CNC机加工FMEA模板
FMEA 分析模板
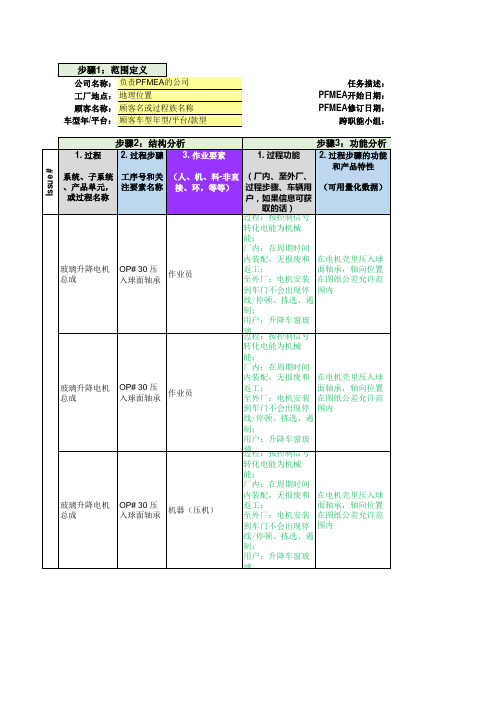
和产品特性
系统、子系统 工序号和关 (人、机、料-非直 (厂内、至外厂、
、产品单元, 注要素名称 接、环,等等) 过程步骤、车辆用 (可用量化数据)
或过程名称
户,如果信息可获
取的话) 过程:按控制信号
转化电能为机械
能;
厂内:在周期时间
内装配,无报废和 在电机壳里压入球
玻璃升降电机 总成
OP# 30 压 入球面轴承
制;
用户:升降车窗玻
璃
过程失效模式及影响分析 - PFMEA
PFMEA项目名称 PFMEA开始日期 最新修订日期 小组名单
:功能分析
3. 作业要素的功 能和过程特性
1. 失效影响 (FE)
(厂内、至外厂、过程步骤、 车辆用户,如果信息可获取的
话)
步骤4:失效分析
2. 过程步骤的失效模式 (FM)
3. 作业要素的失效原因 (FC)
据
进行 中
更新严重度 (S) 更新发生度 (O) 更新探测度 (D) 更新DFMEA AP
备注
持续改进
历史/变更授权 (如适用)
至外厂:无;
用户:车窗玻璃升降困难 (7)
手册(草案)中例子不清晰
8
轴承轴向位置没有达 到,间距过小
压机在还没压到位就停止 了(压力太小)
- PFMEA
PFMEA编号: 按公司内部规定 过程负责人: 即PFMEA负责人
保密等级: 例如:对外/机密/内部使用
当前针对FC的 预防性控制措施
(PC)
步骤5:PFMEA 风险分析
过程:机械能损失,因为球面
轴承与转子间摩擦过大,球面
作业员从料箱拿取 正确型号的清洁的 球面轴承,并放到 压机的上止位
FMEA范例

FMEA 編號Number:頁碼Page:準備人Prepared By:潛在的失效模式及效應分析表POTENTIAL FAILURE MODE AND EFFECTS ANALYSIS(過程PROCESS FMEA)過程責任部門Process Responsibility: 品質部 QA Dept.項目名稱 Item: 關鍵日期Key Date: 2009.09.07車型年/車輛類工FMEA 編號Number:頁碼Page:準備人Prepared By:潛在的失效模式及效應分析表POTENTIAL FAILURE MODE AND EFFECTS ANALYSIS(過程PROCESS FMEA)過程責任部門Process Responsibility: 品質部 QA Dept.項目名稱 Item: 關鍵日期Key Date: 2009.09.07車型年/車輛類工FMEA 編號Number:頁碼Page:準備人Prepared By:潛在的失效模式及效應分析表POTENTIAL FAILURE MODE AND EFFECTS ANALYSIS(過程PROCESS FMEA)過程責任部門Process Responsibility: 品質部 QA Dept.項目名稱 Item: 關鍵日期Key Date: 2009.09.07車型年/車輛類工FMEA 編號Number:頁碼Page:準備人Prepared By:潛在的失效模式及效應分析表POTENTIAL FAILURE MODE AND EFFECTS ANALYSIS(過程PROCESS FMEA)過程責任部門Process Responsibility: 品質部 QA Dept.