铸钢件热裂的产生和防止
分析铸造热裂缺陷形成的原因及改进对策

分析铸造热裂缺陷形成的原因及改进对策铸造热裂缺陷是铸造过程中常见的一种缺陷形态,会对铸件的性能和质量造成重大影响。
为了解决这一问题,需要深入分析其成因,并制定改进对策。
本文将从铸造热裂缺陷的原因以及改进措施两个方面展开讨论,旨在为铸造工艺提升提供思路和指导。
一、铸造热裂缺陷的形成原因铸造热裂缺陷通常在铸件冷却过程中产生,以下是其形成的主要原因:1. 温度梯度引起的应力集中铸件冷却过程中,由于各部分温度变化不一致,会导致内部产生温度梯度,从而引起局部局部应力集中。
当材料的强度无法承受这种应力时,就会发生热裂缺陷。
2. 晶粒的收缩行为铸件在凝固过程中,晶粒会出现收缩。
若凝固过程中晶粒收缩不一致,就会引起内部应力的不平衡,从而产生热裂。
3. 液态膨胀引起的应力铸造过程中,液态金属体积较大,当其冷却凝固时,体积会缩小,引起内部应力。
若应力超过材料的承载能力,就会发生热裂缺陷。
二、改进对策为了解决铸造热裂缺陷问题,可以采取以下改进对策:1. 优化铸造工艺参数通过调整铸造温度、冷却速度以及铸件尺寸等参数,使得整个铸造过程中的温度分布更加均匀,减小温度梯度和晶粒收缩不一致性,从而减轻应力集中的程度,降低热裂的风险。
2. 控制液态膨胀行为合理控制铸造合金的成分,通过合金设计等方法来调整材料的液态膨胀行为。
降低材料在冷却凝固过程中产生的应力,减少热裂的概率。
3. 采用合适的铸型材料选择合适的铸型材料也是防止铸造热裂缺陷的关键。
材料的导热性能和热传导能力会影响铸件冷却的速度,因此在选择铸型材料时要充分考虑其导热性和热传导性能。
4. 进行合理的余热处理通过对已铸造完成的铸件进行合理的余热处理,使其内部温度均衡分布,减少应力集中和热裂的风险。
此外,适当的余热处理还能改善铸件的织构和力学性能。
5. 严格控制冷却速度合理控制冷却速度是防止铸造热裂缺陷的重要措施之一。
通过对冷却介质的选择以及冷却方式的优化,可以实现对冷却速度的有效控制,降低热裂的风险。
铸钢件热裂的产生和防止

铸钢件热裂的产生和防止摘要分析了熔模铸钢件热裂产生的原因和过程,论述了防止热裂的工艺措施,并介绍了自割内浇口转移热裂及其设计方法。
关键词:熔模铸造铸钢热裂热裂是熔模铸钢件常见的缺陷之一。
随着熔模铸造的发展,复杂件、薄壁件越来越多,型壳的强度也得到了很大提高,熔模铸钢件中热裂缺陷的比例也随之上升。
如何防止热裂成了熔模铸造技术工作人员关心和棘手的问题。
1 热裂产生的原因当铸件某个部位的应力达到或超过其材质的强度极限时,铸件该部位将会产生裂纹。
铸件的裂纹分为热裂和冷裂两类。
如果裂纹是在凝固过程中形成,则此裂纹称为热裂。
热裂的裂口断面呈氧化色,裂口粗糙,其微观组织为晶间断裂。
如果裂纹是在铸件完全凝固后形成的,则此裂纹称为冷裂。
铸件在凝固时会产生较大的收缩,当此收缩受铸型的阻碍或受铸件其余部分的牵制,则会产生应力。
而铸件材质在凝固阶段的强度极限极低,因此应力很可能达到或超过其强度极限而使铸件局部产生裂纹。
如果裂纹是在凝固前期形成,而此时仍存在着较大比例的液相且具有良好的流动充填性,则裂纹被液相焊合。
但当裂纹在凝固后期形成(一般指固相率>0.7),此时固相骨架已经比较致密,所残余的液相难以充填弥合裂纹,则裂纹将会进一步发展并残留下来,热裂形成点大致在固相线附近。
