炼铁生产工艺流程(13)
炼铁厂的工艺流程

炼铁厂的工艺流程炼铁是将铁矿石中的铁元素提取出来,并通过冶炼过程将其转化为可用的铁质产品。
炼铁厂的工艺流程通常包括原料处理、炼铁炉炉料制备、高炉冶炼、铁水处理、铁水净化、铁水浇铸等环节。
首先,原料处理是炼铁工艺流程的第一步。
矿石通过矿石加工车间进行粉碎、筛分和磁选等处理,以去除其中的杂质和非铁元素,获得高品质的铁矿石。
然后,矿石通过输送带将其运输到高炉炉料制备车间。
在炉料制备车间,铁矿石与焦炭、石灰石等配料按照一定比例混合,并加入适量的热风脱硫剂。
混合后的炉料通过锤式破碎机进行粗碎,并通过输送带运输到高炉冶炼车间。
高炉冶炼是整个炼铁工艺流程的核心环节。
炉料经过提前预热后,被连续投入到高炉顶部,并与燃烧的焦炭在高炉内进行反应。
这个反应过程是一个高温还原还原的反应,铁矿石中的铁元素被还原为液态铁水,并与炉渣分离。
在这个过程中,通过高炉顶部和炉底的通风系统,注入适量的空气和热风,以保持高炉内的高温状态并促进还原反应的进行。
铁水处理是接下来的一步,将从高炉中流出的炉渣和铁水进行分离。
首先,铁水通过渣口出流,经过一系列的除渣设备,包括渣刀、渣位控制装置等,去除其中的炉渣杂质。
然后,铁水进入铁水处理车间,通过各种设备进行温度和成分的控制,以满足不同类型铁质产品的生产要求。
为了获得质量更好的铁质产品,铁水净化也是非常重要的一步。
铁水净化主要是通过设备进行脱硫、除磷、除硅等操作。
常用的设备有吸附剂装置、除硫装置、捕捉剂装置等,通过这些设备,可以有效提高铁质产品的纯度。
最后,根据产品的需要,铁水可以通过连铸机进行连续浇铸,形成各种形状的铁质产品。
连铸过程中,铁水被注入到连铸机中的铁水槽中,经过一系列的设备,连续浇注成型,然后经过冷却、切割等处理,得到成品铁质产品。
总之,炼铁厂的工艺流程是一个复杂而系统的过程,其中涉及多个环节和设备的配合。
通过这个工艺流程,铁矿石中的铁元素得以提取,并最终转化为高质量的铁质产品,为社会提供各种铁制品的需求。
炼铁炼钢工艺流程

炼铁炼钢工艺流程炼铁炼钢是冶金工艺中的重要环节,通过对铁矿石的提炼和精炼,最终获得高质量的钢铁产品。
下面将详细介绍炼铁炼钢的工艺流程。
一、炼铁工艺流程1. 副矿材料预处理:将收集的副矿材料经过破碎、筛分、磁选等工序处理,去除杂质,得到纯净的副矿材料。
2. 铁矿石处理:将铁矿石破碎、浸泡于水中,去除表面的杂质,然后经过磁力分离、重力选矿等工序,将铁矿石中的有用成分提取出来。
3. 炼铁炉炼炉:将提取的铁矿石与焦炭、石灰石等原料混合,投入高炉中进行炼制。
高炉内温度达到1500℃以上,矿石中的铁含量经过还原反应被提取出来,形成生铁。
4. 生铁处理:将炼出的生铁经过浇铸或炼钢炉炉处理,去除其中的硫、磷等杂质,得到优质的铁合金。
二、炼钢工艺流程1. 炼钢炉前处理:将铁合金破碎、筛分,去除其中的杂质,得到纯净的铁合金。
2. 炼钢炉炼炉:将铁合金与适量的废钢、废铁加入炼钢炉中,进行炼制。
炼钢炉内温度高达1600℃以上,通过氧气吹吹炼,使废钢等物质被氧化,产生大量热,达到熔化的目的。
3. 炼钢炉后处理:炼钢完成后,钢水需要进行过滤、脱硫等处理,以去除其中的杂质。
此外,还需要根据不同的需求,添加适量的合金等元素,调整钢的成分和性能。
4. 连铸成型:将经过处理的钢水注入到连铸机中,通过涡轮旋转或摇摆,使钢水冷却凝固,形成钢坯。
