连铸主要设备介绍共49页
连铸机设备PPT幻灯片课件
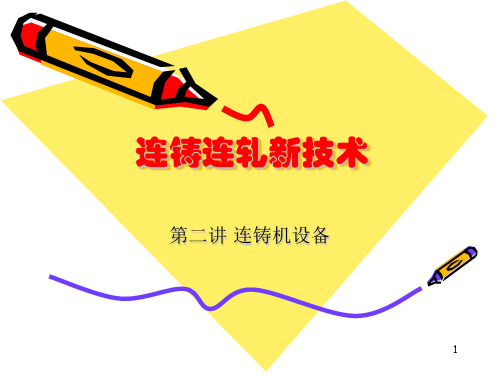
长水口又称保护套管,用于钢包与中间包之间保护 注流不被二次氧化,同时也避免了注流的吸气、飞溅以 及敞开浇注的卷渣问题。
图2-4 长水口保护装置 (a)卡口型;(b)液压型;(c)叉型 1一钢包;2一氩气;3~钢水;4一中间包;5一浇注位置
19
钢包回转台
图2-5 钢包回转台 (a)直臂式;(b)双臂单独升降式;(c)带钢包加盖功能 钢包回转台是现代连铸中应用最普遍的运载和承托钢包进行浇 注的设备,通常设置于钢水接受跨与浇注跨柱列线之间。钢包回转 台能够在转臂上同时承放两个钢包,一个用于浇注,另一个处于待 浇状态。
2
2.1.2 弧形、椭圆形连铸机的表示方法
连铸机的规Leabharlann 表示如下: aRb—c这里:a——机数,若其数为1,则可省略; R——机型为弧形或椭圆形连铸机; b——连铸机的圆弧半径,m;若椭圆形连铸机
为多个半径之乘积,也标志可浇铸坯 的最大厚度; c ——表示拉辊坯辊身长度,mm,它标志着连
铸机可容纳的连铸坯的最大宽度。 B=C-(150~200)mm
1一钢包注流位置;2一中间包水口位置;3一挡渣墙
21
中间包车结构有哪些特点?
中间包车是承载和运送中间包的特殊车辆,根据工艺操作要求,中间包车 必须具备如下功能:
(1)将中间包由预热位置移到浇钢位置上,在浇钢结束后还应移出浇钢位置, 因此中间包车应具有运行功能; 。
(2)在安放中间包时,首先将中间包提起,使水口离开结晶器盖一定高度后 再进入浇钢位置,下降中间包,使水口对准结晶器中心,因此它应具有升降和 微调功能;
内壁之间的滑动摩擦,因此结晶器内壁的材质应有良好的耐磨性和较高的再结晶 温度。 (5)重量要轻,以减少振动时的惯性力。为提高铸坯表面质量,结晶器的振动广 泛采用高频率小振幅,最高已达4 00次/min,在高频振动时惯性力不可忽视, 过大的惯性力不仅影响到结晶器的强度和刚度,进而也影响到结晶器运动轨迹的 精度。
连铸生产安全技术-设备篇

1-连续铸钢简介
弧形连铸机
是世界各国应用最多的一种机型。弧形连铸
机的结晶器、二次冷却段夹辊、拉坯矫直机 等设备均布臵在同一半径的1/4圆周弧线上; 铸坯在1/4圆周弧线内完全凝固,经水平切线 处被一点矫直,而后切成定尺,从水平方向 出坯。弧形连铸机的高度比立弯式连铸机又 降低了许多,仅为立弯式连铸机的1/3,因而 基建投资减少了。
1-连续铸钢简介
5.2 铸坯断面的尺寸规格
小方坯:70×70~200×200mm2; 大方坯:200×200~450×450mm2; 矩形坯:150×100~400×560mm2; 板坯: 圆坯: 150×600~300×2640mm2; φ80mm~φ450mm。
1-连续铸钢简介
5.3 拉坯速度(浇铸速度)
1-连续铸钢简介
多点弯曲、多点矫直连铸机机型示意图
1-连续铸钢简介
椭圆形连铸机
