机械手相关的外文文献
工业机器人发展毕业论文中英文资料外文翻译文献

工业机器人发展中英文资料外文翻译文献The development of industrial robotsIndustrial robot is a robot, it consists of a CaoZuoJi. Controller. Servo drive system and detection sensor device composition, it is a kind of humanoid operating automatic control, can repeat programming, can finish all kinds of assignments in three difficulties in authorship space the electromechanical integration automation production equipment, especially suitable for many varieties, become batch flexible production. It to stabilize and improve the product quality, raise efficiency in production, improve working conditions of the rapid renewal plays an extremely important role.Widely used industrial robots can gradually improve working conditions, stronger and controllable production capacity, speed up product updating and upgrading. Improve production efficiency and guarantee the quality of its products, eliminate dull work, save labor, provide a safe working environment, reduces the labor intensity, and reduce labor risk, improve the machine tool, reduce the workload and reduce process production time and inventory, enhance the competitiveness of enterprises.As technology advances, the development of industrial robot, the process can be divided into three generations -- generation, for demonstration reproduce, and it mainly consists of robot hand controller and demonstration teaching machines composed, can press advance box to record information guide action, the current industry repeated reappearance application of execution most. The second to feel robot, such as powerful sleep touch and vision, it has for some outside information feedback adjustment ability, currently has entered the application stage. Third generation of intelligent robot it has sense and understanding ability, in the external environment for the working environment changed circumstances, can also successfully complete the task, it is still in the experimental research phase.The United States is the birthplace of the robot, as early as in 1961, America's ConsolidedControlCorp and AMF companies developed the first practical demonstration emersion robot. After 40 years of development,the United States in the world of robotics has been in the lead position. Still Its technology comprehensive, advanced, adaptability is strong.Japan imported from America in 1967, the first robot in 1976 later, with the rapid development of the microelectronics and the market demand has increased dramatically, Japan was labor significant deficiencies in enterprise, industrial robots by "savior"'s welcome, make its Japanese industrial robots get fast development, the number of now whether robots or robot densities are top of the world, known as the "robot kingdom," said. The robot introduced from Germany time than Britain and Sweden about late 1956, but the Labour shortages caused by war, national technical level is higher social environment, but for the development and application of industrial robot provides favorable conditions. In addition, in Germany, for some dangerous prescribed, poisonous or harmful jobs, robot instead of ordinary people to the labor. This is the use of robots exploit a wide range of markets, and promote the development of the industrial robot technology. At present, the German industrial robots total of the world, which only behind to Japan.The French government has been more important robot technology, and through a series of research program, support established a complete science and technology system, make the development of the French robot smoothly. In government organization project, pay special attention to the robot research based technique, the focus is on the application research on in robot. And by industry support the development application and development of work, both supplement each other, make robots in France enterprises develop rapidly and popularize and make France in the international industrial machine with indispensable if position.British jamie since the late 1970s, promote and implement a department measures listed support the development of policies and make robots British industrial robots than today's robot powers started to early, and once in Japan has made the early brilliance. However, at this time the government for industrial robots implemented the constraining errors. This mistake in Britain dust, the robot industry in Western Europe was almost in the bottom of it. In recent years, Italy, Sweden, Spain, Finland, Denmark and other countries because of its own domestic robots market in great demand, development at a very fast pace. At present, the international on industrial robot company mainly divided into Japanese and European series. In AnChuan of Japanese are mainly the ethical products, the oTC, panasonic, FANLUC, not two more, etc. The products of the company kawasaki The main Asiatic KUKA, German CLOOS, Sweden's ABB, Italy CO work pelatiah U and Austria GM company.Industrial robot in China started in early 1970s, after 30 years development, roughly experienced three stages: in the 1970s and 1980s budding transplanter and the application of the 1990s initialization period. With the 20th century 70's world technology rapid development, the application of industrial robots in world created a climax, in this context, our country in 1972 start developing their industrial robots. Enter after the 1980s, with the further reform and opening, in high technology waves pound, our research and development of robot technology from the government's attention and support, "during the seventh state funds, thanked the parts were set robot and research, completed demonstration emersion type industrial robot complete technology development, developed spray paint, welding, arc welding and handling robot. , the national high technology research and development program begin to carry out, after several years research and made a large number of scientific research. Successfully developed a batch of special robot.From 9O 2O century since the early, China's national economy achieve two fundamental period of transformation into a a new round of economic restructuring and technological progress, China's industrial robots upsurge in practice and have made strides, and have developed spot welding, welding, assembling, paint, cutting, handling, palletizing etc various USES of industrial robot, and implement a batch of robot application engineering, formed a batch of industrial robots for our country industrialization base, the industrial robot soar laid a foundation. But compared with the developed countries, China also has the very big disparity of industrial robots.Along with the development of industrial robot depth and the breadth and raise the level of robot, industrial robots are has been applied in many fields. From the traditional automobile manufacturing sector to the manufacturing extensions. Such as mining robots, building robots and hydropower system used for maintenance robots, etc. In defense of military, medicine and health, food processing and life service areas such as the application of industrial robots will be more and more. The manufacturing of automobiles is a technology and capital intensive industry, is also the most widely used of industrial robots, accounting for almost to the industry for more than half of the industrial robots. In China, the industrial robot first is also used in automobile and engineering machinery industries. In car production of industrial robot is a major in the equipment, the brake parts and whole production of arc welding, spot welding, painting, handling, glue, stamping process used in large amounts. Our country is forecast to rise period, entered the automobile ownership in the next few years, car will still growing at around 15 percent annually. So the next few years the industrial robot demand willshow high growth trend, about 50% in growth, industrial robots in our automobile industry application will get a rapid development.Industrial robot in addition to the wide application of in the automotive industry in electronic, food processing, nonmetal processing, daily consumer goods and wood furniture processing industries for industrial robots demand is growing rapidly. In Asia, 2005 72,600 sets, installation industrial robots, compared with 2004 grew by 40%, and application in electronic industry accounted for about 31%. In Europe, according to statistics, since 2004 and 2005 in l: tI industry robot in the food processing industry increased 17% the application of left and right sides, in the application of nonmetal processing industry increased 20%, and daily necessities in consumption industries increased by 32% in wood furniture processing industry, up 18% or so. Industrial robot in oil has a wide application in, such as sea oil drilling, oil platforms, pipeline detection, refinery, large oil tank and tank welding etc all can use robots to complete. In the next few years, sensing technology, laser technology, engineering network technology will be widely used in industrial robots work areas, these technologies can cause the industrial robot application more efficient, high quality, lower cost. It is predicted that future robots will in medical and health care, biological technology and industry, education, relief, ocean exploitation, machine maintenance, transportation and agriculture and aquatic products applied field.In China, the industrial robot market share are mostly foreign industrial robots enterprise holds. Before the gunman in the international, domestic industrial robots enterprise facing great pressure of competition. Now China is from a "manufacturing power" to "manufacturing power forward," Chinese manufacturing industry faces and the international community, participate in the international division of labor in the great challenge of industrial automation increase immediate, government must can increase the funds for robots and policy support, will give the industry of industrial robots development into new momentum. With independent brand "devil robot" MoShi special technology company dedicated to providing solutions to the mainboard and robot, is willing with all my colleagues a build domestic industrial robot happy tomorrow!ReferencesElectronic Measurement and Intrumenttations,Cambridge University Press,1996工业机器人的发展工业机器人是机器人的一种,它由操作机.控制器.伺服驱动系统和检测传感器装置构成,是一种仿人操作自动控制,可重复编程,能在三难空间完成各种作业的机电一体化的自动化生产设备,特别适合于多品种,变批量柔性生产。
多自由度机械手毕业论文中英文资料外文翻译文献

毕业论文中英文资料外文翻译文献专业机械设计制造及其自动化课题多自由度机械手机械设计英文原文Automated Tracking and Grasping of a Moving Object with a RoboticHand-Eye SystemAbstractMost robotic grasping tasks assume a stationary or fixed object. In this paper, we explore the requirements for tracking and grasping a moving object. The focus of our work is to achieve a high level of interaction between a real-time vision system capable of tracking moving objects in 3-D and a robot arm with gripper that can be used to pick up a moving object. There is an interest in exploring the interplay of hand-eye coordination for dynamic grasping tasks such as grasping of parts on a moving conveyor system, assembly of articulated parts, or for grasping from a mobile robotic system. Coordination between an organism's sensing modalities and motor control system is a hallmark of intelligent behavior, and we are pursuing the goal of building an integrated sensing and actuation system that can operate in dynamic as opposed to static environments.The system we have built addresses three distinct problems in robotic hand-eye coordination for grasping moving objects: fast computation of 3-D motion parameters from vision, predictive control of a moving robotic arm to track a moving object, and interception and grasping. The system is able to operate at approximately human arm movement rates, and experimental results in which a moving model train is tracked is presented, stably grasped, and picked up by the system. The algorithms we have developed that relate sensing to actuation are quite general and applicable to a variety of complex robotic tasks that require visual feedback for arm and hand control.I. INTRODUCTIONThe focus of our work is to achieve a high level of interaction between real-time vision systems capable of tracking moving objects in 3-D and a robot arm equipped with a dexterous hand that can be used to intercept, grasp, and pick up a movingobject. We are interested in exploring the interplay of hand-eye coordination for dynamic grasping tasks such as grasping of parts on a moving conveyor system, assembly of articulated parts, or for grasping from a mobile robotic system. Coordination between an organism's sensing modalities and motor control system is a hallmark of intelligent behavior, and we are pursuing the goal of building an integrated sensing and actuation system that can operate in dynamic as opposed to static environments.There has been much research in robotics over the last few years that address either visual tracking of moving objects or generalized grasping problems. However, there have been few efforts that try to link the two problems. It is quite clear that complex robotic tasks such as automated assembly will need to have integrated systems that use visual feedback to plan, execute, and monitor grasping.The system we have built addresses three distinct problems in robotic hand-eye coordination for grasping moving objects: fast computation of 3-D motion parameters from vision, predictive control of a moving robotic arm to track a moving object, and interception and grasping. The system is able to operate at approximately human arm movement rates, using visual feedback to track, intercept, stably