四工位组合机床课程设计
四工位组合机床plc课程设计
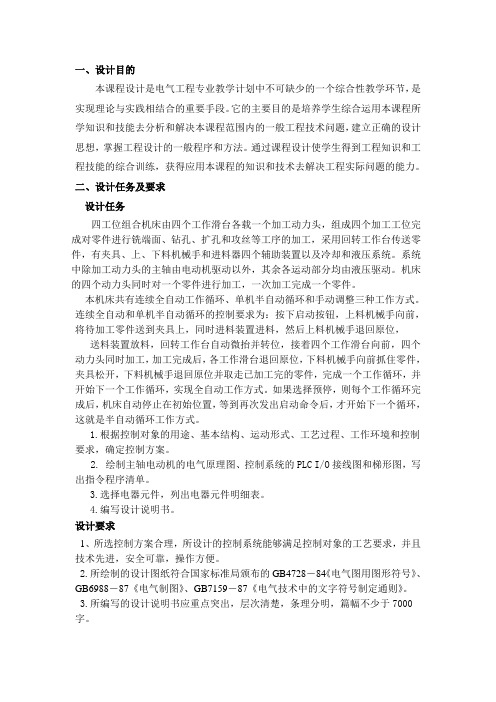
一、设计目的本课程设计是电气工程专业教学计划中不可缺少的一个综合性教学环节,是实现理论与实践相结合的重要手段。
它的主要目的是培养学生综合运用本课程所学知识和技能去分析和解决本课程范围内的一般工程技术问题,建立正确的设计思想,掌握工程设计的一般程序和方法。
通过课程设计使学生得到工程知识和工程技能的综合训练,获得应用本课程的知识和技术去解决工程实际问题的能力。
二、设计任务及要求设计任务四工位组合机床由四个工作滑台各载一个加工动力头,组成四个加工工位完成对零件进行铣端面、钻孔、扩孔和攻丝等工序的加工,采用回转工作台传送零件,有夹具、上、下料机械手和进料器四个辅助装置以及冷却和液压系统。
系统中除加工动力头的主轴由电动机驱动以外,其余各运动部分均由液压驱动。
机床的四个动力头同时对一个零件进行加工,一次加工完成一个零件。
本机床共有连续全自动工作循环、单机半自动循环和手动调整三种工作方式。
连续全自动和单机半自动循环的控制要求为:按下启动按钮,上料机械手向前,将待加工零件送到夹具上,同时进料装置进料,然后上料机械手退回原位,送料装置放料,回转工作台自动微抬并转位,接着四个工作滑台向前,四个动力头同时加工,加工完成后,各工作滑台退回原位,下料机械手向前抓住零件,夹具松开,下料机械手退回原位并取走已加工完的零件,完成一个工作循环,并开始下一个工作循环,实现全自动工作方式。
如果选择预停,则每个工作循环完成后,机床自动停止在初始位置,等到再次发出启动命令后,才开始下一个循环,这就是半自动循环工作方式。
1.根据控制对象的用途、基本结构、运动形式、工艺过程、工作环境和控制要求,确定控制方案。
2. 绘制主轴电动机的电气原理图、控制系统的PLC I/O接线图和梯形图,写出指令程序清单。
3.选择电器元件,列出电器元件明细表。
4.编写设计说明书。
设计要求1、所选控制方案合理,所设计的控制系统能够满足控制对象的工艺要求,并且技术先进,安全可靠,操作方便。
四工位专用机床课程设计
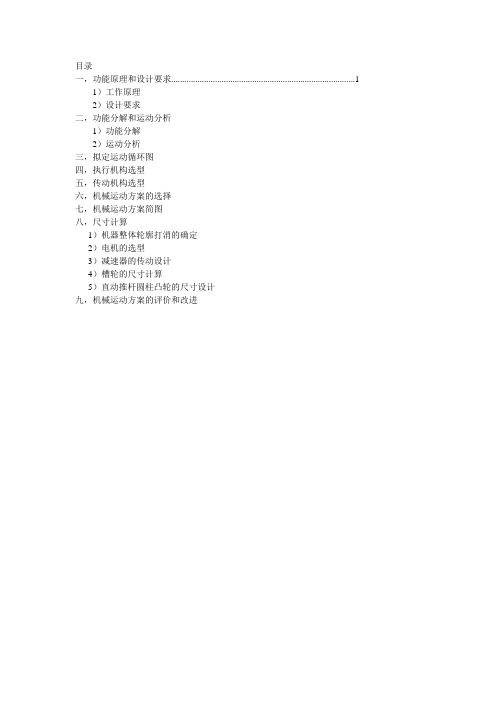
目录一,功能原理和设计要求 (1)1)工作原理2)设计要求二,功能分解和运动分析1)功能分解2)运动分析三,拟定运动循环图四,执行机构选型五,传动机构选型六,机械运动方案的选择七,机械运动方案简图八,尺寸计算1)机器整体轮廓打消的确定2)电机的选型3)减速器的传动设计4)槽轮的尺寸计算5)直动推杆圆柱凸轮的尺寸设计九,机械运动方案的评价和改进一,功能原理和设计要求1.工作原理四工位专用机床是在四个工位上分别完成相应的装卸工件,钻孔,扩孔,绞孔工作,它执行动作有两个:一时装有四工位工件的回转台转动;二十装有由专用电动机丹东的三把专用刀具的主轴箱的刀具的转动和移动。
2.设计要求1)顶端离开工件表面65mm,快速移动送进了60mm后,再匀速送进60mm(包括5mm刀具切入量,45mm工件孔深,10mm刀具切出量),然后快速返回,回程和工作行程的平均速度只比K=2.2)刀具匀速进给速度为2mm/s,工件装,卸时间不超过10s.3)生产率为每小时约75件。
4)执行机构系统应装入机体内。
二.功能分解和运动分析1.功能分解通过对工作原理和设计要求的分析可知,四工位专用机床的回转台与主轴箱的功能分为一下几个动作:1)安装工件的回转台间歇转动。
2)安装刀具的主轴箱要完成快进,匀速进给,快速返回几个动作。
3)主轴箱上的刀具转动切削工件。
2..运动分析设选定电动机型号为Y160M2—8,其转速n=720r/min,P=5.5km,则四工位专用机床的一个周期内的详细运动情况为:1)电动机作为驱动,通过减速装和其他齿轮系将符合要求的转速传递给回转台上的间歇机构,使其做间歇转动,同时也将符合要求的转速传递给主轴箱下的刀具移动机构,使其做符合要求的动作。
