设计失效模式及后果分析(DFMEA)
FMEA失效模式后果分析

• 介绍 • FMEA失效模式分析 • 后果分析 • 风险优先级排序 • 改进措施和预防措施 • 案例分析
01
介绍
FMEA的定义
FMEA(Failure Modes and Effects Analysis)即失效模式和影响分析,是一种预 防性的质量工具,用于评估产品设计或流程中潜在的失效模式及其对系统性能的影 响。
失效模式是指产品或过程中可能发生的故障、异常或性能下降的情况。根据不同的分类标准,失效模式可以分为 不同的类型。
详细描述
失效模式是指产品或过程中可能发生的故障、异常或性能下降的情况。根据产品或过程的性质和用途,失效模式 可以分为机械、电气、化学、热等多种类型。同时,根据失效的严重程度和影响范围,失效模式可以分为致命、 严重、一般和轻微等不同级别。
风险优先级排序的方法和步骤
步骤
风险优先级排序通常包括以下步骤
1. 识别潜在失效模式
分析产品或过程中可能出现的各种失效模式。
2. 评估失效模式的影响
评估每种失效模式对产品或过程性能的影响程度,包括安全性、可 靠性、有效性等方面的影响。
风险优先级排序的方法和步骤
3. 评估失效模式的概率和可检测性
01
应用实例2
医疗器械FMEA分析中,对潜在的失效模式如设备故障、误操作等进行风险评估,制定相应的风险管 理计划,确保产品的安全性和可靠性。
05
改进措施和预防措施
改进措施的定义和分类
定义
改进措施是指针对已经发生的失效模式,采 取的修复、补偿或纠正措施,以降低或消除 失效模式对产品或过程的影响。
分类Βιβλιοθήκη 改进措施可以分为临时性措施和永久性措施。 临时性措施通常用于快速解决问题,而永久 性措施则用于长期解决失效模式。
DFMEA(设计失效模式与效应分析)-20121123

※ RPN(風險順序數):計算並記錄糾正後的RPN值的結果。
14
設計FMEA分析步驟
15
設計FMEA嚴重度評估標準
16
設計FMEA發生率評估標準
17
設計FMEA難檢度評估標準
18
設計FMEA改善對策提出時機
The timing to provide solution / 提出改善對策之時機
以利追蹤
※ Planning Stage(設計階段):填上依據目前所進行分析標的物所處之開發階段 ※ Design Responsibility (設計責任):填入負責的設計與開發之工程師全名
※ Prepared By(編制者):填入負責編制DFMEA的工程師的姓名
※ Part Name/Program(系統、子系統或零部件的名稱及編號):填入適當的分析級別並
12
設計FMEA分析表說明(Ⅲ)
※ POTENTIAL CAUSE(S) / MECHANISM(S) OF FAILURE(失效的潛在原因或機理) :填入每一
個失效模式的所有可以想到的失效原因或失效機理。
※ DESIGN CONTROLS(現行設計管制):填入已經完成或承諾要完成的預防措施、設計確認
DFMEA(設計失效模式與效應分析)
Design Failure Mode and Effect Analysis
1
什麽是FMEA ?
※
FMEA是一種系統方法,使用制式表格及問題解決
方法以確認潛在失效模式及其效應,並評估其嚴重度、 發生度、難檢度(探測/偵測)及目前管制方法,從而計算
風險優先指數(RPN),最後採取進一步改善方法,如此
持續進行,以達防患失效模式及效應發生於未然
FMEA失效分析与失效模式分析 (2)全
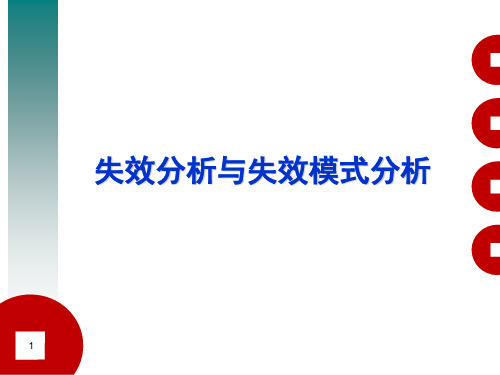
23
失效分析的要点?之三
在一级失效原因正确的基础上,探讨和分析二级失效原 因。例如设计原因引起的失效还可细分为设计思想、结 构、对载荷分析的准确性、选材等二级失效原因。
3.机理清楚
失效机理是指失效的物理、化学变化本质,微观过程可 以追溯到原子、分子尺度和结构的变化,但与此相对的 是它迟早也要表现出一系列宏观(外在的)的性能、性 质变化。
16
什么是失效分析?
