普通车床的螺纹车削加工
车工第六章3螺纹加工

z1 z3 P工 z2 z4 P丝
3)调整机床间隙 间隙大,车削螺纹时容 易产生“扎刀”现象。所以在车螺纹之前, 应调整中、小滑板的镶条间隙,使之松紧适 当。间隙过小,则操作不灵活,摇动滑板费 力。
4)如果车削的是左旋螺纹,则变换三星轮 的位置
螺纹车削调整项: ①调整主轴转速;
②调整螺距;
③脱开光杠进给机构,改由丝杠进给。
例如:P=2.5mm的米制螺纹,进给手柄如何 交换? 按图(铭牌表)6-30并找到手柄所属的位置 手柄Ⅰ置于B上,将手Ⅱ柄2置于Ⅱ处,将手轮3 拉出转到6与 相对的位置后,便可。 交换齿轮箱的齿轮分别是:A=63,B=100,
弹性刀杆螺纹刀
低速车三角形螺纹进给次数进刀格数表
M24 P=3mm
进刀 次数
中滑板进 刀 格 数
小滑板赶刀格数
左
右
1
30
0
中滑板进 刀 格 数
M20 P=2.5mm 小滑板赶刀格数
左
右
30
0
2
15
6
15
6
3
13
6
13
6
4
10
4
8
4
5
8
4
5
2
6
7
2
3
2
7
5
2
2
0
8
3
1
1
1
M16 P=2mm
中滑板 进 刀 格 数
C=75.
2)调整交换齿轮 某些车床需要调整交换齿 轮,根据要求进行调整,
① 切断机床电源,车头变速手柄放在空挡位 置;
普通车床螺纹车削加工讲义

3 ) 车螺纹大径φ24
0 -0.23
4 ) 切槽
三.典型普通螺纹零件的车削加工
2. 确定加工步骤
5 ) 倒角
6 ) 车螺纹
三、典型普通螺纹零件的车削加工
3.选择刀具及切削用量
序 号
加工内容
刀具 名称
1 端面 端面刀
2
φ 24、φ 30外 圆
外圆刀
3
退刀槽
4×φ21.5
切槽刀
螺纹
4 M24X1.5— 螺纹刀
合理分配螺纹加工余量
(一般粗车ap:0.10~0.50;精车ap:0.01~0.10 。)
进刀次数 第一次进刀 第二次进刀 第三次进刀 第四次进刀 第五次进刀 第六次进刀
背吃刀量 ap=0.50mm ap=0.15mm ap=0.10mm ap=0.03mm ap=0.02mm ap=0.01mm
加工步骤 粗加工
三、典型普通螺纹零件的车削加工
7. 螺纹车削操作方法与步骤
1)正反车车削法
开车,对刀
合闸,车螺纹
横向退刀,停车, 反转,纵向回起点
快速退出
开车切削 开反车返回
多刀循环加工
进刀
三、典型普通螺纹零件的车削加工
7. 螺纹车削操作方法与步骤
2)抬闸法 利用开合螺母的压下和抬起来车削螺纹。
控制手柄
正反车车削法
车端面 车螺纹大径 车退刀槽 倒角 车螺纹
d<公称直径 <螺纹小径
多刀车削
三.典型普通螺纹零件的车削加工
1. 分析零件图
查表或计算 d=φ 24 0 -0.23
d2=d-0.6495P=φ 23.026-00.19
三.典型普通螺纹零件的车削加工
螺纹的铣削加工程序编制
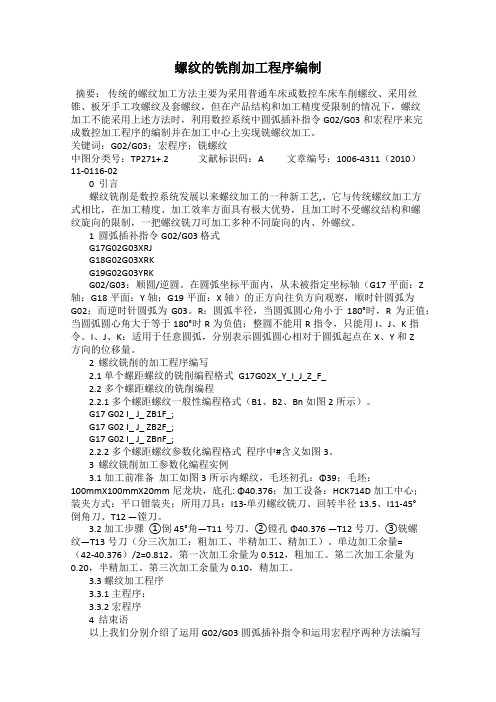
