精密和超精密加工技术第7章精密研磨与抛光
精密研磨与抛光(精密加工)
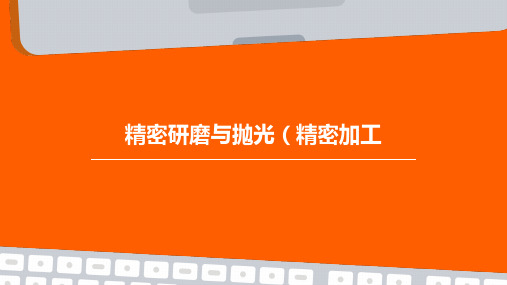
表面平滑
在抛光过程中,工件表面逐渐被 磨平,最终达到镜面或高度平滑
的效果。
表面改性
在抛光过程中,工件表面可能会 发生物理或化学变化,如表面层 晶格结构的变化或表面化学成分
的改变。
抛光工艺参数
压力
抛光压力是影响抛光效果的重要参数,压力过大会导致工件表面 损伤,过小则抛光效率低下。
02
精密研磨技术
研磨材料
01
02
03
04
刚玉
常用作研磨材料,具有高硬度 和耐磨性,适用于硬材料的研
磨。
碳化硅
具有高硬度和高韧性,适用于 研磨硬而脆的材料。
氧化铝
具有较好的韧性和耐磨性,适 用于研磨软材料和中等硬度的
材料。
天然磨料
如河砂、海砂等,可用于粗研 磨和抛光。
研磨机理
切削作用
研磨材料表面上的磨粒在压力作 用下切入工件表面,切削出微小
智能化的发展
智能检测与监控系统
通过引入传感器和智能化检测技术,实现对 研磨与抛光过程的实时监测和数据采集,提 高加工过程的稳定性和可靠性。同时,通过 数据分析与处理,优化加工参数,提高加工 效率和表面质量。
自动化生产线
通过集成机器人、自动化设备和智能化管理 系统,构建自动化生产线,实现研磨与抛光 过程的自动化和连续化生产。这将大幅提高 生产效率,降低人工成本,提升企业竞争力
总结词
高分子材料的研磨与抛光是实现高分子材料表面高精度和高光洁度的重要手段。
详细描述
高分子材料的研磨与抛光主要采用金刚石、刚玉等硬质材料作为磨料,通过研磨、抛光等工艺去除高 分子材料表面的凸起和划痕,以提高其表面质量和性能。高分子材料的研磨与抛光广泛应用于塑料、 橡胶、涂料等领域。
研磨与抛光的区别
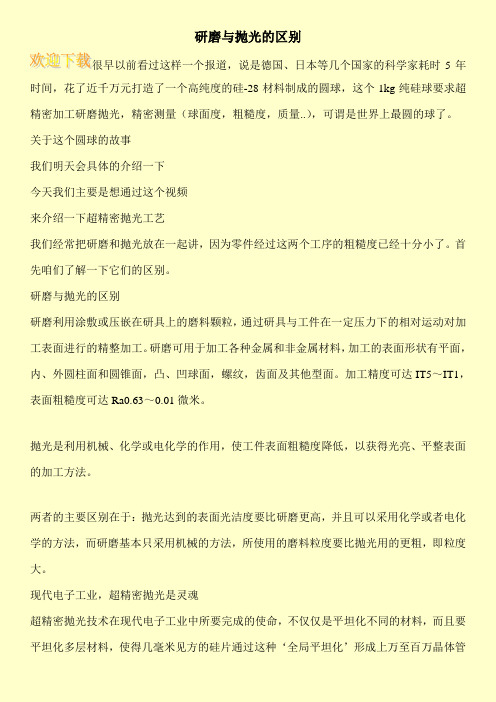
研磨与抛光的区别
很早以前看过这样一个报道,说是德国、日本等几个国家的科学家耗时5年时间,花了近千万元打造了一个高纯度的硅-28材料制成的圆球,这个1kg纯硅球要求超精密加工研磨抛光,精密测量(球面度,粗糙度,质量..),可谓是世界上最圆的球了。
关于这个圆球的故事
我们明天会具体的介绍一下
今天我们主要是想通过这个视频
来介绍一下超精密抛光工艺
我们经常把研磨和抛光放在一起讲,因为零件经过这两个工序的粗糙度已经十分小了。
首先咱们了解一下它们的区别。
研磨与抛光的区别
研磨利用涂敷或压嵌在研具上的磨料颗粒,通过研具与工件在一定压力下的相对运动对加工表面进行的精整加工。
研磨可用于加工各种金属和非金属材料,加工的表面形状有平面,内、外圆柱面和圆锥面,凸、凹球面,螺纹,齿面及其他型面。
加工精度可达IT5~IT1,表面粗糙度可达Ra0.63~0.01微米。
抛光是利用机械、化学或电化学的作用,使工件表面粗糙度降低,以获得光亮、平整表面的加工方法。
两者的主要区别在于:抛光达到的表面光洁度要比研磨更高,并且可以采用化学或者电化学的方法,而研磨基本只采用机械的方法,所使用的磨料粒度要比抛光用的更粗,即粒度大。
现代电子工业,超精密抛光是灵魂
超精密抛光技术在现代电子工业中所要完成的使命,不仅仅是平坦化不同的材料,而且要平坦化多层材料,使得几毫米见方的硅片通过这种‘全局平坦化’形成上万至百万晶体管。
第七讲精密加工和超精密加工

工艺过程的优化
五、游离磨料的高效加工
(一)超声研磨工艺
