磁控溅射镀膜技术的发展及应用_马景灵
无靶直流磁控溅射技术在电镀领域中的应用
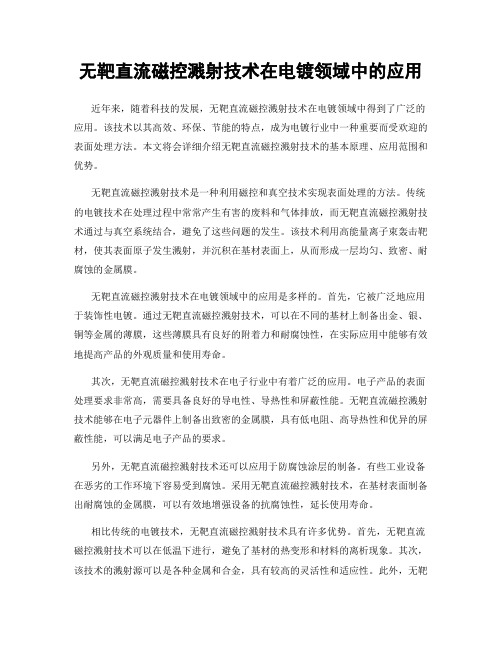
无靶直流磁控溅射技术在电镀领域中的应用近年来,随着科技的发展,无靶直流磁控溅射技术在电镀领域中得到了广泛的应用。
该技术以其高效、环保、节能的特点,成为电镀行业中一种重要而受欢迎的表面处理方法。
本文将会详细介绍无靶直流磁控溅射技术的基本原理、应用范围和优势。
无靶直流磁控溅射技术是一种利用磁控和真空技术实现表面处理的方法。
传统的电镀技术在处理过程中常常产生有害的废料和气体排放,而无靶直流磁控溅射技术通过与真空系统结合,避免了这些问题的发生。
该技术利用高能量离子束轰击靶材,使其表面原子发生溅射,并沉积在基材表面上,从而形成一层均匀、致密、耐腐蚀的金属膜。
无靶直流磁控溅射技术在电镀领域中的应用是多样的。
首先,它被广泛地应用于装饰性电镀。
通过无靶直流磁控溅射技术,可以在不同的基材上制备出金、银、铜等金属的薄膜,这些薄膜具有良好的附着力和耐腐蚀性,在实际应用中能够有效地提高产品的外观质量和使用寿命。
其次,无靶直流磁控溅射技术在电子行业中有着广泛的应用。
电子产品的表面处理要求非常高,需要具备良好的导电性、导热性和屏蔽性能。
无靶直流磁控溅射技术能够在电子元器件上制备出致密的金属膜,具有低电阻、高导热性和优异的屏蔽性能,可以满足电子产品的要求。
另外,无靶直流磁控溅射技术还可以应用于防腐蚀涂层的制备。
有些工业设备在恶劣的工作环境下容易受到腐蚀。
采用无靶直流磁控溅射技术,在基材表面制备出耐腐蚀的金属膜,可以有效地增强设备的抗腐蚀性,延长使用寿命。
相比传统的电镀技术,无靶直流磁控溅射技术具有许多优势。
首先,无靶直流磁控溅射技术可以在低温下进行,避免了基材的热变形和材料的离析现象。
其次,该技术的溅射源可以是各种金属和合金,具有较高的灵活性和适应性。
此外,无靶直流磁控溅射技术的工艺稳定性好,制备的金属膜均匀且致密,具有较高的附着力和耐腐蚀性。
在实际应用中,我们还需要注意到一些问题。
首先,无靶直流磁控溅射技术需要较为复杂的设备和专业的操作技术,因此在使用时需要具备相关的知识和经验。
磁控溅射技术在薄膜材料制备中的应用
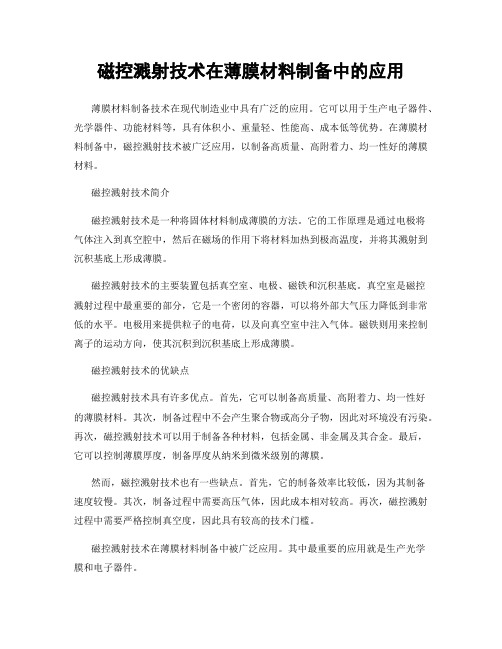
磁控溅射技术在薄膜材料制备中的应用薄膜材料制备技术在现代制造业中具有广泛的应用。
它可以用于生产电子器件、光学器件、功能材料等,具有体积小、重量轻、性能高、成本低等优势。
在薄膜材料制备中,磁控溅射技术被广泛应用,以制备高质量、高附着力、均一性好的薄膜材料。
磁控溅射技术简介磁控溅射技术是一种将固体材料制成薄膜的方法。
它的工作原理是通过电极将气体注入到真空腔中,然后在磁场的作用下将材料加热到极高温度,并将其溅射到沉积基底上形成薄膜。
磁控溅射技术的主要装置包括真空室、电极、磁铁和沉积基底。
真空室是磁控溅射过程中最重要的部分,它是一个密闭的容器,可以将外部大气压力降低到非常低的水平。
电极用来提供粒子的电荷,以及向真空室中注入气体。
磁铁则用来控制离子的运动方向,使其沉积到沉积基底上形成薄膜。
磁控溅射技术的优缺点磁控溅射技术具有许多优点。
首先,它可以制备高质量、高附着力、均一性好的薄膜材料。
其次,制备过程中不会产生聚合物或高分子物,因此对环境没有污染。
再次,磁控溅射技术可以用于制备各种材料,包括金属、非金属及其合金。
最后,它可以控制薄膜厚度,制备厚度从纳米到微米级别的薄膜。
