抛光方法
塑料抛光的方法和技巧

塑料抛光的方法和技巧
1. 漂白剂法:将热水和漂白剂混合之后,涂在塑料表面,然后用温水和肥皂清洗干净。
2. 砂纸法:选择合适的砂纸,将塑料表面打磨,直到表面变得光滑,然后用肥皂水清洗干净。
3. 液体抛光剂法:选择适合塑料的液体抛光剂,将其涂在塑料表面,然后用旋转式抛光机进行抛光。
4. 热气法:将热气对准塑料表面,使塑料变软,然后用布或海绵轻柔擦拭,达到抛光的效果。
5. 牙膏法:将少量牙膏直接涂在塑料表面,然后用干净的布或海绵擦拭,可达到抛光的效果。
技巧:
1. 在进行塑料抛光之前,要先清洗干净塑料表面的污渍和灰尘。
2. 在进行抛光前,应该选择合适的工具和方法,避免对塑料表面造成伤害。
3. 抛光过程中应该保持手法轻柔,避免对塑料表面造成划痕。
4. 抛光完成后,一定要仔细清洗干净,避免残留抛光剂等物质对塑料表面造成损害。
抛光方法
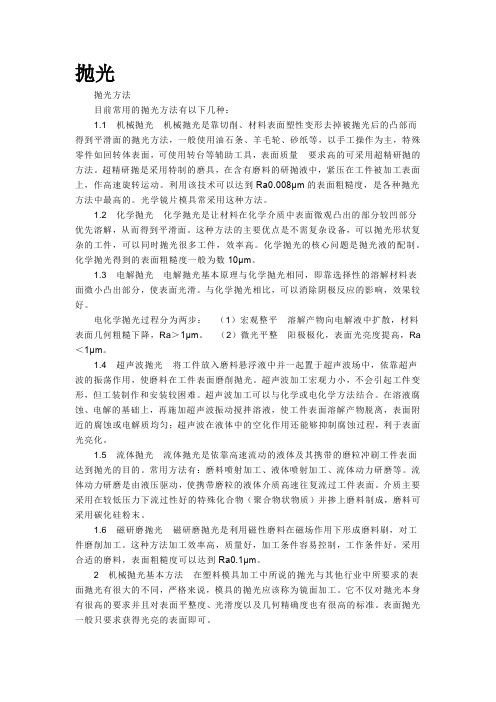
抛光抛光方法目前常用的抛光方法有以下几种:1.1机械抛光机械抛光是靠切削、材料表面塑性变形去掉被抛光后的凸部而得到平滑面的抛光方法,一般使用油石条、羊毛轮、砂纸等,以手工操作为主,特殊零件如回转体表面,可使用转台等辅助工具,表面质量要求高的可采用超精研抛的方法。
超精研抛是采用特制的磨具,在含有磨料的研抛液中,紧压在工件被加工表面上,作高速旋转运动。
利用该技术可以达到Ra0.008μm的表面粗糙度,是各种抛光方法中最高的。
光学镜片模具常采用这种方法。
1.2化学抛光化学抛光是让材料在化学介质中表面微观凸出的部分较凹部分优先溶解,从而得到平滑面。
这种方法的主要优点是不需复杂设备,可以抛光形状复杂的工件,可以同时抛光很多工件,效率高。
化学抛光的核心问题是抛光液的配制。
化学抛光得到的表面粗糙度一般为数10μm。
1.3电解抛光电解抛光基本原理与化学抛光相同,即靠选择性的溶解材料表面微小凸出部分,使表面光滑。
与化学抛光相比,可以消除阴极反应的影响,效果较好。
电化学抛光过程分为两步:(1)宏观整平溶解产物向电解液中扩散,材料表面几何粗糙下降,Ra>1μm。
(2)微光平整阳极极化,表面光亮度提高,Ra <1μm。
1.4超声波抛光将工件放入磨料悬浮液中并一起置于超声波场中,依靠超声波的振荡作用,使磨料在工件表面磨削抛光。
超声波加工宏观力小,不会引起工件变形,但工装制作和安装较困难。
超声波加工可以与化学或电化学方法结合。
在溶液腐蚀、电解的基础上,再施加超声波振动搅拌溶液,使工件表面溶解产物脱离,表面附近的腐蚀或电解质均匀;超声波在液体中的空化作用还能够抑制腐蚀过程,利于表面光亮化。
1.5流体抛光流体抛光是依靠高速流动的液体及其携带的磨粒冲刷工件表面达到抛光的目的。
常用方法有:磨料喷射加工、液体喷射加工、流体动力研磨等。
流体动力研磨是由液压驱动,使携带磨粒的液体介质高速往复流过工件表面。
