FANUC系统参考点建立
FANUC系统有挡块栅格法返回参考点
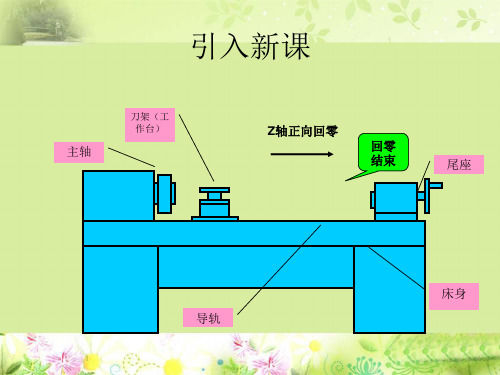
伺服模块
X9.2没有触发
快速接近
减速开关抬起
压下减速开关
超程
负向超程开关
减速开关
正向超程开关
外部接线错误 减速开关损坏
减速开关位置变化
超程
回零 结束
回参考点方向为负向
ZMI
1006
1
回零 结束
负向超程开关
减速开关
正向超程开关负向回零的机床回零 结束X轴负向回零
负向超程开关
减速开关
正向超程开关
(1)工作台快速接近减速开关
快速接近
负向超程开关
减速开关
正向超程开关
(1)工作台快速接近减速开关
• 运动方向设定
参数号
2022
电机旋转方向
• 运动速度设定
参数号
1428
每个轴手动返回参考点的快速移动速度
(2)工作台压下减速开关
• 运动方向
参数号
2022
电机旋转方向
• 运动速度
参数号
1425
每个轴手动返回参考点减速后的速度
• 压下减速开关X9.2(X9.0、X9.1)触发
(X9.0触发X轴减速;X9.1触发Y轴减速;X9.2触发Z轴减速)
(3)减速开关抬起,找到零点
• 运动方向
#7 参数号 #6 #5 ZMI
回零方向设定 #5(ZMI) 0 : 回参考点方向为正向。
#4
#3 #2
#1
#0
1006
• 运动速度
参数号
1 : 回参考点方向为负向。
低速接近
负向超程开关
减速开关
正向超程开关
超程
负向超程开关
减速开关
正向超程开关
FANUC系统的功能(参数信号)

3.1 JOG进给
G100:JOG模式下进给轴正方向选择信号; G102:JOG模式下进给轴负方向选择信号; G010,G011:手动进给速度倍率信号; 参数1423:各轴JOG进给的速度; 参数1002#0:JOG,手动快速和返回参考点时同时控制 轴数;(0:1,1:3)
JOG进给方向选择梯图(X轴正向)
基本连接关系
NC与伺服间采用FSSB- FANUC串行伺服总线技术 (SIEMENS采用PROFIBUS总 线) NC与IO单元间采用IOLink 连 接
系统功能结构框图
SRAM中内容:
CNC参数 PMC参数 加工程序 刀具补偿 用户宏变量
FROM中内容
PMC程序 ROM-CNC软 件
功 能 键 说 明
5.3.2空运行(DRN)
仅对自动运行有效,机床以恒定速度(参数NO1410设 定)运动而不执行程序中所定义的进给速度,用于机床 不安装工件情况下检查机床的运动. 空运行信号DRN(G046.7); 空运行检测信号MDRN(F02.7);
空运行(DRN)梯图
5.3.3 单程序段(SBK)
自动运行期间当单程序段信号(SBK)置1时,执行完当 前程序段后,CNC进入自动运行停止状态. 单程序段运行信号SBK(G046.1); 单程序段检测信号MSBK(F04.3);
选择停止及无条件停止(M01/M00)
5.7程序再启动(SRN)
相关地址
G006.0 SRN 程序再启动 F002.4 SRNMV 程序再启动中
相关参数
7310程序再启动各轴的移动顺序 当设定第1轴=2,第2轴=3,第3轴=4,第4轴=1时,机床以第4, 1,2,3轴的顺序向启动点移动.