grasp, and pick up a moving object. The algorithms we have developed that relate sensing to actuation are quite general and applicable to a variety of complex robotic tasks that require visual feedback for arm and hand control.Our work also addresses a very fundamental and limiting problem that is inherent in building integrated sensing actuation systems; integration of systems with different sampling and processing rates. Most complex robotic systems are actually amalgams of different processing devices, connected by a variety of methods. For example, our system consists of three separate computation systems: a parallel image processing computer; a host computer that filters, triangulates, and predicts 3-D position from the raw vision data; and a separate arm control system computer that performs inverse kinematic transformations and joint-level servicing. Each of these systems has its own sampling rate, noise characteristics, and processing delays, which need to be integrated to achieve smooth and stable real-time performance. In our case, this involves overcoming visual processing noise and delays with a predictive filter basedupon a probabilistic analysis of the system noise characteristics. In addition, real-time arm control needs to be able to operate at fast servo rates regardless of whether new predictions of object position are available.The system consists of two fixed cameras that can image a scene containing a moving object (Fig. 1). A PUMA-560 with a parallel jaw gripper attached is used to track and pick up the object as it moves (Fig. 2). The system operates as follows:1) The imaging system performs a stereoscopic optic-flow calculation at each pixel in the image. From these optic-flow fields, a motion energy profile is obtained that forms the basis for a triangulation that can recover the 3-D position of a moving object at video rates.2) The 3-D position of the moving object computed by step 1 is initially smoothed to remove sensor noise, and a nonlinear filter is used to recover the correct trajectory parameters which can be used for forward prediction, and the updated position is sent to the trajectory-planner/arm-control system.3) The trajectory planner updates the joint-level servos of the arm via kinematic transform equations. An additional fixed-gain filter is used to provide servo-level control in case of missed or delayed communication from the vision and filtering system.4) Once tracking is stable, the system commands the arm to intercept the moving object and the hand is used to grasp the object stably and pick it up.The following sections of the paper describe each of these subsystems in detail along with experimental results.П. PREVIOUS WORKPrevious efforts in the areas of motion tracking and real-time control are too numerous to exhaustively list here. We instead list some notable efforts that have inspired us to use similar approaches. Burt et al. [9] have focused on high-speed feature detection and hierarchical scaling of images in order to meet the real-time demands of surveillance and other robotic applications. Related work has been reported by. Lee and Wohn [29] and Wiklund and Granlund [43] who uses image differencing methods to track motion. Corke, Paul, and Wohn [13] report afeature-based tracking method that uses special-purpose hardware to drive a servocontroller of an arm-mounted camera. Goldenberg et al. [16] have developed a method that uses temporal filtering with vision hardware similar to our own. Luo, Mullen, and Wessel [30] report a real-time implementation of motion tracking in 1-D based on Horn and Schunk’s method. Vergheseetul. [41] Report real-time short-range visual tracking of objects using a pipelined system similar to our own. Safadi [37] uses a tracking filter similar to our own and a pyramid-based vision system, but few results are reported with this system. Rao and Durrant-Whyte [36] have implemented a Kalman filter-based decentralized tracking system that tracks moving objects with multiple cameras. Miller [31] has integrated a camera and arm for a tracking task where the emphasis is on learning kinematic and control parameters of the system. Weiss et al. [42] also use visual feedback to develop control laws for manipulation. Brown [8] has implemented a gaze control system that links a robotic “head” containing binocular cameras with a servo controller that allows one to maintain a fixed gaze on a moving object. Clark and Ferrier [12] also have implemented a gaze control system for a mobile robot. A variation of the tracking problems is the case of moving cameras. Some of the papers addressing this interesting problem are [9], [15], [44], and [18].The majority of literature on the control problems encountered in motion tracking experiments is concerned with the problem of generating smooth, up-to-date trajectories from noisy and delayed outputs from different vision algorithms.Our previous work [4] coped with that problem in a similar way as in [38], using an cy- p - y filter, which is a form of steady-state Kalman filter. Other approaches can be found in papers by [33], [34], [28], [6]. In the work of Papanikolopoulos et al. [33], [34], visual sensors are used in the feedback loop to perform adaptive robotic visual tracking. Sophisticated control schemes are described which combine a Kalman filter’s estimation and filtering power with an optimal (LQG) controller which computes the robot’s motion. The vision system uses an optic-flow computation based on the SSD (sum of squared differences) method which, while time consuming, appears to be accurate enough for the tracking task. Efficient use of windows in the image can improve the performance of this method. The authors have presented good tracking results, as well as stated that the controller is robust enough so the use ofmore complex (time-varying LQG) methods is not justified. Experimental results with the CMU Direct Drive Arm П show that the methods are quite accurate, robust, and promising.The work of Lee and Kay [28] addresses the problem of uncertainty of cameras in the robot’s coordinate frame. The fact that cameras have to be strictly fixed in robot’s frame might be quite annoying since each time they are (most often incidentally) displaced; one has to undertake a tedious job of their recalibration. Again, the estimation of the moving object’s position and orientation is done in the Cartesian space and a simple error model is assumed. Andersen et al. [6] adopt a 3rd-order Kalman filter in order to allow a robotic system (consisting of two degrees of freedom) to play the labyrinth game. A somewhat different approach has been explored in the work of Houshangi [24] and Koivo et al. [27]. In these works, the autoregressive (AR) and auto grassier moving-average with exogenous input (ARMAX) models are investigated for visual tracking.Ш. VISION SYSTEMIn a visual tracking problem, motion in the imaging system has to be translated into 3-D scene motion. Our approach is to initially compute local optic-flow fields that measure image velocity at each pixel in the image. A variety of techniques for computing optic-flow fields have been used with varying results includingmatching-based techniques [5], [ 10], [39], gradient-based techniques [23], [32], [ 113, and patio-temporal, energy methods [20], [2]. Optic-flow was chosen as the primitive upon which to base the tracking algorithm for the following reasons.·The ability to track an object in three dimensions implies that there will be motion across the retinas (image planes) that are imaging the scene. By identifying this motion in each camera, we can begin to find the actual 3-D motion.·The principal constraint in the imaging process is high computational speed to satisfy the update process for the robotic arm parameters. Hence, we needed to be able to compute image motion quickly and robustly. The Hom-Schunck optic-flow algorithm (described below) is well suited for real-time computation on our PIPE image processing engine.·We have developed a new framework for computing optic-flow robustly using anestimation-theoretic framework [40]. While this work does not specifically use these ideas, we have future plans to try to adapt this algorithm to such a framework.Our method begins with an implementation of the Horn-Schunck method of computing optic-flow [22]. The underlying assumption of this method is theoptic-flow constraint equation, which assumes image irradiance at time t and t+σt will be the same:If we expand this constraint via a Taylor series expansion, and drop second- and higher-order terms, we obtain the form of the constraint we need to compute normal velocity:Where u and U are the velocities in image space, and Ix, Iy,and It are the spatial and temporal derivatives in the image. This constraint limits the velocity field in an image to lie on a straight line in velocity space. The actual velocity cannot be determined directly from this constraint due to the aperture problem, but one can recover the component of velocity normal to this constraint lineA second, iterative process is usually employed to propagate velocities in image neighborhoods, based upon a variety of smoothness and heuristic constraints. These added neighborhood constraints allow for recovery of the actual velocities u,v in the image. While computationally appealing, this method of determining optic-flow has some inherent problems. First, the computation is done on a pixel-by-pixel basis, creating a large computational demand. Second, the information on optic flow is only available in areas where the gradients defined above exist.We have overcome the first of these problems by using the PIPE image processor [26], [7]. The PIPE is a pipelined parallel image processing computer capable of processing 256 x 256 x 8 bit images at frame rate speeds, and it supports the operations necessary for optic-flow computation in a pixel parallel method (a typical image operation such as convolution, warping, addition subtraction of images can be done in one cycle-l/60 s).The second problem is alleviated by our not needing to know the actual velocities in the image. What we need is the ability to locate and quantify gross image motion robustly. This rules out simple differencing methodswhich are too prone to noise and will make location of image movement difficult. Hence, a set of normal velocities at strong gradients is adequate for our task, precluding the need to iteratively propagate velocities in the image.A. Computing Normal Optic-Flow in Real-TimeOur goal is to track a single moving object in real time. We are using two fixed cameras that image the scene and need to report motion in 3-D to a robotic arm control program. Each camera is calibrated with the 3-D scene, but there is no explicit need to use registered (i.e., scan-line coherence) cameras. Our method computes the normal component of optic-flow for each pixel in each camera image, finds a centurion of motion energy for each image, and then uses triangulation to intersect the back-projected centurions of image motion in each camera. Four processors are used in parallel on the PIPE. The processors are assigned as four per camera-two each for the calculation of X and Y motion energy centurions in each image. We also use a special processor board (ISMAP) to perform real-time histogram. The steps below correspond to the numbers in Fig. 3.1) The camera images the scene and the image is sent to processing stages in the PIPE.2) The image is smoothed by convolution with a Gaussian mask. The convolution operator is a built-in operation in the PIPE and it can be performed in one frame cycle. 3-4) In the next two cycles, two more images are read in, smoothed and buffered, yielding smoothed images Io and I1 and I2.The ability to buffer and pipeline images allows temporal operations on images, albeit at the cost of processing delays (lags) on output. There are now three smoothed images in the PIPE, with the oldest image lagging by 3/60 s.5) Images Io and I2, are subtracted yielding the temporal derivative It.6) In parallel with step 5, image I1is convolved with a 3 x 3 horizontal spatial gradient operator, returning the discrete form of I,. In parallel, the vertical spatial gradient is calculated yielding I, (not shown).7-8)The results from steps 5 and 6 are held in buffers and then are input to alook-up table that divides the temporal gradient at each pixel by the absolute value of the summed horizontal and vertical spatial gradients [which approximates thedenominator in (3)]. This yields the normal velocity in the image at each pixel. These velocities are then threshold and any isolated (i.e., single pixel motion energy) blobs are morphologically eroded. The above threshold velocities are then encoded as gray value 255. In our experiments, we threshold all velocities below 10 pixels per 60 ms to zero velocity.9-10) In order to get the centurion of the motion information, we need the X and Y coordinates of the motion energy. For simplicity, we show only the situation for the X coordinate. The gray-value ramp in Fig. 3 is an image that encodes the horizontal coordinate value (0-255) for each point in the image as a gray value.Thus, it is an image that is black (0) at horizontal pixel 0 and white (255) at horizontal pixel 255. If we logically and each pixel of the above threshold velocity image with the ramp image, we have an image which encodes high velocity pixels with their positional coordinates in the image, and leaves pixels with no motion at zero.11) By taking this result and histogram it, via a special stage of the PIPE which performs histograms at frame rate speeds, we can find the centurion of the moving object by finding the mean of the resulting histogram. Histogram the high-velocity position encoded images yields 256 16-bit values (a result for each intensity in the image). These 256 values can be read off the PIPE via a parallel interface in about 10 ms. This operation is performed in parallel to find the moving object’s Y censored (and in parallel for X and Y centurions for camera 2). The total associated delay time for finding the censored of a moving object becomes 15 cycles or 0.25 s.The same algorithm is run in parallel on the PIPE for the second camera. Once the motion centurions are known for each camera, they are back-projected into the scene using the camera calibration matrices and triangulated to find the actual 3-D location of the movement. Because of the pipelined nature of the PIPE, a new X or Y coordinate is produced every 1/60 s with this delay. While we are able to derive 3-D position from motion stereo at real-time rates, there are a number of sources of noise and error inherent in the vision system. These include stereo triangulation error, moving shadow s which are interpreted as object motion (we use no special lighting in the scene), and small shifts in censored alignments due to the different viewing angles of the cameras, which have a large baseline. The net effect of this is to create a 3-Dposition signal that is accurate enough for gross-level object tracking, but is not sufficient for the smooth and highly accurate tracking required for grasping the object.英文翻译自动跟踪和捕捉系统中的机械手系统摘要——许多机器人抓捕任务都被假设在了一个固定的物体上进行。
