表面粗糙度的控制
改善机械零件加工表面粗糙度的方法

在机械零件加工行业,工件表面粗糙度也称光洁度,一般精密加工件的表面粗糙度要求比较高,在机械零件加工过程中,以下5种方法可以控制机械零件加工表面粗糙度,快来看看吧!
1.切削加工用量:是指可以在切削进给量上,可适当减少表面加工量。
2.选用刀具几何参数:从加工刀具几何参数上,可适当减小副偏角和增大刀尖圆弧半径,必要时可磨出修光刃。
使切削加工容易,降低表面粗糙度。
3.控制机床振动:可从减小刀具与工件间的摩擦、挤压上着手,使刀具刃磨得锋利,加注切削液和对某些韧性好的工件材料进行适当的热处理等。
4.选择合理的加工工艺:对精密机械零件加工过程中,加工工艺流程也非常重要,如工艺流程不合理可能会影响加工品质与生产效率。
很多精密加工件需要粗加工后精加工完成光洁度要求。
5.原材料选择不同:机械设备零配件上,由很多不同原材料加工组成,根据原材料密度不同,加工过程中刀具与机床选用直接关联到表面粗糙度。
以上就是5种改善机械零件加工表面粗糙度的方法,,希望能够帮助到大家!。
铣削加工中的表面粗糙度控制

铣削加工中的表面粗糙度控制铣削加工是机械加工中常见的一种加工方式,也是比较复杂的加工方式之一。
表面粗糙度是一个表面质量的重要指标,这也是我们在进行铣削加工时需要考虑的一种参数。
表面粗糙度的好坏会直接影响零件的性能以及寿命,因此,控制表面粗糙度成为了铣削加工的重要问题之一。
一、表面粗糙度的定义表面粗糙度指的是表面上凸起和凹陷部分的高低峰差,常见的定义为单峰高度Ra。
Ra值越小,表明表面越光滑,越接近完美的理论表面。
这个参数对于零件的加工质量和性能有着非常重要的影响,所以在机械加工中,控制表面粗糙度是非常关键的。
二、影响表面粗糙度的因素1. 铣削条件铣削条件直接影响到表面粗糙度的好坏。
不同的铣削条件,其效果也会有很大的区别。
比如,切削速度、进给速度和切削深度等参数的不同,都会对表面粗糙度产生影响。
2. 刀具的材料和刃口状态刀具的材料和刃口状态也是影响表面粗糙度的因素之一。
材料的不同会直接影响到刀具的硬度和耐磨性,同时也会对表面粗糙度产生影响。
而刃口的状态则直接影响到铣削时的切削效果,当刃口磨损严重时,其切削效果会变得越来越差,从而影响到表面的质量。
3. 工件材料工件材料是影响表面粗糙度的另一个重要因素。
不同材料的性质和硬度不同,其表面粗糙度的要求也会有所不同。
比如,对于轴承这样的零件来说,表面粗糙度的要求就必须很高,否则就会影响到轴承的使用寿命和性能。
三、表面粗糙度的控制方法1. 提高铣削精度提高铣削精度也是控制表面粗糙度的关键之一。
精度越高,铣削出来的表面就越光滑,表面粗糙度也会变得更低。
2. 选择适合的刀具选择适合的刀具也是控制表面粗糙度的重要方法之一。
刀具的材料、刃口状态等都会对表面粗糙度产生影响,因此选择合适的刀具非常关键。
3. 控制铣削条件控制铣削条件同样也是控制表面粗糙度的重要方法之一。
切削速度、进给速度和切削深度等都会对表面粗糙度产生影响,因此这些参数的控制非常关键。
4. 选择合适的工艺除了选择适合的刀具和铣削条件外,选择合适的工艺同样也是非常重要的。
喷砂机工艺控制中的表面粗糙度控制技巧
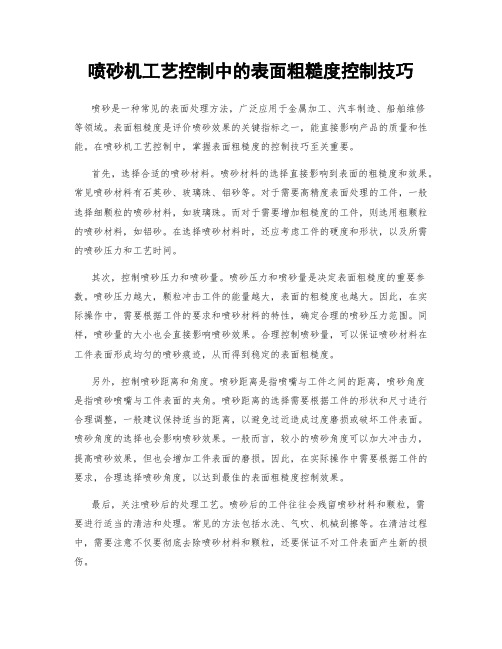
喷砂机工艺控制中的表面粗糙度控制技巧喷砂是一种常见的表面处理方法,广泛应用于金属加工、汽车制造、船舶维修等领域。
表面粗糙度是评价喷砂效果的关键指标之一,能直接影响产品的质量和性能。
在喷砂机工艺控制中,掌握表面粗糙度的控制技巧至关重要。
首先,选择合适的喷砂材料。