结晶器、二次冷却段夹辊、拉坯矫直机均布臵在 1/4椭圆圆弧线上。椭圆形圆弧是由多个半径的圆 弧线组成,其基本特点与全弧形连铸机相同。它又 进一步降低了连铸机和厂房的高度。可为低头和超 低头连铸机。
低头或超低头连铸机的机型是根据连铸机高度(H) 与铸坯厚度(D)之比确定的。连铸机高度是指从结 晶器液面到出坯辊道表面的垂直高度。H/D=25-40 时,成为低头连铸机;H/D<25时,则称为超低头连 铸机。
1-连续铸钢简介
60年代弧形铸机引发的革命
采用了弧形连铸机后,连铸技术的应用才实现了一次 真正的突破,不仅提供了生产率,降低了设备投资,而且 更有利于安装在原有的钢厂内。 1952 年德国人欧 . 萨波尔提出弧形连铸机的概念,瑞 士冯 . 莫斯于 1956 年也申请了同一思路的弧形连铸机专利。 1960年中国的徐宝教授也设计了一台浇 200mm×200mm方坯 的弧形铸机。最先把弧形结晶器连铸机的设想付诸工业性 试验的却是德国曼内斯曼公司。 从全球来看,到本世纪60年代末,铸机总数已达200 多台,尽管总的设备能力已近5000万t/a,但实际上连铸钢 的产量只有2600万t/a。
连续铸造原理和连铸设备简介(PDF 28页)
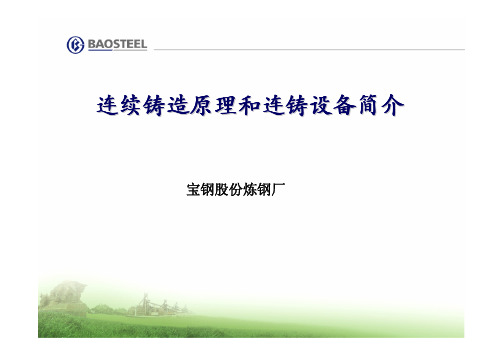
宽度可调结晶器
�小辊密排 �二冷宽向无级调节
扇形段装置
扇形段更换装置
中间包预热
中间包车 自动加渣 引锭杆系统
液压振动
结晶器液面控制 幅切气雾冷却
扇型段轻压下
一连铸概况
一次火焰切割机
一次火焰切割机
去毛刺机
去毛刺机
喷印机
铸坯管理辊道 精整区辊道
推钢机/堆垛机
局部清理机
手清
宽厚板厂
2050热轧
外供
宝钢连铸采用的新技术
2#-8#扇形段:280 min 9#-14#扇形段:220min 15#-17#扇形段:150min 单流驱动电机总功率:209KW
300t转炉
一连铸概况
中间包预热
中间包车 自动加渣 引锭杆系统
液压振动
结晶器液面控制 幅切气雾冷却
扇型段轻压下
LF/RH/KIP/CAS 钢包回转台 中间包
宽度可调结晶器
连续铸造原理和连铸设备简介
宝钢股份炼钢厂
连续铸造原理
一连铸概况
一连铸现装备三台二机二流大型板坯连铸机,2010年实现 年产合格铸坯750万吨。从钢包回转台接受钢水一直到把板坯送 到与轧钢厂的交接点为止的整个连铸过程,已经实现了由计算 机全程控制。
连铸主要工艺
钢包到达 回转台
钢包开浇 流入中间包
炼钢厂连铸设备简介
炼钢厂连铸设备简介
中间包
参数 走行形式
铸机
升降形式
水口形式
SN快换 机构
拖链形式
等离子 设备
长水口 机械手
中间包 形式
中间包 额定 容量
称量 精度
1CC
电机-减 速机
涡轮千斤顶
13.2 连铸机的主要设备
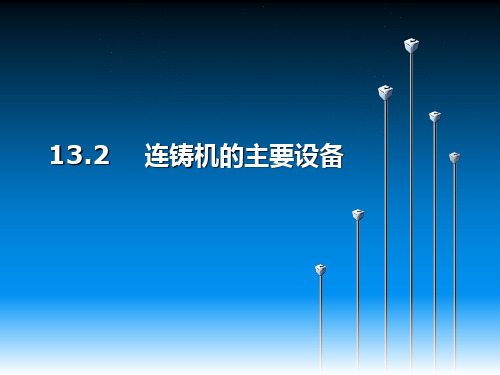
Your company slogan
13.2.1
连铸机的基本参数
