四工位组合机床的电气控制电路设计
四工位组合机床PLC设计说明书
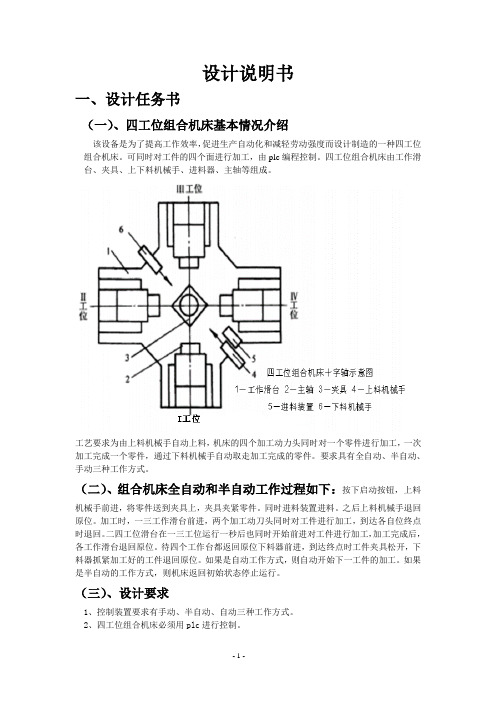
设计说明书一、设计任务书(一)、四工位组合机床基本情况介绍该设备是为了提高工作效率,促进生产自动化和减轻劳动强度而设计制造的一种四工位组合机床。
可同时对工件的四个面进行加工,由plc编程控制。
四工位组合机床由工作滑台、夹具、上下料机械手、进料器、主轴等组成。
工艺要求为由上料机械手自动上料,机床的四个加工动力头同时对一个零件进行加工,一次加工完成一个零件,通过下料机械手自动取走加工完成的零件。
要求具有全自动、半自动、手动三种工作方式。
(二)、组合机床全自动和半自动工作过程如下:按下启动按钮,上料机械手前进,将零件送到夹具上,夹具夹紧零件。
同时进料装置进料。
之后上料机械手退回原位。
加工时,一三工作滑台前进,两个加工动刀头同时对工件进行加工,到达各自位终点时退回。
二四工位滑台在一三工位运行一秒后也同时开始前进对工件进行加工,加工完成后,各工作滑台退回原位。
待四个工作台都返回原位下料器前进,到达终点时工件夹具松开,下料器抓紧加工好的工件退回原位。
如果是自动工作方式,则自动开始下一工件的加工。
如果是半自动的工作方式,则机床返回初始状态停止运行。
(三)、设计要求1、控制装置要求有手动、半自动、自动三种工作方式。
2、四工位组合机床必须用plc进行控制。
3、有急停、预停两种停止按钮。
4、滑台的进退,夹具的夹紧、松开以及上下料之间都进行互锁保护。
5、绘制电器原理图、选择电器元件、编制元件目录表。
6、绘制总接线图、控制面板布置图与接线图等工艺图样。
7、编制设计使用说明书。
8、设计用户程序,编写设计报告。
二、设计过程(一)、总体方案选择说明1、四工位组合机床四个主轴转动分别用M1~M4电机作为动力源。
2、四个滑台的进退以及夹具、上下料机械手和进料装置有一个液压系统进行控制,只需选用一个液压泵。
而冷却装置单独用一个液压系统进行控制。
3、四个滑台上都设有行程开关,来保证主轴与工件的相对位置的准确性。
4、M1~M4为自动控制连续运转,采用热继电器实现过载保护5、滑台的进退,夹具的夹紧、松开以及上下料之间都进行互锁保护。
四工位组合机床PLC电气控制系统设计

第一部分设计任务与调研 (1)第二部分设计说明 (4)第三部分设计成果 (13)第四部分结束语 (21)第五部分致谢 (21)第六部分参考文献 (22)第一部分设计任务与调研1、毕业设计的主要任务设计一台由双面钻床、双面铳床组合夹紧放松,在一次半自动循环中,工件经过钻、铳两个工位进行加工,两个工位各完成一道加工工序,在加工而成的较型壳体零件的粗加工为对象的四工位组合机床的PLC电气控制系统。
2、设计的思路、方法设计思路,依托电工实训中心和自动化设备维修实训中心的钻床、铳床、PLC 等实训设备,充分运用所学专业知识和实践技能,详细制定设计方案和阶段进度计划,通过程序设计、模拟调试,建立正确的设讣思路,掌握正确的设计方法,修订完善,设计出能实现铳、钻双面四工位加工系统功能的组合机床PLC电气控制系统。
设计方法,利用文献检索、图书馆借阅、手册查询、设备选型、PLC编程、PLC 实训室程序调试;分析工艺与控制流程、分析控制要求与方式、分析系统设汁的原则和方法、确定PLC输入输出设备和I/O点数及选择PLC机型、硬件系统设计、软件程序设计、绘制控制系统接线图、电器元件的选择、程序调试。