然而,磁控溅射技术也有一些缺点。
首先,它的制备效率比较低,因为其制备速度较慢。
其次,制备过程中需要高压气体,因此成本相对较高。
再次,磁控溅射过程中需要严格控制真空度,因此具有较高的技术门槛。
磁控溅射技术在薄膜材料制备中被广泛应用。
其中最重要的应用就是生产光学膜和电子器件。
在光学膜的制备过程中,磁控溅射技术被用来生产非常均匀、透明度好的多层光学膜。
这些薄膜可以用来制造太阳能电池板、平面显示器、灯具等产品,具有较好的光学性能。
在电子器件制备过程中,磁控溅射技术被用来生产透明电极、导电膜等材料。
这些薄膜在晶体管、场效应管、LED等器件中得到了广泛应用,提高了器件的性能。
此外,磁控溅射技术还可以生产用于陶瓷、橡胶、塑料等领域的高性能薄膜。
这些膜具有附着力好、耐磨性强、抗腐蚀性能好等特点,可以用于提高产品的性能和寿命。
磁控溅射技术进展及应用
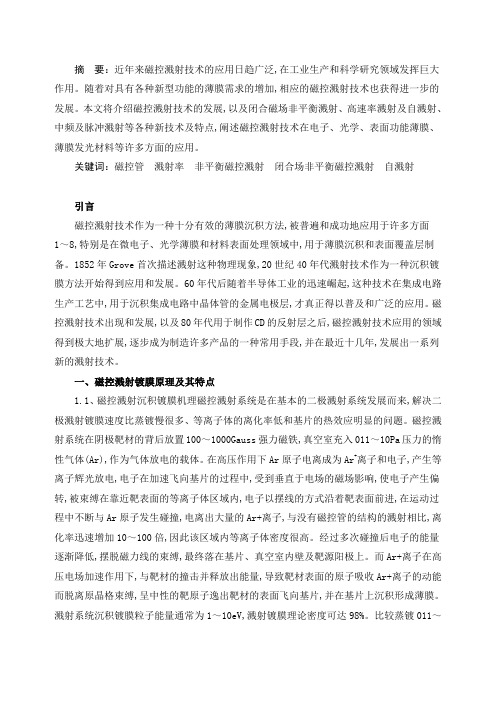
摘要:近年来磁控溅射技术的应用日趋广泛,在工业生产和科学研究领域发挥巨大作用。
随着对具有各种新型功能的薄膜需求的增加,相应的磁控溅射技术也获得进一步的发展。
本文将介绍磁控溅射技术的发展,以及闭合磁场非平衡溅射、高速率溅射及自溅射、中频及脉冲溅射等各种新技术及特点,阐述磁控溅射技术在电子、光学、表面功能薄膜、薄膜发光材料等许多方面的应用。
关键词:磁控管溅射率非平衡磁控溅射闭合场非平衡磁控溅射自溅射引言磁控溅射技术作为一种十分有效的薄膜沉积方法,被普遍和成功地应用于许多方面1~8,特别是在微电子、光学薄膜和材料表面处理领域中,用于薄膜沉积和表面覆盖层制备。
1852年Grove首次描述溅射这种物理现象,20世纪40年代溅射技术作为一种沉积镀膜方法开始得到应用和发展。
60年代后随着半导体工业的迅速崛起,这种技术在集成电路生产工艺中,用于沉积集成电路中晶体管的金属电极层,才真正得以普及和广泛的应用。
磁控溅射技术出现和发展,以及80年代用于制作CD的反射层之后,磁控溅射技术应用的领域得到极大地扩展,逐步成为制造许多产品的一种常用手段,并在最近十几年,发展出一系列新的溅射技术。
一、磁控溅射镀膜原理及其特点1.1、磁控溅射沉积镀膜机理磁控溅射系统是在基本的二极溅射系统发展而来,解决二极溅射镀膜速度比蒸镀慢很多、等离子体的离化率低和基片的热效应明显的问题。
磁控溅射系统在阴极靶材的背后放置100~1000Gauss强力磁铁,真空室充入011~10Pa压力的惰性气体(Ar),作为气体放电的载体。
在高压作用下Ar原子电离成为Ar+离子和电子,产生等离子辉光放电,电子在加速飞向基片的过程中,受到垂直于电场的磁场影响,使电子产生偏转,被束缚在靠近靶表面的等离子体区域内,电子以摆线的方式沿着靶表面前进,在运动过程中不断与Ar原子发生碰撞,电离出大量的Ar+离子,与没有磁控管的结构的溅射相比,离化率迅速增加10~100倍,因此该区域内等离子体密度很高。
磁控溅射薄膜制备工艺及其应用研究
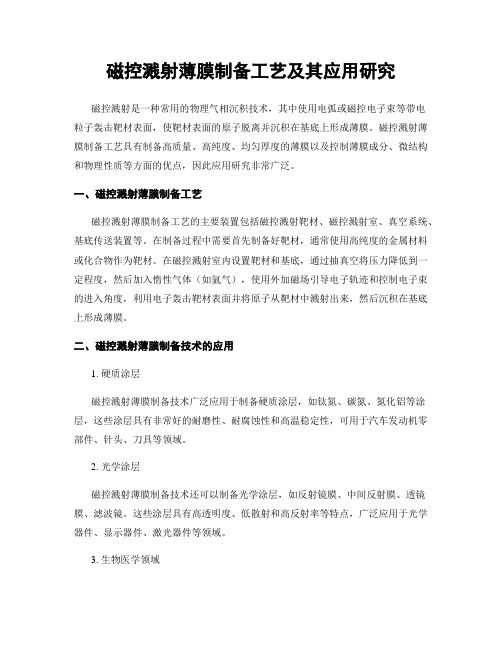
磁控溅射薄膜制备工艺及其应用研究磁控溅射是一种常用的物理气相沉积技术,其中使用电弧或磁控电子束等带电粒子轰击靶材表面,使靶材表面的原子脱离并沉积在基底上形成薄膜。
磁控溅射薄膜制备工艺具有制备高质量、高纯度、均匀厚度的薄膜以及控制薄膜成分、微结构和物理性质等方面的优点,因此应用研究非常广泛。
一、磁控溅射薄膜制备工艺磁控溅射薄膜制备工艺的主要装置包括磁控溅射靶材、磁控溅射室、真空系统、基底传送装置等。
