铸造工艺方案确定(精)
低压铸造参数确定(精)

职业教育材料成型与控制技术专业教学资源库《铝合金铸件铸造技术》课程教案低压铸造参数确定制作人:张保林陕西工业职业技术学院低压铸造参数确定一、引言低压铸造的工艺规范包括升液、充型、增压、保压结晶、卸压、冷却、延时,以及铸型预热温度、浇注温度、铸型的涂料等。
二、升液压力和升液速率升液压力是指当金属液面上升到浇口,所需要的压力。
式中,p1——升液阶段所需压力(MPa ); h1——金属液面至浇道的高度(cm);ρ ——金属液密度(g/cm3 );10200——单位换算系数(g/N); K ——充型阻力因数,K=1~1.5(阻力小取下限,阻力大取上限)。
在升液过程中,升液高度将随着坩埚中金属液面下降而增加。
因此,所需的压力将相应增大。
金属液在升液管内的上升速度即为升液速度,升液应平稳,以有利于型腔内气体的排出,同时也可使金属液在进入浇口时不致产生喷溅。
随着压力增大,升液管中的液面升高。
因此,增压速度实际上反应了升液速度。
增压速度可用下式计算,即式中,v1——升液阶段的增压速度(MPa/s );p1——升液压力(MPa );t1——升液时间(s )。
1020011K h p ρ=111t p v =一般情况下,为了有利于型腔中气体的排出,升液速度缓慢些为好。
对于铝合金,升液速度控制在5~15cm/s ,加压速度为1.27~1.75KPa/s 。
三、充型压力和充型速度充型压力是指使金属液充型上升到铸型顶部所需的压力。
式中,p2——充型压力(MPa );h2——金属液上升至铸件顶面的高度(cm);同样,所需的充型压力随着坩埚中金属液面下降而增大。
充型速度取决于通入坩埚内气体压力增加的速度,可按下式计算:式中,v2——充型速度(MPa/s );p1、p2——分别为升液和充型压力(MPa );t2——充型时间(s ) 充型速度关系到金属液在型腔中的流动状态和温度分布,因而影响铸件的质量。
充型速度慢,金属液充填平稳,有利于型腔中气体的排除,铸件各种温差增大。
铸造工艺方案及工艺图示例解析

16
轴座铸件的一型两铸方案
3#型芯是悬臂型芯,其型芯头的长度较长。大批生产时, 还可考虑一箱中同时铸造两件的方案(图1-49),使悬臂型 芯成为挑担型芯,这样可使芯头长度缩短,且下芯定位简 便,成本更低。
17
C6140车床进给箱体
18
1.分型面的选择
方案Ⅰ 分型面在轴孔的中心线上。此时凸台A因距分型面 较近,又处于上箱,若采用活块、型砂易脱落,故只能 用型芯来形成,但槽C用型芯或活块均可制出。本方案的 主要优点是便于铸出九个轴孔,铸后飞翅少,便于清理。 同时,下芯头尺寸较大,型芯稳定性好,不易产生偏芯 缺陷。其主要缺点是型芯数量较多。 方案Ⅱ 从基准面D分型,铸件绝大部分位于下箱。此时, 凸台A不妨碍起模,但凸台E和槽C妨碍起模,也需用活块 或型芯来克服。其缺点是轴孔难以直接铸出。若铸出轴 孔,因无法制出型芯头,必须加大型芯与型壁的间隙, 使飞翅的清理工作量加大。 方案Ⅲ 从B面分型,即铸件全部置于下箱。其优点是铸件 不会产生错型缺陷。同时,铸件最薄处在铸型下部,金 属液易于填充。缺点是凸台E、A和槽C都需采用活块或型 芯,而内腔型芯上大下小、稳定性差;若铸出轴孔,则 其缺点与方案Ⅱ同。
20
2.铸造工艺图
