影响机械加工表面粗糙度的几个因素及措施
《机械制造工艺学》教案 影响加工表面粗糙度的工艺因素及其改善措施
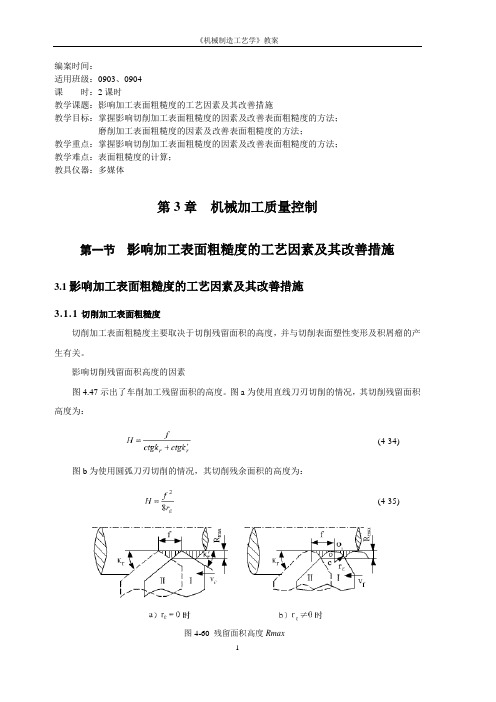
编案时间:适用班级:0903、0904课时:2课时教学课题:影响加工表面粗糙度的工艺因素及其改善措施教学目标:掌握影响切削加工表面粗糙度的因素及改善表面粗糙度的方法;磨削加工表面粗糙度的因素及改善表面粗糙度的方法;教学重点:掌握影响切削加工表面粗糙度的因素及改善表面粗糙度的方法;教学难点:表面粗糙度的计算;教具仪器:多媒体第3章机械加工质量控制第一节影响加工表面粗糙度的工艺因素及其改善措施3.1影响加工表面粗糙度的工艺因素及其改善措施3.1.1切削加工表面粗糙度切削加工表面粗糙度主要取决于切削残留面积的高度,并与切削表面塑性变形及积屑瘤的产生有关。
影响切削残留面积高度的因素图4.47示出了车削加工残留面积的高度。
图a为使用直线刀刃切削的情况,其切削残留面积高度为:(4-34) 图b为使用圆弧刀刃切削的情况,其切削残余面积的高度为:(4-35)图4-60 残留面积高度Rmax从上面两式可知,影响切削残留面积高度的因素主要包括:刀尖圆弧半径、主偏角、副偏角及进给量f等。
影响切削表面塑性变形和积屑瘤的因素图4-61示出了加工塑性材料时切削速度对表面粗糙度的影响。
切削速度v处于20~50m/min 时,表面粗糙度值最大,这是由于此时容易产生积屑瘤或鳞刺。
积屑瘤已在3.4节中介绍,鳞刺是指切削加工表面在切削速度方向产生的鱼鳞片状的毛刺。
在切削低碳钢、中碳钢、铬钢、不锈钢、铝合金、紫铜等塑性金属时,无论是车、刨、钻、插、滚齿、插齿和螺纹加工工序中都可能产生鳞刺。
积屑瘤和鳞刺均使表面粗糙度值加大。
当切削速度超100m/min时,表面粗糙度值下降,并趋于稳定。
在实际切削时,选择低速宽刀精切和高速精切,往往可以得到较小的表面粗糙度值。
图4-61 切削45钢时切削速度与粗糙度关系一般说,材料韧性越大或塑性变形趋势越大,被加工表面粗糙度就越大。
切削脆性材料比切削塑性材料容易达到表面粗糙度的要求。
对于同样的材料,金相组织越是粗大,切削加工后的表面粗糙度值也越大。
浅论表面粗糙度及其影响因素

C OCCUPATION2013 0180案例ASES浅论表面粗糙度及其影响因素高瑞兰摘 要:本文简要介绍了表面粗糙度对机械零件使用性能的影响,强调要获得好的工件表面质量,就必须降低表面粗糙度,并简要列举了降低表面粗糙度的几种措施。
关键词:表面粗糙度 工作精度 配合性质 加工参数 切削液表面粗糙度是指零件加工表面具有的较小间距和峰谷所形成的微观几何形状误差。
表面粗糙度越小,零件表面越光滑。
在机械加工过程中,工件表面粗糙度的大小,是衡量工件表面质量的重要标志,对机械零件的使用性能具有很大影响。
一、工件表面粗糙度对机械零件使用性能的影响1.加剧零件的摩擦和磨损机器做功时,许多零件的表面之间存在着相互运动,相互运动将产生摩擦,进而导致磨损。
由于零件表面粗糙度的存在,当两个零件表面接触时,它们的接触面不是整个零件表面,而仅仅是两加工表面上许多突出小峰的顶端,从而导致实际接触面积只是理论面积的一部分,而加剧了零件的磨损。
并且表面越粗糙,接触面积越小,越易磨损,也就是零件的耐磨性越差。
