环己烷绿色催化氧化法生产环己酮年产10万吨环己酮精馏塔设计计算说明书
正己烷-环己烷设计精馏装置精馏塔
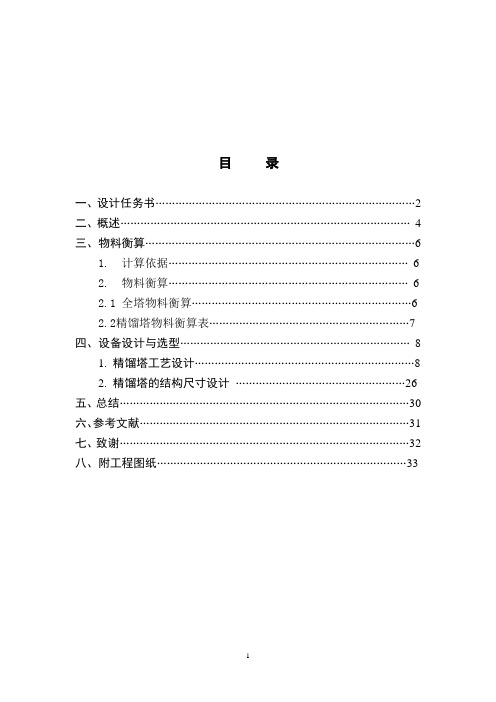
目录一、设计任务书 (2)二、概述 (4)三、物料衡算 (6)1. 计算依据 (6)2. 物料衡算 (6)2.1 全塔物料衡算 (6)2.2精馏塔物料衡算表 (7)四、设备设计与选型 (8)1. 精馏塔工艺设计 (8)2. 精馏塔的结构尺寸设计 (26)五、总结 (30)六、参考文献 (31)七、致谢 (32)八、附工程图纸 (33)08级化学工程专业《化工原理》课程设计任务书设计课题:环己烷-正己烷精馏装置精馏塔设计一、设计条件1、年产环己烷:40000 (吨)2、产品环己烷组成:C6H1299.5% (质量分数,下同) 、C6H140.5%3、原料为常温液体,原料组成:C6H1290%、C6H1410%4、分离要求:塔顶环己烷含量不大于1%二、设计内容1、物料衡算(精馏塔、预热器、冷凝器、再沸器)2、热量衡算(预热器、冷凝器、再沸器)3、精馏塔理论塔板数4、精馏塔实际塔板数、塔径和塔高的计算5、精馏塔结构、材质的选择6、精馏塔工艺尺寸、塔盘结构尺寸的设计计算等7、精馏塔流体力学性能验算8、精馏塔塔板性能负荷图9、精馏塔附件的设计计算(接管、支座、人孔等)10、精馏塔装配图的绘制三、设计要求1、设计方案简介对产品的性能、用途、工业状况及未来的发展前景进行概括和总结。
对给定或选定的工艺流程、主要设备的型式进行简要的论述。
2、工艺设计选定工艺参数,对单个设备作出衡算示意图,进行物料衡算、热量衡算,以表格形式表达衡算结果,其中的数据(非给定数据)及计算公式(经验公式)必须交待来源(即何种参考书目,并在参考文献中列出)。
3、设备计算选择设备的结构形式,并说明理由。
进行设备的结构尺寸和工艺尺寸的设计计算。
4、辅助设备选型典型辅助设备的主要工艺尺寸的计算,设备规格型号的选定。
5、设计说明书的编写要求严格按照邵阳学院毕业设计(论文)格式进行编写。
设计说明书应按顺序包括以下内容:(1)设计说明书封面;(2)设计任务书; (3)目录; (4)概述(设计方案简介);(5)工艺计算(物料衡算、热量衡算); (6)设备设计(主要设备设计、辅助设备设计或选型); (7)设计总结、评述; (8) 参考资料; (9)致谢;(10)附工程图纸。
环己酮生产企业

石家庄焦化集团10万吨环己酮项目,总投资5亿元。
该项目引进日本旭化成株式会社代表国际领先水平的环己烯法工艺路线建设10万吨环己酮生产装置。
该工艺与传统的环己烷法生产工艺相比,原料苯几乎100%转化成可利用的产品,苯耗较传统工艺低200kg/t环己醇以上,用氢量只相当于传统工艺的2/3,无对环境有害的物质产生,具有“本质上节能、无公害和安全”等特点;不产生有机酸,无需碱液中和,减少了装置投资和运行费用,可变成本较传统KA油法降低20~25%;加氢和水合反应均在水相中进行,反应温和,较传统的氧化工艺更安全,避免了腐蚀性副产品堵塞,具有更高的操作性,降低了水、电、气等能源消耗。
该工艺循环利用原料,节约能源,无污染,是清洁、环境友好、经济的生产路线。
项目建成后,年产环己酮10万吨,环己烷2.5万吨,实现销售收入15亿元,利税3亿元,利润2亿元。
项目于09年4月30日投产。
项目投产后,每年可生产9.6万吨环己酮、2.5万吨环己烷、1600吨燃料油、300吨溶剂油和其它副产品。
年可实现销售收入12.5亿元,利税2.87亿元。
