液压课程设计卧式钻镗组合机床液压系统
液压课程设计-卧式单面钻、镗专用机床液压系统的设计
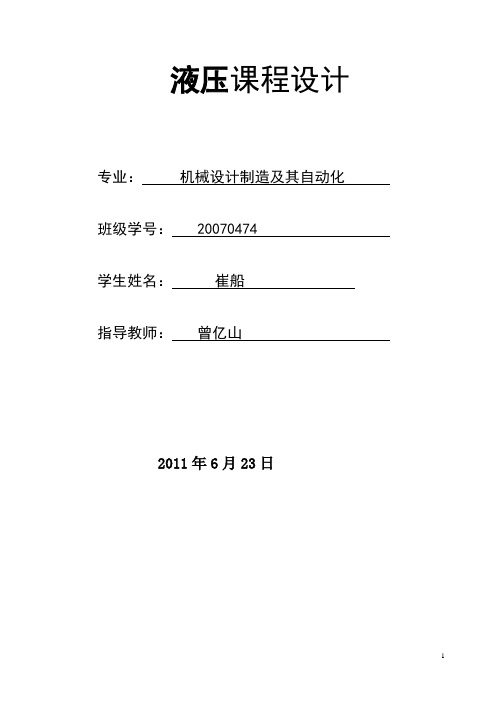
液压课程设计专业:机械设计制造及其自动化班级学号:20070474学生姓名:崔船指导教师:曾亿山2011年6月23日合肥工业大学课程设计任务书设计题目卧式单面钻、镗专用机床液压系统的设计成绩主要内容设计一台卧式单面钻、镗专用机床液压系统。
按加工需要,该系统的工作循环是:快速前进I 工作进给快速退回原位停止。
工作部件自重(含工件)G=25kN,最大切削力F e=18kN。
快进、快退速度v1=0.075m/s,工进速度v2=(0.0003~0.002)m/s范围内无级调速。
最大行程为400mm,其中工进行程为200mm。
采用水平放置的平导轨,静摩擦系数f j=0.2;动摩擦系数f d=0.1。
启动、制动时间Δt=0.1s 。
指导教师意见签名:200 年月日目录1.工况分析 (1)2.拟定液压系统原理图 (2)3.液压系统的计算和选择液压元件 (8)3.1液压缸主要尺寸的确定 (4)3.2确定液压泵的流量、压力和选择泵的规格 (5)3.3液压阀的选择 (5)3.4确定管道尺寸 (6)3.5液压油箱容积的确定 (7)4.液压系统的验算 (6)4.1压力损失的验算 (6)4.2系统温升的验算 (8)设计一卧式单面钻、镗专用机床的液压系统及设计进给液压缸。
按加工需要,该系统的工作循环式:快速前进→工作进给→快速退回→原位停止。
液压系统的主要参数为:切削力 Fg=18000N,工作部件(含工件)总重力G=25000N ;快进行程150mm ;工进行程200mm ;快进快退的速度为0.075m/s ;工进速度为0.0003m/s~0.002m/s 范围内无级调速;加速、减速时间△t=0.1s ;该系统采用水平放置的平导轨,静摩擦系数f s=0.2,动摩擦因数f d=0.1.1.工况分析首先根据已知条件,绘制运动部件的速度循环图,如图1.5所示,然后计算各阶段的外负载并绘制负载图。
液压缸所受外负载F 包括三种类型,即a f w F F F F ++=Fw 为工作负载,对于金属切削机床来说,即为沿活塞运动方向的切削力,在本例中为20500N ;Fa —运动部件速度变化时的惯性负载;Ff —导轨摩擦阻力负载,启动时为静摩擦阻力,启动后为动摩擦阻力,对于平导轨可由下式求得()Rn f F G f F +=G —运动部件重力;F Rn —垂直于导轨的工作负载,事例中为零;f —导轨摩擦系数,本例中取静摩擦系数0.2,动摩擦系数为0.1。
液压课程设计 卧式钻镗组合机床液压系统

液压课程设计卧式钻镗组合机床液压系统The following text is amended on 12 November 2020.液压与气压传动课程设计说明书设计题目卧式钻镗组合机床液压系统设计专业班级机制1512姓名桂新睿学号指导老师夏庆国成绩评定等级评阅签字评阅日期湖北文理学院理工学院机械与汽车工程系2017年12月目录4一.设计的技术要求和设计参数 (5)555负载循环图和速度循环图的绘制 (6)8确定液压缸主要尺寸 (8)计算最大流量需求 (9)拟定液压系统原理图 (10)速度控制回路的选择 (10)换向和速度换接回路的选择 (11)23568油箱的设计 (19)液压系统性能的验算 (20)回路压力损失验算 (20)1附:手绘液压系统图序言作为一种高效率的专用机床,组合机床在大批、大量机械加工生产中应用广泛。
本次课程设计将以组合机床动力滑台液压系统设计为例,介绍该组合机床液压系统的设计方法和设计步骤,其中包括组合机床动力滑台液压系统的工况分析、主要参数确定、液压系统原理图的拟定、液压元件的选择以及系统性能验算等。
组合机床是以通用部件为基础,配以按工件特定外形和加工工艺设计的专用部件和夹具而组成的半自动或自动专用机床。
组合机床一般采用多轴、多刀、多工序、多面或多工位同时加工的方式,生产效率比通用机床高几倍至几十倍。
