统计过程控制培训ppt
合集下载
统计过程控制SPC培训讲座(PPT共 50张)
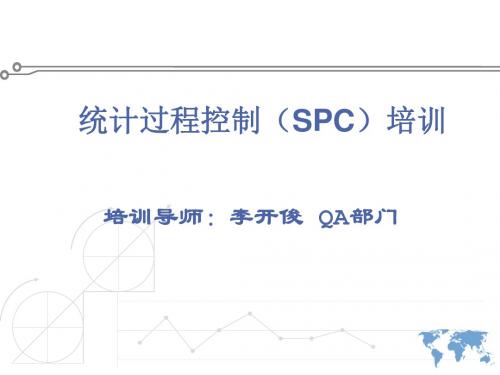
SPC控制图的好处
A. 对工程部门和品质部门来说,SPC可将每一 工序的关键性的参数有系统地记录下来,并研究和 分析其走势、变异,从而预防或补救工序所产生的 问题。 B. 对生产部门来说,用SPC来控制生产工序, 可达到稳定的生产率,减少在品质控制(Q.C.)检查 时,因拒收所做之返检、重做、修理等弊病。 C. 生产工序中之直接生产员工或管理人员,若 能够与工程部及品质部等SPC组员多沟通,可加速 新人对工序的了解,从而提升生产技术,培育员工 的归属感。
3.04 2.25 2.93 4.6 3.07 2.8 2.7 3.67 3.67 2.82 上面5个读数的平均 2.2 2.67 5.75 2.75 2.71 数. 2.56 2.9 4.4 3.14 5.11 3.6 2.5 4 3.07 4.18 / / / / / 2.84 2.604 4.15 3.446 3.578 1.4 0.65 2.82 1.85 此点出现上面各种测试中的任何一 2.4 3 4 5 6 个时,在此点作标示“ 7 x"。并在背 20:15 21:20 21:30 22:30 3:45 面改善行动中进行记录。 李 李 李 李 李
常规控制图
计量管制图:用在可量度的特性,例如:线宽,板厚, 铜厚,距离,浓度,速率等。
X - R Chart (均值与极差管制图) X- MR Chart (单值和移动极差管制图)
计数管制图:用在不可量度的特性(好-坏,是-不是, 通过-不通过,接受-拒收等),如不良率,合格率,缺 陷数,单位不合格数。
Xbar-R Chart • 子组大小的选择
• 子组大小选择的原则:合理的选择子组大小,选择应使得一个子组内中各样 本之间出现变差的机会小。 如果一个子组内的变差代表很短时间内的零件间的变差,则在子组之间出现不 正常的变差则表明过程发生变化,应进行调查并采取适当的措施。 子组一般由4到5件连续生产的产品的组合,这样做的目的是每个子组内的产品
2024版SPC培训教材全课件
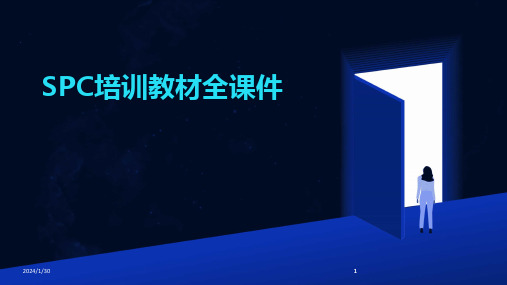
假设检验的基本概念
明确假设检验的定义、原假设与备择假设的设立原则及两类错误 的含义。
参数假设检验
掌握正态总体均值、方差的假设检验方法及步骤,理解t检验和F 检验的原理及应用场景。
非参数假设检验
了解非参数假设检验的适用条件及常用方法,如秩和检验、符号 检验等。
16
方差分析、回归分析应用举例
方差分析
掌握方差分析的基本原理、计算步骤及结果解释,理解其在多因素实验设计中的应用。
化。
大数据在SPC中的应用
大数据技术的不断发展将为SPC提供更丰富的数据来源和分析手段,有助于提高SPC的 应用效果。
2024/1/30
SPC在服务业的拓展
随着服务业的不断发展,SPC的应用领域将逐渐拓展到服务业领域,为服务业的质量管 理提供新的思路和方法。
36
下一讲预告及预备知识
2024/1/30
01
02
03
04
明确数据收集目标
根据业务需求,明确所需数据 的类型、范围和质量要求。
2024/1/30
制定数据收集计划
设计合理的数据收集流程,包 括数据源选择、采集频率、存
储方式等。
执行数据收集
运用合适的数据收集工具和技 术,按照计划进行数据采集。
数据质量监控
建立数据质量评估机制,确保 数据的准确性、完整性和一致
下一讲内容
下一讲将介绍SPC在企业中的实际应 用案例,包括不同行业和不同场景下 的SPC应用实践。
预备知识
为了更好地理解下一讲内容,建议学 员提前了解相关行业的生产流程和质 量管理要求,以及SPC在实际应用中 的挑战和解决方案。
