emissions, environmental harm, must be adopted as soon as possible without endangering the environment refrigerants; the other is to consider the characteristics of CO2 cycle, the most favorable to the use of this cycle of occasions, If heat pump water heater is to supercritical CO2 in hot conditions decentralization there is a significant temperature slip will help heat Water heated to a higher temperature characteristics of the focus of public attention; another one is CO2 into account the nature of heat transfer properties and characteristics of using CO2 as a refrigerant, taking into account CO2 good cold flow properties andheat transfer characteristics, use it as a cascade refrigeration cycle cryogenic stage refrigerants.Compressor transcritical carbon dioxide as an air conditioning system efficiency and reliability of the most affected parts, It should be fully integrated supercritical carbon dioxide cycle specific characteristics of a new design. Like ammonia and CO2, the adiabatic exponent K value higher, up 1.30, it may result in the compressor discharge temperature high, However, as the needs of CO2 compressor pressure ratio small, there is no need for cooling the compressor itself. Adiabatic index is high pressure over the small, I can reduce the gap compressor further expansion of the volume losses to the higher volume efficiency compressors. After experimental and theoretical research, Jurgen Horst SUB and found Kruse, reciprocating compressor is a good film sliding seal as the preferred CO2 system. 8:3 its carbon dioxide compressor exhaust valve for improved Exhaust improved compressor efficiency of carbon dioxide increased by 7%.As the carbon dioxide pressure is far greater than the traditional critical circulatory pressure, compressor shaft seal design requirements than the original compressor is much higher, compressor shaft seal leakage over a period of time is still hampered Actually, the main reason.Danfoss, Denso, ZEXEL such as carbon dioxide compressor has entered the stage of small batch production.The IEA in March 1999, the Joint Japan, Norway, Sweden, Britain and the United States to activate the "Selected Issue on CO2 as working fluid Compression Systems in the "three-year project.Beginning in 1994, BMW, DAIMLERBENZ VOL O, Germany's Volkswagen and Danfoss. Péchiney and other European companies launched the famous "RACE"to the joint project, the Joint European well-known universities, automotive air conditioning manufacturers and other developed CO2 automotive air-conditioning system. Subregion Motor Company has production equipment CO2 carair-conditioning systems of cars, Germany KONVECTA production to the quality of CO2 in the air-conditioned Buses run from 1996 to date. DANFOSS, the Obrist Austria, the United Kingdom have developed a carbon dioxide compressor motor. Japan DENSO, ZEXEL CO2 compressor has entered the stage of mass production.With major manufacturers inputs, the type of CO2 compressor with ordinary motor compressor trend line major swing to determine the displacement swashplate, scroll and the main variable displacement.4. New principle of refrigeration compressorsIn recent years, the new structure and working principle of refrigeration compressor made a more progress, mainly linear compressor, Elliptic compressors, compressor rotor Swing, spiral vane compressor, in the past, the author has been described in the article, here will not repeat it.Linear compressor which is the domestic refrigerator compressor industry the focus of attention. In 2004 the International Compressor Engineering Conference has five linear compressor on the article. LG and researchers still Sunpower two main companies. The past two years, several domestic enterprises in the refrigerator compressor to the development of the linear compressor, However, enterprises have the technical foundation for the domestic financial strength and the limitations of scientific research institutions, believe in a short period of time can not enter the stage of industrialization.5 the classification of the refrigeration compressor5.1 reciprocating compressorReciprocating compressor is a kind of traditional refrigeration compressor, the biggest characteristic is to achieve the capacity and pressure than any of the design. Although it is widely applied, but the market share is gradually reduced.So far, the fridge (including small freezing and cold storage device) host compound compressor is ever to give priority to. Through the optimal design of valve structure, friction pair, reciprocating refrigerator compressor refrigeration coefficient of power refrigerating capacity (units) by 1.0 (w/w) of the early ninety s to today's 1.8 or so; In addition to the energy saving technology progress, and environmental protection is closely related to the refrigerant alternative technology has also made gratifying progress, refrigerator system in our country has a large number of using R600 hydrocarbons, such as small refrigeration device is also used the new working substance such as everything. To further improve the efficiency of the reciprocating compressor refrigerator, to reduce the system noise is still the development direction of it.5.2 linear compressorStill make reciprocating linear compressor, due to the linear motion of the motor can be directly drives the piston reciprocating motion, so as to avoid the complexity of the crank connecting rod mechanism and the resulting mechanical power consumption. Linear compressor assembly as the refrigerator system has appeared, the refrigeration coefficient of linear refrigerator compressor has more than 2.0 (w/w), market prospects look good. The main problem is the design of the compressor oil system and the effective control of linear motor displacement limit point and the corresponding anti-collision cylinder technology.5.3 the swash plate compressorSwash plate compressor is also a kind of variant structure of reciprocating compressor, is mainly used in automotive air conditioning system at present. After decades of development, the swash plate compressor has become a very mature model, in possession of more than 70 of the automotive air conditioning compressor market. In spite of this, because it still belongs to the series of reciprocating structure, so in thecar air conditioning system can effect comparing (refrigeration coefficient) and only around 1.5, weight and volume is big, big. Because of the mature of swashplate automobile air conditioning compressor technology, combined with technology, further improvement in the foreseeable future, will continue to maintain a certain market share, but in a certain displacement range by substituting is inevitable.5.4 rotor compressorRotor compressor in the 1970 s by the attention of domestic, it represents the structure including the rolling piston type, sliding-vane, etc. On the rolling piston type is widely used in household air conditioner at present, there are also some applications on the refrigerator. This kind of compressor don't need air suction valve, make it suitable for variable speed operation, which can improve system performance by frequency conversion control. In order to ensure high power (3 p) of the motor output power in the performance of the rolling piston compressor, the domestic research and development and the end of last century, double rotor rolling piston compressor, is now on the market. Double rotor on the rolling piston compressor structure has two advantages: (1) force of the rotating system be improved, the machine vibration and noise is reduced; (2) increase the standalone swept volume and improve the output power of the