组合机床兼有低成本和高效率的优点,在大批、大量生产中得到广泛应用,并可用以组成自动生产线。
组合机床通常采用多轴、多刀、多面、多工位同时加工的方式,能完成钻、扩、铰、镗孔、攻丝、车、铣、磨削及其他精加工工序,生产效率比通用机床高几倍至几十倍。
液压系统由于具有结构简单、动作灵活、操作方便、调速范围大、可无级连读调节等优点,在组合机床中得到了广泛应用。
液压系统在组合机床上主要是用于实现工作台的直线运动和回转运动,如果动力滑台要实现二次进给,则动力滑台要完成的动作循环通常包括:原位停止快进I 工进II 工进死挡铁停留快退原位停止。
卧式钻镗组合机床的液压系统设计

卧式钻镗组合机床的液压系统设计
首先,需要确定机床所需的液压系统工作压力。
卧式钻、镗组合机床的工作压力通常为10-25MPa。
根据工作压力确定油泵的流量和型号,流量需满足机床加工的需要。
其次,需选择合适的液压元件。
根据机床的加工需求,选择相应的液压元件。
液压缸用于实现主轴、工作台、主轴箱等运动部件的运动,而液压马达则用于切削液的输送。
接下来,需考虑液压系统的控制方式。
对于卧式钻、镗组合机床,可使用手动控制、脚踏开关控制或电脑数控控制。
手动控制简单可靠,适用于简单的加工任务;脚踏开关控制可以实现机床的步进、停止和反转等功能;而电脑数控控制则提供了更高的自动化水平和加工精度。
最后,需考虑液压系统的安全性和可靠性。
在液压系统设计时,需要考虑系统的安全保护装置,如过载保护、泄漏检测、温度保护等,以及系统的故障诊断和报警功能。
在设计完液压系统后,还需进行系统的试运行和调试。
首先,检查液压油的质量和流量是否正常;其次,逐一检查液压元件的工作情况,确保系统各部件正常运行;最后,进行系统的负载试运行和调试,确保系统能够满足加工需求。
总之,卧式钻、镗组合机床的液压系统设计需要考虑工作压力、液压元件的选择、控制方式、系统的安全性和可靠性等因素。
通过合理的设计和调试,能够提高机床的加工效率和精度,提高机床的使用寿命。
液压课程设计卧式钻镗组合机床液压系统

设计一台卧式钻、镗组合机床液压系统1、液压系统用途(包括工作环境与工作条件)及主要参数:1)工作循环:“快进—工进—死挡铁停留—快退—原位停止”。
组合机床动力滑台工作循环2)工作参数轴向切削力12000N,移动部件总重10000N,工作循环为:“快进——工进——死挡铁停留——决退——原位停止”。
行程长度为0、4m,工进行程为0、1,快进与快退速度为0、1m/s,工过速度范围为0、0003~0、005,采用平导轨,启动时间为0、2s。
要求动力部件可以手动调整,快进转工进平稳、可靠。
2、执行元件类型:液压油缸设计内容1、拟订液压系统原理图;2、选择系统所选用的液压元件及辅件;3、验算液压系统性能;4、编写计算说明书。
目录序言: (5)1 设计的技术要求与设计参数 (6)2 工况分析 (6)2、1确定执行元件 (6)2、2分析系统工况 (6)2、3负载循环图与速度循环图的绘制 (8)2、4确定系统主要参数2、4、1初选液压缸工作压力 (9)2、4、2确定液压缸主要尺寸 (9)2、4、3计算最大流量需求 (11)2、5拟定液压系统原理图2、5、1速度控制回路的选择 (12)2、5、2换向与速度换接回路的选择 (12)2、5、3油源的选择与能耗控制 (13)2、5、4压力控制回路的选择 (14)2、6液压元件的选择2、6、1确定液压泵与电机规格 (16)2、6、2阀类元件与辅助元件的选择 (17)2、6、3油管的选择 (19)2、6、4油箱的设计 (20)2、7液压系统性能的验算2、7、1回路压力损失验算 (22)2、7、2油液温升验算 (22)序言作为一种高效率的专用机床,组合机床在大批、大量机械加工生产中应用广泛。
本次课程设计将以组合机床动力滑台液压系统设计为例,介绍该组合机床液压系统的设计方法与设计步骤,其中包括组合机床动力滑台液压系统的工况分析、主要参数确定、液压系统原理图的拟定、液压元件的选择以及系统性能验算等。
卧式钻孔组合机床的液压系统课程设计
