轴流风机后导叶三维数值优化设计方法及其应用
轴流风机机翼型叶片参数化建模方法
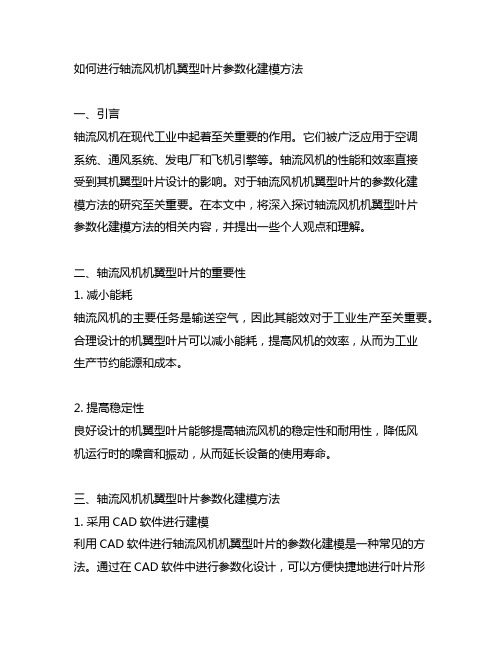
如何进行轴流风机机翼型叶片参数化建模方法一、引言轴流风机在现代工业中起着至关重要的作用。
它们被广泛应用于空调系统、通风系统、发电厂和飞机引擎等。
轴流风机的性能和效率直接受到其机翼型叶片设计的影响。
对于轴流风机机翼型叶片的参数化建模方法的研究至关重要。
在本文中,将深入探讨轴流风机机翼型叶片参数化建模方法的相关内容,并提出一些个人观点和理解。
二、轴流风机机翼型叶片的重要性1. 减小能耗轴流风机的主要任务是输送空气,因此其能效对于工业生产至关重要。
合理设计的机翼型叶片可以减小能耗,提高风机的效率,从而为工业生产节约能源和成本。
2. 提高稳定性良好设计的机翼型叶片能够提高轴流风机的稳定性和耐用性,降低风机运行时的噪音和振动,从而延长设备的使用寿命。
三、轴流风机机翼型叶片参数化建模方法1. 采用CAD软件进行建模利用CAD软件进行轴流风机机翼型叶片的参数化建模是一种常见的方法。
通过在CAD软件中进行参数化设计,可以方便快捷地进行叶片形状的调整和修改,从而实现机翼型叶片的优化设计。
2. 利用计算流体力学(CFD)进行仿真分析结合计算流体力学(CFD)方法,可以对轴流风机机翼型叶片的流场进行精确模拟和分析,从而优化叶片的形状和结构,提高风机的性能和效率。
3. 基于参数化建模的优化设计通过建立基于参数化建模的优化设计方法,可以对轴流风机机翼型叶片的关键参数进行全面的优化设计,从而实现最佳的风机性能和效率。
四、个人观点和理解在我看来,轴流风机机翼型叶片参数化建模方法的研究对于提高轴流风机的性能和效率至关重要。
通过不断优化设计,可以实现能源的节约和环境的保护。
同时, 研究轴流风机机翼型叶片参数化建模方法也有助于加深对于风机流体力学行为的理解,对于未来的风机设计和改进有着积极的影响。
五、总结和回顾本文深入探讨了轴流风机机翼型叶片参数化建模方法的相关内容,介绍了CAD软件建模、CFD仿真分析和基于参数化建模的优化设计等方法。
轴流风机叶片的设计方法及实例

综 合
的作用�传统的轴流通风机设计方法包括以气动性能 良好的机翼为原始叶型 的孤立叶型设计方法 和基于 二元叶栅理论的叶栅设计法,在上世纪 0 年代出现
了一些基于准三元流动的叶片造型方法�采用上述方 参数, 设计了一款实用新型旨在提 供一种流量大, 全 研 法所设计的通风机叶片比较多的是平面叶片, 虽然工 � � � 压高的 系列变压器轴流通风机, 其中 表示风机 艺简单, 但性能较差�少量的扭曲叶片也大多是由平 � � 叶轮直径为 00 毫米, 表示风机为前吹式�其总体 究 面叶栅叠加而成, 而不是真正的基于全三维造型设计 结构形式由电机, 叶轮, 导流罩, 支架, 机 壳和防护罩 的扭曲叶片, 从而也影响了通风机的 性能, 因 而很难 等 6 部分组成�其特征是电机位于风机的进口端, 电 达到变压器轴流通风机流量大, 全压高的要求� 1. 轴流风机的叶片设计理论 轴流风机设计的核 心就是叶片型线设计 �本文 机轴和 叶轮相连 , 驱动叶轮 旋转, 电 机由支 架支撑, 外面套有导流罩, 导流罩位于风机 的进口端, 为中空 的锥形柱体, 底端面的直径和轮毂 的直径相等, 机壳