motor.Below 3 p air conditioning unit, temporarily can not replace a good model of the rolling piston compressor. So improve the efficiency of the compression process, reduce noise and motor speed control and the R410A and other related technical issues after new refrigerating agent, etc., is a research direction of the rolling piston compressor.Sliding vane compressor is a kind of rotor compressor, mainly used to provide compressed air, displacement is in commonly 0.3-3 m3 / min, the market share is low. Rotary vane compressor sliding vane compressor is a kind of transition structure, because of its better starting performance, the compression process torque change is not big, at present is mainly used for miniature cars and some smaller displacementplumbing vehicle air conditioning system. The dynamic characteristics under high speed is the main technology of this compressor research direction.5.5 screw compressorScrew compressor with small size, light weight, easy to maintenance etc., is a model of the fast development in refrigeration compressor. On the one hand, the screw type line, structural design has made considerable progress, on the other hand, the introduction of special screw rotor milling especially grinding, improve the machining precision and machining efficiency of key parts, makes the performance of screw compressor has been effectively improved, industrialization production of the necessary hardware also has the safeguard. At present, the screw compressor is given priority to with compressed air, in medium ReBengShi air conditioning has successful application in the system. Due to increasing the reliability of the screw compressor work within the scope of the medium refrigerating capacity has gradually replace of reciprocating compressor and occupied most of the centrifugal compressor market. 5.6 scroll compressorScroll compressor has been rapid development in the past ten years, the structure of the basic theory, research and development to achieve large-scale industrial production, industrial prototype constitutes the compressor technology development new luminescent spot. The development of numerical control processing technology to realize the mass production, the vortex compressor incomparable performance advantage is the precondition of its vast in the market. A few short years, has been in the field of cabinet air conditioning holds an absolute advantage. In cabinet air conditioning system, scroll compressor refrigeration coefficient has amounted to 3.4 (w/w); In the field of automotive air conditioning, the refrigeration coefficient of scroll compressor has amounted to 2.0 (w/w), and shows strong competition potential. The development of the vortex compressor is to enlarge its range of refrigerating capacity, further improve the efficiency, using alternative working medium and lower the manufacturing cost, etc.Since there is no valve, compression force and torque and small changes in the structure make it more suitable for the advantages of frequency control of motor speed operation, it also become the main direction of scroll compressor technology development. Development of scroll compressor of variable displacement mechanism is the key point of the development of the technology. At present, the use of axial sealing technology, "flexible" theory can realize cooling/heating capacity of 10% to 100% within the scope of the regulation.Due to the vortex compressor suction exhaust characteristic of almost continuous, low starting torque and liquid impact resistance, created the condition for parallel use of vortex compressor. In parallel with the vortex compressor can greatly increase the cooling capacity of the unit, can increase from the current single 25 horsepower to single unit 100 horsepower (4 sets of single parallel), and makes the cold quantity adjustment is more reasonable, give full play to the single machine with the highest efficiency. But single in parallel, one of the biggest problems is the oil return is not the average of the unit when using single machine burning phenomenon.3.1.5 centrifugal compressorAt present in large quantity of cold (greater than 1500 kw) remain within the scope of advantage, this is mainly benefited from the cold quantity range, it has incomparable system overall efficiency. The movement of the centrifugal compressor parts little and simple, and its manufacturing precision is much lower than the screw compressor, these are the characteristics of the manufacturing cost is relatively low, and reliable. Relatively speaking, the development of centrifugal compressor is slow, due to the challenges of the screw compressor and absorption chiller. Centrifuge market capacity is around 700 ~ between 1200, because under the premise that the current technology, the machine is mainly used for air conditioning of large buildings, demand is limited. In recent years because of the large infrastructure projects are built, the centrifugal refrigeration and air conditioning compressor is becoming a hot spot of attention again. Solve surge phenomenon, improve the volume adjustment and theadaptability to change with working condition, miniaturization technology is the main development direction of the centrifugal compressor technology.3.1.6 other structure formsSingle tooth of the compressor, some structures, such as cross slider compressor unique positive displacement compressor also has a certain degree of development, but has not been formed in the domestic production capacity.5. Special refrigeration compressorsAlthough domestic enterprises household refrigeration compressors long accustomed to large-scale production mode, we are accustomed to the number of effectiveness. However, the fierce price competition situation, as products become increasingly lower profit margins, When the production of millions of compressors can only make a few million dollars of profit, some on special refrigeration compressors can be regarded as a way out. Special refrigeration compressor exhaustive, it is impossible in this enumeration. But their common feature is their production scale is small, a single high-profit products faster transition, In most cases the need for the user's requirements designed. These products lead to more and more domestic enterprises to the compressor. If the number of domestic enterprises are developing or already have production capacity of the refrigerator compressor truck翻译小型制冷压缩机研究压缩机是制冷系统的核心和心脏,它决定了制冷系统的能力和特征。
涡旋压缩机英文论文
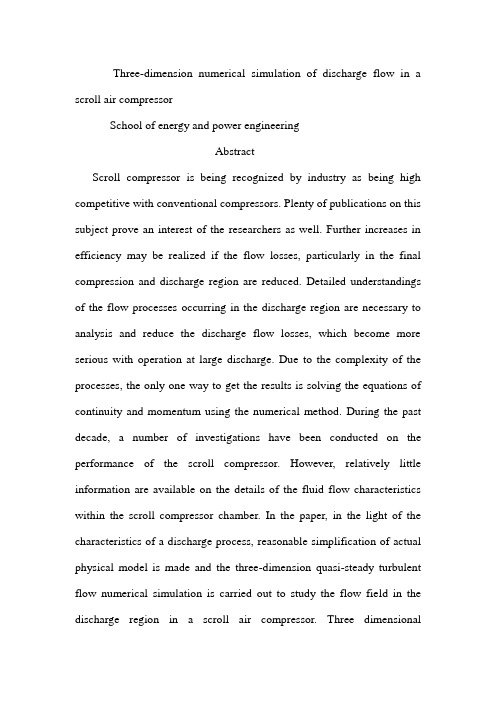