失效分析:考察失效的构件及失效的情景(模式), 以确定失效的原因。
失效分析的目的:在于明确失效的机理与原因。改 进设计、改进工艺过程、正确地使用维护。
失效分析的主要内容:包括明确分析对象,确定失 效模式,研究失效机理,判定失效原因,提出预防 措施(包括设计改进)。
17
失效分析的要点?
24
失效分析的要点?之四
通常可将失效原因分为内因和外因。失效机理即失效的 内因,它是导致发生失效零件或材料的物理、化学或机 械损伤过程等。
4.措施得力,模拟再现,举一反三
措施得力,模拟再现,举一反三是建立在前面对失效模 式、失效原因和失效机理深入分析和准确把握的基础上。 当然制定预防措施需考虑长远的措施和产品使用问题以 及工程上的可行性、经济性等。模拟再现则要分析模拟 的可能性和必要性。同时,随着计算机技术的高速发展, 计算机模拟也成为模拟再现的一个重要手段。
故障原因:直接导致故障或引起性能降低并进一步发展成 故障的那些物理或化学过程、设计缺陷、工艺缺陷、零件 使用不当和其它过程等因素。
故障(失效)机理:引起故障(失效)的物理、化学和生 物等变化的内在原因。
FMEA方法的根本目的
按规定的规则记录产品设计中所有可能的故障模式; 分析每种故障模式对系统的工作及状态(包括战备状态、
潜在失效模式和后果分析FMEA

(18)现
频 度
行控制
车
车门 寿命
7
门 降低
内 导致:
板
-因 漆面
7
下
生锈, 使用
部 户不
腐 蚀
满意
-使 车门
7
内附
件功 能降
7
低
7
车门内板保 护蜡上限太 低
6
整车耐久性试 验 T-118 T-
109 T-301
蜡层 厚度 规定 不足
4 整车耐久 性试验T118 T109T301
蜡的配 方不当
混入的 空气阻 止蜡进 入边脚 部分
潜在失效模式和后果分析FMEA
潜在失效模式和后果分析:Failure Mode and Effects Analysis
FEMA是一组系统化的工作,其目的是: 发现、评价产品/工程中潜在的失效及后果; 找到能够避免或减少这些潜在失效的措施; 将以上过程文件化,作为过程控制计划的输入; FEMA的发展史 FEMA起源于60年代航天航空工业项目。 1974年美军海军首先将它用于军事项目合约。 1970年,汽车工业将FMEA作为在对其零件设计和生产
设计失效模式和后果分析DFMEA
* 分析对象:以系统、子系统或零部件为分析对象;
* 典型的设计失效模式有:裂纹、变形、松动、泄露、短路(电器)、 氧化、粘结、断裂等,应使用规范的专业术语;
* 典型的失效模式后果有:噪声、工作不正常、不良外观、不稳定、 运行中断、粗糙、不起作用、异味、工作减弱等,是下一道工序或客 户的感受;
2
极低:失效不大可能发生,几乎完全 相同的过程也未有过失效
≤1/1500000
≥1.67
1
探测度评价准则
探测性 几乎不可能
失效模式影响及危害性分析(FMEACA)
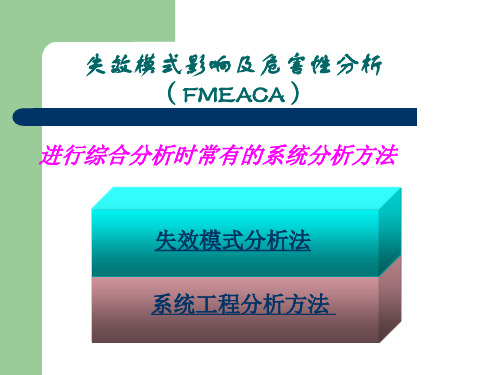
1
结果事件
2
底事件
是基本故障事件(不能再进行分解)或毋须再探明的 事件,但一般它的故障分布是已知的,是导致其他事 件发生的原因事件,位于故障树的底端,是逻辑门的 输入事件而不是作为输出 又称为展开事件或未探明事件。发生的概率小,因此 对此系统来说不需要进一步分析的事件;或暂时不必 或暂时不可能探明其原因的底事件
第七节 故障树分析(FTA)
汽车双管路制动系统故障树:
第七节 故障树分析(FTA)
3.故障树的分析
故障树定性分析 故障树定量分析
第七节 故障树分析(FTA)
故障树的定性分析
主要任务
找出故障树的全部最小割集或全部最小路集。
原则
①比较小概率失效元件组成的各种系统失效概率时,其故障树所含最小割集 的最小阶数越小,系统的失效概率越高;在所含最小割集的最小阶数相同的 情况下,该阶数的最小割集的个数越多,系统的失效概率越高。 ②比较同一系统中各基本事件的重要性时,按各基本事件在不同阶数的最小 割集中出现的次数来确定其重要性大小;所在最小割集的阶数越小,出现的 次数越多,该基本事件的重要性越大。