根据扭曲叶片理论,采 用全三维造型来进行 叶片流 � � 为直径 0 毫米的圆筒形�在进口端略呈喇叭口状, 型设计, 并结合空气动力学理论, 应用变环量 流型设 以使气流平顺地进入 风机的流道,在风机 的进口端 计方法, 使叶片的做功分布更加符合 运动规律, 从而 发挥出更高的功能转换效益� 首先, 基 于抛物面理论, 我们在柱坐标下 建立叶 片中型面方程: ( - / ) 其中: ( ) ( )/ , 通过参数 , 端面上有防护罩,以 避免杂物进入风机流 道和叶片 发生撞击� 其中的风机叶片 为特殊设计,在设计 过程中采 用了抛物面理论和不 等功原理,对叶片的 流型和流 面进行全三维的造型 设计,得到的叶片为 三维的扭 曲叶片 , 其 特征为 叶片不等 厚, 型面 连续光 滑, 任一 相贯面与型面相割, 得到的相贯线呈流线 形状的机 翼形, 以使得本实用新型具有优良的气动性能� 本实用新型的总体结 构中, 增 加了导流罩部分, 导流罩位于风机的进口端 , 套在电 机的外面, 其作用 是使气流平顺地进入 通风机的流道,从而 提高风机
一种轴流式叶轮的全三维优化设计

( 3 )
式中 , 是 湍流粘性 系数 ; “ “ , 是脉动速度; 湍流动能 ; 是克罗 内克尔 函数 ; 是变形率张量 , 是 公式为 :
一
螺旋线 , 螺旋 角 p: 2 。 叶片 高度 B 一 2 rm, 0, 4 a 叶轮
转 速 叫一 8 0 / n 转 轴直 径 D。 2 mm, 流筒 内径 0 rmi, : 7 导 D = 9 rm。 对 轴 流式 叶 轮 进 行 改 进 , 要 考 虑 叶 2 a 要 需 型、 叶片 数等 参数对 内流场 的 影 响 。 按 以 下 3个 步 骤 可
向力 推动 泥浆 自下 向上 流动 ,冲散沙 粒 。在导 流筒 与 内槽 的环 形 空 间 ,泥 浆 自上 向下流 动 ,形 成循环 流 动 。由试验 发现 ,叶轮 的排 液量 较小 ,未 能有 效地 冲散 沙粒 ,需 要对 轴流 式 叶轮进 行 改进 ,以 改善 叶 轮 的水力 性能 。随着计 算技 术 的 飞速发 展 ,计 算 流体 动力学 ( F C D)已经 可 以深刻 了解 、分 析流体 机械 内
用 的 涡粘性 解析 式 。 些 改进保 证 了 R 这 NGk - 型在 大范 围 的湍流模 拟 中能 有较 高 的精度嘲 。 e模
部的 流动状 况 。运用 C D进行 流体 机 械设计 可 以大 大缩短设 计 周期 、节 省 实验 费用 ,是 C D应 用 的前 F F 沿 L 。笔 者应用 C D方 法 ,通过 数值 模 拟 ,对 该装 置 的 内部 结构 进行 改进 。 1 J F
1 研 究 方 法
轴 流式 叶轮 的有 关 参数 如 下 :叶片 内外缘 轮 廓 为
基于CFD模拟的轴流风机扇叶设计优化研究

基于CFD模拟的轴流风机扇叶设计优化研究摘要:本研究采用计算流体动力学(CFD)模拟方法,旨在优化轴流风机扇叶的设计以提高性能和效率。
通过数值模拟,我们系统地研究了不同扇叶参数对风机性能的影响,并提出了一种优化设计方案,以实现更高的能效和性能。
研究结果表明,通过CFD模拟可以有效地改善轴流风机的性能,并为风机工程领域的进一步发展提供有力支持。
关键词: CFD模拟;轴流风机;扇叶设计;优化;性能一、引言轴流风机作为工业和商业领域中广泛应用的关键设备,对能源效率和性能提出了不断增长的需求。
其中,扇叶作为轴流风机的核心部件,其设计和优化对整个风机系统的性能至关重要。
