【外文文献翻译】化学工业
化工专业英语课文翻译
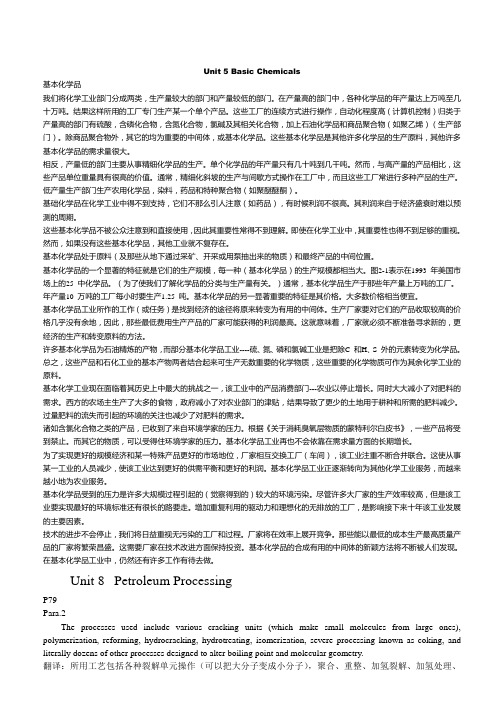
Unit 5 Basic Chemicals基本化学品我们将化学工业部门分成两类,生产量较大的部门和产量较低的部门。
在产量高的部门中,各种化学品的年产量达上万吨至几十万吨。
结果这样所用的工厂专门生产某一个单个产品。
这些工厂的连续方式进行操作,自动化程度高(计算机控制)归类于产量高的部门有硫酸,含磷化合物,含氮化合物,氯碱及其相关化合物,加上石油化学品和商品聚合物(如聚乙烯)(生产部门)。
除商品聚合物外,其它的均为重要的中间体,或基本化学品。
这些基本化学品是其他许多化学品的生产原料,其他许多基本化学品的需求量很大。
相反,产量低的部门主要从事精细化学品的生产。
单个化学品的年产量只有几十吨到几千吨。
然而,与高产量的产品相比,这些产品单位重量具有很高的价值。
通常,精细化斜坡的生产与间歇方式操作在工厂中,而且这些工厂常进行多种产品的生产。
低产量生产部门生产农用化学品,染料,药品和特种聚合物(如聚醚醚酮)。
基础化学品在化学工业中得不到支持,它们不那么引人注意(如药品),有时候利润不很高。
其利润来自于经济盛衰时难以预测的周期。
这些基本化学品不被公众注意到和直接使用,因此其重要性常得不到理解。
即使在化学工业中,其重要性也得不到足够的重视。
然而,如果没有这些基本化学品,其他工业就不复存在。
基本化学品处于原料(及那些从地下通过采矿、开采或用泵抽出来的物质)和最终产品的中间位置。
基本化学品的一个显著的特征就是它们的生产规模,每一种(基本化学品)的生产规模都相当大。
图2-1表示在1993 年美国市场上的25 中化学品。
(为了使我们了解化学品的分类与生产量有关。
)通常,基本化学品生产于那些年产量上万吨的工厂。
年产量10 万吨的工厂每小时要生产1.25 吨。
基本化学品的另一显著重要的特征是其价格。
大多数价格相当便宜。
基本化学品工业所作的工作(或任务)是找到经济的途径将原来转变为有用的中间体。
生产厂家要对它们的产品收取较高的价格几乎没有余地,因此,那些最低费用生产产品的厂家可能获得的利润最高。
化工专业英语 翻译
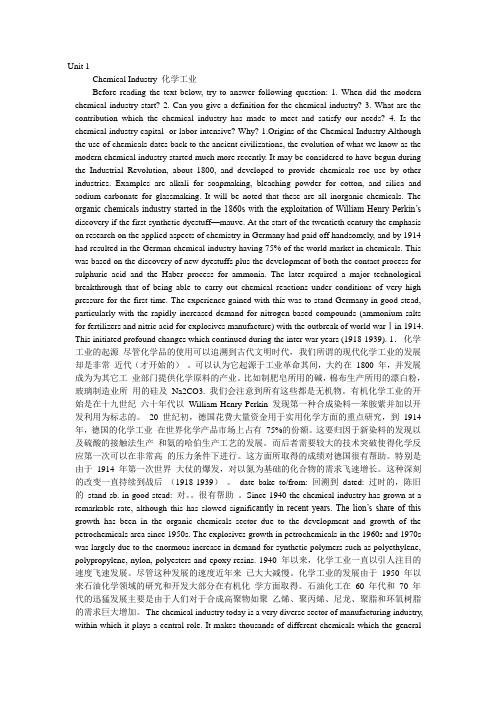
Unit 1Chemical Industry 化学工业Before reading the text below, try to answer following question: 1. When did the modern chemical industry start? 2. Can you give a definition for the chemical industry? 3. What are the contribution which the chemical industry has made to meet and satisfy our needs? 4. Is the chemical industry capital- or labor-intensive? Why? 1.Origins of the Chemical Industry Although the use of chemicals dates back to the ancient civilizations, the evolution of what we know as the modern chemical industry started much more recently. It may be considered to have begun during the Industrial Revolution, about 1800, and developed to provide chemicals roe use by other industries. Examples are alkali for soapmaking, bleaching powder for cotton, and silica and sodium carbonate for glassmaking. It will be noted that these are all inorganic chemicals. The organic chemicals industry started in the 1860s with the exploitation of William Henry Perkin’s discovery if the first synthetic dyestuff—mauve. At the start of the twentieth century the emphasis on research on the applied aspects of chemistry in Germany had paid off handsomely, and by 1914 had resulted in the German chemical industry having 75% of the world market in chemicals. This was based on the discovery of new dyestuffs plus the development of both the contact process for sulphuric acid and the Haber process for ammonia. The later required a major technological breakthrough that of being able to carry out chemical reactions under conditions of very high pressure for the first time. The experience gained with this was to stand Germany in good stead, particularly with the rapidly increased demand for nitrogen-based compounds (ammonium salts for fertilizers and nitric acid for explosives manufacture) with the outbreak of world warⅠin 1914. This initiated profound changes which continued during the inter-war years (1918-1939). 1.化学工业的起源尽管化学品的使用可以追溯到古代文明时代,我们所谓的现代化学工业的发展却是非常近代(才开始的)。
化工英文文献翻译
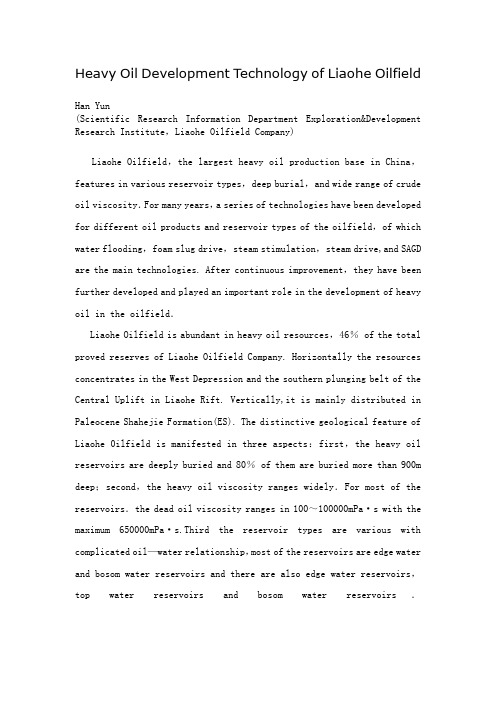
Heavy Oil Development Technology of Liaohe OilfieldHan Yun(Scientific Research Information Department Exploration&Development Research Institute,Liaohe Oilfield Company)Liaohe Oilfield,the largest heavy oil production base in China,features in various reservoir types,deep burial,and wide range of crude oil viscosity.For many years,a series of technologies have been developed for different oil products and reservoir types of the oilfield,of which water flooding,foam slug drive,steam stimulation,steam drive,and SAGD are the main technologies. After continuous improvement,they have been further developed and played an important role in the development of heavy oil in the oilfield.Liaohe Oilfield is abundant in heavy oil resources,46% of the total proved reserves of Liaohe Oilfield Company. Horizontally the resources concentrates in the West Depression and the southern plunging belt of the Central Uplift in Liaohe Rift. Vertically,it is mainly distributed in Paleocene Shahejie Formation(ES). The distinctive geological feature of Liaohe 0ilfield is manifested in three aspects:first,the heavy oil reservoirs are deeply buried and 80% of them are buried more than 900m deep;second,the heavy oil viscosity ranges widely.For most of the reservoirs.the dead oil viscosity ranges in 100~100000mPa·s with the maximum 650000mPa·s.Third the reservoir types are various with complicated oil—water relationship,most of the reservoirs are edge water and bosom water reservoirs and there are also edge water reservoirs,top water reservoirs and bosom water reservoirs.For more than 20 years of development,Liaohe Oilfield has developed series of heavy oil development technologies for different oil products and different types of reservoirs,such as water flooding, foam slug drive,steam stimulation steam drive and SAGD.The most difficult issues have been overcome in the development of the super heavy oil in deeper formation.which has maintained the annual heavy oil output at 8 million tons for many years in Liaohe Oilfield.Water flooding development technology for conventional heavy oil-type 1Based on heavy oil classification,the conventional heavy oil.type I refers to the heavy oil with viscosity ranging in 50~100mPa·s,taking up about 20% of the proved oil reserves of the oilfield.The heavy oil reservoirs of this type are buried ranging from 1 500m to 2400m deep and are capable of flowing.Therefore,natural energy is utilized for conventional development and then water flooding technology is used.For example,the reservoir of $32 oil unit of Block Leng-43 is buried 1 650~l 940m deep with the average oil zone 87.7m thick and the oil viscosity in situ 58mPa·s.In 1992,the 141 m spacing square well pattern was adopted to develop the kind of reservoirs by utilizing natural energy and two sets of oil production zones.In 2004,water flooding technology was applied. Currently,the degree of reserve recovery reaches 14%.the annual oil recovery rate is 1%,and the ultimate recovery ratio is predicted to be as high as 22%.Technology of foam slug and for conventional heavy oil-type steam flooding for conventional heavy oil-type 2 The upper limit of viscosity for the conventional heavy oil—type IIis l 0000mPa·s(the dead oil viscosity in situ).This kind of heavy oil is the dominant type of heavy oil in Liaohe Oilfield,accounting for 60% of total proved reserves.The reservoir of such heavy oil is buffed 800-1 600m deep in genera1. At initial development stage, steam stimulation was carried out to develop this kind of reservoirs.In the higher cycles of steam flooding,the reservoirs with the heavy oil viscosity close to the lower limit of this kind of heavy oil are conversed into the steam drive development.Pilot tests