Three-dimension numerical simulation of discharge flow in a scroll air compressorSchool of energy and power engineeringAbstractScroll compressor is being recognized by industry as being high competitive with conventional compressors. Plenty of publications on this subject prove an interest of the researchers as well. Further increases in efficiency may be realized if the flow losses, particularly in the final compression and discharge region are reduced. Detailed understandings of the flow processes occurring in the discharge region are necessary to analysis and reduce the discharge flow losses, which become more serious with operation at large discharge. Due to the complexity of the processes, the only one way to get the results is solving the equations of continuity and momentum using the numerical method. During the past decade, a number of investigations have been conducted on the performance of the scroll compressor. However, relatively little information are available on the details of the fluid flow characteristics within the scroll compressor chamber. In the paper, in the light of the characteristics of a discharge process, reasonable simplification of actual physical model is made and the three-dimension quasi-steady turbulent flow numerical simulation is carried out to study the flow field in the discharge region in a scroll air compressor. Three dimensionaldistributions of velocity and pressure and typical flow patterns that exits in the discharge region are presented, which gives good understanding about the physical processes in the scroll air compressor.1.INTRODUCTIONScroll compressors are applied widely in the refrigeration, air conditioning and power field as being competitive advantages in terms of high efficiency, reduced part requirement, lower noise, and reduced vibration levels. Three exist various losses when a scroll compressor is running, such as moving resistance losses of the orbiting scroll and Oldham, friction losses and flow losses. The discharge flow is the main part of these losses (approximately 3 percent of the input power is consumed due to the flow losses), especially at large discharge . Understanding of the flow processes occurring in the discharge and the final compression region is necessary to reduce these flow losses, which become more pronounced with operation at increasing speed and large discharge. Therefore, three dimension numerical simulation of discharge flow in scroll air compressor with modified top profile is carried out. The important flow patterns that exist in the discharge and final compression region are presented. The analysis results supply the theory basis for finding the sources caused discharge losses and designing the discharge port of scroll compressor, particularly at large discharge.A scroll air compressor of discharge is studied in this paper. The topprofile is modified with symmetrical arcs and the discharge port is kidney-shape port. The basic parameters and modified parameters of scroll tips are shown in the table 1.Figure 1 shows the schematic region of the scroll compressor.Table 1: The basic parameters and modified parameters of scroll tipsFigure 1: Schematic of scroll compressor discharge region.2.PHYSICAL MODELAND AND NUMERICAL METHOD2.1 Physical modelThe gas is driven and compressed by “squish motion” of the orbiting scroll wrap, and this results that an unsteady compressible viscous flow occurs within the scroll compressor working chamber. Due to high rotating speed and steep velocity gradient near the wrap wall, the turbulence characteristics have to be considered. But the orbiting wall speed is small compared to the gas flow velocities, for example, the wall speed is approximately 5 percent of the average velocity of the discharge flow in a scroll air compressor at discharge studied in this paper, so it appears justified that the quasi-steady approach is made to treat the flow field with stationary wall. That is , to ignore the moving of orbiting scroll wall is justified. Therefore, three dimension steady-state turbulence calculations are performed to predict the flow field in the final compressor and discharge region. Air is injected from two sides of thecentral chamber with the instantaneous flow rate at various crank angles. The volume flow rate at various crank angles during the discharge process is shown in figure 2.The figure 3 shows a computational model at a certain crank angle after onset of discharge.Figure 2: V olume flow rate with orbiting discharge crank angleFigure 3: Three dimensional computation model2.2 Numerical methodTurbulent flow exists in the scroll configurations considered and was treated using a normal k- turbulence model. The governing equations were discretized using finite volume method. The SIMPLE algorithm was employed in order to correct the pressure filed. Near the wall, the improved wall function method was employed. The discretization scheme of convection item and diffusion item are respectively the second-order upwind scheme and the central difference scheme. Tao (2001) shows the details of discretization method. In the light of the geometrical characteristics of computational domain, the geometry scale of different parts of the whole domain differs greatly; the block structure gird method was employed to generate grids of the whole domain being separated into several parts, in which grids were generated by the body-fitted coordinate grid system. Grids are so fine that the numerical results are grid-independent. The computational domains at different crank angles are different, so the grids were generated separately. The boundaryconditions are as the followings:(a) InletThe mass flow rate on each of two inlets is the same and equal to the instantaneous volume change rate multiplied by the density.(b)The outlet is set on the location far away as 5 times of height of discharge port in order to guarantee the constant pressure. The discharge pressure is provided on outlet.(c)Non-slip boundary condition for velocity is provided on walls. Advanced wall function method is employed to tread the near wall domain.3. NUMERRICAL RESULTSIn this paper, 0 is defined as the orbiting discharge crank angle. At the discharge moment, that is the crank angle y=45(x is the discharge crank angle), yis taken as zero. Then, y is changing from 0 to 360 degree during the whole process of discharge. According to this definition, for example, at crank angle of 45 degree after the onset of discharge is described as y=45.In this paper, for the convenience of description, location of the z coordinate equal to zero is define as the inlet of discharge port and is named as the surface of the fixed scroll. Location of the z coordinateequal to h (the height of scroll wrap) is named as the top surface of the fixed scroll.The flow field and its discharge from the central chamber region at several crank angles that correspond to 45, 90,180 degree after the onset of discharge is studied. Flow velocity vectors in different axial sections and three dimensional velocity vectors are detailedly analyzed.3.1 y=45The calculated velocity fields in different axial sections are shown in figure 4 (a)-(c) at orbiting discharge crank angle of 45 degree. The flow velocity in fig.4 indicate that flow being injected in the rear of each half central chamber, being turned as it impinges on the opposing wall of orbiting scroll of fixed scroll and proceeding towards the central region of the central chamber. In the central region, flow enters from both half central chamber, passing through throat region formed by the orbiting and fixed scroll tips and proceeds driven by the inertia. Two large scale vortexes develops in the central region near the scroll tips and some small scale vortexes develops in the rear of central chamber near the outer surface of scroll tips. Compared fig 4 (a), (b) with (c), it is shown that vortex flow develops in all different axial sections and number and scale and location of vortex are different in different axial section. That is to say this basic vortex flow pattern persists in this region throughout the entire axial extent of central chamber. Three dimensional velocity vectorsshown in fig 5 indicate clearly the distribution of axial velocity component. The three dimensional flow tends to move vertically downwards as it approaches the central region of the central chamber which is directly upon the discharge port. The axial velocity component is very large at a small axial distance of 0-10mm from the discharge port (when the height of the profile is 52mm). The axial velocity by the order of magnitude is greater than the radial velocity. In contrast, within the rear region of the central chamber, the flow is essentially two dimensional.From the fig 4 and fig 5, it