粉末冶金常用烧结方法
粉末冶金烧结工艺
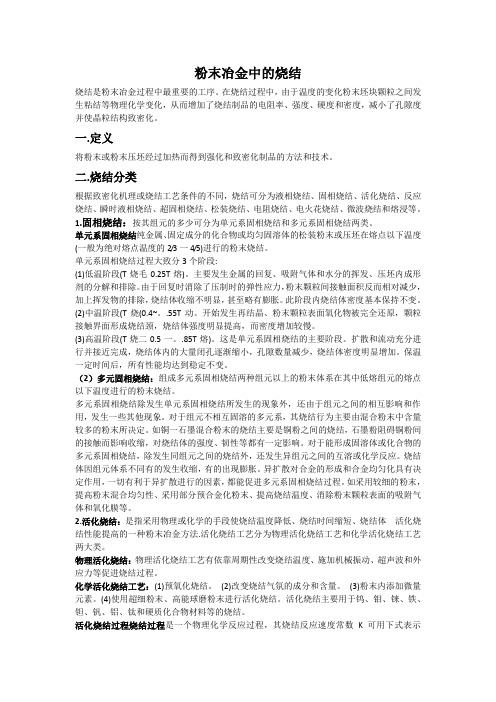
粉末冶金中的烧结烧结是粉末冶金过程中最重要的工序。
在烧结过程中,由于温度的变化粉末坯块颗粒之间发生粘结等物理化学变化,从而增加了烧结制品的电阻率、强度、硬度和密度,减小了孔隙度并使晶粒结构致密化。
一.定义将粉末或粉末压坯经过加热而得到强化和致密化制品的方法和技术。
二.烧结分类根据致密化机理或烧结工艺条件的不同,烧结可分为液相烧结、固相烧结、活化烧结、反应烧结、瞬时液相烧结、超固相烧结、松装烧结、电阻烧结、电火花烧结、微波烧结和熔浸等。
1.固相烧结:按其组元的多少可分为单元系固相烧结和多元系固相烧结两类。
单元系固相烧结纯金属、固定成分的化合物或均匀固溶体的松装粉末或压坯在熔点以下温度(一般为绝对熔点温度的2/3一4/5)进行的粉末烧结。
单元系固相烧结过程大致分3个阶段:(1)低温阶段(T烧毛0.25T熔)。
主要发生金属的回复、吸附气体和水分的挥发、压坯内成形剂的分解和排除。
由于回复时消除了压制时的弹性应力,粉末颗粒间接触面积反而相对减少,加上挥发物的排除,烧结体收缩不明显,甚至略有膨胀。
此阶段内烧结体密度基本保持不变。
(2)中温阶段(T烧(0.4~。
.55T动。
开始发生再结晶、粉末颗粒表面氧化物被完全还原,颗粒接触界面形成烧结颈,烧结体强度明显提高,而密度增加较慢。
(3)高温阶段(T烧二0.5一。
.85T熔)。
这是单元系固相烧结的主要阶段。
扩散和流动充分进行并接近完成,烧结体内的大量闭孔逐渐缩小,孔隙数量减少,烧结体密度明显增加。
保温一定时间后,所有性能均达到稳定不变。
(2)多元固相烧结:组成多元系固相烧结两种组元以上的粉末体系在其中低熔组元的熔点以下温度进行的粉末烧结。
多元系固相烧结除发生单元系固相烧结所发生的现象外,还由于组元之间的相互影响和作用,发生一些其他现象。
对于组元不相互固溶的多元系,其烧结行为主要由混合粉末中含量较多的粉末所决定。
如铜一石墨混合粉末的烧结主要是铜粉之间的烧结,石墨粉阻碍铜粉间的接触而影响收缩,对烧结体的强度、韧性等都有一定影响。
粉末冶金新技术-烧结

用SPS制取块状纳米晶Fe90Zr7B3软磁的过程是: 先将由非 晶薄带经球磨制成的50~150μm非晶粉末装入WC/Co合金 模具内,并在SPS烧结机上烧结(真空度1×10-2Pa以下、升温 速度0.09~1.7K/s、温度673~873K、压力590MPa), 再把所 得的烧结体在1×10-2Pa真空下、以3 7K/s速度加热到923K、 保温后而制成。材料显示较好的磁性能:最大磁导率29800、 100Hz下的动态磁导率3430, 矫顽力12A/m。
3
双频微波烧结炉 生产用大型微波烧结炉 已烧结成多种材料:如陶瓷和铁氧体等材料。另 外,在日本又开发出相似的毫米波烧结技术,并成功 地在2023K下保温1h烧结成全致密的AlN材料。
4
2.爆炸压制技术 爆炸压制又称冲击波压制是一种有前途的工艺
方法,它在粉末冶金中发挥了很重要的作用, 爆炸压 制时,只是在颗粒的表面产生瞬时的高温,作用时间 短,升温和降温速度极快。适当控制爆炸参数,使得 压制的材料密度可以达到理论密度的90%以上,甚至 达到99%。
