艾默生-谷轮R410A产品手册-Veranda(2011)
R410A制冷剂性质简介及安装维修服务指南
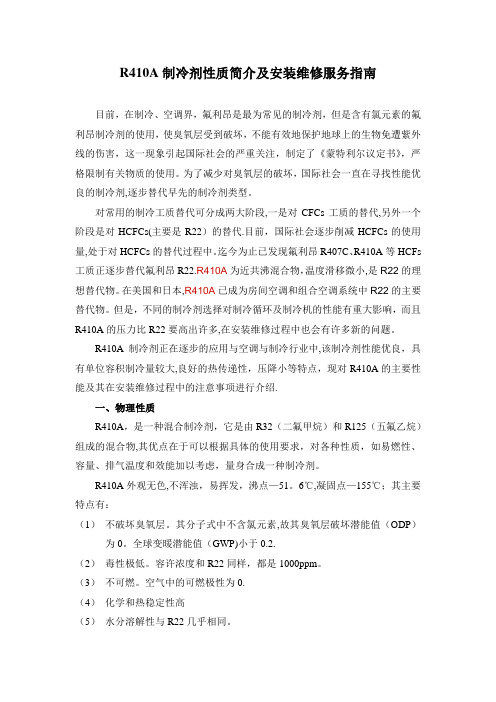
R410A制冷剂性质简介及安装维修服务指南目前,在制冷、空调界,氟利昂是最为常见的制冷剂,但是含有氯元素的氟利昂制冷剂的使用,使臭氧层受到破坏,不能有效地保护地球上的生物免遭紫外线的伤害,这一现象引起国际社会的严重关注,制定了《蒙特利尔议定书》,严格限制有关物质的使用。
为了减少对臭氧层的破坏,国际社会一直在寻找性能优良的制冷剂,逐步替代早先的制冷剂类型。
对常用的制冷工质替代可分成两大阶段,一是对CFCs工质的替代,另外一个阶段是对HCFCs(主要是R22)的替代.目前,国际社会逐步削减HCFCs的使用量,处于对HCFCs的替代过程中。
迄今为止已发现氟利昂R407C、R410A等HCFs 工质正逐步替代氟利昂R22.R410A为近共沸混合物,温度滑移微小,是R22的理想替代物。
在美国和日本,R410A已成为房间空调和组合空调系统中R22的主要替代物。
但是,不同的制冷剂选择对制冷循环及制冷机的性能有重大影响,而且R410A的压力比R22要高出许多,在安装维修过程中也会有许多新的问题。
R410A制冷剂正在逐步的应用与空调与制冷行业中,该制冷剂性能优良,具有单位容积制冷量较大,良好的热传递性,压降小等特点,现对R410A的主要性能及其在安装维修过程中的注意事项进行介绍.一、物理性质R410A,是一种混合制冷剂,它是由R32(二氟甲烷)和R125(五氟乙烷)组成的混合物,其优点在于可以根据具体的使用要求,对各种性质,如易燃性、容量、排气温度和效能加以考虑,量身合成一种制冷剂。
R410A外观无色,不浑浊,易挥发,沸点—51。
6℃,凝固点—155℃;其主要特点有:(1)不破坏臭氧层。
其分子式中不含氯元素,故其臭氧层破坏潜能值(ODP)为0。
全球变暖潜能值(GWP)小于0.2.(2)毒性极低。
容许浓度和R22同样,都是1000ppm。
(3)不可燃。
空气中的可燃极性为0.(4)化学和热稳定性高(5)水分溶解性与R22几乎相同。
R410A分离式空调系列用户手册说明书
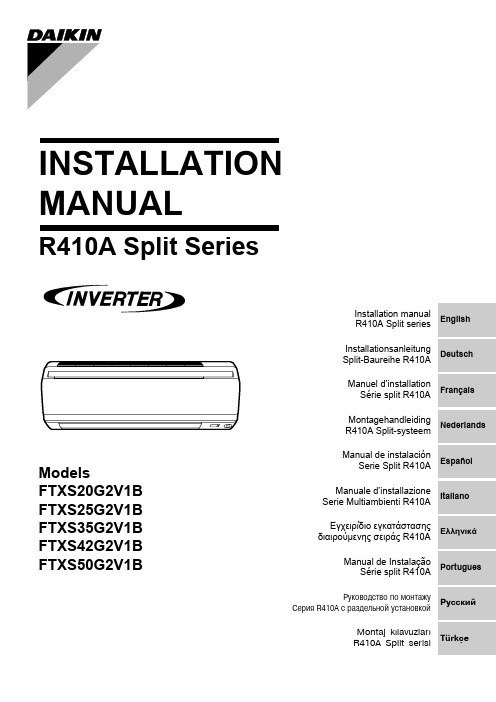
INSTALLATION MANUALR410A Split SeriesModelsFTXS20G2V1B FTXS25G2V1B FTXS35G2V1B FTXS42G2V1BFTXS50G2V1BDeutschFrançaisNederlandsEspañolItalianoΕλληνικÜPortuguesРóссêийEnglishTürkçeInstallation manual R410A Split series Montaj kýlavuzlarý R410A Split serisiInstallationsanleitung Split-Baureihe R410A Manuel d’installation Série split R410A Montagehandleiding R410A Split-systeem Manual de instalaciónSerie Split R410A Manuale d’installazione Serie Multiambienti R410A Εγχειρßδιο εγκατÜστασηòδιαιροýìενηò σειρÜò R410AManual de Instalação Série split R410AРóêоводство по монтажóСерия R410A с раздельной óстановêойU m e d a C e n t e r B l d g ., 2-4-12, N a k a z a k i -N i s h i ,K i t a -k u , O s a k a , 530-8323 J a p a n0G 2V 1B , F T X S 25G 2V 1B , F T X S 35G 2V 1B , F T X S 42G 2V 1B , F T X S 50G 2V 1BI N I N D U S T R I E S , L T D .S h i n r i S a d a M a n a g e r Q u a l i t y C o n t r o l D e p a r t m e n t 1s t . o f N o v . 2008L o w V o l t a g e 2006/95/E C E l e c t r o m a g n e t i c C o m p a t i b i l i t y 2004/108/E C *D A I K I N .T C F .015 L 3/08-2007K E M A Q u a l i t y B .V .74736-K R Q /E M C 97-4957Safety Precautions•The precautions described herein are classified as WARNING and CAUTION. They both contain important informa-tion regarding safety. Be sure to observe all precautions without fail.•Meaning of WARNING and CAUTION noticesWARNING....Failure to follow these instructions properly may result in personal injury or loss of life.CAUTION.....Failure to observe these instructions properly may result in property damage or personal injury, which may be serious depending on the circumstances.•The safety marks shown in this manual have the following meanings:Be sure to follow the instructions. Be sure to establish an earth connection. Never attempt.•After completing installation, conduct a trial operation to check for faults and explain to the customer how to operate the air conditioner and take care of it with the aid of the operation manual.WARNING•Ask your dealer or qualified personnel to carry out installation work.Do not attempt to install the air conditioner yourself. Improper installation may result in water leakage, electric shocks or fire.•Install the air conditioner in accordance with the instructions in this installation manual.Improper installation may result in water leakage, electric shocks or fire.•Be sure to use only the specified accessories and parts for installation work.Failure to use the specified parts may result in the unit falling, water leakage, electric shocks or fire.•Install the air conditioner on a foundation strong enough to withstand the weight of the unit.A foundation of insufficient strength may result in the equipment falling and causing injury.•Electrical work must be performed in accordance with relevant local and national regulations and with instructions in this installation manual. Be sure to use a dedicated power supply circuit only.Insufficiency of power circuit capacity and improper workmanship may result in electric shocks or fire.•Use a cable of suitable length.Do not use tapped wires or an extension lead, as this may cause overheating, electric shocks or fire.•Make sure that all wiring is secured, the specified wires are used, and that there is no strain on the terminal con-nections or wires.Improper connections or securing of wires may result in abnormal heat build-up or fire.•When wiring the power supply and connecting the wiring between the indoor and outdoor units, position the wires so that the control box lid can be securely fastened.Improper positioning of the control box lid may result in electric shocks, fire or over heating terminals.•If refrigerant gas leaks during installation, ventilate the area immediately.Toxic gas may be produced if the refrigerant comes into contact with fire.•After completing installation, check for refrigerant gas leakage. Toxic gas may be produced if the refrigerant gas leaks into the room and comes into contact with a source of fire, such as a fan heater, stove or cooker.•When installing or relocating the air conditioner, be sure to bleed the refrigerant circuit to ensure it is free of air, and use only the specified refrigerant (R410A).The presence of air or other foreign matter in the refrigerant circuit causes abnormal pressure rise, which may result in equipment damage and even injury.•During installation, attach the refrigerant piping securely before running the compressor.If the compressor is not attached and the stop valve is open when the compressor is run, air will be sucked in, causing abnormal pressure in the refrigeration cycle, which may result in equipment damage and even injury.•During pump-down, stop the compressor before removing the refrigerant piping.If the compressor is still running and the stop valve is open during pump-down, air will be sucked in when the refrigerant piping is removed, causing abnormal pressure in the refrigeration cycle, which may result in equipment damage and even injury.•Be sure to earth the air conditioner. Do not earth the unit to a utility pipe, lightning conductor or telephone earth lead.Imperfect earthing may result in electric shocks.•Be sure to install an earth leakage breaker.Failure to install an earth leakage breaker may result in electric shocks or fire.CAUTION•Do not install the air conditioner at any place where there is a danger of flammable gas leakage.In the event of a gas leakage, build-up of gas near the air conditioner may cause a fire to break out.•While following the instructions in this installation manual, install drain piping to ensure proper drainage and insu-late piping to prevent condensation.Improper drain piping may result in indoor water leakage and property damage.•Tighten the flare nut according to the specified method such as with a torque wrench.If the flare nut is too tight, it may crack after prolonged use, causing refrigerant leakage.AccessoriesChoosing an Installation Site•Before choosing the installation site, obtain user approval.1.Indoor unit.•The indoor unit should be sited in a place where:1)the restrictions on installation specified in the indoor unit installation drawings are met,2)both air intake and exhaust have clear paths met,3)the unit is not in the path of direct sunlight,4)the unit is away from the source of heat or steam,5)there is no source of machine oil vapour (this may shorten indoor unit life),6)cool (warm) air is circulated throughout the room,7)the unit is away from electronic ignition type fluorescent lamps (inverter or rapid start type) as they may shorten the remote controller range,8)the unit is at least 1 metre away from any television or radio set (unit may cause interference with the picture or sound),9)install at the recommended height (1.8m).2.Wireless remote controller.1)Turn on all the fluorescent lamps in the room, if any, and find the site where remote controller signals are properly received by the indoor unit (within 7 metres).2)Make the dipswitch settings. Set according to the type of unit purchased by the customer. The default settings are on the heat pump side.•For cooling only (Outdoor unit model: RKS)Set the dipswitches on the cooling only side.•For heat pump (Outdoor unit model: RXS)Check that the dipswitches are on the heat pump side.If they are set on the cooling only side, move them to the heat pump side.Installation Tips1.Removing and installing front panel.•Removal methodHook fingers on the panel protrusions on the left and right of the main body, and open until the panel stops. Slide the front panel sideways to disengage the rotating shaft. Then pull the front panel toward you to remove it.•Installation method2.Removing and installing front grille.•Removal method1)Remove front panel to remove the air filter.2)Remove the front grille.3)In front of the {{{of your other hand.When there is no work space because the unit is close to ceilingCAUTIONBe sure to wear protection gloves.Place both hands under the center of the front grille, and while pushing up, pull it toward you.•Installation method1)Install the front grille and firmly engage the upper hooks (3 locations).2)Install 2 screws of the front grille.3)Install the air filter and then mount the front panel.3.How to set the different addresses.When 2 indoor units are installed in 1 room, the 2 wireless remote controllers can be set for different addresses.1)Remove the metal plate electrical wiring cover.(Refer to the Removal/attachment methods of metal plate electrical wiring covers .)2)Cut the address jumper (JA) on the printed circuit board.3)Cut the address jumper (J4) in the remote controller.4.When connecting to an HA system.(Wired remote controller, central remote controller etc.)1)Remove the metal plate electrical wiring cover.(Refer to the Removal/attachment methods of metal plate electrical wiring covers .) 2)Attach the connection cord to the S21 connector and pull theharness out through the notched part in the figure.3)as it was, and pull the harness around, as shown in the figure.Installation TipsIndoor Unit Installation DrawingsCAUTION1)Do not hit or violently push the Intelligent-eye sensor. This can lead to damage and malfunction.2)Do not place large objects near the sensor. Also keep heating units or humidifiers outside the sensor’s detection area.Indoor Unit Installation1.Installing the mounting plate.•The mounting plate should be installed on a wall which can support the weight of the indoor unit.1)Temporarily secure the mounting plate to the wall, make sure that the panel is completely level, and mark the boringpoints on the wall.2)Secure the mounting plate to the wall with screws.Recommended mounting plate retention spots and Dimensions2.Boring a wall hole and installing wall embedded pipe.•For walls containing metal frame or metal board, be sure to use a wallembedded pipe and wall cover in the feed-through hole to prevent possible heat, electrical shock, or fire.•Be sure to caulk the gaps around the pipes with caulking material to prevent water leakage.1)Bore a feed-through hole of 65mm in the wall so it has a down slope toward the outside.2)Insert a wall pipe into the hole.3)Insert a wall cover into wall pipe.4)After completing refrigerant piping, wiring, and drain piping, caulk pipe hole gap with putty.3.Installing indoor unit.3-1.Right-side, right-back, or right-bottom piping.1)Attach the drain hose to the underside of the refrigerant pipes with an adhesive vinyl tape.2)Wrap the refrigerant pipes and drain hose together with an insulation tape.3)4)(Refer to Installation tips.)5)tape.)6)catch on the edge of the indoor unit.Indoor Unit Installation3-2.Left-side, left-back, or left-bottom piping.1)Attach the drain hose to the underside of the refrigerant pipes with adhesive vinyl tape.2)Be sure to connect the drain hose to the drain port in place of a drain plug.3)Shape the refrigerant pipe along the pipe path marking on the mounting plate.4)Pass drain hose and refrigerant pipes through the wall hole, then set the indoor unit on mounting guide.5)Pull in the interconnecting wires.6)Connect the inter-unit piping.7)Wrap the refrigerant pipes anddrain hose together with insulation tape as right figure, in case of setting the drain hose through the back of the indoor unit.8)While exercising care so that the interconnecting wires do not catch indoor unit, press the bottom edge of indoor unit with both hands until it is firmly caught by the mounting plate hooks. Secure indoor unit to the mounting plate with screws (M4 × 12L).3-3.Wall embedded piping.Follow the instructions given under 1)Insert the drain hose to this depth so it won’t be pulled out of the drain pipe..4.Wiring., install as described in the installation manual supplied with the Multi outdoor unit.1)Strip wire ends (15mm).2)Match wire colours with terminal numbers on indoor and outdoor unit’s terminal blocks and firmly screw wires to the corresponding terminals.3)Connect the earth wires to the corresponding terminals.4)Pull wires to make sure that they are securely latched up, then retain wires with wire retainer.5)In case of connecting to an adapter system. Run the remote controller cable and attach the S21.6)Shape the wires so that the service lid fits securely, then