精益生产各kpi计算公式汇总
精益生产常用指标公式

Methods-Time Measurement)
TMU
(time-measurement unit)
R.W.F (Ready-Work
Facfor)
所有动作分八个基本要素,每执行一个要素动 作时根据动作的困难决定 W/F 数,根据时间表 计算净作业时间的方法
1RU=0.001 分
基本动作分析法
利用科学家研究出来的 17 个动作符号测试作业 动作时尽量以最小单位来分割的方法
PAC
(Performance Analysis & Control)
为了能做到只要作业努力就能提高及维持能力 的效率管理方式的一种。
*作业效率 标准工时 可用工时-损失工时
MTM
(Motion-Time
Measurement
Or
所有作业用基本动作来分析,根据指定的基本 动作的性质和条件提前给予时间的方法 给予基本动作的时间值的单位 1 分=1.667TMU 1 秒=27.8TMU
实际生产工时效率
损失工时以外的纯作业时间和实际生产所用的 时间之比
实际生产率
生产产品所需的时间和纯生产所需的时间内生产产品的 能力(每机型经过商讨后定标准机型)
标准工时 × 作业工时 间 标准时间 实际时间
460 标准机型标准时
效率管理
为了减少生产要素的损耗,用一线监督人员的 指导监督来达到适当地提高并维持作业人员对 作业的态度的一种管理方式
效率损失
按标准方法进行作业时需要的最少时间和与实 际作业中所用的时间之差的比
综合损耗
损耗的总合计
综合能力
按标准方法进行作业时需要的最少时间和与实 际生产所用的时间之差的比
净作业时间 × 100 TACT TIME
KPI考核指标计算大全

KPI考核指标计算大全关键绩效指标(KPI)是衡量一个组织或个人绩效的关键标准,可以帮助组织或个人评估其实现目标的情况并做出相应的改进。
在不同的行业和领域,KPI的具体计算方法会有所不同。
下面将介绍一些常见的KPI指标和计算方法。
销售KPI指标:1.销售额:销售额是衡量一个组织或个人销售业绩的重要指标。
计算公式为:销售额=销售数量×单价。
2.销售增长率:销售增长率是衡量销售业绩增长的指标。
计算公式为:销售增长率=(本期销售额-上期销售额)/上期销售额×100%。
3.销售转化率:销售转化率是衡量销售机会转化为实际销售的比例。
计算公式为:销售转化率=完成销售的客户数量/总销售机会数量×100%。
生产KPI指标:1.产量:产量是指生产单位时间内完成的产品数量。
计算公式为:产量=完成产品的数量。
2.产能利用率:产能利用率是衡量生产设备或工人产能利用情况的指标。
计算公式为:产能利用率=实际产能/理论产能×100%。
3.产品质量合格率:产品质量合格率是衡量产品质量的指标。
计算公式为:产品质量合格率=合格产品数量/总产品数量×100%。
财务KPI指标:1.利润率:利润率是衡量利润占总收入的比例。
计算公式为:利润率=利润/总收入×100%。
2.资产回报率:资产回报率是衡量资产在产生收入时的效率。
计算公式为:资产回报率=总收入/总资产。
3.现金流量:现金流量是衡量一个组织或个人现金流入和流出情况的指标。
计算公式为:现金流入-现金流出。
客户服务KPI指标:1.客户满意度:客户满意度是衡量客户对产品或服务满意程度的指标。
计算公式为:满意客户数量/总客户数量×100%。
2.投诉率:投诉率是衡量客户投诉数量占总客户数量的比例。
计算公式为:投诉率=投诉数量/总客户数量×100%。
以上是一些常见的KPI指标和计算方法,针对不同的组织或个人情况,还可以根据实际情况确定其他KPI指标。