我国的环己酮生产主要集中在9大生产厂家,其中3~7万吨/年规模以上的有南京帝斯曼公司、巴陵分公司、巴陵石油化工有限责任公司、辽阳石化公司、中国神马集团尼龙66盐公司、巨化集团锦纶厂等6家企业。
这6家企业的生产能力达到了26.5万吨,占全国总产能的90%以上。
其中辽阳化纤和神马集团均用于生产己二酸,而巴陵分公司、南京帝斯曼公司为引进装置,其己内酰胺产能经扩改分别达8万吨/年和6.5万吨/年,配套的环己酮产能分别为7万吨/年和5.5万吨/年;其余为国产化装置,其中巴陵石油化工有限责任公司和巨化锦纶厂的环己酮装置在消化吸收国内外先进技术的基础上,也达到了国外的先进技术水平。
其余3家分别是太原化工厂、锦西化工总厂和山东天原化学工业公司,生产规模在1万吨/年以下。
国内环己酮主要生产厂家如表1所示。
年产10万吨年苯加氢制环己烷项目

山东菏泽玉皇化工有限公司10万吨/年苯加氢制环己烷项目可行性研究报告常州化工设计院有限公司二零一零年四月目录第一章总论 01.1概述 01.2编制项目可行性研究报告的依据和原则 01.3项目背景、经营意义、投资意义 (1)1.4项目的范围 (3)1.5研究结果 (3)第二章市场分析和价格预测 (7)2.1产品市场分析和价格预测 (7)2.2原料供求及价格预测 (9)2.3辅助材料、燃料的供应 (13)第三章生产规模、总工艺流程及产品方案 (14)3.1生产规模 (14)3.2总工艺流程 (14)3.3产品方案 (15)3.4全厂自控水平 (16)第四章工艺装置 (17)4.1工艺原理 (17)4.2工艺技术选择 (21)4.3环己烷装置工艺流程 (26)4.4自控水平 (31)4.5主要设备的选择 (35)4.10消耗指标 (36)4.7装置界区内的公用工程设施 (37)4.8装置“三废”排放 (37)第五章建厂地区条件和厂址选择 (39)5.1建厂条件 (39)5.2厂址选择 (42)第六章总图运输、储运、土建、厂内外管网 (43)10.1总图运输 (43)10.2储运 (45)10.3土建 (46)10.4厂区外管 (47)第七章公用工程 (50)7.1给排水 (50)7.2供电、电信 (51)7.3供热、供风 (56)7.4脱盐水站 (57)7.5采暖通风及空气调节 (57)第八章辅助生产设施 (59)8.1消防设施 (59)8.2维修设施 (61)8.3仓库 (62)8.5火炬 (62)第九章能耗分析及节能措施 (63)9.1概述 (63)9.2能耗构成分析 (63)9.3工艺装置节能措施 (65)第十章环境保护 (66)10.1编制依据 (66)10.2设计采用的环境质量标准和排放标准 (66)10.3建设地区环境现状 (66)10.4建设项目主要污染物状况及治理 (68)10.5环境保护工程所需投资和定员 (71)10.10环境影响评价分析 (71)第十一章劳动保护与安全卫生 (72)11.1设计依据 (72)11.2工程概述 (73)11.3建筑和场地布置 (75)11.4生产过程中职业危险、危害因素的分析 (75)11.5设计中采用的主要安全和劳动保护措施 (77)11.10预期效果评价 (78)11.7劳动安全卫生机构设置及人员配备情况 (79)第十二章企业组织及定员 (80)12.1企业经营体制 (80)12.2企业管理体制 (80)12.3装置定员 (80)12.4人员来源和培训 (81)第十三章企业管理设施和生活福利设施 (82)13.1企业管理设施 (82)13.2生活福利设施 (82)第十四章项目实施规划 (83)14.1建设周期的规划 (83)14.2实施进度规划 (83)第十五章投资估算和资金筹措 (85)15.1投资估算 (85)15.2资金筹措 (86)15.3资金运筹计划 (87)第十六章生产成本费用估算 (88)110.1成本费用估算依据 (88)110.2成本费用估算及分析 (89)第十七章财务评价 (90)17.1财务评价的依据和说明 (90)17.2效益及财务评价指标计算 (91)第十八章不确定性分析 (92)18.2敏感性分析 (92)第十九章综合评价 (93)19.1综合评价 (93)19.2研究报告结论 (93)第一章总论1.1概述1.1.1项目名称:10万吨/年苯加氢制环己烷项目1.1.2主办单位:山东菏泽玉皇化工有限公司1.1.3法定地址:山东菏泽市经济技术开发区1.1.4企业性质:民营企业1.1.5 法人代表:王金书1.1.10注册资金:35000万元1.1.7项目建设投资(估算):21089.10 万元1.2 编制项目可行性研究报告的依据和原则1.2.1 编制可行性研究报告的依据(1) 山东菏泽玉皇化工有限公司提供的10万吨/年环己烷工程可行性研究报告设计委托书。
环己烷氧化法制环己酮装置分解反应釜的工艺放大设计
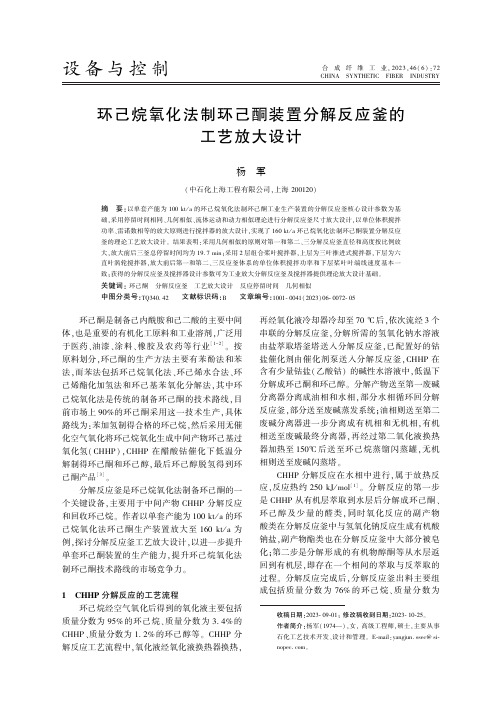
环己酮是制备己内酰胺和己二酸的主要中间
再经氧化液冷却器冷却至 70 ℃ 后,依次流经 3 个
。 按
由盐萃取塔釜塔送入分解反应釜,已配置好的钴
体,也是重要的有机化工原料和工业溶剂,广泛用
己烷氧化法环己酮生产装置放大至 160 kt / a 为
酸类在分解反应釜中与氢氧化钠反应生成有机酸
单套环己酮装置的生产能力,提升环己烷氧化法
化;第二步是分解形成的有机物醇酮等从水层返
例,探讨分解反应釜工艺放大设计,以进一步提升
钠盐,副产物酯类也在分解反应釜中大部分被皂
制环己酮技术路线的市场竞争力。
回到有机层,即存在一个相间的萃取与反萃取的
釜设计仍采用此搅拌器型式,以下层六直叶涡轮
搅拌器为主、上层三叶推进搅拌器为辅。
体现搅拌器混合传质效果的重要指标为 P d ,
体现流体运动和动力相似的重要指标为雷诺数
( Re) [6] ,因此本次放大设计采用 P d 不变的准则
对下层涡轮搅拌器的桨叶进行放大,见式(4) ; 采
用 Re 不变的准则对于上层推进式搅拌器的桨叶
0. 4
0. 7
3
2 CHHP 分解反应釜的关键设计参数
CHHP 分解反应釜的关键设计参数包括反应
小的液滴分散到主液相,若搅拌强度过低,则碱水
相在有机相中分散度低,分解反应在釜内进行不
彻底; 若搅拌强度过高,则碱水相液滴粒径太小,
在后续工序中难以从有机相中去除,影响装置运
行周期。 搅 拌 强 度 通 常 用 单 位 体 积 搅 拌 功 率
(7)
(8)
环己酮装置操作规程
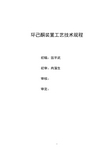
第二章 生产的基本原理、工艺条件、影响因素
一、基本原理 1、苯加氢 氢气和苯在一定的温度和压力下通过催化剂固定床层时, 被催化剂吸附的氢分子离解成氢原 子,并与吸附的苯分子发生加氢反应,生成环己烷,并放出大量热量。 C6H6+3H2 在 Ni3Al2O3, 0.7Mpa/130~180℃条件下 C6H12+216.5KJ/Kmol
反应为体积缩小的放热平衡反应,高压、低温有利于反应向右进行。 同时伴有副反应: C6H6+3H2 C5H9-CH3(甲基环戊烷)
2、环己烷氧化 液态环己烷与空气在 1350kpa 和 183℃~165℃条件下发生氧化反应,该反应的主要产物为环 己基过氧化氢(CHHP) 。 C6H11OOH 总反应方程式为:C6H12+O2