can be seen that the velocity vectors in the mid axial section characterize the general nature of the flow within the entire central chamber. The flow vectors indicate both the two dimensional and the three dimensional nature of the flow depending upon the location. So, only the velocity vectors in the mid plane are analyzed below.Figure 4 : Velocity fields in different axial sectionsFigure 5: Three dimensional velocity vectors3.2 y=90Similar type of flow calculations have been performed at an intermediate crank angle (2=90). It is shown in fig 6. As the discharge process continues in an actual scroll compressor, the orbiting scroll continues to move away from the fixed scroll. This action is associatedwith a progressively increased opening of the central region to the discharge port. This implies a less occluded opening of the discharge port compared with the throat region at y=45.The velocity vectors in axial sections of mid plane and discharge are different from those at y=45 and the magnitude of velocity reduced. A double vortex was predicted to form at the mid axial section and the scale of the vortexes increased to trend to become a large vortex.Figure 6 : Velocity fields in different axial sections3.3 y=180Figure 7 (a)-(b) shows the velocity vectors in the axial sections at orbiting discharge crank angel of 180 degree. From the figure, it is shown that the velocity vectors field is obviously different from those shown in fig .4 and fig.6. A large scale vortex was developed in the discharge region as the discharge port is opened fully. In addition, a less constrictive flow passage exits on the region of the scroll tips, the velocity magnitude reduces further. The velocity vector field shows the occurrence of some small scale vortexes at the rear region of the central chamber.Figure 7: Velocity field in different axial sections4. NONDIMENSIONAL PRESSURE LOSSES COEFFICIENTTo obtain quantitative data characterizing the pressure losses of the final compression and discharge region, nondimensional pressure losses coefficient was define as below:P is the average pressure in the central chamber, pa; pd is the designed discharge pressure, pa.The variation of pressure losses coefficient * with orbiting discharge crank angel for the whole discharge process under different operation conditions is shown in fig 8. the pressure losses coefficient is very large at orbiting discharge crank angel of 0-60 degree. For example, the losses coefficient at 45 degree of orbiting discharge crank angle is approximately ten times larger than the loss coefficient at 180 degree, indicating that the flow losses are largest at the onset of discharge. This result is not surprising, since this is also the point of maximum constriction of the flow area. Furthermore, the high rotating speed and discharge pressure corroborate that significant flow losses would exist. With increasing the opening discharge port, losses coefficient is decreasing rapidly. The results indicate that discharge flow losses concentrate at the onset of discharge and reduce quickly with increasing opening discharge port.In addition, these results imply that the open-close characteristic of discharge port should be stressed to consider when designing a discharge port, particularly for compressor at large discharge. The easier to open, the better the characteristic of discharge port is. Maximum area of discharge port is possibly not the best.Figure 8: Nondimensional pressure losses coefficient with orbitingdischarge crank angle5: CONCLUSIONSInternational Compressor Engineering Conference at Purdue, July 12-15, 2004Three dimension numerical simulation of the discharge flow in a scroll air compressor was conducted to provide the characteristic of flow field in the final compression and discharge region. Detailed analysis is made of the flow velocity vectors in different axial sections. The numerical results show that complex vortex flow patterns exist in the discharge region, not only in axial sections. On the basis of numerical results, the dismensionless pressure losses coefficient is defined and the pressure losses at various crank angles after onset of discharge is analyzed. It is shown that the discharge flow losses greatly large shortly after the onset of discharge. The results shows that, the easier to open, the better the characteristic of discharge port is. Maximum area of discharge port is possibly not the best.REFFRENCES1.Hirano. T., et al., 1989, Development of High Efficiency ScrollCompressor for Heat Pump Air Conditioners, Mitsubishi Heavy Industries, Ltd., Tech. Rev. V ol. 26, No. 3, p: 512-519.2.Patankar S V, Spalding D B., 1972, A calculation procedure forheat、mass and momentum transfer in three-dimensional parabolicflows, Int. J. Heat Transfer, V ol. 15, No.11, p:1787-1806.3.Wang Yunliang, X u zhong, Miao Yongmiao, 1993, Influence ofDifferent Wall Function Methods on turbulent flow fields, Fluid Engineering, V ol. 21, No. 12, : 26-29.4.Tao Wenquan, 2001, Numrical Heat Transfer (second version),Xi’an Jiaotong University Press, Xi’an, 152p.5.Tao Wenquan, 2001, Advanced Numerical Heat Transfer, SciencePublishing Company, Beijing, 41p.6.Thompson J.F., Warsi Z.U.A., Mastin C.W., 1985, Numerical GridGeneration, Foundation and Application, North-Holland New York.。
外文翻译压缩机,泵,制冷工程大学论文

Chemical and Petroleum Engineering, Vol. 40, Nos. 11–12, 2004COMPRESSORS, PUMPS, REFRIGERATION ENGINEERING UPDATING PISTON PUMPS FOR OILPRODUCTIONB. S. Zakharov,1 G. N. Sharikov,2and E. G. Kormishin2The three-plunger acid treatment pump SIN32 and the two-cylinder double-acting pump NPTs-32 with four working chambers (for cementing units) have been updated to control pump delivery. The fluid delivery diagrams for pumps of various designs are examined and the test results are reported.In drilling and oil production, single-acting three-plunger (triplex) pumps or double-acting two-cylinder (duplex) pumps are used.In injecting reagents (clay drilling mud, water, cement, acid, etc.) into wells, depending on the technology applied,it is required to inject the fluid in amounts ranging from the maximum to the minimum in a single operation. If the bed accepts the injected fluid well, it becomes necessary to maximize pump delivery for quick completion of the operation. If on the other hand, the bed does not accept the fluid well, it becomes necessary to reduce pump delivery so as to restrict the injection pressure to the safe limit. At present, because of wear of well (down-hole) equipment, the permissible injectionpressure is not higher than 10–15 MPa..The delivery of a piston (reciprocating) or a plunger (displacement) type of pump can be controlled in the following ways:• by installing several pumps with identical or different pumping capacities;• by changing the drive rotation speed;• by using cylinders (plungers) of the required size;• by channeling a part of the fluid into a bypass; and• by dismounting one or several valves.The first version is used essentially in drilling. In oil production, generally all versions are used either individually or in some combination.All pumping units designed for injection of various fluids (fluidal materials) for cementing, hydraulic formation fracturing, hydraulic sand-jet flushing of sand bridges, and other flushing operations in oil and gas wells are mounted on the chassis of motor vehicles (trucks), tractors, caterpillar (tracked) carriers, and specially made carriages.The operating parameters of the pumps (delivery and injection pressure) depend on the power of the drive and maximum and minimum speed of the engine and the pump. The pump delivery can be changed by