精密丝杆1
一目了然的滚珠丝杆的基础入门知识
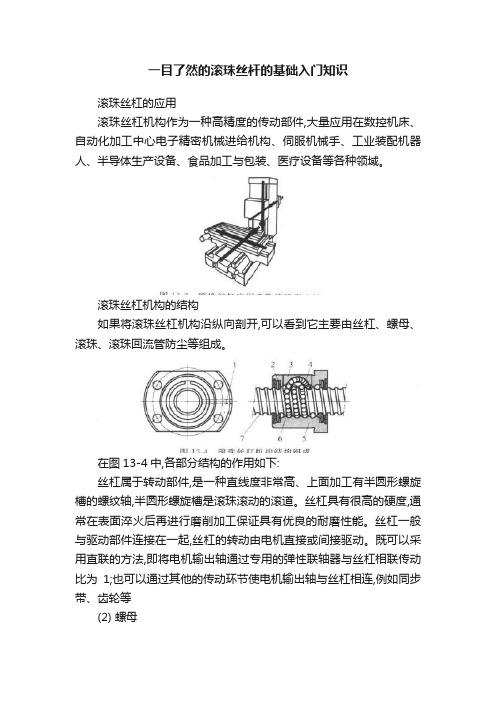
一目了然的滚珠丝杆的基础入门知识滚珠丝杠的应用滚珠丝杠机构作为一种高精度的传动部件,大量应用在数控机床、自动化加工中心电子精密机械进给机构、伺服机械手、工业装配机器人、半导体生产设备、食品加工与包装、医疗设备等各种领域。
滚珠丝杠机构的结构如果将滚珠丝杠机构沿纵向剖开,可以看到它主要由丝杠、螺母、滚珠、滚珠回流管防尘等组成。
在图13-4中,各部分结构的作用如下:丝杠属于转动部件,是一种直线度非常高、上面加工有半圆形螺旋槽的螺纹轴,半圆形螺旋槽是滚珠滚动的滚道。
丝杠具有很高的硬度,通常在表面淬火后再进行磨削加工保证具有优良的耐磨性能。
丝杠一般与驱动部件连接在一起,丝杠的转动由电机直接或间接驱动。
既可以采用直联的方法,即将电机输出轴通过专用的弹性联轴器与丝杠相联传动比为1;也可以通过其他的传动环节使电机输出轴与丝杠相连,例如同步带、齿轮等(2) 螺母螺母是用来固定需要移动的负载的,其作用类似于直线导轨机构的滑块。
一般将所需要移动的各种负载(例如工作台、移动滑块)与螺母连接在一起,再在工作台或移动滑块上安装各种执行机构螺母内部加工有与丝杠类似的半圆形滚道,而且设计有供滚珠循环运动的回流管,螺母是滚珠丝杠机构的重要部件,滚珠丝杠机构的性能与质量很大程度上依赖于螺母。
(3)防尘片防尘片的作用为防止外部污染物进入螺母内部。
由于滚珠丝杠机构属于精密部件如果在使用时污染物(例如灰尘、碎屑、金属渣等)进入螺母,可能会使滚珠丝杠运动副严重磨损,降低机构的运动精度及使用寿命,甚至使丝杠或其他部件发生损坏,因此必须对丝杠螺母进行密封,防止污染物进入螺母4 滚珠在滚珠丝杠机构中,滚珠的作用与其在直线导轨、直线轴承中的作用是相同的,滚珠作为承载体的一部分,直接承受载荷,同时又作为中间传动元件,以滚动的方式传递运动。
由于以滚动方式运动,所以摩擦非常小。
(5) 油孔滚珠丝杠机构运行时需要良好的润滑,因此应定期加注润滑油或润滑脂。
丝杆标准尺寸规格表

丝杆的标准尺寸规格表通常会列出不同直径和螺距的
丝杆,以满足不同的应用需求。
以下是一些常见的丝杆标准尺寸规格:M2丝杠:公称直径为2mm,螺距为0.4mm。
M3丝杠:公称直径为3mm,螺距为0.5mm。
M4丝杠:公称直径为4mm,螺距为0.7mm。
M5丝杠:公称直径为5mm,螺距为0.8mm。
M6丝杠:公称直径为6mm,螺距为1.0mm。
M8丝杠:公称直径为8mm,螺距为1.
