钢铁冶金概论论文-粉末冶金工艺
粉末冶金介绍范文
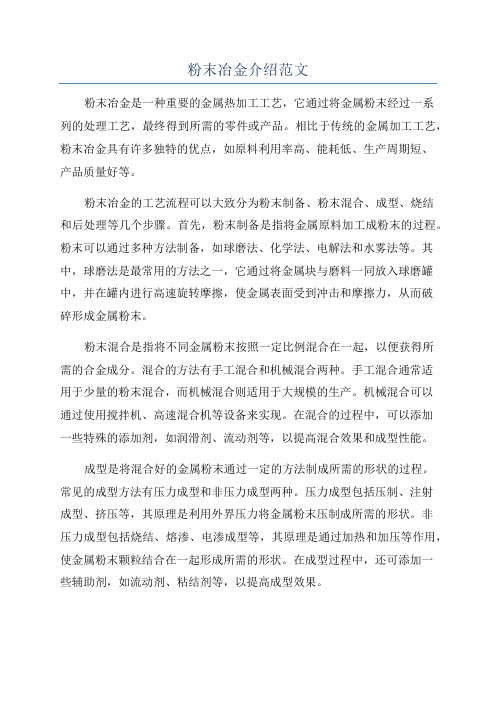
粉末冶金介绍范文粉末冶金是一种重要的金属热加工工艺,它通过将金属粉末经过一系列的处理工艺,最终得到所需的零件或产品。
相比于传统的金属加工工艺,粉末冶金具有许多独特的优点,如原料利用率高、能耗低、生产周期短、产品质量好等。
粉末冶金的工艺流程可以大致分为粉末制备、粉末混合、成型、烧结和后处理等几个步骤。
首先,粉末制备是指将金属原料加工成粉末的过程。
粉末可以通过多种方法制备,如球磨法、化学法、电解法和水雾法等。
其中,球磨法是最常用的方法之一,它通过将金属块与磨料一同放入球磨罐中,并在罐内进行高速旋转摩擦,使金属表面受到冲击和摩擦力,从而破碎形成金属粉末。
粉末混合是指将不同金属粉末按照一定比例混合在一起,以便获得所需的合金成分。
混合的方法有手工混合和机械混合两种。
手工混合通常适用于少量的粉末混合,而机械混合则适用于大规模的生产。
机械混合可以通过使用搅拌机、高速混合机等设备来实现。
在混合的过程中,可以添加一些特殊的添加剂,如润滑剂、流动剂等,以提高混合效果和成型性能。
成型是将混合好的金属粉末通过一定的方法制成所需的形状的过程。
常见的成型方法有压力成型和非压力成型两种。
压力成型包括压制、注射成型、挤压等,其原理是利用外界压力将金属粉末压制成所需的形状。
非压力成型包括烧结、熔渗、电渗成型等,其原理是通过加热和加压等作用,使金属粉末颗粒结合在一起形成所需的形状。
在成型过程中,还可添加一些辅助剂,如流动剂、粘结剂等,以提高成型效果。
烧结是将成形好的金属粉末在一定的温度下进行加热处理,使其颗粒结合在一起形成致密的块体。
由于金属粉末颗粒之间存在一定的空隙,必须通过烧结工艺来实现颗粒之间的结合。
烧结温度通常为金属的熔点以下,以避免金属的熔化。
烧结温度和时间可以根据金属粉末的性质和产品要求来确定。
在烧结过程中,还需进行一些辅助处理,如减压、加压、保护气氛等,以提高烧结效果和产品质量。
最后,通过后处理工艺对烧结好的金属块进行进一步的处理,以获得所需的产品。
粉末冶金新工艺1
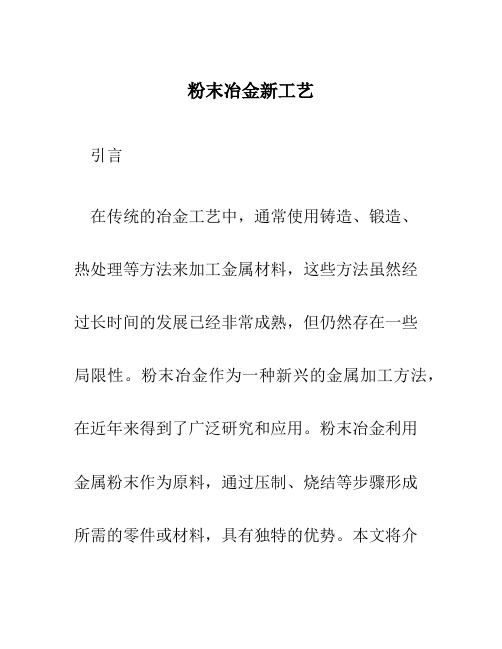
粉末冶金新工艺引言在传统的冶金工艺中,通常使用铸造、锻造、热处理等方法来加工金属材料,这些方法虽然经过长时间的发展已经非常成熟,但仍然存在一些局限性。
粉末冶金作为一种新兴的金属加工方法,在近年来得到了广泛研究和应用。
粉末冶金利用金属粉末作为原料,通过压制、烧结等步骤形成所需的零件或材料,具有独特的优势。
本文将介绍一种新的粉末冶金工艺——粉末冶金新工艺1,以及其在金属材料加工中的应用。
粉末冶金新工艺1的原理和步骤粉末冶金新工艺1是一种基于烧结的加工方法,其具体步骤如下:1.原料准备:选取合适的金属粉末作为原料,根据所需产品的要求选择不同种类和粒度的粉末,并进行预处理,如调整湿度和筛分等。
2.混合与成型:将不同种类的金属粉末按照一定的比例混合,并通过压制成型的方式得到所需形状的绿体。
3.烧结:将成型后的绿体在高温条件下进行烧结,使粉末颗粒间相互结合,形成致密的金属材料。
在烧结过程中,可根据需要添加适量的添加剂来改善材料的性能。
4.后续处理:烧结后的材料可以进行一些后续处理步骤,如热处理、表面处理等,以进一步改善材料的性能和外观。
粉末冶金新工艺1的优势和应用粉末冶金新工艺1相比传统的金属加工方法,具有以下优势:•原料利用率高:粉末冶金可以有效利用金属粉末,几乎没有材料浪费。
•复杂形状制造:通过粉末冶金新工艺1,可以制造出复杂形状的零件和材料,提供更大的设计自由度。
