炼铁生产工艺技术简介
烧结炼铁生产工艺简介

烧结炼铁生产工艺简介4.1.1生产工艺调查4.1.1.1烧结系统生产工艺调查4.1.1.1.1生产单元工艺调查因5座烧结生产工艺相同,此处以3#烧结系统生产工艺为例介绍。
烧结系统以含铁原料、焦粉、生石灰、白云石、高炉煤气为原料,通过配料、混料、烧结、破碎、筛分工序制得烧结矿,烧结矿作为炼铁原料进入炼铁系统。
具体烧结工艺如下。
1)配料工序铲车司机将焦粉、含铁原料、生石灰、白云石加入地下配料仓,配料仓下方设有圆盘给料机,原料自给料机中落至配料皮带,按配比进行配料。
皮带将原料输送至一次混料机内。
在配料仓旁设有布袋除尘器,对配料仓含尘废气进行净化。
除尘器所收集灰渣由除尘工定期清理。
2)混料工序输水管向一次混料机(以下简称一混机)加水,一混机滚动将物料混匀,然后经皮带输送至二次混料机(以下简称二混机),再次加水,调整混合料水分,二混机滚动进行制粒。
混料完成后,物料经皮带机送入烧结机上方混合料矿槽。
整个混料过程均为机械操作,员工进行巡检。
混料工序与配料工序共用一套布袋除尘器,除尘器对混料过程产生的粉尘进行净化。
3)烧结工序烧结机设铺底料装置。
从后续筛分工序中运来的Φ5~20mm铺底料,由皮带机送入铺底料矿槽,由矿槽下的给料闸门及摆动漏斗均匀地布在台车上,铺底料厚度约为30~50mm,铺底料槽设有料位信号。
然后混合料矿槽内的原料由布料机均匀地布在烧结台车上。
布料厚度一般600mm,稍低于台车栏板高度。
以高炉煤气为燃料,经点火器进行点火烧结,炉膛压力为微正压。
点火前,启动主烟道风机进行负压抽风。
点火后,随着台车向前运行,在抽风机的抽力作用下烧结矿层逐渐下移。
到达烧结机倒数第二风箱处,料层全部烧透,成为烧结矿。
烧结完成后台车移动,离开点火器,进入冷却段。
在冷却装置下方设抽风机进行冷却,将烧结矿冷却到150℃以下。
台车运行到机尾,通过翻车机将烧结矿卸到四辊破碎机内。
烧结机中烧结段产生的废气经电除尘器除尘后,由抽风机抽入脱硫塔,净化后直接排空;冷却段产生的废气经电除尘器除尘后直接排空。
高炉炼铁工艺流程简介
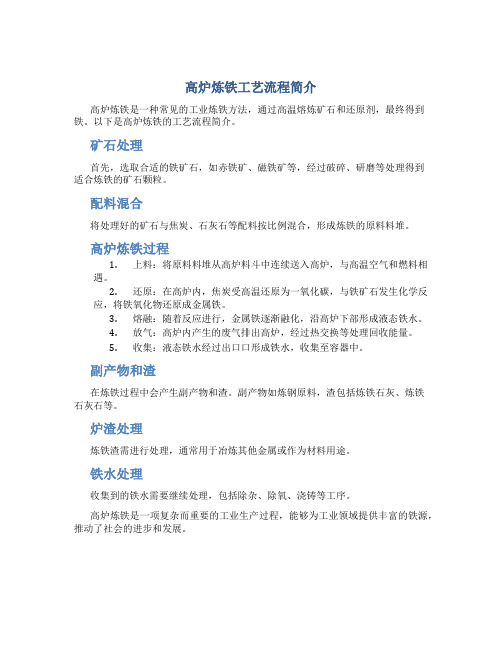
高炉炼铁工艺流程简介
高炉炼铁是一种常见的工业炼铁方法,通过高温熔炼矿石和还原剂,最终得到铁。
以下是高炉炼铁的工艺流程简介。
矿石处理
首先,选取合适的铁矿石,如赤铁矿、磁铁矿等,经过破碎、研磨等处理得到
适合炼铁的矿石颗粒。
配料混合
将处理好的矿石与焦炭、石灰石等配料按比例混合,形成炼铁的原料料堆。
高炉炼铁过程
1.上料:将原料料堆从高炉料斗中连续送入高炉,与高温空气和燃料相
遇。
2.还原:在高炉内,焦炭受高温还原为一氧化碳,与铁矿石发生化学反
应,将铁氧化物还原成金属铁。
3.熔融:随着反应进行,金属铁逐渐融化,沿高炉下部形成液态铁水。
4.放气:高炉内产生的废气排出高炉,经过热交换等处理回收能量。
5.收集:液态铁水经过出口口形成铁水,收集至容器中。
副产物和渣
在炼铁过程中会产生副产物和渣。
副产物如炼钢原料,渣包括炼铁石灰、炼铁
石灰石等。
炉渣处理
炼铁渣需进行处理,通常用于冶炼其他金属或作为材料用途。
铁水处理
收集到的铁水需要继续处理,包括除杂、除氧、浇铸等工序。
高炉炼铁是一项复杂而重要的工业生产过程,能够为工业领域提供丰富的铁源,推动了社会的进步和发展。
钢铁的冶炼原理及生产工艺流程