但同时也要注意并不是表面越光滑越好,当表面粗糙度值超过一定值后,会由于表面过于光滑不利于润滑液的储存,且使接触表面之间的分子亲和力增大,甚至发生分子粘合,使摩擦阻力增大,从而进入一个急剧磨损阶段。
2.影响机器和仪器的工作精度工件的粗糙表面易于磨损,使配合间隙增大,从而使运动件灵敏度下降,影响机器和仪器的工作精度。
3.对配合性质造成影响在间隙配合中,如果零件的配合表面粗糙,就会使配合件很快磨损而增大配合间隙,改变配合性质,降低配合精度;在过盈配合中,如果零件的配合表面粗糙,则装配后配合表面的凸峰被挤平,配合件间的有效过盈量减小,降低配合件间的连接强度,从而影响配合的有效性。
4.对零件强度造成影响零件表面越粗糙,对应力集中越敏感,特别是在交变载荷作用下,产生的交变应力在工件表面微观不平度凹谷处易造成应力集中,从而形成细小裂纹,甚至使工件损坏。
机械加工表面粗糙度的影响因素
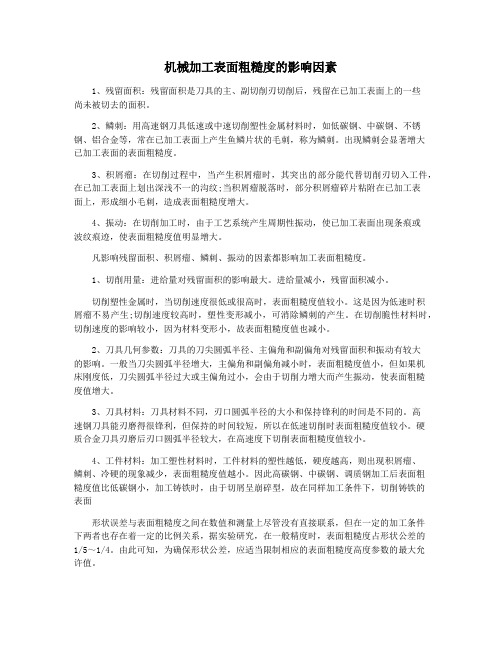
机械加工表面粗糙度的影响因素1、残留面积:残留面积是刀具的主、副切削刃切削后,残留在已加工表面上的一些尚未被切去的面积。
2、鳞刺:用高速钢刀具低速或中速切削塑性金属材料时,如低碳钢、中碳钢、不锈钢、铝合金等,常在已加工表面上产生鱼鳞片状的毛刺,称为鳞刺。
出现鳞刺会显著增大已加工表面的表面粗糙度。
3、积屑瘤:在切削过程中,当产生积屑瘤时,其突出的部分能代替切削刃切入工件,在已加工表面上划出深浅不一的沟纹;当积屑瘤脱落时,部分积屑瘤碎片粘附在已加工表面上,形成细小毛刺,造成表面粗糙度增大。
4、振动:在切削加工时,由于工艺系统产生周期性振动,使已加工表面出现条痕或波纹痕迹,使表面粗糙度值明显增大。
凡影响残留面积、积屑瘤、鳞刺、振动的因素都影响加工表面粗糙度。
1、切削用量:进给量对残留面积的影响最大。
进给量减小,残留面积减小。
切削塑性金属时,当切削速度很低或很高时,表面粗糙度值较小。
这是因为低速时积屑瘤不易产生;切削速度较高时,塑性变形减小,可消除鳞刺的产生。
在切削脆性材料时,切削速度的影响较小,因为材料变形小,故表面粗糙度值也减小。
2、刀具几何参数:刀具的刀尖圆弧半径、主偏角和副偏角对残留面积和振动有较大的影响。
一般当刀尖圆弧半径增大,主偏角和副偏角减小时,表面粗糙度值小,但如果机床刚度低,刀尖圆弧半径过大或主偏角过小,会由于切削力增大而产生振动,使表面粗糙度值增大。
3、刀具材料:刀具材料不同,刃口圆弧半径的大小和保持锋利的时间是不同的。
高速钢刀具能刃磨得很锋利,但保持的时间较短,所以在低速切削时表面粗糙度值较小。
硬质合金刀具刃磨后刃口圆弧半径较大,在高速度下切削表面粗糙度值较小。
4、工件材料:加工塑性材料时,工件材料的塑性越低,硬度越高,则出现积屑瘤、鳞刺、冷硬的现象减少,表面粗糙度值越小。
因此高碳钢、中碳钢、调质钢加工后表面粗糙度值比低碳钢小,加工铸铁时,由于切屑呈崩碎型,故在同样加工条件下,切削铸铁的表面形状误差与表面粗糙度之间在数值和测量上尽管没有直接联系,但在一定的加工条件下两者也存在着一定的比例关系,据实验研究,在一般精度时,表面粗糙度占形状公差的1/5~1/4。
浅谈加工表面粗糙度和物理力学性能的影响因素研究
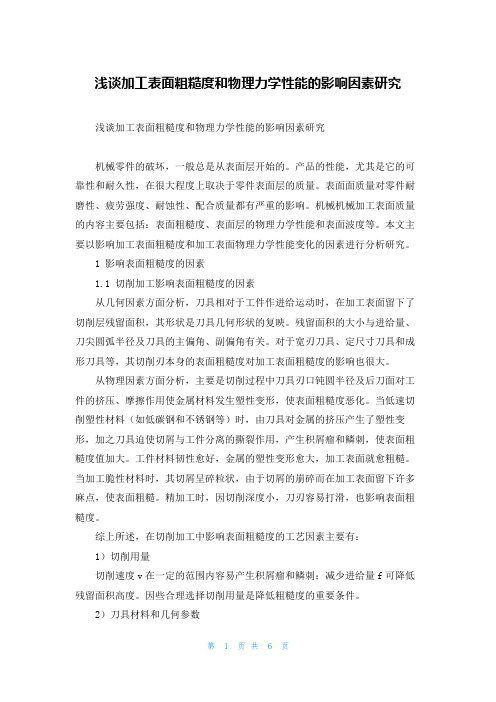
浅谈加工表面粗糙度和物理力学性能的影响因素研究浅谈加工表面粗糙度和物理力学性能的影响因素研究机械零件的破坏,一般总是从表面层开始的。