3、本课题相关的资料4、调研的目的和总结4. 1调研的目的起初的组合机床于1911年在美国制成,用于加工汽车零件。
1953年,美国 福特汽车公司和通用汽车公司与美国机床制造厂协商,确定了组合机床通用部件 标准化的原则。
初期,各机床制造厂都有各自的通用部件标准。
为了提高不同制 造厂的通用部件的互换性,便于用户使用和维修。
1973年,国际标准化组织(ISO ) 公布了第一批组合机床通用部件标准。
1975年,中国第一机械工业部颁布了中 国的第一批组合机床通用部件标准。
二十世纪70年代以来,随着可转位刀具、 密齿铳刀、锤孔尺寸自动检测和刀具自动补偿技术的发展,组合机床的加工精度 也有所提高。
铳削平面的平面度可达0. 05毫米/ 1000亳米,表面粗糙度可低达 2. 5〜0.63微米;镇孔精度可达IT7〜6级,孔距精度可达0. 03〜0. 02微米。
基于PLC的四工位组合机床控制系统设计

本科毕业论文(设计)设计题目:基于PLC的四工位组合机床控制系统设计学院:专业:机械设计制造及其自动化班级:学号:学生姓名:指导教师:第2页贵州大学本科毕业论文(设计)诚信责任书本人郑重声明:本人所呈交的毕业论文(设计),是在导师的指导下独立进行研究所完成。
毕业论文(设计)中凡引用他人已经发表或未发表的成果、数据、观点等,均已明确注明出处。
特此声明。
论文(设计)作者签名:日期:目录摘要 (III)Abstract (IV)第一章绪论 (5)1.1组合机床概述 (5)1.2 PLC的四工位组合机床控制系统设计的目的和意义 (5)1.3 PLC的四工位组合机床控制系统设计的国内外现状和发展趋势 (6)第二章四工位组合机床原理及液压系统 (8)2.1四工位组合机床的工作原理与过程分析 (8)2.1.1 回转台工作原理 (9)2.1.2 钻孔工作原理 (9)2.1.3 扩孔工作原理 (9)2.2 四工位组合机床的液压控制系统 (11)第三章 PLC概述与方案论证 (13)3.1 PLC概述 (13)3.1.1 PLC基本介绍 (13)3.1.2 PLC硬件组成 (13)3.2方案论证 (17)3.2.1 PLC与继电器-接触器相比较: (17)3.2.2 PLC与单片机比较 (18)第四章电气控制系统硬件设计 (20)4.1选择PLC机型 (20)4.1.1 结构选择 (20)4.1.2 I/O点选取原则 (20)4.1.3确定PLC机型及扩展模块 (21)4.2设计I/O分配表 (22)4.3设计PLC控制系统电气原理图 (24)4.3.1 PLC的详细接线图 (24)4.3.2 电机电气原理图 (26)4.4设计PLC控制系统操作面板 (26)4.5相关元器件的选择 (28)4.5.1电气元件的选取 (28)4.5.2液压元器件的选择 (29)第五章部分程序的分析以及程序调试结果 (30)5.1 以下程序段的分析: (30)5.2 此次设计的程序建立以及调试结果分析如下: (32)第六章设计总结与体会 (34)6.1设计总结 (34)6.2心得体会 (35)参考文献 (36)致谢 (37)附录一 (38)附录二 (52)基于PLC的四工位组合机床控制系统设计摘要文章以四工位组合机床为研究对象,四工位主要包括钻孔、扩孔、攻丝、机械手上下料等工位,通过对主要结构和运动形式的探究以及对机床的工作过程和控制要求分析,给出了机床动作循环图、液压元件动作表以及四工位组合机床的液压控制系统;并采用PLC控制系统的设计方法, 进行了软硬件设计,列出了PLC的I/O地址分配表,绘制了PLC 的I/O分配图和单循环自动工作流程图,编写PLC控制程序的梯形图和指令表;由操作面板组成的人机界面,使整个控制系统的操作变得简单,方便,大大提高了系统的自动化程度和实用性。