机械手臂外文文献翻译、中英文翻译、外文翻译

外文出处:《Manufacturing Engineering and Technology—Machining》附件1:外文原文ManipulatorRobot developed in recent decades as high-tech automated production equipment. I ndustrial robot is an important branch of industrial robots. It features can be program med to perform tasks in a variety of expectations, in both structure and performance a dvantages of their own people and machines, in particular, reflects the people's intellig ence and adaptability. The accuracy of robot operations and a variety of environments the ability to complete the work in the field of national economy and there are broad p rospects for development. With the development of industrial automation, there has be en CNC machining center, it is in reducing labor intensity, while greatly improved lab or productivity. However, the upper and lower common in CNC machining processes material, usually still use manual or traditional relay-controlled semi-automatic device . The former time-consuming and labor intensive, inefficient; the latter due to design c omplexity, require more relays, wiring complexity, vulnerability to body vibration inte rference, while the existence of poor reliability, fault more maintenance problems and other issues. Programmable Logic Controller PLC-controlled robot control system for materials up and down movement is simple, circuit design is reasonable, with a stron g anti-jamming capability, ensuring the system's reliability, reduced maintenance rate, and improve work efficiency. Robot technology related to mechanics, mechanics, elec trical hydraulic technology, automatic control technology, sensor technology and com puter technology and other fields of science, is a cross-disciplinary integrated technol ogy.First, an overview of industrial manipulatorRobot is a kind of positioning control can be automated and can be re-programmed to change in multi-functional machine, which has multiple degrees of freedom can be used to carry an object in order to complete the work in different environments. Low wages in China, plastic products industry, although still a labor-intensive, mechanical hand use has become increasingly popular. Electronics and automotive industries thatEurope and the United States multinational companies very early in their factories in China, the introduction of automated production. But now the changes are those found in industrial-intensive South China, East China's coastal areas, local plastic processin g plants have also emerged in mechanical watches began to become increasingly inter ested in, because they have to face a high turnover rate of workers, as well as for the workers to pay work-related injuries fee challenges.With the rapid development of China's industrial production, especially the reform and opening up after the rapid increase in the degree of automation to achieve the wor kpiece handling, steering, transmission or operation of brazing, spray gun, wrenches a nd other tools for processing and assembly operations since, which has more and mor e attracted our attention. Robot is to imitate the manual part of the action, according to a given program, track and requirements for automatic capture, handling or operation of the automatic mechanical devices.In real life, you will find this a problem. In the machine shop, the processing of part s loading time is not annoying, and labor productivity is not high, the cost of producti on major, and sometimes man-made incidents will occur, resulting in processing were injured. Think about what could replace it with the processing time of a tour as long a s there are a few people, and can operate 24 hours saturated human right? The answer is yes, but the robot can come to replace it.Production of mechanical hand can increase the automation level of production and labor productivity; can reduce labor intensity, ensuring product quality, to achieve saf e production; particularly in the high-temperature, high pressure, low temperature, lo w pressure, dust, explosive, toxic and radioactive gases such as poor environment can replace the normal working people. Here I would like to think of designing a robot to be used in actual production.Why would a robot designed to provide a pneumatic power: pneumatic robot refers to the compressed air as power source-driven robot. With pressure-driven and other en ergy-driven comparison have the following advantages: 1. Air inexhaustible, used late r discharged into the atmosphere, does not require recycling and disposal, do not pollu te the environment. (Concept of environmental protection) 2. Air stick is small, the pipeline pressure loss is small (typically less than asphalt gas path pressure drop of one-thousandth), to facilitate long-distance transport. 3. Compressed air of the working pre ssure is low (usually 4 to 8 kg / per square centimeter), and therefore moving the mate rial components and manufacturing accuracy requirements can be lowered. 4. With th e hydraulic transmission, compared to its faster action and reaction, which is one of th e advantages pneumatic outstanding. 5. The air cleaner media, it will not degenerate, n ot easy to plug the pipeline. But there are also places where it fly in the ointment: 1. A s the compressibility of air, resulting in poor aerodynamic stability of the work, resulti ng in the implementing agencies as the precision of the velocity and not easily control led. 2. As the use of low atmospheric pressure, the output power can not be too large; i n order to increase the output power is bound to the structure of the entire pneumatic s ystem size increased.With pneumatic drive and compare with other energy sources drive has the followin g advantages:Air inexhaustible, used later discharged into the atmosphere, without recycling and disposal, do not pollute the environment. Accidental or a small amount of leakage wo uld not be a serious impact on production. Viscosity of air is small, the pipeline pressu re loss also is very small, easy long-distance transport.The lower working pressure of compressed air, pneumatic components and therefor e the material and manufacturing accuracy requirements can be lowered. In general, re ciprocating thrust in 1 to 2 tons pneumatic economy is better.Compared with the hydraulic transmission, and its faster action and reaction, which is one of the outstanding merits of pneumatic.Clean air medium, it will not degenerate, not easy to plug the pipeline. It can be saf ely used in flammable, explosive and the dust big occasions. Also easy to realize auto matic overload protection.Second, the composition, mechanical handRobot in the form of a variety of forms, some relatively simple, some more complic ated, but the basic form is the same as the composition of the , Usually by the implem enting agencies, transmission systems, control systems and auxiliary devices composed.1.Implementing agenciesManipulator executing agency by the hands, wrists, arms, pillars. Hands are crawlin g institutions, is used to clamp and release the workpiece, and similar to human finger s, to complete the staffing of similar actions. Wrist and fingers and the arm connecting the components can be up and down, left, and rotary movement. A simple mechanical hand can not wrist. Pillars used to support the arm can also be made mobile as needed .2. TransmissionThe actuator to be achieved by the transmission system. Sub-transmission system c ommonly used manipulator mechanical transmission, hydraulic transmission, pneuma tic and electric power transmission and other drive several forms.3. Control SystemManipulator control system's main role is to control the robot according to certain p rocedures, direction, position, speed of action, a simple mechanical hand is generally not set up a dedicated control system, using only trip switches, relays, control valves a nd circuits can be achieved dynamic drive system control, so that implementing agenc ies according to the requirements of action. Action will have to use complex program mable robot controller, the micro-computer control.Three, mechanical hand classification and characteristicsRobots are generally divided into three categories: the first is the general machinery does not require manual hand. It is an independent not affiliated with a particular host device. It can be programmed according to the needs of the task to complete the oper ation of the provisions. It is characterized with ordinary mechanical performance, also has general machinery, memory, intelligence ternary machinery. The second category is the need to manually do it, called the operation of aircraft. It originated in the atom, military industry, first through the operation of machines to complete a particular job, and later developed to operate using radio signals to carry out detecting machines suc h as the Moon. Used in industrial manipulator also fall into this category. The third cat egory is dedicated manipulator, the main subsidiary of the automatic machines or automatic lines, to solve the machine up and down the workpiece material and delivery. T his mechanical hand in foreign countries known as the "Mechanical Hand", which is t he host of services, from the host-driven; exception of a few outside the working proc edures are generally fixed, and therefore special.Main features:First, mechanical hand (the upper and lower material robot, assembly robot, handlin g robot, stacking robot, help robot, vacuum handling machines, vacuum suction crane, labor-saving spreader, pneumatic balancer, etc.).Second, cantilever cranes (cantilever crane, electric chain hoist crane, air balance th e hanging, etc.)Third, rail-type transport system (hanging rail, light rail, single girder cranes, doubl e-beam crane)Four, industrial machinery, application of handManipulator in the mechanization and automation of the production process develo ped a new type of device. In recent years, as electronic technology, especially comput er extensive use of robot development and production of high-tech fields has become a rapidly developed a new technology, which further promoted the development of ro bot, allowing robot to better achieved with the combination of mechanization and auto mation.Although the robot is not as flexible as staff, but it has to the continuous duplication of work and labor, I do not know fatigue, not afraid of danger, the power snatch weig ht characteristics when compared with manual large, therefore, mechanical hand has b een of great importance to many sectors, and increasingly has been applied widely, for example:(1) Machining the workpiece loading and unloading, especially in the automatic lat he, combination machine tool use is more common.(2) In the assembly operations are widely used in the electronics industry, it can be used to assemble printed circuit boards, in the machinery industry It can be used to ass emble parts and components.(3) The working conditions may be poor, monotonous, repetitive easy to sub-fatigue working environment to replace human labor.(4) May be in dangerous situations, such as military goods handling, dangerous go ods and hazardous materials removal and so on..(5) Universe and ocean development.(6), military engineering and biomedical research and testing.Help mechanical hands: also known as the balancer, balance suspended, labor-saving spreader, manual Transfer machine is a kind of weightlessness of manual load system, a novel, time-saving technology for material handling operations booster equipment, belonging to kinds of non-standard design of series products. Customer application ne eds, creating customized cases. Manual operation of a simulation of the automatic ma chinery, it can be a fixed program draws ﹑ handling objects or perform household to ols to accomplish certain specific actions. Application of robot can replace the people engaged in monotonous ﹑ repetitive or heavy manual labor, the mechanization and a utomation of production, instead of people in hazardous environments manual operati on, improving working conditions and ensure personal safety. The late 20th century, 4 0, the United States atomic energy experiments, the first use of radioactive material ha ndling robot, human robot in a safe room to manipulate various operations and experi mentation. 