炼铁原理与工艺1炼铁概述
高炉炼铁
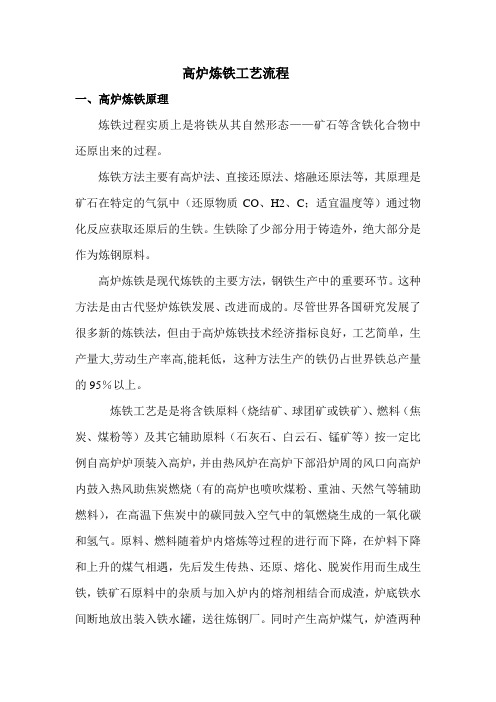
高炉炼铁工艺流程一、高炉炼铁原理炼铁过程实质上是将铁从其自然形态——矿石等含铁化合物中还原出来的过程。
炼铁方法主要有高炉法、直接还原法、熔融还原法等,其原理是矿石在特定的气氛中(还原物质CO、H2、C;适宜温度等)通过物化反应获取还原后的生铁。
生铁除了少部分用于铸造外,绝大部分是作为炼钢原料。
高炉炼铁是现代炼铁的主要方法,钢铁生产中的重要环节。
这种方法是由古代竖炉炼铁发展、改进而成的。
尽管世界各国研究发展了很多新的炼铁法,但由于高炉炼铁技术经济指标良好,工艺简单,生产量大,劳动生产率高,能耗低,这种方法生产的铁仍占世界铁总产量的95%以上。
炼铁工艺是是将含铁原料(烧结矿、球团矿或铁矿)、燃料(焦炭、煤粉等)及其它辅助原料(石灰石、白云石、锰矿等)按一定比例自高炉炉顶装入高炉,并由热风炉在高炉下部沿炉周的风口向高炉内鼓入热风助焦炭燃烧(有的高炉也喷吹煤粉、重油、天然气等辅助燃料),在高温下焦炭中的碳同鼓入空气中的氧燃烧生成的一氧化碳和氢气。
原料、燃料随着炉内熔炼等过程的进行而下降,在炉料下降和上升的煤气相遇,先后发生传热、还原、熔化、脱炭作用而生成生铁,铁矿石原料中的杂质与加入炉内的熔剂相结合而成渣,炉底铁水间断地放出装入铁水罐,送往炼钢厂。
同时产生高炉煤气,炉渣两种副产品,高炉渣铁主要矿石中不还原的杂质和石灰石等熔剂结合生成,自渣口排出后,经水淬处理后全部作为水泥生产原料;产生的煤气从炉顶导出,经除尘后,作为热风炉、加热炉、焦炉、锅炉等的燃料。
二、高炉冶炼主要工艺设备简介高护炼铁设备组成有:①高炉本体;②供料设备;③送风设备;④喷吹设备;⑤煤气处理设备;⑥渣铁处理设备。
通常,辅助系统的建设投资是高炉本体的4~5倍。
生产中,各个系统互相配合、互相制约,形成一个连续的、大规模的高温生产过程。
高炉开炉之后,整个系统必须日以继夜地连续生产,除了计划检修和特殊事故暂时休风外,一般要到一代寿命终了时才停炉。
炼铁设计原理
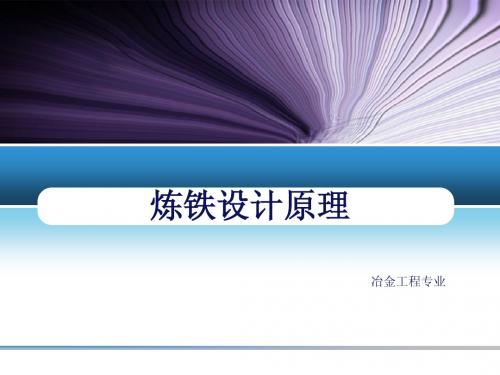
D
h3 一般取值1~3m
D/d
小型高炉
1.25~1.5
h0 h1
hz
3.1.2.5 炉腰
承 上 启 下
h2
Hu
3.1.2.6 炉喉
作用:承接炉料,稳定料面,保证炉料合理分布
d1/D取值在0.64~0.73之间。
3.1.2.7 死铁层厚度
定义:铁口中心线到炉底砌砖表面之间的距离
作用:隔绝铁水和煤气对炉底的侵蚀,其热容量可使炉底温度均匀稳定,
具有 时间性和相对性
1. 比较法 产量确定炉容 寻找条件相似 确定几个主要设计参数
合理的炉型
比较、修订计算
容积计算
2. 计算法
经验数据的统计法 分析和统计 关系式 计算校核 修定
设计炉型
h0 0.0937 Vu d 2
(3-15)
大型高炉:
H u 6.44Vu
0.2
d 0.32Vu
