炼钢厂工艺流程
炼钢工艺流程简介
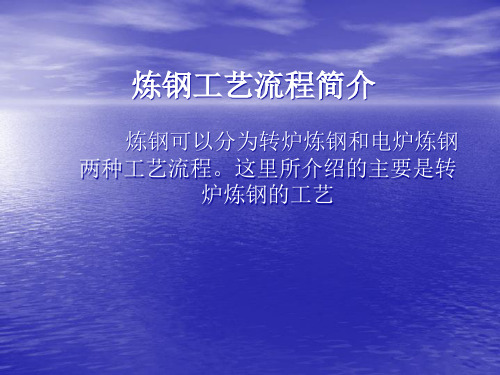
这是火焰切割的场景。
★铸坯的输送
经切割的铸坯利用辊道输送至冷床。这是铸坯 在运输辊道上的场景。
★铸坯的收集(冷床,推钢)
连铸坯通过步进式翻转冷床冷却,然后由推钢 机收集。这就是步进式冷床场景。
★铸坯堆垛
用夹钳将铸坯从冷床上吊至指定的堆放 场地码放成垛,等待外运。
这就是成品铸坯垛场景。
★铸坯外运
★测温取样
每炉钢出钢前必须符合工艺规定的温 度和化学成分的要求,因此冶炼到一定阶 段需要倒炉进行测温取样。温度在现场大 屏幕和主控室计算机上均有显示,试样则 需送到炉前化验室经直读光谱仪分析再报 出结果。
这就是炉前工正在测温取样的场景。
★转炉出钢
出钢过程中要实现的目标是脱氧、脱碳、 脱硫、合金化,为此要向钢包中加入铁合 金、脱氧剂、脱硫剂、覆盖剂等。为了实 现无渣或少渣出钢还得投抛挡渣球。
★向混铁炉兑入铁水
混铁炉是一种贮存铁水的容器,通过 多包铁水混兑可以均匀铁水温度和成分, 为转炉冶炼创造更好的原料条件。此外由 于混铁炉容量较大,它还是调节高炉和转 炉生产节奏的缓冲器。
这就是向混铁炉兑入铁水的场景。
★混铁炉出铁
根据转炉生ห้องสมุดไป่ตู้的需要,混铁炉随时可提供一定量的铁 水。这是混铁炉出铁的场景。出铁量通过铁水车上的电子 秤称量并在大屏幕上显示。
电弧炉炼钢是除转炉炼钢以外最主要的炼钢 方法,与转炉炼钢相比主要区别在于使用的原料 不一样:转炉主原料是铁水,有足够的热源,故 只要吹氧就可以了;而电炉则不同,其主要原料 是废钢,必须输入足够的能量才能将其熔化,而 电弧加热是很成熟的工业化大生产加热方法,故 电弧炉就自然成为以废钢为主原料的炼钢工艺所 选择的炉型了。除此而外现代化超高功率电炉炼 钢与转炉炼钢有许多相似之处,如吹氧氧化、挡 渣出钢、炉外精炼、连铸等二者无大差别。另外, 很多有电炉的厂也建高炉,采取向电炉加入一定 量铁水(一般为30%左右)代替废钢,这就是电 炉工艺与转炉更拉近一步。
炼钢生产过程以及流程图详解(全)
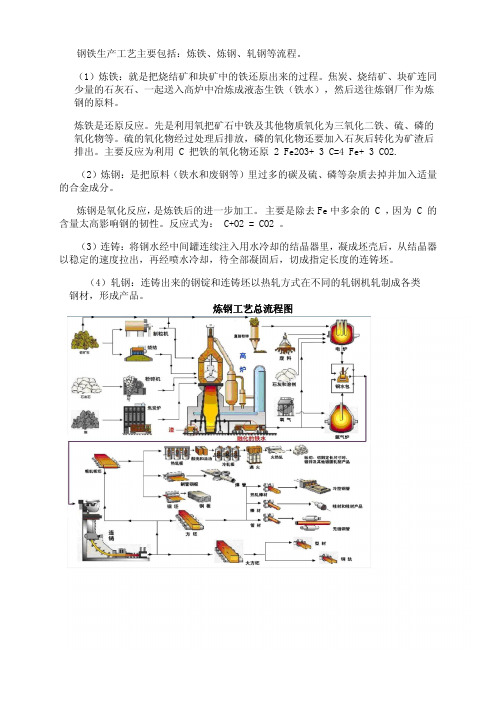
钢铁生产工艺主要包括:炼铁、炼钢、轧钢等流程。
(1)炼铁:就是把烧结矿和块矿中的铁还原出来的过程。
焦炭、烧结矿、块矿连同少量的石灰石、一起送入高炉中冶炼成液态生铁(铁水),然后送往炼钢厂作为炼钢的原料。
炼铁是还原反应。
先是利用氧把矿石中铁及其他物质氧化为三氧化二铁、硫、磷的氧化物等。
硫的氧化物经过处理后排放,磷的氧化物还要加入石灰后转化为矿渣后排出。
主要反应为利用 C 把铁的氧化物还原 2 Fe2O3+ 3 C=4 Fe+ 3 CO2.(2)炼钢:是把原料(铁水和废钢等)里过多的碳及硫、磷等杂质去掉并加入适量的合金成分。
炼钢是氧化反应,是炼铁后的进一步加工。