close service lid.WARNING1)Do not use tapped wires, strand wires, extensioncords, or starburst connections, as they may cause overheating, electrical shock, or fire.2)Do not use locally purchased electrical parts inside the product. (Do not branch the power for the drain pump, etc., from the terminal block.) Doing so may cause electric shock or fire.5.Drain piping.1)Connect the drain hose, as described right.2)Remove the air filters and pour some water into the drain pan to check the water flows smoothly.3)When drain hose requires extension, obtain an extension hose commercially available.Be sure to thermally insulate the indoor section of the extension hose.4)When connecting a rigid polyvinyl chloride pipe (nominal diameter 13mm) directly to the drain hose attached to the indoor unit as withembedded piping work, use any commercially available drain socket (nominal diameter 13mm) as a joint.Refrigerant Piping Work, install as described in the installation manual supplied with the Multi outdoor unit.1.Flaring the pipe end.1)Cut the pipe end with a pipe cutter.2)Remove burrs with the cut surface facing downward so that the chips do not enter the pipe.3)Put the flare nut on the pipe.4)Flare the pipe.5)Check that the flaring is properly made.WARNING1)Do not use mineral oil on flared part.2)Prevent mineral oil from getting into the system as this would reduce the lifetime of the units.3)Never use piping which has been used for previous installations. Only use parts which are delivered with the unit.4)Do never install a drier to this R410A unit in order to guarantee its lifetime.5)The drying material may dissolve and damage the system.6)Incomplete flaring may cause refrigerant gas leakage.2.Refrigerant piping.CAUTION1)Use the flare nut fixed to the main unit. (To prevent cracking of the flare nut by aged deterioration.)2)To prevent gas leakage, apply refrigeration oil only to the inner surface of the flare. (Use refrigeration oil for R410A.)3)Use torque wrenches when tightening the flare nuts to prevent damage to the flare nuts and gas leakage.Align the centres of both flares and tighten the flare nuts 3 or 4 turns by hand. Then tighten them fully with the torque wrenches.2-1.Caution on piping handling.1)Protect the open end of the pipe against dust and moisture.2)All pipe bends should be as gentle as possible. Use a pipe bender for bending.2-2.Selection of copper and heat insulation materials.•When using commercial copper pipes and fittings, observe the following:1)Insulation material: Polyethylene foamHeat transfer rate: 0.041 to 0.052W/mK (0.035 to 0.045kcal/(mh•°C))Refrigerant gas pipe’s surface temperature reaches 110°C max.Choose heat insulation materials that will withstand this temperature.2)Be sure to insulate both the gas and liquid piping and to provide insulation dimen-sions as below.3)Use separate thermal insulation pipes for gas and liquid refrigerant pipes.Pump Down OperationIn order to protect the environment, be sure to pump down when relocating or disposing of the unit.1)Remove the valve cap from liquid stop valve and gas stop valve.2)Carry out forced cooling operation.3)After 5 to 10 minutes, close the liquid stop valve with a hexagonal wrench.4)After 2 to 3 minutes, close the gas stop valve and stop forced cooling operation.How to force cooling operation mode■Using the indoor unit operation/stop buttonPress the indoor unit operation/stop button for at least 5 seconds. (Operation will start.)•Forced cooling operation will stop automatically after around 15 minutes. To force a test run to stop, press the indoor unit operation/stop button.■Using the main unit’s remote controller 1)Press the “operation/stop” button. (Operation will start.)2)Press the temperature button and the “operation select” button at the same time.3)Press the “operation select” button twice.( will be displayed and the unit will enter test run mode.)4)Press the “operation select” button to return the operation mode to cooling.•Test run mode will stop automatically after around 30 minutes. To force a test run to stop, press the operation/stop button.CAUTION1)After closing the liquid stop valve, close the gas stop valve within 3 minutes, then stop the forced operation.Gas side Liquid side Gas pipe thermal insulation Liquid pipethermal insulation 20/25/35/42 class50 class 20/25/35/42class 50 classO.D. 9.5mm O.D. 12.7mm O.D. 6.4mm I.D. 12-15mm I.D. 14-16mm I.D. 8-10mmMinimum bend radius Thickness 10mm Min.30mm or more 40mm or more 30mm or moreThickness 0.8mm (C1220T-O)Trial Operation and Testing1.Trial operation and testing.1-1Measure the supply voltage and make sure that it falls in the specified range.1-2Trial operation should be carried out in either cooling or heating mode.■For Heat pump•In cooling mode, select the lowest programmable temperature; in heating mode, select the highest programmable temperature.1)Trial operation may be disabled in either mode depending on the room e the remote controller for trial operation as described below.2)After trial operation is complete, set the temperature to a normal level (26°C to 28°C in cooling mode, 20°C to 24°C in heating mode).3)For protection, the system disables restart operation for 3 minutes after it is turned off.■For Cooling only•Select the lowest programmable temperature.1)Trial operation in cooling mode may be disabled depending on the room e the remote controller for trial operation as described below.2)After trial operation is complete, set the temperature to a normal level (26°C to 28°C).3)For protection, the unit disables restart operation for 3 minutes after it is turned off.1-3Carry out the test operation in accordance with the Operation Manual to ensure that all functions and parts,such as louver movement, are working properly.•The air conditioner requires a small amount of power in its standby mode. If the system is not to be used for some time after installation, shut off the circuit breaker to eliminate unnecessary power consumption.•If the circuit breaker trips to shut off the power to the air conditioner, the system will restore the original operation mode when the circuit breaker is opened again.2.Test items.Test itemsSymptom(diagnostic display on RC)CheckIndoor and outdoor units are installed properly on solid bases.Fall, vibration, noiseNo refrigerant gas leaks.Incomplete cooling/heating function Refrigerant gas and liquid pipes and indoor drain hose extension are thermally insulated.Water leakage Draining line is properly installed.Water leakage System is properly earthed.Electrical leakage The specified wires are used for interconnecting wire connections.Inoperative or burn damage Indoor or outdoor unit’s air intake or exhaust has clear path of air.Stop valves are opened.Incomplete cooling/heating function Indoor unit properly receives remote controller commands.InoperativeThe heat pump or cooling only mode is selectable with the dipswitches of the remote controller.Remote controller malfunctioning。
R410A分体式空调安装手册说明书
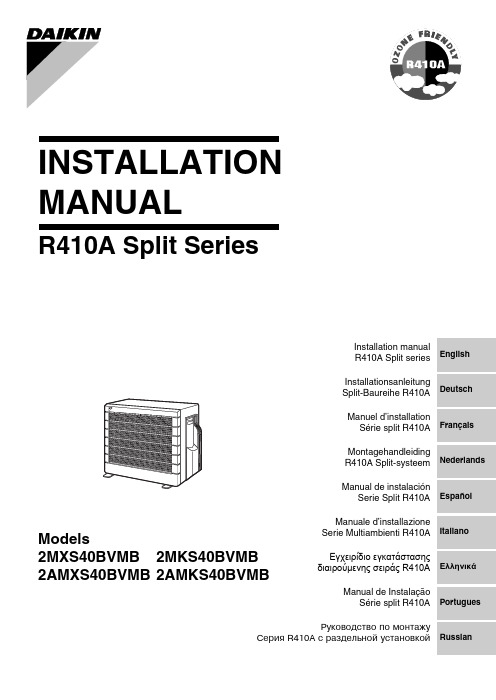
INSTALLATION MANUALR410A Split SeriesModels2MXS40BVMB 2MKS40BVMB 2AMXS40BVMB 2AMKS40BVMBEnglishDeutschFrançaisNederlandsEspañolItalianoΕλληνικÜPortuguesRussianInstallation manual R410A Split series Installationsanleitung Split-Baureihe R410A Manuel d’installation Série split R410A Montagehandleiding R410A Split-systeem Manual de instalaciónSerie Split R410A Manuale d’installazione Serie Multiambienti R410A Εγχειρßδιο εγκατÜστασηòδιαιροýìενηò σειρÜò R410AManual de Instalação Série split R410AРóêоводство по монтажóСерия R410A с раздельной óстановêойSafety Precautions•Read these Safety Precautions carefully to ensure correct installation.•This manual classifies the precautions into WARNINGS and CAUTIONS.Be sure to follow all the precautions below: they are all important for ensuring safety.WARNINGS............Failure to follow any of WARNING is likely to result in such grave consequences as death or serious injury.CAUTIONS............Failure to follow any of CAUTION may in some cases result in grave consequences.•The following safety symbols are used throughout this manual:•After completing installation, test the unit to check for installation errors. Give the user adequate instructions concerning the use and cleaning of the unit according to the Operation Manual.AccessoriesAccessories supplied with the outdoor unit:Outside DrawingsPrecautions for Selecting the Location1)Choose a place solid enough to bear the weight and vibration of the unit, where the operation noise will not be amplified.2)Choose a location where the hot air discharged from the unit or the operation noise, will not cause a nuisance to theneighbors of the user.3)Avoid places near a bedroom and the like, so that the operation noise will cause no trouble.4)There must be sufficient spaces for carrying the unit into and out of the site.5)There must be sufficient space for air passage and no obstructions around the air inlet and the air outlet.6)The site must be free from the possibility of flammable gas leakage in a nearby place. Locate the unit so that the noiseand the discharged hot air will not annoy the neighbors.7)Install units, power cords and inter-unit cables at least 3 meter away from television and radio sets. This is to preventinterference to images and sounds. (Noises may be heard even if they are more than 3 meter away depending on radiowave conditions.)8)In coastal areas or other places with salty atmosphere of sulfate gas, corrosion may shorten the life of the air condi-tioner.9)Since drain flows out of the outdoor unit, do not place under the unit anything which must be kept away from moisture.Note:Phased installation is not possible.CautionWhen operating the air conditioner in a low outdoor ambient temper-ature, be sure to follow the instructions described below.tion side facing the wall.2)Never install the outdoor unit at a site where the suction side maybe exposed directly to wind.3)T o prevent exposure to wind, it is recommended to install a baffleplate on the air discharge side of the outdoor unit.4)In heavy snowfall areas, select an installation site where the snowwill not affect the unit.Indoor/outdoor Unit Installation DrawingsFor installation of the indoor units, refer to the installation manual which was provided with the units.(The diagram shows a wall-mounted indoor unit.)Caution1)Do not connect the embedded connect piping and the outdoor unit when only carrying out piping work without connecting the indoor unit in order to add another indoor unit later.Make sure no dirt or moisture gets into either side of the embedded connect piping.See “6. Refrigerant Piping Work” on page 8 for details.2)[2MXS40, 2AMXS40 only] Do not connect to one indoor unit. Always connect to two indoor units. [2MKS40, 2AMKS40 only] Can be connected to one indoor unit.•Install the unit horizontally.•The unit may be installed directly on a concrete verandah or a solid place if drainage is good.•If the vibration may possibly be transmitted to the building, use a vibration-proof rubber (field supply).Clamping materialInsulation tubeService lidTapeUse tape or insulating material on all connections to prevent air from getting in between the copper piping and the insulation tube.Be sure to do this if the outdoor unit is installedOutdoor Unit Installation Guideline•Where a wall or other obstacle is in the path of outdoor unit intake or exhaust airflow, follow the installation guidelines below.•For any of the below installation patterns, the wall height on the exhaust side should be 1200 mm or less.Selecting a location for installation of the indoor units•The maximum allowable length of refrigerant piping, and the maximum allowable height difference between the outdoor and indoor units, are listed below.Outdoor unit2MXS40, 2MKS402AMXS40, 2AMKS40Piping to each indoor unit1.5m min. 20m max.Total length of piping between all units30m max.If the outdoor unit is positioned higher than the indoor units.If the outdoor unit is positioned otherwise.(If lower than one or more indoor units)1.Installing Outdoor Unit1)When installing the outdoor unit, refer to “Precautions for Selecting the Location” and the “Indoor/outdoor Unit Installation Drawings.”2)If drain work is necessary, follow the procedures below.2.Drain Work1)Use drain plug for drainage.2)If the drain port is covered by a mounting base or floor surface, place additional foot bases of at least 30 mm in height under the outdoor unitís feet.3)In cold areas, do not use a drain hose with the outdoor unit.(Otherwise, drain water may freeze, impairing heating performance.)3.Refrigerant Piping1)Align the centres of both flares and tighten the flare nuts 3 or 4 turns by hand. Then tighten them fully with the torque wrenches.•Use torque wrenches when tightening the flare nuts to prevent damage to the flare nuts and escaping gas.2)T o prevent gas leakage, apply refrigeration machine oil on both inner and outer surfaces of the flare. (Use refrigeration oil for R410A)4.Purging Air and Checking Gas LeakageWarning1)Do not mix any substance other than the specified refrigerant (R410A) into the refrigeration cycle.2)Refrigerant gas leaks during air purging, ventilate the room as soon as possible.3)T o prevent air pollution, a vacuum pump should be used for air purging wherever possible.4)Be sure to check for gas leaks.