弧齿锥齿轮的加工调整计算
弧齿锥齿轮几何参数设计

第14章 弧齿锥齿轮的轮坯设计14.1 弧齿锥齿轮的基本概念14.1.1 锥齿轮的节锥对于相交轴之间的齿轮传动,一般采用锥齿轮。
锥齿轮有直齿锥齿轮和弧齿锥齿轮。
弧齿锥齿轮副的形式如图14-1所示,与直齿锥齿轮相比,轮齿倾斜呈弧线形。
但弧齿锥齿轮的节锥同直齿锥齿轮的节锥一样,相当于一对相切圆锥面作纯滚动,它是齿轮副相对运动的瞬时轴线绕齿轮轴线旋转形成的(图14-2)。
两个相切圆锥的公切面成为齿轮副的节平面。
齿轮轴线与节平面的夹角,即节锥的半锥角称为锥齿轮的节锥角δ1或δ2。
两齿轮轴线之间的夹角称为锥齿轮副的轴交角∑。
节锥任意一点到节锥顶点O 的距离称为该点的锥距R i ,节点P 的锥距为R 。
因锥齿轮副两个节锥的顶点重合,则 21δδ+=∑大小轮的齿数之比称为锥齿轮的传动比1212z z i =(14-1) 小轮和大轮的节点半径r 1、r 2分别为11sin δR r = 22sin δR r = (14-2)它们与锥齿轮的齿数成正比,即121212sin sin z z r r ==δδ (14-3) 传动比与轴交角已知,则节锥可惟一的确定,大、小轮节锥角计算公式为∑+∑=cos 1sin 12122i i tg δ 21δδ-∑= (14-4)当090=∑时,即正交锥齿轮副,122i tg =δ 14.1.2弧齿锥齿轮的旋向与螺旋角1.旋向弧齿锥齿轮的轮齿对母线的倾斜方向称为旋向,有左旋和右旋两种(图14-3)。
面对轮齿观察,由小端到大端顺时针倾斜者为右旋齿轮(图14-3b ),逆时针倾斜者则为左旋齿(图14-3a )。
大小轮的旋向相图14-2 锥齿轮的节锥与节面(a) 左旋 (b) 右旋图14-3 弧齿锥齿轮的旋向图14-1 弧齿锥齿轮副反时,才能啮合。
一般情况下,工作面为顺时针旋转的(从主动轮背后看,或正对被动轮观察),主动锥齿轮的螺旋方向为左旋,被动轮为右旋(图14-1);工作面为逆时针旋转的,情况相反。
弧齿锥齿轮铣齿计算

弧齿锥齿轮铣齿计算弧齿锥齿轮是传动行业中常用的一种齿轮,其结构相对复杂,铣齿计算难度较大。
本文将围绕弧齿锥齿轮铣齿计算进行分步骤的阐述。
第一步:确定齿轮参数在进行弧齿锥齿轮铣齿计算之前,需要确定齿轮参数,包括轴距、锥距、锥度、压力角等参数。
这些参数需要在设计时给出,或者由实际应用中的传递比、轴功率等参数推算得出。
第二步:计算齿数弧齿锥齿轮铣齿计算的第一步是计算齿数。
通常情况下,弧齿锥齿轮的齿数较小,一般不超过20个。
计算齿数需要使用弧齿锥齿轮铣刀的几何参数,以及齿面曲线的基本方程。
每个齿面曲线可以看做一条螺旋线,其截面积呈三角形状。
根据这些参数计算得出的齿数,不一定是整数,需要舍入到最接近的整数。
第三步:计算铣刀参数在确定齿数之后,就可以开始计算铣刀参数了。
铣刀的参数包括齿宽、齿高、齿间隙等。
齿宽可以由齿数和啮合角度计算得出;齿高可以由矢高、压力角等参数计算得出;齿间隙可以采用经验数据或理论计算得出。
第四步:计算加工参数铣齿前需要确定加工参数,包括进给量、转速等。
这些参数需要根据加工机床和工件材质等具体情况进行选取,以获得最佳的加工效果。
进给量的选择要尽量保证加工效率和质量,而转速的选择则要考虑切削油,刀具材料等方面的因素。
第五步:检验加工精度最后一步是检验加工精度。
通过测量齿轮的齿高、齿宽、轴向距离、齿距等参数,可以判断齿轮加工的精度是否符合要求。
如果齿轮加工精度不足,则需要对铣刀的加工参数进行调整,并重新进行铣齿计算。
综上所述,弧齿锥齿轮铣齿计算需要经过齿轮参数计算、齿数计算、铣刀参数计算、加工参数选择和加工精度检验等多个步骤,这些步骤需要根据具体的工件、机床和材料等因素进行调整。