0.3942
0.719Vu
0.2152
0.517Vu
0.7848
0.841
)
h3 0.3586Vu
0.7848
6.3278Vu
0.7701
h4 (6.3008Vu 47.7323 ) (Vu
d1 0.4317Vu
0.3771
0.7833Vu
0.2446
0.5769Vu
(6)生铁成本 (7)休风率
(8)高炉一代寿命
1.3 高炉炼铁设计的基本原则
一. 高炉炼铁设计应遵循的基本原则
1)合法性。
2)客观性。 3)先进性。
4)经济性。
5)综合性。 6)发展远景。 7)安全和环保。 8)标准化。
炼铁生产的原理
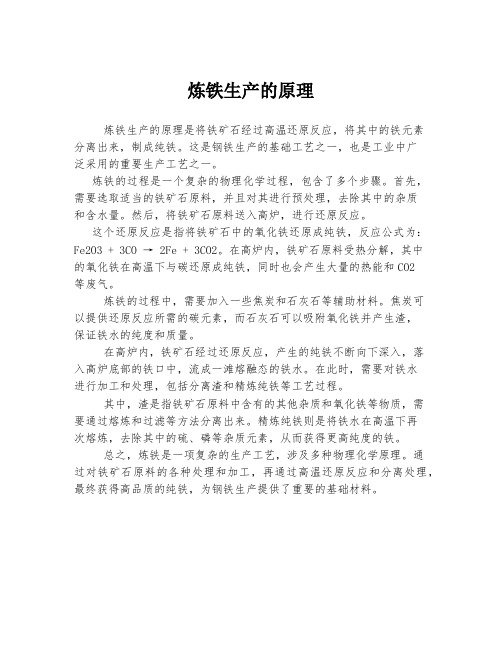
炼铁生产的原理
炼铁生产的原理是将铁矿石经过高温还原反应,将其中的铁元素
分离出来,制成纯铁。
这是钢铁生产的基础工艺之一,也是工业中广
泛采用的重要生产工艺之一。
炼铁的过程是一个复杂的物理化学过程,包含了多个步骤。
首先,需要选取适当的铁矿石原料,并且对其进行预处理,去除其中的杂质
和含水量。
然后,将铁矿石原料送入高炉,进行还原反应。
这个还原反应是指将铁矿石中的氧化铁还原成纯铁,反应公式为:Fe2O3 + 3CO → 2Fe + 3CO2。
在高炉内,铁矿石原料受热分解,其中
的氧化铁在高温下与碳还原成纯铁,同时也会产生大量的热能和CO2
等废气。
炼铁的过程中,需要加入一些焦炭和石灰石等辅助材料。
焦炭可
以提供还原反应所需的碳元素,而石灰石可以吸附氧化铁并产生渣,
保证铁水的纯度和质量。
在高炉内,铁矿石经过还原反应,产生的纯铁不断向下深入,落
入高炉底部的铁口中,流成一滩熔融态的铁水。
在此时,需要对铁水
进行加工和处理,包括分离渣和精炼纯铁等工艺过程。
其中,渣是指铁矿石原料中含有的其他杂质和氧化铁等物质,需
要通过熔炼和过滤等方法分离出来。
精炼纯铁则是将铁水在高温下再
次熔炼,去除其中的硫、磷等杂质元素,从而获得更高纯度的铁。
总之,炼铁是一项复杂的生产工艺,涉及多种物理化学原理。
通
过对铁矿石原料的各种处理和加工,再通过高温还原反应和分离处理,最终获得高品质的纯铁,为钢铁生产提供了重要的基础材料。
钢铁的冶炼原理及生产工艺流程

炼铁过程本质上是将铁从其自然形态——矿石等含铁化合物中还原出来的过程。
炼铁方法主要有高炉法、直接复原法、熔融复原法等,其原理是矿石在特定的氛围中(复原物质CO、H2、C;适合温度等)经过物化反响获得复原后的生铁。
生铁除了少部分用于锻造外,绝大多半是作为炼钢原料。
1、高炉炼铁的冶炼原理(应用最多的)一)炼铁的原理(如何从铁矿石中炼出铁)用复原剂将铁矿石中的铁氧化物复原成金属铁。
铁氧化物(Fe2O3、Fe3O4、FeO)+复原剂(C、CO、H2)铁( Fe)二)炼铁的方法(1)直接复原法(非高炉炼铁法)(2)高炉炼铁法(主要方法)三)高炉炼铁的原料及其作用(1)铁矿石:(烧结矿、球团矿)供给铁元素。
冶炼一吨铁大概需要— 2吨矿石。