項目名稱 Item: 關鍵日期Key Date: 2009.09.07車型年/車輛類工FMEA 編號Number:頁碼Page:準備人Prepared By:潛在的失效模式及效應分析表POTENTIAL FAILURE MODE AND EFFECTS ANALYSIS(過程PROCESS FMEA)過程責任部門Process Responsibility: 品質部 QA Dept.項目名稱 Item: 關鍵日期Key Date: 2009.09.07車型年/車輛類工machiningFMEA 編號Number:頁碼Page:準備人Prepared By:潛在的失效模式及效應分析表POTENTIAL FAILURE MODE AND EFFECTS ANALYSIS(過程PROCESS FMEA)過程責任部門Process Responsibility: 品質部 QA Dept.項目名稱 Item: 關鍵日期Key Date: 2009.09.07車型年/車輛類工FMEA 編號Number:頁碼Page:準備人Prepared By:潛在的失效模式及效應分析表POTENTIAL FAILURE MODE AND EFFECTS ANALYSIS(過程PROCESS FMEA)過程責任部門Process Responsibility: 品質部 QA Dept.項目名稱 Item: 關鍵日期Key Date: 2009.09.07車型年/車輛類工FMEA 編號Number:頁碼Page:準備人Prepared By:潛在的失效模式及效應分析表POTENTIAL FAILURE MODE AND EFFECTS ANALYSIS(過程PROCESS FMEA)過程責任部門Process Responsibility: 品質部 QA Dept.項目名稱 Item: 關鍵日期Key Date: 2009.09.07車型年/車輛類工FMEA 編號Number:頁碼Page:準備人Prepared By:潛在的失效模式及效應分析表POTENTIAL FAILURE MODE AND EFFECTS ANALYSIS(過程PROCESS FMEA)過程責任部門Process Responsibility: 品質部 QA Dept.項目名稱 Item: 關鍵日期Key Date: 2009.09.07車型年/車輛類工FMEA 編號Number:頁碼Page:準備人Prepared By:潛在的失效模式及效應分析表POTENTIAL FAILURE MODE AND EFFECTS ANALYSIS(過程PROCESS FMEA)過程責任部門Process Responsibility: 品質部 QA Dept.項目名稱 Item: 關鍵日期Key Date: 2009.09.07車型年/車輛類工。
机加工件PFMEA 样例

项目名称:
XXX
过程责任部门:XXX
关键日期:
核心小組:
原材料宽度偏大,(超差上
限)送了不顺无法生存导致
模具错位.2
铁板分条时刀口之隔
片使用时间长,不锋
利
3
同一规格之材料抽一卷用卡
尺检验宽度8
原材料宽度偏小,(超差下
限)模具错位.2铁板分条时刀口之隔
片位置偏移所致.3
同一规格之材料抽一卷用卡
尺检验宽度8
原材料厚度偏大,(超差上
限)外观会擦伤,角度小无
法组装退货外7
铁板压沿处理不好,
成型型腔发生变异.2
同一规格之材料抽一卷用千
分尺检验厚度 T9
原材料厚度偏小,(超差下
限)角度大无法組裝.退貨.7铁板压沿处理不好,
成型型腔发生变异.2
同一规格之材料抽一卷用千
分尺检验厚度 T9
(过程FMEA)
现行预防过
程控制现行探测过程控制
探测
度(D)
潜在失效模式潜在失效后果严
重
度
(S)
分
类潜在失效起因/机理