changing the number of pump strokes without stopping the engine with the help of a gearbox (by gear shifting) and with stopping of the engine by installing cylinders of the required size. Replacement of the cylinders takes a lot of time and is not always possible in a continuous echnological process. In the existing pumping plants, the delivery variation range is inadequate. At the minimum rotation speed and cylinder diameter, the delivery remains extremely high, and for injecting the fluid into the bed the pressure has to be raised above what is permissible.Assigned by NGDU Zainskneft’, Ékogermet carried out updating of two types of pumps, namely, SIN32 and NPTs-32.In the three-plunger (triplex) acid treatment pump SIN32, for reducing the minimum delivery down to 1.0 m3/h,plungers having a diameter of 125 mm were replaced with plungers having a diameter of 55 mm. As a result, the theoretical pump delivery was reduced from 16 down to 3.3 m3/h. Further reduction of the pump delivery was achieved by reducing the rotation speed of the vehicle engine to the possible minimum (500–600 rpm).Simultaneously with this, a new design of packing glands (sealing devices) of plungers of the UPN55 type was developed.It was based on Zakharov mechanical seal [1], which demonstrated high reliability and durability in sucker-rod (oil) pumps. The sealing units and the pistons with a diameter of 55 mm were made for the SIN32 pump by ÉLKAMneftemash in Perm. Its finishing and testing were done by Ékogermet jointly with NGDU Zainskneft’.The design of the UPN55-type plunger seal is shown in Fig. 1. The combined seal consists of the main threestage mechanical seal 4 and an elastic sealingcollar 2. Each stage of the mechanical seal consists of ten rings that are elastically pressed against each other and simultaneously against the plunger surface. The rings are pressed against theplunger in pairs from the opposite sides. The next pair is turned relative to the preceding one by 90º. The rings are pressed in the axial direction by rubber rings of round cross section and in the radial direction, by rubber girdles with eccentric collars. The plunger 5 is made of steel 45 and is chromium-plated and the sealing rings are of bronze. Threecartridges with mechanical seals were installed in the housing bore 3 with a clearance that helps self-centering of the seals relative to the plunger. The cartridges are pressed together by a round nut 1 through a bushing with the sealing collar 2. There are holes in the housing for injecting oil and draining out the overflow into the receiving (suction) line of the pump.In contrast to the well-known elastic glands, the mechanical seal does not require periodic adjustments and ensures reliable operation of the assembly over a long period [2]. Use of the updated SIN32 pump having a UPN55 type of mechanical plunger seals confirmed that the proposed design operationally fit.From August through December 2003, NGDU Zainskneft’ carried out s even bottom-hole treatments (BHT) of six wells using the updated SIN32 pump. Different types of technological operations were carried out in the wells: mud acid BHT, muriatic (hydrochloric) acid BHT, injection of the reagents SNPKh-9021, MIAPROM, and RMD, for which SIN32 and ATs-32 pumping units were generally used. If acid or any other reagent could not be forced through (injected) at 12–15 MPa pressure, a low-capacity unit was connected with the SIN32 pump. In that case, the injection pressure dropped by 2–4 MPa。
汽车专业毕业论文毕业设计外文文献翻译中英文电动汽车空调系统发展趋势

外文翻译:Electric automobile air conditioning system trend ofdevelopment1. electric automobile air conditioning systemGlobal warming, air pollution and higher energy costs and other problems have become more severe, as environmental pollution and energy consumption is one of the major sources of energy saving and emission reduction, the problem is more and more extensive attention, governments and automobile enterprises will be energy saving and environmental protection as the future of automotive technology development direction of energy saving and environmental protection, such as the electric emerge as the times require. Electric vehicle is set car technology, electronic and computer technology, electrochemical technology, energy and new materials technology in one of the high-tech products, and common internal combustion engine vehicles, has the advantages of no pollution, low noise and save petroleum resource characteristics. Based on the above electric vehicle characteristics, it is very likely to become the human a new generation of clean environmentally friendly transportation, its popularization has the inestimable significance.Electric vehicle emerged for electric automobile air-conditioning research and development offerred new task and challenge. Automotive air conditioning function is put inside the temperature, humidity, air cleanliness and air flow is maintained in a comfortable state. In various climate conditions, electric car should maintain the comfortable state, to provide a comfortable driving and riding environment. In addition, a set of energy-saving and efficient air conditioning system on electric vehicle market also plays an important role. Therefore, in the development of electric vehicles at the same time, necessary to support the air conditioning system development and research.For the traditional fuel automobile air-conditioning systems, refrigeration mainly uses the engine driven steam compression refrigeration system for cooling and heating, using waste heat from fuel engine. But for the electric automobile in the pure electric vehicles and fuel cell vehicles, no air conditioning compressor engine as power source, also cannot provide as automotive air conditioning heating using heat source in winter, so it cannot be directly using conventional automotive air conditioning system solutions; for hybrid cars, the engine control means diversity, so the air conditioning compressor also cannot use the engine directly driving scheme. Integrated the above reasons, the electric vehicle development process, must study for electric vehicle using a new type of air conditioning system. For electric car,the car has a high voltage DC power supply, therefore, the use of electric heat pump type air conditioning system, compressor with motor direct drive electric vehicle, become feasible solution.2.the characteristics of electric vehicle air conditioningElectric automobile air conditioner and common air conditioning device, electric vehicle air conditioning device and car environment has the following characteristics:①automotive air conditioning system mounted on a moving vehicle, to withstand the severe and frequent vibration and shock, requirements of electric vehicle air conditioning device structure in the various components should have sufficient resistance to vibration and impact strength and good sealing performance of the system;②electric car mostly short distance walking, riding in a relatively short time, plus electric car occupant space ratio, the heat generated is relatively high, relatively large heat load of air conditioning, refrigeration, heating and has the advantages of fast speed ability;③electric automobile air conditioning is the use of the car battery to provide DC power, the working efficiency of the compressor is high, control of high reliability, convenient maintenance;④automobile body heat insulation layer is thin, and doors and windows, large glass area, insulation performance is poor, electric car is no exception, resulting in serious car heat leakage;⑤ inside the facilities is rugged and seat, air distribution organization