炼铁方法主要有高炉法、直接还原法、熔融还原法等,其原理是矿石在特定的气氛中(还原物质CO、H2、C;适宜温度等)通过物化反应获取还原后的生铁。
生铁除了少部分用于铸造外,绝大部分是作为炼钢原料。
1、高炉炼铁的冶炼原理(应用最多的)
1)炼铁的原理:用还原剂将铁矿石中的铁氧化物还原成金属铁。
铁氧化物(Fe2O3、Fe3O4、FeO)+还原剂(C、CO、H2)铁(Fe)
2) 炼铁的方法
(1)直接还原法(非高炉炼铁法)
(2)高炉炼铁法(主要方法)
3)高炉炼铁的原料及其作用
(1)铁矿石:(烧结矿、球团矿)提供铁元素。
(2)焦碳:提供热量;提供还原剂;作料柱的骨架。
(3)熔剂:(石灰石、白云石、萤石)
使炉渣熔化为液体;去除有害元素硫(S)。
(4)空气:为焦碳燃烧提供氧。
2、工艺流程
生铁的冶炼虽原理相同,但由于方法不同、冶炼设备不同,所以工艺流程也不同。
下面分别简单予以介绍。
高炉生产是连续进行的
从炉顶(一般炉顶是由料种与料斗组成,现代化高炉是钟阀炉顶和无料钟炉顶)不断地装入铁矿石、焦炭、熔剂,从高炉下部的风口吹进热风(1000~1300摄氏度),喷入油、煤或天然气等燃料。
装入高炉中的铁矿石,主要是铁和氧的化合物。
在高温下,焦炭中和喷吹物中的碳及碳燃烧生成的一氧化碳将铁矿石中的氧夺取出来,得到铁,。
炼铁高炉 生产工艺

炼铁高炉生产工艺炼铁高炉是一种常见的冶金设备,用于将铁矿石转化为铁水。
下面是炼铁高炉的生产工艺,共700字。
炼铁高炉的生产工艺主要包括原料准备、炉顶喷吹、炉料下料、高炉的操作和维护等几个方面。
首先是原料准备。
高炉的主要原料是铁矿石、焦炭和石灰石。
这些原料需要经过粉碎、筛分和称量等工艺进行准备。
具体来说,铁矿石需要经过破碎、碎矿和磁选等工艺,将矿石分解成合适的粒度;焦炭需要经过煤气化和碳化等工艺,将煤转化为焦炭;石灰石需要经过粉碎和预煅等工艺,将其变成石灰。
准备好的原料需要按照一定比例进行混合。
接下来是炉顶喷吹。
喷吹是高炉冶炼的重要环节,通过喷吹氧气、柴油或天然气等燃料,使高炉内的燃烧反应达到最佳状态。
喷吹能够提供高炉所需的热量和氧气,提高炉内的温度,加速矿石的还原反应。
通过合理调节喷吹参数,可以提高高炉的冶炼效率和产能。
然后是炉料下料。
炉料下料是将准备好的炉料从上料斗倒入高炉中的过程。
通过计量设备和控制系统,按照一定的配比将炉料逐层放入高炉炉腔。
炉料的下料速度需要适应高炉冶炼的需求,以保证炉内矿石和焦炭的适度接触,促进还原反应的进行。
高炉的操作和维护是保证生产顺利进行的关键。
操作人员需要通过仪表监测高炉的温度、压力和流量等参数,及时调整燃料供给、喷吹氧气的速度和炉料的下料速度,以维持高炉的正常运行。
同时,操作人员还需要定期检查高炉的设备状态,清理和维修设备,防止故障和事故的发生。
总之,炼铁高炉的生产工艺包括原料准备、炉顶喷吹、炉料下料、高炉的操作和维护等几个环节。
每个环节都有其具体的操作步骤和要求,通过科学合理的操作和维护,能够提高高炉的冶炼效率和产品质量。
炼铁工艺中的烧结与球团化技术
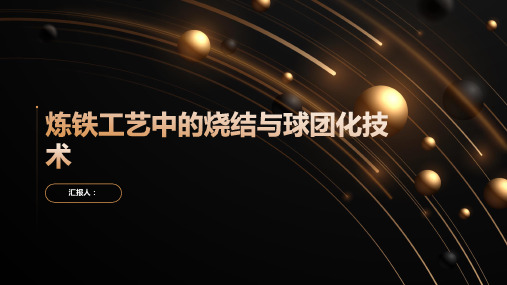
焙烧:在高温下焙烧球团,
使其发生化学反应,形成具
配料:根据生产需求和原料
有一定强度的球团矿
性质进行配料
分选:根据球团矿的粒度和
造球:通过造球机将混合料 制成球团
成分进行分选,保证产品质 量
原料准备:选择合适的铁矿 石、燃料和熔剂
干燥:将球团干燥至一定湿 度,便于后续处理
成品:将分选后的球团矿包 装入库,供后续使用
新型烧结剂:提高烧结效率,降低能耗