50 years later, manipulator and gradually extended to industrial production sector, for the temperatures, polluted areas, and loading and unloading to take place t he work piece material, but also as an auxiliary device in automatic machine tools, ma chine tools, automatic production lines and processing center applications, the comple tion of the upper and lower material, or From the library take place knife knife and so on according to fixed procedures for the replacement operation. Robot body mainly b y the hand and sports institutions. Agencies with the use of hands and operation of obj ects of different occasions, often there are clamping ﹑ support and adsorption type of care. Movement organs are generally hydraulic pneumatic ﹑﹑ electrical device dri vers. Manipulator can be achieved independently retractable ﹑ rotation and lifting m ovements, generally 2 to 3 degrees of freedom. Robots are widely used in metallurgic al industry, machinery manufacture, light industry and atomic energy sectors.Can mimic some of the staff and arm motor function, a fixd procedure for the capture, handling objects or operating tools, automatic operation device. It can replace hum an labor in order to achieve the production of heavy mechanization and automation th at can operate in hazardous environments to protect the personal safety, which is wide ly used in machinery manufacturing, metallurgy, electronics, light industry and nuclea r power sectors. Mechanical hand tools or other equipment commonly used for additio nal devices, such as the automatic machines or automatic production line handling an d transmission of the workpiece, the replacement of cutting tools in machining centers , etc. generally do not have a separate control device. Some operating devices require direct manipulation by humans; such as the atomic energy sector performs household hazardous materials used in the master-slave manipulator is also often referred to as m echanical hand.Manipulator mainly by hand and sports institutions. Task of hand is holding the wor kpiece (or tool) components, according to grasping objects by shape, size, weight, mat erial and operational requirements of a variety of structural forms, such as clamp type, type and adsorption-based care such as holding. Sports organizations, so that the com pletion of a variety of hand rotation (swing), mobile or compound movements to achie ve the required action, to change the location of objects by grasping and posture. Robot is the automated production of a kind used in the process of crawling and mo ving piece features automatic device, which is mechanized and automated production process developed a new type of device. In recent years, as electronic technology, esp ecially computer extensive use of robot development and production of high-tech fiel ds has become a rapidly developed a new technology, which further promoted the dev elopment of robot, allowing robot to better achieved with the combination of mechani zation and automation. Robot can replace humans completed the risk of duplication of boring work, to reduce human labor intensity and improve labor productivity. Manipu lator has been applied more and more widely, in the machinery industry, it can be use d for parts assembly, work piece handling, loading and unloading, particularly in the a utomation of CNC machine tools, modular machine tools more commonly used. At pr esent, the robot has developed into a FMS flexible manufacturing systems and flexibl e manufacturing cell in an important component of the FMC. The machine tool equipment and machinery in hand together constitute a flexible manufacturing system or a f lexible manufacturing cell, it was adapted to small and medium volume production, y ou can save a huge amount of the work piece conveyor device, compact, and adaptabl e. When the work piece changes, flexible production system is very easy to change wi ll help enterprises to continuously update the marketable variety, improve product qua lity, and better adapt to market competition. At present, China's industrial robot techno logy and its engineering application level and comparable to foreign countries there is a certain distance, application and industrialization of the size of the low level of robo t research and development of a direct impact on raising the level of automation in Ch ina, from the economy, technical considerations are very necessary. Therefore, the stu dy of mechanical hand design is very meaningful.附件1:外文资料翻译译文机械手机械手是近几十年发展起来的一种高科技自动化生产设备。
机械手臂应用领域的外文文献以及翻译

机械手臂应用领域的外文文献以及翻译1. Introduction机械手臂是一种用于执行各种任务的自动化设备,其应用领域广泛。
本文档提供了一些关于机械手臂应用领域的外文文献,并附有简要的翻译。
2. 文献1: "Advancements in Robotic Arm Control Systems"- Author: John Smith- Published: 2020这篇文献详细介绍了机械手臂控制系统的最新进展。
作者讨论了各种控制算法、传感器和执行器的应用,以提高机械手臂的性能和精确度。
3. 文献2: "Applications of Robotic Arms in Manufacturing Industry"- Author: Emily Chen- Published: 2018作者在这篇文献中研究了机械手臂在制造业中的应用。
她列举了多个实例,包括机械手臂在装配、焊接和搬运等任务中的应用,以及通过使用机械手臂能够提高生产效率和质量的案例。
4. 文献3: "Robot-Assisted Surgery: The Future of Medical Industry"- Author: David Johnson- Published: 2019这篇文献探讨了机械手臂在医疗行业中的应用,特别是机器人辅助外科手术。
作者解释了机械手臂在手术过程中的优势,包括更小的切口、更高的精确度和减少术后恢复时间等方面。
5. 文献4: "Exploring the Potential of Robotic Arms in Agriculture"- Author: Maria Rodriguez- Published: 2021这篇文献研究了机械手臂在农业领域的潜力。
作者探讨了机械手臂在种植、收割和除草等农业任务中的应用,以及如何通过机械化技术改善农业生产的效率和可持续性。
关于机械手的英语专业论文
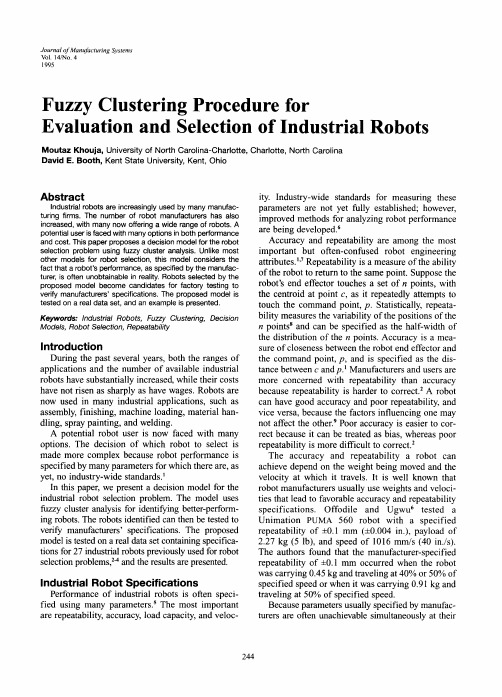
Abstract
Industrial robots are increasingly used by many manufacturing firms. The number of robot manufacturers has also increased, with many now offering a wide range of robots. A potential user is faced with many options in both performance and cost. This paper proposes a decision model for the robot selection problem using fuzzy cluster analysis. Unlike most other models for robot selection, this model considers the fact that a robot's performance, as specified by the manufacturer, is often unobtainable in reality. Robots selected by the proposed model become candidates for factory testing to verify manufacturers' specifications. The proposed model is tested on a real data set, and an example is presented.
Journal of Manufacturing Systems
Vol. 14/No. 4 1995
机械手相关的外文文献

附件一:A Rapidly Deployable Manipulator SystemAuthor:Christiaan J.J.Paredis,H.Benjamin Brown,Pradeep K.Khosla Abstract:A rapidly deployable manipulator system combines the flexibility of reconfigurable modular hardware with modular programming tools,allowing the user to rapidly create a manipulator which is custom-tailored for a given task.This article describes two main aspects of such a system,namely,the Reconfigurable Modular Manipulator System(RMMS)hardware and the corresponding control software.1 IntroductionRobot manipulators can be easily reprogrammed to perform different tasks,yet the range of tasks that can be performed by a manipulator is limited by mechanicalstructure.Forexample,a manipulator well-suited for precise movement across the top of a table would probably no be capable of lifting heavy objects in the vertical direction.Therefore,to perform a given task,one needs to choose a manipulator with an appropriate mechanical structure.We propose the concept of a rapidly deployable manipulator system to address the above mentioned shortcomings of fixed configuration manipulators.As is illustrated in Figure 1,a rapidly deployable manipulator system consists of software and hardware that allow the user to rapidly build and program a manipulator which is customtailored for a given task.The central building block of a rapidly deployable system is a Reconfigurable Modular Manipulator System(RMMS).The RMMS utilizes a stock of interchangeable link and joint modules of various sizes and performance specifications.One such module is shown in Figure 2.By combining these general purpose modules,a wide range of special purpose manipulators can be assembled.Recently,there has been considerable interest in the idea of modular manipulators,for research applications as well as for industrial applications.However,most of these systems lack the property of reconfigurability,which is key to the concept of rapidly deployable systems.The RMMS is particularly easy to reconfigure thanks to its integrated quick-coupling connectors described in Section 3.Effective use of the RMMS requires,Task Based Design software.This software takes as input descriptions of the task and of the available manipulator modules;it generates as output a modular assembly configuration optimally suited to perform the given task.Several different approaches have been used successfully to solve simpli-fied instances of thisA third important building block of a rapidly deployable manipulator system is a framework for the generation of control software.To reduce the complexity of softwaregeneration for real-time sensor-based control systems,a software paradigm called software assembly has been proposed in the Advanced Manipulators Laboratory at CMU.This paradigm combines the concept of reusable and reconfigurable software components,as is supported by the Chimera real-time operating system,with a graphical user interface and a visual programming language,inplemented in Onika.Although the software assembly paradigm provides thesoftware infrastructure for rapidly programming manipulator systems,it does not solve the programming problem itself.Explicit programming of sensor-based manipulator systems is cumbersome due to the extensive amount of detail which must be specified for the robot to perform the task.The software synthesis problem for sensor-based robots can be simplified dramatically,by providing robust robotic skills,that is,encapsulated strategies for accomplishing common tasks in the robots task domain.Such robotic skills can then be used at the task level planning stage without having to consider any of the low-level detailsAs an example of the use of a rapidly deployable system,consider a manipulator in a nuclear environment where it must inspect material and space for radioactive contamination,or assemble and repair equipment.In such an environment,widely varied kinematic(e.g.,workspace)and dynamic(e.g.,speed,payload)performance is required,and these requirements may not be known a priori.Instead of preparing a large set of different manipulators to accomplish these tasks—an expensive solution—one can use a rapidly deployable manipulator system.Consider the following scenario:as soon as a specific task is identified,the task based design software determinesthe task.This optimal configuration is thenassembled from the RMMS modules by a human or,in manipulator.The resulting manipulator is rapidly programmed by using the software assembly paradigm and our library of robotic skills.Finally,the manipulator is deployed to perform its task.Although such a scenario is still futuristic,the development of the reconfigurable modular manipulator system,described in this paper,is a major step forward towards our goal of a rapidly deployable manipulator system.Our approach could form the basis for the next generation of autonomous manipulators,in which the traditional notion of sensor-based autonomy is extended to configuration-based autonomy.Indeed,although a deployed system can have all the sensory and planning information it needs,it may still not be able to accomplish its task because the task is beyond the system’s physical capabilities.A rapidly deployable system,on the other hand,could adapt its physical capabilities based on task specifications and,with advanced sensing,control,and planning strategies,accomplish the task autonomously.2 Design of self-contained hardware modulesIn most industrial manipulators,the controller is a separate unit housing the sensor interfaces,power amplifiers,and control processors for all the joints of the manipulator.A large number of wires is necessary to connect this control unit with the sensors,actuators and brakes located in each of the joints of the manipulator.The large number of electrical connections and the non-extensible nature of such a system layout make it infeasible for modular manipulators.The solution we propose is to distribute the control hardware to each individual module of the manipulator.These modules then become self-contained units which include sensors,an actuator,a brake,a transmission,a sensor interface,a motor amplifier,and a communication interface,as is illustrated in Figure 3.As a result,only six wires are required for power distribution and data communication.2.1 Mechanical designThe goal of the RMMS project is to have a wide variety of hardware modules available.So far,we have built four kinds of modules:the manipulator base,a link module,three pivot joint modules(one of which is shown in Figure 2),and one rotate joint module.The base module and the link module have no degrees-of-freedom;the joint modules have degree-of-freedom each.The mechanical design of the joint modules compactly fits a DC-motor,a fail-safe brake,a tachometer,a harmonic drive and a resolverThe pivot and rotate joint modules use different outside housings to provide the right-angle or in-line configuration respectively,but are identical internally.Figure 4shows in cross-section the internal structure of a pivot joint.Each joint module includes a DC torque motor and 100:1 harmonic-drive speed reducer,and is rated at a maximum speed of 1.5rad/s and maximum torque of 270Nm.Each module has a mass of approximately 10.7kg.A single,compact,X-type bearing