is difficult, difficult to achieve uniform airflow distribution.3.domestic and international current situation of the development of electric vehicle air conditioning① domestic electric car air-conditioning development statusThe early domestic electric car due to battery capacity constraints, in order not to affect electric vehicle mileage, most electric cars are not equipped with air conditioning system.With the domestic electric car gradually industrialization, marketization, electric vehicles must be equipped with air conditioning system. Due to the unique effects of electric vehicles to electric vehicles, the pure electric vehicles and fuel cell vehicles, no air conditioning compressor engine as power source, also cannot provide as automotive air conditioning heating using heat source in winter, domestic car manufacturers from the traditional fuel automobile air conditioner based onpartial replacement of design, will fuel the engine to drive the the compressor is replaced by a DC motor direct drive compressors, control corresponding change, to complete the refrigeration function, the replacement design effect to resolve the basic problem of electric automobile air-conditioning refrigeration, but the cooling efficiency to be improved. Due to the lack of fuel to the engine waste heat generated by heating, domestic manufacturers mainly use PTC heating and electric heating pipe, the heating mode can meet the heating effect, but these heating mode is hard on the consumption of electric vehicle battery power, the heating efficiency is relatively low, affect electric vehicle mileage.Air conditioning in the selection of the main parts, the current domestic electric car in addition to the compressor and control mode, the other main parts or the use of fuel automotive air conditioning parts, condensing equipment is mainly used to parallel flow condenser, evaporator is mainly used to laminated evaporator, throttle device is still a thermostatic expansion valve, a refrigerant is still R134a.According to the incomplete understanding, the domestic in developing electric vehicle manufacturers such as Chery, BYD,FAW, SAIC, JAC.the current electric vehicle air conditioning facilities basically similar, is in the development present situation.②current situation of the development of foreign electric vehicle air conditioningForeign electric automobile air conditioner development relative to domestic abroad is relatively mature, there is no lack of electric automobile air conditioner with domestic similar patterns, but in the heat pump electric automobile air conditioning already had certain foundation, Japan Honda pure electric cars use electric driven heat pump type air conditioning system, system has a built-in Reverse Converter Control compression pump. In addition, in very cold areas, some type of customers can be optional a fuel heater heating system.Japan electric ( DENSO ) company a few years earlier developed using R134a refrigerant electric car air-conditioning heat pump system, the heat pump system used in the car inside air condenser and evaporator structure. Electric ( DENSO ) Company in 2003also developed as a result of natural refrigerant COgood thermal physical2properties, Denso Japan company for electric car develops a set of COheat pump air2conditioning system, also used in the air duct system is arranged in the2heat exchanger, and R134a system is different when the system for refrigeration mode when the refrigerant flows through the condenser, and internal and external condenser.In order to reduce the air conditioning on battery power consumption, the UnitedStates of America Amerigon company developed air-conditioning seat, the chair is provided with a thermoelectric heat pump, heat pump action is through the need to regulate the temperature in space outside the water tank to transfer heat, thereby realizing the need to regulate the temperature of space refrigeration or heating. This kind of air conditioning seat in addition to energy saving but also can improve the driving, riding comfort, in electric vehicle supporting the use of suitable.Therefore, the foreign electric automobile air conditioner from energy efficient and practical breakthrough, domestic electric car air-conditioning industry should actively to study overseas advanced technology, draw lessons from, and on the basis of innovation breakthrough.4.the development trend of electric vehicle air conditioningElectric automobile driving energy from the battery, which is different from the traditional fuel automobile, made it to the air conditioning system also differed from the fuel of automobile air conditioner, as a drive source of energy for the limited battery capacity, the energy consumption of air conditioning system on electric vehicle mileage has bigger effect. Compared with cars, car air conditioning system energy saving and high efficiency raised taller requirement. At the same time, the electric car air-conditioning refrigeration, heating to solve two problems. According to the electric car special properties, the electric automobile air conditioner using thermoelectric ( I ) air conditioning system and electric heat pump type air conditioning system.1).a thermoelectric ( I ) electric vehicle air conditioning systemThe technology has many suitable for electric vehicles use characteristics, and with the traditional mechanical compression type air conditioning system compared, thermoelectric air conditioning has the following characteristics:① thermoelectric elements work to DC power supply;②change the direction of the current to generate refrigeration, heating the converse effect;③thermoelectric refrigeration piece of thermal inertia is small, cooling time is very short, the hot end heat well cold end load cases, energized in less than a minute, the refrigeration sheet can achieve the maximum temperature difference;④ component for regulating current size can adjust refrigeration speed and temperature, the temperature control precision can reach 0.001℃, and can easily realize the continuous regulating energy;⑤in the correct design and application conditions, the refrigerationefficiency can reach above 90%, and the heating efficiency is greater than 1;⑥ has the advantages of small volume, light weight, compact structure, reduces the electric vehicle kerb mass; high reliability, long service life and convenient maintenance; no moving components, therefore, no vibration, no friction, no noise and impact resistance.2).the heat pump type air conditioning system for electric automobileThe heat pump type air conditioning system on the original fuel car to be improved, the compressor is composed of permanent magnet brushless DC motor for direct drive, the system and the ordinary heat pump air conditioning system have no essential difference, as in electric vehicles, compressor and other major components has its particularity. And foreign heat pump technology has had certain foundation, the biggest advantage is that the refrigeration, heating efficiency is high, relevant enterprise development of full closed electric scroll compressor, is composed of a DC brushless motor drive, through the refrigerant return air cooling, with low noise, small vibration, compact structure, light weight etc.. In the test conditions for the environmental temperature of 40 degrees Celsius, the temperature inside the car is27℃,50% relative humidity conditions, when the system is stable it to1kW energy2.9kW refrigeration quantity; when the environmental temperature is - l0C, the temperature inside the car to25 DEG C,1kW can get the 2.3kW heating energy consumption. In the - l0℃to 40 ℃ under