2)当间歇机构开始第一次循环时,安装,并加紧工件,间歇机构从0°转至90°3)间歇机构从从90°转至180°,主轴完成一次工作循环(快进,刀具匀速进给,快退)。
四工位专业机床课程设计

四工位专业机床课程设计一、课程目标知识目标:1. 学生能够掌握四工位专业机床的基本结构、功能及操作流程。
2. 学生能够理解机床坐标系、工件坐标系及编程中的坐标变换原理。
3. 学生能够运用所学知识,对中等复杂程度的零件进行加工工艺分析及编程。
技能目标:1. 学生能够熟练操作四工位专业机床,完成铣削、钻削等基本加工任务。
2. 学生能够运用CAD/CAM软件进行零件造型、加工路径规划及生成加工程序。
3. 学生能够根据实际加工要求,合理选择切削参数,提高加工效率及质量。
情感态度价值观目标:1. 培养学生对机械加工行业的兴趣和热爱,激发他们投身制造业的积极性。
2. 培养学生严谨、细致的工作态度,提高他们在实际工作中解决问题的能力。
3. 培养学生的团队协作意识,使他们能够在实际工作中与同事密切配合,共同完成任务。
本课程针对中职或高职学生,结合四工位专业机床的实际情况,注重理论联系实际,提高学生的实际操作能力和工艺分析能力。
课程目标旨在帮助学生掌握机床操作、加工工艺及编程等方面的知识,为将来从事机械加工行业工作打下坚实基础。
同时,注重培养学生的情感态度和价值观,使他们成为具有较高职业素养的技能型人才。
1. 四工位专业机床结构及功能:介绍机床的组成、各部件的功能及作用,以教材第3章为基础,重点讲解主轴、进给系统、冷却系统等关键部分。
2. 坐标系及坐标变换:以教材第4章为参考,讲解机床坐标系、工件坐标系的建立及编程中的坐标变换方法。
3. 零件加工工艺分析:结合教材第5章,分析铣削、钻削等加工工艺,教授学生如何根据零件图纸制定合理的加工方案。
4. CAD/CAM软件应用:以教材第6章为例,教授学生使用CAD/CAM软件进行零件造型、加工路径规划及生成加工程序。
5. 切削参数的选择:参考教材第7章,讲解切削速度、进给量、切削深度等参数对加工效率和质量的影响,教授学生如何合理选择切削参数。
6. 实践操作:安排教材第8章内容,指导学生进行四工位专业机床的操作,完成铣削、钻削等基本加工任务。
四工位机床课程设计心得

四工位机床课程设计心得一、课程目标知识目标:1. 理解并掌握四工位机床的基本结构、工作原理及功能。
2. 学习并熟知四工位机床的操作步骤、编程方法及相关工艺参数。
3. 了解四工位机床在制造业中的应用及其在现代化生产中的重要性。
技能目标:1. 能够独立操作四工位机床,完成简单的零件加工。
2. 能够正确编写四工位机床的加工程序,并对其进行调试和优化。
3. 能够分析并解决四工位机床在加工过程中出现的问题,提高加工质量和效率。
情感态度价值观目标:1. 培养学生对制造业的兴趣和热爱,提高其职业素养。
2. 增强学生的团队合作意识,培养其沟通协调能力。
3. 培养学生严谨细致的工作态度,提高其安全意识和责任感。
课程性质:本课程为实践性较强的课程,以学生动手操作为主,理论讲解为辅。
学生特点:学生具备一定的机械基础知识,但对四工位机床的了解有限,动手操作能力有待提高。
教学要求:注重理论与实践相结合,强调学生的参与和体验,通过实际操作让学生深入了解四工位机床的各个方面,培养其综合运用所学知识解决实际问题的能力。
同时,关注学生的情感态度价值观的培养,使其成为具备良好职业素养的技能人才。
在教学过程中,将课程目标分解为具体的学习成果,便于教学设计和评估。