制造业各部门的KPI考核指标
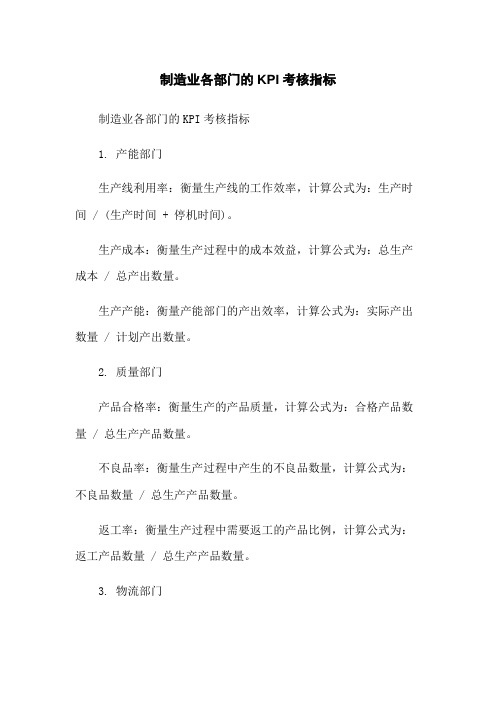
制造业各部门的KPI考核指标
制造业各部门的KPI考核指标
1. 产能部门
生产线利用率:衡量生产线的工作效率,计算公式为:生产时间 / (生产时间 + 停机时间)。
生产成本:衡量生产过程中的成本效益,计算公式为:总生产成本 / 总产出数量。
生产产能:衡量产能部门的产出效率,计算公式为:实际产出数量 / 计划产出数量。
2. 质量部门
产品合格率:衡量生产的产品质量,计算公式为:合格产品数量 / 总生产产品数量。
不良品率:衡量生产过程中产生的不良品数量,计算公式为:不良品数量 / 总生产产品数量。
返工率:衡量生产过程中需要返工的产品比例,计算公式为:返工产品数量 / 总生产产品数量。
3. 物流部门
仓储周转率:衡量仓储部门的效率,计算公式为:(年度出库量 + 年度入库量)/ 2 / 平均库存量。
准时交货率:衡量配送部门的准时交货能力,计算公式为:按时交货客户数量 / 总客户订单数量。
订单处理时效:衡量订单处理的效率,计算公式为:(订单处理完成时间订单接收时间)/ 订单数量。
4. 设备部门
设备利用率:衡量设备的使用效率,计算公式为:设备运行时间 / (设备运行时间 + 停机时间)。
设备故障率:衡量设备的故障频率,计算公式为:故障次数 / 设备运行时间。
设备维修时效:衡量设备维修的效率,计算公式为:(设备修复完成时间报修时间)/ 维修次数。
注意:以上指标仅为参考,实际的KPI考核指标应根据企业自身情况进行调整和设定。
KPI计算公式汇总(初订版)
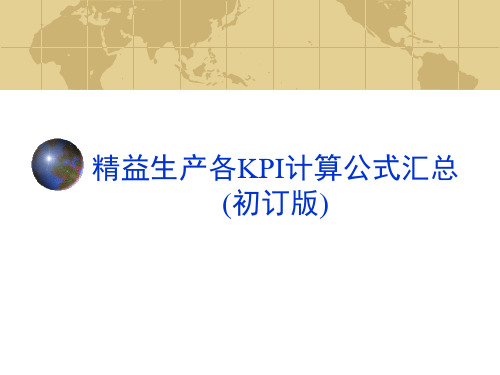
VA / NVA---value added /non value added 增值率与非增值率
增值时间:站在客户立场看制造过程中的增值动作和时间 如:改变形状、改变性能、组装、包装等 非增值的:隻增加了成本但未為產品增加如顧客所定 義的價值(浪費)的活動
增值率
=
X 100% 制造周期(Manufacturing cycle time)
增值时间(Value added time)
非增值比率计算方式:
非增值率= 1 - 增值率
Labor Productivity -- 工人生產力
操作工的数量等于总的单件产品的人工工作量除以单条生 产线之节拍时间
操作工数量 =
人工工作总量(VA + NVA ) 生产线节拍时间
注:(VA + NVA)指包括所有增值与非增值时间
底部(鞋材)FTT: = 合格率(大底)x合格率(PU) x合格率(PH) 例:= 0.98 x 0.89 x 0.90 = 0.78 = 78%
BTS ---Build To Schedule 準交率(一)
定义:衡量按考量数量,混合生产和順序生產的计划生产产 品的能力。 準交率 =(數量達成率)X(SIZE達成率)X(順序達成率) 實際生產數量 數量達成率= 計劃生產數量 依計劃尺碼實際生產 SIZE達成率= 實際生產尺碼數量 實際依計劃順序生產 順序達成率= 計劃生產順序
5
T/T & C/T 的聯系
如果Takt time(节拍時間)不等於Cycle Time (产距时 间),則流程存在不平衡问题。 當T/T 等于C/T 时,表示沒有生产过剩,且員工效率刚好 满足客戶需求
Process Time 流程時間= Cycle time 產距時間 x 操作員人數 Lead Time 流程週期 = Process Time 流程時間 + (在制品數 x 產距時間)