2、化学性质 1)分子式 C6H10O 2)结构式 =O 3)分子量:98.15 4)化学特性:环己酮的结构式中,具有羰基(>C=O) ,羰基中的碳氧双键由氧的 2p 轨道和 2 两原子的 2p 轨道侧面又重叠形成一个 π 键, 一起组成双键。 碳的 sp 杂化轨道重叠形成一个 σ 键, C=O 键能为 176—179 千卡/摩,比两个 C—O 键的键能(2×86 千卡/摩)还大,而酮分子的羰基 由于氧原子的电负性比碳原子大,故其有相当大的极性,对酮的某些化学性质起决定性作用,其 易与氢、氢氰酸,亚硫酸氢钠,格氏试剂,羟胺,苯胺等物质起加成反应,也能够自身发生羟醛 缩合反应。 3、用途 环己酮主要用于生产己内酰胺,也用于制造防老剂,树脂,溶剂,医药等。 4、质量标准 1)中华人民共和国标准(GB10669-89)
环己酮装置工艺技术规程
初稿:翁平武 初审:肖藻生 审核: 审定:
1
目
第一章 第二章 第三章 第四章 第五章 第六章 第七章 第八章 第九章 产品介绍
环己烷绿色催化氧化法生产环己酮项目可行性研究报告
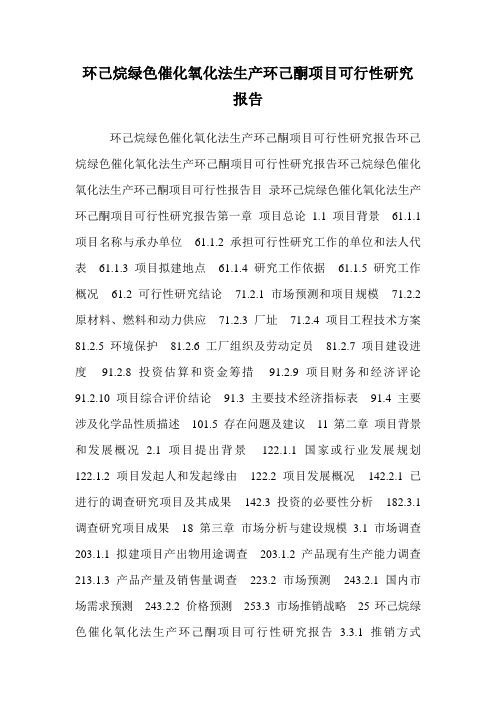
环己烷绿色催化氧化法生产环己酮项目可行性研究报告环己烷绿色催化氧化法生产环己酮项目可行性研究报告环己烷绿色催化氧化法生产环己酮项目可行性研究报告环己烷绿色催化氧化法生产环己酮项目可行性报告目录环己烷绿色催化氧化法生产环己酮项目可行性研究报告第一章项目总论 1.1 项目背景61.1.1 项目名称与承办单位61.1.2 承担可行性研究工作的单位和法人代表61.1.3 项目拟建地点61.1.4 研究工作依据61.1.5 研究工作概况61.2 可行性研究结论71.2.1 市场预测和项目规模71.2.2 原材料、燃料和动力供应71.2.3 厂址71.2.4 项目工程技术方案81.2.5 环境保护81.2.6 工厂组织及劳动定员81.2.7 项目建设进度91.2.8 投资估算和资金筹措91.2.9 项目财务和经济评论91.2.10 项目综合评价结论91.3 主要技术经济指标表91.4 主要涉及化学品性质描述101.5 存在问题及建议11第二章项目背景和发展概况 2.1 项目提出背景122.1.1 国家或行业发展规划122.1.2 项目发起人和发起缘由122.2 项目发展概况142.2.1 已进行的调查研究项目及其成果142.3 投资的必要性分析182.3.1 调查研究项目成果18第三章市场分析与建设规模 3.1 市场调查203.1.1 拟建项目产出物用途调查203.1.2 产品现有生产能力调查213.1.3 产品产量及销售量调查223.2 市场预测243.2.1 国内市场需求预测243.2.2 价格预测253.3 市场推销战略25环己烷绿色催化氧化法生产环己酮项目可行性研究报告 3.3.1 推销方式253.3.2 推销措施263.3.3 促销价格制度273.4 产品方案和建设规模283.4.1 产品方案283.4.2 建设规模283.5 产品销售收入预测28第四章建设条件与厂址选择 4.1 资源和原材料294.1.1 资源评述294.1.2 原材料及主要辅助材料供应294.2 厂址的选择324.2.1 自然条件324.2.2 基础设施344.2.3 社会经济条件344.3 总图布置及主要建筑物、设备概况35第五章工厂技术方案5.1 项目组成365.1.1 生产工序365.1.2 配套工程365.2 产品开发改进365.2.1 设计原则365.2.2 