37
THANKS
感谢观看
2024/1/30
统计过程控制(SPC)(PPT58页)
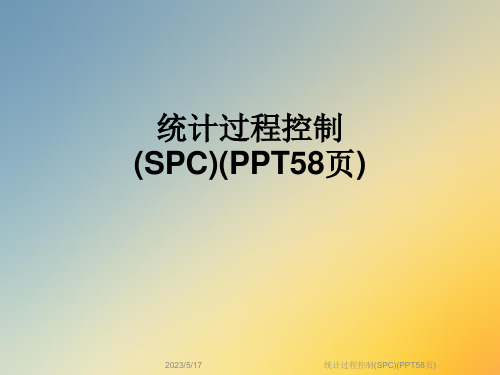
➢ 普通原因 ➢ 特殊原因
江铃汽车股份有限公司
统计过程控制(SPC)(PPT58页)
普通原因 普通原因造成变差的一个原因,它影响被研究过程的所
有单值。(处于统计控制状态;在统计上受控;受控) 造成随着时间的推移具有稳定的且可重复的分布过程中
的许多变差的原因 特点
过程分布将不发生变化 过程的输出是可预测的 过程是稳定、可控的。 采取系统的措施,由管理人员解决问题
江铃汽车股份有限公司
统计过程控制(SPC)(PPT58页)
2.3局部措施和系统措施
措施 对比
对象
系统措施
通常用来消除变差的普 通原因
局部措施
通常用来消除变 差的特殊原因
实施人员
几乎总是要求管理措施, 以便纠正
通常由与过程直 接相关的人员实 施
效果
大约可纠正85%的过程 问题
通常可纠正大约 15%的过程问题
一个可接受的过程必须是处于受控统计控制 状态的且其固有变差(能力)必须小于图纸 的公差
应通过检查并消除变差的特殊原因使过程处 于受统计控制状态,那么性能是可预测的, 变可评定其满足顾客期望的能力。这是持续 改进的基础
江铃汽车股份有限公司
统计过程控制(SPC)(PPT58页)
3.4过程改进循环
2.1过程的理解及过程控制
1.过程—所谓过程是指共同作用以产出输出的供方、生产 者、人、设备、输入材料、方法和环境及使用输出的顾 客的集合。
过程性能取决于:
供方与顾客之间的沟通
过程设计及实施的方式
运作和管理的方式
2.过程的信息
通过分析过程输出可以获得许多与过程性能有关的信息。如过程 是否稳定,过程能力如何。
4.1控制图应用说明
江铃汽车股份有限公司
统计过程控制(SPC)(PPT58页)
普通原因 普通原因造成变差的一个原因,它影响被研究过程的所
有单值。(处于统计控制状态;在统计上受控;受控) 造成随着时间的推移具有稳定的且可重复的分布过程中
的许多变差的原因 特点
过程分布将不发生变化 过程的输出是可预测的 过程是稳定、可控的。 采取系统的措施,由管理人员解决问题
江铃汽车股份有限公司
统计过程控制(SPC)(PPT58页)
2.3局部措施和系统措施
措施 对比
对象
系统措施
通常用来消除变差的普 通原因
局部措施
通常用来消除变 差的特殊原因
实施人员
几乎总是要求管理措施, 以便纠正
通常由与过程直 接相关的人员实 施
效果
大约可纠正85%的过程 问题
通常可纠正大约 15%的过程问题
一个可接受的过程必须是处于受控统计控制 状态的且其固有变差(能力)必须小于图纸 的公差
应通过检查并消除变差的特殊原因使过程处 于受统计控制状态,那么性能是可预测的, 变可评定其满足顾客期望的能力。这是持续 改进的基础
江铃汽车股份有限公司
统计过程控制(SPC)(PPT58页)
3.4过程改进循环
2.1过程的理解及过程控制
1.过程—所谓过程是指共同作用以产出输出的供方、生产 者、人、设备、输入材料、方法和环境及使用输出的顾 客的集合。
过程性能取决于:
供方与顾客之间的沟通
过程设计及实施的方式
运作和管理的方式
2.过程的信息
通过分析过程输出可以获得许多与过程性能有关的信息。如过程 是否稳定,过程能力如何。
4.1控制图应用说明
SPC统计过程控制173页PPT培训教材
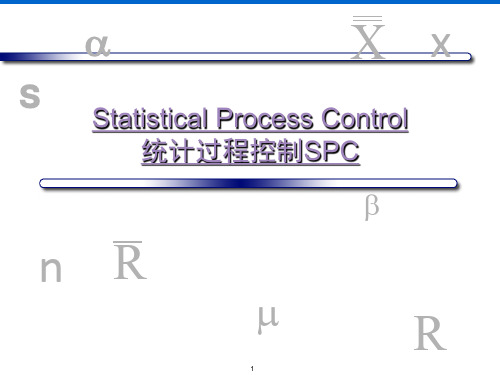
管理层授权并支持问题调 查和过程改进
当图表有异常信号时, 通 过根本原因分析采取正确 的行动以预防问题的再次 发生
YES
NO NO NO NO
15
YES
YES NO NO NO
YES
YES YES YES YES
为什么我们会关注统计控制?