螺纹的铣削加工程序编制摘要:传统的螺纹加工方法主要为采用普通车床或数控车床车削螺纹、采用丝锥、板牙手工攻螺纹及套螺纹,但在产品结构和加工精度受限制的情况下,螺纹加工不能采用上述方法时,利用数控系统中圆弧插补指令G02/G03和宏程序来完成数控加工程序的编制并在加工中心上实现铣螺纹加工。
关键词:G02/G03;宏程序;铣螺纹中图分类号:TP271+.2 文献标识码:A 文章编号:1006-4311(2010)11-0116-020 引言螺纹铣削是数控系统发展以来螺纹加工的一种新工艺,。
它与传统螺纹加工方式相比,在加工精度、加工效率方面具有极大优势,且加工时不受螺纹结构和螺纹旋向的限制,一把螺纹铣刀可加工多种不同旋向的内、外螺纹。
1 圆弧插补指令G02/G03 格式G17G02G03XRJG18G02G03XRKG19G02G03YRKG02/G03:顺圆/逆圆。
在圆弧坐标平面内,从未被指定坐标轴(G17平面:Z 轴;G18平面:Y轴;G19平面:X轴)的正方向往负方向观察,顺时针圆弧为G02;而逆时针圆弧为G03。
R:圆弧半径,当圆弧圆心角小于180°时,R为正值;当圆弧圆心角大于等于180°时R为负值;整圆不能用R指令,只能用I、J、K指令。
I、J、K:适用于任意圆弧,分别表示圆弧圆心相对于圆弧起点在X、Y和Z方向的位移量。
2 螺纹铣削的加工程序编写2.1 单个螺距螺纹的铣削编程格式 G17G02X_Y_I_J_Z_F_2.2多个螺距螺纹的铣削编程2.2.1 多个螺距螺纹一般性编程格式(B1、B2、Bn如图2所示)。
G17 G02 I_ J_ ZB1F_;G17 G02 I_ J_ ZB2F_;G17 G02 I_ J_ ZBnF_;2.2.2 多个螺距螺纹参数化编程格式程序中#含义如图3。
3 螺纹铣削加工参数化编程实例3.1加工前准备加工如图3所示内螺纹,毛坯初孔:Φ39;毛坯:100mmX100mmX20mm尼龙块,底孔: Φ40.376;加工设备:HCK714D加工中心;装夹方式:平口钳装夹;所用刀具:I13-单刃螺纹铣刀、回转半径13.5、I11-45°倒角刀、T12 —镗刀。
螺纹加工方法详细讲解
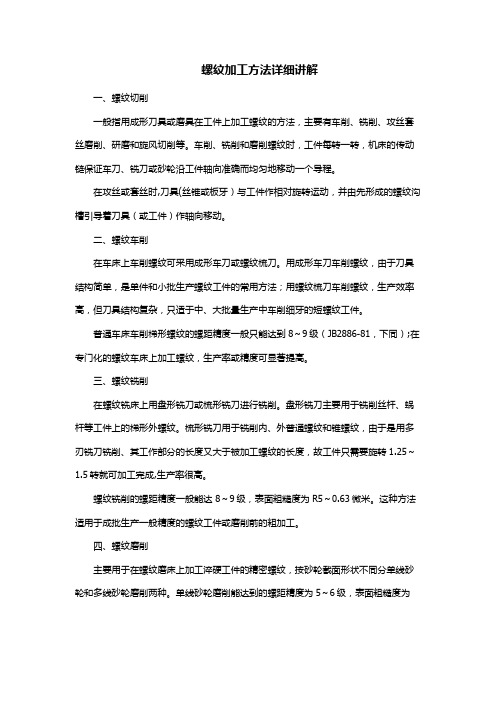
螺纹加工方法详细讲解一、螺纹切削一般指用成形刀具或磨具在工件上加工螺纹的方法,主要有车削、铣削、攻丝套丝磨削、研磨和旋风切削等。
车削、铣削和磨削螺纹时,工件每转一转,机床的传动链保证车刀、铣刀或砂轮沿工件轴向准确而均匀地移动一个导程。
在攻丝或套丝时,刀具(丝锥或板牙)与工件作相对旋转运动,并由先形成的螺纹沟槽引导着刀具(或工件)作轴向移动。
二、螺纹车削在车床上车削螺纹可采用成形车刀或螺纹梳刀。
用成形车刀车削螺纹,由于刀具结构简单,是单件和小批生产螺纹工件的常用方法;用螺纹梳刀车削螺纹,生产效率高,但刀具结构复杂,只适于中、大批量生产中车削细牙的短螺纹工件。