• 超声研磨是一种采用游离磨料(研磨膏或研磨液)进 行切削的加工方法。磨料通过研磨工具的振动产生切 削功能,从而把研磨头(工具)的形状传递到工件 上。 • 超声研磨正是利用脆性材料的这一特点。有目的有控 制地促进材料表层的断裂和切屑的形成。
二、金刚石车削技术及其应用
1. 金刚石车床的技术关键
• 除了必须满足很高的运动平稳性外,还必须具有很高 的定位精度和重复精度。镜面铣削平面时,对主轴只 需很高的轴向运动精度,而对径向运动精度要求较 低。金刚石车床则须兼备很高的轴向和径向运动精 度,才能减少对工件的形状精度和表面粗糙度的影 响。 • 目前市场上提供的金刚石车床的主轴大多采用气体静 压轴承,轴向和径向的运动误差在50nm以下,个别主 轴的运动误差已低于25nm。金刚石车床的滑台在90年 代以前绝大部分采用气体静压支承,荷兰的Hembrug 公司则采用液体静压支承。进入90年代以来,美国的 Pneumo公司(现已与Precitech公司合并)的主要产品 Nanoform600和250也采用了具有高刚性、高阻尼和高
(二)超声研磨加工玻璃
• 在玻璃上钻孔时,超声加工已经可以与金刚石钻削竞 争,优化后的超声钻孔已经达到金刚石钻削时的材料 切除速度。根据孔径和孔深的不同,超声钻孔时的进 钻速度可也达到20~40mm/min。 • 用金刚石钻削玻璃上的孔时,需要从两面进刀,以免 钻透时出现玻璃崩裂,采用超声钻孔时,则可从一侧 直接钻通,工具出口时不会出现玻璃的崩裂。从而可 以省去金刚石钻孔时的校正和倒角等加工工序。 • 在玻璃上钻小孔时,超声研磨的作用变得更为重要。 普通的金刚石钻孔,最小孔径大约在2mm左右。超声 钻孔时的最小孔径几乎没有任何限制,目前在实验室 中进行的实验表明,用超声研磨可在3mm厚的玻璃上 钻出直径为0.5~1.0mm的小孔
精密研磨与抛光ppt课件
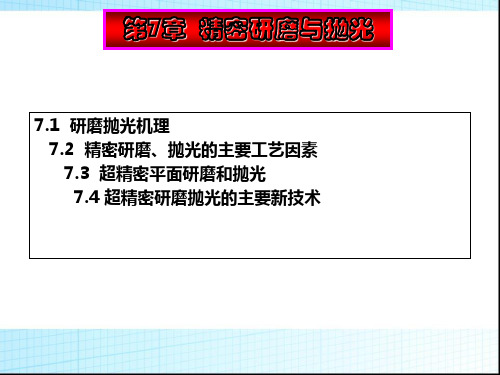
课后思考题
习题6-2 习题6-15
第7章 精密研磨与抛光
7.1 研磨抛光机理 7.2 精密研磨、抛光的主要工艺因素 7.3 超精密平面研磨和抛光 7.4 超精密研磨抛光的主要新技术
第1节 研磨抛光机理
一、研磨加工的机理
1.研磨时磨料的工作状态 1)磨粒在工件与研具之间发生滚动,产生滚轧 效果;
2)磨粒压入到研具表面,用露出的磨粒尖端对 工件表面进行刻划,实现微切削加工;
软质磨粒机械抛光(弹性发射加工)
最小切除可以达到原子级,直至切去一层 原子,而且被加工表面的晶格不致变形,能 够获得极小表面粗糙度和材质极纯的表面。 加工原理实质是磨粒原子的扩散作用和加速 的微小粒子弹性射击的机械作用的综合效果。 真空中带静电的粉末粒子加速法、空气流或 水流来加速。
化学机械抛光
3.金属材料的研磨
当金属表面用硬度计压头压入时,只在表面 产生塑性变形的压坑,不会发生脆性材料那 样的破碎和裂纹。
研磨时,磨粒的研磨作用相当于极微量切削 和磨削时的状态,且表面不会产生裂纹。
二、抛光加工的机理
抛光的机理:1)以磨粒的微小塑性切削生成切屑, 但是它仅利用极少磨粒强制压入产生作用。2)借助磨 粒和抛光器与工件流动摩擦使工件表面的凸凹变平。
磁流体精密研磨
磁性流体为强磁粉末在液相中分散为胶态尺寸 (<0.015μm)的胶态溶液,由磁感应可产生流动性,特 性是:每一个粒子的磁力矩较大,不会因重力而沉降,磁 化强度随磁场增加而增加。当将非磁性材料的磨料混入磁 流体,置于磁场中,则磨粒在磁流体浮力作用下压向旋转 的工件而进行研磨。磁流体精研的方法又有磨粒悬浮式加 工、磨料控制式加工及磁流体封闭式加工。