随着计算流体动力学(CFD)模拟方法的不断发展,研究人员可以更深入地理解风机流场,并进行更精确的性能预测和优化设计。
二、文献综述2.1 轴流风机的发展历程轴流风机作为工业领域的核心设备,其发展历程从19世纪末至今经历了令人瞩目的进步。
早期,轴流风机的设计主要依赖于经验和试验,限制了其性能和效率。
然而,随着科学和工程技术的进步,数学模型、实验室测试和计算流体力学等新方法的应用使轴流风机的设计变得更精确和可预测。
这些技术创新促使了风机的能效提升、噪音降低和寿命延长,从而为各行业带来了更高水平的气流控制和空气处理能力。
2.2 扇叶设计的重要性扇叶作为轴流风机的核心组成部分,其设计对风机性能至关重要。
扇叶的几何形状、叶片数目、叶片角度等参数直接影响风机的效率、噪音产生、能耗和寿命。
一个优化的扇叶设计可以显著提高风机的能效,降低运行成本,减少环境影响。
所以,深入研究和优化扇叶设计是提高轴流风机性能的关键步骤。
近年来,计算流体动力学(CFD)模拟技术的不断发展已经引领了轴流风机研究的新时代。
这一技术的崭新应用为风机工程领域带来了深刻的影响。
通过CFD,研究人员能够以前所未有的准确性模拟轴流风机内部复杂流动现象,如湍流、涡流和分离现象。
这种全面的流场信息为风机性能的深入理解提供了强大工具,并且为设计和优化提供了坚实基础。
管式斜流风机后导叶的数值设计和优化

2 后导叶的数值设计
后导叶雏形的数值设计首先是导叶型 线、叶间轴向距离、叶片数和导叶安装角 等主要参数的确定。由于这是雏形,有些 参数以后还要优化, 所以可以先大致选定。 导叶轴向型线按常规采用为圆弧,相应的 轴向长度为 150mm (参考动叶叶根轴向宽 度为 300mm, 叶顶为 150mm) , 其前缘 (进 口)几何角选为叶轮后来流流动角,由数 值模拟确定,它沿着径向是变化的,但出 口几何角沿径向均为 900,所以导叶径向 是扭曲的。导叶离叶轮后盘轴向距离(即 叶间距离)选为 108 mm,叶片数选为 9 (与动叶数 8 互质) 。 雏形导叶的数值设计 除确定上述参数成型导叶,并合适地安装 在管道中, 完成叶片建模, 其要步骤如下: (1) 确定导叶的进口几何角: 根据无导叶 数值模拟结果的动叶出口轴向距离为
3 导叶优化
导叶优化的主要参数为叶间距离、导 叶型线、安装角、叶片数等。 3.1 叶间距离优化 导叶分别安装在叶间距离为 68mm, 108mm,190mm 处,注意:上述 3 种方案 中,导叶仍为轴向长度 150mm 的圆弧叶 片,但叶片成型时的叶片进口角都是对应 原机无导叶时的来流角,它们随不同叶间 距离位置是不同的,所以导叶成型不同、 安装角也是不同的,但导叶数仍为 9,用
量的壁面静压作为风机出口静压,加上 8.5d 的 管 道 摩 擦 损 失 和 轴 向 平 均 动 压 (10.6Pa)作为风机出口全压,减去风机 进口全压后就是风机全压,它再减去 10.6Pa 就是风机静压,网格试验的计算结 果如表 1 所示。
表 1 网格实验数值模拟结果 (n=1500rpm,Q=6000m /h) 网格数/万 风机全压/pa 全压效率/% 叶轮效率/% 风机静压/pa 静压效率/% 200 505.2 42.7 78.9 494.6 41.8 300 508.6 43.2 78.8 498.0 42.3 377 514.3 43.7 78.7 503.7 42.8
新型舰船轴流风机优化设计(论文)