•材料性能可调控:可以通过调整不同金属粉末的比例和添加剂的种类和含量,来调控材料的物理、化学和机械性能。
•节能环保:相比传统的金属加工方法,粉末冶金新工艺1在能源消耗和环境污染方面都更加节约和环保。
粉末冶金新工艺1在金属材料加工中有着广泛的应用,主要包括以下几个方面:1.制造耐磨材料:通过粉末冶金新工艺1,可以制造出各种耐磨材料,如高硬度的刀具、磨料和磨损件等。
2.制造高强度材料:通过控制金属粉末的成分和烧结工艺,可以制造出高强度的材料,常用于航空航天、汽车和机械工程等领域。
粉末冶金制备工艺
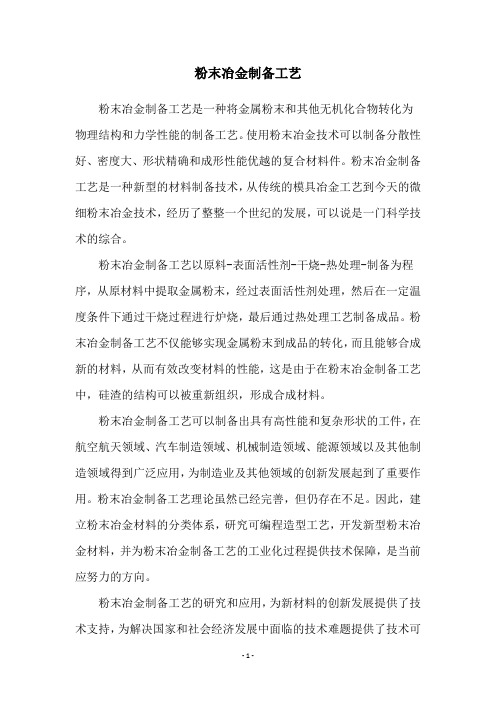
粉末冶金制备工艺粉末冶金制备工艺是一种将金属粉末和其他无机化合物转化为物理结构和力学性能的制备工艺。
使用粉末冶金技术可以制备分散性好、密度大、形状精确和成形性能优越的复合材料件。
粉末冶金制备工艺是一种新型的材料制备技术,从传统的模具冶金工艺到今天的微细粉末冶金技术,经历了整整一个世纪的发展,可以说是一门科学技术的综合。
粉末冶金制备工艺以原料-表面活性剂-干烧-热处理-制备为程序,从原材料中提取金属粉末,经过表面活性剂处理,然后在一定温度条件下通过干烧过程进行炉烧,最后通过热处理工艺制备成品。
粉末冶金制备工艺不仅能够实现金属粉末到成品的转化,而且能够合成新的材料,从而有效改变材料的性能,这是由于在粉末冶金制备工艺中,硅渣的结构可以被重新组织,形成合成材料。
粉末冶金制备工艺可以制备出具有高性能和复杂形状的工件,在航空航天领域、汽车制造领域、机械制造领域、能源领域以及其他制造领域得到广泛应用,为制造业及其他领域的创新发展起到了重要作用。
粉末冶金制备工艺理论虽然已经完善,但仍存在不足。
因此,建立粉末冶金材料的分类体系,研究可编程造型工艺,开发新型粉末冶金材料,并为粉末冶金制备工艺的工业化过程提供技术保障,是当前应努力的方向。
粉末冶金制备工艺的研究和应用,为新材料的创新发展提供了技术支持,为解决国家和社会经济发展中面临的技术难题提供了技术可能性,为社会及经济发展提供了有效和有益的支持。
粉末冶金制备工艺的不断发展,在国家科技技术和工业制造工艺方面有着重大而深远的影响。
从长远来看,在我国粉末冶金制备工艺的研究和实现中,应践行可持续发展的经济发展理念,落实“节约资源、绿色发展”的科学发展观,以提高节能效果、节约能源、降低污染,实现可持续发展。
同时,在研究和实践中,要提高科技技能水平,开发适应经济发展和社会需求的复合材料,不断推动粉末冶金制备工艺的发展,为国家和社会的可持续发展进程做出积极的贡献。
粉末冶金技术论文
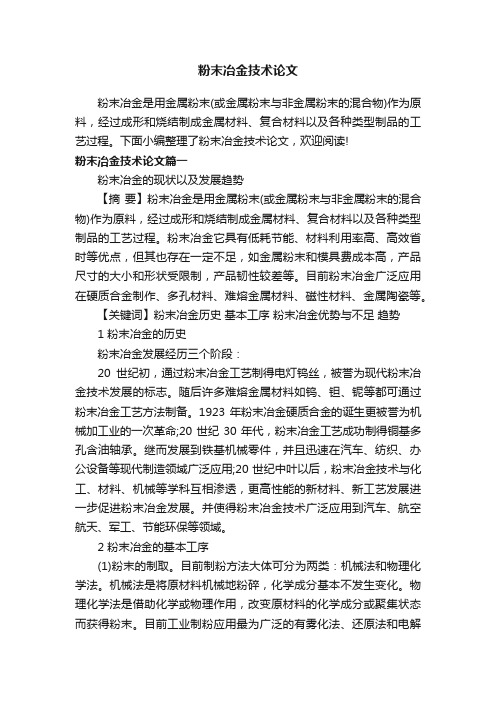
粉末冶金技术论文粉末冶金是用金属粉末(或金属粉末与非金属粉末的混合物)作为原料,经过成形和烧结制成金属材料、复合材料以及各种类型制品的工艺过程。
下面小编整理了粉末冶金技术论文,欢迎阅读!粉末冶金技术论文篇一粉末冶金的现状以及发展趋势【摘要】粉末冶金是用金属粉末(或金属粉末与非金属粉末的混合物)作为原料,经过成形和烧结制成金属材料、复合材料以及各种类型制品的工艺过程。
粉末冶金它具有低耗节能、材料利用率高、高效省时等优点,但其也存在一定不足,如金属粉末和模具费成本高,产品尺寸的大小和形状受限制,产品韧性较差等。
目前粉末冶金广泛应用在硬质合金制作、多孔材料、难熔金属材料、磁性材料、金属陶瓷等。
【关键词】粉末冶金历史基本工序粉末冶金优势与不足趋势1 粉末冶金的历史粉末冶金发展经历三个阶段:20世纪初,通过粉末冶金工艺制得电灯钨丝,被誉为现代粉末冶金技术发展的标志。