3)快速脉冲电流的加入, 无论是粉末内的放电部位还是焦耳 发热部位, 都会快速移动, 使粉末的烧结能够均匀化。
11
与传统的粉末冶金工艺相比,SPS工艺的特点是:
• 粉末原料广泛:各种金属、非金届、合金粉末,特别是 活性大的各种粒度粉末都可以用作SPS 烧结原科。
• 成形压力低:SPS烛结时经充分微放电处理,烧结粉末表 面处于向度活性化状态.为此,其成形压力只需要冷压烧 结的l/10~1/20。
17
SPS制备软磁材料 通常用急冷或喷射方法可得到FeMe(Nb、Zr、Hf)B的非 晶合金,在稍高于晶化温度处理后, 可得到晶粒数10nm,具有 体心立方结构,高Bs 、磁损小的纳米晶材料。但非晶合金目 前只能是带材或粉末, 制作成品还需要将带材重叠和用树脂固 结, 这使得成品的密度和Bs均变低。近年, 日本采用SPS工艺研 究FeMeB块材的成形条件及磁性能。
粉末烧结技术
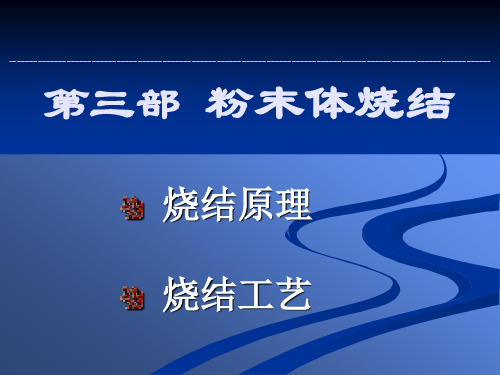
加压烧结—加压和加热同时并用,以达到消除孔
隙的目的,从而大幅度提高粉末制品的性能。常用
的加压烧结工艺有热压、热等静压及烧结-热等静压。
热压—将粉末装在压模内,在加压的同时把粉末加热到熔
点以下,使之加速烧结成比较均匀致密的制品。
热等静压—把粉末压坯或把装入特制容器内的粉末置于热
等静压机高压容器内,使其烧结成致密的材料或零件的过 程。
烧结-热等静压—把压坯放入烧结-热等静压设备的高压容
器内,先进行脱蜡、烧结,再充入高压气体进行热等静压。
反应烧结—先将原材料(如制备Si3N4时使用Si粉)
粉末以适当方式成形后,在一定气氛中(如氮气)
加热发生原位反应合成所需的材料并同时发生烧结。
微波烧结—材料内部整体地吸收微波能并被加热,
使得在微波场中试样内部的热梯度和热流方向与常规 烧结的试样相反。
电火花等离子烧结—也叫等离子活化烧结或电火
花等离子烧结,是利用粉末间火花放电多产生的等
离子活化颗粒,同时在外力作用下进行的一种特殊
烧结方法。
真空热压烧结炉图
微波生物陶瓷烧结炉图
微波烧结炉图
热等静压烧结炉图
放电等离子烧结炉图
物理 化学变化
烧结后期还可能出现二次再结还可能发生固相的溶解与析出。
烧结驱动力
烧结的驱动力----一般为体系的表面能和缺陷能。烧
结实际上是体系表面能和缺陷能降低的过程。通常体
系能量的降低靠的是高温热能激活下的物质传递过程。
烧结原动力----烧结颈部与粉末颗粒其它部位之间存 在化学位差。
扩散机制将发生孔隙的孤立、球化及收缩。
氧化铝陶瓷典 型的不同烧结 阶段显微结构
不锈钢粉末烧结

不锈钢粉末烧结不锈钢粉末烧结,是一种常用的金属粉末冶金加工技术。
该技术可以制备出高密度、高强度、高精度的不锈钢零件,具有良好的耐腐蚀性、耐高温性和耐磨性。
下面将详细介绍不锈钢粉末烧结的工艺流程、特点及应用。
一、不锈钢粉末烧结的工艺流程不锈钢粉末烧结的工艺流程主要包括原料制备、粉末混合、压制成型、烧结处理和后续加工等环节。
1. 原料制备不锈钢粉末烧结的原料主要包括不锈钢粉末、添加剂和溶剂。
其中,添加剂通常包括增塑剂、润滑剂、流动剂和抗氧化剂等,用于改善粉末的流动性、压制性和烧结性。
