注塑机螺杆与料筒结构设计
螺杆与料筒结构
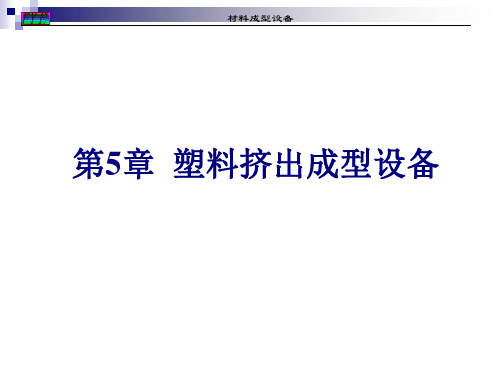
材料成型设备
塑料挤出机的型号
例:主机SJ-150×20 表示 螺杆直径φ150mm,长径比 为20:1的塑料挤出机。辅 机SJ-FM1700表示上吹法、 牵引辊筒工作长度为1700 mm的塑料吹塑薄膜辅机, 其中FM为辅机代号。
材料成型设备
5.2 挤出机的工作过程及控制参数
5.2.1 挤出机的工作过程
材料成型设备
(4)螺杆的分段及各段参数的确定
加料段:核心是输送能力问题。
螺纹升角φ:从物料最大输送能力出发,φ=17~20°为最佳;实际 为了便于加工,一般取螺纹升程(螺距)S等于螺杆直径Db,此时 螺纹升角φ=17°42ˊ。 螺槽深度h1:要考虑螺杆机械强度和物料的物理压缩比大小。
加料段长度L1:根据经验选取
材料成型设备
第5章 塑料挤出成型设备
材料成型设备
第5章 塑料挤出成型设备
材料成型设备
5.1 概述
挤出成型:生产具有相同截面形状而长度任意的塑料制品 (如管、棒、板及各种异型材等)的成型加工方法;挤出 成型制品的产量居首位。
5.1.1 塑料挤出成型特点和应用
特点: 挤出生产过程是连续的; 生产效率高,应用范围广; 投资少,见效快。
对于结晶型塑料:L2=(3~5)Db
材料成型设备
(4)螺杆的分段及各段参数的确定 均化段:将已熔融的塑料定压、定量、定温地挤入机头。
螺槽深度h3:按经验法取h3=(0.025~0.06)Db ;对于螺杆直径较小 者,加工粘度低,热稳定性较好的塑料,或机头压力大者,取小值; 反之取大值。 均化段长度L3:按经验法取L3 =(0.2~0.25)L;对于热敏性塑料,如 PVC,L3取短些。对于高速挤出,L/ Db要取大些,相应L3取大些,以 适应其定量定压挤出和进一步均化作用的要求。
塑料螺杆设计制造及螺杆与料筒间隙的确定与调整

塑料螺杆设计制造及螺杆与料筒间隙的确定与调整螺杆是塑料加工机械的塑化部件,螺杆结构的好坏会对塑料加工产生关键影响。
螺杆从外形看是有一定长度带螺纹的圆柱体,看似简单不复杂,但是塑料从整个塑化过程中发生在螺杆上的变化却是相当复杂的。
在塑料输送过程中还有压力的产生、能量的传递和转换以及塑料物态变化。
所以,螺杆的设计显得尤为重要。
通过本文介绍,就会对螺杆设计有深入了解。
三段长度、螺杆导程、螺棱宽度、进料段和出料段的螺槽深度以及压缩比确定,常规通用型的螺杆参数就设定完毕了。
但实际使用还要考虑到螺杆和机筒的配合,螺杆和机筒之间的间隙也是重要的参数。
间隙经验值(最小间隙~最大间隙)螺杆直径30:0.10 ~0.25螺杆直径45:0.15 ~0.30螺杆直径65:0.20 ~0.40螺杆直径90:0.30 ~0.50螺杆直径120:0.35 ~0.55螺杆直径150:0.40~0.60国产挤出机螺杆参数表(请横屏查看)特殊螺杆设计之分离型BM螺杆除了普通三段式经典螺杆设计外,为了一步提高混炼和塑化效果,常见的还有各种带混炼结构的螺杆设计。
这些混炼结构多位于压缩段和计量段头部。
其中分离型BM螺杆是最常见的类型之一。
分离型螺杆(英文名barrier screw或者barrier flight screw),是在普通三段式螺杆的基础上研发出来的新型螺杆,其基本机构与普通三段式螺杆相似。