喷砂材料的选择直接影响到表面的粗糙度和效果。
常见喷砂材料有石英砂、玻璃珠、铝砂等。
对于需要高精度表面处理的工件,一般选择细颗粒的喷砂材料,如玻璃珠。
而对于需要增加粗糙度的工件,则选用粗颗粒的喷砂材料,如铝砂。
在选择喷砂材料时,还应考虑工件的硬度和形状,以及所需的喷砂压力和工艺时间。
其次,控制喷砂压力和喷砂量。
喷砂压力和喷砂量是决定表面粗糙度的重要参数。
喷砂压力越大,颗粒冲击工件的能量越大,表面的粗糙度也越大。
因此,在实际操作中,需要根据工件的要求和喷砂材料的特性,确定合理的喷砂压力范围。
同样,喷砂量的大小也会直接影响喷砂效果。
合理控制喷砂量,可以保证喷砂材料在工件表面形成均匀的喷砂痕迹,从而得到稳定的表面粗糙度。
另外,控制喷砂距离和角度。
喷砂距离是指喷嘴与工件之间的距离,喷砂角度是指喷砂喷嘴与工件表面的夹角。
喷砂距离的选择需要根据工件的形状和尺寸进行合理调整,一般建议保持适当的距离,以避免过近造成过度磨损或破坏工件表面。
喷砂角度的选择也会影响喷砂效果。
一般而言,较小的喷砂角度可以加大冲击力,提高喷砂效果,但也会增加工件表面的磨损。
因此,在实际操作中需要根据工件的要求,合理选择喷砂角度,以达到最佳的表面粗糙度控制效果。
最后,关注喷砂后的处理工艺。
喷砂后的工件往往会残留喷砂材料和颗粒,需要进行适当的清洁和处理。
常见的方法包括水洗、气吹、机械刮擦等。
在清洁过程中,需要注意不仅要彻底去除喷砂材料和颗粒,还要保证不对工件表面产生新的损伤。
总之,喷砂机工艺控制中的表面粗糙度控制技巧涉及到喷砂材料的选择、喷砂压力和喷砂量的控制、喷砂距离和角度的调整,以及喷砂后的适当处理等方面。
机械零件表面粗糙度的测量与控制

机械零件表面粗糙度的测量与控制在机械加工领域中,表面粗糙度是一个极为重要的参数。
表面粗糙度的好坏直接影响着零件的质量、使用寿命以及工作效率。
因此,精确测量和控制机械零件表面粗糙度是非常关键的。
首先,我们需要明确表面粗糙度的定义和影响因素。
表面粗糙度是指物体表面的不平整程度。
它受到加工方式、刀具磨损、材料特性等多个因素的影响。
一个零件的表面粗糙度越小,表示其表面越光滑。
光滑的表面能够减少摩擦、提高密封性以及降低磨损程度,从而提升零件的性能。
其次,我们来探讨一下表面粗糙度的测量方法。
目前常用的测量方法包括划痕法、直接比较法、轮廓法、光学法和电子扫描法等。
其中,光学法和电子扫描法是目前比较先进和常用的方法。
光学法通常使用光学投影仪或激光干涉仪来测量零件表面的几何形状和表面粗糙度。
电子扫描法则通过采用激光或电子束扫描零件表面,然后用计算机分析得出表面粗糙度的参数。
然而,测量表面粗糙度并不仅仅是对数字的测量,更需要进一步对其进行控制。
表面粗糙度的控制主要包括原料选择、加工方式和刀具选择等方面。
不同的原料和加工方式会对表面粗糙度产生不同的影响。
例如,合适的原料可以提供较好的切削性能,从而减少加工时对零件表面的损伤。
此外,选择合适的刀具也可以有效地改善加工表面的粗糙度。
尖角刃刀具常用于精密加工,能够提供更平滑的切削表面,从而减小表面粗糙度。
另外,还有一些先进的技术和工艺可以帮助我们更好地控制表面粗糙度。
例如,数控加工技术可以提供更精确、更稳定的加工过程,从而减小表面粗糙度。
另外,电化学抛光和电镀等技术也可以改善零件的表面质量和粗糙度。
这些技术的应用可以在一定程度上提高零件的表面光滑度,并减小表面粗糙度。
综上所述,机械零件表面粗糙度的测量与控制是一个复杂而又重要的过程。
准确测量和控制表面粗糙度可以提高零件的质量和性能。
