SPC统计过程控制培训课件.pptx
合集下载
SPC统计过程控制培训教材(PPT 72页)

➢ 戴明博士对日本指导质量管理的成功,让美国 人惊醒原来日本工商经营成功的背后竟然有一 位美国人居功最大,故开始对戴明博士另眼看 待。1980年6月24日全国广播公司(NBC)在电视 播放举世闻名的“日本能为什么我们不能”(If Japan Can, Why Can‘t We?),使戴明博士一 夜成名。从此以后美国企业家重新研究戴明的 质量管理经营理念。
步骤8:运用控制限进行控制;
计数控制图和计点控制图
不良品率控制图(P图)
对产品不良品率进行监控时用的控制图 ;
质量特性良与不良,通常服从二项分 布; 当不良率P较小样本量n足够大时,该 分布趋向于正态分布
适用于全检零件或每个时期的检验样本 含量不同。
不良品率控制图(P图)
检验并记录数据 计算平均不合格品率P 计算中心线和控制界限 绘制控制图并进行分析
20世纪50年代以来,科学技术和工业生产的发展,对质量要求越来越高 ,要求人们运用“系统工程”的概念,把质量问题作为一个有机整体加以综 合分析研究,实施全员、全过程、全企业的管理。
SPC(统计过程控制)
--统计性的反馈系统
Statistical: (统计)以概率统计学为基础,用 科学的方法分析数据、得出结论; ——使用数据分析
标准正态分布函数:N(0,1)
小概率事件理解
1.例行检查身体 2.烟雾探测器
正态分布图与控制图
正态分布图与控制图
??那是不是说只有符合正态分布的特性(变量) 才可以用控制图呢?
休哈特实验
休哈特分别从矩形分布和三角分布的总体中,抽取n =4的样本,计算样本均值Xbar,经过多次实验后发 现,Xbar基本符合正态分布。
(William Edwards Deming)
步骤8:运用控制限进行控制;
计数控制图和计点控制图
不良品率控制图(P图)
对产品不良品率进行监控时用的控制图 ;
质量特性良与不良,通常服从二项分 布; 当不良率P较小样本量n足够大时,该 分布趋向于正态分布
适用于全检零件或每个时期的检验样本 含量不同。
不良品率控制图(P图)
检验并记录数据 计算平均不合格品率P 计算中心线和控制界限 绘制控制图并进行分析
20世纪50年代以来,科学技术和工业生产的发展,对质量要求越来越高 ,要求人们运用“系统工程”的概念,把质量问题作为一个有机整体加以综 合分析研究,实施全员、全过程、全企业的管理。
SPC(统计过程控制)
--统计性的反馈系统
Statistical: (统计)以概率统计学为基础,用 科学的方法分析数据、得出结论; ——使用数据分析
标准正态分布函数:N(0,1)
小概率事件理解
1.例行检查身体 2.烟雾探测器
正态分布图与控制图
正态分布图与控制图
??那是不是说只有符合正态分布的特性(变量) 才可以用控制图呢?
休哈特实验
休哈特分别从矩形分布和三角分布的总体中,抽取n =4的样本,计算样本均值Xbar,经过多次实验后发 现,Xbar基本符合正态分布。
(William Edwards Deming)
SPC统计过程控制教材ppt(37张)

– 5、确定各组的频数 – 6、作直方图 – 7、对直方图的观察: 特点, 中间高、两头低、左右对称
7
SPC
3、基础知识
(2)、正态分布 (Normal Distribution) 当抽取的数据个数趋于无穷大而区间宽度趋向于0时,外形轮廓的折线就趋向于光滑的曲
线,即:概率密度曲线。 特点:面积之和等于1。
11
SPC统计过程控制教材(PPT37页)
SPC
• (4)、使用控制图应考虑的问题
– a、控制图用于何处? – b、如何选择控制对象? – c、怎样选择控制图? – d、如何分析控制图? – e、点出界或违反其他准则的处理。 – f、控制图的重新制定。 – g、控制图的保管问题。
SPC统计过程控制教材(PPT37页)
– 1、找出最大值和最小值,确定数据分散宽度 数据分散宽度=(最大值 最小值)
– 2、确定组数 k n
– 3、确定组距 h=(最大值最小值)/组数
– 4、确定各组的边界 第一组的组下限=最小值 最小测量单位的一半 第一组的组上限=第一组的组下限+组距=第二组的组下限 第二组的组上限=第二组的组下限+组距=第三组的组下限,依此类推。
2
SPC
3、为什么要学习SPC(二)?