不同点在于整根螺杆有两段螺纹组成,可以有导程不等的前螺纹和后螺纹组成,也可以导程相同的主螺纹和副螺纹组成。
由于固相熔融而形成的熔膜越过间隙进入液相螺槽中,未容固相留在固相槽,形成固液分离。
故名分离型螺杆。
分离型螺杆设计参数设定S1:主螺纹导程S2:副螺纹导程e:螺棱宽度θ:螺纹升角常见分离型螺杆主螺纹和副螺纹螺棱宽度一致,螺纹圈数相差一圈。
基于经过的长度相同得到如下等式:ZS1+(2e+2K)/cosθ=(Z+1)S2推导出设计参数设定公式:(S1-S2)Z=S2-(2e+2K)/cosθ其中Z=L/S1注:K是副螺纹起始时和主螺纹的间距,Z是主螺纹和副螺纹相交时主螺纹行程圈数,一般取整数然后推导出L数值分离型螺杆有如下特点:一、只有熔化了的塑料才能越过间隙进入液相螺槽,尚未完全塑化的小颗粒在通过间隙时在高剪切速率的作用下也能完全塑化。
注塑机工作原理及构造

第一章 注塑机工作原理及构造第一节 注塑机工作原理一、注塑机工作原理 注塑成型机简称注塑机,其机械部分主要由注塑部件和合模部件组成。
注塑部件主要由料筒和螺杆及注射油缸组成示意如图1-19所示。
注塑成型是用塑性 的热物理性质,把物料从料斗加入料筒内,料筒外由加热圈加热,使物料熔融。
在料筒内装有在外动力油马达作用下驱动旋转的螺杆。
物料在螺杆的作用下,沿着螺槽向前输送并压实。
物料在外加热和螺杆剪切的双重作用下逐渐的塑化、熔融和均化。
当螺杆旋转时,物料在螺槽摩擦力及剪切力的作用下把已熔融的物料推到螺杆的头部,与此同时,螺杆在物料的反作用力作用下向后退,使螺杆头部形成储料空间,完成塑化过程。
然后,螺杆在注射油缸活塞杆推力的作用下,以高速、高压,将储料室的熔融料通过喷嘴注射到模具的型腔中。
型腔中的容料经过保压、冷却、固化定型后,模具在合模机构的作用下,开启模具,并通过顶出装置把定型好的制件从模具顶出落下。
塑料从固体料经料斗加入到料筒中,经过塑化熔融阶段,直到注射、保压、冷却、启模、顶出制品落下等过程,全是按着严格地自动化工作程序操作的,如图1-20所示。
1-模具 2-喷嘴 3-料筒 4-螺杆 5-加热圈6-料斗 7-油马达 8-注射油缸 9-储料室 10-制件 11-顶杆图1-19 注塑成型原理图注射座动作选择第二节 注塑机组成注塑机根据注塑成型工艺要求是一个机电一体化很强的机种,主要由注塑部件、合模部件、机身、液压系统、加热系统、冷却系统、电气控制系统、加料装置等组成,如图1-21所示。
第二节注 塑 机 结 构注塑机总体结构公司目前主力机型为HTFX 系列,该机型主要可分为注射部分(01注塑机注塑部件塑化装置 注射座 注射油缸 螺杆驱动装置 注射座油缸 螺杆 料筒 螺杆头 喷嘴合模部件合模装置 调模装置 制品顶出装置机身液压系统泵、油马达、阀蓄能器、冷却器、过滤装置 管路、压力表冷却系统 入料口冷却、模具冷却 润滑系统 润滑装置、分配器电器控制系统动作程序控制;料筒温度控制;泵电机控制安全保护;故障监测、报警;显示系统机械手加料装置图1-21 注塑机组成示图部分)、合模部分(02部分)、安全防护门(03部分)、液压传动部分(04部分)、润滑部分(05部分)、电器控制部分(06部分)和机身部分(07部分),括号内为公司内部简称。
塑料注塑机注射螺杆的设计方法及原则研究
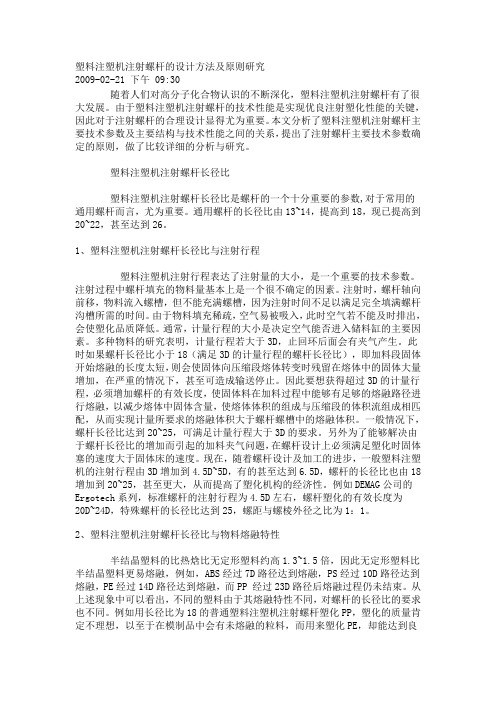