介质主要采用在较低压力下流过性好的特殊化合物(聚合物状物质)并掺上磨料制成,磨料可采用碳化硅粉末。
不锈钢抛光的方法
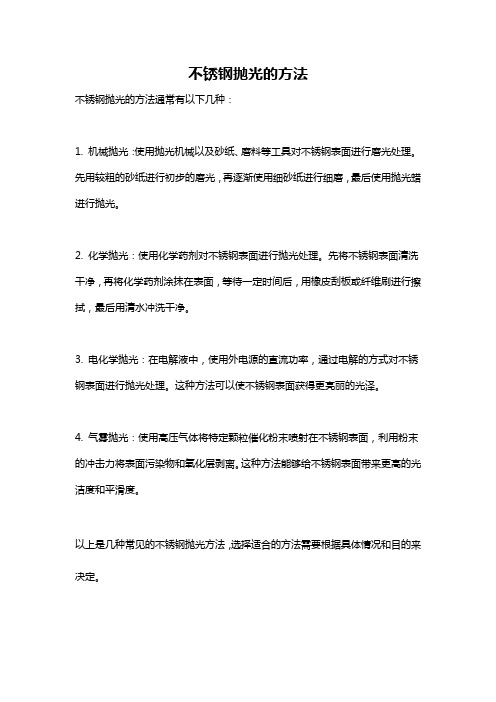
不锈钢抛光的方法
不锈钢抛光的方法通常有以下几种:
1. 机械抛光:使用抛光机械以及砂纸、磨料等工具对不锈钢表面进行磨光处理。
先用较粗的砂纸进行初步的磨光,再逐渐使用细砂纸进行细磨,最后使用抛光蜡进行抛光。
2. 化学抛光:使用化学药剂对不锈钢表面进行抛光处理。
先将不锈钢表面清洗干净,再将化学药剂涂抹在表面,等待一定时间后,用橡皮刮板或纤维刷进行擦拭,最后用清水冲洗干净。
3. 电化学抛光:在电解液中,使用外电源的直流功率,通过电解的方式对不锈钢表面进行抛光处理。
这种方法可以使不锈钢表面获得更亮丽的光泽。
4. 气雾抛光:使用高压气体将特定颗粒催化粉末喷射在不锈钢表面,利用粉末的冲击力将表面污染物和氧化层剥离。
这种方法能够给不锈钢表面带来更高的光洁度和平滑度。
以上是几种常见的不锈钢抛光方法,选择适合的方法需要根据具体情况和目的来决定。
金属镜面抛光方法

金属镜面抛光方法
金属制品在使用过程中,由于摩擦、氧化等因素,表面容易产生划痕、氧化、锈蚀等问题。
为了让金属制品保持亮丽的外观,需要进行抛光处理。
下面介绍几种金属镜面抛光方法。
1. 机械抛光法
机械抛光法是将金属制品放在抛光机上,通过旋转磨头、研磨片等工具对金属表面进行抛光。
机械抛光法可分为手动和自动两种方式,一般适用于大批量的金属制品。
2. 化学抛光法
化学抛光法是在金属制品表面施加特定的化学物质,使其表面氧化物被溶解掉,从而达到抛光的效果。
化学抛光法适用于特殊形状的金属制品,如管道、弯管等。
3. 电解抛光法
电解抛光法是将金属制品放在电解槽中,通过电解作用将金属表面进行抛光。
电解抛光法的优点是抛光效果好,表面光洁度高,适用于对表面光洁度要求高的金属制品。
4. 光学抛光法
光学抛光法是以光学原理为基础,通过利用光学仪器对金属表面进行抛光。
光学抛光法的优点是抛光效果好,表面光洁度高,适用于对表面光洁度要求极高的金属制品。
以上是金属镜面抛光的几种方法,具体的抛光方法应根据不同的金属制品和要求进行选择。
常用的几种抛光方法

常用的几种抛光方法抛光是一种常见的表面处理方法,用于改善工件表面的平滑度、光泽度和装饰效果。
在工业制造、汽车修复、家具制作等领域中广泛应用。
以下是常用的几种抛光方法:1.机械抛光:机械抛光是通过机械设备进行表面处理的方法。
常用的机械设备有抛光机、砂带机、砂轮机等。
通过磨头或砂纸、砂轮等磨料进行抛光,能够去除工件表面的凹凸不平和氧化层,提高工件表面的平滑度和光泽度。
2.手工抛光:手工抛光是通过人工操作进行的表面处理方法。
常用的手工抛光工具有砂纸、抛光布、抛光膏等。
手工抛光较为简便灵活,适用于较小的工件或不规则形状的工件。