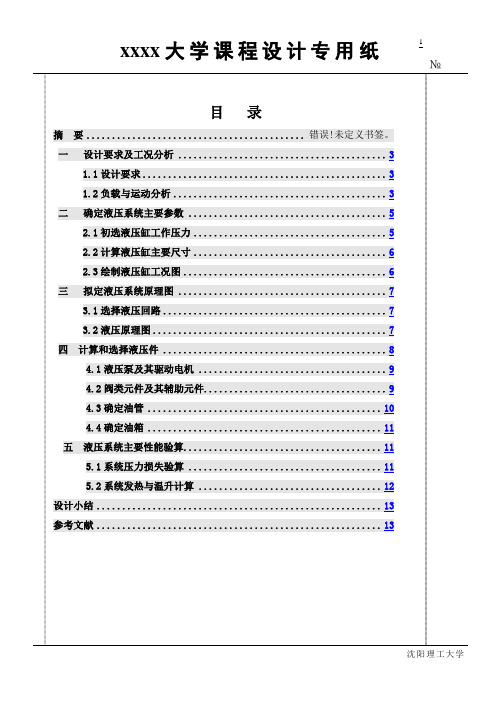
摘要关键词:液压液压系统组合机床液压系统已经在各个部门得到越来越广泛的应用,而且越先进的设备,其应用液压系统的部门就越多。
液压传动是用液体作为来传递能量的,液压传动有以下优点:易于获得较大的力或力矩,功率重量比大,易于实现往复运动,易于实现较大范围的无级变速,传递运动平稳,可实现快速而且无冲击,与机械传动相比易于布局和操纵,易于防止过载事故,自动润滑、元件寿命较长,易于实现标准化、系列化。
液压传动的基本目的就是用液压介质来传递能量,而液压介质的能量是由其所具有的压力及力流量来表现的。
而所有的基本回路的作用就是控制液压介质的压力和流量,因此液压基本回路的作用就是三个方面:控制压力、控制流量的大小、控制流动的方向。
所以基本回路可以按照这三方面的作用而分成三大类:压力控制回路、流量控制回路、方向控制回路。
一.设计要求及工况分析1.1设计要求要求设计一台卧式钻孔组合机床的液压系统。
要求完成如下工作循环:快进→工进→快退→停止。
机床的切削力为F e =25000N ,工作部件的重量为9800N ,快进与快退的速度均为7m/min ,工进速度为0.05m/min ,快进行程为150mm ,工进行程为40mm ,加速、减速时间要求不大于0.2s ,动力平台采用平导轨,静摩擦系数0.2;动摩擦系数为0.1。
要求活塞杆固定,油缸与工作台连接。
设计该组合机床的液压传动系统。
设计参数如下:切削力F e =25000N 工作部件质量G=9.8KN 快进速度1V =7m/min=0.12m/s 工进速度2V =0.05m/s=8.3×410-m/s 快退速度3V =7m/min=0.12m/s快进行程1S =150mm ,工进行程2S =40mm,则快退行程3S =150+40=190mm 1.2负载与运动分析(1)工作负载。
工作负载即轴向切削力,F e =25000N 。
(2)摩擦负载工作部件重量为G=9.8KN ,则摩擦负载为f F =µG静摩擦负载 0.298001960fs F N =⨯= 动摩擦负载 0.19800980fd F N =⨯=(3)惯性负载 取加速、减速时间均为0.2s ,则惯性负载为 a 98000.126009.80.2G v F N N g t ∆=⨯=⨯=∆ (4) 液压缸在各工作阶段的负载值设液压缸的机械效率 w η=0.9,根据公式计算得出液压缸在各阶段的负载和推力。
液压课程设计--设计一台卧式钻孔组合机床的液压系统

目录0.摘要 (1)1.设计要求 (2)2.负载与运动分析 (2)2.1负载分析 (2)2.2快进、工进和快退时间 (3)2.3液压缸F-t图与v-t图 (3)3.确定液压系统主要参数 (4)3.1初选液压缸工作压力 (4)3.2计算液压缸主要尺寸 (4)3.3绘制液压缸工况图 (5)4.拟定液压系统的工作原理图 (7)4.1拟定液压系统原理图 (7)4.2原理图分析 (8)5.计算和选择液压件 (8)5.1液压泵及其驱动电动机 (8)5.2阀类元件及辅助元件的选 (10)6.液压系统的性能验算 (10)6.1系统压力损失验算 (10)6.2系统发热与温升验算 (11)7.课设总结 (12)0.摘要液压传动技术是机械设备中发展最快的技术之一,特别是近年来与微电子、计算技术结合,使液压技术进入了一个新的发展阶段,机、电、液、气一体是当今机械设备的发展方向。
在数控加工的机械设备中已经广泛引用液压技术。
作为机械制造专业的学生初步学会液压系统的设计,熟悉分析液压系统的工作原理的方法,掌握液压元件的作用与选型是十分必要的。
液压传动在国民经济的各个部门都得到了广泛的应用,但是各部门采用液压传动的出发点不尽相同:例如,工程机械、压力机械采用液压传动的主要原因是取其结构简单、输出力大;航空工业采用液压传动的主要原因取其重量轻、体积小;机床上采用液压传动的主要原因则是取其在工作过程中能无级变速,易于实现自动化,能实现换向频繁的往复运动等优点。