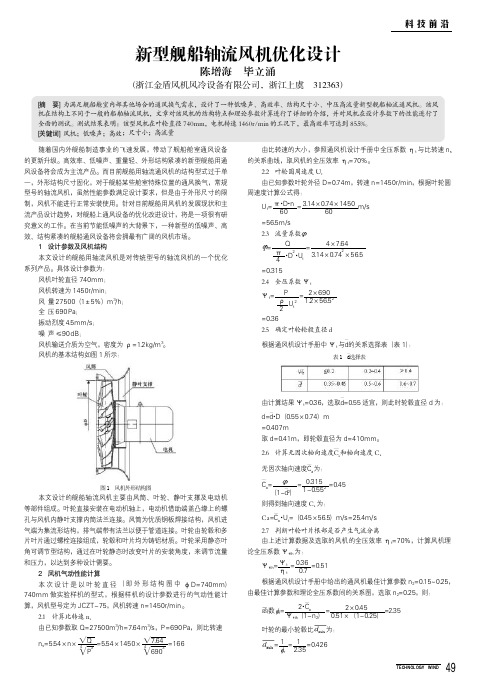
3 主要部件技术要求
3.1 风筒
风机风筒采用优质钢板焊接而成,保证足够的强度。设计过程中采
用先进的 ANSYS10.0 有限元分析软件,对风筒进行三维造型,并模拟
分析其强度,保证其满足使用条件的要求。
3.2 电动机
电机作为风机的重要组成部件,其防护等级、绝缘等级、防湿热等
都要有一定的保证,选取具有舰船产品制造合格认证的电动机产品。
ns=5.54×n×
姨Q
姨4 P3
=5.54×1450×
姨7.64
姨4 6903
=166
由计算结果 Ψt=0.36,选取d軈=0.55 适宜,则此时轮毂直径 d 为:
d=d軈·D (0.55×0.74) m =0.407m 取 d=0.41m,即轮毂直径为 d=410mm。
2.6 计算无因次轴向速度軓Ca和轴向速度 Ca
由 设 计 参 数 Q=27500m3/h; P =690 Pa 和 风 机 全 压 效 率
ηt=70%;则 N 为:
N
=K·1Q·P 0 Nhomakorabea0·ηt
=1.1×
7.64×690 1000×0.7
=8.28kw
根据电动机功率与风机轴功率的关系 P≥N=8.28kw,选取电动机
的功率为 11kw,转速为 1450r/min。
子午加速轴流风机的全三维优化设计
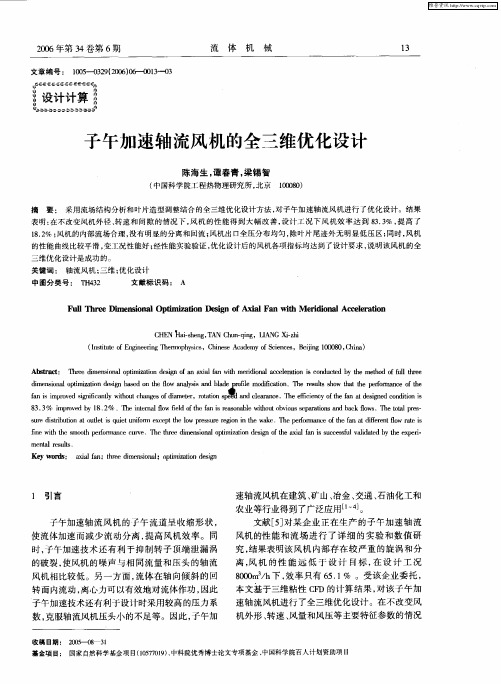
子午加速轴 流风机 的全三维优化设计
陈海生 。 谭春青 。 梁锡智
( 中国科 学院工程 热物理研究所 , 北京 108 ) 000 摘 要 : 采用 流场结构 分析 和叶片造 型调整结 合的全三维优化设 计方法 , 对子午加速轴 流风机进行 了优化设计 。结果
表明 : 在不 改变风机外径 、 转速和 间隙 的情况 下 , 风机 的性 能得 到大 幅 改善 , 计工 况下 风机效 率达 到 8 . % , 高 了 设 33 提 l.% ; 82 风机的 内部流场合理 , 没有明显的分离和 回流 ; 机出 口全压分 布均 匀 , 风 除叶片尾迹 外无 明显 低压 区; 同时 , 风机 的性能 曲线 比较平滑 , 变工况性能好 ; 经性能实验验证 , 优化设计后的风机各项指标均达到 了设计要求 , 明该风机 的全 说
d e s m pii t nd s ae nt o a s n l e o l m df a o .T e r ut so a tep r r a c e i ni l t z i ei b 8do ef w a l i ad b d  ̄r e o i t n h sl w t t h e o n eo t m m o m ao n g h l n ys a i f i i c e sh h f m fh
10MW轴流空气透平叶片全三维反向优化设计
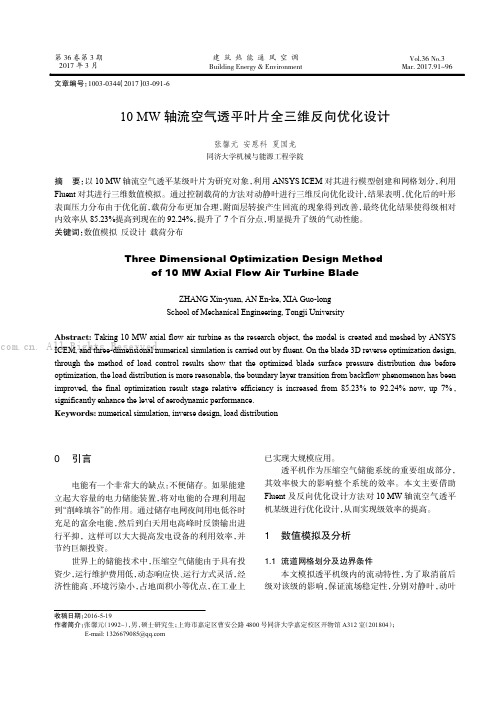
10MW 轴流空气透平叶片全三维反向优化设计张馨元 安恩科 夏国龙同济大学机械与能源工程学院摘 要: 以10MW 轴流空气透平某级叶片为研究对象, 利用 ANSYS ICEM 对其进行模型创建和网格划分, 利用 Fluent 对其进行三维数值模拟。
通过控制载荷的方法对动静叶进行三维反向优化设计,结果表明, 优化后的叶形 表面压力分布由于优化前, 载荷分布更加合理, 附面层转捩产生回流的现象得到改善, 最终优化结果使得级相对 内效率从85.23%提高到现在的92.24%, 提升了7个百分点, 明显提升了级的气动性能。