connects the two joint halves and provides the needed overturning rigidity.A hollow motor shaft passes through all the rotary components,and provides a channel for passage of cabling with minimal flexing.2.2 Electronic designThe custom-designed on-board electronics are also designed according to the principle of modularity.Each RMMS module contains a motherboard which provides the basic functionality and onto which daughtercards can be stacked to add module specific functionality.The motherboard consists of a Siemens 80C166 microcontroller,64K of ROM,64K of RAM,an SMC COM20020 universal local area network controller with an RS-485 driver,and an RS-232 driver.The function of the motherboard is to establish communication with the host interface via an RS-485 bus and to perform the lowlevel control of the module,as is explained in more detail in Section 4.The RS-232 serial bus driver allows for simple diagnostics and software prototyping.A stacking connector permits the addition of an indefinite number of daughtercards with various functions,such as sensor interfaces,motor controllers,RAM expansion etc.In our current implementation,only modules with actuators include a daughtercard.This card contains a 16 bit resolver to digital converter,a 12 bit A/D converter to interface with the tachometer,and a 12 bit D/A converter to control the motor amplifier;we have used an ofthe-shelf motor amplifier(Galil Motion Control model SSA-8/80)to drive the DC-motor.For modules with more than one degree-of-freedom,for instance a wrist module,more than one such daughtercard can be stacked onto由e s创ne motherboard.3 Integrated quick-coupling connectorsTo make a modular manipulator be reconfigurable,it is necessary that the modules can be easily connected with each other.We have developed a quick-coupling mechanism with which a secure mechanical connection between modules can be achieved by simply turning a ring handtight;no tools are required.As shown in Figure 5,keyed flanges provide precise registration of the two modules.Turning of thelocking collar on the male end produces two distinct motions:first the fingers of the locking ring rotate(with the collar)about 22.5 degrees and capture the fingers on the flanges;second,the collar rotates relative to the locking ring,while a cam mechanism forces the fingers inward to securely grip the mating flanges.A ball-transfer mechanism between the collar and locking ring automatically produces this sequence of motions.At the same time the mechanical connection is made,pneumatic and electronic connections are also established.Inside the locking ring is a modular connector that has 30 male electrical pins plus a pneumatic coupler in the middle.These correspond to matching female components on the mating connector.Sets of pins are wired in parallel to carry the 72V-25A power for motors and brakes,and 48V–6A power for the electronics.Additional pins carry signals for two RS-485 serial communication busses and four video busses.A plastic guide collar plus six alignment pins prevent damage to the connector pins and assure proper alignment.The plastic block holding the female pins can rotate in the housing to accommodate the eight different possible connection orientations(8@45 degrees).The relative orientation is automatically registered by means of an infrared LED in the female connector and eight photodetectors in the male connector.4 ARMbus communication systemEach of the modules of the RMMS communicates with a VME-based host interface over a local area network called the ARMbus;each module is a node of the network.The communication is done in a serial fashion over an RS-485 bus which runs through the length of the manipulator.We use the ARCNET protocol[1]implemented on a dedicated IC(SMC COM20020).ARCNET is a deterministic token-passing network scheme which avoids network collisions and guarantees each node its time to access the network.Blocks information called packets may be sent from any node on the network to any one of the other nodes,or to all nodes simultaneously(broadcast).Each node may send one packet each time it gets the token.The maximum network throughput is 5Mb/s.The first node of the network resides on the host interface card,as is depicted in Figure 6.In addition to a VME address decoder,this card contains essentially the same hardware one can find on a module motherboard.The communication between the VME side of the card and the ARCNET side occurs through dual-port RAM.There are two kinds of data passed over the local area network.During the manipulator initialization phase,the modules connect to the network one by one,starting at the base and ending at the end-effector.On joining the network,each module sends a data-packet to the host interface containing its serial number and its relative orientation with respect to the previous module.This information allows us to automatically determine the current manipulator configuration.During the operation phase,the host interface communicates with each of the nodes at 400Hz.The data that is exchanged depends on the control mode—centralized or distributed.In centralized control mode,the torques for all the joints are computed on the VME-based real-time processing unit(RTPU),assembled into a data-packet by the microcontroller on the host interface card and broadcast over the ARMbus to all the nodes of the network.Each node extracts its torque value from the packet and replies by sending a data-packet containing the resolver and tachometer readings.In distributed control mode,on the other hand,the host computer broadcasts the desired joint values and feed-forward torques.Locally,in each module,the control loop can then be closed at a frequency much higher than 400Hz.The modules still send sensor readings back to the host interface to be used in the computation of the subsequent feed-forward torque.5 Modular and reconfigurable control softwareThe control software for the RMMS has been developed using the Chimera real-time operating system,which supports reconfigurable and reusable software components.The software components used to control the RMMS are listed in Table 1.The trjjline,dls,and of the RMMS,such as the number of degrees-of-freedom,the Denavit-Hartenberg parameters etc.During the initialization phase,the RMMS interface establishes contact with each of the hardware modules to determine automatically which modules are being used and in which order and orientation they have been assembled.For each module,a data file with a parametric model is read.By combining this information for all the modules,kinematic and dynamic models of the entire manipulator are.After the initialization,the rmms software component operates in a distributed control mode in which the microcontrollers of each of the RMMS modules perform PID control locally at 1900Hz.The communication between the modules and the host interface is at 400Hz,which can differ from the cycle frequency of the rmms softwarecomponent.Since we use a triple buffer mechanism for the communication through the dual-port RAM on the ARMbus host interface,no synchronization or handshaking is necessary.Because closed form inverse kinematics do not exist for all possible RMMS configurations,we use a damped least-squares kinematic controller to do the inverse kinematics computation numerically.6 Seamless integration of simulationTo assist the user in evaluating whether an RMMS con-figuration can successfully complete a given task,we have built a simulator.The simulator is based on the TeleGrip robot simulation software from Deneb Inc.,and runs on an SGI Crimson which is connected with the real-time processing unit through a Bit3 VME-to-VME adaptor,as is shown in Figure 6.A graphical user interface allows the user to assemble simulated RMMS configurations very much like assembling the real pleted configurations can be tested and programmed using the TeleGrip functions for robot devices.The configurations can also be interfaced with the Chimera real-time softwarerunning on the same RTPUs used to control the actual hardware.As a result,it is possible to evaluate not only the movements of the manipulator but also the realtime CPU usage and load balancing.Figure 7 shows an RMMS simulation compared with the actual task execution.7 SummaryWe have developed a Reconfigurable Modular Manipulator System which currently consists of six hardware modules,with a total of four degrees-of-freedom.These modules can be assembled in a large number of different configurations to tailor the kinematic and dynamic properties of the manipulator to the task at hand.The control software for the RMMS automatically adapts to the assembly configuration by building kinematic and dynamic models of the manipulator;this is totally transparent to the user.To assist the user in evaluating whether a manipulator configuration is well suited for a given task,we have alsobuilt a simulator.AcknowledgmentThis research was funded in part by DOE under grant DE-F902-89ER14042,by Sandia National Laboratories under contract AL-3020,by the Department of Electrical and Computer Engineering,and by The Robotics Institute,Carnegie Mellon University.The authors would also like to thank Randy Casciola,Mark DeLouis,Eric Hoffman,and Jim Moody for their valuable contributions to the design of the RMMS system.附件二:可迅速布置的机械手系统作者:Christiaan J.J.Paredis,H.Benjamin Brown,Pradeep K.Khosla摘要:一个迅速可部署的机械手系统,可以使再组合的标准化的硬件的灵活性用标准化的编程工具结合,允许用户迅速建立为一项规定的任务来通常地控制机械手。
简易机械手及控制外文文献翻译、机械手类中英翻译、外文翻译
附录外文文献原文:Simple Manipulator And The Control Of ItAlong with the social production progress and people life rhythm is accelerating, people on production efficiency also continuously put forward new requirements. Because of microelectronics technology and calculation software and hardware technology rapid development and modern control theory, the perfection of the fast development, the robot technology pneumatic manipulator system because its media sources do not pollute the environment, simple and cheap components, convenient maintenance and system safety and reliability characteristic, has penetrated into every sector of the industrial field, in the industrial development plays an important role. This article tells of the pneumatic control robots, furious manipulator XY axis screw group, the turntable institutions, rotating mechanical parts base. Main effect is complete mechanical components handling work, to be placed in different kinds of line or logistics pipeline, make parts handling, transport of goods more quick and convenient.Matters of the manipulator axial linkage simple structure and action processManipulator structure, as shown in figure 1 below have accused of manipulator (1), XY axis screw group (2), the turntable institutions (3), rotating base (4), etc.Figure 1 Manipulator StructureIts motion control mode is: (1) can rotate by servomotor Angle for 360 °breath control manipulator (photoelectric sensor sure start 0 point); (2) by stepping motor drive screw component make along the X, Y manipulators move (have X, Y axis limit switches); (3) can rotates 360 °can drive the turntable institutions manipulators and bushings free rotation (its electric drag in part by the dc motivation, photoelectric encoder, close to switch etc); (4) rotating base main support above 3 parts; (5) gas control manipulator by pressure control (Zhang close when pressed on, put inflatable robot manipulators loosen) when gas.Its working process for: when the goods arrived, manipulator system begins to move; Stepping motor control, while the other start downward motion along the horizontal axis of the step-motor controller began to move exercise; Servo motor driver arrived just grab goods manipulators rotating the orientation of the place, then inflatable, manipulator clamped goods.Vertical axis stepper motor drive up, the other horizontal axis stepper motor driver started to move forward; rotary DC motor rotation so that the whole robot motion, go to the cargo receiving area; longitudinal axis stepper motor driven down again, arrived at the designated location, Bleed valve, mechanical hand release the goods; system back to the place ready for the next action.II.Device controlTo achieve precise control purposes, according to market conditions, selection of a variety of keycomponents as follows:1. Stepper motor and driveMechanical hand vertical axis (Y axis) and horizontal (X axis) is chosen Motor Technology Co., Ltd. Beijing Stone 42BYG250C type of two-phase hybrid stepping motor, step angle of 0.9 °/ 1.8 °, current is 1.5A. M1 is the horizontal axis motor driven manipulator stretch, shrink; M2 is the vertical axis motor driven manipulator rise and fall. The choice of stepper motor drive is SH-20403 type, the drive uses 10 ~ 40V DC power supply, H-phase bridge bipolar constant current drive, the maximum output current of 3A of the 8 optional, maximum fine of 64 segments of 7 sub-mode optional optical isolation, standard single-pulse interface, with offline capabilities to maintain semi-sealed enclosure can be adapted to environmental conditions even worse, provide semi-current energy-saving mode automatically. Drive the internal switching power supply design to ensure that the drive can be adapted to a wide voltagerange, the user can according to their circumstances to choose between the 10 ~ 40VDC. Generally the higher rated power supply voltage can improve high-speed torque motor, but the drive will increase the loss and temperature rise. The maximum output drive current is 3A / phase (peak), six drive-panel DIP switch on the first three can be combined 5,6,7 8 out of state, corresponding to the 8 kinds of output