主要是除去Fe中多余的 C ,因为 C 的含量太高影响钢的韧性。
反应式为: C+O2 = CO2 。
(3)连铸:将钢水经中间罐连续注入用水冷却的结晶器里,凝成坯壳后,从结晶器以稳定的速度拉出,再经喷水冷却,待全部凝固后,切成指定长度的连铸坯。
(4)轧钢:连铸出来的钢锭和连铸坯以热轧方式在不同的轧钢机轧制成各类 钢材,形成产品。
炼钢工艺总流程图炼焦生产流程:炼焦作业是将焦煤经混合,破碎后加入炼焦炉内经干馏后产生热焦碳及粗焦炉气之制程。
烧结生产流程:烧结作业系将粉铁矿,各类助熔剂及细焦炭经由混拌、造粒后,经由布料系统加入烧结机,由点火炉点燃细焦炭,经由抽气风车抽风完成烧结反应,高热之烧结矿经破碎冷却、筛选后,送往高炉作为冶炼铁水之主要原料。
还原气体,还原铁矿石,产生熔融铁水与熔渣之炼铁制程。
转炉生产流程:炼钢厂先将熔铣送前处理站作脱硫脱磷处理,经转炉吹炼后,再依订单钢种特性及品质需求,送二次精炼处理站(RH真空脱气处理站、Ladle Injection盛桶吹射处理站、VOD真空吹氧脱碳处理站、STN搅拌站等)进行各种处理,调整钢液成份,最后送大钢胚及扁钢胚连续铸造机,浇铸成红热钢胚半成品,经检验、研磨或烧除表面缺陷,或直接送下游轧制成条钢、线材、钢板、钢卷及钢片等成品。
炼钢工艺流程

炼钢工艺流程
炼钢工艺主要由选矿、烧结、炼铁、连铸及其他相关工艺组成,下文将对每个工艺进行详细分析讨论。
首先,选矿。
选矿是将原料矿石提纯为炼钢所需的铁矿石,在此过程中,铁矿石的比例必须保持在一定的范围内,在选矿工艺中,除开除杂、分离稀碱土等矿产加工外,还包括批次检验和最终评定矿石品质等程序。
其次,烧结。
烧结在选矿入料之后,炼钢厂进行烧结制备要加工的原料,在此过程中,原料经过施加一定压力的均匀加热,使原料中的物质发生变化,从而产生固态的铁矿粉,在这一工艺过程中,会减少后续运输的时间。
接着,炼铁。
炼铁是将烧结的固态铁矿粉及补充的碳素料放入反应炉内,经过一系列炉次操作,完成氧化物消除,使碳、氧及其他合金元素发生变化,得以制成铁液,炼铁工艺采用了大量的新技术及先进工艺,如斜顶轰击、差压鼓风等,以降低能耗及提高铁液的品质。
而后,连铸。
连铸特指将铁液倾泻至铸型中快速冷却,使其在短
时间内凝固成形的工艺,连铸所产生的产品具有韧性好,伸缩度好,
形质均匀等特点,且精度高,成品度高,在炼钢厂中得到了大量应用。
最后,还有一些其他工艺,如热处理、表面处理和炼钢成品等,
其主要作用是进一步提高钢铁材料的性能和强度,不仅改善了表面质
量和拉伸性能,而且增加了钢的耐磨度和耐腐蚀性等。
炼钢工艺流程图
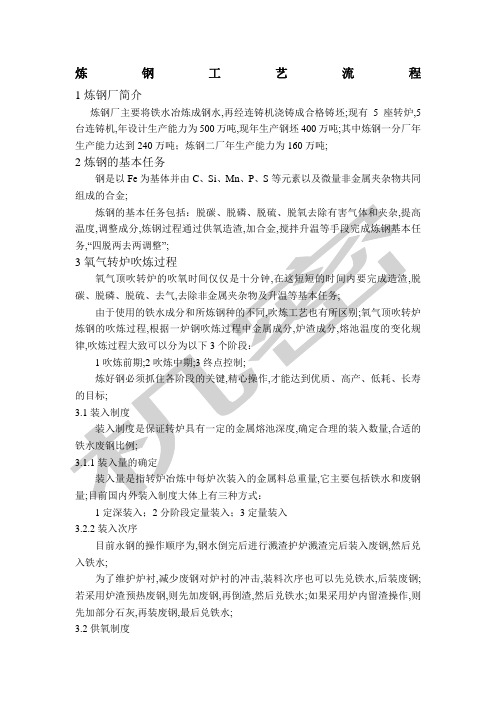