塑料注塑机注射螺杆的设计方法及原则研究2009-02-21 下午 09:30随着人们对高分子化合物认识的不断深化,塑料注塑机注射螺杆有了很大发展。
由于塑料注塑机注射螺杆的技术性能是实现优良注射塑化性能的关键,因此对于注射螺杆的合理设计显得尤为重要。
本文分析了塑料注塑机注射螺杆主要技术参数及主要结构与技术性能之间的关系,提出了注射螺杆主要技术参数确定的原则,做了比较详细的分析与研究。
塑料注塑机注射螺杆长径比塑料注塑机注射螺杆长径比是螺杆的一个十分重要的参数,对于常用的通用螺杆而言,尤为重要。
通用螺杆的长径比由13~14,提高到18,现已提高到20~22,甚至达到26。
1、塑料注塑机注射螺杆长径比与注射行程塑料注塑机注射行程表达了注射量的大小,是一个重要的技术参数。
注射过程中螺杆填充的物料量基本上是一个很不确定的因素。
注射时,螺杆轴向前移,物料流入螺槽,但不能充满螺槽,因为注射时间不足以满足完全填满螺杆沟槽所需的时间。
由于物料填充稀疏,空气易被吸入,此时空气若不能及时排出,会使塑化品质降低。
通常,计量行程的大小是决定空气能否进入储料缸的主要因素。
多种物料的研究表明,计量行程若大于3D,止回环后面会有夹气产生。
此时如果螺杆长径比小于18(满足3D的计量行程的螺杆长径比),即加料段固体开始熔融的长度太短,则会使固体向压缩段熔体转变时残留在熔体中的固体大量增加,在严重的情况下,甚至可造成输送停止。
因此要想获得超过3D的计量行程,必须增加螺杆的有效长度,使固体料在加料过程中能够有足够的熔融路径进行熔融,以减少熔体中固体含量,使熔体体积的组成与压缩段的体积流组成相匹配,从而实现计量所要求的熔融体积大于螺杆螺槽中的熔融体积。
一般情况下,螺杆长径比达到20~25,可满足计量行程大于3D的要求。
另外为了能够解决由于螺杆长径比的增加而引起的加料夹气问题,在螺杆设计上必须满足塑化时固体塞的速度大于固体床的速度。
现在,随着螺杆设计及加工的进步,一般塑料注塑机的注射行程由3D增加到4.5D~5D,有的甚至达到6.5D,螺杆的长径比也由18增加到20~25,甚至更大,从而提高了塑化机构的经济性。
注塑机的组成结构分析

注塑机的组成结构分析注塑机根据注射成型工艺要求是一个机电一体化很强的机种,主要由注射部件,合模部件,机身,液压系统,加热系统,控制系统,加料装置等组成.注塑机根据注射成型工艺要求是一个机电一体化很强的机种,主要由注射部件、合模部件、机身、液压系统、加热系统、控制系统、加料装置等组成。
如图2所示。
图2 注塑机组成示意图(一)注塑部件的典型结构1.注射部件的组成目前,常见的注塑装置有单缸形式和双缸形式,我厂注塑机都是双缸形式的,并且都是通过液压马达直接驱动螺杆注塑。
因不同的厂家、不同型号的机台其组成也不完全相同,下面就对我厂用的机台作具体分析。
立式机和卧式机注塑装置的组成图分别如图3和图4。
工作原理是:预塑时,在塑化部件中的螺杆通过液压马达驱动主轴旋转,主轴一端与螺杆键连接,另一端与液压马达键连接,螺杆旋转时,物料塑化并将塑化好的熔料推到料筒前端的储料室中,与此同时,螺杆在物料的反作用下后退,并通过推力轴承使推力座后退,通过螺母拉动活塞杆直线后退,完成计量,注射时,注射油缸的杆腔进油通过轴承推动活塞杆完成动作,活塞的杆腔进油推动活塞杆及螺杆完成注射动作。
图3 卧式机双缸注射注塑装置示意图(a)是俯视图;? (b)为注射座与导杆支座间的平视图1-油压马达;2,6 -导杆支座;3-导杆;4-注射油缸;5-加料口;7-推力座;8-注射座;9-塑化部件;10-座移油缸用的角式注塑机的注射部件与卧式机注塑机也是一样的。
