水泥厂脱硝工艺
水泥窑脱硝技术

水泥窑脱硝技术水泥窑脱硝技术是一种用于减少水泥生产过程中氮氧化物(NOx)排放的方法。
随着环境保护意识的增强和环境法规的加强,水泥企业对于减少污染物排放的要求也越来越高。
水泥窑脱硝技术应运而生,成为一种有效的减排手段。
水泥生产过程中产生的NOx主要来自燃烧过程中的高温氧化反应。
NOx是一种有害气体,对大气环境和人体健康都有一定的危害。
因此,减少NOx的排放对于保护环境和改善空气质量至关重要。
水泥窑脱硝技术的基本原理是通过在水泥窑燃烧区域注入脱硝剂,将NOx转化为无害的氮气和水。
常用的脱硝剂包括氨水、尿素等。
脱硝剂与燃烧产生的NOx发生反应,生成氮气和水,从而达到减少NOx排放的目的。
水泥窑脱硝技术具有以下几个优点。
首先,它可以高效地降低NOx 排放浓度,达到环保要求。
其次,该技术对水泥生产过程的影响较小,不会对产品质量产生明显影响。
此外,水泥窑脱硝技术还可以与其他污染物治理技术相结合,形成综合治理,进一步提高治理效果。
然而,水泥窑脱硝技术也存在一些挑战和限制。
首先,脱硝剂的选择和投加量需要根据具体情况进行优化,以确保脱硝效果和经济性的平衡。
其次,脱硝剂的投加和混合需要精确控制,以避免对水泥生产过程的干扰。
此外,脱硝剂的储存和处理也需要注意安全性和环保性。
为了实现水泥窑脱硝技术的有效应用,水泥企业需要加强技术研发和设备更新,提高脱硝效率和稳定性。
同时,加强监测和管理,确保脱硝系统的正常运行和排放达标。
此外,政府和相关部门也应加强监管和支持,推动水泥企业采用脱硝技术,促进水泥行业的可持续发展。
水泥窑脱硝技术是一种有效的减少水泥生产过程中NOx排放的方法。
通过合理选择脱硝剂和优化投加量,水泥企业可以实现环境保护和经济效益的双赢。
水泥行业应积极采用水泥窑脱硝技术,为改善环境质量和可持续发展做出贡献。
水泥厂脱硝系统工艺流程

水泥厂脱硝系统工艺流程英文回答:Cement Plant Denitration System Process Flow.1. Limestone Crushing and Preparation.Limestone, typically obtained from nearby quarries, is crushed into smaller pieces to increase its surface area and reactivity. The crushed limestone is then transported to the denitrification reactor.2. Raw Material Preheating.The crushed limestone and coal, used as the primary fuel, are preheated in a preheater to raise their temperature and enhance the denitrification efficiency.3. Calcination and Clinker Formation.The preheated materials enter a kiln, where the limestone decomposes to form calcium oxide (CaO) and releases carbon dioxide (CO2). The CaO then reacts with clay and other raw materials to form cement clinker.4. Denitrification