浅谈韶钢烧结余热发电运行现状
烧结不稳定对余热发电的影响及其解决方案

烧结不稳定对余热发电的影响及其解决方案摘要:烧结余热发电是一项将烧结废气余热资源转变为电力的节能技术。
该技术不产生额外的废气、废渣、粉尘和其他有害气体,能够有效提高烧结工序的能源利用效率。
当前国家能源紧缺、大力提倡生产过程的节能降耗的关键时期,烧结余热回收发电可以帮助钢铁企业实现节能降耗目标,同时也能为企业本身创造可观的经济效益。
关键词:烧结;余热发电;不稳定性;节能减排引言烧结余热有自身不稳定的特点,严重影响了发电机组稳定性、安全性及运行寿命。
针对烧结余热发电不稳定性对机组产生的影响做了分析和总结,并介绍了市场常用的解决方案,并分析了各方案的优缺点。
1烧结余热回收发电应用现状1.1造成的原因。
(1)运行工况波动影响。
烧结烟气量大,每吨烧结矿最终产生4000~6000m3烟气。
由于烧结料透气性的差异及铺料不均等原因,造成烧结烟气系统的阻力变化较大,最终导致烟气量变化大,变化幅度可高达40%以上。
同时,烧结混合料水分、燃料比、环冷机进料口温度等都影响了烟气整体热量的稳定。
由于烧结环冷机结构特性和运行特点,以及烧结生产设备大小、环境温度及湿度、生产组织及工艺调整、市场需求的波动等诸多因素的影响,导致了进入余热锅炉的烟气热量波动大,连续性差。
(2)漏风影响。
烧结环冷机排出的大量烟气,有含粉尘量大、有害气体多、湿度高等特点。
为防止烟气外溢造成环冷机场地内灰尘过大,甚至影响工人操作,环冷机烟罩通常微负压运行。
尽管加强密封,包括台车与烟罩间的密封、烟罩及烟囱的密封、环冷机头部受料点的密封等,烧结环冷机漏风还是高达40%~50%,漏风导致热辐射散热、热风外溢、吸冷风等问题,使烟气温度下降,使进入余热锅炉的烟气温度低且不稳定。
(3)频繁启停机影响。
生产过程中,各类生产性热停,如堵料、生产性皮带跑偏等生产线短时检修,造成机组被迫频繁停机,严重影响了蒸汽生产的稳定性。
烧结机时常需要检修,根据某厂实际操作经验,单台烧结机平均一个月停5、5次。
烧结过程余热利用现状及趋势
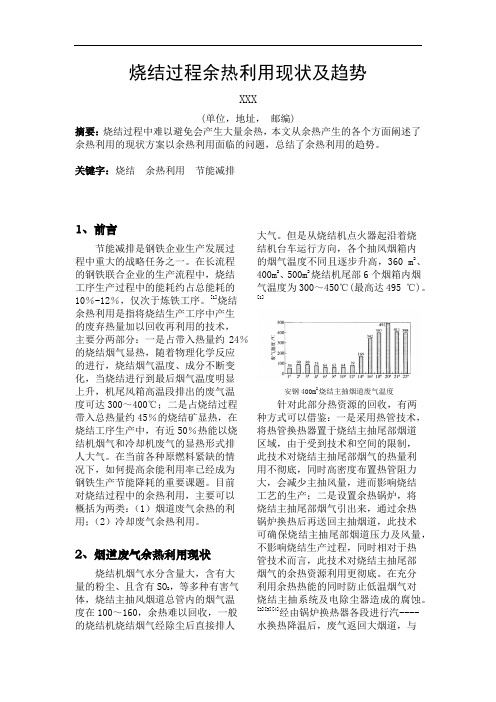
烧结过程余热利用现状及趋势XXX(单位,地址,邮编)摘要:烧结过程中难以避免会产生大量余热,本文从余热产生的各个方面阐述了余热利用的现状方案以余热利用面临的问题,总结了余热利用的趋势。
关键字:烧结余热利用节能减排1、前言节能减排是钢铁企业生产发展过程中重大的战略任务之一。
在长流程的钢铁联合企业的生产流程中,烧结工序生产过程中的能耗约占总能耗的10%-12%,仅次于炼铁工序。
[1]烧结余热利用是指将烧结生产工序中产生的废弃热量加以回收再利用的技术,主要分两部分:一是占带入热量约24%的烧结烟气显热,随着物理化学反应的进行,烧结烟气温度、成分不断变化,当烧结进行到最后烟气温度明显上升,机尾风箱高温段排出的废气温度可达300~400℃;二是占烧结过程带入总热量约45%的烧结矿显热,在烧结工序生产中,有近50%热能以烧结机烟气和冷却机废气的显热形式排人大气。
在当前各种原燃料紧缺的情况下,如何提高余能利用率已经成为钢铁生产节能降耗的重要课题。