图4 立式注塑机注射装置示意图1.液压马达;2-推力座;3-注射油缸;4-注射座;5-加料口;6-座移油缸;7-塑化部件;8-上范本2.塑化部件塑化部件有柱塞式和螺杆式两种,下面就对螺杆式做一下介绍。
螺杆式塑化部件如图5所示,主要由螺杆、料筒、喷嘴等组成,塑料在旋转螺杆的连续推进过程中,实现物理状态的变化,最后呈熔融状态而被注入模腔。
因此,塑化部件是完成均匀塑化,实现定量注射的核心部件。
图5 螺杆式塑化部件结构图1-喷嘴;2-螺杆头;3-止逆环;4-料筒;5-螺杆;6-加热圈;7-冷却水圈螺杆式塑化部件的工作原理:预塑时,螺杆旋转,将从料口落入螺槽中的物料连续地向前推进,加热圈通过料筒壁把热量传递给螺槽中的物料,固体物料在外加热和螺杆旋转剪切双重作用下,并经过螺杆各功能段的热历程,达到塑化和熔融,熔料推开止逆环,经过螺杆头的周围通道流入螺杆的前端,并产生背压,推动螺杆后移完成熔料的计量,在注射时,螺杆起柱塞的作用,在油缸作用下,迅速前移,将储料室中的熔体通过喷嘴注入模具。
螺杆作用

注塑机---螺杆料筒与塑化相关部件介绍注射部分与塑化相关的部件主要有:螺杆、料筒、分流梭、止逆环、射咀、法兰、加料斗等。
下面分别就其在塑化过程中的作用与影响加以说明。
螺杆是注塑机的重要部件。
它的作用是对塑料进行输送、压实、熔化、搅拌和施压。
所有这些都是通过螺杆在料筒内的旋转来完成的。
在螺杆旋转时,塑料对于机筒内壁、螺杆螺槽底面、螺棱推进面以及塑料与塑料之间在都会产生摩擦及相互运动。
塑料的向前推进就是这种运动组合的结果,而摩擦产生的热量也被吸收用来提高塑料温度及熔化塑料。
螺杆的结构将直接影响到这些作用的程度。
普通注塑螺杆结构,也有为了提高塑化质量设计成分离型螺杆,屏障型螺杆或分流型螺杆。
料筒的结构其实就是一根中间开了下料口的圆管。
在塑料的塑化过程中,其前进和混合的动力都是来源于螺杆和料筒的相对旋转。
根据塑料在螺杆螺槽中的不同形态,一般把螺杆分为三段:固体输送段(也叫加料段)、熔融段(也叫压缩段)、均化段(也称计量段)。
在有关塑料塑化的教材上中,都把塑料在螺杆的固体输送段看成一个塑料颗粒间没有相互运动的固体床,然后通过固体床与料筒壁、与螺棱推进面以及与螺槽表面相互运动和摩擦的理想状态的计算,来确定塑料向前输送的速度。
这与实际情况有不少差距,也不能以此为依据来分析不同形状塑料颗粒的进料情况。
如果塑料的颗粒不大,它们在被料筒内壁拉动向前运动时会出现分层和翻滚,并逐步被压实形成固体塞。
当望料颗粒的直径与螺槽深度尺寸差不多时,它们的运动轨迹基本上是沿螺槽径向的直线运动加上转一个角度的直线运动。
由于颗粒大时塑料在螺槽中的排列很疏松,所以其输送速度也较慢。
当颗粒大到一定程度,在进入压缩段而其直径大于螺槽深度时,塑料就会卡在螺杆与机筒之间,如果向前拉动的力不足以克服压扁塑料颗粒所需的力,则塑料会卡在螺槽里不向前推进。
塑料在接近熔点温度时,、与料筒相接触的塑料已开始熔融而形成一层熔膜。
当熔膜厚度超过螺杆与料筒间的间隙时,螺棱顶部把熔膜从料筒内壁径向地刮向螺棱根部,从而逐渐在螺棱的推进面汇集成旋涡状的流动区——熔池。
注塑机螺杆结构