(2)焦碳:冶炼一吨铁大概需要 500Kg 焦炭。
供给热量;供给复原剂;作料柱的骨架。
(3)熔剂:(石灰石、白云石、萤石)使炉渣融化为液体;去除有害元素硫( S)。
(4)空气:为焦碳焚烧供给氧。
2、工艺流程生铁的冶炼虽原理同样,但因为方法不一样、冶炼设施不一样,因此工艺流程也不一样。
下边分别简单予以介绍。
高炉生产是连续进行的。
一代高炉(从开炉到大修停炉为一代)能连续生产几年到十几年。
生产时,从炉顶(一般炉顶是由料种与料斗构成,现代化高炉是钟阀炉顶和无料钟炉顶)不停地装入铁矿石、焦炭、熔剂,从高炉下部的风口吹进热风( 1000~1300 摄氏度),喷入油、煤或天然气等燃料。
装入高炉中的铁矿石,主假如铁和氧的化合物。
在高温下,焦炭中和喷吹物中的碳及碳焚烧生成的一氧化碳将铁矿石中的氧争夺出来,获得铁,这个过程叫做复原。
铁矿石经过复原反响炼出生铁,铁水从出铁口放出。
铁矿石中的脉石、焦炭及喷吹物中的灰分与加入炉内的石灰石等熔剂联合生成炉渣,从出铁口和出渣口分别排出。
煤气从炉顶导出,经除尘后,作为工业用煤气。
现代化高炉还能够利用炉顶的高压,用导出的部分煤气发电。
生铁是高炉产品(指高炉冶炼生铁),而高炉的产品不不过生铁,还有锰铁等,属于铁合金产品。
炼铁原理与工艺

炼铁原理与工艺炼铁是将铁矿石经过一系列的物理和化学变化,最终得到纯铁的过程。
它是钢铁工业的基础生产工艺,也是现代工业化不可或缺的一环。
炼铁的原理和工艺经过长时间的发展和改进,已经非常成熟和高效。
炼铁的原理主要包括铁矿石还原和熔融两个过程。
首先是铁矿石的还原,即将铁矿石中的氧化铁还原为金属铁。
这一过程通常使用焦炭作为还原剂,通过高温和还原剂的作用,将铁矿石中的氧化铁还原为金属铁。
还原反应的化学方程式为:Fe2O3 + 3C = 2Fe + 3CO。
在这个反应中,焦炭中的碳与氧化铁发生反应,生成金属铁和一氧化碳。
还原后的金属铁并不是纯铁,还含有一些杂质,如硅、锰、磷等。
因此,还需要进行二次处理,即熔融。
熔融是将还原后的金属铁与其他添加剂一起加热到高温,使其融化并进行反应。
熔融的目的是去除杂质,并加入适量的合金元素,以提高铁的性能。
通常加入的合金元素有碳、铬、镍等。
熔融过程中,炉温要达到1600℃以上,使铁液中的杂质和氧化物被还原和脱离,形成纯净的铁水。
炼铁的工艺包括高炉法和直接还原法两种。
高炉法是目前应用最广泛的炼铁工艺,它使用高炉作为主要设备。
高炉法的工艺流程一般包括炉料的装入、预热、还原和熔融等过程。
炉料主要由铁矿石、焦炭和石灰石组成,其中焦炭是还原剂,石灰石用于脱硫。
在高炉中,炉料从顶部装入,燃料从底部喷入,通过燃烧产生的高温将铁矿石还原和熔化。
熔融的铁水经过除渣、出铁等处理后,得到纯铁。
直接还原法是近年来发展起来的一种新型炼铁工艺。
它通过在直接还原炉中加热还原剂和铁矿石,将铁矿石直接还原为金属铁。
这种工艺省去了高炉的熔融步骤,节约了能源和时间。
