金刚石线切割的原理、特点及其在精密超精密加工领域的应用
金刚石绳锯切割原理

金刚石绳锯切割原理
嘿,朋友们!今天咱就来讲讲那神奇的金刚石绳锯切割原理!你知道吗,这就好比一把超级锋利的宝剑,可以斩断各种坚硬的东西!就像孙悟空的金箍棒,威力巨大!
想象一下,一块巨大的石头或者厚厚的墙壁挡在面前,那可真是让人头疼啊!但有了金刚石绳锯,嘿,那就不一样啦!金刚石绳锯它就像一个不知疲倦的小勇士,勇往直前地去切割。
它是怎么工作的呢?简单来说,就是靠那细细的绳锯上镶嵌的金刚石颗粒呀!这些小颗粒可厉害了,就像一群小战士,一个劲儿地去攻克那些坚硬的目标。
比如说,盖房子的时候遇到特别硬的石头,工人师傅们就会拿出金刚石绳锯,“唰唰唰”几下,石头就乖乖被切开啦!这不就好比你遇到一个难题,一下子就找到了解决办法,那得多爽啊!你说是不是?
而且哦,它可灵活啦!不管什么形状、什么角度,它都能应付自如。
就像一个灵活的舞者,在各种场景中翩翩起舞。
哎呀,你想想,如果没有它,那得费多大劲儿去处理那些坚硬的东西呀!
金刚石绳锯虽然厉害,但也需要我们好好爱护和使用它哦!就像你有一个特别棒的玩具,你肯定也会好好珍惜它呀!只有这样,它才能更好地为我们服务,为我们创造更多的价值呢!咱可不能浪费了这么个好东西呀!
总之,金刚石绳锯切割原理真的太有意思啦!它就像一个默默无闻的英雄,在各种需要它的地方发挥着巨大的作用,为我们的生活和建设立下汗马功劳!你们难道不想更深入地了解它吗?。
超精密切削加工主要指金刚石刀具的超精密切削

超精密切削加工主要指金刚石刀具的超精密切削。
超精密切削的工作机理:普通的切削的切削深度一般远大于材料晶粒的尺寸,切削加工以数十计的晶粒团为加工单位,在切削力的作用下从基体上去除金属。
而超精密加工的切削层很薄或尺寸很小,切削深度和进给量必然很小,特别是亚微米和纳米级的超精密切削,切削深度通常小于材料晶粒直径,使的切削只能在晶粒内部进行。
超精密切削时的切削力的特征为:切削力微小,单位切削力很大,切削力随着切削深度的减小而增大,而在切深很小时切削力却急剧上升。
超精密切削加工的特点与应用(1)单位切削力大实现纳米级的超精密加工的物理实质是切断材料的分子、原子间的结合,实现原子或者分子的去除,因此切削力必须超过晶体内部的分子、原子结合力。
(2)切削温度由于超精密切削的切削用量极小以及金刚石刀具和工件材料具有的高导热性,因此超精密切削温度相当低。
(3)刀刃圆弧半径对最小切削厚度的限制刀具刃口半径限制了其最小的切削厚度,刀具刃口越小,允许的最小切削厚度也越小。
超精密切削的应用超精密加工主要用于加工软金属材料以及光学玻璃、大理石和碳素纤维板等非金属材料,主要加工对象是精度要求很高的镜面零件。
(下图是超精密切削球面镜的加工原理图)球面镜的加工原理1-主轴;2-凹面镜;3-刀具轴超精密磨削超精密磨削是当代能达到最低磨削表面粗糙度值和最高加工精度的磨削方法。
超精密磨削去除量最薄,采用较小修整导程和吃刀量来修整砂轮,是靠超微细磨粒等高微刃磨削作用,并采用较小的磨削用量磨削。
超精密磨削要求严格消除振动,并保证恒温及超净的工作环境。
超精密磨削的光磨微细摩擦作用带有一定的研抛作用性质。