• 3控制方式与6控制方式的比较:
3
SPC
4、开展SPC工程的步骤
• 培训SPC
– 正态分布等统计基础知识 – 品管七工具:调查表、分层法、散布图、排列图、直方图、因果图、控制图 – 过程控制网图的做法 – 过程控制标准的做法
• 确定关键质量因素
– 对每道工序,用因果图进行分析,造出所有关键质量因素,再用排列图找出 最终产品影响最大的因素,即关键质量因素;
7
SPC
3、基础知识
(2)、正态分布 (Normal Distribution) 当抽取的数据个数趋于无穷大而区间宽度趋向于0时,外形轮廓的折线就趋向于光滑的曲
线,即:概率密度曲线。 特点:面积之和等于1。
11
SPC统计过程控制教材(PPT37页)
SPC
• (4)、使用控制图应考虑的问题
– a、控制图用于何处? – b、如何选择控制对象? – c、怎样选择控制图? – d、如何分析控制图? – e、点出界或违反其他准则的处理。 – f、控制图的重新制定。 – g、控制图的保管问题。
SPC统计过程控制教材(PPT37页)
– 1、找出最大值和最小值,确定数据分散宽度 数据分散宽度=(最大值 最小值)
– 2、确定组数 k n
– 3、确定组距 h=(最大值最小值)/组数
– 4、确定各组的边界 第一组的组下限=最小值 最小测量单位的一半 第一组的组上限=第一组的组下限+组距=第二组的组下限 第二组的组上限=第二组的组下限+组距=第三组的组下限,依此类推。
2
SPC
3、为什么要学习SPC(二)?
• 3控制方式与6控制方式的比较:
3
SPC
4、开展SPC工程的步骤
• 培训SPC
– 正态分布等统计基础知识 – 品管七工具:调查表、分层法、散布图、排列图、直方图、因果图、控制图 – 过程控制网图的做法 – 过程控制标准的做法
• 确定关键质量因素
– 对每道工序,用因果图进行分析,造出所有关键质量因素,再用排列图找出 最终产品影响最大的因素,即关键质量因素;
spc培训资料-SPC-统计过程控制(ppt 88页)

重复这三个阶段从而不断改进过程
控制图类型
X-R 均值和极差图
P chart 不合格品
计
计 率控制图
量 X-s均值和标准差图 数 nP chart 不合格品
型
型 数控制图
数 X -R 中位值极差图 数 C chart 缺点数控
据
据 制图
X-MR 单值移动极差 图
U chart 单位缺点 数控制图
控制图的选择方法
流等。(注:数据仅代表单一刀具、冲头、模具等 生产出来的零件,即一个单一的生产流。) 1-1-2 子组频率:在适当的时间内收集足够的数据,这样子组才能 反映潜在的变化,这些变化原因可能是换班/操作人 员更换/材料批次不同等原因引起。对正在生产的产 品进行监测的子组频率可以是每班2次,或一小时一 次等。
12 34 56
计量单位:(mm, kg等)
控制图举例
X图 R图
接上页
测量方法必须保证始终产生准确和精密的结果 不精密
不准确
••••••••
准确
•••••
• ••••
精密
•••••• •••••
使用控制图的准备
1、建立适合于实施的环境 a 排除阻碍人员公正的因素 b 提供相应的资源 c 管理者支持
范围 不受控
(存在特殊原因)
受控 (消除了特殊原因)
时间
过程能力
范围
受控且有能力符合规范 (普通原因造成的变差已减少) 规范下限
规范上限 时间
受控但没有能力符合规范 (普通原因造成的变差太大)