只有经过认真的计算和精细的加工,才能获得符合要求的弧齿锥齿轮。
Matlab与VB混合编程在弧齿锥齿轮SGM调整卡计算中的应用

加工小轮机床坐标关系【5】5。
由图4可知机床调整参数可由下列公式确定
Eol=R01sin(筋一风1)
(1)
G,:盟掣 Sll-=_—_R—ol—C0—6届■01_
(LZ2,)
(3)
o
S1nOfl
ql=筋+jl
(4)
施施2=Gf一一盂鲁瓦
(L35’)
i‘:2——r'ROollC—OS卢fl
(Lo6,)
Spiral bevel gear SGM adjusmlent card
O引言
弧齿锥齿轮由于原理复杂,其设计和加工过程十 分繁琐,加工过程中的齿形参数和机床调整参数非常 多,所以其调整卡计算经常遇到复杂的数据计算和查 表等问题。Matlab以其科学计算功能的强大和开放式 的开发思想而成为当今最为流行的、最为优秀的科技 应用软件之一,在数值分析、科学计算、算法开发等方 面具有独特的优势,用其进行复杂算法设计和方程组 求解的效率很高,但Matlab也有局限性,一般它不能脱 离Matlab的集成环境,而且生成良好的人机交互图形 界面的功能不强…。VB是一种简单、易学和高效的可 视化软件拉J,但它的计算功能薄弱,因此将Matlab强大 的计算功能与VB在图形用户界面方面的优势结合起 来,可以有效缩短开发周期,提高程序开发的效率。
一1.3681
1.5489
一1.3684
1.5489
从上表的比较中可以看出两者计算得到的大部分 数据还是相同的,只有少数数据存在差异,且差异都在 误差允许范围的之内。
5结论
图5软件输入界面
4应用实例
在图5所示的VB界面中输入齿数、模数、齿面 宽、弧齿角和刀盘半径等基本参数时(其余界面略),系
统计算并输出调整卡参数计算结果,表1是其与商用 软件计算结果的比较(其余计算参数略)。
全工序法弧齿锥齿轮加工参数计算方法

全工序法弧齿锥齿轮加工参数计算方法
全工序法是一种用于弧齿锥齿轮加工的常用方法,它通过一系列工序来逐步完成锥齿轮的加工。
以下是全工序法中常用的弧齿锥齿轮加工参数计算方法:
1.齿轮模数:齿轮模数是弧齿锥齿轮加工的基本参数,表示
齿轮齿数与有效齿轮直径的比值,用M表示。
根据具体
应用需求和设计要求,选择合适的齿轮模数。
2.压力角:压力角是指斜齿轮齿廓与法线之间的夹角,常用
标准值为20度。
选择合适的压力角,以确保齿轮的传动
效果和强度。
3.齿数:根据需要计算齿数。
在弧齿锥齿轮加工中,通常齿
数是通过参考传动比和齿轮齿数之间的关系来计算的。
4.锥度:锥度是指齿轮齿条与齿轮轴的夹角,常用度数表示。
计算锥度的方法包括参考标准值、设计要求和实际使用情
况。
5.齿轮齿宽:齿轮齿宽是指齿轮齿条的宽度,一般由设计要
求和传动功率等因素决定。
6.齿根圆直径:计算齿根圆直径以确定弧齿锥齿轮的基准尺
寸。
齿根圆直径是齿轮齿廓最低点的圆形位置。
7.齿顶圆直径:计算齿顶圆直径以确定弧齿锥齿轮的基准尺
寸。
齿顶圆直径是齿轮齿廓最高点的圆形位置。
8.齿廓修形参数:根据特定设计要求和加工方法,确定齿廓
修形参数,如修形系数和修形位移。
以上仅是全工序法中一些常用的弧齿锥齿轮加工参数计算方法的概述。
在实际应用中,还需结合具体工件的设计要求、加工设备和工艺流程等因素来确定适当的参数值。
弧齿、零度弧齿锥齿轮计算-任意轴交角
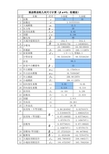