1.超精密砂轮磨削的磨削超精密砂轮磨削机理:( 1 ) 超微量切除超精密磨削是一种极薄切削,切屑厚度极小,磨削深度可能小于晶粒的大小,磨削就在晶粒内进行,因此磨削力一定要超过晶体内部非常大的原子、分子结合力,从而磨粒上所承受的切应力就急速地增加并变得非常大,可能接近被磨削材料的剪切强度的极限。
论述金刚石刀具超精密切削的机理丶条件和应用范围

金刚石刀具超精密切削的机理丶条件和应用范围
金刚石刀具是超精密切削中常用的刀具材料,其切削机理、条件和应用范围如下:
1.切削机理:
⏹金刚石刀具的切削刃非常锋利,在切削过程中能够实现“切入式切削”,
使切削力大大减小。
⏹金刚石的硬度极高,切削时不易被工件材料磨损,能够保持良好的切削刃
形状。
⏹金刚石的传热性能极佳,能够快速地将切削热量传递出去,从而降低切削
温度,减少热损伤。
1.切削条件:
⏹刀具刃口半径:为了实现超精密切削,需要将刀具的刃口半径减小到亚微
米级,以提高切削的精度和表面粗糙度。
⏹切削用量:为了减小切削力和热量,需要选择较小的切削深度和进给速度,
以提高切削效率。
⏹工件材料:金刚石刀具适用于加工各种硬材料,如淬火钢、硬质合金等。
但是,对于一些韧性较大的材料,需要进行预处理或选择其他刀具材料。
1.应用范围:
⏹金刚石刀具广泛应用于超精密切削领域,如光学零件、轴承、硬盘磁头、IC
芯片等高精度、高表面质量的零件加工。
⏹在加工过程中,金刚石刀具还可以用于制作各种微细结构,如微孔、微槽
等。
综上所述,金刚石刀具的超精密切削需要满足一定的条件,并具有广泛的应用范围。
金刚石绳锯切割工艺介绍

框架梁切割(金刚石绳锯)1施工工艺2施工要点(1)固定绳锯机及导向轮用M16化学锚栓固定绳锯主脚架及辅助脚架,导向轮安装一定要稳定,且轮的边缘一定要和穿绳孔的中心线对准,以确保切割面的有效切割速度,严格执行安装精度要求。
(2)安装绳索根据已确定的切割形式将金刚石绳索按一定的顺序缠绕在主动轮及辅助轮上,注意绳子的方向应和主动轮驱动方向一致.(3)相关操作系统的连接及安全防护技术措施根据现场情况,水、电、机械设备等相关管路的连接应正确规范、相对集中,走线摆放严格执行安全操作规程,以防机多、人多、辅助设备、材料乱摆、乱放,造成事故隐患。
绳索切割过程中,绳子运动的方向的前面一定用安全防护拦防护,并在一定区域内设安全标志,以提示行人不要进入施工作业区域。
(4)切割启动电动马达,通过控制盘调整主动轮提升张力,保证金刚石绳适当绷紧,供应循环冷却水,再启动另一个电动马达,驱动主动轮带动金刚石绳索回转切割。
切割过程中必须密切观察机座的稳定性,随时调整导向轮的偏移,以确保切割绳在同一个平面内。
(5)切割参数的选择切割过程中通过操作控制盘调整切割参数,确保金刚石绳运转线速度在20m/s左右,另一方面切割过程中应保证足够的冲洗液量,以保证对金刚石绳的冷却,并把磨削下来的粉屑带走。
切割操作做到速度稳定,参数稳定、设备稳定。
(6)切割过程中应注意的问题如遇到发生卡绳,断绳等现象要有相应措施解决。
安全防护措施一定严格、严密,否则断掉的金刚石绳索上的金刚石串珠会像子弹一样飞出伤人。
故现场除搞好必要的防护措施外,一律谢绝来往无关人员观摩。