随后许多难熔金属材料如钨、钽、铌等都可通过粉末冶金工艺方法制备。
1923年粉末冶金硬质合金的诞生更被誉为机械加工业的一次革命;20世纪30年代,粉末冶金工艺成功制得铜基多孔含油轴承。
继而发展到铁基机械零件,并且迅速在汽车、纺织、办公设备等现代制造领域广泛应用;20世纪中叶以后,粉末冶金技术与化工、材料、机械等学科互相渗透,更高性能的新材料、新工艺发展进一步促进粉末冶金发展。
并使得粉末冶金技术广泛应用到汽车、航空航天、军工、节能环保等领域。
2 粉末冶金的基本工序(1)粉末的制取。
目前制粉方法大体可分为两类:机械法和物理化学法。
机械法是将原材料机械地粉碎,化学成分基本不发生变化。
物理化学法是借助化学或物理作用,改变原材料的化学成分或聚集状态而获得粉末。
目前工业制粉应用最为广泛的有雾化法、还原法和电解法;而沉积法(气相或液相)在特殊应用时也很重要。
(2)粉末成型。
成型是使金属粉末密实成具有一定形状、尺寸、孔隙度和强度坯块的工艺过程。
成型分普通模压成型和特殊成型两类。
粉末冶金工艺
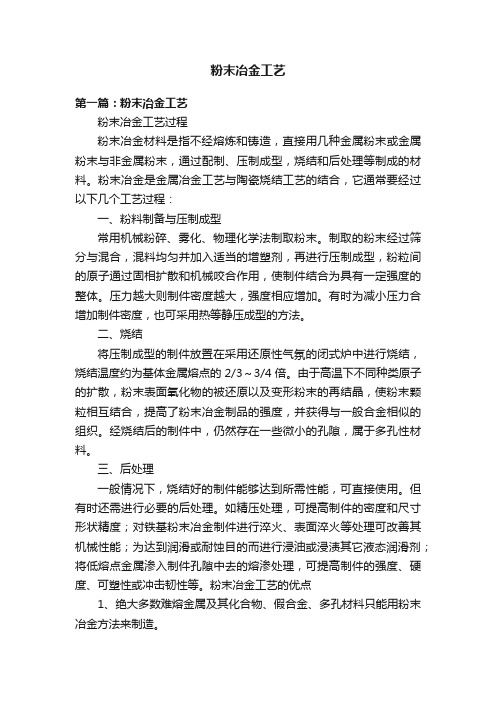
粉末冶金工艺第一篇:粉末冶金工艺粉末冶金工艺过程粉末冶金材料是指不经熔炼和铸造,直接用几种金属粉末或金属粉末与非金属粉末,通过配制、压制成型,烧结和后处理等制成的材料。
粉末冶金是金属冶金工艺与陶瓷烧结工艺的结合,它通常要经过以下几个工艺过程:一、粉料制备与压制成型常用机械粉碎、雾化、物理化学法制取粉末。
制取的粉末经过筛分与混合,混料均匀并加入适当的增塑剂,再进行压制成型,粉粒间的原子通过固相扩散和机械咬合作用,使制件结合为具有一定强度的整体。
压力越大则制件密度越大,强度相应增加。
有时为减小压力合增加制件密度,也可采用热等静压成型的方法。
二、烧结将压制成型的制件放置在采用还原性气氛的闭式炉中进行烧结,烧结温度约为基体金属熔点的2/3~3/4倍。
由于高温下不同种类原子的扩散,粉末表面氧化物的被还原以及变形粉末的再结晶,使粉末颗粒相互结合,提高了粉末冶金制品的强度,并获得与一般合金相似的组织。
经烧结后的制件中,仍然存在一些微小的孔隙,属于多孔性材料。
三、后处理一般情况下,烧结好的制件能够达到所需性能,可直接使用。
但有时还需进行必要的后处理。
如精压处理,可提高制件的密度和尺寸形状精度;对铁基粉末冶金制件进行淬火、表面淬火等处理可改善其机械性能;为达到润滑或耐蚀目的而进行浸油或浸渍其它液态润滑剂;将低熔点金属渗入制件孔隙中去的熔渗处理,可提高制件的强度、硬度、可塑性或冲击韧性等。
粉末冶金工艺的优点1、绝大多数难熔金属及其化合物、假合金、多孔材料只能用粉末冶金方法来制造。
2、由于粉末冶金方法能压制成最终尺寸的压坯,而不需要或很少需要随后的机械加工,故能大大节约金属,降低产品成本。
用粉末冶金方法制造产品时,金属的损耗只有1-5%,而用一般熔铸方法生产时,金属的损耗可能会达到80%。
3、由于粉末冶金工艺在材料生产过程中并不熔化材料,也就不怕混入由坩埚和脱氧剂等带来的杂质,而烧结一般在真空和还原气氛中进行,不怕氧化,也不会给材料任何污染,故有可能制取高纯度的材料。
粉末冶金及模具设计论文
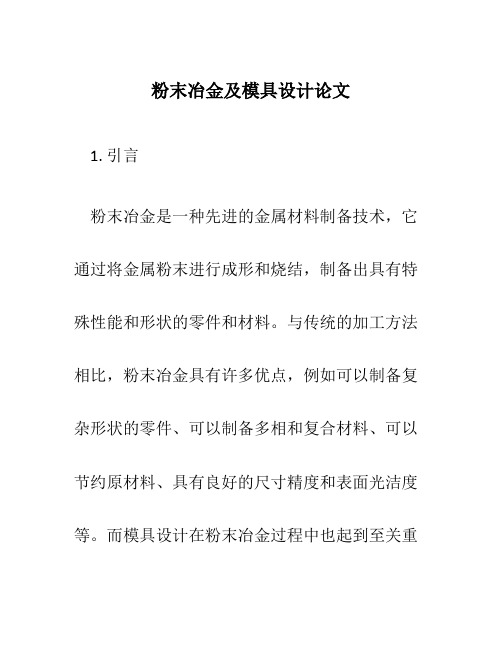
粉末冶金及模具设计论文1. 引言粉末冶金是一种先进的金属材料制备技术,它通过将金属粉末进行成形和烧结,制备出具有特殊性能和形状的零件和材料。
与传统的加工方法相比,粉末冶金具有许多优点,例如可以制备复杂形状的零件、可以制备多相和复合材料、可以节约原材料、具有良好的尺寸精度和表面光洁度等。
而模具设计在粉末冶金过程中也起到至关重要的作用,它直接影响着成形零件的质量和性能。
