6063铝型材挤压工艺的优化(2)#铝型材挤压机工作原理
6063铝棒挤压工艺
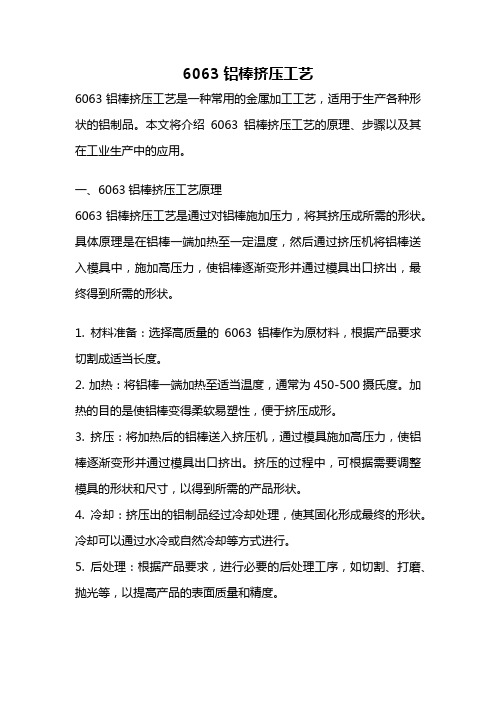
6063铝棒挤压工艺6063铝棒挤压工艺是一种常用的金属加工工艺,适用于生产各种形状的铝制品。
本文将介绍6063铝棒挤压工艺的原理、步骤以及其在工业生产中的应用。
一、6063铝棒挤压工艺原理6063铝棒挤压工艺是通过对铝棒施加压力,将其挤压成所需的形状。
具体原理是在铝棒一端加热至一定温度,然后通过挤压机将铝棒送入模具中,施加高压力,使铝棒逐渐变形并通过模具出口挤出,最终得到所需的形状。
1. 材料准备:选择高质量的6063铝棒作为原材料,根据产品要求切割成适当长度。
2. 加热:将铝棒一端加热至适当温度,通常为450-500摄氏度。
加热的目的是使铝棒变得柔软易塑性,便于挤压成形。
3. 挤压:将加热后的铝棒送入挤压机,通过模具施加高压力,使铝棒逐渐变形并通过模具出口挤出。
挤压的过程中,可根据需要调整模具的形状和尺寸,以得到所需的产品形状。
4. 冷却:挤压出的铝制品经过冷却处理,使其固化形成最终的形状。
冷却可以通过水冷或自然冷却等方式进行。
5. 后处理:根据产品要求,进行必要的后处理工序,如切割、打磨、抛光等,以提高产品的表面质量和精度。
三、6063铝棒挤压工艺的应用6063铝棒挤压工艺广泛应用于工业生产中,主要用于生产各种形状的铝制品,如铝型材、铝合金门窗、铝管、铝棚架等。
由于6063铝合金具有良好的耐腐蚀性、可塑性和机械性能,且重量轻、易加工,因此在建筑、航空航天、汽车、电子等领域得到广泛应用。
6063铝棒挤压工艺具有以下优点:1. 可生产各种复杂形状的铝制品,灵活性高。
2. 生产效率高,可以进行大批量生产。
3. 产品表面质量好,尺寸精度高。
4. 节约材料,减少废料产生。
5. 环保,无污染。
然而,6063铝棒挤压工艺也存在一些局限性:1. 产品长度有限,一般在6-12米之间。
2. 对模具的精度要求较高,制造成本较高。
3. 对材料的要求较高,需要选择优质的6063铝棒。
总结:6063铝棒挤压工艺是一种常用的金属加工工艺,通过对铝棒施加压力,将其挤压成所需的形状。
6063铝合金型材挤压工艺对型材表面质量的影响论文

降低、 不均匀, 在金属通过模孔时产生的摩擦力较大, 金属之间产生严重的流速不均, 也会造成表面挤压条
纹和表面粗糙严重。只要把模具的加热温度降低, 加
3 表面质量缺陷的产生原因
31 铝合金型材表面夹渣、 . 划痕的产生原因 一般认为型材表面夹渣及划痕是铸锭夹渣或夹 灰所造成的, 而实际生产过程中, 夹渣和划痕的产生
K w r . 5 1 G D cn rrpl cdr e o s D S03 A ; v t; e e y d C 0 ; o ee u o s
1 前
言
与挤压工艺控制不严有关。挤压时, 必须严格控制铸 锭表面洁净。如果铸锭表面带有一些废的铝屑或杂 质清理不净, 在高温挤压时这些杂质浮在型材表面或 挂在模具工作带上, 必将造成型材表面夹渣或划痕。 正常挤压时, 每天应采用专用清理垫, 把挤压筒内壁 的一些杂质清理干净, 以防止这些杂质卷人模孔中, 挂在模具的工作带上或浮在型材表面上, 造成型材表 面的划痕和夹渣。再者, 挤压铸锭的压余控制, 压余 过小, 一部分残余的氧化皮及杂质会流人模孔中, 在 连续挤压时也会使型材表面划伤或造成夹渣。严重