25mm。
M10丝杠:公称直径为10mm,螺距为1.5m m。
M12丝杠:公称直径为12mm,螺距为1.75mm。
M16丝杠:公称直径为16mm,螺距为2.0mm。
这些规格表通常会列出不同直径和螺距的丝杆,以满足不同的应用需求。
在选择丝杆时,需要根据具体的应用场景和要求来选择合适的规格。
光学二级实验讲义 (1)

实验一迈克尔逊干涉仪的调节和使用【实验目的】1.了解迈克尔逊干涉仪的工作原理,掌握其调节和使用的方法。
2.应用迈克尔逊干涉仪,测量He-Ne激光的波长【实验仪器】迈克尔逊干涉仪(WSM-200 03040303 20100538)He-Ne激光器扩束镜迈克尔逊干涉仪的主体结构如图1(a)所示,由下面6个部分组成。
1微调手轮2粗调手轮3读数窗口4可调螺母5毫米刻度尺6精密丝杆7导轨(滑槽)8螺钉9调平螺丝10锁紧圈11移动镜底座12紧固螺丝13滚花螺丝14全反镜15水平微调螺丝16垂直微调螺丝17观察屏固定杆18观察屏图1迈克尔逊干涉仪结构(1)底座底座由生铁铸成,较重,确保仪器的稳定性。
由3个调平螺丝9支撑,调平后可以拧紧锁紧圈10以保持座架稳定。
(2)导轨导轨7由两根平行的长约280mm的框架和精密丝杆6组成,被固定在底座上,精密丝杆穿过框架正中,丝杆螺距为1mm,如图1(b)所示。
(3)拖板部分拖板是一块平板,反面做成与导轨吻合的凹槽,装在导轨上,下方是精密螺母,丝杆穿过螺母,当丝杆旋转时,拖板能前后移动,带动固定在其上的移动镜11(即M1)在导轨面上滑动,实现粗动。
M1是一块很精密的平面镜,表面镀有金属膜,具有较高的反射率,垂直地固定在拖板上,它的法线严格地与丝杆平行。
倾角可分别用镜背后面的3颗滚花螺丝13来调节,各螺丝的调节范围是有限度的,如果螺丝向后顶得过松,在移动时可能因震动而使镜面有倾角变化,如果螺丝向前顶得太紧,致使条纹不规则,严重时,有可能使螺丝口打滑或平面镜破损。
(4)定镜部分定镜M2是与M1相同的一块平面镜,固定在导轨框架右侧的支架上。
通过调节其上的水平拉簧螺钉15使M2在水平方向转过一微小的角度,能够使干涉条纹在水平方向微动;通过调节其上的垂直拉簧螺钉16使M2在垂直方向转过一微小的角度,能够使干涉条纹上下微动;与3颗滚花螺丝13相比,15、16改变M2的镜面方位小得多。
常用丝杠品牌

常用丝杠品牌引言概述:丝杠是一种常用的机械传动元件,广泛应用于各个行业的机械设备中。