新型球团化工艺:提高球团化效率,降 低能耗
新型球团化剂:提高球团强度,改善球 团质量
新型烧结设备:提高生产效率,降低能 耗
新型烧结工艺:提高烧结速度,降低生 产成本
新型球团化设备:提高球团化效率,降 低能耗
提高产品质量: 通过改进工艺 和设备,提高 烧结与球团化 产品的质量, 降低废品率。
降低生产成本: 通过优化生产 流程和采用节 能技术,降低 生产成本,提 高产品竞争力。
提高生产效率: 通过采用自动 化和智能化技 术,提高生产 效率,缩短生
产周期。
开发新产品: 通过研发新技 术和新材料, 开发具有更高 附加值的新产 品,满足市场
需求。
汇报人:
原料准备:选择合适的原料,如铁矿石、 燃料、熔剂等
混合:将原料按比例混合,形成烧结料
制粒:将混合后的烧结料制成颗粒状, 便于烧结
烧结:将制粒后的烧结料放入烧结设备 中,在高温下进行烧结反应,形成烧结 矿
冷却:烧结完成后,将烧结矿冷却至常 温,便于后续处理
分选:将烧结矿进行分选,去除杂质, 得到合格的烧结矿产品
节能技术的应用:如高效燃烧技 术、余热回收技术等
减排技术的应用:如废气净化技 术、废水处理技术等
高炉炼铁工艺介绍

高炉炼铁工艺介绍1. 简介高炉炼铁是一种重要的冶金工艺,用于将铁矿石转化为生铁的过程。
它是钢铁工业的核心环节之一,用于生产各种钢材。
2. 高炉炼铁的基本原理高炉炼铁的基本原理是将铁矿石与焦炭等还原剂混合后,在高温下进行还原反应,将铁矿石中的氧化铁还原为金属铁。
同时,炉内的温度和化学反应条件还可以使一部分其他有害物质被除去。
3. 高炉炼铁的工艺流程3.1 高炉炉缸高炉炉缸是高炉的主要部分,通常由炉壳、炉缸和炉缸衬板组成。
炉缸衬板由耐火材料制成,以承受高温和化学侵蚀。
3.2 上料系统上料系统的主要作用是将矿石、焦炭、燃料及其他辅助材料送入高炉。
通常,这些原料需要经过破碎、筛分、称重等处理。
3.3 炉冰炉冰是指在高炉顶部装置的冷却设备,用于冷却进入高炉的热气体。
这样可以减少热能的损失,并为高炉提供所需的煤气流动动力。
3.4 高炉通气系统高炉通气系统主要包括风机和风口。
高炉顶部的风机通过送风管将空气送入高炉,从而维持高炉的氧气供应。
风口是位于炉缸底部的通气装置,用于引入煤气和空气,同时也是控制和调节高炉燃烧的关键。
3.5 高炉冷却系统高炉冷却系统主要用于冷却高炉的各个部位,包括炉缸、炉壁和炉顶。
这些部位会受到高温的侵蚀,而冷却系统可以降低温度,延长高炉使用寿命。
3.6 出铁系统出铁系统用于从高炉底部将生铁和渣铁分离出来。
通常通过出铁口将液态金属铁和渣铁分别引出,然后进一步处理。
3.7 气体处理系统高炉产生的煤气会通过气体处理系统进行处理。
其中一种常见的处理方法是将煤气用作燃料,同时采用高炉煤气洗涤的方式除去其中的尘埃和硫化物等有害物质。
4. 高炉炼铁的优缺点4.1 优点•高炉炼铁工艺稳定,适合大规模生产。
•可以利用多种铁矿石和煤炭,适应不同的原料条件。
•高炉炼铁可以同时除去一部分有害物质,对环境保护有一定的效果。
4.2 缺点•高炉炼铁能耗较高,对资源消耗较大。
•高炉炼铁产生的煤气和废渣需要进一步处理,处理过程中会产生一定的环境污染物。
高炉炼铁生产工艺流程简介
高炉炼铁生产工艺流程简介高炉炼铁是一种重要的冶炼工艺,用于从铁矿石中提取纯铁。
这种工艺已经存在了数百年,经过不断的改进和创新,如今已经成为现代钢铁工业中不可或缺的一部分。
在高炉炼铁的生产工艺中,铁矿石经过一系列的处理和反应,最终得到纯净的铁。