Reactor.The cement clinker and hot gases are directed to a denitrification reactor, where ammonia (NH3) is injected. The ammonia reduces the nitrogen oxides (NOx) in the flue gases to nitrogen gas (N2) and water vapor.5. Burnout Zone.After the denitrification reaction, the gases pass through a burnout zone to ensure complete combustion and decomposition of any remaining ammonia.6. Bag Filter.The flue gases are further cleaned in a bag filter to remove any particulate matter and dust.7. Heat Exchanger.The flue gases are cooled down in a heat exchanger, recovering heat for use in other processes within the cement plant.8. Scrubber.The cooled flue gases are passed through a scrubber, which uses lime or other alkaline reagents to remove any remaining acidic gases and pollutants.9. Stack.The cleaned flue gases are released into the atmosphere through a stack.中文回答:水泥厂脱硝系统工艺流程。
水泥厂scr脱硝工艺流程
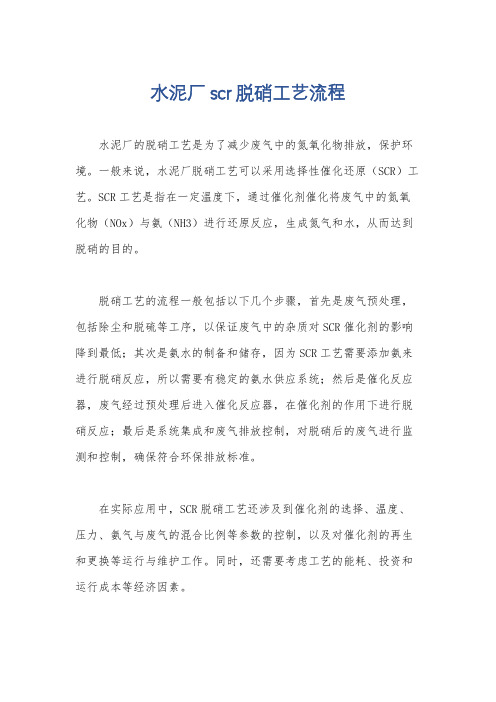
水泥厂scr脱硝工艺流程
水泥厂的脱硝工艺是为了减少废气中的氮氧化物排放,保护环境。
一般来说,水泥厂脱硝工艺可以采用选择性催化还原(SCR)工艺。
SCR工艺是指在一定温度下,通过催化剂催化将废气中的氮氧化物(NOx)与氨(NH3)进行还原反应,生成氮气和水,从而达到脱硝的目的。
脱硝工艺的流程一般包括以下几个步骤,首先是废气预处理,包括除尘和脱硫等工序,以保证废气中的杂质对SCR催化剂的影响降到最低;其次是氨水的制备和储存,因为SCR工艺需要添加氨来进行脱硝反应,所以需要有稳定的氨水供应系统;然后是催化反应器,废气经过预处理后进入催化反应器,在催化剂的作用下进行脱硝反应;最后是系统集成和废气排放控制,对脱硝后的废气进行监测和控制,确保符合环保排放标准。
在实际应用中,SCR脱硝工艺还涉及到催化剂的选择、温度、压力、氨气与废气的混合比例等参数的控制,以及对催化剂的再生和更换等运行与维护工作。
同时,还需要考虑工艺的能耗、投资和运行成本等经济因素。
总的来说,水泥厂的SCR脱硝工艺流程是一个复杂的系统工程,需要综合考虑环保、经济和工程实际情况,以达到高效、稳定地减
少氮氧化物排放的目的。
水泥厂脱硫脱硝工艺流程简介