传统的测量方法包括划痕法、直接比较法等,而现代化的方法则包括光学法和电子扫描法。
此外,通过正确选择原料、加工方式和刀具,我们可以有效地控制表面粗糙度。
机械表面粗糙度控制方法

机械表面粗糙度控制方法机械表面的粗糙度是产品质量的一个重要指标,也直接影响到产品的性能和寿命。
因此,对机械表面粗糙度的控制是制造业中非常关键的一项工作。
在机械加工过程中,常见的控制方法有以下几种:工艺参数的优化、切削力的监测、切削液的选择和应用、刀具和夹具的优化设计以及表面处理等。
下面将逐一进行讨论。
首先,工艺参数的优化是控制机械表面粗糙度的基础。
在机械加工过程中,切削速度、进给速度、切削深度等工艺参数的选择会直接影响到表面粗糙度的大小。
一般来说,较高的切削速度和较小的切削深度可以获得较低的表面粗糙度。
此外,合理选择切削道次和切削方向也是降低表面粗糙度的有效方式。
其次,切削力的监测也是一种有效的控制方法。
切削力是机械加工过程中的一项重要指标,可以通过力传感器来实时监测。
合理监控和控制切削力的大小,可以有效降低切削振动和切削时产生的热量,从而提高表面加工质量。
切削液的选择和应用也是影响机械表面粗糙度的重要因素。
切削液不仅可以降低切削摩擦系数,减小切削温度,还可以冷却切削区域,防止切削热引起的变形和表面质量问题。
选择适合材料和切削类型的切削液,并进行正确的应用,可以显著改善机械表面的粗糙度。
此外,刀具和夹具的优化设计也是一项重要的控制方法。
刀具和夹具的设计不仅关系到切削过程的稳定性和精度,还会对表面质量产生直接影响。
合理选择刀具的材料、刀具的刃角和刃磨方式,以及优化夹具的刚性和稳定性,都可以改善表面的加工质量。
最后,表面处理是一种常见的提高机械表面粗糙度控制的方法。
表面处理包括磨削、抛光、电镀、化学处理等多种方式。
这些处理方式可以去除切削加工留下的毛刺和残留物,改变表面的光洁度和形貌,从而达到控制粗糙度的目的。
综上所述,机械表面粗糙度的控制方法包括工艺参数的优化、切削力的监测、切削液的选择和应用、刀具和夹具的优化设计以及表面处理等。
通过合理应用这些方法,可以有效地控制机械表面的粗糙度,提高产品的质量和性能。
汽车部件表面粗糙度

汽车部件表面粗糙度汽车部件表面粗糙度步骤一:引言汽车部件的表面粗糙度是指零部件表面的不平整程度。
它直接影响着零部件的性能和使用寿命。
因此,了解和控制汽车部件表面粗糙度对于确保汽车的质量和可靠性至关重要。
本文将逐步介绍汽车部件表面粗糙度的重要性以及如何进行控制。
步骤二:了解表面粗糙度的定义和测量方法表面粗糙度是指零部件表面的不规则度和不光滑程度。
它通常用参数来表示,如Ra值。
Ra值表示在一个特定的测量长度内,零部件表面的平均高度差。
测量表面粗糙度通常使用仪器设备,如激光干涉仪或光学仪器。
步骤三:表面粗糙度对汽车部件的影响汽车部件的表面粗糙度直接影响着零部件的功能和性能。
首先,表面粗糙度会影响零部件的摩擦和磨损特性。
如果表面粗糙度过高,摩擦会增加,导致能量损耗和磨损加剧。
其次,表面粗糙度也会影响零部件的密封性能。
如果表面粗糙度不合适,密封件无法紧密贴合,从而导致泄漏和损坏。
此外,表面粗糙度还会影响零部件的润滑性能和阻尼特性。
步骤四:控制表面粗糙度的方法为了确保汽车部件的质量和可靠性,需要控制表面粗糙度。
控制表面粗糙度的方法有很多,以下是一些常见的方法:1. 使用合适的加工技术:选择合适的加工技术可以改善零部件表面的粗糙度。
例如,精密加工技术如磨削、抛光和喷砂可以帮助提高表面质量。
2. 优化刀具和切削参数:刀具的选择和切削参数的优化也可以对表面粗糙度产生影响。