13.2.1.1 弧形连铸机规格表示方法 弧形连铸机规格表示方法为:aRb-C 其中 a—组成1台铸机的机数,机数为1时可以省略; R—机型为弧形或圆形连铸机; b—连铸机的圆弧半径(m),若椭圆形铸机为多个半径之乘积,也 示 表示可浇铸坯的最大厚度:坯厚= b/(30~36) mm C—表示铸机拉坯辊辊身长度,mm,还表示可容纳铸坯的最大宽度 : 坯宽=C—(150~200) mm 13.2.1.2 铸坯断面尺寸规格 铸坯断面尺寸是确定连铸机的依据。由于成材需要,铸坯断面形状和尺才也不同。目 前已生产的连铸坯形状和尺寸范围如下: 小方坯:70×70~200×200mm2; 大方坯: 200×200~450×450mm2;
Your company slogan
13.2.2
钢包
钢包又称为大包,是用于盛放钢液并进行精练和浇铸的容器。钢包的容量应 与炼钢炉的最大出钢量相匹配。钢包由外壳、内衬和注流控制机构三部分组成。 钢包内衬一般由保温层、永久层和工作层组成。内衬耐火材料的选择对改善钢 的质量、稳定操作、提高生产率有着重要的意义。钢包使用前必须经过充分烘烤
13.2.3
中间包
中间包的结构应具有最小的散热面积,良 好的保温性能。一般常用的中间包断面形状 为圆形、椭圆形、三角形、矩形和”T”字 形等。中间包内衬是由保温层、永久层和工 作层组成。保温层紧贴包壳钢板,以减少散 热,一般可用石棉板、保温砖或轻质挠注料 砌筑。永久层与钢液直接接触,可用高铝砖 、镁质砖砌筑,也可用硅质绝热板、镁质绝 热板或镁橄榄石质绝热板组装砌筑。 中间包没有包盖,目的在于保温和保护 钢包包底不致过分受烤而变形。在包盖上开 有注入孔和塞棒孔。水口直径应根据连铸机 在最大拉速时所需的钢液流量来确定。水口 直径可由下式计算确定:
连铸主要设备介绍

RH示意图
(五)VOD真空吹氧脱碳法炉 VOD法(Vacuum Oxygen Decarburization)称为真空吹氧脱碳法, 它是1965年由德国维腾公司开发出的技术。 VOD设备与VD设备的构成基本相同,主要 的区别在于VOD法增加了氧枪及其升降系 统、供氧系统。
真空循环脱气的工作原理:当两个插入管 插入钢液一定深度时,启动真空泵,真空 室被抽成真空,由于内外压力差,钢液上 升一定高度;与此同时上升管输入驱动气 体(氩气),受热膨胀,引起等温膨胀, 钢液与气体混合比重降低,驱动钢液项喷 泉一样涌入真空室,使真空室的平衡破坏, 为保持平衡,一部分钢液从下降管回到钢 包中,就这样在钢水压力差和驱动气体的 作用下不断地从上升管涌入真空室,并经 过下降管回落到钢包内,周而复始的实现 钢液循环,从而通过造渣净化钢液。
(二)双流板坯连铸机的主要平台及设备 主要设备由钢包回转台、中间包(车)、结晶器、结晶 器振动装置、二次冷却和铸坯导向装置、拉坯矫直装置、 切割装置、出坯装置等部分组成
连铸机横向布置示意图 1—操作台,2—转炉;3—铸锭 设备;4—连铸机 5—铸坯运行辊道;6—大包转 台
1、浇注平台及二冷室(功能及结构)