水泥厂脱硫脱硝工艺流程简介英文回答:Desulfurization and denitrification are important processes in cement plants to reduce the emission of pollutants. There are various methods and technologies available for these processes, and the specific process flow can vary depending on the plant's requirements and local regulations. In general, the desulfurization and denitrification process in cement plants involves several steps.Firstly, desulfurization is carried out to removesulfur dioxide (SO2) from the flue gas. One commonly used method is wet scrubbing, which involves spraying a slurry of limestone or lime in water onto the flue gas. The sulfur dioxide reacts with the limestone or lime to form calcium sulfite or calcium sulfate, which can be easily removed from the flue gas. Another method is dry scrubbing, which involves injecting dry sorbents such as activated carbon orsodium bicarbonate into the flue gas to adsorb the sulfur dioxide.After desulfurization, the flue gas undergoes denitrification to remove nitrogen oxides (NOx). There are several methods for denitrification, including selective catalytic reduction (SCR) and selective non-catalytic reduction (SNCR). In SCR, a catalyst is used to convert nitrogen oxides into nitrogen and water through a chemical reaction with ammonia or urea. In SNCR, ammonia or urea is directly injected into the flue gas, and the nitrogen oxides are reduced through a high-temperature reaction.Once the desulfurization and denitrification processes are completed, the cleaned flue gas is released into the atmosphere. However, the by-products of these processes, such as calcium sulfite or sulfate and ammonium salts, need to be properly