3.2.2金刚石绳锯机工作性能采用型号DSM-10A(见下图)绳锯机,具体性能参数如下所述:金刚石绳锯机DSM-10A型绳锯机主要技术参数:驱动轮:φ600 mm;额定功率:10KW;额定电压:400V-50/60HZ;钢丝线速度:0—27m/s;缠绳容量:最大9.0米;外型尺寸:1370×557×(1840-2054)mm;防护等级:TP65;液压泵量:40-100L/min;最大工作压力:21MPa;最大切割面积:20m2;设备重量:150kg(主机)+190 kg(高压油泵)(1)金刚石绳锯切割的原理金刚石绳锯切割是金刚石绳索在液压马达驱动下绕切割面高速运动研磨切割体,完成切割工作。
金刚石切割线的原理是什么

金刚石切割线的原理是什么金刚石切割线是一种利用金刚石的高硬度和耐磨性进行材料切割的工具。
它主要是由金刚石颗粒与金属粉末等物质组成的混合物,通过高温高压技术形成了金刚石晶体,进而制成各种切割工具。
金刚石切割线的原理主要包括金刚石颗粒的硬度和尖锐度、金刚石颗粒与被切割材料之间的磨蚀作用以及金刚石切割线的设计结构等方面。
首先,金刚石的硬度和尖锐度是金刚石切割线能够有效切割各种材料的基础。
金刚石是目前已知最硬的材料,其摩氏硬度达到10,在硬度尺度上处于最高位。
这种高硬度使得金刚石能够在切割过程中快速穿透并切割材料,具有很高的硬度补偿能力。
同时,金刚石的尖锐度指的是切割线上金刚石颗粒的尖锐程度。
金刚石颗粒越尖锐,切割时对材料的作用力越集中,切割效果越好。
其次,金刚石切割线实际切割材料的过程主要是通过金刚石颗粒与材料之间的磨蚀作用。
金刚石颗粒具有很高的耐磨性和耐腐蚀性,不易被切割材料磨损或被化学物质侵蚀。
在切割过程中,金刚石颗粒以其尖锐的角度侵入被切割材料,并以高速旋转的方式在材料上摩擦和磨蚀。
这种磨蚀作用可以剥离材料的微粒,使其逐渐被金刚石切割线切割。
最后,金刚石切割线的设计结构也对切割效果产生重要影响。
由于不同被切割材料的特性不同,金刚石切割线的设计结构需根据具体的切割需求进行选择。
一般而言,金刚石切割线的结构应该具备合适的金刚石颗粒大小、尖锐度和布局,以及适当的结构形状和密度。
例如,对于需要高速切割的材料,金刚石颗粒的布局应较为疏松,以便提高切割线的磨蚀效率;而对于需要较高切割精度的材料,金刚石颗粒的布局应更为密集,以保证切割的平整度和精度。
综上所述,金刚石切割线主要通过金刚石颗粒的硬度和尖锐度、金刚石颗粒与被切割材料之间的磨蚀作用以及金刚石切割线的设计结构等因素来实现材料的切割。
由于金刚石的高硬度和耐磨性,使得金刚石切割线成为一种高效、高精度的切割工具,在广泛的工业领域得到应用。
金刚石线切割机的工作原理及分类
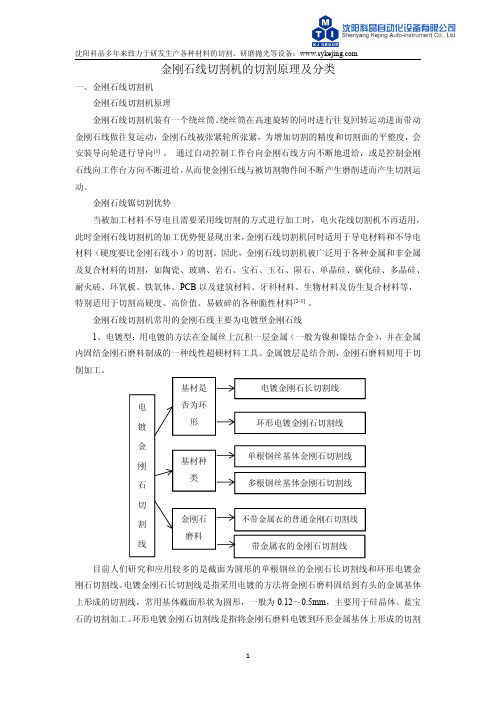
金刚石线切割机的切割原理及分类一、金刚石线切割机金刚石线切割机原理金刚石线切割机装有一个绕丝筒。
绕丝筒在高速旋转的同时进行往复回转运动进而带动金刚石线做往复运动,金刚石线被张紧轮所张紧,为增加切割的精度和切割面的平整度,会安装导向轮进行导向[1]。