生产指标及工艺参数365.3 工艺流程385.3.1 催化剂生产原理385.3.2 生产环己酮主要流程简介385.3.3 环己酮氧化工序395.3.4 环己酮回收工序405.3.5 环己酮精馏工序405.4 总平面图405.4.1 总图布置原则405.4.2 总图布置及主要建筑物、设备概况415.5 运输及仓储415.5.1 物料运输415.5.2 仓储415.6 土建工程425.6.1 厂房建设425.6.2 工程预算425.7 给水排水425.8 供电系统425.9 其它供应43第六章环境保护与劳动安全环己烷绿色催化氧化法生产。
环己酮生产中萃取塔的模拟计算和改造
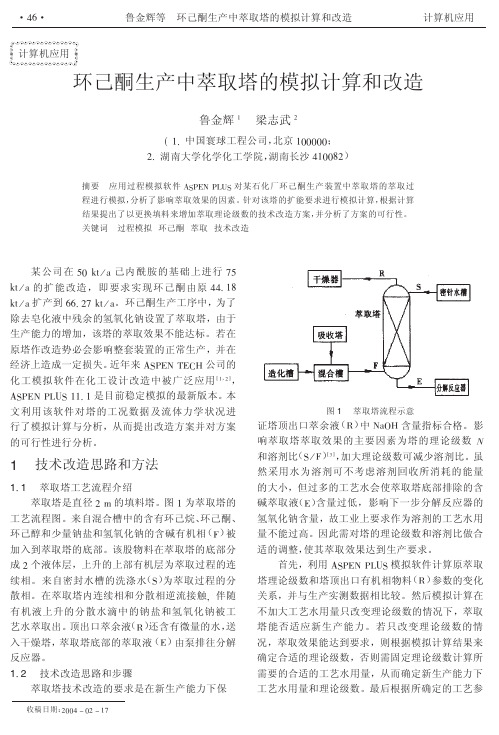
1. 1 萃取塔工艺流程介绍 萃取塔是直径 2 m 的填料塔。图 1 为萃取塔的
工艺流程图。来自混合槽中的含有环己烷、环己酮、 环己醇和少量钠盐和氢氧化钠的含碱有机相(F)被 加入到萃取塔的底部。该股物料在萃取塔的底部分 成 2 个液体层,上升的上部有机层为萃取过程的连 续相。来自密封水槽的洗涤水(S)为萃取过程的分 散相。在萃取塔内连续相和分散相逆流接触, 伴随 有机液上升的分散水滴中的钠盐和氢氧化钠被工 艺水萃取出。顶出口萃余液(R)还含有微量的水,送 入干燥塔,萃取塔底部的萃取液(E)由泵排往分解 反应器。 1. 2 技术改造思路和步骤
等活度计算公式,有所需的调节参数少、简便、关联
效果好等优点,适用于本文所述系统的液液平衡关
联。
In
fi = In
Фi xi
+
1
-
Фi xi
1 2
zq(i In
Фi θi
+
1
-
Фi )θi
A A qiIn(
K
θjтji)+ qi - qi
θj тij
K
j
A j = 1
θK тkj
k= 1
(1)
改变塔理论级数的模拟计算结果如表 1。
图 2 新生产能力下萃取塔理论级数与萃余液(R)中 NaOH 质量浓度的关系
从图 2 可以看出,在一定生产能力下,理论级数 越大,塔顶出口产物 R 中的碱质量浓度越小即萃取 效果越好,但是在级数较大(如超过 10)时级数变化 对 R 中 NaOH 的质量流量影响不再显著,曲线趋于 平缓。这说明在新生产能力下工艺水体积流量若保 持 3. 7 m3 / h,只有无限增加理论级数才能达到萃取 要求,这在实际中是不可行的,故必须加大工艺水用 量。
一种环己烷催化氧化制备环己醇和环己酮的方法

一种环己烷催化氧化制备环己醇和环己酮的
方法
这种方法是使用催化剂将环己烷氧化,并将其转化为环己醇和环
己酮。
具体步骤如下:
1. 准备催化剂:首先选择一种适合氧化反应的催化剂,例如铬酸、钨酸、钛酸等。
2. 加入催化剂:将催化剂加入环己烷反应体系中,催化剂浓度一
般在0.5%-10%之间。
3.氧化反应:在空气中或氧气中进行反应,在适当的温度(一般
在100°C-160°C)和反应时间(几小时到几十小时)下进行反应。
反应过程中,环己烷被氧化成环己醇和环己酮。
4. 分离纯化:反应结束后,需要对产物进行分离纯化,以得到高
纯度的环己醇和环己酮。
总之,这种方法利用了催化剂的作用,加速了环己烷的氧化反应,提高了反应的效率和产物的纯度,具有一定的实用价值。
- 1、下载文档前请自行甄别文档内容的完整性,平台不提供额外的编辑、内容补充、找答案等附加服务。
- 2、"仅部分预览"的文档,不可在线预览部分如存在完整性等问题,可反馈申请退款(可完整预览的文档不适用该条件!)。
- 3、如文档侵犯您的权益,请联系客服反馈,我们会尽快为您处理(人工客服工作时间:9:00-18:30)。