在市场上,有许多不同品牌的丝杠可供选择。
本文将介绍一些常用的丝杠品牌,并对它们的特点和应用进行详细阐述。
正文内容:1. THK品牌1.1 高精度:THK丝杠具有高精度的特点,能够满足精密机械设备的需求。
1.2 高刚性:THK丝杠采用优质材料制造,具有较高的刚性,能够承受较大的载荷。
1.3 长寿命:THK丝杠采用特殊的设计和制造工艺,具有较长的使用寿命。
2. HIWIN品牌2.1 高速度:HIWIN丝杠采用先进的技术,具有较高的传动速度,适用于高速运动的设备。
2.2 高负载:HIWIN丝杠采用优质材料和特殊的设计,能够承受较大的负载。
2.3 低噪音:HIWIN丝杠采用特殊的制造工艺,具有较低的噪音水平,适用于对噪音要求较高的设备。
3. NSK品牌3.1 高精度:NSK丝杠采用高精度的加工工艺,具有较高的定位精度。
3.2 高刚性:NSK丝杠采用优质材料和特殊的设计,具有较高的刚性,能够承受较大的载荷。
3.3 高速度:NSK丝杠采用先进的技术,具有较高的传动速度,适用于高速运动的设备。
4. TBI品牌4.1 高精度:TBI丝杠采用先进的制造工艺,具有较高的定位精度。
4.2 高刚性:TBI丝杠采用优质材料和特殊的设计,具有较高的刚性,能够承受较大的载荷。
4.3 高速度:TBI丝杠采用特殊的结构设计,具有较高的传动速度,适用于高速运动的设备。
5. Kuroda品牌5.1 高精度:Kuroda丝杠采用高精度的制造工艺,具有较高的定位精度。
5.2 高刚性:Kuroda丝杠采用优质材料和特殊的设计,具有较高的刚性,能够承受较大的载荷。
5.3 高速度:Kuroda丝杠采用先进的技术,具有较高的传动速度,适用于高速运动的设备。
总结:综上所述,常用的丝杠品牌包括THK、HIWIN、NSK、TBI和Kuroda。
这些品牌的丝杠具有高精度、高刚性和高速度等特点,适用于不同行业的机械设备。
1mm导程行星滚柱丝杠
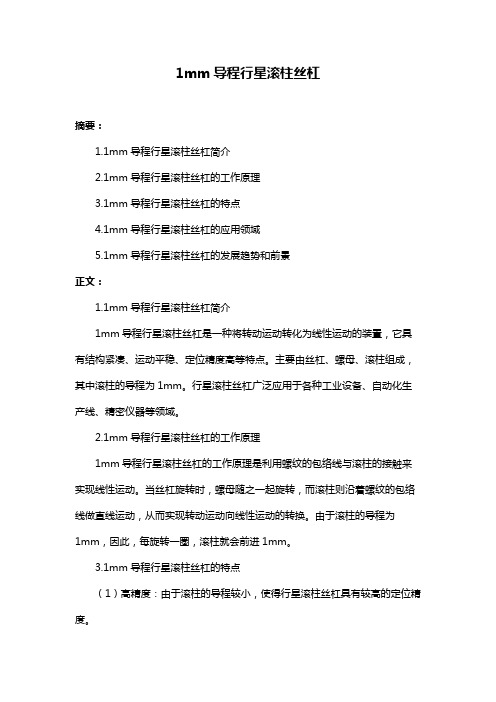
1mm导程行星滚柱丝杠摘要:1.1mm导程行星滚柱丝杠简介2.1mm导程行星滚柱丝杠的工作原理3.1mm导程行星滚柱丝杠的特点4.1mm导程行星滚柱丝杠的应用领域5.1mm导程行星滚柱丝杠的发展趋势和前景正文:1.1mm导程行星滚柱丝杠简介1mm导程行星滚柱丝杠是一种将转动运动转化为线性运动的装置,它具有结构紧凑、运动平稳、定位精度高等特点。