通过自动控制工作台向金刚石线方向不断地进给,或是控制金刚石线向工作台方向不断进给,从而使金刚石线与被切割物件间不断产生磨削进而产生切割运动。
金刚石线锯切割优势当被加工材料不导电且需要采用线切割的方式进行加工时,电火花线切割机不再适用,此时金刚石线切割机的加工优势便显现出来,金刚石线切割机同时适用于导电材料和不导电材料(硬度要比金刚石线小)的切割。
因此,金刚石线切割机被广泛用于各种金属和非金属及复合材料的切割,如陶瓷、玻璃、岩石、宝石、玉石、陨石、单晶硅、碳化硅、多晶硅、耐火砖、环氧板、铁氧体、PCB以及建筑材料、牙科材料、生物材料及仿生复合材料等,特别适用于切割高硬度、高价值、易破碎的各种脆性材料[2-3]。
金刚石线切割机常用的金刚石线主要为电镀型金刚石线1、电镀型:用电镀的方法在金属丝上沉积一层金属(一般为镍和镍钴合金),并在金属内固结金刚石磨料制成的一种线性超硬材料工具。
金属镀层是结合剂,金刚石磨料则用于切削加工。
基材是否为环形基材种类金刚石磨料电镀金刚石长切割线环形电镀金刚石切割线单根钢丝基体金刚石切割线多根钢丝基体金刚石切割线不带金属衣的普通金刚石切割线带金属衣的金刚石切割线电镀金刚石切割线目前人们研究和应用较多的是截面为圆形的单根钢丝的金刚石长切割线和环形电镀金刚石切割线。
电镀金刚石长切割线是指采用电镀的方法将金刚石磨料固结到有头的金属基体上形成的切割线,常用基体截面形状为圆形,一般为0.12~0.5mm,主要用于硅晶体、蓝宝石的切割加工。
环形电镀金刚石切割线是指将金刚石磨料电镀到环形金属基体上形成的切割线。
该类切割线使用时一般缠绕到几个导轮上进行单向循环切割,切割过程中无需换向,因此切割速度高。
金刚石线锯
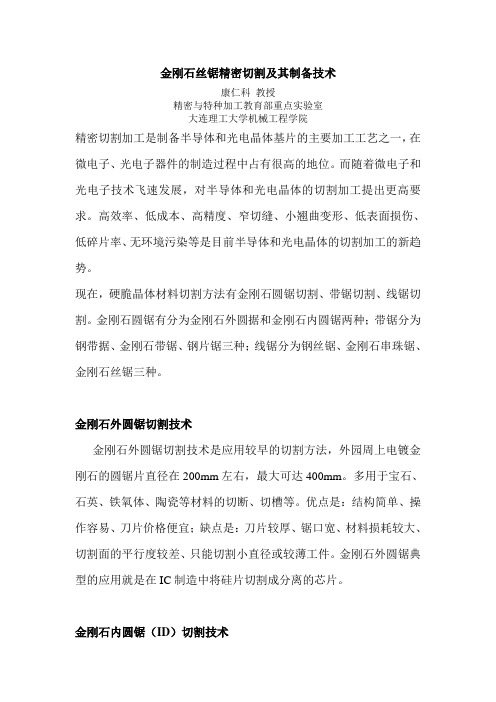
金刚石丝锯精密切割及其制备技术康仁科教授精密与特种加工教育部重点实验室大连理工大学机械工程学院精密切割加工是制备半导体和光电晶体基片的主要加工工艺之一,在微电子、光电子器件的制造过程中占有很高的地位。
而随着微电子和光电子技术飞速发展,对半导体和光电晶体的切割加工提出更高要求。
高效率、低成本、高精度、窄切缝、小翘曲变形、低表面损伤、低碎片率、无环境污染等是目前半导体和光电晶体的切割加工的新趋势。
现在,硬脆晶体材料切割方法有金刚石圆锯切割、带锯切割、线锯切割。
金刚石圆锯有分为金刚石外圆据和金刚石内圆锯两种;带锯分为钢带据、金刚石带锯、钢片锯三种;线锯分为钢丝锯、金刚石串珠锯、金刚石丝锯三种。
金刚石外圆锯切割技术金刚石外圆锯切割技术是应用较早的切割方法,外园周上电镀金刚石的圆锯片直径在200mm左右,最大可达400mm。
多用于宝石、石英、铁氧体、陶瓷等材料的切断、切槽等。
优点是:结构简单、操作容易、刀片价格便宜;缺点是:刀片较厚、锯口宽、材料损耗较大、切割面的平行度较差、只能切割小直径或较薄工件。
金刚石外圆锯典型的应用就是在IC制造中将硅片切割成分离的芯片。
金刚石内圆锯(ID)切割技术金刚石内圆锯(ID)切割技术示意图金刚石内圆锯切割技术的优点是:1.刚性好,可做的很薄,达到0.1mm;2.切片精度高,直径200mm晶片的厚度差仅为0.01mm;3.设备低廉,所用切割机价格仅为其它工具多使用切割机价格的1/3——14;4.每片都可以进行径向调整和切片厚度的调整;5.小批量多规格加工时,具有灵活的可调性。