目前对烧结过程中的余热利用,主要可以概括为两类:(1)烟道废气余热的利用;(2)冷却废气余热利用。
2、烟道废气余热利用现状烧结机烟气水分含量大,含有大量的粉尘、且含有SO2,等多种有害气体,烧结主抽风烟道总管内的烟气温度在100~160,余热难以回收,一般的烧结机烧结烟气经除尘后直接排人大气。
但是从烧结机点火器起沿着烧结机台车运行方向,各个抽风烟箱内的烟气温度不同且逐步升高,360 m2、400m2、500m2烧结机尾部6个烟箱内烟气温度为300~450℃(最高达495 ℃)。
[1]安钢400m2烧结主抽烟道废气温度针对此部分热资源的回收,有两种方式可以借鉴:一是采用热管技术,将热管换热器置于烧结主抽尾部烟道区域,由于受到技术和空间的限制,此技术对烧结主抽尾部烟气的热量利用不彻底,同时高密度布置热管阻力大,会减少主抽风量,进而影响烧结工艺的生产;二是设置余热锅炉,将烧结主抽尾部烟气引出来,通过余热锅炉换热后再送回主抽烟道,此技术可确保烧结主抽尾部烟道压力及风量,不影响烧结生产过程,同时相对于热管技术而言,此技术对烧结主抽尾部烟气的余热资源利用更彻底。
烧结不稳定对余热发电的影响分析及其解决方案探讨

烧结不稳定对余热发电的影响分析及其解决方案探讨摘要:烧结余热发电是能源利用的重要形式,是钢铁厂常用的能源节约途径,但烧结不稳定也会影响着余热发电的效率,通过对烧结不稳定对余热发电产生的影响,从余热锅炉运行的工况、取风罩漏风、频繁停机等方面分析了其中的原因,并针对烧结具体形式,提出了解决烧结不稳定的策略。
关键词:烧结;余热发电;影响目前,能源紧缺已经成为国家关注的重点问题,在钢铁工业生产中也需要实现节能减耗,但钢铁的烧结工序能耗占总能耗的9%~12%之间,采用烧结余热将废弃余热资源转化电力节能技能,还不会产生废气、废渣等,对提高烧结工序的能源利用效率十分有益,通过研究发现,平均每吨烧结矿产生的烟气余热回收可发电20kw·h,可以节省大量的煤炭资源。
一、烧结不稳定对余热发电产生的影响分析1、对余热锅炉的运行工况波动产生影响在钢铁的烧结工序中,烧结烟气量十分巨大,每吨烧结矿大约可以产生4000~600m3烟气,就会产生大量的热量,如果不及时利用,就造成大量的能源浪费,但由于烧结料的透气性与辅料不均等相关因素的影响,就会对整个余热锅炉的烟气系统阻力造成影响,导致烟气变化量达到40%以上,而且,烧结混合料的水分、燃料比、环冷机进料口温度都会影响系统的烟气整体热量,对锅炉的运行工况造成一定的影响。
由于烧结环冷机设备的结构与运行特征、生产设备的功率、环境温度与湿度等,造成余热锅炉的烟气波动量比较巨大,对整体锅炉的运行工况产生影响。
2、漏风与余热发电产生的影响由于环冷机排出的烟气中含有大量的粉尘与有害气体,而且气体的湿度也比较高,容易造成环境污染,为防止烧结环冷机烟气外溢造成的工作场地灰尘过大,影响工作人员的操作,将环冷机烟罩采用微负压运行,这就需要加强对环冷机的台罩、烟罩、烟囱、环冷机头部受料点的密封,减少环冷机漏风而产生的影响。
环冷机的漏风容易导致热辐射散热、热风外溢、吸冷风等一系列的问题,导致烧结余热锅炉的烟气不稳定,从而影响着余热发电的影响。
钢铁企业烧结余热利用与发电技术