2. 粉末混合将原料按一定比例混合均匀,可以通过机械混合、湿法混合和干法混合等方法进行。
3. 压制成型将混合好的粉末放入模具中,施加一定的压力进行压制成型,常用的压制方式有单向压制、等静压和注射成型等。
4. 烧结处理将压制成型后的零件放入高温炉中,进行烧结处理。
该过程主要包括初期加热、恒温保温和冷却等步骤,以实现不锈钢粉末的烧结和致密化。
5. 后续加工经过烧结处理后的不锈钢零件通常需要进行后续加工,以达到所需的形状和尺寸。
常用的后续加工方式有磨削、铣削、车削和抛光等。
1. 高精度:不锈钢粉末烧结可以制备出高精度、高精密度的零件,可达到精度在0.1mm以内。
2. 高强度:经过烧结处理后的不锈钢零件具有很高的强度和硬度,可达到1300MPa以上。
3. 耐腐蚀:不锈钢粉末烧结的零件具有良好的耐腐蚀性,能够在恶劣的环境下长期使用。
4. 耐高温:不锈钢粉末烧结的零件具有很好的耐高温性能,能够在高温环境下使用。
5. 环保:不锈钢粉末烧结的过程中不会产生废水、废气和废渣等污染物,是一种相对环保的加工技术。
三、不锈钢粉末烧结的应用不锈钢粉末烧结技术具有广泛的应用前景,目前已被应用于航空、航天、汽车、电子、机械制造等领域。
具体应用包括:1. 制造高精度的航空零部件,如发动机叶片、涡轮叶片等。
2. 制造高强度、高硬度的汽车零部件,如齿轮、减震器等。
粉末冶金的烧结技术

粉末冶金的烧结技术粉末冶金是一种通过将金属或非金属粉末在一定条件下,加工成具有一定形状和尺寸的零部件的方法。
烧结技术是粉末冶金中的关键步骤之一,它将粉末颗粒通过加热并施加压力使其质点之间结合得更加牢固,形成一体化的零部件。
本文将对粉末冶金的烧结技术进行深入探讨。
一、烧结技术的基本原理和过程烧结技术是将粉末颗粒通过加热至其熔点以下,但高于材料的再结晶温度,同时施加压力,使粉末颗粒发生结合,形成一体化的零部件。
其基本原理是利用了粉末颗粒与粉末颗粒之间的扩散作用和表面张力降低效应。
烧结过程中,颗粒间的间隙先得到迅速消除,然后颗粒之间产生再结晶,通过扩散使粒间结合更为牢固。
整个烧结过程可以分为初期活化期、再结晶期和液相期三个阶段。
初期活化期是指在烧结过程开始的阶段,颗粒发生活化并形成结合,此时烧结坯体变得更为致密。
再结晶期是指烧结坯体中增强再结晶的发生。
液相期是指在达到受结合的颗粒之间的最小距离后,材料产生液相,并通过液相扩散加快了颗粒间的结合。
在这个过程中,烧结坯体结构的致密度和强度会显著提高。
二、烧结技术的主要参数在进行粉末冶金的烧结过程中,有许多参数需要注意和控制,如温度、压力、时间和气氛等。
这些参数会对烧结过程和烧结产品的质量产生重要影响。
1. 温度:温度是烧结过程的关键参数之一。
合适的温度能够使粉末颗粒迅速熔结,并形成均匀的结构。
过高或过低的温度都会影响烧结效果和质量。
2. 压力:在烧结过程中,施加的压力可以使粉末颗粒更加紧密地结合在一起。
增加压力可以提高烧结物品的致密度和强度。
3. 时间:烧结时间是烧结过程中的一个重要参数。
适当的烧结时间可以使粉末颗粒充分结合并形成致密的结构。
时间过长或过短都会影响产品的质量。
4. 气氛:烧结过程中的气氛对烧结质量和产品性能有很大影响。
不同的气氛可以对不同材料产生不同的效果。