在制备过程中需要首先制备好靶材,通常使用高纯度的金属材料或化合物作为靶材。
在磁控溅射室内设置靶材和基底,通过抽真空将压力降低到一定程度,然后加入惰性气体(如氩气),使用外加磁场引导电子轨迹和控制电子束的进入角度,利用电子轰击靶材表面并将原子从靶材中溅射出来,然后沉积在基底上形成薄膜。
二、磁控溅射薄膜制备技术的应用1. 硬质涂层磁控溅射薄膜制备技术广泛应用于制备硬质涂层,如钛氮、碳氮、氮化铝等涂层,这些涂层具有非常好的耐磨性、耐腐蚀性和高温稳定性,可用于汽车发动机零部件、针头、刀具等领域。
2. 光学涂层磁控溅射薄膜制备技术还可以制备光学涂层,如反射镜膜、中间反射膜、透镜膜、滤波镜。
这些涂层具有高透明度、低散射和高反射率等特点,广泛应用于光学器件、显示器件、激光器件等领域。
3. 生物医学领域磁控溅射薄膜制备技术还可以制备生物医学材料,如医用钢、医用钛、金属合金等薄膜,这些薄膜具有良好的生物相容性和生物可降解性,可用于人工骨骼、人工关节和牙科修补材料等方面。
4. 电子器件磁控溅射薄膜制备技术还可以制备电子器件材料,如导电膜、隔离膜、介质膜等,这些薄膜具有优良的电学性能和化学稳定性,可用于半导体器件、光电子器件等领域。
5. 其他应用除了以上应用之外,磁控溅射薄膜制备技术还可以用于制备防腐蚀、阻燃和防弹涂层,磁记忆材料、人工晶体、存储介质、光电子元器件、传感器等领域。
三、磁控溅射薄膜制备技术的优势和发展方向磁控溅射薄膜制备技术具有许多优势,如具有高质量、高可控性、高纯度、良好的附着性、高重复性等,与传统的化学气相沉积、离子束沉积、溅射沉积等技术相比具有明显的优势。
磁控溅射技术及其应用

•
•
•
三、磁控溅射镀膜技术发展
3、反应磁控溅射技术
• 靶中毒:迟滞现象使反应气体与靶材作用生成的化合物覆盖在靶材表面,积 累大量的正电荷无法中和,在靶材表面建立越来越高的正电位,阴极位降区 的电位随之降低,最终阴极位降区电位降减小到零,放电熄灭,溅射停止, 这种现象称为靶中毒。 • 打弧:当靶材表面化合物层电位足够高时,进而发生击穿,巨大的电流流过 击穿点,形成弧光放电,导致局部靶面瞬间被加热到很高的温度,发生喷射
可以制备成靶材。磁控溅射镀膜在相互垂直的磁场和电场的双重作用
下,沉积速度快,膜层致密且与基片附着性好,非常适合于大批量且高 效率的工业化生产。
二、磁控溅射镀膜技术原理
2、磁控溅射技术
• 磁控溅射的工作原理是在辉光放电 的两极之间引入磁场,电子受电场 加速作用的同时受到磁场的束缚作 用,运动轨迹成摆线,增加了电子
三、磁控溅射镀膜技术发展
5、脉冲磁控溅射技术
• 脉冲磁控溅射是采用矩形波电压的脉冲电源
代替传统直流电源进行磁控溅射沉积。脉冲
磁控溅射技术可以有效的抑制电弧产生进而 消除由此产生的薄膜缺陷,同时可以提高溅 射沉积速率,降低沉积温度等一系列显著优
点。
• 脉冲可分为双向脉冲和单向脉冲。双向脉冲 在一个周期内存在正电压和负电压两个阶段 ,在负电压段,电源工作于靶材的溅射,正
射的同时,阳极靶完成表面清洁,
如此周期性地变换磁控靶极性,就 产生了“自清洁”效应。
四、磁控溅射镀膜技术的发展
6、磁控溅射新发展
•
高速溅射:高速溅射能够实现高速率沉积,可以缩短溅射镀膜的时间,提高 工业生产的效率;有可能替代目前对环境有污染的电镀工艺。
•