第一个原因是福特PFMEA流程中要求需要对CC, SC和过程HIC采取 特殊控制, SPC就是其中的一种.
24
控制过程变差 无法控制的
随机的, 不可预知的变差, 影响到每个零件
例如: 普通原因
减少变差需要过程或系统的改变
25
控制过程变差 可控制的
变差是随时间而定的 可以被测量或补偿, 是可预知的 变差的减少通过作业水平的补偿就可以
26
数据类型
计数型
不通过
通过
失败
通过
电子的线路
27
计量型
卡尺
时间
温度
过程是统计受控的 过程是可预测的
稳定的过程状态
22
两种过程状态:普通原因和特殊原因
存在变差的特殊原因
分布不稳定,偏离典型分布
过程是不受控的
如果存在特殊原因,过程输 出随时间将不稳定,同时也 不可预测。
过程是不可预测的 控制图可检出
不稳定的过程状态
23
变差的普通原因和特殊原因
休哈特的贡献就在于发现了:虽然产生变差的来 源包括人、机、料、法、环等各种原因,但可分 为普通原因及特殊原因,后者(特殊原因)在控制 图上有信号,因此,可用来对过程进行控制。
5
引言
当过程超出控制 (Out-of-Control) 或生产了问题零 件的时候应该怎么办?
如何运用平均运行长度 (ARL-Average Run Length) 即 基于变量数据的围堵策略, 包括怎样识别损失函数. 如何采取永久的系统性的纠正措施用于预防问题永远 不再发生.
当图表有异常信号时, 通 过根本原因分析采取正确 的行动以预防问题的再次 发生
YES
NO NO NO NO
15
YES
YES NO NO NO
YES
YES YES YES YES
为什么我们会关注统计控制?
第一个原因是福特PFMEA流程中要求需要对CC, SC和过程HIC采取 特殊控制, SPC就是其中的一种.
24
控制过程变差 无法控制的
随机的, 不可预知的变差, 影响到每个零件
例如: 普通原因
减少变差需要过程或系统的改变
25
控制过程变差 可控制的
变差是随时间而定的 可以被测量或补偿, 是可预知的 变差的减少通过作业水平的补偿就可以
26
数据类型
计数型
不通过
通过
失败
通过
电子的线路
27
计量型
卡尺
时间
温度
过程是统计受控的 过程是可预测的
稳定的过程状态
22
两种过程状态:普通原因和特殊原因
存在变差的特殊原因
分布不稳定,偏离典型分布
过程是不受控的
如果存在特殊原因,过程输 出随时间将不稳定,同时也 不可预测。
过程是不可预测的 控制图可检出
不稳定的过程状态
23
变差的普通原因和特殊原因
休哈特的贡献就在于发现了:虽然产生变差的来 源包括人、机、料、法、环等各种原因,但可分 为普通原因及特殊原因,后者(特殊原因)在控制 图上有信号,因此,可用来对过程进行控制。
5
引言
当过程超出控制 (Out-of-Control) 或生产了问题零 件的时候应该怎么办?
如何运用平均运行长度 (ARL-Average Run Length) 即 基于变量数据的围堵策略, 包括怎样识别损失函数. 如何采取永久的系统性的纠正措施用于预防问题永远 不再发生.