五、获得高质量平面研磨抛光的工艺规律
精密加工和超精密加工技术期末复习资料

考试复习题库一、填空题(本大题共10小题,每小题2分,共20分)请在每小题的空格中填上正确答案。
错填、不填均无分。
1、精密和超精密加工目前包含的三个领域:(超精密切削)、(精密和超精密磨削研磨)和(精密特种加工)。
2、金刚石晶体的激光定向原理是利用金刚石在不同的(结晶方向)上因晶体结构不同而对激光放射形成不同的(衍射图像)进行的。
3、金刚石刀具在超精密切削时所产生的积屑瘤,将影响加工零件的(表面质量)和(尺寸精度)。
4、目前金刚石刀具主要用于(铝、铜及其合金等软金属)材料的精密与超精密加工,而对于(黑色金属、硬脆)材料的精密与超精密加工,则主要应用精密和超精密磨料加工。
5、金刚石刀具在超精密切削时所产生的积屑瘤,将影响加工零件的(表面质量)和(尺寸精度)。
6、金刚石有(人工目测定向)、(X射线定向)和(激光定向)三种方法。
7、由于金刚石的脆性,在保证获得较小的加工表面粗糙度前提下,为增加切削刃的强度,应采用(较大)的刀具楔角β,故刀具的前角和后角都取得(较小)。
8、金刚石刀具适合加工(铝合金)、无氧铜、黄铜、(非电解镍)等有色金属和某些非金属材料。
9、单晶金刚石有(100 )、(110 )、(111 )三个主要晶面。
10、研磨金刚石晶体时,(110 )晶面摩擦因数最大,(100 )晶面次之,(111 )晶面最小。
11、在高磨削率方向上,(110 )晶面的磨削率最高,最容易磨;(100 )晶面的磨削率次之,(111 )晶面磨削率最低,最不容易磨。
12、单晶金刚石的(破损)机理主要产生于(111 )晶面的解理。
13、单晶金刚石的磨损机理主要属(机械磨损),其磨损的本质是(微观解理)的积累。
14、超硬磨料在当前是指(金刚石)和(立方氮化硼)以及它们为主要成分的复合材料。
15、用普通磨料砂轮或砂块与超硬磨料砂轮对磨进行修整的(磨削法)是目前最为广泛采用的(修整方法)。
16、精密和超精密磨料加工分为(固结磨料)加工和(游离磨料)加工两大类。
精密与超精密加工技术课件

珩磨效果受到多种因素的影响 ,如磨石的粒度、粘结剂的类 型、珩磨头的转速和压力等。
电解加工工艺
电解加工工艺概述
电解加工是一种利用电化学反应去除 工件材料的加工方法,具有加工精度 高、表面质量好等特点。
电解加工工艺流程
电解加工工艺通常包括工件表面处理 、电解液的选择和调整、电解加工设 备的设置以及加工参数的控制等步骤 。
、汽车和航空领域。
陶瓷材料
陶瓷材料具有高硬度、高耐磨性和 耐高温等特点,常用于制造刀具、 磨具和高温部件。
复合材料
复合材料由两种或多种材料组成, 具有优异的综合性能,如碳纤维复 合材料具有高强度和轻质的特点。
复合材料
玻璃纤维复合材料
玻璃纤维复合材料具有高 强度、高刚性和耐腐蚀等 特点,广泛应用于建筑、 船舶和汽车领域。
抛光效果受到抛光轮的材料、转速、抛光膏或抛光液的成分以及抛光 压力等因素的影响。
珩磨工艺
珩磨工艺概述
珩磨是一种利用珩磨头上的磨 石与工件表面进行摩擦,以去 除表面微小凸起和划痕的加工
方法。
珩磨材料
珩磨头上的磨石由硬质颗粒和 粘结剂组成,具有较高的硬度 和耐磨性。
珩磨工艺流程