1、分析过程 本过程应做什么? 会出现什么错误? 本过程正在做什么? 达到统计控制状态? 确定能力
计划
措施
每件产品的尺寸与别的都不同
控制图类型
X-R 均值和极差图
P chart 不合格品
计
计 率控制图
量 X-s均值和标准差图 数 nP chart 不合格品
型
型 数控制图
数 X -R 中位值极差图 数 C chart 缺点数控
据
据 制图
X-MR 单值移动极差 图
U chart 单位缺点 数控制图
控制图的选择方法
流等。(注:数据仅代表单一刀具、冲头、模具等 生产出来的零件,即一个单一的生产流。) 1-1-2 子组频率:在适当的时间内收集足够的数据,这样子组才能 反映潜在的变化,这些变化原因可能是换班/操作人 员更换/材料批次不同等原因引起。对正在生产的产 品进行监测的子组频率可以是每班2次,或一小时一 次等。
12 34 56
计量单位:(mm, kg等)
控制图举例
X图 R图
接上页
测量方法必须保证始终产生准确和精密的结果 不精密
不准确
••••••••
准确
•••••
• ••••
精密
•••••• •••••
使用控制图的准备
1、建立适合于实施的环境 a 排除阻碍人员公正的因素 b 提供相应的资源 c 管理者支持
范围 不受控
(存在特殊原因)
受控 (消除了特殊原因)
时间
过程能力
范围
受控且有能力符合规范 (普通原因造成的变差已减少) 规范下限
规范上限 时间
受控但没有能力符合规范 (普通原因造成的变差太大)
1、分析过程 本过程应做什么? 会出现什么错误? 本过程正在做什么? 达到统计控制状态? 确定能力
计划
措施
每件产品的尺寸与别的都不同
统计过程控制SPC培训教材(PPT89页).pptx

(不可以容許的偏差→要排除)
16
如果制程中, 只有普通原因的變異存在, 則其成品將形成依各很穩定 的分佈,而且是可以預測的
如果制程中,
範圍 →
有特殊原因的變異存在,
則其成品將為不穩定的分佈, 而且是無法預測的
範圍 →
可預測
無法 預測
17
局部措施→改善特殊原因
特殊原因的变异
簡單的統計分 析可發現
如管制圖
直接負責制程的人 員去改善
局部措施改善 對策
牽涉到消除產生变异的特殊原因
可由製程人員直接加以改善
大約可以解決15%之制程上的問題
18
系統措施 → 改善普通原因
普通原因的变异
製程能力分 析可發現
如Ca,Cp, Cpk,及管制 圖上點的變化
管理當局參與及製 程人員合作去改善
系統改善對策
必須改善造成变异的普通原因 經常需要管理階層的努力與對策 大約可以解決85%之制程上的問題
(可以容許的偏差)
15
❖ 特殊原因(系统性,易识别,可以消除) :
指的是造成不是始终作用于过程的变差的原因,即当 它们出现时将造成(整个)过程的分布改变。除非所有 的特殊原因都被查找出来并且采取了措施,否則它们 将继续用不可预测的方式来影响过程的输出。如果系 统內存在变差的特殊原因,随时间的推移,过程的输 出将不稳定。
7
4.SPC 的焦點 → 制程 ( Process ) ❖ 品質變異的大小,也是決定產品優劣的關鍵
制程起伏條件 因
品質異常 果
因
產品優劣
果
8
三.SPC目的
❖ 对异常因素分类和控制,当制程有问题,立即 停止并找出原因,解决异常因素。
❖ 使制程稳定 ❖ 提高制程能力 ❖ 预防品质问题
16