热裂往往产生在铸件“弱点”部位,所谓“弱点”即铸件凝固过程中结壳最薄部位。
这些“弱点”通常是铸件壁连接的内角或浇注系统引入部位等一些局部过热部位。
热裂的产生过程大致如下:铸件凝固初期,在其平面和圆柱表面部位以及外圆角部位凝固结壳而具有了一定强度和刚度。
之后在内圆角部位也凝固结壳而具有一定强度和刚度。
同时结壳因凝固冷却而产生收缩,此时结壳将受到与其相连的铸型型壁的阻碍而产生应力,特别是铸件的突起部位。
随着凝固的进行,结壳增厚,浇注金属的比强度增大,结壳的总强度也增大。
但是由于铸型型壳受热产生膨胀、烧结而使铸件的收缩受阻增大,引起了凝固结壳中应力增大。
铸件裂纹和六种铸件常见缺陷的产生原因及防止方法
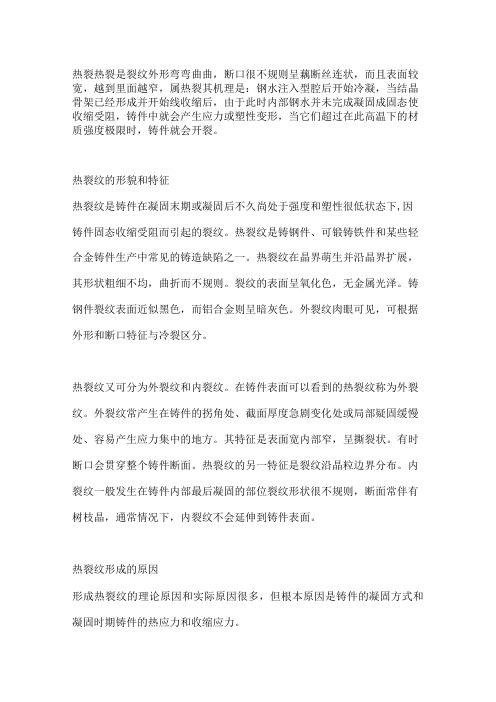
热裂热裂是裂纹外形弯弯曲曲,断口很不规则呈藕断丝连状,而且表面较宽,越到里面越窄,属热裂其机理是:钢水注入型腔后开始冷凝,当结晶骨架已经形成并开始线收缩后,由于此时内部钢水并未完成凝固成固态使收缩受阻,铸件中就会产生应力或塑性变形,当它们超过在此高温下的材质强度极限时,铸件就会开裂。
热裂纹的形貌和特征热裂纹是铸件在凝固末期或凝固后不久尚处于强度和塑性很低状态下,因铸件固态收缩受阻而引起的裂纹。
热裂纹是铸钢件、可锻铸铁件和某些轻合金铸件生产中常见的铸造缺陷之一。
热裂纹在晶界萌生并沿晶界扩展,其形状粗细不均,曲折而不规则。
裂纹的表面呈氧化色,无金属光泽。
铸钢件裂纹表面近似黑色,而铝合金则呈暗灰色。
外裂纹肉眼可见,可根据外形和断口特征与冷裂区分。
热裂纹又可分为外裂纹和内裂纹。
在铸件表面可以看到的热裂纹称为外裂纹。
外裂纹常产生在铸件的拐角处、截面厚度急剧变化处或局部疑固缓慢处、容易产生应力集中的地方。
其特征是表面宽内部窄,呈撕裂状。
有时断口会贯穿整个铸件断面。
热裂纹的另一特征是裂纹沿晶粒边界分布。
内裂纹一般发生在铸件内部最后凝固的部位裂纹形状很不规则,断面常伴有树枝晶,通常情况下,内裂纹不会延伸到铸件表面。
热裂纹形成的原因形成热裂纹的理论原因和实际原因很多,但根本原因是铸件的凝固方式和凝固时期铸件的热应力和收缩应力。
液体金属浇入到铸型后,热量散失主要是通过型壁,所以,凝固总是从铸件表面开始。
当凝固后期出现大量的枝晶并搭接成完整的骨架时,固态收缩开始产生。
但此时枝晶之间还存在一层尚未凝固舶液体金属薄膜(液膜),如果铸件收缩不受任何阻碍,那么枝晶骨架可以自由收缩,不受力的作用。
当枝晶骨架的收缩受到砂型或砂芯等的阻碍时,不能自由收缩就会产生拉应力。
当拉应力超过其材料强度极限时,枝晶之间就会产生开裂。
如果枝晶骨架被拉开的速度很慢,而且被拉开部分周围有足够的金属液及时流入拉裂处并补充,那么铸件不会产生热裂纹。
相反,如果开裂处得不到金属液的补充,铸件就会出现热裂纹。
铸件热裂缺陷的成因及防止措施
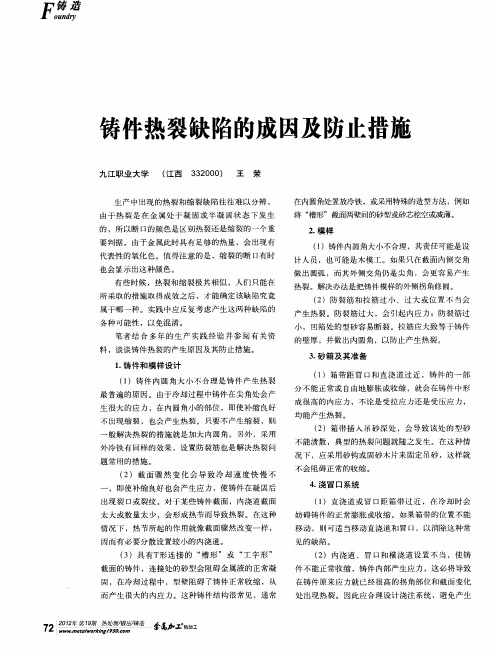
密性和 内部 质量直 接影 响到发动机 的工作效率 。 我 公司现 为某 主机厂生产 的进气歧 管最大轮 廓尺
寸 为7 5 4 mm ×1 5 1O 3 mm X lmm,重 量 3 k ,材 质 . g 4 牌 号 为 L 2 。该 铸 件 壁 厚 偏差 大 ,最 厚 处 壁 厚 达 M 7