钢铁企业烧结余热利用与发电技术摘要:钢铁企业烧结工序的能耗仅次于炼铁工序,一般为钢铁企业总能耗的10%〜20%。
我国烧结工序的能耗与先进国家相比有较大差距,每吨烧结矿的平均能耗要高20kgce。
在烧结工序总能耗中,有近50%的热能以烧结机烟气和冷却机废气的显热形式排入大气,即浪费了热能又污染了环境。
据日本某钢铁厂热平衡测试数据表明,烧结机的热收入中烧结矿显热占28.2%、废气显热占31.8%。
可见,烧结厂余热回收的重点为烧结废(烟)气余热和烧结矿(产品)显热回收。
烧结余热也是目前我国低温余热资源应用的重点。
一、烧结余热利用方式与现状烧结余热主要利用方式有(1)在点火前对烧结料层进行预热;(2)送到点火器,进行热风点火;(3)实行热风烧结,回收烧结过程的热量和成品矿显热,降低烧结能耗;(4)利用余热锅炉回收烧结或冷却热废风,所产蒸汽用于预热烧结混合料或生活取暖等,或者进行蒸汽升值发电。
目前,我国大型烧结厂普遍采用了余热回收利用装置,但多数中、小烧结厂的余热仍未得到有效利用。
国内重点大中型企业,钢铁协会会员单位在2006年钢铁协会调研时,只有不到三分之一的烧结机配备了烧结余热利用设备,大部分是蒸汽回收并入全厂动力蒸汽管网,很少利用余热发电的。
近年来,随着低温烟气余热锅炉技术和低参数补汽式汽轮机技术的发展,使低温烟气余热发电成为可能。
二、烧结余热利用与发电技术目前我国烧结余热利用的重点和难点在于:由于存在漏风率高导致废气温度降低,又要保证进入除尘器前废气温度在露点以上等原因,回收利用烧结余热较困难。
因此,如何降低漏风率以提高烧结机烟气温度,以及在保证烧结废气除尘所需温度条件下,实现烧结机尾部高温段废气显热回收?烧结余热蒸汽发电核心技术的消化吸收和本土化,是烧结余热回收的重点。
如开发此技术将烧结矿余热充分利用,则钢铁行业年可节约能源约900万吨标准煤。
烧结余热发电是利用低温余热的一个有效途径,但目前来说应用很少,且存在一些问题,在运行过程中,由于烧结机和环冷机工况发生变化时,余热回收系统的工作参数也将随之变动,输出的蒸汽压力、温度、流量也将发生变化,从而影响发电机组的运行效率。
韶钢烧结生产的发展与技术进步
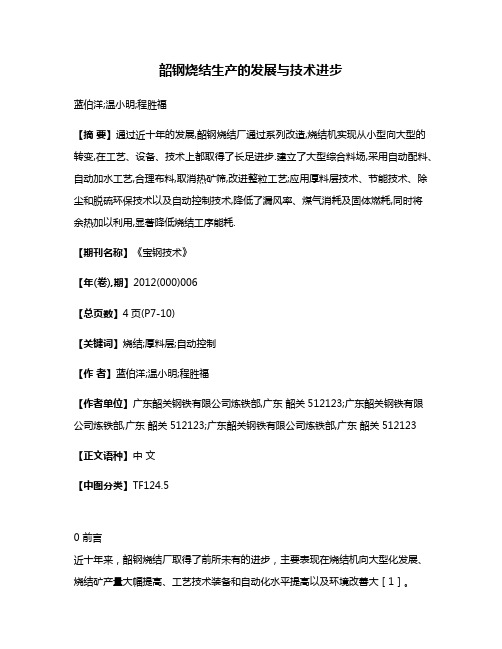
韶钢烧结生产的发展与技术进步蓝伯洋;温小明;程胜福【摘要】通过近十年的发展,韶钢烧结厂通过系列改造,烧结机实现从小型向大型的转变,在工艺、设备、技术上都取得了长足进步.建立了大型综合料场,采用自动配料、自动加水工艺,合理布料,取消热矿筛,改进整粒工艺;应用厚料层技术、节能技术、除尘和脱硫环保技术以及自动控制技术,降低了漏风率、煤气消耗及固体燃耗,同时将余热加以利用,显著降低烧结工序能耗.【期刊名称】《宝钢技术》【年(卷),期】2012(000)006【总页数】4页(P7-10)【关键词】烧结;厚料层;自动控制【作者】蓝伯洋;温小明;程胜福【作者单位】广东韶关钢铁有限公司炼铁部,广东韶关512123;广东韶关钢铁有限公司炼铁部,广东韶关512123;广东韶关钢铁有限公司炼铁部,广东韶关512123【正文语种】中文【中图分类】TF124.50 前言近十年来,韶钢烧结厂取得了前所未有的进步,主要表现在烧结机向大型化发展、烧结矿产量大幅提高、工艺技术装备和自动化水平提高以及环境改善大[1]。