treated and disposed of to prevent environmental pollution. These by-products can be converted into gypsum, which has various uses in industries such as construction and agriculture.In summary, the process flow for desulfurization and denitrification in cement plants involves wet or dry scrubbing for desulfurization, and selective catalytic reduction or selective non-catalytic reduction for denitrification. The by-products generated during these processes need to be treated and disposed of properly. These processes play a crucial role in reducing the emission of pollutants from cement plants and ensuring environmental compliance.中文回答:水泥厂脱硫脱硝是减少污染物排放的重要工艺。
水泥窑深度脱硝工艺及关键性能参数探讨
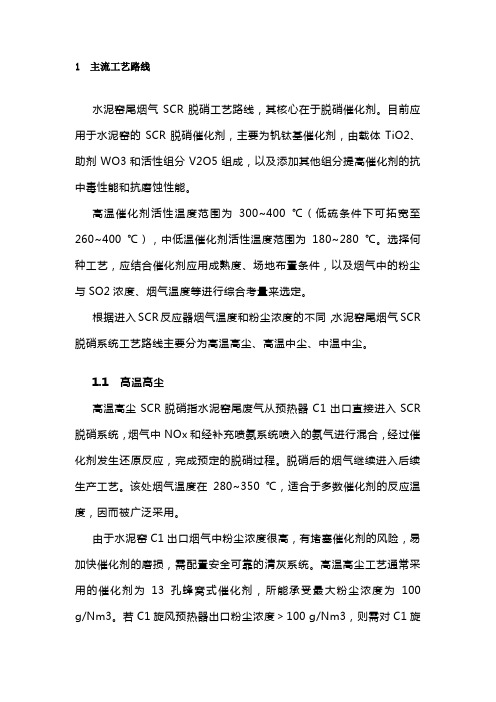
1 主流工艺路线水泥窑尾烟气SCR脱硝工艺路线,其核心在于脱硝催化剂。
目前应用于水泥窑的SCR脱硝催化剂,主要为钒钛基催化剂,由载体TiO2、助剂WO3和活性组分V2O5组成,以及添加其他组分提高催化剂的抗中毒性能和抗磨蚀性能。
高温催化剂活性温度范围为300~400 ℃(低硫条件下可拓宽至260~400 ℃),中低温催化剂活性温度范围为180~280 ℃。
选择何种工艺,应结合催化剂应用成熟度、场地布置条件,以及烟气中的粉尘与SO2浓度、烟气温度等进行综合考量来选定。
根据进入SCR反应器烟气温度和粉尘浓度的不同,水泥窑尾烟气SCR 脱硝系统工艺路线主要分为高温高尘、高温中尘、中温中尘。
1.1 高温高尘高温高尘SCR脱硝指水泥窑尾废气从预热器C1出口直接进入SCR 脱硝系统,烟气中NOx和经补充喷氨系统喷入的氨气进行混合,经过催化剂发生还原反应,完成预定的脱硝过程。
脱硝后的烟气继续进入后续生产工艺。
该处烟气温度在280~350 ℃,适合于多数催化剂的反应温度,因而被广泛采用。
由于水泥窑C1出口烟气中粉尘浓度很高,有堵塞催化剂的风险,易加快催化剂的磨损,需配置安全可靠的清灰系统。
高温高尘工艺通常采用的催化剂为13孔蜂窝式催化剂,所能承受最大粉尘浓度为100 g/Nm3。
若C1旋风预热器出口粉尘浓度>100 g/Nm3,则需对C1旋风预热器进行降尘改造或在SCR脱硝装置入口增加收尘装置。
高温高尘工艺,在增加脱硝反应器及进出口烟道后增加阻力约800 Pa,所以在脱硝改造时要同时核对高温风机电机功率和高温风机本体是否能满足要求。
1.2 高温中尘高温中尘脱硝技术是指窑尾烟气经过C1旋风分离器后,先经过高温电除尘器进行预处理,使粉尘浓度降到30 g/Nm3以下,然后再进入SCR 脱硝反应器进行脱硝处理。
这样可以降低粉尘对催化剂的磨损、堵塞问题。
但是高温中尘增加了除尘器,占地面积大,系统阻力大,运行费用略高。
电除尘器故障率高,施工难度大,投资成本高。