失效模式影响及危害性分析 (FMEACA)
主要特点: 易懂 只能分析硬件
时间花费长
通常不考虑失效与人为因素的关 系
进行FMEA分析的优点
确保所有的风险提前识别并采取相应的措施 确保产品和优化后的措施的基本原理和有线等级 减少废料、返工和制造成本 减少外厂故障、降低保修成本 减少“召回”的发生概率
失效模式影响及危害性分析 (FMEACA)
第七节 故障树分析(FTA)
收集各故障发生的概率数据;
选定系统可能发生的最不希望发生的故障状态作为顶事件,画逻 辑图;
失效模式与后果分析(新版FMEA)

失效模式与后果分析(新版FMEA)●课程特色用客户的产品为案例,学员以小组的方式,学习界限图、接触矩阵图、P图、DRBFM为DFMEA奠定基础;学习过程流程图、特性矩阵图、过程变差识别和过程参数控制,为PFMEA奠定基础;掌握新版FMEA 的更新内容和要求;帮助学员学会真正将FMEA作为工程师必需掌握的设计工具。
●课程目标n 掌握新版FMEA(第四版)的更新的内容和要求n 理解失效模式和后果分析(FMEA)概念、信息流、步骤和方法;n 通过界限图,正确界定FMEA的范围;n 应用接触矩阵图,分析零件与零件之间在物体、能量、信息、物质形态方面的交互作用;n 建立P图,分析产品的错误状态,揭露导致产品不可靠的原因;n 通过过程流程图,建立产品特性和过程参数的对应关系;n 具备运用FMEA、过程控制计划等工具,提高产品和过程的可靠性;n 理解FMEA与其他任务和工具之间的关系。
n 掌握FMEA和其它文件之间的相互关联●课程大纲课程名称:失效模式与后果分析(新版FMEA)开课地点:广州市黄埔区黄埔东路2926号万好万家A座302室培训对象:质保部经理,设计工程师、制造工程师和其他直接负责过程标准化和改进的人员,那些直接负责引进新产品或新制造过程的人员。
培训目标:n 掌握新版FMEA(第四版)的更新的内容和要求n 理解失效模式和后果分析(FMEA)概念、信息流、步骤和方法;n 通过界限图,正确界定FMEA的范围;n 应用接触矩阵图,分析零件与零件之间在物体、能量、信息、物质形态方面的交互作用;n 建立P图,分析产品的错误状态,揭露导致产品不可靠的原因;n 通过过程流程图,建立产品特性和过程参数的对应关系;n 具备运用FMEA、过程控制计划等工具,提高产品和过程的可靠性;n 理解FMEA与其他任务和工具之间的关系。
n 掌握FMEA和其它文件之间的相互关联课程内容简介:三天课程结合美国奥曼克丰富的实际案例,系统地讲解新版FMEA(第四版)的内容、要求、信息流、实施步骤和方法;包括DFMEA, DVP&R, 应用界限图、接触矩阵图、P图、设计矩阵表、DRBFM(基于失效模式的设计评估)、过程流程图、PFMEA、控制计划等工具,帮助学员了解通过实施FMEA 的过程,掌握产品特性内部、产品特性与过程特性、DFMEA和PFMEA、DFMEA与DVP&R、流程图和PFMEA、PFMEA和控制计划以及系统、子系统、部件、零件之间的相互关联,解决产品设计和过程设计可能出现的问题,在产品实现过程的前期确保失效模式得到考虑并实现失效的控制和预防。
失效模式与影响分析(FMEA)

可能给错药 药物名称或外表 厂商制造原 造成病人伤 相似 因 害
1
1
10
10
三、举例
4.分析失效模型和影响因素 表4.3 护士到病人单位给药 失效模式 原因 结果 S 1.护士太 可能给错 护士没有核对 匆忙。2. 药造成病 10 病人身份 病人没有 人伤害 识别手圈 1.无法识 给药途径 药物给药途径 别医嘱。 错误造成 10 错误 2.缺乏相 影响结果 关知识。
护士对药 卡 到备药间 备药 到病人病 房给药
三、举例
4.分析失效模型和影响因素
4.1 护士给药 表4.1护士核对给药纪录单