手工抛光通常分为粗磨、中磨和精磨等步骤,每一步都使用不同的磨料和抛光工具,最终达到所需的光洁度和光泽度。
3.化学抛光:化学抛光是利用化学药品进行表面处理的方法。
常用的化学药品有酸洗剂、腐蚀剂、除漆剂等。
化学抛光能够去除工件表面的氧化层、锈蚀、油污等,使工件恢复光洁的表面。
但需要注意的是,化学药品的使用需要具备一定的安全措施,以免对工人和环境造成伤害。
4.电解抛光:电解抛光是利用电解作用进行表面处理的方法。
通过将工件作为阳极,在电解液中进行电解,使工件表面产生物理和化学反应,从而获得平滑光洁的表面。
电解抛光能够去除工件表面的细微瑕疵,提高其表面质量和美观度。
但使用电解抛光需要注意安全防护,避免电解液的溅入眼睛或皮肤。
5.光学抛光:光学抛光是在光学显微镜下进行的高精度抛光方法。
它通常用于制造光学元件、半导体材料等需要极高光洁度和平整度的工件。
光学抛光的磨料和抛光工具要求非常严格,其中常用的抛光液有氧化铁、氧化铝等。
光学抛光的过程需要十分小心和耐心,以获得所需的高精度光洁表面。
总的来说,不同的抛光方法有不同的适用场景和效果。
选择合适的抛光方法需要根据工件材质、表面质量要求、生产效率和环境安全等因素综合考虑。
在实际应用中,可以根据需要结合不同抛光方法,进行多种方法的组合使用,以获得最佳的抛光效果。
抛光原理及方法

抛光原理及方法
抛光是一种通过磨擦和摩擦作用使工件表面光洁度提高的表面处理方法。
它可以去除工件表面的划痕、氧化层、腐蚀层,达到提高工件表面质量和光洁度的目的。
以下是抛光的原理与方法:
原理:
1.磨擦作用:通过使用磨料和磨具在工件表面产生一定的摩擦,从而剥除表面的不均匀物质并平滑表面。
2.热作用:在抛光过程中,摩擦会产生热量,使工件表面的薄
层材料软化并流动,从而填补表面微小孔隙和划痕,提高表面光洁度。
方法:
1.机械抛光:使用磨料和磨具在工件表面进行机械磨削,常用
的机械抛光方法有手工抛光、磨头抛光和自动抛光机等。
2.化学抛光:使用一定的化学药品溶解或改变工件表面的化学
成分,从而达到抛光的效果。
常用的化学抛光方法有电解抛光和酸洗抛光等。
3.电解抛光:将工件作为阳极,通过外加电压使金属离子从工
件表面溶解,从而改善表面质量和光洁度。
4.喷砂抛光:使用高压气体将磨料或砂粒喷射到工件表面,以
刮蚀和磨削的方式去除表面不均匀物质,适用于较粗糙的表面抛光。
以上是抛光的原理及常用方法,根据不同的工件和要求,选择适当的抛光方法可以有效改善工件的表面质量和光洁度。
目前几种最常用的抛光方式

最长常用的几种抛光方式1.1机械抛光方式所谓的机械抛光就是靠切削、材料表面塑性变形去掉被抛光后的凸部而得到平滑面的抛光方法,大多采用油石条、羊毛轮、砂纸等,以手工操作为主,特殊零件如回转体表面,可使用转台等辅佐工具,表面质量要求高的可采用超精研抛的方式。
超精研抛是采用特制的磨具,在含有磨料的研抛液中,紧压在工件被加工表面上,作高速旋转运动。