水泥厂脱硝技术简介
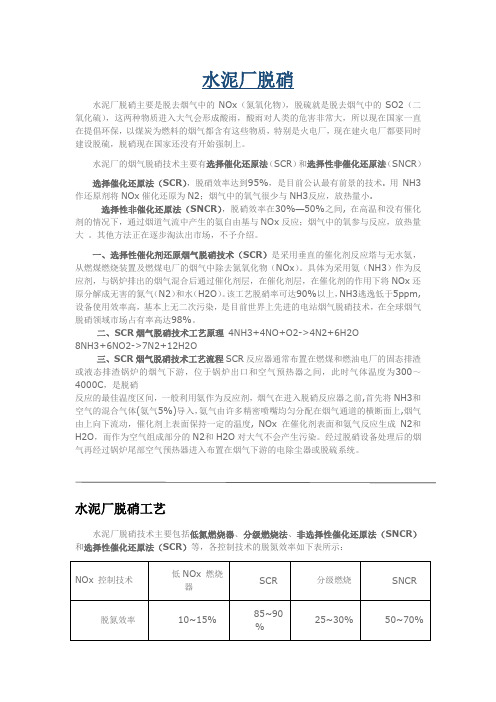
水泥厂脱硝水泥厂脱硝主要是脱去烟气中的NOx(氮氧化物),脱硫就是脱去烟气中的SO2(二氧化硫),这两种物质进入大气会形成酸雨,酸雨对人类的危害非常大,所以现在国家一直在提倡环保,以煤炭为燃料的烟气都含有这些物质,特别是火电厂,现在建火电厂都要同时建设脱硫,脱硝现在国家还没有开始强制上。
水泥厂的烟气脱硝技术主要有选择催化还原法(SCR)和选择性非催化还原法(SNCR)选择催化还原法(SCR),脱硝效率达到95%,是目前公认最有前景的技术. 用NH3作还原剂将NOx催化还原为N2;烟气中的氧气很少与NH3反应,放热量小.选择性非催化还原法(SNCR),脱硝效率在30%—50%之间, 在高温和没有催化剂的情况下,通过烟道气流中产生的氨自由基与NOx反应;烟气中的氧参与反应,放热量大。
其他方法正在逐步淘汰出市场,不予介绍。
一、选择性催化剂还原烟气脱硝技术(SCR)是采用垂直的催化剂反应塔与无水氨,从燃煤燃烧装置及燃煤电厂的烟气中除去氮氧化物(NOx)。
具体为采用氨(NH3)作为反应剂,与锅炉排出的烟气混合后通过催化剂层,在催化剂层,在催化剂的作用下将NOx还原分解成无害的氮气(N2)和水(H2O)。
该工艺脱硝率可达90%以上,NH3逃逸低于5ppm,设备使用效率高,基本上无二次污染,是目前世界上先进的电站烟气脱硝技术,在全球烟气脱硝领域市场占有率高达98%。
二、SCR烟气脱硝技术工艺原理4NH3+4NO+O2->4N2+6H2O8NH3+6NO2->7N2+12H2O三、SCR烟气脱硝技术工艺流程SCR反应器通常布置在燃煤和燃油电厂的固态排渣或液态排渣锅炉的烟气下游,位于锅炉出口和空气预热器之间,此时气体温度为300~4000C,是脱硝反应的最佳温度区间,一般利用氨作为反应剂,烟气在进入脱硝反应器之前,首先将NH3和空气的混合气体(氨气5%)导入,氨气由许多精密喷嘴均匀分配在烟气通道的横断面上,烟气由上向下流动,催化剂上表面保持一定的温度, NOx在催化剂表面和氨气反应生成N2和H2O,而作为空气组成部分的N2和H2O对大气不会产生污染。
水泥厂脱硝 (2)
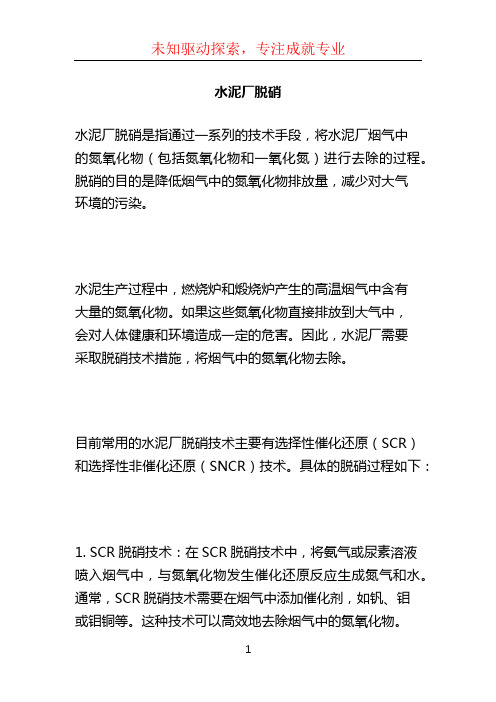
水泥厂脱硝
水泥厂脱硝是指通过一系列的技术手段,将水泥厂烟气中
的氮氧化物(包括氮氧化物和一氧化氮)进行去除的过程。
脱硝的目的是降低烟气中的氮氧化物排放量,减少对大气
环境的污染。
水泥生产过程中,燃烧炉和煅烧炉产生的高温烟气中含有
大量的氮氧化物。
如果这些氮氧化物直接排放到大气中,
会对人体健康和环境造成一定的危害。
因此,水泥厂需要
采取脱硝技术措施,将烟气中的氮氧化物去除。
目前常用的水泥厂脱硝技术主要有选择性催化还原(SCR)和选择性非催化还原(SNCR)技术。
具体的脱硝过程如下:
1. SCR脱硝技术:在SCR脱硝技术中,将氨气或尿素溶液喷入烟气中,与氮氧化物发生催化还原反应生成氮气和水。
通常,SCR脱硝技术需要在烟气中添加催化剂,如钒、钼
或钼铜等。
这种技术可以高效地去除烟气中的氮氧化物。
2. SNCR脱硝技术:在SNCR脱硝技术中,通过在烟气中
喷射氨水或尿素溶液,利用高温条件下的非催化还原反应,将氮氧化物转化为氮气和水。
SNCR脱硝技术相对于SCR
脱硝技术更简单,但其脱硝效率较低。
需要注意的是,水泥厂脱硝技术的选择需要结合实际情况
和要求,包括烟气特性、排放标准、工艺条件、经济性等
方面进行综合考虑。
此外,脱硝过程还需要对脱硝剂的储存、供应和废水处理等进行合理设计和管理。
水泥厂脱硝工艺

