扩散工艺
半导体不同扩散工艺的特点

半导体不同扩散工艺的特点半导体扩散工艺是一种用于改变半导体材料中杂质浓度分布的方法。
通过控制杂质的浓度分布,可以改变半导体材料的电学特性,从而实现半导体器件的制备和调控。
根据不同的扩散工艺,可以分为几种常见的类型,包括固相扩散、液相扩散和气相扩散,每种工艺都有其特点和适用范围。
1. 固相扩散:固相扩散是最早被广泛应用的扩散工艺之一。
其特点是使用固态杂质源,如固态的金属盐或金属氧化物,通过热处理将杂质扩散到半导体材料中。
固相扩散的过程较为简单,易于控制,适用于大批量半导体器件的生产。
然而,固相扩散工艺的主要缺点是扩散速度较慢,需要较长的时间完成杂质的扩散,且扩散深度不易控制。
2. 液相扩散:液相扩散是使用液态杂质源将杂质扩散到半导体材料中的工艺。
液相扩散的特点是扩散速度较快,扩散深度和浓度也较容易控制。
液相扩散的主要优点是可以在相对较短的时间内完成扩散过程,并且可以实现较高的杂质浓度。
然而,液相扩散过程中,需要使用到液态杂质源,这可能会对半导体材料的结构和性能产生不利影响,需要注意杂质源的选择和处理,以避免对器件性能造成负面影响。
3. 气相扩散:气相扩散是使用气态杂质源将杂质扩散到半导体材料中的工艺。
与固相和液相扩散相比,气相扩散具有更高的扩散速率和更好的控制性能。
气相扩散工艺通常是在高温下进行,通过将气态杂质源分解生成活性的杂质气体,然后将其扩散到半导体材料中。
气相扩散的优点是可以实现较高的杂质浓度和较深的扩散深度,且扩散速度较快。
然而,气相扩散工艺需要较高的温度和气压条件,且对设备和工艺环境要求较高,因此工艺的成本较高,适用于对器件性能要求较高、生产规模较小的应用领域。
总之,不同的扩散工艺具有各自的特点和适用范围。
在选择和使用扩散工艺时,需要根据实际需求综合考虑工艺的控制性能、扩散速度、成本等因素,以及对半导体器件性能的影响。
对于不同类型的半导体器件,可能需要采用不同的扩散工艺来实现特定的杂质浓度分布和形状控制,以满足器件设计和制备的要求。
扩散工艺介绍

扩散工艺知识介绍
1: 扩散工序简要介绍 2: 扩散工艺控制
扩散工序简要介绍
1: 2: 3: 4: 5: 扩散炉系统 热氧化 掺杂 扩散 其它
扩散炉系统
其它
氮气(HCL)退火和烘焙:工艺的稳定和重复 合金:工艺条件的严格控制
其它
退火 激活杂质 消除晶格损伤 钝化表面保护膜 合金 形成金属与硅的欧姆接触 烘焙
氧化层质量控制
氧化条件的选择: 厚度 质量要求 效率 条件管理 厚度均匀性 表面斑点 氧化膜针孔 反型层(低掺杂P型硅) 热氧化层错
掺杂质量控制
掺杂和扩散是联系在一起的 掺杂薄层的严格控制:条件的选择 气流的稳 定控制是难点 条件管理是关键 掺杂量的表征:表面方块电阻的局限性
扩散质量控制
扩散条件的选择: 满足设计要求 工艺重复性 稳定性(理论结合工艺试验) 条件管理 扩散速度:表面杂质浓度 杂质扩散系数 气氛 硅体内缺陷密度 扩散参数控制 表面质量控制 :合金点 白雾 硅片翘曲 表面 划伤 表面沾污
扩散质量控制
漏电流控制(器件特性异常):沾污 氧化层缺 陷 (表面沟道效应) 硅体内缺陷(管道效应) 表面杂质浓度偏低(复合电流) 氧化扩散与扩散氧化:杂质分凝效应 扩散参数偏差控制:温度分布 气流和排片方 式 进出舟速度和片间距 HFE 控制:综合考虑
Байду номын сангаас杂
其它杂质源 在硅表面淀积一薄的杂质层 优缺点:设备简单,操作方便,工艺简 单.精确掺杂控制能力低而且表面浓度不适 宜做大范围的调整,有污染.