高炉炼铁的工艺流程可以分为几个关键步骤:原料准备、炉料装入、炉内反应和铁的提取。
首先是原料准备。
在高炉炼铁的工艺中,主要原料包括铁矿石、焦炭和石灰石。
铁矿石是含有铁的矿石,通常是氧化铁或含铁的矿物。
焦炭是一种煤炭的变种,经过高温处理后,除去了大部分杂质,成为一种理想的还原剂。
石灰石主要用于吸收炉内产生的硫化物。
这些原料需要经过精确的配比和处理,以确保炉内反应的顺利进行。
接下来是炉料装入。
在高炉炼铁的工艺中,原料需要按照一定的比例和顺序装入高炉中。
通常情况下,铁矿石、焦炭和石灰石会被混合在一起,然后通过输送带或其他装料设备装入高炉的上部。
这个过程需要精确的控制,以确保炉料的均匀分布和稳定的运行。
然后是炉内反应。
一旦炉料装入高炉中,就会开始炉内的化学反应。
在高炉内,炉料经历高温和还原气氛的作用,铁矿石中的氧化铁被还原为纯铁,并与焦炭中的碳结合成为铁的合金。
同时,石灰石会吸收炉内产生的硫化物,防止铁中含有过多的硫。
这些反应需要在高炉内精确控制温度、气氛和炉料的流动,以确保产生高质量的铁。
最后是铁的提取。
经过一段时间的炉内反应,纯铁会从高炉底部的风口处流出,并收集在铁水槽中。
这个过程需要精确的控制高炉的操作参数,以确保铁的质量和产量。
一旦铁水收集起来,就需要进行进一步的处理和冶炼,以得到最终的铁产品。
总的来说,高炉炼铁是一个复杂的工艺过程,需要精密的设备和精确的操作。
通过不断的改进和创新,现代高炉炼铁工艺已经成为一种高效、环保和可持续的生产方式,为钢铁工业的发展做出了重要贡献。
随着科技的不断进步,相信高炉炼铁工艺在未来会有更多的发展和突破,为人类社会的发展带来更多的好处。
高炉炼铁生产工艺流程简介
高炉炼铁生产工艺流程简介[导读]:高炉炼铁生产是冶金(钢铁)工业最要紧的环节。
高炉冶炼是把铁矿石复原成生铁的连续生产过程。
铁矿石、焦炭和熔剂等固体原料按规定配料比由炉顶装料装置分批送进高炉,并使炉喉料面维持一定的高度。
焦炭和矿石在炉内形成交替分层结构。
矿石料在下落过程中逐步被复原、熔化成铁和渣,聚拢在炉缸中,定期从铁口、渣口放出。
高炉生产是连续进行的。
一代高炉〔从开炉到大修停炉为一代〕能连续生产几年到十几年。
本专题将具体介绍高炉炼铁生产的工艺流程,要紧工艺设备的工作原理以及操纵要求等信息。
由于时刻的仓促和编辑水平有限,专题中难免出现遗漏或错误的地点,送不大伙儿补充指正。
高炉冶炼目的:将矿石中的铁元素提取出来,生产出来的要紧产品为铁水。
付产品有:水渣、矿渣棉和高炉煤气等。
高炉冶炼原理简介:高炉生产是连续进行的。
一代高炉〔从开炉到大修停炉为一代〕能连续生产几年到十几年。
生产时,从炉顶〔一般炉顶是由料种与料斗组成,现代化高炉是钟阀炉顶和无料钟炉顶〕不断地装进铁矿石、焦炭、熔剂,从高炉下部的风口吹进热风〔1000~1300摄氏度〕,喷进油、煤或天然气等燃料。
装进高炉中的铁矿石,要紧是铁和氧的化合物。
在高温下,焦炭中和喷吹物中的碳及碳燃烧生成的一氧化碳将铁矿石中的氧夺取出来,得到铁,那个过程喊做复原。
铁矿石通过复原反响炼出生铁,铁水从出铁口放出。
铁矿石中的脉石、焦炭及喷吹物中的灰分与参加炉内的石灰石等熔剂结合生成炉渣,从出铁口和出渣口分不排出。
煤气从炉顶导出,经除尘后,作为工业用煤气。
现代化高炉还能够利用炉顶的高压,用导出的局部煤气发电。
高炉冶炼工艺流程简图:[高炉工艺]高炉冶炼过程:高炉冶炼是把铁矿石复原成生铁的连续生产过程。