水泥厂脱硝工艺我在水泥厂工作也有好些年头了,今天就想跟大家唠唠水泥厂脱硝工艺这档子事儿。
您可能会问,水泥厂为啥要脱硝呢?这就好比人要呼吸干净的空气一样,咱们的环境也需要“呼吸”清新的空气啊!氮氧化物这玩意儿,从水泥厂的烟囱里排出去,那对大气的污染可不小,就像个小恶魔,在空气中捣乱,让蓝天不再那么蓝,还可能影响到人们的健康呢。
那水泥厂脱硝工艺到底是怎么一回事呢?这里面可大有学问。
我们厂的老张,那可是这方面的行家。
他常说:“这脱硝啊,就像是给水泥厂的废气做一场大扫除。
”老张给我介绍过一种选择性催化还原法(SCR)。
这方法就像是一个魔法阵,在合适的温度下,把氨气注入到含有氮氧化物的废气中。
催化剂就像是魔法阵里的魔法棒,能让氨气和氮氧化物发生反应,把氮氧化物变成氮气和水。
氮气是空气中本来就大量存在的,水呢,排出去也没啥危害。
这就把原本有害的东西,变成了无害的。
我当时就忍不住感叹:“哇塞,这也太神奇了吧!”老张笑着说:“这还只是其中一种办法呢。
”还有一种叫选择性非催化还原法(SNCR)。
这就有点像打仗时的游击战了。
在没有催化剂的情况下,直接把还原剂喷到温度比较高的地方,让氮氧化物和还原剂反应。
不过这方法可不像SCR那么精确,就像打游击战一样,效果可能没那么好控制。
有次我跟厂里的小李讨论这个事儿,小李就说:“SNCR虽然简单,但是效果有时候不太稳定,就像个调皮的孩子,有时候听话,有时候又不听话。
”我也深有同感,不过它成本低啊,所以在一些要求不是特别高的情况下,也还是会被采用的。
除了这两种常见的方法,还有一些其他的技术也在不断发展。
我们厂里有时候也会请一些专家来交流。
有个专家就说:“现在的水泥厂脱硝工艺就像是一场科技竞赛,大家都在想办法让这个过程更高效、更环保。
”这话说得真对。
我们也在不断探索新的方法,想把水泥厂的氮氧化物排放降得更低。
在这个过程中,也不是一帆风顺的。
我记得有一次,我们厂在调整SCR工艺的参数。
- 1、下载文档前请自行甄别文档内容的完整性,平台不提供额外的编辑、内容补充、找答案等附加服务。
- 2、"仅部分预览"的文档,不可在线预览部分如存在完整性等问题,可反馈申请退款(可完整预览的文档不适用该条件!)。
- 3、如文档侵犯您的权益,请联系客服反馈,我们会尽快为您处理(人工客服工作时间:9:00-18:30)。
泥行业尾气排放的NOx 主要有热式NOx、燃料NOx及瞬时NOx等三种,其中主要部分为热式NOx。
•热式NOx:燃烧空气中的一部分N2,直接和O2反应生成各种氮氧化物。
温度在1200ºC以上时,燃烧空气的N2和O2分子反应生成热式NOx,在窑里它主要生成于燃烧区域,因为那个地方的温度很高。
这些NOx主要形成在高温回转窑的前部。
•燃料Nox :氮元素可以形成很多化合物,其以化物形式存于燃料中的氮元素,可以合空气中的氧发生反应形成各种氮氧化物。
燃料氮氧化物是由存于燃料里的氮元素在850~950ºC温度范围里燃烧形成的。
对于带分解炉的新型干法线,燃料NOx 主要生成于分解炉处。
•瞬时NOx:l碳氢化合物燃烧过程中分解的CH,CH2和C2等基团破坏了空气中的N2分子键,并经反应生成HCN,NH和N等原子基团,它们再与O,OH等基团反应生成NO;快速NOx只有在富燃的情况下,即碳氢化合物较多,氧浓度相对较低时才发生。
工艺优化:主要是通过优化水泥工艺、精心操控等技术,在保证水泥的正常烧成和水泥的质量情况下,挖掘潜力,最大可能的降低NOx;在欧洲水泥协会的BAT文件,该技术也被成为脱硝的主
要措施。
1.燃料氮含量的控制
2.提高生料易烧性
3.烧成操作优化
4.火焰冷却
5.分级燃烧
6.......
