Deform实验报告镦粗报告.pdf
Deform实验报告镦粗报告.pptx
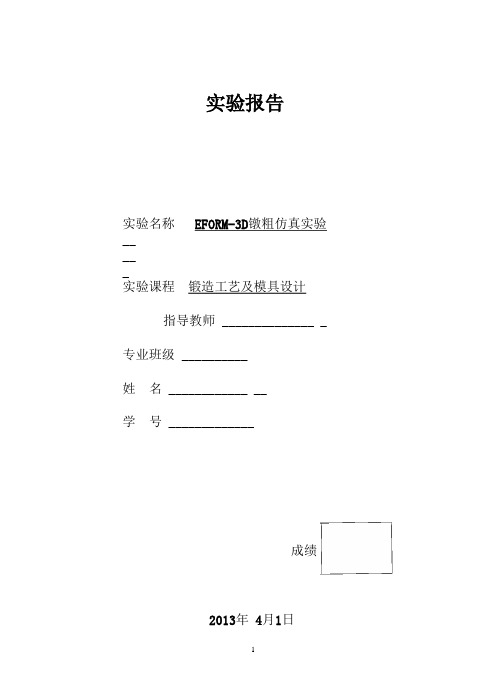
d. 设定 Bottom Die 的 General,其中设定 Object Type 为 Rigid, Assign Temperature 为 200;
e. 设定 Simulation Control 中的 Units 为 SI,Step 中的 Starting Step Number 为-1, Number of Simulation Steps 为 40,Step Increment to Save 为 1, Primary Die 为 Top Die ,With Constant Die Displacement 为 1in.,然后点击 OK 。
第二组数据:
13
第三组数据:
14
第四组数据:
15
5)最大应力分布(抓取6步) 第一组数据:
第二组数据:
16
第三组数据:
17
第四组数据:
18
4实验小结
答: 通过1、2、3、4的变形可以看出,1和3没有在压缩的过程中是属于均
匀的变形过程,而2和4由于存在摩擦力,出现了不均匀的变形,圆柱体四 周出现鼓形轮廓。圆柱体在镦粗时除了受到变形工具的压缩力外,在断面 接 触处有摩擦力作用,摩擦力阻碍金属质点横向流动,使得圆柱体产生鼓 形。 对比2和4可知,2比4出现的鼓形更为明显。
实验报告
实验名称 __ __ _ 实验课程
EFORM-3D镦粗仿真实验 锻造工艺及模具设计
指导教师 ______________ _
专业班级 __________
材料成型数值模拟设计实验

学生学号实验课成绩学生实验报告书实验课程名称材料成型数值模拟设计实验开课学院材料学院指导教师姓名学生姓名学生专业班级成型1001班2012-- 2013学年第二学期实验教学管理基本规范实验是培养学生动手能力、分析解决问题能力的重要环节;实验报告是反映实验教学水平与质量的重要依据。
为加强实验过程管理,改革实验成绩考核方法,改善实验教学效果,提高学生质量,特制定实验教学管理基本规范。
1、本规范适用于理工科类专业实验课程,文、经、管、计算机类实验课程可根据具体情况参照执行或暂不执行。
2、每门实验课程一般会包括许多实验项目,除非常简单的验证演示性实验项目可以不写实验报告外,其他实验项目均应按本格式完成实验报告。
3、实验报告应由实验预习、实验过程、结果分析三大部分组成。
每部分均在实验成绩中占一定比例。
各部分成绩的观测点、考核目标、所占比例可参考附表执行。
各专业也可以根据具体情况,调整考核内容和评分标准。
4、学生必须在完成实验预习内容的前提下进行实验。
教师要在实验过程中抽查学生预习情况,在学生离开实验室前,检查学生实验操作和记录情况,并在实验报告第二部分教师签字栏签名,以确保实验记录的真实性。
5、教师应及时评阅学生的实验报告并给出各实验项目成绩,完整保存实验报告。
在完成所有实验项目后,教师应按学生姓名将批改好的各实验项目实验报告装订成册,构成该实验课程总报告,按班级交课程承担单位(实验中心或实验室)保管存档。
6、实验课程成绩按其类型采取百分制或优、良、中、及格和不及格五级评定。
附表:实验考核参考内容及标准观测点考核目标成绩组成实验预习1.预习报告2.提问3.对于设计型实验,着重考查设计方案的科学性、可行性和创新性对实验目的和基本原理的认识程度,对实验方案的设计能力20%实验过程1.是否按时参加实验2.对实验过程的熟悉程度3.对基本操作的规范程度4.对突发事件的应急处理能力5.实验原始记录的完整程度6.同学之间的团结协作精神着重考查学生的实验态度、基本操作技能;严谨的治学态度、团结协作精神30%结果分析1.所分析结果是否用原始记录数据2.计算结果是否正确3.实验结果分析是否合理4.对于综合实验,各项内容之间是否有分析、比较与判断等考查学生对实验数据处理和现象分析的能力;对专业知识的综合应用能力;事实求实的精神50%实验课程名称材料成型数值模拟实验项目名称利用DEFORM模拟镦粗锻造成型实验成绩实验者专业班级成型1001班组别同组者实验日期2013年4月8日第一部分:实验预习报告(包括实验目的、意义,实验基本原理与方法,主要仪器设备及耗材,实验方案与技术路线等)一、实验目的1)了解认识DEFORM软件的窗口界面。