环己烷绿色催化氧化法生产环己酮年产10万吨环己酮精馏塔设计计算说明书环己烷绿色催化氧化法生产环己酮年产10万吨环己酮精馏塔设计计算说明书环己烷绿色催化氧化法生产环己酮环己酮精馏塔设计计算说明书项目名称环己烷绿色催化氧化法生产环己酮一设计方案确定………………………………………………………………………………………… 3 二已知物料条件………………………………………………………………………………………… 3 三实际塔板数计算…………………………………………………………………………………… 4 四塔径计算……………………………………………………………………………………………… 7 五塔体主要工艺结构计算………………………………………………………………………… 9 六塔板流体力学验算………………………………………………………………………………… 12 七塔板负荷性能图…………………………………………………………………………………… 13 八主要接管尺寸计算………………………………………………………………………………… 15 九除沫器设备设计……………………………………………………………………………………… 16 十塔总体结构强度核算……………………………………………………………………………… 16 十一设计结果概要…………………………………………………………………………………… 21 参考文献…………………………………………………………………………………………………… 22 一、设计方案确定(一)塔型:选择轻型浮阀塔浮阀塔兼有泡罩塔和筛板塔的优点:处理能力大,操作弹性大,塔板效率高,压强降小,液面梯度小,使用周期长,结构简单,便于安装,其制造费用为泡罩塔的60%~80%,但为筛板塔的120%~130%。
F1型浮阀塔结构简单,制造方便,节省材料,性能良好。
轻阀虽然操作稳定性较重阀差,但是其压降小,而精馏环己酮要求压力降很低。
综上所述,选择F1型轻阀浮阀塔。
(二)进料状态:泡点进料因为泡点进料会使塔的操作比较容易控制,不受季节气温影响。
环己酮混合原料经预热器加热到泡点后,送进精馏塔,塔顶上升的蒸汽采用全凝器冷凝后,一部分回流,其余出料得到塔顶产物。
(三)加热方式:间接蒸汽加热(四)操作压力:真空精馏在常压下,环己酮的沸点是155.7℃,环己醇的沸点是161.1℃,相差不大,需在真空下操作。
二、已知物料条件由物料衡算(详见《物料衡算》说明书),得到环己酮塔的物料条件如下:组分轻质油环己烷环己酮环己醇X油总量摩尔质量kg/kmol 84.8 86.16 98.15 100.16 176.92 进料平均摩尔质量kg/kmol 98.99 摩尔分数0.00023 0.0019 0.6369 0.3590 0.0019 1 摩尔流量kmol/h 0.052 0.443 144.460 81.428 0.433 226.816 塔顶产品平均摩尔质量kg/kmol 98.11 摩尔分数0.0004 0.0031 0.9945 0.002 - 1 摩尔流量kg/kmol 0.052 0.443 140.78 0.277 - 141.571 塔釜产品平均摩尔质量kg/kmol 100.46 摩尔分数- - 0.043 0.952 0.005 1 摩尔流量kmol/h - - 3.661 81.151 0.433 85.245 因为在环己酮的分离当中,主要的物料是环己酮和环己醇,而轻质油,环己烷和X 油的含量极少,采用清晰分割,以环己酮和环己醇为关键组分,其中环己酮是轻关键组分,环己醇重关键组分,比环己酮要轻的轻质油和环己烷全部从塔顶出来,而X油全部从塔釜出来。