二、教学内容1. 四工位机床概述- 机床基本结构- 工作原理与功能- 四工位机床在制造业中的应用2. 四工位机床操作与编程- 操作步骤与方法- 编程语言及编程方法- 工艺参数设定与调整3. 四工位机床加工工艺- 零件加工工艺流程- 刀具选择与安装- 加工过程中问题分析及解决方法4. 四工位机床加工程序编写与调试- 编程规范与要求- 程序编写技巧- 程序调试与优化5. 安全生产与职业道德- 机床操作安全知识- 职业道德与规范- 案例分析与讨论教学内容根据课程目标制定,分为五个部分,涵盖四工位机床的基本知识、操作与编程、加工工艺、程序编写与调试以及安全生产与职业道德。
教学大纲明确教学内容安排和进度,与教材章节紧密关联,确保教学内容的科学性和系统性。
四工位加工机床课程设计

四工位加工机床课程设计一、课程目标知识目标:1. 学生能够理解并掌握四工位加工机床的基本结构及其工作原理;2. 学生能够了解并描述四工位加工机床的常见加工工艺流程;3. 学生能够掌握四工位加工机床的安全操作规程和相关术语。
技能目标:1. 学生能够独立操作四工位加工机床完成指定零件的加工;2. 学生能够运用CAD/CAM软件进行四工位加工机床的编程;3. 学生能够解决四工位加工机床操作过程中遇到的一般性问题。
情感态度价值观目标:1. 培养学生热爱机械加工专业,增强其对制造业的认识和兴趣;2. 培养学生具有良好的团队合作精神,遵守加工机床操作规程,养成良好的安全生产意识;3. 培养学生勇于创新,善于思考,具备解决实际问题的自信心。
课程性质:本课程为机械加工专业课程,以实践操作为主,理论联系实际。
学生特点:学生具备一定的机械加工基础知识,动手能力较强,对新鲜事物充满好奇心。
教学要求:教师需结合学生特点,采用讲解与实践相结合的教学方法,充分调动学生的学习积极性,注重培养其操作技能和解决问题的能力。
在教学过程中,关注学生的个体差异,鼓励学生相互交流与合作,确保课程目标的实现。
通过本课程的学习,使学生具备四工位加工机床操作所需的基本知识和技能,为未来从事相关领域工作打下坚实基础。
二、教学内容1. 四工位加工机床概述:介绍四工位加工机床的发展历程、分类及其在制造业中的应用。
教材章节:《机械加工机床》第二章第一节。
2. 四工位加工机床的结构与原理:详细讲解四工位加工机床的各个组成部分及其工作原理。
教材章节:《机械加工机床》第二章第二节。
3. 四工位加工机床的加工工艺:分析四工位加工机床的加工工艺流程、参数设置及优化。
教材章节:《机械加工机床》第二章第三节。
4. 四工位加工机床操作与编程:讲解四工位加工机床的安全操作规程、编程方法及注意事项。
教材章节:《机械加工机床》第二章第四节。
5. 四工位加工机床维护与故障排除:介绍四工位加工机床的日常维护保养方法及常见故障的排除方法。
四工位机床课程设计

四工位机床 课程设计一、课程目标知识目标:1. 让学生理解并掌握四工位机床的基本结构、工作原理及功能;2. 了解四工位机床在制造业中的应用,以及其在现代工业生产中的重要性;3. 掌握四工位机床的操作步骤、编程方法及相关注意事项。
技能目标:1. 培养学生运用四工位机床进行加工的动手操作能力,提高其操作熟练度和准确性;2. 培养学生编制四工位机床加工程序的能力,使其能够根据实际需求设计合理的加工方案;3. 培养学生运用四工位机床解决实际问题的能力,提高其创新意识和实践能力。
情感态度价值观目标:1. 激发学生对制造业的兴趣,培养其热爱机械、追求技术进步的情感态度;2. 培养学生具备安全生产意识,使其认识到遵守操作规程、确保生产安全的重要性;3. 引导学生树立团队协作意识,培养其在实际工作中沟通、协调、合作的能力。
课程性质分析:本课程属于机械加工领域,具有较强的实践性和应用性。
结合学生特点,注重理论知识与实践操作的相结合,以培养学生的实际操作能力和解决问题能力为核心。