14 齿宽中点螺旋角 15 中点模数 16 中点法向模数 17 中点锥距 18 小端锥距 19 切向变位系数 20 径向变位系数 21 齿顶高 22 齿根高 23 顶隙 24 全齿高 25 工作齿高 26 27 28 齿顶角(不等顶隙) 齿顶角(等顶隙) 齿根角
m em m nm Rm Ri xt x ha hf C
K ψ mn S mn
h am d0
β β
e i
533.4 39.87016633 30.84621438 48.69468613 29.79729163 22.24976736 18.51003688 18.8973945 14.27481083 8.179908056
Pe
se s ne h ne
ht h
θ
a
θ δ δ
f
2.165679711 27.27235224 21.0329108 265.7804032 184.6753387
29 顶锥角(等顶隙) 30 根锥角 31 大端齿顶圆直径 32 小端齿顶圆直径
a
f
d ae d ai
33 冠顶距 34 中点法向齿厚 35 中点法向齿厚半角 36 中点齿厚角系数 37 中点分度圆弦齿厚 38 中点分度圆弦齿高 39 铣刀盘名义直径 40 大端螺旋角 41 小端螺旋角 42 齿距 43 大端分度圆理论弧齿厚 44 大端理论弦齿厚 45 大端理论弦齿高 46 当量齿数 47 48 49 50 51 端面重合度 52 纵向重合度 53 总重合度 54 不根切的许用最大齿根角 55 不产生根切的最少齿数
Zv
at
α
vat
α β
29.69023654 161.6468434 23.95680324 0.418125095 36.92510996 0.644464745 25.43970428 0.4440066
弧齿锥齿轮计算范文

弧齿锥齿轮计算范文1.基本概念:-弧齿锥齿轮:是一种带有锥面的圆锥形齿轮,在用于传动时,锥齿轮的啮合点在轴心线上。
-基本参数:包括齿数、模数、齿顶高系数、齿根高系数等。
-啮合角:两个齿轮齿廓线的交线与轴线间的夹角。
2.弧齿锥齿轮计算的基本公式:-模数m:弧齿锥齿轮齿数与模数的比值。
-齿距p:两个邻齿间的同心圆周弧长。
-齿厚s:齿顶与齿底之间的距离。
-齿顶高h_a:从齿顶到基圆的距离。
-齿根高h_f:从齿底到基圆的距离。
-齿顶宽b:两齿轮在法向上的接触宽度。
-(注:以上参数表示的是单齿齿轮的大小)3.弧齿锥齿轮计算的步骤:a.齿轮参数的确定:确定需求参数,如传递功率、转速比、传动效率、齿轮种类等。
b.模数的选择:应满足传递功率与转速的要求,并考虑加工性与强度。
c.齿数及啮合角的计算:使用基本公式计算齿数和啮合角。
d.齿顶高和齿根高的计算:使用基本公式计算齿顶高和齿根高,考虑强度。
e.齿轮啮合宽度的计算:使用齿顶高和齿根高计算齿轮啮合宽度,与承载能力有关。
f.齿轮等效齿数的计算:计算齿轮的等效齿数,以确定传动比。
g.法向变位系数及挤压系数的计算:根据实际情况计算法向变位系数及挤压系数,控制齿轮传动质量。
h.齿轮加工校核:计算齿轮加工校核参数。
i.绘制齿轮图样:根据以上计算结果,绘制齿轮尺寸图样。
弧齿锥齿轮计算涉及到多个参数和公式的运用,需要根据实际情况进行具体的计算和校核。
以上给出的步骤和基本公式只是一个简单的概述,实际计算中还需要考虑更多的因素,如弯曲应力、接触应力、表面质量等。
因此,在实际应用中,建议根据实际情况进行具体的计算和校核,确保齿轮传动的正常运行。
弧齿锥齿轮和准双曲面齿轮节齿调整计算新方法
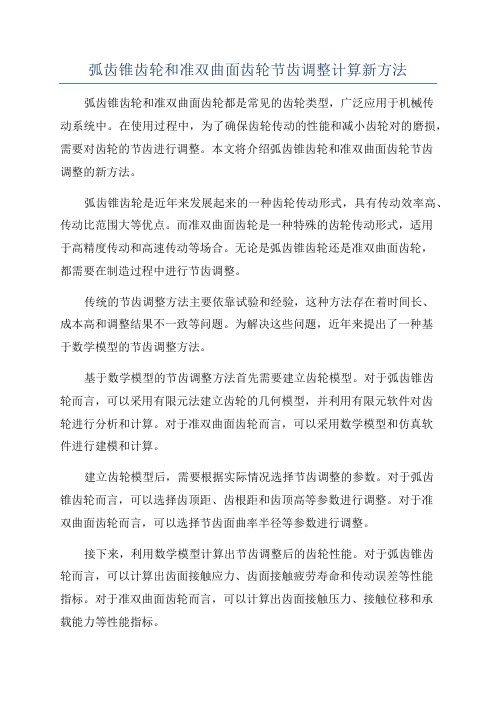