钢坯可进一步进行轧制、锻造等加工,制成不同形状的钢材。
以上就是炼铁炼钢的工艺流程。
通过这个过程,铁矿石和副矿材料得到了有效的利用,矿石中的铁成分被提取出来,并经过加工得到高质量的钢材。
这个工艺流程不仅具有广泛的应用价值,还在很大程度上推动了工业化的进程。
炼铁厂的工艺流程
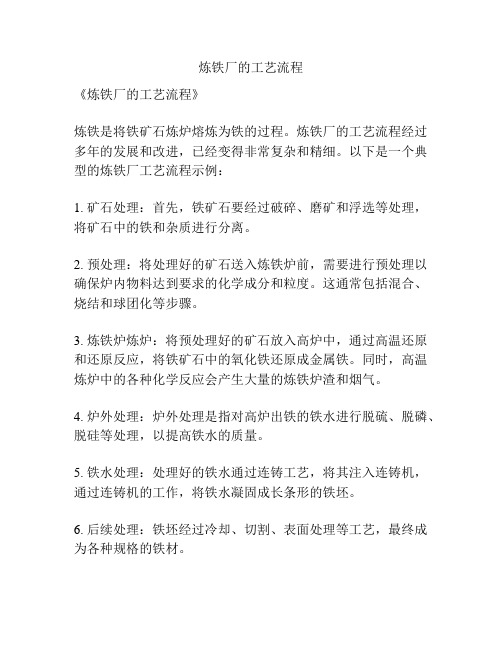
炼铁厂的工艺流程
《炼铁厂的工艺流程》
炼铁是将铁矿石炼炉熔炼为铁的过程。
炼铁厂的工艺流程经过多年的发展和改进,已经变得非常复杂和精细。
以下是一个典型的炼铁厂工艺流程示例:
1. 矿石处理:首先,铁矿石要经过破碎、磨矿和浮选等处理,将矿石中的铁和杂质进行分离。
2. 预处理:将处理好的矿石送入炼铁炉前,需要进行预处理以确保炉内物料达到要求的化学成分和粒度。
这通常包括混合、烧结和球团化等步骤。
3. 炼铁炉炼炉:将预处理好的矿石放入高炉中,通过高温还原和还原反应,将铁矿石中的氧化铁还原成金属铁。
同时,高温炼炉中的各种化学反应会产生大量的炼铁炉渣和烟气。
4. 炉外处理:炉外处理是指对高炉出铁的铁水进行脱硫、脱磷、脱硅等处理,以提高铁水的质量。
5. 铁水处理:处理好的铁水通过连铸工艺,将其注入连铸机,通过连铸机的工作,将铁水凝固成长条形的铁坯。
6. 后续处理:铁坯经过冷却、切割、表面处理等工艺,最终成为各种规格的铁材。
总的来说,炼铁厂的工艺流程包括矿石处理、预处理、炼炉、炉外处理、铁水处理和后续处理等环节,每个环节都需要严格控制各种参数,以确保最终生产出符合要求的铁材产品。
同时,为了实现高效、环保的生产,炼铁厂在工艺流程中还需要注重节能减排和资源综合利用的工作。
铁的冶炼工艺流程
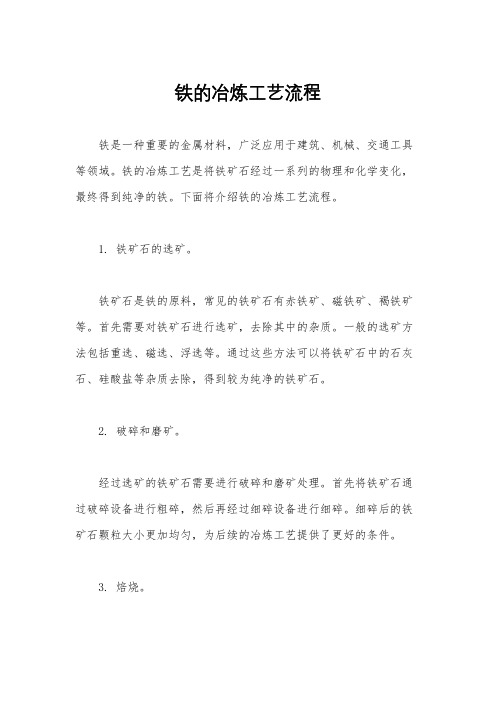
铁的冶炼工艺流程铁是一种重要的金属材料,广泛应用于建筑、机械、交通工具等领域。
铁的冶炼工艺是将铁矿石经过一系列的物理和化学变化,最终得到纯净的铁。
下面将介绍铁的冶炼工艺流程。
1. 铁矿石的选矿。
铁矿石是铁的原料,常见的铁矿石有赤铁矿、磁铁矿、褐铁矿等。
首先需要对铁矿石进行选矿,去除其中的杂质。
一般的选矿方法包括重选、磁选、浮选等。
通过这些方法可以将铁矿石中的石灰石、硅酸盐等杂质去除,得到较为纯净的铁矿石。
2. 破碎和磨矿。
经过选矿的铁矿石需要进行破碎和磨矿处理。
首先将铁矿石通过破碎设备进行粗碎,然后再经过细碎设备进行细碎。
细碎后的铁矿石颗粒大小更加均匀,为后续的冶炼工艺提供了更好的条件。
3. 焙烧。
磨矿后的铁矿石需要进行焙烧处理。
焙烧是指将铁矿石在高温下进行加热,使其中的水分和挥发物质得以挥发。
通过焙烧可以使铁矿石中的水分和有机物质得到去除,同时也有助于铁矿石的还原反应。
4. 还原。
经过焙烧处理后的铁矿石需要进行还原反应。
在高温下,将焙烧后的铁矿石与还原剂(如焦炭、木炭)一起放入冶炼炉中进行加热。
在还原剂的作用下,铁矿石中的氧化铁得以还原为金属铁。
这一步是铁冶炼过程中最关键的一步,也是得到纯净铁的关键。
5. 炼铁。
经过还原反应后,得到的金属铁需要进行炼铁处理。
炼铁是指将还原后的金属铁与炼铁渣、炼铁矿等材料一起放入高炉或其他冶炼设备中进行加热。
在高温下,金属铁与炼铁渣发生反应,最终得到纯净的铁水。
6. 铁水处理。
得到的铁水需要进行进一步的处理。
首先需要对铁水进行除渣,去除其中的杂质和炼铁渣。