学生特点分析:学生为高年级学生,具有一定的机械基础知识、动手能力和自主学习能力。
在此基础上,通过本课程的学习,使其能够更好地掌握四工位机床的操作与应用。
教学要求:1. 理论教学与实践教学相结合,注重学生的实际操作训练;2. 教师引导学生积极参与课堂讨论,培养学生的思维能力和创新意识;3. 强化安全意识教育,确保学生在操作过程中的人身安全和设备安全;4. 注重课后评估,及时了解学生的学习进度和成果,调整教学方法和策略。
二、教学内容1. 四工位机床概述- 机床基本结构- 工作原理与功能- 四工位机床在制造业中的应用2. 四工位机床操作与编程- 操作步骤与方法- 编程基本原理- 编程实例分析3. 四工位机床加工工艺- 加工工艺参数选择- 刀具选择与使用- 工件装夹与定位4. 四工位机床安全与维护- 安全操作规程- 常见故障分析与排除- 机床日常维护与保养5. 实践操作环节- 四工位机床操作训练- 编程与加工实践- 综合加工案例分析与操作教学内容安排与进度:第一周:四工位机床概述第二周:四工位机床操作与编程第三周:四工位机床加工工艺第四周:四工位机床安全与维护第五周:实践操作环节(一)第六周:实践操作环节(二)第七周:综合加工案例分析与操作教材章节及内容:第一章:机床概述第二章:机床操作与编程第三章:加工工艺第四章:机床安全与维护第五章:实践操作案例教学内容科学性和系统性:确保教学内容与课程目标紧密结合,遵循由浅入深、循序渐进的原则,注重理论与实践相结合,提高学生的实际操作能力。
四工位专用机床课程设计

一,功能原理和设计要求 1.工作原理
四工位专用机床是在四个工位上分别完成相应的装卸工件,钻孔,扩孔,绞孔工作,它执行动作 有 两个:一时装有四工位工件的回转台转动;二十装有由专用电动机丹东的三把专用刀具的主轴箱的 刀具 的转动和移动。
2.设计要求 1 顶端离开工件表面 65mm,快速移动送进了 60mm 后,再匀速送进 60mm(包括 5mm 刀具切入量 ,
45mm 工件孔深,10mm 刀具切出量),然后快速返回,回程和工作行程的平均速度只比 K=2. 2 刀具匀速进给速度为 2mm/s,工件装,卸时间不超过 10s. 3 生产率为每小时约 75 件。
4 执行机构系统应装入机体内。
二.功能分解和运动分析
1.功能分解 通过对工作原理和设计要求的分析可知,四工位专用机床的回转台与主轴箱的功能分为一下几
方案一:槽轮机构。如图 3—1 所示槽轮机构的结构简单外形尺寸小,机械效率高,并能较平稳的,间 歇的进行转位。但因传动时尚存在柔性冲击,故常用于速度不高的场合。
方案二:不完全齿轮机构。如图 3—2 所示,它室友齿轮机构演变而得到的一种间歇欲动机构。即在主动 轮上制作出一部分齿,并根据运动时间与停歇时间的要求,在从动轮上做出与主动轮轮齿相啮合的轮齿 。 当从动轮做连续回转运动时,从东轮做间歇回转运动。不完全齿轮的结构简单,制造容易,工作可靠 , 设计时从动轮的运动时间和静止时间的比例可在较大范围内变化。其缺点是有较大冲击,故质疑与 低速, 轻载场合。
功能元解(匹配机构)
回转台间歇运动机构 主轴箱刀具移动机构 传动机构
1
槽轮机构 凹槽圆柱凸轮机构 定轴轮系减速器
2
3
不完全齿轮机构 盘装凸轮机构 外啮合行星齿轮减速器
棘轮机构 凸轮连杆机构
四工位机床课程设计