扩散的工艺流程

扩散的工艺流程扩散工艺是集成电路制造中的一项重要工艺,主要用于在半导体材料表面形成掺杂区域,以改变材料的电学性质。
下面将介绍一种典型的扩散工艺流程。
首先是准备工作,包括物料准备、设备检查和工艺参数设置。
物料准备包括半导体晶片、扩散材料和掩膜材料的选择与准备。
设备检查主要是确保扩散炉和扩散源的正常运行状态。
工艺参数设置根据掺杂要求和材料特性,确定扩散温度、时间和气氛等工艺参数。
其次是扩散源的制备,扩散源一般是通过在高温条件下将掺杂材料与半导体材料反应生成的。
按照所需的掺杂浓度和材料属性,可以选择不同的扩散源。
通常情况下,将掺杂材料和半导体材料混合,并加入任何必要的添加剂,形成均匀的混合物。
然后,将混合物放入扩散源槽或坩埚中,在高温条件下进行预热、热分解和扩散源的形成。
形成的扩散源粉末可以直接用于扩散过程,也可以制备成片状等形状。
接下来是掩模制备,掩模是指在扩散过程中所需的模板,用于限制掺杂区域的形成。
一般使用光刻技术将掩模图案转移到掩膜材料上,形成掩模。
然后,将掩模放置在待扩散的半导体晶片表面,并通过光刻和显影等步骤将掩模图案转移到晶片表面。
扩散工艺是在控制的温度条件下进行的,常用的扩散方式有氧化物扩散和固相扩散。
以氧化物扩散为例,首先将掺杂源和半导体片放置在扩散炉中,然后控制炉温使其达到扩散温度。
在扩散温度下,掺杂源释放出掺杂原子,这些原子通过热扩散作用在半导体片中形成掺杂区域。
扩散时间的长短决定了掺杂的深度和浓度。
固相扩散的工艺流程类似,只是没有氧化物参与,直接通过固态反应实现掺杂。
扩散完成后,进行清洗和后续处理。
清洗是为了去除掉表面的杂质和残留的化学物质,以及掩模材料。
清洗可以使用不同的溶液和超声波等方法。
后续处理包括表面加工、封装和测试等步骤,以完成集成电路的制造。
总的来说,扩散工艺是集成电路制造中的一项关键工艺,通过控制温度、时间和掺杂原料,将掺杂原子引入半导体材料中,实现电学性质的改变。
扩散工艺知识

第三章 扩散工艺在前面“材料工艺”一章,我们就曾经讲过一种叫“三重扩散”的工艺,那是对衬底而言相同导电类型杂质扩散.这样的同质高浓度扩散,在晶体管制造中还常用来作欧姆接触,如做在基极电极引出处以降低接触电阻.除了改变杂质浓度,扩散的另一个也是更主要的一个作用,是在硅平面工艺中用来改变导电类型,制造PN 结。
第一节 扩散原理扩散是一种普通的自然现象,有浓度梯度就有扩散。
扩散运动是微观粒子原子或分子热运动的统计结果.在一定温度下杂质原子具有一定的能量,能够克服某种阻力进入半导体,并在其中作缓慢的迁移运动。
一.扩散定义在高温条件下,利用物质从高浓度向低浓度运动的特性,将杂质原子以一定的可控性掺入到半导体中,改变半导体基片或已扩散过的区域的导电类型或表面杂质浓度的半导体制造技术,称为扩散工艺。
二.扩散机构杂质向半导体扩散主要以两种形式进行:1.替位式扩散一定温度下构成晶体的原子围绕着自己的平衡位置不停地运动。