利用该技术可以达到Ra0.008μm的表面粗糙度,是各种抛光方法中最高的。
光学镜片模具常采用这种方法。
1.2化学抛光方式化学抛光工艺是让材料在化学介质中表面微观凸出的部分较凹部分优先溶解,从而得到平滑面。
这种抛光方法主要优点是不需复杂设备,可以抛光形状复杂的工件,可以同时抛光很多工件,效率高。
化学抛光的核心问题是抛光液的配制。
化学抛光得到的表面粗糙度一般为数10μm。
1.3电解抛光方式电解抛光的基本原理与化学抛光相同,即靠选择性的溶解材料表面微小凸出部分,使表面光滑。
与化学抛光相比,可以消除阴极反应的影响,效果较好。
电化学抛光过程分为一下两步:(1)宏观整平溶解产物向电解液中扩散,材料表面几何粗糙下降,Ra>1μm。
(2)微光平整阳极极化,表面光亮度提高,Ra<1μm。
1.4超声波抛光方式将工件放入磨料悬浮液中并一起置于超声波场中,依靠超声波的振荡作用,让磨料在工件表面磨削抛光。
超声波加工宏观力小,不会引起工件变形,但工装制作和安装较困难。
超声波加工可以与化学或电化学方法结合。
在溶液腐蚀、电解的基础上,再施加超声波振动搅拌溶液,使工件表面溶解产物脱离,表面附近的腐蚀或电解质均匀;超声波在液体中的空化作用还能够抑制腐蚀过程,利于表面光亮化。
1.5流体式抛光方法流体抛光方法是依靠高速流动的液体及其携带的磨粒冲刷工件表面达到抛光的目的。
常用方法有:磨料喷射加工、液体喷射加工、流体动力研磨等。
流体动力研磨是由液压驱动,使携带磨粒的液体介质高速往复流过工件表面。
介质主要采用在较低压力下流过性好的特殊化合物(聚合物状物质)并掺上磨料制成,磨料可采用碳化硅粉末。
目前常用的几种抛光方法
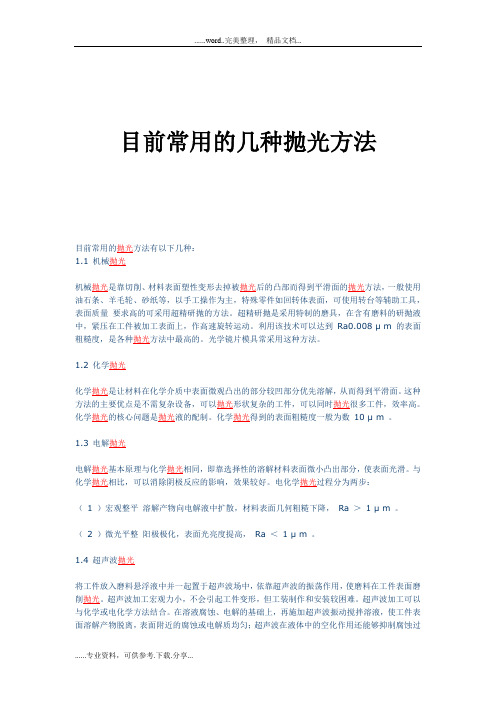
目前常用的几种抛光方法目前常用的抛光方法有以下几种:1.1 机械抛光机械抛光是靠切削、材料表面塑性变形去掉被抛光后的凸部而得到平滑面的抛光方法,一般使用油石条、羊毛轮、砂纸等,以手工操作为主,特殊零件如回转体表面,可使用转台等辅助工具,表面质量要求高的可采用超精研抛的方法。
超精研抛是采用特制的磨具,在含有磨料的研抛液中,紧压在工件被加工表面上,作高速旋转运动。
利用该技术可以达到Ra0.008 μ m 的表面粗糙度,是各种抛光方法中最高的。
光学镜片模具常采用这种方法。
1.2 化学抛光化学抛光是让材料在化学介质中表面微观凸出的部分较凹部分优先溶解,从而得到平滑面。
这种方法的主要优点是不需复杂设备,可以抛光形状复杂的工件,可以同时抛光很多工件,效率高。
化学抛光的核心问题是抛光液的配制。
化学抛光得到的表面粗糙度一般为数10 μ m 。
1.3 电解抛光电解抛光基本原理与化学抛光相同,即靠选择性的溶解材料表面微小凸出部分,使表面光滑。
与化学抛光相比,可以消除阴极反应的影响,效果较好。
电化学抛光过程分为两步:(1 )宏观整平溶解产物向电解液中扩散,材料表面几何粗糙下降,Ra > 1 μ m 。