然后还需要对铁水进行调质,添加合适的合金元素,以提高铁的性能和品质。
7. 铁水浇铸。
最后一步是将处理好的铁水进行浇铸。
铁水可以浇铸成各种形状的铁件,如铸铁管、铸铁板、铸铁轴等。
通过浇铸可以使铁水凝固成固体铁件,最终得到成品铁材料。
以上就是铁的冶炼工艺流程,经过以上一系列的步骤,铁矿石最终得以转化为纯净的铁材料。
高炉炼铁工艺流程
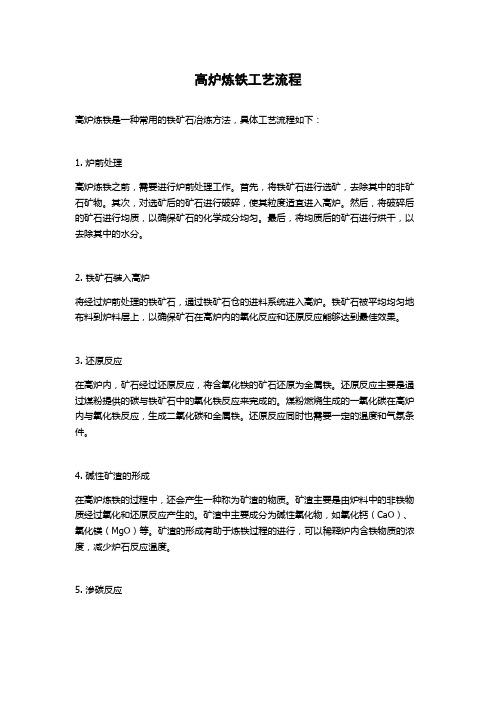
高炉炼铁工艺流程高炉炼铁是一种常用的铁矿石冶炼方法,具体工艺流程如下:1. 炉前处理高炉炼铁之前,需要进行炉前处理工作。
首先,将铁矿石进行选矿,去除其中的非矿石矿物。
其次,对选矿后的矿石进行破碎,使其粒度适宜进入高炉。
然后,将破碎后的矿石进行均质,以确保矿石的化学成分均匀。
最后,将均质后的矿石进行烘干,以去除其中的水分。
2. 铁矿石装入高炉将经过炉前处理的铁矿石,通过铁矿石仓的进料系统进入高炉。
铁矿石被平均均匀地布料到炉料层上,以确保矿石在高炉内的氧化反应和还原反应能够达到最佳效果。
3. 还原反应在高炉内,矿石经过还原反应,将含氧化铁的矿石还原为金属铁。
还原反应主要是通过煤粉提供的碳与铁矿石中的氧化铁反应来完成的。
煤粉燃烧生成的一氧化碳在高炉内与氧化铁反应,生成二氧化碳和金属铁。
还原反应同时也需要一定的温度和气氛条件。
4. 碱性矿渣的形成在高炉炼铁的过程中,还会产生一种称为矿渣的物质。
矿渣主要是由炉料中的非铁物质经过氧化和还原反应产生的。
矿渣中主要成分为碱性氧化物,如氧化钙(CaO)、氧化镁(MgO)等。
矿渣的形成有助于炼铁过程的进行,可以稀释炉内含铁物质的浓度,减少炉石反应温度。
5. 渗碳反应在高炉内,碳通过渗碳反应进一步与铁进行反应,生成碳化物。
这个过程通常需要在高炉底部的温度比较高的炉渣中进行,以确保足够的反应速率。
碳化物生成后,还需要通过进一步的处理来使其转变为可用的铁。
6. 炉缸维护和清理高炉炼铁过程中,会产生一些固体杂质物质,如炉渣和金属铁结晶等。
这些杂质会在高炉底部形成一层坚硬的物质,称为炉缸。
定期对高炉进行炉缸维护和清理是必要的,以保证高炉运行的正常和稳定。
7. 铁水和渣化处理高炉炼铁过程中,会产生两种产品,一种是铁水,另一种是矿渣。
铁水通过高炉底部的铁口流出,进入铁水包。
然后,将铁水通过通道输送到后续的冶金工艺中进行进一步的处理。
矿渣则从高炉底部的渣口流出,进入矿渣车,最终被运到矿渣堆存放。
传统炼铁生产工艺流程
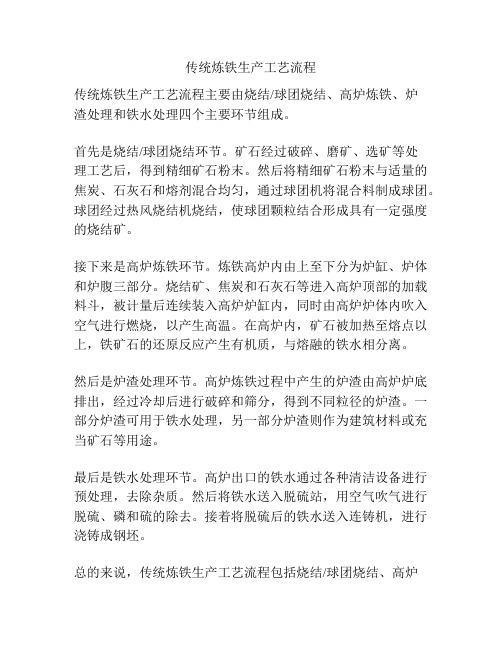
传统炼铁生产工艺流程
传统炼铁生产工艺流程主要由烧结/球团烧结、高炉炼铁、炉
渣处理和铁水处理四个主要环节组成。
首先是烧结/球团烧结环节。
矿石经过破碎、磨矿、选矿等处
理工艺后,得到精细矿石粉末。
然后将精细矿石粉末与适量的焦炭、石灰石和熔剂混合均匀,通过球团机将混合料制成球团。
球团经过热风烧结机烧结,使球团颗粒结合形成具有一定强度的烧结矿。
接下来是高炉炼铁环节。
炼铁高炉内由上至下分为炉缸、炉体和炉腹三部分。
烧结矿、焦炭和石灰石等进入高炉顶部的加载料斗,被计量后连续装入高炉炉缸内,同时由高炉炉体内吹入空气进行燃烧,以产生高温。
在高炉内,矿石被加热至熔点以上,铁矿石的还原反应产生有机质,与熔融的铁水相分离。
然后是炉渣处理环节。
高炉炼铁过程中产生的炉渣由高炉炉底排出,经过冷却后进行破碎和筛分,得到不同粒径的炉渣。