缺点是:1.切片表面损伤层较大;2.刀口宽,材料损失大;3.生产率低,每次只切割一片;4.只能切割直线,无法切割曲面;5.只能切割直径小于200mm的晶片。
带锯切割金刚石带锯是以电镀金刚石磨料或镶焊金刚石烧结块为主题的环形锯条,带锯出现于20世纪50年代,我国八十年代才开始研制该类设备。
优点是:锯切速度快,刀具材料消耗少,噪音小。
超精密切削加工与金刚石刀具(精密加工

2.5 切削刃锋锐度对切削变形、加工表面质量的影 响
三、切削刃锋锐度对切削变形和切削力的影响
2021/5/1
锋锐车刀切削变形系数明显低于 较钝的车刀。 刀刃锋锐度不同,切削力明显不 同。刃口半径增大,切削力增大, 即切削变形大。背吃刀量很小时, 切削力显著增大。因为背吃刀量很 小时,刃口半径造成的附加切削变 形已占总切削变形的很大比例,刃 口的微小变化将使切削变形产生很 大的变化。所以在背吃刀量很小的 精切时,应采用刃口半径很小的锋 锐金刚石车刀。
(FN ) Ff cos FP sin
A点为极限临界点,极限最小切削厚度 hDmin 应为
hDmin rn(1 cos ) rn1
2021/5/1
第2章 超精密切削与金刚石刀具
2.1超精密切削时刀具的切削速度、磨损和耐用度 2.2超精密切削时积屑瘤的生成规律 2.3切削参数变化对加工表面质量的影响 2.4刀刃锋锐度对切削变形和加工表面质量的影响 2.5超精密切削时的最小切削厚度 2.6金刚石刀具晶面选择对切削变形和加工表面质
2021/5/1
2.2 超精密切削时刀具的磨损和寿命
后刀面 前刀面
2021/5/1
图2-2:切削刃正常磨损;
图 2-3 : 图 a 是 刀 刃 磨 损 的 正常情况,图b是剧烈磨损 情况,可以看到磨损后成 层状,即刀具磨损为层状 微小剥落;
图2-4:图中所示沿切削速 度方向出现磨损沟槽,由 于金刚石和铁、镍的化学 和物理亲和性而产生的腐 蚀沟槽;
2.3 超精密切削时积屑瘤的生成规律
2、进给量f和背吃刀量 p的影响
• 由图2-7可以看出在进给量很小时,积屑瘤的高度很大,在 f=5μm/r时,h0值最小,f值再增大时,h0值稍有增加。
- 1、下载文档前请自行甄别文档内容的完整性,平台不提供额外的编辑、内容补充、找答案等附加服务。
- 2、"仅部分预览"的文档,不可在线预览部分如存在完整性等问题,可反馈申请退款(可完整预览的文档不适用该条件!)。
- 3、如文档侵犯您的权益,请联系客服反馈,我们会尽快为您处理(人工客服工作时间:9:00-18:30)。
1金刚石线切割
20世纪90年代,国际上为了解决大尺寸硅片的加工问题,采用了线锯加工技术将硅棒切割成片。
早期的线锯加工技术是采用裸露的金属线和游离的磨料,在加工过程中,将磨料以第三者加入到金属线和加工件之间产生切削作用[1]。
这种技术被成功地用于对硅和碳化硅的加工。
为了进一步缩短加工时间,以及对其它坚硬物质和难以加工的陶瓷进行加工,人们将金刚石磨料以一定的方式固定到金属线上,从而产生了固定金刚石线锯。