普通车床车削梯形螺纹的螺距精度一般只能达到8~9级(JB2886-81,下同);在专门化的螺纹车床上加工螺纹,生产率或精度可显著提高。
三、螺纹铣削在螺纹铣床上用盘形铣刀或梳形铣刀进行铣削。
盘形铣刀主要用于铣削丝杆、蜗杆等工件上的梯形外螺纹。
梳形铣刀用于铣削内、外普通螺纹和锥螺纹,由于是用多刃铣刀铣削、其工作部分的长度又大于被加工螺纹的长度,故工件只需要旋转1.25~1.5转就可加工完成,生产率很高。
螺纹铣削的螺距精度一般能达 8~9级,表面粗糙度为R5~0.63微米。
这种方法适用于成批生产一般精度的螺纹工件或磨削前的粗加工。
四、螺纹磨削主要用于在螺纹磨床上加工淬硬工件的精密螺纹,按砂轮截面形状不同分单线砂轮和多线砂轮磨削两种。
单线砂轮磨削能达到的螺距精度为5~6级,表面粗糙度为R1.25~0.08微米,砂轮修整较方便。
这种方法适于磨削精密丝杠、螺纹量规、蜗杆、小批量的螺纹工件和铲磨精密滚刀。
多线砂轮磨削又分纵磨法和切入磨法两种。
纵磨法的砂轮宽度小于被磨螺纹长度,砂轮纵向移动一次或数次行程即可把螺纹磨到最后尺寸。
切入磨法的砂轮宽度大于被磨螺纹长度,砂轮径向切入工件表面,工件约转1.25转就可磨好,生产率较高,但精度稍低,砂轮修整比较复杂。
切入磨法适于铲磨批量较大的丝锥和磨削某些紧固用的螺纹。
普通车床车螺纹教程

普通车床车螺纹教程
车螺纹是车床加工中常见的操作之一,下面将详细介绍普通车床车螺纹的操作步骤。
1. 准备工作:选择合适的车刀、切削液和螺纹规格。
根据需要,选择合适的螺距和螺纹类型。
2. 将工件固定在车床的夹持装置上。
确保工件稳固,并根据需要进行适当的夹紧和支撑。
3. 调整车床的转速和进给速度。
根据工件材料和螺纹规格,选择合适的车削参数。
4. 使用车刀将工件端面削平,确保车削开始时刀具与工件的接触面积充分。
5. 将车刀切削边缘与工件端面垂直对齐。
开始车削前,注意刀具的朝向和位置。
6. 缓慢向工件表面进给车刀,保持适当的切削深度。
同时,使用适量的切削液进行冷却和润滑。
7. 轻轻地转动手轮,同时保持车刀沿着工件轮廓移动,形成螺纹的切削。
8. 控制进给速度,使车床给进床移动的距离等于螺纹螺距。
一圈结束后,及时调整车床床的位置,开始下一圈的车削。
9. 继续进行车削,直到螺纹的长度满足要求。
10. 完成车削后,停止车床的运转。
使用刷子清除工件表面的切削屑,并进行必要的修整和磨光。
11. 检查车削的螺纹是否符合规格要求,可以使用螺纹量规进行测量。
12. 若需要进行下一步工序,及时清洁工件和车床。
若不需要继续加工,可以拆卸工件,并妥善保管。
以上是普通车床车螺纹的简要步骤,希望对您有所帮助。
干货,螺纹加工常见问题及解决方法,车工必备

扎刀1、主要原因(1)车刀的前角太大,机床X轴丝杆间隙较大;(2)车刀安装得过高或过低;(3)工件装夹不牢;(4)车刀磨损过大;(5)切削用量太大。
2、解决方法(1)减小车刀前角,维修机床调整X 轴的丝杆间隙,利用数控车床的丝杆间隙自动补偿功能补偿机床X 轴丝杆间隙。