量查起。有些表面质量问题是能够解决的, 但有些表 面质量问题单从铸锭和模具去查找原因是解决不了 的, 因为影响型材表面质量的重要因素之一与型材的 挤压工艺有着直接关系。根据我公 司几年来的挤压 生产经验, 从挤压工艺方面进行分析并找出影响型材 表面质量的原因效果显著。下面简要论述挤压工艺 对型材表面质量的影响。
(en Dn a im .L .Tn h , i , 1 , a Bjg g A m u C ,t ,o zu Big 1 1 Ci ) i oy l n o d i u g o en 0 3 h j 1 n
6063铝合金挤压型材质量影响因素及对策
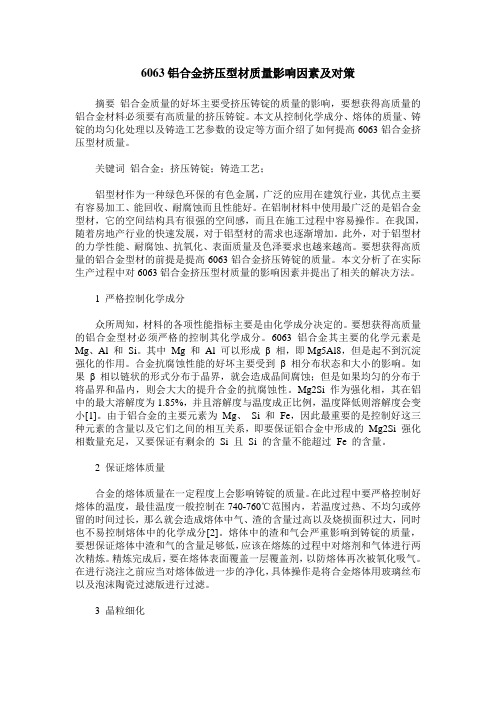
6063铝合金挤压型材质量影响因素及对策摘要铝合金质量的好坏主要受挤压铸锭的质量的影响,要想获得高质量的铝合金材料必须要有高质量的挤压铸锭。
本文从控制化学成分、熔体的质量、铸锭的均匀化处理以及铸造工艺参数的设定等方面介绍了如何提高6063铝合金挤压型材质量。
关键词铝合金;挤压铸锭;铸造工艺;铝型材作为一种绿色环保的有色金属,广泛的应用在建筑行业,其优点主要有容易加工、能回收、耐腐蚀而且性能好。
在铝制材料中使用最广泛的是铝合金型材,它的空间结构具有很强的空间感,而且在施工过程中容易操作。
在我国,随着房地产行业的快速发展,对于铝型材的需求也逐渐增加。
此外,对于铝型材的力学性能、耐腐蚀、抗氧化、表面质量及色泽要求也越来越高。
要想获得高质量的铝合金型材的前提是提高6063铝合金挤压铸锭的质量。
本文分析了在实际生产过程中对6063铝合金挤压型材质量的影响因素并提出了相关的解决方法。
1 严格控制化学成分众所周知,材料的各项性能指标主要是由化学成分决定的。
要想获得高质量的铝合金型材必须严格的控制其化学成分。
6063铝合金其主要的化学元素是Mg、Al 和Si。
其中Mg 和Al 可以形成β 相,即Mg5Al8,但是起不到沉淀强化的作用。
合金抗腐蚀性能的好坏主要受到β 相分布状态和大小的影响。
如果β 相以链状的形式分布于晶界,就会造成晶间腐蚀;但是如果均匀的分布于将晶界和晶内,则会大大的提升合金的抗腐蚀性。
Mg2Si 作为强化相,其在铝中的最大溶解度为1.85%,并且溶解度与温度成正比例,温度降低则溶解度会变小[1]。
由于铝合金的主要元素为Mg、Si 和Fe,因此最重要的是控制好这三种元素的含量以及它们之间的相互关系,即要保证铝合金中形成的Mg2Si 强化相数量充足,又要保证有剩余的Si 且Si 的含量不能超过Fe 的含量。
2 保证熔体质量合金的熔体质量在一定程度上会影响铸锭的质量。
在此过程中要严格控制好熔体的温度,最佳温度一般控制在740-760℃范围内,若温度过热、不均匀或停留的时间过长,那么就会造成熔体中气、渣的含量过高以及烧损面积过大,同时也不易控制熔体中的化学成分[2]。
论铝合金的挤压机固溶热处理及6063-t6材料的优化生产工艺参数
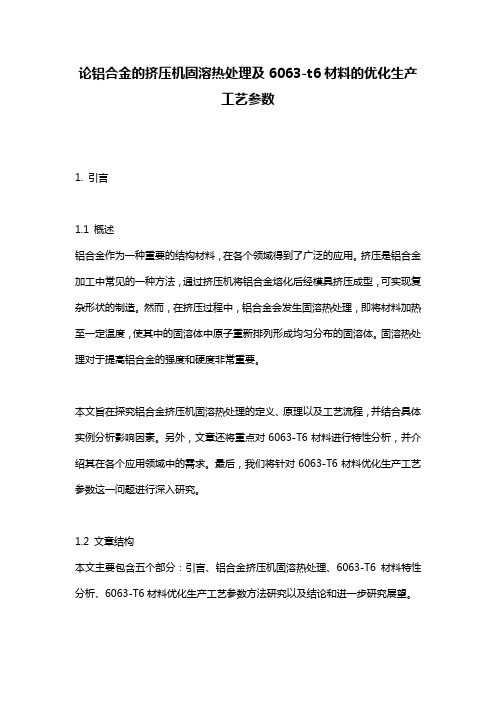