DEFORM

k = (d max− d min)
d min
12.5% 2.4%
从对比图和尺寸的比较可以看出, 从对比图和尺寸的比较可以看出,扭压成型可以明 显减小鼓形。 为鼓形系数 扭压鼓形系数只有2.4,而 为鼓形系数,扭压鼓形系数只有 显减小鼓形。K为鼓形系数 扭压鼓形系数只有 而 普通镦粗达到了12.5 普通镦粗达到了
扭压复合加载成型
LOGO
锻造镦粗出现的问题 工件与工具接触面存在摩擦,阻碍 金属流动,使成型所需的压力增加及导 致不均匀的变形,可能产生裂纹,鼓形 等。 在高温下镦粗时,温度降低快,屈 服极限较高,产生不均匀变形更为明显。
Your site here
LOGO
如上图所示,开始镦粗后上下表面有摩擦力, 如上图所示,开始镦粗后上下表面有摩擦力,阻碍金属向外 流动,中间不存在摩擦力,而由于塑性变形总体积不变, 流动,中间不存在摩擦力,而由于塑性变形总体积不变,所以出 现了如图的鼓形。 现了如图的鼓形。 Your site here
Your site here
LOGO
提高镦粗时均匀性的工艺方法
B :结果分析 结果分析
鼓形对比 以下是每20步的对比图(上边为普通镦粗,下边为 扭压加载)
Your site here
LOGO
提高镦粗时均匀性的工艺方法
最终尺寸比较 最终尺寸
成型方法
最小直径 普通镦粗 扭压复合加载 104.1 112.1 最大直径 117.1 114.8
Your site here
LOGO
提高镦粗时均匀性的工艺方法 第三类方法: 第三类方法:扭压复合加载成型 一.原理:扭压复合成型工艺是在
工件高度方向上施加压力的同时, 使工件产生扭转运动,将被动摩擦 转化为促进金属流动的主动摩擦的 一种新型工艺。
基于DEFORM的镦粗过程有限元模拟分析
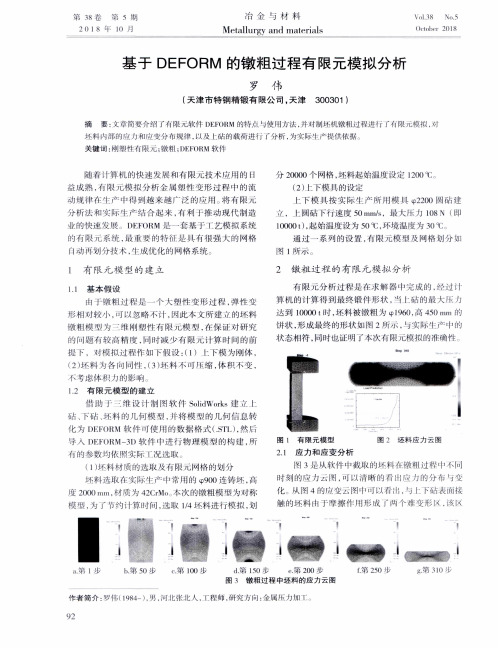
2.1 应 力和 应 变 分 析
图 3是从软件 中截取的坯料 镦、 卡H过 秤巾 /f
时刻 的应力 云 ,可 以清晰 的 胥}t1应 的分 布 j变
化。从图 4的应 变云图 中可 以行 … , } 下砧表 Inf接
触 的坯 料 由于 摩擦 作用 形 成 rI埘个难 变形 f ,陔Jx
图 4 坯 料 应 变 云 图 2.2 材 料 流 动 和 定 点 追 踪
在坯 料上 点取 i个追踪 点 ,清晰地 看到 追踪 点 的初 始位置 和每步移 动 的位置 ,可 以细致地 观察 金 属流 动的过程 ,这有 利 于在 金属 塑性 变形过 程 中观 察缺陷 的生 成 ,有助 于分析缺陷产生 的原因 ,也可 以 指导控制金属的流动趋势 。限于篇幅 ,图 5仅给 出 4 张追 踪点的位置截图 。
摘 要 :义卷简要介绍 了有 限冗软件 DEFORM的特点 0使用方法 ,并对制坯机镦粗 过程进行 _r仃 元模拟 ,埘 坯 料 【7、J部 的 心 乃和 应 变 分 布规 律 ,以 及上 砧 的 载荷 进 " J 分 析 .为实 际生 产提 供 依 批 关 键 词 :刚 有 限元 ;镦 粗 ;I)EFORM 软 件
(】)坯 料 材 质 的 选 取 及 有 限 兀 刚格 的 划 分 坯 料选 取 实际生 产 中常用 的  ̄900连 铸坯 ,高 度 2000 llln1.材 质 为 42CrMo 本次 的镦 粗 模 型 为对 称 模 ,为 j- 约 计算时问 .选取 l,4 料进 行模拟 ,划