如果制程中, 只有普通原因的變異存在, 則其成品將形成依各很穩定 的分佈,而且是可以預測的
如果制程中,
範圍 →
有特殊原因的變異存在,
則其成品將為不穩定的分佈, 而且是無法預測的
範圍 →
可預測
無法 預測
17
局部措施→改善特殊原因
特殊原因的变异
簡單的統計分 析可發現
如管制圖
直接負責制程的人 員去改善
局部措施改善 對策
牽涉到消除產生变异的特殊原因
可由製程人員直接加以改善
大約可以解決15%之制程上的問題
18
系統措施 → 改善普通原因
普通原因的变异
製程能力分 析可發現
如Ca,Cp, Cpk,及管制 圖上點的變化
管理當局參與及製 程人員合作去改善
系統改善對策
必須改善造成变异的普通原因 經常需要管理階層的努力與對策 大約可以解決85%之制程上的問題
(可以容許的偏差)
15
❖ 特殊原因(系统性,易识别,可以消除) :
指的是造成不是始终作用于过程的变差的原因,即当 它们出现时将造成(整个)过程的分布改变。除非所有 的特殊原因都被查找出来并且采取了措施,否則它们 将继续用不可预测的方式来影响过程的输出。如果系 统內存在变差的特殊原因,随时间的推移,过程的输 出将不稳定。
7
4.SPC 的焦點 → 制程 ( Process ) ❖ 品質變異的大小,也是決定產品優劣的關鍵
制程起伏條件 因
品質異常 果
因
產品優劣
果
8
三.SPC目的
❖ 对异常因素分类和控制,当制程有问题,立即 停止并找出原因,解决异常因素。
❖ 使制程稳定 ❖ 提高制程能力 ❖ 预防品质问题
SPC统计过程控制培训(PPT64页).pptx

4.1.1 正态分布曲线
f (x)
y
2
1
(
x
)
2
2
e ( x , 0)
2
---平均值
--- 标准差
4.1.2 正态分布的参数 、
4.1.3 正态分布的特点
• 曲线以 x = 直线为轴,左右对称 • 曲线与横坐标轴所围成的面积等于1
其中 在±范围内的面积占68.26 % 在±2范围内的面积占95.45 % 在±3范围内的面积占99.73 %
例:疵点数、沙眼数等
3、总体和样本(子组)
3.1 总体 研究对象的全体 总体含量记为 N
3.2 样本(子组) 总体中的部分样品 样本含量记为 n
4、常见的典型分布
4.1 正态分布 —— 计量值数据 4.2 二项分布 —— 计件值数据 4.3 泊松分布 —— 计点值数据
4.1 正态分布
X ~ N(, 2)
不同类型控制图的适用范围
适用范围
计 产品批量较大,稳定正常工序 量 产品批量较大,稳定正常工序 数 据 产品批量较大,稳定正常工序
每次只能得一个数据,见效快
计
样本含量可以不等
件 样本含量相等
计
样本含量相等
点 样本含量可以不等
用符号表示的控制图
X?R 图 均值极差图ቤተ መጻሕፍቲ ባይዱ
X桽 图 均值标准差图
X桽 图 中位数极差图
4 . 3 泊松分布: (常见于计点分布) 二项分布的极限分布 — P()
• 分布列
•P(均X值、x方)差和标x e准差 , (x 0,1,)
x!
均值: E(X)= ;
方差: V(X)= ;
标准差:
;
spc统计过程控制ppt课件
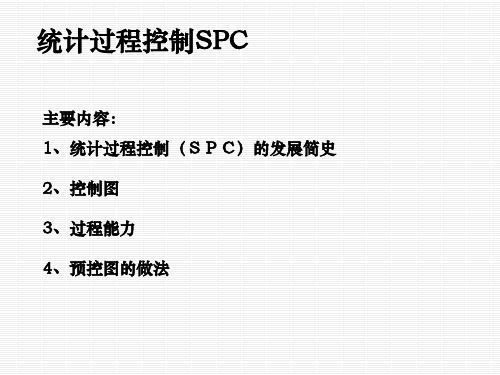
但是。。。被送进了医院。
波 动 ( 散 布 ) 大
平 均 发 生 偏 移
波 动 ( 散 布 ) 小
平 均 发 生 偏 移
Bad! Good!