8、钢包长水口操作机构 功能及结构: 长水口操作机构用于钢包长口的安装,操 作过程手动完成。把长水口接到钢包滑动 水口下端后,由液压缸压紧。为避免吸入 空气,长水口将接上Ar气。 长水口操作机构位于长水口操作平台上, 并有一个保护罩以防钢水喷溅。 液压动力来源是铸机主液压系统。
连铸设备介绍
一、浇注跨的布置形式 分为:横向布置、纵向布置及靠近轧钢车间布置等几种形式 1、横向布置:横向布置是指连铸机的中心线与厂房纵向柱列 线相垂直的布置形式,我厂主厂房有 、原料跨、转炉跨、分配 跨(钢水及炉外精炼跨)、浇铸跨、出坯跨、成品跨多个跨间 平行布置。而连铸机的摆布采用的就是这种横向布置方式。
连铸的主要设备的组成
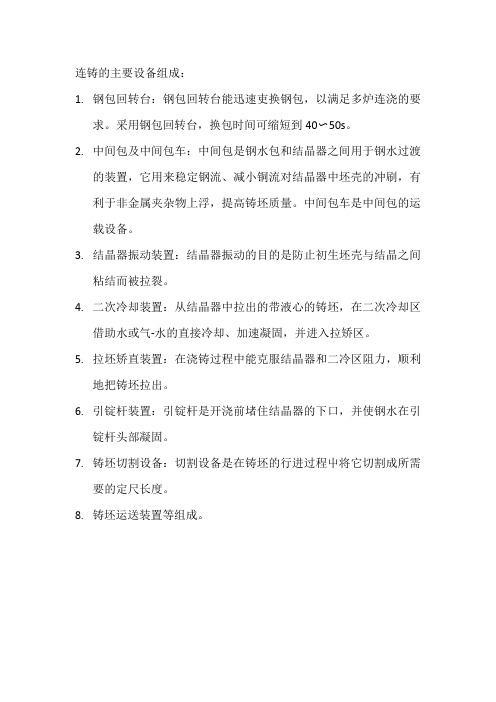
连铸的主要设备组成:
1.钢包回转台:钢包回转台能迅速吏换钢包,以满足多炉连浇的要
求。
采用钢包回转台,换包时间可缩短到40〜50s。
2.中间包及中间包车:中间包是钢水包和结晶器之间用于钢水过渡
的装置,它用来稳定钢流、减小铜流对结晶器中坯壳的冲刷,有利于非金属夹杂物上浮,提高铸坯质量。
中间包车是中间包的运载设备。
3.结晶器振动装置:结晶器振动的目的是防止初生坯壳与结晶之间
粘结而被拉裂。
4.二次冷却装置:从结晶器中拉出的带液心的铸坯,在二次冷却区
借助水或气-水的直接冷却、加速凝固,并进入拉矫区。
5.拉坯矫直装置:在浇铸过程中能克服结晶器和二冷区阻力,顺利
地把铸坯拉出。
6.引锭杆装置:引锭杆是开浇前堵住结晶器的下口,并使钢水在引
锭杆头部凝固。
7.铸坯切割设备:切割设备是在铸坯的行进过程屮将它切割成所需
要的定尺长度。
8.铸坯运送装置等组成。
连续铸造原理和连铸设备简介
连续铸造原理和连铸设备简介连续铸造设备主要包括连铸机、送丝装置、拉拔机、冷却设备等组成。
连铸机是整个连续铸造线的核心设备,它包括浇注部分和凝固部分。
浇注部分通过浇注头将熔化金属浇注到冷却结晶器中,使得熔化金属得到成型。
凝固部分则是通过在凝固过程中对金属坯料进行冷却处理,使得金属坯料在不断移动的过程中逐渐凝固成型。
送丝装置和拉拔机是用来控制金属坯料的尺寸和形状的关键装置。
送丝装置通过控制坯料的拉丝速度和张力,使得坯料能够在凝固过程中得到适当的形状和尺寸。
拉拔机则是用来拉拔和整形坯料,从而使得金属坯料得到精确的尺寸和形状。
最后,冷却设备是用来对金属坯料进行冷却处理的设备。
通过控制冷却设备的参数,可以使得坯料在凝固过程中能够得到适当的温度和结晶结构,从而保证产品质量。
总的来说,连续铸造设备通过不断地控制和调整熔炼金属的流动和凝固过程,使得金属坯料能够在连续铸造过程中得到高质量的产品。
这种生产方式不仅提高了生产效率,降低了能耗成本,还能够获得更加均匀的产品质量,因此在金属加工行业得到了广泛的应用。
很高兴继续介绍连续铸造的相关内容。
连续铸造设备是现代工业领域中一个重要的技术装备,它广泛应用于钢铁、铝合金、铜合金等金属材料的生产中。
通过连续铸造设备,工厂可以实现高效、精确的生产过程,满足市场对于高质量金属坯料的需求。
在连续铸造的过程中,关键的一环是冷却设备。