失效模式 结果 S 没有依照处 1.医嘱遗失。 给药记录单没有 方给药可能 10 2.书写医嘱 更新 影响病人结 时分心 果 1.书写医嘱 时不注意。 没有依照处 2.写后的医 方给药可能 给药时间不正确 嘱没有双重 10 影响病人结 核对。3.没 果 有计算机处 方系统 原因 O 5 D 5 RPN 改善措施 250
O
D RPN 改善措施
1.加强培 训。2.病 10 人佩戴手 圈
1
1
5
5
250
三、举例
5. 评判结果 失效模式 给药记录单没有更新 RPN 250
给药时间不正确 药物不正确 药物名称或外表相似
护士没有核对病人身份
250 250 10
10
药物给药途径错误
250
三、举例
6.根本原因分析 6.1列出最需要改善的失效模式: 给药记录单没有更新、给药时间不正确、药物不 正确、药物给错途径 6.2 对相应失效模式分析原因。
三、举例
3. 分析流程 主题1:病人辨识和输血流程:
制作及佩 戴手圈 采血和 备血 检验科 流程 送血到 病房 核对 病人
失效模式及影响分析

失效模式及影响分析失效模式及影响分析(Failure mode and effects analysis,简称FMEA)是一种用于系统故障预防和可靠性改进的方法。
通过对系统的各个组成部分及其可能的失效模式和影响进行分析,能够帮助识别和消除潜在的故障点,提高系统的可靠性和安全性。
失效模式(Failure mode)是指系统、产品或组件在正常条件下未能按预期执行其功能或要求的方式,即失效的特定表现形式。
常见的失效模式包括:停止工作、性能下降、产生误差、漏水/泄露、短路、断裂等。
影响(Effects)是指失效模式对系统、用户、环境或企业造成的潜在危害或负面影响。
影响的级别可以从事故、严重故障、中度故障、轻微故障、降低可靠性等方面来评估。
FMEA通过对失效模式和其影响进行分析,可以进行以下几个方面的评估:1. 严重性评估(Severity Evaluation):根据失效模式对系统、用户或环境的影响程度,评估其严重性级别。
将影响分为高、中、低等级,并确定具体的损失程度。
2. 发生频率评估(Occurrence Evaluation):根据失效模式发生的概率或频率,评估其出现的可能性。
通过对设备或系统历史数据的统计分析,可确定每年失效次数或概率。
3. 检测能力评估(Detection Evaluation):根据可用的检测手段和方法,评估对失效模式的检测能力。
检测能力可以通过验证和验证手段的准确性和可靠性来评估。
通过对这三个因素进行综合评价,可以计算出风险优先数(Risk Priority Number, RPN)。
RPN是一个综合评估指标,用于确定优先改进的失效模式。
FMEA的主要目的是帮助预防失效,减少系统故障,并且在设计或改进产品或过程时识别并降低风险。
通过FMEA分析,可以及早发现和解决潜在问题,提高系统可靠性,减少维修和停机时间,降低成本和提高用户满意度。
FMEA可以应用于各个领域,如制造业、软件开发、航空航天等。
- 1、下载文档前请自行甄别文档内容的完整性,平台不提供额外的编辑、内容补充、找答案等附加服务。
- 2、"仅部分预览"的文档,不可在线预览部分如存在完整性等问题,可反馈申请退款(可完整预览的文档不适用该条件!)。
- 3、如文档侵犯您的权益,请联系客服反馈,我们会尽快为您处理(人工客服工作时间:9:00-18:30)。
(设计FMEA)X 系统FEMA编号:A11-3510010AC001 子系统页码:第 1 页共37 页零部件A11-3510010AC 设计责任:技质部编制者:王勇——技质部车型年/车辆类型:A11奇瑞关键日期:2002.02.14FMEA日期:2002.02.14(设计FMEA)X 系统FEMA编号:A11-3510010AC002 子系统页码:第 2 页共37 页零部件:A11-3510010AC 设计责任:技质部编制者:王勇——技质部车型年/车辆类型:A11奇瑞关键日期:2002.02.14FMEA日期:2002.02.14潜在失效模式及后果分析(设计FMEA)X 