SPC统计过程控制培训课件PPT(48张)

音干扰、振动、照明、室内净化、现场
因 污染程度等等。
素
7
过程能力
SQE Training
过程能力(process capability)以往称为工序能力
过程能力是指工序处于控制状态下的实际加工能 力。---素充分标准化,处于稳定状态 下,工序所表现出来的保证工序质量的能力。
14
指数分类
SQE Training
1、Cp:分布中心无偏离规格中心时衡量 过程能力的指数;
2、Cpk: 分布中心偏离规格中心时衡量 过程能力的指数;
3、Cpm:目标值与规格中心不一致时衡量 过程能力的指数;
4、Cpu:上单侧过程能力指数; 5、Cpl: 下单侧过程能力指数。
15
SQE Training
过程能力决定于质量因素:人、机、料、法、环, 而与公差无关。过程能力是过程的固有属性。
8
SQE Training
进行过程能力分析的意义
一、保证产品质量的基础工作; 二、提高过程能力的有效手段; 三、找出产品质量改进的方向; 四、向客户证明加工过程的能力。
9
指数分类
SQE Training
Cp,Cpk,Cpm Pp,Ppk,Ppm
Ppk修正的过程性能指数 Ppk:“我们实际真正做到多好”
13
SQE Training
Cp,Cpk与Pp,Ppk的应用时机
短期过程能力指数
长期过程能力指数
Cp,Cpk,Cpm
Pp,Ppk,Ppm
新产品试作阶段; 初期生产阶段; 工程变更或设备变更时; 用于初始过程能力研究;
• 量产阶段; • 用于过程能力研究;
SQE Training
Statistical
因 污染程度等等。
素
7
过程能力
SQE Training
过程能力(process capability)以往称为工序能力
过程能力是指工序处于控制状态下的实际加工能 力。---素充分标准化,处于稳定状态 下,工序所表现出来的保证工序质量的能力。
14
指数分类
SQE Training
1、Cp:分布中心无偏离规格中心时衡量 过程能力的指数;
2、Cpk: 分布中心偏离规格中心时衡量 过程能力的指数;
3、Cpm:目标值与规格中心不一致时衡量 过程能力的指数;
4、Cpu:上单侧过程能力指数; 5、Cpl: 下单侧过程能力指数。
15
SQE Training
过程能力决定于质量因素:人、机、料、法、环, 而与公差无关。过程能力是过程的固有属性。
8
SQE Training
进行过程能力分析的意义
一、保证产品质量的基础工作; 二、提高过程能力的有效手段; 三、找出产品质量改进的方向; 四、向客户证明加工过程的能力。
9
指数分类
SQE Training
Cp,Cpk,Cpm Pp,Ppk,Ppm
Ppk修正的过程性能指数 Ppk:“我们实际真正做到多好”
13
SQE Training
Cp,Cpk与Pp,Ppk的应用时机
短期过程能力指数
长期过程能力指数
Cp,Cpk,Cpm
Pp,Ppk,Ppm
新产品试作阶段; 初期生产阶段; 工程变更或设备变更时; 用于初始过程能力研究;
• 量产阶段; • 用于过程能力研究;
SQE Training
Statistical
统计过程控制培训讲义(PPT 67页)
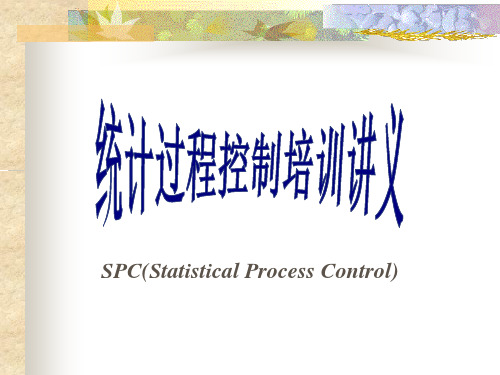
SPC(Statistical Process Control)
持续改进及过程控制 • 企业目标-客户满意 • 实现目标-持续改进,强调缺陷的预防 • 有效方法-统计过程控制
检验和预防 • 检验是对过程结束后的输出进行测量 – 通过抽样检验--发现合格/不合格 – 通过100%检验--发现合格/不合格 • 预防是在生产中对过程进行测量 – 通过对过程的测量,使质量问题在导致报废、返
计数型数值和计量型数值
特殊原因
普通原因
一种间断性的,不可预 造成变差的一个原因,
计的,不稳定的变差来
它影响被研究过程输
源。有时被称为可查明
出的所有单值;在控
原因,存在它的信号是: 制图分析中,它表现
存在超过控制线的点或
为随机过程变差的一
存在在控制线之内的链
部分。
或其他非随机性的情形。
局部措施和对系统采取措施
1-4、选择控制图的刻度 4-1 两个控制图的纵坐标分别用于 X 和 R 的测量值。 4-2 刻度选择 :
接上页
对于X 图,坐标上的刻度值的最大值与最小值的差应至少为子组均值 (X)的最大值与最小值的差的2倍,对于R图坐标上的刻度值的最大值 与最小值的差应为初始阶段所遇到的最大极差(R)的2倍。 注:一个有用的建议是将 R 图的刻度值设置为 X 图刻度值的2倍。
等过程调整到稳态后,延长控制图的控制线作为控 制用控制图。应用过程参数判断
控制图类型
X-R 均值和极差图 计量 型数 X-δ均值和标准差图 据
X -R 中位值极差图
X-MR 单值移动极差图
计数 型数 据
P chart 不合格品率控制图 nP chart不合格品数控制图 C chart 缺陷数控制图
持续改进及过程控制 • 企业目标-客户满意 • 实现目标-持续改进,强调缺陷的预防 • 有效方法-统计过程控制