冷却设备的设计和操作对于金属坯料的凝固过程至关重要。
凝固速率的控制能够对金属晶粒的尺寸和分布进行调节,进而对产品的力学性能和内部组织进行精确控制。
冷却设备的设计也需要考虑如何降低能耗和提高运行效率,同时保证产品质量。
一些先进的连续铸造设备还配备了智能控制系统,可以实时监测和调整坯料的凝固过程,从而提高产量和坯料质量。
与传统的间歇铸造相比,连续铸造设备具有很高的生产率和效率。
通过连续铸造,金属坯料可以实现自动化和连续化的生产过程,降低了生产周期和人工成本。
连铸设备
连续铸造: 是将液态金属通过连铸机浇铸、凝固成形、切割,直接得到铸坯的新工艺、新技术。
3.1 连续铸造的分类按台、机、流分: ?台钢包;?铸机驱动系统(机);?流按结晶器类型分: 固定式、随动式按连铸机型分: 立式连铸、立弯式连铸、直结晶器立弯式、结晶器弧形、全弧形连铸、多半径椭圆形连铸、水平连铸、轮带式连铸、履带式连铸等.按铸坯弯曲矫直方式分: 单点矫直连铸机、多点弯矫连铸、连续弯矫连铸(又分固定辊和浮动辊两类)、渐进矫直连铸(又称固定辊连续矫直连铸)等按铸造材料分: 连续铸钢、连续铸铝、连续铸镁等. 特殊钢连铸、不锈钢板坯(方坯)连铸、合金钢板坯(方坯)连铸等.按所浇铸的断面形状分: 板坯连铸、带坯连铸、小方坯连铸、大方坯连铸、圆坯连铸、异型(如,工字形、八角形)断面坯连铸、板方坯兼容连铸(板方坯复合连铸).按照铸坯厚度分:常规板坯连铸<150mm.中厚度板坯连铸90~150mm;薄板坯连铸40~70(90)mm; 带坯连铸~25mm;薄带连铸~10mm;极薄带连铸<3mm,最薄可达0.15~0.3mm.按是否接近最终产品形状分: 传统连铸、近终形连铸.3.2.1 传统连铸的一般过程钢包、中间包、结晶器(一次冷却)、结晶器振动装置、二次冷却和铸坯导向装置、拉坯矫直装置、切割装置、出坯装置等组成.钢水→钢包(二次精炼)→中间包→打开塞棒或滑动水口(或定径水口)→水冷结晶器(引锭杆头封堵)→凝成钢壳→启动拉坯机和结晶器振动装置→带液芯铸坯进入弧形导向段→喷水强制冷却→矫直→切割→出坯.3.2.2 浇铸设备钢包、钢包回转台、中间包、中间包车.3.3 连铸连轧设备近终形连铸: 薄板坯/薄带连铸技术、薄带铸轧技术、异型坯连铸技术等. 连铸连轧(CC-DR, Continuous Casting and Direct Rolling): 在连铸机拉辊位置安装了低速水平轧机和立式轧机,组成连轧机组. 铸坯通过拉矫区后,经在线加热,进入连轧机组轧成型材.3.4.2 浇铸系统前箱、横浇道、供料嘴、分流块等组成. 输送液体金属进入铸轧辊.3.4.2.1 流槽引导金属液由静置炉到前箱的保温通道.。
连铸三大件的生产与应用PPT课件
01 03 04 02
二 三大件产品设计
与生产
➢ 三大件产品的设计
➢ 三大件产品的生产
第10页/共52页
塞棒设计
棒身设计: 棒身设计考虑安全与安装等因素。塞棒整体壁厚要求大
于40mm,渣线处不小于50mm,如果是采用碳素丝堵的在 丝堵处壁厚要求不小于30mm。