目录1 设计任务书1.1 设计任务 (02)1.2 设计要求 (02)2 方案设计与选择2.1 回转台的间歇转动 (03)2.1.1 棘轮机构 (03)2.1.2 槽轮机构(马尔它机构) (03)2.1.3 不完全齿轮机构 (04)2.1.4 凸轮式间歇运动机构 (04)2.2主轴箱的往复移动 (05)2.2.1 曲柄滑块机构 (05)2.2.2 圆柱凸轮机 (05)2.2.3 盘形凸轮机构 (06)2.2.4 凸轮连杆机构 (06)2.3 减速机构 (07)2.3.1 蜗轮蜗杆机构 (07)2.3.2 链传动机构 (07)2.3.3 定轴轮系 (07)2.3.4 外啮合行星轮系 (08)2.4 方案选择 (08)2.4.1 方案列表 (08)2.4.2 选择标准 (08)2.4.3 方案比较 (08)2.5 机械运动循环图 (09)2.6 数据计算 (10)2.6.1 减速机构 (10)2.6.2 主轴箱的往复移动 (10)2.6.3 回转台的间歇转动 (10)2.7 参考资料 (11)1 设计任务书1.1 设计任务:1 按工艺动作过程拟定机构运动循环图2 进行回转台间歇机构,主轴箱道具移动机构的选型,并进行机械运动方案评价和选择3 按选定的电动机和执行机构的运动参数进行机械传动方案的拟定4 对传动机构和执行机构进行运动尺寸设计5 在2号图纸上画出最终方案的机构运动简图6 编写设计计算说明书。
1.2 设计要求:1 刀具顶端离开工作表面65mm,快速移动送进60mm后,再匀速送进60mm(包括5mm 刀具切入量、45mm工件孔深、10mm刀具切出量,如图所示),然后快速返回。
回程和进程的平均速度之比K=2。
2 刀具匀速进给速度为2mm/s,工件装卸时间不超过10s。
3 机床生产率每小时约75件。
4 执行机构及传动机构能装入机体内。
5 传动系统电机为交流异步电动机,功率1.5Kw,转速960r/min。
- 1、下载文档前请自行甄别文档内容的完整性,平台不提供额外的编辑、内容补充、找答案等附加服务。
- 2、"仅部分预览"的文档,不可在线预览部分如存在完整性等问题,可反馈申请退款(可完整预览的文档不适用该条件!)。
- 3、如文档侵犯您的权益,请联系客服反馈,我们会尽快为您处理(人工客服工作时间:9:00-18:30)。
《电器与可编程控制器课程设计》课程设计题目:四工位组合机床班级:电气工程及其自动化1班姓名:学号:指导老师:2012 年6 月28 日1目录《电器与可编程控制器》课程设计任务书 (3)第1章绪论 (5)1.1机床介绍 (5)1.2流程控制 (6)1.3设计过程 (7)第二章硬件设计 (8)2.1硬件清单 (8)2.2地址分配 (9)2.3控制系统的PLC I/O接线图 (10)2.4主轴电动机的电气原理图 (12)第三章软件设计 (13)3.1状态转移图 (13)3.2公共模块 (14)3.3总程序 (14)3.4指令程序清单 (20)第4章操作与调试 (24)参考文献 (24)总结 (24)2《电器与可编程控制器》课程设计任务书学年学期:2011/2012 第2学期专业班级:09电气工程及其自动化指导教师:刘美俊设计时间:2012年6月25日~30日学时周数:1周一、设计目的本课程设计是电气工程专业教学计划中不可缺少的一个综合性教学环节,是实现理论与实践相结合的重要手段。
它的主要目的是培养学生综合运用本课程所学知识和技能去分析和解决本课程范围内的一般工程技术问题,建立正确的设计思想,掌握工程设计的一般程序和方法。
通过课程设计使学生得到工程知识和工程技能的综合训练,获得应用本课程的知识和技术去解决工程实际问题的能力。
二、设计任务及要求设计任务四工位组合机床由四个工作滑台各载一个加工动力头,组成四个加工工位完成对零件进行铣端面、钻孔、扩孔和攻丝等工序的加工,采用回转工作台传送零件,有夹具、上、下料机械手和进料器四个辅助装置以及冷却和液压系统。
系统中除加工动力头的主轴由电动机驱动以外,其余各运动部分均由液压驱动。
机床的四个动力头同时对一个零件进行加工,一次加工完成一个零件。
本机床共有连续全自动工作循环、单机半自动循环和手动调整三种工作方式。