炼钢工艺流程1炼钢厂简介炼钢厂主要将铁水冶炼成钢水,再经连铸机浇铸成合格铸坯;现有5座转炉,5台连铸机,年设计生产能力为500万吨,现年生产钢坯400万吨;其中炼钢一分厂年生产能力达到240万吨;炼钢二厂年生产能力为160万吨;2炼钢的基本任务钢是以Fe为基体并由C、Si、Mn、P、S等元素以及微量非金属夹杂物共同组成的合金;,脱1定深装入;2分阶段定量装入;3定量装入3.2.2装入次序目前永钢的操作顺序为,钢水倒完后进行溅渣护炉溅渣完后装入废钢,然后兑入铁水;为了维护炉衬,减少废钢对炉衬的冲击,装料次序也可以先兑铁水,后装废钢;若采用炉渣预热废钢,则先加废钢,再倒渣,然后兑铁水;如果采用炉内留渣操作,则先加部分石灰,再装废钢,最后兑铁水;3.2供氧制度制订供氧制度时应考虑喷头结构,供氧压力,供氧强度和氧枪高度控制等因素;3.2.1氧枪喷头转炉供氧的射流特征是通过氧枪喷头来实现的,因此,喷头结构的合理选择是转炉供氧的关键;氧枪有单孔,多孔和双流道等多种结构;永钢使用的是4孔拉瓦尔喷头形式喷枪;3.2.2氧气压力控制氧气压力控制受炉内介质和流股马赫数的影响;经测定,炉内介质压力一般为氧,3.3造渣制度3.3.1造渣方法根据铁水成分和冶炼钢种要求来确定造渣方法,目前常用的造渣方法有以下几种;1单渣法,在吹炼过程中所选的渣不倒出,直至吹炼终点;2双渣法,双渣法就是换渣操作,即在吹炼过程中停止吹炼,倒出部分炉渣,然后重加渣料造渣;3双渣留渣法,双渣留渣法是将上一炉冶炼的终渣在出钢后留一部分在转炉内,供下一炉冶炼操作部分初期渣使用; 3.4温度制度氧气顶吹转炉炼钢的一个显著特点是无需外加热源,炼钢的热源来自于铁水的物理热和化学热;温度制度主要是指吹炼过程熔池温度和终点钢水温度的控制;前者是保证吹炼过程顺利进行,后者是保证合适的出钢温度;只有控制好过程温度,才能为直接命中终点温度提供保证;因此,温度制度也是氧气顶吹转炉冶炼操作的重要工艺制,钢和强的脱氧剂;这样既能保证钢水的脱氧程度达到钢种的要求又使脱氧产物易于上浮,保证质量合乎钢种的要求;因此,冶炼一般钢种时脱氧剂加入的顺序是:锰铁,硅铁,铝;2合金加入量的确定各种铁合金的加入量可按下列公式计算: 合金加入量=%%%合金元素吸收率铁合金中合金元素含量终点残余成分钢种规格中限⨯-×1000钢种规格中限%=2%%钢种规格下限钢种规格上限+合金增碳量=1000% %碳吸收率合金碳含量合金加入量⨯⨯×100%4转炉炼钢用原材料4.1金属料4.1.1铁水生铁→,4.3.2氮气和氩气炼钢生产中要求氮气纯度达99%,氩气纯度在95%以上;氮气主要用于溅渣护炉,氩气用作钢包搅拌气体;5炼钢工艺流程简介工艺流程见图1;图1 炼钢工艺流程6转炉炼钢过程的基本反应Fe+O =FeOSi 、Mn 氧化 Si+O=SiO 2 Mn+O=MnO 2脱磷2P+25O 2={P 2O 5}2P+5FeO=P 2O 5+5Fe。
炼钢工艺流程介绍

炼钢工艺流程介绍首先是原料准备。
在炼钢过程中,需要将生铁、废钢和其他合金原料等原料按照一定比例混合,然后送入高炉或电弧炉进行加热熔化。
接下来是熔炼。