弧齿锥齿轮和准双曲面齿轮节齿调整计算新方法弧齿锥齿轮和准双曲面齿轮都是常见的齿轮类型,广泛应用于机械传动系统中。
在使用过程中,为了确保齿轮传动的性能和减小齿轮对的磨损,需要对齿轮的节齿进行调整。
本文将介绍弧齿锥齿轮和准双曲面齿轮节齿调整的新方法。
弧齿锥齿轮是近年来发展起来的一种齿轮传动形式,具有传动效率高、传动比范围大等优点。
而准双曲面齿轮是一种特殊的齿轮传动形式,适用于高精度传动和高速传动等场合。
无论是弧齿锥齿轮还是准双曲面齿轮,都需要在制造过程中进行节齿调整。
传统的节齿调整方法主要依靠试验和经验,这种方法存在着时间长、成本高和调整结果不一致等问题。
为解决这些问题,近年来提出了一种基于数学模型的节齿调整方法。
基于数学模型的节齿调整方法首先需要建立齿轮模型。
对于弧齿锥齿轮而言,可以采用有限元法建立齿轮的几何模型,并利用有限元软件对齿轮进行分析和计算。
对于准双曲面齿轮而言,可以采用数学模型和仿真软件进行建模和计算。
建立齿轮模型后,需要根据实际情况选择节齿调整的参数。
对于弧齿锥齿轮而言,可以选择齿顶距、齿根距和齿顶高等参数进行调整。
对于准双曲面齿轮而言,可以选择节齿面曲率半径等参数进行调整。
接下来,利用数学模型计算出节齿调整后的齿轮性能。
对于弧齿锥齿轮而言,可以计算出齿面接触应力、齿面接触疲劳寿命和传动误差等性能指标。
对于准双曲面齿轮而言,可以计算出齿面接触压力、接触位移和承载能力等性能指标。
最后,根据计算结果确定最佳的节齿调整方案。
可以比较不同调整方案的性能指标,选择性能最优的方案。
需要注意的是,节齿调整应该尽量保持齿轮的传动效率和稳定性,同时考虑制造成本和可行性等因素。
总之,基于数学模型的节齿调整方法可以提供准确、高效和可行的节齿调整方案。
通过该方法,可以优化齿轮的性能和减小齿轮对的磨损,提高齿轮传动系统的可靠性和使用寿命。
弧齿锥齿轮副参数计算(格里森制等顶隙收缩齿)

名 称 齿数 旋向 大端端面模数 齿形角 齿顶高系数 顶隙系数 轴交角 齿宽中点螺旋角 大端螺旋角 齿数比 变位系数 切向变为系数 分锥角 分度圆直径 分度圆锥距 齿宽系数 齿宽 铣刀盘名义直径 齿顶高 全齿高 符号 Z1 Z2 主动轮 从动轮 m α ha* c* ∑ β m β μ x1 x2 xt δ δ
备
注
单位° 单位° 单位° 单位° 单位° 单位° 单位° 单位°
δ a1 δ a2 δ f1 δ f2 Ak1 Ak2 A1 A2 H1 H2 Rm s1 s2 Zv1 Zv2
按结构确定,一般凑成整数
A1-Ak1 A2-Ak2 19.27414012 2.395974063 1.923715762 28.10354121 42.19802237
f1 f2 a1 a2
数值 1.182150 1.672350 21.81275382 27.63823083 2.971416149 4.199805087 4.199805087 2.971416149 29.20045046 37.97077078 22.02922922 30.79954954 20.04273869 18.12585546
1 2
数值 14 19 左旋 右旋 1.375 20 0.85 0.188 60 35 40.92242589 1.357143 0.18 -0.18 0.00 25.00064537 34.99935463 19.25 26.125 22.77414012 R/3.5~R/3 7 38.1 1.413850 0.923650 2.596000
ε α 端面重合度 1.222798812 对于α =20°可查表 注:只要填写黄色区域,其余将自动生成