(2 )微光平整阳极极化,表面光亮度提高,Ra < 1 μ m 。
1.4 超声波抛光将工件放入磨料悬浮液中并一起置于超声波场中,依靠超声波的振荡作用,使磨料在工件表面磨削抛光。
超声波加工宏观力小,不会引起工件变形,但工装制作和安装较困难。
超声波加工可以与化学或电化学方法结合。
在溶液腐蚀、电解的基础上,再施加超声波振动搅拌溶液,使工件表面溶解产物脱离,表面附近的腐蚀或电解质均匀;超声波在液体中的空化作用还能够抑制腐蚀过程,利于表面光亮化。
1.5 流体抛光流体抛光是依靠高速流动的液体及其携带的磨粒冲刷工件表面达到抛光的目的。
常用方法有:磨料喷射加工、液体喷射加工、流体动力研磨等。
流体动力研磨是由液压驱动,使携带磨粒的液体介质高速往复流过工件表面。
- 1、下载文档前请自行甄别文档内容的完整性,平台不提供额外的编辑、内容补充、找答案等附加服务。
- 2、"仅部分预览"的文档,不可在线预览部分如存在完整性等问题,可反馈申请退款(可完整预览的文档不适用该条件!)。
- 3、如文档侵犯您的权益,请联系客服反馈,我们会尽快为您处理(人工客服工作时间:9:00-18:30)。
抛光方法目前常用的抛光方法有以下几种:1.1机械抛光机械抛光是靠切削、材料表面塑性变形去掉被抛光后的凸部而得到平滑面的抛光方法,一般使用油石条、羊毛轮、砂纸等,以手工操作为主,特殊零件如回转体表面,可使用转台等辅助工具,表面质量要求高的可采用超精研抛的方法。
超精研抛是采用特制的磨具,在含有磨料的研抛液中,紧压在工件被加工表面上,作高速旋转运动。
利用该技术可以达到Ra0.008μm的表面粗糙度,是各种抛光方法中最高的。
光学镜片模具常采用这种方法。
1.2化学抛光化学抛光是让材料在化学介质中表面微观凸出的部分较凹部分优先溶解,从而得到平滑面。
这种方法的主要优点是不需复杂设备,可以抛光形状复杂的工件,可以同时抛光很多工件,效率高。
化学抛光的核心问题是抛光液的配制。
化学抛光得到的表面粗糙度一般为数10μm。
1.3电解抛光电解抛光基本原理与化学抛光相同,即靠选择性的溶解材料表面微小凸出部分,使表面光滑。
与化学抛光相比,可以消除阴极反应的影响,效果较好。
电化学抛光过程分为两步:(1)宏观整平溶解产物向电解液中扩散,材料表面几何粗糙下降,Ra>1μm。
(2)微光平整阳极极化,表面光亮度提高,Ra<1μm。
1.4超声波抛光将工件放入磨料悬浮液中并一起置于超声波场中,依靠超声波的振荡作用,使磨料在工件表面磨削抛光。
超声波加工宏观力小,不会引起工件变形,但工装制作和安装较困难。
超声波加工可以与化学或电化学方法结合。
在溶液腐蚀、电解的基础上,再施加超声波振动搅拌溶液,使工件表面溶解产物脱离,表面附近的腐蚀或电解质均匀;超声波在液体中的空化作用还能够抑制腐蚀过程,利于表面光亮化。
1.5流体抛光流体抛光是依靠高速流动的液体及其携带的磨粒冲刷工件表面达到抛光的目的。