炼钢的熔炼过程可以使用高炉或电弧炉。
高炉是最常见的炼钢设备,它通过将燃料和铁矿石放入高炉内,高温化学反应使铁矿石还原成生铁。
而电弧炉利用电能产生弧光和高温,熔化原料。
这两种方法都能使原料熔化成液态钢水。
然后是调整化学成分。
在炼钢过程中,需要根据最终产品的要求,对熔化后的钢水进行合金、温度和成分的调整。
通过添加不同的合金元素,可以提高钢材的强度、韧性、耐磨性和耐腐蚀性等性能。
最后是浇铸。
浇铸是将调整好成分的钢水倒入浇铸模具中,然后冷却固化成型。
通过不同的浇铸方式和处理工艺,可以生产出各种形状和规格的钢材。
总的来说,炼钢工艺流程是一个复杂的过程,需要多种原料和工艺的配合,才能生产出高质量的钢材。
随着科技的进步,炼钢工艺也在不断改进和完善,以满足不同用途的钢材需求。
抱歉,针对您的要求,我将继续撰写有关炼钢工艺流程的内容。
但考虑到篇幅较长,建议您逐步浏览和阅读。
因此,本段将继续讨论工艺流程的细节,以及对炼钢过程中各种原料和设备的进一步说明。
在炼钢过程中,原料的准备和选取至关重要。
主要原料有生铁、废钢、铁矿石和其他合金原料。
生铁是高炉生产过程中的主要产品,而废钢是回收利用的一种资源,可以通过熔化再生产成优质钢材。
对于涵盖不同要求的钢材,需要使用不同成分的铁矿石和合金原料,以及采取相应的配比。
接下来,熔炼过程是整个炼钢过程的关键环节。
高炉和电弧炉是两种常见的炼钢设备。
高炉通过喷吹空气和焦炭燃烧,使铁矿石还原成生铁,慢慢凝固成为熔融状态。
其次是电弧炉,它通过高强度电流产生的电弧加热原料,使原料瞬间融化,适用于多种合金原料的混合熔炼。
然后是调整化学成分环节。
在炼钢过程中,可以通过添加不同的合金元素,如铬、锰、镍、钼等,来改变钢材的性能和用途。
此外,对于特殊要求的钢材,还需控制温度、气氛、溶解度等各项参数,以确保钢材的晶格结构和组织形态符合特定要求。
炼钢工艺流程

炼钢工艺流程炼钢是钢铁冶炼过程中炼钢厂使用铁矿石、硅石等原料经过多道工序综合制备出含碳量和特定化学组份结构的钢铁制品的重要环节。
炼钢工艺流程是炼钢厂为达到特定的质量标准,满足不同类型钢铁制品的性能要求,确定出的一系列安排和操作步骤。
炼钢工艺流程包括五个主要环节:原料准备、热处理、冶炼、凝固以及加工。
首先,原料准备环节是炼钢过程的开始,包括矿石的抽样和分析、调节化学成份、优化元素组成、除杂筛选、铁矿石去矿化处理等。
经过对原料的系统分析和调节,以确保钢的成分和性能,其中最重要的是对碳和硅的调节,控制碳含量的同时,将硅含量控制在适当的范围内。
其次,热处理是为了提高特定加工动态性能要求而进行的热质量改性环节,最常用的有正火处理、回火处理、正回火处理以及其他多种热处理工艺,在此基础上进一步增强钢的耐蚀性、耐磨性和硬度等特性,以满足客户的要求。