直接还原法适用于一些高品质的铁矿石,能够生产出高品质的铁水。
炼铁的原理和工艺的发展离不开现代化的科学技术和工艺装备的进步。
随着炼铁技术的不断改进,炼铁工艺变得更加高效、环保和节能。
新型的炼铁工艺,如高炉煤气脱硫、废气脱硝等技术的应用,使得炼铁过程中的废气和废水得到了有效的处理和利用,减少了对环境的污染。
炼铁原理
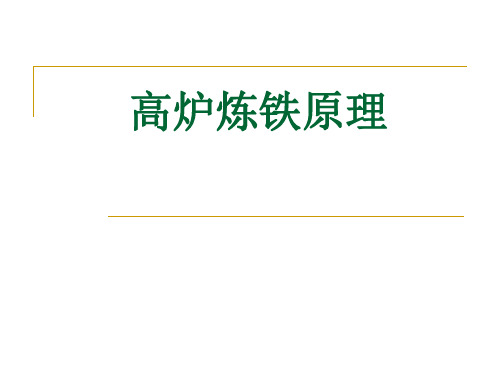
炉喉
原 始 的 高 炉
炉身
炉腰 炉腹 炉缸
五 段 式 炉 型 的 现 代 高 炉
高炉炉型演变示意图
3、 附属系统的组成和作用
(1)原料系统; (2)送风系统; (3)渣铁处理系统; (4)煤气清洗系统; (5)喷吹系统。
4 、炉内冶炼工艺过程(介绍)
炼铁系统
三、 高炉内冶炼过程的描述
(3)高炉煤气
高炉煤气化学成分为CO , CO2 , H2, N2, 及少量 CH4。高炉冶炼每吨普通生铁所产生的煤气量随焦 比水平的差异及鼓风含氧量的不同差别很大,低者 只有1600m3/t,高者可超过3500 m3/t。煤气成分差 异很大,先进的高炉煤气的化学能得到充分利用, 其 η co( = CO2%/CO2%+CO% )可超过50%,即煤气 中CO%可低于21, CO2%比之稍高。
碱性熔剂:硅石,很少使用。
对碱性熔剂质量的要求
(1)碱性氧化物(CaO, MgO)含量高;
(2)有害杂质(S, P)少; (3)有较高的机械强度和适宜的粒度。
• 1.5.2.2 其它含铁原料
高炉炉尘 氧气转炉炉尘 电炉烟灰尘 轧钢皮 铁屑料 钢渣
四、燃料
焦炭的作用:
(1)发热剂 (2)还原剂 (3)高炉料柱骨架
高炉的精料
应用最为广泛的造块方法主要有:烧结法和球 团法。 人造富矿(熟料):粉矿经造块获得的烧结矿 和球团矿。
人造富矿的种类
பைடு நூலகம்烧结矿 球团矿 天然块矿
高炉的炉料结构
图 烧结生产流程
1-驱动大星轮;2-布料器;3-给料漏斗;4-点火器;5-台车;6- 风箱;7-排矿部分;8-破碎机(格筛);9-抽风之管;10-大烟道; 11-灰箱;12-双星档板;13-至主风机 图 带式烧结机
炼铁的原理

炼铁的原理
炼铁是最古老的一种金属加工方式,被用来制造工具和武器。
自古以来,它一直被认为是重要的金属加工工艺。
炼铁的原理是,从矿石中提取铁,并通过高温熔炼将其转变成铁。
炼铁过程主要包括矿石加工、焙烧分解、熔炼提取和铸造冷却四个步骤。
首先,将矿石经过研磨、细碎和筛选等加工后分解成小颗粒,然后将其加入焙烧炉中,在高温环境中进行熔炼,提取铁,然后将铁倒入铸模中,形成铸件。
最后,将铸件冷却,然后就可以使用了。
炼铁可以制造出高质量的金属铸件,具有良好的耐热性、耐腐蚀性和耐冲击性。
炼铁还可以用来制造工具和武器,如农具、铲子、斧头和剑等。
这些工具和武器可以帮助人们完成日常工作和保护自己。
炼铁的原理至今仍然被广泛应用,这种古老的方式也可以改良,使之更加有效地制造出高质量的金属制品。