•Be sure to perform an air purge for all the rooms at the same time.•Be sure to use the special tools for the R410A. (gauge manifold, charge hose, vacuum pump, vacuum pump adapter, etc.)•Use a hexagonal wrench (4 mm) to operate the shut-off valve rod.•All refrigerant pipe joints should be tightened with a torque wrench at the specified tightening torque.1)Connect the charge hose protrusions (the side for pushing the pin) for low pressure and high pressure on the gauge manifoldto the gas shut-off valve service port for rooms A and B. (Air purge carried out simultaneously at the pipes for rooms A and B.)2)Fully open gauge manifold’s low-pressure valve (Lo) and high-pressure valve (Hi).3)Apply vacuum pumping for 20 minutes or longer. Check that the compound pressure gauge reads –0.1 MPa (–76cm Hg).4)After checking the vacuum, close the low pressure and high pressure valves on the gauge manifold and stop the vacuumpump. (Leave as is for 4-5 minutes and make sure the coupling meter needle does not go back. ) If it does go back, this may indicate the presence of moisture or leaking from connecting parts.After inspecting all the connection and loosening then retightening the nuts, repeat steps 2 – 4.5)Remove the valve caps on the liquid and gas shut-off valves at the pipes for rooms A and B.7)Remove the charge hose from the gas shut-off valve service ports at the pipes for rooms A and B and completely open the liq-uid and gas shut-off valves at the pipes for rooms A and B.(Stop the valve rods as far as they go and do not attempt to turn them any further.)8)Use a torque wrench to tighten the valve caps and service port caps on the liquid and gas shut-off valves at the pipes forrooms A and B to the designated torque.5.Charging with Refrigerant•If the total length of piping for all rooms exceeds 20m, additionally charge with (R410A) 20 g of refrigerant for each addi-tional meter of piping.When extra refrigerant is added, write down the total length of the piping and the amount added on the nameplate for recording how much refrigerant has been added on the back of the service lid on the outdoor unit.Caution1)Even though the shut-off valve is fully closed, the refrigerant may slowly leak out; do not leave the flare nut removed for a long period of time.When using commercial copper pipes and fittings, observe the following:1)Insulation material: Polyethylene foamHeat transfer rate: 0.041 to 0.052kW/mK (0.035 to 0.045 kcal/mh°C)Refrigerant gas pipe’s surface temperature reaches 110°C max.Choose heat insulation materials that will withstand this temperature.2)Be sure to insulate both the gas and liquid piping and to provide insulation dimen-sions as below.3)Use separate thermal insulation pipes for gas and liquid refrigerant pipes.2)Prevent mineral oil from getting into the system as this would reduce the lifetime of the units.3)Never use piping which has been used for previous installations. 4)Only use parts which are delivered with the unit.5)Do never install a drier to this R410A unit in order to guarantee its lifetime. The drying material may dissolve and damage the system.6)Incomplete flaring may cause refrigerant gas leakage.Gas pipeGas pipe insulationO.D.: 9.5mm / Thickness:0.8mm I.D.: 12 – 15mm / Thickness:13mm min.Liquid pipeLiquid pipe insulationO.D.: 6.4mm / Thickness:0.8mmI.D.: 8 – 10mm / Thickness:10mm min.WiringC5~C8, SHC1:CAP ACITORR1T :OUTDOOR THERMISTER Y1R : REVERSING SOLENOIDE VAL VE COIL CT1:CURRENT TRANSFORMER R2T :CONDENSER THERMISTER Z1C : FERRITE COREDB1, DB3:DIODE BRIDGER3T :DISCHARGE PIPE THERMISTERFU1~FU3:FUSELIQUID PIPE S10~S12, S20, S21, S30,L :LIVE R5T :THERMISTER ROOM-A S40, S45, S70, S80, S90~S92, L1:COIL R6T:THERMISTER ROOM-BHL1, HL2, HN1, HN2, HR3, HR4,L1R :REACTOR GAS PIPE AC1, AC2, HC3, HC4, E, X30A :CONNECTOR M1C :COMPRESSOR MOTOR R7T :THERMISTER ROOM-A BLK : BLACK M1F :FAN MOTOR R8T :THERMISTER ROOM-B BLU : BLUE MRCW, MRM10, SA1:SURGE ARRESTER BRN : BROWN MRM20:MAGNETIC RELAY TFU :THERMAL FUSEGRY : GREY N :NEUTRAL TRM1:TRANSISTOR MODULE ORG : ORANGE OIS3:TRIAC V1, V2, V3:VARISTORRED : RED PCB1, PCB2:PRINTED CIRCUIT BOARD X1M, X2M :TERMINAL STRIPWHT : WHITE Q1L:OVERLOAD PROTECTORY1E :ELECTRONIC EXP ANSION VALVE COIL ROOM- AYLW : YELLOWY2E:ELECTRONIC EXP ANSION VALVE COIL ROOM-BWarningDo not use tapped wires, stand wires, extensioncords, or starbust connections, as they may cause overheating, electrical shock, or fire.•Do not turn ON the safety breaker until all work is completed.1)Strip the insulation from the wire (20 mm).2)Connect the connection wires between theindoor and outdoor units so that the terminal numbers match . Tighten the terminal screws securely.We recommend a flathead screwdriver be used to tighten the screws.The screws are packed with the terminal board.3)Pull the wire and make sure that it does not disconnect. Then fix the wire in place with a wire stop.Test Run and Final Check•Before starting the test run, measure the voltage at the primary side of the safety breaker. Check that it is 230 V .•Check that all liquid and gas shut-off valves are fully open.•Check that piping and wiring all match.1.Test Run and Final Check1)T o test cooling, set for the lowest temperature. To test heating, set for the highest temperature. (Depending on the room temperature, only heating or cooling (but not both) may be possible.)2)After the unit is stopped, it will not start again (heating or cooling) for approximately 3 minutes.3)During the test run, first check the operation of each unit individually. Then also check the simultaneous operation of all indoor units.Check both heating and cooling operation.4)After running the unit for approximately 20 minutes, measure the temperatures at the indoor unit inlet and outlet. If the measurements are above the values shown in the table below, then they are normal.(When running in one room)5)During cooling operation, frost may form on the gas shut-off valve or other parts. This is normal.6)Operate the indoor units in accordance with the included operation manual. Check that they operate normally.2.Items to checkI ATTENTION1)Have the customer actually operate the unit while looking at the manual included with the indoor unit. Instruct the customer how to operate the unit correctly (particularly cleaning of the air filters, operation procedures, and temperature adjustment).2)Even when the air conditioner is not operating, it consumes some electric power. If the customer is not going to use the unit soon after it is installed, turn OFF the breaker to avoid wasting electricity.3)If additional refrigerant has been charged because of long piping, list the amount added on the nameplate on the reverse side of the shut-off valve cover.CoolingHeating Temperature difference between inlet and outletApprox. 8 °CApprox. 15 °CCheck itemConsequences of troubleCheckAre the indoor units installed securely?Falling, vibration, noise Has an inspection been made to check for gas leakage?No cooling, no heating Has complete thermal insulation been done (gas pipes, liquid pipes, indoor portions of the drain hose extension)?Water leakage Is the drainage secure?Water leakageAre the ground wire connections secure?Danger in the event of a ground fault Are the electric wires connected correctly?No cooling, no heating Is the wiring in accordance with the specifications?Operation failure, burning Are the inlets/outlets of the indoor and outdoor units free of any obstructions? Are the shut-off valves open?No cooling, no heating Do the marks match (room A, room B) on the wiring and piping for each indoor unit?No cooling, no heatingMaximum Power Input Limitation SettingWarningAlways shut off the power supply breaker before starting.•The Maximum Power Input Limitation needs to be set when the unit is installed.•This function limits the power input of the unit to 1700W.•It is recommended for locations with low-capacity circuit breakers.CautionThis function is only for the 2MKS40 and 2AMKS40.•Set as follows.1)Remove the three screws on the side and remove the top of the outdoor unit.2)Remove the fan motor lead wire from the hook and loosen it.3)Disengage the four tabs marked with a triangle and remove the electrical cabinet.4)Cut the jumper (J9) of the Printed circuit board inside.5)Go back through step 3) → 2) → 1). Make sure all components are well secured when doing this.Service1.Concerning Handling of High Voltage Parts Do not touch the charged parts for 10 minutes after the safety breaker is turned off, because of the danger of high voltage .2.To Prevent Electrical Shock Use a tester to check that the voltage between DB1 “ + ” and “ – ” is 50V or less.(Refer to the Figure at below for the locations to check.)3.Reconnecting After CheckWhen reconnecting, be sure to reconnect everything the same way it was before.4.Layout Diagram of Electrical ComponentsFault Diagnosis by LED on Outdoor Unit PCB.Notes:1)Switch the power off and back on again if the LED display recurs, the outdoor unit PCB is fault.2)Switch the power off and back on again if the LED display recurs, either the outdoor unit PCB is at fault or the thermal fuse inthe terminal strip (X2M) is severed.Error detection should be performed using the malfunction diagnosis function on the remote controller.MULTIMETER(DC. VOLTAGE RANGE)S70FAN MOTER LEAD WIRES91THERMISTOR LEAD WIRE (LIQUID & GAS PIPE)LED A(SLIT INSIDE)S90THERMISTOR LEAD WIRE S80 (2AMXS, 2MXS only)REVERSING SOLENOID VALVE COIL LEAD WIRES20ELECTRONIC EXP ANSION VALVE COIL LEAD WIRE (ROOM A)S21ELECTRONIC EXP ANSION VALVE COIL LEAD WIRE (ROOM B)REACTOR LEAD WIRETHERMISTOR LEAD WIRECOMPRESSOR & OL LEAD WIREDB1LED A(SLIT INSIDE)Pump Down OperationIn order to protect the environment, be sure to pump down when relocating or disposing of the unit.1)Remove the valve caps on the liquid and shut-off valves at the pipes for rooms A and B.2)Run the unit on forced cooling. (Refer to the below.)3)After 5 to 10 minutes, close the liquid shut-off valves at the pipes for rooms A and B using a hex wrench.4)After 2 to 3 minutes, stop the forced cooling operation as quickly as possible after the gas shut-off valves at the pipes forrooms A and B have been shut off.5)T urn the power breaker off.CautionRun cooling operation at the pipes for rooms A and B when performing a pump down.1.Forced Cooling Operationing the indoor unit start/stop button1)Press the start/stop button on the indoor unit in either room A or B for 5 seconds continuously.The units in both rooms will start.2)Forced cooling operation will end after around 15 minutes and the unit will stop automatically. Press the start/stopbutton on the indoor unit to force the operation to stop.3)Use this method to force cooling operation when the outside temperature is 10°C or lower.ing the wireless remote controller1)Select cooling operation and press the start/stop button. (The unit will start.)2)Press the temperature button, button, and the ”mode” button at the same time.3)Press the “mode” button twice.4)T est-run mode will end after around 30 minutes and the unit will stop automatically. Press the start/stop button toforce the test-run to stop.1-3.For set-ups where the indoor unit is a low static pressure duct FDBQ series.1)Perform cooling operation in test-run mode.CautionIf the outside temperature is 10°C or lower, the safety device might start, preventing operation. In this situation, warmthe outside temperature thermistor on the outdoor unit to 10°C or warmer. Operation will start.。
Daikin R-410A Ducted Horizontal Heat Pump产品说明书
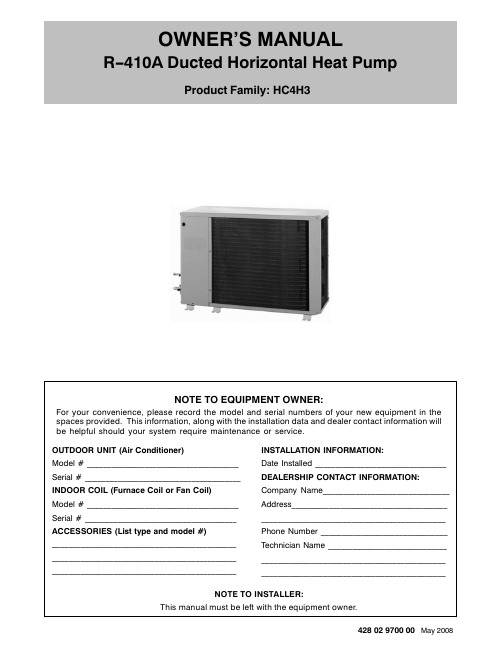