程序再启动(SRN)梯图
FANUC数控系统基本参数的操作与设定
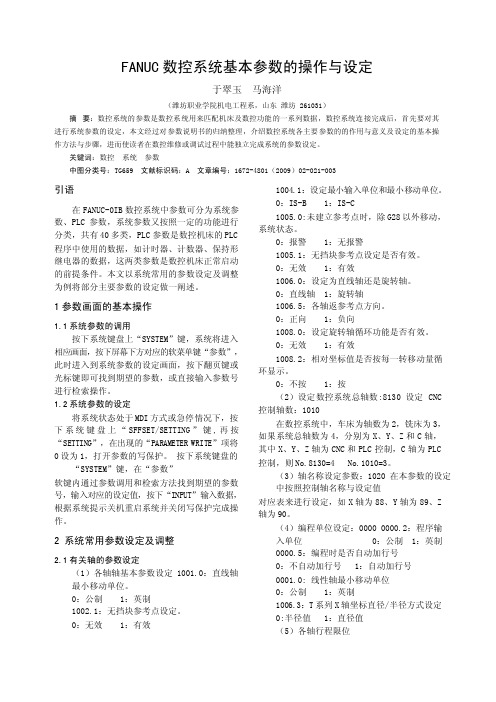
FANUC 数控系统基本参数的操作与设定于翠玉马海洋(潍坊职业学院机电工程系,山东潍坊 261031)摘要:数控系统的参数是数控系统用来匹配机床及数控功能的一系列数据,数控系统连接完成后,首先要对其进行系统参数的设定,本文经过对参数说明书的归纳整理,介绍数控系统各主要参数的的作用与意义及设定的基本操作方法与步骤,进而使读者在数控维修或调试过程中能独立完成系统的参数设定。
关键词:数控系统参数中图分类号:TG659 文献标识码:A 文章编号:1672-4801(2009)02-021-003引语在FANUC-0IB 数控系统中参数可分为系统参数、PLC 参数,系统参数又按照一定的功能进行分类,共有40 多类,PLC 参数是数控机床的PLC 程序中使用的数据,如计时器、计数器、保持形继电器的数据,这两类参数是数控机床正常启动的前提条件。
本文以系统常用的参数设定及调整为例将部分主要参数的设定做一阐述。
1 参数画面的基本操作1.1 系统参数的调用按下系统键盘上“SYSTEM”键,系统将进入相应画面,按下屏幕下方对应的软菜单键“参数”,此时进入到系统参数的设定画面,按下翻页键或光标键即可找到期望的参数,或直接输入参数号进行检索操作。
1.2 系统参数的设定将系统状态处于MDI 方式或急停情况下,按下系统键盘上“SFFSET/SETTING ”键, 再按“SETTING”,在出现的“PARAMETER WRITE”项将0 设为1,打开参数的写保护。
按下系统键盘的“SYSTEM”键,在“参数”软键内通过参数调用和检索方法找到期望的参数号,输入对应的设定值,按下“INPUT”输入数据,根据系统提示关机重启系统并关闭写保护完成操作。
2 系统常用参数设定及调整2.1 有关轴的参数设定(1)各轴轴基本参数设定 1001.0:直线轴最小移动单位。
0:公制1:英制1002.1:无挡块参考点设定。
0:无效1:有效1004.1:设定最小输入单位和最小移动单位。
FANUC机器人参考位置功能介绍与设定方法
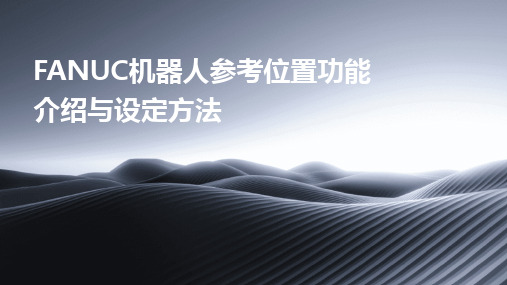
设定过程中出现异常提示
问题原因
可能是由于设定步骤错误、系统参数 设置不当或硬件故障导致。
解决方案
根据异常提示信息,检查设定步骤是 否正确,核对系统参数设置。如果问 题依旧存在,可能需要联系技术支持 进行排查。
应用价值评估
提高生产效率
通过设定合理的参考位置,可以 优化机器人的运动轨迹,减少无 效行程,从而提高生产效率。
降低维护成本
精确的参考位置设定可以减少机 器人的磨损和故障,降低维护成 本和停机时间。
增强产品品质
高精度的位置控制有助于提高产 品的加工精度和一致性,从而提 升产品品质。
未来发展趋势预测
参考位置功能可以帮助机器人快速定位到关键路径点,减少路径规划的
计算量和时间。
03
多机器人协同
在多机器人协同作业的场景中,各个机器人需要共享位置和姿态信息。
通过设定参考位置,可以实现多机器人之间的快速定位和协同运动。
相关术语解析