- 1、下载文档前请自行甄别文档内容的完整性,平台不提供额外的编辑、内容补充、找答案等附加服务。
- 2、"仅部分预览"的文档,不可在线预览部分如存在完整性等问题,可反馈申请退款(可完整预览的文档不适用该条件!)。
- 3、如文档侵犯您的权益,请联系客服反馈,我们会尽快为您处理(人工客服工作时间:9:00-18:30)。
第15章 弧齿锥齿轮的加工调整计算弧齿锥齿轮的切齿是按照“假想齿轮”的原理进行的,而采用的切齿方法要根据具体情况而定。
15.1 弧齿锥齿轮的切齿原理与刀号对于收缩齿弧齿锥齿轮的加工,通常采用平顶齿轮原理进行加工。
就是在切齿的过程中,假想有一个平顶齿轮与机床摇台同心,它通过机床摇台的转动而与被切齿轮做无隙的啮合。
这个假想平顶齿轮的轮齿表面,是由安装在机床摇台上的铣刀盘刀片切削刃的相对于摇台运动的轨迹表面所代替,如图15-1中所示。
在这个运动过程中,代表假想平顶齿轮轮齿的刀片切削刃就在被切齿轮的轮坯上逐渐地切出齿形。
YS2250(Y225)和Y2280等机床就是按“假想平顶齿轮”原理设计的。
在调整切齿机床的时候,必须使被切齿轮的节锥面与假想平顶齿轮的节锥面相切并做纯滚动。
而切齿时刀顶旋转平面则需和被切齿轮的根锥相切,也就是说,刀盘轴线与根锥母线垂直,而非与节锥母线垂直,如图15-2所示。
所以铣刀盘轴线与被切齿轮的节锥面倾斜了一个大小等于被切齿轮齿根角θf 的角度,使被切齿轮两则齿面的压力角出现了误差,这样就产生了刀号修正问题。
如图15-2,用螺旋角接近900时的情况予以说明刀号与压力角的关系。
由于在切齿时采用了“平顶产形轮”原理,工件是按照根锥角进行安装的,铣刀盘轴线垂直于根锥母线,因而和节锥母线倾斜一个齿根角θf 。
这样,当外切刀片与内切刀片使用相同的压力角时,切出来的齿轮凹面与凸面在节锥上的压力角是不相等的(α”≠α’)。
如果要使轮齿中点处的两侧压力角相等,就需要对刀具的两个侧刃的压力角进行修图15-1弧齿锥齿轮的切齿原理摇台刀盘 被加工齿轮正。
修正时,外侧刃齿形角减少α∆,内侧刃增加α∆。
α∆的确定可按以下公式计算βθαsin f ≈∆ (15-1)其中β代表螺旋角。
由于大轮与小轮具有不同齿根角θf ,所以从严格意义上来讲,在加工大轮与小轮时,相应的切齿刀盘的刀刃修正量α∆也应不同。
按照现有的刀号制度,将α∆的单位设置为分,并规定10分为一号,则刀号的计算公式为小轮理论刀盘刀号βθβθαsin 610sin 6010c 111*1f f ==∆= (15-2a)大轮理论刀盘刀号βθβθαsin 610sin 6010c 222*2f f ==∆=(15-2b) 所以,在用双面法分别加工大轮与小轮时,应该用不同刀号的刀盘。
但是,制造各种刀号的刀盘,也不太现实。
为了简化刀具规格,制定了标准刀号规格,常见的刀号如表15-1所示。
选择时应尽量选择与理论刀号相近的刀盘。
例如,压力角α=200,刀号c 2*=12的刀盘,其内刀齿形角为220,外刀齿形角为180。
对于弧齿锥齿轮内刀齿形角总是大于外刀齿形角(绝对值)。
常见刀号对应的齿形角如表15-1所示。
刀盘直径根据齿轮的中点锥距确定,选取的合适与否将影响被加工齿轮的轮齿的收缩方式。
刀盘直径计算公式如下D 0 =180cos 1sin 20βαθβg t z R s ∑-(15-3)表15-1 常用刀号及其对应的齿形角常用刀号3.54.55.567.5912内外齿形角 20035’19025’20045’19015’20055’19005’21019021045’18045’21030’18030’220180图15-2刀盘齿形角对轮齿压力角的影响θfδf由上式可以看出,在螺旋角350附近,刀盘公称直径与中点锥距相近。