常用方法有:磨料喷射加工、液体喷射加工、流体动力研磨等。
流体动力研磨是由液压驱动,使携带磨粒的液体介质高速往复流过工件表面。
介质主要采用在较低压力下流过性好的特殊化合物(聚合物状物质)并掺上磨料制成,磨料可采用碳化硅粉末。
1.6磁研磨抛光磁研磨抛光是利用磁性磨料在磁场作用下形成磨料刷,对工件磨削加工。
这种方法加工效率高,质量好,加工条件容易控制,工作条件好。
采用合适的磨料,表面粗糙度可以达到Ra0.1μm。
在塑料模具加工中所说的抛光与其他行业中所要求的表面抛光有很大的不同,严格来说,模具的抛光应该称为镜面加工。
它不仅对抛光本身有很高的要求并且对表面平整度、光滑度以及几何精确度也有很高的标准。
表面抛光一般只要求获得光亮的表面即可。
镜面加工的标准分为四级:AO=Ra0.008μm,A1=Ra0.016μm,A3=Ra0.032μm,A4=Ra0.063μm,由于电解抛光、流体抛光等方法很难精确控制零件的几何精确度,而化学抛光、超声波抛光、磁研磨抛光等方法的表面质量又达不到要求,所以精密模具的镜面加工还是以机械抛光为主。
2.1机械抛光基本程序要想获得高质量的抛光效果,最重要的是要具备有高质量的油石、砂纸和钻石研磨膏等抛光工具和辅助品。
而抛光程序的选择取决于前期加工后的表面状况,如机械加工、电火花加工,磨加工等等。
机械抛光的一般过程如下:(1)粗抛经铣、电火花、磨等工艺后的表面可以选择转速在35000—40000rpm的旋转表面抛光机或超声波研磨机进行抛光。
常用的方法有利用直径Φ3mm、WA#400的轮子去除白色电火花层。
然后是手工油石研磨,条状油石加煤油作为润滑剂或冷却剂。
一般的使用顺序为#180~#240~#320~#400~#600~#800~#1000。
许多模具制造商为了节约时间而选择从#400开始。
(2)半精抛半精抛主要使用砂纸和煤油。
砂纸的号数依次为:#400~#600~#800~#1000~#1200~#1500。
实际上#1500砂纸只用适于淬硬的模具钢(52HRC以上),而不适用于预硬钢,因为这样可能会导致预硬钢件表面烧伤。
(3)精抛精抛主要使用钻石研磨膏。
若用抛光布轮混合钻石研磨粉或研磨膏进行研磨的话,则通常的研磨顺序是9μm(#1800)~6μm(#3000)~3μm(#8000)。
9μm的钻石研磨膏和抛光布轮可用来去除#1200和#1500号砂纸留下的发状磨痕。
接着用粘毡和钻石研磨膏进行抛光,顺序为1μm(#14000)~1/2μm(#60000)~1/4μm(#100000)。
精度要求在1μm以上(包括1μm)的抛光工艺在模具加工车间中一个清洁的抛光室内即可进行。
若进行更加精密的抛光则必需一个绝对洁净的空间。
灰尘、烟雾,头皮屑和口水沫都有可能报废数个小时工作后得到的高精密抛光表面。
2.2机械抛光中要注意的问题用砂纸抛光应注意以下几点:(1)用砂纸抛光需要利用软的木棒或竹棒。