分型面确定之后, 便可依据有关资料 绘制铸造工艺图。 图2—42为采用分 型方案Ⅰ时的铸造 工艺图。由于本书 省略了其它视图, 故组装而成的型腔 大型芯的细节图中 未能示出。
21
铸造工艺设计实例4
图示是支承轮铸造工艺图。材料
HT200,铸件质量约19 kg,轮廓
尺寸φ300 mm×100 mm,生产批 量为单件。 (1)从图纸上可以看出,该铸件 外形结构为旋转体,辐板下有三 根加强肋并与φ40孔形成六等分均 布,外形较为简单。主要壁厚为
第二章-铸造工艺方案的确定
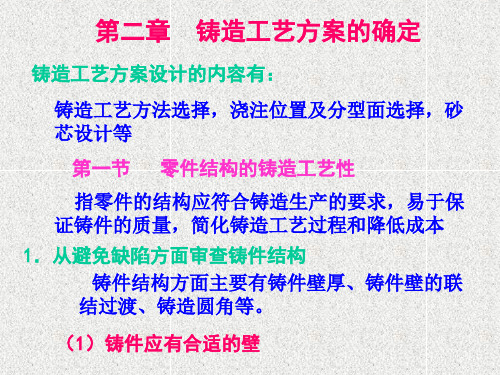
课堂讨论 图3-2-26
1.应使铸件全部或大部分置于同一半型内
图2-15 轮毂分型方案
2.应尽可能减少分型面数目 铸件的分型面少,铸件精度容易保ቤተ መጻሕፍቲ ባይዱ,且砂箱数目 少
图2-16 确定分型面数目的实例
3.平直分型面和曲折分型面的选择 尽可能选择平直分型面以简化工装结构及
其制造、加工工序和造型操作
图2-17 摇臂铸件的分型面
最小壁厚/㎜
高温合金
铝合金
0.6~1.0
1.5~2.0
0.8~1.5
2.0~2.5
1.0~2.0
2.5~3.0
—
3.0~3.5
—
3.5~4.0
铸件尺寸㎜
50×50 100×100 225×225
金属型铸造时铸件的最小壁厚
铝硅合 金
最小壁厚/㎜
铝镁合金、镁合 铜合金 金
灰铸铁
2.2
3
2.5
3
2.5
3
3
(1)改进妨碍起模的凸台、凸缘和肋板结构
改进妨碍起模的铸件结构 a)不合理 b)合理
教材220面,学生看,老师提问
(2)尽量取消铸件外表侧凹
图2-6 外壁内凹的框形件 a)不合理 b)合理
(3)有利于砂芯的固定和排气 (4) 减少或简化分型面(P221)
轴承架铸件
P222
(5)便于铸件的清理 (P222,图3-2-15) (6)简化模具制造 (P222,图3-2-16)
原则:
铸件精度和生产批量 吃砂量要求 吃砂量的确定
吃砂量: 铸件表面所需要的的最小型砂厚度。
根据铸件大小、重量、厚度、种类以 及型砂的特性和砂箱的结构确定。
吃砂量过小 砂型紧实困难,易引起胀砂、包砂、掉砂、
63-工作任务10-5:绘制铸造工艺图(精)

灰铸铁铸件生产技术
工作任务10-5:绘制铸造工艺图
【任务提出】 确定铸造工艺参数,运用手工和软件两种方
法绘制规范的铸造工艺图。 任务要求: (1)确定铸造工艺方案。 (2)使用红蓝铅笔绘制铸造工艺图。 (3)使用绘图软件绘制铸造工艺图
灰铸铁铸件生产技术
工作任务10-5:绘制铸造工艺图
【制定计划】 (1)准备红蓝铅笔。 (2)拟定铸造工艺图绘制思路。 (3)明确各种铸造工艺及其参数的表达方法。
【分析决策】 (1)确定铸造工艺方案。 (2)确定铸造工艺图绘制的步骤。 (3)利用铸造手册查取铸造工艺参数。
【实施计划】 (1)使用红蓝铅笔绘制铸造工艺图。 (2)使用绘图软件绘制铸造工艺图
灰铸铁铸件生产技术
工作任务10-5:绘制铸造工艺图
【监控评估】 (1)铸造工艺图的内容及Байду номын сангаас达方法。 (2)运用铸造工艺手册情况。 (3)绘图软件的使用情况。
铸造工艺方案

3) 工人技术水平、生产经验及技术习惯。
4) 模样芯盒等工艺装备的加工能力和生产经验。
三、设计工作内容和程序
1.设计工作内容