有限 元分析 过程 是在求 解 器 巾完 成 的 , 过 汁 算 机 的计 算得 到最终 锻件 形状 .、【,上 砧 的最 大Jlli,J 达 到 10000 t时 ,坯 料被镦粗 为 ‘pl960,高 450 mill的 饼状 ,形成最终 的形 状如 冈 2所,J ,与实际生产 r I,J 状态 相符 ,同时也证 明丫本次有 限7己模拟 的准确性 ,、
Deform3D实验

学生实验报告书实验课程名称材料成型数值模拟开课学院材料学院指导教师姓名学生姓名学生专业班级2011 -- 2012 学年第二学期实验课程名称材料成型数值模拟点击,增加一个新问题,出现问题设置窗口。
保持系统设置不变,单击图1单击”窗口。
在该窗口中选择系统单位为“SI”,其他按钮退出窗口。
如图2.1所示:图2.13.增加新对象通过单击对象树下等插入对象按钮,添加Top Die 和Bottom Die。
使之加亮显示,单击按钮,为新增对象建立几何模型。
单击图4.1图5单击图标,打开模拟控制窗口,再单击step按钮进入步控制,依次对各项进行设置,使步数与每步进给量的积等于压下量,单击ok退出,如图6.1所示:图6.1然后在“simulation control”中设置stop停止内容,如图6.2所示:单击图8.1图8.2Inter-Object”设定单击按钮,由于当前没有设定关系,会弹出一个对话框询问是否希望系统添加默认的按钮后,进入过盈对象关系设定窗口,如图9.1所示:图9.1图9.2单击图标,然后单击Generate All按钮,毛坯与凸凹模的接触即生成,接触处出现所示,单击Ok退出。
图9.3凸模运动参数的设置,待其高亮显示后单击Movement图标,设定凸模的运动参数,如图单击图11 退出前处理窗口单击保存按钮,关闭前处理窗口。
Deform求解打开一个刚才生成xufujia-28.DB的文件图3.1单击按钮图3.23.输出载荷行程曲线单击图标,按图3.3(a)所示进行设置,单击Ok得到载荷行程曲线,如图图3.3(b)在模型基础上,分别改变凸模压下速度(5、10、15mm/s)进行模拟测量三种速度下对应的、盲孔直径D2、下凸台直径D3、盲孔深度H1、下凸台高。
实验二 圆环镦粗法测摩擦系数
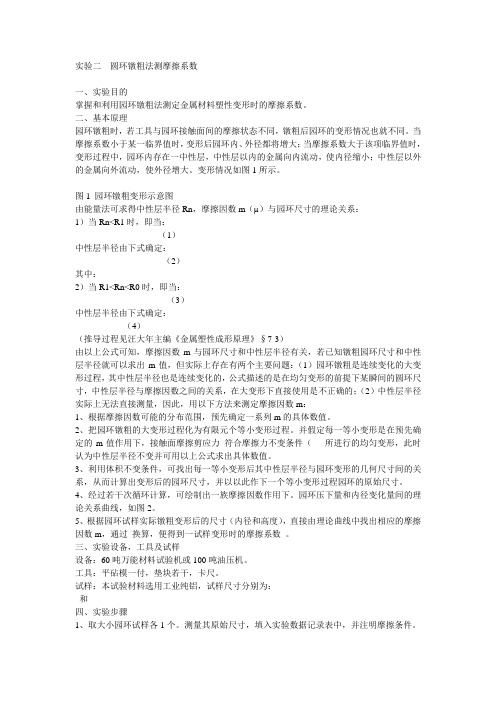
六、实验报告
1、确定摩擦系数并分析所得结果和影响测量精度的因素。
2、编写绘制园环镦粗的理论校准曲线程序。
表1实验记录表
序
号试样原始尺寸
D×d×H
(毫米)实润滑Байду номын сангаас
条件镦粗平
均高度
(毫米)镦粗后内径(毫米)摩擦
因数
m摩擦系数
测点平均
123
七、绘制理论曲线的计算机程序参考资料
一)计算公式
图1园环镦粗变形示意图
由能量法可求得中性层半径Rn,摩擦因数m(µ)与园环尺寸的理论关系:
1)当Rn<R1时,即当:
(1)
中性层半径由下式确定:
(2)
其中:
2)当R1<Rn<R0时,即当:
(3)
中性层半径由下式确定:
(4)
(推导过程见汪大年主编《金属塑性成形原理》§7-3)
由以上公式可知,摩擦因数m与园环尺寸和中性层半径有关,若已知镦粗园环尺寸和中性层半径就可以求出m值,但实际上存在有两个主要问题:(1)园环镦粗是连续变化的大变形过程,其中性层半径也是连续变化的,公式描述的是在均匀变形的前提下某瞬间的圆环尺寸,中性层半径与摩擦因数之间的关系,在大变形下直接使用是不正确的;(2)中性层半径实际上无法直接测量,因此,用以下方法来测定摩擦因数m:
6)以r0,r1和h1作为园环的原始尺寸,重复步骤3),4),5),一直到hj=H/2时为止。这使得到在给定m=0时一系列的rj和hj值,即给出m=0的一条理论曲线。△h取值愈小,曲线上的点愈密,曲线也愈准确。