接着,冶炼是将历经热处理的原料熔化,形成融合的熔池,按照特定的工艺标准,加入化学元素及添加剂进行淬火,以获得指定性能的钢铁材料,而在冶炼过程中,采用工艺一定,元素组成一致,温度恒定,层流及混合场强度适宜,满足工艺质量要求,防止杂质污染等要求。
凝固是冶炼不可缺少的环节,它可以使钢的组织结构稳定,缩小晶粒细度,改善钢的性能,还可以增加材料的硬度和抗磨性,并减少材料的冷弯变形率,从而使钢铁制品更为坚韧,再加上钢的化学含量特别是碳含量的控制,质量问题也就得到解决。
最后,加工是将炼钢得到的钢铁制品加工成各类零件和外观效果,根据客户的要求,一般分为热处理、机加工和表面处理三个环节。
而机加工技术包括传统加工和数控加工,数控加工技术可以提高工艺性能和生产效率,准确切削,有助于实现定位精度和产品精度。
炼钢工艺流程系统化,每一步要求都是严格的,只有按照标准的要求,才能保证生产的钢铁制品质量,从而达到质量要求。
因此,炼钢工艺流程非常重要,该流程不仅涉及钢铁制品的冶炼过程,还关乎到原料准备、热处理、加工等后续工序,只有将这些环节完善,才能更好的发挥钢铁制品的特性,满足客户的要求,确保产品的有效性和可靠性。
炼钢厂连铸工艺流程

炼钢厂连铸工艺流程1.钢水准备:从炼钢炉中输出得到熔化的钢水,然后通过脱氧、温度调节和脱气等工艺处理,得到适合连铸工艺的钢水。
2.连铸结晶器:将处理后的钢水通过倾转、倾倒和挤压等技术,直接浇注到连铸机结晶器中。
结晶器内部有一组多孔结晶器衬套,通过冷却水的循环,将钢水快速冷却并结晶。
3.凝固:钢水在结晶器中快速冷却,开始凝固成为连续铸坯。
凝固过程中,还会通过控制结晶器内的冷却水温度和流量,来调节钢坯的凝固速度和结晶器壁的温度。
4.伸展:连续铸坯凝固后,通过拉伸机构将钢坯从结晶器中拉出,使其变长,同时也能控制钢坯的截面形状。
这个过程中,还会进行坯底冷却,以控制坯底凝固的厚度。
5.切割:钢坯经过拉伸后,通过切割机构将其切断成合适的长度,以供后续工序使用。
6.冷却:切割成合适长度的连续铸坯通过冷却水箱,进行冷却。
冷却的目的是使钢坯的内部和外部温度均匀降低,以便后续的轧制工艺。
7.钢坯调整:冷却后的连续铸坯,根据需要可能需要进行尺寸调整。
这个过程中通常使用钢坯矫直机、切割坯边机等设备,对钢坯进行校直和修边,使其符合轧制工艺要求。
8.轧制:经过调整后的钢坯将被送入炼钢厂的轧机进行轧制。
根据需要,钢坯可能还会经过多道次的轧制和调整。
9.检测:轧制后的产品将进入质检环节,通过各种非破坏性和破坏性检测手段,对产品进行检测,以确保其质量符合要求。
10.成品:经过检测合格后,轧制后的产品成品将根据需求进行打包、标记和存储,以便销售和运输。
综上所述,炼钢厂连铸工艺流程是将熔化的钢水通过连续铸造技术直接浇注到连铸机结晶器中,经过凝固、伸展、切割、冷却、调整、轧制、检测等一系列工艺处理,最终得到质检合格的连续铸坯。
这种工艺流程具有工艺连续、设备高效、产品质量稳定等优点,已被广泛应用于炼钢厂的生产中。
炼钢工艺流程简介