頻度
(O)
潜在失效模式及后果分析
Failure Mode and Effect Analysis
制作年度: MM/DD/YYYY MM/DD/Y A,B,C, D
过程功能
或要求
样品预生产量产
進料檢
驗
FMEA 编号:
編制者:FMEA 日期:
过程FMEA)
页码: 第 页 共 页
/DD/YYYY
Abc。
FMEA模板及介绍
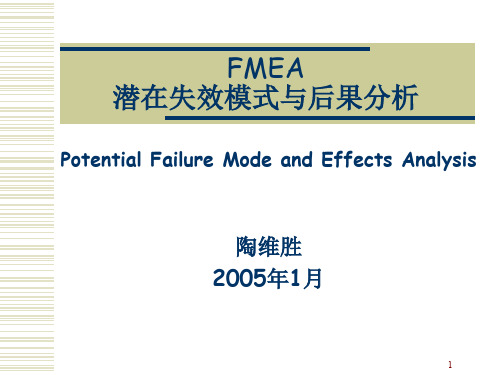
果。 要清楚地说明该失效模式是否会影响到安全性,或
与法规不符。 不同级别的系统、子系统或零件之间存在着系统层
次上的关系。
Prepared by Justin Tao Not Copy Without Permission
Prepared by Justin Tao Not Copy Without Permission
33
2. 特性分类
按状态分: 产品特性和过程特性
按重要程度分: 1)关键特性: 与安全、法规有关的关键特性(特殊特性) 与功能、装配有关的关键特性(重要特性) 2)普通特性:除关键特性之外的所有特性
任何一个产品应该有关键特性,但不易太多,运 用二八原则,抓住关键的少数。
Prepared by Justin Tao Not Copy Without Permission
是指失效发生的根本原因,其作业结果的显 现就是失效模式。
Prepared by Justin Tao Not Copy Without Permission
28
12. PFMEA现行过程控制
现行过程控制 :
是指尽可能阻止失效模式或失效起因/机理的 发生,或者探测将发生的失效模式或失效起因 /机理的控制的描述。
FMEA 潜在失效模式与后果分析
Potential Failure Mode and Effects Analysis
陶维胜 2005年1月
1
FMEA理解
预见风险,防止失败,促进提升 周全考虑,应对风险,事半功倍
Prepared by Justin Tao Not Copy Without Permission
fmea及对应控制计划的模板

fmea及对应控制计划的模板FMEA(Failure Mode and Effects Analysis)是一种用于识别和评估潜在故障模式及其对系统性能和安全性的影响的方法。
对应的控制计划是为了降低或消除潜在故障模式的风险而制定的一系列控制措施。
下面是一个常见的FMEA及对应控制计划的模板,供参考:1. FMEA模板:- 故障模式(Failure Mode):列出可能的故障模式。
- 故障原因(Failure Cause):对每个故障模式列出可能的原因。
- 故障影响(Failure Effect):描述每个故障模式对系统性能和安全性的影响。
- 严重度(Severity):评估每个故障模式的严重程度,通常使用1-10的评分,10表示最严重。
- 发现性(Detection):评估当前探测到故障模式的能力,通常使用1-10的评分,10表示最容易发现。
- 发生性(Occurrence):评估每个故障模式发生的可能性,通常使用1-10的评分,10表示最容易发生。
- RPN(Risk Priority Number):根据严重度、发现性和发生性计算出的风险优先级数值,用于确定优先处理的故障模式。
2. 对应控制计划模板:- 控制措施(Control Measures):针对每个故障模式,列出相应的控制措施,以降低或消除风险。
- 负责人(Responsible):指定负责实施和监督控制措施的人员。