关键词:钻孔组合机床卧式动力滑台液压系统1.设计要求设计一台卧式钻孔组合机床的液压系统,要求完成如下工作循环式:快进→工进→快退→停止。
机床的切削力为25000N ,工作部件的重量为9800N ,快进与快退速度均为7m/min ,工进速度为0.05m/min ,快进行程为150mm ,工进行程40mm ,加速、减速时间要求不大于0.2s ,动力平台采用平导轨,静摩擦系数为0.2,动摩擦系数为0.1 。
卧式钻镗两用组合机床的液压系统设计文档
卧式钻镗两用组合机床的液压系统设计文档一、引言液压系统是卧式钻镗两用组合机床中的重要部分,主要用于实现机床在加工过程中的各种动作控制。
本文档旨在设计一套稳定可靠的液压系统,以满足卧式钻镗两用组合机床的加工需求。
二、系统结构1.液压泵站:液压泵站是液压系统的动力源,主要由液压泵、电机和控制阀组成。
液压泵负责将液压油从油箱中抽取并压力传输至液压马达或液压缸,电机用于驱动液压泵的运转,控制阀用于调节油压和流量。
2.液压油箱:液压油箱用于存放液压油,并通过滤油器来保证油液的清洁。
油箱内还设置有油位显示器、温度传感器等装置,以便监测液压系统的工作状态。
3.液压马达:液压马达是卧式钻镗两用组合机床中驱动主轴转动的关键元件。
液压马达的转速和扭矩可以通过调节液压系统中的油压和流量来实现。
4.液压缸:液压缸主要用于实现机床在加工过程中的直线运动,例如镗削过程中的进给和退刀等操作。
液压缸的活塞直径和行程应根据机床的加工需求来确定,同时需要有充足的力量来保证加工负载。
5.控制阀组:控制阀组由数个液控阀组成,用于控制液压系统中油液的流向和压力。
应根据机床的运动要求来选择合适的控制阀,以满足机床的工作需求。
三、设计要点1.液压系统的压力和流量应根据机床的加工要求来确定,以保证机床能够稳定运行并满足加工负载。
2.液压系统应具备过热保护功能,通过设置合适的油温传感器和过热报警装置,可以在油温过高时及时发出警报并停止液压泵的工作,以防止系统损坏。
3.液压系统中应安装滤油器,以保证油液的清洁,避免杂质进入液压元件造成损坏。
4.液压系统中的液压油应定期更换,并注意油液的粘度和温度,在不同的季节和环境条件下进行调整,以保证系统的良好工作。
5.液压系统应配备完善的安全保护装置,例如安全阀、溢流阀和接触器等,以确保系统在异常情况下能够及时切断液压油的供给,并保护机床和操作人员的安全。
四、总结本文档对卧式钻镗两用组合机床的液压系统进行了设计,并提出了相关要点。
液压课程设计卧式钻镗组合机床液压系统
液压课程设计卧式钻镗组合机床液压系统集团标准化工作小组 #Q8QGGQT-GX8G08Q8-GNQGJ8-MHHGN#液压与气压传动课程设计说明书设计题目卧式钻镗组合机床液压系统设计专业班级机制1512姓名桂新睿学号指导老师夏庆国成绩评定等级评阅签字评阅日期湖北文理学院理工学院机械与汽车工程系2017年12月目录4一.设计的技术要求和设计参数 (5)555负载循环图和速度循环图的绘制 (6)8确定液压缸主要尺寸 (8)计算最大流量需求 (9)拟定液压系统原理图 (10)速度控制回路的选择 (10)换向和速度换接回路的选择 (11)23568油箱的设计 (19)液压系统性能的验算 (20)回路压力损失验算 (20)1附:手绘液压系统图序言作为一种高效率的专用机床,组合机床在大批、大量机械加工生产中应用广泛。
本次课程设计将以组合机床动力滑台液压系统设计为例,介绍该组合机床液压系统的设计方法和设计步骤,其中包括组合机床动力滑台液压系统的工况分析、主要参数确定、液压系统原理图的拟定、液压元件的选择以及系统性能验算等。
组合机床是以通用部件为基础,配以按工件特定外形和加工工艺设计的专用部件和夹具而组成的半自动或自动专用机床。
组合机床一般采用多轴、多刀、多工序、多面或多工位同时加工的方式,生产效率比通用机床高几倍至几十倍。
组合机床兼有低成本和高效率的优点,在大批、大量生产中得到广泛应用,并可用以组成自动生产线。
组合机床通常采用多轴、多刀、多面、多工位同时加工的方式,能完成钻、扩、铰、镗孔、攻丝、车、铣、磨削及其他精加工工序,生产效率比通用机床高几倍至几十倍。