包括:铸造工艺图、铸件图、铸型装配图(合型图)、工 艺卡、操作工艺规程。
不宜将内腔砂芯横截分块来制芯组合,这样较难保证偏心距e的尺寸公差。 合理的方案是最好制成整芯装入铸型内。
应使砂芯起模斜度和模样起模斜度大小、方向一致,保证铸件壁厚均匀。
2.尽量减少砂芯数目,保证操作方便
3.砂芯形状要与生产条件、造型、制芯方法相适应
(二)芯头与芯座
铸型中使用砂芯时,为使砂芯在铸型中定位准确、 安放稳固及砂芯内部排气通畅,在砂芯及模样上均需 做出芯头。
第二节 铸造工艺方案的拟定
包含:a.造型、制芯方法和铸型种类的选择; b.浇注位置和分型面的确定; c.工艺参数的选定等。
一、零件结构的铸造工艺性分析 (一)先作好整体性的了解
a.根据零件样图参数及要求查定该产品是否能根据 现有生产条件铸得出来;
b. 能否容易铸出而不易出现铸造缺陷。
(二)从壁厚大小、分布及热节布局去审查铸件结构的 合理性
改进后( 虚线所示),呈对称 结构,减少模具制造费用。
尽量采用对称结构,回转铸型可采用刮板造型法,减少模具制造费用。
大而复杂的铸件可考虑分成若干简单铸件分开铸造再行焊接 或用螺栓将其联接固定。
大而复杂的铸件可考虑分成若干简单铸件分开铸造再行焊接 或用螺栓将其联接固定。
对于一些很小的简易零件,常把这些小件毛坯连接成一个较 长的大铸件。
确定浇注位置很大程度上着眼于控制铸件的凝固顺 序,铸件上部易发生缺陷的可能。
精密铸造工艺方案范本

精密铸造工艺方案范本1. 引言本文档对精密铸造工艺方案进行了详细介绍和说明,包括工艺流程、材料选用、设备配置等内容。
精密铸造是一种重要的制造工艺,在各个行业中得到广泛应用,本文档旨在提供一个范本,帮助读者编写适用于各种精密铸造项目的工艺方案。
2. 工艺流程精密铸造的工艺流程可以分为以下几个主要步骤:1.模具制备:根据产品要求,制作精密的铸造模具,包括精密机械加工、热处理等工艺。
2.熔炼与浇注:选取合适的原料,进行熔炼,然后将熔融金属倒入预制的模具中进行铸造。
3.冷却与固化:待浇注完成后,让铸件自然冷却,使其固化成型。
4.模具拆卸:将固化成型的铸件从模具中拆卸出来。
5.去毛刺与清洁:清理铸件表面的毛刺,进行清洁处理,保证产品质量。
6.加工与检验:对铸件进行机械加工,如车削、铣削等,然后进行质量检验。
3. 材料选用精密铸造的材料选用十分重要,需要根据产品要求和工艺性能选择合适的材料。
常用的精密铸造材料包括:•不锈钢:具有优异的耐腐蚀性和耐高温性,适用于制作复杂的零件。
•高温合金:具有优异的高温强度和耐腐蚀性能,适用于高温工作环境。
•钛合金:具有优良的力学性能和化学稳定性,适用于航空航天领域。
•铝合金:具有较低的密度和良好的强度,适用于汽车零部件等领域。
在选择材料时,还需要考虑到成本、加工性能、产品质量等方面的因素。
4. 设备配置精密铸造需要使用到一系列设备和工具来完成铸造过程。
常用的设备包括:•高频感应熔炼炉:用于将金属材料熔融成液态,以便进行浇注。
•真空铸造设备:通过在高真空环境中进行铸造,避免气体和杂质对产品质量的影响。
•数控机床:用于对铸件进行加工和修整,提高产品尺寸精度和表面质量。
•检测设备:包括X射线探伤、超声波检测、金相分析等,用于对铸件进行质量检验。
根据具体的生产需求,可以进行设备配置的调整和选型。