一部分炉渣可用于铁水处理,另一部分炉渣则作为建筑材料或充当矿石等用途。
最后是铁水处理环节。
高炉出口的铁水通过各种清洁设备进行预处理,去除杂质。
然后将铁水送入脱硫站,用空气吹气进行脱硫、磷和硫的除去。
接着将脱硫后的铁水送入连铸机,进行浇铸成钢坯。
总的来说,传统炼铁生产工艺流程包括烧结/球团烧结、高炉
炼铁、炉渣处理和铁水处理四个环节。
这个流程是过去常用的炼铁工艺流程,虽然在一些地方已经被新型工艺替代,但在许多国家和地区仍然广泛应用。
高炉炼铁生产工艺流程
高炉炼铁生产工艺流程
高炉炼铁生产工艺流程是指利用高炉将铁矿石还原为铁的整个过程,下面以700字左右简要介绍高炉炼铁生产工艺流程。
高炉炼铁生产工艺流程主要包括原料准备、炉料制备、高炉的运行和操作以及产物处理等环节。
在高炉炼铁生产中,原料准备是首要环节,主要包括铁矿石的选矿、破碎、磁选等工序。
选矿和磁选可将铁矿石中的杂质去除,提高铁矿石的品位。
破碎则是将大块的铁矿石破碎成适合高炉入炉的大小。
炉料制备是指将铁矿石与其他辅料按一定比例混合烧结而成的固体料块,主要包括铁矿石、焦炭和石灰石等。
混合烧结的目的是提高炉料的强度和透气性,保证高炉正常运行。
高炉的运行和操作是指高炉内矿料的还原和产物的处理过程。
高炉内的还原过程是指将铁矿石中的氧化铁还原为金属铁的过程。
高炉内温度较高,铁矿石中的氧化铁在还原剂(主要为焦炭)的作用下被还原为CO和H2,并最终在高炉底部还原为铁。
高炉产物的处理主
要包括炉渣处理和收集炉气中的有价金属。
炉渣是高炉还原过程中由炉料和矿石中的杂质形成的。
通过适当的操作,可以将炉渣中的有价金属(如铜、锌等)回收利用。
炉气是高炉过程中产生的气体,在高炉炼铁生产中,通常以废气发电的方式将炉气利用起来,不仅能减少能源的消耗,还可以降低对环境的污染。
总的来说,高炉炼铁生产工艺流程主要包括原料准备、炉料制备、高炉的运行和操作以及产物处理等环节。
通过合理的工艺流程,可以高效地将铁矿石还原为金属铁,实现铁的生产和利
用。
高炉炼铁工艺流程在全球范围内得到广泛应用,对推动经济的发展和保障国家的资源安全起到了重要作用。
炼铁工艺流程
炼铁过程实质上是将铁从其自然形态——矿石等含铁化合物中还原出来的过程。
炼铁方法主要有高炉法、直接还原法、熔融还原法等,其原理是矿石在特定的气氛中(还原物质CO、H2、C;适宜温度等)通过物化反应获取还原后的生铁。
生铁除了少部分用于铸造外,绝大部分是作为炼钢原料。
1、高炉炼铁的冶炼原理(应用最多的)高炉冶炼用的原料高炉冶炼用的原料主要由铁矿石、燃料(焦炭)和熔剂(石灰石)三部分组成。
通常,冶炼1吨生铁需要1.5-2.0吨铁矿石,0.4-0.6吨焦炭,0.2-0.4吨熔剂,总计需要2-3吨原料。
为了保证高炉生产的连续性,要求有足够数量的原料供应。
因此,无论是生铁厂家还是钢厂采购原料的工作是尤其重要。
生铁的冶炼虽原理相同,但由于方法不同、冶炼设备不同,所以工艺流程也不同。
下面分别简单予以介绍。
高炉生产是连续进行的。
一代高炉(从开炉到大修停炉为一代)能连续生产几年到十几年。
生产时,从炉顶(一般炉顶是由料种与料斗组成,现代化高炉是钟阀炉顶和无料钟炉顶)不断地装入铁矿石、焦炭、熔剂,从高炉下部的风口吹进热风(1000~1300摄氏度),喷入油、煤或天然气等燃料。
装入高炉中的铁矿石,主要是铁和氧的化合物。