- 实施期限(Implementation Deadline):规定控制措施的实施期限。
- 实施状态(Implementation Status):记录控制措施的实施状态,例如已实施、正在实施或未实施。
- 效果验证(Effectiveness Verification):评估控制措施的有效性,可以记录验证方法和结果。
举例说明:假设我们正在开发一款电子产品,其中一个潜在的故障模式是电池过热。
故障原因可能是电池过充、电路设计问题或温度过高等。
FEMA控制程序文件模板
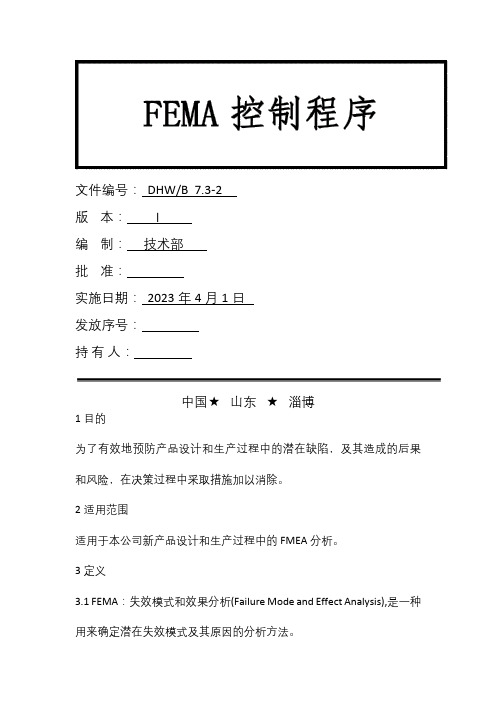
文件编号: DHW/B 7.3-2版本:Ⅰ编制:技术部批准:实施日期: 2023年4月1日发放序号:持有人:中国★山东★淄博1目的为了有效地预防产品设计和生产过程中的潜在缺陷,及其造成的后果和风险,在决策过程中采取措施加以消除。
2适用范围适用于本公司新产品设计和生产过程中的FMEA分析。
3定义3.1 FEMA:失效模式和效果分析(Failure Mode and Effect Analysis),是一种用来确定潜在失效模式及其原因的分析方法。
4职责4.1 技术部4.1.1本文件由技术部制订、修改并组织培训。
4.1.2负责组织项目小组针对产品特性要求开展FMEA分析工作;5程序5.1确定缺陷项目的依据5.1.1在产品设计过程中,根据与过去同类产品的设计和工艺比较而了解到的,什么问题已经发生过,现在不允许再发生等类似经验的反馈。
5.1.2在生产工艺执行过程中,用挑剔的眼光来观测,可能会发生什么问题,虽然这类问题未曾发生过,但经过分析估计可能会发生。
根据本公司的生产特点,对所有的产品都应进行FMEA分析。
5.2 FMEA小组的组成5.2.1 设计FMEA小组由负责设计的主管工程师,联系相关部门的代表,如:技术、制造、品质、购买、销售等组成。
5.2.2 过程FMEA小组由负责过程的主管工程师联系相关部门的代表,如:技术、制造、品质、购买、销售等组成。
5.3 对所确定的缺陷项目,进行缺陷分析,包括:5.3.1 缺陷形式——可能产生的缺陷模式;5.3.2 缺陷原因——可能引起缺陷的原因;5.3.3 缺陷后果——缺陷可能产生的影响和后果。
5.4将所作的缺陷分析,填入FMEA表的相应的栏目内。
5.5结合目前检验措施执行的状况,对当前的状态作缺陷风险率(风险顺序数RPN)的评价。
风险顺序数包含以下因素:5.5.1 严重度数:指潜在的失效模式对顾客造成后果的严重程度;5.5.2 频度数:指具体的失效起因/机理的发生频率;5.5.3不易探测度数:用相应的现行控制方法来探测潜在失效原因/机理能力的评价指标。
FMEA英文模板
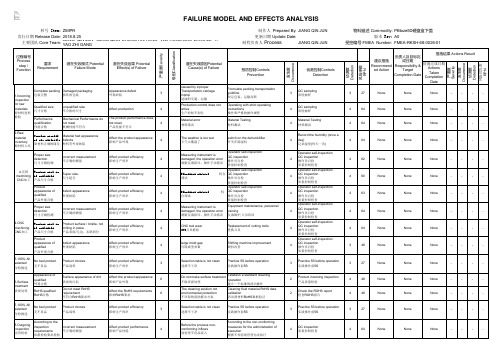
负责人及目标完
措施结果 Actions Result
建议措施 Recommend
ed Action
成日期 Responsibility &
Target Completion Date
措施完成日期 Actions Taken
Completion
Date
3
27
None
None
None
-
-
-
-
4
QC sampling 质检抽样
unqualified size 不合格的尺寸
Affect production
4
检验
Performance
Mechanical Performance do The product performance does
qualification
not meet
not meet
4
性能合格
机械性能不符合
产品性能不符合