珩磨工艺通常包括工件表面处 理、涂敷润滑剂、珩磨头的旋 转运动以及工件的往复运动等 步骤。
碳纤维复合材料
碳纤维复合材料具有高强 度、轻质和耐高温等特点 ,常用于制造航空器和体 育用品。
金属基复合材料
金属基复合材料以金属为 基体,加入增强纤维或颗 粒,以提高材料的强度、 刚度和耐磨性。
04
精密与超精密加工工艺
研磨工艺
研磨工艺概述
研磨材料
研磨是一种通过研磨剂去除工件表面微小 凸起和划痕的加工方法,以达到平滑表面 的效果。
《超精密加工技术》PPT课件

1〕砂带与工件柔性接触,磨粒载荷小,且均匀,工件受 力、热作用小,加工质量好〔 Ra 值可达 0.02μm〕。
2〕静电植砂,磨粒 有方向性,尖端向 上 〔 图 12〕 , 摩 擦 生热小,磨屑不易 堵塞砂轮,磨削性 能好。
磨粒 粘接剂 规格涂层 基带 图12 静电植砂砂带结构
3〕强力砂带磨削,磨削比〔切除工件重量与砂轮磨耗重量 之比〕高,有“高效磨削〞之称。
➢由聚氨基甲酸〔乙〕 酯制成,磨料直径 0.1~0.01μm
图13 弹性发射加工原理
➢ 机理:微切削+被加工材料的微塑性流动作用
一、 精细与超精细加工技术
★ 液体动力抛光 ➢ 工作原理〔图14〕
工具运动方向 抛光工具
➢抛光工具上开有锯齿槽, 抛光液
磨粒
靠楔形挤压和抛光液的反
弹,增加微切削作用。
工件
一、 精细与超精细加工技术
概述
◆精细加工 —— 在一定的开展时期,加工精度和外表质量 到达较高程度的加工工艺。
超精细加工 —— 在一定的开展时期,加工精度和外表质 量到达最高程度的加工工艺。 ◆瓦特改进蒸汽机 —— 镗孔精度 1mm
20 世纪 40 年代 —— 最高精度 1μm 20 世纪 末 ——
工件
砂带
b)砂带定心外圆磨削 (接触轮式)
支承板 主动轮
砂带 工件 c)砂带定心外圆磨削
(接触轮式)
砂带
接触轮
砂带
接触轮 d)砂带内圆磨削
(回转式)
工件
工件
砂带
工作台
e)砂带平面磨削 (支承板式)
支承轮 f)砂带平面磨削
(支承轮式)
图11 几种砂带磨削形式
一、 精细与超精细加工技术
《精密和超精密加工技术(第3版)》第3章精密磨削和超精密磨削
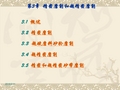
2018/3/11
第1节 概述
二、精密和超精密砂轮磨料磨具
磨料及其选择
超硬磨料制作的磨具在以下几方面能够满足精密加工和超精密加工 的要求,因此使用广泛。
1)磨具在形状和尺寸上易于保持,使用寿命高,磨削精度高。
2)磨料本身磨损少,可较长时间保持切削性,修整次数少,易于保持精度。
3)磨削时,一般工件温度较低,因此可以减小内应力、裂纹和烧伤等缺
磨具的形状和尺寸及其基体材料
根据机床规格和加工情况选择磨具的 形状和尺寸。 基体材料与结合剂有关。
2018/3/11
第1节 概述
三、精密和超精密涂覆磨具
涂覆磨具分类
根据涂覆磨具的形状、基底材料和工作条件与用途等,分类见下表
涂 覆 磨 具
工 作 条 件
基 底 材 料
形 状
耐 水 (N)
2018/3/11
精密砂带磨削:砂带粒度F230~F320,加
工精度1μm,Ra0.025; 超精密砂带磨削:砂带粒度W28~W3,加工精 度0.1μm,Ra0.025~0.008μm。
2018/3/11
第1节 概述
一、精密和超精密加工分类
游离磨料加工
磨料或微粉不是固结在一起, 而是成游离状态。 传统方法:研磨和抛光 新方法:磁性研磨、弹性发射 加工、液体动力抛光、液中研 抛、磁流体抛光、挤压研抛、 喷射加工等。