系统FEMA编号:A11-3510010AC003 子系统页码:第 3 页共37 页零部件:A11-3510010AC 设计责任:技质部编制者:王勇——技质部车型年/车辆类型:A11奇瑞关键日期:2002.02.14FEMA日期:2002.02.14在失效模式及后果分析(设计FMEA)X 系统FEMA编号:A11-3510010AC003 子系统页码:第 4 页共37 页零部件:A11-3510010AC 设计责任:技质部编制者:王勇——技质部车型年/车辆类型:A11奇瑞关键日期:2002.02.14FEMA日期:2002.02.14潜在失效模式及后果分析(设计FMEA)X 系统FEMA编号:A11-3510010AC004 子系统页码:第 5 页共37 页零部件:A11-3510010AC 设计责任:技质部编制者:王勇——技质部车型年/车辆类型:A11奇瑞关键日期:2002.02.14FEMA日期:2002.02.14(设计FMEA)X 系统FEMA编号:A11-3510010AC004 子系统页码:第 5 页共37 页零部件:A11-3510010AC 设计责任:技质部编制者:王勇——技质部车型年/车辆类型:A11奇瑞关键日期:2002.02.14FEMA日期:2002.02.14核心小组:张平、王国强——厂务部/王勇、王小龙、夏根生、王玮、张延云——技质部(设计FMEA)X 系统FEMA编号:A11-3510010AC005 子系统页码:第7 页共37 页零部件:A11-3510010AC 设计责任:技质部编制者:王勇——技质部车型年/车辆类型:A11奇瑞关键日期:2002.02.14FEMA日期:2002.02.14(设计FMEA)X 系统FEMA编号:A11-3510010AC005 子系统页码:第8 页共37 页零部件:A11-3510010AC 设计责任:技质部编制者:王勇——技质部车型年/车辆类型:A11奇瑞关键日期:2002.02.14FEMA日期:2002.02.14(设计FMEA)X 系统FEMA编号:A11-3510010AC006 子系统页码:第9 页共37 页零部件:A11-3510010AC 设计责任:技质部编制者:王勇——技质部车型年/车辆类型:A11奇瑞关键日期:2002.02.14FEMA日期:2002.02.14(设计FMEA)X 系统FEMA编号:A11-3510010AC006 子系统页码:第10 页共37 页零部件:A11-3510010AC 设计责任:技质部编制者:王勇——技质部车型年/车辆类型:A11奇瑞关键日期:2002.02.14FEMA日期:2002.02.14潜在失效模式及后果分析(设计FMEA)X 系统FMEA编号:A11-3510010AC006 子系统第11 页共37 页零部件:A11-3510010AC 设计责任:技质部编制者:王勇—技质部车型年/车辆类型:A11-奇瑞关键日期:2002.02.14 FMEA日期:2002.02.14潜在失效模式及后果分析(设计FMEA)X 系统FMEA编号:A11-3510010AC006 子系统第12 页共37 页零部件:A11-3510010AC 设计责任:技质部编制者:王勇—技质部车型年/车辆类型:A11-奇瑞关键日期:2002年2月14日FMEA日期:2002年2月14日潜在失效模式及后果分析(设计FMEA)X 系统FMEA编号:A11-3510010AC 子系统第13 页共37 页零部件:A11-3510010AC 设计责任:技质部编制者:王勇—技质部车型年/车辆类型:A11-奇瑞关键日期:2002年2月14日FMEA日期:2002年2月14日潜在失效模式及后果分析(设计FMEA)X 系统FMEA编号:A11-3510010AC007 子系统第14 页共37 页零部件:A11-3510010AC 设计责任:技质部编制者:王勇—技质部车型年/车辆类型:A11-奇瑞关键日期:2002年2月14日FMEA日期:2002年2月14日潜在失效模式及后果分析(设计FMEA)X 