在高温下,焦炭中和喷吹物中的碳及碳燃烧生成的一氧化碳将铁矿石中的氧夺取出来,得到铁,这个过程叫做还原。
铁矿石通过还原反应炼出生铁,铁水从出铁口放出。
铁矿石中的脉石、焦炭及喷吹物中的灰分与加入炉内的石灰石等熔剂结合生成炉渣,从出铁口和出渣口分别排出。
煤气从炉顶导出,经除尘后,作为工业用煤气。
现代化高炉还可以利用炉顶的高压,用导出的部分煤气发电。
生铁是高炉产品(指高炉冶炼生铁),而高炉的产品不只是生铁,还有锰铁等,属于铁合金产品。
锰铁高炉不参加炼铁高炉各种指标的计算。
高炉炼铁过程中还产生副产品水渣、矿渣棉和高炉煤气等。
高炉炼铁的特点:规模大,不论是世界其它国家还是中国,高炉的容积在不断扩大,如我国宝钢高炉是4063立方米,日产生铁超过10000吨,炉渣4000多吨,日耗焦4000多吨。
炼铁生产工艺流程
炼铁生产工艺流程炼铁是从矿石中提取出铁金属的过程,它是整个钢铁行业中最基础的环节之一。
下面我来介绍一下炼铁的生产工艺流程。
首先,炼铁的第一步是选矿。
选矿是指从原生铁矿石中选出富含铁元素的矿石。
常见的矿石有赤铁矿、磁铁矿等。
在选矿过程中,工人会使用重力分选、磁选、浮选等方法来分离出铁矿石。
接下来是矿石炼焙。
矿石炼焙是将铁矿石加热使其发生化学反应,去除其中非铁金属元素。
这个过程一般在高炉中进行。
高炉是一个巨大的圆柱形窑体,内部有坩埚,坩埚下方有炭斗和风口。
燃料通常是焦炭,燃烧后产生高温,将矿石加热。
在高炉中,矿石逐渐熔化,非铁金属元素分解释放出来,而金属铁则被保留下来。
第三步是炼铁。
在高炉中,矿石熔化后,会产生高温高压的液态铁和矿渣。
液态铁比矿渣密度大,会自然下沉到底部。
矿渣则会浮在液态铁上方。
工人会通过倾吊装置将底部的液态铁放出,并用矿渣渣石填满,防止液态铁跑溜。
之后是铸铁生产。
液态铁放出后,可以用来生产铸铁。
通常情况下,液态铁会流入连铸机内,冷却成铸坯。
连铸机是一个灵活和高效的设备,可以将液态铁快速冷却成坯料,并通过成型辊来定形。
这样得到的铸坯可以根据需要进一步加工成铸件。
最后一步是铁的精炼。
炼铁过程中得到的铸坯中还存在一些杂质和气体,需要通过精炼来去除。
精炼通常是在电炉中进行。
电炉是一种能将电能转化为热能的设备,通过电炉加热铸坯,使其重新熔化。
在熔化过程中,杂质和气体会从铁液中挥发出来或沉积下来,从而实现铁的精炼。
以上就是炼铁的生产工艺流程。
通过选矿、矿石炼焙、炼铁、铸铁生产和精炼等步骤,从原生铁矿石中得到纯净的铁金属,为后续的钢铁加工奠定了基础。
炼铁生产工艺流程的不断改进和创新,使得炼铁工艺更加高效、环保和节能,为钢铁产业的发展做出了重要贡献。
高炉炼铁工艺流程
高炉炼铁工艺流程
高炉炼铁是指将铁矿石通过高炉的加热、还原、冶炼过程,得到纯铁
的工艺流程。
它是钢铁工业中最重要的生产方式之一,也是铁矿石资源利
用的主要方式之一
高炉炼铁的流程包括炉料装入、加热还原、炉渣形成、熔化冶炼和产
铁等环节。
下面将详细介绍这些环节的工艺流程。
1.炉料装入:将铁矿石(主要是赤铁矿)、焦炭、石灰石、焦炉煤气
等炉料按照一定比例装入高炉的上部。
2.加热还原:在高炉的下部引入煤气、空气和预热的鼓风,并点燃煤气。
煤气燃烧产生的高温火焰将炉料加热至1000-1300℃左右,使铁矿石
中的Fe2O3被还原成铁(Fe)和一氧化碳(CO)。
还原反应如下:2Fe2O3+3C=4Fe+3CO2
3.炉渣形成:在高炉中,铁矿石中的杂质(如硅、锰、磷等)与石灰