代表性的氧化色 。值得注意的是 ,缩裂的断 I有时 = 1
也 会 显 示 出这 种颜 色 。 有 些 时候 ,热 裂 和 缩裂 极 其 相 似 ,人们 只 能 在
所采取的措施取得成效之后 ,才能确定该缺 陷究竟 属于哪一种。实践 中应反复考虑产生这两种缺 陷的
各 种可 能 性 ,以 免混 淆 。 笔者 结 合 多 年 的Байду номын сангаас生 产 实 践 经 验 并 参 阅 有 关 资 料 ,谈 谈 铸件 热 裂 的产 生 原 因及 其 防止 措 施 。
2 模样 .
()铸件 内圆角大小不合理 ,其责任可能是设 1 计人员,也可能是木模工 。如果只在截面内侧交角 做出圆弧 ,而其外侧交角仍是尖角 ,会更容易产生
热 裂 。解决 办法 是把铸 件 模样 的外 侧拐 角修 圆。 ( )防 裂 筋 和 拉 筋 过 小 、过 大 或 位 置 不 当会 2 产 生 热 裂 。防 裂 筋过 大 ,会 引起 内应 力 ;防 裂 筋过
热 裂 倾 向大 的 金 属 。 浇 注温 度 低 ,则 不 能将 砂 型 或 砂 芯 中 的 粘 结 剂 烧 掉 , 以 使 其 适 度 溃 散 。 另一 方 面 ,若 浇 注 温 度 太 高 ,则会 在 截 面 不均 匀的 铸 件 中 形成 较 大 的 温 度梯 度 。 因此 ,在 保 证 金 属 液 有 足够 热量 烧 掉 砂 型 ( 或 砂 芯 ) 中粘 结 剂 的 前 提 下 ,浇 注 温 度越 低 越 好 。如
铸件热裂原因
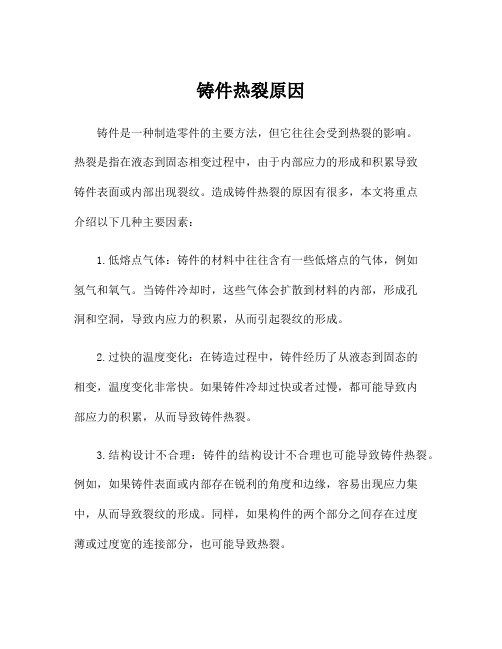
铸件热裂原因
铸件是一种制造零件的主要方法,但它往往会受到热裂的影响。
热裂是指在液态到固态相变过程中,由于内部应力的形成和积累导致
铸件表面或内部出现裂纹。
造成铸件热裂的原因有很多,本文将重点
介绍以下几种主要因素:
1.低熔点气体:铸件的材料中往往含有一些低熔点的气体,例如
氢气和氧气。
当铸件冷却时,这些气体会扩散到材料的内部,形成孔
洞和空洞,导致内应力的积累,从而引起裂纹的形成。
2.过快的温度变化:在铸造过程中,铸件经历了从液态到固态的
相变,温度变化非常快。
如果铸件冷却过快或者过慢,都可能导致内
部应力的积累,从而导致铸件热裂。
3.结构设计不合理:铸件的结构设计不合理也可能导致铸件热裂。
例如,如果铸件表面或内部存在锐利的角度和边缘,容易出现应力集中,从而导致裂纹的形成。
同样,如果构件的两个部分之间存在过度
薄或过度宽的连接部分,也可能导致热裂。
4.金属成分的变化:铸件的金属成分对铸件的热裂性能有很大的影响。
例如,硅、铜、锰等元素的含量过高,会导致内部应力的增加,从而导致铸件热裂。
5.冷却方式不适当:铸造过程中冷却方式不合理也常常是引起热裂的原因之一。
如果冷却过程中所用的冷却剂温度过低或过高,或者冷却的速度过快或过慢,都会导致铸件内部产生应力,从而引起铸件热裂。
综上所述,铸件热裂的原因复杂,需要进行全面的分析和研究。
在铸造中要避免热裂,需要在制作工艺与工作水平的不断提升上进行不断地思考和改进。
树脂砂铸钢件产生热裂缺陷的原因及其防止措施有哪些

树脂砂铸钢件产生热裂缺陷的原因及其防止措施有哪些?用树脂砂生产薄壁、形状复杂的铸钢件时,最容易产生的一种缺陷是热裂。