5. 质量控制精密铸造的质量控制是保证产品质量的关键。
在工艺流程中,需要进行严格的质量控制措施,包括:•材料检验:对原材料进行化学成分、力学性能等方面的检测。
铸造工艺设计

浇铸系统和冒口
一、. 浇注系统
浇注系统是引导金属液流入型腔的一系列通道的总称。
作用:确保液态金属能够平稳而合理地充满型腔。
浇口杯 接纳、引入金属,减轻金属液
对铸型的冲击。
组
直浇道 引入金属,提供压力头以克
服流动阻力充满型腔
成 横浇道 引入金属、阻撇熔渣
引入金属、控制金属液的充型
内浇道 速度和流动方向→调控温度场
6)冒口布置在加工面上,可借加工精整铸件表面,零件外观 质量好。
7)对不同高度上的多个冒口,应用冷铁使各个冒口的补缩范 围相隔开
15
16
冒口尺寸计算的基本原理
冒口根部的直径d大于铸件被补缩处的热节圆直径dy 冒口高度H由所选定的系数乘以d得出。
见图4-8,表4-6。
17
18
19
第四节铸造工艺方案及工艺图 32 示例
铸造工艺图是铸造过程最基本和最重要的工艺文件 之一,它对模样的制造、工艺装备的准备、造型造芯、 型砂烘干、合型浇注、落砂清理及技术检验等,都起着 指导和依据的作用。
铸造工艺图是利用红、蓝两色铅笔,将各种简明的工 艺符号,标注在产品零件图上的图样。
20
铸造工艺图绘制
零件的铸造工艺图的制定及铸件图举例(一) 首先应综合考虑浇注位置和分型面的确定,1 加工余 量、2 起模斜度,3 砂芯的部位,要画出砂芯的位置、 形状和芯头。
缺点:金属液难以充满这种浇注系统中的所有单元, 撇渣能力较差,渣和气体容易随液进入型腔,造成 废品。
6
2. 常见浇注系统的类型
顶注式 底注式
中间注入式 阶梯注入式
7
2. 常见浇注系统的类型
(3)底注式浇注系统 内(浇1)道顶开注式浇注系统 内浇道开设
铸造工艺方案

铸造工艺方案1. 简介铸造是一种重要的制造工艺,主要通过将熔化后的金属或合金倒入模具中,经凝固、凝固和冷却过程,制造出所需的零件或产品。
铸造工艺方案是指针对特定产品和材料,制定的一套铸造工艺流程和参数,旨在保证零件质量和生产效率。
2. 工艺流程通常,铸造工艺包括以下几个主要步骤:2.1 模具制备模具是铸造过程中用于容纳熔化金属的形状工具。
根据产品的设计和要求,选择合适的模具,并确保其具有足够的强度和耐磨性。
常用的模具材料包括铸铁、钢等。
2.2 材料准备根据产品的要求,选择适合的金属或合金作为铸造材料。
根据材料的成分和比例,进行合金配料和坩埚熔炼,确保熔化金属的化学成分符合要求。
2.3 熔化和浇注将准备好的铸造材料放入熔炉中进行熔化。
根据不同的金属,选择适当的熔炉和熔炼工艺。
熔化后的金属通过浇注系统,倒入模具中。
2.4 凝固和冷却在模具中倒入的熔化金属逐渐凝固。
根据不同的工艺和产品要求,控制凝固过程中的温度和时间,以保证零件的结构和机械性能。
2.5 脱模和后处理经过一定的凝固和冷却时间后,零件可以从模具中取出。
根据需要,进行去毛刺、修整、退火等后处理工艺,以提高零件的表面质量和性能。
3. 工艺参数铸造工艺方案中的参数设置对于零件的品质和生产效率具有重要影响。
以下是一些常见的工艺参数:•浇注温度:熔化金属的温度,根据金属的熔点和浇注系统的特点确定;•浇注速度:控制熔化金属流动的速度,避免产生气孔和缺陷;•浇注压力:在一些特殊情况下,通过施加压力,改善金属的凝固结构;•凝固时间:根据零件的尺寸和凝固速率,确定零件在模具中的冷却时间;•冷却介质:通过选择适当的冷却介质,加速零件的冷却过程;•后处理工艺:根据产品的要求,选择合适的去毛刺、退火等工艺,提高零件的性能。