产品的性能,尤其是它的可靠性和耐久性,在很大程度上取决于零件表面层的质量。
表面面质量对零件耐磨性、疲劳强度、耐蚀性、配合质量都有严重的影响。
机械机械加工表面质量的内容主要包括:表面粗糙度、表面层的物理力学性能和表面波度等。
本文主要以影响加工表面粗糙度和加工表面物理力学性能变化的因素进行分析研究。
1 影响表面粗糙度的因素1.1 切削加工影响表面粗糙度的因素从几何因素方面分析,刀具相对于工件作进给运动时,在加工表面留下了切削层残留面积,其形状是刀具几何形状的复映。
残留面积的大小与进给量、刀尖圆弧半径及刀具的主偏角、副偏角有关。
对于宽刃刀具、定尺寸刀具和成形刀具等,其切削刃本身的表面粗糙度对加工表面粗糙度的影响也很大。
从物理因素方面分析,主要是切削过程中刀具刃口钝圆半径及后刀面对工件的挤压、摩擦作用使金属材料发生塑性变形,使表面粗糙度恶化。
当低速切削塑性材料(如低碳钢和不锈钢等)时,由刀具对金属的挤压产生了塑性变形,加之刀具迫使切屑与工件分离的撕裂作用,产生积屑瘤和鳞刺,使表面粗糙度值加大。
工件材料韧性愈好,金属的塑性变形愈大,加工表面就愈粗糙。
当加工脆性材料时,其切屑呈碎粒状,由于切屑的崩碎而在加工表面留下许多麻点,使表面粗糙。
精加工时,因切削深度小,刀刃容易打滑,也影响表面粗糙度。
综上所述,在切削加工中影响表面粗糙度的工艺因素主要有:1)切削用量切削速度v在一定的范围内容易产生积屑瘤和鳞刺;减少进给量f可降低残留面积高度。
因些合理选择切削用量是降低粗糙度的重要条件。
2)刀具材料和几何参数实践表明,在切削条件相同时,用硬质合金刀具加工的工作表面粗糙度比用高速钢刀具加工的低。
用金钢石车刀加工因不易形成积屑瘤,故可获得粗糙度很低的表面。
刀类圆弧半径rE、主偏角KC和副偏角kcC均影响残留面积的大小。
关于机械加工中表面粗糙度的成因及改进措施的分析
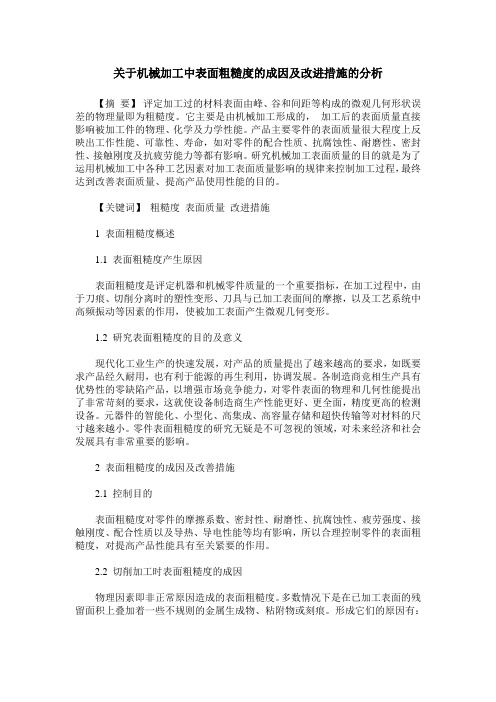
关于机械加工中表面粗糙度的成因及改进措施的分析【摘要】评定加工过的材料表面由峰、谷和间距等构成的微观几何形状误差的物理量即为粗糙度。
它主要是由机械加工形成的,加工后的表面质量直接影响被加工件的物理、化学及力学性能。
产品主要零件的表面质量很大程度上反映出工作性能、可靠性、寿命,如对零件的配合性质、抗腐蚀性、耐磨性、密封性、接触刚度及抗疲劳能力等都有影响。
研究机械加工表面质量的目的就是为了运用机械加工中各种工艺因素对加工表面质量影响的规律来控制加工过程,最终达到改善表面质量、提高产品使用性能的目的。
【关键词】粗糙度表面质量改进措施1 表面粗糙度概述1.1 表面粗糙度产生原因表面粗糙度是评定机器和机械零件质量的一个重要指标,在加工过程中,由于刀痕、切削分离时的塑性变形、刀具与已加工表面间的摩擦,以及工艺系统中高频振动等因素的作用,使被加工表面产生微观几何变形。
1.2 研究表面粗糙度的目的及意义现代化工业生产的快速发展,对产品的质量提出了越来越高的要求,如既要求产品经久耐用,也有利于能源的再生利用,协调发展。
各制造商竞相生产具有优势性的零缺陷产品,以增强市场竞争能力,对零件表面的物理和几何性能提出了非常苛刻的要求,这就使设备制造商生产性能更好、更全面,精度更高的检测设备。
元器件的智能化、小型化、高集成、高容量存储和超快传输等对材料的尺寸越来越小。
零件表面粗糙度的研究无疑是不可忽视的领域,对未来经济和社会发展具有非常重要的影响。