关键词: 数值模拟 反设计 载荷分布Three Dimensional Optimization Design Methodof 10MW Axial Flow Air Turbine BladeZHANG Xinyuan,AN Enke,XIA Guolong School of Mechanical Engineering,Tongji UniversityAbstract: Taking 10MW axial flow air turbine as the research object,the model is created and meshed by ANSYSICEM,and threedimensional numerical simulation is carried out by fluent.On the blade 3D reverse optimization design,through the method of load control results show that the optimized blade surface pressure distribution due before optimization,the load distribution is more reasonable,the boundary layer transition from backflow phenomenon has been improved,the final optimization result stage relative efficiency is increased from 85.23%to 92.24%now,up 7%, significantly enhance the level of aerodynamic performance.Keywords:numerical simulation,inverse design,load distribution收稿日期: 2016519作者简介: 张馨元 (1992~), 男, 硕士研究生; 上海市嘉定区曹安公路 4800号同济大学嘉定校区开物馆A312室 (201804); Email:*****************0 引言电能有一个非常大的缺点: 不便储存。
- 1、下载文档前请自行甄别文档内容的完整性,平台不提供额外的编辑、内容补充、找答案等附加服务。
- 2、"仅部分预览"的文档,不可在线预览部分如存在完整性等问题,可反馈申请退款(可完整预览的文档不适用该条件!)。
- 3、如文档侵犯您的权益,请联系客服反馈,我们会尽快为您处理(人工客服工作时间:9:00-18:30)。
轴流风机后导叶三维数值优化设计方法及其应用
本篇论文介绍了一种针对轴流风机后导叶的三维数值优化设计
方法,并探讨了该方法在实际应用中的效果。
首先,论文介绍了轴流风机后导叶的基本结构和工作原理,以及现有设计方法的局限性和不足之处。
接着,论文详细介绍了基于计算流体力学方法的三维数值优化设计方法的原理和流程,包括建立数值模型、确定优化目标和约束条件、选择优化算法等内容。
最后,论文通过实例分析和仿真验证,证明了该三维数值优化设计方法具有较高的设计效率和设计精度,能够有效优化轴流风机后导叶的性能表现,提高整机的效率和稳定性。
- 1 -。