连续全自动和单机半自动循环的控制要求为:按下启动按钮,上料机械手向前,将待加工零件送到夹具上,同时进料装置进料,然后上料机械手退回原位,送料装置放料,回转工作台自动微抬并转位,接着四个工作滑台向前,四个动力头同时加工,加工完成后,各工作滑台退回原位,下料机械手向前抓住零件,夹具松开,下料机械手退回原位并取走已加工完的零件,完成一个工作循环,并开始下一个工作循环,实现全自动工作方式。
如果选择预停,则每个工作循环完成后,机床自动停止在初始位置,等到再次发出启动命令后,才开始下一个循环,这就是半自动循环工作方式。
1.根据控制对象的用途、基本结构、运动形式、工艺过程、工作环境和控制要求,确定控制方案。
2. 绘制主轴电动机的电气原理图、控制系统的PLC I/O接线图和梯形图,写出指令程序清单。
3.选择电器元件,列出电器元件明细表。
34.编写设计说明书。
设计要求1、所选控制方案合理,所设计的控制系统能够满足控制对象的工艺要求,并且技术先进,安全可靠,操作方便。
2.所绘制的设计图纸符合国家标准局颁布的GB4728-84《电气图用图形符号》、GB6988-87《电气制图》、GB7159-87《电气技术中的文字符号制定通则》。
3.所编写的设计说明书应重点突出,层次清楚,条理分明,篇幅不少于7000字。
三、设计时间进度安排1.2012年6月25日上午:课题内容介绍。
2.2012年6月25日下午:仔细阅读设计任务书,明确设计任务与要求,收集设计资料,准备设计工具。
确定控制方案。
绘制电气原理图、控制系统的PLC I/O接线图和梯形图,3.2012年6月26日~2012年6月28日:写出指令程序清单。
设计控制系统的工艺图纸。
选择电器元件,列出电器元件明细表。
4. 2012年6月29日上午:编写设计说明书,准备答辩。
5. 2012年6月29日下午:答辩。
四、成绩考核设计70%答辩与考勤30%五、报告书写格式1.课程设计说明书封面。
2.课程设计任务书。
3.说明书目录。
4.前言。
5.正文(按设计内容逐项书写)。
6.总结。
7.参考文献。
六、参考资料1.刘美俊电气控制与PLC工程应用[M] 北京机械工业出版社 2011年2 刘美俊.可编程控制器应用技术[M].福州:福建科技出版社,20063 刘美俊.PLC控制系统故障检测与显示[J].上海:低压电器,2002,4:32~494 刘美俊.PLC在四工位组合机床控制系统中的应用[J].大连:组合机床与自动化加工技术,2003.5:73~745 刘美俊.PLC在压滤机控制系统中的应用[J].大连:组合机床与自动化加工技术,2003.11:58~594第1章绪论机床控制是PLC的主要应用领域之一。
传统上,机床的控制大多使用继电器逻辑控制系统,这种控制系统功能比较单一,在用于具有复杂逻辑关系的机床控制时,电路复杂,元器件多,可靠性差。
用PLC对机床控制进行技术改造是PLC的主要应用领域之一1.1机床介绍机床由四个工作滑台各载一个加工动力头,组成四个加工工位。
上图所示为该机床十字轴铣端面打中心孔的俯视示意图。
除了四个加工工位外,还有夹具,上、下料机械手和进料器四个辅助装置以及冷却和液压系统共14个部分。
机床的四个加工动力头同时对一个零件的四个端面及中心孔进行加工。
一次加工完成一个零件,由上料机械手自动上料,下料机械手自动取走加工完成的零件51.2 流程控制机床控制流程组合机床要求有全自动、半自动、手动三种工作方式。
图所示为组合机床控制系统全自动工作循环和半自动工作循环时的状态流程图。
图中S2是初始状态,实现初始状态的条件是各滑台、各辅助装置都处在原位,夹具为松开状态,料道放料且润滑系统情况正常。
现在把组合机床全自动和半自动工作循环介绍一下。
当按下启动按钮后,上料机械手向前,将零件送到夹具上,夹具夹紧零件,同时进料装置进料。