According to the
inspection
incorrect measurement
requirements
不正确的测量
依据检验要求检验
Affect product performance 影响产品性能
4
Before the process nonconforming inflows 前处理不良品流入
3
Selection table is not clean 选择不干净
Practice 5S before operation 实践操作前5S
3
Practice 5S before operation 实践操作前5S
3
27
fmea报告模板范例
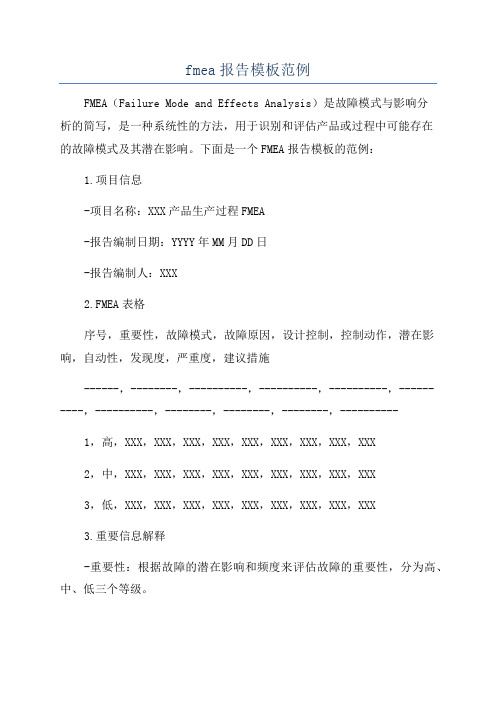
fmea报告模板范例FMEA(Failure Mode and Effects Analysis)是故障模式与影响分析的简写,是一种系统性的方法,用于识别和评估产品或过程中可能存在的故障模式及其潜在影响。
下面是一个FMEA报告模板的范例:1.项目信息-项目名称:XXX产品生产过程FMEA-报告编制日期:YYYY年MM月DD日-报告编制人:XXX2.FMEA表格序号,重要性,故障模式,故障原因,设计控制,控制动作,潜在影响,自动性,发现度,严重度,建议措施------,--------,----------,----------,----------,----------,----------,--------,--------,--------,----------1,高,XXX,XXX,XXX,XXX,XXX,XXX,XXX,XXX,XXX2,中,XXX,XXX,XXX,XXX,XXX,XXX,XXX,XXX,XXX3,低,XXX,XXX,XXX,XXX,XXX,XXX,XXX,XXX,XXX3.重要信息解释-重要性:根据故障的潜在影响和频度来评估故障的重要性,分为高、中、低三个等级。
-故障模式:记录故障出现的模式或类型,例如机器停机、设备损坏等。
-故障原因:识别导致故障的根本原因,例如零部件磨损、操作错误等。
-设计控制:标记故障模式是否由设计决策引起。
-控制动作:记录已经或将要采取的控制措施来减少或消除故障模式。
-潜在影响:分析故障可能带来的影响,如生产延误、产品质量下降等。
-自动性:描述人工检查效果,区分人工检查的故障发现自动性高低。
-发现度:根据控制措施可能发现的故障数量进行评估。
-严重度:根据故障带来的影响评估故障的严重性,分为高、中、低三个等级。
-建议措施:记录针对每个故障模式采取的应对措施和改进建议。
4.分析结果总结-根据FMEA表格中的评估和分析,我们可以得出以下结论:-高重要性的故障模式需要优先处理,并采取相应措施进行风险控制。
- 1、下载文档前请自行甄别文档内容的完整性,平台不提供额外的编辑、内容补充、找答案等附加服务。
- 2、"仅部分预览"的文档,不可在线预览部分如存在完整性等问题,可反馈申请退款(可完整预览的文档不适用该条件!)。
- 3、如文档侵犯您的权益,请联系客服反馈,我们会尽快为您处理(人工客服工作时间:9:00-18:30)。
等
压伤、碰 伤
6
产品报废 或夹具铣 9
坏
产品报废 或刀具损 9
坏
1.作业指导书未制作
2.丢失、未悬挂
1.作业员装夹手法不 到位
2.作业员装夹,夹具 未吹干净
技术员对产品工艺、 刀具清单不熟悉 技术员对产品工艺、 刀具清单不熟悉;技 能不足
加工程式出错
产品报废 、撞机
10
工程师编程式出错
4 及时制作
3 36
探 测 率 D
风 险 系 数 RPN