使用合适的刀具和切削参数可以减少切削力,并获得更好的表面质量。
3. 采用适当的表面处理方法:表面处理方法如电镀、喷涂和热处理也可以改善零部件的表面粗糙度。
这些方法可以填补表面缺陷和提高表面的耐磨性。
步骤五:质量控制和检测为了确保零部件的表面粗糙度达到要求,需要进行质量控制和检测。
这可以通过使用合适的检测设备和技术来实现。
如前所述,激光干涉仪和光学仪器可以用于测量表面粗糙度。
此外,还可以使用一些表面检测设备进行缺陷检测和质量控制。
步骤六:总结汽车部件的表面粗糙度对于确保汽车的质量和可靠性至关重要。
机械制造中的机械加工表面粗糙度工作原理

机械制造中的机械加工表面粗糙度工作原理机械加工是指通过削、切、磨等工艺将工件原有形状进行改变以满足一定尺寸、形状和粗糙度要求的加工方法。
在机械制造过程中,机械加工表面粗糙度的控制是十分重要的,它直接影响到零件的功能和使用寿命。
本文将介绍机械加工表面粗糙度的工作原理。
一、表面粗糙度的概念表面粗糙度是指工件表面上凹凸不平的程度,通常用Ra(平均粗糙度)来表示。
在机械加工中,我们常常要求工件表面光洁度高、粗糙度小,以确保零件的密封性、运动性和装配性能。
二、机械加工表面粗糙度的影响因素机械加工表面粗糙度受到多种因素的影响,主要包括以下几个方面:1.切削参数:切削速度、进给量、切削深度等切削参数直接影响到工件表面的质量。
一般来说,切削速度越大、进给量越小、切削深度越小,工件表面的粗糙度就越小。
2.切削工具状况:切削工具的磨损情况对工件表面质量有重要影响。
切削工具磨损过度会导致切削力增大、表面粗糙度加大。
所以,及时更换和修磨切削工具能够有效控制表面粗糙度。
3.工件材料:工件材料的硬度、韧性等性质会影响机械加工的精度和表面质量。
例如,硬度较高的材料可能导致切削刀具的磨损,从而影响表面的粗糙度。
4.切削方式:不同的切削方式,如车削、铣削、磨削等,对工件表面粗糙度的影响也有所不同。
三、机械加工表面粗糙度的控制方法为了能够控制机械加工表面的粗糙度,在实际操作中可以采取以下措施:1.选择合适的工艺参数:根据工件材料、形状和要求,合理选择切削速度、进给量、切削深度等参数,以获得较小的粗糙度。
2.使用高质量的切削工具:选择具有良好刚性和耐磨性的切削工具,并保持其锋利度,以便实现更好的切削效果。
3.优化切削方式:根据工件的特点,选择合适的切削方式。
有时候,可以采用一些先进的切削方式,如超声波切削、电火花加工等,以改善表面粗糙度。
4.后续加工工艺:有时候,机械加工的表面粗糙度无法满足要求,可以考虑通过后续加工工艺来改善。
例如,研磨、抛光等方法可以使工件表面更加光滑。
数控机床加工材料表面粗糙度的控制方法

数控机床加工材料表面粗糙度的控制方法数控机床是一种精密加工设备,广泛应用于制造业中。
在加工过程中,控制材料表面粗糙度是至关重要的。
本文将介绍几种常用的数控机床加工材料表面粗糙度的控制方法。
首先,选择合适的切削速度和进给速度。
切削速度和进给速度是影响材料表面粗糙度的重要因素。
在数控机床加工过程中,合理的切削速度和进给速度可以有效地控制材料的切削厚度和表面质量。
一般来说,切削速度越高,材料表面粗糙度越小;进给速度越小,材料表面粗糙度越小。
因此,在实际加工中,需要根据材料的性质和加工要求选择合适的切削速度和进给速度,以达到理想的表面粗糙度。
其次,正确选择和使用切削刀具。
切削刀具的选择和使用也是影响材料表面粗糙度的重要因素。
合适的切削刀具可以有效地降低切削力和切削温度,减小切削时的振动和共振现象,从而达到更好的加工效果。
通常情况下,硬度高、耐磨性好的切削刀具可以获得更好的表面质量。