其中总有一些原子振动得较厉害,有足够的能量克服周围原子对它的束缚,跑到其它地方,而在原处留下一个“空位".这时如有杂质原子进来,就会沿着这些空位进行扩散,这叫替位式扩散。
硼(B )、磷(P )、砷(As )等属此种扩散。
2.间隙式扩散构成晶体的原子间往往存在着很大间隙,有些杂质原子进入晶体后,就从这个原子间隙进入到另一个原子间隙,逐次跳跃前进.这种扩散称间隙式扩散.金、铜、银等属此种扩散。
三. 扩散方程扩散运动总是从浓度高处向浓度低处移动。
运动的快慢与温度、浓度梯度等有关。
其运动规律可用扩散方程表示,具体数学表达式为:N D tN 2∇=∂∂ (3—1) 在一维情况下,即为: 22xN D t N ∂∂=∂∂ (3-2) 式中:D 为扩散系数,是描述杂质扩散运动快慢的一种物理量;N 为杂质浓度;t 为扩散时间;x 为扩散到硅中的距离。
四.扩散系数杂质原子扩散的速度同扩散杂质的种类和扩散温度有关.为了定量描述杂质扩散速度,引入扩散系数D 这个物理量,D 越大扩散越快。
扩散工艺
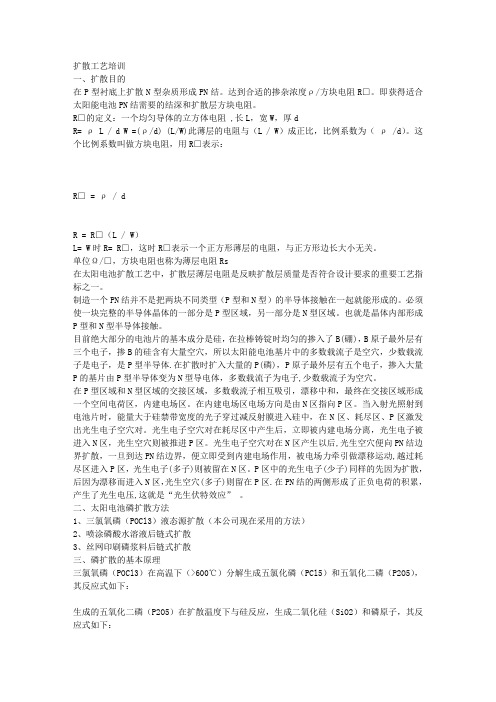
扩散工艺培训一、扩散目的在P型衬底上扩散N型杂质形成PN结。
达到合适的掺杂浓度ρ/方块电阻R□。
即获得适合太阳能电池PN结需要的结深和扩散层方块电阻。
R□的定义:一个均匀导体的立方体电阻 ,长L,宽W,厚dR= ρ L / d W =(ρ/d) (L/W)此薄层的电阻与(L / W)成正比,比例系数为(ρ /d)。
这个比例系数叫做方块电阻,用R□表示:R□ = ρ / dR = R□(L / W)L= W时R= R□,这时R□表示一个正方形薄层的电阻,与正方形边长大小无关。
单位Ω/□,方块电阻也称为薄层电阻Rs在太阳电池扩散工艺中,扩散层薄层电阻是反映扩散层质量是否符合设计要求的重要工艺指标之一。
制造一个PN结并不是把两块不同类型(P型和N型)的半导体接触在一起就能形成的。
必须使一块完整的半导体晶体的一部分是P型区域,另一部分是N型区域。
也就是晶体内部形成P型和N型半导体接触。
目前绝大部分的电池片的基本成分是硅,在拉棒铸锭时均匀的掺入了B(硼),B原子最外层有三个电子,掺B的硅含有大量空穴,所以太阳能电池基片中的多数载流子是空穴,少数载流子是电子,是P型半导体.在扩散时扩入大量的P(磷),P原子最外层有五个电子,掺入大量P的基片由P型半导体变为N型导电体,多数载流子为电子,少数载流子为空穴。
在P型区域和N型区域的交接区域,多数载流子相互吸引,漂移中和,最终在交接区域形成一个空间电荷区,内建电场区。
在内建电场区电场方向是由N区指向P区。
当入射光照射到电池片时,能量大于硅禁带宽度的光子穿过减反射膜进入硅中,在N区、耗尽区、P区激发出光生电子空穴对。
光生电子空穴对在耗尽区中产生后,立即被内建电场分离,光生电子被进入N区,光生空穴则被推进P区。