波 动 ( 散 布 ) 大
平 均 没 有 偏 移
波 动 ( 散 布 ) 小
平 均 没 有 偏 移
假设我们的生产过程中其中一个工序是将金属材料切割成每个长度为 10mm的产品。当我们完成切割1000个产品后,测量每个产品的长度,
统计过程控制-SPC
常用的质量管理工具,包括直方图,鱼刺图,散布图,都是对 “昨天”情况的分析和解释,可以用在“救火”和解决问题,
但若想实现过程控制,则需要专门的预防工具-SPC。
统计过程控制SPC
统计过程控制(SPC)就是: 应用统计的方法,对生产/服务过程进行控制。 它能够区分产生变异的普通原因和特殊原因。 在生产过程中,对过程进行监控,当出现会产生异常情况的趋 势时进行预警,对过程进行适当的调整。
二、应用控制图的步骤
应用步骤如下:
1. 选择控制图拟控制的质量特性,如重量、不合格品数等;
2. 选用合适的控制图种类;
3. 确定样本容量和抽样间隔; 4. 收集并记录至少20~ 25组样本的数据,或使用以前所记录的数据; 5. 计算各个样本的统计量,如样本平均值、样本极差/样本标准差等; 6. 计算各统计量的控制界限; 7. 画控制图并标出各样本的统计量,
不合格品数 计 控制图
数 不合格品率 型 控制图
控 缺陷数控制 制图
图 单位缺陷数 控制图
控制图符号
x -R
特点
适用场合
最常用,判断工序是否正常的效 果好,但计算工作量很大。
适用于产品批量较大的工序。
波 动 ( 散 布 ) 大
平 均 发 生 偏 移
波 动 ( 散 布 ) 小
平 均 发 生 偏 移
Bad! Good!
波 动 ( 散 布 ) 大
平 均 没 有 偏 移
波 动 ( 散 布 ) 小
平 均 没 有 偏 移
假设我们的生产过程中其中一个工序是将金属材料切割成每个长度为 10mm的产品。当我们完成切割1000个产品后,测量每个产品的长度,
统计过程控制-SPC
常用的质量管理工具,包括直方图,鱼刺图,散布图,都是对 “昨天”情况的分析和解释,可以用在“救火”和解决问题,
但若想实现过程控制,则需要专门的预防工具-SPC。
统计过程控制SPC
统计过程控制(SPC)就是: 应用统计的方法,对生产/服务过程进行控制。 它能够区分产生变异的普通原因和特殊原因。 在生产过程中,对过程进行监控,当出现会产生异常情况的趋 势时进行预警,对过程进行适当的调整。
二、应用控制图的步骤
应用步骤如下:
1. 选择控制图拟控制的质量特性,如重量、不合格品数等;
2. 选用合适的控制图种类;
3. 确定样本容量和抽样间隔; 4. 收集并记录至少20~ 25组样本的数据,或使用以前所记录的数据; 5. 计算各个样本的统计量,如样本平均值、样本极差/样本标准差等; 6. 计算各统计量的控制界限; 7. 画控制图并标出各样本的统计量,
不合格品数 计 控制图
数 不合格品率 型 控制图
控 缺陷数控制 制图
图 单位缺陷数 控制图
控制图符号
x -R
特点
适用场合
最常用,判断工序是否正常的效 果好,但计算工作量很大。
适用于产品批量较大的工序。
SPC统计过程控制培训课程(PPT 87页)
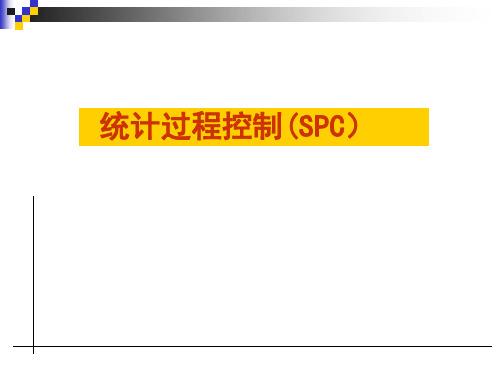
製程能力指標Ca
Ca
X
(T / 2)
(雙邊規格)
ˆ R
d2
製程能力指標C p
Cp
USL LSL
6ˆ
(雙邊規格)
Cp
USL
3ˆ
X
(單邊規格上規格界限)
Cp
X
LSL (單邊規格下規格界限)
3ˆ
ˆ R
d2 只考慮到固定變差或組內變差
製程能力指標C pk
C pk min(C pu , C pl )
C1分析极差图上的数据点
超出控制限的 点
C2识別并标注特殊原因(极差图链)
明显的非随机
C3重新计算控制界限(极差图)超图出形控制限的点
C4分析均值图上的数据点 链
明显的非随机图形 C5识別并标注特殊原因(均值图)
C6重新计算控制界限(均值图)
C7为了继续进行控制延长控制限
控制图的判读
超出控制界限的点:出现一个或多个点超出任何 一个控制界限是该点处于失控状态的主要证据
作控制图的目的是为了使生产过程或工作过程 处于“控制状态”. 控制状态即稳定状态, 指 生产过程或工作过程仅受偶然因素的影响, 产 产品质量特性的分布基本上不随时间而变化的 状态. 反之, 则为非控制状态或异常状态.