2 表面粗糙度的成因及改善措施2.1 控制目的表面粗糙度对零件的摩擦系数、密封性、耐磨性、抗腐蚀性、疲劳强度、接触刚度、配合性质以及导热、导电性能等均有影响,所以合理控制零件的表面粗糙度,对提高产品性能具有至关紧要的作用。
2.2 切削加工时表面粗糙度的成因物理因素即非正常原因造成的表面粗糙度。
多数情况下是在已加工表面的残留面积上叠加着一些不规则的金属生成物、粘附物或刻痕。
形成它们的原因有:(1)积屑瘤。
车床工件表面粗糙度的形成原因及解决措施

车床工件表面粗糙度的形成原因及解决措施表面粗糙度是机械加工中衡量加工质量的重要因素,表面粗糙度对零件和机器有着重要的意义。
但由于工件材料、切削加工方式、表面硬化等原因,造成了表面粗糙度值提高。
本文详细分析了车床工件表面粗糙度的形成原因,并提出相应的解决措施。
标签:车床工件:表面:粗糙度:原因:解决措施1.引言在实际的机械加工中,工件表面会存在许多高低不平的微小峰谷,这是因为切屑分离时塑性变形、工艺系统的振动以及刀具与已加工表面问的摩擦等因素的影响。
这些零件被加工表面上的微观几何形状误差称为表面粗糙度。
表面粗糙度对零件的耐磨性、耐腐蚀性、疲劳强度和配合性质都有很大影响。
本文详细分析了车床工件表面粗糙度的形成原因,并提出相应的解决措施,具有一定的实际意义。
2.影响工件表面粗糙度的原因2.1工件材料性能。
塑性金属材料在加工的过程中,刀具挤压金属材料,使其产生塑性变形,切屑和工件分离是由于刀具外力的挤压,表面出现撕裂现象,这严重影响表面粗糙度。
伴随着工件材料韧性的提高,在切屑过程中材料的塑性变形也就越大,加工表面粗糙度也就越差。
脆性材料在加工时,所切削形成的铁屑为颗粒状,在切屑崩碎的过程中,加工表面容易产生细小的坑点,提高表面粗糙度值。
2.2刀具切削加工。
在普通刀具在切屑过程中,切削表面势必会产生残留面积,残留面积的高度则是影响加工表面粗糙度的主要因素。
在整个加工过程中,刀具的进给量、主偏角、副偏角、圆弧半径则是造成切削残留面积的主要因素。
砂轮磨削加工过程中,砂轮上硬质颗粒断裂后形成微刃,其分布情况和外形对表面粗糙度有着直接的影响。
因为磨削加工表面是大量微刃在金属表面切削出细小的切削痕迹构成的,所形成的切削痕迹越细小、越密集则表面粗糙度就越好,相反切削痕迹粗大、分布疏散,则表面粗糙度越差。
2.3表面冷作硬化。
在普通刀具切削或砂轮磨削过程中,表面层金属由于刀具外在切削力和材料本身的塑性,使其晶格产生剪切、滑移、拉长、扭曲、破碎,宏观的表现特点则是材料表面层变硬,屈服点提高,延生率降低。
机械零件加工存在的问题及对策
机械零件加工存在的问题及对策
随着工业化的发展,机械零件作为机械设备的重要组成部分,其加工质量直接影响着整个设备的性能和使用寿命。
在机械零件加工过程中,经常会出现一些问题,例如加工精度不高、表面粗糙度较大、加工效率低下等,这些问题不仅影响了零件的质量,还增加了生产成本和时间成本。
针对机械零件加工存在的问题,急需采取相应的对策来解决,以提高加工质量和效率。
一、加工精度不高
在机械零件加工过程中,加工精度不高是一个比较常见的问题。
这主要是由于加工设备的精度不高、刀具磨损严重、加工过程中受到振动等因素影响造成的。
对此,可以采取以下对策来解决:
1. 选用高精度的加工设备和刀具,确保加工精度;
2. 加强设备维护保养,及时更换磨损严重的刀具;