其原因有三:1、使用树脂砂流动性好,易紧实;树脂加入量少,砂粒上包覆的粘结剂膜薄,这样砂粒受热膨胀,砂芯、砂型的热膨胀率会比水玻璃砂芯(型)高。
2、树脂砂受热后,在还原性气氛下树脂炭化结焦而形成坚硬的焦炭骨架,能提高砂芯热强度(如1000℃时树脂砂的抗压强度是水玻璃砂的5~10倍),严重阻碍砂芯(型)退让。
呋喃树脂中糠醇的含量越高(氮含量越低),铸件的热裂倾向越大,因为糠醇提高了树脂的热分解温度,降低了树脂的热分解速度,从而降低了砂型或砂芯的溃散性,使砂型或砂芯更加阻碍铸件收缩,造成铸件热裂倾向加重。
由于铸钢凝固时液一固两相区的区间较宽,因此呋喃树脂砂铸钢时更易产生热裂缺陷,尤其是框架结构件。
3、用呋喃树脂砂时,采用对甲苯磺酸作催化剂会增硫,从而加大热裂倾向性。
高温金属凝固时产生的收缩受到砂芯(型)较大的阻力,使铸件产生应力和变形,而合金表面增硫,又降低了抗热裂的能力。
当应力或变形超过合金在该温度下的强度极限或变形能力时,就会形成热裂。
为使树脂砂,尤其呋喃树脂砂避免或减少热裂,可采取以下几个方面的措施:1、合金方面(1)控制铸件的含硫量,宜在0.03%以下,并且避免铸件中出现Ⅱ型硫化物。
(铸钢件中的硫化物呈三种形态,即Ⅰ型、Ⅱ型和Ⅲ型,其中Ⅱ型的硫化物沿晶界分布,呈断续状,容易引起铸件热裂。
)通过调整锰硫比来改变硫的分布型态。
(2)对于碳钢件,应使S+P≤0.07%,因为硫与磷的叠加作用,使热裂倾向性增加。
(3)用A1脱氧时,应将铝的残留量A1残留控制≤0.1%;过高的A1残量,有利于形成A12S3,甚至可能形成A1N,使钢的断口呈现“岩石状”,大大降低铸钢件的抗热裂能力。
(4)使钢的晶粒能细化。
如在钢液中加入稀土和硅钙,既可脱氧、脱硫,又可以细化晶粒。
对NiCrMoV钢的测定表明:在相同的条件下,经稀土+硅钙处理的钢液,较之未处理的钢液,其抗裂能力高2倍以上。
铸件开裂的原因

铸件开裂的原因
铸件开裂是在铸造过程中经常发生的问题,可能会造成产品质量下降甚至损坏。
下面将从几个方面分析铸件开裂的原因。
温度控制不当是导致铸件开裂的主要原因之一。
在铸造过程中,如果铸件冷却过快或温度变化过大,容易造成内部应力过大,从而导致铸件开裂。
因此,对于不同材料和结构的铸件,需要合理控制铸造温度和冷却速度,避免温度梯度过大造成应力集中。
金属液体的浇注方式也会影响铸件的质量。
如果浇注速度过快或浇注过程中存在气泡和气体混入,会导致铸件内部存在气孔和夹杂物,降低铸件的强度和韧性,容易发生开裂。
因此,在铸造过程中需要采取适当的浇注方式和控制浇注速度,确保金属液体充分填充模具且不受气体污染。
金属合金的成分和熔炼工艺也会影响铸件的质量。
如果金属合金成分不均匀或存在杂质,会导致铸件内部组织不均匀,容易出现晶粒过大或过小的情况,从而影响铸件的力学性能,导致开裂。
因此,在选择合金材料和熔炼工艺时,需要严格控制合金成分和熔炼温度,确保合金均匀混合且无杂质。
模具设计和制造也会对铸件开裂产生影响。
如果模具设计不合理或制造精度不高,会导致铸件表面粗糙或存在凹凸不平的情况,容易造成应力集中和裂纹产生。
因此,在模具设计和制造过程中,需要
考虑铸件的结构和形状,确保模具表面光洁度和精度要求,减少铸件在脱模过程中的变形和损伤。
铸件开裂是由多种因素综合作用导致的问题,需要在铸造过程中综合考虑温度控制、浇注方式、合金成分、模具设计等多个方面的因素,以避免铸件开裂的发生,提高铸件的质量和性能。