自溅射:当溅射率非常高,以至于在完全没有惰性气体的情况下也能维持放 电,即是仅用离化的被溅射材料的蒸汽来维持放电,这种磁控溅射被称为自 溅射。被溅射材料的离子化以及减少甚至取消惰性气体,会明显地影响薄膜 形成的机制,加强沉积薄膜过程中合金化和化合物形成中的化学反应。由此 可能制备出新的薄膜材料,发展新的溅射技术,例如在深孔底部自溅射沉积 薄膜。
磁控溅射镀膜技术的研究进展

磁控溅射镀膜技术的研究进展磁控溅射镀膜技术是一种常见的表面处理技术,它可以在各种基材表面制备出具有特殊性能的薄膜层。
随着技术的不断发展,在材料的选择、制备工艺、表面状态分析等方面都有所进步,使得磁控溅射镀膜技术在科学研究和实际应用中发挥着重要作用。
一、磁控溅射镀膜技术的基本原理磁控溅射镀膜技术基于靶材发射金属离子的原理,通过高能离子轰击固体靶材表面,使得金属离子从靶材表面脱离并沉积在基材表面上,从而形成具有一定厚度和化学组成的功能性膜层。
这种技术的独特之处在于可以通过控制靶材的化学成分和溅射工艺参数来调控薄膜层的结构和性能。
其中,靶材的化学成分直接影响薄膜层的组成,而溅射工艺参数如气压、功率、溅射气体种类和气体流量等则直接影响溅射速率和膜层的质量。
二、材料选择与制备工艺磁控溅射镀膜技术广泛用于各种材料的制备,包括金属、合金、氧化物、硅类材料以及半导体材料等。
对于不同的材料,其制备工艺也有所不同。
金属材料通常采用单一金属靶材或合金靶材进行制备,而合金靶材的组成比例可以通过调整靶材的制备工艺来实现。
氧化物材料则需要先将靶材还原成金属或合金形态,然后利用气氛调节技术调节气氛中氧气含量来制备氧化物膜层。
在制备工艺方面,需要进行适当的气氛调节和工艺优化。
例如,在制备合金材料时,需要考虑合金靶材的制备过程中的变形问题,找到合适的制备参数来保证靶材的均匀溅射和膜层的均匀沉积。
三、表面状态分析磁控溅射镀膜技术制备出的膜层常常需要通过表面状态分析来控制其性能,最常用的分析方法是X射线衍射和扫描电镜技术。
X射线衍射技术可以用于分析膜层的结晶性、晶格参数和晶胞结构等信息,从而定量描述膜层的结构和性能。
而扫描电镜技术则可以提供更丰富和直观的表面形貌信息,包括表面粗糙度、形貌变化和结构特征等。
此外,还有一些其他的表面分析技术如原子力显微镜、能量散射光谱和X射线光电子能谱等,可以用于全面分析膜层的属性和性能。
四、应用前景磁控溅射镀膜技术在各种领域都得到了广泛应用,在新能源、医疗、航空航天等高科技产业中有着重要的地位。
磁控真空溅射镀膜
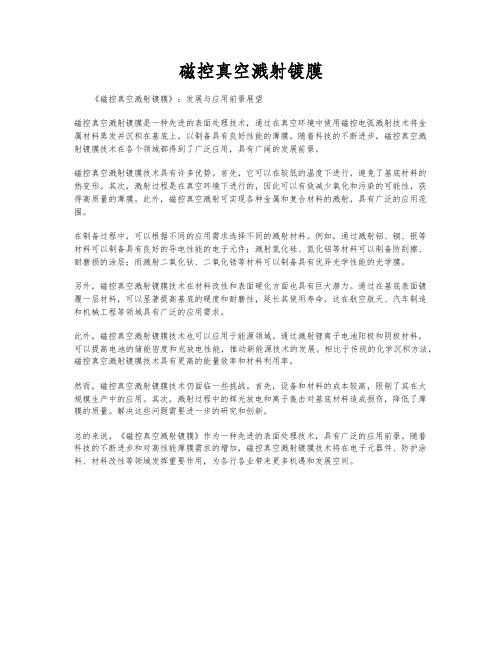
磁控真空溅射镀膜《磁控真空溅射镀膜》:发展与应用前景展望磁控真空溅射镀膜是一种先进的表面处理技术,通过在真空环境中使用磁控电弧溅射技术将金属材料蒸发并沉积在基底上,以制备具有良好性能的薄膜。
随着科技的不断进步,磁控真空溅射镀膜技术在各个领域都得到了广泛应用,具有广阔的发展前景。
磁控真空溅射镀膜技术具有许多优势。
首先,它可以在较低的温度下进行,避免了基底材料的热变形。
其次,溅射过程是在真空环境下进行的,因此可以有效减少氧化和污染的可能性,获得高质量的薄膜。
此外,磁控真空溅射可实现各种金属和复合材料的溅射,具有广泛的应用范围。
在制备过程中,可以根据不同的应用需求选择不同的溅射材料。
例如,通过溅射铝、铜、银等材料可以制备具有良好的导电性能的电子元件;溅射氮化硅、氮化铝等材料可以制备防刮擦、耐磨损的涂层;而溅射二氧化钛、二氧化锆等材料可以制备具有优异光学性能的光学膜。
另外,磁控真空溅射镀膜技术在材料改性和表面硬化方面也具有巨大潜力。
通过在基底表面镀覆一层材料,可以显著提高基底的硬度和耐磨性,延长其使用寿命。