同时,由于炼铁的方式使用的是更加环保的燃料,所以这种方式对环境的影响也较小。
此外,由于炼铁的方法不需要特殊的设备,也不需要高昂的费用,因此在发展中国家仍然是一种可行且受欢迎的加工方式。
总之,炼铁是一种古老而又经久不衰的加工方式,它可以制造出高质量的金属制品,并且不会对环境造成太大的影响。
炼铁的原理化学反应

炼铁的原理化学反应炼铁是指将铁矿石经过高温还原反应,从中提取出金属铁的过程。
炼铁是工业生产中非常重要的环节,铁是一种重要的结构材料,广泛用于建筑、制造业等领域。
炼铁的原理可以归纳为以下几个方面:铁矿石的还原、熔化和分离。
以下将详细介绍每个步骤的化学反应。
首先,铁矿石中主要含有的铁矿石是铁石和赤铁矿(化学式为Fe2O3)。
铁石和赤铁矿中的铁是以三价和二价状态存在的。
在炼铁的过程中,需要将三价铁还原成二价铁,这个还原反应可以表示为:Fe2O3 + 3CO →2Fe + 3CO2这个反应是一个热力学上的可行反应,也是炼铁最关键的一步。
还原反应需要提供足够高的温度和适当的还原剂,常用的还原剂为一氧化碳(CO)或水蒸气(H2O)。
在高温下,一氧化碳和水蒸气能够与铁石或赤铁矿中的氧气反应,将氧还原成水蒸气或二氧化碳,从而将铁的价态从三价还原为二价。
其次,还原反应发生后得到的二价铁就是我们所需的金属铁。
二价铁随着高温的升高逐渐熔化,形成熔融铁。
熔融铁中还会含有少量的不纯物,如硫、磷等。
为了降低不纯物的含量,需要通过添加矿石、焦碳等还原剂进行除杂。
此外,炼铁过程中还需要加入熔剂,主要是石灰石(CaCO3)或白云石(MgCO3)。
这些矿石在高温下能够与熔融铁中的硫反应生成硫化物,并与矿渣分离。
化学反应如下:CaCO3 + FeS →CaS + FeO + CO2最后,熔融铁和矿渣在高温下会分离。
铁较重,所以砂岩矿石中主要含有铁,矿渣剩余的则是一些杂质。
分离的目的是将金属铁从其他杂质中分离出来,进一步提高纯度。
总结起来,炼铁的原理主要包括矿石的还原、熔化和分离。
还原反应将铁矿石中的三价铁还原成二价铁,熔化反应将二价铁熔化成熔融铁,分离反应将熔融铁与矿渣分离。
这些过程中涉及到的化学反应需要提供高温、适当的还原剂和熔剂,以及通过添加矿石除杂等方法来实现铁的提取和纯化。
炼铁是一项复杂而重要的工艺,这些步骤中的化学反应确保了金属铁的提取和纯化过程。
- 1、下载文档前请自行甄别文档内容的完整性,平台不提供额外的编辑、内容补充、找答案等附加服务。
- 2、"仅部分预览"的文档,不可在线预览部分如存在完整性等问题,可反馈申请退款(可完整预览的文档不适用该条件!)。
- 3、如文档侵犯您的权益,请联系客服反馈,我们会尽快为您处理(人工客服工作时间:9:00-18:30)。
1.1高炉炼铁生产工艺流程
1. 高炉本体 2. 上料系统 3. 送风系统 4. 煤气净化系统 5. 渣铁处理系统 6. 喷吹燃料系统
3பைடு நூலகம்
1.2炼铁原料及评价