3. 采取减少振动的措施,例如增加刚性支撑、改善加工环境等。
二、表面粗糙度较大
1. 适当降低加工速度,提高切削质量;
2. 选择合适的切削液,并及时更换;
3. 定期检查和更换磨损严重的刀具,保持刀具的良好状态。
三、加工效率低下
1. 优化加工工艺,合理安排加工顺序,提高生产效率;
2. 及时更换老化的加工设备,提高生产效率;
3. 加强操作员的培训和技术指导,提高操作技术水平。
四、设备故障频发
设备故障频发也是机械零件加工中的常见问题。
造成设备故障频发的原因主要有设备老化、设备维护不到位、工作环境不清洁等。
对此,可以采取以下对策来解决:
1. 及时更换老化的设备,提高设备可靠性;
2. 加强设备的维护保养工作,确保设备的良好状态;
3. 保持工作环境的清洁整洁,减少设备故障发生的概率。
机械制造中的机械加工表面粗糙度工作原理
机械制造中的机械加工表面粗糙度工作原理机械加工是指通过削、切、磨等工艺将工件原有形状进行改变以满足一定尺寸、形状和粗糙度要求的加工方法。
在机械制造过程中,机械加工表面粗糙度的控制是十分重要的,它直接影响到零件的功能和使用寿命。
本文将介绍机械加工表面粗糙度的工作原理。
一、表面粗糙度的概念表面粗糙度是指工件表面上凹凸不平的程度,通常用Ra(平均粗糙度)来表示。
在机械加工中,我们常常要求工件表面光洁度高、粗糙度小,以确保零件的密封性、运动性和装配性能。
二、机械加工表面粗糙度的影响因素机械加工表面粗糙度受到多种因素的影响,主要包括以下几个方面:1.切削参数:切削速度、进给量、切削深度等切削参数直接影响到工件表面的质量。
一般来说,切削速度越大、进给量越小、切削深度越小,工件表面的粗糙度就越小。
2.切削工具状况:切削工具的磨损情况对工件表面质量有重要影响。
切削工具磨损过度会导致切削力增大、表面粗糙度加大。
所以,及时更换和修磨切削工具能够有效控制表面粗糙度。
3.工件材料:工件材料的硬度、韧性等性质会影响机械加工的精度和表面质量。
例如,硬度较高的材料可能导致切削刀具的磨损,从而影响表面的粗糙度。
4.切削方式:不同的切削方式,如车削、铣削、磨削等,对工件表面粗糙度的影响也有所不同。
三、机械加工表面粗糙度的控制方法为了能够控制机械加工表面的粗糙度,在实际操作中可以采取以下措施:1.选择合适的工艺参数:根据工件材料、形状和要求,合理选择切削速度、进给量、切削深度等参数,以获得较小的粗糙度。
2.使用高质量的切削工具:选择具有良好刚性和耐磨性的切削工具,并保持其锋利度,以便实现更好的切削效果。
3.优化切削方式:根据工件的特点,选择合适的切削方式。
有时候,可以采用一些先进的切削方式,如超声波切削、电火花加工等,以改善表面粗糙度。
4.后续加工工艺:有时候,机械加工的表面粗糙度无法满足要求,可以考虑通过后续加工工艺来改善。
例如,研磨、抛光等方法可以使工件表面更加光滑。
影响机械加工表面质量的因素及采取措施毕业论文
影响机械加⼯表⾯质量的因素及采取措施毕业论⽂毕业论⽂(设计)题⽬:影响机械加⼯表⾯质量的因素及采取措施影响机械加⼯表⾯质量的因素及采取措施摘要:机械产品的使⽤性能的提⾼和使⽤寿命的增加与组成产品的零件加⼯质量密切相关,零件的加⼯质量是保证产品质量基础。
衡量零件加⼯质量好坏的主要指标有:加⼯精度和表⾯粗糙度。