液压系统由于具有结构简单、动作灵活、操作方便、调速范围大、可无级连读调节等优点,在组合机床中得到了广泛应用。
液压系统在组合机床上主要是用于实现工作台的直线运动和回转运动,如果动力滑台要实现二次进给,则动力滑台要完成的动作循环通常包括:原位停止快进I工进II 工进死挡铁停留快退原位停止。
液压课程设计:卧式钻镗组合机床的液压动力滑台液压系统(DOC)
液压课程设计说明书题目:卧式钻镗组合机床的液压动力滑台液压系统学院:机电工程学院班级:学号:设计者:指导老师:目录一、课程设计技术要 (2)二、工况分析 (3)1、工况分析及液压缸的推力: (3)2、确定液压缸工作压力、结构尺寸、初定液压缸流量 (4)3、确定液压缸结构尺寸 (4)4、认证液压缸筒壁厚 (5)5、定液压缸筒的长度 (5)6、求最少活塞杆直径 (5)7、校核活塞杆的稳定性 (5)8、液压缸各截面积3 (6)9、初定液压缸流量 (6)10、液压缸的负载、压力、流量、功率的工况表 (6)11、确定定位夹紧液压缸结构尺寸及流量 (7)三、设计卧式钻镗组合机床的液压动力滑台的液压系统图 (8)四、液压元件设计计算与选择 (9)1、液压泵工作压力、流量、驱动功率计算 (9)2、确定液压缸的输入输出流量和移动速度 (10)3、根据工作压力和通流量选取液压元件 (10)4、油管尺寸 (11)5、油箱容积 (11)五、液压系统稳定性论证 (11)1、液压泵工作压力稳定性校核 (11)2、校核系统驱动电机功率 (12)3、系统热能工况的稳定性校核 (12)六、利用FluidSIM进行液压仿真 (14)七、液压系统的PLC控制程序与接线图 (15)1、PLC接线图 (15)八、课程设计简单小结 (15)九、参考文献 (15)一、课程设计技术要快进→工进→快退→停止;切削推力30000N,快进行程400mm,工进行程50mm,V快=5m/min、V工进=0.04-0.10m/min,运动部件重G=9800N,试确定液压缸结构尺寸。
静摩擦系数:fj =0.2,动摩擦系数:fd=0.1,液压缸机械效率:9.0=η,快速起动时间不大于0.2s.原理图1、大泵,2、小泵,3、滤油器,4、外控顺序阀,5、15、单向阀,6、溢流阀,,7、电液换向阀,8、单向行程调速阀,,9、压力继电器,10、主液压缸,11、二位三通电磁换向阀,12、背压阀,13、二位二通换向阀,14、减压阀,16、带定位装置的二位四通电磁换向阀,17、单向顺序阀,18、定位液压缸,19、夹紧液压缸二、工况分析1、工况分析及液压缸的推力:(1)、工况分析切削推力:F切=30000N静摩擦力: Fj = fjG=1960N动摩擦力: Fd = fdG=980N启动惯性力: Fg=ma=(9800/9.8)*[5/(0.2*60)]=417N (2)、液压缸的推力(液压缸效率9.0=η)启动推力: F启= Fj/η= 2178N加速推力: F加=(Fd+Fg)/η=1552N快进推力: F快= Fd/η=1089N工进推力: F工=(F切+ Fd)/η=(30000+980)/0.9=34422N反向启动过程作用力与F启、F加、F快大小相同,方向相反。
卧式钻镗组合机床的液压系统设计
卧式钻镗组合机床的液压系统设计卧式钻、镗组合机床是一种多功能的机床,广泛应用于金属加工行业。
其液压系统是该机床能正常运行的关键部分。
液压系统主要包括供油系统、动力系统、控制系统和液压元件等。
下面将详细介绍卧式钻、镗组合机床液压系统的设计。
首先是供油系统的设计。
供油系统主要包括供油泵、滤油器、储油箱等。
供油泵负责向液压元件提供工作液压油,因此需要选择合适的供油泵,确保其输出流量和压力能够满足机床的工作要求。
同时,滤油器的作用是过滤油液中的杂质,保护液压元件的正常工作,因此需要选择滤油器的类型和等级。
储油箱用于储存液压油,并起到平稳油液压力的作用,因此需要选择合适的储油箱容量。
其次是动力系统的设计。
动力系统主要包括电动机、液压缸、执行器等。