此外,在使用切削刀具时,还需要注意及时更换刀具,保持刀具的锋利度,以保证加工质量。
另外,合理使用冷却润滑剂。
冷却润滑剂的使用可以有效降低表面粗糙度和切削力,减少切削过程中的摩擦和热量积聚,防止刀具过早磨损。
不同的材料和加工情况需要使用不同类型和浓度的冷却润滑剂。
因此,在加工过程中,需要根据实际情况选择合适的冷却润滑剂,并保持其良好的工作状态。
此外,适当的刀具半径补偿也是控制材料表面粗糙度的一种有效方法。
刀具半径补偿是一种数控机床中常用的加工方式,通过控制加工轮廓的形状和大小,可以有效地修正加工误差和提高表面质量。
在进行刀具半径补偿时,需要根据加工要求和工件形状选择合适的工具路径和补偿参数,以达到所需的表面粗糙度。
最后,加工前的预处理也是控制材料表面粗糙度的重要环节。
在进行数控机床加工之前,需要对工件进行合适的预处理,包括清洁、除锈、调整表面粗糙度等。
这些预处理措施可以有效减小加工时的摩擦阻力和表面缺陷,提高加工质量。
总结起来,数控机床加工材料表面粗糙度的控制方法有选择合适的切削速度和进给速度、正确选择和使用切削刀具、合理使用冷却润滑剂、适当的刀具半径补偿以及加工前的预处理。
- 1、下载文档前请自行甄别文档内容的完整性,平台不提供额外的编辑、内容补充、找答案等附加服务。
- 2、"仅部分预览"的文档,不可在线预览部分如存在完整性等问题,可反馈申请退款(可完整预览的文档不适用该条件!)。
- 3、如文档侵犯您的权益,请联系客服反馈,我们会尽快为您处理(人工客服工作时间:9:00-18:30)。
项目 质量不合格原因 1 主偏角过大 2 刀尖圆弧半径过小 3 修光刃不平直 4 刀具 采用了负刃倾角刀具,使切削划伤 已加工表面 减小主偏角 加大刀尖圆弧半径 重磨修光刃 采用正刃倾角或零度刃倾角的刀具 修磨、更换铣刀或铰刀 控制措施
5 铣刀或铰刀刀刃有缺陷 6
刀具切削部分表面粗糙度数值偏高 提高刀具刃磨质量 重磨或更换刀具 增加刀杆刚性或减少刀杆伸出长度 减小刀具后角或使用负后角刀具 修整砂轮或选择粒度号较大的砂轮 减小进给量或改进刀具几何参数 减小背吃刀量或改进刀具几何参数 避免使用中等切削速度、加强 润滑消除积屑瘤 调整、清洗机床刀架及拖板, 机床增大刚性 减少顶尖和尾架伸出量 增加工艺系统刚性,使用中心 架或跟刀架 降低转速、校正平衡 在许可的情况下改善工件材料 的物理机械性能 在许可的情况下改善工件材料的物 理机械性能、增பைடு நூலகம்刀具的断屑能力 选用符合质量标准的材料 有色金属宜采用高速细车或高速细 铣不宜磨削 选用润滑性能较好的切削液 增大定位副接触面以增大接触刚度 增加辅助支承 改滑动摩擦为滚动摩擦、降低支 撑爪接触面的表面粗糙度、提供 良好的润滑、支承不宜过紧
机床
1 工件材质过硬或过软 2 工件 3 工件韧性过大不宜断屑,致使切屑 划伤工件已加工表面 工件材质不均匀或有铸造缺陷
4 磨削有色金属砂轮堵塞 1 加工时润滑不良 2 其它 3 使用夹具时定位副,接触面积过小 产生振动 夹具缺少辅助支承产生振动
使用跟刀架时支承面划伤工件 4 已加工表面
7 刀具磨损严重 8 刀杆刚性差火伸出过长引起振动 9 刀具后角过大引起振动 10 砂轮钝化或粒度号偏小 1 切削 用量 进给量过大或与刀具参数不匹配 2 背吃刀量过大或与刀具参数不匹配
3 切削速度与背吃刀量、给进量不匹配 调整切削用量的配搭关系 4 产生了积屑瘤
1 机床刚性差,引起振动 2 3 4 两顶尖装夹工件时,顶尖或尾架主 轴伸出过长,产生振动 加工刚性差的工件参数振动 回转部件不平衡造成振动