(2)车刀安装得过高或过低:过高,则吃刀到一定深度时,车刀的后刀面顶住工件,增大摩擦力,甚至把工件顶弯,造成扎刀现象;过低,则切屑不易排出,车刀径向力的方向是工件中心,加上横进丝杠与螺母间隙过大,致使吃刀深度不断自动趋向加深,从而把工件抬起,出现扎刀。
此时,应及时调整车刀高度,使其刀尖与工件的轴线等高(可利用尾座顶尖对刀)。
在粗车和半精车时,刀尖位置比工件的中心高出1%D左右(D表示被加工工件直径)。
(3)工件装夹不牢:工件本身的刚性不能承受车削时的切削力,因而产生过大的挠度,改变了车刀与工件的中心高度(工件被抬高了),形成切削深度突增,出现扎刀,此时应把工件装夹牢固,可使用尾座顶尖等,以增加工件刚性。
(4)车刀磨损过大:引起切削力增大,顶弯工件,出现扎刀。
此时应对车刀加以修磨。
(5)切削用量(主要是背吃刀量和切削速度)太大:根据工件5 导程大小和工件刚性选择合理的切削用量。
乱扣1、故障现象当丝杠转一转时,工件未转过整数转而造成的。
2、主要原因(1)机床主轴编码器同步传动皮带磨损,检测不到主轴的同步真实转速;(2)编制输入主机的程序不正确;X轴或Y轴丝杆磨损。
3、解决方法(1)主轴编码器同步皮带磨损由于数控车床车削螺纹时,主轴与车刀的运动关系是由机床主机信息处理中心发出的指令来控制的,车削螺纹时,主轴转速恒定不变,X 或Y 轴可以根据工件导程大小和主轴转速来调整移动速度,所以中心必须检测到主轴同步真实转速,以发出正确指令控制X 或Y 轴正确移动。
如果系统检测不到主轴的真实转速,在实际车削时会发出不同的指令给X或Y,那么这时主轴转一转,刀具移动的距离就不是一个导程,第二刀车削时螺纹就会乱扣。
普通车床螺纹车削常见故障及解决方法(三篇)

普通车床螺纹车削常见故障及解决方法1. 放松刀夹:在车削过程中,如果刀夹没有固定好,会导致刀具松动或者偏位,从而造成螺纹不良。
解决方法是检查刀夹固定螺母是否紧固,如果松动则重新固定。
2. 刀具磨损:长时间使用刀具会磨损,导致刀尖变钝,从而无法进行正常的车削。
解决方法是更换刀具,保持刀具的锐利度。
3. 机床不稳定:如果机床本身存在不稳定的问题,例如床身变形、主轴不平衡等,会导致螺纹加工时产生偏差。
解决方法是定期检测和调整机床,确保其稳定性。
4. 刀具与工件匹配不良:在螺纹车削过程中,刀具与工件的匹配也非常重要。
如果选用的刀具尺寸不合适,就会导致螺纹加工结果不理想。
解决方法是选择合适尺寸的刀具,确保刀具与工件的配合良好。
5. 刀具进给速度不恰当:刀具进给速度过快或者过慢都会影响螺纹加工的质量。
解决方法是根据不同的工件材料和螺纹规格,调整刀具的进给速度,确保加工的质量。
6. 冷却液不适用:在螺纹车削过程中,适当使用冷却液可以降低温度,减少摩擦,提高切削润滑效果,从而改善加工质量。
如果使用的冷却液性质不合适,也会影响螺纹加工结果。
解决方法是选择合适的冷却液,根据加工工件的要求进行选择。