二、类型和特点 渐变型螺杆:指螺槽深度由加料段深的螺槽向均化段的螺槽逐渐过度。 特点:压缩段较长,占螺杆总长的50%,塑化时能量转换缓和,多用于PVC 等热稳定性差的塑料。
突变型螺杆:指螺杆槽深度由深变浅的过程是在一个较短的轴向距离内完 在的。 特点:压缩段较短,占螺杆总长的5%~15%左右,塑化时能量转换较剧烈, 多用于聚烯烃、PA等结晶型塑料。 通用型螺杆:压缩段长度介于突变型螺杆与渐变型螺杆之间,但塑化质量 和能耗比专用差。 特点:适应性比较强的通用型螺杆,可适应多种塑料的加工。 三、螺杆分段说明
七、工艺设置
料筒末端过冷是引起螺杆打滑的主要原因之一。注射机的料筒分为3段,在 末端,即加料段,粒料在加热和压缩的过程中,会形成一层熔体薄膜粘到 螺杆上。没有这层薄膜,粒料就不容易被输送到前端。
加料段的材料必须被加热到临界温度,以形成那层关键的熔体膜。然而, 通常物料在加料段的停留时间很短,无法达到要求的温度。而这种情况一 般会在小型注射机上发生。停留时间过短会造成聚合物的熔融和混合过程 的不完全,从而导致螺杆打滑或失速。
4、使用防涎时要确定料筒内塑料完全熔融,以免螺杆后退时损 坏传动系统零件。
5、避免螺杆空转、打滑等现象。 6、使用新塑料时,应把料筒的余料清洗干净。使用POM、PVC、 PA+GF等料时尽量减少原料降解,停机后及时用ABS等水口料冲洗 干净。
7、避免POM与PVC同时混入料筒,在熔融温度下将会发生反应造 成严重工业事故。
五、螺杆使用方法
1、料筒未达到预调温度时,切勿启动机器。新开电热一般要求 温度达到设定值30分钟后再操作螺杆 2、每次停机超过半小时以上的,最好关闭落料口并清扫料筒内 料,设置保温
3、避免异物落入料料筒损坏螺杆及料筒。防止金属碎片及杂物 落入料斗,若加工回收料,需加上磁性料斗以防止铁屑等进入料 筒。
注塑机螺杆设计依据3

1 目的:指导注塑机螺杆及熔胶筒的规范设计。
2 适用范围:本标准适用于注塑机螺杆和熔胶筒的开发设计计算。
3 具体内容:3.1 螺杆结构:螺杆是螺杆式注射装置塑化部件中的重要零件。
从塑料进入熔胶筒塑化过程来看,经过了固体加料和输送、压实和熔融、进一步塑化和均匀化并计量三个过程。
因此通常将螺杆设计成加料段、压缩段、均化段等三段。
为适应加工塑料性能方面(如软化温度范围、硬度、粘度、摩擦系数、比热、热稳定性、导热性等)的不同要求,通常将螺杆设计成渐变型、突变型和通用型三种螺杆,它们主要在分段和螺槽深度上有所不同。
3.1.1、渐变型螺杆:即长压缩段的螺杆。
特征是塑化时能量转换较缓和,主要用于加工硬聚氯乙烯、聚苯乙烯、聚碳酸酯、聚砜、ABS等塑料(具有宽的软化温度范围,高粘度非结晶型塑料)。
3.1.2、突变型螺杆:即短压缩段的螺杆。
特征是塑化时能量转换较剧烈。
主要用于加工聚乙烯、聚丙烯、聚甲醛、尼龙、含氟塑料等(结晶型塑料)。
●突变型螺杆设计的出发点:认为塑料是在短压缩区内实现全部状态的转变。
●根据熔融理论和塑料在螺槽内的实际熔融过程,是一个逐渐熔融的过程,而且从工艺上也很难准确控制塑料在突变区内实现状态全部转变的位置点。
3.1.3、通用型螺杆:注塑机在实际生产过程中,经常需要更换塑料品种,拆换螺杆比较频繁,且比较费力和影响生产。
因此在实际使用过程中,一般不经常更换螺杆,而通过调整工艺参数(温度、螺杆转速、背压等)的办法,来满足不同塑料制品的加工要求,为此设计了一种通用型螺杆,其特征是压缩段的长度介于渐变型螺杆和突变型螺杆之间,约4~5个螺距。