因此,研究粉末冶金及模具设计对于提高金属材料的制备效率和性能具有重要的意义。
2. 粉末冶金的工艺过程粉末冶金的工艺过程包括粉末的选择和处理、粉末成形和烧结等步骤。
2.1 粉末的选择和处理粉末的选择和处理是粉末冶金过程的第一步。
在粉末的选择中,需要考虑金属粉末的纯度、粒度和形状等因素。
高纯度的金属粉末可以得到高质量的成品,而合适的粒度和形状可以提高成形性能和烧结性能。
在粉末的处理中,通常包括混合、干燥和筛分等步骤。
混合是将所需金属粉末按一定比例混合以获得所需的合金成分,干燥则是去除粉末中的水分,筛分则是按照所需粒度进行筛选。
2.2 粉末成形粉末成形是指将混合并处理好的粉末以一定的压力加工成形。
常见的粉末成形方法包括压制、注射成形和挤压成形等。
压制是将粉末放置于模具中,然后施加压力使其形成一定形状的零件。
注射成形则是将粉末加入模具中,然后通过注射机将粉末充填模腔,最后再施加压力形成零件。
挤压成形是将粉末放置于模具中,然后通过挤压机施加压力使其在模腔中流动并形成零件。
2.3 烧结烧结是粉末冶金过程中的关键步骤,它是指将成形好的粉末在一定条件下进行加热处理,使其颗粒之间产生扩散和结合从而形成致密的固体材料。
烧结温度、时间和气氛都会影响烧结过程的质量和性能。
3. 模具设计在粉末冶金中的应用模具设计在粉末冶金中起到至关重要的作用,它直接影响着成形零件的质量和性能。
模具设计主要包括模具材料的选择、模腔设计和模具加工工艺的确定。
3.1 模具材料的选择模具材料的选择对于模具的寿命和成形零件的质量都有很大的影响。
《粉末冶金》结课论文

粉末冶金高速压制技术的研究现状及发展摘要:介绍一种低成本高密度粉末冶金零件成形技术一高速压制技术,通过阐述该技术的特点、原理、关键技术分析,指出其材料性能和应用前景以及高速压制技术目前存在的问题。
关键词:粉末冶金;高速压制;高密度粉末冶金技术以其低成本、近净形等加工特点在许多领域得到广泛应用。
密度对粉末冶金材料至关重要,它显著影响结构材料的力学性能,尤其是疲劳性能。
因此提高材料密度是粉末冶金的主要研究内容之一。
近年来粉末冶金新技术、新工艺层出不穷,温压技术、表面致密技术、高速压制技术等新技术的出现,使得粉末冶金技术不断取得突破性进展。
高速压制技术(high velocity compaction,简称HVC)是瑞典Hoganas公司在2001年6月主持召开的专门会议所推介的一种新技术,它所使用的重锤能产生强烈的冲击波,能在0.02s内将能量通过压模传给粉末进行致密化,间隔0.3s 的一个个附加的冲击波可将密度不断提高,使材料的性能更加优异,成本更加低廉,采用该技术可利用比传统压制小的设备生产超大零件。
HVC可能是粉末冶金工业寻求低成本高密度材料加工技术的又一次新突破。
1 高速压制技术的特点1.1高密度高性能HVC技术通过强烈的冲击波进行压制,使P/M零件达到高密度,它不仅可以使零件高致密化,而且可以使其密度均匀化。
与传统压制相比,HVC技术可使压坯密度提高0.3 g/cm3以上,如右图1所示。
典型的齿轮冲击试验表明其密度变化小于0.01 g/cm3。
将高速压制与其它工艺相结合,可使粉末压坯密度更高。
以铁基压坯为例,HVC技术与模壁润滑相结合,压坯密度可达7.6 g/cm3,与模壁润滑和温压结合的压坯密度达7.7g/cm3,若采用高速复压复烧工艺,压坯密度可达7.8g/cm3,接近全致密。
密度对提高材料性能的影响显而易见,如基于D.AE和Astaloy CrM的、采用HVC技术制备的材料与传统压制技术制备的材料相比,抗拉强度和屈服强度均提高20%~25%,其他各项性能指标也均有较大提高。