OWNER'S MANUALR-410A Ducted Horizontal Heat PumpProduct Family: HC4H3NOTE TO EQUIPMENT OWNER:For your convenience, pleas e record the model and s erial numbers of your new equipment in the spaces provided. This information, along with the installation data and dealer contact information will be helpful s hould your s ys tem require maintenance or s ervice.OUTDOOR UNIT (Air Conditioner)Model # _____________________________________ Serial # ______________________________________ INDOOR COIL (Furnace Coil or Fan Coil)Model # _____________________________________ Serial # _____________________________________ ACCESSORIES (List type and model #)_____________________________________________ _____________________________________________ _____________________________________________INSTALLATION INFORMATION:Date Installed ________________________________ DEALERSHIP CONTACT INFORMATION: Company Name_______________________________ Address______________________________________ _____________________________________________ Phone Number _______________________________ Technician Name _____________________________ _____________________________________________ _____________________________________________NOTE TO INSTALLER:This manual must be left with the equipment owner.WELCOME TO EFFICIENTYEAR-ROUND COMFORT CONGRATULATIONS! You have made an excellent choice and sound investment in home cooling comfort!Your new Heat Pump is a product of that experience, and will provide you and your family with years of dependable, energy efficient cooling comfort.This booklet provides information on how your system works as well as helpful hints on operation and maintenance so you can enjoy peak performance for years to come. For even greater peace of mind, your expert dealer can provide professional maintenance and service on an annual or as-needed basis to ensure that your system receives the very best care from the industry experts. Ask your dealer about scheduling annual maintenance visits or about the benefits of a service contract. In addition, your installing dealer can offer expert recommendations on all of the products, accessories and services available to enhance your comfort through personalized control of your system and improved indoor air quality.A NOTE ABOUT SAFETYAny time you see this symbol in manuals, instructions and on the unit, be aware of the potential for personal injury. There are three levels of precaution:DANGER identifies the most serious hazards which will result in severe personal injury or death.W ARNING signifies hazards that could result in personal injury or death.CAUTION is used to identify unsafe practices which would result in minor personal injury or product and property damage.ABOUT YOUR HEAT PUMP SYSTEMIdentifying Your SystemYour new Heat Pump system is what we call a ”split system.” It has an outdoor unit and an indoor unit connected to each other with copper tubing called refrigerant lines. Each of these units has a rating plate with the model and serial numbers you will need to reference when calling an authorized dealer about your system.Take a few moments now to locate those numbers and record them in the spaces provide on the cover of this booklet. USING YOUR NEW SYSTEMYour Heat Pump system is controlled by a thermostat inside your home. Because there are so many thermostats available, please refer to the owner's manual supplied with your thermostat or indoor unit for complete details on system operation. Or, read the next section for basic operating instructions.SYSTEM OPERATION WITH BASIC THERMOSTATMost basic thermostats have three main controls:S S ystem or Mode Control: Typically offers the following selections: Cool, Off, and Heat. Some thermostats also have Auto, which lets the system switch between heating and cooling as needed.S Temperature Control: A button, lever, or set of buttons that allows you to select the temperature inside your home.S Fan Control: Typically offers two options: Auto and O n.”Auto” provides slightly higher energy efficiency by circulating air only during cooling (or heating) operation.”On” provides better air circulation, better dehumidification and better air cleaning by running the system's blower continuously.HEATING YOUR HOMEFor heating operation, make sure the System or Mode control is set for Heating. Then, adjust the Temperature control to your desired setting. Finally, use the Fan control to select Automatic (turns on and off as heating is needed) or On (runs continuously). Depending on your typical heating needs, your home comfort system may also include a supplementary heating source that will automatically turn on as needed. You may also select this heat source manually if desired.COOLING YOUR HOMEFor cooling operation, make sure the System or Mode control is set for Cooling. Then, adjust the Temperature control to your desired setting. Finally, use the Fan control to select Automatic (turns on and off as cooling is needed) or On (runs continuously).DELUXE THERMOSTATSThere are a number of deluxe thermostats, including programmable models, which can provide a number of benefits depending on the model:S Customized daily and/or weekly comfort schedules that you create to match your lifestyleS Enhanced energy efficiency and comfortS Enhanced comfort through humidity controlS Enhanced maintenance remindersS Remote system operationAsk your dealer for information on a deluxe thermostat option that matches your Heat Pump system.OPERATION UNDER EXTREME CONDITIONSYour Heat Pump will run as long as necessary to maintain the indoor temperature selected on your thermostat. On colder days, in the heat pump mode, the system will run for longer periods at a time than on moderate days. the same is true in the cooling mode. O n extremely hot days, the system will run for longer periods at a time than on moderate days. Your system will also run for longer periods of time under the following cooling conditions:S Frequent opening of exterior doorsS Operating laundry appliancesS Taking hot showersS More than the usual number of people present in the homeS More than the normal number of electric lights in useS Drapes or blinds are open on the sunny side of the home IMPORTANT FACTS ABOUT HEAT PUMP SYSTEMSHeat pump systems have a few unique features and operations that you should be aware of:S During the heating cycle, air from your registers may seem cooler than you may expect. This is because your heat pump delivers a constant flow of air at around 90_F (32_C) to about 105_F (41_C), compared to sudden blasts of hot air provided by a typical furnace. This air may feel cool if it is slightly below your body temperature, however it is warm enough to keep your home comfortable.S Ice or frost may form on the outdoor coil during winter heating operation. Your heat pump will automatically melt the ice using its defrost cycle. During defrost, you may see steam or fog rising from the outdoor unit, which is normal.S Heat pumps installed in areas expecting snow are elevated with support feet.GET THE MOST FROM YOUR HEAT PUMP SYSTEMThese simple suggestions can help you enjoy years of maximum comfort:S Listen To Your SystemGet to know the start-up and operational sounds your indoor and outdoor units make. Learn to recognize and identify unusual sounds that may signal the need for service.S Keep Filter CleanA clogged or improperly installed air filter on your indoor unit will increase operating costs and shorten the life of the unit. Plan to inspect the filter monthly and clean or replace it as needed.S Do Not Block Floor, Wall or Ceiling VentsWhen drapes, furniture, toys or other common household items block vents, the restricted airflow lessens the system's efficiency and life span.S Do Not Cover or Block Outdoor UnitThe outdoor unit needs unrestricted airflow. Do not cover it or place items on or next to it. Do not allow grass clippings, leaves, or other debris to accumulate on the sides or top of the unit. And, maintain a 12” (304.8 mm) minimum clearance between the outdoor unit and tall grass, vines, shrubs, etc.S Check Condensate DrainYour Heat Pump removes humidity from your home during the cooling season. After a few minutes of operation, water should trickle from the condensate drain of the indoor coil. Check this occasionally to be sure the drain system is not clogged. Drainage will be limited if you live in a very dry environment.S Do Not Operate Below 55_F (13_C) On Cooling Mode Your outdoor unit is not designed to operate when outdoor temperatures are lower than 55_F (13_C) without modification. If operation below this temperature is required, consult your dealer.S Do Not Operate Above 66_F (19_C) on Heating Mode Your outdoor unit is not designed to operate on heating mode when outdoor temperatures are higher than 66_ (19_C). You can safely operate the system above 66_ (19_C) on emergency or auxiliary heat.S Increase Heating Temperature 1-2 Degrees at a Time During heating operation, increasing the thermostat setting more than 2 degrees at a time may cause the supplemental heat source to turn on. Needless use of supplemental heat can reduce potential energy savings.ROUTINE MAINTENANCESimple, routine maintenance as described below will enhance your Heat Pump system's ability to operate economically anddependably. Always remember the following safety precautions: NOTE: There may be more than one electrical disconnect switch.Fig. 1 - Main Electrical Disconnect INDOOR UNIT (Furnace or Fan Coil)(Also refer to the furnace or fan coil Owner's Manual)S Check the Air Filter MonthlyThere are no filters on your outdoor unit. However, a dirty air filter on the indoor unit can cause overheating, automatic system shutdown, and in extreme cases, component failure.CHECK THE FILTER(S) MO NTHLY AND CLEAN O R REPLACE AS NEEDED. For details on how to check, clean or replace your filter(s), refer to your furnace or fan coil owner's manual. O R, if you have an electronic air cleaner or a larger,”boxed” air filter, refer to the owners manual supplied with those products.S Coil CleaningYour indoor coil is located in a sealed cabinet on your indoor unit and will require minimal cleaning with routine filter maintenance. Longer operating cycles and reduced energy efficiency may indicate the need for a coil cleaning by your dealer. OUTDOOR UNITS Coil CleaningThe most visible part of the outdoor unit is the large ”coil”wrapped around the inner components of the Heat Pump. If grass clippings, leaves, shrubbery, and debris are kept away from the coil, minimal care is needed. If the coil becomes dirty, clean the coil surface with a vacuum cleaner using a soft brush attachment. Use an up and down motion being careful not to bend or damage the delicate, aluminum coil fins. If dirt is deep in the coil, contact your dealer for service.S Base Pan DrainagePeriodically check for and remove debris that has settled around the base of your outdoor unit. This will ensure proper drainage of the base pan and eliminate standing water inside the outdoor unit.S Level InstallationYour dealer will install the outdoor unit in a level position. If the support base settles or shifts and the unit is no longer level, be sure to re-level it promptly to assure proper drainage. If you notice water or ice collecting beneath the unit, arrange for it to be drained away from the unit.SEA COAST COIL MAINTENANCECoastal locations often require additional maintenance of the outdoor unit due to highly corrosive airborne ocean salt. Although your new system is made of galvanized metal and is protected by top-grade paint, take the additional precaution of periodically washing all exposed surfaces and the outdoor coil approximately every 3 months. Consult your installing dealer for proper cleaning intervals and procedures for your geographic area or ask about a service contract for regularly scheduled professional cleaning and inspections.TROUBLESHOOTINGBefore you request dealer service, check for these easily solved problems:S Check the indoor and outdoor disconnect switches (see Fig.1.) Also check your main electrical panel circuit breakers orfuses.S Check for sufficient airflow. Air filter(s) should be reasonably clean and interior vents should be open and unobstructed.S Check thermostat settings. For cooling, your desired temperature setting should be LO WER than the displayed room temperature, and the System/Mode control should be on Cool or Auto. For heating, your temperature setting should be HIGHER than the displayed room temperature, and the System/Mode control is set to Heat or Auto.S Time delays - depending on the Heat Pump model you have, there may be delays in unit operation that are built-in to protect the equipment and your comfort. Don't be alarmed if you notice a time delay in operation. It may be a standard protection feature of your equipment. Check with your dealer for more informationon time delays.If you need to contact your dealer for troubleshooting and/or repairs, be sure to have the model and serial numbers of your equipment available (there are spaces on the cover for you to write this information). With this information, your dealer may be able to offer helpful suggestions over the phone or save valuable time through knowledgeable preparation for the service call. REGULAR DEALER MAINTENANCEIn addition to the routine maintenance that you perform, your home comfort system should be inspected regularly by a properly trained service technician. Many dealers offer this service at a reduced rate with a service contract. Some service contracts offer additional benefits such as parts discounts and no additional charge for ”after hours” or emergency service.Your annual system inspection should include:S Routine inspection of air filter(s) with replacement or cleaning as requiredS Inspection and cleaning of the blower wheel housing and motorS Inspection and, if required, cleaning of indoor and outdoor coilsS Inspection of the indoor coil drain pan, as well as the primary and secondary drain lines. If the system has an auxiliary drain pan and line, they should be inspected at this time as well. Service should include cleaning if required.S Check all electrical wiring and connectionsS Check for secure physical connections of individual parts in each unitS O perational check of the Heat Pump system to determine actual working condition. Necessary repair and, or adjustment should be performed at this time.TURN TO THE EXPERTSYour Heat Pump system, backed by the world's best name in comfort, and supported with expert installation, maintenance, and service by your local dealer should provide years of reliable, energy efficient comfort.。
R410A注意事项

铜管外径 6.35 9.52 12.7
通常 >100 >100 >100
最小 >30 >30 >30
包装与运输
谢谢!