2002 年之前 2台 24 m2、1 台33 m2烧结机均已淘汰,新建成 3台105、360、405 m2烧结机,工艺完善,自动化水平大大提高。
在环保及节能减排方面也取得较大进步,采用脱硫技术以及利用烧结余热发电,既改善了生产作业环境,又使能源得到充分利用。
通过一系列的扩建、技术改造,以及采用创新工艺、新设备、新技术,烧结矿生产规模以及各项技术经济指标都有了显著的提高与进步。
1 发展概况1.1 建立大型综合料场近年来,我国钢铁工业快速发展造成自产铁矿石严重不足,进口的铁矿石量逐年大幅度增加。
由于铁矿石来源广,品位波动大,导致烧结矿品位波动大,影响高炉冶炼指标。
2002年以前韶钢烧结的综合料场规模只有210万 t/a,经过2002、2005和2008年三次扩建后,规模达1430万t/a,堆料层数可达到400层,有效解决了含铁原料来源广泛,品种较多,品位波动大的难题。
中国钢铁余热发电行业发展现状分析及市场前景预测报告

中国钢铁余热发电行业发展现状分析及市场前景预测报告摘要:随着中国钢铁产能的不断增加和钢铁企业能源消耗的不断增长,钢铁余热发电作为一种清洁能源利用方式备受关注。
本报告通过对中国钢铁余热发电行业的发展现状进行分析,并结合市场前景预测,为行业发展提供参考和建议。
一、行业发展现状分析1.钢铁产能持续增加:中国是世界上最大的钢铁生产和消费国,钢铁产能持续增加,直接导致钢铁行业能源消耗的增加,钢铁余热发电发展前景广阔。
2.可利用余热资源巨大:钢铁生产过程中产生的高温余热资源丰富,据统计,每生产1吨钢铁可产生约400-600度的余热,可作为发电的可利用资源。
3.技术成熟度较高:钢铁余热发电技术在国内外已经有较多应用案例,并取得了较好的经济和环境效益,技术成熟度较高,为行业发展奠定了基础。
4.政策支持力度加大:中国政府对于清洁能源的发展给予了极大的关注和支持,通过出台一系列激励措施和政策引导,为钢铁余热发电行业的发展创造了有利的环境。
二、市场前景预测1.市场需求潜力巨大:目前我国钢铁产能仍在增长中,能源消耗也在增加,因此钢铁余热发电的市场需求潜力巨大。
根据预计,未来几年钢铁余热发电市场年均增长率有望达到20%左右。
2.技术进步带来发展机遇:随着技术的不断进步,钢铁余热发电的效率和经济性将进一步提高,将更好地满足市场需求,提供更好的发展机遇。
3.环保政策的持续推进:政府对于环保政策的逐步加码,并要求钢铁企业加大绿色转型力度,使得钢铁余热发电这一清洁能源利用方式成为绿色转型的重要选择,市场前景广阔。
4.投资回报率高:钢铁余热发电项目投资周期较短,且可利用余热资源稳定,具备较高的投资回报率,吸引了越来越多的投资者进入市场。
三、发展建议1.加强技术研发和创新,提高钢铁余热发电技术的效率和经济性。
2.加大政策支持力度,出台更多鼓励钢铁企业进行余热发电的激励政策和补贴。
结论:钢铁余热发电作为一种清洁能源利用方式,在中国的发展前景广阔。
我国钢铁企业余热利用的现状及对策分析
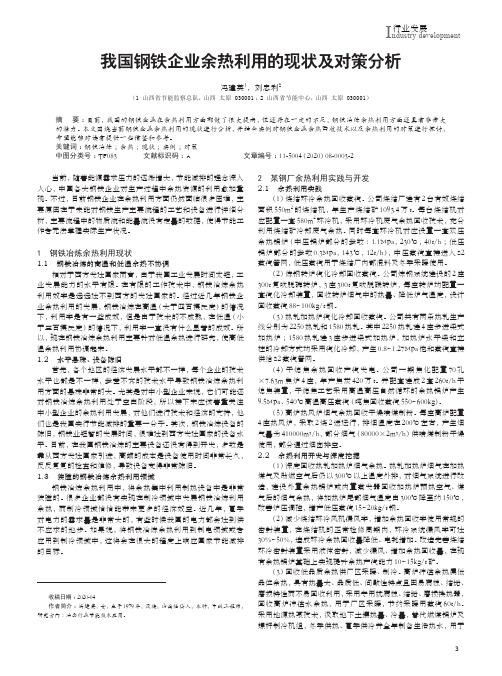