只有在铸造过程中严格控制每个环节,才能确保铸件的质量和稳定性,避免开裂等质量问题的发生。
铸件热裂纹的原因及其防治措施
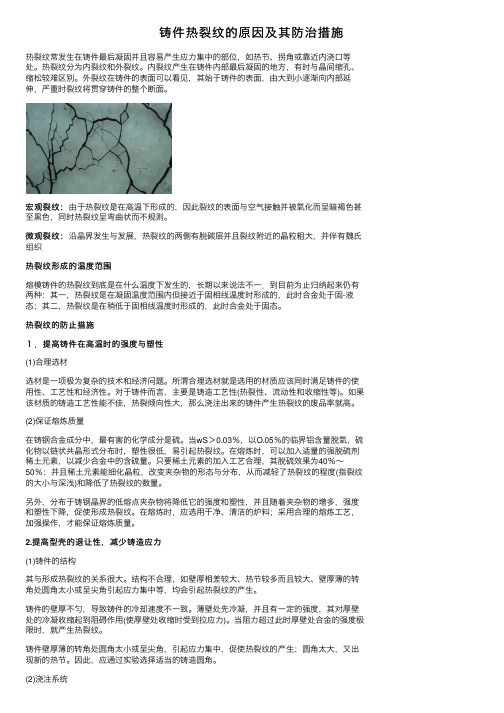
铸件热裂纹的原因及其防治措施热裂纹常发⽣在铸件最后凝固并且容易产⽣应⼒集中的部位,如热节、拐⾓或靠近内浇⼝等处。
热裂纹分为内裂纹和外裂纹。
内裂纹产⽣在铸件内部最后凝固的地⽅,有时与晶间缩孔、缩松较难区别。
外裂纹在铸件的表⾯可以看见,其始于铸件的表⾯,由⼤到⼩逐渐向内部延伸,严重时裂纹将贯穿铸件的整个断⾯。
宏观裂纹:由于热裂纹是在⾼温下形成的,因此裂纹的表⾯与空⽓接触并被氧化⽽呈暗褐⾊甚宏观裂纹:⾄⿊⾊,同时热裂纹呈弯曲状⽽不规则。
微观裂纹:沿晶界发⽣与发展,热裂纹的两侧有脱碳层并且裂纹附近的晶粒粗⼤,并伴有魏⽒微观裂纹:组织热裂纹形成的温度范围熔模铸件的热裂纹到底是在什么温度下发⽣的,长期以来说法不⼀.到⽬前为⽌归纳起来仍有两种:其⼀,热裂纹是在凝固温度范围内但接近于固相线温度时形成的,此时合⾦处于固-液态;其⼆,热裂纹是在稍低于固相线温度时形成的,此时合⾦处于固态。
热裂纹的防⽌措施1.提⾼铸件在⾼温时的强度与塑性(1)合理选材选材是⼀项极为复杂的技术和经济问题。
所渭合理选材就是选⽤的材质应该同时满⾜铸件的使⽤性、⼯艺性和经济性。
对于铸件⽽⾔,主要是铸造⼯艺性(热裂性、流动性和收缩性等)。
如果该材质的铸造⼯艺性能不佳,热裂倾向性⼤,那么浇注出来的铸件产⽣热裂纹的废品率就⾼。
(2)保证熔炼质量在铸钢合⾦成分中,最有害的化学成分是硫。
当wS>0.03%,以O.05%的临界铝含量脱氧,硫化物以链状共晶形式分布时,塑性很低,易引起热裂纹。
在熔炼时,可以加⼊适量的强脱硫剂稀⼟元素,以减少合⾦中的含硫量。
只要稀⼟元素的加⼊⼯艺合理,其脱硫效果为40%~50%:并且稀⼟元素能细化晶粒,改变夹杂物的形态与分布,从⽽减轻了热裂纹的程度(指裂纹的⼤⼩与深浅)和降低了热裂纹的数量。
另外,分布于铸钢晶界的低熔点夹杂物将降低它的强度和塑性,并且随着夹杂物的增多,强度和塑性下降,促使形成热裂纹。
在熔炼时,应选⽤⼲净、清洁的炉料;采⽤合理的熔炼⼯艺,加强操作,才能保证熔炼质量。
- 1、下载文档前请自行甄别文档内容的完整性,平台不提供额外的编辑、内容补充、找答案等附加服务。
- 2、"仅部分预览"的文档,不可在线预览部分如存在完整性等问题,可反馈申请退款(可完整预览的文档不适用该条件!)。
- 3、如文档侵犯您的权益,请联系客服反馈,我们会尽快为您处理(人工客服工作时间:9:00-18:30)。
铸钢件热裂的产生和防止摘要分析了熔模铸钢件热裂产生的原因和过程,论述了防止热裂的工艺措施,并介绍了自割内浇口转移热裂及其设计方法。
关键词:熔模铸造铸钢热裂热裂是熔模铸钢件常见的缺陷之一。
随着熔模铸造的发展,复杂件、薄壁件越来越多,型壳的强度也得到了很大提高,熔模铸钢件中热裂缺陷的比例也随之上升。
如何防止热裂成了熔模铸造技术工作人员关心和棘手的问题。
1 热裂产生的原因当铸件某个部位的应力达到或超过其材质的强度极限时,铸件该部位将会产生裂纹。
铸件的裂纹分为热裂和冷裂两类。
如果裂纹是在凝固过程中形成,则此裂纹称为热裂。