检验和预防 • 检验是对过程结束后的输出进行测量 – 通过抽样检验--发现合格/不合格 – 通过100%检验--发现合格/不合格 • 预防是在生产中对过程进行测量 – 通过对过程的测量,使质量问题在导致报废、返
计数型数值和计量型数值
特殊原因
普通原因
一种间断性的,不可预 造成变差的一个原因,
计的,不稳定的变差来
它影响被研究过程输
源。有时被称为可查明
出的所有单值;在控
原因,存在它的信号是: 制图分析中,它表现
存在超过控制线的点或
为随机过程变差的一
存在在控制线之内的链
部分。
或其他非随机性的情形。
局部措施和对系统采取措施
1-4、选择控制图的刻度 4-1 两个控制图的纵坐标分别用于 X 和 R 的测量值。 4-2 刻度选择 :
接上页
对于X 图,坐标上的刻度值的最大值与最小值的差应至少为子组均值 (X)的最大值与最小值的差的2倍,对于R图坐标上的刻度值的最大值 与最小值的差应为初始阶段所遇到的最大极差(R)的2倍。 注:一个有用的建议是将 R 图的刻度值设置为 X 图刻度值的2倍。
等过程调整到稳态后,延长控制图的控制线作为控 制用控制图。应用过程参数判断
控制图类型
X-R 均值和极差图 计量 型数 X-δ均值和标准差图 据
X -R 中位值极差图
X-MR 单值移动极差图
计数 型数 据
P chart 不合格品率控制图 nP chart不合格品数控制图 C chart 缺陷数控制图
统计过程控制培训教材(PPT 38张)

控制图原理
2、基本原理
质量波动理论
“人、机、料、法、环” + “软(件)、辅(助材料)、公用系统
质量波动因素 = 偶然因素 +异常因素
偶然因素:过程固有、始终存在、影响微小、难以除去 异常因素:并非固有、时有时无、影响较大、不难去除
小概率原理
小概率事件在一次试验中几乎不可能发生、若发生则判断异常。 超出UCL为千分之一。
12
13 14 15 16 17 18 19 20
100
100 100 100 100 100 100 100 100
6
8 5 2 3 6 2 7 5
0.06
0.08 0.05 0.02 0.03 0.06 0.02 0.07 0.05
22
23 24 25 合计 平均
100
100 100 100 2500 100
P控制图(不良率)
1.公式 (1) 公组样本大小n相等时:
P CL = P UCL = P
LCL =
P(1 -P)/n -P)/n + 3 P(1
P (2) n不等,且相差小于20% 时: P(1 -P)/ n P P(1 -P)/ n CL = P
UCL = LCL = + 3 - 3
判定规则
判定规则
判定规则
判定规则
判定规则
案例
案例
案例
常规控制图及用途
计量控制图
计量值的数据收集:按一定时间间 隔抽取一定的样本,然后进行测量, 再将测量到的数据记录下来。计量 型数据具有连续性,故它的抽样计 划与计数值有很大的差异。它通常 根据产品要求,对产品的重要特性 定时抽取固定样本个数。
初级SPC培训教程PPT共4-2024鲜版

21
05
不合格品控制及改进措施
2024/3/27
22
不合格品定义及分类方法
2024/3/27
不合格品定义
不符合规定要求或标准的产品、 半成品、原材料等。
分类方法
按性质可分为严重不合格、一般 不合格和轻微不合格;按来源可 分为设计不合格、制造不合格、 采购不合格等。
23
不合格品处理程序和责任人划分
。
其他领域
除了制造业和服务业外,SPC还 可以应用于农业、能源等领域。 通过对相关数据进行监控和分析 ,提高生产效率和资源利用率。
2024/3/27
7
02
测量系统分析
2024/3/27
8
测量系统基本概念
01
测量系统定义
测量系统是指用于获取产品或 过程特性量值的一组操作、程 序、量具、设备、软件及操作
软件资源
选择合适的SPC软件,确保其功能满足企业的实际 需求。
人力资源
通过内部培训或外部引进具备SPC技能和知识的人 才。
2024/3/27
32
成功案例分享
案例背景
某制造企业在生产过程中遇到质量问 题,产品不良率较高,严重影响企业 声誉和市场竞争力。
实施过程
该企业决定引入SPC进行质量改进。 首先进行了全面的质量诊断,识别出 关键的质量问题和影响因素。然后制 定了详细的SPC实施计划,包括选择 合适的SPC工具、培训员工、建立质 量监控体系等。在实施过程中,企业 克服了各种困难和挑战,最终成功建 立了有效的SPC系统。
根据收集到的数据计制步骤与注意事项
将观测值用点子描在控制图上 。
02
4. 判稳
01
3. 描点
2024/3/27
- 1、下载文档前请自行甄别文档内容的完整性,平台不提供额外的编辑、内容补充、找答案等附加服务。
- 2、"仅部分预览"的文档,不可在线预览部分如存在完整性等问题,可反馈申请退款(可完整预览的文档不适用该条件!)。
- 3、如文档侵犯您的权益,请联系客服反馈,我们会尽快为您处理(人工客服工作时间:9:00-18:30)。
3、全面质量管理阶段。
大家知道这几个概念吗?