主要由丝杠、螺母、滚柱组成,其中滚柱的导程为1mm。
行星滚柱丝杠广泛应用于各种工业设备、自动化生产线、精密仪器等领域。
2.1mm导程行星滚柱丝杠的工作原理1mm导程行星滚柱丝杠的工作原理是利用螺纹的包络线与滚柱的接触来实现线性运动。
当丝杠旋转时,螺母随之一起旋转,而滚柱则沿着螺纹的包络线做直线运动,从而实现转动运动向线性运动的转换。
由于滚柱的导程为1mm,因此,每旋转一圈,滚柱就会前进1mm。
3.1mm导程行星滚柱丝杠的特点(1)高精度:由于滚柱的导程较小,使得行星滚柱丝杠具有较高的定位精度。
(2)高刚性:行星滚柱丝杠的滚柱与螺纹的接触面积大,使得其在承受外力时具有较高的刚性。
(3)运动平稳:由于滚柱的滚动摩擦,使得行星滚柱丝杠在运动过程中能够减小摩擦,从而使运动更加平稳。
(4)结构紧凑:行星滚柱丝杠的结构设计紧凑,占用空间小,方便安装和集成。
4.1mm导程行星滚柱丝杠的应用领域(1)工业设备:行星滚柱丝杠广泛应用于各类工业设备,如数控机床、加工中心、自动化生产线等,提高设备的运动精度和性能。
(2)精密仪器:由于其高精度、高刚性的特点,行星滚柱丝杠被广泛应用于精密仪器领域,如测量仪器、分析仪器等。
(3)航空航天:在航空航天领域,行星滚柱丝杠可用于飞行器的姿态控制、卫星天线展开等关键部件。
(4)医疗器械:在医疗器械领域,行星滚柱丝杠可用于手术机器人、牙科设备等精密医疗设备。
5.1mm导程行星滚柱丝杠的发展趋势和前景随着科技的不断发展,对精密运动控制的需求越来越高。
滚珠丝杆技术要求-凡一提供
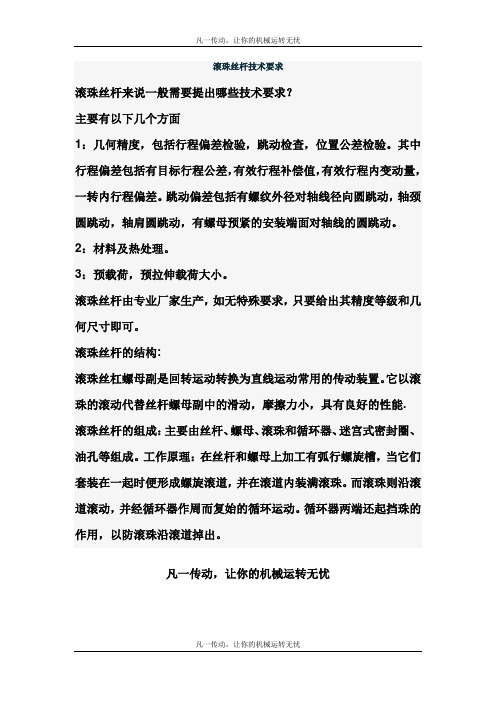
凡一传动,让你的机械运转无忧
滚珠丝杆技术要求
滚珠丝杆来说一般需要提出哪些技术要求?
主要有以下几个方面
1:几何精度,包括行程偏差检验,跳动检查,位置公差检验。
其中行程偏差包括有目标行程公差,有效行程补偿值,有效行程内变动量,一转内行程偏差。
跳动偏差包括有螺纹外径对轴线径向圆跳动,轴颈圆跳动,轴肩圆跳动,有螺母预紧的安装端面对轴线的圆跳动。
2:材料及热处理。
3:预载荷,预拉伸载荷大小。
滚珠丝杆由专业厂家生产,如无特殊要求,只要给出其精度等级和几何尺寸即可。
滚珠丝杆的结构:
滚珠丝杠螺母副是回转运动转换为直线运动常用的传动装置。
它以滚珠的滚动代替丝杆螺母副中的滑动,摩擦力小,具有良好的性能.