【正式版】精益生产各计算公式汇总PPT
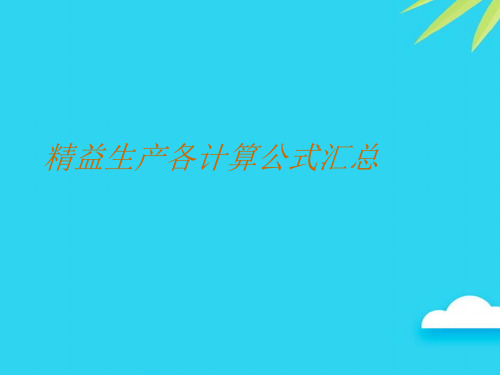
BTS ---Build To Schedule 準交率(一)
定义:衡量按考量数量,混合生产和順序生產的计划生产产 品的能力。
準交率 =(數量達成率)X(SIZE達成率)X(順序達成率)
數量達成率= 實際生產數量 計劃生產數量
SIZE達成率=
依計劃尺碼實際生產 實際生產尺碼數量
順序達成率=
➢定义:人均产能,每人每小時几双 ➢單位, 每人每小時几双 = 底部总产量 / 工作小時 / 人數
人力包含直接人工,干部,补料員,维修,QC等直接与非直接人力 ➢外包人力不算在內 注:POH或称PPH:pairs/people/hour
TT---Takt Time節拍時間
定义:也称产距时间,指能满足客户需求的每双制造速度
定义:产距时间或周期时间,是指一个人彧一组人在某道工序平均完成一件产品所花的时间。
T裁/C断D--合-TT格ota率=l C(=o机s生t 產總器的成總本故片數障-(瑕时疵+间反修到數)机器正常运转时间的时长) / 2 8非小增异时值*6的常0分:*隻机60增秒加器了成设本但备未為完產品全增加停如顧止客所生定 产时.停机时间的计算公式为
DT=机器故障时间到机器正常运转时间的时长 群体性停机时间只需纪录异常开始到异常结束时的时间.时间不 需累加
注:按分钟计算停工期
Line Balancing rate平衡率
定义:用於衡量流程中各工站節拍符合度的一個綜合比值﹔
單件標準時間
POH---Pairs = 78%
per
operator
平衡率= per hour人均產能
定义:是一个对生产流的计量单位。其定义为产品最长交 付周期时间,即从接受最初原材料开始,到最终成 品出货的消耗时间。
精益生产各绩效指标计算公式汇总教程文件
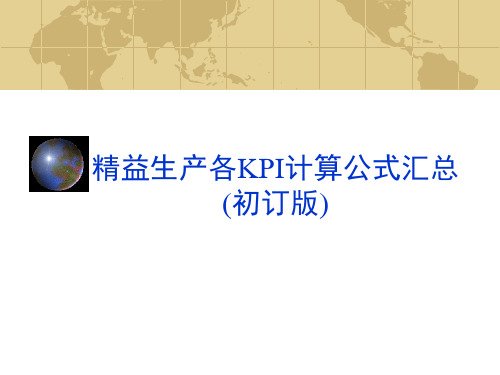
6
QR---Quality Rate合格率
生產/收到的總双(片)數-不合格品 合格率=
生產/收到的總双(片)數
裁断合格率 = 生產的總片數-(瑕疵+反修數) 生產的總片數
生产计划 #9
#10
#11
进度
20
30
50
实60
5
数量达成率= 实际生产数量 计划生产数量
例:实际生产数量 = 95, 计划生产数量 = 100
数量达成率= 95/100 = 0.95 =95%
BTS ---Build To Schedule 準交率(三)
SIZE达成率=依实計际划 生尺产码尺码实数际生量产
注:總片數=每日目標X每雙片數
面部,半成品&底部的合格率:以半双計算
合格率= 半雙總數-(不合格品+反修品)
半雙的總數
不良品率计算方式:
1 – 合格率 = 不良品率
FTT ---First Time Through 直通率
定义:衡量在第一時間里生產出不用反修的無瑕疵产品的能力。
核心价值流FTT: = 合格率 (裁断)X 合格率(半成品)X 合格率(周边)
依计划尺码实际生產=5+30+50=85,实际生产尺码数量=95 SIZE達成率= 85/95 =0.89
BTS准交率 =(数量达成率)X(SIZE达成率) 数量达成率=0.95 SIZE达成率=0.89
BTS = 0.95 x 0.89 = 0.85 = 85%
精益生产常用指标公式

生产率
一般用产量对投入的比
OUT PUT IN PUT
工时 标准时间 (Standard Time)