• 参考位置(Reference Position):在FANUC机器人中,参考位置是指用户设 定的一个或多个特定的机器人位置,用于后续操作中的快速定位或路径规划。
FANUC机器人参考位置功能 介绍与设定方法
目 录
• 参考位置功能概述 • 参考位置类型及特点 • 设定方法与步骤 • 常见问题与解决方案 • 案例分析与应用实例 • 总结与展望
01
参考位置功能概述
定义与作用
定义
参考位置功能是FANUC机器人中的一项重要功能,它允许用户设定一个或多个 特定的机器人位置作为参考点,以便在后续的操作中进行快速定位或路径规划。
FANUC系统1815

FANUC系统,编码器更换后如何设置回零点我的是fanuc系统,加工中心。
更换了一个新的编码器,绝对的编码器。
就是x轴电机屁股后面的红盖盖就是编码器。
更换后,要重新设置零点,回零点,请问如何设置?要详细的操作步骤!满意回答两种方法:A、对准标记设定参考点在机床上设置对准标记,注意对于磨床使用倾斜轴控制功能的轴上不能使用本功能。
准备工作:a:1005#1设为1——各轴返回参考点不使用挡块方式此时返回参考点就不需要使用减速信号*DEC。
b:1815#5设为1——使用绝对位置编码器1815#4设为0——绝对位置编码器原点位置未确立1006#5设为0——返回参考点方向为正向c:切断NC电源,断开主断路器d:把绝对位置编码器的电池连接到伺服放大器上e:接通电源自动检测编码器基准点(检测编码器的1转信号)(如果未进行此项操作继而进行参考点回零的话出现PS0090号报警)a:用手动或者手轮方式进给,让机床电机转动1转以上b:断开电源再接通电源设定参考点a:JOG方式下对各轴手动移动,将机床移动到10 06#5设定的反方向处,例如上面设的1006#5为0即返回参考点方向为正向,则将机床移至负向,如下图:b:按1006#5设定的返回参考点的方向移动机床,直至机床对准标记与参考点位置重合,当位置快要重合时使用手轮进给进行微调。
c:将1815#4设为1——绝对位置编码器原点位置已确立。
B、无挡块返回参考点不需要安装限位开关和挡块准备工作:a:1005#1设为1——各轴返回参考点不使用挡块方式此时返回参考点就不需要使用减速信号*DEC。
b:181 5#5设为1——使用绝对位置编码器1815#4设为0——绝对位置编码器原点位置未确立1006#5设为0——返回参考点方向为正向c:切断NC电源,断开主断路器d:把绝对位置编码器的电池连接到伺服放大器上e:接通电源自动检测编码器基准点(检测编码器的1转信号)(如果未进行此项操作继而进行参考点回零的话出现PS0 090号报警)a:用手动或者手轮方式进给,让机床电机转动1转以上b:断开电源再接通电源设定参考点a:JOG方式下对各轴手动移动至参考点返回方向的反方向,然后以1006#5设置的方向向参考点移动。
FANUC系统培训教案10
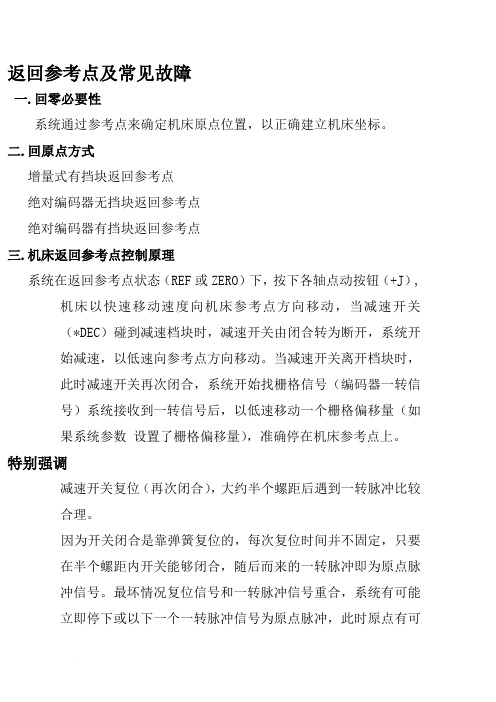
返回参考点及常见故障一.回零必要性系统通过参考点来确定机床原点位置,以正确建立机床坐标。