0~0.5
使用原R22用工具时 R410A R22 1.0~1.5 0.5~1.0 1.0~1.5 0.5~1.0 1.0~1.5 0.5~1.0
3. 喇叭口螺母尺寸: B (mm)
铜管外径 6.35 9.52 12.7
R410A用 17 22 26
R22用 17 22 24
4. 室内机/室外机连接配管弯曲半径: R (mm)
R410A 注意事项
R410A冷媒特性
对比项目
成分
温度滑移 沸 点 (℃) 工作压力
冷凝压力(MPa) 蒸发压力(MPa)
排气温度(℃) 压缩比(Pd/Ps)
单位能力容积 功率
COP(%)
R22 HCFC-22 (100%) 单一冷媒 (00C)
-40.8 100% 2.15
0.625
101.9 3.43 100%
干燥过滤器不要串联在循环系统上,最好旁通在冷凝器出口
3. 系统匹配性能改善注意点
系统各温度分布与R22同等. (压力分布为R410A物性对 应压力, 见下页).
压缩机使用压力条件限制变更(见附图), 温度限制条件 与R22相同.
细管化: R410A压损小活用, 性能UP, 耐压强度UP. 螺纹管: 齿型优化, 换热性能UP. 毛细管: 与R22相比, 加长 (R410A压损小) . 压力表: R410A专用.
其它
冷媒封入装置请设为R410A专用. (特别注意避免误封入): 液态制冷剂高压侧封入; R410A钢瓶其他 颜色处理区分,封入接口尺寸变更.
R-410A空调与热泵分离系统长线集合应用指南说明书

1INDEXSECTION 1.General Requirements for All Long Line Set Applications..............................2SECTION 2.Outdoor Unit and Indoor Unit are at the Same Elevation...............................4SECTION 3.Outdoor Unit is Above the Indoor Unit............................................................5SECTION 4.Outdoor Unit is Below the Indoor Unit............................................................6SECTION 5.Calculations - Tubing Equivalent Length, Tube Size and Refrigerant (7)This long line set application guideline applies to all AHRI listed R-410A air conditioner and heat pump split system matches of nominal capacity 18,000 to 60,000 Btuh. This guideline will cover installation requirements and additional accessories needed for split system installations where the line set exceeds 80 feet (24.4 m) in actual length. The long line sets can have three different configurations (1) Outdoor unit and Indoor unit are at the same level, (2) Outdoor unit is above the Indoor unit coil, (3) Outdoor unit is below the Indoor unit.This guideline is meant to provide installation instructions based on most common long line set applications.Installation variables may affect the system operation.Contact Technical Servicesfor variations or applications outside those outlined in this document.TP-107KTECHNICAL PUBLICATIONTP-107KGoodman Company, L.P .April 2017LONG LINE SETAPPLICATION R-410ASECTION 1. GENERAL REQUIREMENTS FOR ALL LONG LINE SET APPLICATIONS1.Equivalent length must be used to determine acceptability of any long line set application. See Section 5for equivalent length calculations.2.For any residential split system installed with a long line set, 3/8” liquid line size must be used.Limiting the liquid line size to 3/8” is critical since an increased refrigerant charge level from having a larger liquid line could possibly shorten a compressor’s life-span.a.Exceptions for air conditioning (cooling only) applications, 1/4" liquid line may be used in:i. 1.5 ton applications for up to 100 equivalent feet (30.5 equivalent meters) with maximum 40’(12.2 m) vertical liftii. 2.0 ton applications for up to 75 equivalent feet (22.9 equivalent meters) with maximum 20’(6.1 m) vertical liftb.Exceptions for air conditioning (cooling only) applications, 5/16" liquid line may be used in:i. 1.5 ton applications for up to 250 equivalent feet (76.2 equivalent meters) with maximum 60’(18.3 m) vertical liftii. 2.0 ton applications for up to 200 equivalent feet (61.0 equivalent meters) with maximum 40’(12.2 m) vertical liftiii. 2.5 ton applications for up to 175 equivalent feet (53.3 equivalent meters) with maximum 30’(9.1 m) vertical lift3.Most refrigerant tubing kits are supplied with 3/8” (9.5 mm) thick insulation on the suction line. For longline installations over 80 feet (24.4 m) , if the line set passes through a high ambient temperature zone, 1/2” (12.7 mm) thick suction line insulation is required to reduce loss of capacity. The liquid line must be insulated if more than 50 feet (15.2 m) of liquid line will pass through an area that might reach temperatures of 30°F or higher than outdoor ambient. Never attach a liquid line to any uninsulated portion of the suction line.4. A crankcase heater must be installed on any compressor (if crankcase heater is not already factoryinstalled).5.Hard start assist kit is required.e of a thermostatic expansion valve (TXV) is required in all long line set applications. Unit must becharged to 7 to 9 ºF subcooling at the indoor unit.7.Maximum equivalent length of line set is:a. 250 feet (76.2 m) for single stage units with scroll or reciprocating compressors.b. 150 feet (45.7 m) for single stage units with rotary compressors.c. 150 feet (45.7 m) for two stage units.8.Maximum linear length of line set is:a. 200 feet (61.0 m) for single stage units with scroll or reciprocating compressors.b. 150 feet (45.7 m) for single stage units with rotary compressors.c. 150 feet (45.7 m) for two stage units.9.Low voltage wiring. Verify low voltage wire gauge is adequate for the length used due to increased lineset application.10.Vibration and Noise: In long line applications, refrigerant tubing is highly prone to transmit noise andvibration to the adjoining structure. Use adequate vibration-isolating hardware when mounting line set to structural members. See Figures 1-1, 1-2 and 1-3 for example of proper mounting.2Wrapped in Armaflex®Figure 1-1.Installation of Refrigeration Piping From Vertical to HorizontalIMPORT ANT - Refrigerant lines must not touch wall.Figure 1-2. Installation of Refrigerant Piping (Vertical)New construction shownNOTE: If line set is installed on the exterior of an outside wall, similar installation practices are to be used.Figure 1-3. Installation of Refrigerant Piping (Horizontal)3Figure 1-3. Installation of Refrigerant Piping (Horizontal)11.Heat Pump Application Only. Liquid line solenoid must be installed less than 2 feet (61cm) from theoutdoor unit following the solenoid supplier information for installation.12.Heat Pump Application Only. Heating piston change (in the outdoor unit) is not required.13.Final Charge Adjustment. All units must have refrigerant charge verified by proper adjustment ofsubcooling at the indoor unit after initial charge adjustment per Section 5. Proper adjustment means pressure and temperature of the liquid line at the indoor unit must be measured to calculate subcooling at the indoor unit. If subcooling at the indoor unit is less than 5°F, then additional refrigerant must be added until this subcooling level is achieved. If subcooling at the indoor unit is more than 7°F, then refrigerant must be removed until this subcooling level is achieved.SECTION 2. OUTDOOR UNIT AND INDOOR UNIT ARE AT THE SAME ELEVATION1.In a completely horizontal installation with a long line set where the indoor unit is at the same altitude as(or slightly below) the outdoor unit, the line set should be sloped continuously towards the indoor unit. This helps reduce refrigerant migration to the outdoor unit during a system’s off-cycle.2.The maximum elevation (vertical) difference for this section to be applicable is 10 feet (3.0 m) separationbetween outdoor unit and indoor unit. If outdoor unit is more than 10 feet (3.0 m) above indoor unit use Section 3. If outdoor unit is more than 10 feet (3.0 m) below indoor unit use Section 4.3.Inverted suction loop is not required at either unit.44.An accumulator is not required for air conditioners (accumulators are factory installed on heat pumps).5.An oil trap at the indoor unit is not required.6.Liquid Line Solenoid not required if non-bleed TXV is used on the outdoor unit.SECTION 3. OUTDOOR UNIT IS ABOVE THE INDOOR UNIT**An oil trap at the indoor unit is required if the elevation difference exceeds 80' (24.4 m). The trap can be constructed of standardrefrigerant fitting (See Figure 3-1.)1.Suction line must be sloped continuously towards the indoor unit.2.The maximum elevation (vertical) difference between the outdoor unit and indoor unit is:a. not restricted in this configuration for single stage air conditioning units (must adhere tomaximum equivalent length).b. 80 feet (24.4m) for single stage heat pump units. Exception: 200ft (61 m) vertical separation allowedfor 14 SEER Long Line Set models and 16 SEER single stage HP models.c. 25 feet (7.6 m) for two stage units.3.Inverted suction loop is not required at either unit.4.An accumulator is not required for air conditioners (accumulators are factory installed on heat pumps).5.Liquid Line Solenoid not required if non-bleed TXV is used on the outdoor unit.Long Radius Street Ell45°Ell45°Street EllShort RadiusStreet EllFigure 3-1. Oil Trap5SECTION 4. OUTDOOR UNIT IS BELOW THE INDOOR UNIT1.The maximum elevation (vertical) difference between the outdoor unit and the indoor unit is 80 feet(24.4 m).2.Suction line must be installed in a manner to prevent liquid migration to the outdoor unit from theindoor unit (see following note 3).3.An inverted suction line trap must be installed on the suction line just before the inlet to the indoor unit(see Figure 4-1). The top of the inverted loop must be slightly above the top of the indoor unit coil and can be created simply by brazing two 90° long radius elbows together if a bending tool is unavailable.Properly support and secure the inverted loop to the nearest point on the indoor unit or adjacent structure.4.An accumulator is required to be added (external to the outdoor unit, within 2 linear feet (61 linearcentimeters) of the outdoor unit) for air conditioning installations. See Table 4-1 for accumulator selection.Adapter fittings at the accumulator connection may be required. Do NOT install an accumulator in the suction line set in heat pump applications.5.Liquid Line Solenoid not required if non-bleed TXV is used on the outdoor unit.HL = Length of trap must be more than Indoor Unit Height (H)Figure 4-1. Indoor Unit with Inverted SuctionTable 4-1. Accumulator Size67SECTION 5. CALCULATIONS - TUBING EQUIVALENT LENGTH, TUBE SIZE ANDREFRIGERANT1.In long line applications the “equivalent line length” is the sum of the straight length portions of the suction line plus losses (in equivalent length) from 45 and 90 degree bends. Add the total straight (lineal) length of tubing to the equivalent length of elbows and bends to get total equivalent length.Equivalent length = Length Horizontal + Length Vertical + Losses from bends (see Table 5-1)2.Table 5-1 lists the equivalent length gained from adding bends to the suction line. Properly size the suction line to minimize capacity loss.Table 5-1. Losses from suction line elbows (equivalent length, ft.)Table 5-2. Losses from suction line elbows (equivalent length, m)Table 5-1. Losses from suction line elbows (equivalent length, ft.)EXAMPLE: 3/4” suction line using 3/4” elbows150 feet of straight tubing + (four short radius elbows x1.7) + (2 long radius elbows x1.5) =150 + 3.4 + 3 = 156.4 equivalent feet3.Table 5-2 lists multiplier values to recalculate system cooling