热裂的裂口断面呈氧化色,裂口粗糙,其微观组织为晶间断裂。
如果裂纹是在铸件完全凝固后形成的,则此裂纹称为冷裂。
铸件在凝固时会产生较大的收缩,当此收缩受铸型的阻碍或受铸件其余部分的牵制,则会产生应力。
而铸件材质在凝固阶段的强度极限极低,因此应力很可能达到或超过其强度极限而使铸件局部产生裂纹。
如果裂纹是在凝固前期形成,而此时仍存在着较大比例的液相且具有良好的流动充填性,则裂纹被液相焊合。
但当裂纹在凝固后期形成(一般指固相率>0.7),此时固相骨架已经比较致密,所残余的液相难以充填弥合裂纹,则裂纹将会进一步发展并残留下来,热裂形成点大致在固相线附近。
热裂往往产生在铸件“弱点”部位,所谓“弱点”即铸件凝固过程中结壳最薄部位。
这些“弱点”通常是铸件壁连接的内角或浇注系统引入部位等一些局部过热部位。
热裂的产生过程大致如下:铸件凝固初期,在其平面和圆柱表面部位以及外圆角部位凝固结壳而具有了一定强度和刚度。
之后在内圆角部位也凝固结壳而具有一定强度和刚度。
同时结壳因凝固冷却而产生收缩,此时结壳将受到与其相连的铸型型壁的阻碍而产生应力,特别是铸件的突起部位。
随着凝固的进行,结壳增厚,浇注金属的比强度增大,结壳的总强度也增大。
但是由于铸型型壳受热产生膨胀、烧结而使铸件的收缩受阻增大,引起了凝固结壳中应力增大。
当铸件凝固结壳的“弱点”部位处的应力达到了浇注金属的强度极限,则在“弱点”部位产生裂纹,此裂纹穿透了“弱点”部位结壳的整个厚度。
在此裂纹形成的同时,应力将相应缓解。
随着凝固的继续进行,在断裂点形成了新的凝固结壳,应力又将重新产生和增大,且集中在原断裂点的相对部位。
当此“弱点”部位的应力再次达到浇注金属材料的强度极限时,则会再次断裂。
如此裂纹继续发展直到贯穿铸件“弱点”部位整个截面。
但是如果型壳表面层过热超过1 100~1 200 ℃以后产生软化,则能激烈降低收缩应力,裂纹的发展也会中止。
提高模壳退让性!2 热裂的防止由上可知,热裂的产生部位是在铸件的“弱点”上,此“弱点”可以是铸件结构不合理引起的,例如铸件壁的连接结构不合理,内圆角半径过小等。
也可以是铸造工艺不合理引起的,例如浇注系统设计不合理,导致局部过热而形成“弱点”。
本文主要是从铸造工艺角度来分析探讨如何防止熔模铸钢件的热裂缺陷。
2.1 选择热裂敏感小的铸造合金,严格控制有害元素S的含量不同铸造合金,对热裂的敏感性也不同。
凡是凝固过程中收缩系数较小,凝固时形成的固相的强度较高的合金,其热裂敏感性较小。
因此凡有利于提高固相线附近结壳高温强度和降低结壳收缩率的因素都有利于减缓热裂的产生。
表1所示为某些合金钢在固相线以上30~40 ℃时的高温强度。
ZG20虽然其凝固时的高温强度较高,但由于其凝表1 合金钢在固相线以上30~40 ℃时的高温强度[1]Table 1High temperature strength of alloy steel over solidus 30~40 ℃钢的牌号Mn13 1Cr13 T10 ZG55 ZG35 30CrNiMo 工业纯铁 ZG20 1Cr18Ni9Ti 高温强度/MPa 0.3 0.4 0.5 0.7 1.2 1.2 1.4 2.1 2.5固时会发生δ→γ的相变而产生大的线收缩,因此该合金仍然具有较大的热裂敏感性而较容易产生热裂。
硫是钢中有害元素。