论铝合金的挤压机固溶热处理及6063-t6材料的优化生产工艺参数1. 引言1.1 概述铝合金作为一种重要的结构材料,在各个领域得到了广泛的应用。
挤压是铝合金加工中常见的一种方法,通过挤压机将铝合金熔化后经模具挤压成型,可实现复杂形状的制造。
然而,在挤压过程中,铝合金会发生固溶热处理,即将材料加热至一定温度,使其中的固溶体中原子重新排列形成均匀分布的固溶体。
固溶热处理对于提高铝合金的强度和硬度非常重要。
本文旨在探究铝合金挤压机固溶热处理的定义、原理以及工艺流程,并结合具体实例分析影响因素。
另外,文章还将重点对6063-T6材料进行特性分析,并介绍其在各个应用领域中的需求。
最后,我们将针对6063-T6材料优化生产工艺参数这一问题进行深入研究。
1.2 文章结构本文主要包含五个部分:引言、铝合金挤压机固溶热处理、6063-T6材料特性分析、6063-T6材料优化生产工艺参数方法研究以及结论和进一步研究展望。
引言部分主要介绍本文的背景和目的,并概述了铝合金挤压机固溶热处理及6063-T6材料优化生产工艺参数这两个主要内容。
接下来,将详细阐述铝合金挤压机固溶热处理的定义、原理和工艺流程,以及影响因素。
随后,会对6063-T6材料进行特性分析,包括其组成、性质以及在不同领域中的需求。
然后,我们将深入探讨如何通过实验设计与方法来优化6063-T6材料的生产工艺参数,并介绍相关的参数优化模型构建和求解过程。
最后,将总结本文的主要研究结论,并展望未来关于铝合金挤压机固溶热处理以及6063-T6材料优化生产工艺参数方面的进一步研究方向。
1.3 目的本文旨在全面了解铝合金挤压机固溶热处理这一重要环节,并深入分析其中的定义、原理、工艺流程以及影响因素。
同时,通过对6063-T6材料的特性分析,可以更好地理解该材料在不同领域中的需求,并强调生产工艺参数优化的重要性。
最后,本文将通过实验设计与方法研究6063-T6材料的优化生产工艺参数,以期为相关领域提供有益的参考和指导。
6063铝合金连续挤压工艺研究
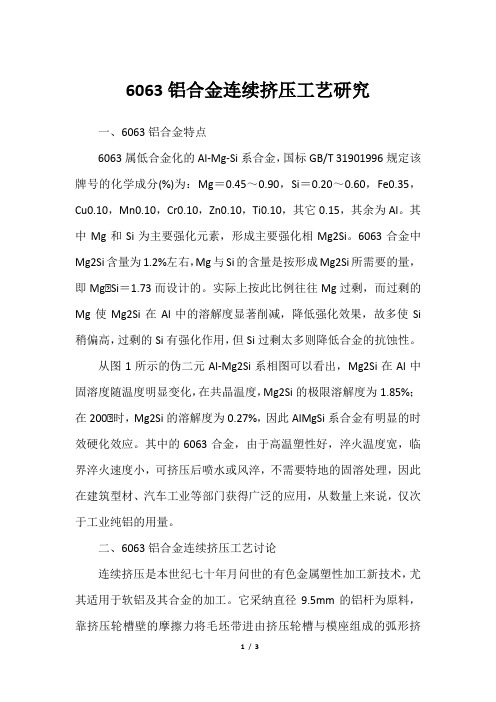
6063铝合金连续挤压工艺研究一、6063铝合金特点6063属低合金化的Al-Mg-Si系合金,国标GB/T 31901996规定该牌号的化学成分(%)为:Mg=0.45~0.90,Si=0.20~0.60,Fe0.35,Cu0.10,Mn0.10,Cr0.10,Zn0.10,Ti0.10,其它0.15,其余为Al。
其中Mg和Si为主要强化元素,形成主要强化相Mg2Si。
6063合金中Mg2Si含量为1.2%左右,Mg与Si的含量是按形成Mg2Si所需要的量,即Mg∶Si=1.73而设计的。
实际上按此比例往往Mg过剩,而过剩的Mg使Mg2Si在Al中的溶解度显著削减,降低强化效果,故多使Si 稍偏高,过剩的Si有强化作用,但Si过剩太多则降低合金的抗蚀性。
从图1所示的伪二元Al-Mg2Si系相图可以看出,Mg2Si在Al中固溶度随温度明显变化,在共晶温度,Mg2Si的极限溶解度为1.85%;在200∶时,Mg2Si的溶解度为0.27%,因此AlMgSi系合金有明显的时效硬化效应。
其中的6063合金,由于高温塑性好,淬火温度宽,临界淬火速度小,可挤压后喷水或风淬,不需要特地的固溶处理,因此在建筑型材、汽车工业等部门获得广泛的应用,从数量上来说,仅次于工业纯铝的用量。