• 控制图是什么?有什么用? • 什么是X?什么是R图? • X-R,是一张图还是两张图,是先做R
图,还是X图,还是无所谓先后? • UCL、LCL、USL、LSL 本次培训将给大家讲解这些问题。
•目录
•一、基本概念 •二、统计过程控制特点 •三、控制图结构和结构 •四、分析用控制图和控制用控制图 •五、控制图的两类错误和判异准则 •六、控制图的类型及选用原则
控制用控制图
• 当过程达到了我们所确定的状态后,才能将分 析用控制图的控制线延长作为控制用控制图。 由于后者相当于生产中的立法,故由前者转为 后者时应有正式交接手续。 进入日常管理后,关键是保持所确定的状态。 经过一个阶段的使用后,可能又会出现异常, 这时应查出异因,采取必要措施,加以消除, 以恢复统计控制状态。
一.基本概念
• SPC的定义
SPC:Statistical Process Control
利用统计学的原理对过程中的各个阶段进 行评估和监控,建立并保持过程处于可接 受的并且稳定的水平,从而保证产品和服 务符合规定要求的质量管理技术。
•控制图由来
•SPC是美国休哈特在20世纪20年代所创造 的理论,它能科学地区分出生产过程中产 品质量的偶然波动与异常波动,从而对过 程的异常及时告警,以便人们采取措施, 消除异常,恢复过程的稳定
• 3、SPC要解决的不是对特定工序要用什 么控制图的问题,它强调整个过程,重 点在“P”(Process)
三.控制图结构和原理
•样本统计量数值
•UCL •CL
•LCL
•控制图示例
•时间或样本号
• 图上横坐标:以时间先后排列的样本组号(子组号);
• 纵坐标为质量特性值或样本统计量。
• 两条控制限线一般用虚线表示,上面一条称为上控制限(记为UCL,Upper Control Limit),下面一条称为下控制限(记为LCL,Lower Control Limit) ;
•三.控制图结构和原理
• 3σ 原则即是控制图中的CL,UCL及LCL由下式确定 UCL=μ + 3σ CL = μ LCL= μ - 3σ
μ 和σ分别是统计量的总体均值和总体标准差,不可 能精确知道,可以通过已知的数据来加以估计。
注意:规范限(USL、LSL)不能用做控制限。规范限 用以区分合格与不合格,控制限用以区分偶然和异 常波动,两者不能混淆。
• 中心线用实线表示(记为CL,Central Line)。
三.控制图结构和原理
• 正态性假定:
任何生产过程生产出来的产品,其质量特性值总会存 在一定程度的波动,当过程稳定或者说受控时,这些 波动主要是由5M1E的微小变化造成的随机误差。此时 ,绝大多数质量特性值均服从或近似服从正态分布。
•5M1E:
• 小概率原理又称为实际推断原理,当然运用小概 率原理也可能导致错误,但犯错误的可能性恰恰就是 此小概率。
三.控制图结构和原理
• 反证法思想
• 一旦控制图上点子越出界限线或其他小概率事件发生 ,则怀疑原生产过程失控,也即不稳定,此时要从5MIE去 找原因,看是否发生了显著性变化。
三.控制图结构和原理
统计过程控制培训ppt
2020年7月12日星期日
前言(1)
• 日本名古屋大学调查了115家日本中小型企业 ,结果发现平均每家工厂采用137张控制图
• 美国柯达彩色胶卷公司有5000职工,一共应用 35000张控制图,平均每个员工7张。因为胶卷 的片基上需要分别涂上8层厚度为1um至2um的 药膜;此外,对于种类繁多的化学原料也要应 用控制图进行控制。
我们并不单纯追求控制图的多少,但工厂中使 用控制图的张数在一定程度上反映上管理现代 化的程度。
前言(2)
• 从上世纪初至今,质量管理发展阶段回顾 1、以产品检验为主要手段的质量检验阶段。 2、以数理统计方法和质量管理相结合的统计
质量控制阶段。
统计过程控制之父——休哈特,于1924年提出了世界上 第一张控制图。
三.控制图原理和结构
•规范限 •控制限
•3δ
•μ
•3δ
四、分析用控制图和控制用ห้องสมุดไป่ตู้制图
•分析用控制图主要分析两个方面的问题:
• 所分析的过程 是否处与稳态
• 过程能力指数是否满足要求,过程能力指数必须在 稳态下计算,故先要将过程调整到统计稳态,然后 再调整到技术稳态。