铁矿石、焦炭和熔剂等固体原料按规定配料比由炉顶装料装置分批送进高炉,并使炉喉料面维持一定的高度。
焦炭和矿石在炉内形成交替分层结构。
矿石料在下落过程中逐步被复原、熔化成铁和渣,聚拢在炉缸中,定期从铁口、渣口放出。
炼铁原理与工艺
炼铁原理与工艺炼铁是将铁矿石经过一系列的物理和化学变化,最终得到纯铁的过程。
它是钢铁工业的基础生产工艺,也是现代工业化不可或缺的一环。
炼铁的原理和工艺经过长时间的发展和改进,已经非常成熟和高效。
炼铁的原理主要包括铁矿石还原和熔融两个过程。
首先是铁矿石的还原,即将铁矿石中的氧化铁还原为金属铁。
这一过程通常使用焦炭作为还原剂,通过高温和还原剂的作用,将铁矿石中的氧化铁还原为金属铁。
还原反应的化学方程式为:Fe2O3 + 3C = 2Fe + 3CO。
在这个反应中,焦炭中的碳与氧化铁发生反应,生成金属铁和一氧化碳。
还原后的金属铁并不是纯铁,还含有一些杂质,如硅、锰、磷等。
因此,还需要进行二次处理,即熔融。
熔融是将还原后的金属铁与其他添加剂一起加热到高温,使其融化并进行反应。
熔融的目的是去除杂质,并加入适量的合金元素,以提高铁的性能。
通常加入的合金元素有碳、铬、镍等。
熔融过程中,炉温要达到1600℃以上,使铁液中的杂质和氧化物被还原和脱离,形成纯净的铁水。
炼铁的工艺包括高炉法和直接还原法两种。
高炉法是目前应用最广泛的炼铁工艺,它使用高炉作为主要设备。
高炉法的工艺流程一般包括炉料的装入、预热、还原和熔融等过程。
炉料主要由铁矿石、焦炭和石灰石组成,其中焦炭是还原剂,石灰石用于脱硫。
在高炉中,炉料从顶部装入,燃料从底部喷入,通过燃烧产生的高温将铁矿石还原和熔化。
熔融的铁水经过除渣、出铁等处理后,得到纯铁。
直接还原法是近年来发展起来的一种新型炼铁工艺。
它通过在直接还原炉中加热还原剂和铁矿石,将铁矿石直接还原为金属铁。
这种工艺省去了高炉的熔融步骤,节约了能源和时间。
直接还原法适用于一些高品质的铁矿石,能够生产出高品质的铁水。
炼铁的原理和工艺的发展离不开现代化的科学技术和工艺装备的进步。
随着炼铁技术的不断改进,炼铁工艺变得更加高效、环保和节能。
新型的炼铁工艺,如高炉煤气脱硫、废气脱硝等技术的应用,使得炼铁过程中的废气和废水得到了有效的处理和利用,减少了对环境的污染。
炼铁生产工艺流程
炼铁生产工艺流程炼铁是从矿石中提取出铁金属的过程,它是整个钢铁行业中最基础的环节之一。
下面我来介绍一下炼铁的生产工艺流程。
首先,炼铁的第一步是选矿。
选矿是指从原生铁矿石中选出富含铁元素的矿石。
常见的矿石有赤铁矿、磁铁矿等。
在选矿过程中,工人会使用重力分选、磁选、浮选等方法来分离出铁矿石。
接下来是矿石炼焙。
矿石炼焙是将铁矿石加热使其发生化学反应,去除其中非铁金属元素。
这个过程一般在高炉中进行。
高炉是一个巨大的圆柱形窑体,内部有坩埚,坩埚下方有炭斗和风口。
燃料通常是焦炭,燃烧后产生高温,将矿石加热。
在高炉中,矿石逐渐熔化,非铁金属元素分解释放出来,而金属铁则被保留下来。
第三步是炼铁。
在高炉中,矿石熔化后,会产生高温高压的液态铁和矿渣。
液态铁比矿渣密度大,会自然下沉到底部。
矿渣则会浮在液态铁上方。
工人会通过倾吊装置将底部的液态铁放出,并用矿渣渣石填满,防止液态铁跑溜。
之后是铸铁生产。
液态铁放出后,可以用来生产铸铁。
通常情况下,液态铁会流入连铸机内,冷却成铸坯。
连铸机是一个灵活和高效的设备,可以将液态铁快速冷却成坯料,并通过成型辊来定形。
这样得到的铸坯可以根据需要进一步加工成铸件。