粉末冶金论文
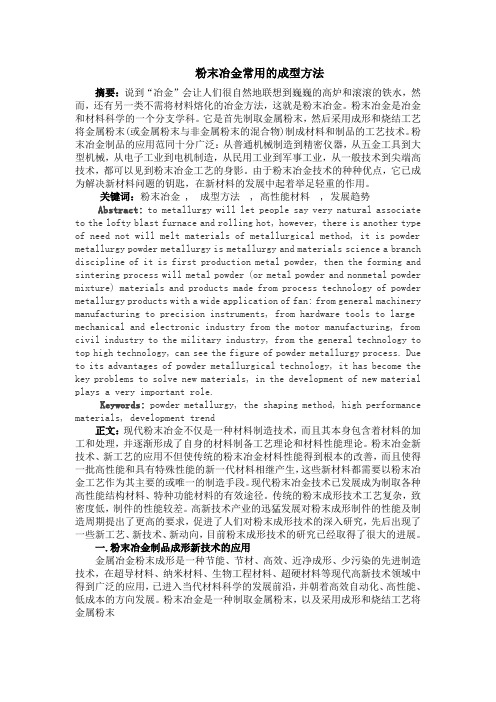
粉末冶金常用的成型方法摘要:说到“冶金”会让人们很自然地联想到巍巍的高炉和滚滚的铁水,然而,还有另一类不需将材料熔化的冶金方法,这就是粉末冶金。
粉末冶金是冶金和材料科学的一个分支学科。
它是首先制取金属粉末,然后采用成形和烧结工艺将金属粉末(或金属粉末与非金属粉末的混合物)制成材料和制品的工艺技术。
粉末冶金制品的应用范同十分广泛:从普通机械制造到精密仪器,从五金工具到大型机械,从电子工业到电机制造,从民用工业到军事工业,从一般技术到尖端高技术,都可以见到粉末冶金工艺的身影。
由于粉末冶金技术的种种优点,它已成为解决新材料问题的钥匙,在新材料的发展中起着举足轻重的作用。
关键词:粉末冶金 , 成型方法 , 高性能材料 , 发展趋势Abstract: to metallurgy will let people say very natural associate to the lofty blast furnace and rolling hot, however, there is another type of need not will melt materials of metallurgical method, it is powder metallurgy powder metallurgy is metallurgy and materials science a branch discipline of it is first production metal powder, then the forming and sintering process will metal powder (or metal powder and nonmetal powder mixture) materials and products made from process technology of powder metallurgy products with a wide application of fan: from general machinery manufacturing to precision instruments, from hardware tools to large mechanical and electronic industry from the motor manufacturing, from civil industry to the military industry, from the general technology to top high technology, can see the figure of powder metallurgy process. Due to its advantages of powder metallurgical technology, it has become the key problems to solve new materials, in the development of new material plays a very important role.Keywords: powder metallurgy, the shaping method, high performance materials, development trend正文:现代粉末冶金不仅是一种材料制造技术,而且其本身包含着材料的加工和处理,并逐渐形成了自身的材料制备工艺理论和材料性能理论。