3.1金刚石线切割的原理
图3.1金刚石线切割原理图
如图3.1高速往复运动的切割线带动砂浆到切割区,使砂浆中的研磨颗粒(SiC颗粒)与硅棒表面高速磨削,由于研磨颗粒有非常锐利的棱角,并且硬度远大于硅棒的硬度,所以硅棒与线锯接触的区域逐渐被砂浆磨削掉,进而达到切割的效果,同时砂浆也可以带走磨削中产生的大量热[2]。
在对金刚石线锯切割机理的认识过程中,许多研究者认为,金刚石磨粒的微观切削运动是一个滚动、嵌入过程,提出了“滚动 -嵌入”模型。
Li 等人提出锯丝施加在磨粒上的力带动磨粒沿切削表面滚动,同时压挤磨粒嵌入切削表面,从而形成剥落片屑和表面裂缝,形成宏观的切割作用。
重点研究了磨粒嵌入工件时的应力分布和作用,发现磨粒对材料的最大剪切应力发生在微观切削表面之下,据此对磨料的选择进行优化。
Kao 等人指出在“滚动 - 嵌入”模型中,磨粒的运动除滚动和嵌入外,还包括刮擦,三者共同形成切削作用。
Bhagavat等人则在这个模型中考虑了磨浆的作用并认为,在锯丝带动游离磨料切割硅锭的小区域内,锯丝与磨浆的运动构成了一个弹性流体动力学环境,用有限元方法分析锯丝与硅锭间的磨浆弹性流体动力学模型,得到磨浆薄膜厚度和压力分布关于走丝速度、磨浆粘度和切割条件的函数,还得出结论:磨浆薄膜厚度大于平均磨粒尺寸,是磨粒的流动产生了切削[3]。
3.2 金刚石线切割的导线轮
根据切割材料直径不同和设备制造厂家的技术考虑导线轮有2轮、3轮、4轮不等,安装方法有2轮平行、等边三角形或梯形,如图3.2所示。
图3.2导线轮安装形式
导线轮是控制片厚的关键部件,导线轮是用高分子材料制作的精密滚轮,在其表而刻有等同于线宽、深的螺旋槽,切割时将线绕在导线轮上。
要求其材料耐磨性要好、刚度要高,在切割张紧时不能变形:片厚的控制取决于槽间宽度,槽间宽度误差应小于5um,所以对材质要求和加工精度都非常高[4]。
3.3 金刚石线切割的特点[5]
a)可加工非导电材料而传统的放电加工则不能
b)可进行多线切割
c)刀缝损失小这对加工成本高的半导体和贵重材料非常重要。
用直径350 m 的金刚石线
切SiC单晶时刀缝才为0 .3048 mm
d)可自由改变切割位向
3.4 金刚石线切割的应用
20世纪90年代,国际上为了解决大尺寸硅片的加工问题,采用了线锯加工技术将硅棒切割成片,这种技术被成功地用于对硅和碳化硅的加工。
目前,采用金刚石工具切割花岗石是石材加工常用的方法之一
目前在光电子工业中使用最为广泛的是往复式多线锯
金刚石线切割被广泛的用在大尺寸半导体和光电池薄片切割
参考文献
[1]Ito S,Murata R Study on machining characteristics of dia—mond abrasive wire EJ].J Mechanical Engineering Lab,1987,41(5):236
[2]冯涛,李保军,马玉通.锗单晶切割工艺研究[J].电子工业专用设备,2009,175.
[3]周锐,李剑峰等.金刚石线锯的研究现状与进展[J].现代制造工程,2004,(6):112-115.
[4]杨树人,王宗昌.半导体材料[M].北京:科学出版社,2003,56-59.。