滚珠丝杆的组成:主要由丝杆、螺母、滚珠和循环器、迷宫式密封圈、油孔等组成。
工作原理:在丝杆和螺母上加工有弧行螺旋槽,当它们套装在一起时便形成螺旋滚道,并在滚道内装满滚珠。
而滚珠则沿滚道滚动,并经循环器作周而复始的循环运动。
循环器两端还起挡珠的作用,以防滚珠沿滚道掉出。
凡一传动,让你的机械运转无忧
凡一传动,让你的机械运转无忧。
梯形丝杆1
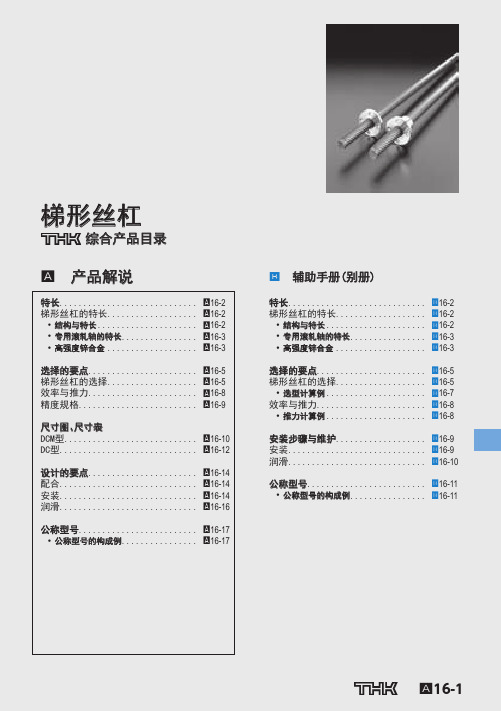
上式的计算结果如图4所示。 当施加扭矩时,所产生的推力可用下式计算。
Fa =
Fa T R
2 •π • η • T R 10–3
∶产生的推力 ∶扭矩(输出) ∶导程 (N) (N · m) (mm)
μ
效率η
μ μ
导程角α 图4 效率
A
选择的要点
精度规格
精度规格
表2 DCM、 DC型用丝杠轴的精度 轴标记 精度 单一节距误差 (最大) 累积节距误差 (最大) 滚轧轴 T注) 0.020 0.15/300 切削轴 K注) 0.015 0.05/300 研磨轴 G注) 0.005 0.015/300
使用温度 图2 温度系数 温度系数 fT 磨损量 mm
fS
fS fT F PF
fT•F PF
∶安全系数 ∶温度系数 ∶动态容许推力 ∶轴向载荷 (参照A 上的表1) (参照图2) (N) (N)
表面硬度与耐磨损性
轴的硬度对梯形丝杠的耐磨损性影响极大,如果 硬度等于或小于250HV,磨损量就会如 图3 所示增 大。 另外, 表面粗糙度最好为0.80a或更低。 通过滚轧的加工硬化,滚轧轴的表面硬度可以达 到250HV以上,而表面粗糙度为0.20a或更低。 因 此,滚轧轴可以获得很高的耐磨损性。
安装步骤与维护 安装步骤与维护................... B16-9 安装............................. B16-9 润滑............................. B16-10 公称型号......................... B16-11 公称型号 公称型号的构成例 ................ B16-11
滚珠丝杆的工业用途

滚珠丝杆的工业用途
滚珠丝杆是一种传动元件,主要用于精密机械传动系统中,具有高速、高精度、高效率的特点。
工业上常用的滚珠丝杆有以下几种用途:
1. 机床:滚珠丝杆可以用于各种机床的进给传动系统,例如铣床、车床、磨床等。
其高速、高精度的特点可以提高机床的加工效率和加工精度。
2. 机器人:滚珠丝杆被广泛应用于工业机器人的运动控制系统中,用于实现机器人的各个关节的精确移动和定位。
3. 自动化设备:滚珠丝杆也可以作为自动化设备中的传动元件,用于各种自动输送、装配和定位系统中。
例如用于电子设备的面板组装线、汽车工业的焊接生产线等。
4. CNC机床:在数控机床中,滚珠丝杆可以用于实现数控系
统的运动精度和定位控制。
5. 3D打印机:滚珠丝杆也可以用于3D打印机中,用于实现
打印平台的升降和定位控制。
总之,滚珠丝杆在工业中的用途非常广泛,主要应用于各种需要高速、高精度运动控制的设备和系统中。
- 1、下载文档前请自行甄别文档内容的完整性,平台不提供额外的编辑、内容补充、找答案等附加服务。
- 2、"仅部分预览"的文档,不可在线预览部分如存在完整性等问题,可反馈申请退款(可完整预览的文档不适用该条件!)。
- 3、如文档侵犯您的权益,请联系客服反馈,我们会尽快为您处理(人工客服工作时间:9:00-18:30)。