这在航空航天、汽车制造和机械工程等领域具有广泛的应用需求。
此外,磁控真空溅射镀膜技术也可以应用于能源领域。
通过溅射锂离子电池阳极和阴极材料,可以提高电池的储能密度和充放电性能,推动新能源技术的发展。
相比于传统的化学沉积方法,磁控真空溅射镀膜技术具有更高的能量效率和材料利用率。
然而,磁控真空溅射镀膜技术仍面临一些挑战。
首先,设备和材料的成本较高,限制了其在大规模生产中的应用。
其次,溅射过程中的辉光放电和离子轰击对基底材料造成损伤,降低了薄膜的质量。
解决这些问题需要进一步的研究和创新。
总的来说,《磁控真空溅射镀膜》作为一种先进的表面处理技术,具有广泛的应用前景。
随着科技的不断进步和对高性能薄膜需求的增加,磁控真空溅射镀膜技术将在电子元器件、防护涂料、材料改性等领域发挥重要作用,为各行各业带来更多机遇和发展空间。
试谈磁控溅射镀膜技术的研究及发展趋势
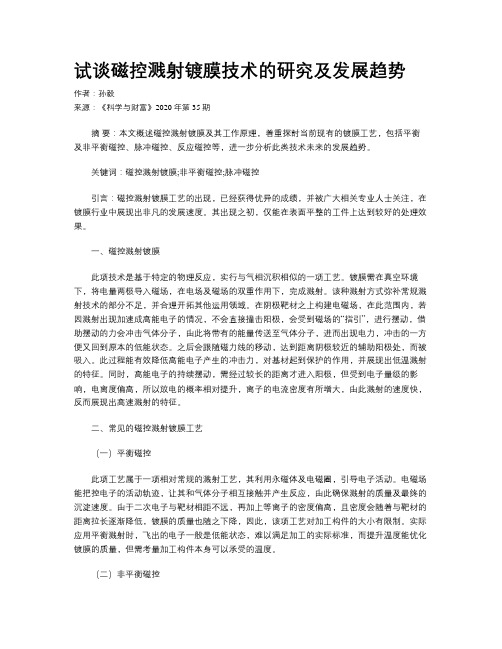
试谈磁控溅射镀膜技术的研究及发展趋势作者:孙毅来源:《科学与财富》2020年第35期摘要:本文概述磁控溅射镀膜及其工作原理,着重探討当前现有的镀膜工艺,包括平衡及非平衡磁控、脉冲磁控、反应磁控等,进一步分析此类技术未来的发展趋势。
关键词:磁控溅射镀膜;非平衡磁控;脉冲磁控引言:磁控溅射镀膜工艺的出现,已经获得优异的成绩,并被广大相关专业人士关注,在镀膜行业中展现出非凡的发展速度。
其出现之初,仅能在表面平整的工件上达到较好的处理效果。
一、磁控溅射镀膜此项技术是基于特定的物理反应,实行与气相沉积相似的一项工艺。
镀膜需在真空环境下,将电量两极导入磁场,在电场及磁场的双重作用下,完成溅射。
该种溅射方式弥补常规溅射技术的部分不足,并合理开拓其他运用领域。
在阴极靶材之上构建电磁场,在此范围内,若因溅射出现加速成高能电子的情况,不会直接撞击阳极,会受到磁场的“指引”,进行摆动,借助摆动的力会冲击气体分子,由此将带有的能量传送至气体分子,进而出现电力,冲击的一方便又回到原本的低能状态。
之后会跟随磁力线的移动,达到距离阴极较近的辅助阳极处,而被吸入。
此过程能有效降低高能电子产生的冲击力,对基材起到保护的作用,并展现出低温溅射的特征。
同时,高能电子的持续摆动,需经过较长的距离才进入阳极,但受到电子量级的影响,电离度偏高,所以放电的概率相对提升,离子的电流密度有所增大,由此溅射的速度快,反而展现出高速溅射的特征。
二、常见的磁控溅射镀膜工艺(一)平衡磁控此项工艺属于一项相对常规的溅射工艺,其利用永磁体及电磁圈,引导电子活动。
电磁场能把控电子的活动轨迹,让其和气体分子相互接触并产生反应,由此确保溅射的质量及最终的沉淀速度。
由于二次电子与靶材相距不远,再加上等离子的密度偏高,且密度会随着与靶材的距离拉长逐渐降低,镀膜的质量也随之下降,因此,该项工艺对加工构件的大小有限制。
实际应用平衡溅射时,飞出的电子一般是低能状态,难以满足加工的实际标准,而提升温度能优化镀膜的质量,但需考量加工构件本身可以承受的温度。
- 1、下载文档前请自行甄别文档内容的完整性,平台不提供额外的编辑、内容补充、找答案等附加服务。
- 2、"仅部分预览"的文档,不可在线预览部分如存在完整性等问题,可反馈申请退款(可完整预览的文档不适用该条件!)。
- 3、如文档侵犯您的权益,请联系客服反馈,我们会尽快为您处理(人工客服工作时间:9:00-18:30)。
溅射镀膜过程主要是将欲沉积成薄膜的材料制成靶材,固定在溅射沉积系统的阴极上,待沉积薄膜的基片放在正对靶面的阳极上。