of foam slug and steam flooding have conducted in Block Jin-90 and Block Qi-40 successfully,and they will be applied to the whole blocks in near future.The recovery factor is forecast to be up to 50% ~60%.Steam stimulation technology for special heavy oilThe special heavy oil refers to the heavy oil with the viscosity ranging in 10000~50000mPa·s in situ,which takes up 10% of proved oil reserves of the oilfield. The reservoir of the kind of oil is buried ranging from 1400m to 1800m. Steam simulation technology is often applied to develop such reservoirs. However, technology of steam drive or SAGD are also under research and experiments for reservoirs of good quality.SAGD technology for super heavy oilThe super heavy oil reservoir refers to the heavy oil with dead oil viscosity in situ over 50000mPa·s, which accounts for 10% of proved reserves of the oilfield. Due to its extremely high viscosity, it is just developed for few years. For the massive super heavy oil reservoirs, SAGD can be applied in the late stage of steam stimulation. At present, good intermediate results have been obtained in SAGD pilot test in Block Du-84 of Guantao Formation, showing good prospect for application. Theyhave been applied in the whole block and the ultimate recovery factor is predicted to achieve 55%.ConclusionVarious technology should be applied to develop different types of heavy oil reservoirs. Besides the technologies mentioned above, the technologies of combustion in situ, flue gas drive, and steam foam drive are also under research currently. Therefore, various development technologies will be increasingly improved with the heavy oil development of Liaohe Oilfield.References[1] Wang Xu. 2006. Heavy Oil Development Technologies and Discussion on the Research Orientation in the Next Step. Petroleum Exploration and Development [J],33(4):484~490[2] Liu Junrong. The Paper Collection of Liaohe Oilfield Development Seminar[C]:Beijing, Petroleum Industry Press, 2002[3] Zeng Yuqiang. 2006. Heavy Oil steam Stimulation Review. Special Oil&Gas Reservoir[J], 13(6):5~9辽河油田的重油开发技术韩云(科研信息部门勘探和开发研究所、辽河油田公司)辽河油田,在中国最大的重油生产基地,在不同的储层类型,具有埋藏深,与原油粘度范围宽。
化学专业外文文献原稿和译文
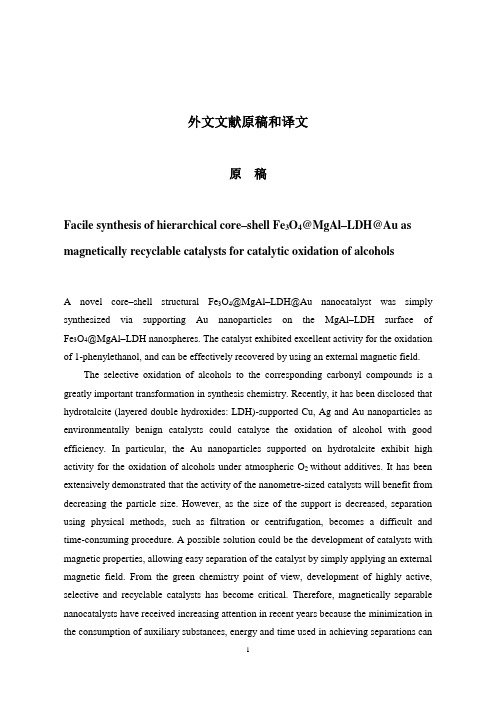
外文文献原稿和译文原稿Facile synthesis of hierarchical core–shell Fe3O4@MgAl–LDH@Au as magnetically recyclable catalysts for catalytic oxidation of alcoholsA novel core–shell structural Fe3O4@MgAl–LDH@Au nanocatalyst was simply synthesized via supporting Au nanoparticles on the MgAl–LDH surface of Fe3O4@MgAl–LDH nanospheres. The catalyst exhibited excellent activity for the oxidation of 1-phenylethanol, and can be effectively recovered by using an external magnetic field.The selective oxidation of alcohols to the corresponding carbonyl compounds is a greatly important transformation in synthesis chemistry. Recently, it has been disclosed that hydrotalcite (layered double hydroxides: LDH)-supported Cu, Ag and Au nanoparticles as environmentally benign catalysts could catalyse the oxidation of alcohol with good efficiency. In particular, the Au nanoparticles supported on hydrotalcite exhibit high activity for the oxidation of alcohols under atmospheric O2 without additives. It has been extensively demonstrated that the activity of the nanometre-sized catalysts will benefit from decreasing the particle size. However, as the size of the support is decreased, separation using physical methods, such as filtration or centrifugation, becomes a difficult and time-consuming procedure. A possible solution could be the development of catalysts with magnetic properties, allowing easy separation of the catalyst by simply applying an external magnetic field. From the green chemistry point of view, development of highly active, selective and recyclable catalysts has become critical. Therefore, magnetically separable nanocatalysts have received increasing attention in recent years because the minimization in the consumption of auxiliary substances, energy and time used in achieving separations canresult in significant economical and environmental benefits.Magnetic composites with a core–shell structure allow the integration of multiple functionalities into a single nanoparticle system, and offer unique advantages for applications, particularly in biomedicine and catalysis. However it is somewhat of a challenge to directly immobilize hierarchical units onto the magnetic cores. In our previous work, the Fe3O4 submicro-spheres were first coated with a thin carbon layer, then coated with MgAl–LDH to obtain an anticancer agent-containing Fe3O4@DFUR–LDH as drug targeting delivery vector. Li et al. prepared Fe3O4@MgAl–LDH through a layer-by-layer assembly of delaminated LDH nanosheets as a magnetic matrix for loading W7O24as a catalyst. These core–shell structural nanocomposites possess the magnetization of magnetic materials and multiple functionalities of the LDH materials. Nevertheless, these reported synthesis routes need multi-step and sophisticated procedures. Herein, we design a facile synthesis strategy for the fabrication of a novel Fe3O4@MgAl–LDH@Au nanocatalyst, consisting of Au particles supported on oriented grown MgAl–LDH crystals over the Fe3O4 nanospheres, which combines the excellent catalytic properties of Au nanoparticles with the superparamagnetism of the magnetite nanoparticles. To the best of our knowledge, this is the first instance of direct immobilization of vertically oriented MgAl–LDH platelet-like nanocrystals onto the Fe3O4 core particles by a simple coprecipitation method and the fabrication of hierarchical magnetic metal-supported nanocatalysts via further supporting metal nanoparticles.As illustrated in Scheme 1, the synthesis strategy of Fe3O4@MgAl–LDH@Au involves two key aspects. Nearly monodispersed magnetite particles were pre-synthesized using a surfactant-free solvothermal method. First, the Fe3O4 suspension was adjusted to a pH of ca. 10, and thus the obtained fully negatively charged Fe3O4spheres were easily coated with a layer of oriented grown carbonate–MgAl–LDH via electrostatic attraction followed by interface nucleation and crystal growth under dropwise addition of salts and alkaline solutions. Second, Au nanoparticles were effectively supported on thus-formed support Fe3O4@MgAl–LDH by a deposition–precipitation method (see details in ESI).Fig. 1 depicts the SEM/TEM images of the samples at various stages of the fabrication of the Fe3O4@MgAl–LDH@Au nanocatalyst. The Fe3O4nanospheres (Fig. 1a) show asmooth surface and a mean diameter of 450 nm with a narrow size distribution (Fig. S1, ESI). After direct coating with carbonate–MgAl–LDH (Fig. 1b), a honeycomb like morphology with many voids in the size range of 100–200 nm is clearly observed, and