current from 0.9A to 3A to meet the different motors. The drive can provide full step, half step improvement, subdivision 4, 8 segments, 16 segments, 32 segments and 64 segments of 7 operating modes. The use of six of the drive panel DIP switches 1,2and3 can be combined from three different states.2. Servo motors and drivesManipulator with Panasonic servo motor rotational movement A series of small inertia MSMA5AZA1G, the rated 50W, 100/200V share, rotary incremental encoder specifications (number of pulses 2500p / r, resolution of 10000p / r, Lead 11 lines) ; a seal, no brakes, shaft with keyway connections. The motor uses Panasonic's unique algorithms, the rate increased by 2 times the frequency response, to 500Hz; positioning over the past adjust the scheduled time by Panasonic servo motor products for the V Series of 1 / 4. With the resonance suppression, control, closed loop control, can make up for lack of mechanical rigidity, in order to achieve high positioning accuracy can also be an external grating to form closed loop control to further improve accuracy. With a conventional automatic gain adjustment and real-time automatic gainInterest adjustment in the automatic gain adjustment methods, which also has RS-485, RS-232C communication port, the host controller can control up to 16 axes. Servo motor drives are a series MSDA5A3A1A, applicable to small inertia motor.3. DC machine360 ° swing of the turntable can be a brushless DC motor driven organization, the system is chosen when the profit company in Beijing and the 57BL1010H1 brushless DC motor, its speed range, low-speed torque, smooth running, low noise, high efficiency. Brushless DC motor drive using the Beijing and when Lee's BL-0408 produced by the drive, which uses 24 ~ 48V DC power supply, a start-stop and steering control, over current, overvoltage and locked rotor protection, and there is failure alarm output external analog speed control, braking down so fast.4. Rotary encoderCan swing 360 ° in the body on the turntable, fitted with OMRON E6A2 produced incremental rotary encoder, the encoder signals to the PLC, to achieve precise positioning of rotary bodies.5. PLC SelectionAccording to the system design requirements, the choice of OMRON CPM2A produced minicomputer. CPM2A in a compact unit integrated with a variety of properties, including the synchronization pulse control, interrupt input, pulse output, analog set and clock functions. CPM2A the CPU unit is astand-alone unit, capable of handling a wide range of application of mechanical control, it is built in the device control unit for the ideal product. Ensure the integrity of communications and personal computers, other OMRON PC and OMRON Programmable Terminal communication. The communication capability allows the robot to Axis simple easy integration into industrial control systems.III. Software programming1. Software flow chartPLC programming flow chart is based. Only the design flow, it may be smooth and easy to prepare and write a statement form the ladder, and ultimately complete the process design. So write a flow chart of program design is critical to the task first thing to do. Axis Manipulator based on simple control requirements, drawing flow chart shown in Figure 2.Figure 2 Software flow chart2. Program partBecause space is limited, here only paper listed the first two program segment for readers see.Figure 3 Program partIV. ConclusionAxis simple robot state by the various movements and PLC control, the robot can not only meet the manual, semi-automatic mode of operation required for such a large number of buttons, switches, position detection point requirements, but also through the interface components and Computer Organization PLC industrial LAN, network communication and network control. Axis simple robot can be easily embedded into industrial production pipeline.中文译文:简易机械手及控制随着社会生产不断进步和人们生活节奏不断加快,人们对生产效率也不断提出新要求。
工业机器人外文参考文献
工业机器人外文参考文献工业机器人外文参考文献1. Gao, Y., & Chen, J. (2018). Review of industrial robots for advanced manufacturing systems. Journal of Manufacturing Systems, 48, 144-156.2. Karaman, M., & Frazzoli, E. (2011). Sampling-based algorithms for optimal motion planning. The International Journal of Robotics Research, 30(7), 846-894.3. Khatib, O. (1986). Real-time obstacle avoidance for manipulators and mobile robots. The International Journal of Robotics Research, 5(1), 90-98.4. Lee, J. H., & Kim, E. B. (2019). Energy-efficient path planning for industrial robots considering joint dynamics. Journal of Mechanical Science and Technology, 33(3),1343-1351.5. Li, D., Li, Y., Wang, X., & Li, H. (2019). Design and implementation of a humanoid robot with flexible manipulators. Robotica, 37(12), 2008-2025.6. Liu, Y., Ren, X., & Wang, T. (2019). A novel adaptive fuzzy sliding mode control for a nonholonomic mobile robot. Soft Computing, 23(3), 1197-1209.7. Loh, A. P., & Tan, K. K. (2014). Vision-based controlof industrial robots using an adaptive neural network. Robotics and Computer-Integrated Manufacturing, 30(2), 177-184.8. Niemeyer, G., & Slotine, J. J. (1990). Stable adaptive teleoperation. The International Journal of Robotics Research, 9(1), 85-98.9. Park, J. Y., & Cho, C. H. (2018). Optimal path planning for industrial robots using a hybrid genetic algorithm. International Journal of Precision Engineering and Manufacturing, 19(5), 755-761.10. Wang, Z., Wang, X., & Liu, Y. (2019). Design and analysis of a novel humanoid robot with intelligent control. International Journal of Advanced Manufacturing Technology, 102(5-8), 1391-1403.。
机器人机械手外文文献
A Nonlinear Disturbance Observer forRobotic ManipulatorsWen-Hua Chen,Member,IEEE,Donald J.Ballance,Member,IEEE,Peter J.Gawthrop,Senior Member,IEEE,and John O’Reilly,Senior Member,IEEEAbstract—A new nonlinear disturbance observer(NDO) for robotic manipulators is derived in this paper.The global exponential stability of the proposed disturbance observer(DO) is guaranteed by selecting design parameters,which depend on the maximum velocity and physical parameters of robotic manipulators.This new observer overcomes the disadvantages of existing DO’s,which are designed or analyzed by linear system techniques.It can be applied in robotic manipulators for various purposes such as friction compensation,independent joint control, sensorless torque control,and fault diagnosis.The performance of the proposed observer is demonstrated by the friction estimation and compensation for a two-link robotic manipulator.Both simulation and experimental results show the NDO works well. Index Terms—Friction,nonlinear estimation,observers,robots.I.I NTRODUCTIOND ISTURBANCE observers(DO’s)have been used inrobotic manipulator control for a long time.In general, the main objective of the use of DO’s is to deduce external unknown or uncertain disturbance torques without the use of an additional sensor.The use of DO’s in robotic manipulators can be divided into the following categories.1)Independent joint control is widely used in industrialrobots where a multilink manipulator is divided into several independent links with linear dynamics.The per-formance of these kind of controllers can be improved by the use of a DO.This is accomplished by considering the coupling torques from other links as an unknown external disturbance and using a DO to estimate and compensate for it[1].This technique has also been extended to deal with parameter variations and unmodeled dynamics whereby it improves the robustness of robots[2];2)Friction is a common phenomenon in mechanical sys-tems and plays an important role in system performance.Many friction models and compensation methods have been proposed[3].One of the most promising methodsManuscript received December22,1998;revised March23,2000.Abstract published on the Internet April21,2000.An earlier version of this paper was presented at the38th IEEE Control and Decision Conference,Phoenix,AZ, December7–10,1999.This work was supported by the U.K.Engineering and Physical Sciences Research Council under Grant GR/L62665.W.-H.Chen and J.O’Reilly are with the Centre for Systems and Control, Department of Electronics and Electrical Engineering,University of Glasgow, Glasgow G128QQ,U.K.(e-mail:w.chen@).D.J.Ballance and P.J.Gawthrop are with the Centre for Systems and Control, Department of Mechanical Engineering,University of Glasgow,Glasgow G12 8QQ,U.K.(e-mail:D.Ballance@).Publisher Item Identifier S0278-0046(00)06805-2.is observer-based control where a DO is used to estimate friction[4];3)DO’s have been used in robotic manipulators for forcefeedback and hybrid position/force control where the DO works as a torque sensor[5]–[7].In this case,it is sup-posed that the friction and other dynamics are well mod-eled and compensated for.The use of a DO,rather than several torque sensors(for each link,at least one torque sensor is required),simplifies the structure of the system, reduces the cost,and improves the reliability.With this technique,sensorless torque control can be implemented[5]–[7].4)Robotic manipulators work in a dynamic highly uncertainenvironment.In this application,DO’s provide signals for monitoring and trajectory planning rather than for control.For example,in robotic assembly when the component is misinserted,the reaction torque/force is greatly increased and could damage the robotic manipulator.A DO can es-timate the reaction torque online and transmit this infor-mation to the monitoring or planning level.Chan[8]usesa DO in electronic component assembly,while Ohishi andOhde[9]give an example of the use of a DO in collision. Although the DO technique has been widely used in robotic manipulator control for various purposes,in almost all cases, the analysis or design is based on linearized models or using linear system techniques.Since a multilink robotic manipulator is a highly nonlinear and coupled system,the validity of using linear analysis and synthesis techniques may be doubtful.Many important properties of existing DO’s have not been established, e.g.,unbiased estimation or even global stability.There are, however,some recent results using nonlinear disturbance ob-servers(NDO’s).A variable structure DO has been proposed [10]and a nonlinear observer for a special kind of friction,i.e., Coulomb friction,has been proposed by Friedland and Park [11].This nonlinear observer is designed based on the model of Coulomb friction,and the global convergence ability has been shown.It has been further modified and implemented on robotic manipulators by Tafazoli et al.[12].However,a specific model of friction will not be used in this paper,and the whole design is based on the DO concept.That is,similar to other unknown torques,the friction is considered as a disturbance on the control torque.It should be stressed that the DO rather than a velocity ob-server of a manipulator is considered in this paper.A velocity observer has been considered by many authors.Bona and Indri have compared and implemented several linear and nonlinear velocity observers on a robotic manipulator[13].0278–0046/00$10.00©2000IEEEAn NDO for multilink robotic manipulators will be presented in this paper.By carefully selecting the observer gain function,it will be shown that global convergence is guaranteed.This result is based on Lyapunov theory.II.P ROBLEM F ORMULATION AND A B ASIC O BSERVER A.Problem FormulationFor the sake of simplicity,a two-link robotic manipulator is considered in this paper.The main idea is readily extended to the more general case.The model of a two-link robotic manipulator can be representedbyis either the torque orforce.has different meaningsin different observer applications.For example,it can be fric-tion in friction compensation,reaction torque or force in forcecontrol,and unmodeled dynamics in independent joint control.Since a general observer will be derived in this paper,all of themare considered as“disturbances.”When the first-order dynamicsof dc motors are included in the abovemodel,is the disturbancevoltage in this case.The objective of this paper is to design an observer suchthat the estimation yielded by the observer exponentiallyapproaches thedisturbance,,and(2)a DO is proposedas,it is reasonable to supposethat(4)which implies that the disturbance varies slowly relative to theobserver dynamics.However,it will be illustrated by simulationand experiment that the observer developed in this paper canalso track some fast time-varying disturbances.Define the observererror(6)That is,the observer error is governedby.III.NDOThe acceleration signal is not available in many robotic ma-nipulators,and it is also difficult to construct the accelerationsignal from the velocity signal by differentiation due to mea-surement noise.However,although the observer(3)is not prac-tical to implement,it provides a basis for the further nonlinearobserver design.A.Modified ObserverDefine an auxiliary variablevector(12)and(14)The estimation approaches thedisturbance(15)where are inertial parameters,which dependon the masses of the links,motors and tip load,and the lengthsof the links.Theorem:For the two-link robotic manipulator(1),when thefunction(16)and(17)where denotes the maximum velocity of the second link,then the observer(12)and(13)is globally asymptotically stable.Proof:Since(19)since and and,therefore,invertible.From(15),(20)where,a Lyapunov func-tion candidate for the observer(12)and(13)can be chosenas(23)Differentiating the Lyapunov function with respect totimeandif(25)Thatis,(26)Since)is then globally asymptotically stable.From the Theorem,the stability of the observer depends onthe maximum velocity of the second link and other physicalparameters.By choosing