图1所示为不同浇注温度时硫对钢高温强度的影响。
钢在凝固时,由于硫的存在,在晶界处出现FeS和Fe的低熔点共晶,而使钢在高温时的强度降低。
因此含硫高的钢,其热裂敏感性大。
图1 含硫量对钢在结晶温度附近的强度影响[1]Fig.1Strength of steel nearby crystallization temperature withS content表2所示为含硫量与铸件热裂产生的关系。
由表可知,含硫量高时铸件中形成热裂多。
因此用稀土对钢冶炼时进行纯化处理,降低钢中含硫量是防止熔模铸钢件产生热裂的有效措施之一。
表2 含S量与铸钢件热裂的关系[2]Table 2Hot tear of steel casting with S content铸钢件热裂含S量/%碱性电炉钢酸性平炉钢没有0.002~0.008 0.024不多0.015~0.020 0.024多0.020~0.028 0.0332.2 低温钢水红壳浇注中碳钢在结晶温度附近的强度极限值很低,大约为0.5~2.0 MPa。
图2所示为中碳钢结壳的强度极限与图2 中碳钢结壳强度与其平均温度的关系[1]Fig.2 Strength of forming shell for medium-carbon steel withaverage temperature其平均温度的关系。
提高浇注温度将降低凝固时结壳的强度。
对于ZG35,当浇注温度由1 580 ℃降低到1 530 ℃,其在热裂危险期的结壳强度将提高31%,因而有利于防止热裂产生。
但是降低浇注温度,特别是对于薄壁铸件,很容易产生冷隔、浇不足等缺陷,因此必须提高浇注时型壳的温度。
一般对于水玻璃型壳希望浇注时型壳温度大于600 ℃,即要求红壳浇注。
提高型壳温度到600 ℃以上还可以避开石英砂(粉)在573 ℃的β→α的相变膨胀(0.82%),并有利于内层型壳出现1 100 ℃以上的软化,从而减缓了型壳对铸件“弱点”的收缩阻碍。
因此低温钢水红壳浇注是熔模铸件防止热裂产生的有效措施。
2.3 薄壁铸件采用扁宽浇口,浇口的模数大于铸件的模数随着熔模铸造的发展,熔模铸造薄壁铸钢件的品种、数量呈增长趋势。
由于熔模铸钢件浇注系统设计长期以来采用以补缩为主的原则,薄壁铸钢件的内浇口厚度习惯上不小于薄壁件的壁厚,加上浇注温度较高,导致铸件浇注系统引入处局部过热而成为“弱点”。
这些局部过热的“弱点”凝固收缩时,其四周的铸件薄壁本体已经凝固,因此过热的“弱点”的收缩受到铸件薄壁本体的牵制,收缩受阻,因而往往在铸件的内浇口附近出现热裂。
避免这类热裂的方法就是将内浇口改为扁宽内浇口。
内浇口厚度一般可取铸件壁厚的1/2。
为了不降低浇注速度,避免局部过热,增强模组的装配强度,内浇口宽度比正常值增大1~2倍。
扁宽内浇口有利于缓和浇注系统引入部位过热而防止热裂产生。
图3所示为板手铸件的浇注系统设计方案。
图3a为改进前的方案,该铸件在内浇口附近出现热裂。
图3b将内浇口厚度减薄一半,宽度增宽一倍,热裂基本消除。
图3 板手精铸件浇注系统方案示意图Fig.3Scheme of the gating system for the investment casting of spanner2.4 浇注金属应尽量均匀充填型腔,避免因浇注金属冲击型腔固定点后分流而形成“热点”浇注金属进入型腔的流向、速度受内浇口的设置位置、大小、形状的限制。