光生电子空穴对在N区产生以后,光生空穴便向PN结边界扩散,一旦到达PN结边界,便立即受到内建电场作用,被电场力牵引做漂移运动,越过耗尽区进入P区,光生电子(多子)则被留在N区。
半导体不同扩散工艺的特点

半导体不同扩散工艺的特点
半导体的扩散技术是将特定种类的杂质原子在半导体晶体中扩散,并改变半导体材料的导电性质。
半导体扩散工艺主要分为以下几种:
1. 扩散氧化法:将硅片加热至高温,使气体中的氧气(O2)分解,产生的氧分子与硅片表面反应,生成二氧化硅(SiO2),从而控制扩散层的深度和宽度。
该工艺的特点是扩散面积大,扩散层深度均匀,但是扩散速度较慢,适用于生产较高质量要求的器件。
2. 氧化掩蔽扩散法(LOCOS):利用化学气相沉积或物理气相沉积在硅片表面沉积一层硅氧化物光刻膜(LOCOS法)或硅酸盐膜(LOCAT法),通过扩散杂质(如磷、硼等)和高温处理,使膜下方的硅衬底发生晶格变形和氧化,形成带孔的氧化硅层,从而形成了扩散区域。
该工艺特点是可制造出复杂的器件结构,但是对于大尺寸芯片来说,芯片表面会过度弯曲,造成拉应力,最终导致母片变形,影响器件性能和可靠性。
3. 氧化铝扩散法:在扩散前利用化学气相沉积在硅片表面沉积一层氧化铝膜,再在这层氧化铝膜上打一个小口(缺口),通过缺口在晶体下面扩散,形成扩散区。
该工艺特点是可保护芯片表面,避免造成晶片变形,但是扩散层较浅,仅适用于制造器件的浅扩散层。
4. 离子注入法:利用离子加速器将杂质离子注入到硅晶体中,形成扩散区。
该
种方法的特点是扩散速度快,扩散深度大,适用于生产器件的深扩散层,但是也存在与晶片表面反应的问题,同时也会导致结果分布不均匀的问题。
总之,选择适当的扩散工艺需要根据所需器件的性质和质量要求来确定。
扩散工艺和离子注入
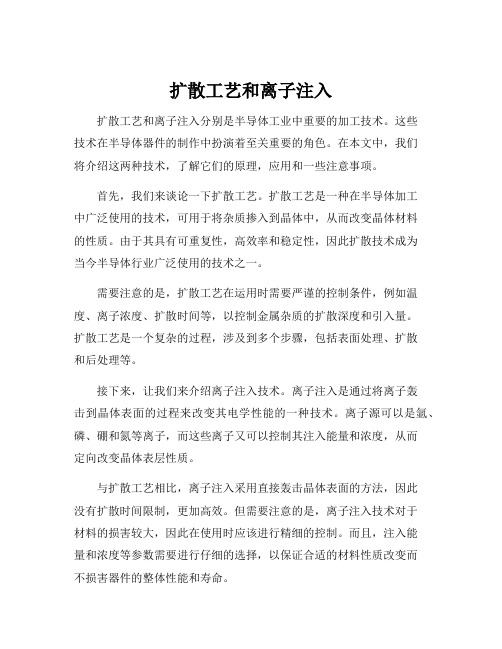
扩散工艺和离子注入
扩散工艺和离子注入分别是半导体工业中重要的加工技术。
这些
技术在半导体器件的制作中扮演着至关重要的角色。
在本文中,我们
将介绍这两种技术,了解它们的原理,应用和一些注意事项。
首先,我们来谈论一下扩散工艺。
扩散工艺是一种在半导体加工
中广泛使用的技术,可用于将杂质掺入到晶体中,从而改变晶体材料
的性质。
由于其具有可重复性,高效率和稳定性,因此扩散技术成为
当今半导体行业广泛使用的技术之一。
需要注意的是,扩散工艺在运用时需要严谨的控制条件,例如温度、离子浓度、扩散时间等,以控制金属杂质的扩散深度和引入量。
扩散工艺是一个复杂的过程,涉及到多个步骤,包括表面处理、扩散
和后处理等。
接下来,让我们来介绍离子注入技术。
离子注入是通过将离子轰
击到晶体表面的过程来改变其电学性能的一种技术。
离子源可以是氩、磷、硼和氮等离子,而这些离子又可以控制其注入能量和浓度,从而
定向改变晶体表层性质。
与扩散工艺相比,离子注入采用直接轰击晶体表面的方法,因此
没有扩散时间限制,更加高效。