建议措施
进料
5
送货单物料编 码与实物不符
无法使用
5
1.由于核对送货单时 未核对出
2.由于外箱标识与送 货单一致,但内装实 物与单据不一致
收料员在接收原材料时,
3
核对送货单与外箱标识、 实物的物料编码、及采购
2
30
订单确认一致后方可收货
2
对原包装最小包装5%的比 例进行抽检
确认,监控
5 100 制作NG限度 样品对员工 进行培训,
3 60 定期考核
黄律 2019.3.2
现场培训
5 3 2 30 5 3 2 30
光线暗
漏检、误 判
4
日光灯坏
4 每日点检
4 64
4
检验员技能不 漏检、误
足
判
QA检验
4
1.检查员未经培训上 岗
2.管理员临时调用非 本工序检查员
3
每日点检,禁止无上岗证 的检查员
不能辨别 产品外
观,不良 品流出
严 重分 度类 S
失效的潜在要因
控 制 预 防
频 度 O
现行过程 控制探测
刀具由工程、生产共同验
7
刀具寿命到未及时更 换
证实际寿命,并在程式中 7 设寿命预警;当生产现场
刀具寿命报警后,及时更
换 1.生产技术员应定时检查
刀具磨损情况
8 刀具断刀未及时更换
5 2.作业员每一次加工完
7 3 2 42
张浩中/邓
锦锐
现场培训
2019.3.2
8 3 1 24
5
检验标准不全 不良流出
面或错
或误判
5
标准制作不全 丢失、未悬挂
3
标准制作后,实行两人确 认
3
45
4
每日点检生产线所有作业 指导书进行点检
3
60
检验样板不正 不良流出
确
或误判
5
1.样板制作错误,标 识卡填写不完整
5 1.未作首件检查
格后方可上岗
工程师编程或改程式后, 必须由另一个工程师或工 1 程主管检查后,现场找一 1 10 台机验证程式,验证合格 后方可批量生产
8 3 2 48 6 3 3 54
物料上线
第 2 页,共 5 页
要求
过程 功能
潜在失效模式
失效模式 潜在后果
物料上线
刀具磨损
产品尺寸 不良、漏
铣
检验灯光亮度 不够
4
每日对各工位作业指导书 进行点检
3
36
6
对员工装夹进行培训,考 核合格后方能上岗
7
对员工装夹进行培训,考 核合格后方能上岗
3 3
144 126
制作NG不良 样品对员工 进行培训, 定期考核
张浩中/邓 锦锐
2019.3.2
现场培训
技术工程师及以上人员安 2 排培训并考核,合格后方 2 36
可上岗
技术工程师、主管及以上 2 人员安排培训并考核,合 2 36
首件(检查) 不良流出
出错
或误判
5
2.首检人员未掌握首 检流程/方法
5
制作样板后,实行两人确 认并签名
3
75
按《产品检验控制程序》 4 要求的时机作首件检查并 3 60
记录
3
按照《产品检验控制程序 》作业
3
45
5 首件人员疏忽
3 首件后,实行两人确认 3 45
研磨/溜毛 产品毛刺未溜 未达到溜 刺 掉、碰伤 光效果
后,目视刀具是否还在刀
盘上
3 灯管不能正常发光
5 每日对照明系统进行点检
探 测 率 D
风 险 系 数 RPN
建议措施
3
147
在程式中设 刀具寿命
3
120
班组长加强 培训并监督
2 30
措施结果
责任&目标 完成日期
采取的措施 和生效日期
严 重 度 S
频 度 O
探 测 度 D
R P N
颜国营 程式中设寿 2019.3.2 命管控
深圳市xxxxxxxx有限公司
潜在失效模式及后果分析(过程FMEA)
项 目型:号 年核/心 小
过程 功能
综合运营、生产、质量、工艺技术、设备
要求
潜在失效模式
失效模式 潜在后果
严 重分 度类 S
失效的潜在要因
过程职责:设备、生产、工艺技术、质量提供