电动机主要负责提供动力,需要选择合适的电动机功率和转速,以满足机床的工作要求。
液压缸主要负责转换液压能为机械能,需要选择合适的液压缸类型和规格,以满足机床的工作要求。
执行器是液压系统中的关键元件,负责实现各种动作和运动,因此需要选择合适的执行器类型和规格,以满足机床的工作要求。
再次是控制系统的设计。
控制系统主要包括控制阀、油泵控制系统、安全保护装置等。
控制阀的作用是控制液压流量和压力,需要根据机床的工作要求选择合适的控制阀类型和规格。
油泵控制系统主要负责控制油泵的运行状态,需要选择合适的控制方式和系统结构。
安全保护装置是为了保障机床的安全运行,需要选择合适的安全保护装置类型和规格。
最后是液压元件的设计。
液压元件主要包括液压缸、控制阀、油泵等。
液压缸的设计需要根据机床的工作需求选择合适的液压缸类型和规格。
控制阀的设计需要根据机床的工作要求选择合适的控制阀类型和规格。
油泵的设计需要根据机床的工作要求选择合适的油泵类型和规格。
总之,卧式钻、镗组合机床的液压系统设计需要考虑供油系统、动力系统、控制系统和液压元件等多个方面的因素。
只有通过合理的设计,才能确保机床的正常运行和高效工作。
- 1、下载文档前请自行甄别文档内容的完整性,平台不提供额外的编辑、内容补充、找答案等附加服务。
- 2、"仅部分预览"的文档,不可在线预览部分如存在完整性等问题,可反馈申请退款(可完整预览的文档不适用该条件!)。
- 3、如文档侵犯您的权益,请联系客服反馈,我们会尽快为您处理(人工客服工作时间:9:00-18:30)。
设计一台卧式钻、镗组合机床液压系统1、液压系统用途(包括工作环境与工作条件)及主要参数:1)工作循环:“快进—工进—死挡铁停留—快退—原位停止”、组合机床动力滑台工作循环2)工作参数轴向切削力12000N,移动部件总重10000N,工作循环为:“快进——工进-—死挡铁停留-—决退——原位停止”、行程长度为0.4m,工进行程为0.1,快进与快退速度为0。
1m/s,工过速度范围为0。
0003~0.005,采用平导轨,启动时间为0、2s。
要求动力部件可以手动调整,快进转工进平稳、可靠。
2.执行元件类型:液压油缸设计内容1。
拟订液压系统原理图;2.选择系统所选用得液压元件及辅件;3。
验算液压系统性能;4。
编写计算说明书。
目录序言: (5)1 设计得技术要求与设计参数ﻩ 62 工况分析 (6)2、1确定执行元件ﻩ 62.2分析系统工况 (6)2。
3负载循环图与速度循环图得绘制ﻩ82、4确定系统主要参数2。
4、1初选液压缸工作压力ﻩ92、4。
2确定液压缸主要尺寸ﻩ92。
4.3计算最大流量需求 (11)2、5拟定液压系统原理图2.5。
1速度控制回路得选择 (12)2.5。
2换向与速度换接回路得选择 (12)2.5.3油源得选择与能耗控制ﻩ132.5、4压力控制回路得选择................................... 142。
6液压元件得选择2。
6。
1确定液压泵与电机规格................................. 162.6、2阀类元件与辅助元件得选择 (17)2、6。
3油管得选择ﻩ192。
6。
4油箱得设计ﻩ202。
7液压系统性能得验算2.7。
1回路压力损失验算 (22)2.7。
2油液温升验算ﻩ2 2序言ﻩ作为一种高效率得专用机床,组合机床在大批、大量机械加工生产中应用广泛、本次课程设计将以组合机床动力滑台液压系统设计为例,介绍该组合机床液压系统得设计方法与设计步骤,其中包括组合机床动力滑台液压系统得工况分析、主要参数确定、液压系统原理图得拟定、液压元件得选择以及系统性能验算等。
组合机床就是以通用部件为基础,配以按工件特定外形与加工工艺设计得专用部件与夹具而组成得半自动或自动专用机床。
组合机床一般采用多轴、多刀、多工序、多面或多工位同时加工得方式,生产效率比通用机床高几倍至几十倍、组合机床兼有低成本与高效率得优点,在大批、大量生产中得到广泛应用,并可用以组成自动生产线。