常用的烧结气氛有氢气、氮气、氧气和真空等。
三、烧结技术的应用和优点烧结技术在现代工业中有着广泛的应用,尤其是在金属材料和陶瓷材料的制备过程中。
粉末冶金烧结方法

粉末冶金烧结方法嘿,朋友们!今天咱就来好好聊聊粉末冶金烧结方法。
你说这粉末冶金啊,就像是一场奇妙的魔法秀。
把那些细细小小的粉末们聚集在一起,通过烧结这个神奇的过程,让它们变成坚固又好用的东西。
烧结呢,其实就好比是让这些粉末小伙伴们开一场盛大的聚会。
它们在高温的环境下,彼此拥抱、融合,慢慢变得亲密无间,最后形成一个整体。
常见的烧结方法有好几种呢。
比如说固相烧结,这就像是一群小伙伴手拉手,紧紧地靠在一起,不需要太多其他的东西来帮忙,它们自己就能变得很牢固。
还有液相烧结,这就有点像在聚会里加了一些特殊的“胶水”,让粉末们能更好地结合在一起,形成更结实的物件。
那烧结过程中温度可重要啦!就像做饭时火候的把握一样,温度太高或者太低可都不行哦。
温度太低,粉末们就没办法好好地融合;温度太高呢,又可能会把它们给“烤坏”了。
而且啊,时间也是个关键因素呢。
太短了,粉末们还没来得及好好交流感情;太长了,又可能会出现一些意想不到的问题。
这粉末冶金烧结方法,可不只是在工业上有大用处哦。
你想想看,我们生活中的好多东西可能都离不开它呢。
说不定你现在手里拿着的某个小物件,就是通过这种神奇的方法制造出来的呢!那这粉末冶金烧结方法难不难呢?其实啊,就和学骑自行车差不多。
一开始可能会觉得有点难,不知道怎么掌握平衡,怎么踩踏板。
但只要你多练习,慢慢就会找到感觉,变得熟练起来。
咱再回过头来想想,这粉末从小小的一粒粒,变成有用的物件,这过程多神奇呀!就好像是丑小鸭变成白天鹅一样。
所以说呀,这粉末冶金烧结方法可真是个了不起的技术呢!它让那些看似不起眼的粉末,发挥出了大大的作用,为我们的生活带来了好多便利。
是不是很厉害呢?大家可别小瞧了它哟!。
粉末冶金烧结原理

粉末冶金烧结原理
粉末冶金烧结是一种常用的制备金属和陶瓷材料的工艺。
其原理基于粉末颗粒在高温下通过表面扩散和颗粒间的相互作用力而实现的固相结合。
首先,通过研磨和混合的方式将所需的金属或陶瓷粉末混合均匀。
混合的目的是使不同粉末颗粒在烧结过程中能够更好地接触和相互结合。
接下来,将混合后的粉末填充到模具中,并施加一定的压力。
压力的作用是使粉末颗粒之间产生一定的接触力,这样可以促进烧结过程中的颗粒扩散。
然后,将填充好的模具放入烧结炉中,进行高温处理。
在高温下,粉末颗粒表面会发生表面扩散,即颗粒表面的原子或离子会向颗粒内部扩散。
同时,由于高温下颗粒间的相互作用力增强,颗粒之间产生局部的结合。
经过一段时间的高温处理,粉末颗粒表面扩散和颗粒间的结合逐渐扩展到整个颗粒,形成了一个密实的整体。
这个过程称为固相烧结,通过这种方式,粉末的体积会明显减小。
最后,将烧结后的样品冷却并取出,进行进一步的加工和处理。
根据需要,可以对烧结样品进行后续的热处理、机加工等工艺步骤。
总之,粉末冶金烧结是一种通过高温和压力作用下,将粉末颗
粒固相结合的制备材料的方法。
通过控制烧结过程中的温度、压力和时间等参数,可以获得具有预期性能的金属和陶瓷材料。
粉末冶金材料的烧结
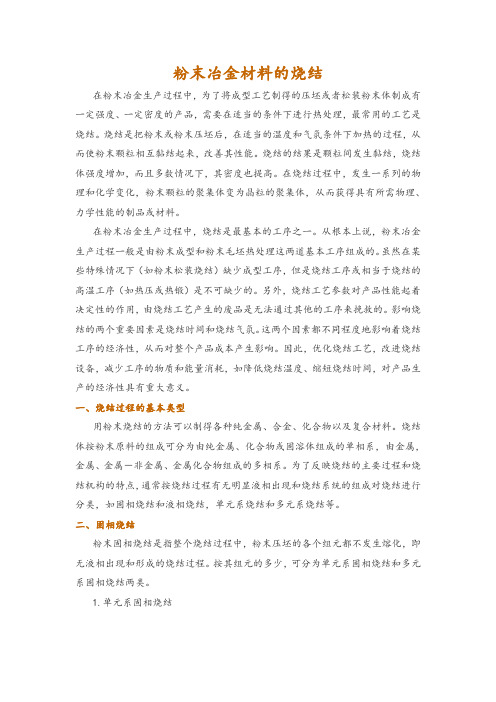