二、6063铝合金连续挤压工艺讨论连续挤压是本世纪七十年月问世的有色金属塑性加工新技术,尤其适用于软铝及其合金的加工。
它采纳直径9.5mm的铝杆为原料,靠挤压轮槽壁的摩擦力将毛坯带进由挤压轮槽与模座组成的弧形挤压室。
坯料被伸入轮槽的挡料块拦住,在摩擦力的持续作用下,温度和压力不断上升,达到材料的屈服强度,便从设置在挡料块旁的模具中挤出形成产品。
因此连续挤压不需要毛坯加热装置,节约了设备占地面积与。
只要连续供应毛坯,便能生产出任意长度的产品。
产品的特点是小截面(最小为6mm2),高精度(直径与壁厚公差为0.05mm)。
汽车等工业部门所用6063合金产品,因其截面小精度高,过去生产用常规挤压毛坯再进行拉拔的工艺,现在看来不如采纳连续挤压工艺经济。
6063铝合金挤压型材觉缺陷及其解决方法

6063铝合金挤压型材觉缺陷及其解决方法
1.毛刺:毛刺是挤压型材表面的突出物,会影响外观和触感。
毛刺的
主要原因是金属挤压时的不均匀变形和模具壁口的磨损。
解决方法包括增
加材料的充填比例,优化挤压工艺参数,增加模具壁口的滑移润滑剂等。
2.断裂:断裂是挤压型材在生产和使用过程中出现的一个严重问题。
断裂的原因可以是材料本身的强度不足、挤压工艺参数设置不当、模具设
计不合理等。
解决方法包括选择合适的6063铝合金型材,优化挤压工艺
参数,加强模具的冷却和加热控制等。
3.冷裂纹:冷裂纹是在挤压型材的表面或内部出现的长而细的裂纹。
冷裂纹的出现与材料的热处理过程和冷却速度不当有关。
解决方法包括优
化挤压工艺参数,控制冷却速度,合理设计材料的热处理过程等。
4.物理性能不稳定:6063铝合金挤压型材的物理性能,如硬度、抗
拉强度、延展性等,可能存在不稳定的情况。
这可能是由于挤压工艺中的
应力集中和不均匀变形导致的。
解决方法包括优化挤压工艺参数,增加冷
却控制,合理设计模具结构等。
5.起皮:起皮是指挤压型材表面出现的局部脱层现象,降低了型材的
使用寿命。
起皮的原因主要是模具的磨损和使用不当。
解决方法包括定期
检查和维护模具,增加模具的使用寿命,减少起皮现象的发生。
总之,6063铝合金挤压型材的觉缺陷可能会影响其质量和使用寿命。
通过合理选择材料、优化挤压工艺参数、改进模具设计和加强质量控制等
措施,可以有效地解决这些问题,提高挤压型材的质量和性能。
挤压及热处理对6063铝合金组织及性能的影响

文献标识码 : A
Ef fe c t o f e x t r u s i o n a nd he a t t r e a t me n t o n mi c r o s t r u c t ur e n d a me c h a ni c a l p r o p e r t i e s o f 6 0 6 3 a l u mi n u m a l l o y
摘 要: 对6 0 6 3铝 合金 采用 了等通道转 角挤压 工艺及 随后 的热处理 , 利 用光 学显微镜 、 扫描 电子显微镜及拉伸 实验
分析 了挤压及热处理对 6 0 6 3铝合金 的微观 组织及力 学性能的影响 。研 究表 明: 等通道转角挤 压显著细化 了铝合金