在欧美地区,很多水泥厂实施了该技术,并有效于降低烟囱处氮氧化物的浓度。
在水泥厂里,煤是通过喷煤管喷射进窑或分解炉的,并在喷煤管末端附近形成很强的火焰,其温度很高,窑里面的NOx主要在该火焰区域形成,因此为了减少NOx,对喷煤管进行优化是非常有必要的。
通常我们称能降低NOx生成的喷煤管为低氮燃烧器:根据氮氧化物的生成机理,主要通过采用空气分级燃烧、燃料分级燃烧、烟气再循环和低氮燃烧器等方法降低煤粉燃烧过程中氮氧化物的生成量。
该装置相对简单,投资、运行费用较低,是经济、有效的技术措施。
在水泥回转窑中,由于设置低的一次风/煤比率,低氮喷煤管在火焰内部形成一个还原气氛,该还原气氛能还原部分NOx成N2(由于低的一次风比率,在火焰内部形成一个还原性气氛,低氮燃烧器的空气比率为:6~8%,而常规喷煤管的空气比率为20~25%)。
低氮燃烧器减少NO的另外一个因素是:更均匀平稳的火焰流(避免高温峰点)
1.操作适用性
∙低氮燃烧器可以应用所有的水泥回转窑,可以安装在窑尾和分解炉,其效果都比较好。
∙另外该技术在国内外有很多的运行业绩,也是非常成熟的一种脱硝技术.
∙根据国家颁布“十二五”减排规划指南-环办[2010]97号文件,低氮燃烧器为推荐的一种技术。
∙该技术不需要很高的投资,而且可以对低氮喷煤管灵活设置
2.脱硝效率
∙根据中能环的实际水泥厂工程,低氮燃烧器的应用可以达到600~1000mg/Nm3的排放水平;
∙低氮燃烧器的脱氮效率从0~30%不等,(如果最初的NOx排放基准在2000mg/Nm3的水平,并且喷煤管处于优化的情况下运行,脱硝效率能达到30%)。
3.对水泥窑生产的影响
∙在实际的水泥生产过程中,该技术的脱硝效率并不是很平稳;
∙其脱硝效率具有局限性,针对NOx 排放要求较严的地区,单纯使用该技术,达标较为困难;
∙不适合在燃用高硫煤质或石油焦等燃料的时候使用
低氮燃烧器图片
分级燃烧降氮技术为国、内外常用的脱硝技术。
主要分为燃料分级燃烧和空气分级燃烧。
1.典型的分级燃烧原理主要如下
第一步是在燃料燃烧处于还原气氛中,形成富燃料区,以减少或抑制氮氧化物的生成;
第二步是未完全燃烧的燃料与三次风过量的燃用空气汇合,在富氧区完全燃烧。
2.该技术需基于水泥厂实际的工艺情况合理的进行设计,脱硝效率为10%~50%,具有投资
低、运行经济、安装/改造工期短等特点。
3.基于多年的水泥工艺经验,中能环将水泥工艺优化与分级燃烧技术合理的有机结合起来,
使分级燃烧装置发挥其最大的脱硝潜力,降低氮氧化物排放。
水泥厂空气分级燃烧脱硝系统
NCR是选择性非催化还原Selective Non-Catalytic Reduction 的英文缩写,SNCR技术是一种成熟的NOx控制处理技术。
此方法是在800~1200℃温度范围,将氮还原剂(一般是氨或尿素)喷入烟气中,将NOx还原,生成氮气和水,脱硝率一般在30~75%之间.