the LDH shell is composed of interlaced platelets of ca. 20 nm thickness. Interestingly, the MgAl–LDH shell presents a marked preferred orientation with the c-axis parallel to, and the ab-face perpendicular to the surface of the magnetite cores, quite different from those of a previous report. A similar phenomenon has only been observed for the reported LDH films and the growth of layered hydroxides on cation-exchanged polymer resin beads. The TEM image of two separate nanospheres (Fig. 1d) undoubtedly confirms the core–shell structure of the Fe3O4@MgAl–LDH with the Fe3O4 cores well-coated by a layer of LDH nanocrystals. In detail, the MgAl–LDH crystal monolayers are formed as large thin nanosheet-like particles, showing a edge-curving lamella with a thickness of ca. 20 nm and a width of ca. 100 nm, growing from the magnetite core to the outer surface and perpendicular to the Fe3O4surface. The outer honeycomb like microstructure of the obtained core–shell Fe3O4@MgAl–LDH nanospheres with a surface area of 43.3 m2g_1 provides abundant accessible edge and junction sites of LDH crystals making it possible for this novel hierarchical composite to support metal nanoparticles. With such a structural morphology, interlaced perpendicularly oriented MgAl–LDH nanocrystals can facilitate the immobilization of nano-metal particles along with avoiding the possible aggregation.Scheme 1 The synthetic strategy of an Fe3O4@MgAl–LDH@Au catalyst.Fig. 1 SEM (a, b and c), TEM (d and e) and HRTEM (f) images and EDX spectrum (g) of Fe3O4 (a), Fe3O4@MgAl–LDH (b and d) and Fe3O4@MgAl–LDH@Au (c, e, f and g).Fig. 2 XRD patterns of Fe3O4 (a), Fe3O4@MgAl–LDH (b) and Fe3O4@MgAl–LDH@Au(c).The XRD results (Fig. 2) demonstrate that the Fe3O4@MgAl–LDH nanospheres are composed of an hcp MgAl–LDH (JCPDS 89-5434) and fcc Fe3O4 (JCPDS 19-0629). It canbe clearly seen from Fig. 2b that the series (00l) reflections at low 2θ angles aresignificantly reduced compared with those of single MgAl–LDH (Fig. S2, ESI), while the (110) peak at high 2θangle is clearly distinguished with relatively less decrease, as revealed by greatly reduced I(003)/I(110) = 0.8 of Fe3O4@MgAl–LDH than that of MgAl–LDH (3.9). This phenomenon is a good evidence for an extremely well-oriented assembly of MgAl–LDH platelet-like crystals consistent with the c-axis of the crystals being parallel to the surface of an Fe3O4core. The particle dimension in the c-axis is calculated as ~ 25 nm using the Scherrer equation (eqn S1, ESI) based on the (003) line width (Fig. 2b), in good agreement with the SEM/TEM results. The energy-dispersive X-ray (EDX) result (Fig. S3, ESI) of Fe3O4@MgAl–LDH reveals the existence of Mg, Al, Fe and O elements, and the Mg/Al molar ratio of 2.7 close to the expected one (3.0), indicating the complete coprecipitation of metal cations for MgAl–LDH coating on the surface of Fe3O4.The FTIR data (Fig. S4, ESI) further evidence the chemical compositions and structural characteristics of the composites. The as-prepared Fe3O4@MgAl–LDH nanosphere shows a sharp absorption at ca. 1365 cm_1 being attributed to the ν3 (asymmetric stretching) mode of CO32_ ions and a peak at 584 cm_1 to the Fe–O lattice mode of the magnetite phase, indicating the formation of a CO32–LDH shell on the surface of the Fe3O4 core. Meanwhile, a strong broad band around 3420 cm_1 can be identified as the hydroxyl stretching mode, arising from metal hydroxyl groups and hydrogen-bonded interlayer water molecules. Another absorption resulting from the hydroxyl deformation mode of water, δ(H2O), is recorded at ca. 1630 cm_1.Based on the successful synthesis of honeycomb like core–shell nanospheres, Fe3O4@MgAl–LDH, our recent work further reveals that this facile synthesis approach can be extended to prepare various core–shell structured LDH-based hierarchical magnetic nanocomposites according to the tenability of the LDH layer compositions, such as NiAl–LDH and CuNiAl–LDH (Fig. S3, ESI).Gold nanoparticles were further assembled on the honeycomb likeMgAl–LDH platelet-like nanocrystals of Fe3O4@MgAl–LDH. Though the XRD pattern (Fig. 2c) fails to show the characteristics of Au nanoparticles, it can be clearly seen by the TEM of Fe3O4@MgAl–LDH@Au (Fig. 1e) that Au nanoparticles are evenly distributed on the edgeand junction sites of the interlaced MgAl–LDH nanocrystals with a mean diameter of 7.0 nm (Fig. S5, ESI), implying their promising catalytic activity. Meanwhile, the reduced packing density (large void) and the less sharp edge of LDH platelet-like nanocrystals can be observed (Fig. 1c and e). To get more insight on structural information of Fe3O4@MgAl–LDH@Au, the HRTEM image was obtained (Fig. 1f). It can be observed that both the Au and MgAl–LDH nanophases exhibit clear crystallinity as evidenced by well-defined lattice fringes. The interplanar distances of 0.235 and 0.225 nm for two separate nanophases can be indexed to the (111) plane of cubic Au (JCPDS 89-3697) and the (015) facet of the hexagonal MgAl–LDH phase (inset in Fig. 1f and Fig. S6 (ESI)). The EDX data (Fig. 1g) indicate that the magnetic core–shell particle contains Au, Mg, Al, Fe and O elements. The Au content is determined as 0.5 wt% upon ICP-AES analysis.Table 1 Recycling results on the oxidation of 1-phenylethanol The VSM analysis (Fig. S7, ESI) shows the typical superparamagnetism of the samples. The lower saturation magnetization (Ms) of Fe3O4@MgAl–LDH (20.9 emu g_1) than the Fe3O4 (83.8 emu g_1) is mainly due to the contribution of non-magnetic MgAl–LDH coatings (68 wt%) to the total sample. Interestingly, Ms of Fe3O4@MgAl–LDH@Au is greatly enhanced to 49.2 emu g_1, in line with its reduced MgAl–LDH content (64 wt%). This phenomenon can be ascribed to the removal of weakly linked MgAl–LDH particles among the interlaced MgAl–LDH nanocrystals during the Au loading process, which results in a less densely packed MgAl–LDH shell as indicated by SEM. The strong magnetic sensitivity of Fe3O4@MgAl–LDH@Au provides an easy and effective way to separate nanocatalysts from a reaction system.The catalytic oxidation of 1-phenylethanol as a probe reaction over the present novel magnetic Fe3O4@MgAl–LDH@Au (7.0 nm Au) nanocatalyst demonstrates high catalytic activity. The yield of acetophenone is 99%, with a turnover frequency (TOF) of 66 h_1,which is similar to that of the previously reported Au/MgAl–LDH (TOF, 74 h_1) with a Au average size of 2.7 nm at 40 1C, implying that the catalytic activity of Fe3O4@MgAl–LDH@Au can be further enhanced as the size of Au nanoparticles is decreased. Meanwhile, the high activity and selectivity of the Fe3O4@MgAl–LDH@Au can be related to the honeycomb like morphology of the support Fe3O4@MgAl–LDH being favourable to the