控制状态的标准可归纳为二條:
第一條, 控制图上点不超过控制界限; 第二條, 控制图上点的排列分布沒有缺陷.
产品的质量特性有时不止一个, 则应同时采 取几个特性作为控制項目.
使用控制图的注意事項
分组问题
主要是使在大致相同的条件下所收集的质量 特性值分在一组, 组中不应有不同本质的数 据, 以保证组内仅有偶然因素的影响.
我们所使用的控制图是以影响过程的许多变 动因素中的偶然因素所造成的波动为基准来 找出异常因素的, 因此, 必须先找出过程中 偶然因素波动这个基准.
SPC 统计过程控制培训课件(PPT 48页)

14
指数分类
SQE Training
1、Cp:分布中心无偏离规格中心时衡量 过程能力的指数;
2、Cpk: 分布中心偏离规格中心时衡量 过程能力的指数;
3、Cpm:目标值与规格中心不一致时衡量 过程能力的指数;
4、Cpu:上单侧过程能力指数; 5、Cpl: 下单侧过程能力指数。
15
SQE Training
过程能力决定于质量因素:人、机、料、法、环, 而与公差无关。过程能力是过程的固有属性。
8
SQE Training
进行过程能力分析的意义
一、保证产品质量的基础工作; 二、提高过程能力的有效手段; 三、找出产品质量改进的方向; 四、向客户证明加工过程的能力。
9
指数分类
SQE Training
Cp,Cpk,Cpm Pp,Ppk,Ppm
5
SQE Training
影 ☆ 人、机、料、法、测、环
响 (5M1E)
过 操作者方面:如操作者的技术水平、熟练 程 程度、质量意识、责任心、管理程度等;
能 设备方面:如设备精度的稳定性,性能
力
的可靠性,定位装置和传动装置的准 确性,设备的冷却、润滑情况等等;
的 材料方面:如材料的成分,配套元器件
指数分类
二、过程性能指数(Process Performance Index) 1、Pp: 分布中心无偏离规格中心时衡量
过程能力的指数; 2、Ppk: 分布中心偏离规格中心时衡量
过程能力的指数; 3、Ppm:目标值与规格中心不一致时衡量
过程能力的指数; 4、Ppu:上单侧过程能力指数; 5、Ppl: 下单侧过程能力指数。
因 的质量等等;
素
6
SQE Training
指数分类
SQE Training
1、Cp:分布中心无偏离规格中心时衡量 过程能力的指数;
2、Cpk: 分布中心偏离规格中心时衡量 过程能力的指数;
3、Cpm:目标值与规格中心不一致时衡量 过程能力的指数;
4、Cpu:上单侧过程能力指数; 5、Cpl: 下单侧过程能力指数。
15
SQE Training
过程能力决定于质量因素:人、机、料、法、环, 而与公差无关。过程能力是过程的固有属性。
8
SQE Training
进行过程能力分析的意义
一、保证产品质量的基础工作; 二、提高过程能力的有效手段; 三、找出产品质量改进的方向; 四、向客户证明加工过程的能力。
9
指数分类
SQE Training
Cp,Cpk,Cpm Pp,Ppk,Ppm
5
SQE Training
影 ☆ 人、机、料、法、测、环
响 (5M1E)
过 操作者方面:如操作者的技术水平、熟练 程 程度、质量意识、责任心、管理程度等;
能 设备方面:如设备精度的稳定性,性能
力
的可靠性,定位装置和传动装置的准 确性,设备的冷却、润滑情况等等;
的 材料方面:如材料的成分,配套元器件
指数分类