- 1、下载文档前请自行甄别文档内容的完整性,平台不提供额外的编辑、内容补充、找答案等附加服务。
- 2、"仅部分预览"的文档,不可在线预览部分如存在完整性等问题,可反馈申请退款(可完整预览的文档不适用该条件!)。
- 3、如文档侵犯您的权益,请联系客服反馈,我们会尽快为您处理(人工客服工作时间:9:00-18:30)。
粉末冶金工艺学生姓名:年级:学号:摘要:粉末冶金是制取金属或用金属粉末(或金属粉末与非金属粉末的混合物)作为原料,经过成形和烧结,制造金属材料、复合以及各种类型制品的工艺技术。
粉末冶金法与生产陶瓷有相似的地方,因此,一系列粉末冶金新技术也可用于陶瓷材料的制备。
由于粉末冶金技术的优点,它已成为解决新材料问题的钥匙,在新材料的发展中起着举足轻重的作用。
关键词:粉末冶金高密度硬质合金粉末高速钢前言我国粉末冶金行业已经经过了近60年的发展,经历了从无到有、多领域发展。
但与国外的同行业仍存在以下几方面的差距:(1)企业多,规模小,经济效益与国外企业相差很大。
(2)产品交叉,企业相互压价,竞争异常激烈。
(3)多数企业缺乏技术支持,研发能力落后,产品档次低,难以与国外竞争。
(4)再投入缺乏与困扰。
(5)工艺装备、配套设施落后。
(6)产品出口少,贸易渠道不畅。
随着我国加入WTO以后,以上种种不足和弱点将改善,这是因为加入WTO后,市场逐渐国际化,粉末冶金市场将得到进一步扩大的机会;而同时随着国外资金和技术的进入,粉末冶金及相关的技术水平也必将得到提高和发展。
【1】【2】【3】1.粉末冶金基础【4】1.1粉末的化学成分及性能尺寸小于1mm的离散颗粒的集合体通常称为粉末,其计量单位一般是以微米(μm)或纳米(nm)。
1.1.1粉末的化学成分常用的金属粉末有铁、铜、铝等及其合金的粉末,要求其杂质和气体含量不超过1%~2%,否则会影响制品的质量。
1.1.2粉末的物理性能(1)粒度及粒度分布粉料中能分开并独立存在的最小实体为单颗粒。
实际的粉末往往是团聚了的颗粒,即二次颗粒。
实际的粉末颗粒体中不同尺寸所占的百分比即为粒度分布。
(2)颗粒形状即粉末颗粒的外观几何形状。
常见的有球状、柱状、针状、板状和片状等,可以通过显微镜的观察确定。
(3)比表面积即单位质量粉末的总表面积,可通过实际测定。
比表面积大小影响着粉末的表面能、表面吸附及凝聚等表面特性。
1.1.3粉末的工艺性能粉末的工艺性能包括流动性、填充特性、压缩性及成形性等。
(1)填充特性指在没有外界条件下,粉末自由堆积时的松紧程度。
常以松装密度或堆积密度表示。
粉末的填充特性与颗粒的大小、形状及表面性质有关。
(2)流动性指粉末的流动能力,常用50克粉末从标准漏斗流出所需的时间表示。
流动性受颗粒粘附作用的影响。
(3)压缩性表示粉末在压制过程中被压紧的能力,用规定的单位压力下所达到的压坯密度表示,在标准模具中,规定的润滑条件下测定。
影响粉末压缩性的因素有颗粒的塑性或显微硬度,塑性金属粉末比硬、脆材料的压缩性好;颗粒的形状和结构也影响粉末的压缩性。
(4)成形性指粉末压制后,压坯保持既定形状的能力,用粉末能够成形的最小单位压制压力表示,或用压坯的强度来衡量。
成形性受颗粒形状和结构的影响。
1.2粉末冶金的机理1.2.1压制的机理压制就是在外力作用下,将模具或其它容器中的粉末紧密压实成预定形状和尺寸压坯的工艺过程。
钢模冷压成形过程如图7.1.2所示。
粉末装入阴模,通过上下模冲对其施压。
在压缩过程中,随着粉末的移动和变形,较大的空隙被填充,颗粒表面的氧化膜破碎,颗粒间接触面积增大,使原子间产生吸引力且颗粒间的机械楔合作用增强,从而形成具有一定密度和强度的压坯。