石反应形成炉渣,同时焦炭燃烧的一氧化碳也与掺入的石灰石反应生成二
氧化硅。
这些炉渣混合在一起,并与铁水和残余焦炭一起下降到高炉底部。
4.熔化冶炼:高炉底部温度达到1500℃以上,铁水和炉渣分离。
铁
水是含有铁和少量碳、硅、锰等元素的液体,通过出铁口排出。
炉渣是含
有二氧化硅、石灰石、氧化铁等成分的熔融物,通过炉渣口排出。
在熔化
冶炼的过程中,还会通过喷吹鼓风提高冶炼效果和热效率。
5.产铁:经过一系列的化学反应和物理变化,铁水中的杂质逐渐被除去,得到纯铁。
最后,铁液从出铁口流出,得到熟铁或铸铁。
- 1、下载文档前请自行甄别文档内容的完整性,平台不提供额外的编辑、内容补充、找答案等附加服务。
- 2、"仅部分预览"的文档,不可在线预览部分如存在完整性等问题,可反馈申请退款(可完整预览的文档不适用该条件!)。
- 3、如文档侵犯您的权益,请联系客服反馈,我们会尽快为您处理(人工客服工作时间:9:00-18:30)。
能力,力求强度要高一些为好。 铁矿石的软化性包括铁矿石的软化温度和软化温度区
间。高炉冶炼要求铁矿石的软化温度要高,软化温度区间 要窄。
63
2)பைடு நூலகம்熔剂
熔剂的作用: 熔剂在冶炼过程中的主要作用有两个:造渣和使渣铁分离。 熔剂的种类: 按其性质熔剂可分为碱性、酸性和中性三类。
0 0 0 19.89652 4.17442 0
59
2)高炉冶炼对铁矿石的要求是: 含铁量高,脉石少,有害杂质少,化学成分稳定,粒
度均匀,良好的还原性及一定的机械强度等性能。 ①铁矿石的品位 指铁矿石的含铁量,以TFe%表示。
铁矿石含铁量高有利于降低焦比和提高产量。一般矿 石品位提高1%,焦比降低2%,产量提高3%。品位较 低,不能直接入炉的叫贫矿。
15
二、烧结生产工艺流程
烧结就是将各种粉状含铁原料,配入适量的燃料和熔剂, 加入适量的水,经混合和造球后在烧结设备上进行烧结的过 程。
采用带式抽风烧结机生产。 烧结厂有360、280、180 、130 m2烧结机各一台。 烧结生产工艺流程主要包括:烧结料的准备,配料与混 合,烧结和产品处理等工序。
炼铁生产工艺流程
一、钢铁工业生产工艺流程 二、焦化生产工艺流程 三、烧结生产工艺流程 四、炼铁生产工艺流程
2
一、钢铁工业生产工艺流程图
3
二、焦化生产
4
一 )焦化设备
公司本部焦化厂现有一座58孔JN84型焦炉和两座共115 孔JN60型焦炉,炭化室高分别为4.3m和6m,年设计生产能 力分别为38万吨和115万吨。公司与安石集团合资建设的 湖南煤化新能源公司,有两座炭化室高5.5m的捣固焦炉和 六座无回收清洁型捣固焦炉,年设计产能分别为130万吨和 15万吨。煤化公司新焦炉于2009年7月和9月先后投产,因 此,公司当前实际焦炭产能为298万吨,年需炼焦煤415万 吨。
焦末 7.81
碎矿
39.4
烧结厂
2800m3 高炉年产 260 万吨铁水主要物料平衡
40
一) 高炉生产工艺过程 高炉冶炼的任务:把铁矿石冶炼成合格生铁。要求以
最小的投入,获得最大的产出,即做到优质、高产、低耗、 长寿、环保。
高炉生产工艺过程由高炉本体和五个辅助设备系统完成。 1.高炉本体 高炉本体包括炉基、炉壳、炉衬、冷 却设备、炉顶装料设备等。高炉的内部空间叫炉型。从上 到下分为五段,即炉喉、炉身、炉腰、炉腹、炉缸。
49
50
4).渣铁处理系统 渣铁处理系统包括出铁场、炉前设备、渣铁运输设备、