系统FMEA编号:A11-3510010AC007 子系统第15 页共37 页零部件:A11-3510010AC 设计责任:技质部编制者:王勇—技质部车型年/车辆类型:A11-奇瑞关键日期:2002年2月14日FMEA日期:2002年2月14日潜在失效模式及后果分析(设计FMEA)X 系统FMEA编号:A11-3510010AC008 子系统第16 页共37 页零部件:A11-3510010AC 设计责任:技质部编制者:王勇—技质部车型年/车辆类型:A11-奇瑞关键日期:2002年2月14日FMEA日期:2002年2月14日潜在失效模式及后果分析(设计FMEA)X 系统FMEA编号:A11-3510010AC008 子系统第17 页共37 页零部件:A11-3510010AC 设计责任:技质部编制者:王勇—技质部车型年/车辆类型:A11-奇瑞关键日期:2002年2月14日FMEA日期:2002年2月14日潜在失效模式及后果分析(设计FMEA)X 系统FMEA编号:A11-3510010AC008 子系统第18 页共37 页零部件:A11-3510010AC 设计责任:技质部编制者:王勇—技质部车型年/车辆类型:A11-奇瑞关键日期:2002年2月14日FMEA日期:2002年2月14日潜在失效模式及后果分析(设计FMEA)X 系统FMEA编号:A11-3510010AC008 子系统第19 页共37 页零部件:A11-3510010AC 设计责任:技质部编制者:王勇—技质部车型年/车辆类型:A11-奇瑞关键日期:2002年2月14日FMEA日期:2002年2月14日潜在失效模式及后果分析(设计FMEA)X 系统FMEA编号:A11-3510010AC008 子系统第20 页共37 页零部件:A11-3510010AC 设计责任:技质部编制者:王勇—技质部车型年/车辆类型:A11-奇瑞关键日期:2002年2月14日FMEA日期:2002年2月14日潜在失效模式及后果分析(设计FMEA)X 系统FMEA编号:A11-3510010AC009 子系统第21 页共37 页零部件:A11-3510010AC 设计责任:技质部编制者:王勇—技质部车型年/车辆类型:A11-奇瑞关键日期:2002年2月14日FMEA日期:2002年2月14日潜在失效模式及后果分析(设计FMEA)X 系统FMEA编号:A11-3510010AC009 子系统第22 页共37 页零部件:A11-3510010AC 设计责任:技质部编制者:王勇—技质部车型年/车辆类型:A11-奇瑞关键日期:2002年月14日FMEA日期:2002年2月14日潜在失效模式及后果分析(设计FMEA)X 系统FMEA编号:A11-3510010AC009 子系统第23 页共37 页零部件:A11-3510010AC 设计责任:技质部编制者:王勇—技质部车型年/车辆类型:A11-奇瑞关键日期:2002年2月14日FMEA日期:2002年2月14日潜在失效模式及后果分析(设计FMEA)X 系统FMEA编号:A11-3510010AC009 子系统第24 页共37 页零部件:A11-3510010AC 设计责任:技质部编制者:王勇—技质部车型年/车辆类型:A11-奇瑞关键日期:2002年2月14日FMEA日期:2002年2月14日潜在失效模式及后果分析(设计FMEA)X 系统FMEA编号:A11-3510010AC009 子系统第25 页共37 页零部件:A11-3510010AC 设计责任:技质部编制者:王勇—技质部车型年/车辆类型:A11-奇瑞关键日期:2002年2月14日FMEA日期:2002年2月14日潜在失效模式及后果分析(设计FMEA)X 系统FMEA编号:A11-3510010AC009 子系统第26 页共37 页零部件:A11-3510010AC 设计责任:技质部编制者:王勇—技质部车型年/车辆类型:A11-奇瑞关键日期:2002年2月14日FMEA日期:2002年2月14日潜在失效模式及后果分析(设计FMEA)X 