7. 机床刚度不足:机床刚度不足会导致在螺纹车削过程中产生振动和共振,造成螺纹不良。
解决方法是增加机床的刚度,例如加强机床床身的结构,增加加工时的稳定性。
8. 机床零件磨损:长时间使用机床,有些零部件会磨损,例如导轨、导向轨等,会导致加工误差。
解决方法是定期检查和更换机床零部件,保证机床的准确性和稳定性。
总之,普通车床螺纹车削常见故障的解决方法就是:确保刀具的固定和锐利度,稳定机床的结构和性能,选择合适尺寸和质量的刀具,调整进给速度和冷却液的使用,定期检查和维护机床零部件,确保加工质量和效果。
普通车床螺纹车削常见故障及解决方法(二)车床螺纹车削是机械加工中常见的一种加工方式,常用于制作螺纹零件。
然而,在车削过程中,可能会遇到一些常见的故障。
普通车床的螺纹车削加工

1)正反车车削法
开车,对刀
合闸,车螺纹
横向退刀,停车, 反转,纵向回起点
快速退出
开车切削 开反车返回
多刀循环加工
进刀
三、典型普通螺纹零件的车削加工
7. 螺纹车削操作方法与步骤
2)抬闸法 利用开合螺母的压下和抬起来车削螺纹。
控制手柄
正反车车削法
抬闸法
退刀方式 利用丝杆的反转纵向返回起点
进刀次数 第一次进刀 第二次进刀 第三次进刀 第四次进刀 第五次进刀 第六次进刀
背吃刀量 ap=0.50mm ap=0.15mm ap=0.10mm ap=0.03mm ap=0.02mm ap=0.01mm
加工步骤 粗加工
精加工
加工余量 0.75mm
0.06mm
三、典型普通螺纹零件的车削加工
4. 安装工件
5 ) 倒角
6 ) 车螺纹
三、典型普通螺纹零件的车削加工
刀具 名称
1 端面 端面刀
2
φ 24、φ 30外 圆
外圆刀
3
退刀槽
4×φ21.5
切槽刀
螺纹
4 M24X1.5— 螺纹刀
7h6h
刀具 材料
硬质 合金
硬质 合金
ap
f
(mm) (mm/r)
Vc
(m/mi n)
n (r/min)
1 0.2 62 500
1.5 0.25 62 500 0.5 0.1 68 700
高速钢 1 手动 15 200
高速钢 ? 1.5 4.5
60
三、典型普通螺纹零件的车削加工
螺纹总背吃刀量ap=h=0.54P=0.81mm
合理分配螺纹加工余量
- 1、下载文档前请自行甄别文档内容的完整性,平台不提供额外的编辑、内容补充、找答案等附加服务。
- 2、"仅部分预览"的文档,不可在线预览部分如存在完整性等问题,可反馈申请退款(可完整预览的文档不适用该条件!)。
- 3、如文档侵犯您的权益,请联系客服反馈,我们会尽快为您处理(人工客服工作时间:9:00-18:30)。
背吃刀量
ap=0.50mm ap=0.15mm ap=0.10mm ap=0.03mm ap=0.02mm ap=0.01mm
加工步骤 粗加工
精加工
加工余量 0.75mm
0.06mm
2021/3/11
பைடு நூலகம்
17
三、典型普通螺纹零件的车削加工
4. 安装工件
1)选择合适的夹紧位置。 2)有足够的夹紧力。
2021/3/11