●这样的分段,既考虑到一些非结晶型塑料,经受不了突变螺杆在压缩段高的剪切塑化作用;同时又注意到一些结晶型塑料未经足够的预热是不能软化熔融和难以压缩的特点。
●但是应当强调指出,这种适应性较强的通用型螺杆绝非是“万能”螺杆,所谓通用是相对而言。
上述三种螺杆的分段范围见下表:注:本表为L/D s =15~20范围内的分段情况。
- 1、下载文档前请自行甄别文档内容的完整性,平台不提供额外的编辑、内容补充、找答案等附加服务。
- 2、"仅部分预览"的文档,不可在线预览部分如存在完整性等问题,可反馈申请退款(可完整预览的文档不适用该条件!)。
- 3、如文档侵犯您的权益,请联系客服反馈,我们会尽快为您处理(人工客服工作时间:9:00-18:30)。
= (6.5/12) x π x (50/12) x 387 = 2744瓦特 也就是說每一小時需要損失2.744度的電費 如果按照以上表格的數據使用1.5"厚的陶瓷隔熱(事實上玻璃纖維 毯的隔熱效果比1.5"厚的陶瓷隔熱效果更好),其熱損失為 = (6.5/12) x π x (50/12) x 22.9 =162.37瓦特 很明顯地,電熱方面每天24小時運轉可以省下約60度的電費。
去;當然進料段越深,原料進入越多,輸送就越快(熔膠率會越大), 重點是原料能不能夠完全熔解,而且要混合的非常均勻才是正確。
• 進料段的長度必需要≧機器射出行程+進料口後端到第一個電熱片中
央的距離。
• 如果進料段太短,較冷的料粒尚未到達高溫的料管位置,就要開始
壓縮,堅硬的料粒磨擦螺桿與料管表面,會造成螺桿與料管的局部 快速且嚴重的磨蝕磨損。
射出成型機料管電熱容量之設計
從以上的討論,已經很清楚地說明了塑膠射出成型機的料管電熱圈的容 量,主要是要把螺桿與料管的金屬在運轉前,先加熱到所設定之溫 度,此時可以把料管加螺桿考慮成一個實心鋼棒,而當螺桿旋轉儲 料時,原料的剪切熱將提供大部份的熔解熱的需求,此時電熱只是 在維持熔料環境的穩定溫度與提供少部份的熔解熱量。因此電熱容 量的計算公式如下:
接著射出成型的生產循環動作開始之後,油壓馬達、電動馬達或伺 服馬達旋轉螺旋桿,讓塑膠原料往前輸送、料粒外部接觸螺桿與料 管的金屬,表面先軟化、熔解,然後接著進入壓縮、間隙減小、半 固液的原料往前流→擠壓,黏稠的液體大量產生剪切熱(磨擦熱), 把熱量傳給仍然固態的較低溫原料小粒子,此時的剪切熱將佔塑膠 原料熔解所需要的熱量的40~100多%,其中如果超過100%者會造成實 際溫度讀值超過溫度的設定值;此剪切熱稱之為內熱。
一個廠家去區分為4或5個溫度控制段。 一般國內產製雲母片絕緣的電熱片,其加熱能力約4W/cm2,最高使用
溫度為320 ℃;陶瓷絕緣的電熱片,其加熱能力約7W/cm2,最高使 用溫度可達650 ℃。
射出成形的一般螺旋桿
一般螺旋桿的螺紋設計分為三段:
• 進料段:
• 其深度Hf必需要大於原料粒子的最大對角線,否則原料粒子進不
料管的電熱容量KW = [ (πD2)/4 ]x L x δsteel x 預定上升溫度℃ x ξsteel 106 x 加熱時間Hr x 860(Kcal/Hr)
其中: D = 料管外徑 mm L = 料管加熱部份長度 mm δsteel = 鋼鐵的密度 7.878 g/cc ξsteel = 鋼合金的熱含量 0.112 Kcal/Kg‧℃
名機的ATM100等等
螺旋桿與料管組的材質