组合机床通常采用多轴、多刀、多面、多工位同时加工得方式,能完成钻、扩、铰、镗孔、攻丝、车、铣、磨削及其她精加工工序,生产效率比通用机床高几倍至几十倍。
液压系统由于具有结构简单、动作灵活、操作方便、调速范围大、可无级连读调节等优点,在组合机床中得到了广泛应用。
液压系统在组合机床上主要就是用于实现工作台得直线运动与回转运动,如图1所示,如果动力滑台要实现二次进给,则动力滑台要完成得动作循环通常包括:原位停止快进I工进II工进死挡铁停留快退原位停止。
1.设计得技术要求与设计参数工作循环:快进→工进→快退→停止;系统设计参数如表1、1所示,动力滑台采用平面导轨,其静、动摩擦系数分别为fs = 0。
2、f d = 0、1。
2.工况分析2.1. 确定执行元件金属切削机床得工作特点要求液压系统完成得主要就是直线运动,因此液压系统得执行元件确定为液压缸。
2.2. 分析系统工况在对液压系统进行工况分析时,本设计实例只考虑组合机床动力滑台所受到得工作负载、惯性负载与机械摩擦阻力负载,其她负载可忽略。
(1)工作负载FW工作负载就是在工作过程中由于机器特定得工作情况而产生得负载,对于金属切削机床液压系统来说,沿液压缸轴线方向得切削力即为工作负载,即=12000N(2)惯性负载最大惯性负载取决于移动部件得质量与最大加速度,其中最大加速度可通过工作台最大移动速度与加速时间进行计算、已知加、减速时间为0、2s,工作台最大移动速度,即快进、快退速度为5m/min,因此惯性负载可表示为(2-1)(3)阻力负载阻力负载主要就是工作台得机械摩擦阻力,分为静摩擦阻力与动摩擦阻力两部分。
静摩擦阻力(2-2)动摩擦阻力(2-3)根据上述负载力计算结果,可得出液压缸在各个工况下所受到得负载力与液压缸所需推力情况,如表2。
1所示、加速=+ 1357、14N1507.9N快进=1000N1111。
1 N工进=+ 13000 N 14444、4N 反向起动= 2000N 2222、2N加速=+ 1357。
14N 1507、9N快退=1000 N 1111。
1N注:此处未考虑滑台上得颠覆力矩得影响。
2.3. 负载循环图与速度循环图得绘制根据表2。
1中计算结果,绘制组合机床动力滑台液压系统得负载循环图如图2-1所示。
图2-1 组合机床动力滑台液压系统负载循环图图2—1表明,当组合机床动力滑台处于工作进给状态时,负载力最大为14444、4N,其她工况下负载力相对较小。
所设计组合机床动力滑台液压系统得速度循环图可根据已知得设计参数进行绘制,已知快进与快退速度、快进行程,工进行程、快退行程,工进速度=50mm/min。
根据上述已知数据绘制组合机床动力滑台液压系统得速度循环图如图2—2所示。
图2-2 组合机床液压系统速度循环图2.4. 确定系统主要参数2.4.1.初选液压缸工作压力所设计得动力滑台在工进时负载最大,其值为14444、4N,其它工况时得负载都相对较低,按照负载大小或按照液压系统应用场合来选择工作压力得方法,初选液压缸得工作压力=4MPa、2.4.2.确定液压缸主要尺寸由于工作进给速度与快速运动速度差别较大,且快进、快退速度要求相等,从降低总流量需求考虑,应确定采用单杆双作用液压缸得差动连接方式。
通常利用差动液压缸活塞杆较粗、可以在活塞杆中设置通油孔得有利条件,最好采用活塞杆固定,而液压缸缸体随滑台运动得常用典型安装形式。
这种情况下,应把液压缸设计成无杆腔工作面积就是有杆腔工作面积两倍得形式,即活塞杆直径d与缸筒直径D呈d= 0。
707D得关系。
工进过程中,当孔被钻通时,由于负载突然消失,液压缸有可能会发生前冲得现象,因此液压缸得回油腔应设置一定得背压(通过设置背压阀得方式),选取此背压值为=0.8MPa。
快进时液压缸虽然作差动连接(即有杆腔与无杆腔均与液压泵得来油连接),但连接管路中不可避免地存在着压降,且有杆腔得压力必须大于无杆腔,估算时取0。