3I ndustry development行业发展我国钢铁企业余热利用的现状及对策分析冯建英1,刘忠利2(1 山西省节能监察总队,山西 太原 030001;2 山西省节能中心,山西 太原 030001)摘 要:目前,我国的钢铁企业在余热利用方面都做了很大提高,但还存在一定的不足,钢铁冶炼余热利用方面还具有非常大的潜力。
本文围绕当前钢铁企业余热利用的现状进行分析,并结合实例对钢铁企业余热回收技术以及余热利用的对策进行探讨,希望能够对读者提供一些借鉴和参考。
关键词:钢铁冶炼;余热;现状;实例;对策中图分类号:TF083 文献标识码:A 文章编号:11-5004(2020)08-0003-2收稿日期:2020-04作者简介:冯建英,女,生于1979年,汉族,山西临猗人,本科,中级工程师,研究方向:冶金行业节能技术应用。
当前,随着能源需求压力的逐渐增大,节能减排的理念深入人心,中国各大钢铁企业对生产过程中余热资源的利用愈加重视。
不过,目前钢铁企业在余热利用方面仍然面临很多困难,主要原因在于未能对钢铁生产主要流程的工艺和设备进行详细分析,主要流程中的物质流和能量流没有定量的数据,使得节能工作者无法掌握实际生产状况。
1 钢铁冶炼余热利用现状1.1 钢铁冶炼的高温和低温余热不协调相对于西方发达国家而言,由于我国工业发展时间太短,工业发展能力的水平有限。
在有限的工作技术中,钢铁冶炼余热利用效率是远远达不到西方的发达国家的。
经过近几年钢铁企业余热利用的发展,钢铁冶炼在高温(大于四百摄氏度)的情况下,利用率是有一些成效,但是由于技术的不成熟,在低温(小于三百摄氏度)的情况下,利用率一直没有什么显著的成效。
所以,现在钢铁冶炼余热利用主要针对低温余热进行研究,使高低温余热利用协调起来。
1.2 水平悬殊、设备陈旧首先,各个地区的经济发展水平都不一样,每个企业的技术水平也都是不一样,参差不齐的技术水平导致钢铁冶炼余热利用方面的悬殊非常的大。
试析钢铁企业烧结余热发电应用

试析钢铁企业烧结余热发电应用摘要:钢铁生产过程中,烧结工序的能耗约占总能耗的10%,仅次于炼铁工序而位居第二。
由于以前余热回收技术的局限在烧结工序总能耗中,有近50%的热能以烧结机烟气和冷却机废气的显热形式排入大气,既浪费了热能又污染了环境。
因此,采用新技术对余热余能进行利用就显得势在必行,而烧结余热发电就是一项利用烧结废气余热能源转变为电能的余热回收利用技术,该技术不需要消耗一次能源,不产生额外的废气、废渣、粉尘以及其它有害气体。
随着近几年来余热回收技术的发展,钢铁行业的余热回收项目造价也大幅降低,同时余热回收效率大大提高,特别是闪蒸汽发电技术和补汽式凝汽式汽轮机在技术上的突破,为钢铁行业余热回收创造了条件。
关键词:钢铁企业;烧结余热;发电应用1钢铁工业余热回收利用概况钢铁工业烧结余热回收主要有两部分:一部分是烧结机尾部废气余热,另一部分是热烧结矿在冷却机前段空冷时产生的废气余热。
这两部分废气所含热量约占烧结总能耗的50%,充分利用这部分热量是提高烧结工艺的效率,显著降低烧结工序能耗的途径之一。