粉末冶金材料的烧结在粉末冶金生产过程中,为了将成型工艺制得的压坯或者松装粉末体制成有一定强度、一定密度的产品,需要在适当的条件下进行热处理,最常用的工艺是烧结。
烧结是把粉末或粉末压坯后,在适当的温度和气氛条件下加热的过程,从而使粉末颗粒相互黏结起来,改善其性能。
烧结的结果是颗粒间发生黏结,烧结体强度增加,而且多数情况下,其密度也提高。
在烧结过程中,发生一系列的物理和化学变化,粉末颗粒的聚集体变为晶粒的聚集体,从而获得具有所需物理、力学性能的制品或材料。
在粉末冶金生产过程中,烧结是最基本的工序之一。
从根本上说,粉末冶金生产过程一般是由粉末成型和粉末毛坯热处理这两道基本工序组成的。
虽然在某些特殊情况下(如粉末松装烧结)缺少成型工序,但是烧结工序或相当于烧结的高温工序(如热压或热锻)是不可缺少的。
另外,烧结工艺参数对产品性能起着决定性的作用,由烧结工艺产生的废品是无法通过其他的工序来挽救的。
影响烧结的两个重要因素是烧结时间和烧结气氛。
这两个因素都不同程度地影响着烧结工序的经济性,从而对整个产品成本产生影响。
因此,优化烧结工艺,改进烧结设备,减少工序的物质和能量消耗,如降低烧结温度、缩短烧结时间,对产品生产的经济性具有重大意义。
一、烧结过程的基本类型用粉末烧结的方法可以制得各种纯金属、合金、化合物以及复合材料。
烧结体按粉末原料的组成可分为由纯金属、化合物或固溶体组成的单相系,由金属,金属、金属-非金属、金属化合物组成的多相系。
为了反映烧结的主要过程和烧结机构的特点,通常按烧结过程有无明显液相出现和烧结系统的组成对烧结进行分类,如固相烧结和液相烧结,单元系烧结和多元系烧结等。
二、固相烧结粉末固相烧结是指整个烧结过程中,粉末压坯的各个组元都不发生熔化,即无液相出现和形成的烧结过程。
按其组元的多少,可分为单元系固相烧结和多元系固相烧结两类。
1.单元系固相烧结单元系固相烧结,即单一粉末成分的烧结。
例如各种纯金属的烧结、预合金化粉末的烧结、固定成分的化合物粉末的烧结等,均为单元系固相烧结。
- 1、下载文档前请自行甄别文档内容的完整性,平台不提供额外的编辑、内容补充、找答案等附加服务。
- 2、"仅部分预览"的文档,不可在线预览部分如存在完整性等问题,可反馈申请退款(可完整预览的文档不适用该条件!)。
- 3、如文档侵犯您的权益,请联系客服反馈,我们会尽快为您处理(人工客服工作时间:9:00-18:30)。
粉末冶金常用烧结方法 Document serial number【UU89WT-UU98YT-UU8CB-UUUT-UUT108】粉末冶金常用烧结方法《often-used teehnigues in powder metallurgy sintering》摘要:粉末冶金是一门重要的零件成形技术。
粉末冶金新技术、新工艺的不断出现,必将促进高技术产业的快速发展,也必将带给材料工程和制造技术光明的前景。
目前,我国粉末冶金行业整体技术水平低下、工艺装备落后,与国外先进技术水平相比存在较大差距。
因此,大力发展粉末冶金新技术的研究,对提高我国粉末冶金产品的档次和技术水平,缩短与国外先进水平的差距具有非常重要的意义。
粉末冶金烧结就是将粉末或粉末压坯经过加热而得到强化和致密化制品的方法和技术。