本⽂主要通过对影响零件表⾯粗糙度的因素、零件表⾯层的物理⼒学性能(表⾯冷作硬化、残余应⼒、⾦相组织的变化与磨削烧伤)、表⾯质量影响零件使⽤性能等因素的分析和研究,来提⾼机械加⼯表⾯质量的⼯艺措施。
关键词:机械加⼯;表⾯质量;影响因素;控制措施⽬录前⾔ (1)⼀、概述 (1)(⼀)、基本概念 (1)1、机械加⼯ (1)2、零件的失效 (2)3、磨削烧伤 (2)4、表⾯冷作硬化 (2)⼆、影响⼯件表⾯质量的因素 (2)(⼀)、加⼯过程对表⾯质量的影响 (2)1、⼯艺系统的振动对⼯件表⾯质量的影响 (2)2、⼑具⼏何参数、材料和刃磨质量对表⾯质量的影响 (2)3、切削液对表⾯质量的影响 (3)4、⼯件材料对表⾯质量的影响 (3)5、切削条件对⼯件表⾯质量的影响 (3)6、切削速度对表⾯粗糙度的影响 (4)7、磨削加⼯影响表⾯质量的素 (4)8、影响⼯件表⾯物理机械性能的素 (5)(⼆)、使⽤过程中影响表⾯质量的因素 (7)1、耐磨性对表⾯质量的影响 (7)2、疲劳强度对表⾯质量的响 (8)3、耐蚀性对表⾯质量的响 (8)三、机械加⼯表⾯质量对零件使⽤性能的影响 (8)(⼀)、表⾯质量对零件耐磨性的影响 (8)(⼆)、表⾯质量对零件疲劳强度的影响 (9)(三)、表⾯质量对零件耐腐蚀性能的影响 (9)(四)、表⾯质量对零件间配合性质的影响 (9)(五)、表⾯质量对零件其他性能的影响 (10)四、控制表⾯质量的途径 (10)(⼀)、降低表⾯粗糙度的加⼯⽅法....、 (10)(⼆)、改善表⾯物理⼒学性能的加⼯⽅法 (13)五、提⾼机械加⼯⼯件表⾯质量的措施 (15)六、结论 (16)七、参考⽂献 (16)前⾔随着⼯业技术的飞速发展机械化⽣产以⾛进各⼤⼩企业,与之息息相关的就是各式各样的机器。
影响机械加工表面质量的因素及改进措施
影响机械加工表面质量的因素及改进措施在现代工业生产中,生产机械需要在高速运转的状态下工作。
这就需要机械加工零件具有较高的抗磨损、抗腐蚀能力、零件表面具有较高的质量。
机械加工表面质量对机械生产效率与产品质量的影响非常大,要提升机械生产的效率与产品质量,就需要了解影响机械加工表面质量的因素,并对这些因素加以控制,从而提升机械加工表面的质量,促进机械生产效率与产品质量的提升。
本文将对机械加工表面质量影响因素及改进措施进行了一定的阐述。
标签:影响;机械加工;表面质量;因素;改进措施一、影响机械加工表面质量的关键因素(一)切削力和切削热切削加工是机械零件加工中的一道重要工序,是机械零件加工的一种主要的加工方法,而切削热和切削力则是影响加工表面质量的重要因素。
在切削加工中,加工表面的质量在很大程度上受到切削热和切削力的影响。
机械零件在切削加工过程中,会产生残余应力,表面层硬度也会发生改变,甚至改变金属材料的金相组织。
在切削热和切削力的作用下,在切削的过程中,机械零件的表面层形态发生变形,进而导致冷却硬化的现象出现在机加工零件的表面,零件变形的阻力加大,改变零件的物理机械性能。
零件和刀具的相对高速运动中,会产生大量的切削热。
零件表面层材料的温度如果超过特定的界限,金属零件表层的硬度和强度将会降低,零件表面层材料的金相组织也会受到影响,在表层产生一定的残余应力,零件的机械加工表面质量也会受到不同程度的影响。
(二)原始误差理想化的零件机械加工质量同零件加工精度和表面加工质量的偏差值,就是所说的原始误差,它是在机械零件的加工过程中产生的。
分析其形成的原因可知,机械零件的加工技术手段、加工工艺系统都是造成原始误差的首要原因。