目前,国内烧结废气余热回收利用主要有三种方式:一是直接将废烟气经过净化后作为点火炉的助燃空气或用于预热混合料,以降低燃料消耗,这种方式较为简单,但余热利用量有限,一般不超过烟气量的10%;二是将废烟气通过余热锅炉或热管装置产生蒸汽,并入全厂蒸汽管网,替代部分燃煤锅炉;三是将余热锅炉产生蒸汽用于驱动汽轮机组发电。
从实现能源梯级利用的高效性和经济性角度来看,最为有效的余热利用途径是余热发电,对烧结矿产生的烟气余热回收,平均每吨可发电20kWh,折合每吨钢综合能耗可降低8kg标准煤。
2烧结余热回收中出现得较为普遍的问题2.1漏风現象在余热回收系统中的漏风问题主要是通过台车与烟罩之间的密封以及台车与风箱之间的密封体现出来的。
因为烟气系统属于全闭路式循环,台车与烟罩、台车与风箱都是在实际运转过程中进行相互配合的,风箱中一般为正压3000PA-4000PA之间,眼罩中为负压-100PA-400PA。
- 1、下载文档前请自行甄别文档内容的完整性,平台不提供额外的编辑、内容补充、找答案等附加服务。
- 2、"仅部分预览"的文档,不可在线预览部分如存在完整性等问题,可反馈申请退款(可完整预览的文档不适用该条件!)。
- 3、如文档侵犯您的权益,请联系客服反馈,我们会尽快为您处理(人工客服工作时间:9:00-18:30)。
浅谈韶钢烧结余热发电运行现状
文章简要说明了韶钢烧结环冷机余热发电技术的原理与基本工艺,分析了韶钢烧结环冷机废气余热利用过程中存在的问题以及改进的方向。
标签:烧结余热;环冷机;烟气余热;余热回收;余热发电;改进方向
1 烧结余热发电技术在韶钢的应用现状
1.1 韶钢烧结余热发电项目建设背景
韶钢原有5号和6号烧结机均为360m2,设计烧结矿年产量均为370万吨;其中5号烧结机2005年2月建成投产,6号烧结机2008年2月建成投产,2台烧结机均没有建设环冷机烟气余热回收装置。
2010年韶钢为满足节能减排需要,利用当时国内较成熟的技术水平,对烧结厂环冷机烟气进行余热回收利用技术改造,以回收5号和6号烧结环冷机的烟气余热进行发电。
1.2 烧结环冷机余热发电原理与基本工艺
烧结矿在环冷机上通过鼓风进行冷却,底部鼓入的冷风在穿过热的烧结矿层时与热烧结矿进行换热,产生大量的高温废气。
将这些高温的废气通过引风机引入锅炉,加热锅炉内的水产生蒸汽,蒸汽推动汽轮机转动带动发电机发电。
烧结余热发电工艺流程由三部分组成:烟气系统、锅炉系统、汽轮机及发电机系统。
烟气回收系统主要由烟囱、烟气引出管、烟气流量控制阀和烟筒的对空排气阀构成,主要功能是利用锅炉引风机产生的负压将带冷机烟罩内温度较高的烟气引到锅炉内,同时避免外界的冷风进入锅炉。
锅炉系统是余热回收的核心,在锅炉受热面上,高温烟气将热量逐级传递给受热面内的工质(水或者蒸汽)生成过热蒸汽。
汽轮机及发电机系统将过热蒸汽携带的能量转化成电能,最终完成烟气余热能向电能的转化。
韶钢烧结环冷机余热发电工艺流程如图1所示。
1.3 韶钢烧结余热发电的运行模式
烧结余热热源具有整体品质低、废气温度波动大和连续性差的特点。
其中废气温度波动大和热源连续性差是当前技术条件下,烧结余热发电技术应用的最大难点。
另外,如何有效的提高系统的回收效率,尽可能多的提高吨矿发电量也是烧结厂所关心的。