capacity as a function of a system’s equivalent line length (as calculated from the suction line) and the selected suction tube size.NOTE: Select the proper suction tube size based on equivalent length of the suction line (see Tables 5-1 and 5-2) and recalculated system capacity.Table 5-3. Capacity Multipliers (feet)1 Equivalent length is to be used for capacity multiplier reduction.2 7/8” suction line is not approved for 2-ton two stage heat pump applications.3 7/8” suction line is not approved for 3-ton two stage heat pump applications over 80 feet.4 1-1/8 suction line is not approved for 4-ton and 5-ton two stage heat pump applications over 80 feet.Table 5-4. Capacity Multipliers (meters)84.Refrigerant Quantity Adjustment. All residential R-410A outdoor units are factory charged for 15 feet(4.6 m) of line set.To calculate the initial amount of extra refrigerant (in ounces):a. Subtract 15 feet (4.6 m) from the total linear (not equivalent) length of actual line setb. Multiply that value by 0.6 (oz. per foot) or 17.0 (g per meter) of R-410A refrigerantc. This will be the initial amount of R-410A refrigerant that must be added prior to finalcharge adjustment.All systems must have final charge adjustment performed as required in Section 1. In most residential applications a minimal amount of additional refrigerant will be needed to account for the volume in the suction line. For some applications using 1 1/8” suction line and/or over 150 feet of lineal length (45.7 m), approximately 3 pounds (1.4 kg) of additional refrigerant may be needed to account for the suction line.For a more precise calculation of refrigerant needs use Table 5-3. The additional refrigerant for given line lengths can be found in Table 5-4.RA (oz.) = (LA- 15) ft. x 0.6 oz./ft.RA ( g ) = (LA- 4.6) m. x 55.8 g/m.Where:RA = Initial additional refrigerant neededLA= Actual lineal line set lengthTable 5-5 Additional Refrigerant Per Unit Length.Table 5-6 Initial Refrigerant for Given Line Length (feet)Table 5-7 Initial Refrigerant for Given Line Length (meters)9THIS PAGE LEFT INTENTIONALLY BLANK 10THIS PAGE LEFT INTENTIONALLY BLANK11NOTE: SPECIFICATIONS AND PERFORMANCE DATA LISTED HEREIN ARE SUBJECT TO CHANGE WITHOUT NOTICEQuality Makes the Difference!All of our systems are designed and manufactured with the same high quality standards regardless of size or efficiency. We have designed these units to significantly reduce the most frequent causes of product failure. They are simple to service and forgiving to operate. We use quality materials and components. Finally, every unit is run tested before it leaves the factory.That’s why we know. . .There’s No Better Quality.Goodman Company, L.P.5151 San Felipe, Suite 500, Houston, TX 77056© 2015-2017 Goodman Company, L.P.12。
Sporlan R-410A产品介绍说明书
Sporlan products suitable for R-410A are introduced in this publication,Including special features,specifications, and characteristics of the devices for R-410A systems. Additional features,specifications,and characteristics for other refrigerants are included in appropriate sections of the Sporlan Catalogue.For immediate access to Sporlan literature please visit .R-410A is a 50% / 50% blend,by weight,of R-32 and R-125. The vapor pressure of R-410A is almost 50% greater than R-22’s vapor pressure.New R-410A systems must be designed to handle the higher pressure and require special service tools,such as manifold gauge sets,recovery units,and recovery tanks.R-410A is intended for use solely with polyolester (POE) oil, while R-22 can be used with POE,Alkylbenzene,or Mineral Oil.The higher pressure,and the fact that R-410A performs very much like a single component refrigerant,provide an opportunity to produce a more compact system with greater efficiency.In addition,R-410A refrigerant allows more suction line pressure drop since it is less sensitive to suction line efficiency losses.The future of the HVAC & R market looks promising for the development and use of R-410A systems.Applications primarily include air conditioning,chillers and commercial refrigeration.The superior performance characteristics of R-410A and the industry’s transition to HFCs have made this refrigerant a viable alternative to R-22 and other refrigerants,and is becoming the refrigerant of choice for many new air conditioning and heat pump designs.Catalogue R-410A MEJuly 2001Page 2— Catalogue R-410A&E Z I B EZ I B B g u o r h T t h g i a r t &E Z I EZ I B B el g n A &E Z I B I B B C u o r h T t h g i a r EZ I B B C el g n A THERMOSTATIC EXPANSION VALVESSporlan offers thermostatic expansion valves in R-410A nominal capacities between 0.88 and 28 kW. The models offered are externally equalized, have straight through or angle configuration, and SAE or ODF connections. The Sporlan refrigerant code for R-410A is the letter "Z ",which is used in the designation of products especially designed for R-410A service.The BIZE models have a conventional port construction.BBIZE models have the advantage of a balanced port construction,which makes them ideally suited for systems with a wide range of operating conditions.The CBIZE and CBBIZE models are similar to the BIZE and BBIZE, but have an internal check valve to allow refrigerant flow to bypass the expansion valve port in the reverse flow direction in heat pump systems.The integral check valve means fewer connections, easier installation,and increased reliability.The Sporlan TEVs designed for R-410A have replaceable thermostatic elements with a locknut ring stronger than normally used with common refrigerants such as R-22 or R-134a. This feature makes the thermostatic element capable of withstanding higher pressures. Replaceable thermostatic elements are designated by “KT-45-” plus the charge.Example: KT-45-ZGA.Currently, three thermostatic charges are available for R-410A service:ZGA – Has similar performance to the VGA charge used in R-22or NGA charge used in R-407C systems. The constituents and heavy thermal ballasts in the charge provide excellent anti-hunt characteristics by dampening the valve in the opening direction. The maximum operating pressure or MOP of this charge is not as defined as the ZCP160 charge,an alternate charge for R-410A air conditioning and heat pump applications.ZCP160– Has similar performance to the VCP100 charge used in R-22 systems or the NCP100 charge used in R-407C systems. The maximum operating pressure or MOP of this charge takes effect around 12°C evaporator temperature.The ZCP160 charge has a mild thermal ballast that dampens the valve in the opening direction only.ZN – Has similar performance to the VN charge used in R-22or NN charge used in R-407C systems. A heavy thermal ballast dampens the valve in the opening and closing directions.The ZN charge is a non-condensable charge without an MOP, and thus not subject to charge migration. It is used in special medium and high temperature applications, such as chillers located outdoors that must operate while exposed to cold temperatures.Contact the nearest Acal sales office if you have an application that requires a valve or charge that is not listed.Catalogue R-410A — Page 3ODF ConnectionsPage 4— Catalogue R-410ABIZE & BBIZEStraight Through ConfigurationB55 mmADDCCBIZE & BBIZEAngle ConfigurationE n i m 9n i m 9n i m 7n i m 7ni m 1Capillary Tube Length 76.2 cm Standard 152.4 cm Available47 mm49 mm56 mm90 mm30°7.9 m m m i n .B I ZE = 46 m m B B I Z E = 47 m mBIZE 46 mm BBIZE 47 mmCC E E49 mm49 mmDDDDDBCE Equalizer Option:1/8" OD x 31 cm ,61 cm or 91 cmlong capillary tube external equalizer with or without 1/4" SAE flare nutEqualizer Option:1/8" OD x 31 cm,61 cm or 91 cm long capillary tube external equalizer with or without 1/4" SAE flare nutE EGGFA1/4" ODFExternal Equalizer Fitting 1/4" ODF external equalizer fitting35Catalogue R-410A — Page 5CBIZE & CBBIZEStraight Through ConfigurationCBBIZEAngle ConfigurationEqualizer option:1/8" OD x 31 cm,61 cm or 91 cm long capillary tube external equalizer with or without 1/4" SAE flare nutEqualizer option:1/8" OD x 31 cm,61 cm or 91 cmlong capillary tube external equalizer with or without 1/4" SAE flare nut58 mmABCC30°DDG46mm49 mm59 mm93 mmFCBDAEHChatleff fittingsoption7.9 m m m i n .48 m m O D F 41 m mS A E6.4 m m 49 mm49 mmPage 6— Catalogue R-410AFor more information on Sporlan distributors please refer to Bulletin 20-10.SOLENOID VALVESValves with 4 different port sizes and ODF solder connections are available. The smallest port valve uses a MKC-1 coil while the rest use a MKC-2 coil. Sporlan solenoid valves are available in many different voltage and cycle ratings. Standard coils are listed in the specifications table below.Solenoid coils are available with either an integral junction box, a 1/2" conduit boss, or DIN connector. Hirshman connectors are also available. Models with other sizes and features are under development. Please contact the nearest Acal sales office if you have an application that requires a solenoid valve with capacities or voltages not shown in this catalogue.Catalogue R-410A — Page 7E6 SeriesE19 SeriesCoil removal 40 mmCoil removal 45 mmCoil removal 45 mm*B*BAADDDD*BAACCC E E14 SeriesFor more information on solenoid valves refer to Bulletin 30-10E6S130-HPE19S250-HPME9S240-HPPage 8— Catalogue R-410ACatch-All ®FILTER-DRIERSAll sealed models of Sporlan’s Catch-All and the HPC-100(heat pump) models are suitable for use in R-410A systems. The high water capacity and the acid removal ability of the Catch-All core are well suited to meet the demands of R-410A refrigerant and POE oil.Extensive testing of the materials and the molded core in the Catch-All have demonstrated its compatibility and effectiveness in systems using R-410A. Form 40-139 has a detailed explanation of R-410A compatibility testing of the Catch-All.fittingsFiberglass pad 100 mesh screenH ea v yl ea f sp ri n gCatalogue R-410A — Page 9 It’s the CORE that Counts!Page 10— Catalogue R-410ASA-14SU For more information refer to Bulletin 70-10Overall width is:33 mm for 1/4" and 3/8" sizes, 40 mm for 1/2" and 5/8" sizes, and 35 mm for 7/8" and 1-1/8" sizes.Most solder connections can be used as male fittings as well as female fittings.The 1/4”ODF is 3/8" ODM, the 3/8" ODF is 1/2" ODM, the 1/2" ODF is 5/8" ODM, and the 5/8"ODF is 3/4"ODM.Models with female flare and/or swivel nut connections are supplied with a copper gasket in the fitting.