第3章 精密磨削和超精密磨削 3.1 概述
3.2 精密磨削 3.3 超硬磨料砂轮磨削
3.4 超精密磨削
3.5 精密和超精密砂带磨削
2018/3/11
第1节 概述
精密和超精密磨料加工是利用细粒度的磨粒和 微粉对黑色金属、硬脆材料等进行加工,得到高 加工精度和低表面粗糙度值。对于铜、铝及其 合金等软金属,用金刚石刀具进行超精密车削是 十分有效的,而对于黑色金属、硬脆材料等,用 精密和超精密磨料加工在当前是最主要的精密 加工手段。
- 1、下载文档前请自行甄别文档内容的完整性,平台不提供额外的编辑、内容补充、找答案等附加服务。
- 2、"仅部分预览"的文档,不可在线预览部分如存在完整性等问题,可反馈申请退款(可完整预览的文档不适用该条件!)。
- 3、如文档侵犯您的权益,请联系客服反馈,我们会尽快为您处理(人工客服工作时间:9:00-18:30)。
第2节 抛光
抛光加工:利用微细磨粒的机械作用和化学作用,在 软质抛光工具或化学加工液、电 / 磁场等辅助作用下, 为获得光滑或超光滑表面,减小或完全消除加工变质 层,从而获得高表面质量的加工方法。 抛光与研磨的区别: 磨料。抛光使用1µm以下的微细磨粒。研磨是采用微 米级磨粒。 研具材料的选择。抛光盘选用沥青、石蜡、合成树 脂和人造革、锡等软质金属或非金属材料制成,可根 据接触状态自动调整磨粒的切削深度、减缓较大磨粒 对加工表面引起的划痕损伤,提高表面质量。研磨采 用硬质研磨盘。
第3节 精密研磨与抛光的主要工艺因素 二、研磨与抛光设备
工件保持架齿面与设备的内齿圈和太阳轮同时啮合, 2018/6/30 使工件得到均匀不重复的加工轨迹。
2018/6/30
2.硬脆材料的研磨
一部分磨粒由于研磨压力的作用,嵌入研磨盘表面, 用露出的尖端刻划工件表面进行微切削加工;另一部分 磨粒则在工件与研磨盘之间发生滚动,产生滚轧效果。 在给磨粒加压时,就在硬脆材料加工表面的拉伸应力最 大部位产生微裂纹。当纵横交错的裂纹扩展并产生脆性 崩碎形成磨屑,达到表面去除的目的。
第7章 精密研磨与抛光
7.1 研磨 7.2 抛光 7.3 精密研磨与抛光的主要工艺因素 7.4 精密研磨抛光新技术 7.5 曲面研磨抛光技术
2018/6/30
第7章 精密研磨与抛光
在超精密加工中,超精密切削和超精密磨削的实
现在很大程度上依赖于加工设备、加工工具以及相关 技术的支持,并受到加工原理及环境因素的影响和限 制,要实现更高精度的加工十分困难。 超精密研磨抛光具有独特的加工原理,对加工设 备和环境因素要求不高,可以实现纳米级甚至原子级 的加工,已经成为超精密加工技术中一个十分重要的 部分。 精密研磨与抛光加工涉及的材料:金属材料,硅 、砷化镓等半导体材料,蓝宝石、铌酸锂等光电子材 2018/6/30 料,压电材料,磁性材料,光学材料等。
研 磨 脆 硬 材 料 时 , 要控制产生裂纹的大 小和均匀性。
2018/6/30
通 过 选 择 磨 粒 的 粒 度及控制粒度的均匀 性 ,可避免产生特别 大的加工缺陷。
3.金属材料的研磨
当金属表面用硬度计压头压入时,只在表面 产生塑性变形的压坑,不会发生脆性材料那 样的破碎和裂纹。
研磨时,磨粒的研磨作用相当于极微量切削 和磨削时的状态。磨粒是游离状态的,其与 工件仅是断续的研磨状态。 研磨表面不会产生裂纹。但研磨铝、铜等软 质材料时,磨粒会被压入工件材料内,影响 表面质量。