系统FMEA编号:A11-3510010AC009 子系统第27 页共37 页零部件:A11-3510010AC 设计责任:技质部编制者:王勇—技质部车型年/车辆类型:A11-奇瑞关键日期:2002年2月14日FMEA日期:2002年2月14日潜在失效模式及后果分析(设计FMEA)X 系统FMEA编号:A11-3510010AC010 子系统第28 页共37 页零部件:A11-3510010AC 设计责任:技质部编制者:王勇—技质部车型年/车辆类型:A11-奇瑞关键日期:2002年2月14日FMEA日期:2002年2月14日潜在失效模式及后果分析(设计FMEA)X 系统FMEA编号:A11-3510010AC011 子系统第29 页共37 页零部件:A11-3510010AC 设计责任:技质部编制者:王勇—技质部车型年/车辆类型:A11-奇瑞关键日期:2002年2月14日FMEA日期:2002年2月14日潜在失效模式及后果分析(设计FMEA)X 系统FMEA编号:A11-3510010AC012 子系统第30 页共37 页零部件:A11-3510010AC 设计责任:技质部编制者:王勇—技质部车型年/车辆类型:A11-奇瑞关键日期:2002年2月14日FMEA日期:2002年2月14日潜在失效模式及后果分析(设计FMEA)X 系统FMEA编号:A11-3510010AC013 子系统第31 页共37 页零部件:A11-3510010AC 设计责任:技质部编制者:王勇—技质部车型年/车辆类型:A11-奇瑞关键日期:2002年2月14日FMEA日期:2002年2月14日潜在失效模式及后果分析(设计FMEA)X 系统FMEA编号:A11-3510010AC013 子系统第32 页共37 页零部件:A11-3510010AC 设计责任:技质部编制者:王勇—技质部车型年/车辆类型:A11-奇瑞关键日期:2002年2月14日FMEA日期:2002年2月14日潜在失效模式及后果分析(设计FMEA)X 系统FMEA编号:A11-3510010AC013 子系统第33 页共37 页零部件:A11-3510010AC 设计责任:技质部编制者:王勇—技质部车型年/车辆类型:A11-奇瑞关键日期:2002年2月14日FMEA日期:2002年2月14日潜在失效模式及后果分析(设计FMEA)X 系统FMEA编号:A11-3510010AC013 子系统第34 页共37 页零部件:A11-3510010AC 设计责任:技质部编制者:王勇—技质部车型年/车辆类型:A11-奇瑞关键日期:2002年2月14日FMEA日期:2002年2月14日潜在失效模式及后果分析(设计FMEA)X 系统FMEA编号:A11-3510010AC013 子系统第35 页共37 页零部件:A11-3510010AC 设计责任:技质部编制者:王勇—技质部车型年/车辆类型:A11-奇瑞关键日期:2002年2月14日FMEA日期:2002年2月14日潜在失效模式及后果分析(设计FMEA)X 系统FMEA编号:A11-3510010AC014 子系统第36 页共37 页零部件:A11-3510010AC 设计责任:技质部编制者:王勇—技质部车型年/车辆类型:A11-奇瑞关键日期:2002年2月14日FMEA日期:2002年2月14日潜在失效模式及后果分析(设计FMEA)X 系统FMEA编号:A11-3510010AC015 子系统第37 页共37 页零部件:A11-3510010AC 设计责任:技质部编制者:王勇—技质部车型年/车辆类型:A11-奇瑞关键日期:2002年2月14日FMEA日期:2002年2月14日芜湖华亨汽车部件有限公司A11-3510010AC真空助力器带主缸总成DFMEA顾客名称:上汽奇瑞公司产品名称:真空助力器带主缸总成件号:A11-3510010AC编制部门:技术部门编制人/日期:夏根生/2002.02.14 审核人/日期:王小龙/2002.02.14。