* These models have copper connections and feature a removable element cartridge — for replacement cartridge specify AC-20.Note:Change or add Catch-All Filter-Drier when the paper turns from green to chartreuse .SA-13SCatalogue R-410A — Page 11Zhu Gao DeRm. 1010, Tower 1 Kerry Everbright City 218 Tian Mu Road West Shanghai 200070, P.R. of China Tel: (86) 21 6353 4577Fax: (86) 21 6354 1227E-mail:*******************Acal China China Acal plcAir Conditioning & RefrigerationHeadquarters Office United Kingdom Peter Hogan 2 Chancellor Court Occam Road, Surrey Research Park Guildford GU2 7AH, United Kingdom Tel: (44) 1483 544500 Fax: (44) 1483 544550E-mail:*****************.ukwebsite:Helen Rosalia 10 Cutter Mill Road, Suite 203Great Neck, New York 11021, U.S.A. Tel: (1) 516 487 9870 Fax: (1) 516 487 9342E-mail:***************website: Hugo Dalla ZannaRua Conde do Pinhal, 2267, Suite 201 CEP 13560-140São Carlos, SP , Brasil Tel: (55) 16 270 8027 Fax: (55) 16 270 1604E-mail:**************A cal New York Inc International Sales Headquarters (excludes Europe & Japan)Acal S.A.Acal Brazil Brazil U.S.A.New York France Eliane Emerit-Bonnot Zone d'Activite des Marais 1 Avenue Louison Bobet BP 6494122 Fontenay-sous-Bois,Cedex, France Tel: (33) 1 4514 7300 Fax: (33) 1 4877 6230E-mail:***********website: www.acal.fr Acal Controls Ltd.European Sales Office Headquarters (excludes France & Germany)England Angus Mackintosh Unit 2, The Rose Estate, Osborn Way Hook, Hampshire RG27 9UT, United Kingdom Tel: (44) 1256 382520Fax: (44) 1256 382530E-mail: **********************.uk website: Elke Villhauer Fischeracker 274223 Flein/Heilbronn, Germany Tel: (49) 7 131 5810 Fax: (49) 7 131 5812 90E-mail:************website: www.acal.de Acal GmbH Germany Tony Koh Tampines Central P.O. Box 400, Singapore 915214Tel: (65) 654 65461 Fax: (65) 654 65462E-mail:******************.sgAcal Singapore Singapore Sarkis Ohannessian P.O. Box 70-994Antelias, Lebanon Tel: (961) 4 522 309 Fax: (961) 4 522 309E-mail:****************.lb A cal Middle East Lebanon Anil Yadav 16/34 1st. Floor Sidhora Kalan Near Shakti Nagar Rly Bridge Delhi, India 110052Tel: (91) 11 364 3211 Fax: (91) 11 364 3212E-mail:******************Acal India India Mike Rivera PMB# 2195944 Coral Ridge Drive Coral Springs, Florida 33076, U.S.A.Tel: (1) 954 345 8278 Fax: (1) 954 255 6468E-mail:********************.net Acal Florida U.S.A.Florida Peter Harms Suite 3, 70 Kingsway Glen Waverley VIC 3150Tel: (61) 3 95747810Fax: (61) 3 9574 7820E-mail:****************Acal Australia Pty. Ltd.Australia。
2011版华安达谷轮R410A涡旋压缩机样本
R410A Scroll Compressor For Air ConditioningR410A 空 调 涡 旋 压 缩 机NEW低运行成本可靠环保宁静高效high efficiencylow noiseenvironment protectionhigh reliabilitylow operation cost目 录压缩机特性及运行范围.................................2产品型谱图................................................3技术参数...................................................4性能参数...................................................5注油量......................................................11电气参数...................................................12压缩机接线图.............................................13外形尺寸图................................................15压缩机配置................................................23应用小常识................................................24应用注意事项.............................................27命名规则 (29)ZP/VP系列柔性涡旋压缩机特性及运行范围7060ZP系列柔性涡旋(ZP57-ZP485)基于优越的谷轮涡旋技术平台,特别为高效系统优化。
LG ARUN LM3系列R410A双功能热泵机维护手册说明书
Internal Use Only CAUTIONBefore Servicing the unit, read the safety precautions in General SVC manual.Only for authorized service personnel.Outdoor Unit SERVICE MANUAL(Exploded View)MODEL : A RUN***LM3 SeriesR410A Solo - Heat Pump1. Specifications (3)2. Function (4)3. Dimensions (5)4. Piping Diagrams (6)5. Wiring Diagrams (17)6. Exploded View (22)1. SpecificationsSpecificationHeat Pump(50Hz/60Hz)Notes:1. Capacities are based on the following conditions:Cooling: - Indoor Temperature 27°C(80.6°F) DB/19°C(66.2°F) WB- Outdoor Temperature 35°C(95°F) DB/24°C(75.2°F) WB Heating: - Indoor Temperature 20°C(68°F) DB/15°C(59°F) WB- Outdoor Temperature 7°C(44.6°F) DB/6°C(42.8°F) WB Piping Length - Interconnecting Piping Length 7.5m 4. Wiring cable size must comply with the applicable local and national code.5. Due to our policy of innovation some specifications may be changed withoutprior notificationConversion FormulaRT = kW x 0.284kcal/h = kW x 860Functions2. FunctionsCategory Function Multi V III Solo – Heat pump Defrost/ Deicing O High pressure switch O Phase protection O Restart delay(3-minutes) OSelf diagnosis O Soft start O Trial operation O Auto operation(Artificial intelligence) OAuto restart operation O Network Solution(LGAP) O Power Distribution Indicator(PNU-D1S00) OReliabilityConvenienceCAC networkFunction O : Applied X : Not applied - : No reationOption : Model name & price are different according to options, and assembled in factory with main unitAccessory : Installed at field, ordered and purchased separately by the corresponding model name,supplied with separated package.O : Applied X : Not applied - : No reationOption : Model name & price are different according to options, and assembled in factory with main unitDeviceMulti V III Solo – Heat pumpCentral ControllerSimple Controller PQCSB101S0AC EzPQCSZ250S0Function controller PQCSB101S0 + PQCSC101S0Function SchedulerPQCSB101S0 + PQCSD130A0AC Smart ll PQCSW320A1E Expansion Kit PQCSE440U0Option Kit PQCSE341A0 / PQCSE342A0ACP PQCPA11A0E / PQCPB11A0E AC ManagerPQCSS520A0E BNU LONWORKS Gateway PQNFB16A1BACnet GatewayPQNFB17B0Do KitPQNFP00T0Power Distribution Indicator(PDI)PQNUD1S00Cool / Heat Selector PRDSBM ODU Dry Contact PQDSBCDVM0ProgramLG MV Option OtherY branchAccessory Header branch Accessory Air GuideAccessory Refrigerant Charging Kit PRAC1DimensionsO u t d o o r U n i tA R U N 80L M 33. DimensionsDimensionsO u t d o o r U n i tA R U N 100L M 3A R U N 120L M 3Piping Diagrams 4. Piping Diagrams4.1.1 8HP(UX2 1Comp.)Piping DiagramsPiping DiagramsPiping Diagrams4.1.2 10, 12HP(UX2 2Comp.)Piping DiagramsPiping DiagramsWiring Diagrams 5. Wiring Diagrams5.1.1 8HP(UX2 1Comp.)Wiring Diagrams5.1.2 10, 12HP(UX2 2Comp.)Wiring DiagramsnMain PCB220V Power output Terminal220V Power Output TerminalHeat Pumpn Noise FilterWiring Diagrams n Inverter PCB- 8Hp (UX2 1 Comp)- 10/12Hp (UX2 2 Comp)CN_T2_1R Phase Terminal CN_P1T Phase TerminalCN_L1(R)R Phase TerminalCN_N1N Phase Terminal CN13 15V OUTPUT DC 15V Output TerminalCN04 PFC LGMV PFC Onboarding Terminal CN12 DC LINK 700 V (700V DC LINK)CN06 AC 220V INPUT 220V Power Input TerminalCN_R2_1T Phase Terminal CN_L3(T)T Phase Terminal CN01 FANCommunication Terminal to Fan PCBCN02 MAINCommunication Terminal to Main PCBCN03 INV LGMV INV Onboarding TerminalCH14 U.V.W OUT UVW Output TerminalCN-T2CN-R2R Phase TerminalT Phase TerminalCN06 FANCommunication Terminal to Fan PCBCH07 MAINCommunication Terminal to Main PCB CN03 INV LGMVINV Onboarding TerminalCN04 15V OUTPUT DC 15V Output TerminalCN08 AC220 INPUT 220V Power Input TerminalCN01 COMP CON U.V.W Output TerminalCN-N1N Phase Terminal CN05 DC-LINK(700V)700V DC LinkCN-P1T Phase TerminalCN-L1_R R Phase TerminalCN-L3_T T Phase TerminalWiring DiagramsnFAN PCB(Reset button)Exploded view6. Exploded View6.1 Heat Pump ModelPart L/No. RemarkInv Comp. Heater 553000A Housing Color : BlueExploded view55211655211455211G352114552115552201A552201C552203B552203A148000D165010B552204B561410A263230B263230A552200A165010A561410D552202552117W52240BW52240C661400566000Inv. PCB Grease(Inv. Heat Sink)RAC31217901(Fan Heat Sink)268711AW0DSW6200268711B261704263230EW6640135500D435511W49200BW49200A263230DW6631A268711CPart L/No. Sensor location RemarkTemp. Sensor 1 263230A Sub-Cool Out + Liquid Pipe Housing Color : YellowExploded view6.1.2 10,12HP(UX2 2Comp.)Copyright ©2011 LG Electronics. Inc. All right reserved.Only for training and service purposesLGE Internal Use Only- 21-W6640268711BW49200AInv. PCB GreaseRAC31217901(Fan Heat sink)268711A263230EPart L/No. Sensor location RemarkTemp. Sensor 1 263230A Sub-Cool Out + Liquid Pipe Housing Color : Yellow Temp. Sensor 2 263230B Suction Pipe + Inv. Discharge + HEX Housing Color : Purple Temp. Sensor 3 263230C Const. Speed Discharge Housing Color : GreenExploded viewP/NO : MFL54555530September, 2011。
R410A冷媒使用指南
抽真空操作步骤
5. 用内六角扳手打开细角阀90度,五秒钟关 用内六角扳手打开细角阀90度 观察是否有泄漏点; 闭,观察是否有泄漏点; 6. 用肥皂水检查室内外联机处是否有泄漏, 用肥皂水检查室内外联机处是否有泄漏, 检查完要将肥皂水擦干; 检查完要将肥皂水擦干; 7. 从维修口取下软管,完全打开细角阀与粗 从维修口取下软管, 角阀。 角阀。 8. 确认维修口处没有泄露; 确认维修口处没有泄露;
制冷剂与冷冻机油匹配
• R22冷媒压缩机一般采用矿物油; R22冷媒压缩机一般采用矿物油 冷媒压缩机一般采用矿物油; • R410A冷媒压缩机一般采用有机合成油,常 R410A冷媒压缩机一般采用有机合成油, 冷媒压缩机一般采用有机合成油 见PVE(醚类)、POV(酯类); PVE(醚类)、 )、POV(酯类); • R410A与矿物油不能互溶。R410A空调系统 R410A与矿物油不能互溶 R410A空调系统 与矿物油不能互溶。 混入矿物油(R22用),会导致冷冻油劣化 会导致冷冻油劣化、 混入矿物油(R22用),会导致冷冻油劣化、 水解生成金属盐,空调毛细管堵塞等, 水解生成金属盐,空调毛细管堵塞等,所 以应该严格控制
R410A冷媒使用指南 R410A冷媒使用指南
制冷剂介绍
• 制冷循环中用于传递、转移热量的流体; • 常见制冷剂有氟利昂、水、氨、二氧化碳 等 • 单一工质制冷剂: R22、水、氨 单一工质制冷剂: R22、水、氨 • 混合工质制冷剂: R407C、R410A 混合工质制冷剂: R407C、
制冷剂性质
制冷剂填充压力特性
• R410A冷媒大约是R-22冷媒压力的1.6倍左右。 R410A冷媒大约是 22冷媒压力的 倍左右 冷媒大约是R 冷媒压力的1.6倍左右。 高压力条件使R410A冷媒使用 冷媒使用R410A冷媒专 高压力条件使R410A冷媒使用R410A冷媒专 用工具和安装材料。 用工具和安装材料。
- 1、下载文档前请自行甄别文档内容的完整性,平台不提供额外的编辑、内容补充、找答案等附加服务。
- 2、"仅部分预览"的文档,不可在线预览部分如存在完整性等问题,可反馈申请退款(可完整预览的文档不适用该条件!)。
- 3、如文档侵犯您的权益,请联系客服反馈,我们会尽快为您处理(人工客服工作时间:9:00-18:30)。
R410A Scroll Compressor For Air ConditioningR410A 空 调 涡 旋 压 缩 机NEW低运行成本可靠环保宁静高效high efficiencylow noiseenvironment protectionhigh reliabilitylow operation cost目 录压缩机特性及运行范围.................................2产品型谱图................................................3技术参数...................................................4性能参数...................................................5注油量......................................................11电气参数...................................................12压缩机接线图.............................................13外形尺寸图................................................15压缩机配置................................................23应用小常识................................................24应用注意事项.............................................27命名规则 (29)ZP/VP系列柔性涡旋压缩机特性及运行范围7060ZP系列柔性涡旋(ZP57-ZP485)基于优越的谷轮涡旋技术平台,特别为高效系统优化。
因此制造商使用它设计最高能效系统时将省去很多工作。
当然,就像艾默生环境优化技术一直以来的作风,我们将通过经验丰富的工程师和优越的系统设计软件为制造商提供完善的技术支持。
VP系列柔性涡旋(VP90-VP144)QuestSummitLCSR410A产品型谱图︾7.5 HP12 HP5 HP40 HP型 号电 压(V)相 数排量(m3/hr)额定功率(HP)制冷量(W)输入功率(W)COP(W/W)电流(A)重量(Kg)ZP57K3E-PFJ220-24019.44 4.813950465032441 ZP57K3E-TFD380-42039.44 4.813950465038.141 ZP61KCE-PFZ220-240110.115148004933323.340 ZP61KCE-TFD380-420310.115147004742 3.18.340 ZP67KCE-PFZ220-240110.965162005400325.740 ZP67KCE-TFD380-420310.96 5.6161005194 3.19.140 ZP72KCE-TFD380-420311.68617100570039.840 ZP83KCE-TFD380-420313.437199006419 3.111.740 VP90KSE-TFP380314.647.5219006844 3.212.357 VP103KSE-TFP380316.839252007875 3.213.660 VP120KSE-TFP380319.8410293009156 3.216.661 VP137KSE-TFP380322.1611.53260010188 3.217.861 VP144KSE-TFP380323.42123540010727 3.318.761 ZP154KCE-TFD380-420324.87133730011303 3.320.765 ZP182KCE-TFD380-420329.08154400013333 3.325.766 ZP235KCE-TWD380-420337.97205700017273 3.329.9140 ZP295KCE-TWD380-420346.71257150021667 3.337.2160 ZP385KCE-TWD380-420360.79309250028030 3.348.1177 ZP485KCE-TWD380-420377.334011700035455 3.360.3200备注:*1:在ARI工况下测试得到的制冷量。