high dispersion of Au nanoparticles and possible concerted catalysis of the basic support. Five reaction cycles have been tested for the Au nanocatalysts after easy magnetic separation by using a magnet (4500 G), and no deactivation of the catalyst has been observed (Table 1). Moreover, no Au, Mg and Al leached into the supernatant as confirmed by ICP (detection limit: 0.01 ppm) and almost the same morphology remained as evidenced by SEM of the reclaimed catalyst (Fig. S8, ESI).In conclusion, a novel hierarchical core–shell magnetic gold nanocatalyst Fe3O4@MgAl–LDH@Au is first fabricated via a facile synthesis method. The direct coating of LDH plateletlike nanocrystals vertically oriented to the Fe3O4 surface leads to a honeycomb like core–shell Fe3O4@MgAl–LDH nanosphere. By a deposition–precipitation method, a gold-supported magnetic nanocatalyst Fe3O4@MgAl–LDH@Au has been obtained, which not only presents high 1-phenylethanol oxidation activity, but can be conveniently separated by an external magnetic field as well. Moreover, a series of magnetic Fe3O4@LDH nanospheres involving NiAl–LDH and CuNiAl–LDH can be fabricated based on the LDH layer composition tunability and multi-functionality of the LDH materials, making it possible to take good advantage of these hierarchical core–shell materials in many important applications in catalysis, adsorption and sensors.This work is supported by the 973 Program (2011CBA00508).译文简易合成易回收的分层核壳Fe3O4@MgAl–LDH@Au磁性纳米粒子催化剂催化氧化醇类物质一种新的核壳结构的Fe3O4@MgAl–LDH@Au纳米催化剂的制备只是通过Au离子负载在已合成的纳米粒子Fe3O4@MgAl–LDH球体的MgAl–LDH的表面上。
中英文文献以及翻译(化工类)

Foreign material:Chemical Industry1.Origins of the Chemical IndustryAlthough the use of chemicals dates back to the ancient civilizations, the evolution of what we know as the modern chemical industry started much more recently. It may be considered to have begun during the Industrial Revolution, about 1800, and developed to provide chemicals roe use by other industries. Examples are alkali for soapmaking, bleaching powder for cotton, and silica and sodium carbonate for glassmaking. It will be noted that these are all inorganic chemicals. The organic chemicals industry started in the 1860s with the exploitation of William Henry Perkin’s discovery if the first synthetic dyestuff—mauve. At the start of the twentieth century the emphasis on research on the applied aspects of chemistry in Germany had paid off handsomely, and by 1914 had resulted in the German chemical industry having 75% of the world market in chemicals. This was based on the discovery of new dyestuffs plus the development of both the contact process for sulphuric acid and the Haber process for ammonia. The later required a major technological breakthrough that of being able to carry out chemical reactions under conditions of very high pressure for the first time. The experience gained with this was to stand Germany in good stead, particularly with the rapidly increased demand for nitrogen-based compounds (ammonium salts for fertilizers and nitric acid for explosives manufacture) with the outbreak of world warⅠin 1914. This initiated profound changes which continued during the inter-war years (1918-1939).Since 1940 the chemical industry has grown at a remarkable rate, although this has slowed significantly in recent years. The lion’s share of this growth has been in the organic chemicals sector due to the development and growth of the petrochemicals area since 1950s. The explosives growth in petrochemicals in the 1960s and 1970s was largely due to the enormous increase in demand for synthetic polymers such as polyethylene, polypropylene, nylon, polyesters and epoxy resins.The chemical industry today is a very diverse sector of manufacturing industry, within which it plays a central role. It makes thousands of different chemicals whichthe general public only usually encounter as end or consumer products. These products are purchased because they have the required properties which make them suitable for some particular application, e.g. a non-stick coating for pans or a weedkiller. Thus chemicals are ultimately sold for the effects that they produce.2. Definition of the Chemical IndustryAt the turn of the century there would have been little difficulty in defining what constituted the chemical industry since only a very limited range of products was manufactured and these were clearly chemicals, e.g., alkali, sulphuric acid. At present, however, many intermediates to products produced, from raw materials like crude oil through (in some cases) many intermediates to products which may be used directly as consumer goods, or readily converted into them. The difficulty cones in deciding at which point in this sequence the particular operation ceases to be part of the chemical industry’s sphere of activities. To consider a specific example to illustrate this dilemma, emulsion paints may contain poly (vinyl chloride) / poly (vinyl acetate). Clearly, synthesis of vinyl chloride (or acetate) and its polymerization are chemical activities. However, if formulation and mixing of the paint, including the polymer, is carried out by a branch of the multinational chemical company which manufactured the ingredients, is this still part of the chemical industry of does it mow belong in the decorating industry?It is therefore apparent that, because of its diversity of operations and close links in many areas with other industries, there is no simple definition of the chemical industry. Instead each official body which collects and publishes statistics on manufacturing industry will have its definition as to which operations are classified as the chemical industry. It is important to bear this in mind when comparing statistical information which is derived from several sources.3. The Need for Chemical IndustryThe chemical industry is concerned with converting raw materials, such as crude oil, firstly into chemical intermediates and then into a tremendous variety of other chemicals. These are then used to produce consumer products, which make our livesmore comfortable or, in some cases such as pharmaceutical produces, help to maintain our well-being or even life itself. At each stage of these operations value is added to the produce and provided this added exceeds the raw material plus processing costs then a profit will be made on the operation. It is the aim of chemical industry to achieve this.It may seem strange in textbook this one to pose the question “do we need a chemical industry?” However trying to answer this question will provide(ⅰ) an indication of the range of the chemical industry’s activities, (ⅱ) its influence on our lives in everyday terms, and (ⅲ) how great is society’s need for a chemical industry. Our approach in answering the question will be to consider the industry’s co ntribution to meeting and satisfying our major needs. What are these? Clearly food (and drink) and health are paramount. Other which we shall consider in their turn are clothing and (briefly) shelter, leisure and transport.