水力冲渣设备等。其任务是将炉内放出的渣、铁,按要求 进行处理。 5).喷吹燃料系统
喷吹燃料系统的任务是将按一定要求准备好的燃料喷 入炉内。
51
52
53
54
55
喷煤车间管带机
56
涟钢3200M3高炉余压透平发电机组
干焦 93.75
焦丁 8.13 (10~25mm)
碎焦 15.94
2800m3 高炉
原煤 55.15
高炉鼓风 27.2×108Nm3/a
富氧 1.075×108Nm3/a
热风炉
1.65×109Nm3/a
炉 台 垃 圾 0.25
水渣 107.2
4
铁水 260
计算单位: ×104t/a
煤气灰 5.2
高炉煤气 3.887×109Nm3/a
GATE VALVE WITH E-DRIVE
DAMPER WITH HYDR. DRIVE
CONDENSATE TRAP NOZZLE COUPLING
VENTILATION
BATTERY LIMIT INPUT-OUTPUT
PUMP WITH E-DRIVE
EXPANSION JOINT
ORIFICE PUGMILL
三)、烧结生产 烧结作业是烧结生产的中心环节,包括:布料、点火、
烧结等主要工序。 1、布料:布铺底料和布混合料; 2、点火:煤气条件
点火炉的主要性能 3、烧结:在点火后直至烧结整个过程中,对烧结的风量、 真空度、料层厚度、机速和烧结终点的准确控制。
26
烧结过程由料层表面开始逐渐往下进行,根据各层 温度水平和物理化学变化的不同,可以将正在烧结的料层 自上而下分为五层:烧结矿层、燃烧层、预热层、干燥层 和过湿层。如图所示。
钛(Ti)等。可显著改善钢的可加工性,强度和耐磨、耐热、 耐腐蚀等性能。
62
④铁矿石的还原性 铁矿石的还原性是指铁矿石被还原性气体CO或H2还原
的难易程度。铁矿石的还原性好,有利于降低焦比。 烧结矿和球团矿还原性一般比天然富矿要好。
⑤矿石粒度、机械强度和软化性 矿石的粒度是指矿石颗粒的直径。入炉矿石粒度在
64
熔剂的种类 ★碱性熔剂(普遍使用的)
当矿石中的脉石主要为酸性氧化物时,则使用碱性熔剂。 常用的碱性熔剂有石灰石和白云石。 ★酸性熔剂 使用含碱性脉石的矿石冶炼时,可加入酸性熔剂。作为酸 性熔剂使用的有石英石、均热炉渣等。 ★中性熔剂 亦称高铝质熔剂。当矿石和焦炭灰分中A1203很少,渣中 A1203含量很低,炉渣流动性很差时,在炉料中加入高铝原 料作熔剂。
57
二)高炉冶炼原料 1、铁矿石 2、溶剂 3、高炉燃料
58
1、铁矿石
项目
一、含铁原料
烧结矿 竖炉球团矿 外购球团矿
南非块 PB块
巴西块 MAC块 洗炉锰矿 大宝块 纽曼块矿
1)涟钢矿石构成
计量单位
小高炉
Kg/t Kg/t Kg/t Kg/t Kg/t Kg/t Kg/t Kg/t Kg/t Kg/t
13
煤在炭化室内的结焦过程。
1、干燥和预热阶段 2、部分分解和焦油析 出阶段 3、胶质体形成阶段 4、胶质体固化半焦形 成阶段 5、半焦转为焦炭阶段
14
炼焦过程除生产焦炭外,还产生大量焦炉煤气和化学 副产品。焦炉煤气经洗涤冷却处理后,作为炼焦本身和烧 结,炼铁、炼钢、轧钢生产的燃料。
其主要成分见表。
60
②脉石成分 铁矿石的脉石成分绝大多数为酸性的,Si02含量较
高,铁矿石中Si02含量愈高,将使焦比升高,产量下降。 所以要求铁矿石中含Si02愈低愈好。
脉石中含碱性氧化物(CaO、MgO)较多的矿石,冶炼时 可少加或不加石灰石,对降低焦比有利,具有较高的冶炼 价值。