人或机器能做的或已做的量用时间来表示 熟练程度和技能都达到平均水平的作业人员用 正常速度按规定的作业条件和作业方法生产出 规定质量的产品一个单位时所需要的时间。 用语 详细说明 拥有人员的工时 公式 拥有人员×正常作业时间
TACT TIME(T/T)节拍时间 NECK TIME 瓶颈时间 RATING 等级
制造一件物品时所需要的实际时间 整个工序中 1 个循环作业时间最长的工序时间 作业按标准方法进行时作业速度的快或慢的程 度用数字进行换算的时间
净作业时间 运转率
作业按标准方法进行时所需的最少时间 生产产品所需的时间及实际生产中所用的时间 之比
制造周期、废品率、设备综合效率OEE、停工期、计划完成率、执行的改善建议数、改善成效、
用语 CYCLE TIME(C/T)制造周期
详细说明 每单位(所有)工序中 1 个循环的作业所需的 时间
公式 单位工序 C/T 的和 测试次数 作业时间(460 分) 生产数 最大的 CYCLE TIME 很快:125%;快:100% 一般:85%; 慢:60% CYCLE TIME×RATING(%) NECK TIME × 100 TACT TIME 整个工序 C/T 的和 ×100 NECK TIME×工序数
效率损失
按标准方法进行作业时需要的最少时间和与实 际作业中所用的时间之差的比
综合损耗
损耗的总合计
综合能力
按标准方法进行作业时需要的最少时间和与实 际生产所用的时间之差的比
净作业时间 × 100 TACT TIME
时间观测法
用秒表观测分析作业人员的作业时间或设备运 转的方法
各项KPI计算公式及注意事项

(2)任务(计划)量——产线当天执行的最终计划量,即为 任务(计划)量——产线当天执行的最终计划量,即为
产线当天的任务量。
1
1
线长考核指标 “任务完成率” 任务完成率”
三、定义; 定义;
外在原因影响:指由于非产线原因造成各产线任务没有按时完成, 它包括:待料 (主板,部件)、设备故障、工艺问题、计划调整、待 主板,部件) 抽检(9:00以前送检) 抽检(9:00以前送检)、非产线原因待确认、返工等。 1、待料:由于待主板或某部件造成产线停工而不能按时投入完计 待料: 划量。外在原因影响程度需要有外损工时确认单或正式邮件 通知为据,并严格按照工艺定额计算影响产量台数经车间领 班确认。 2、设备故障:指生产部门由于设备线体、条码打印机等故障致使生 设备故障: 产被迫中断待处理的情况
1
2
线长考核指标 “任务完成率” 任务完成率”
3、由于批量问题造成的待工艺、PQE确认、待分析: 由于产线在 由于批量问题造成的待工艺、PQE确认 待分析: 确认、 生产时出现的批量不良问题,工艺或PQE待相关人员没有及 生产时出现的批量不良问题,工艺或PQE待相关人员没有及 时分析或确认造成的产线主机不能及时入库; 4、返工:如果由于软性故障、电性能故障或其它因产线不可控原因 返工: 造成的产线返工。 5、入其它库别:由于量产机小批量试产要求或非产线原因造成的批 入其它库别: 量不良工艺要求入质检、研发库、待处理库的数量。 6、其它原因:除上述原因外的其它非产线原因造成的产能损失,领 其它原因: 班签字确认后有效;
1
3
线长考核指标 “任务完成率” 任务完成率”
注意事项: 注意事项: 1 2 入质检库数或其它库别的数量及原因需在合格入库量的后面一栏 备注清楚,特别是返修机有的返成内购机一定要标明。 备注清楚,特别是返修机有的返成内购机一定要标明。 待料等其它原因造成产线任务不能完成的, 待料等其它原因造成产线任务不能完成的,要写清楚影响的台数 及原因,并与《外损工时单》原因一致。 及原因,并与《外损工时单》原因一致。