溅射系统抽至高真空后充入氩气等,在阴极和阳极之间加几千伏的高压,阴阳极之间会产生低压辉光放电。
放电产生的等离子体中,氩气正离子在电场作用下向阴极移动,与靶材表面碰撞,受碰撞而从靶材表面溅射出的靶材原子称为溅射原子,溅射原子的能量一般在一至几十电子伏范围,溅射原子在基片表面沉积而后成膜。
溅射镀膜就是利用低气压辉光放电产生的氩气正离子在电场作用下高速轰击阴极靶材,把靶材中的原子或分子等粒子溅射出而沉积到基片或者工件表面,形成所需的薄膜层。
但是溅射镀膜过程中溅射出的粒子的能量很低,导致成膜速率不高。
磁控溅射技术是为了提高成膜速率在溅射镀膜基础上发展起来的,在靶材表面建立与电场正交的磁场,氩气电离率从0.3%~0.5%提高到了5%~6%,这样就解决了溅射镀膜沉积速率低的问题,是目前工业上精密镀膜的主要方法之一[1]。
可制备成磁控溅射阴极靶材的原料很广,几乎所有金属、合金以及陶瓷材料都可以制备成靶材。
磁控溅射镀膜在相互垂直的磁场和电场的双重作用下,沉积速度快,膜层致密且与基片附着性好,非常适合于大批量且高效率的工业化生产。
1磁控溅射的工艺流程在磁控溅射过程中,具体工艺过程对薄膜性能影响很大,主要工艺流程如下[2]:(1)基片清洗,主要是用异丙醇蒸汽清洗,随后用乙醇、丙酮浸泡基片后快速烘干,以去除表面油污;(2)抽真空,真空须控制在2×104Pa以上,以保证薄膜的纯度;(3)加热,为了除去基片表面水分,提高膜与基片的结合力,需要对基片进行加热,温度一般选择在150℃~200℃之间;(4)氩气分压,一般选择在0.0l~lPa范围内,以满足辉光放电的气压条件;(5)预溅射,预溅射是通过离子轰击以除去靶材表面氧化膜,以免影响薄膜质量;(6)溅射,氩气电离后形成的正离子在正交的磁场和电场的作用下,高速轰击靶材,使溅射出的靶材粒子到达基片表面沉积成膜;(7)退火,薄膜与基片的热膨胀系数有差异,结合力小,退火时薄膜与基片原子相互扩散可以有效提高粘着力。
2磁控溅射镀膜技术的发展近年来磁控溅射技术发展非常迅速,代表性方法有非平衡磁控溅射、反应磁控溅射及高速溅射等等。
平衡磁控溅射技术:即最传统的磁控溅射技术,将永磁体或电磁线圈放到在靶材背后,在靶材表面会形成与电场方向垂直的磁场。
在高压作用下氩气电离成等离子体,Ar+离子经电场加速轰击阴极靶材,靶材二次电子被溅射出,且电子在相互垂直的电场及磁场作用下,被束缚在阴极靶材表面附近,增加了电子与气体碰撞的几率,即增加了氩气电离率,使氩气在低气体下也可维持放电,因而磁控溅射既降低了溅射气体压力,同时也提高了溅射效率及沉积速率[3]。
但传统磁控溅射有一些缺点,比如:低气压放电产生的电子和溅射出的靶材二次电子都被束缚在靶面附近大约60mm的区域内,这样工件只能被安放在靶表面50~100mm的范围内。
这样小的镀膜区间限制了待镀工件的尺寸,较大的工件或装炉量不适合传统方法。
非平衡磁控溅射技术:这种磁控溅射方法部分解决了平衡磁控溅射的不足,是将靶面的等离子体引到靶前200~300mm的范围内,使阳极基片沉浸在等离子体中,减少了粒子移动的距离,离子束起到辅助沉积的作用[4]。
然而单独的非平衡磁控靶在基片上很难沉积出均匀的薄膜层,为此研究人员开发出了多靶非平衡磁控溅射镀膜系统,弥补了单靶非平衡磁控溅射的不足。
反应磁控溅射:随着表面工程技术的发展,越来越多地用到各种化合物薄膜材料。
可以直接使用化合物材料制作的靶材通过溅射来制备化合物薄膜,也可在溅射金属或合金靶材时,通入一定的反应气体,通过发生化学反应制备化合物薄膜,后者被称为反应磁控溅射。