四工位组合机床动力头主控制电路的设计

四工位组合机床动力头主控制电路的设计作者:张继波来源:《山东工业技术》2017年第18期摘要:四工位组合机床及其自动线在当今机械制造业中扮演着越来越重要的角色。
本文对于组合机床的动力头的主控制电路的设计,分析了系统的主电路及控制电路图,并根据系统运行要求,确定了机床及控制系统的元件型号。
关键词:组合机床;动力头;主控制DOI:10.16640/ki.37-1222/t.2017.18.0321 引言组合机床是由一些通用部件和专用部件组成的高效率自动化专用加工设备。
组合机床中使用的通用部件,按其功能可分为:动力部分、传递部分、支撑部件、控制部件和辅助部件等。
动力部件指用来实现主运动和进给运动的部件,包括动力头和动力滑台,在动力部件中,能同时完成加工刀具的切削及进给运动的称为动力头;而只能完成进给运动的动力部件称为动力滑台。
2 总体设计组合机床的控制系统大多采用机械、液压、电器、气压相结合的控制方式。
本设计的机床主要由液压回转工作台和液压动力头两个通用部件组合而成,从而进行控制的,如图1所示。
T1、T2和T3是通用的动力头,是完成进给运动的动力部件。
在动力头上可以安装多轴箱,安装各种切削刀具完成钻、扩、铰、镗、刮端面、倒角、铣削和攻丝等工序。
工作台是以四个位置旋转,每回转90°为一个工位,工作台面上装有专门的夹具,夹紧被加工的工件。
该组合机床的自动工作循环是:花盘上升→花盘转动→花盘下降→摆动缸复位→松开工件→夹紧工作动力头快进→动力头工进→动力头延时停留→动力头快退。
3 主电路设计及关键元件选型该机床共有五台电动机:液压油泵电动机M1、冷却泵电动机和三个动力头电动机M3、M4、M5。
五台电动机均直接启动,分别由KM1、KM2、KM3、KM4、KM5控制单向运转,均没有电气变速、制动要求,由FR1、FR2、FR3、FR4和FR5作过载保护,FU1、FU2、FU3、FU4和FU5作M1、M2、M3、M4和M5作短路保护,QS为电源引入开关。
组合机床电气控制课程设计

目录第一章绪论 (1)第二章设计方案 (3)2.1 左、右两动力头进给电机 (3)2.2电动机控制电路 (3)2.3液压泵电动机 (4)2.4液压动力滑台控制 (4)2.5主电路及照明电路 (6)2.6保护与调整环节 (6)2.7继电器电气原理简图 (8)第三章I/O分配表 (10)第四章组合机床电气控制电路图 (11)第五章课程设计的具体内容 (12)5.1单循环自动工作 (12)5.1.1单循环自动工作循环图 (12)5.1.2单循环自动工作功能表 (12)5.1.3单循环自动工作梯形图 (12)5.2左铣单循环工作 (13)5.2.1左铣单循环功能表 (13)5.2.2左铣单循环梯形图 (13)5.3右铣单循环工作梯形图 (13)5.4公用程序 (13)5.5回原位程序 (14)5.6手动程序 (15)5.7 PLC梯形图总体结构图 (15)5.8面板设计 (16)第六章系统调试 (17)第七章设计心得 (18)第八章参考文献 (19)第一章绪论对于机械—电气结合控制的组合机床,电气控制系统起着重要的神经中枢作用。
传统的组合机床采用的继电器—接触器控制系统,接线复杂、故障率高、调试和维护困难。