在抛光圆面或球面时,使用软木棒可更好的配合圆面和球面的弧度。
而较硬的木条像樱桃木,则更适用于平整表面的抛光。
修整木条的末端使其能与钢件表面形状保持吻合,这样可以避免木条(或竹条)的锐角接触钢件表面而造成较深的划痕。
(2)当换用不同型号的砂纸时,抛光方向应变换45°~90°,这样前一种型号砂纸抛光后留下的条纹阴影即可分辨出来。
在换不同型号砂纸之前,必须用100%纯棉花沾取酒精之类的清洁液对抛光表面进行仔细的擦拭,因为一颗很小的沙砾留在表面都会毁坏接下去的整个抛光工作。
从砂纸抛光换成钻石研磨膏抛光时,这个清洁过程同样重要。
在抛光继续进行之前,所有颗粒和煤油都必须被完全清洁干净。
(3)为了避免擦伤和烧伤工件表面,在用#1200和#1500砂纸进行抛光时必须特别小心。
因而有必要加载一个轻载荷以及采用两步抛光法对表面进行抛光。
用每一种型号的砂纸进行抛光时都应沿两个不同方向进行两次抛光,两个方向之间每次转动45°~90°。
钻石研磨抛光应注意以下几点:(1)这种抛光必须尽量在较轻的压力下进行特别是抛光预硬钢件和用细研磨膏抛光时。
在用#8000研磨膏抛光时,常用载荷为100~200g/cm2,但要保持此载荷的精准度很难做到。
为了更容易做到这一点,可以在木条上做一个薄且窄的手柄,比如加一铜片;或者在竹条上切去一部分而使其更加柔软。
这样可以帮助控制抛光压力,以确保模具表面压力不会过高。
(2)当使用钻石研磨抛光时,不仅是工作表面要求洁净,工作者的双手也必须仔细清洁。
(3)每次抛光时间不应过长,时间越短,效果越好。
如果抛光过程进行得过长将会造成“橘皮”和“点蚀”。
(4)为获得高质量的抛光效果,容易发热的抛光方法和工具都应避免。
比如:抛光轮抛光,抛光轮产生的热量会很容易造成“橘皮”。
(5)当抛光过程停止时,保证工件表面洁净和仔细去除所有研磨剂和润滑剂非常重要,随后应在表面喷淋一层模具防锈涂层。
由于机械抛光主要还是靠人工完成,所以抛光技术目前还是影响抛光质量的主要原因。
除此之外,还与模具材料、抛光前的表面状况、热处理工艺等有关。
优质的钢材是获得良好抛光质量的前提条件,如果钢材表面硬度不均或特性上有差异,往往会产生抛光困难。
钢材中的各种夹杂物和气孔都不利于抛光。
3.1不同硬度对抛光工艺的影响硬度增高使研磨的困难增大,但抛光后的粗糙度减小。
由于硬度的增高,要达到较低的粗糙度所需的抛光时间相应增长。
同时硬度增高,抛光过度的可能性相应减少。
3.2工件表面状况对抛光工艺的影响钢材在切削机械加工的破碎过程中,表层会因热量、内应力或其他因素而损坏,切削参数不当会影响抛光效果。
电火花加工后的表面比普通机械加工或热处理后的表面更难研磨,因此电火花加工结束前应采用精规准电火花修整,否则表面会形成硬化薄层。
如果电火花精修规准选择不当,热影响层的深度最大可达0.4mm。
硬化薄层的硬度比基体硬度高,必须去除。
因此最好增加一道粗磨加工,彻底清除损坏表面层,构成一片平均粗糙的金属面,为抛光加工提供一个良好基础。