7)再给定一个m值(如Ⅰ=2,m(2)=0.05,重复步骤3),4),5),6),又得到一组rj和hj,又可以绘出m=0.05的理论曲线。反复计算,便可绘制出该尺寸园环m=0~1.6的理论曲线来。
DEFORM实验报告

铜陵学院课程实验报告实验名称圆柱体压缩过程模拟实验课程材料成型计算机模拟指导教师张金标. 专业班级10 材控(2)姓名孟来福学号 1 0 1 0 1 2 1 0 5 82013年05月14日实验一 圆柱体压缩过程模拟1 实验目的与内容1.1 实验目的进一步熟悉AUTOCAD 或PRO/E 实体三维造型方法与技艺,掌握DEFORM 软件的前处理、后处理的操作方法与热能,学会运用DEFORM 软件分析压缩变形的变形力学问题。
1.2 实验内容运用DEFORM 模拟如图1所示的圆柱坯压缩过程。
(一)压缩条件与参数锤头与砧板:尺寸200×200×20mm ,材质DIN-D5-1U,COLD ,温度室温。
工件:材质DIN_CuZn40Pb2,尺寸如表1所示,温度室温。
(二)实验要求砧板工件锤头图1 圆柱体压缩过程模拟(1)运用AUTOCAD或PRO/e绘制各模具部件及棒料的三维造型,以stl格式输出;(2)设计模拟控制参数;(3)DEFORM前处理与运算(参考指导书);(4)DEFORM后处理,观察圆柱体压缩变形过程,载荷曲线图,通过轴对称剖分观察圆柱体内部应力、应变及损伤值分布状态;(5)比较方案1与2、3与4、1与3和2与4的模拟结果,找出圆柱体变形后的形状差别,说明原因;(6)提交分析报告(纸质和电子版)、模拟数据文件、日志文件。
2 实验过程2.1工模具及工件的三维造型根据给定的几何尺寸,运用AUTOCAD或PRO/E分别绘制坯料、锤头和砧板的几何实体,文件名称分别为workpiece,topdie,bottomdie,输出STL格式。
2.2 压缩过程模拟2.2.1 前处理建立新问题:程序→DEFORM5.03→File→New Problem→Next→在Problem Name栏中填写“Forging”→ Finish→进入前前处理界面;单位制度选择:点击Simulation Conrol按钮→Main按钮→在Units栏中选中SI (国际标准单位制度)。
2020年Deform实验报告镦粗报告

实验报告实验名称EFRH-3D徹粗仿真实验实验课程锻造工艺及模具设计指导教师专业班级姓名学号成绩213年 4月1日实验一 DEFRM-3D徹粗仿真实验1实验目的与内容实验目的通过DEFORM软件平台实现徹粗过程的仿真模拟实验。
了解材料在不同工艺条件下的变形流动情况,熟悉徹粗变形工艺待点。
掌握圆柱体徹粗过程的应力应变场分布特点。
实验内容运用DEFORM模拟如图1所示的圆柱坯压缩过程。
图1傲粗实验模型(一)工艺条件上模①2X5,刚性材料,初始温度2°C;下模2X2X4o工件16钢,尺寸如表1所示。
表1实验参数序号圆柱体直径,mm圆柱体高度, mm摩擦系数,滑动摩擦加热温度°C锤头运动速度,mm/s 徹粗行程1815954281512543SO2595448251254(二)实验要求(1)运用三维如阿健绘制各模具部件及棒料的三维造型,以St2格式输出;(2)设计模拟控制参数;(3)DEFORM前处理与运算;(4)DEFORM后处理,观察圆柱体压缩变形过程,载荷曲线图;(5)比较方案1与2、3与4、1与3和2与4的模拟结果,找出圆柱体变形后的形状差别,说明原因;(6)提交分析报告及分析日志文件(log)。
2实验过程1)建模通过UG将压缩的模型绘制出来,分别为坯料圆柱直径8mm高15mm 和圆柱直径8mm高25mm,并将它们各自的三部分分别导出为stl格式,并保存。
2)徹粗模拟打开一个deform软件,新建一个文件。