关
键 FM
EA
控 制 预 防
频 度 O
现行过程 控制探测
后方能上岗
建议措施
措施结果
责任&目标 完成日期
采取的措施 和生效日期
严 重 度 S
频 度 O
探 测 度 D
R P N
检验仪器用校验合格的仪器设备 3 45
不按标准 3
作业指导书不 、流程作
全
业,流出
不良 3
装夹不良
用错刀具 调机出错
产品尺寸
不良、过 铣、打飞
8
4
48
3 管理员合理安排
4 48
5
检验标准不全 面或错
客户投诉
5
客户提供标准不全或 标准描述不清楚
标准制作人疏忽
3
检验标准发行前与客户确 认
2
30
3
标准制作人完成检验标准 后自检
3
45
包装入库
产品少数
客户投诉 4 影响出货 4
1.员包装少数 2.仓库员疏忽
3 产线员工包装时仔细检查 3 36
3 实行复查制度
严 重 度 S
频 度 O
探 测 度 D
R P N
出货
送货单错
客户投诉 6
外箱和产
外箱包装破损
品在搬运 过程中撞
5
坏
仓库员疏忽
包装箱设计不合理, 搬运过程撞坏
3 核对送货单与实物
2 36
包装箱设计时应考虑产品 3 在箱内晃动,并打样确 3 45
认;搬运过程,轻拿轻放
第 5 页,共 5 页
5
未按作业指导书作业
3
加强培训,并定期考核及 监督操作流程
4
60
第 3 页,共 5 页
过程 功能
要求
潜在失效模式
失效模式 潜在后果
严 重分 度类 S
失效的潜在要因
控 制 预 防
频 度 O
现行过程 控制探测
探 测 率 D
风 险 系 数 RPN
建议措施
超声波清 产品表面油污 未达到清 洗 未清洗干净 洗效果
影响生产 进度
3
来料检验安排不合理
漏检 5 1.标准制作不完善
标准不完善
进料检验 /IQC
误判 5 2.标准制订不合理
4
IQC合理安排工作,急料 先检
4 48
及时制作并不断完善检验 3 标准,按检验标准或参考 3 45
实物规格书实施减
由IQC工程师及以上人员 3 制订标准,并根据实际情 3 45
况修订标准
5
未按作业指导书作业
3
加强培训,并定期考核及 监督操作流程
4
60
措施结果
责任&目标 完成日期
采取的措施 和生效日期
严 重 度 S
频 度 O
探 测 度 D
R P N
全捡
5
全捡员检验技 不良流出
能不足
或误判
5
1.全捡员对标准不熟 悉
2.全捡员未按标准检 验
4 培训全捡员掌握检验标准
线长每2小时对外观全捡 4 工位的检验报告进行签名
5
50
FMEA编号:
编制: 措施结果
责任&目标 完成日期
采取的措施 和生效日期
严 重 度 S
频 度 O
探 测 度 D
R P N
3
送货单数量与 实物不符
影响生产
3
1.原包装本身就少料 2.收料时点数大意
4
对原包装最小包装6%的比 例进行抽检
5
60
2
收料时认真点数,贵重的 、散包装的必须全数清点
5
30
IQC检验不及 时
3 36
入库单错
影响出货 4 作业员疏忽
3
作业员核对实物及单据时 粗心
2
24
第 4 页,共 5 页
过程 功能
要求
潜在失效模式
失效模式 潜在后果
严 重分 度类 S
失效的潜在要因
控 制 预 防
频 度 O
现行过程 控制探测
探 测 率 D
风 险 系 数 RPN
建议措施
措施结果
责任&目标 完成日期
采取的措施 和生效日期
第 1 页,共 5 页
要求
进料检验 过程/IQC 功能
潜在失效模式
失效模式 潜在后果
严 重分 度类 S
失效的潜在要因
控 制 预 防
频 度 O
现行过程 控制探测
探 测 率 D
风 险 系 数 RPN
作业员技能不 漏判、误