课程设计说明书设计题目:1、精密测试数据采集系统设计2、测控网络通信系统及人机交互接口设计3、精密丝杠加工工艺设计专业:测控技术与仪器班级:08测控一班学生:王赛学号:0828060034指导教师:袁兴起河南理工大学机械与动力工程系2011年12月5日至12月31日共4周综合性课程设计报告前言课程设计是我们在学完机械制造基础课程、进行了生产实习之后,对机械加工工艺过程,和机械零件结构设计进一步了解的一个综合性和实践性很强的教学环节。
学生通过课程设计,能综合运用所学基本理论以及在生产实习中学到的实践知识进行工艺及结构设计的基本训练,掌握中等复杂程度的机械零件制造工艺设计和工艺装备选用,机械制造过程中的加工方法、加工装备等基本知识,确定各工序的工装与设备等方面的综合知识。
本课程设计培养学生分析生产实际加工过程中的具体工艺问题,并能初步提出改进产品质量、提高生产率与降低成本的工艺途径和方法的能力。
为后续课程的学习及毕业设计和将来从事机械设计、机械制造技术工作打下基础。
由于能力有限,设计尚有许多不足之处,恳请各位老师给予指正。
一、零件的分析(一)、零件的作用题目给定的零件是丝杠,丝杠是将旋转运动变成直线运动的传动副零件,它被用来完成机床的进给运动。
机床丝杠不仅要能传递准确的运动,而且还要能传递一定的动力。
所以它在精度、强度以及耐磨性各个方面,都有一定的要求。
其功用为支承传动零件(齿轮、皮带轮等)、传动扭矩、承受载荷,以及保证装在主轴上的工件或刀具具有一定的回转精度。
表面特点:外圆、内孔、圆锥、螺纹、花键、横向孔。
(二)、零件的工艺分析丝杠是细而长的柔性轴,它的长径比往往很大,一般都在20~50左右,刚度很差。
加上其结构形状比较复杂,有要求很高的螺纹表面,又有阶梯及沟槽,因此,在加工过程中,很容易产生变形。
这是丝杠加工中影响精度的一个主要矛盾。
主要技术要求:1、尺寸精度轴颈是轴类零件的主要表面,它影响轴的回转精度及工作状态。
轴颈的直径精度根据其使用要求通常为IT6~9,精密轴颈可达IT5。
2、几何形状精度轴颈的几何形状精度(圆度、圆柱度),一般应限制在直径公差点范围内。
对几何形状精度要求较高时,可在零件图上另行规定其允许的公差。
3、位置精度主要是指装配传动件的配合轴颈相对于装配轴承的支承轴颈的同轴度,通常是用配合轴颈对支承轴颈的径向圆跳动来表示的;根据使用要求,规定高精度轴为0.001~0.005mm,而一般精度轴为0.01~0.03mm。
此外还有内外圆柱面的同轴度和轴向定位端面与轴心线的垂直度要求等。
4.表面粗糙度根据零件的表面工作部位的不同,可有不同的表面粗糙度值,例如普通机床主轴支承轴颈的表面粗糙度为Ra0.16~0.63um,配合轴颈的表面粗糙度为Ra0.63~2.5um,随着机器运转速度的增大和精密程度的提高,轴类零件表面粗糙度值要求也将越来越小。
轴类零件的加工工艺因其用途、结构形状、技术要求、产量大小的不同而有差异。
而轴的工艺规程编制是生产中最常遇到的工艺工作。
轴类零件加工的主要问题:轴类零件加工的主要问题是如何保证各加工表面的尺寸精度、表面粗糙度和主要表面之间的相互位置精度。
具体指标有:(1)单个螺距允差(2)中径圆度允差;(3)外径相等性允差;(4)外径跳动允差;(5)牙形半角允差;(6)中径为尺寸公差;(7)外径为尺寸公差;(8)内径为尺寸公差。
二、工艺规程设计(一)、确定毛坯的制造形式题目给定的零件是丝杠,轴类零件可根据使用要求、生产类型、设备条件及结构,选用棒料、锻件等毛坯形式。