与外螺纹牙底或内螺纹牙顶相重合的假想圆柱体直径,是 螺纹的最小直径。
2021/3/11
7
一、螺纹概述
3. 螺纹的基本要素
4)螺距(P):
螺纹上相邻两牙在中径线上对 应两点间的轴向距离。
5)导程(L ):
沿同一条螺旋线形成的螺纹上 相邻两牙在中径线上对应两点间的 轴向距离。
导程=螺距x线数
6)牙形角(α) :
适用于所有 螺距螺纹的加工。
刃切削。
斜进法
2021/3/11
垂直进刀+小刀架 向一个方向移动。
适用于较大
螺距螺纹的粗加 工。
23
四、螺纹的测量
1. 单项测量法
测量要素 大径 螺距 牙型角 中径
量(检)具 游标卡尺或千分尺
钢尺 螺距规或样板 螺纹千分尺
测量时点 车螺纹大径时 表面可见螺旋线时 牙型轮廓清晰时 精车前直到加工结束
— 7h6h — L — LH
2021/3/11
9
二、螺纹的车削加工工艺
螺纹常用的切削加工方法
车
铣
螺
螺
纹
纹
套 螺 纹
2021/3/11
攻 螺 纹
10
二、螺纹的车削加工工艺
1. 螺纹车削原理
车床主轴与刀具之间必须保持严格的运动关系:即主 轴(工件)每旋转一周,刀具均匀地移动一个导程的距离。
2021/3/11
在通过螺纹轴向的剖面上,螺 纹的轮廓形状称螺纹牙型,相邻两 牙侧之间的夹角即为牙形角。
2021/3/11
螺距
导程L 螺距P
α
8
一、螺纹概述
4. 螺纹的标注
特征代号、尺寸代号 公差带代号 旋合长度代号 旋向代号
左旋(LH)、右旋
长(L)、中(N)、短(S)
例: M 10×1
中径和大径的公差等级、基本偏差 牙型(M、Tr...)、公称直径、导程、螺距、线数
溜板箱
开合螺母
11
二、螺纹的车削加工工艺
2. 普通外螺纹的车削加工工艺流程
车端面 车螺纹大径 车退刀槽 倒角 车螺纹
d<公称直径 <螺纹小径
多刀车削
2021/3/11
12
三.典型普通螺纹零件的车削加工
1. 分析零件图
查表或计算 d=φ24 0 -0.23
d2=d-0.6495P=φ23.026
0 -0.19
2021/3/11
3
一、螺纹概述
螺纹是在圆柱(圆锥)工件表面上,沿着螺旋线所形 成的、具有相同剖面的连续凸起和沟槽。
2021/3/11
4
一、螺纹概述
1. 螺纹的应用
联接
2021/3/11
紧固
传动
5
一、螺纹概述
2. 螺纹的种类
联接 三角形螺纹 管螺纹
螺纹 梯形螺纹
传动 矩形螺纹 锯齿形螺纹
2021/3/11
200
螺纹
4 M24X1.5— 螺纹刀 高速钢 ? 1.5 4.5
60
7h6h
2021/3/11
16
三、典型普通螺纹零件的车削加工
螺纹总背吃刀量ap=h=0.54P=0.81mm
合理分配螺纹加工余量
(一般粗车ap:0.10~0.50;精车ap:0.01~0.10 。)
进刀次数 第一次进刀 第二次进刀 第三次进刀 第四次进刀 第五次进刀 第六次进刀
3.选择刀具及切削用量
序 号
加工内容
刀具 名称
刀具
ap
f
Vc
n