的 晶 粒 尺 寸 并 改善 了 晶粒 分 布 的 均 匀 性 。挤 压 道 次 越 多 , 晶 粒 细 化 作 用越 明 显 且 晶 粒 分 布 的 均 匀 性 也 越 好 。 经 4 道 次 挤 压 及 时 效 处理 后 , 铝 合 金 的 平 均 晶粒 尺 寸 减 小 到 1 . 3 m, 材 料 的 强度 和 硬 度 得 到 显 著 提 高 而延 伸 率 仍 保 持
a nd h e a t t r e a t me nt o n mi c r o s t r uc t u r e a n d me c h a n i c l a p r o p e r t i e s o f 6 0 63 a l u mi n um a l l o y we r e a n a l y z e d t h r o ug h o pt i c l a mi c r o —
M 金属材料 e a l M a t e r i a l s I I 2 o 1 7第 期
6063铝合金型材表面麻点的成因及解决方法

收稿日期:2006-08-03 作者简介:杜新宇(1968-),男,河南南阳人,工程师。
6063铝合金型材表面麻点的成因及解决方法杜新宇(南阳市康远机器总厂,河南南阳473125)摘要:通过生产实践与试验分析,找出6063铝合金型材产生麻点缺陷的各种原因,提出了避免和减轻这一缺陷的方法。
关键词:6063铝合金;型材;麻点;挤压工艺;铸锭;挤压工具中图分类号:TG 379 文献标识码:A 文章编号:1007-7235(2006)12-0032-03Countermeasures and causes of point defects on 6063aluminiumalloy profile surfacesDU X in 2yu(N anyang K angyu an Machine Work ,N anyang 473125,China)Abstract :Through practice and test analysis ,the author of the paper has found out the various reas ons for the formation of the vice of rough points in the production of 6063aluminum alloy.Then he has suggested methods for av oiding or abating such a vice.K ey w ords :6063aluminum alloy ;profile ;rough point ;extrusion process ;ing ot ;extrusion implement 在6063合金挤压生产中,型材表面常出现麻点现象。
麻点的形状像彗星轨迹,好像缝衣针的针尖在型材表面剜挑的犁痕。
麻点头部小、尾部大,严重时用手摸可感觉麻点尾部有硬质点。
- 1、下载文档前请自行甄别文档内容的完整性,平台不提供额外的编辑、内容补充、找答案等附加服务。
- 2、"仅部分预览"的文档,不可在线预览部分如存在完整性等问题,可反馈申请退款(可完整预览的文档不适用该条件!)。
- 3、如文档侵犯您的权益,请联系客服反馈,我们会尽快为您处理(人工客服工作时间:9:00-18:30)。
对挤压生产来说,挤压温度是最基本的且最关键的工艺因素。