随着PLC控制技术日益成熟并得到越来越广泛的应用,利用原有的继电器—接触器控制电路设计PLC控制系统,或直接进行PLC控制系统的设计,都能很好地满足组合机床自动化控制的要求。
本次设计的要求如下:组合机床结构示意图组合机床工作循环图组合机床采用两个动力头从两个侧面分别加工,左、右动力头的电动机均为2.2kw,进给系统和工件夹紧都用液压系统驱动,液压泵电动机的功率为3kw,动力头和夹紧装置的动作由电磁阀控制。
设计要求如下:(1)两台铣削动力头分别由两台笼型异步电动机拖动,单向旋转,无须电气变速和停机制动控制,但要求铣刀能进行点动对刀。
(2)液压泵电动机单向旋转,机床完成一次半自动工作循环后按下总停机按钮时才停机。
基于PLC的四工位组合机床控制系统设计

基本内容
基本内容
摘要: 本次演示介绍了一种基于可编程逻辑控制器(PLC)的四工位组合机床控制系 统设计。该系统通过优化硬件和软件配置,实现了高效、准确的工位控制,提高 了生产效率。本次演示详细阐述了PLC控制技术
基本内容
的原理和特点,并对四工位组合机床控制系统的硬件和软件进行了设计。最 后,通过实验验证了该控制系统的可靠性和有效性。
3.3输入输出接口
3.3输入输出接口
PLC作为控制系统的核心,需要与外围设备进行交互。因此,输入输出接口的 设计也至关重要。常见的输入接口包括按钮、开关和传感器信号接口;输出接口 则包括继电器、伺服电机等执行机构接口。这些接口通过相应的硬件和软件配置 实现与外围设备的连接与控制。
实际应用
实际应用
三、基于PLC的组合机床控制系 统设计
1、硬件设计
1、硬件设计
基于PLC的组合机床控制系统的硬件设计主要包括输入输出模块、中央处理单 元、通信接口等。输入模块主要接收操作面板、各个传感器等输入信号;输出模 块主要控制各个执行元件;中央处理单元是整个控制系统的核心,主要负责处理 输入信号,
1、硬件设计
一、组合机床的结构与工作原理
一、组合机床的结构与工作原理
组合机床主要由动力头、滑台、夹具、冷却系统、液压系统、电控制系统等 组成。其工作原理是利用动力头带动刀具进行切削,滑台负责带动工件进行移动, 夹具对工件进行定位和夹紧,液压系统提供动力,电控制系统控制整个加工过程 的运行。
二、PLC在组合机床中的应用
基本内容
2、灵活性:PLC可通过编程实现不同的控制逻辑,满足各种不同的生产需求。 3、易于维护:PLC具有自诊断功能,便于排查故障,维护简单。
四工位组合机床的plc控制系统设计 正文

正文第一章绪论一、组合机床概述组合机床是针对特定工件,进行特定加工而设计的一种高效率自动化专用加工设备,这类设备大多能多刀同时工作,并且具有自动循环的功能。
组合机床是随着机械工业的不断发展,由通用机床、专用机床发展起来的。
通用机床一般用一把刀具进行加工,自动化程度低、辅助时间长、生产效率低,但通用机床能够重新调整,以适应加工对象的变化。
专用机床可以实现的多刀切削,自动化程度较高,结构较简单,生产效率也较高。
但是,专用机床的设计,制造周期长,造价高,工作可靠性也较差。
专用机床是针对某工件的一定工序设计的,当产品进行改进,工件的结构,尺寸稍有变化时,它就不能继续使用。
在综合了通用机床、专用机床优点的基础上产生了组合机床。
组合机床通常由标准通用部件和加工专用部件组合构成,动力部件采用电动机驱动或采用液压系统驱动,由电气系统进行工作自动循环的控制,是典型的机电或机电液一体化的自动加工设备。
常见的组合机床,标准通用部件有动力滑台各种加工动力头以及回转工作台等,可用电动机驱动,也可用液压驱动。