(1)Food. The chemical industry makes a major contribution to food production in at least three ways. Firstly, by making available large quantities of artificial fertilizers which are used to replace the elements (mainly nitrogen, phosphorus and potassium) which are removed as nutrients by the growing crops during modern intensive farming. Secondly, by manufacturing crop protection chemicals, i.e., pesticides, which markedly reduce the proportion of the crops consumed by pests. Thirdly, by producing veterinary products which protect livestock from disease or cure their infections.(2)Health. We are all aware of the major contribution which the pharmaceutical sector of the industry has made to help keep us all healthy, e.g. by curing bacterial infections with antibiotics, and even extending life itself, e.g. ß–blockers to lower blood pressure.(3)Clothing. The improvement in properties of modern synthetic fibers over the traditional clothing materials (e.g. cotton and wool) has been quite remarkable. Thus shirts, dresses and suits made from polyesters like Terylene and polyamides like Nylon are crease-resistant, machine-washable, and drip-dry or non-iron. They are also cheaper than natural materials.Parallel developments in the discovery of modern synthetic dyes and the technology to “bond” th em to the fiber has resulted in a tremendous increase in the variety of colors available to the fashion designer. Indeed they now span almost every color and hue of the visible spectrum. Indeed if a suitable shade is not available, structural modification of an existing dye to achieve this canreadily be carried out, provided there is a satisfactory market for the product.Other major advances in this sphere have been in color-fastness, i.e., resistance to the dye being washed out when the garment is cleaned.(4)Shelter, leisure and transport. In terms of shelter the contribution of modern synthetic polymers has been substantial. Plastics are tending to replace traditional building materials like wood because they are lighter, maintenance-free (i.e. they are resistant to weathering and do not need painting). Other polymers, e.g. urea-formaldehyde and polyurethanes, are important insulating materials f or reducing heat losses and hence reducing energy usage.Plastics and polymers have made a considerable impact on leisure activities with applications ranging from all-weather artificial surfaces for athletic tracks, football pitches and tennis courts to nylon strings for racquets and items like golf balls and footballs made entirely from synthetic materials.Like wise the chemical industry’s contribution to transport over the years has led to major improvements. Thus development of improved additives like anti-oxidants and viscosity index improves for engine oil has enabled routine servicing intervals to increase from 3000 to 6000 to 12000 miles. Research and development work has also resulted in improved lubricating oils and greases, and better brake fluids. Yet again the contribution of polymers and plastics has been very striking with the proportion of the total automobile derived from these materials—dashboard, steering wheel, seat padding and covering etc.—now exceeding 40%.So it is quite apparent even from a brief look at the chemical industry’s contribution to meeting our major needs that life in the world would be very different without the products of the industry. Indeed the level of a country’s development may be judged by the production level and sophistication of its chemical industry4. Research and Development (R&D) in Chemical IndustriesOne of the main reasons for the rapid growth of the chemical industry in the developed world has been its great commitment to, and investment in research and development (R&D). A typical figure is 5% of sales income, with this figure being almost doubled for the most research intensive sector, pharmaceuticals. It is important to emphasize that we are quoting percentages here not of profits but of sales income, i.e. the total money received, which has to pay for raw materials, overheads, staff salaries, etc. as well. In the past this tremendous investment has paid off well, leading to many useful and valuable products being introduced to the market. Examplesinclude synthetic polymers like nylons and polyesters, and drugs and pesticides. Although the number of new products introduced to the market has declined significantly in recent years, and in times of recession the research department is usually one of the first to suffer cutbacks, the commitment to R&D remains at a very high level.The chemical industry is a very high technology industry which takes full advantage of the latest advances in electronics and engineering. Computers are very widely used for all sorts of applications, from automatic control of chemical plants, to molecular modeling of structures of new compounds, to the control of analytical instruments in the laboratory.Individual manufacturing plants have capacities ranging from just a few tones per year in the fine chemicals area to the real giants in the fertilizer and petrochemical sectors which range up to 500,000 tonnes. The latter requires enormous capital investment, since a single plant of this size can now cost $520 million! This, coupled with the widespread use of automatic control equipment, helps to explain why the chemical industry is capital-rather than labor-intensive.The major chemical companies are truly multinational and operate their sales and marketing activities in most of the countries of the world, and they also have manufacturing units in a number of countries. This international outlook for operations, or globalization, is a growing trend within the chemical industry, with companies expanding their activities either by erecting manufacturing units in other countries or by taking over companies which are already operating there.化学工业1.化学工业的起源尽管化学品的使用可以追溯到古代文明时代,我们所谓的现代化学工业的发展却是非常近代(才开始的)。
化学工业中英文对照外文翻译文献

中英文对照外文翻译(文档含英文原文和中文翻译)译文:化学工业1. 化学工业的定义在本世纪初,定义出化学工艺制品的构成是不难的,因为那时制造出来的化学产品很有限,例如,强碱、硫酸溶液。
现在,千上万的化学品从天然材料中提炼出来,例如原油(某些领域)被加工成很多中间产品,可以作为消费品,或着转变成消费品。
困难是在于裁决那一部分的过程属于化学工业领域,举个例子来阐释这种情况,乳化油漆可以含有聚合物(聚乙烯树脂)/聚脂(乙烯基醋酸纤维)。
很明显的,人造聚乙烯树脂(或醋酸纤维)和它们的聚合物都是化工产品。
然而,如果油漆的合成和配制中含有聚脂,它是由多种化工加工产生的副产品,那它是属于化学工业产品还是装饰工业产品呢?办公多样化和各个工业领域的相似性造成的,是由于没有给化学工业简单定义。
相反,每一个办公个体搜集和出版关于工业生产的数据,将会给那些化工生产过程一个简单的定义。
在比较那些不同来源的统计信息的时候,这是需要铭记于心的。
2. 化学工业的需要化学工业与许多原材料的加工有密切关系。
如原油,首先要变成化工中间产品,然后被加工成各种各样的其他化工产品。