二.回原点方式增量式有挡块返回参考点绝对编码器无挡块返回参考点绝对编码器有挡块返回参考点三.机床返回参考点控制原理系统在返回参考点状态(REF或ZERO)下,按下各轴点动按钮(+J),机床以快速移动速度向机床参考点方向移动,当减速开关(*DEC)碰到减速档块时,减速开关由闭合转为断开,系统开始减速,以低速向参考点方向移动。
当减速开关离开档块时,此时减速开关再次闭合,系统开始找栅格信号(编码器一转信号)系统接收到一转信号后,以低速移动一个栅格偏移量(如果系统参数设置了栅格偏移量),准确停在机床参考点上。
特别强调减速开关复位(再次闭合),大约半个螺距后遇到一转脉冲比较合理。
因为开关闭合是靠弹簧复位的,每次复位时间并不固定,只要在半个螺距内开关能够闭合,随后而来的一转脉冲即为原点脉冲信号。
最坏情况复位信号和一转脉冲信号重合,系统有可能立即停下或以下一个一转脉冲信号为原点脉冲,此时原点有可能偏移一个螺距的距离,原点返回便不准确了。
基本概念:1.栅格偏移量16/18/21/16i/18i/21i 系统 18500 系统 508-511减速开关由压下断开到复位(由0变为1后)检测到的第1个1转信号后系统的偏移量调整栅格偏移量可调整原点位置2.手动返回参考点方向16/18/21/0i 系统 1006#50系统 3#3设为0,按正方向设为1,按负方向3. 手动返回参考点,同时控制轴数16/18/21/0i 系统 1002#00系统 49#4设为1:3轴设为0:1轴4.第一,第二参考点16/18/21/ 0i 系统 1240 12410 系统 708-711 735-7375.栅格宽度:16/18/21/ 0i 系统 18210 系统 570-573可以在伺服设定画面中参考计数器中直接设定,电机每转进给长度或角度值6.手动返回参考点速度16/18/21/ 0i 系统 14200系统 518 519 520 5217.返回参考点减速速度16/18/21/ 0i 系统 14250 系统 534四.数控系统返回参考点故障1.找不到参考点①机床回零过程无减速动作或一直以减速回零。
FANUC系统校基准点步骤

1、 MDI方式下,按功能键[OFFSET] - [SETTING],找到设定界面,将“写参数”改为“1 可以”,此时参数可写;
2、 按[SYSTEM]进入参数界面,找到1815参数,将需要校参考点的那个轴的1815号参数改为0(直接按0,然后按input即可),关开机一次;
3、 确保1240,1320,1321参数还在,此分别为机床基点坐标值和正负软限位值;
②、重复X轴校基点步骤中的3,4两步;
③、也可粗略的设定Z轴基点,用卷尺直接测量刀盘端面到主轴端面的距离,使之达到参数1240中设定的值,然后重复X轴校基点步骤中的3,4两步即可;
6、 为防止误改参数,将第一步中的“写参数”改为“0 不可以”,基点设定完成。
另外一种校X轴参考点的方法:
前提条件:刀具刀补已知,并且刀具没有被拆下来过;
①、跟对刀步骤一样,先取消刀补(用指令Txx00)和坐标偏移;
②、切削零件;
③、记下当前屏幕上的尺寸(X轴)B;
④、测量零件尺寸;
⑤、计算:A=参数1240中设定的值-刀补-零件尺寸+屏幕上显示的尺寸B
⑥、移动坐标到A点上(X轴基点位置);
⑦、重复X轴校基点步骤中的3,4两步。
如有问题请联系
祝好!