关键组分中,以环己酮组分作为计算的依据。
(一) 摩尔分数:(二) 摩尔流量:总的摩尔流量: 分开两个塔后的摩尔流量:(三) 分子量:(四) 塔顶的压强: 根据气液平衡数据,要取得良好的分离效果,必须在高真空的条件下分离,由气液平衡效果,故取(五) 温度(查t-x-y图)塔顶:,塔釜:,进料:三、实际塔板数的计算(一) 理论塔板数的求取(图解法)1. 环己酮气液平衡数据作x-y图(数据来自《己内酰胺生产及应用》[8])由上述梯级图求得理论板数为18.5块(包括再沸器)2. 最小回流比从图上读得操作线与平衡线的交点坐标是(0.6369,0.7802)3. 精馏段方程取精馏段方程:4. 提馏段方程提馏段方程: (二) 全塔效率 1. 计算液体粘度查《石油化工基础数据手册》(文献[6] P626),《石油化工基础数据手册续篇》(文献[7] P704)得环己酮和环己醇的粘度如下: ()塔釜进料塔顶温度125 104 70 环己酮0.4855 0.572 0.954 环己醇0.532 0.903 4.89 在各温度下, 精馏段: 提馏段: 2. 计算平均相对挥发度由气液平衡数据可以得到塔顶、进料、塔釜的气液平衡数据如下:各组分摩尔分数环己酮环己醇yF 0.7802 0.2198 xf0.6369 0.3631 yB 0.0803 0.9197 xB 0.043 0.957 yD 0.9979 0.0021 xD 0.9945 0.0055 由得进料、塔顶、塔釜的相平衡常数为:环己酮环己醇1.2245 0.6062 1.003 0.4800 1.806 0.9638 在低压下,两者的相对挥发度可由算得:精馏段: 提馏段: 3. 计算全塔效率: 精馏段: 提馏段: (三) 实际塔板数实际塔板数:精馏段: 提馏段: 实际塔板数: 进料板是第24块。
四、塔径计算塔径D分别计算精馏段和提馏段的塔径。
精馏段以塔顶第1块板计算,提馏段以最后一块(第40块)计算。
1.平均分子量进料,塔顶,塔釜的平均分子量相差不大,故由平均值作为精馏段和提馏段的平均分子量. 精馏段: 提馏段:2.平均密度(1)液相密度环己酮和环己醇的不同温度下的液相密度(单位:kg/m3)温度70 80 90 100 110 120 130 环己醇910 901 892 883 873 863 854 环己酮904 985 885 875.5 869 860 850 塔顶:进料板: 塔釜:(2)气相密度:塔顶的压力为PD=0.0053MPa 进料板: 塔釜的压力经估算,设为PD=0.0226MPa 3.气液负荷计算塔顶: 塔釜: 4. 液体表面张力σm:环己酮和环己醇的不同温度下的液相表面张力如下,可见两者的液相表面张力变化不大. 液相表面张力(mN/m) 温度70 80 90 100 110 120 130 环己醇28.90 28.00 27.10 26.19 25.29 24.38 23.47 环己酮28.79 27.56 26.35 25.14 23.95 22.76 21.59 在塔顶温度70℃时, 塔顶: 塔釜: 5. 求空塔气速u u=(安全系数)×umax 塔顶:(1) (2)由于气体流速大,初选板间距HT是0.9m,板上液层厚度hL是0.04m HT-hL=0.9-0.04=0.86 m (3) 由史密斯(Smith)关联图,得(4)空塔气速取安全系数为0.6, 则塔釜:(1) (2)初选板间距HT 是0.6m,板上液层厚度hL是0.04m HT-hL=0.6-0.04=0.56 m (3) 查由史密斯(Smith)关联图,得(4)空塔气速取安全系数为0.6, 则6.塔径D 塔顶: 塔釜: 考虑到制作和操作方便,塔径大小取一致,故取塔顶完整后的塔径。