这些产品经常被用来生产消费产品,使得我们的生活更加舒适,或者在另外一些领域比如制药方面,用于保持我们身体健康。
每一个阶段产生的价值都被加入到产品中,而且它提供的这些附加价值远远超过了原材料价值和制造加工过程的成本,这样过程中就产生了利润。
这也是化学工业的目的所在。
在书中提出这样一个问题可能会很奇怪:“我们需要化学工业么。
”然而,如果尝试去回答这个问题就会得出:(1)化学工业活动的领域很广泛(2)它影响我们的日常生活(3)社会很需要化学工业我们的话题是回答这个问题化学工业对我们的贡献。
这些需要包括什么呢?新鲜的食物(和饮料)和健康是主要的。
其它我们考虑的还有服饰,住房,娱乐及交通运输。
1.食物。
化学工业对食物生产的主要贡献至少体现在三个方面。
首先,生产大量可用化肥代替作物生长需要的自然化肥(如氮、磷、钾),促使现代农业增产。
化学化工类外文翻译 原文
化学化工类外文翻译原文Original Text:Chapter 1 Introduction1.1 BackgroundNuclear energy has been providing a significant share of the world’s electricity for more than half a century. Currently, nuclear power plants generate approximately 10% of the world’s electricity supply, with this figure increasing to over 30% in some countries such as France [1]. However, for nuclear energy to continue to be an important source of electricity in the future, the safe and efficient operation of nuclear power plants must be ensured. A key component of ensuring safe and efficient operation is the availability of inspection techniques that can detect defects, assess their severity, and monitor their growth over time.The presence of defects in materials used in nuclear power plants can arise from a number of sources including fabrication, welding, and service exposure. Defects can manifest themselves as a variety of features such as cracks, voids, inclusions, and inhomogeneities. Defects can be classified based on their size, shape, and orientation, with some defectsbeing more critical to the performance and safety of a component than others. For example, surface-breaking transverse cracks in pressure vessel components can be particularly critical since they can rapidly propagate under service loading and can lead to catastrophic failure if not detected and remedied in a timely manner [2].Inspection techniques used to detect and monitor defects in nuclear power plant components are continually evolving. Inspection methods have traditionally included visual examination, ultrasonics, radiography, and eddy current testing [3]. These techniques have proven reliable and effective, but have limitations such as the inability to inspect certain materials and geometries. In addition, advances in materials science and technology have led to the development of new materials with different physical and chemical properties that may not be well-suited to traditional inspection techniques. Therefore, there is a need to develop and optimize inspection techniques that are capable of detecting andmonitoring defects in advanced materials and structures.1.2 Objectives and ScopeThe primary objective of this chapter is to provide an overview of the different types of inspection techniques that are currently used in the nuclearpower industry for detecting, characterizing, and monitoring defects in materials and components. The chapter will discuss the limitations of current inspection techniques and the challenges associated with the inspection of advanced materials and structures. The chapter will also highlight recent developments in inspection techniques including the use of advanced sensors, imaging, and data analysis techniques.The scope of the chapter will cover a range of inspection techniques used in the nuclear power industry including visual examination, ultrasonics, radiography, eddy current testing, and other techniques such as thermography and acoustic emission testing. The chapter will focus on the application of these techniques to welds, pressure vessels, steam generators, and reactor components. The chapter will also briefly discuss the use of inspection techniques for other applications such as monitoring corrosion and degradation of materials.1.3 Organization of the ChapterThe remainder of this chapter is organized as follows. Section 2 provides an overview of visual examination and its application to the inspection of nuclear power plant components. Section 3 describes ultrasonic inspection techniques and their use in detecting and characterizing defects in materials and components.Section 4 discusses radiography and its use forimaging defects in materials. Section 5 covers eddy current testing and its application to the detectionof surface and subsurface defects. Section 6 provides an overview of other non-destructive evaluation techniques such as thermography and acoustic emission testing. Section 7 summarizes recent developments in inspection techniques including the use of advanced sensors and imaging techniques. Section 8 concludesthe chapter with a discussion of challenges and future directions in inspection technology for nuclear power plant components.中文翻译:第一章绪论1.1 背景核能已经为全球电力供应提供了半个多世纪的重要部分。
化学工程 油气运输 外文翻译 外文文献 英文文献
毕业设计(论文)外文翻译毕业设计(论文)题目:关于加油站及油罐车的油气回收外文翻译(一)题目:Mechanical Degradation and Changes in Conformation ofHydrophobically Modified StarchOSA改性淀粉的机械降解和结构变化外文翻译(二)题目:Preparation and Properties of Octenyl Succinic AnhydrideModified Early Indica Rice Starch辛烯基丁二酸酐(OSA)改性早籼淀粉的制备和性能低成本和高可靠的喷射压缩机采用油气回收领域,以解决生态问题,在开发节能技术。
一定的技术困难,但是,这个操作复杂设备在最佳条件下,即:有效的参数范围狭窄喷气熟悉设计压缩机遇到喷射压缩机启动和稳定运行的复杂性液体收益访问接收室。
血压波动也使自己感到液体喷射压缩机的运作产生负面影响。
在同时,压力和流量的变化是恢复,积累就业的运作系统的特点,石油和天然气的加工。
在这方面,要研究液体喷射压缩机的操作下变条件,包括该设备的监管。
OAO跟Orenburgneft “液体喷射压缩机的设计,开发与双流量喷嘴集结合可调驱动电源泵,使人们有可能以不同的尺寸和无量纲特征喷射装置。
液体喷射压缩机的实验研究进行了在一条长凳上安装的IM Gubkin俄罗斯石油和天然气的州立大学。
在这些调查过程中,添置介绍了液体喷射压缩机相似理论[1]。
喷射压缩机的基本组件如下:- 直接流喷嘴组,以确保工作液喷射形成与调节的可能性射流压缩部分,科里奥利和Boussienesq系数的直径;- 一个环形接收室的入口和出口之间的部分,以确保交付的介质转移到工作液喷射;- 在第一套可互换组件(不同的入口和出口之间的混合室内部的直径和长度),确保工作与正在传输介质液体混合,- 扩散器与一组可互换组件(不同的入口部分的内部直径),从而确保在气液混合物的流速减少。
最新化工专业英语翻译(全21单元)01620资料
化学工程与工艺专业英语课文翻译Unit 1 Chemical Industry化学工业 ...................................................................................... - 1 -Unit 2 Research and Development研究和开发................................................................... - 3 -Unit 3 Typical Activities of Chemical Engineers化学工程师的例行工作............................ - 5 -Unit 4 Sources of Chemicals化学资源 ................................................................................. - 7 -Unit 5 Basic Chemicals基本化学品...................................................................................... - 9 -Unit 6 Chlor-Alkali and Related Processes氯碱及其相关过程.......................................... - 10 -Unit 7 Ammonia, Nitric Acid and Urea氯、硝酸和尿素 ................................................... - 12 -Unit 8 Petroleum Processing石油加工 .............................................................................. - 15 -Unit 9 Polymers 聚合物 ................................................................................................... - 16 -Unit 10 What Is Chemical Engineering?什么是化学工程学 .............................................. - 18 -Unit 11 Chemical and Process Thermodynamics化工热力学 ........................................... - 21 -Unit 12 What do we mean by transport phenomena ?