塞棒棒尾A、B段的设计,塞棒棒尾有两段,一段是直段 A,作用是保证丝堵附近有较高的强度,另一段是斜段B,作 用是保证渣线厚度。
4还需注意现场竞争对手的破坏如在塞棒内孔中注二掉棒头1热震烘烤问题材料问题2强度过度缺陷3外力烘烤粘连机械碰撞38三棒头粘连39四棒头冲刷1形状4氧含量烧氧2特殊钢种40长水口常见问题热震损毁渣线侵蚀内孔扩孔断裂和穿孔41长水口常见问题一热震损毁日照钢铁包头钢厂42长水口常见问题二渣线侵蚀湘潭钢厂43长水口常见问题三内孔扩孔湘潭钢厂44长水口常见问题四断裂和穿孔日照钢厂45浸入式水口常见问题变径处穿孔渣线侵蚀穿孔内孔结瘤水口堵塞46浸入式水口常见问题一变径处穿孔47浸入式水口常见问题二渣线侵蚀穿孔穿孔48浸入式水口常见问题宝钢德盛不锈钢49浸入式水口常见问题四内孔结瘤及水口堵塞内孔结瘤浸入式水口堵塞的主要原因是耐火材料中的氧和钢水中的铝发生反应生成高熔点的氧化铝以及耐材中的氧化铝在流经水口分流处容易附着从而导致浸入式水口堵塞
第15页/共52页
浸入式水口设计
侧孔出钢口和渣线设计:
侧孔出钢口经验尺寸: 两个侧孔的截面积应稍大于或等于两倍水口流钢中孔的截面积。
这样钢流稳定,扩径速度缓慢。 侧孔倾角:
对于侧孔的倾角,有水平方向的、向上倾的和向下倾的,倾角在 15~30度。目前向下倾15度的较多。水口侧孔底部的厚度,一般控制 在25~40mm之间。 渣线:
连铸设备教学课件PPT
拉坯速度
• 通常,连铸机冶金长度确定后,铸机可能
达到的最大拉速也就随之确定,拉速和冶
金长度是相互联系、相互制约的。
• 铸机可达到的最大拉速按下式计算:
式中
vmax
K 2Lm
2
vmax: 最大理论拉速,m/min K: 凝固系数,mm ·min-0.5 Lm: 冶金长度,m : 最小坯壳厚度,mm
• 在铸坯内钢水完全凝固之前,上部结构和立式 连铸机相同。
• 在铸坯完全凝固之后,用顶弯设备将铸坯顶弯, 使铸坯在水平方向进行切割和出坯,大大减小 设备总高度
• 小断面(100mm*100mm)铸坯完全凝 固时间短,大断面150mm*150mm以上) 铸坯完全凝固时间长。大断面不适合通过顶弯 降低设备高度。顶弯设备庞大。
• 内外弧冷却强度不一致。所以要合理布 置二冷强度。
设备高度的降低,使得弧形连铸机得到广 泛使用
多点矫直弧形连铸机基本特点
多点矫直弧形连铸机基本特点
• 原理和设备和单点矫直弧形连铸机一样。 • 拉速增加,使得钢水不能在四分之一圆弧内完
全凝固,因此在矫直时,铸坯中心还有钢液液 芯,形成所谓带液芯矫直。 • 单点矫直会导致带液芯矫直时的一次变形量大, 铸坯中心区产生裂纹缺陷。而将一次变形变成 多次变形,可解决这一问题。
• 铸机长度按冶金长度确定,取1.1倍冶金长度。
连铸机总体尺寸(长度)
• 连铸机总长度是指从结晶器外弧线(即 连铸机基准线)至冷床后固定挡板的距 离,与采用的引锭杆型式有关。
• 如图
连铸机总体尺寸(长度)
• L=R十L1十L2+ L3十L4十L5