1. 铁矿石的分类 2. 对铁矿石的评价: ① 含铁品位 • p1=(F/f)(P-Cp2-Cp3-g) • 式中p1 为原料的价值;F为原料的含铁品位;f为生铁中含铁;p为生铁的
4
1.2炼铁原料及评价
3. 矿石入炉前的处理 ① 整粒.8-30mm ② 造块. ③ 分级和筛分.
5
1.3熔剂
1.碱性熔剂 石灰石,白云石[(Ca,Mg)CO3], 2.酸性熔剂 硅石(SiO2) 3.有效熔剂性 有效熔剂性= [w(CaO) +w(MgO) ]-
w( SiO2 ) ×R 2
6
1.4锰矿
气,而焦炉煤气主要供民用,只有在特殊 条件下高炉才使用少量焦炉煤气。故高炉 煤气就成为钢铁企业内部的主要气体燃料 了。
13
1.7高炉冶炼产品
1.生铁 炼钢生铁,铸造生铁,铁合金一般不用高炉,用
电炉 2.煤气 3.炉渣(水渣)
14
1.8高炉冶炼主要经济指标
1.利用系数: ηV=P/V------t/(m3.d) 2.焦比 K=Q/P------kg/t 3.煤比 PCI=M/P -----kg/t 4.燃料比 Kf =QfP 式中Kf——冶炼1 t生铁消耗的焦炭和喷吹燃料的数量之和; Qf——高炉一昼夜消耗的干焦量和喷吹燃料之和。
车间成本;C为焦比;c为单位生铁消耗的熔剂;p2 为焦炭的价格;p3 为 熔剂的价格;g为每吨生铁的车间生产费用。 ② 脉石的成分及分布 ③ 有害元素的含量. 1. S (0.1-0.3) %, 2. 矿最低允许P=([P]铁-[P焦.熔])/K. K---单位(吨)生铁矿耗量. 3. K=Fe生/Fe矿 4. (K,Na) <2-3Kg/t铁, Zn <0.15 Kg/t铁 ④ 有益元素,矿石的还原性 ⑤ 矿石的高温性能 ⑥ 矿石的其它性能(强度,粒度,热爆裂性,化学成分的稳定性)
1. 锰矿用途 2. 质量要求(和铁矿石一样) • w(Fe允) ={100-
[w(C)+w(Si)+w(P)+w(S)+w(Mn)+…]}/K K=w(Mn)η·w(Mn)矿 • 式中w(Fe允)——锰矿允许的极限Fe的质量分数, %; • K——冶炼单位重量合金时锰矿消耗量;w(Mn) 矿——锰矿含Mn品位,%;η ——炉内Mn的回 收率,冶炼一般生铁时此值为50%~60%,炼锰 铁时此值可达80%~85%。
15
1.8高炉冶炼主要经济指标
5.置换比
• R=(K0-K1+ΣΔK)/PCI
• 式中R——喷吹的辅助燃料的置换比;
•
K0——未喷吹辅助燃料前的实际平均焦比;
•
K1——喷吹辅助燃料后的平均入炉焦比;
•
∑ΔK——其他各种因素对实际焦比影响的代
数和。
16
1.8高炉冶炼主要经济指标
6.冶炼强度。 • 冶炼强度(I)是冶炼过程强化的程度,即
每昼夜(d)每1 m3高炉有效容积燃烧的干 焦耗用量: • 冶炼强度=干焦耗用量有效容积×实际工作 日t/(m3·d) • 利用系数(ηV)=综合冶炼强度(If)综合焦 比(Kf)t/(m3·d)
炉容级别/m3 焦炭灰分/% 焦炭含硫/%