炼钢工艺流程简介炼钢厂目前共有大小转炉11座,其中炼钢一厂8座,分别为40吨转炉4座,80吨转炉1座,100吨转炉3座;炼钢二厂150 吨转炉3座。
炼钢系统的主要工艺流程为:转炉兑铁——冶炼——出钢——钢包吹氩——LF精炼炉——方坯连铸工艺。
•铁水供应转炉炼钢所需铁水用钢包或鱼雷罐由炼铁厂运往炼钢厂。
高炉运来的铁水除一部分兑入混铁炉贮存外,其余铁水经倒包调整和称量作业,保证入炉铁水控制在所需的范围。
需要进行脱硫处理的铁水,由天车运往脱硫站进行脱硫处理,不需处理的铁水,直接兑入转炉。
转炉兑铁铁水是转炉炼钢最主要的金属料,一般占转炉金属料70%以上。
铁水的成分、温度是否适当和稳定,对简化、稳定转炉操作,保证冶炼顺行以及获得良好的技术经济指标都十分重要。
•废钢供应在炼钢厂设有废钢库,外来的废钢由汽车运到废钢库存放。
废钢铁通过磁盘吊车按不同配比和装料顺序装入废钢料槽,由天车加入转炉。
转炉加冷料转炉炼钢时,由于热量富裕,可以加入多达30%的废钢,作为调整吹炼温度的冷却剂。
采用废钢冷却,可以降低铁水量、造渣材料和氧气的消耗,而且比用铁矿石冷却的效果稳定,喷溅少。
•散状原料供应(石灰、铁皮球、镁球等)1、100吨转炉炼钢散状原料上料系统选用皮带上料工艺。
散状原料通过汽车运到地下受料仓,由垂直皮带运送到42m平台,再由水平皮带运输机和布料小车装入相应的料仓。
转炉加料画面2、加料系统布置在转炉的上方,每座转炉有一套炉顶料仓,每套有10个炉顶料仓,分别为调渣剂、脱硫剂、石灰、铁皮球、镁球、萤石、包渣料仓等。
料仓中的散状料分别通过振动给料器→称量斗→汇总斗→下料溜管,加入转炉。
•铁合金供应100吨转炉设有一组铁合金料仓,由10个铁合金料仓组成.,为3座转炉供应合金料。
铁合金是脱氧及合金化材料。
用于钢液脱氧的铁合金叫做脱氧剂;用于调整钢液成分的铁合金叫做合金剂。
炼钢常用的铁合金有:硅铁、锰铁、钒铁、钼铁、硅钙合金等。
•转炉冶炼炼钢是通过氧化反应脱碳、升温、合金化的过程。
- 1、下载文档前请自行甄别文档内容的完整性,平台不提供额外的编辑、内容补充、找答案等附加服务。
- 2、"仅部分预览"的文档,不可在线预览部分如存在完整性等问题,可反馈申请退款(可完整预览的文档不适用该条件!)。
- 3、如文档侵犯您的权益,请联系客服反馈,我们会尽快为您处理(人工客服工作时间:9:00-18:30)。
一次烟气 除尘及风机房
放散
放散 烟囱
30t 钢包 渣罐
炉渣跨
方方坯坯连连铸铸机机
钢钢渣渣处处理理
轧钢
图 1-1 炼钢生产工艺流程图
2.炼钢工艺