挤压温度对产品质量、生产效率、模具寿命、能量消耗等都产生很大影响。
挤压最重要的问题是金属温度的控制,从铸锭开始加热到挤压型材的淬火都要保证可溶解的相组织不从固溶中析出或呈现小颗粒的弥散析出。
6063合金铸锭加热温度一般都设定在M安徽工程技术学校g2Si析出的温度范围内,加热的时间对Mg2Si的析出有重要的影响,采用快速加热可以大大减少可能析出的时间。
一般来说,对6063合金铸锭的加热温度可设定为:
未均匀化铸锭:460-520℃;均匀化铸锭:430-480℃。
其挤压温度在操作时视不同制品及单位压力大小来调整。
在挤压过程中铸锭在变形区的温度是变化的,随着挤压过程的完成,变形区的温度逐渐升高,而且随着挤压速度的提高而提高。
因此为了防止出现挤压裂纹,随着挤压过程的进行和变形区温度的升高,挤压速度应逐渐降低。
3.2挤压速度
挤压过程中必须认真控制挤压速度。
挤压速度对变形热效应、变形均匀性、再结晶和固溶过程、制品力学性能及制品表面质量均有重要影响。
挤压速度过快,制品表面会出现麻点、裂纹等倾向。
同时挤压速度过快增加了金属变形的不均匀性。
挤压时的流出速度取决于合金种类和型材的几何形状、尺寸和表面状况。
6063合金型材挤压速度(金属的流出速度)可选为20-100米/分。
近代技术的进步,挤压速度可以实现程序控制或模拟程序控制,同时也发展了等温挤压工艺和CADEX等新技术。
通过自动调节挤压速度来使变形区的温度保持在某一恒定范围内,可达到快速挤压而不产生裂纹的目的。
为了提高生产效率,在工艺上可以采取很多措施。
当采用感应加热时,沿铸锭长度方向上存在着温度梯度40-60℃(梯度加热),挤压时高温端朝挤压模,低温端朝挤压垫,以平衡一部分变形热;也有采用水冷模挤压的,即在模子后端通水强制冷却,试验证明可以提高挤压速度30%-50%。
近年来在国外用氮气或液氮冷却模具(挤压模)以增加挤压速度,提高模具寿命和改善型材表面质量。
在挤压过程中将氮气引到挤压模出口处放出,可以使被冷却的制品急速收缩,冷却挤压模和变形区金属,使变形热被带走,同时模子出口处被氮的气铝型材1800吨压力机氛所控制,减少了铝的氧化,减少了氧化铝粘接和堆积,所以氮气的冷却提高了制品的表面质量,可大大的提高挤压速度。
CADEX是最近发展的一种挤压新工艺,它挤压过程中的挤压温度、挤压速度和挤压力形成一个闭环系统,以最大限度地提高挤压速度和生产效率,同时保证最优良的性能。
3.3在线淬火
6063-T5淬火是为了将在高温下固溶于基体金属中的Mg2Si出模孔后经快速冷却到室温而被保留下来。
冷却速度常和强化相含量成正比。
6063合金可强化的最小的冷却速度为38℃/分,因此适合于风冷淬火。
改变风机和风扇转数可以改变冷却强度,使制品在张力矫直前的温度降至60℃以下。
3.4张力矫直
型材出模孔后,一般皆用牵引机牵引。
牵引机工作时在给挤压制品以一定的牵引张力,同时与制品流出速度同步移动。
使用牵引机的目的在于减轻多线挤压时长短不齐和抹伤,同时也可防止型材出模孔后扭拧、弯曲,给张力矫直带来麻烦。
张力矫直除了可以使制品消除纵向形状不整外,还可以减少其残余应力,提高强度特性并能保持其良好的表面。
3.5人工时效
时效处理要求温度均匀,温差不超过±3-5℃。
6063合金人工时效温度一般为200℃。