一般来说纯金属作为靶材和气体反应较容易得到高质量的化合物薄膜,因而大多数化合物薄膜是用纯金属为靶材的反应溅磁控射来制备的[5]。
中频磁控溅射:这种镀膜方法是将磁控溅射电源由传统的直流改为中频交流电源。
在溅射过程中,当系统所加电压处在交流电负半周期时,靶材被正离子轰击而溅射,而处于正半周期时,靶材表面被等离子体中的电子轰击而溅射,同时靶材表面累积的正电荷被中和,打弧现象得到抑制。
中频磁控溅射电源的频率通常在10~80kHz之间,频率高,正离子被加速的时间就短,轰击靶材时的能量就低,溅射沉积速率随之下降。
中频磁控溅射系统一般有两个靶,这两个靶周期性轮流作为阴极和阳极,一方面减小了基片溅伤;另一方面也消除了打弧现象。
高速溅射与自溅射:随着工业发展和表面工程的需求,高速溅射与自溅射等新型磁控溅射成膜方法成为镀膜领域新的发展趋势。
高速溅射能够缩短镀膜时间,提高沉积速率,当溅射速率非常高,以至于在没有惰性气体氩气的情况下也能维持辉光放电,这种溅射方法称为自溅射[6]。
高速溅射与自溅射中,被溅射材料的离子、电子化以及减少甚至取消惰性气体,都明显影响薄膜的形成机理,因此,可以制备出特殊性能的薄膜材料。
①基金项目:河南科技大学实验技术开发基金(SY1112008); 科研创新能力培育基金(2012ZCX017)。
作者简介:马景灵(1970—),女,河南科技大学副教授,博士,E-mail:majingling.student@sina.com。
磁控溅射镀膜技术的发展及应用①马景灵 任风章 孙浩亮(河南科技大学材料科学与工程学院 河南洛阳 471023)摘 要:近年来,随着新材料的开发,尤其是薄膜材料的发展和应用,带动磁控溅射沉积技术的飞速发展,在科学研究领域和工业生产中有着不可替代的重要作用。
本文主要介绍了磁控溅射沉积技术的工艺过程及其发展情况,各种主要磁控溅射镀膜技术的特点,并介绍磁控溅射技术在各个领域的主要应用。
关键词:磁控溅射 镀膜 辉光放电中图分类号:G4文献标识码:A文章编号:1673-9795(2013)10(b)-0136-02(下转138页)3磁控溅射镀膜技术的应用磁控溅射镀膜技术主要用于塑料、陶瓷、玻璃、硅片等制品来沉积金属或化合物薄膜,从而获得光亮、美观、经济的塑料、陶瓷表面金属化制品。
装饰、灯具、家具、玩具、工艺美术、装璜等生活领域的制膜技术通常用磁控溅射方法,该方法还应用于军事保护膜、光学产品、磁记录介质、电路印制板、防潮增透膜、耐磨膜、防锈抗蚀等工业领域。
磁控溅射不仅应用于科研及工业领域,已延伸到许多日常生活用品,主要应用在化学气相沉积制膜困难的薄膜制备。
磁控溅射技术在制备电子封装及光学薄膜方面已有多年,特别是先进的中频非平衡磁控溅射技术也已在光学薄膜、透明导电玻璃等方面得到应用。
透明导电玻璃目前应用广泛,如电视电脑平板显示器件、电磁微波与射频屏蔽装置及器件、太阳能电池等[7]。
另外,在光学存储领域中磁控溅射镀膜技术也发挥着很大的作用。
再者,该制膜技术在表面功能薄膜、自润滑薄膜、超硬薄膜等方面的应用也很广泛。
除上述已被大量应用的领域外,磁控溅射镀膜技术还在高温、超导薄膜、巨磁阻薄膜、铁电体薄膜、发光薄膜、形状记忆合金薄膜、太阳能电池等研究方面发挥着重要作用。
4结论磁控溅射镀膜技术由于其显著的优点已经成为制备薄膜的主要技术之一。
非平衡磁控溅射改善了等离子体区域的分布,显著提高了薄膜的质量。
中频溅射镀膜技术的发展有效克服了反应溅射过程中出现的打弧现象,减少了薄膜的结构缺陷,明显提高了薄膜的沉积速率。