5MPa、快退时回油腔中也就是有背压得,这时选取背压值=0.6MPa、工进时液压缸得推力计算公式为(2-4)式中:F ——负载力m—-液压缸机械效率A1—-液压缸无杆腔得有效作用面积A2—-液压缸有杆腔得有效作用面积p1-—液压缸无杆腔压力p2—-液压有无杆腔压力因此,根据已知参数,液压缸无杆腔得有效作用面积可计算为(2—5)液压缸缸筒直径为(2—6)由于有前述差动液压缸缸筒与活塞杆直径之间得关系,d =0、707D,因此活塞杆直径为d=0。
707×71.36=50、45mm,根据GB/T2348—1993对液压缸缸筒内径尺寸与液压缸活塞杆外径尺寸得规定,圆整后取液压缸缸筒直径为D=80mm,活塞杆直径为d=50mm。
此时液压缸两腔得实际有效面积分别为:(2—7)(2—8)2.4.3.计算最大流量需求工作台在快进过程中,液压缸采用差动连接,此时系统所需要得流量为=(A1—A2)×v1=8、27 L/minq快进(2-9)工作台在快退过程中所需要得流量为q快退=A2×v2=12、85L/min(2-10)工作台在工进过程中所需要得流量为q工进=A1×v1’=0。
25 L/min(2-11)其中最大流量为快退流量为12.85L/min。
根据上述液压缸直径及流量计算结果,进一步计算液压缸在各个工作阶段中得压力、流量与功率值,如表2.2所示、表2。
2各工况下得主要参数值注:1。
差动连接时,液压缸得回油口之间得压力损失,而。
2.快退时,液压缸有杆腔进油,压力为,无杆腔回油,压力为。
2.5. 拟定液压系统原理图根据组合机床液压系统得设计任务与工况分析,所设计机床对调速范围、低速稳定性有一定要求,因此速度控制就是该机床要解决得主要问题、速度得换接、稳定性与调节就是该机床液压系统设计得核心、此外,与所有液压系统得设计要求一样,该组合机床液压系统应尽可能结构简单,成本低,节约能源,工作可靠、2.5.1.速度控制回路得选择工况表3表明,所设计组合机床液压系统在整个工作循环过程中所需要得功率较小,系统得效率与发热问题并不突出,因此考虑采用节流调速回路即可。
虽然节流调速回路效率低,但适合于小功率场合,而且结构简单、成本低。
该机床得进给运动要求有较好得低速稳定性与速度-负载特性,因此有三种速度控制方案可以选择,即进口节流调速、出口节流调速、限压式变量泵加调速阀得容积节流调速、钻镗加工属于连续切削加工,加工过程中切削力变化不大,因此钻削过程中负载变化不大,采用节流阀得节流调速回路即可、但由于在钻头钻入铸件表面及孔被钻通时得瞬间,存在负载突变得可能,因此考虑在工作进给过程中采用具有压差补偿得进口调速阀得调速方式,且在回油路上设置背压阀。
由于选定了节流调速方案,所以油路采用开式循环回路,以提高散热效率,防止油液温升过高。
2.5.2.换向与速度换接回路得选择所设计多轴钻床液压系统对换向平稳性得要求不高,流量不大,压力不高,所以选用价格较低得电磁换向阀控制换向回路即可、为便于实现差动连接,选用三位五通电磁换向阀。
由前述计算可知,当工作台从快进转为工进时,进入液压缸得流量由8。
25L/min降为0。
25 L/min,可选二位二通行程换向阀来进行速度换接,以减少速度换接过程中得液压冲击。
由于工作压力较低,控制阀均用普通滑阀式结构即可。
由工进转为快退时,在回路上并联了一个单向阀以实现速度换接。
为了控制轴向加工尺寸,提高换向位置精度,采用死挡块加压力继电器得行程终点转换控制。
a。
换向回路b、速度换接回路图2—3 换向与速度切换回路得选择2.5.3.油源得选择与能耗控制表 2.2表明,本设计多轴钻床液压系统得供油工况主要为快进、快退时得低压大流量供油与工进时得高压小流量供油两种工况,若采用单个定量泵供油,显然系统得功率损失大、效率低、在液压系统得流量、方向与压力等关键参数确定后,还要考虑能耗控制,用尽量少得能量来完成系统得动作要求,以达到节能与降低生产成本得目得。
在图2-2工况图得一个工作循环内,液压缸在快进与快退行程中要求油源以低压大流量供油,工进行程中油源以高压小流量供油。
其中最大流量与最小流量之比,而快进与快退所需得时间与工进所需得时间分别为:(2-12)(2—13) 上述数据表明,在一个工作循环中,液压油源在大部分时间都处于高压小流量供油状态,只有小部分时间工作在低压大流量供油状态。