韶钢烧结余热发电系统结合本厂生产工艺特点,采用“二炉带一机”的配置模式:配有二台双压余热锅炉(型号:QC360(410)/400(285)-47(20)-2.45(0.78)/375(225))和一台25MW补汽式凝汽机组(型号:BN25-1.96/0.49)。
在两台烧结机旁分别建设一台余热锅炉,用两台余热锅炉带动一套汽轮机发
电机组(简称“两炉带一机”)。
当一台烧结机出现故障后,其对应的锅炉热源中断后,另一台烧结余热锅炉可以维持机组的正常运行,不至于出现解列;除此之外,两台锅炉并行运行对稳定蒸汽温度也有一定的作用。
采用“二炉带一机”的配置模式,较好的解决了烧结余热热源稳定性差的问题,大大减少了发电机组的解列次数,增加发了电量。
1.4 韶钢烧结余热发电项目生产情况
韶钢烧结余热发电项目于2011年4月投产,2011年至2013年间,分别发电7427万kWh、8408万kWh、10670万kWh,累计达26505万kWh。
按同规模燃煤电厂煤耗460g/kWh计算,年可节约标煤121913t,减排SO2(Sy=0.6%计算)1463吨,减排CO2量约31.7万吨。
为韶钢在日益激烈的市场竞争中进一步降低生产成本、实现节能降耗发挥积极作用。
2 韶钢烧结余热发电项目存在的问题及改进方向
韶钢烧结余热发电项目投产三年来,相关技术、运行人员积累了一定的经验,通过测试找出了存在的问题,摸索出了解决问题的改进方向。
2.1 韶钢烧结余热发电项目存在的问题
2.1.1 五号烧结环冷机的1#、2#鼓风机存在风压低、风量不足的严重问题。
其风压比六号烧结机低900Pa左右,1#鼓风机风量比六号烧结机低10万Nm3/h 以上,2#鼓风机风量比六号烧结机低2万Nm3/h以上。
2.1.2 两台环冷机的漏风率较高。
I、II号余热锅炉的漏风率分别为27%、29%左右,另外,环冷机台车下部的密封橡胶存在老化和损坏现象。
2.1.3 锅炉的热效率在0.54~0.63之间,而且存在随落料量的增加而增加的趋势。
设计工况下,锅炉的热效率高于0.63。
2.1.4 随着蒸汽热量的增加,发电功率增加,热耗率和汽耗率均降低,说明在高负荷时热量的利用更充分。
2.2 改进方向
2.2.1 对五号烧结环冷机的鼓风机进行整修,确保鼓风风压、风量,满足锅炉额定热烟气量。
2.2.2 对环冷机的密封进行进一步的完善,对环冷机台车下部老化损坏的密封橡胶进行更换,降低漏风率,减少热量流失。
2.2.3 余热发电成套设备在满负荷运行时,热耗率低,自用电率低,经济效
益高,建议在满足烧结厂生产要求的前提下,尽量高负荷运行。
2.2.4 余热发电成套设备可考虑改用闭式系统,将排烟作为鼓风机的入口气体,以进一步利用烟气的余热。
3 结束语
当前,钢铁行业发展面临严峻挑战和新的发展机遇,传统的粗放型发展模式已难以为继,迫切要求行业企业以节能减排为抓手,积极转变发展方式,利用高新技术改造、提升行业技术管理水平,走科技含量高、经济效益好、资源消耗低、环境污染少的新型工业化道路。
参考文献
[1]中国金属学会,冶金工业经济发展研究中心.2006年度冶金科技进步发展报告(之二),中国冶金,2008,18(2):2.
[2]卢红军,戚云峰.烧结余热的基本特点及对烧结余热发电的影响[J].烧结球团,2008,33(1):35-36.。