1.2.2等静压制压力直接作用在粉末体或弹性模套上,使粉末体在同一时间内各个方向上均衡受压而获得密度分布均匀和强度较高的压坯的过程。
按其特性分为冷等静压制和热等静压制两大类。
(1)冷等静压制即在室温下等静压制,液体为压力传递媒介。
将粉末体装入弹性模具内,置于钢体密封容器内,用高压泵将液体压入容器,利用液体均匀传递压力的特性,使弹性模具内的粉末体均匀受压。
因此,冷等静压制压坯密度高,较均匀,力学性能较好,尺寸大且形状复杂,已用于棒材、管材和大型制品的生产。
(2)热等静压制把粉末压坯或装入特制容器内的粉末体置入热等静压机高压容器中,施以高温和高压,使这些粉末体被压制和烧结成致密的零件或材料的过程。
在高温下的等静压制,可以激活扩散和蠕变现象的发生,促进粉末的原子扩散和再结晶及以极缓慢的速率进行塑性变形,气体为压力传递媒介。
粉末体在等静压高压容器内同一时间经受高温和高压的联合作用,强化了压制与烧结过程,制品的压制压力和烧结温度均低于冷等静压制,制品的致密度和强度高,且均匀一致,晶粒细小,力学性能高,消除了材料内部颗粒间的缺陷和孔隙,形状和尺寸不受限制。
但热等静压机价格高,投资大。
热等静压制已用于粉末高速钢、难熔金属、高温合金和金属陶瓷等制品的生产。
1.2.3粉末轧制将粉末通过漏斗喂入一对旋转轧辊之间使其压实成连续带坯的方法。
将金属粉末通过一个特制的漏斗喂入转动的轧辊缝中,可轧出具有一定厚度、长度连续、强度适宜的板带坯料。
这些坯体经预烧结、烧结,再轧制加工及热处理等工序,就可制成具有一定孔隙度的、致密的粉末冶金板带材。
粉末轧制制品的密度比较高,制品的长度原则上不受限制,轧制制品的厚度和宽度会受到轧辊的限制;成材率高为80%~90%,熔铸轧制的仅为60%或更低。
粉末轧制适用于生产多孔材料、摩擦材料、复合材料和硬质合金等的板材及带材。
1.2.4粉浆浇注是金属粉末在不施加外力的情况下成形的,即将粉末加水或其它液体及悬浮剂调制成粉浆,再注入石膏模内,利用石膏模吸取水分使之干燥后成形。
常用的悬浮剂有聚乙烯醇、甘油、藻肮酸钠等,作用是防止成形颗粒聚集,改善润湿条件。
为保证形成稳定的胶态悬浮液,颗粒尺寸不大于5μm~10μm,粉末在悬浮液中的质量含量为40%~70%。
粉浆成形工艺参见本书6.2.2。
1.2.5挤压成形将置于挤压筒内的粉末、压坯或烧结体通过规定的模孔压出。
按照挤压条件不同,分为冷挤压和热挤压。
冷挤压是把金属粉末与一定量的有机粘结剂混合在较低温度下(40℃~200℃)挤压成坯块;粉末热挤压是指金属粉末压坯或粉末装入包套内加热到较高温度下压挤,热挤压法能够制取形状复杂、性能优良的制品和材料。
挤压成形设备简单,生产率高,可获得长度方向密度均匀的制品。
挤压成形能挤压出壁很薄直经很小的微形小管,如厚度仅0.01mm,直径1mm 的粉末冶金制品;可挤压形状复杂、物理力学性能优良的致密粉末材料,如烧结铝合金及高温合金。
挤压制品的横向密度均匀,生产连续性高,因此,多用于截面较简单的条、棒和螺旋形条、棒(如麻花钻等)。
1.2.6松装烧结成形粉末未经压制而直接进行烧结,如将粉末装入模具中振实,再连同模具一起入炉烧结成形,用于多孔材料的生产;或将粉末均匀松装于芯板上,再连同芯板一起入炉烧结成形,再经复压或轧制达到所需密度,用于制动摩擦片及双金属材料的生产。
将置于挤压筒内的粉末、压坯或烧结体通过规定的模孔压出。
按照挤压条件不同,分为冷挤压和热挤压。
冷挤压是把金属粉末与一定量的有机粘结剂混合在较低温度下(40℃~200℃)挤压成坯块;粉末热挤压是指金属粉末压坯或粉末装入包套内加热到较高温度下压挤,热挤压法能够制取形状复杂、性能优良的制品和材料。