材料 (mm) (mm/r) (m/min) (r/min)
硬质
1
端面
端面刀 合金
1
0.2
62
500
2
φ24、φ30外 圆
外圆刀
硬质 合金
1.5 0.25 0.5 0.1
62 68
500 700
3
退刀槽
4×φ21.5
切槽刀 高速钢
1
手动
15
2021/3/11
24
四、螺纹的测量
2. 综合测量法
利用螺纹环规或塞规对螺纹多个要素进行检测,测 量外螺纹用环规,内螺纹用塞规。
环规
塞规
2021/3/11
25
退刀方式 利用丝杆的反转纵向返回起点
手动纵向返回起点
适用范围
适用于任何螺距的加工
只适用于丝杆螺距是工件 螺距整数倍时
2021/3/11
22
三、典型普通螺纹零件的车削加工
8. 螺纹车削进刀方式
加工方法 加工示意
加工特点
适用范围
直进法
垂直进刀,两刀刃
适用于小螺
同时车削。
距螺纹的加工。
左右车削法
垂直进刀+小刀架 左右移动,只有一条刀
6
一、螺纹概述
3. 螺纹的基本要素
1)大径( d 、 D) :
与外螺纹牙顶或内螺纹牙 底相重合的假想圆柱体直径, 是螺纹的最大直径。
2)中径( d2 、 D2 ):
一个假想圆柱的直径,其 圆柱母线通过牙型上沟槽和凸 起宽度相等的地方。
牙牙 底顶
d1 d2 d D1 D2 D
3)小径( d1 、 D1 ):
2021/3/11
13
三.典型普通螺纹零件的车削加工
2. 确定加工步骤
1 ) 车右端端面
2 ) 粗、精车φ30外圆
3 ) 车螺纹大径φ24
0 -0.23
4 ) 切槽
2021/3/11
14
三.典型普通螺纹零件的车削加工
2. 确定加工步骤
5 ) 倒角
6 ) 车螺纹
2021/3/11
15
三、典型普通螺纹零件的车削加工
普通外螺纹在普通车床加工
姜海 二零一三年十一月
2021/3/11
1
教学目的和要求
1 了解螺纹的应用、种类及基本要素; 2 了解螺纹车削原理和加工工艺; 3 初步掌握直进法车削普通外螺纹及其测量方法; 4 独立完成普通外螺纹车削实训件 。
2021/3/11
2
主要内容
一、螺纹概述 二、螺纹的车削加工工艺 三、典型普通螺纹零件的车削加工 四、螺纹的测量 五、课堂小结 六、作业
7. 螺纹车削操作方法与步骤
1)正反车车削法
开车,对刀
合闸,车螺纹
横向退刀,停车, 反转,纵向回起点
2021/3/11
快速退出
开车切削 开反车返回
多刀循环加工
进刀 21
三、典型普通螺纹零件的车削加工
7. 螺纹车削操作方法与步骤
2)抬闸法 利用开合螺母的压下和抬起来车削螺纹。
控制手柄
正反车车削法
抬闸法
18
三、典型普通螺纹零件的车削加工
5. 安装刀具
安装要点:刀尖分角线垂直于工件轴线。
工件
60°
对刀样板
2021/3/11
19
三、典型普通螺纹零件的车削加工
6. 机床调整
针对螺纹车削: 1)调整主轴转速; 2)调整螺距; 3)脱开光杠进给机构,改由丝杠进给。
2021/3/11
20
三、典型普通螺纹零件的车削加工