各标准通用动力部件组合构成一台组合机床时,该机床的控制电路可由各动力部件的控制电路通过一定的连接电路组合构成。
多动力部件构成的组合机床,其控制通常有三方面的工作要求:第一方面是动力部件的点动和复位控制。
第二方面是动力部件的半自动循环控制。
第三方面是整批全自动工作循环控制。
组合机床具有生产率高、加工精度稳定的优点。
因而,在汽车、柴油机、电机、机床等一些具有一定生产批量的企业中得到了广泛应用。
目前,组合机床的研制正向高效、高精度、高自动化和柔和性化方向发展。
本文所用组合机床为四工位组合机床,该机床由四个滑台,各载一个加工动力头,组成四个加工工位,除了四个加工工位外,还有夹具,上下料机械手和进料器,四个辅助装置以及冷却和液压系统共14个部分。
机床的四个加工动力头同时对一个零件的四个端面以及中心孔进行加工,一次加工完成一个零件,由上料机械手自动上料,下料机械手自动取走加工完成的零件,零件每小时可加工80件。
组合机床的电气控制系统设计
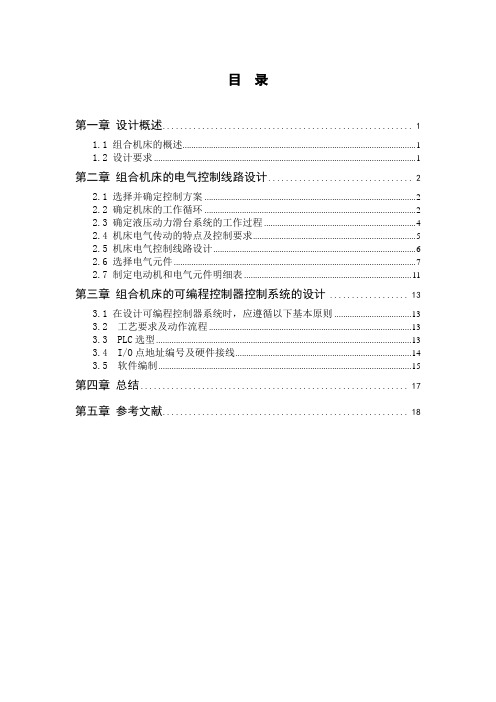
目录第一章设计概述 (1)1.1 组合机床的概述 (1)1.2 设计要求 (1)第二章组合机床的电气控制线路设计 (2)2.1 选择并确定控制方案 (2)2.2 确定机床的工作循环 (2)2.3 确定液压动力滑台系统的工作过程 (4)2.4 机床电气传动的特点及控制要求 (5)2.5 机床电气控制线路设计 (6)2.6 选择电气元件 (7)2.7 制定电动机和电气元件明细表 (11)第三章组合机床的可编程控制器控制系统的设计 (13)3.1 在设计可编程控制器系统时,应遵循以下基本原则 (13)3.2 工艺要求及动作流程 (13)3.3 PLC选型 (13)3.4 I/O点地址编号及硬件接线 (14)3.5 软件编制 (15)第四章总结 (17)第五章参考文献 (18)第一章设计概述1.1 组合机床的概述组合机床通常是采用多刀、多面、多工序、多工位同时加工,由通用部件和专用部件组成的工序集中的高效率专用机床。
它的电气控制线路是将各个部件组合成一个统一的循环系统。
在组合机床上可以完成钻孔、扩孔、铰孔、镗孔、攻螺纹、铣削及磨削等工序。
组合机床用于大批量生产。
组合机床的控制系统大多采用机械、液压或气动、电气相结合的控制方式。
其中,电气控制又起中枢连接的作用。
因此,应分析组合机床电气控制系统与机械、液压或气动部分的相互关系。
1.2 设计要求设计两面加工组合机床的电气控制线路及其可编程控制器的控制系统。
要求如下:1)能按照本组最终要求合理设计继电器电气原理图,PLC电气原理图,再做成控制板,最后连线试验。
2)要求上交1份设计说明书,2张图纸,测试结果。
第二章组合机床的电气控制线路设计2.1 选择并确定控制方案组合机床组成部件不是一成不变的,它将随着生产力的向前发展而不断更新,因此与相适应的电气控制线路也随着更新换代,目前主要有以下两种:1)机械动力滑台控制线路机械动力滑台和液压动力滑台都是完成进给运动的动力部件,两者区别仅在于进给的驱动方式不同。
- 1、下载文档前请自行甄别文档内容的完整性,平台不提供额外的编辑、内容补充、找答案等附加服务。
- 2、"仅部分预览"的文档,不可在线预览部分如存在完整性等问题,可反馈申请退款(可完整预览的文档不适用该条件!)。
- 3、如文档侵犯您的权益,请联系客服反馈,我们会尽快为您处理(人工客服工作时间:9:00-18:30)。