ambient temperature, both with high efficiency for electric vehicles to provide a comfortable driving environment. If the component technology is improved, the corresponding efficiency can also be improved.Based on the above mentioned, from air conditioning technology is mature and the sources of energy to use efficiency comparison, for thermoelectric ( I ) electric vehicle air conditioning system, the existence of thermoelectric materials, figure of merit is low, performance is not ideal, and the thermopile output by constitute a thermoelectric element element yield limit hoof. Does not have the electric automobile air-conditioning energy efficiency requirements. This makes the electric automobile air conditioner are more inclined to use energy efficient heat pump type air conditioner, the technical scheme for different types of motor vehicle has good commonality, and the vehicle structural change is small, is the future development trend of electric vehicle air conditioning.The heat pump type electric automobile air conditioner biggest weakness is the low temperature heating problems, especially in the northeast region, which is also the future of the industry research problem. In order to make the heat pump type electric automobile air conditioner more energy efficient, can from the followingaspects to solve:① to develop more efficient DC scroll compressor;②development control is more accurate, more energy-efficient silicon electronic expansion valve;③ using an efficient parallel flow condenser;④ improve microchannel evaporator structure, so that the refrigerant evaporates more uniform.In addition, the number of electric car door open and in driving by speed, light, speed and other factors, air conditioning heat load. The compressor and the air conditioning system to adapt to the change of condition factors, so the heat pump type air conditioning system for electric automobile variational design is particularly important.电动汽车空调系统发展趋势一、电动汽车空调系统全球气候变暖、大气污染以及能源成本高涨等问题日趋严峻,汽车作为环境污染和能源消耗的主要来源之一,其节能减排问题受到了越来越广泛的重视,各国政府和汽车企业均将节能环保当作未来汽车技术发展的指导方向,这样节能环保的电动也就应运而生。
涡旋压缩机在R410a方面的应用
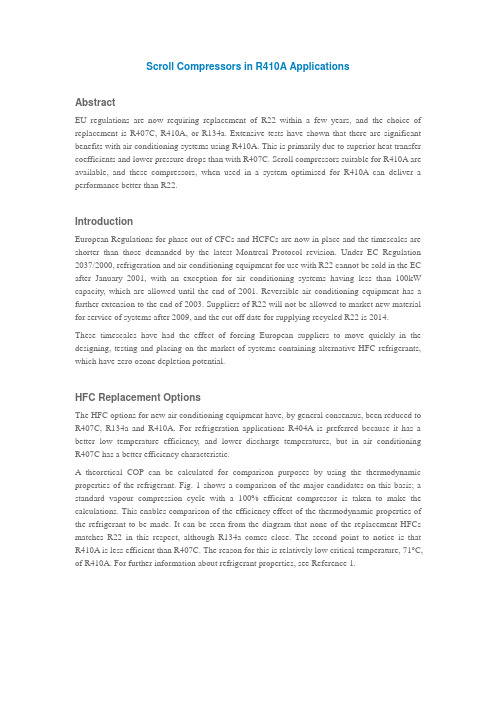
Scroll Compressors in R410A ApplicationsAbstractEU regulations are now requiring replacement of R22 within a few years, and the choice of replacement is R407C, R410A, or R134a. Extensive tests have shown that there are significant benefits with air conditioning systems using R410A. This is primarily due to superior heat transfer coefficients and lower pressure drops than with R407C. Scroll compressors suitable for R410A are available, and these compressors, when used in a system optimised for R410A can deliver a performance better than R22.IntroductionEuropean Regulations for phase out of CFCs and HCFCs are now in place and the timescales are shorter than those demanded by the latest Montreal Protocol revision. Under EC Regulation 2037/2000, refrigeration and air conditioning equipment for use with R22 cannot be sold in the EC after January 2001, with an exception for air conditioning systems having less than 100kW capacity, which are allowed until the end of 2001. Reversible air conditioning equipment has a further extension to the end of 2003. Suppliers of R22 will not be allowed to market new material for service of systems after 2009, and the cut off date for supplying recycled R22 is 2014.These timescales have had the effect of forcing European suppliers to move quickly in the designing, testing and placing on the market of systems containing alternative HFC refrigerants, which have zero ozone depletion potential.HFC Replacement OptionsThe HFC options for new air conditioning equipment have, by general consensus, been reduced to R407C, R134a and R410A. For refrigeration applications R404A is preferred because it has a better low temperature efficiency, and lower discharge temperatures, but in air conditioning R407C has a better efficiency characteristic.A theoretical COP can be calculated for comparison purposes by using the thermodynamic properties of the refrigerant. Fig. 1 shows a comparison of the major candidates on this basis; a standard vapour compression cycle with a 100% efficient compressor is taken to make the calculations. This enables comparison of the efficiency effect of the thermodynamic properties of the refrigerant to be made. It can be seen from the diagram that none of the replacement HFCs matches R22 in this respect, although R134a comes close. The second point to notice is that R410A is less efficient than R407C. The reason for this is relatively low critical temperature, 71°C, of R410A. For further information about refrigerant properties, see Reference 1.Fig.1 Comparison of Theoretical COP for Refrigerants, based on Condensing Temperature 40°C, Suction Superheat 20K, zero SubcoolingThere are several other vital properties of a refrigerant which contribute towards the overall system behaviour. They are summarised in the table shown in Fig 2. The first is operating pressure. R134a has a lower pressure than R22, and it requires a larger displacement compressor and larger tubing to achieve the same performance as for R22. These factors tend to increase system cost, although there are some applications for which R134a is particularly suited, such a screw chillers. R410A has a pressure considerably above that of R22, which should tend to reduce system cost. However it has taken time for proven high pressure components suitable for R410A to become available. This, combined with the fact that the theoretical COP is poorer, has lead to the extensive adoption of R407C as an R22 replacement. A further benefit of high pressures is that there is a reduction in the effect of pressure drops. This can either result in smaller tubing for equivalent pressure drop effect, or lower losses if the same size tube is used.Fig 2. Refrigerant Properties and System Effects, Reference R22R407C has a similar pressure to R22, making it an obvious choice, with little system redesign necessary. A property which needs consideration with R407C is the temperature glide, which makes careful definition of temperatures necessary. A full explanation of the effect of temperature glide on compressor and system performance definition is given in Reference 2. Some concerns about the effects of composition changes with glide refrigerants have been expressed, but system designers have demonstrated that R407C works perfectly well in properly designed installations, with an efficiency close to that of R22.Merits of R410AThe next environmental issue which manufacturers will need to face will certainly be energy efficiency, because the efficiency is directly related to carbon dioxide emissions from power generation, and most countries are committed to reducing these emissions under the Kyoto agreement. In the USA energy efficiency of air conditioning has always had a high profile. Efficiency regulations will play an important role in moving the U.S. market away from use of R22. Recently enacted ASHRAE 90.1 standards will increase efficiency demands on commercial A/C systems by up to 20%, and a new, higher minimum efficiency regulation is under consideration for the U.S. residential market.In order to appreciate why R410A has the potential for improvements over R22 and R407C, it is necessary to consider the relative effects on parameters round the system. Copeland has been heavily involved in evaluating R22 alternatives for both residential and commercial air conditioning applications, and the results of those studies can be summarised with reference to Fig 3. The nominal operating conditions for the tests were: evaporating temperature, 