4、 X轴校基点步骤:
①、测量刀盘上镗孔刀座孔中心到镗孔刀座在刀盘上安装面的距离A;
②、使用工具使镗孔刀座孔与主轴中心对中,此时将X轴相对坐标U设定为“2*A”,再使用手轮将X轴向正方向移动至参数1240中设定的坐标(X轴基点位置);
③、将对应轴的1815#5(1815参数从右边数第六位)改为“1”, 关开机一次,再将1815#4改为“1”,再关开机一次;
FANUC数控系统加工中心工件坐标系建立与操作技巧
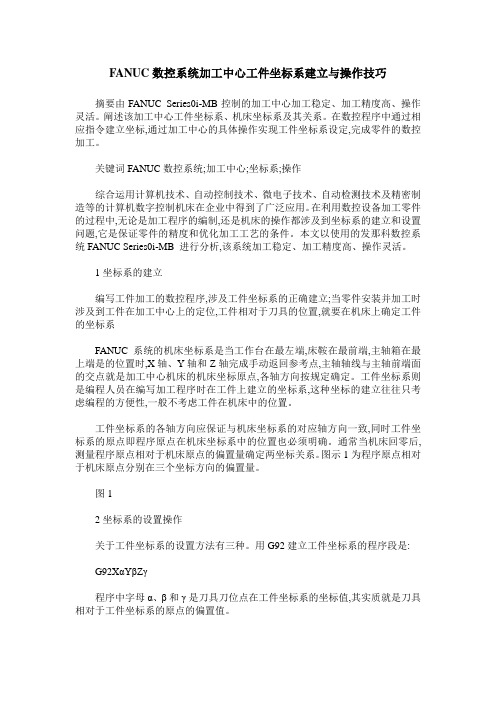
FANUC数控系统加工中心工件坐标系建立与操作技巧摘要由FANUC Series0i-MB控制的加工中心加工稳定、加工精度高、操作灵活。
阐述该加工中心工件坐标系、机床坐标系及其关系。
在数控程序中通过相应指令建立坐标,通过加工中心的具体操作实现工件坐标系设定,完成零件的数控加工。
关键词FANUC数控系统;加工中心;坐标系;操作综合运用计算机技术、自动控制技术、微电子技术、自动检测技术及精密制造等的计算机数字控制机床在企业中得到了广泛应用。
在利用数控设备加工零件的过程中,无论是加工程序的编制,还是机床的操作都涉及到坐标系的建立和设置问题,它是保证零件的精度和优化加工工艺的条件。
本文以使用的发那科数控系统FANUC Series0i-MB 进行分析,该系统加工稳定、加工精度高、操作灵活。
1坐标系的建立编写工件加工的数控程序,涉及工件坐标系的正确建立;当零件安装并加工时涉及到工件在加工中心上的定位,工件相对于刀具的位置,就要在机床上确定工件的坐标系FANUC系统的机床坐标系是当工作台在最左端,床鞍在最前端,主轴箱在最上端是的位置时,X轴、Y轴和Z轴完成手动返回参考点,主轴轴线与主轴前端面的交点就是加工中心机床的机床坐标原点,各轴方向按规定确定。
工件坐标系则是编程人员在编写加工程序时在工件上建立的坐标系,这种坐标的建立往往只考虑编程的方便性,一般不考虑工件在机床中的位置。
工件坐标系的各轴方向应保证与机床坐标系的对应轴方向一致,同时工件坐标系的原点即程序原点在机床坐标系中的位置也必须明确。
通常当机床回零后,测量程序原点相对于机床原点的偏置量确定两坐标关系。
图示1为程序原点相对于机床原点分别在三个坐标方向的偏置量。
图12坐标系的设置操作关于工件坐标系的设置方法有三种。
用G92建立工件坐标系的程序段是: G92XαYβZγ程序中字母α、β和γ是刀具刀位点在工件坐标系的坐标值,其实质就是刀具相对于工件坐标系的原点的偏置值。