但需要注意的是,离子注入技术对于
材料的损害较大,因此在使用时应该进行精细的控制。
而且,注入能
量和浓度等参数需要进行仔细的选择,以保证合适的材料性质改变而
不损害器件的整体性能和寿命。
总之,扩散工艺和离子注入技术是现代半导体器件制造中必不可少的工艺,对于半导体行业的发展和进步有着重要的作用。
因此,在使用这些技术时,一定要掌握其原理,选择合适的条件并特别注意细节,从而确保制造出高质量、可靠的半导体器件。
扩散工艺的化学原理

扩散工艺的化学原理扩散工艺是一种将固体材料中的原子或分子在另一固体材料中扩散的方式。
它是一种重要的材料加工技术,被广泛应用于半导体行业、材料科学、电子设备制造等领域。
1.气相扩散:气相扩散是一种将气体原子或分子从高浓度区域扩散到低浓度区域的过程。
它广泛应用于半导体制造中。
在气相扩散过程中,气体原子或分子通过与被处理材料的表面发生化学反应来扩散。
这种化学反应的速率由固体表面与气体界面之间的反应速率决定。
例如,氮化硅薄膜的制备常采用氨气(NH3)与硅表面上的硅原子发生反应,形成氮化硅层。
氨气的浓度差异使其向硅表面扩散,反应的速率主要取决于氨气与硅表面反应的速率。
2.液相扩散:液相扩散是指液体中原子或分子通过扩散来实现的过程,这种扩散通常发生在固体表面和液体之间。
液相扩散常用于金属合金的制备。
在液相扩散过程中,金属原子在固相间扩散,并在固体和液体相界面处重新结晶。
液体中的浓度差异是驱动液相扩散的主要原因。
例如,当固体镍和固体铬在液体中混合时,镍原子和铬原子会相互扩散使合金形成均匀的镍铬分布。
这种液相扩散过程中,镍原子和铬原子之间的化学反应被加速,形成新的镍铬化合物。
3.固相扩散:固相扩散是指固体材料中的原子或分子通过固体晶界、点缺陷、空位等的移动来实现的扩散过程。
固相扩散通常发生在材料的固态结构中,是一种非常缓慢的过程。
固相扩散的速率取决于晶体中原子或分子的浓度差异以及晶界和缺陷的性质。
例如,金属在高温下会发生固相扩散。
当金属中的原子在晶界或点缺陷处移动时,它们会在固态结构中扩散,从而改变金属的组织结构和性能。
这种固相扩散对于合金的制备和材料的加工具有重要意义。
总之,扩散工艺是通过利用浓度差异从而使固体材料中的原子或分子在其它材料中扩散的一种技术。
气相扩散、液相扩散和固相扩散是扩散工艺的常见形式,它们的化学原理基于热运动和化学反应,其中浓度差异是驱动扩散的主要力量。
这些扩散过程对于材料的合成、改性和加工具有重要作用,广泛应用于各个领域。
- 1、下载文档前请自行甄别文档内容的完整性,平台不提供额外的编辑、内容补充、找答案等附加服务。
- 2、"仅部分预览"的文档,不可在线预览部分如存在完整性等问题,可反馈申请退款(可完整预览的文档不适用该条件!)。
- 3、如文档侵犯您的权益,请联系客服反馈,我们会尽快为您处理(人工客服工作时间:9:00-18:30)。
3.4 影响杂质分布的其他因素