时效保温时间为1-2小时。
为了提高力学性能,也有采用180-190℃时效3-4小时,但此时生产效率会有所降低。
3.6铸锭长度的优化与计算
铸锭长度的计算方法有体积法和质量法。
通过建立数学关系式,就很容易地选取出最佳的铸锭规格,大大提高型材的几何成品率。
(1)体积法
Vo=V1十Vn
AoLo=A1·L1十A·Ln
Lo=(L1/λ+Ln).K&helli铝材价格p; (1)
式中:Vo——铸锭体积(mm3);
V1——型材体积(mm3);
Vn——压余体积(mm3);
Ao——铸锭面积(mm2);
Lo——铸锭长度(mm);
A1——型材截面积(mm2);
L1——型材长度(mm);
A——挤压筒面积(mm2);
Ln——压余长度(mm);
K=A/Ao充填系数;
λ=A/A1挤压系数。
按照体积不变道理,经简化之后整理为公式(1),K与Ln可以认为是常数,只要求λ,确定Lmax,可方便地求出Lo,即铸锭长度。
(2)质量法
mo=m1十mn
ρLoLo=L1·ρL1+mn
Lo=(L1.ρL1+mn).PLo (2)
式中:Lo铸锭长度;
L1型材压出长度(m);
ρL1型材线密度(Kg/m);
mn压余重量(Kg);
mo铸锭重量(kg)
m1压出型材重量(kg)
ρLo铸锭线密度(Kg/m);
(2)式还可以再变化一下,即:L1=n·L定+L12
Lo=·ρLo-1
(3)
式中:n定尺支数;
L定定尺寸长度(m);L12切头切尾长度(m)。
(3)式比较直观方便的计算出Lo在实际工作中ρL1是随着型材壁厚的不断变化而增加的。
为方便上工序供锭,大设备的铸锭长度可设定30mm为一档,小设备设定为20mm为一档。
我们可以根据公式(3)制订ρL1、Lo、n、L1对照表。
一般民用建筑型材供货长度为6m。
这种对照表对工艺技术员和计划员的使用是十分方便的。
公式(3)又可以简化为下式:
Lo=KnL1+C (4)
Kn是与n有关的系数;
C是与机型有关的常数;
ρL1是Lo的函数,可以编好程序输入计算机,比较精确地计算出Lo。
3.7提高挤压成品率的措施
影响挤压型材成品率的因素很多我们能计算得出几何废料,在挤压生产中产生的废料一般分为几何废料和技术废料,几何废料是生产过程中仅与制品生产工艺有关的废料。
压余、切头、切尾等均属几何废料。
技术废料是在生产过程中,由于不正确执行工艺操作规程,人为造成废品(包括试模废料、铸造缺陷带来的废品等)。
技术废品是可以避免和减少的,几何废品是不可避免的,但可通过优化挤压工艺和精确计算铸锭长度等措施来减少。
挤压生产中几何废料的大小可用下式表示:
N=Nn十N12 (5)
N几伺废料(%)
Nn压余废料(%)
N12切头废料(%)
Hn=K/Lo·Ln
N12=K/Lo·L12/λ
N=K/Lo.(Ln+L12/λ) (6)
N=K/Lo·(Ln+L12/λ)
K充填系数;
Lo铸锭长度(mm);
Ln压余长度(mm,随挤压筒直广东铝型材价格径而变);
L12切头尾(mm,随制品规格而变);
λ挤压系数。
从(6)式中可以明显看出,铸锭长度Lo越长,挤压系数越大,则几何废料N越小,即几何成品率越高。
其中铸锭长度影响较大些。
但是,不能无限制地增加Lo和λ,因为它们受挤压机能力、压出长度等因素限制。