以NH3为还原剂,其反应式如下:
●4NH3 + 4NO +O2 → 4N2 + 6H2O
●4NH3 + 2NO + 2O2 → 4N2 + 6H2O
●8NH3 + 6NO2 → 7N2 + 12H2O
以尿素(CO(NH2)2)为还原剂时:
●CO(NH2)2 + H2O → 2NH3 + CO2
●4NH3 + 4NO + O2 → 4N2 + 6H2O
对燃烧过程中少量NO2,其化学反应为:
●8NH3 + 6NO2 → 7N2 + 12H2O
相比SCR选择催化还原技术,SNCR技术在电厂应用的相对较少,但根据水泥工艺的具体情况,SNCR 系统非常适合水泥厂的脱硝,该技术不用催化剂,设备运行费用省,具有一定的优势。
1.操作适用性
•该技术可应用于所有水泥窑;
•在国外水泥工业已广泛应用;
•根据国家颁布“十二五”减排规划指南-环办[2010]97号文件,低氮燃烧器为推荐的一种技术;
• SNCR脱硝装置投资较低,运行操作便利,可靠性较高。
2.脱硝效率
•大部分运行的SNCR装置,其设计的脱硝效率普遍在10-60%之间,控制的排放水平在500~800mg NOx/m3之间,该效果已足够满足当前的法规要求。
•基于中能环在水泥厂脱硝总包工程,通过CFD、Chemkin等软件的计算模拟,并以现场实测佐证,由中能环总包的水泥脱硝项目,脱硝效率最高在96%以上,NOx 排放浓度能稳定的控制在
100mg/Nm3以下。
3.对水泥窑生产的影响
•在实际的水泥生产过程中,SNCR操作便利,脱硝反应极快;
•对现有窑的运行影响小,可靠性非常高。
SCR是选择性非催化还原SelectiveCatalytic Reduction 的英文缩写,SCR技术是利用NH3与NO反应的选择性,在催化剂表面将富氧烟气中的NO还原成N2和H2O. NH3与NO反应在一个狭窄的温度范围内进行,不同的催化剂的作用温度不一样,使用最广泛的温度为350~400℃,最初的SCR催化剂是铂Pt等贵金属,70年代后期,日本人开始使用钒V、钛Ti、钨W等金属。
80年代,TiO2、ZrO2、V2O5等金属化合物开始得到应用,反应的温度窗口也得到的拓宽。
最新的SCR工业催化剂一般使用TiO2:为载体的 V2O5/WO3及MoO3等金属氧化物。
SCR是目前商业技术当中脱硝效果最好的成熟技术,其脱硝效率可以达到80%,甚至90%以上,但投资巨大,操作运行费用也非常高。
SCR其化学反应式如下:
●4NH3 + 4NO +O2 → 4N2 + 6H2O
●4NH3 + 2NO + 2O2 → 4N2 + 6H2
对燃烧过程中少量NO2,其化学反应为:
●8NH3 + 6NO2 → 7N2 + 12H2O
根据上述反应公式,可认为:脱硝率与NH3/NOx成正比,即如果脱硝率为80%~90%,则NH3/ NOx 近似为0.8~0.9。
发生反应的温度一般在300~400℃,在此温度下,脱硝率可达到80%以上并且未与NOx 反应的NH3逃脱率不超过6ppm.
1.操作适用性
•在水泥工业中,SCR工艺主要在3000~420℃的温度区间进行,基于这点,SCR在水泥工业的设计主要有以下两种:
–低尘废气应用装置:窑尾布袋后面,低粉尘,但相应温度角度,需额外能量身高废气温度;
–高尘废气应用装置:预热器出口处,温度为310~390℃,为SCR反应温度区间,但粉尘浓度
较高;
•投资及运行费用非常昂贵
•受水泥实际工况及运行费用的限制,SCR工艺运行于水泥工业的案例较少,世界范围内在水泥工业,目前只有几个案例在NOx 控制非常严格的欧洲地区。
2.脱硝效率
• SCR 的脱硝效率很高,可以达到90%以上;
•能轻松稳定的把窑尾烟囱的NOx排放控制在200mg/Nm3以下。
3.对水泥窑生产的影响
•优点:非常高的脱硝率,脱硝还原剂的使用效率高,氨逃逸极小;
•缺点:投资费用高,运行费用高,工艺控制繁琐。