(ARI工况为:蒸发温度 7.2℃,冷凝温度 54.4℃,环境温度 35℃,液体温度 46.1℃,回气温度 18.3℃)*2:在ARI工况下测试得到运行电流:220V(单相),380V(三相)。
R410A系列 - ZP∕VP 技术参数 50Hz-20(4)-15(4.8)-10(5.7)-5(6.8)0(8)5(9.3)7(9.9)10(10.8)12(11.5)C 925011500125001410015200P 56005500545054005350A 27.827.427.226.926.7C 710091001130013750148001650017700P 44504380431043204190414004100A 2322.722.42221.821.621.4C 495067508650107001300015600168001860019900P 356035103470342033603300327032303200A 19.219.118.918.618.418.11817.817.6C 62507950985012001440017200184002040021800P 277027402710267026302590257025502530A15.915.815.715.515.315.11514.914.8-20(4)-15(4.8)-10(5.7)-5(6.8)0(8)5(9.3)7(9.9)10(10.8)12(11.5)C 1015012450134501500016100P 57005650565056005600A 26.726.526.526.426.4C 795099001210014550156001730018500P 4520450044904480448044904490A 21.321.221.121.121.221.221.3C 590074509300114001375016400176001940020700P 362036103610362036303650366036703690A 17.217.217.217.217.317.417.417.617.7C 6750840010400126001520018000193002120022600P 292029202940296029803010302030403050A14.214.214.214.314.314.514.614.714.9-20(4)-15(4.8)-10(5.7)-5(6.8)0(8)5(9.3)7(9.9)10(10.8)12(11.5)C 1125013650147001630017500P 62006200620062006200A 29.329.229.229.329.3C 8750108501320015900171001890020300P 4940492049304940495049604960A 23.323.223.223.323.323.323.4C 6300810010100124001500018000193002130022800P 396039603970399040104020402040104000A 18.818.818.818.919191918.918.9C 7300920011350138001670019900213002360025200P 320032303260327032703230321031603120A15.315.415.615.615.615.415.31514.850Hz Operation R410A COPELAND SCROLL PFJ/Z 220-1-50冷凝温度 ℃(饱和压力,巴)蒸发温度 ℃(饱和压力,巴)ZP57K3E-PFJ60(38.2) 50(30.5) 40(24.1) 30(18.8)ZP61KCE-PFZ60(38.2) 50(30.5) 40(24.1)ZP67KCE-PFZ60(38.2) 50(30.5) 40(24.1) 30(18.8)30(18.8)-20(4)-15(4.8)-10(5.7)-5(6.8)0(8)5(9.3)7(9.9)10(10.8)12(11.5)C 955011700126001410015100P 54505350530052505200A 9.2998.98.8C 750093501140013700147001630017500P 4370429042204150412040904060A 7.87.77.67.57.57.57.4C 555071008850108001300015500166001840019600P 344033903340329032503200318031603140A 6.7 6.6 6.6 6.5 6.5 6.4 6.4 6.4 6.4C 650081009950120501445017200184002030021700P 263026102580254025002450243024002370A5.8 5.85.8 5.75.7 5.7 5.6 5.6 5.6-20(4)-15(4.8)-10(5.7)-5(6.8)0(8)5(9.3)7(9.9)10(10.8)12(11.5)C 975012150132001485016000P 55505450540053505300A 9.59.49.39.29.1C 750096001190014500156001740018700P 46004520443043400430042304180A 87.97.87.77.67.57.5C 525071009100113001375016500177001960021000P 378037303680361035403460343033803340A 6.9 6.8 6.7 6.6 6.5 6.4 6.4 6.3 6.2C 6600840010400126501520018100194002150023000P 299029502910286028103760273027002670A5.7 5.75.6 5.65.5 5.4 5.4 5.3 5.3-20(4)-15(4.8)-10(5.7)-5(6.8)0(8)5(9.3)7(9.9)10(10.8)12(11.5)C 1100013450145501620017400P 595005900590059005900A 10.210.210.210.210.2C 8600107501320015900171001890020200P 4710471047104710470047004710A 8.48.48.48.48.48.48.4C 6450820010200125001510018000193002130022700P 372037303740374037403750375037603760A 77777777.17.1C 7700950011600140001680020000214002350025100P 295029602970298029903000301030303050A6666666 6.1 6.140(24.1) 30(18.8)30(18.8)ZP67KCE-TFD60(38.2) 50(30.5)ZP61KCE-TFD60(38.2) 50(30.5) 40(24.1) 60(38.2) 50(30.5) 40(24.1) 30(18.8)50Hz Operation R410A COPELAND SCROLL TFD 380-3-50冷凝温度 ℃(饱和压力,巴)蒸发温度 ℃(饱和压力,巴)ZP57K3E-TFD-20(4)-15(4.8)-10(5.7)-5(6.8)0(8)5(9.3)7(9.9)10(10.8)12(11.5)C 1190014350155001720018500P 65006500650065006450A 1111111111C 9550116501410016900181002010021500P 5100510051005100510051005100A 9999999C 7150895011000134001610019200206002280024300P 400040104020403040404060406040704080A 7.47.47.47.47.57.57.57.57.5C 82001015012400149501790021300228002510026800P 318031803190321032303260327032903310A6.3 6.36.3 6.36.4 6.4 6.4 5.5 6.5-20(4)-15(4.8)-10(5.7)-5(6.8)0(8)5(9.3)7(9.9)10(10.8)12(11.5)C 1380016800181002020021700P 73507350735073507350A 1313131313C 10900134001630019600211002340025100P 5750575057505800580058005850A 10.810.810.810.910.910.911C 81501025012700155001860022200238002630028100P 444044704490451045504590462046604700A 9.19.29.29.29.39.39.49.49.5C 94501175014350173002070024500262002890031000P 345034803520355036003670371037703810A7.9888.18.18.28.28.38.4-20(4)-15(4.8)-10(5.7)-5(6.8)0(8)5(9.3)7(9.9)10(10.8)12(11.5)C 1500018200196002190023400P 80507950795079007900A 13.913.713.713.713.7C 12100148501800021500231002560027300P 6300625062506250625063006350A 11.411.311.311.311.311.411.4C 91501140014000170002040024300261002880030500P 500050004990499050005050510051505200A 9.79.79.69.79.79.89.89.99.9C 103501275015600189002260026900288003200034000P 407040504050406040904130416042004240A8.58.58.58.58.68.68.78.78.730(18.8)40(24.1) 30(18.8)VP90KSE-TFP60(38.2) 50(30.5) 40(24.1) 50Hz Operation R410A COPELAND SCROLL TFD/P 380-3-50冷凝温度 ℃(饱和压力,巴)蒸发温度 ℃(饱和压力,巴)ZP72KCE-TFD60(38.2) 50(30.5) 40(24.1) 30(18.8)ZP83KCE-TFD60(38.2) 50(30.5)-20(4)-15(4.8)-10(5.7)-5(6.8)0(8)5(9.3)7(9.9)10(10.8)12(11.5)C 1730021200229002540027200P 90508950895089508950A 15.115151515C 13500169002070024800266002940031500P 7250715070507050705071007150A 12.912.812.712.712.712.812.8C 99001275015900195002350028000300003300035500P 575057005650565056505650570057505800A 11.211.211.111.111.111.111.211.311.3C 117001455017900217002610031000330003650039000P 452045304520451045104560459046604720A10109.99.99.9101010.110.2-20(4)-15(4.8)-10(5.7)-5(6.8)0(8)5(9.3)7(9.9)10(10.8)12(11.5)C 1995024400263002940031600P 1060010500104501040010350A 18.7518.618.5518.4518.4C 15850197502410029100312003460037000P 8390832082608210819081808180A 15.515.415.3515.2515.2515.2515.25C 117501505018800230002780033100354003900041500P 659065806560652065006500651065506580A 131312.9512.912.912.912.912.9512.95C 140001745021400258003080036300387004250045100P 515051505140513051505210525053305400A11.1511.1511.1511.1511.1511.211.2511.311.35-20(4)-15(4.8)-10(5.7)-5(6.8)0(8)5(9.3)7(9.9)10(10.8)12(11.5)C 2220027200294003300035000P 1160011600116001160011600A 19.919.919.919.819.8C 17600220002680032000345003850041000P 9200920092009200920092009250A 16.416.416.416.416.416.416.4C 131001680020900255003050036500390004350046500P 735073507350735073507350740074007450A 13.713.713.713.813.813.813.813.813.8C 156001940023600285003400041000435004850052000P 585058505850590059005950600060506100A11.711.811.811.811.811.911.9121260(38.2) 50(30.5) 冷凝温度 ℃(饱和压力,巴)蒸发温度 ℃(饱和压力,巴)50Hz Operation R410A COPELAND SCROLL TFP 380-3-50VP137KSE-TFPVP103KSE-TFP40(24.1) 60(38.2) 50(30.5) 40(24.1) 30(18.8)VP120KSE-TFP60(38.2) 50(30.5) 40(24.1) 30(18.8)30(18.8)-20(4)-15(4.8)-10(5.7)-5(6.8)0(8)5(9.3)7(9.9)10(10.8)12(11.5)C 2430029700319003520037400P 1195012050121001225012400A 20.820.820.820.8520.95C 186500238002930034900373004080043100P 945094909580977098701005010200A 16.916.9517.0517.2517.317.517.6C 132501755022400277003340039300418004560048100P 744075207610771078608080819083808530A 13.91414.1514.314.514.814.9515.1515.35C 163002060025500310003700043300460005000052700P 608062106310641065406710680069507070A11.9512.0512.2512.4512.71313.213.4513.65-20(4)-15(4.8)-10(5.7)-5(6.8)0(8)5(9.3)7(9.9)10(10.8)12(11.5)C 2590031000335003700039500P 1290013000130001310013100A 22.3232323.123.1C 20900256003100037000395004350046500P 10300103001040010500105001060010600A 18.818.91919.119.219.219.3C 15400196002420029200350004150044500490052500P 810081508200830084008500855086508700A 15.715.815.91616.116.316.316.516.5C 179002210026900325003850046000495005450058500P 650065506600675068507000710072007300A13.613.713.813.914.114.314.414.514.6-20(4)-15(4.8)-10(5.7)-5(6.8)0(8)5(9.3)7(9.9)10(10.8)12(11.5)C 3050037000395004400047000P 1510015100151001520015200A 28.128.228.228.228.3C 24700300003650043500465005150055000P 12000121001210012200123001240012400A 23.623.723.8242424.124.1C 182002310028400345004100049000525005800062000P 9500960097009800990010000101001020010200A 20.220.320.520.720.8212121.121.2C 210002590031500380004550054000580006450069000P 770078007900800081508250825083008350A1818.218.318.418.618.718.718.818.850Hz Operation R410A COPELAND SCROLL TFP/D 380-3-50 冷凝温度 ℃(饱和压力,巴)蒸发温度 ℃(饱和压力,巴)VP144KSE-TFP60(38.2) 50(30.5) 40(24.1) 30(18.8)ZP154KCE-TFD60(38.2) 50(30.5) 40(24.1) 30(18.8)ZP182KCE-TFD60(38.2) 50(30.5) 40(24.1) 30(18.8)-20(4)-15(4.8)-10(5.7)-5(6.8)0(8)5(9.3)7(9.9)10(10.8)12(11.5)C 4000048500520005800062000P 1980019900199002000020000A 3333.133.133.133.1C 31000385004650056000605006700072000P 15500156001570015900159001610016100A 27.427.627.727.827.827.927.9C 230002900036000440005300063500685007550081000P 124001240012500127001280013000131001320013300A 23.123.423.523.723.823.92424.124.2C 264003300040500495005950071000760008400090000P 101001030010400105001070010900109001110011200A20.420.620.720.82121.221.321.421.6-20(4)-15(4.8)-10(5.7)-5(6.8)0(8)5(9.3)7(9.9)10(10.8)12(11.5)C 5000060500650007200077500P 2460024700247002480024800A 40.640.740.740.840.9C 40000485005900070500755008400089500P 19600198001990020000201002020020200A 34.134.334.534.734.734.834.9C 3000037500460005550067000795008550094500101000P 156001580015900161001620016400165001660016700A 29.329.529.729.930.130.330.460.530.6C 34000420005100061500740008800094000104000111000P 127001290013000132001340013600137001390014000A26.126.326.526.626.827.127.227.327.5-20(4)-15(4.8)-10(5.7)-5(6.8)0(8)5(9.3)7(9.9)10(10.8)12(11.5)C 6550078500840009300099500P 3190032000321003230032400A 53.153.353.453.653.8C 5150063500765009150098000108000115500P 25600256002560025800259002610026300A 444444.144.344.544.845C 3700047500590007200086500103000110500122000130000P 206002050020500207002090021100213002150021600A 37.237.137.237.337.537.938.138.438.6C 4300053500655007950095500113500121500134500143500P 164001650016700169001720017600177001800018100A31.93232.332.532.933.333.533.834.130(18.8)40(24.1) 50(30.5) 40(24.1) 30(18.8)30(18.8)ZP385KCE-TWD60(38.2)ZP295KCE-TWD60(38.2) 50(30.5) 40(24.1) 60(38.2) 50(30.5) 50Hz Operation R410A COPELAND SCROLL TWD 380-3-50冷凝温度 ℃(饱和压力,巴)蒸发温度 ℃(饱和压力,巴)Z P235KCE-TWD-20(4)-15(4.8)-10(5.7)-5(6.8)0(8)5(9.3)7(9.9)10(10.8)12(11.5)C 825009900010600117500126000P 4030040300403004030040300A 66.766.766.766.766.7C 670008100097000116000124000137500146500P 32100324003270033000331003330033400A 54.75555.455.95656.356.4C 51000630007650092500110500131500140500155000165500P 252002570026200267002720027600278002800028200A 45.145.646.246.947.648.348.548.949.1C 575007050085000102500122000145000155000170500182000P 207002130021900225002300023500237002390024000A3939.740.541.34242.742.943.243.4L1L2L1L222 3.2 3.122 3.2 3.12233223322332254227722662.5 2.4663.23.150Hz Operation R410A COPELAND SCROLL TWD 380-3-50冷凝温度 ℃(饱和压力,巴)蒸发温度 ℃(饱和压力,巴)Z P485KCE-TWD备注:以上性能参数(±5%)是基于72小时的运行测试,如有改动恕不预先通知。