雙金屬材料:主要功能為耐腐蝕性+耐磨耗性
• 一般其基材為SCM440;AISI4140;AISI4340 • 料管使用離心鑄造,螺旋桿採用離子噴焊或牙頂燒焊 • 所使用之材料舉例:(高雄路竹鼎基公司之資料)
材質編號 成份
TCB-12 TCB-20 TCB-60 TCB-90
旋轉,造成原料的滾動,也產生更多的剪切熱;當此時的剪切熱再提昇熔解 原料的溫度,而超過料管設定的溫度,這是經常會有射出成型機所遇到的現 象。
• 對於液態時黏稠度較高的原料,如硬質PVC、壓克力厚製品、難燃性樹脂、
像防火ABS等,其計量段的深度盡量深一點,可以減少剪切熱的產生,當然 轉速也要慢。
原料在螺桿料管中的溫度變化
由於一般塑膠原料的熱傳導係數約為金屬的1/30,料管與螺旋桿的 高溫只對原料顆粒與其接觸時,才有傳熱的效果。原料熔解過程產 生的擠壓剪切熱是內熱,它對原料中央部份均勻的加熱升溫,是原 料熔解所需要的主要熱源。
最佳的螺旋桿設計是當儲料時,內熱大約為塑膠原料加熱、熔解時 所需要熱量的80%。
電熱與剪切熱的控制
材料的密度與熱含量
材料種類
鋼鐵 Steel 鋁 Aluminum 銅 Copper 不鏽鋼 Stainless Steel 水 Water 油 Oil 橡膠 Rubber PS聚苯乙烯 Polystyrene PE聚乙烯 Polyethylene 聚氯乙烯 P.V.C. 聚丙烯 Polypropylene PA尼龍 Nylon6 PC聚碳酸酯 Polycarbonate
熱量的流失也就是無形能源的損失,能夠減少此外部的散熱,就能 夠讓電熱加熱的時間縮短,而獲得能源節約的效果。
只要能減少熱量的散失,相對於周圍的環境溫度就可以降低,至少 操作人員不必要因此而吹電扇,也是衍生出來的能源節約。
最有效的能源節約方法為在料管電熱圈的外面包上一層玻璃纖維絲 編織的隔熱毯。
以下資料為美國Watlow公司所作的研究結果,其使用陶瓷圈包裹電 熱片作為最基本之隔熱:
1”厚陶瓷隔熱 23.4 26.0 29.0 31.5 34.3 37.2 40.1 43.2 46.5 49.9 54.1
以上熱損失之單位為Watts/平方英呎的面積
1.5”厚陶瓷 15.6 17.3 19.0 21.0 22.9 24.8 25.8 26.9 28.3 29.9 32.1
料管包陶瓷隔熱的熱損失案例
熱處理與鍍硬鉻
• 耐磨耗者:SACM645;NITRALLOY 135-M;DIMI-8550;ACM2 → 含
少量的鋁,可氮化處理表面形成硬化之氮化鋼
• 使用溫度超過3500C時,或超耐磨耗的需求:SKD61;D-2, H-13, CPM
Tool Steels
• 耐腐蝕者:以上的鋼材鍍硬鉻;SUS-420J2;300, 17-4 Stainless steel • 機械廠與金屬材料製造廠共同研發的配方,如日本三菱的MAC24,日本
62-68 A
B
11.4 x 10-6
48-55 B
A
11.9 x 10-6
60-66 AA A
8.0 x 10-6
電熱與剪切熱的控制
塑膠射出成型機的螺旋桿與料管是以電熱來加熱料管,使其金屬料 管與螺旋桿在起動前必需要達到設定的溫度,以便讓內部的塑膠原 料軟化後,螺旋桿才能夠轉得動,此熱量稱之為外熱。
螺桿設計不良將產生的問題