不合理地设计内浇口的设置点、大小、形状可以导致浇注金属冲击型壳某个部位,然后分流,使受冲击部位局部过热而成为“热点”,此“热点”也即是容易产生热裂的“弱点”。
图4所示拐臂精铸件由某厂携压型来我厂进行生产,原浇注系统设计如图所示有两个内浇口A和B,浇注金属液从B内浇口进入型腔后冲击型腔K处然后分流,使K处过热,导致铸件相应该处成为“弱点”而产生热裂。
我们去掉了B内浇口,并适当增大内浇口A的长度后,此热裂随即消除。
图4 拐臂精铸件原内浇口方案及液流示意简图Fig.4Scheme of the former gate and liquid-flow forthe investment castingof corner-arm2.5 浇注系统设计应尽量避免框形结构熔模铸造技术人员对具有两个热节的精铸件或长精铸件往往设计两个内浇口,于是使得铸件-内浇口-直浇道成为一个框形结构系统,这类结构最容易出现收缩受阻,而很容易在内浇口附近产生热裂,也容易产生变形,因此应尽量避免框形结构。
图5a所示为这类铸件-内浇口-直浇道系统框形结构示意图。
铸件A 和B处局部厚大形成两个热节,为了保证A和B热节的补缩,在A和B 部位设置两个内浇口,内浇口附近过热而成为“弱点”,其收缩受铸件本身以及c处型壳的阻碍,“弱点”部位很容易产生热裂。
如将浇注系统改为图5b所示楔条形结构,则浇注金属从整个楔条进入型腔,而不是从两个热节部位集中进入,因而降低了原内浇口附近的过热程度,同时楔条增大了铸件散热面积,提高了凝固结壳强度,c处型壳的阻碍收缩也得以缓和,因此减缓了热裂的产生。
如果再采用低温钢水红壳浇注,基本上可避免这类铸件的热裂产生。
图5 铸件-内浇口-直浇道系统框形结构示意图Fig.5Scheme of frame structure forthe casting-gate-sprue system2.6 设置防裂工艺肋如果用户允许铸件结构改进,可以在易产生热裂的部位设置防裂工艺肋。
防裂工艺肋不仅可以提高铸件热裂部位的强度,更主要是可起散热片作用,改善散热条件,也可使浇注金属合理分流,从而减缓“热点”集中程度,缓解热裂的产生。
因此防裂工艺肋不宜厚,一般为相应部位壁厚的1/3左右,但为保证浇足,厚度应大于2 mm。
图6所示为防裂工艺肋设置举例。
如果用户不同意改变铸件结构,可以在铸件退火消除应力后去除工艺肋。
图6 防裂工艺肋设置举例Fig.6Exemple of technical rib for preventing hot tear2.7 热裂的转移——自割浇口的应用设计浇注系统时可以采用控制浇注系统各组元凝固速度的方法,让热裂转移到内浇口或工艺肋上。
图7所示为热裂往内浇口上转移的设计实例。
这类浇注系统称为自割浇口。
自割浇口还能减少浇口切割工作量,特别是对于大型精铸铸钢件能大大减轻铸件清理、切割工作量,很有推广价值。
图7 自割浇口的设计结构示意图Fig.7Scheme of structure for the self-cut-gate图7所示为自割浇口的设计结构示意。
图中内浇口处设置了过热套4。
过热套采用导热性差的耐火材料混合成水玻璃砂经硬化制成。
制作蜡模时将过热套嵌在压型中,使过热套与蜡模成为一个整体,经制壳、脱蜡、焙烧后,过热套成为型壳的一部分。