四工位组合机床的电气控制电路概述四工位组合机床的对某种特定工件进行特定加工的一种高效率、自动化的专用设备。
这种机床是具有自动工作循环并能实现自动调整的加工设备,它能够用十几把刀甚至几十把刀具同时进行加工。
本组合机床是由通用部件组合而成,其控制系统是采用电气、液压、机械组合的控制方式。
该组合机床由液压动力头和液压回转工作台两大部分组合而成,它用来加工一种轮毂工件上十二个孔所用的专用机床,立式动力头上装有36把刀具,其中12把钻头,12把扩钻头和12把铰刀。
加工位共有四个:第一是装卸工件;第二个是钻孔工序;第三个是扩孔工序;第四个是铰孔工序。
加工工位布置图见下图所示。
图2-22 四工位组合机床示意图 一工位(装卸)四工位(铰孔) 三工位(扩孔)二工位(钻孔)目录第一章设计思想和步骤1.1设计任务1.2设计条件1.3设计要求1.4设计思想及步骤第二章四工位的电路设计2.1主电路设计2.2变压器设计2.3控制电路设计第三章四工位机床的工作台电路设计3.1液压回转工作台的控制电路设计3.2液压动力头控制电路设计3.3指示灯电路设计3.4总电路设计第四章PLC电路设计4.1 PLC控制设计4.2电路元件选择4.3明细表第五章总结5.1参考文献5.2设计小结第一章设计思想和步骤1.1设计任务1.1设计任务1:根据条件与要求设计出KA-KM电路。
2:根据设计的KA-KM电路做一张J-C电路图。
3:根据KA-KM列出输入状态表。
4:根据KA-KM列出输出状态表。
5:根据KA-KM列出中间元件状态表。
6:根据KA-KM列出定时器状态表。
7:根据上表绘制梯形图。
8:根据梯形图编制程序。
9:作出现场接线图。
10:编写说明书。
1.2设计条件(一)组合机床的启动工作状态回转台抬起→回转抬回转→回转台反靠→回转台夹紧→动力头快进→动力头工进→延时停留→动力头快退。
(二)液压回转工作台回转控制状态液压回转工作台是靠控制液压系统的油路来实现工作台转位动作,而液压系统的动作循环是靠电气电路控制。
1:回转台的转台动作。
自锁销脱开及回转台抬起→回转台回转及缓冲→回转工作台反靠→回转工作台夹紧。
2:液压回转工作台控制电路采用低压直流信号控制。
(三)液压动力头控制状态动力头是既能完成进给运动,又能同时完成刀具切削与动的动力部件。
1:液压动力头的自动工作循环动力头快进→力头工进→延时停留→快速退回原位。
2:工作状态图四工位组合机床动力头的工作状态示意图如下图所示。
图2-24 动力头工作示意图3:动力头工作要求本组合机床有三个动力头,分别控制钻头、扩孔、铰孔工作,这三个动力头是同步实现。
钻孔、扩孔、铰孔的工艺分别是根据距离的不同由机械来保证,故在此我只作出一个动力头的电气控制原理图。
①动力头必须在回转工作台夹紧后才能移动。
②要求动力头能实现点动调整控制。
③要求动力头在任意时刻实现快退控制。
1.3设计要求①机床的主电路由三台三相交流异步电动机及、及其附属电气元件组成,由于各电动机容量不大,可采用直接起动控制。
②M1是主电动机,只需单方向起动,要求有短路及过载保护。
③M2是液压泵电动机,也只需单方向起动,要求有短路及过载保护。
④M3是冷却泵电动机,功率较小,单方向运转,要求有短路及过载保护。
⑤M1和M2可以同时起停,也可单独起停。
⑥要求在动力头工作时,M3才接通,但也可以随时调整。
⑦主电路供电电压为380V;控制电路电压为220V;直流控制电路电压24V,由桥式全波整流电路供给(整流之前为交流28V),指示灯电路为6.3V。