1. 產品品質不良 - 脆化、黃化 2. 原料熔解溫度需求偏高,熔膠率比較慢 3. 熔料接合線明顯且全部長度均顯現 4. 成品翹曲變形 - 原料熔解溫度與密度不均勻導致 5. 顏色不均一,花花地,有如大理石花紋 6. 每一個產品的顏色感覺有所改變 7. 產品的某些部份變得脆弱 8. 機器換色時間很長,浪費很多原料 9. 螺桿或料管局部升高塑料溫度,造成原料局部劣解,產品有銀線、
塑膠射出成型機的螺旋桿與料管
螺旋桿與料管組的主要ห้องสมุดไป่ตู้能
從料斗中加入的包含:
1. 原料 – 粒狀或粉狀 2. 色母或色粉 – 含量極少 3. 回收料 – 不規則形狀 4. 其他添加物 – 一般複合成份可能在押出機已經進行與少量原料複合完成
以上各項必需在加入料斗前攪拌均勻
螺旋桿與料管的功能
1. 料粒或料粉的輸送 2. 原料熔解 3. 混合均勻 4. 獲得均勻的溫度與密度,並且沒有劣解或變色的問題 5. 每次精確控制準備射出的體積 – 控制精確之儲料完位置 6. 射出開始時止料機構(止料環或鋼珠等)很準確的塞住回流 7. 把一定量的液態原料射入模具 8. 執行保壓的動作
此時外部的電熱一方面必須維持環境中冷空氣對流帶走的熱量,與 高溫料管對低溫周遭空氣的熱輻射所損失掉的熱量,一方面也保持 料管的恆溫。
剪切熱的產生有多少,也同時影響了機器電熱控制器的加熱時間, 而剪切熱的產生量取決於原料在液體狀態時的黏度、射出成形溫度 設定的高低(液態原料的黏度)、螺旋桿的轉速快慢、螺旋桿的壓縮斜 坡度與壓縮比、背壓的高低等等,其中以背壓的提升產生剪切熱最 為嚴重,其次是螺旋桿的壓縮設計斜率大小與RPM 。
然熔解了,但是與液態的原料並沒有均勻混合。
• 因此混鍊段主要功能就是要把全部液體的顏色與成份作最均勻的混合,並且
有均一的溫度及密度。
• 當此均勻的液體原料經過止逆機構進入待射區,只要計量的位置準確,其射
出產品的重量與品質就會穩定、精確,因此此段又稱為計量段。
• 當然如果有未熔解的小顆粒,也希望能夠在此處把它熔解,並攪拌均勻。 • 通常原料到了計量段,其壓力都到達儲料時的最高點,因此料管靜止、螺桿
密度 Bulk Density Kg/m3
7878 2691 8906 10657 1000 987 1218 1052 920~970 1160~1580 910 1130 1200
熱含量 S.H.C. Kcal/Kg/℃
0.112 0.217 0.0985 0.112
1 0.5 0.42 0.32 HDPE 0.6 (LDPE 0.4) 0.24 0.37 0.38 0.28
傳熱,事實上接觸時間甚短,對大量且快速移動的原料粒子的熔解 速率幫助非常有限,當然儲料完成後,螺桿停止運轉,螺桿溝槽內 的原料會持續接受螺桿與料管的熱傳導。
• 有些塑膠原料,如壓克力PMMA、PC、硬質PVC等,在壓縮的狀態
下,其開始熔解的黏度非常大,會造成螺桿卡死轉不動,必需要把 驅動的油壓馬達加大規格,但是過大的壓縮斜度,使用太大扭力的 油壓馬達,會造成螺桿扭曲折斷的結果。
[ (πD2)/4 ]x L x δsteel x 預定上升溫度℃ x ξsteel 106 x 加熱時間Hr x 860(Kcal/Hr)
=[ (π‧1652)/4]x1270x7.878x230℃x0.112÷106 ÷(1/3Hr) ÷ 860 = 19.2 KW 也就是說:像這樣的料管組的電熱瓦特數,大約在19KW左右,再由每
射出成型機料管電熱容量之設計