之后上料机械手退回原位,进料装置放料。
接下来是四个工作滑台向前,四个加工动力头同时加工,铣端面,打中心孔。
加工完成后,各工作滑台退回原位。
下料机械手向前抓住零件,夹具松开,下料机械手退回原位并取走加工完成的零件,一个工作循环结束。
如果没有选择预停,则机床自动开始下一个工作循环,实现全自动加工工作方式。
如果选择了预停,则每个工作循环完成后,机床自动停止在初始状态,当再次发出工作启动命令后,才开始下一个工作循环,这就是半自动工作方式总体的控制流程当按下启动按扭后,上料机械手向前,将零件送到夹具上,夹具加紧零件,同时进料装置进料,之后上料机械手退回原位,进料装置放料,然后四个工作滑台向前,四个加工动力头同时加工(洗端面),加工完成后。
由四工位加所实现的是加工按次序加工。
本次加工按次序分为在一工位装卸、二工位打中心孔、三工位钻孔、四工位加工螺纹。
由此可以得到机床加工流程如下图实际组合机床加工过程,每个动力头加工时都是按照快进-工进-快退过程实现的。
由查阅资料得知动力头加工的进退速由液压缸本身的结构特性所决定的,本组PLC为设计要求的设计任务中没有此方面的要求所以本段加以省略。
1)回转台工作原理按下回转台工作按钮后,电磁阀S02通电,使得回转台微抬,碰到行程开关SQ02,电磁阀S01, S03通电,回转台开始回转,当碰到行程开关SQ03,电磁阀S01, S03, S05通电,使得回转台低回;离开行程开关SQ03电磁阀S01, S04, S056通电,回转台反靠;碰到行程开关SQ04,电磁阀S02通电,回转台夹紧;当压力继电器KP1发出信号,电磁阀S02, S06通电,回转台脱离;碰到行程开关SQ05,电磁阀S02, S04, S06通电,回转台返回;碰到行程开关SQ01,回转液压缸返回原位等待下一次循环。
2.)钻孔工作原理按下钻孔工作按钮,电磁阀S11, S13通电,钻孔工位快进;当碰到行程开关SQ12,电磁阀S11,接触器线圈KM3通电,钻孔工位转为工进,同时钻孔电动机启动;当碰到行程开关SQ13,电磁阀S12, S13通电,钻孔工位快退;当碰到行程开关SQ11,接触器线圈KM3断电,钻孔电动机停止,钻孔工位返回到了原位。
3)扩孔工作原理当工作台夹紧后,S05、1DP发出信号,电磁铁10YA带电,扩孔液压杆快进,碰到行程开关S22,电磁铁13YA带电,液压杆工进。
碰到行程开关S23,10YA、13YA断电,11YA带电,液压杆快退。
碰到S21,11YA断电,扩孔工位回原位。
4)攻丝工作原理按下攻丝工作按钮,电磁阀S31通电,攻丝工位快进;碰到行程开关SQ32,工位停止,接触器线圈KM5通电,攻丝电动机正传开始;碰到行程开关SQ33,接触器线圈KM6通电,攻丝电动机反转;碰到行程开关SQ34,攻丝电动机停止,电磁阀S32通电,工位快退;碰到行程开关SQ31,攻丝工位返回原位停止,等待下次循环。
1.3 设计过程总体方案选择设计:1.四个工作台的前后移动分别由电机M1 M2 M3 M4控制2.冷却装置有SB23控制由电机M5提供动力,而供油系统在系统通电之后便开始工作由电机M6提供动力3.各工作台加工时工位的距离由形成开关控制,移动时ⅠⅢ工作台先移动,1秒之后ⅡⅣ工作台再移动,有利于力的平衡4.六台电机均采用热继电器实现过载保护5.采用指示灯控制按钮以显示设备运动状态6.主电路及控制电路采用熔断器实现短路保护7.电气控制箱置于专门的操作室。