高速溅射、自溅射镀膜技术为溅射镀膜开辟了崭新的研究领域。
在未来的研究中,新溅射技术向生活领域的推广、磁控溅射镀膜技术与计算机的结合都将成为研究热点,利用计算机模拟镀膜时的磁场、电场、温度场、以及等离子体的分布,必将能给溅射镀膜技术的发展提供巨大的扩展空间,推动磁控溅射镀膜技术向工业及生活领域转化。
参考文献[1]石永敬,龙思远,王杰,等.直流磁控溅射研究进展[J].材料导报,2008,22(1):65-68.[2]程建平,杨晓东.真空磁控溅射镀膜设备及工艺技术研究[J].电子工业专用设备,2009,38(11):28-31.[3]储志强.国内外磁控溅射靶材的现状及发展趋势[J].金属材料与冶金工程,2011,39(4):44-49.[4]王雷敏,曾小勤,吴国松,等.磁控溅射在镁合金表面处理中的应用[J].铸造技术,2006,27(4):412-415.[5]李芬,朱颖,李刘合,等.磁控溅射技术及其发展[J].真空电子技术,2011(3):43-49.[6]方亮,彭丽萍,杨小飞.磁控溅射制备In掺杂ZnO薄膜及NO2气敏特性分析[J].重庆大学学报,2009,32(9):1002-1005.[7]Brauer G,Szyszka B,Vergohl M. Mag-netron Sputtering-Milestones of 30Years[J].Vacuum,2010:1-6.局,原理是教师给出的,电路板用万能板,布局完全可以由学生设计完成。
由学生设计的电路图可能存在这样、那样的错误或不足,需要教师的进一步指导。
虽然学生和老师都会付出更多的时间与精力,但远比学生一成不变照抄教材原理图,机械地进行组装所获得的知识多更重要的是强化了学生的创新意识,培养了学生的创新能力。
实训中会出现许多新颖的、灵活的设计方案,设计方案五花八门,这样学生具备了更多的灵活应用能力。
在实训过程中采取开放式教学,不断更新实训内容,使学生接触到更新的知识,有利培养学生的创新能力。
实训室在时间、场地、设备等方面进行全方位开放,给学生充分展示自己设计、创新能力的空间,为培养学生的创新能力提供一个必要的条件。
在完成基本教学任务的基础上,鼓励学生进行课外电工电子创作、搞设计,全面调动他们的自主、创新意识。
4多层次的评价,给予成功的体验教师要给学生合理的评价,实训教学的评价方式直接影响到教学成果。
每个学生都希望能够听到对他好的评价。
但是学生的水平差异较大。
所以可以开展多层次的实训、配合多层次的评价,尽可能的给予每个学生成功的机会。
成功的必备要素是自信心和持久性,如果学生在实训教学中取得了成功,也就意味着他们取得了学习的自信心和持久性,也就会给他们带来无穷的学习动力。
所以,教师在实训教学中积极肯定学生的成果,必要时创造成功的条件,让每个学生都获得成功的机会,使学生在享受成功的同时不断地自发的进取、超越自己。
例如,碰到必须进行的较难项目时,可以采用分解法,即将项目易、难两部分分开,将较难部分单独拿出来再细分细讲细练。
项目以激励每一个学生的积极性、主动性为目的,使实训教学取得成功。
多层次的教学内容与评价体系,使较差的学生在较简单的项目,得到了鼓励,同时教师关注学生的进步,对较差学生取得的进步给予及时的、大力的肯定,能进一步增加学生的学习积极性;而优秀的学生在较难的项目中提现了突出能力,自然也要给予肯定,并可以培养这类学生参加国家、省、市级的各类竞赛,取得较好成绩的同时也鞭策了其他学生,从而形成较好的学习氛围,在整体上提高了学生的技能水平。