(Insert object)添加坯料Workpiece,上模Top Die,下模Bottom Die,并导入相应的之前保存的stl格式文件(Import );修改坯料的General,其中设定Object Type为plastic , AssignTemperature 为给定的9/12;(Mesh)将坯料分为 2/4 份,并预览(Preview), General Mesh选择坯料的材料(Material)为 16号钢;在Property中计算坯料的体积,选择自动计算(Active);修改 Top Die 的 General,其中设定 Object Type 为 Rigid, Assign Temperature 为2;设定其 Movement 速度为 5in/sec;设定 Bottom Die 的 General ,其中设定 Object Type 为 Rigid, Assign Temperature 为 2设定 Simulation Control 中的 Units 为 SI, Step 中的 Starting Step Number■为T, Number of Simula tion St eps 为 4, Step Increme nt to Save 为 1, Primary Die 为Top Die , With Constant Die Displacement 为lin.,然后点击OK。
- 1、下载文档前请自行甄别文档内容的完整性,平台不提供额外的编辑、内容补充、找答案等附加服务。
- 2、"仅部分预览"的文档,不可在线预览部分如存在完整性等问题,可反馈申请退款(可完整预览的文档不适用该条件!)。
- 3、如文档侵犯您的权益,请联系客服反馈,我们会尽快为您处理(人工客服工作时间:9:00-18:30)。
d. 设定 Bottom Die 的 General ,其中设定 Object Type 为 Rigid,Assign Temperature 为 200;
度,mm 滑动摩擦 度℃
mm/s
150
0
900
500
150
0.2
1200
500
250
0
900
500
250
0.2
1200
500
镦粗行程
40 40 40 40
(二)实验要求
2
(1)运用三维如阿健绘制各模具部件及棒料的三维造型,以 stl 格式输出; (2)设计模拟控制参数; (3)DEFORM 前处理与运算; (4)DEFORM 后处理,观察圆柱体压缩变形过程,载荷曲线图; (5)比较方案 1 与 2、3 与 4、1 与 3 和 2 与 4 的模拟结果,找出圆柱体变 形后的形状差别,说明原因; (6)提交分析报告及分析日志文件(log)。
实验报告
实验名称 EFORM-3D 镦粗仿真实验 实验课程 锻造工艺及模具设计 指导教师 专业班级 姓名 学号
成绩 2013 年 4 月 1 日
1
实验一 DEFORM-3D 镦粗仿真实验
1 实验目的与内容
1.1 实验目的 通过 DEFORM 软件平台实现镦粗过程的仿真模拟实验。了解材料在不同工艺
条件下的变形流动情况,熟悉镦粗变形工艺特点。掌握圆柱体镦粗过程的应力应 变场分布特点。 1.2 实验内容
e. 设定 Simulation Control 中的 Units 为 SI,Step 中的 Starting Step Number 为-1,Number of Simulation Steps 为 40,Step Increment to Save 为 1,Primary Die 为 Top Die ,With Constant Die Displacement 为 1in.,然后点击 OK。
运用 DEFORM 模拟如图 1 所示的圆柱坯压缩过程。
图 1 镦粗实验模型 (一)工艺条件
上模:Φ200×50,刚性材料,初始温度 200℃; 下模:200×200×40。 工件:16 钢,尺寸如表 1 所示。
序号
1 2 3 4
圆柱体直 径,mm
80 80 80 80