3.4.5 二维扩散(横向扩散)
实际扩散:杂质在垂直Si表面扩散的同时,也进行平 行Si表面的横向扩散。
横向扩散深度: ①当硅内的浓度比Ns小两
个数量级,为纵向扩散的 75%-85%。 ②高浓度掺杂,则为 纵向扩散的65%- 70%。
3.4 影响杂质分布的其他因素
横向扩散的影响 ①横向穿通效应; ②影响结电容。
3.5 扩散工艺
按扩散系统:开管、闭管、箱法; 按杂质源:固态,液态,气态;
:
3.5 扩散工艺
3.5.1 固态源扩散 组成:主要是掺杂元素的氧化物,如B2O3、P2O5、BN 形态:片状、粉状、乳胶状、薄膜(掺杂的多晶硅) 扩散方式: ①开管: 片状和粉状,与Si平分开,不接触。 ②箱法:杂质源和Si片放在有盖的石英箱里。
的扩散深度大于发射区(P扩散形成)外的基区扩散深 度。 推进(陷落)机理: ① P+ + V-2 → P+V-2
P+V-2 → P+ + V- + e 大量过饱和V-扩散相当远,深入基区,增强了B
的扩散速度; ② P+V-2的分解导致大量的间隙Si,也增强了B扩散。
npn晶体管硼和磷分布的计算结果与实测结果
特点:恒定表面源扩散,即NS=NSi;兼有开管和闭管的优 点。
③涂源法:将掺有扩散杂质的乳胶源旋涂在Si片上。 特点:适于各种扩散杂质。
④薄膜法:用CVD方法先在Si片上淀积一层含扩散杂质的薄 膜,如SiO2、Poly-Si、Si3N4。
特点:工艺灵活。
3.5 扩散工艺
3.5.2 液态源扩散 掺杂源:液态化合物,如POCl3、PCl3、AsCl3等。 方法:通过携带气体(N2)进入扩散炉; 特点:掺杂量控制精确,均匀性、重复性好。
3.4 影响杂质分布的其他因素
总的扩散系数
①低掺杂(本征扩散系数) Di= Di0+ Di++ Di-+ Di2-
②高掺杂(非本征扩散系数) De= Di0+ Di+(p/ni)+ Di-(n/ni)+ Di2-(n/ni)2 ni-本征载流子浓度;p-空穴浓度;n-电子浓度
引自李乃平《微电子器件工艺》
3.4 影响杂质分布的其他因素
3.4.1 硅中的点缺陷
缺陷:任何对周期晶格形成扰动都称为“缺陷”。 ①面缺陷:层错、多晶的晶粒间界等; ②线缺陷:位错等; ③点缺陷:杂质原子产生的缺陷,如空位、间隙、间隙
原子团。 空位缺陷:晶格上缺失一个Si原子。主要包括4种: ①中性空位V0 ②带一个负电荷的空位V- ③带两个负电
PCl5 +O2→ P2O5+Cl2 P2O5的性质:白色粉末,熔点420 ℃,300 ℃升华,
吸水性强。
3.5 扩散工艺
石英管
硅晶片
电炉
N2 电炉
液态杂质源
O2
排气口
3.6 扩散工艺的发展
自学
3.7 扩散层的质量参数
包括:结深xJ ,方块电阻R□(RS) ,表面浓度 NS, 击穿电压BV等。
能溶于酸和醇。
3.5 扩散工艺
2. P掺杂源
①固态:粉状P2O5;陶瓷片 P3N5、Si·P2O7+Al(PO3)3