最后一步是铁的精炼。
炼铁过程中得到的铸坯中还存在一些杂质和气体,需要通过精炼来去除。
精炼通常是在电炉中进行。
电炉是一种能将电能转化为热能的设备,通过电炉加热铸坯,使其重新熔化。
在熔化过程中,杂质和气体会从铁液中挥发出来或沉积下来,从而实现铁的精炼。
以上就是炼铁的生产工艺流程。
通过选矿、矿石炼焙、炼铁、铸铁生产和精炼等步骤,从原生铁矿石中得到纯净的铁金属,为后续的钢铁加工奠定了基础。
炼铁生产工艺流程的不断改进和创新,使得炼铁工艺更加高效、环保和节能,为钢铁产业的发展做出了重要贡献。
- 1、下载文档前请自行甄别文档内容的完整性,平台不提供额外的编辑、内容补充、找答案等附加服务。
- 2、"仅部分预览"的文档,不可在线预览部分如存在完整性等问题,可反馈申请退款(可完整预览的文档不适用该条件!)。
- 3、如文档侵犯您的权益,请联系客服反馈,我们会尽快为您处理(人工客服工作时间:9:00-18:30)。
常见氧化物的ΔG0-T关系曲线(Ellingham图)
• •
0 0
千卡
ΔG0-T关系曲线
② ① ⑤ ③ ④
⑥
0
⑦ ⑧⑨ ⑩
200
0
0
温度
• • • • • • • • • • • • •
① 2C + O2 = 2CO ② 2Cu + O2 = 2CuO ③ 2Ni + O2 = 2NiO ④ 2Fe +O2 = 2FeO ⑤ 5P + O2 = P2O5 ⑥ 4/3Cr + O2 = 2/3Cr2O3 ⑦ 2Mn + O2 = 2MnO ⑧ 4/3V + O2 = 2/3V2O3 ⑨ Si + O2 = SiO2 ⑩ Ti + O2 = TiO ⑾ 4/3Al + O2 = 2/3Al2O3 (12) 2Mg + O2 = 2MgO (13) 2Ca + O2 = 2CaO
二、烧结工序
烧结工序的流程图如图所示
• 1、混合 • 从配料室出的料与冷、热返和水封料在混 一皮带上混合。冷、热返的配加采用圆盘 给料器;水封采用SFB型号的水封拉链机。 经混一皮带进入一混圆筒,在一混圆筒中 加水混匀进入二混圆筒。在二混中加入部 分水和水蒸气,以达到充分混匀、强化制 粒和提高混合料料温的作用。
用固体还原剂还原
由于在高温区有大量焦炭存在,生成的CO2立即与焦炭反应生成CO CO2+C─→2CO -165686kJ,因此最终反应为: FeO+CO─→Fe+3;) CO2+C─→2CO -165686kJ
FeO+C─→Fe+CO -152088kJ CO只是中间产物,最终消耗固体C,同时反应消耗大量热量。
烧结工艺流程简介
• 烧结处理的原料种类繁多,且物理化学性 质差异大,为使烧结矿的物理化学性能和 化学成份稳定,符合冶炼要求,同时使烧 结料具有良好的透气性以获得较高的烧结 生产率,必须把不同成份的含铁原料、熔 剂、燃料等根据烧结过程的要求和烧结矿 质量的要求进行精确的配料,配好的物料 经混匀、制粒、布料、烧结等工序处理生 产出符合高炉需要的烧结矿。
四、球团工艺流程简介
高炉炼铁原理简介