圆整,取塔径D=3.4m; 校正, 则塔的截面积是:五、塔体主要工艺结构计算由于真空精馏,从塔顶到塔釜,随着压力的增大,气相的密度变化大,对精馏塔分段进行工艺计算。
实际总板数为40块,每8块为一段,分成5段。
以每段的第一块板为基准。
以下的工艺计算是以塔顶第1块到第8块的工艺计算,以第1块为基准。
液相流量很小,尽管塔径比较大,仍然采用单溢流装置。
其它四段的计算方法不变,其计算过程略,具体结果见后面的“设计结果概要”。
(一)溢流装置:选用单溢流,弓形降液管,不设进口堰,平型受液盘以及平形溢流堰。
1.堰长lW 取堰长lW=0.628D=0.628×3.4=2.111m 2.出口堰高hW (1)液流收缩系数 E 查流体收缩系数计算图(Bolles,W.L.提出)得E=1.02 (2)堰上液层高度:(3)堰高:3.弓形降液管高度Wd及降液管面积Aa 取,故故4.验算液体在降液管中停留时间保留时间θ>(3-5)s,故降液管适用。
6. 降液管底隙高度ho 取液体通过降液管底隙的高度uo 为0.13m/s。
则,(二)塔板位置及浮阀数目与排列选用F1型轻阀。
1. 浮阀数通过阀孔时的动能因数:取,则每层塔板上的浮阀数为:2. 取边缘区宽度:取泡沫区宽度:3. 鼓泡区面积计算塔板上鼓泡区面积,即:4.浮阀排孔排列方式采用等腰三角形叉排,取孔心距同一排的阀孔中心矩t, 腰高:取腰高:t=65mm。
排得1148孔,如图所示:5. 验算气速及阀孔动能因数:阀孔动能因数变化不大,仍在9-12范围之内。
六、塔板流体力学验算(一) 气相通过浮阀塔板的压强降1. 干板阻力2. 板上充气液层阻力:由于环己酮混合原料里,液相是有机物油,故取εo=0.2 3. 液体表面张力所造成的阻力: 浮阀塔的hσ值通常很小,计算时忽略不计。
4. 单板压降(二) 液泛1.计算降液管内清液层高度(1) 与上升气体通过一层塔板的压强降所相当的液柱高度,m液柱hp=0.05157m。
(2) 液体流过降液管的压强降相当的液柱高度,m液柱(3) 板上液层高度:(4) 2.验算取Φ=0.5 则Φ(hw+HT)=0.5×(0.027+0.9)=0.4634m Hd (三) 雾沫夹带或者1. 泛点负荷系数CF 由于ρG,D=0.1832kg/m3, 查图(《化工原理》下册P160 ,文献[4])得CF=0.127 2. 物性系数K 环己酮混合物是正常系统,K=1。
3. 板上液流面积4. 板上液体流径长度5.泛点率因为55.73% 对于减压塔,泛点率应该小于75%。
符合要求,可保证雾沫夹带量达到标准的指标,即。
七、塔板负荷性能图1. 雾沫夹带线对于一定的物系,及一定的塔板结构,式子ρV,ρL,Ab,K,CF及ZL均为已知值,相应于ρV=0.1的泛点率上限值亦可确定,将各已知数代入上式,使得到Vs-Ls的关系式,据此可作出负荷性能图中的雾沫夹带线。
按泛点率=75%计算整理得到雾沫夹带线的方程:2. 液泛线因为物系一定,塔板结构尺寸一定,则HT,hw,ho,lw,ρV,ρL,及Φ等均为定值,而uo,Vs有如下关系,即:整理可以得到液泛线的方程:3. 液相负荷上限线液体最大流量应保证在降液管中停留时间不低于3~5s,则液体在降液管内停留时间为:求出上限液体流量Ls值(常数),在Vs-Ls图上,液相负荷上限线为与气体流量Vs无关的竖直线。