the designparameteris givenby(28)Let.It then follows from(24)that,the desired exponential conver-gence rate can be achieved.IV.S IMULATION AND E XPERIMENTAL R ESULTSThe proposed NDO is tested in this section.As stated in Sec-tion I,the NDO can be used in robotic manipulators for variouspurposes.In what follows,the NDO is designed as a frictionobserver.That is,the NDO is used to estimate the friction fora two-link robotic manipulator.The reason for designing a fric-tion observer here is that friction varies rapidly,even discontin-uously.It is a challenging task in observer design.The simula-tion and experiment are based on a two-link manipulator withFig.1.Structure of the revised friction model.dc motor actuators.The dynamic model of the manipulator in-cluding the first-order dc motor dynamics is governed by(1)and is detailed in[15].A.Friction SimulationThe friction considered is Coulomb and Viscous friction, givenbyNNis given by(30),is asmall positive scalar,and,thefriction.Whenthe velocity is greater than this,the second term in the above ex-pression vanishes and thefrictionis chosenas0.001.The frictions given by these two models are almost in-distinguishable.However,experience has shown that using therevised model greatly improves the computational efficiency forsimulation.B.Simulation ResultsA controller is designed by computed torque control wherethe disturbance is not taken into account.When square-wavecommand references are given for first and second links,respec-tively,the velocity and friction histories are shown in Figs.3and4.It can be seen that the friction varies very rapidly with the ve-locity.A friction observer is designed by the NDO technique de-veloped in this paper.The designparameterFig.4.Second link velocity and friction time histories.Fig.5.First-link friction estimated by the friction observer.C.Experimental ResultsThe proposed NDO is implemented on a two-link robotic ma-nipulator in the laboratory.The experimental results for a com-puted torque controller with and without the NDO are com-pared.The control structure,which combines a computed torque controller with the NDO,is shown in Fig.7,where the effect of the friction is compensated for by the outputs of the NDO viafeedforward.With the NDO,the parameterFig.9.Experimental results with DO:estimatedfriction.Fig.10.Experimental results with DO:velocity.Fig.11.Experimental results with DO:motor voltages.V .C ONCLUSIONThis paper has presented a procedure for the design of an NDO for robotic manipulators.Following the procedure presented in this paper,a condition for convergence was established.The speed of the convergence can be specified by the design parameters.The proposed observer was tested by simulation and experiment.Even though the theory is developed for constant disturbances,it was shown that,for a rapid time-varying signal like friction,the observer exhibits satisfactory performance.By feedforward compensation of the estimated friction yielded by the DO,the performance,in particular,the steady-state performance,was significantly improved.The NDO proposed in this paper can also be applied in independent joint control,sensorless torque control,and fault diagnosis in robotics.A CKNOWLEDGMENTThe authors greatly appreciate the comments and discussion by Dr.J.J.Gribble pertaining to the earlier version of this paper.R EFERENCES[1]K.S.Eom,I.H.Suh,and W.K.Chung,“Disturbance observer basedpath tracking control of robot manipulator considering torque satura-tion,”in Proc.Int.Advanced Robot.Conf.,1997,pp.651–657.[2] B.K.Kim,W.K.Chung,and Y .Youm,“Robust learning control forrobot manipulator based on disturbance observers,”in Proc.IEEE Ind.Electron.Conf.,1996,pp.1276–1282.[3]H.Olsson,K.J.Åström,C.C.de Wit,M.Gafvert,and P.Lischinsky,“Friction models and friction compensation,”Eur.J.Control ,vol.4,no.3,pp.176–195,1998.[4]G.Zhang and J.Furusho,“Control of robot arms using joint torque sen-sors,”IEEE Control Syst.Mag.,vol.18,no.1,pp.48–55,1998.[5]S.Komada and K.Ohnishi,“Force feedback control of robot manipu-lator by the acceleration tracing orientation method,”IEEE Trans.Ind.Electron.,vol.37,pp.6–12,Feb.1990.[6]S.Komada,K.Nomura,M.Ishida,and T.Hori,“Robust force controlbased on compensation for parameter variations of dynamic environ-ment,”IEEE Trans.Ind.Electron.,vol.40,pp.89–95,Feb.1993.[7]T.Murakami,F.Yu,and K.Ohnishi,“Torque sensorless control in mul-tidegree-of-freedom manipulator,”IEEE Trans.Ind.Electron.,vol.40,pp.259–265,Apr.1993.[8]S.P.Chan,“A disturbance observer for robot manipulators with appli-cation to electronic components assembly,”IEEE Trans.Ind.Electron.,vol.42,pp.487–493,Oct.1995.[9]K.Ohishi and H.Ohde,“Collision and force control for robot manip-ulator without force sensor,”in Proc.IEEE Ind.Electron.Conf.,1994,pp.766–771.[10]H.N.Lin and Y .Kuroe,“Decoupling control of robot manipulators byusing variable structure disturbance observer,”in Proc.IEEE Ind.Elec-tron.Conf.,1995,pp.1266–1271.[11] B.Friedl and Y .J.Park,“On adaptive friction compensation,”IEEETrans.Automat.Contr.,vol.37,pp.1609–1612,Oct.1992.[12]S.Tafazoli,C.W.de Silva,and wrence,“Tracking control of anelectrohydraulic manipulator in the presence of friction,”IEEE Trans.Contr.Syst.Tech.,vol.6,pp.401–411,May 1998.[13] B.Bona and M.Indri,“Analysis and implementation of observersfor robotic manipulators,”in Proc.IEEE Int.Conf.Robot.Automat.,Leuven,Belgium,1998,pp.3006–3011.[14]P.J.Gawthrop and L.P.S.Smith,Metamodeling:Bond Graphs andDynamic Systems .New York:Prentice-Hall,1996.[15]W.-H.Chen,D.J.Ballance,and P.J.Gawthrop,“Nonlinear generalizedpredictive control and optimal dynamic inversion control,”in Proc.14th IFAC World Congr.,vol.E,Beijing,China,1999,pp.415–420.[16] D.Karnopp,“Computer simulation of strick-stip friction in mechanicaldynamic systems,”ASME J.Dynam.Syst.,Meas.,Contr.,vol.107,pp.100–103,1985.Wen-Hua Chen(M’00)received the M.Sc.and Ph.D.degrees from Northeast University,Shengyang,China,in1989and1991,respectively.From1991to1997,he was a Lecturer in the De-partment of Automatic Control,Nanjing Universityof Aeronautics and Astronautics.He then held a re-search position in the Centre for Systems and Con-trol,Department of Mechanical Engineering,Univer-sity of Glasgow,Glasgow,U.K.He is currently a Lec-turer at the Centre for Systems and Control,Depart-ment of Electronics and Electrical Engineering,Uni-versity of Glasgow.His research interests include robust control,nonlinear con-trol and their application in mechatronics,and aerospaceengineering.Donald J.Ballance(M’91)received the D.Phil.de-gree in control engineering from the University ofOxford,Oxford,U.K.,in1989.Since then,he has been at the Centre for Systemsand Control,Department of Mechanical Engi-neering,University of Glasgow,Glasgow,U.K.,initially as a Research Assistant and currently asa Senior Lecturer.His research interests includemodeling and analysis of systems using bond graphs,quantitative feedback theory and the effect of pa-rameter uncertainty on control system performance,nonlinear control,and the practical application of thesetechniques.Peter J.Gawthrop(M’82–SM’94)was born inSeascale,Cumberland,U.K.,in1952.He receivedthe B.A.(first class honors),D.Phil.and M.A.de-grees in engineering science from Oxford University,Oxford,U.K.,in1973,1977,and1979,respectively.Following a period as a Research Assistant withthe Department of Engineering Science,Oxford Uni-versity,he became a W.W.Spooner Research Fellowat the New College,Oxford.He then moved to theUniversity of Sussex,initially as a Lecturer,and thenas a Reader in control engineering.Since1987,he hasheld the Wylie Chair of Control Engineering in the Department of MechanicalEngineering,Glasgow University,Glasgow,U.K.He was involved in foundingthe Centre for Systems and Control,which is a cross-departmental researchgrouping at Glasgow University.His research interests include self-tuning con-trol,continuous-time system identification,and system modeling,particularlyusing bond graphs in the context of partially known systems.He is also inter-ested in applying control techniques to a number of areas,including process con-trol,robotics,aerospace systems,and anaesthesia.He has authored and co-au-thored approximately120conference and journal papers and three books inthese areas.He was an associate editor of Automatica and an honorary editorof the Proceeding of the IEE,and serves on the editorial boards of a numberof journals,including the IMechE Journal of Systems and Control,Journal ofProcess Control,IMA Journal of Mathematical Control and Information,theInternational Journal of Adaptive Control and Signal processing,and the Euro-pean Journal of Control.Dr.Gawthrop was the recipient of the1994Honeywell International Medalpresented by the Institute of Measurement andControlJohn O’Reilly(M’82–SM’00)received the B.Sc.,Ph.D.,and D.Sc.degrees in engineering fromQueen’s University,Belfast,Belfast,NorthernIreland,in1972,1976,and1985,respectively.He is currently a Professor of control engineeringat the Centre for Systems and Control,Departmentof Electronics and Electrical Engineering,Universityof Glasgow,Glasgow,U.K.He is currently a VisitingErskine Fellow in the Department of Electrical andElectronic Engineering,University of Canterbury,Canterbury,New Zealand.His main research inter-ests are centered on integrated and nonlinear control,with particular applicationto aerospace and deregulated power systems.He is also a Consultant Editorfor the International Journal of Control.Dr.O’Reilly was the recipient of a U.K.Royal Academy of Engineering Fore-sight Award.。
机械手设计英文参考文献原文翻译
翻译人:王墨墨山东科技大学文献题目:Automated Calibration of Robot Coordinatesfor Reconfigurable Assembly Systems翻译正文如下:针对可重构装配系统的机器人协调性的自动校准T.艾利,Y.米达,H.菊地,M.雪松日本东京大学,机械研究院,精密工程部摘要为了实现流水工作线更高的可重构性,以必要设备如机器人的快速插入插出为研究目的。
当一种新的设备被装配到流水工作线时,应使其具备校准系统。
该研究使用两台电荷耦合摄像机,基于直接线性变换法,致力于研究一种相对位置/相对方位的自动化校准系统。
摄像机被随机放置,然后对每一个机械手执行一组动作。
通过摄像机检测机械手动作,就能捕捉到两台机器人的相对位置。
最佳的结果精度为均方根值0.16毫米。
关键词:装配,校准,机器人1 介绍21世纪新的制造系统需要具备新的生产能力,如可重用性,可拓展性,敏捷性以及可重构性[1]。
系统配置的低成本转变,能够使系统应对可预见的以及不可预见的市场波动。
关于组装系统,许多研究者提出了分散的方法来实现可重构性[2][3]。
他们中的大多数都是基于主体的系统,主体逐一协同以建立一种新的配置。
然而,协同只是目的的一部分。
在现实生产系统中,例如工作空间这类物理问题应当被有效解决。
为了实现更高的可重构性,一些研究人员不顾昂贵的造价,开发出了特殊的均匀单元[4][5][6]。
作者为装配单元提出了一种自律分散型机器人系统,包含多样化的传统设备[7][8]。
该系统可以从一个系统添加/删除装配设备,亦或是添加/删除装配设备到另一个系统;它通过协同作用,合理地解决了工作空间的冲突问题。
我们可以把该功能称为“插入与生产”。
表1:合作所需的调节和量度在重构过程中,校准的装配机器人是非常重要的。
这是因为,需要用它们来测量相关主体的特征,以便在物理主体之间建立良好的协作关系。
这一调整必须要达到表1中所列到的多种标准要求。
- 1、下载文档前请自行甄别文档内容的完整性,平台不提供额外的编辑、内容补充、找答案等附加服务。
- 2、"仅部分预览"的文档,不可在线预览部分如存在完整性等问题,可反馈申请退款(可完整预览的文档不适用该条件!)。
- 3、如文档侵犯您的权益,请联系客服反馈,我们会尽快为您处理(人工客服工作时间:9:00-18:30)。
附件一:A Rapidly Deployable Manipulator SystemAuthor:Christiaan J.J.Paredis,H.Benjamin Brown,Pradeep K.Khosla Abstract:A rapidly deployable manipulator system combines the flexibility of reconfigurable modular hardware with modular programming tools,allowing the user to rapidly create a manipulator which is custom-tailored for a given task.This article describes two main aspects of such a system,namely,the Reconfigurable Modular Manipulator System(RMMS)hardware and the corresponding control software.1 IntroductionRobot manipulators can be easily reprogrammed to perform different tasks,yet the range of tasks that can be performed by a manipulator is limited by mechanicalstructure.Forexample,a manipulator well-suited for precise movement across the top of a table would probably no be capable of lifting heavy objects in the vertical direction.Therefore,to perform a given task,one needs to choose a manipulator with an appropriate mechanical structure.We propose the concept of a rapidly deployable manipulator system to address the above mentioned shortcomings of fixed configuration manipulators.As is illustrated in Figure 1,a rapidly deployable manipulator system consists of software and hardware that allow the user to rapidly build and program a manipulator which is customtailored for a given task.The central building block of a rapidly deployable system is a Reconfigurable Modular Manipulator System(RMMS).The RMMS utilizes a stock of interchangeable link and joint modules of various sizes and performance specifications.One such module is shown in Figure 2.By combining these general purpose modules,a wide range of special purpose manipulators can be assembled.Recently,there has been considerable interest in the idea of modular manipulators,for research applications as well as for industrial applications.However,most of these systems lack the property of reconfigurability,which is key to the concept of rapidly deployable systems.The RMMS is particularly easy to reconfigure thanks to its integrated quick-coupling connectors described in Section 3.Effective use of the RMMS requires,Task Based Design software.This software takes as input descriptions of the task and of the available manipulator modules;it generates as output a modular assembly configuration optimally suited to perform the given task.Several different approaches have been used successfully to solve simpli-fied instances of thisA third important building block of a rapidly deployable manipulator system is a framework for the generation of control software.To reduce the complexity of softwaregeneration for real-time sensor-based control systems,a software paradigm called software assembly has been proposed in the Advanced Manipulators Laboratory at CMU.This paradigm combines the concept of reusable and reconfigurable software components,as is supported by the Chimera real-time operating system,with a graphical user interface and a visual programming language,inplemented in Onika.Although the software assembly paradigm provides thesoftware infrastructure for rapidly