表 1 实验参数
圆柱体高 摩擦系数, 加热温 锤头运动速度,
3 实验结果及讨论
1) 变形过程(抓取 6 步) 第一组数据:
3
第二组数据:
4ቤተ መጻሕፍቲ ባይዱ
第三组数据:
5
第四组数据:
6
2) 载荷行程曲线 第一组数据:
第二组数据:
7
第三组数据:
8
第四组数据:
9
3) 等效应变(抓取 6 步) 第一组数据:
第二组数据:
10
第三组数据:
11
第四组数据:
12
4) 等效应力(抓取 6 步) 第一组数据:
2 实验过程
1) 建模 通过 UG 将压缩的模型绘制出来,分别为坯料圆柱直径 80mm 高 150mm 和圆 柱直径 80mm 高 250mm,并将它们各自的三部分分别导出为 stl 格式,并保存。
2) 镦粗模拟 a. 打开一个 deform 软件,新建一个文件。( Insert object )添加坯料
Workpiece,上模 Top Die,下模 Bottom Die,并导入相应的之前保存的 stl 格式 文件(Import);
b. 修改坯料的 General,其中设定 Object Type 为 plastic,AssignTemperature 为给定的 900/1200;(Mesh)将坯料分为 20000/40000 份,并预览(Preview),General Mesh;选择坯料的材料(Material)为 16 号钢;在 Property 中计算坯料的体积, 选择自动计算(Active);
圆柱体的摩擦系数为 0 的时候,其表面应变与内部的应变分布都比较均 匀,变形为均匀的变形;摩擦系数为 0.2 的时候,表面的应变与内部的应变 分布不均匀,各部分的最大应变都存在明显的差异。
比较载荷行程曲线,1、2、3、4 都是上升的趋势,主要分为两段,第一 段为弹性变形阶段,载荷曲线的斜率较大;第二段为塑性变形阶段,载荷曲 线的斜率比较小。摩擦力越大,载荷力越大;反之,载荷力越小。高度越低 载荷力越大,高度越高,载荷越小。
f. 设置摩擦系数,分别为 0 和 0.2 g. 保存并检核(Check),然后退出 h. 运行(Run) 3)后处理 可以通过选择查看压缩的每一步的变形过程,Damage ,Strain-Effective , Strain Rate -Effective ,Stress Effective ,Stress Max-Principal ,Temperature , 以及载荷行程曲线等。通过这些参数来检查所设定的这些数据是否合理。
比较损伤情况,由于 1 和 3 是不存在摩擦力的,它们是属于均匀变形的, 损伤系数几乎为 0。而 2 和 4 存在摩擦系数不为 0,产生的不均匀变形,出 现了鼓形,存在缺陷或缺陷隐患。
无摩擦镦粗时应变分布比较均匀,有摩擦存在时镦粗应变是不均匀的。 摩擦系数和高度都对变形有影响。
比较 1 和 3 的变形情况可以看出 1 和 3 变形都比较均匀,因为他们的摩 擦力都是 0,温度也是相同的 900 摄氏度;损伤度也几乎很少;但是 1 最终 的等效应变约为 0.31,而 3 最终等效应变约为 0.17;就等效应力看,1 的最 终等效应力约为 47,而 3 最终的等效应力就比它小,约为 38;
第二组数据:
13
第三组数据:
14
第四组数据:
15
5) 最大应力分布(抓取 6 步) 第一组数据:
第二组数据:
16
第三组数据:
17
第四组数据:
18
4 实验小结
答: 通过 1、2、3、4 的变形可以看出,1 和 3 没有在压缩的过程中是属于均
匀的变形过程,而 2 和 4 由于存在摩擦力,出现了不均匀的变形,圆柱体四 周出现鼓形轮廓。圆柱体在镦粗时除了受到变形工具的压缩力外,在断面接 触处有摩擦力作用,摩擦力阻碍金属质点横向流动,使得圆柱体产生鼓形。 对比 2 和 4 可知,2 比 4 出现的鼓形更为明显。