挤压成形设备简单,生产率高,可获得长度方向密度均匀的制品。
1.2.7爆炸成形借助于爆炸波的高能量使粉末固结的成形方法。
爆炸成形的特点是爆炸时产生压力很高,施于粉末体上的压力速度极快。
如炸药爆炸后,在几微秒时间内产生的冲击压力可达106MPa(相当于107个大气压),比压力机上压制粉末的单位压力要高几百倍至几千倍。
爆炸成形压制压坯的相对密度极高,强度极佳。
如用炸药爆炸压制电解铁粉,压坯的密度接近纯铁体的理论密度值。
爆炸成形可加工普通压制和烧结工艺难以成形的材料,如难熔金属、高合金材料等,还可压制普通压力无法压制的大型压坯。
除上述方法外,还有注射成形及热等静压制新技术等新的成形方法。
2.粉末冶金特点粉末冶金具有独特的化学组成和机械、物理性能,而这些性能是用传统的熔铸方法无法获得的。
运用粉末冶金技术可以直接制成多孔、半致密或全致密材料和制品,如含油轴承、齿轮、凸轮、导杆、刀具等,是一种少无切削工艺。
(1)粉末冶金技术可以最大限度地减少合金成分偏聚,消除粗大、不均匀的铸造组织。
在制备高性能稀土永磁材料、稀土储氢材料、稀土发光材料、稀土催化剂、高温超导材料、新型金属材料(如Al-Li合金、耐热Al合金、超合金、粉末耐蚀不锈钢、粉末高速钢、金属间化合物高温结构材料等)具有重要的作用。
(2)可以制备非晶、微晶、准晶、纳米晶和超饱和固溶体等一系列高性能非平衡材料,这些材料具有优异的电学、磁学、光学和力学性能。
(3)可以容易地实现多种类型的复合,充分发挥各组元材料各自的特性,是一种低成本生产高性能金属基和陶瓷复合材料的工艺技术。
(4)可以生产普通熔炼法无法生产的具有特殊结构和性能的材料和制品,如新型多孔生物材料,多孔分离膜材料、高性能结构陶瓷磨具和功能陶瓷材料等。
(5)可以实现近净形成形和自动化批量生产,从而,可以有效地降低生产的资源和能源消耗。
(6)可以充分利用矿石、尾矿、炼钢污泥、轧钢铁鳞、回收废旧金属作原料,是一种可有效进行材料再生和综合利用的新技术。
我们常见的机加工刀具,五金磨具,很多就是粉末冶金技术制造的。
3.粉末的制取方法(1)还原法这是一种应用最广的金属粉末制取方法,是采用氢气、一氧化碳等作为还原剂,使金属氧化物或氧化物矿石在高温下与之反应,制得金属粉末。
这种粉末多呈多面体形,其成形性与烧结性良好。
粉末粒度可由原料的粒度及还原条件的不同任意调整并均匀化。
目前,粉末成形使用的铁粉大部分由还原法产生;难熔化合物粉末(如硬质合金)的制取也用此类方法。
(2)雾化法这是一种生产效率较高、成本较低、易于制得高纯度粉末的生产方法。
它利用高压惰性气体或高速旋转的叶片将从小孔喷嘴中熔融的金属扩散成雾状液滴并迅速使之冷却成金属微粒的制粉方法。
雾化粉末的颗粒形状因雾化条件而异。
金属液的温度越高,球化的倾向越显著。
其缺点是易产生偏析和不易制得超细粉末。
(3)电解沉积法在金属熔盐或金属盐的水溶液中通入直流电,使金属离子重新获得外层电子,变成金属粉末。
电解沉积法制取的粉末纯度高,颗粒成树枝状或针状,成形性和烧结性都很好,但生产率低,成本较高,仅适用于制造要求纯度高、密度高的粉末材料和制品。
(4)机械粉碎法利用机械,通过压碎、击碎和磨削等作用,使金属块、合金或化合物机械地粉碎成粉末。
这种方法生产效率低,动力消耗大,成本较高。
3.1粉末冶金的基本工序(1)原料粉末的制备。
现有的制粉方法大体可分为两类:机械法和物理化学法。
而机械法可分为:机械粉碎及雾化法;物理化学法又分为:电化腐蚀法、还原法、化合法、还原-化合法、气相沉积法、液相沉积法以及电解法。
(2)粉末成型为所需形状的坯块。
成型的目的是制得一定形状和尺寸的压坯,并使其具有一定的密度和强度。