4. 质量控制在铸造过程中,质量控制是至关重要的,以确保生产出符合要求的零件。
以下是一些常用的质量控制措施:•材料检验:对铸造材料进行化学成分和物理性能的检验,确保其符合标准;•模具检查:检查模具的磨损和变形情况,及时进行维修和更换;•熔炼质量控制:对熔炼过程中的温度、时间和熔化金属的化学成分进行监控;•壳材质量检验:对制作壳材的材料和工艺进行检验,确保壳材的质量和性能;•零件外观检查:对铸造零件的表面和尺寸进行检查,确保不存在缺陷和变形;•机械性能测试:通过拉伸试验、硬度测试等手段,评估铸件的机械性能。
- 1、下载文档前请自行甄别文档内容的完整性,平台不提供额外的编辑、内容补充、找答案等附加服务。
- 2、"仅部分预览"的文档,不可在线预览部分如存在完整性等问题,可反馈申请退款(可完整预览的文档不适用该条件!)。
- 3、如文档侵犯您的权益,请联系客服反馈,我们会尽快为您处理(人工客服工作时间:9:00-18:30)。
手工操作压型结构图 1-活接螺栓 2-蝶形螺母 3-上半 压型 4-注模料口 5-型芯销 6定位销 7-型腔 8-型芯 9-内浇 道 10-下半压型
铜合金铸件铸造技术 课程
工艺方案的确定
1.确定分型面 1)确定分型面的意义
正确地择分型面,是保証制模工艺正常进行和获得 优质熔模的先决条件;也是决定压型结构是否经济、 合理的基本条件。必须综合考虑各方面的要求和影响 因素,分析在铸件上不同部位分型,对熔模质量的影 响,以及压型结构的经济性和合理性。在保証熔模质 量的前提下,只有结构简单的压型才被认为是经济合 理的。只有合理的分型面,才能设计出合理的压型。
铜合金铸件铸造技术 课程
工艺方案的确定
1.确定分型面 2.基准面的选择 1)基准面选择的意义
2)基准面选择的原则
3)基准面选择实例
右图所示为前支架零件。基准面A与B用工艺符号标注于图中。这样的基 准面可使工艺基准与设计基准重合,先加工余量大的面,后加工余量小的 面,可保证最后加工面的余量足够,且A、B面平整、粗糙度小。(端面、 外圆为基准)
铜合金铸件铸造技术 课程
工艺方案的确定
1.确定分型 面 2.基准面的 选择 1)基准面 选择的意义
熔模铸造可获得精度和粗糙度低的铸件,有些尺寸虽然要由 机械加工来保证,但一般加工余量不大,所以基准面选择比较重 要。特别是利用高效自动机床加工时,对基准面的要求较为严格。 因此在铸造工艺上要重视基准面的选择,要保证基准面的几何形 状和尺寸精度。 铸件上的外圆、平面、内孔和端面等都可以做为基准面。从 零件的精度要求出发,最适宜的定位基准一般由设计、机加工和 铸造三方面技术人员共同商定。
(2)应当尽可能具有一个基面,既是划线基面,同 时又是压型型腔尺寸基准和机械加工用基准面。
铜合金铸件铸造技术 课程
工艺方案的确定
1.确定分型 面 2.基准面的 选择 1)基准面 选择的意义 2)基准面 选择的原则