烧结是粉末冶金过程中最重要的工序。
在烧结过程中,由于温度的变化粉末坯块颗粒之间发生粘结等物理化学变化,从而增加了烧结制品的电阻率、强度、硬度和密度,减小了孔隙度并使晶粒结构致密化。
Abstract:Powder metallurgy forming technology is an important part。
New technology of powder metallurgy technologies, emerging, will promote the rapid development of high-tech industry, will bring brighter prospects of material engineering and manufacturing technology. At present, the low overall level of powder metallurgy industry in China, process and equipment behind, compared with foreign advanced technical level there is a large gap. Therefore, development of study on the new technology of powder metallurgy, on improving the grade of powder metallurgical products and technology, reduced the gapwith foreign advanced level has very important significance. Powder metallurgy sintering powder or powder Compact is strengthening and densification of products by the heating method and technology. Sintering is the most important process of powder metallurgy process. During the sintering process, due to changes in temperature of the Compact of powder particles bond between physical and chemical changes, thus increasing the resistivity of sintered products, strength, hardness and density, reduces the porosity of densification and grain structure.关键词:粉末冶金(Powder metallurgy),烧结(Sintering),技术(technology),粉末冶金烧结是使压坯或松装粉末体进一步结合起来,以提高强度及其他性能的一种高温处理工艺。
它是粉末冶金的重要工序之一。