刀盘的旋向的选择,应该使得在加工时形成顺铣。
刀尖圆角半径可以查表选择。
刀顶距W 2根据被加工齿轮的齿槽宽与加工余量进行调整。
W 2根据要控制的弧齿厚来取,其理论值为αtg h s R R W f e em2122-=(15-4) 15.2弧齿锥齿轮的切齿方法弧齿锥齿轮的单齿切削方法分为成形法和展成法两大类。
15.2.1成形法用成形法加工的大齿轮齿廓与刀具切削刃的形状一样。
渐开线齿廓的曲率和它的基圆大小有关,基圆越大、齿廓曲率就越小,渐开线就直些;当基圆足够大时,渐开线就接近于直线。
而齿轮的基圆大小是由模数m 、齿数z 和压力角α的余弦大小来决定的。
模数和压力角一定时,齿数愈多,基圆直径就越大,相应的齿廓曲率越小,也就是齿廓越接近于直线。
对于螺旋锥齿轮,传动比也是影响因素之一,当传动比大一些时,大轮的齿廓就更直一些。
小轮齿数(z 1)一定时,传动比越大,大轮齿数也就越多,这时大轮的当量圆柱齿轮的基圆直径也越大,其齿廓接近于直线形,采用成形加工比较方便. 当锥齿轮传动比大于2.5时,大轮的节锥角往往在700以上,大轮就可采用成形加工。
同时,为了保证其正确啮合,相配小轮的齿廓应加以相应的修正,用展成法加工,这种组合切齿方法叫半滚切法或成形法。
此法生产效率较高,适于大批量生产。
半滚切法用以下三种方法加工:1.用普通铣刀盘加工,齿廓为直线形,用于被切齿轮节角大于45︒的粗切或传动比大于2.5,节角大于70︒的大轮的精切,如图15-3。
2.在专用机床上以圆盘拉刀加工,简称拉齿,齿廓是直线形的,粗、精拉可一次完成,适用于传动比大于2.5的大轮。
图15-3 成形法刀盘位置图图15-4 螺旋成形法刀盘位置图3.螺旋成形法是半滚切法的特殊形式。
在专用机床上,用特殊的圆拉刀盘,精加工传动比大于2.5齿轮副中的大轮,齿廓是直线形的。
如图15-4。
切齿时,刀盘安装轴线垂直于被切齿轮的面锥母线,刀盘除具有圆周方向的旋转运动外,还沿其自身轴向作往复运动,每个刀片通过齿槽的同时,刀盘轴向往复一次,而使刀齿顶刃始终沿着被切齿轮齿根切削。
由于大齿轮的顶锥母线与小齿轮的根锥母线平行,所以大轮圆盘拉刀与小轮铣刀盘的轴线平行。
螺旋成形法切出的轮齿纵向曲面是一个有规则的、可展的和同向弯曲的渐开螺旋面,它得到的是收缩齿。
采用螺旋成型法加工的大、小齿轮,不仅在齿宽中点处,而且在齿宽任意一点处,相啮合的凸凹面的压力角都相等,这样就提高了大小齿轮的啮合质量,并且对载荷变化、安装误差不敏感。
载荷增加时,接触区长度不变,其位置移向大端。
螺旋成形法是当前弧齿锥齿轮和双曲线齿轮切齿方法中较完善的一种,但由于螺旋成形法拉齿设备调整较复杂,目前实际生产中并没有大规模应用。
15.2.2 展成法(滚切法)展成法是被切齿轮与旋转着的铣刀盘(摇台)按照一定的比例关系进行滚切运动,加工出来的齿廓是渐开线形的,它是由刀片切削刃顺序位置的包络线形成的,如图15-5所示,在切齿过程中刀片的顺序位置如图15-6所示.切削时,先切一面(如图的上侧面)的齿顶和另一面(如图的下侧面)的齿根:在滚切过程中,逐渐移向上侧面的齿根和下侧面的齿顶,最后脱离切削,如同一对轮齿的啮合运动一样.用此法加工的有以下两种常用的齿线形状:1.在YS2250、Y2280或格利森16号等机床上,用刀片切削刃为直线的铣刀盘,齿长方向曲线是圆弧的一部分。
2.在奥利康2号等机床上用刀片切削刃为直线的铣刀盘用连续切削法加工,齿长方向曲线是延伸外摆线的一部分。
15.2.3 弧齿锥齿轮的加工方法弧齿锥齿轮的切齿方法组合很多.粗切多数是用双面刀盘同时切齿槽的两侧齿面。