在确定基准面时,要考虑下述各点原则: (3)取不需加工与待加工面距离变动最小的面作为基面。 (4)基准面的数目应能约束六个自由度,故一般均选择三个基 面(回转体零件则选择二个基面),并力求划线与加工为同一基面。 (5)基准面应当是平整、粗糙度小和尺寸稳定的表面,表面没 有浇口残余、斜度和毛刺(压型分型痕迹)。不用或少用顶杆和活 块形成的面,以保证定位精度。 对于回转体零件用三爪或四爪卡盘定位时,基准面一般选外圆 和某一端面。(如下图所示零件)
铜合金铸件铸造技术 课程
工艺方案的确定
1.确定分型 面
1)确定分 型面的意义
2)确定分 型面的原 则 。
确定分型面,应该遵循下列几个原则: (1)分型面应尽可能的在同一平面上, 如果曲线分型面不可避免存在时,也应作成 有规则的曲线分型。这样不但减少了压型加 工工时;而且便于分型面的吻合和压型的清 理。 (2)尽可能减少压型可拆件(活块)的 数量。过多的可拆件,不仅使压型结构复杂, 而且还会影响铸件精度,缩短压型寿命,并 且降低生产率。
熔模铸造生产,铸件浇注系统形式多样,各有其应 用特点,必须合理选用。
铜合金铸件铸造技术 课程
工艺方案的确定
1.确定分型面 2. 基准面的选择 3.浇注系统的选择
浇注系统的选择是根据铸件的结构、重量、壁厚、轮廓尺寸、合金牌 号及其铸造性能,并结合不同类型浇注系统的特点,本着最大限度的满 足对浇注系统的各项要求进行选择。选择内容主要是确定内浇口在铸件 上的位置、数量及其形状;铸件在型内的浇注位置;浇注系统的类型; 补缩方法;撇渣及出气措施等。 有关浇注系统的选择等内容,在熔模铸造浇注系统设计课程中详细讲 解,本次课程暂不涉及。
工艺分析及方案
——工艺方案确定
铜合金铸件铸造技术课程
铜合金铸件铸造技术 课程
铸造工艺方案确定
一、 二、 三、 确定分型面 基准面的选择 浇注系统的选择
铜合金铸件铸造技术 课程
工艺方案的确定
1.确定分型面 1)确定分型面的意义
为使熔模能从压型 中顺利地取出而将封闭 的压型分成若干个型块, 这些型块的结合面,称 为分型面。
铜合金铸件铸造技术 课程
工艺方案的确定
1.确定分型 面
1)确定分 型面的意义
2)确定分 型面的原则
(3)分型面应尽量不通过熔模的某一完 整表面,特别是基准面。因为分型面不可 避免地要在熔模上留下分型痕迹和铸造斜 度。 (4)应确定上型、下型各构成熔模的那 些部分。确定开型过程中应使熔模保持在 设计者预先确定的位置上。设有起模装置 的压型,开型后,熔模务必留在设有起模 装置的一压型内。 (5)上压型内型腔体积应尽量小,以减 小上压型的体积和重量,从而便于操作。 一个分型面要同时满足上述要求是困难的, 但至少应保証熔模能从压型内顺利取出和 满足铸件的基本要求。
要点:
铜合金铸件铸造技术 课程
工艺方案的确定
1.确定分型面 2.基准面的选 择 1)基准面选 择的意义 2)基准面选 择的原则
在确定基准面时,要考虑下述各点原则:
(1)基准面应是尺寸比較稳定的表面。尽可能不 用由顶杆和可拆垫嵌块形成的表面。非采用这些表面 不可时,也应当选择当頂杆、活块移动时,不导致精 度降低的表面。铜合金铸件铸造技术 课程
工艺方案的确定
1.确定分 型面
2.基准面 的选择 3.浇注系 统的选择
专设冒口的浇注系统 采用底注式浇冒口系统
1-冒口 2-排气道 3-铸件 4-集渣包 5-直浇道
铸件热节 D=115mm D1=1.6D=184mm D2=0.9D=110mm D3=1.3D=143mm H=1.6D=184mm h=15mm