P3N5 +O2→ P2O5+N2
P2O5+Si →P+SiO2;
P2O5+SiO2 →PSG(磷硅玻璃)
②液态:POCl3、PCl5、PBr3、P(CH3O)3。
Байду номын сангаас
高温(> 600℃)下,POCl3 → P2O5+PCl5
因此,其扩散速度比单纯替位方式快。 Sb的氧化扩散是减弱的:Sb是替位扩散为主,间隙Si
与空位复合,减小了空位浓度。 As氧化增强低于B、P:替位-间隙两种扩散作用相
当。
B、P的扩散系数与晶向、气氛的关系
3.4 影响杂质分布的其他因素
3.4.4 发射区推进(陷落)效应 实验现象:NPN 管的工艺中,发射区下方的内基区B
x j D eE/ 2kT
可见,温度对结深的影响是很大的。精确地控制扩 散温度(炉温)是搞好扩散工艺的关键之一。
3.7 扩散层的质量参数
2、扩散时间t
在实际工艺中:
3.4 影响杂质分布的其他因素
3.4.3 氧化增强扩散(OED)
实验结果:P、B、As等在氧化气氛中的扩散增强。
3.4 影响杂质分布的其他因素
3.4.3 氧化增强扩散(OED)
氧化增强机理——存在替位-间隙交替的双扩散: 在氧化过程中,Si-SiO2界面产生的大量间隙Si与
替位B、P等相互作用,使替位B、P变为间隙B、P; 间隙B、P在近邻晶格有空位时以替位方式扩散,无空 位时以间隙方式扩散;B、P的间隙扩散作用更强;
荷的空位V-2 ④带一个正电荷的空位V+
图3.13 硅中空位的能带图
3.4 影响杂质分布的其他因素
3.4.2 扩散系数与杂质浓度的关系
实验证明: ① 当N<ni,D与N无关,称为本征扩散系数(Di); ② 当N>ni,D与N有关,称为非本证扩散系数(De)。 扩散系数与空位浓度成正比 空位浓度与掺杂浓度的关系: ①V0与N无关 ;②高掺杂施主可使V-和V-2浓度增加; ③高掺杂受主可使V+浓度增加。 各种空位以不同方式与离化的掺杂原子相互作用,从 而具有不同的ΔE(激活能)和D。
3.5.3 气态源扩散 掺杂源:气态化合物,如PH3、AsH3、B2H6、BCl等;
毒性较大,需用N2、Ar2稀释到1%-2%。 特点:相比液态源扩散,操作更方便。
3.5 扩散工艺
3.5.4 杂质源 1. B掺杂源 固态:粉状B2O3 、BN;陶瓷片BN、 B2O3+SiO2+Al2O3
BN+O2→ B2O3+N2 B2O3+Si →B+SiO2 B2O3+SiO2 →BSG(硼硅玻璃) B2O3的性质:无色粉末、熔点577℃,沸点1860℃,
①结深xj 定义:pn结的几何位置与扩散层表面的距离。 对erfc分布和高斯分布,其结深近似有相同的表达
式:
x j A Dt
3.7 扩散层的质量参数
影响xj的工艺因素: 1、扩散温度T
扩散系数D对结深的影响就体现在扩散温度T的影响 上,对替位式扩散来说(制结的掺杂扩散是替位扩 散),D=D0e-ΔE/kT,则