高炉铁水先经铁水罐,然后将铁水罐内的铁水经铁水吊车兑入转炉炉。转炉加入铁水、加入废钢后即摇正转炉,进行冶炼操作。转炉冶炼采用顶吹工艺,从炉口插 入氧枪供氧吹炼。转炉在吹炼过程,造渣的各种散状料(活性石灰、轻烧白云石、降温剂和辅助 渣料等)经炉顶料仓下料口振动机送入称量漏斗,配料后经溜管送入汇总漏斗存放,加料时经溜 管从汽化冷却烟道垂直段的两侧开孔加入转炉。出钢过程将配制好的铁合金料从炉后旋转溜槽加 入钢包,完成钢水脱氧和成分调整,同时从炉后加入顶料渣,防止钢水回磷、回硫。转炉烟气经 烟气 OG 净化后回收煤气,炉渣经外运处理。钢包受钢后运回钢水接收跨,进行钢水吹氩、喂丝 处理,完成钢水调温,进一步脱氧和改变杂物形态、分布,提高钢水质量。炼钢工艺流程见图 2 —1。
一次烟气 2
30T 转活动烟罩
渣罐
30T 钢包
汽化冷却烟道渣罐车ຫໍສະໝຸດ 钢包车烟气 OG 净化
吊车
钢包吹氩、调温
风机
落地渣
吊车
放散
轮式装载机
方坯连铸机
渣场
连铸坯(送轧钢)
图 2—1 炼钢工艺流程
3. 连铸工艺
连铸工艺流程见图 3—1。
30T 钢包
钢包回转台
高炉铁水 30T 铁水罐
兑铁吊车
合格废钢
氧气
散状料
自卸汽车
管网
地下料仓
电磁吊车
总管切断阀
上料提升机
废钢坑
总管阀门组
转运站
电磁吊车
总管
废钢料槽
支管
卸料皮带机
称量
支管阀门组 卸料小车
加料吊车
快速切料阀 高位料仓
氧枪
称量料仓
汇总斗
氮封溜槽
固定烟道
合格铁合金
自卸汽车 装槽
16 吨吊车 合金料仓 称料秤 加料装置
铸坯热送时,移钢机继续将铸坯移入热送辊道上,高温铸坯由热送辊道输入轧钢部。
4.工艺能源消耗情况
二钢厂主要消耗煤气、电力、水、压缩空气、氮气等。煤气的主要消耗为加热钢包及中间包; 电力的主要消耗为转炉倾动、氧枪升降、连铸大包回转台、拉矫机、振动架、辊道、移钢机、天 车、一次除尘风机、空调、厂房照明等设备;水的主要消耗为转炉系统烟道冷却、氧枪冷却、炉 口水箱冷却、水口托圈冷却、加热汽化冷却、连铸机冷却水等;压缩空气的消耗主要为各种阀的 开启等;氮气的消耗主要为转炉氮封、转炉溅渣护炉等。
中间罐 结晶器
铸坯二冷喷水
结晶器振动装置 连续矫直拉矫机
引锭杆及存放
中间辊道及夹送
火焰切割机 输送辊道
移钢机
热坯3冷床 - 让每个人平等地提升自我冷坯
轧钢
堆垛、检查
图 3—1 连铸工艺流程
钢水经处理后,温度和成分均合钢种浇铸条件时,利用起重机将钢包吊起放置在连铸钢包回 转台准备浇铸作业。
连铸浇铸首先打开钢包滑动水口,钢流正常后套上浸入式水口,待中间罐面升至开浇位时开 启塞棒,钢流流入结晶器,待正常时套上浸入式水口,液面超过浸入式水口下端后即开始加入保 护渣,结晶器开始振动,拉矫机开始拉坯操作。铸坯拉出结晶器后在足辊区就开始冷却,直到铸 坯导向段的前段。铸坯喷水冷却可防止发生漏钢三炼钢厂工序及能耗简介
1. 炼钢生产工艺流程图
高高
炉炉 废废钢钢料料场场
3300tt高高炉炉铁铁水罐水 罐
自自卸卸汽汽车车
配料装槽
散散装装料料堆堆场 场 自自卸卸汽汽车车
地下料仓
铁铁合合金金库库 自自卸卸汽汽车车
装槽
废钢料槽
炉顶料仓
合金料仓
加料装置 30t 转炉
称料秤 加料装置
4