在烧结过程中粉末颗粒要发生相互流动、扩散、熔解、再结晶等物理化学过程,使粉末体进一步致密,消除其中的部分或全部孔隙。
烧结方法通常有以下几类:液相烧结?粉末压坯中如果有两种以上的组元,烧结有可能在某种组元的熔点以上进行,因而烧结时粉末压坯中出现少量的液相。
加压烧结在烧结时,对粉末体施加压力,以促进其致密化过程。
加压烧结有时与热压(hot pressing)为同义词,热压是把粉末的成形和烧结结合起来,直接得到制品的工艺过程。
活化烧结在烧结过程中采用某些物理的或化学的措施,使烧结温度大大降低,烧结时间显着缩短,而烧结体的性能却得到改善和提高。
电火花烧结粉末体在成形压制时通入直流电和脉冲电,使粉末颗粒间产生电弧而进行烧结;在烧结时逐渐地对工件施加压力,把成形和烧结两个工序合并在一起。
一、粉末固相烧结(solid-state sintering of powder)松装粉末或压坯在烧结过程中组元不发生熔化的粉末烧结方法。
粉末固相烧结按其组元多少可分为单元系固相烧结和多元系固相烧结两类。
单元系固相烧结纯金属、固定成分的化合物或均匀固溶体的松装粉末或压坯在熔点以下温度(一般为绝对熔点温度的2/3~4/5)进行的粉末烧结。
单元系固相烧结过程除发生粉末颗粒间粘结、致密化和纯金属的组织变化外,不存在组织间的溶解,也不出现新的组成物或新相。
又称为粉末单相烧结。
单元系固相烧结过程大致分3个阶段:(1)低温阶段(T烧≤熔)。
主要发生金属的回复、吸附气体和水分的挥发、压坯内成形剂的分解和排除。
由于回复时消除了压制时的弹性应力,粉末颗粒间接触面积反而相对减少,加上挥发物的排除,烧结体收缩不明显,甚至略有膨胀。
此阶段内烧结体密度基本保持不变。
(2)中温阶段(T烧≤~熔)。
开始发生再结晶、粉末颗粒表面氧化物被完全还原,颗粒接触界面形成烧结颈,烧结体强度明显提高,而密度增加较慢。
(3)高温阶段(T烧=~熔)。
这是单元系固相烧结的主要阶段。
扩散和流动充分进行并接近完成,烧结体内的大量闭孔逐渐缩小,孔隙数量减少,烧结体密度明显增加。
保温一定时间后,所有性能均达到稳定不变。
影响单元系固相烧结的因素主要有烧结组元的本性、粉末特性(如粒度、形状、表面状态等)和烧结工艺条件(如烧结温度、时间、气氛等)。
增加粉末颗粒间的接触面积或改善接触状态,改变物质迁移过程的激活能,增加参与物质迁移过程的原子数量以及改变物质迁移的方式或途径,均可改善单元系固相烧结过程。
多元系固相烧结两种组元以上的粉末体系在其中低熔组元的熔点以下温度进行的粉末烧结。
多元系固相烧结除发生单元系固相烧结所发生的现象外,还由于组元之间的相互影响和作用,发生一些其他现象。
对于组元不相互固溶的多元系,其烧结行为主要由混合粉末中含量较多的粉末所决定。
如铜一石墨混合粉末的烧结主要是铜粉之间的烧结,石墨粉阻碍铜粉间的接触而影响收缩,对烧结体的强度、韧性等都有一定影响。
对于能形成固溶体或化合物的多元系固相烧结,除发生同组元之间的烧结外,还发生异组元之间的互溶或化学反应。
烧结体因组元体系不同有的发生收缩,有的出现膨胀。
异扩散对合金的形成和合金均匀化具有决定作用,一切有利于异扩散进行的因素,都能促进多元系固相烧结过程。