61
③有害杂质和有益元素的含量 有害元素主要有S、P、Pb、Zn、As、K、Na等。 有益元素有锰(Mn)、铬(Cr)、钴(Co)、镍(Ni)、钒(v)、
6
煤在焦炉炭化室内隔绝空气加热,焦化4.3m焦炉的设 计结焦时间为18h,6m焦炉结焦时间19h。当焦饼中心温 度达到1000℃±50℃时,焦碳成熟,推出炭化室,熄焦 后送往筛焦楼,将焦碳筛分成大于40mm,40~25mm, 25~10mm,小于10mm的四种规格,装入焦仓后分别送烧 结、炼铁工序。
一般认为焦粉作烧结燃料最好。
22
二)、配料与混合 1、配料 2、混合
混合的目的是使烧结料的成分均匀,水分合适,易于 造球,从而获得粒度组成良好的烧结混合料,以保证烧结 矿的质量和提高产量。
混合作业包括加水润湿、混匀和造球,并通入蒸汽以 提高混合料的温度。
23
24
360烧结车间一次圆筒混合机
25
34
球 团 生 产 工 艺 流 程
35
圆 盘 造 球 机
36
竖 炉 结 构 示 意 图
37
四、炼铁生产工艺流程
铁矿(烧结矿、球团矿及块矿) 焦炭 熔剂(石灰石、白云石) 其他
热风炉
喷吹燃料
高炉
除尘
铁水
高炉渣
高炉煤气
38
39
球团 65.66 0
烧结矿 393.44
39.40
块矿 17.51 杂矿
3)高炉燃料
高炉都使用焦炭做燃料,全部从炉顶装入。 近年来,从风口喷入一些燃料,替代一部分焦炭,只占 全部燃料用量的10%--30%。 ①焦炭在高炉冶炼中的作用 焦炭在高炉冶炼中主要作为发热剂、还原剂,料柱骨架和 生铁的渗碳剂。 高炉冶炼过程中的热量有70%~80%来自焦炭的燃烧。焦炭 燃烧产生的CO及焦炭中的固定碳是铁矿石的还原剂。 在高炉下部高温区只有焦炭是以固体状态存在,它对料柱 起骨架作用,高炉下部料柱的透气性完全由焦炭来维持。
65
对碱性熔剂的质量要求 ●碱性氧化物(CaO+MgO)含量高,酸性氧化物(Si02+A|203)
愈少愈好。 ●有害杂质硫、磷含量要少。 ●要有较高的机械强度,粒度均匀,大小适中。
当炉渣黏稠引起炉况失常时,还可短期适量加入萤石 (CaF2),以稀释炉渣和洗掉炉衬上的堆积物。故把萤石称 做洗炉剂。
66
1938.585
1640.576 298.0089
0 0 0 0 0
六高炉
1911.781
1665.821 0.095893 11.13787 112.0904
0 0 16.44096 0.192461 0 106.0024
七高炉
1901.776
1534.419 100.1323
0 243.1539
B.F. TOP PRESSURE
OPEN CLOSE
EMERGENCY WATER DIRTY WATER FLUSHING WATER COLD-WATER BLAST FURNACE GAS RECIRCULATION WATER SIGNAL LINE DIFFIRENTIAL PRESSURE LINE NORMAL OPERATING CLOSED NORMAL OPERATING CLOSED NORMAL OPERATING OPEN NORMAL OPERATING OPEN GATE VALVE SHUTOFF VALVE TO CORDON OFF, BALL VALVE BUTTERFLY VALVE NON-RETURN VALVE ORIFICE PLATE