如何定义传递现象 ...................... - 23 -Unit 13 Unit Operations in Chemical Engineering化学工程中的单元操作...................... - 24 -Unit14 Distillation蒸馏....................................................................................................... - 26 -Unit 15 Solvent Extraction, Leaching and Adsorption溶剂萃取,浸取和吸附................ - 28 -Unit 16 Evaporation, Crystallization and Drying蒸发、结晶和干燥................................. - 31 -Unit 17 Chemical Reaction Engineering化学反应工程 ..................................................... - 33 -Unit18 Chemical Engineering Modeling化工建模 ............................................................. - 36 -Unit 19 Introduction to Process Design过程设计简介...................................................... - 37 -Unit 20 Material Science and Chemical Engineer材料科学和化学工程........................... - 39 -Unit 21 Chemical Industry and Environment化学工业与环境 ......................................... - 42 -Unit 1 Chemical Industry化学工业1.化学工业的起源尽管化学品的使用可以追溯到古代文明时代,我们所谓的现代化学工业的发展却是非常近代(才开始的)。
化工专业及其材料的英语翻译
化工专业及其材料的英语翻译化工专业及其材料的英语翻译篇一:化工翻译Unit 1Chemical Industry化学工业1.化学工业的起源尽管化学品的使用可以追溯到古代文明时代,我们所谓的现代化学工业的发展却是非常近代(才开始的)。
可以认为它起源于工业革命其间,大约在1800年,并发展成为为其它工业部门提供化学原料的产业。
比如制肥皂所用的碱,棉布生产所用的漂白*,玻璃制造业所用的硅及Na2CO3. 我们会注意到所有这些都是无机物。
有机化学工业的开始是在十九世纪六十年代以William Hey Perkin 发现第一种合成染料—苯胺紫并加以开发利用为标志的。
20世纪初,德国花费大量资金用于实用化学方面的重点研究,到1914年,德国的化学工业在世界化学产品市场上占有75%的份额。
这要归因于新染料的发现以及硫酸的接触法生产和氨的哈伯生产工艺的发展。
而后者需要较大的技术突破使得化学反应第一次可以在非常高的压力条件下进行。
这方面所取得的对德国很有帮助。
特别是由于1914年第一次世界大仗的爆发,对以氮为基础的化合物的需求飞速增长。
这种深刻的改变一直持续到战后(1918-1939)。
1940年以来,化学工业一直以引人注目的速度飞速发展。
尽管这种发展的速度近年来已大大减慢。
化学工业的发展由于1950年以来石油化学领域的研究和开发大部分在有机化学方面取得。
石油化工在60年代和70年代的迅猛发展主要是由于人们对于合成高聚物如聚乙烯、聚丙烯、尼龙、聚脂和环氧树脂的需求巨大增加。
今天的化学工业已经是制造业中有着许多分支的部门,并且在制造业中起着核心的作用。
它生产了数千种不同的化学产品,而人们通常只接触到终端产品或消费品。
这些产品被购买是因为他们具有某些性质适合(人们)的一些特别的用途,例如,用于盆的不粘涂层或一种杀虫剂。
这些化学产品归根到底是由于它们能产生的作用而被购买的。
2.化学工业的定义在本世纪初,要定义是化学工业是不太困难的,因为那时所生产的化学品是很有限的,而且是非常清楚的化学品,例如,烧碱,硫酸。
- 1、下载文档前请自行甄别文档内容的完整性,平台不提供额外的编辑、内容补充、找答案等附加服务。
- 2、"仅部分预览"的文档,不可在线预览部分如存在完整性等问题,可反馈申请退款(可完整预览的文档不适用该条件!)。
- 3、如文档侵犯您的权益,请联系客服反馈,我们会尽快为您处理(人工客服工作时间:9:00-18:30)。
XXXX大学本科毕业设计(论文)外文翻译原文:Chemical Industry1.Origins of the Chemical IndustryAlthough the use of chemicals dates back to the ancient civilizations, the evolution of what we know as the modern chemical industry started much more recently. It may be considered to have begun during the Industrial Revolution, about 1800, and developed to provide chemicals roe use by other industries. Examples are alkali for soapmaking, bleaching powder for cotton, and silica and sodium carbonate for glassmaking. It will be noted that these are all inorganic chemicals. The organic chemicals industry started in the 1860s with the exploitation of William Henry Perkin’s discovery if the first synthetic dyestuff—mauve. At the start of the twentieth century the emphasis on research on the applied aspects of chemistry in Germany had paid off handsomely, and by 1914 had resulted in the German chemical industry having 75% of the world market in chemicals. This was based on the discovery of new dyestuffs plus the development of both the contact process for sulphuric acid and the Haber process for ammonia. The later required a major technological breakthrough that of being able to carry out chemical reactions under conditions of very high pressure for the first time. The experience gained with this was to stand Germany in good stead, particularly with the rapidly increased demand for nitrogen-based compounds (ammonium salts for fertilizers and nitric acid for explosives manufacture) with the outbreak of world warⅠin 1914. This initiated profound changes which continued during the inter-war years (1918-1939).Since 1940 the chemical industry has grown at a remarkable rate, although this has slowed significantly in recent years. The lion’s share of this growth has been in the organic chemicals sector due to the development and growth of the petrochemicals area since 1950s. The explosives growth in petrochemicals in the 1960s and 1970s was largely due to the enormous increase in demand for synthetic polymers such as polyethylene, polypropylene, nylon, polyesters and epoxy resins.The chemical industry today is a very diverse sector of manufacturing industry, within which it plays a central role. It makes thousands of different chemicals which the general public only usually encounter as end or consumer products. These products are purchased because they have the required properties which make them suitable for some particular application, e.g. a non-stick coating for pans or a weedkiller. Thus chemicals are ultimately sold for the effects that they produce.2. Definition of the Chemical IndustryAt the turn of the century there would have been little difficulty in defining what constituted the chemical industry since only a very limited range of products was manufactured and these were clearly chemicals, e.g., alkali, sulphuric acid. At present, however, many intermediates to productsproduced, from raw materials like crude oil through (in some cases) many intermediates to products which may be used directly as consumer goods, or readily converted into them. The difficulty cones in deciding at which point in this sequence the particular operation ceases to be part of the chemical industry’s sphere of activities. To consider a specific example to illustrate this dilemma, emulsion paints may contain poly (vinyl chloride) / poly (vinyl acetate). Clearly, synthesis of vinyl chloride (or acetate) and its polymerization are chemical activities. However, if formulation and mixing of the paint, including the polymer, is carried out by a branch of the multinational chemical company which manufactured the ingredients, is this still part of the chemical industry of does it mow belong in the decorating industry?It is therefore apparent that, because of its diversity of operations and close links in many areas with other industries, there is no simple definition of the chemical industry. Instead each official body which collects and publishes statistics on manufacturing industry will have its definition as to which operations are classified as the chemical industry. It is important to bear this in mind when comparing statistical information which is derived from several sources.3. The Need for Chemical IndustryThe chemical industry is concerned with converting raw materials, such as crude oil, firstly into chemical intermediates and then into a tremendous variety of other chemicals. These are then used to produce consumer products, which make our lives more comfortable or, in some cases such as pharmaceutical produces, help to maintain our well-being or even life itself. At each stage of these operations value is added to the produce and provided this added exceeds the raw material plus processing costs then a profit will be made on the operation. It is the aim of chemical industry to achieve this.It may seem strange in textbook this on e to pose the question ―do we need a chemical industry?