二、过程性能指数(Process Performance Index) 1、Pp: 分布中心无偏离规格中心时衡量
过程能力的指数; 2、Ppk: 分布中心偏离规格中心时衡量
过程能力的指数; 3、Ppm:目标值与规格中心不一致时衡量
过程能力的指数; 4、Ppu:上单侧过程能力指数; 5、Ppl: 下单侧过程能力指数。
因 的质量等等;
素
6
SQE Training
- 1、下载文档前请自行甄别文档内容的完整性,平台不提供额外的编辑、内容补充、找答案等附加服务。
- 2、"仅部分预览"的文档,不可在线预览部分如存在完整性等问题,可反馈申请退款(可完整预览的文档不适用该条件!)。
- 3、如文档侵犯您的权益,请联系客服反馈,我们会尽快为您处理(人工客服工作时间:9:00-18:30)。
操作规程
融
环境(供电电压、温度、湿度、振动……) 合
轴外圆 尺寸
表面粗糙度
顾客
过程示例——用普通机床生产一种轴的外圆
1.2.1 过程特性
• 特性:定量、定性 可区分的特征
按重要程度分:关键、一般
按状态分:产品、过程
如何定义关键质量特性呢?
6
1.3 基本统计概念
统计学(Statistics)
为了了解被检验总体的某些隐含的特性,运用合理的抽样方法 从被调整总体中取得适当的样本,通过研究样本来发现总体的特 征
• 如设备的正常震动,刀具的磨损,同一批材料的品质差异, 熟练工人间的替换;
•
• 特殊原因:指的是造成不是始终作用于过程的变差的 原因,即当它们出现时将造成(整个)过程的分布改变。除 非所有的特殊原因都被查找出来并且采取了措施,否則它 们将继续用不可预测的方式来影响过程的输出。如果系统 內存在变差的特殊原因,随时间的推移,过程的输出将不 稳定。
• 异常波动:是由特殊(异常)原因造成的。如原 材料不合格,设备出现故障,工夹具不良,操作 者不熟练等。异常波动引起工序质量变化较大, 容易发现,应该由操作人员发现并纠正。
1.3.3、基本统计量说明
• 1、平均值 X 设X1,X2,…….Xn是一个大小为n的样本,
则X=(X1+X2+……+Xn)/n 2、中位数~ X
s
N
( X i X )2
i 1
N
n
( X i X )2
i 1
n 1
总结: 通过收集、计算、分析和改进数据的
手段,从而了解制造、服务等过程其最 佳范围(低成本、低风险),并确定其 控制范围的异常和正常规律,达成一种 事先预测并实施改进措施的方法。
17
SPC的发展
– 过程控制的概念与实施过程监控的方法早在20世纪20年代 就由美国的休哈特(W.A.Shewhart)提出。
1.3.1 数据的种类
• 计量型 特点:可以连续取值
也称连续型数据。
如:零件的尺寸、强 度、重量、时间、 温度等
• 计数型
特点:不可以连续取 值,也称离散型数 据。
如:废品的件数、缺 陷数
1.3.2 波动(变差)的概念:
波动的概念是指在现实生活中没有两件东西是完 全一样的。生产实践证明,无论用多么精密的设备 和工具,多么高超的操作技术,甚至由同一操作工 ,在同一设备上,用相同的工具,生产相同材料的 同种产品,其加工后的质量特性(如:重量、尺寸 等)总是有差异,这种差异称为波动。公差制度实 际上就是对这个事实的客观承认。消除波动不是 SPC的目的,但通过SPC可以对波动进行预测和控 制。
(1)、波动的原因:
材料
机器
人
环境
测量
方法
波动原因
(2)、普通原因、特殊原因