第1节 研磨
一、研磨加工的机理
研磨加工:利用硬度比被加工材料更高的微米级磨粒, 在硬质研磨盘作用下产生微切削和滚扎作用,实现被 加工表面的微量材料去除,使工件的形状、尺寸精度 达到要求值,并降低表面粗糙度、减小加工变质层的 加工方法。 1.研磨时磨料的工作状态 1)磨粒在工件与研具之间发生滚动,产生滚轧效果; 2)磨粒压入到研具表面,用露出的磨粒尖端对工件表 面进行刻划,实现微切削加工; 3)磨粒对工件表面的滚轧与微量刻划同时作用。
2018/6/30
第3节 精密研磨与抛光的主要工艺因素 一、工艺因素及其选择原则
精密研磨与抛光加工的主要工艺因素: 加工条件:对残留有裂纹的硬脆材料和不产生裂纹的 金属材料的加工条件不同; 研磨方式:单面研磨和双面研磨; 研磨机:应能均匀地加工工件,研具磨损要小并要求 能容易修整精度; 研具和抛光盘:必须避免因工作面磨损和弹性变形引 起精度下降; 研具材料:微细的磨粒和使磨粒对工件作用很浅的材 料; 加工液:提供磨粒、排屑、冷却和减轻不必要摩擦的 2018/6/30 效果。
2018/6/30
第1节 研磨 二、研磨加工特点
1.微量切削
由于众多磨粒参与研磨,单个磨粒所受载荷很小,控 制适当的加工载荷范围,可得到小于 1µ m的切削深度。
2.多刃多向切削 磨粒形状不一致,分布随机,有滑动、滚动,可实现 多方向切削。
2018/6/30
第1节 研磨 二、研磨加工特点
3.按进化原理成形
当研具与工件接触时,在非强制性研磨压力作用下,能自动 地选择局部凸出处进行加工,故仅切除两者凸出处的材料。 超精密研磨的加工精度与构成相对运动的机床运动精度几乎 无关。加工精度主要由工件与研具间的接触性质和压力特性, 以及相对运动轨迹的形态等因素决定。
获得理想加工表面要求:
1)研具与工件能相互修整; 2) 尽量使被加工表面上各点的加工痕迹与研磨盘的相对运动轨 迹不重复,以减小研具表面的几何形状误差对工件表面形状所 引起的“复印”现象,同时减小划痕深度,减小表面粗糙度。 3)在保证研具具有理想几何形状的前提下,采用浮动的研磨盒, 2018/6/30 可以保证加工质量。
第2节 抛光 二、研磨、抛光的加工变质层(接上页) 抛光加工后的加工变质层,由表层向里依 次为:抛光应力层、经腐蚀出现的二次裂纹应 力层、二次裂纹影响层和完全结晶层,整个加 工变质层深度约为 3μm。并且加工表面越粗, 加工变质层深度越大。 在加工过程中的化学反应对材料去除和减少加 工变质层有利。
2018/6/30
第2节 抛光 一、抛光加工的机理
1)以磨粒的微小塑性切削生成切屑,但是它仅利用极 少磨粒强制压入产生作用。 2)借助磨粒和抛光器与工件流动摩擦使工件表面的凸 凹变平。
2018/6/30
第2节 抛光 二、研磨、抛光的加工变质层
不管采取什么加工方法,或多或少要在被加工表 面上产生加工变质层,加工变质层使工件材质的结构、 组织和组成遭到破坏或接近于破坏状态,使工件表面 的力学性能、物理化学性能与母体材料不同,进而影 响制成元件的性能,因此在超精密研磨抛光中要求变 质层越薄越好。 硬脆材料研磨后的表面,从表层向里依次为:非 晶体层或多晶体层、镶嵌结构层、畸变层和完全结晶 结构,从弹塑性力学的角度评价变质层,依次为:极 薄的塑性流动层、有异物混入的裂纹层、裂纹层、弹 性变形层和母体材料。金属材料研磨后的加工表面变 质层与硬脆材料类似。 2018/6/30