机械加工的表面质量,在很大程度上受到原始误差的影响。
另外,机床设备、待加工零件的材料特性、所采用的刀具和夹具都会对表面质量造成很大的影响,测量仪器也会造成一定影响。
原始误差主要包括两个方面,即调整误差和原理误差。
- 1、下载文档前请自行甄别文档内容的完整性,平台不提供额外的编辑、内容补充、找答案等附加服务。
- 2、"仅部分预览"的文档,不可在线预览部分如存在完整性等问题,可反馈申请退款(可完整预览的文档不适用该条件!)。
- 3、如文档侵犯您的权益,请联系客服反馈,我们会尽快为您处理(人工客服工作时间:9:00-18:30)。
职教类
影响机械加工表面粗糙度的几个因素及措施
摘要:表面粗糙度是零件表面所具有的微小峰谷的不平程度,它是评价零件的一项重要指标。
一般说来,它的波距和波高都比较小,是一种微观的几何形状误差。
对机械加工表面,表面粗糙度是由切削时的刀痕,刀具和加工表面之间的摩擦,切削时的塑性变形,以及工艺系统中的高频振动等原因所造成的。
表面粗糙度是检验零件质量的主要依据,它的选择直接关系到生产成本、产品的质量、使用寿命。
关键词:机械加工表面粗糙度提高措施
随着工业技术的飞速发展,机器的使用要求越来越高,一些重要零件在高压力、高速、高温等高要求条件下工作,表面层的任何缺陷,不仅直接影响零件的工作性能,而且还可能引起应力集中、应力腐蚀等现象,将进一步加速零件的失效,这一切都与加工表面质量有很大关系。
因而表面质量问题越来越受到各方面的重视。
一、机械加工表面粗糙度对零件使用性能的影响
表面粗糙度对零件的配合精度,疲劳强度、抗腐蚀性,摩擦磨损等使用性能都有很大的影响。
1、表面质量对零件配合精度的影响
(1)对间隙配合的影响
由于零件表面的凹凸不平,两接触表面总有一些凸峰相接触。
表面粗糙度
过大,则零件相对运动过程中,接触表面会很快磨损,从而使间隙增大,引起配合性质改变,影响配合的稳定性。
特别是在零件尺寸和公差小的情况下,此影响更为明显。
(2)对过盈配合的影响
粗糙表面在装配压入过程中,会将相接触的峰顶挤平,减少实际有效过盈量,降低了配合的连接强度。
2、表面质量对疲劳强度的影响
零件表面越粗糙,则表面上的凹痕就越深明,产生的应力集中现象就越严重。
当零件受到交变载荷的作用时,疲劳强度会降低,零件疲劳损坏的可能性增大。
3、表面质量对零件抗腐蚀性的影响
零件表面越粗糙,则积聚在零件表面的腐蚀气体或液体也越多,且通过表面的微观凹谷向零件表层渗透,形成表面锈蚀。
4、表面质量对零件摩擦磨损的影响
两接触表面作相对运动时,表面越粗糙,摩擦系数越大,摩擦阻力越大,因摩擦消耗的能量也越大,并且还影响零件相对运动的灵活性。
此外,表面越粗糙,两配合表面的实际有效接触面积越小,单位面积压力越大,更易磨损。
此外,表面粗糙度还影响零件的接触刚度、密封性能、产品的美观和表面涂层的质量等。
因此,提高产品的质量和寿命应选取合理的表面粗糙度。
二、影响表面粗糙度的因素及措施
1、切削加工影响表面粗糙度的因素
在加工表面留下了切削层残留面积,其形状是刀具几何形状的复映。
减小
进给量vf、主偏角、副偏角以及增大刀尖圆弧半径,均可减小残留面积的高度。
此外,适当增大刀具的前角以减小切削时的塑性变形程度。
合理选择润滑液和提高刀具刃磨质量以减小切削时的塑性变形和抑制刀瘤、鳞刺的生成,也是减小表面粗糙度值的有效措施。