抛丸与喷砂的区别抛丸是利用高速旋转的叶轮把小钢丸或者小铁丸抛掷出去高速撞击零件表面,故可以除去零件表面的氧化层。
同时钢丸或铁丸高速撞击零件表面,造成零件表面的晶格扭曲变形,使表面硬度增高,是对零件表面进行清理的一种方法,抛丸常用来铸件表面的清理或者对零件表面进行强化处理。
一般抛丸用于规则形状等,几个抛头上下左右一起,效率高,污染小。
修、造船业,抛丸、喷砂是普遍使用的。
但是无论是抛丸还是喷砂,都是使用压缩空气的形式。
当然并不是抛丸就非用高速旋转的叶轮不可。
在修、造船业一般来说,抛丸(小钢丸)多用在钢板预处理(涂装前除锈);喷砂(修、造船业用的是矿砂)多用在成型的船舶或者分段,作用是把钢板上的旧油漆和锈除掉,重新涂装。
在修、造船业,抛丸、喷砂的主要作用是增加钢板涂装油漆的附着力。
其实铸造件清理不只是用抛丸,对于大件一般先进行滚筒清砂,就是把铸造件的冒口切除后放在滚筒内滚,由零件在滚筒内互相碰撞,把表面的砂大部分先清掉再进行抛丸或喷丸的,抛丸丸子大小是1.5mm。
研究表明,就破坏而言,金属材料表面存在拉应力时比压应力要容易的多,表面呈压应力时,材料的疲劳寿命大大提高,因此,对于轴类等容易疲劳断裂的部件通常采用喷丸形成表面压应力,提高产品寿命,此外,金属金属材料对拉伸很敏感,这就是材料的拉伸强度比压缩强度低的多的原因,这也是金属材料一般用拉伸强度(屈服,抗拉)表示材料性能的原因。
我们日常乘坐的汽车的钢板的工作面就是用喷丸来强化的,可以显著的提高材料的抗疲劳强度。
抛丸是用电机带动叶轮体旋转,靠离心力的作用,将直径在0.2~3.0的丸子(有铸丸\切丸\不锈钢丸等)抛向工件的表面,使工件的表面达到一定的粗造度,使工件变的美观,或着改变工件的焊接拉应力为压应力,提高工件的使用寿命.几乎用于机械的大多数领域,修造船\汽车零部件\飞机部件\枪炮坦克表面\桥梁\钢结构\玻璃\钢板\管道\等等.喷砂(丸)是用压缩空气作为动力将直径在40~120目的砂或0.1~2.0左右的丸喷向工件的表面,使工件达到同样的效果.丸粒的大小不同,达到的处理效果就不一样.重点提出:喷丸同样能起到强化的作用.现在国内的设备走进了一个误区,认为只有抛丸才能达到强化的目的.美国\日本的企业用于强化的是抛喷丸并用的!各有各的优势.比如象齿轮这样的工件,抛丸的出丸角度无法改变,只能用变频改变初速度.但它处理的量大,速度快,而喷丸则正好于之相反,抛丸的效果就没有喷丸的效果好喷砂是利用压缩空气把石英砂高速吹出去对零件表面进行清理的一种方法。
工厂里也叫吹砂,不仅去锈,还可以顺带除油,对涂装来说非常有用。
常用于零件表面除锈;对零件表面修饰(市场卖的小型的湿式喷砂机就是这个用途,砂粒通常是刚玉,介质是水);在钢结构中,应用高强螺栓进行联接是一种比较先进的方法,由于高强联接是利用结合面之间的摩擦来传力的,所以对结合表面的质量要求很高,这时必须用喷砂对结合表面进行处理。