• 普通原因:指的是造成随着时间推移具有稳定的且可重 复的分布过程中的许多变差的原因,我们称之为:“处于 统计控制状态”、“受统计控制”,或有时间称“受控”, 普通原因表现为一个稳定系統的偶然原因。只有变差的普 通原因存在且不改变时,过程的输出才可以预测。
• 收集、整理、展示、分析解释统计资料
• 由样本(sample)推论母体群体(population)
• 能在不确定情况下作决策
• 是一门科学方法、决策工具
x 推论
抽样ቤተ መጻሕፍቲ ባይዱ
7
基本的统计概念
• 数据的种类
计量型 计数型
• 波动(变差)——波动的概念、原理及波动的种类
• 普通原因/异常原因
• 基础的统计量——平均值X、中位数~ X、极差R 标准偏差 s 、
– 美国从20世纪80年代起开始推行SPC。美国汽车工业已大 规模推行了SPC,如福特汽车公司,通用汽车公司,克莱斯 勒汽车公司等美国钢铁工业也大力推行了SPC,如美国LTV 钢铁公司,内陆钢铁公司,伯利恒钢铁公司等等。
备注: SPC是全系统的,全过程的,要求全员参加,人人有责。这点与全面质 量管理的精神完全一致。
3
1.2 过程
过程:将输入转化为输出的相互关联和相互作用的 活动。
过程的声音
人 机 料 法 环 测
统计方法 过程 顾客的声音
产品
客户
机床(主轴承间隙、刀具……)
资
操作工(进给率、对中准确度……)
源
原材料(棒料尺寸、硬度……)
将数据按数值大小顺序排列后,位于中间 位置的书,称为中位数。 如:5,9,10,4,7, ~X=7; 如:5,9,10,4,7,8 ~X=(7+8)/2=7.5
• 3、极差R 样本数据中的最大值Xmax与最小值
Xmin的差值。R= Xmax- Xmin • 4、标准偏差s 、 (1)总体标准偏差 (2)样本的标准偏差
Statistical Process Control
(统计过程控制)
李明
1
统计过程控制(SPC)
1、SPC的发展史与基本统计概念 2、SPC的基本原理 3、控制图 4、过程能力和过程能力指数
2
1.1 什么是SPC
什么是SPC – 统计过程控制即SPC(statistical process control).它是利用统计方法对过程中的各个 阶段进行监控,从而达到改进与保证质量的目 的.SPC强调全过程的预防为主。 – SPC不仅用于生产过程,而且可用于服务过程 和一切管理过程.
• 如设备故障,原材料不合格,没有资格的操作工、未按照 作业指导书操作、工艺参数设定不对……
普通原因和特殊原因的区别
存在性 方向
影响大小 消除的难 易度
普通原因 始终
偏向
小
难
特殊原因 有时
或大或小 大
易
(3)、波动的种类:
• 正常波动:是由普通(偶然)原因造成的。如操 作方法的微小变动,机床的微小振动,刀具的正 常磨损,夹具的微小松动,材质上的微量差异等。 正常波动引起工序质量微小变化,难以查明或难 以消除。它不能被操作工人控制,只能由技术、 管理人员控制在公差范围内。
– 在第二次世界大战后期,美国开始将休哈特方法在军工部 门推行.但是上述统计过程按制方法尚未在美国工业牢固扎 根。
– 反之,战后经济遭受严重破坏的日本在1950年通过体哈特 早期的一个同事戴明(W.Edwards Deming)博士,将SPC 的概念引入日本.从1950年至1980,经过三十年的努力, 日本跃居世界质量与生产率方面的领先地位。美国著名质量 管理专家伯格(Roger W.Bergcr)教授指出,日本成功的基 石之一就是SPC。