⑧要求各工作状态有指示灯显示,以便说明机床工作在什么状态。
⑨电路中设置必要的各种保护,联锁控制。
1.4设计思想及步骤由于四工位组合机床是由一些电气控制基本环节组成。
我们可以利用这些基本环节的组合机床进行设计,然后将各部分联系起来,再根据要求对整体电路进行分析,进行修正,直至达到控制要求,作出继电接触器原理图。
㈠电力拖动方案确定和电动机选择①机床的主电路由三台三相交流笼型异步电动机及其附属电气元件组成,由于电动机容量都不大,故可采用直接起动控制。
②根据生产机械的技术要求,选择电动机。
主轴电动机为立式、防护式、断续周期性工作制,额定电压为380V。
液压泵电动机为卧式、封闭式、连续工作制,额定电压为380V的交流异步电动机。
㈡继电-接触器控制系统设计方案确定①为满足生产机械的工艺要求,应充分了解工作性能、结构性能、运动情况、加工工艺及加工情况。
考虑控制方案时,采用必要的联锁与保护环节,保证生产工艺要求。
②为满足控制电路的电压值要求,采用降压变压器,二次电压为6.3V、28V、220V三种电压再经桥式全波整流为24V直流输出供给电磁阀电路。
③为保证控制电路工作的可靠性,对电器元件的联接要求需考虑,应尽量减少触点数和联接导线数,防止出现寄生电路。
各种指示灯与控制电路分开供电。
④为了保证操作人员、电器设备、生产机械设备的安全,并能有效地控制事故的扩大,在电器控制电路中,采取了一定的保护措施,有短路保护、过载保护、失电压、欠电压、零电压保护、联锁保护、限位保护、过电流保护等。
第二章四工位的电路设计2.1主电路设计1.设计要求①主轴电动机单方向起动,要求有过载及短路保护。
②液压泵电动机单方向起动,过载及短路保护。
③冷却泵电动机单向工作,过载及短路保护。
2.元件选用根据上面要求,要选用三台电动机:M1——控制主轴的电动机;M2——控制液压泵的电动机;M3——控制冷却泵的电动机。
再根据电动机的控制要求选择元件:QF——控制总电源的断路器,实现短路和过载保护;FU1~FU3——控制各电动机短路保护;KM1——控制主轴电动机单向工作;KM2——控制液压泵电动机工作;KM3——控制冷却泵电动机工作;FR1~FR3——用与各电动机的过载保护控制。
3.作出电路草图如下:图2-25 主电路冷却泵电动机液压泵电动机主轴电动机~~~2.2变压器设计1.设计条件:①主电路要求供电电压为交流380V。
②控制电路要求供电电压为交流220V。
③直流控制电路(电磁阀电路)供电为直流24V,由桥整电路供给。
④指示灯电路供电为交流6.3V。
2.元件选用TC——选用输出端的变压器,分别输出为220V、28V、6.3V;VC——桥式整流装置,输出24V。
3.作变压器草图如下:~~380~~6.3图2-26 变压器电路2.3控制电路设计1.设计要求主轴电动机M1和液压泵电动机M2可以同时起停,也可以单独起停。
要求在动力头工作进给时,冷却泵电动机M3才接通,但也可以随时调整。
2.元件选用KM1~KM3——控制M1~M3单向起动动作接触器;SB1——总停按钮;SB2、SB3——M1与M2起动按钮;SB4、SB5——M1与M2停止按钮;SB6——冷却泵电动机(M3)调整按钮;SB7——冷却泵电动机单独停止按钮;SA1——控制M1与M2的同时与单独起停开关;SA2—实现动力头工进时自动起动与手动调整的开关;FR1~FR3——M1~M3过载保护热继电器;SA3——照明开关;HL1——电源指示灯;EL——照明灯。