● 高炉是一种竖炉型的气体、液体、固体三相流共存的逆流式反应器。 ● 高炉生产具有高度的连续性,一代高炉(从开炉到大修停炉为一代)能 连续生产十年到二十年或更长。 ● 炉料(铁矿石、焦炭、熔剂等)从高炉炉顶(由料钟与料斗组成的钟式炉 顶,或无料钟炉顶)按规律分批层状加入,因重力自上而下运动,运动 过程中伴随炉料的干燥、加热、分解、还原、软化、熔融、滴落、渗碳、 熔化及铁渣分离,温度由常温升高到1450 -1500℃。 ● 热风(1000~1300 ℃ )从高炉下部的风口鼓入,并可喷入油、煤或天然 气等燃料以减少焦碳消耗。热风与风口前的焦炭反应生成以CO、N2为主 要成分的还原气体,还原气体自下而上运动,温度由2000-2300℃降低到 100-200℃。 ● 装入高炉中的铁矿石主要是铁的氧化物,在高温下,还原气体中的CO夺 取铁矿石中的氧,还原出金属铁,最终铁水从出铁口放出;铁矿石中的 脉石、焦炭及喷吹物中的灰分与加入炉内的石灰石等熔剂结合生成炉渣, 从出铁口和出渣口分别排出;煤气从炉顶导出,经除尘后,作为企业能 源平衡中的重要燃料。 运动中的炉料和还原气体间的动量、热量和质量传递构成了“传输原 理”这门钢铁冶金学科的重要专业基础理论课程
-Δ
氧化物的逐级还原原则
• 高炉中的还原剂为气体CO、H2和固体C, • 不论何种还原剂,铁氧化物的还原都遵循逐级还原原则。 >570℃ Fe2O3 <570℃ Fe2O3 (MnO2 (SiO2 Mn2O3 SiO Fe3O4 Fe3O4 Mn3O4 FeO Fe MnO Mn) Fe
Si )
铁-氧-碳平衡图
2 • 还原反应的基本原理
铁氧化物的还原
金属氧化物的还原反应可表示为; MeO + B = Me + BO ±Q 凡是与氧的亲和力大于金属元素(Me)与氧的亲和力的物质(B)都 可以作为还原剂,夺取金属氧化物(MeO)中的氧,使金属元素得以还原。
碳作为还原剂具有成本低、储量大并易于获取、随着温度升高与氧 的亲和力增大的特点,只要温度足够高,碳可以还原出绝大多数金属元素, 因此是火法冶金过程中最常用和最重要的还原剂。
高炉炼铁生产工艺技术 简 介
炼铁生产的重要地位
高炉炼铁是钢铁联合企业中最重要的工序
●生产成本占企业总成本的50%左右 ●工序能耗占企业总能耗的50--70% ●高度连续化的生产作业方式及其工艺技术特点所决定的极高的生产率 和作业率要求 ●对前(烧结、焦化)后(炼钢、制氧)工序生产组织的重大影响 ●对整个钢铁公司能源(煤气)平衡的重大影响 ●特有的生产条件(高温环境、液态渣铁、煤气、粉尘等 )对整个钢铁 公司安全管理的重大影响 ●多种外部条件对炼铁生产的影响和制约使炼铁生产组织的特有困难 ●高炉的停炉和开炉、以及日常检修中休风送风的特有的难度 ●工艺技术特点所决定的实现冶炼过程自动控制的困难 炼铁理所当然地成为钢铁联合企业的龙头工序,对企业的规模、生产 组织、经营、效益、安全等都产生极其重要影响
直接还原和间接还原
• 间接还原 用气体还原剂还原铁氧化物称为间接还原 大部分间接还原反应都是放热反应 (5个铁氧化物的还原反应中有4个是放热反应) 直接还原 用固体C还原铁氧化物称为直接还原 所有直接还原反应都是吸热反应 铁的直接还原度(rd) : 高价铁氧化物还原到FeO完全是通过间接还原完成,而FeO还原到Fe既有 间接还原又有直接还原,铁的直接还原度rd则表示经直接还原途径从FeO中 还原出的铁与被还原的全部铁量之比。 增加间接还原、减少直接还原、降低直接还原度是降低焦比的重要措施 改善矿石还原性、矿石整粒、提高熟料比、改善矿石高温性能、改善焦炭 的高温性能、高炉高压操作、高炉煤气的合理分布。
• 二)、配料 • 配料作为一重要的环节,是保证烧结过程的要求 和烧结质量的基础。 • 系统主要由pc机、plc、变频柜、电子皮带秤等几 部分构成。其配料过程:将计算好的配比输入pc 机上的配比输入栏,并在参数输入栏中选取要开 启的仓号和备用仓号及输入焦粉用量和混合料料 量。确定后,pc机将把各开启仓分配的料量传给 plc柜,plc再将料量信息传给变频柜。电子皮带秤 由变频柜控制,当皮带上的下料量与分配的料量 不相符合时,偏差信息将反馈给plc和变频柜,从 而调整皮带秤的转速以达到料量的准确性。