电器板与控制板之间,以及电控箱与执行系统之间的连接,采用接线板进出线方式7第二章硬件设计2.1 硬件清单表2.1 电器元件明细表名称元件符号型号与规格数量刀开关QF DZ5-20/330 1熔断器FU1-5 RL1-1513FU6BLX-12按钮SB LA2型,开起式,550V,5A 6转换开关SA LW6-2/B7行程开关SQ LXJ-1A8接触器KM CJX1-12 3压力继电器KP DP-63B 1电动机M JO2-31-4 3YV MFZ1-0.79 电磁阀中间继电器KA HH54 9指示灯HL XD-1-6.3,6.3V,1W,0.18A9变压器TC BK-100型,380/220-110 1时间继电器KT ST3PC 1二极管VD ZPZ17A-X 4电容C 选耐压50V,470 1照明灯EL182.2 地址分配表 2.2地址分配表输入输出功能地址功能地址功能地址功能地址回原点X0 快转工X24 动力头快速Y20 手动X1 终点X25 铣端面Y0 扩孔半自动X2 过载X26 钻孔Y1 向前Y21 全自动X3 点动X27 扩孔Y2 向后Y22 夹紧X4 钻孔动力头攻螺纹Y3 快速Y23 松开X5 原位X30 退刀Y4 攻螺纹Y24 进料X6 已快进X31 上料进Y5 快退Y25Y26 放料X7 已工进X32 上料退Y6 润滑电动机Y27 润滑压力X10 点动X33 下料进Y7 冷却电动机总停X11 扩孔动力头下料退Y10 蜂咛器Y30 起动X12 原位X34 夹紧机构预停X13 已快进X35 夹紧Y11紧急停止X14 已共进X36 松开Y12冷却泵开X15 点动X37 铣端面冷却泵停X16 攻丝动力头向前Y13上料原位X17 原位X40 向后Y14上料终点X20 已快进X41 快速Y15下料原位X21 已攻螺纹X42 钻孔下料终点X22 已腿丝X43 向前Y169铣端面动力头点动X44 向后Y17原位X23 ------- -----2.3控制系统的PLC I/O接线图10KM6 KM5KMKM AC220V紧急停车钻孔扩孔 攻螺纹 退刀上料进 上料退 下料进 下料退 夹紧 松开向前 快速 向前 向后 快速负载电源KMKMFX2N-80MR-001X4 夹紧 X5 松开 X6 进料 X7 放料 X10 滑润压力 X11 总停 X12 启动 X13 预停 X14 紧急停止 X15 冷却泵开X 16 冷却泵停 COM1 X17 上料原位 COM2 X20 上料终点X21 下料原位 Y1 X22 下料终点 Y2 X23 原位Y3X24 快转工X25 终点 Y4 X26 过载X27 点动 Y5 X1 手动X0 回原点 Y6 X3 半自动X30 原位 Y7 X31 已快进X32 已工进 Y10 X33 点动X34 原位 Y11 X35 已快进X36 已工进 Y12 X37 点动X40 原位 Y13 X41 已快进X42 已攻螺纹 Y20 X43 已退丝 X44 点动 Y21 Y22COM Y23图2.2 控制系统的PLC I/O接线图2.4 主轴电动机的电气原理图1)由接触器KM1 KM2 KM3 KM4控制四台电机M1 M2 M3 M4 ,KM5控制M5,KM6控制M62)M1 M2 M3 M4由热继电器FR1 FR2 FR3 FR4实现过载保护根据以上设计原则绘制如图所示的主电路图主轴电动机的电气原理图图3.3主轴电动机的电气原理图第三章软件设计根据设计的内容和目的可以得到以下程序3.1 状态转移图状态转移图3.13.2公共模块图3.2 公用模块3.3总程序3.4指令程序清单图3.3指令程序清单第4章操作与调试将电动机、控制系统按要求连线,导入PLC程序送PLC机调式,先对照输入信号表,设置好原始状态下所有输入信号的状态,再使PLC运行,按下相应按钮,按梯形图程序,观察输出情况,经观察符合程序设定的输出;按工步状态在一个工作循环里逐步转换的顺序依次发出状态转移指令信号,系统将结束一个工步状态转入下一个工步状态,将转换情况和已编的程序相比较,知转换情况与程序设定的输出情况相同,在调试过程中注意各部分是否满足要求,有无失步现象,依次调试各个步骤,看是否满足要求。