2、工件材料的性质
加工塑性材料时,由于刀具对金属的挤压产生了塑性变形,加之刀具迫使切屑与工件分离的撕裂作用,使表面粗糙度值加大。
加工脆性材料时,其切屑呈碎粒状,由于切屑的崩碎而在加工表面留下许多麻点,使表面粗糙度值加大。
3、切削用量
(1)进给量ƒ影响
采用较小的进给量ƒ,加工表面残留面积高度较小,对减小粗糙度Ra值有利。
(2)切削速度υ的影响
切削塑性材料,当切削速度υ小于5 m/min或大于100 m/min时,不易产生积屑瘤,对减小粗糙度Ra值有利。
当切削速度υ在20--25 m/min,且切削温度约为300ºC时,切屑与刀具前刀面摩擦系数最大,此时积屑瘤高度最大,使粗糙度Ra值增加。
(3)切削深度αp影响
切削深度αp比进给量ƒ和切削速度υ对粗糙度Ra值的影响要小。
当αp 减小时,切削力减小,不易产生振动,对减小粗糙度Ra值有利。
4、磨削加工影响表面粗糙度的因素
像切削加工时表面粗糙度的形成过程一样,磨削加工表面粗糙度的形成也
是由几何因素和表面金属的塑性变形来决定的。
影响磨削表面粗糙的主要因素有:(1)砂轮的粒度;(2)砂轮的硬度;(3)砂轮的修整;(4)磨削速度;(5)磨削径向进给量与光磨次数;(6)工件圆周进给速度与轴向进给量;(7)冷却润滑液。
三、提高表面粗糙度的措施
1、减小切削加工表面粗糙度的措施
(1)刀具方面:在工艺系统刚度足够时,采用较大的刀尖圆弧半径re,较小副偏角k'r,使用长度比进给量稍大一些的k'r=0的修光刃;采用较大的前角r。
加工塑性的材料,提高刀具的刃磨质量,减小刀具前、后刀面的粗糙度数值,使其不大于Ra1.25μm;选用与工件亲和力小的刀具材料;对刀具进行氧、氮化处理;限制副刀刃上的磨损量;选用细颗粒的硬质合金做刀具等。
(2)工件方面:应有适宜的金相组织(低碳钢、低合金钢中应有铁素体加低碳马氏体、索氏体或片状珠光体,高碳钢、高合金钢中应有粒状珠光体);加工中碳钢及中碳合金钢时若采用较高切削速度,应为粒状珠光体;若采用较低切削速度,应为片状珠光体组织。
合金元素中碳化物的分布要细匀;易切钢中应含有硫铅等元素;对工件进行调质处理,提高硬度,降低塑性;减小铸铁中石墨的颗粒尺寸等。
(3)切削条件方面:以较高的切削速度切削塑性材料;减小进给量;采用高效切削液;提高机床的运动精度,增强工艺系统刚度;采用超声波振动切削加工等。
2、减小磨削加工表面粗糙度参数值的措施
(1)砂轮特性方面:采用细粒度砂轮;提高磨粒切削刃的等高性;根据工件材料、磨料等选择适宜的砂轮硬度;选择与工件材料亲和力小的磨料;采用适宜的弹性结合剂的砂轮,采用直径较大的砂轮;增大砂轮的宽度等。
(2)砂轮修整方面:金刚石的耐磨性、刃口形状、安装角度应满足一定要求;选择适当的修整用量。
(3)磨削条件方面:提高砂轮速度或降低工作速度,使V砂/V工的比值增大;采用较小的纵向进给量、磨削深度,最后进行无进给光磨。
正确选用切削液的种类、浓度比、压力、流量和清洁度等;提高砂轮的平衡精度;提高主轴的回转精度、工作台运动的平衡性及整个工艺系统的刚度。
四、结论
由于机械加工表面对机器零件的使用性能如耐磨性、接触刚度、疲劳强度、配合性质、抗腐蚀性能及精度的稳定性等有很大的影响,因此对机器零件的重要表面应提出一定的表面粗糙度要求。
由于影响表面粗糙度的因素是多方面的,因此应该综合考虑各方面的因素,对表面粗糙度根据需要提出比较经济适用的要求。