状态I:统计控制状态与技术控制状态同时达到是最 理想的状态Ⅱ:统计控制状态未达到,技术控制状 态达到; 状态Ⅲ:统计控制状态达到,技术控制状态未达到 ; 状态Ⅳ:统计控制状态与技术控制状态均未达到, 是最不理想的状态。
•SPC的内容包括2个方面:
• 利用控制图分析 • 计算过程能力指 过程的稳定性, 数分析稳定的过 看过程是否稳定 程能力满足技术 ,对过程的异常 要求的程度,对 因素进行预警。 过程质量进行评
价。
二.统计过程控制的特点
1、贯彻预防性原则是现代质量管理的一个 特点。 SPC是一种预防性的方法。
• 2、SPC不是少数质量管理人员的事情, 它强调全员参与和团队合作精神。
•三.控制图结构和原理
•异常波动对控制图来说,包括两方面的内容: •1. 控制图界外的点 •2.控制图内不随机的点
•85
•80 •UCL
•75
•70 •CL
•65 •60•LCL
异常波动
三.控制图结构和原理
• 小概率原理
• 所谓小概率原理,即认为小概率事件一般是不会 发生的。
• 由准则可知,若X服从正态分布,则X的可能值 超出控制界限的可能性只有0.27%。因此,一般认为 不会超出控制界限。
•人、机器、原材料、工艺方法、测量及生产环境
• 正态曲线演化成控制图
•UCL •CL •LCL
三.控制图结构和原理
质量波动理论: 偶然原因:过程固有,始终存在,对质量影
响微小,但难以去除。如脱水机开动时的 振动。 异常原因:非过程固有,有时存在,有时不 存在,对质量影响大,但不难去除,如切 割刀片的磨损。
•3σ准则
•在生产过程中,仅有偶然性误差存在时,质量特性X服 从正态分布N( µ, σ ),则据正态分布的概率性质,有
•P{µ - 3 σ < X< µ + 3 σ }=99.73 %
•根据3σ原理,在一次试验中,如果样品出现在分布范围 (μ-3σ,μ+3σ)的外面,则认为生产处于非控制状态。 我们把μ-3σ定为LCL,μ+3σ定为UCL,μ定为CL,这样得 到的控制图称为3σ原理的控制图,也即称为休哈特控制图 。
大家知道这几个概念吗?
• 控制图是什么?有什么用? • 什么是X?什么是R图? • X-R,是一张图还是两张图,是先做R
图,还是X图,还是无所谓先后? • UCL、LCL、USL、LSL 本次培训将给大家讲解这些问题。
•目录
•一、基本概念 •二、统计过程控制特点 •三、控制图结构和结构 •四、分析用控制图和控制用控制图 •五、控制图的两类错误和判异准则 •六、控制图的类型及选用原则
控制用控制图
• 当过程达到了我们所确定的状态后,才能将分 析用控制图的控制线延长作为控制用控制图。 由于后者相当于生产中的立法,故由前者转为 后者时应有正式交接手续。 进入日常管理后,关键是保持所确定的状态。 经过一个阶段的使用后,可能又会出现异常, 这时应查出异因,采取必要措施,加以消除, 以恢复统计控制状态。
一.基本概念
• SPC的定义
SPC:Statistical Process Control
利用统计学的原理对过程中的各个阶段进 行评估和监控,建立并保持过程处于可接 受的并且稳定的水平,从而保证产品和服 务符合规定要求的质量管理技术。
•控制图由来
•SPC是美国休哈特在20世纪20年代所创造 的理论,它能科学地区分出生产过程中产 品质量的偶然波动与异常波动,从而对过 程的异常及时告警,以便人们采取措施, 消除异常,恢复过程的稳定
• 3、SPC要解决的不是对特定工序要用什 么控制图的问题,它强调整个过程,重 点在“P”(Process)
三.控制图结构和原理
•样本统计量数值
•UCL •CL
•LCL
•控制图示例
•时间或样本号
• 图上横坐标:以时间先后排列的样本组号(子组号);
• 纵坐标为质量特性值或样本统计量。
• 两条控制限线一般用虚线表示,上面一条称为上控制限(记为UCL,Upper Control Limit),下面一条称为下控制限(记为LCL,Lower Control Limit) ;
•三.控制图结构和原理
• 3σ 原则即是控制图中的CL,UCL及LCL由下式确定 UCL=μ + 3σ CL = μ LCL= μ - 3σ