‖ However trying to answer this question will provide(ⅰ) an indication of the range of the chemical industry’s activities, (ⅱ) its influence on our lives in everyday terms, and (ⅲ) how great is society’s need for a chemical industry. Our approach in answering the question will be to consider the industry’s co ntribution to meeting and satisfying our major needs. What are these? Clearly food (and drink) and health are paramount. Other which we shall consider in their turn are clothing and (briefly) shelter, leisure and transport.(1)Food. The chemical industry makes a major contribution to food production in at least three ways. Firstly, by making available large quantities of artificial fertilizers which are used to replace the elements (mainly nitrogen, phosphorus and potassium) which are removed as nutrients by the growing crops during modern intensive farming. Secondly, by manufacturing crop protection chemicals, i.e., pesticides, which markedly reduce the proportion of the crops consumed by pests. Thirdly, byproducing veterinary products which protect livestock from disease or cure their infections.(2)Health. We are all aware of the major contribution which the pharmaceutical sector of the industry has made to help keep us all healthy, e.g. by curing bacterial infections with antibiotics, and even extending life itself, e.g. ß–blockers to lower blood pressure.(3)Clothing. The improvement in properties of modern synthetic fibers over the traditional clothing materials (e.g. cotton and wool) has been quite remarkable. Thus shirts, dresses and suits made from polyesters like Terylene and polyamides like Nylon are crease-resistant, machine-washable, and drip-dry or non-iron. They are also cheaper than natural materials.Parallel developments in the discovery of modern synthetic dyes and the technology to ―bond‖ th em to the fiber has resulted in a tremendous increase in the variety of colors available to the fashion designer. Indeed they now span almost every color and hue of the visible spectrum. Indeed if a suitable shade is not available, structural modification of an existing dye to achieve this can readily be carried out, provided there is a satisfactory market for the product. Other major advances in this sphere have been in color-fastness,i.e., resistance to the dye being washed out when the garment is cleaned.(4)Shelter, leisure and transport. In terms of shelter the contribution of modern synthetic polymers has been substantial. Plastics are tending to replace traditional building materials like wood because they are lighter, maintenance-free (i.e. they are resistant to weathering and do not need painting). Other polymers, e.g. urea-formaldehyde and polyurethanes, are important insulating materials f or reducing heat losses and hence reducing energy usage.Plastics and polymers have made a considerable impact on leisure activities with applications ranging from all-weather artificial surfaces for athletic tracks, football pitches and tennis courts to nylon strings for racquets and items like golf balls and footballs made entirely from synthetic materials.Likewise the chemical industry’s contribution to transport over the years has led to major improvements. Thus development of improved additives like anti-oxidants and viscosity index improves for engine oil has enabled routine servicing intervals to increase from 3000 to 6000 to 12000 miles. Research and development work has also resulted in improved lubricating oils and greases, and better brake fluids. Yet again the contribution of polymers and plastics has been very striking with the proportion of the total automobile derived from these materials—dashboard, steering wheel, seat padding and covering etc.—now exceeding 40%.So it is quite apparent even from a brief look at the chemical industry’s contribution to meeting our major needs that life in the world would be very different without the products of the industry. Indeed the level of a country’s development may be judged by the production level and sophistication of its chemical industry4. Research and Development (R&D) in Chemical IndustriesOne of the main reasons for the rapid growth of the chemical industry in the developed world has been its great commitment to, and investment in research and development (R&D). A typical figure is 5% of sales income, with this figure being almost doubled for the most research intensive sector, pharmaceuticals. It is important to emphasize that we are quoting percentages here not of profits but of sales income, i.e. the total money received, which has to pay for raw materials, overheads, staff salaries, etc. as well. In the past this tremendous investment has paid off well, leading to many useful and valuable products being introduced to the market. Examples include synthetic polymers like nylons and polyesters, and drugs and pesticides. Although the number of new products introduced to the market has declined significantly in recent years, and in times of recession the research department is usually one of the first to suffer cutbacks, the commitment to R&D remains at a very high level.The chemical industry is a very high technology industry which takes full advantage of the latest advances in electronics and engineering. Computers are very widely used for all sorts of applications, from automatic control of chemical plants, to molecular modeling of structures of new compounds, to the control of analytical instruments in the laboratory.Individual manufacturing plants have capacities ranging from just a few tones per year in the fine chemicals area to the real giants in the fertilizer and petrochemical sectors which range up to 500,000 tonnes. The latter requires enormous capital investment, since a single plant of this size can now cost $520 million! This, coupled with the widespread use of automatic control equipment, helps to explain why the chemical industry is capital-rather than labor-intensive.The major chemical companies are truly multinational and operate their sales and marketing activities in most of the countries of the world, and they also have manufacturing units in a number of countries. This international outlook for operations, or globalization, is a growing trend within the chemical industry, with companies expanding their activities either by erecting manufacturing units in other countries or by taking over companies which are already operating there.。