对于外圆直径相差不大的轴,一般以棒料为主;而对于外圆直径相差大的阶梯轴或重要的轴,常选用锻件,这样既节约材料又减少机械加工的工作量,还可改善机械性能。
轴类零件的材料和毛坯,合理选用材料和规定热处理的技术要求,对提高轴类零件的强度和使用寿命有重要意义,同时,对轴的加工过程有极大的影响。
1、轴类零件的材料一般轴类零件常用45钢,根据不同的工作条件采用不同的热处理规范(如正火、调质、淬火等),以获得一定的强度、韧性和耐磨性。
对中等精度而转速较高的轴类零件,可选用40Cr等合金钢。
这类钢经调质和表面淬火处理后,具有较高的综合力学件能。
精度较高的轴,有时还用轴承钢GCrls和弹簧钢65Mn等材料,它们通过调质和表面淬火处理后,具有更高耐磨性和耐疲劳性能。
对于高转速、重载荷等条件下工作的轴,可选用20CrMnTi、20MnZB、20Cr等低碳含金钢或38CrMoAIA氮化钢。
低碳合金钢经渗碳淬火处理后,具有很高的表面硬度、抗冲击韧性和心部强度,热处理变形却很小。
2、轴类零件的毛坯轴类零件的毛坯最常用的是圆棒料和锻件,只有某些大型的、结构复杂的轴才采用铸件。
因而结合题目给定车床丝杠零件的作用及工作要求,材料可选用45钢,也可用题中所给的Y40Mn(高硫中碳切削钢),毛坯应采用锻件,以保证机械性能。
(二)、基面的选择基面的选择是工艺规程设计的重要工作之一,基面选择的正确与合理,可以使加工质量得以保证,生产率得以提高。
否则,加工工艺过程中会问题百出,甚至会造成零件的大批报废,使生产无法正常运行。
(1)粗基准的选择。
对于本零件而言,按照粗基准的选择原则,以外圆为粗基准是完全合理的。
(2)精基准的选择。
主要考虑到基准重合的问题,和便于装夹,以工件端面中心孔为精基准。
(三)、制订工艺路线1.工艺路线方案一毛坯(热处理)—校直—车端面打中心孔—外圆粗加工—校直热处理—重打中心孔(修正)—外圆半精加工—加工螺纹—校直、低温时效—修正中心孔—外圆、螺纹精加工。
工序Ⅰ毛坯(热处理)工序Ⅱ校直工序Ⅲ车端面打中心孔工序Ⅳ外圆粗加工工序Ⅴ校直热处理工序Ⅵ重打中心孔(修正)工序Ⅶ外圆半精加工工序Ⅷ加工螺纹工序Ⅸ校直、低温时效工序Ⅹ修正中心孔工序ⅩⅠ外圆、螺纹精加工2.工艺路线方案二工序Ⅰ锻造(弯曲度不超过5mm)工序Ⅱ球面退火工序Ⅲ车端面打中心孔工序Ⅳ车外圆工序V 粗车梯形螺纹槽工序VI 半精车外圆工序VII 粗磨外圆工序VIII 车梯形螺纹工序IX 半精磨外圆工序X 半精车螺纹工序XI 研磨外圆工序XII 终磨外圆3.工艺方案的比较与分析1、丝杠的校直及热处理:丝杠工艺除毛坯工序外,在粗加工及半精加工阶段,都安排了校直及热处理工序。
校直的目的是为了减少工件的弯曲度,使机械加工余量均匀。
时效热处理以消除工件的残余应力,保证工件加工精度的稳定性。
一般情况下,需安排三次。
一次是校直及高温时效,它安排在粗车外圆以后,还有两次是校直及低温时效,它们分别安排在螺纹的粗加工及半精加工以后。
2、定位基准面的加工:丝杠两端的中心孔是定位基准面,在安排工艺路线时,应一首先将它加工出来,中心孔的精度对加工质量有很大影响,丝杠多选用带有120。
保护锥的中心孔。
此外,在热处理后,最后精车螺纹以前,还应适当修整中心孔以保持其精度。
丝杠加工的定位基准面除中心孔外,还要用丝杠外圆表面作为辅助基准面,以便在加工中采用跟刀架,增加刚度。
3、螺纹的粗、精加工粗车螺纹工序一般安排在精车外圆以后,半精车及精车螺纹工序则分别安排在粗磨及精磨外圆以后。