μ 和σ分别是统计量的总体均值和总体标准差,不可 能精确知道,可以通过已知的数据来加以估计。
注意:规范限(USL、LSL)不能用做控制限。规范限 用以区分合格与不合格,控制限用以区分偶然和异 常波动,两者不能混淆。
• 中心线用实线表示(记为CL,Central Line)。
三.控制图结构和原理
• 正态性假定:
任何生产过程生产出来的产品,其质量特性值总会存 在一定程度的波动,当过程稳定或者说受控时,这些 波动主要是由5M1E的微小变化造成的随机误差。此时 ,绝大多数质量特性值均服从或近似服从正态分布。
•5M1E:
• 小概率原理又称为实际推断原理,当然运用小概 率原理也可能导致错误,但犯错误的可能性恰恰就是 此小概率。
三.控制图结构和原理
• 反证法思想
• 一旦控制图上点子越出界限线或其他小概率事件发生 ,则怀疑原生产过程失控,也即不稳定,此时要从5MIE去 找原因,看是否发生了显著性变化。
三.控制图结构和原理
统计过程控制培训ppt
2020年7月12日星期日
前言(1)
• 日本名古屋大学调查了115家日本中小型企业 ,结果发现平均每家工厂采用137张控制图
• 美国柯达彩色胶卷公司有5000职工,一共应用 35000张控制图,平均每个员工7张。因为胶卷 的片基上需要分别涂上8层厚度为1um至2um的 药膜;此外,对于种类繁多的化学原料也要应 用控制图进行控制。
我们并不单纯追求控制图的多少,但工厂中使 用控制图的张数在一定程度上反映上管理现代 化的程度。
前言(2)
• 从上世纪初至今,质量管理发展阶段回顾 1、以产品检验为主要手段的质量检验阶段。 2、以数理统计方法和质量管理相结合的统计
质量控制阶段。
统计过程控制之父——休哈特,于1924年提出了世界上 第一张控制图。
三.控制图原理和结构
•规范限 •控制限
•3δ
•μ
•3δ
四、分析用控制图和控制用ห้องสมุดไป่ตู้制图
•分析用控制图主要分析两个方面的问题:
• 所分析的过程 是否处与稳态
• 过程能力指数是否满足要求,过程能力指数必须在 稳态下计算,故先要将过程调整到统计稳态,然后 再调整到技术稳态。
状态I:统计控制状态与技术控制状态同时达到是最 理想的状态Ⅱ:统计控制状态未达到,技术控制状 态达到; 状态Ⅲ:统计控制状态达到,技术控制状态未达到 ; 状态Ⅳ:统计控制状态与技术控制状态均未达到, 是最不理想的状态。
•SPC的内容包括2个方面:
• 利用控制图分析 • 计算过程能力指 过程的稳定性, 数分析稳定的过 看过程是否稳定 程能力满足技术 ,对过程的异常 要求的程度,对 因素进行预警。 过程质量进行评
价。
二.统计过程控制的特点
1、贯彻预防性原则是现代质量管理的一个 特点。 SPC是一种预防性的方法。
• 2、SPC不是少数质量管理人员的事情, 它强调全员参与和团队合作精神。
•三.控制图结构和原理
•异常波动对控制图来说,包括两方面的内容: •1. 控制图界外的点 •2.控制图内不随机的点
•85
•80 •UCL
•75
•70 •CL
•65 •60•LCL
异常波动
三.控制图结构和原理
• 小概率原理
• 所谓小概率原理,即认为小概率事件一般是不会 发生的。
• 由准则可知,若X服从正态分布,则X的可能值 超出控制界限的可能性只有0.27%。因此,一般认为 不会超出控制界限。
•人、机器、原材料、工艺方法、测量及生产环境
• 正态曲线演化成控制图
•UCL •CL •LCL
三.控制图结构和原理
质量波动理论: 偶然原因:过程固有,始终存在,对质量影
响微小,但难以去除。如脱水机开动时的 振动。 异常原因:非过程固有,有时存在,有时不 存在,对质量影响大,但不难去除,如切 割刀片的磨损。
•3σ准则
•在生产过程中,仅有偶然性误差存在时,质量特性X服 从正态分布N( µ, σ ),则据正态分布的概率性质,有
•P{µ - 3 σ < X< µ + 3 σ }=99.73 %
•根据3σ原理,在一次试验中,如果样品出现在分布范围 (μ-3σ,μ+3σ)的外面,则认为生产处于非控制状态。 我们把μ-3σ定为LCL,μ+3σ定为UCL,μ定为CL,这样得 到的控制图称为3σ原理的控制图,也即称为休哈特控制图 。