7C, condensing temperature 40C with 11K superheat and 8.3K subcooling. The first parameter is the theoretical efficiency, and as already discussed this is approximately 4% lower than R22, and is shown as a negative in Fig 3.Fig.3 Percentage Efficiency Effects for R410A, Reference R22Compressor testing has demonstrated that there can be a gain of up to 2% in compressor efficiency in the R410A system. This is shown as a positive in Fig 3 and goes some way towards offsetting the negative refrigerant properties effect, although it should still be noted that the COP of the R410A scroll will generally be slightly below that of the R22 equivalent, as shown in Fig.2. The compressor COP is a combination of the compressor efficiency and the refrigerant properties.Now we move on to other system parameters. The superheat and subcooling will have a small effect as shown, due to refrigerant properties. By far the largest effect is the major gain in performance due to better heat transfer in the evaporator. This gain has the effect of raising the evaporating temperature by 2K. For the same air temperatures, the increased evaporating temperature with the R410A system improves system efficiency and capacity by a significant amount. There was also a small effect due to improved heat transfer in the condenser. The overall COP percentage improvement is shown in Fig 3 as 6% when referenced to the compressor only, or 5% for the system, which takes account of the fan power.Practical Considerations for R410AR410A operating pressures are 50% higher than R22 pressures. That means using gauges specifically designed for higher pressures and gives added importance to the quality of joint brazing during installation.Although it might seem that R410A's higher pressures would result in higher system temperatures, in fact, tests have shown the opposite. Under similar conditions, R410A systems actually ran at cooler temperatures than R22 systems.Because R410A systems in common with all other HFC systems use polyol ester oil, and cleanliness is important because POE oils are hydroscopic. That is, they readily absorb moisture, so units should be capped whenever possible, and exposure to the atmosphere should be kept to a minimum. This is normal good practice for all refrigeration systems.Compressors for R410ACopeland Scroll Compressors are available in 5 models which will deliver 5 to 15kW cooling (ARI conditions). Fig.4 shows a cross section of the “ZP” or R410A scroll, and the components which differ from the previous R22 model are indicated.Fig.4 ZP Scroll Compressor Showing Changes Made for R410AConclusionsOptimised system tests have shown R410A delivers higher system efficiency than R22. Its higher heat transfer coefficient and lower pressure drop allow for these performance gains. This means coil surface areas can be reduced while maintaining the same system efficiency.Actual field experience has confirmed that systems using Copeland Scrolls with R410A are more reliable, more efficient and offer greater sound reduction than those using R22. Its increasing use in the high-volume residential market, particularly in the USA should eventually drive down R410A's cost and provide stocking and service advantages in the commercial market as well.Thicker Top CoverHigh PressureDifferential IPR ValveRedesigned Lower CoverSmaller Scroll SetSmallerCounterweights Changed for R410ADischarge GasTemperature SensorReferences(1) Domanski, P A. “La Storia attuale e futura nell’impiego dei refrigeranti”, Congresso Internationale Della Refrigerazione, 4 maggio 1999, Milano(2) Hundy, G F and Vittal R., “Compressor Performance Definition for Refrigerants with Glide”. Proceedings of the 2000 International Refrigeration Conference at Purdue, 2000.。
- 1、下载文档前请自行甄别文档内容的完整性,平台不提供额外的编辑、内容补充、找答案等附加服务。
- 2、"仅部分预览"的文档,不可在线预览部分如存在完整性等问题,可反馈申请退款(可完整预览的文档不适用该条件!)。
- 3、如文档侵犯您的权益,请联系客服反馈,我们会尽快为您处理(人工客服工作时间:9:00-18:30)。
三维排放涡旋空气压缩机流动数值模拟Jian Mei Feng, Zong Chang Qu, Xin Wei Lin能源与动力工程学院中国西安交通大学,西安710049E- mail地址:jmfeng@zchqu@lxw5837@概述涡旋压缩机在传统压缩机行业里被公认为有较高的竞争力。
大量的出版物极有兴趣的证明了这一点。
在流动损失效率得到进一步提高的同时,特别是在最后的压缩区和排放区,流动损失更是大大地被减少。
详细了解流动过程中发生在排放区的流动损失是分析和减少排放流量损失的有利条件,这对减少严重损失是非常必要地。
由于过程的复杂性,只有一个方法可以解决连续性和动量方程,那就是采用数值计算方法。
在过去的10年里,进行了一些对涡旋压缩机的性能的调查。
不过,对流体流动特性的细节的讲解的资料是相对很少的,尤其是在涡旋压缩机室。
在本论文中,应用物理模型对实际的涡旋空气压缩机排放区的放电过程中的一个特点,作出合理的简化和三维准稳态湍流数值模拟。
通过对排放区出口端的三维速度和压力分布进行典型流动分析,我们可以对涡旋空气压缩机的物理过程有深入地了解。
1. 引言涡旋压缩机广泛应用于制冷,空调及电力领域,其竞争优势是在于它的高效率,和能够减少部分损失的要求,降低噪音,减少振动水平。
三维模拟涡旋压缩机的运行,如:移动动涡盘的轨道、摩擦损失和流动阻力损失等各种损失。
这些损失是该排放流量(由于流动损失约消耗百分之3的输入功率)的主要部分,特别是在大流量过程中。
在流动过程中存在放电现象,因此在最后压缩地区要减少这些流动亏损,尤其是在速度增加的大流量区域更明显。
因此,在涡旋空气压缩机顶部进行三维放电数值模拟是十分有必要的。
最重要的流动模式,是在排放和最终压缩区。
尤其是在大流量涡旋压缩机排气口务必要根据分析结果,来为寻找供应来源的排放所造成的损失进行理论分析和设计。
本文研究的对象是一个1.6 的涡旋空气压缩机的排放量。
最重要的理论研究对象是对对称弧和排放区的修改和整定。
基本参数和修改后的提示参数列于表1。
示意图1显示了涡旋压缩机的排放区域。
表1:基本参数和修改后的参数图1:涡旋压缩机排放区示意图。
2. 物理模型与数值方法2.1 物理模型这种气体通过涡旋齿的“压缩运动”而提供动力,而涡旋齿的这种运动可以在涡旋压缩机的工作腔内对可压缩性粘性非定常流的气体进行压缩。
由于高转速和附近的靠近腔壁的速度梯度,所以气体的湍流特性必须加以考虑。
但绕壁速度比较小的气体速度,例如,在腔壁上的速度大约是百分之5的气体速度是本文研究空气压缩机排放的平均速度,因此它必须在准稳态的环境下,并且有固定的流场。
也就是说,忽略轨道流动的腔壁运动是有道理的。
因此,进行三维稳态湍流计算分析,是对压缩区和排放区流场的预测和分析。
在涡旋压缩机中空气是从两个方向注入到压缩腔内的,并且两侧各有曲柄角度。
不同的体积流量在不同曲轴的排放过程中显示的数字在一定的曲柄角度是不一样的,曲柄角度如图2。
图3显示了一个计算模型的角度。
图2:排放量与轨道曲轴转角的关系图3:三维计算模型2.2 数值方法湍流流动中存在着已经被公认、和经常应用的k -x湍流模型。
应用离散方程,和有限体积法可以解决湍流模型。
通常采用SIMPLE算法以纠正压力系数。
附近的腔壁,通过改进方法,可以求得腔壁函数。
对于对流项和扩散项的离散格式可以采用二阶求导式和中心差分格式。
数值模拟(2001)显示了离散化方法的细节。
在对计算域的几何特点进行的分析可以看出,整个域的不同部分的几何尺寸相差是很大的;用分割块结构网格的方法来使全域网分成几个部分,其中排放产生的分离是可以在坐标网格系统中求得(Thompson J.F., et al., 1985)。
总体网格是通过电网的独立精细计算结果来确立的。
在不同的计算过程中曲柄角度是不同的,所以产生了网格分开。
边界条件如下所示:(a) 进口每两个入口质量流率是相同的,瞬时体积变化率是成倍增加的。
(b)出口出口的位置设置在远离排放区的5倍的高度,以保证恒定的压力。
排放压力提供了出口压力。
(c)腔壁非滑移边界条件为腔壁的速度提供了条件。
先进的腔壁函数法用来确定腔壁附近的速度条件。
3. 数值结果在本文中,被定义为轨道排放曲轴转角。
在排放气体的时刻,即曲柄角度y =45(是排放曲轴角度),y为零。
然后,在整个排放过程中,是从0到360度变化。
根据这一定义,例如,在排放后曲轴转角为45度角时,这时x= 45 。
本文为了描述方便,在z坐标等于零的位置定义为排放区的进口,并以固定滚动表面的名字命名。
在z坐标位置等于涡旋齿的高度时,以固定滚动顶面的名字命名。
中心流场和中心腔在几个不同区域的流量的曲柄角度为45,90,180度,本文只对曲柄角度为90度和180度进行了研究。
并且对不同的轴向速度矢量和三维速度向量进行了详细分析。
3.1 y = 45在图4(a)-(c)中显示的是不同的轴向速度场的计算结果,但其在轨道排放上的曲轴错角都为45度角。
图4表明,当流速以一半的速度注入在腔壁中央后方时,这种情况就不成立,因为流速在轨道上流动时是以固定的方式流动的,对腔壁区域有反流动趋势。
在中部区域,流体从半流动状态进入腔壁中央室,通过固定的轨道以及在流动所形成的惯性推动力的作用下在喉咙地区传递。
对于两项大型涡旋压缩机中外表面和腔壁中央室的发展规模已经有所壮大,而小型压缩机在其动涡盘的中心的发展方向也有了一定的规模。
比较图4(1)、(b)、(c),结果表明,随着涡旋流轴节的位置、数量、规模以及动涡盘涡的位置的不同,所显示的轴节也就不同。
这就是说这个基本涡流动态模式在这一区域是仍然存在的,特别是在整个腔壁中央室的轴向流动过程中。
三维速度向量如图5所示,清楚表明了轴向速度分量的分布。
三维涡流趋于垂直向下移动,因为它在接近腔壁中央室是直接排放流体的。
轴向速度分量是在0 - 10mm这一小的区域内变化,并且在排放区等于轴向距离(当轴向距离的高度为52mm时非常大)。
在数量级上轴向速度比径向速度更大。
与此相反,在腔壁中央室后方区域内,流动基本上是二维的。
从图4和图5可以看出,在某一节中的轴向速度向量图刻画了在整个腔壁中央室中的流体流动的一般性质。
证明流动载体无论是二维的还是三维的模型,其都在具体位置上具有流动性。
因此,现仅对中期的速度矢量做以下分析。
图4:不同的轴向速度场位置图5:三维速度矢量3.2 y= 90在上面的计算中已完成了一个中间曲柄角度(y = 90 )。
如图6所示。
随着涡旋压缩机实际排放过程的持续,流体继续从固定的轨道流动。
这一过程是在排放区域逐步增加的基础上实现的。
这意味着该排放口在低排放情况下比y =45 的情况下更低。
在另一平面中和排放区域速度矢量的轴向部分比y =45 在速度和程度上都有不同的减少现象。
对于双涡旋我们假意预测,在曲柄转角和中间轴方向上涡流速度得到提升后,有可能成为漩涡。
图6:不同的轴向速度场位置3.3 y= 180图7(a)- (b)显示的是在排放过程中曲柄转角为180度的情况下的速度矢量。
图中所作出的速度矢量场,显然是与图4和图6所示的有所不同的。
此时的涡旋涡轮在排放时时完全打开的。
此外,流体流动面积较少的区域的有的流体流出通道,使速度幅度进一步降低。
在腔壁中央室里,速度向量场发生小规模的湍动,形成漩涡。
图7:不同的轴向速度场位置4. 无量纲压力损失系数无量纲压力损失系数能够表征最后压缩区和排放区的压力损失情况,其定义如下:P是在中央腔的平均压力,单位为Pa; Pd是设计流量的压力,单位为pa。
压力损失的变化与排放过程中曲轴的不同转角有关,并且在不同的操作条件还与整个排放过程的无量纲压力损失系数有关。
如图8所示。
压力损失系数在曲轴转角为0-60度的情况下是非常大的。
举例来说,在45度曲轴转角时的压力损失系数约为10倍于180度的压力损失系数,这表明流动损失在排放转角小时最多。
这个结果并不令人惊讶,因为这也是该排放区域的最大收缩流动点。
此外,在高转速情况下,证实排气压力有显着的流量损失存在。
随着排放区域的开启,压力损失系数迅速下降。
结果表明,排放区的开启加快了排放流量损失。
此外,这些结果意味着,排放区开闭的特点,应在设计时要特别的考虑,特别是一个有着大流量的排放区的压缩机。
想要获取好的排放效益,好的排放区设计是必须的。
另外,排放区的面积不是越大越好的。
图8:无量纲压力损失与轨道排放系数曲轴转角5:结论在对涡旋空气压缩机排放流量进行了三维数值模拟以后,可以为我们提供最后的压缩区和排放区的流场特性。
本文也详细分析了在不同曲轴转角下流速向量。
计算结果表明,复杂的旋涡流动状态存在于排放区不同的曲轴转角上。
在计算结果的基础上,分析了压力损失系数的定义和不同的压力损失在不同的曲柄角度下的模拟数值计算。
结果表明,排放流量大的压力损失系数也越大。
结果也同样表明,排放区的特点是排放面积不是越大越好。