不淬硬丝杜一般采用车削工艺,经多次加工,逐渐减少切削力和内应力;对于淬硬丝杠,则采用“先车后磨”或“全磨”两种不同的工艺。
后者是从淬硬后的光杜上直接用单线或多线砂轮粗磨出螺纹,然后用单线砂轮精磨螺纹。
4、重钻中心孔:工件热处理后,会产生变形。
其外圆面需要增加的加工余量,为减少其加工余量,而采用重钻中心孔的方法。
在重钻中心孔之前,先找出工件上径向圆跳动为最大值的一半的两点,以这两点后作为定位基准面,用个端面的方法切去原来的中心孔,重新钻中心孔。
当使用新的中心孔定位时,工件所必须切会的额外的加工余量将减少到原有值。
由于该丝杠为单件生产,要求较高,故加工工艺过程严格按照工序划分阶段的原则,将整个工艺过程分为五个阶段:准备和预先热处理阶段(工序1—6),粗加工阶段(工序7—13),半精加工阶段(工序14—23),精加工阶段(工序24—25),终加工阶段(工序26—28)。
为了消除残余应力,整个工艺过程安排了四次消除残余应力的热处理,并严格规定机械加工和热处理后不准冷校直,以防止产生残余应力。
为了消除加工过程中的变形,每次加工后工件应垂直吊放,并采用留加工余量分层加工的方法,经过多道工序逐步消除加工过程中引起的变形。
所以选择方案一为最佳方案。
(四)、机械加工余量、工序尺寸及毛坯尺寸的确定(五)、确定切削用量及基本工时工序一:粗车外圆(1)确定背吃刀量粗车外圆,加工余量为5mm,一次走刀。
Asp=5/2=2.5mm. (2)确定进给量刀杆尺寸16 25,as 3,工件直径为65mm,则f=0.5~0.7。
由《简明手册》表4.2—3查取f =0.56mm。
根据《切削用量简明手册》表1.11查取:VC=1.33(由182~199HBS、asp=2.5、f =0.56mm/r、车刀为YG硬质合金),由于实际车削过程使用条件的改变,查取切削速度修正系数:K =1.0,K =1.0,K =0.73,K =(190/HBS)1.25=1.0,KSV=0.85,Kkv=1.0。
则VC =VC 60V = VC K K K K KSV K = 1.33 60 1.0 1.0 0.73 1.0 0.85 1.0=49.5n = 157.6r/min按CA6140车床转速(《机械制造工艺设计简明手册》表4.2-2)选择与157.5r/min相近似的机床转速n =183r/min,则实际切削速度V = n /1000=3.14 100 183/1000=57.5m/min。
综上,此工步的切削用量为:a =2.5mm,f =0.56, n =183r/min, V =57.5m/min。
(3) 计算基本工时:T=(L+L1+L2+L3)×i/(f×n)=(9+3+3+0)×2/(0.76×183)=0.22min。
其中L=9,L1=3,L2=3,L3=0,i=2工序二:倒角切削用量:背吃刀量asp=1.5,手动进给,一次走刀。
V =80m/min, n =1000× V / =1000×80/3.14×100=254.7r/min按CA6140说明书:n =238r/min, V = n /1000=3.14×238×100/1000=74.7基本工时:由工人操控,大约为0.03min。
工序三:车2×2退刀槽(1)选择刀具:选择90°切槽刀,刀杆尺寸16×25mm,刀片厚度取3mm,选用YG6刀具材料,前刀面形状为平面带倒棱型,前角为10°,后角8°,主偏角90°,副偏角3°,刀尖圆弧半径0.2--0.5取0.5mm,刃倾角0°。