3.控制电路草图根据所选元件与工作要求画出控制电路图,如下图:图2-27 控制电路4.工作原理⑴主轴起动首先合QF→HL1灯亮,表示电源供电正常按下SB2→KM1(+)→KM1主闭→M1起动运转,拖动主轴旋转,KM1辅闭自锁。
⑵主轴停止按SB4(或SB1)→KM1(–)→KM1主复位→M1停止。
⑶液压泵起动按SB3→KM2(+)KM2主闭→M2起动,提供高压油,为液压系统工作准备,KM2辅闭自锁。
⑷液压泵停止按SB5→KM2(–)→RM2主复位→M2停止。
⑸主轴与液压泵同时工作首先将SA1打开向左位置按SB2→KM1(+)→KM1主闭→M1起动工作,同时KM2(+)→KM2主闭→M2同时起动工作。
⑹冷却泵手动控制首先将SA2打在M位置,然后按SB6→KM3(+)→M3起动,提供冷却液,KM3辅闭自锁。
停止冷却泵按SB7即可。
⑺冷却泵自动控制首先将SA2打在A位置,当动力头工作进给时KA2(+)→KA2常开闭合→KM3(+)→KM3主闭→M3自行起动工作,提供冷却液。
第三章四工位机床的工作台电路设计3.1液压回转工作台的控制电路设计1.设计要求①液压回转台是靠油路来实现工作台转位工作,液压系统的动作循环是靠电气电路控制。
②液压回转工作台上加工工位有四个,一装卸工件、二钻孔、三扩孔、四铰孔。
③回转台的转台动作→自锁销脱开→回转台抬起→回转台回转及缓冲→回转台反靠→回转工作台夹紧→向动力头发出工作信号。
④回转台转位必须动力头在原位时才能实现。
2.元件选用一般电磁阀均由中间继电器控制,实现对各种现场信号的传递转换及放大功能。
现选:KA4——回转台抬起KA5——回转台回转KA6——回转台反靠KA7——回转台夹紧KA8——动力头退回原位SA1——回转台手动、自动工作选择开关SA2——回转台回转按钮SA8——回转台回转按钮3.液压回转工作台电气控制电路图如下所示:图2-30 液压回转台电气控制电路4.工作原理本液压回转台可实现自动循环与调整的动能,由转换开关SA1实现,SA1打在M档,按动调整按钮SB8即可实现调整,若SA1打在A档,当动力头快退至原位,则回转工作台可自动回转。
当动力头退回原位,压下行程开关SQ1,同时由于回转台在原位SQ9被压合,KA8得电,使YV5得电,回转工作台抬起,自锁销脱开,压下SQ5,由于KA5处于失电状态,电磁阀YV7得电,回转工作台由于YV10不得电,离合器合着而回转,回转了一定角度压下SQ6,SQ6常开闭合,使KA4得电并自琐,由于KA7、KA6、SQ8均处于常态,YV9得电,回转台实现反靠,反靠后压合行程开关SQ7,因为KA4一直得电,回转台自动落下夹紧。
当回转台夹紧压力足够时,压力继电器KP合上,KA7得电,KA7常开闭合,YV10得电,离合器脱开,KA7常闭断开,YV9失电,离合器脱开后压下SQ8,电磁阀YV8得电,液压缸返回,为回转工作台下次工作做准备,同时由KA7常开触点发出向动力头工作信号,使动力头准备工作。
若SA1打在M档,按下SB8实现手动调整,控制回转工作台的工作,松开SB8,回转台则停止工作。
3.2液压动力头控制电路设计动力头是既能完成进给运动,又能同时完成刀具的切削运动。
现设计的四工位组合机床,有三个动力头,每个动力头上有12把刀,在回转台夹紧后要求从三个方面同时对工件进行钻、扩、绞功能,从而提高了生产效率。
1.设计要求①动力头必须在回转工作台夹紧后才能起动工作。
②要求动力头能实现点动调整控制。
③要求动力头在任意时刻实现快退控制。
④三个动力头同步工作,电路相同。
⑤液压动力头的工作示意图见图2-24。