如采用较细的粉末,提高粉末混合均匀性、采用部分预合金化粉末、提高烧结温度、消除粉末颗粒表面的吸附气体和氧化膜等。
在决定烧结体性能方面,多元系固相烧结时的合金均匀化比烧结体的致密化更为重要。
多元系粉末固相烧结后既可得单相组织的合金,也可得多相组织的合金,这可根据烧结体系合金状态图来判断二、粉末液相烧结粉末液相烧结(liquid phase sintering of powder)具有两种或多种组分的金属粉末或粉末压坯在液相和固相同时存在状态下进行的粉末烧结。
此时烧结温度高于烧结体中低熔成分或低熔共晶的熔点。
由于物质通过液相迁移比固相扩散要快得多,烧结体的致密化速度和最终密度均大大提高。
液相烧结工艺已广泛用来制造各种烧结合金零件、电接触材料、硬质合金和金属陶瓷等。
类型根据烧结过程中固相在液相中的溶解度不同,液相烧结可分为3种类型。
(1)固相不溶于液相或溶解度很小,称为互不溶系液相烧结。
如w-Cu 、w-Ag 等假合金以及A12O 3-Cr 、Al 2O 3一Cr-Co —Ni 、A12O 3一Cr —W 、BeO 一Ni 等氧化物-金属陶瓷材料的烧结。
(2)固相在液相中有一定的溶解度,在烧结保温期间,液相始终存在,称为稳定液相烧结。
如Cu —Pb 、w —Cu —Ni 、WC 一Co 、TiN 一Ni 等材料的烧结。
(3)因液相量有限,又因固相大量溶入而形成固溶体或化合物,使得在烧结保温后期液相消失,这类液相烧结称为瞬时液相烧结。
如Fe —Cu(<10%)、Fe —Ni —Al 、Ag —Ni 、Cu —Sn 等混合粉末材料的烧结。
条件液相烧结能否顺利完成,达到完全致密化,主要决定于同液相性质有关的3个基本条件:(1)液相对固相颗粒表面的润湿性要好,其润湿角口<90。
,最好是接近于零度。
任何有利于提高液相对固相润湿性的措施都有利于液相烧结。
(2)固相在液相中有一定的溶粉fen 解度,而液相在固相中的溶解度很小,或者不溶解。
(3)液相要有一定的数量。
一般以冷却时能填满固相颗粒间的间隙为限。
通常以20%~50%(体积分数)为宜。
致密化过程大致可分为3个阶段。
(1)液相生成和颗粒重排。
当液相生成后,因液相润湿固相,并渗入颗粒间隙,如果液相量足够,固相颗粒将完全被液相包围而近似于悬浮状态,在液相表面张力作用下发生位移、调整位置,从而达到最紧密的排列。
在这一阶段,烧结体密度增加迅速。
(2)固相溶解和析出。
由于固相颗粒大小不同、表面形状不规整、颗粒表面备部位的曲率不同,溶解于液相的平衡浓度不相等,由浓差引起颗粒之间和颗粒不同部位之间的物质迁移也就不一致。
小颗粒或颗粒表面曲率大的部位溶解较多;另一方面,溶解的物质又在大颗粒表面或其有负曲率的部位析出。
结果是固相颗粒外形逐渐趋于球形或其他规则形状,小颗粒逐渐缩小或消失,大颗粒长大,颗粒更加靠拢。
但因在此阶段充分进行之前,烧结体内气孔已基本消失,颗粒间距已很小,故致密化速度显着减慢。
(3)固相骨架形成。
液相烧结经过上述两阶段后,固相颗粒相互靠拢,颗粒间彼此粘结形成骨架,剩余的液相充填于骨架的间隙。
此时以固相烧结为主,致密化速度显着减慢,烧结体密度基本不变。
三、电火花烧结电火花烧结也可称为电活化压力烧结,它是利用粉末间火花放电所产生的高温,并且同时受外应力作用的一种特殊烧结方法。