M40/% M10/% CSR/% CRI/% 粒度范围/% 大于上限/% 小于下限/%
1000 ≤13 ≤0.7 ≥78 ≤8 ≥58 ≤28 75-20 ≤10 ≤8
2000 ≤13 ≤0.7 ≥82 ≤7.5 ≥60 ≤26 75-25 ≤10 ≤8
3000 ≤12.5 ≤0.7 ≥84
≤7 ≥62 ≤25 75-25 ≤10 ≤8
4000 ≤12 ≤0.7 ≥85 ≤6.5 ≥65 ≤25 75-25 ≤10 ≤8
5000 ≤12 ≤0.7 ≥86 ≤6 ≥66 ≤25 75-30 ≤10 ≤8
10
1.6高炉燃料
3.对煤粉的质量要求 ①煤的燃烧性能好 ②煤的灰分越低越好,要求低于12%。 ③煤的硫分越低越好,一般要求小于0.7%,最高不
炼铁原理与工艺
1
一、高炉炼铁简介
• 钢铁联合企业中的炼铁生产 • 一种是高炉-氧气转炉-轧机流程;一种是直接还原或熔融还原-电炉
-轧机流程。前者被称为长流程,后者则被称为短流程。目前长流程 是主要流程。但因它必须使用块状原料,需要配用质量好的炼焦煤在 焦炉内炼成性能好的冶金焦,粉矿和精矿粉要制成烧结矿或球团矿。 这两道生产工序不但能耗高,而且生产中产生粉尘,污水和废气等对 环境造成污染。所以长流程面临能源和环保等的挑战,直接还原和熔 融还原是用来替代高炉炼铁的两种工艺。 • 直接还原和熔融还原炼铁工艺的特点是,用块煤或气体还原剂代替高 炉炼铁工艺所必需的焦炭来还原天然块矿、粉矿或人造块矿(烧结矿 或球团矿)具有相当大的适应性,特别适用于某些资源匮乏,环保要 求特别严格的地区或国家,但其生产规模较高炉小而且很多技术问题 还有待解决或完善。 • 各种炼铁法的设备及生产方式差别很大,但其原理是相同的。
⑦ ⑥胶质层越薄越好,Y<10rnrn,以免在 喷吹过程中结焦,堵塞喷枪影响煤粉喷吹 和高炉正常生产。
⑧ ⑦煤的灰熔点温度,要求高一些。因为灰 熔点太低时风口容易结焦和堵塞煤枪。
⑨ ⑧流动性和输送性能高。。
12
1.6高炉燃料
• 气体燃料 • 气体燃料在钢铁企业中有重要作用。天然
气、石油气、高炉煤气、发生炉煤气等。 • 根据我国资源条件,不可能普遍使用天然
7
1.6高炉燃料
1.焦炭 焦炭的作用: ① 在风口前燃烧,提供冶炼所需热量 ② 固体C及其氧化产物CO,是氧化物的还原
剂 ③ 高温区料柱的骨架,煤气通路 ④ 铁水渗碳
8
1.6高炉燃料
2.高炉对焦炭质量要求: 化学成分,C,A,W,S, 冷强度:M40,M10 热强度,CSR 反应性.CRI
9
焦炭质量要求
大于0.8% ④ 煤粉的粒度合适 ⑤ ④煤的可磨性好,高炉喷煤需要将煤磨到一定细
度,煤的可磨性指数(哈氏HGI)应在60~90之间, 低于50的煤很硬,难磨。高于90的烟煤虽然易 磨,但往往是粘结性强的煤,可能给磨煤和输煤 造成困难。
11
1.6高炉燃料
⑥ 煤的发热值越高越好,烟煤的低位发热值 不小于26000kJ/kg,无烟煤的低位发热值 不小于29000kJ/kg。