精切常用三种方法,即:单面切削法、双面切削法和双重双面法。
这些方法的特性、优缺点和适用范围列于表15-2中。
选择切齿方法时,应按具体情况。
诸如根据现有的切齿机床和刀盘的数量以及被加工齿轮的精度要求等,做出符合客观实际的决定。
如果齿轮的加工精度要求较高,产量较大、机床与刀盘齐全时,采用固定安装法比较合适。
精度要求不太高的齿轮可用单刀号单面切削法。
半滚切和螺旋成形法适宜于大批量生产。
图15-5 图15-6表 15-2 弧齿锥齿轮切齿方法表15.3 加工参数与机床的调整参数对于螺旋锥齿轮加工,固定安装法有以下几种组合:大轮用成形法加工,小轮用刀倾法加工称为SFT、HFT法。
大轮用滚切法加工,小轮用变性法加工称为HGM、HGM法。
三个英文字母表示的含义为第一个字母表示被加工齿轮的类型,S—表示弧齿锥齿轮(Spiral bevel Gears),H —表示准双曲面齿轮(Hypoid Gears)。
第二个字母表示大轮的加工方法,G——表示展成法加工(Generated),F—表示成形法加工(Formate)。
第三个字母表示小轮的加工方法,T—表示刀倾法(Tite),M—表示变性法(ModifiedRoll)。
把上述两种方法做一下调整,重新组合,则可构成SGT、HGT、SFM、HFM两类四种方法。
这里要说明的是,通常在应用刀倾的时候,不应用变性;在应用变性的时候,不应用刀倾。
针对不同的加工方法,加工参数上也有一些差别。
在机床上对应的有不同的调整位置(以下用“加工参数”指代锥齿轮加工所对应的基本参数,这些参数与机床类型无关,“调整参数”指代针对各类机床的调整位置的参数,是加工参数在机床上的具体现)。
这些参数与机床调整参数对应关系如表15-6所示。
小轮加工参数列表大轮加工参数列表图15-7 机床调整参数刀盘的位置参数——刀位刀盘的位置由径向刀位S d 与角向刀位q 两个参数确定,总称刀位。
这是一种极坐标表示方法。
也可以用直角坐标系垂直刀位V 、水平刀位H 表示。
但本质上是一致的。
两种刀位表示方法的之间的关系如下:22d H V S += HVtg q 1-= 不同的机床有着不同的设定方法,但是都要实现刀盘与工件间正确的相对位置关系。
例如,No.116、Y2280等机床通过偏心鼓轮的偏心角调整径向刀位S d ,通过摇台角体现角向刀位q 。
见图15-8、15-9。
而No.607、No.609拉齿机则通过量棒尺寸控制垂直刀位V 、水平刀位H 。
图15-8 刀位的表示以Y2280偏心机构为例,如图15-9, O m 为机床摇台中心,O e 为偏心鼓轮中心,O d (O d ’)为刀盘中心,在初始位置O d 与O m 重合,当偏心鼓轮旋转β角后,可使刀盘中心处于O d 的位置。
实现径向刀位S d ,即O m O d =S d 。
在d e m O O O ∆中KSd =2sin β,所以偏心角KS2sin d 1-=βK 为机床常数,对于Y2280机床K=340。
偏心鼓轮旋转β角后,刀位中心位于O d 的位置,要想得到正确的角向刀位q ,还需使摇台旋转一个角度Q 到达O d ’的位置,即为摇台角Q ,由图中可以看出⎪⎪⎭⎫⎝⎛-+±=右旋左旋q 2Q β水平轮位X G1:摇台中心到工件箱主轴端面的距离,为图纸中的安装距。
垂直轮位E m1:被切齿轮的中心线相对于摇台中心线的垂直偏置量。
床位X B1:控制切齿时的深度。
轮坯安装角δm 1:轮坯根锥角。
此外,对于No.116等机床还有刀倾角I X 、刀转角J 。
参见第16章。
二阶变性系数与变形凸轮:变性法是指小轮的滚切过程中,摇台与被切小轮之间的滚比是瞬时变化的。