programming manipulator systems,it does not solve the programming problem itself.Explicit programming of sensor-based manipulator systems is cumbersome due to the extensive amount of detail which must be specified for the robot to perform the task.The software synthesis problem for sensor-based robots can be simplified dramatically,by providing robust robotic skills,that is,encapsulated strategies for accomplishing common tasks in the robots task domain.Such robotic skills can then be used at the task level planning stage without having to consider any of the low-level detailsAs an example of the use of a rapidly deployable system,consider a manipulator in a nuclear environment where it must inspect material and space for radioactive contamination,or assemble and repair equipment.In such an environment,widely varied kinematic(e.g.,workspace)and dynamic(e.g.,speed,payload)performance is required,and these requirements may not be known a priori.Instead of preparing a large set of different manipulators to accomplish these tasks—an expensive solution—one can use a rapidly deployable manipulator system.Consider the following scenario:as soon as a specific task is identified,the task based design software determinesthe task.This optimal configuration is thenassembled from the RMMS modules by a human or,in manipulator.The resulting manipulator is rapidly programmed by using the software assembly paradigm and our library of robotic skills.Finally,the manipulator is deployed to perform its task.Although such a scenario is still futuristic,the development of the reconfigurable modular manipulator system,described in this paper,is a major step forward towards our goal of a rapidly deployable manipulator system.Our approach could form the basis for the next generation of autonomous manipulators,in which the traditional notion of sensor-based autonomy is extended to configuration-based autonomy.Indeed,although a deployed system can have all the sensory and planning information it needs,it may still not be able to accomplish its task because the task is beyond the system’s physical capabilities.A rapidly deployable system,on the other hand,could adapt its physical capabilities based on task specifications and,with advanced sensing,control,and planning strategies,accomplish the task autonomously.2 Design of self-contained hardware modulesIn most industrial manipulators,the controller is a separate unit housing the sensor interfaces,power amplifiers,and control processors for all the joints of the manipulator.A large number of wires is necessary to connect this control unit with the sensors,actuators and brakes located in each of the joints of the manipulator.The large number of electrical connections and the non-extensible nature of such a system layout make it infeasible for modular manipulators.The solution we propose is to distribute the control hardware to each individual module of the manipulator.These modules then become self-contained units which include sensors,an actuator,a brake,a transmission,a sensor interface,a motor amplifier,and a communication interface,as is illustrated in Figure 3.As a result,only six wires are required for power distribution and data communication.2.1 Mechanical designThe goal of the RMMS project is to have a wide variety of hardware modules available.So far,we have built four kinds of modules:the manipulator base,a link module,three pivot joint modules(one of which is shown in Figure 2),and one rotate joint module.The base module and the link module have no degrees-of-freedom;the joint modules have degree-of-freedom each.The mechanical design of the joint modules compactly fits a DC-motor,a fail-safe brake,a tachometer,a harmonic drive and a resolverThe pivot and rotate joint modules use different outside housings to provide the right-angle or in-line configuration respectively,but are identical internally.Figure 4shows in cross-section the internal structure of a pivot joint.Each joint module includes a DC torque motor and 100:1 harmonic-drive speed reducer,and is rated at a maximum speed of 1.5rad/s and maximum torque of 270Nm.Each module has a mass of approximately 10.7kg.A single,compact,X-type bearing connects the two joint halves and provides the needed overturning rigidity.A hollow motor shaft passes through all the rotary components,and provides a channel for passage of cabling with minimal flexing.2.2 Electronic designThe custom-designed on-board electronics are also designed according to the principle of modularity.Each RMMS module contains a motherboard which provides the basic functionality and onto which daughtercards can be stacked to add module specific functionality.The motherboard consists of a Siemens 80C166 microcontroller,64K of ROM,64K of RAM,an SMC COM20020 universal local area network controller with an RS-485 driver,and an RS-232 driver.The function of the motherboard is to establish communication with the host interface via an RS-485 bus and to perform the lowlevel control of the module,as is explained in more detail in Section 4.The RS-232 serial bus driver allows for simple diagnostics and software prototyping.A stacking connector permits the addition of an indefinite number of daughtercards with various functions,such as sensor interfaces,motor controllers,RAM expansion etc.In our current implementation,only modules with actuators include a daughtercard.This card contains a 16 bit resolver to digital converter,a 12 bit A/D converter to interface with the tachometer,and a 12 bit D/A converter to control the motor amplifier;we have used an ofthe-shelf motor amplifier(Galil Motion Control model SSA-8/80)to drive the DC-motor.For modules with more than one degree-of-freedom,for instance a wrist module,more than one such daughtercard can be stacked onto由e s创ne motherboard.3 Integrated quick-coupling connectorsTo make a modular manipulator be reconfigurable,it is necessary that the modules can be easily connected with each other.We have developed a quick-coupling mechanism with which a secure mechanical connection between modules can be achieved by simply turning a ring handtight;no tools are required.As shown in Figure 5,keyed flanges provide precise registration of the two modules.Turning of thelocking collar on the male end produces two distinct motions:first the fingers of the locking ring rotate(with the collar)about 22.5 degrees and capture the fingers on the flanges;second,the collar rotates relative to the locking ring,while a cam mechanism forces the fingers inward to securely grip the mating flanges.A ball-transfer mechanism between the collar and locking ring automatically produces this sequence of motions.At the same time the mechanical connection is made,pneumatic and electronic connections are also established.Inside the locking ring is a modular connector that has 30 male electrical pins plus a pneumatic coupler in the middle.These correspond to matching female components on the mating connector.Sets of pins are wired in parallel to carry the 72V-25A power for motors and brakes,and 48V–6A power for the electronics.Additional pins carry signals for two RS-485 serial communication busses and four video busses.A plastic guide collar plus six alignment pins prevent damage to the connector pins and assure proper alignment.The plastic block holding the female pins can rotate in the housing to accommodate the eight different possible connection orientations(8@45 degrees).The relative orientation is automatically registered by means of an infrared LED in the female connector and eight photodetectors in the male connector.4 ARMbus communication systemEach of the modules of the RMMS communicates with a VME-based host interface over a local area network called the ARMbus;each module is a node of the network.The communication is done in a serial fashion over an RS-485 bus which runs through the length of the manipulator.We use the ARCNET protocol[1]implemented on a dedicated IC(SMC COM20020).ARCNET is a deterministic token-passing network scheme which avoids network collisions and guarantees each node its time to access the network.Blocks information called packets may be sent from any node on the network to any one of the other nodes,or to all nodes simultaneously(broadcast).Each node may send one packet each time it gets the token.The maximum network throughput is 5Mb/s.The first node of the network resides on the host interface card,as is depicted in Figure 6.In addition to a VME address decoder,this card contains essentially the same hardware one can find on a module motherboard.The communication between the VME side of the card and the ARCNET side occurs through dual-port RAM.There are two kinds of data passed over the local area network.During the manipulator initialization phase,the modules connect to the network one by one,starting at the base and ending at the end-effector.On joining the network,each module sends a data-packet to the host interface containing its serial number and its relative orientation with respect to the previous module.This information allows us to automatically determine the current manipulator configuration.During the operation phase,the host interface communicates with each of the nodes at 400Hz.The data that is exchanged depends on the control mode—centralized or distributed.In centralized control mode,the torques for all the joints are computed on the VME-based real-time processing unit(RTPU),assembled into a data-packet by the microcontroller on the host interface card and broadcast over the ARMbus to all the nodes of the network.Each node extracts its torque value from the packet and replies by sending a data-packet containing the resolver and tachometer readings.In distributed control mode,on the other hand,the host computer broadcasts the desired joint values and feed-forward torques.Locally,in each module,the control loop can then be closed at a frequency much higher than 400Hz.The modules still send sensor readings back to the host interface to be used in the computation of the subsequent feed-forward torque.5 Modular and reconfigurable control softwareThe control software for the RMMS has been developed using the Chimera real-time operating system,which supports reconfigurable and reusable software components.The software components used to control the RMMS are listed in Table 1.The trjjline,dls,and of the RMMS,such as the number of degrees-of-freedom,the Denavit-Hartenberg parameters etc.During the initialization phase,the RMMS interface establishes contact with each of the hardware modules to determine automatically which modules are being used and in which order and orientation they have been assembled.For each module,a data file with a parametric model is read.By combining this information for all the modules,kinematic and dynamic models of the entire manipulator are.After the initialization,the rmms software component operates in a distributed control mode in which the microcontrollers of each of the RMMS modules perform PID control locally at 1900Hz.The communication between the modules and the host interface is at 400Hz,which can differ from the cycle frequency of the rmms softwarecomponent.Since we use a triple buffer mechanism for the communication through the dual-port RAM on the ARMbus host interface,no synchronization or handshaking is necessary.Because closed form inverse kinematics do not exist for all possible RMMS configurations,we use a damped least-squares kinematic controller to do the inverse kinematics computation numerically.6 Seamless integration of simulationTo assist the user in evaluating whether an RMMS con-figuration can successfully complete a given task,we have built a simulator.The simulator is based on the TeleGrip robot simulation software from Deneb Inc.,and runs on an SGI Crimson which is connected with the real-time processing unit through a Bit3 VME-to-VME adaptor,as is shown in Figure 6.A graphical user interface allows the user to assemble simulated RMMS configurations very much like assembling the real pleted configurations can be tested and programmed using the TeleGrip functions for robot devices.The configurations can also be interfaced with the Chimera real-time softwarerunning on the same RTPUs used to control the actual hardware.As a result,it is possible to evaluate not only the movements of the manipulator but also the realtime CPU usage and load balancing.Figure 7 shows an RMMS simulation compared with the actual task execution.7 SummaryWe have developed a Reconfigurable Modular Manipulator System which currently consists of six hardware modules,with a total of four degrees-of-freedom.These modules can be assembled in a large number of different configurations to tailor the kinematic and dynamic properties of the manipulator to the task at hand.The control software for the RMMS automatically adapts to the assembly configuration by building kinematic and dynamic models of the manipulator;this is totally transparent to the user.To assist the user in evaluating whether a manipulator configuration is well suited for a given task,we have alsobuilt a simulator.AcknowledgmentThis research was funded in part by DOE under grant DE-F902-89ER14042,by Sandia National Laboratories under contract AL-3020,by the Department of Electrical and Computer Engineering,and by The Robotics Institute,Carnegie Mellon University.The authors would also like to thank Randy Casciola,Mark DeLouis,Eric Hoffman,and Jim Moody for their valuable contributions to the design of the RMMS system.附件二:可迅速布置的机械手系统作者:Christiaan J.J.Paredis,H.Benjamin Brown,Pradeep K.Khosla摘要:一个迅速可部署的机械手系统,可以使再组合的标准化的硬件的灵活性用标准化的编程工具结合,允许用户迅速建立为一项规定的任务来通常地控制机械手。