Fe-O-C系气相平衡图各反应式
用气体还原剂还原
>570 ℃ 3Fe2O3+CO─→2Fe3O4+CO2 +37112kJ Fe3O4+CO─→3FeO+CO2 -20878kJ FeO+CO─→Fe+CO2 +13598kJ < 570 ℃ 3Fe2O3+CO─→2Fe3O4+CO2 +37112kJ Fe3O4+CO─→3Fe+4CO2 +17154kJ
高炉炼铁生产的优点
●两相流充分的热交换,具有高的热效率,大型高炉的有效 热量利用系数可达90%。 ●气固相反应的特点:气体的高扩散性,与固体物料的充分 接触,反应界面大,传热与传质动力学条件好。 ●大型和连续化的生产方式,具有高的生产率,大型高炉日 产铁可达10000t以上。 (2006年宝钢4350m3高炉,利用系数2.311,日产10052t。 京唐联合钢铁公司建设中的2 × 5500m3高炉,年产生铁 898万t,利用系数2.3以上。目前世界最大的高炉是日本 新日铁大分2#高炉5775m3,日产铁13000t以上。) ●成熟的工艺流程,具有极高的作业率,可达到98-99%。 (2006年全国大中型高炉年平均休风率为1.661,新兴铸 管0.628%最低。)
炉料在高炉内下降过程中的形态变化
● 焦炭和矿石在下降过程中,一直保持交替分层的结构。焦炭在高炉中 不熔化,只是到风口前才燃烧气化,少部分焦炭在还原氧化物时气化成 CO。而矿石在部分还原并升温到1000~1100℃时就开始软化,到 1350~1400℃时完全熔化,超过1400℃开始滴落。 ● 焦炭在高炉内起发热剂、还原剂、渗碳剂和料柱骨架的作用,对冶炼 过程具有非常重要的影响。 ● 由于高炉中的热交换,形成了温度分布不同的几个区域,根据炉料物理 性状的不同高炉分为5个区域。 块状带:该区内矿石与焦炭均保持固体状态,没有液体; 软熔带:该区由开始软化的矿石软熔层和仍保持固体状态焦炭夹层组成, 矿石开始软化到完全熔化,软熔带的性状对高炉顺行影响极大; 滴落带:该区只有焦炭仍是固态,其它炉料均呈液态,在焦炭料柱的孔 隙中滴落; 风口回旋区:风口前有一个袋形区域,在这里,受鼓风能量的作用,焦 炭强烈地回旋和燃烧,该区是炉内热量和气体还原剂的主要产生地。 渣铁贮存区:液态渣铁在该区完成最终的反应和热量传递。
• 2、布料 • 从二混出来的混匀料经分料小车将料分到 1#、2#号矿槽。矿槽下部是布料系统。布 料系统由圆筒、料门、反射板、透气棒等 组成。 • 布料圆筒采用φ800×1530mm,在布料过 程中通过调整料门的开度、圆筒的转速来 控制下料量,将物料均匀给到烧结机上。
• 3、点火、烧结 • 点火的目的是供给混合料表层足够的热量, 使其中的固体燃料燃烧,同时借助抽风使 烧结过程由上而下进行。点火采用两种燃 烧气体:混合煤气、天然气,烧嘴采用双 斜式两用烧嘴,点火温度1050±50℃,点 火时间1min。 • 烧结采用的是两台28.5m2烧结机(扩容 后)。烧结机运行速度1.39m/min,烧结过 程中废气流量约2950m3/h,废气温度控制 在90~100℃。
高炉剖面示意图
矿石层 焦炭层
块状带 软融带 滴落带 死料堆(炉芯) 焦炭疏松区
热风 渣口 铁口
风口回旋区 渣铁储存区
高炉冶炼过程主要物理化学变化