- 1、下载文档前请自行甄别文档内容的完整性,平台不提供额外的编辑、内容补充、找答案等附加服务。
- 2、"仅部分预览"的文档,不可在线预览部分如存在完整性等问题,可反馈申请退款(可完整预览的文档不适用该条件!)。
- 3、如文档侵犯您的权益,请联系客服反馈,我们会尽快为您处理(人工客服工作时间:9:00-18:30)。
第一步,判断位置检测器类型:增量式编码器和绝对式编码器。
判断方法:查看系统参数1815第五位APCX勺值0 :增量式编码器,
1:绝对式脉冲编码器
注:(当系统指定此轴使用绝对式脉冲编码器时,伺服模块上必须安装电池来记忆参考点)
第二步,设定参考点:A、增量式(1815.5=0): 1、手动将机床移动到指定的参考点位置(挡块式的必须使会参考点减速信号(*DEC由0变1回到原状。
)
2、MDI模式将参数写保护打开。
3、1815的第四位APZx先改成1,再改成0。
4、关机重启,参数写保护恢复。
5、手动回零检查参考点位置是否正确。
B、绝对式(1815.5=1 ):
1、手动将机床移动到指定的参考点位置。
(挡块式的必须使会参考点减速信号(*DEC由0变1回到原状。
)
2、M DI模式将参数写保护打开。
3、1815的第四位APZx先改成0,再改成1。
4、关机重启,参数写保护恢复。
5 、手动回零检查参考点位置是否正确。
FANUC 18l5t 的参数:
一。
增量方式的编码器伺服电机:(机床每次上电都要进行回零的操作)
1. 1815#5设0,使用增量方式的编码器伺服电机;1815#4设0当前位置不是考点。
2. 关机重启,移动轴到参考点附近(要保证电机至少转一转以上的距离)
3. 选择回零方式,并按轴正向移动,该轴就会找下一个栅格信号,该点即为参考点,然后将1815#5、#4设为1。
(在加工前需要重新进行对刀。
)
二。
绝对方式的编码器伺服电机:(机床首次调好零点后,不再需要机床每次上电都进行回零的操作)
FANUOI MATETD系统无撞块回零点的设定步骤:分别把X轴,Z轴放大器上的电池安装上。
把参数1815#5设为1 ,无撞块回零点方式有效。
把参数1815#4设为零。
在手摇方式下分别把X轴,丫轴,Z轴摇到要设定为零点的地方,再把参数1815#4 设为1.
把机床下电,再重新上电。
在手摇方式下分别把X轴和Z轴摇回100多MM, 再把方式选择放到回零方式,分别进行手动回零操作。
回零完成后,相应轴的回零指示灯会亮。
(手动回零操作完后,X和Z轴的回零灯会亮。
表示零点位置设定完毕。
然后设定软限位的值:参数1320号和参数1321号。
在加工前需要重新进行对刀。
)。